
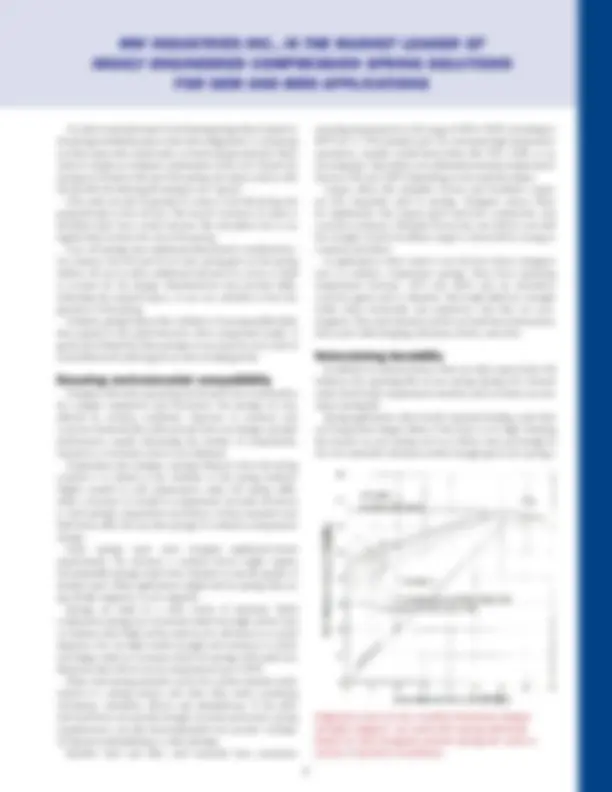
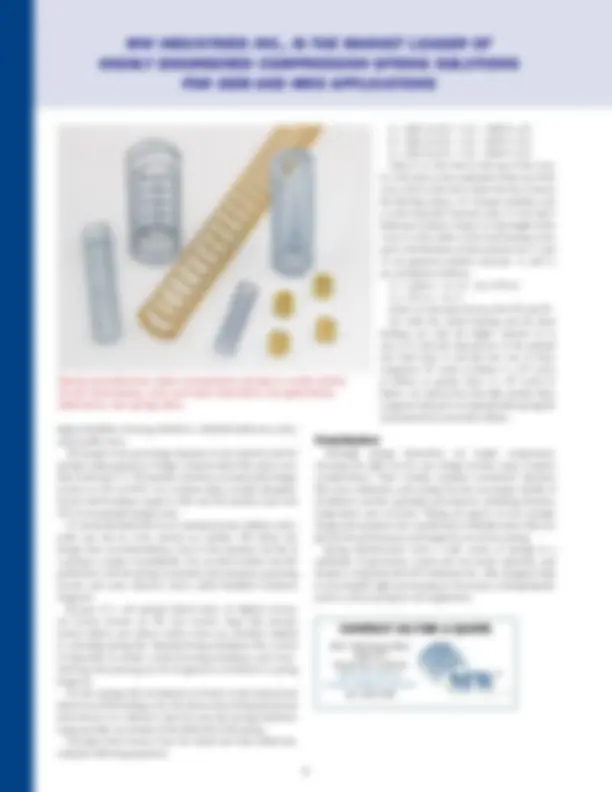
Study with the several resources on Docsity
Earn points by helping other students or get them with a premium plan
Prepare for your exams
Study with the several resources on Docsity
Earn points to download
Earn points by helping other students or get them with a premium plan
Community
Ask the community for help and clear up your study doubts
Discover the best universities in your country according to Docsity users
Free resources
Download our free guides on studying techniques, anxiety management strategies, and thesis advice from Docsity tutors
basics of design: Designing with compression springs
Typology: Papers
Uploaded on 06/11/2025
1 / 4
This page cannot be seen from the preview
Don't miss anything!
Take a look at any industrial or consumer product with moving parts; there’s a good chance you’ll find a spring that is somehow integral to that design. Compression springs are among the most common types of springs, although many designs also incorporate extension, torsion, and specialty springs. Compression springs vary widely to accommodate the different environmental, geometric, and dynamic requirements of their varied applications. Many designers assume that they will need to have a spring custom- designed for their needs. In reality, spring manufacturers stock a dizzying array of spring types, sizes, and constructions. Designers can often find springs in stock that meet their application needs and avoid the cost of custom design. This can be particularly useful in cases where lead times are short, or designers might want to try more than one spring solution. So, the first step in designing with springs is to identify the specific needs of your application. As it pertains to springs, you’ll need to ask yourself what force the spring needs to supply or withstand, how much and how frequently the spring needs to deflect, what space the spring needs to fit into, what environment the spring will be used in, and how the spring will be installed.
Defining the forces on the spring in your design is a good starting point for determining the spring you need. Compression springs react against compressing forces. Whether they are assisting in the opening of a heavy-duty die or maintaining pressure on a gasket in a tiny valve, it’s vital to know the force they have to exert or resist. You probably already have a feel for the magnitude of this force based on the weight of your die, the durometer of your gasket, or other application-specific forces. Just remember that a compression spring only reacts the component of the force that is aligned with its axis. Next, translate the required force into a spring configuration. Ideal springs operate according to Hooke’s Law: F = -kx where F is the reacting force of the spring, and x is the spring deflection, and k is the spring constant in lb/ in or N/mm. The presence of the negative sign indicates that the spring supplies more reactive force the more it is deflected. The linear nature of k holds as long as the spring is within its elastic limit, and higher values of k represent stiffer springs. The spring constant, k, in turn, depends on the spring’s physical attributes: k = G×d^4 ÷ [8×D^3 ×na] where na is the number of active coils, d is the spring wire diameter, and D is the spring coil’s mean diameter, calculated by subtracting d from the coil’s outer diameter. G is the material’s shear modulus, calculated from the more commonly stated elastic or Young’s modulus by: G = E ÷ 2(1 + ν) where E is the Young’s modulus and ν is the material’s Poisson’s ratio. These equations address the spring constant for the most common type of compression spring, the coil design. For wave springs, spring constant calculations must also
Load (P) PI Deflection (f)
spaces between the coils. However, the spring constant, k, discussed above that linearly links spring force and deflection is only constant between approximately 15 to 85% of a coil spring’s deflection. Different ranges apply for wave and disc springs. Be sure to choose a spring with a range of motion wide enough that your likely deflection falls within this linear region. Some applications need a high deflection range. You could look at the difference between free and solid heights, but to achieve longer life and a greater factor of safety, look for the manufacturer’s suggested maximum deflection. Some stock coil springs are available with suggested maximum deflections as large as 16 in. For applications that require the smallest possible solid height with low to moderate forces in comparison to cavity size, look for tapered springs. This design allows the coils nest for a solid height that approaches the wire thickness. If you need a spring that deflects as little as possible with high forces in comparison to cavity size, consider a disc spring. Other choices include stock coil springs that can have suggested maximum deflections as small as 0.030 in or less, and urethane springs.
In addition to deflection, you’ll want to consider the space into which you are fitting your spring. Does your spring need to fit into a bore? If so, you’ll be more interested in outer diameter (OD) of the spring coil. If the spring is meant to slide onto a shaft, inner diameter (ID) is your dimension of interest. Not all specifications list ID, but it can be easily calculated as follows: ID = OD - 2d where d is the wire diameter. In either case, take care to note the manufacturer’s tolerance range on the spring’s diameter and the tolerance range on your bore or shaft to allow the spring to operate freely. take the width and thickness of the flat wire into account along with the number of waves per turn. Disc springs or Belleville washers are another type of compression spring. These are often used when designers need to react relatively high loads with minimal deflection. Their force-deflection curve is approximately linear for certain ratios of cone height to material thickness. The load on the spring for a given deflection is: P =[(Ef) [(h-f/2)(h-f)t + t^3 ]] ÷ [(1-μ^2 )MR^2 ] where P is the load in pounds, E is the Young’s modulus of the disc material, f is the deflection, μ is the material’s Poisson’s ratio, R is the radius from the disc centerline to the point where the cone contacts the bearing surface, h is the cone height, and t is the material thickness. M is a ratio factor given by: M = 6(α-1)^2 ÷ α^2 (π ln α) where α is ratio of the disc’s outer diameter to its inner diameter. The preceding load equation can be plotted to determine the theoretical spring constant for a single disc washer. Disc springs are commonly stacked to achieve the desired height, deflection, and stiffness. To determine the effective spring constant for a stack of nested washers, also referred to as a parallel stack, sum the spring constants of each spring in the stack: keff = k 1 + k 2 + k 3 …+ kn For springs stacked in series, that is, OD to OD or ID to ID, take the reciprocal of the sum of the reciprocals of the spring constants of each spring in the stack: keff = 1 ÷ (1/k 1 + 1/k 2 + 1/k 3 …+ 1/kn) A third category is urethane compression springs. These are solid, thick-walled urethane tubes with durometer ratings of 65A, 80A, 90A, or 95A. A urethane spring can carry over five times the load of a typical steel spring of comparable size. These types of springs are most ideal for general use applications where high levels of precision are not required. For any of these spring types, knowing any combination of your force, deflection, and spring constant will put you on the right track to specifying the perfect spring. For instance, in high force applications, spring designers use 0.75-in-thick hand-drawn steel wire to form coils 6.25 in diameter and 12 in long that can react up to 1,500 lb. On the other end of the spectrum, stock springs can be designed for tiny loads, less than 0.02 lb. These springs are made from 0.005 in-diameter music wire coiled for an outer diameter of 0.062 in and a free length of 0.16 in.
In addition to choosing a compression spring that can react the forces it will see in your application, you’ll need to be sure its deflection capabilities also meet your needs. Spring specifications usually cite a compression spring’s free height, the height of the spring when no load is applied. Specs also list the solid height, how tall the spring is when it is completely compressed with no
S 1 = Ef[C 1 (h-f/2) + C 2 t] ÷ [MR^2 (1-μ^2 )] S 2 = Ef[C 1 (h-f/2) – C 2 t] ÷ [MR^2 (1-μ^2 )] S 3 = Ef[T 1 (h-f/2) + T 2 t] ÷ [MR^2 (1-μ^2 )] where S 1 is the stress at the top of the cone, S 2 is the stress at the underside of the top of the cone, and S 3 is the stress where the disc contacts the bearing surface. E is Young’s modulus, and μ is the material’s Poisson’s ratio. F is the disc’s deflection (initial or final), h is the height of the cone, R is the radius of the load bearing circle, and t is the thickness of the material. M, C1, and C2 are geometry-related constants. T 1 and T 2 are calculated as follows: T 1 = α[αln α – (α-1)] ÷ [(α-1)^2 ln α] T 2 = (0.5 α) ÷ (α-1) where α is the ratio between the OD and ID. For both the initial loading and the final loading, use only the higher amount of S 2 and S 3 to find the intersection of the preload and final load. It will fall into one of three categories: 10^5 cycles to failure, 5 x 10^5 cycles to failure, or greater than 2 x 10^6 cycles to failure. An intersection that falls outside these categories indicates an unpredictable spring life and potential for premature failure.
Although springs themselves are simple components, choosing the right one for your design involves many complex considerations. These include standard mechanical elements like stress, deflection, and cycling, but also encompass details of installation and the operating environment, including abrasion, temperature and corrosion. Taking all aspects of your spring’s design and operation into consideration will help ensure that you get the best performance and longevity out of your spring. Spring manufacturers stock a wide variety of springs in a multitude of geometries, metal and non-metal materials, and finishes. Companies like MW Industries Inc. offer designers help in choosing the right stock spring or, if necessary, in designing the perfect custom spring for each application. high probability of lasting 100,000 to 1,000,000 deflection cycles, and possibly more. The design stress percentage depends on the material and the spring’s unique geometry. Fatigue-resistant alloys like music wire, alloy steels and 17-7 PH stainless steel have recommended design stresses at 45% of MTS. Less resistant alloys include phosphor bronze and beryllium copper at 40% and 302 stainless steel with 35% recommended design stress. To extend the likely life of your spring beyond a million cycles, make sure the its cyclic stresses are another 10% below the design stress recommendation. Even in this situation, the life of a spring is a matter of probability. You can delve further into life predictions with the spring’s maximum and minimum operating stresses and some reference charts called Modified Goodman Diagrams. Because of a coil spring’s helical form, its highest stresses are torsion stresses on the wire surface. Steps that prevent surface defects and relieve surface stress are, therefore, helpful in extending spring life. Manufacturing techniques like control of impurities in metals, careful drawing techniques, and stress- relieving shot peening are all recognized as beneficial to spring longevity. For disc springs, life calculations are based on the preload and final stress of the loading cycle. The intersection of the preload and final stresses on a reference chart for your disc spring’s thickness range provides an estimate of the likely life of the spring. Calculate both stresses from the initial and final deflections using the following equations:
9501 Technology Blvd. Suite 401 Rosemont, IL 60018 www.mw-ind.com e-mail: info@mw-ind.com 847.349.