
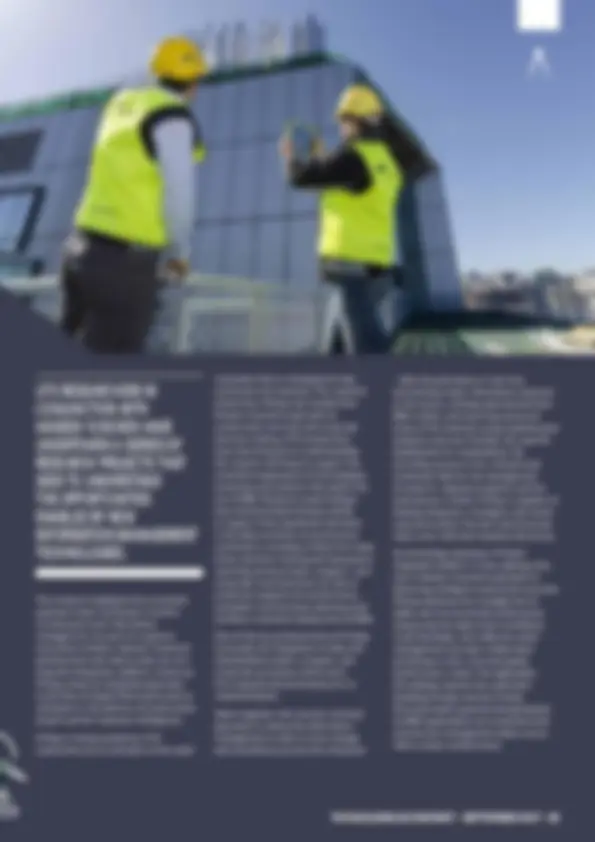
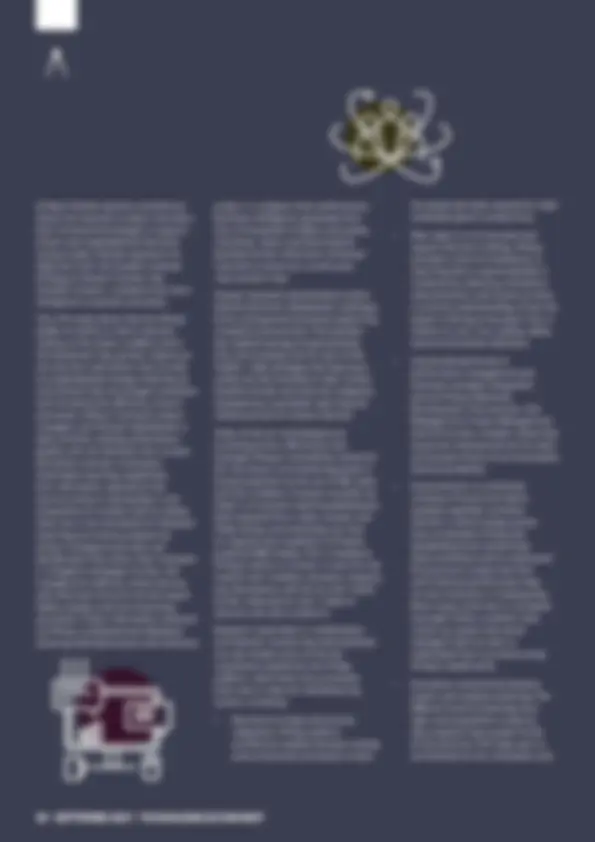
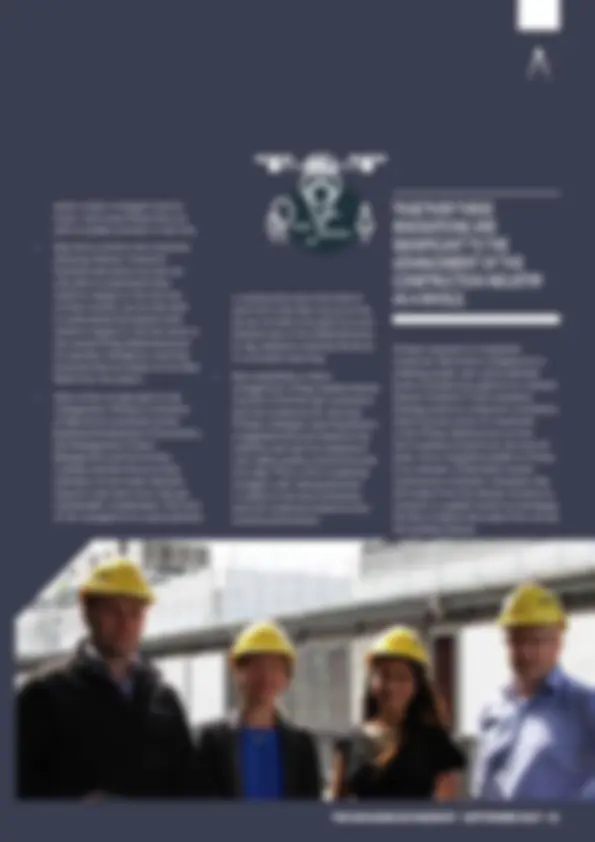
Study with the several resources on Docsity
Earn points by helping other students or get them with a premium plan
Prepare for your exams
Study with the several resources on Docsity
Earn points to download
Earn points by helping other students or get them with a premium plan
Community
Ask the community for help and clear up your study doubts
Discover the best universities in your country according to Docsity users
Free resources
Download our free guides on studying techniques, anxiety management strategies, and thesis advice from Docsity tutors
This report explores how Hansen Yuncken, a leading construction contractor, is utilizing data as an enterprise asset through the use of building information modeling (BIM), the Internet of Things (IoT), machine learning, and smart infrastructure. the potential benefits and challenges of increased data integration and the role of HYway, Hansen Yuncken's integration platform, in supporting real-time data-driven decision making, predictive analytics, and consistent BIM deployment.
Typology: Study notes
1 / 5
This page cannot be seen from the preview
Don't miss anything!
The use of digital building data is transformative for all construction industry professionals, and above all for the main contractor. The digitization of building information is reshaping the roles and responsibilities of many of Australia’s top Tier 1 and 2 contractors, including their relationship to project stakeholders up- and down- stream of delivery who plan, design, operate, and maintain buildings and infrastructure.
The flow of digitised information, through the use of building information modelling (BIM), the Internet of Things (IoT), machine learning, and smart infrastructure, has the potential to enable greater levels of integration across both the project and corporate activities of construction firms, which have long been considered separately. Whether related to the building product, its management processes or the contractor’s business strategy, digital information is no longer collected, analysed and made available through a contractor’s single mainframe computer; it is now available in a highly distributed manner. For tech-savvy construction contractors, data collection either occurs automatically via the IoT – including embedded sensors and small consumer devices such as smartphones
previously very separate activities) in the development and delivery processes of construction require sophisticated quality control systems and standardised digital workflows throughout project delivery and across the corporate business activities. This systems approach emphasises the importance of aligned implementation and integration across a construction contractor’s organisational network and throughout the entire project life cycle. The potential of increased integration raises new questions about the potential for delivery and corporate business improvement whilst also presenting new challenges in the longer term use and reuse of information about the built asset itself. There are questions about the collation of data to support operational decisions (at the project and program level) as well as strategic decisions (at the business and corporate level). There is also increasing potential for contractors to use data analytics to interrogate this information in new ways to improve both the building’s performance and help improve the performance of owners operating and maintaining the facility being delivered. New challenges also arise as the volume of digital data is doubling in size every two years. Building projects that were delivered through paper-based methods are now modelled across multiple dimensions and with a variety of model uses. Together with the vast amounts of project management data collected, a need to better leverage the flow of digital information is seeing a steady but deliberate change in the way contractors approach its use and reuse. Research on the transformative effects of digitised information on construction contractors in Australia is nascent.
As a result of these rapidly evolving capabilities in computing, it is not surprising that main contractors are seeking new ways to leverage the vast amounts of data generated on projects, across programs of projects, and throughout their organisations’ functional business units. The integration systems that can create a ‘digital thread’ are now being developed and implemented, which provides a link between the building product and project with corporate and strategic level business activities. Such integration and flow of digital information thus signals an important turning point for main contractors. Enterprise-level information systems are not new, and high levels of maturity are typically found in the integration platforms that support the development and production processes of complex products in discrete manufacturing, such as the aerospace and automotive sectors. Arguably, the same levels of integration have until recent years been unfeasible in the construction sector due to the structural differences between these industries. The new levels of data integration and information flow across temporary project stakeholders (and their
DATA MINING, MACHINE LEARNING, AND ARTIFICIAL INTELLIGENCE ARE BEING USED MORE FREQUENTLY TO ANALYSE DATA AND MAKE PREDICTIONS ABOUT THE FUTURE.
HYway’s flexible systems architecture allows the business to adopt innovative, best-of-breed technologies to support project and organisational functions using an agile modular approach. Its alignment with the broader business strategy at Hansen Yuncken has resulted in leaner, consistent and more transparent corporate processes.
The UTS study shows that the HYway platform’s ability to inform decision making at the project coalface and in the boardroom has positive impacts on not only the triple bottom line but also on organisational change, fostering an environment that encourages innovation and increasing the efficiency of work processes. Hansen Yuncken’s project managers use HYway’s dashboards in daily activities utilising performance graphs and risk indicators from project disciplines and sub-contractors. Automated reporting capabilities from information captured at the source process is saving days in the preparation of monthly reports. Added value lies in the elimination of ‘cleansed’ reporting (commonly prepared by project managers) and early risk identification that utilise ‘lead’ indicators in mitigation strategies. Further, site management staff use mobile devices with electronic forms for all site-based Safety, Quality and Commissioning processes. Project information collected via HYway is analysed and displayed showing individual project and collective
project- or program-level performance. Business intelligence generated from tens of thousands of safety and quality checklists, issues and observations facilitate further refinement of Hansen Yuncken’s process as a continuous improvement loop. Hansen Yuncken’s administrators utilise tailored electronic dashboards, roadmaps, forms and approval processes supporting consistent procurement. The business has realised savings of approximately 2hrs of processing time for each of the 12,000+ trade packages that have been performed electronically to date. Further benefits include improved risk mitigation, transparency, automated reporting and refined process for lessons learned. State-of-the-art technologies are providing further efficiencies that leverage HYway’s extensibility. Using the IoT, the project commissioning phase is being supported via the use of QR codes with the condition of assets recorded via iPads in structured reporting dashboards. Data captured from codes, sensors and iPads during commissioning can then be mapped and visualised in HYway’s graphical BIM display. This is leading to HYway’s ability to monitor in real-time the location and condition of assets, mapping any discrepancy with the as-built model, further reducing the time it takes to discover and solve problems. Research undertaken in collaboration with Hansen Yuncken has demonstrated via case studies some of the key innovations enabled by the HYway platform, which have only previously been seen in discrete manufacturing sectors, including:
the speed and scale required to make noticeable gains in productivity.
senior project managers need to know—and using HYway they are able to update priorities in real time.
in construction since the kinds of short-term risks that crop up on the job are not able to be given as much attention due to the traditional focus on lag indicators, whereby the focus is on incident reporting.
HYway’s approach to integrated enterprise information management is enabling greater and unprecedented levels of productivity gains to be realised. Hansen Yunken’s IT and innovation strategy points to a long-term orientation, where success relies on investment in the HYway infrastructure to drive their business forward over the next 50 years. As an integration platform, HYway is an exemplar of Australian-owned construction contractor innovation that will enable firms like Hansen Yuncken to compete in a global market by leveraging the flow of digital information from across the building network.
TOGETHER THESE INNOVATIONS ARE SIGNIFICANT TO THE ADVANCEMENT OF THE CONSTRUCTION INDUSTRY AS A WHOLE.