
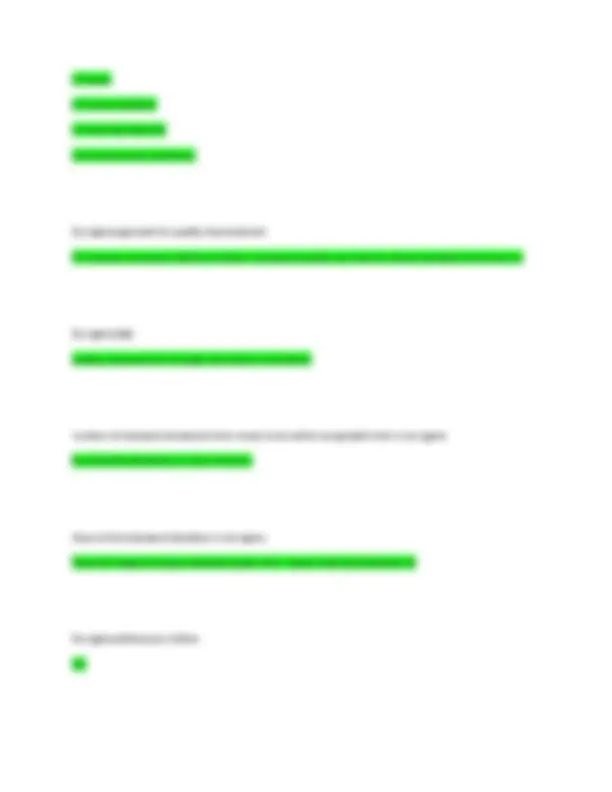
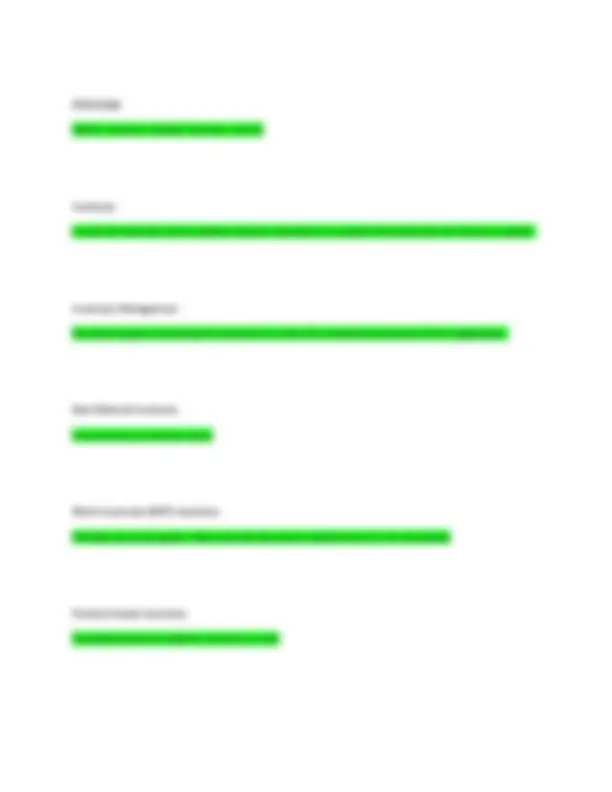
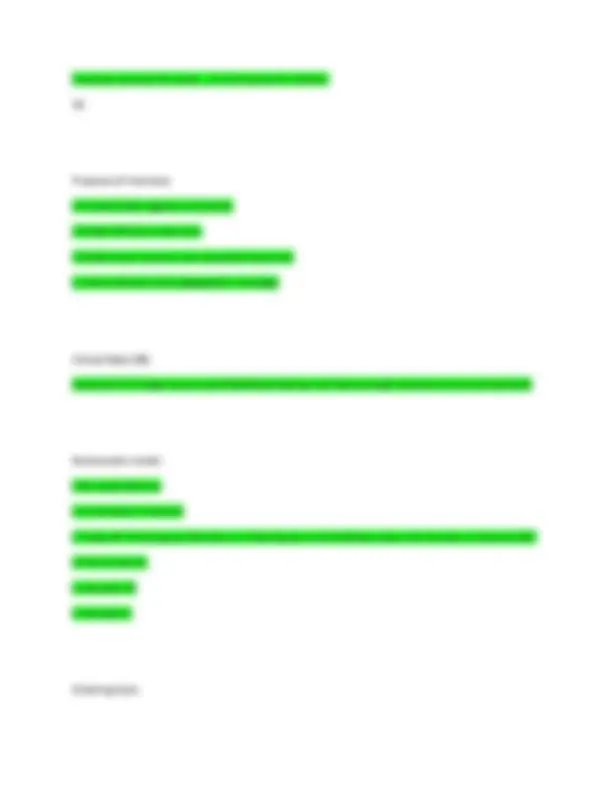
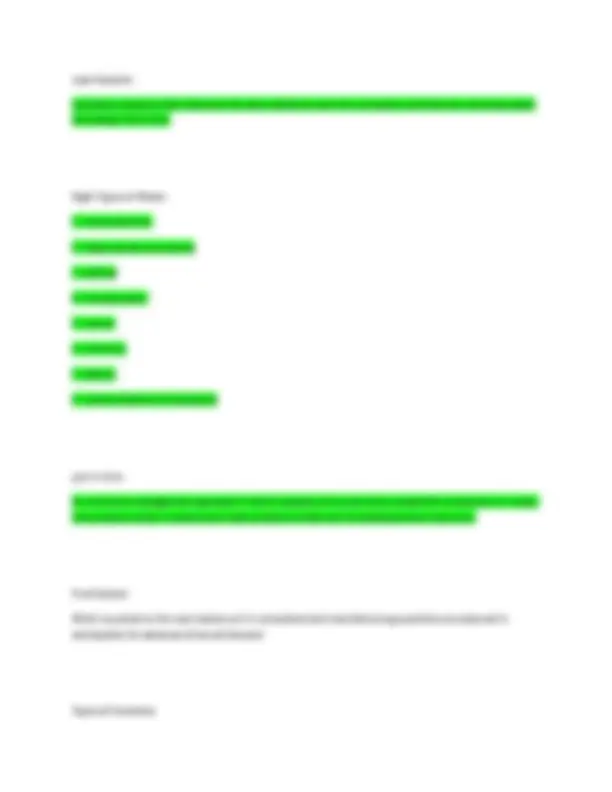
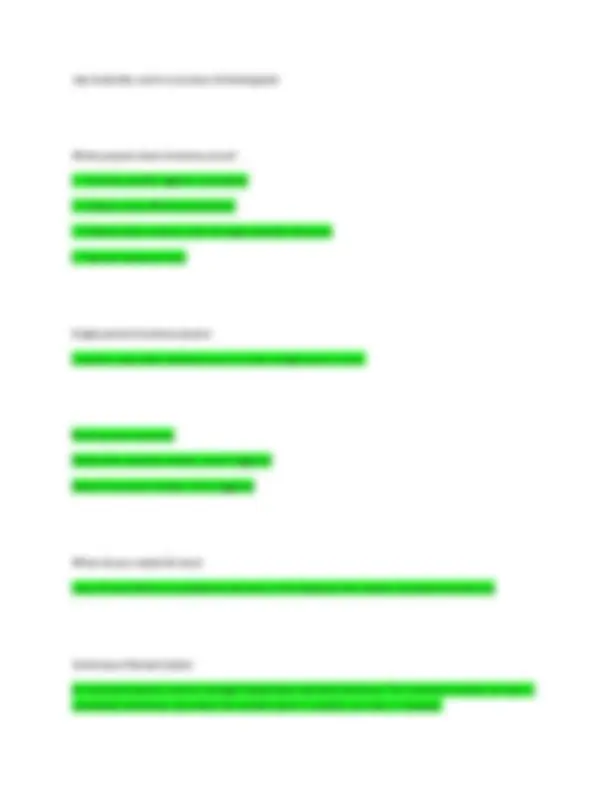
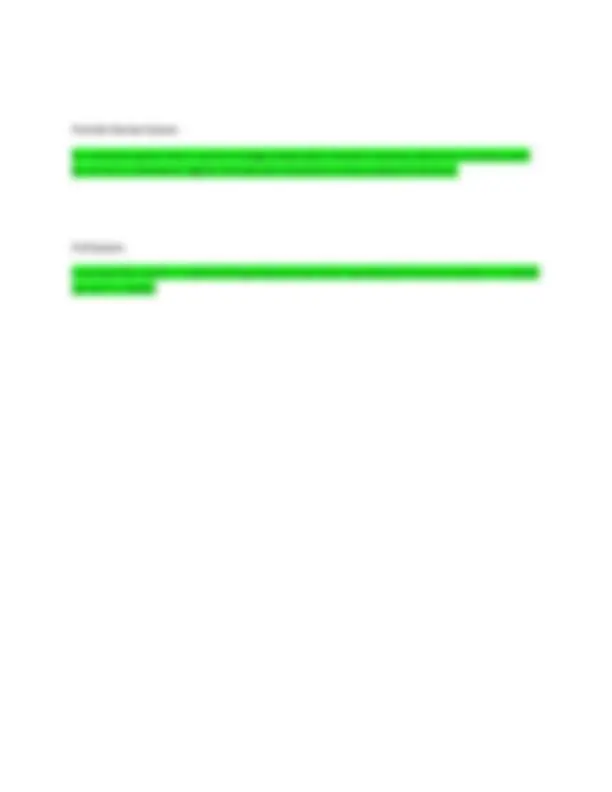
Study with the several resources on Docsity
Earn points by helping other students or get them with a premium plan
Prepare for your exams
Study with the several resources on Docsity
Earn points to download
Earn points by helping other students or get them with a premium plan
Community
Ask the community for help and clear up your study doubts
Discover the best universities in your country according to Docsity users
Free resources
Download our free guides on studying techniques, anxiety management strategies, and thesis advice from Docsity tutors
Bcor 2206 Final Exam CU Boulder Latest Prep Guide With Real Final Exam Questions With Correct Answers/ Bcor 2206 Final Exam 2025 (Brand New!)
Typology: Exams
1 / 10
This page cannot be seen from the preview
Don't miss anything!
Product Quality the degree to which output meets customer requirements- is determined by a combination of design and conformance quality Design Quality fit between designed features and customer requirements Conformance Quality degree to which a delivered product or service meets its design specification Four Components to cost of poor quality prevention costs, appraisal costs, internal failure costs, external failure costs Prevention Costs costs associated with preventing defects and limiting failure and appraisal costs Appraisal costs costs associated with inspection to asses quality levels
Internal failure costs costs from defects found before delivery to the customer External failure costs costs associated with defects found after delivery to customer Total Quality Management (TQM) A management system for a customer-focused organization that involves all employees in continual improvement. TQM Principles o Customer satisfaction: customers are the ultimate judge o Employee involvement: everyone in the organization impacts quality o Continuous improvement: starting with those "on the line", not top management central tenet of TQM Most cost effective to eliminate source rather than treat symptom of poor quality Four sources of variation in a process's output
DMAIC(6σ) define, measure, analyze, improve, control Inventory A stock of materials used to satisfy customer demand or to support the production of services or goods. Inventory Management The planning and controlling of inventories to meet the competitive priorities of the organization. Raw Material Inventory Unprocessed, purchased inputs Work-in-process (WIP) Inventory Partially processed goods. Raw materials have been transformed, but not completed Finished Goods Inventory Completed product ready for shipment or sale
Inventory accounts for what __% of all assets for retailers 30 Purposes of inventory o Provide buffer against uncertainty o Enable efficient production o Enable lower product costs (quantity discounts) o reduce delivery times (geographic coverage) Critical Ratio (CR) represents the target service level (likelihood that you will have enough inventory to serve all demand) Newsvendor model: o No replenishment o Uncertainty in demand o Trade-off: Ordering too little (Cu) vs. Ordering too much (Co)How many units to order or produce (Q)? o Find Cu and Co o Calculate CR o Calculate Q Ordering Costs
Economic Order Quantity (EOQ) minimizes total acquisition costs; the point where holding costs and ordering costs are equal EOQ o Non-immediate replenishment o Known and deterministic demand o Stable over time Re-order Point (ROP) Level of inventory that triggers replenishment Lead time (LT) The time that elapses the placement of an order to receiving the units requested. Make sure time and demand in the same units of time. Zara on inventory Management § Information sharing =Better forecasts § Small batches, exclusivity =Understocking and overstocking are less costly at Zara § Frequent and fast shipments =Shorter lead times, which decrease reorder point and safety stock
Lean Systems operations systems that maximize the value added by each of a company's activities by removing waste and delays from them Eight Types of Waste
Periodic Review System An inventory system that is used to manage independent demand inventory where the inventory level for an item is checked at regular intervals and restocked to some predetermined level. Pull System a concept that results in material being produced only when requested and moved to where it is needed just as it is needed