
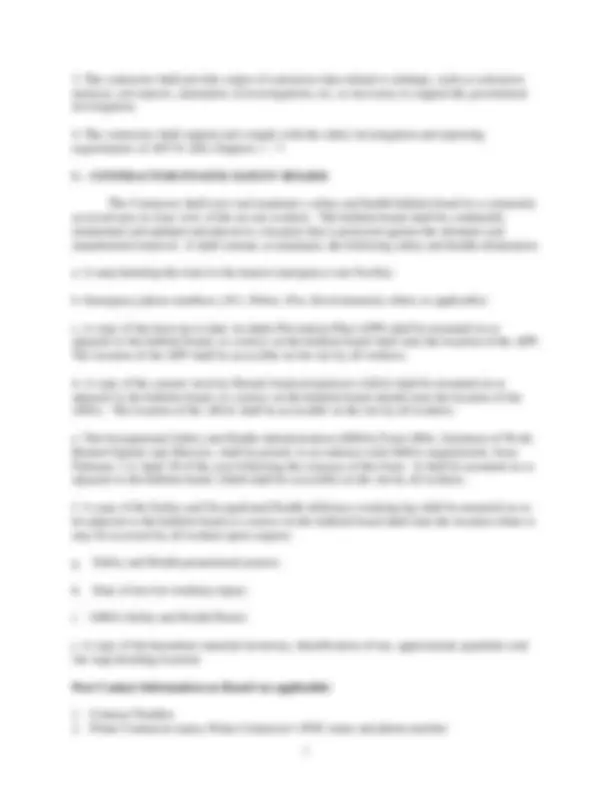
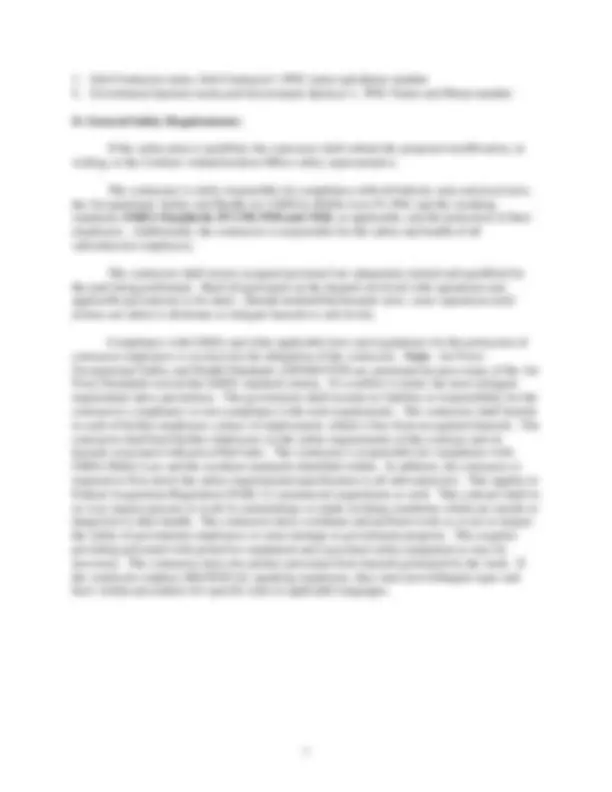
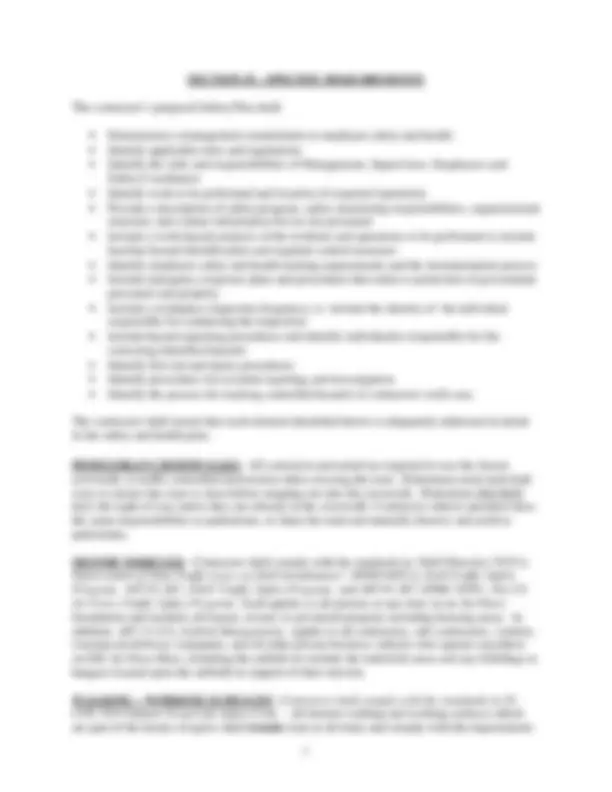
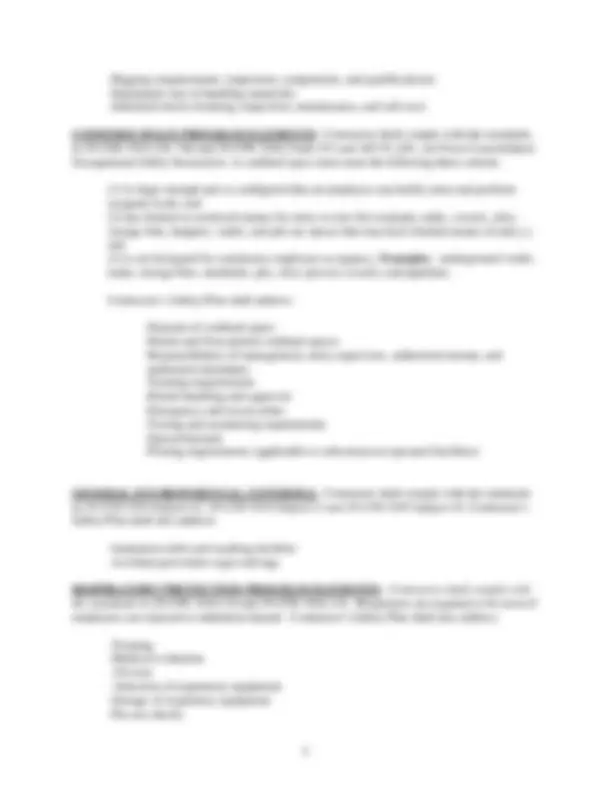
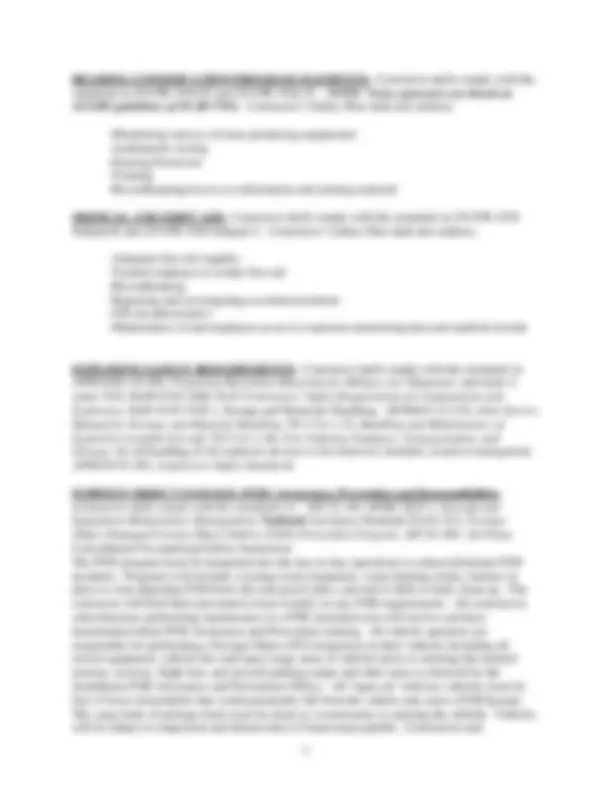
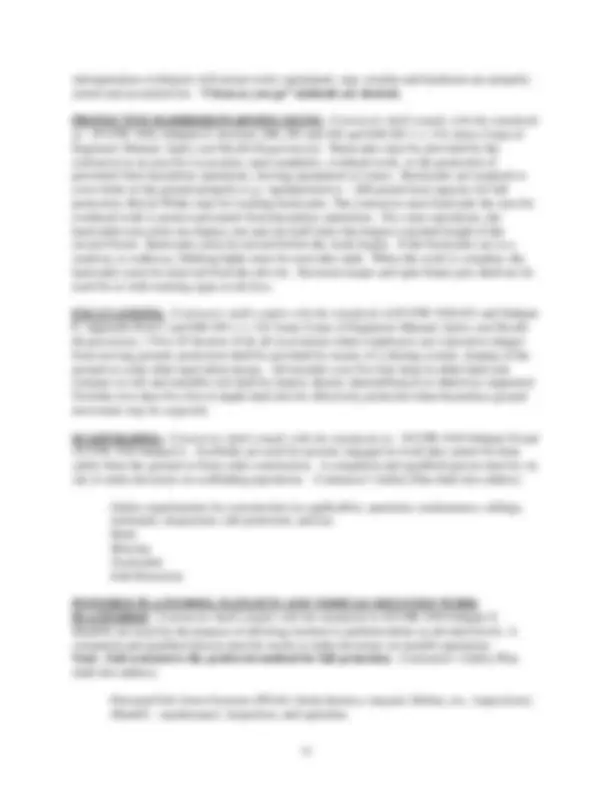
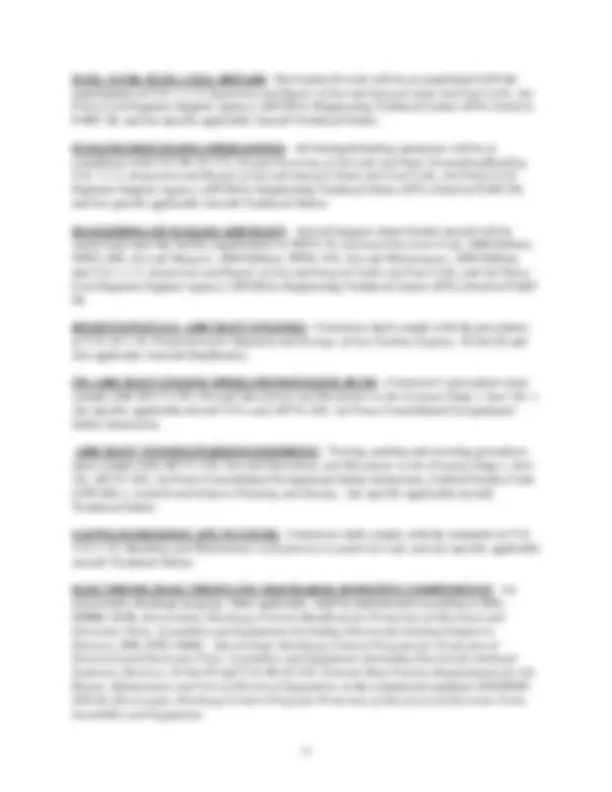
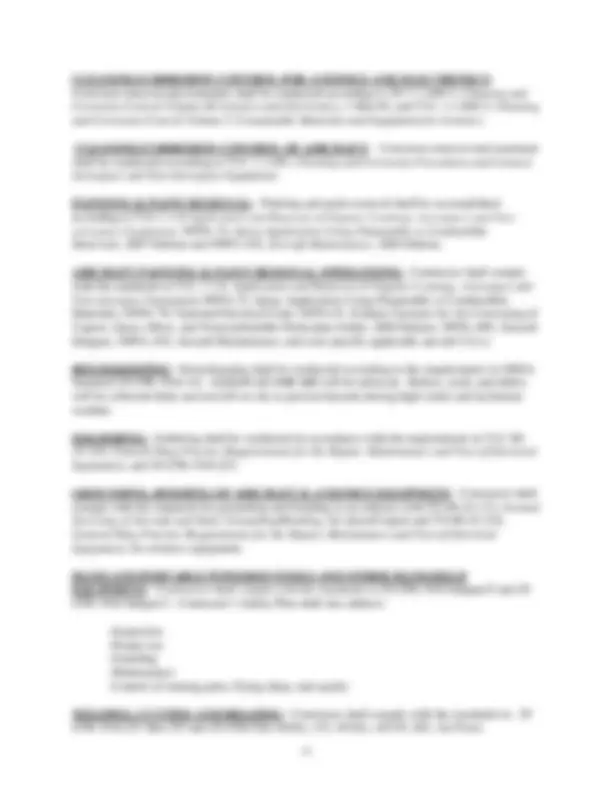
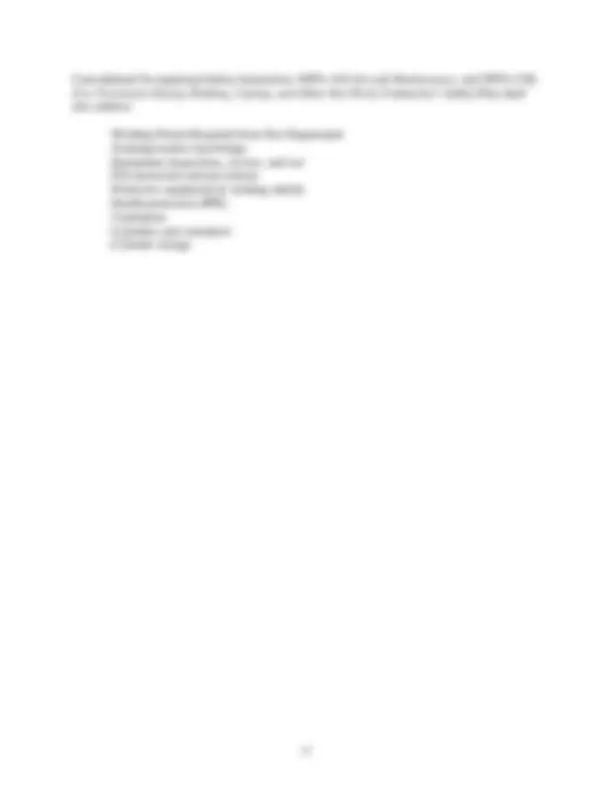
Study with the several resources on Docsity
Earn points by helping other students or get them with a premium plan
Prepare for your exams
Study with the several resources on Docsity
Earn points to download
Earn points by helping other students or get them with a premium plan
Community
Ask the community for help and clear up your study doubts
Discover the best universities in your country according to Docsity users
Free resources
Download our free guides on studying techniques, anxiety management strategies, and thesis advice from Docsity tutors
The identification of segregated work site locations for operations that cannot be co-mingled with general industrial operations. It provides a description of safety programs, safety monitoring responsibilities, organizational structure, and contact information for on-site personnel. The document also includes a work hazard analysis, employee safety and health training requirements, emergency response plans, workplace inspection frequency, hazard reporting procedures, first aid and injury procedures, and procedures for accident reporting and investigation. Contractors are required to comply with various DoD and NFPA standards for different types of operations, including walking and working surfaces, hazardous waste operations, confined space program elements, explosive safety requirements, and more.
What you will learn
Typology: Lecture notes
1 / 15
This page cannot be seen from the preview
Don't miss anything!
DATE: 23 July 2015
Michael R. Harbert, 75 ABW/SEG, (DSN: 777-2125)
A. Safety Program Requirements.
The contractor will implement a safety program plan that ensures protection of Government personnel and property. The program will consist of, as a minimum:
B. Mishap Notification
Mishap notifications shall contain, as a minimum, the following information:
(a) Contract, Contract Number, Name and Title of Person(s) Reporting
(b) Date, Time and exact location of accident/incident
(c) Brief Narrative of accident/incident (Events leading to accident/incident)
(d) Cause of accident/incident, if known
(e) Estimated cost of accident/incident (material and labor to repair/replace)
(f) Nomenclature of equipment and personnel involved in accident/incident
(g) Corrective actions (taken or proposed)
(h) Other pertinent information
D. General Safety Requirements:
If the safety plan is modified, the contractor shall submit the proposed modification, in writing, to the Contract Administration Office safety representative.
The contractor is solely responsible for compliance with all federal, state and local laws, the Occupational, Safety and Health Act (OSHA) (Public Law 91-596) and the resulting standards, OSHA Standards 29 CFR 1910 and 1926 , as applicable, and the protection of their employees. Additionally, the contractor is responsible for the safety and health of all subcontractor employees.
The contractor shall ensure assigned personnel are adequately trained and qualified for the task being performed. Brief all personnel on the hazards involved with operations and applicable precautions to be taken. Should unidentified hazards arise, cease operations until actions are taken to eliminate or mitigate hazards to safe levels.
Compliance with OSHA and other applicable laws and regulations for the protection of contractor employees is exclusively the obligation of the contractor. Note: Air Force Occupational Safety and Health Standards (AFOSH STD) are annotated because many of the Air Force Standards exceed the OSHA standard criteria. If a conflict is noted, the most stringent requirement takes precedence. The government shall assume no liability or responsibility for the contractor's compliance or non-compliance with such requirements. The contractor shall furnish to each of his/her employees a place of employment, which is free from recognized hazards. The contractor shall brief his/her employees on the safety requirements of this contract and on hazards associated with prescribed tasks. The contractor is responsible for compliance with OSHA Public Law and the resultant standards identified within. In addition, the contractor is required to flow down the safety requirements/specification to all subcontractors. This applies to Federal Acquisition Regulation (FAR) 12 commercial acquisitions as well. This contract shall in no way require persons to work in surroundings or under working conditions which are unsafe or dangerous to their health. The contractor must coordinate and perform work so as not to impact the safety of government employees or cause damage to government property. This requires providing personnel with protective equipment and associated safety equipment as may be necessary. The contractor must also protect personnel from hazards generated by the work. If the contractor employs BILINGUAL speaking employees, they must post bilingual signs and have written procedures for specific tasks in applicable languages.
The contractor’s prepared Safety Plan shall:
The contractor shall ensure that each element identified below is adequately addressed in detail in the safety and health plan:
crosswalk, or traffic controlled intersection when crossing the road. Pedestrians must look both ways to ensure the coast is clear before stepping out into the crosswalk. Pedestrians DO NOT have the right of way unless they are already in the crosswalk. Contractor vehicle operators have the same responsibilities as pedestrians, to share the road and mutually observe and yield to pedestrians.
MOTOR VEHICLES : Contractor shall comply with the standards in : DoD Directive 5525.4, Enforcement of State Traffic Laws on DoD Installations ", DODI 6055.4 , DoD Traffic Safety Program, AFI 91-207, USAF Traffic Safety Program, and AFI 91-207 AFMC SUP1, The US Air Force Traffic Safety Program. Each applies to all persons at any time on an Air Force Installation and includes all leased, owned, or privatized property including housing areas. In addition: AFI 13-213 , Airfield Management , applies to all contractors, sub-contractors, vendors, commercial delivery companies, and all other private business vehicles who operate anywhere on Hill Air Force Base, including the airfield (to include the industrial areas and any buildings or hangars located upon the airfield) in support of their mission.
WALKING – WORKING SURFACES Contractor shall comply with the standards in 29 CFR 1910 Subpart D and Life Safety Code. All interior walking and working surfaces which are part of the means of egress shall remain clear at all times and comply with the requirements
-Medical surveillance -Work practices -Engineering controls -Respiratory protection -Protective clothing (PPE)
SYSTEM MODIFICATION-WHICH ALTERS FORM, FIT OR FUNCTION: Contractor shall comply with latest version of Mil Standard 882, Standard Practice for System Safety , and AFI 91-202, The US Air Force Mishap Prevention Program, for system modifications, which alter form, fit, or function.
ELECTRICAL: Contractor shall comply with the standards in 29 CFR 1910 Subpart S, 29 CFR 1926 Subpart K, AFI 91-203, Air Force Consolidated Occupational Safety Instruction and NFPA 70. All electrical wiring must be IAW National Electrical Code (NEC) 70. Electrical wiring and equipment shall be a type listed by UL or another recognized listing agent. Contractor’s Safety Plan shall also address:
-Selection and use of work practices -Training (basic electrical safety knowledge) -Use of equipment (handling, visual inspection, rating of equipment) -GFCI Protection for outside contractor drops and wet/damp areas -Arc Flash
FIRE PROTECTION FOR FACILITIES: Contractor’s procedures shall comply with NFPA 10, Portable Fire Extinguishers, 2007 Edition; NFPA 13, Installation of Sprinkler Systems, 2007 Edition; NFPA 33, Spray Application Using Flammable or Combustible Materials , 2007 Edition; NFPA 70, National Electrical Code , 2008 Edition; NFPA 72, National Fire Alarm Code , 2007 Edition; NFPA 91, Exhaust Systems for Air Conveying of Vapors, Gases, Mists, and Noncombustible Particulate Solids , 2004 Edition.
HAZARDOUS ENERGY CONTROL PROGRAM ELEMENTS (LOCKOUT-TAGOUT) Contractor shall comply with the standards 29 CFR 1910 Subpart S, 29 CFR 1926 Subpart K and AFI 91-203, and Air Force Consolidated Occupational Safety Instruction. Contractor’s Safety Plan should also address: -Purpose of hazardous energy control program -Employee training -Lockout/tagout procedures -Restoring equipment to normal operations -Removal of locks and tags -Periodic inspections -Portable Fire Extinguishers – proper type, inspection, maintenance, testing, and training
MATERIALS HANDLING AND STORAGE: Contractor shall comply with the standards in 29 CFR 1926.250, 953, 957 and 29 CFR 1910.101, Subparts F, H & N; and 29 CFR 1910.178, Powered Industrial Truck. Contractor’s Safety Plan shall also address:
-Storage and handling of materials -Disposal of trash from elevations -Personnel lifting techniques--proper storage to prevent shifting, for stability, etc.
-Rigging (requirements, inspection, components, and qualifications) -Equipment (use in handling materials) -Industrial trucks (training, inspection, maintenance, and safe use)
CONFINED SPACE PROGRAM ELEMENTS: Contractor shall comply with the standards in 29 CFR 1910.120, 146 and 29 CFR 1926.21and 353 and AFI 91-203, Air Force Consolidated Occupational Safety Instruction. A confined space must meet the following three criteria:
(1) Is large enough and so configured that an employee can bodily enter and perform assigned work; and (2) has limited or restricted means for entry or exit (for example, tanks, vessels, silos, storage bins, hoppers, vaults, and pits are spaces that may have limited means of entry.); and (3) is not designed for continuous employee occupancy. Examples : underground vaults, tanks, storage bins, manholes, pits, silos, process vessels, and pipelines.
Contractor’s Safety Plan shall address:
-Hazards of confined space -Permit and Non-permit confined spaces -Responsibilities of management, entry supervisor, authorized entrant, and authorized attendants -Training requirements -Permit handling and approval -Emergency and rescue plans -Testing and monitoring requirements -Special hazards -Posting requirements (applicable to subcontractor operated facilities)
GENERAL ENVIRONMENTAL CONTROLS: Contractor shall comply with the standards in 29 CFR 1910 Subpart G, 29 CFR 1910 Subpart J and 29 CFR 1926 Subpart D. Contractor’s Safety Plan shall also address:
-Sanitation-toilet and washing facilities -Accident prevention signs and tags
RESPIRATORY PROTECTION PROGRAM ELEMENTS: Contractor shall comply with the standards in 29 CFR 1910.134 and 29 CFR 1926.134. Respirators are required to be worn if employees are exposed to inhalation hazard. Contractor’s Safety Plan shall also address:
-Training -Medical evaluation
site/operations evaluators will ensure tools; equipment, rags, residue and hardware are properly stored and accounted for. “Clean as you go” methods are desired.
PROTECTIVE BARRIERS/WARNING SIGNS: Contractor shall comply with the standards in: 29 CFR 1926, Subpart G, Sections 200, 201 and 202 and EM 385-1-1, US Army Corps of Engineers Manual, Safety and Health Requirements. Barricades must be provided by the contractor in an area for excavation, open manholes, overhead work, or the protection of personnel from hazardous operations, moving equipment or cranes. Barricades are required to cover holes in the ground properly (e.g.: rigid/protective – 200 pound load capacity for fall protection, Red & White rope for warning barricades. The contractor must barricade the area for overhead work to protect personnel from hazardous operations. For crane operations, the barricaded area must encompass one and one half times the longest extended length of the erected boom. Barricades must be erected before the work begins. If the barricades are in a roadway or walkway, blinking lights must be used after dark. When the work is complete, the barricades must be removed from the job site. Kerosene lamps and open flame pots shall not be used for or with warning signs or devices.
EXCAVATIONS: Contractor shall comply with the standards in 29 CFR 1926.651 and Subpart P, Appendix B & C and EM 385-1-1, US Army Corps of Engineers Manual, Safety and Health Requirements , 3 Nov 03 Section 25.In all excavations where employees are exposed to danger from moving ground, protection shall be provided by means of a shoring system, sloping of the ground or some other equivalent means. All trenches over five feet deep in either hard and compact or soft and unstable soil shall be sloped, shored, sheeted/braced or otherwise supported. Trenches less than five feet in depth shall also be effectively protected when hazardous ground movement may be expected.
SCAFFOLDING: Contractor shall comply with the standards in: 29 CFR 1910 Subpart D and 29 CFR 1926 Subpart L. Scaffolds are used for persons engaged in work that cannot be done safely from the ground or from solid construction. A competent and qualified person must be on site to make decisions on scaffolding operations. Contractor’s Safety Plan shall also address:
-Safety requirements for construction (as applicable), operation, maintenance, railings, toeboards, inspections, fall protection, and use -Rails -Bracing -Toeboards -Fall Protection
POWERED PLATFORMS, MANLIFTS AND VEHICLE-MOUNTED WORK PLATFORMS: Contractor shall comply with the standards in 29 CFR 1910 Subpart F_._ Manlifts are used for the purpose of allowing workers to perform duties at elevated levels. A competent and qualified person must be onsite to make decisions on manlift operations. Note: Fall restraint is the preferred method for fall protection. Contractor’s Safety Plan shall also address:
-Personal Fall Arrest Systems (PFAS) {body harness, lanyard, lifeline, etc., inspections} -Manlift – maintenance, inspection, and operation
AERIAL LIFT EQUIPMENT: Contractor shall comply with the standards in 29 CFR 1910.66 Subpart F , American National Standards Institute (ANSI) ANSI 92.2, ANSI 92.5, ANSI 92.6 , and AFI 91-203, Air Force Consolidated Occupational Safety Instruction. Aerial lifts have inherent risks associated with their use. The Air Force has established procedures to ensure only trained and qualified personnel are operating aerial lifts. In the past, the lifts were identified that did not meet regulatory safety requirements and foreign objects (FO) were found on the equipment. Based on this negative trend and a fatal mishap in years past, the following policies, procedures and processes will be adhered to when aerial lifts are used to support a contractor mission:
(1) Aerial devices shall include the following types of vehicle mounted aerial devices used to elevate personnel to job sites above ground:
(2) Aerial equipment may be made of metal, wood, fiberglass reinforced plastic, or other material; may be powered or manually operated, and are deemed to be aerial lifts whether or not they are capable of rotating about a substantially vertical axis.
CONTRACTOR AERIAL LIFT DEVICES: Contractors shall comply with the standards in 29 CFR 1910.67 , 29 CFR 1926.453, and ANSI 92.2, Standards for "Vehicle Mounted Elevating and Rotating Work Platforms. Contractors, subcontractors, vendors, commercial delivery companies, and all other private business vehicles will comply with the following requirements while operating any type of aerial lift as described above, while on a DOD installation. This includes contractor owned equipment, leased or rented equipment acquired to support the contractual activities. Unless otherwise provided in this section, aerial devices (aerial lifts) acquired on or after July 1, 1975, shall be designed and constructed in conformance with the applicable requirements of the American National Standards for "Vehicle Mounted Elevating and Rotating Work Platforms, ANSI A92.2 - 1969, including appendix which is incorporated by reference as specified in 29 CFR 1910.66. Aerial lifts acquired for use before July 1, 1975 which do not meet the requirements of ANSI A92.2 - 1969, may not be used after July 1, 1976, unless they shall have been modified so as to conform to the applicable design and construction requirements of ANSI A92.2 - 1969.Prior to bringing an aerial device on a DoD installation, the contractor will ensure: Aerial devices meet the above 29 CFR 1910.66 and 1910. requirements. Aerial devices meet certification and classification for the designated work area. Aerial devices are serviceable, and all safety devices, warning devices, and interlocks operate. Aerial devices (regardless of guardrail, mid-rail or toe board configuration) will have fall protection attach points installed. Aerial devices will contain the manufacturer’s manual and operator’s safety manual. The applicable ANSI Standard will satisfy the requirement for a safety manual. The contractor and operating employee will be trained and certified on the leased/rental device and provide visual certification upon request. Aerial lifts will not be used to deliver employees to higher levels unless so certified.
PERSONAL PROTECTIVE EQUIPMENT FOR AERIAL LIFT DEVICES: To ensure compliance with 29 CFR 1910.66, Subpart F, Appendix C, 29 CFR 1910.133, Personal
FUEL TANK /FUEL CELL REPAIR: Fuel tank/cell work will be accomplished IAW the requirements in T.O. 1-1-3, Inspection and Repair of Aircraft Integral tanks and Fuel Cells , Air Force Civil Engineer Support Agency (AFCESA) Engineering Technical Letters (ETL) listed in PART III, and list specific applicable Aircraft Technical Orders.
FUELING/DEFUELING OPERATIONS: All fueling/defueling operations will be in compliance with T.O. 00-25-172, Ground Servicing of Aircraft and Static Grounding/Bonding, T.O. 1-1-3, Inspection and Repair of Aircraft Integral Tanks and Fuel Cells , Air Force Civil Engineer Support Agency (AFCESA) Engineering Technical letters (ETL) listed in PART III, and list specific applicable Aircraft Technical Orders.
HANGERING OF FUELED AIRCRAFT: Aircraft hangars where fueled aircraft will be stored must meet the facility requirements in NFPA 70, National Electrical Code , 2008 Edition, NFPA 409, Aircraft Hangars , 2004 Edition; NFPA 410, Aircraft Maintenance , 2004 Edition, and T.O. 1-1-3, Inspection and Repair of Aircraft Integral Tanks and Fuel Cells , and Air Force Civil Engineer Support Agency (AFCESA) Engineering Technical Letters (ETL) listed in PART III.
REMOVE/INSTALL AIRCRAFT ENGINES: Contractor shall comply with the procedures in T.O. 2J-1-18, Preparation for Shipment and Storage of Gas Turbine Engines , 30 Jun 02 and (list applicable Aircraft Handbooks).
ON-AIRCRAFT ENGINE OPERATIONS/ENGINE RUNS: Contractor’s procedures must comply with AFI 11-218, Aircraft Operations and Movement on the Ground , Chap 1, Sect 1D, 1, site specific applicable aircraft T.O.s and AFI 91-203, Air Force Consolidated Occupational Safety Instruction.
AIRCRAFT TOWING/PARKING/MOORING: Towing, parking and mooring procedures must comply with AFI 11-218, Aircraft Operations and Movement on the Ground , Chap 1, Sect 1D, AFI 91-203, Air Force Consolidated Occupational Safety Instruction, Unified Facility Code (UFC260-1, Airfield and heliport Planning and Design, site specific applicable aircraft Technical Orders.
SAFING/EGRESS/ESCAPE SYSTEMS: Contractor shall comply with the standards in T.O. 11A-1-33, Handling and Maintenance of Explosives-Loaded Aircraft , and site specific applicable aircraft Technical Orders.
ELECTRONIC/ELECTROSTATIC DISCHARGE SENSITIVE COMPONENTS: An electrostatic discharge program, when applicable, shall be implemented according to MIL- HDBK-263B, Electrostatic Discharge Control Handbook for Protection of Electrical and Electronic Parts, Assemblies and Equipment (Excluding Electrically Initiated Explosive Devices), MIL-STD-1686C, Electrostatic Discharge Control Program for Protection of Electrical and Electronic Parts, Assemblies and Equipment (Excluding Electrically Initiated Explosive Devices), 25 Oct 95 and T.O. 00-25-234, General Shop Practice Requirements for the Repair, Maintenance and Test of Electrical Equipment, or the commercial standard ANSI/ESD S20.20, Electrostatic Discharge Control Program-Protection of Electrical & Electronic Parts, Assemblies and Equipment.
Corrosion removal and treatment shall be conducted according to TO 1-1-689-3, Cleaning and Corrosion Control Volume III Avionics and Electronics, 1 Mar 05; and T.O. 1-1-689-5, Cleaning and Corrosion Control Volume V Consumable Materials and Equipment for Avionics.
CLEANING/CORROSION CONTROL OF AIRCRAFT: Corrosion removal and treatment shall be conducted according to T.O. 1-1-691, Cleaning and Corrosion Prevention and Control, Aerospace and Non-Aerospace Equipment.
PAINTING & PAINT REMOVAL: Painting and paint removal shall be accomplished according to T.O. 1-1-8 Application and Removal of Organic Coatings, Aerospace and Non- aerospace Equipment, NFPA 33, Spray Application Using Flammable or Combustible Materials , 2007 Edition and NFPA 410, Aircraft Maintenance , 2004 Edition.
AIRCRAFT PAINTING & PAINT REMOVAL OPERATIONS: Contractor shall comply with the standards in T.O. 1-1-8, Application and Removal of Organic Coatings, Aerospace and Non-aerospace Equipment,NFPA 33, Spray Application Using Flammable or Combustible Materials, NFPA 70, National Electrical Code, NFPA 91, Exhaust Systems for Air Conveying of Vapors, Gases, Mists, and Noncombustible Particulate Solids, 2004 Edition; NFPA 409, Aircraft Hangars, NFPA 410, Aircraft Maintenance, and (cite specific applicable aircraft T.O.s)
HOUSEKEEPING: Housekeeping shall be conducted according to the requirements in OSHA Standard 29 CFR 1910.141. CLEAN AS YOU GO will be enforced. Refuse, trash, and debris will be collected daily and not left on site to prevent hazards during high winds and inclement weather.
SOLDERING: Soldering shall be conducted in accordance with the requirements in T.O. 00- 25-234, General Shop Practice Requirements for the Repair, Maintenance and Test of Electrical Equipment, and 29 CFR 1910.253.
GROUNDING, BONDING OF AIRCRAFT & AVIONICS EQUIPMENT: Contractor shall comply with the standards for grounding and bonding in accordance with TO 00-25-172, Ground Servicing of Aircraft and Static Grounding/Bonding, for aircraft repair and TO 00-25-234, General Shop Practice Requirements for the Repair, Maintenance and Test of Electrical Equipment, for avionics equipment.
HAND AND PORTABLE POWERED TOOLS AND OTHER HAND-HELD EQUIPMENT: Contractor shall comply with the standards in 29 CFR 1910 Subpart P and 29 CFR 1926 Subpart I_._ Contractor’s Safety Plan shall also address:
-Inspection -Proper use -Guarding -Maintenance -Control of rotating parts, flying chips, and sparks
WELDING, CUTTING AND BRAZING: Contractor shall comply with the standards in: 29 CFR 1910.251 thru 255 and 29 CFR1926.102(b), 153, 453(b), AFI 91-203, Air Force