
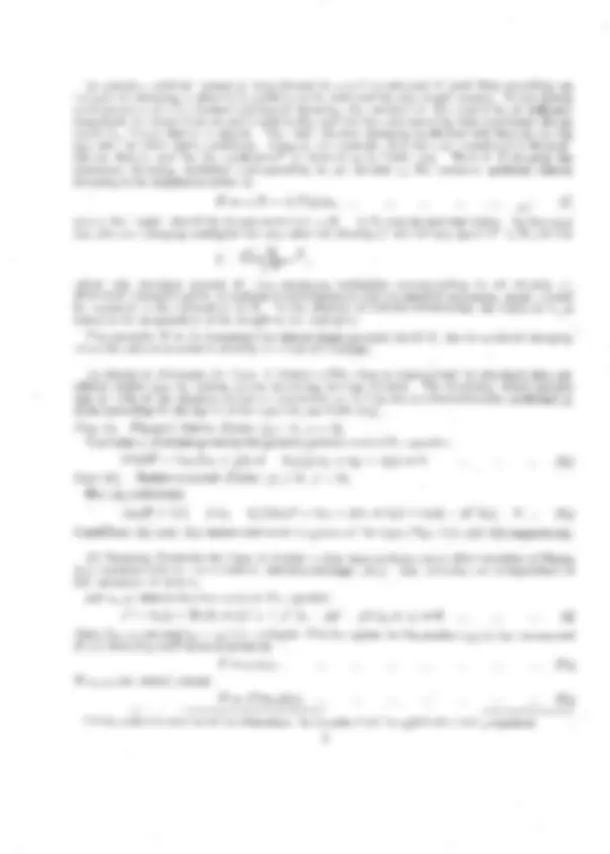
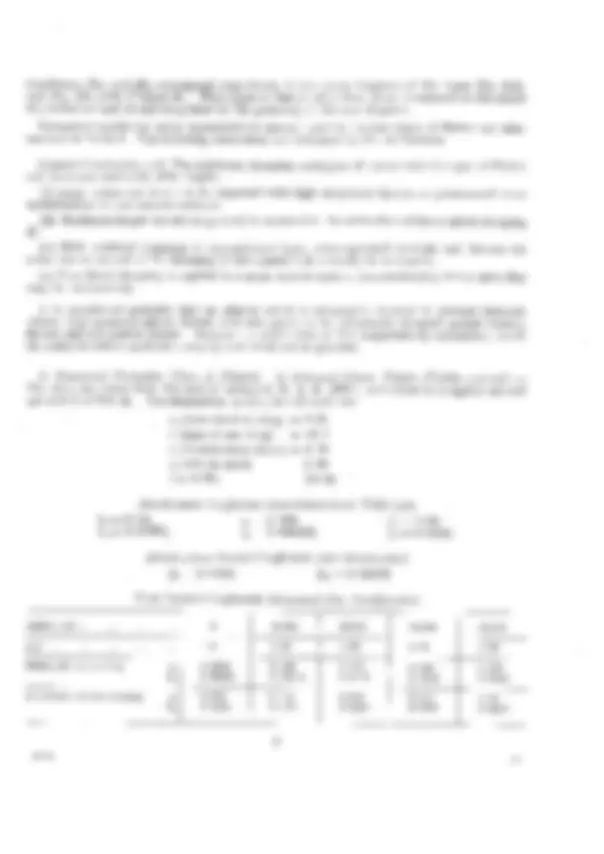
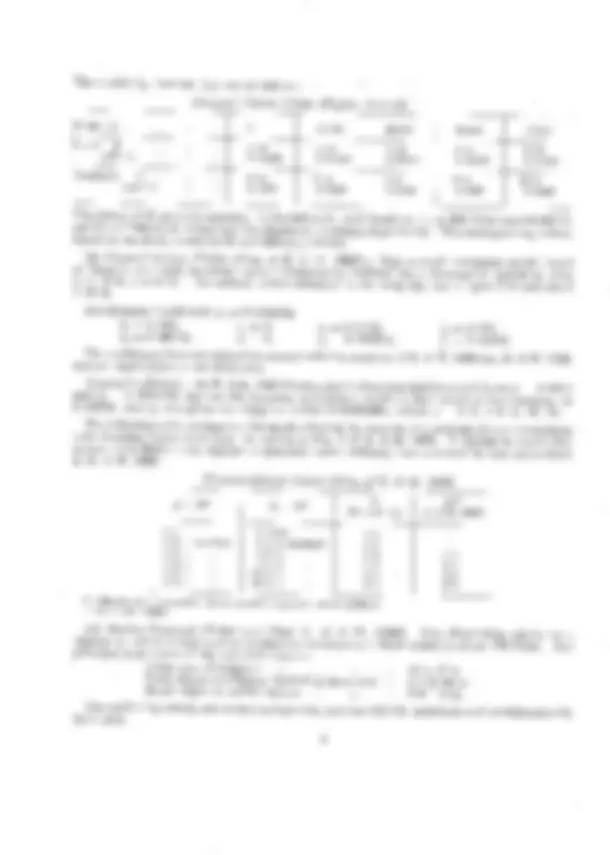
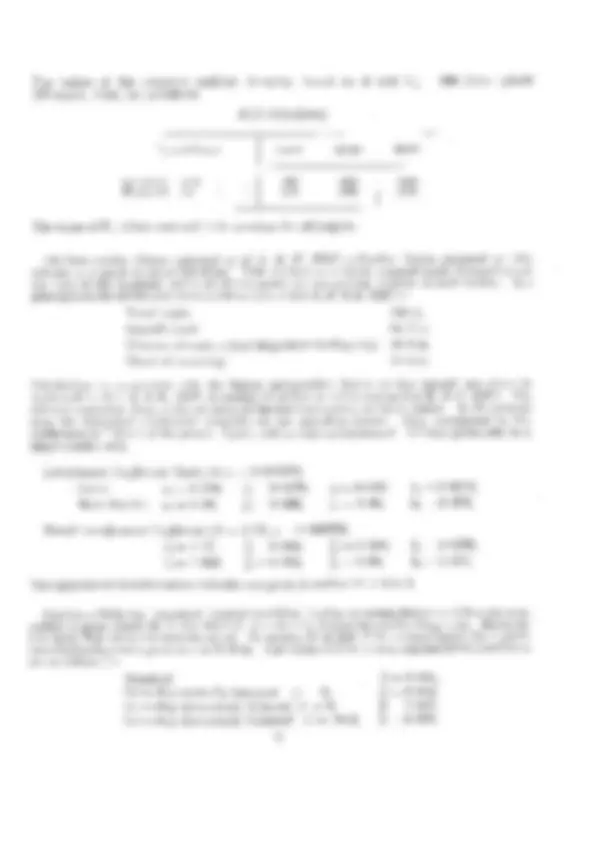
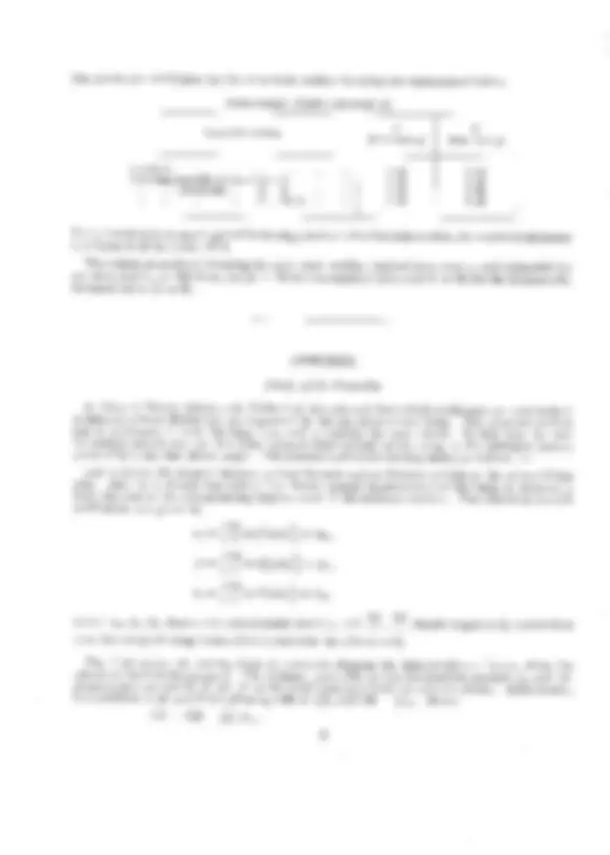
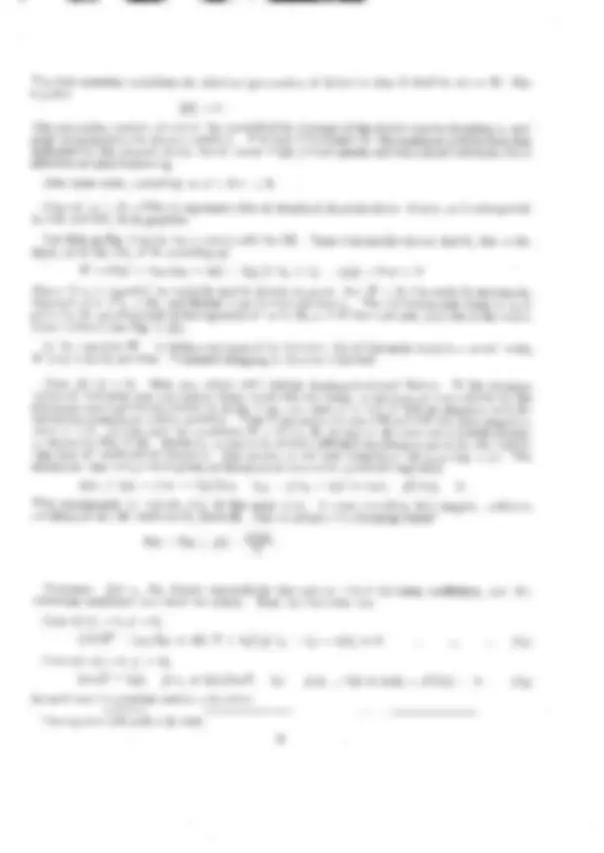
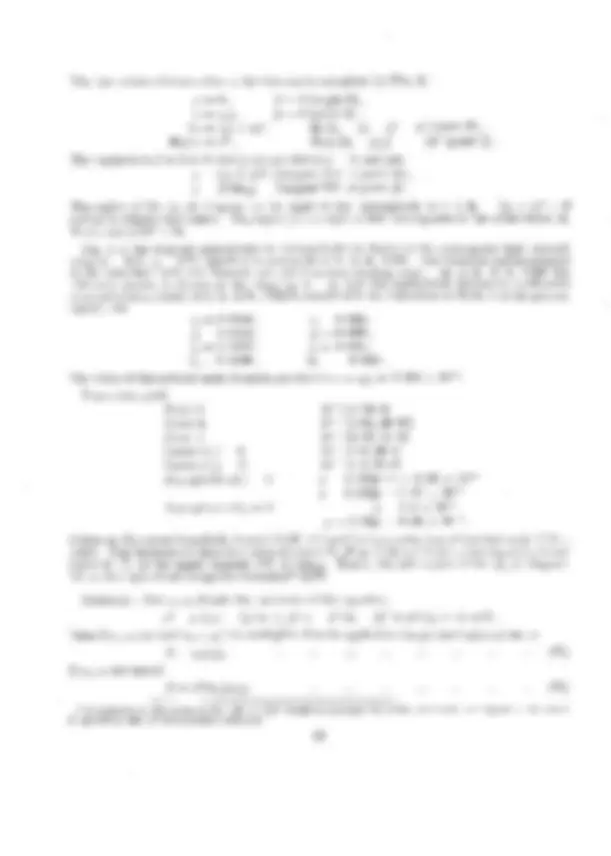
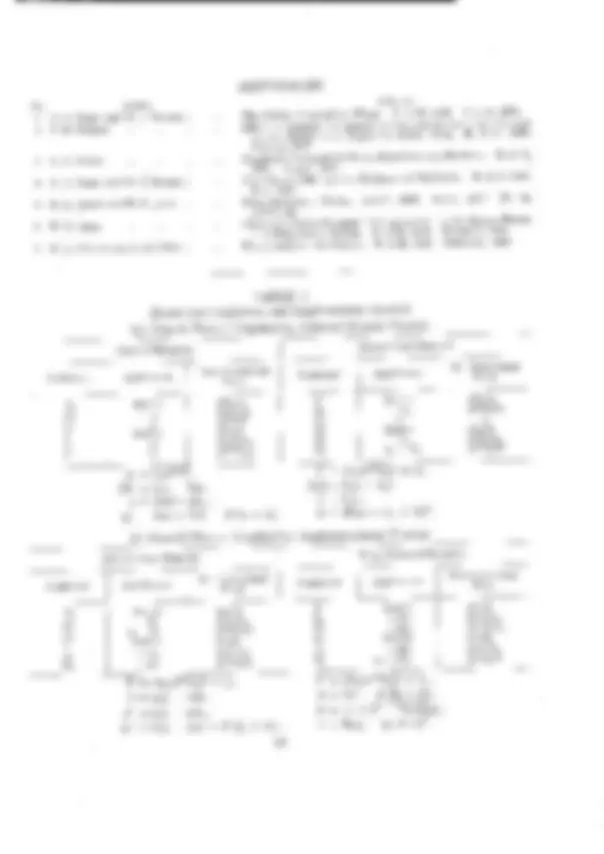
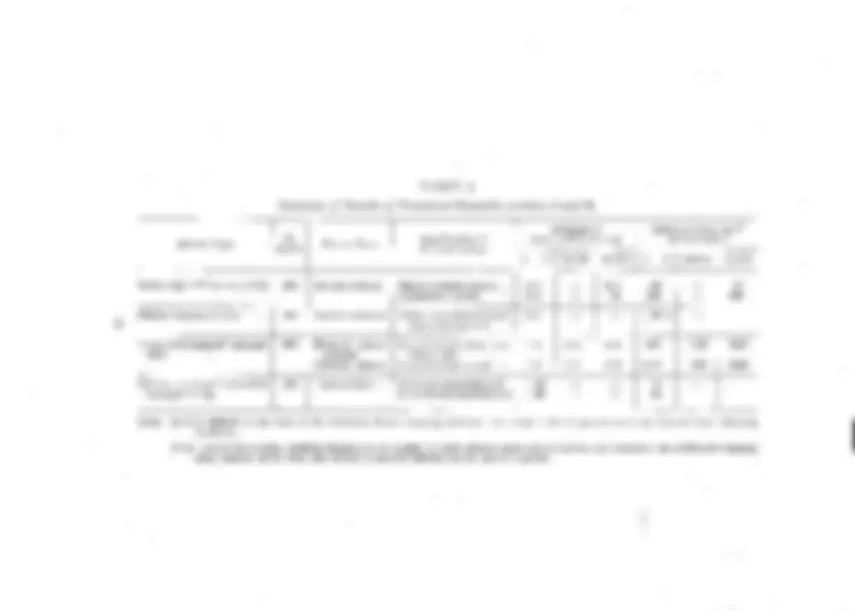
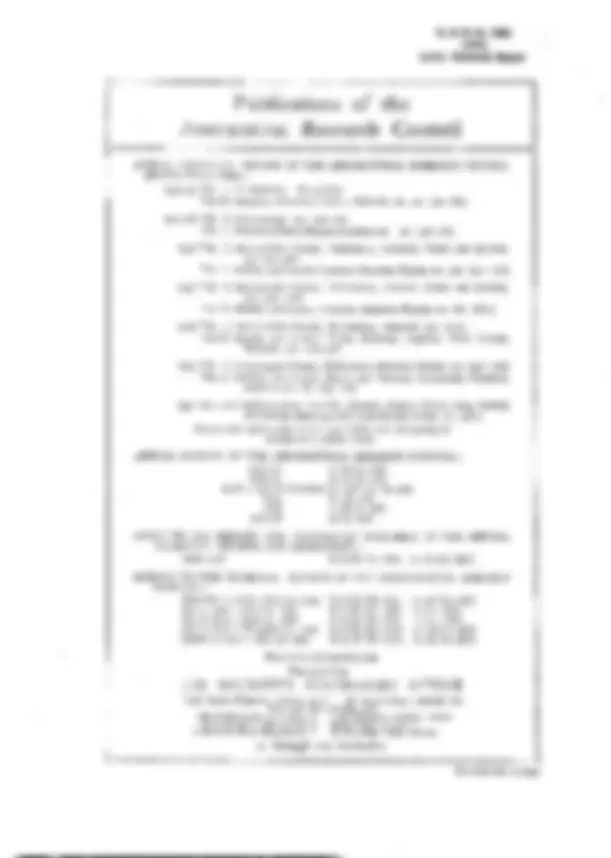
Study with the several resources on Docsity
Earn points by helping other students or get them with a premium plan
Prepare for your exams
Study with the several resources on Docsity
Earn points to download
Earn points by helping other students or get them with a premium plan
Community
Ask the community for help and clear up your study doubts
Discover the best universities in your country according to Docsity users
Free resources
Download our free guides on studying techniques, anxiety management strategies, and thesis advice from Docsity tutors
The prevention of binary flutter in aviation through damping. The author, R.A. Frazer, presents the conclusions of his research, which include the variation of the minimum damping multiplier R with flutter type and the impact of structural density or mass-underbalance on large values of R. The document also includes formulas and numerical examples for different types of flutter, such as flexural-aileron flutter and servo-rudder flutter.
What you will learn
Typology: Lecture notes
1 / 18
This page cannot be seen from the preview
Don't miss anything!
Z' ~-P'-.
/ N ~- " /.-':< <;2' ~, Y'
./1 7-t^ ';^ " Y - : ~2"^ ~ " ' J^ ,"5>-</ / ' i~_i'~-//L
' :. i; ,: ;./',],i:%.................. ,j <', [,% o ,..^ 7i~i^ '
< " " " ~ :"' r " -' '~" '~' = ~ ......... ; 7 " H[[ I~,iJ"%I l'_;!'~',~, t [P-;' ' l,[ ..i {: "- il ! o,A-,.I ~S'0,¢
. r,
iOAl_ V ;i it h
FLe 2 r e v e n t ~ o n °^ o^ f B~ns~r °^ y ~'~utter
by Artiicia~ ©ampinS
C r o ~ o z C o p y N g ~ t Re;emed
L O N D O N , " HIS M A J E S T Y ' S S T A T I O N E R Y O F F i C ~
P&xc~. 4s 5d N~.'r
The Prevention of Binary Flutter by
Damping
R. A. FRAZF.R, B.A., D.Sc.,
of the Aerodynamics Division, N. P. L.
Artificial
Summary.--Range of InvesEgation.--Formulae are obtained which provide an estimate of the amount of artificial control needed to prevent binary flutter. Results are expressed in terms of a 'minimum damping multiplier' R, defined as the ratio of the least direct damping coefficient required for absolute flutter prevention to the ' n a t u r a l ' direct aerodynamic damping coefficient of the control surface concerned. Numerical results are obtained for five different types of aircraft. ComIusioas.--The main conclusions are as follows :-- (i) R varies with the type of flutter and increases markedly with l~eight. (ii) Large values of R are to be expected with high structural density or mass-underbalance of the control surfaces. (iii) Maximum height should (in general) be assumed in the estimation of artificial damping. (iv) With artificial damping of conventional type servo-operated controls and devices for reduction or cut-out of the damping at low speeds will normally be necessary. (v) If artificial damping is applied to a main control surface, mass-balancing of the servo-flap may be necessary.
surfaces from the standpoint of flutter prevention have long been recognized.* Recently it has been suggested that artificial damping might be preferable to mass-balancing as a means of preventing flutter, since weight might be saved. The purpose of the present paper is to provide simple formulae from which the amount of additional damping required can be estimated. Attention is restricted to binary flutter, which is referred to as being of Class A or B according
stiffness coefficients are zero (cl = c~ -- 0) ; whereas with Class B all the aerodynamic stiffnesses are present. The formulae obtained differ for the two classes of flutter• The detailed proofs, which assume simple classical derivative theory and depend on the properties of test conics,~ are given in the Appendix. In general, the control surfaces considered are assumed to be mass underbalanced.
The damping values obtained are theoretically sufficient for the absolute prevention of flutter
absolute flutter prevention to the ' n a t u r a l ' direct aerodynamic damping coefficient of the control surface concerned. The value of R varies with the altitude h owing to the increasing influence of the structural inertias with decreasing air density p.
* See, for example, recommendation (e) of section 9, R. & M. 11551. t See Chapters III and VIII of R. & M. 1155I.
Also Conclusion (d) on p. 1 of R. & IV[. 16852.
(9zoo~) A
Conditions (B~) and (B~) correspond respectively to test conic diagrams of the types Fig. 2(d),
the formulae used should be guided by the geometry of the test diagram. Numerical results for some representative aircraft and for various types of flutter are sum- marized in Table 2. ~Ihe following conclusions are indicated by the calculations.
and increases markedly with height. (fi) Large values for R are to be expected with high structural density or pronounced mass underbalance of the control surfaces. (iii) Maximum height should (in general) be assumed in the estimation of the artificial damping K. (iv) With artificial damping of conventional type, servo-operated controls and devices for reduction or cut-out of the damping at low speeds will normally be necessary. (v) If artificial damping is applied to a main control surface, mass-balancing of the servo-flap may be unnecessary.
It is considered probable that an aileron which is adequately damped to prevent flexural- aileron and torsional-aileron flutter, will also prove to be adequately damped against ternary flutter and tab-aileron flutter. However, a verification of this conjecture by calculation would be desirable before altificial damping were tried out in practice.
The data are taken from the end of section 2, R. & M. 2551 a, and relate to a fighter aircraft (aircraft S of Ref. 5). ~fhe dimensions, in feet, for full-scale are Co (ro0t-chord of wing) = 5. s (span Of one wing) = 18. G (aileron mean chord) = 1. s~ (aileron span) = 6- 1 = 0.57s = 10.
bl -- 5.78, el = 0.298, fl = 1.39, b~ = 0-00972, e2 = 0.009225, f2 = 0. 0146.
Po =: 0.0162, d2o = 0"00054.
dtitude (ft).....
"abric aileron covering
duminium aileron covering
d~
p d~
0
1-
0-
10,
1 '
0'
0"
20,
1 "
0" 0'
0' 0'
30,
2"
.0"
0" 0"
40,
4"
0" 0"
1 " 0"
(93004) .A. 2
The results by fornmla (A,) are as follows : ~..... '
H e i g h t (ft)....
F a b r i c R...... p ( R - - 1 )......
A l u m i n i u m R...... p ( R - - 1 )....
0
8 ' 5 4
10,
3" 0"
11"
20,
4" 0"
15" 0"
6- 30 O- 00472
2 2. 0 0 - 0 1 8 7
40,
9" O. 00489
33" 0"
The values of K given by equation (1) for full-scale, and based on V,,, = 800 ft/sec and 40,000 ft, are 77 and 298 for the fabric and the a l u m i n i u m covering respectively. T h e corresponding values, based on sea level, would be 63 and 283 respectively.
on formula (A,) with d a m p i n g values calculated by Falkner ~ for a rectangular cantilever wing (s = 15 ft, c = 5 ft). The aileron, which e x t e n d e d to the wing tip, was of span 7 It and chord 1.25 ft.
bl = 0" 334, cl = 0, el = 0" 0122, fl -- 0" 211, b2 = 0"00114, c2 = 0, & = 0"000517, f2 = 0"00302. The coefficients here are defined to accord with the notation of R. & M. 1685 and R. & M. 1155, and are appropriate to sea-level only.
and d.., = 0"0001226, but for the d a m p i n g calculations m a d e in t h a t r e p o r t p was increased to 0.00176, and d~ was given the range of values 0"0001226n, where n = 0.2, 1.6. 5, 10, 50. The following table summarizes the results obtained by formula (A~), and also gives a comparison - with d a m p i n g ratios read from the curves in Fig. 7 of R. & M. 1685. It should be noted t h a t symmetrical flutter only (against a specified elastic stiffness) was assumed for the calculations in R. & M. 1685.
p X 10 a (^) d~ × 10 a
0.1226~
. 1 0. 0 × ,, 5 0. 0 × ,,
R ( F o r m u l a A1)
1.1 t
R** (R. & M. 1685 a)
1" 2" 2 " 2 2 " 6 ** E f f e c t i v e for s y m m e t r i c a l f l u t t e r against a specified elastic stiffness. ' S t a n d a r d ' values.
biplane on which violent r u d d e r oscillations occurred a t a flight speed of about 250 ft/sec. The principal dimensions of the tail unit Were : - Total span of tailplane .. 12 ft. 8 in. Total chord of tailplane (including elevators) .. 4 ft 8.95 in. Total height of rudder surface...... 5 It 1.5 in. The rudder lay wholly above the fuselage axis, and was slightly underbalanced aerodynamically b y a horn. -
/I=fl +NA,
where N denotes the gearing ratio.
~ 2 ~ e 2 52 ~--~c 2 - @ N f 2 ,
=
bl = 0.799, 51 = 1.10, gl -- 0.00183, /1 = 0.306, b2 = 0. 00240, 52 = 0. 00596, 82 = 0- 000612, [2 = 0. 002214.
The estimated structural inertial coefficients for sea-level were p = 0. 00210 and d2 = 0.000117, giving the following values for the total barred inertias.
Height (ft)
dz
0" 0"
10,
0"
20,
0"
30,
40,
0-
With the present type of flexural-aileron flutter, formula (B), with the appropriate interchange of symbols, must of course be used, since all the aerodynamic stiffnesses are present. Moreover,
coefficients. The corresponding bounds for the true direct aileron damping coefficient e2 are then given by
with bl, el, b.~ treated as assigned.
The final values of the minimum (tree) aileron damping multipliers R, corresponding to the geared control N = 2.5, and to the normal control N = 0, are given below. The table also
Height (ft)
N = 2.5,
R p (R--l)
. ~!..
N = 0 ,
R p ( R - l ) R!. ,
. °
9
10,
00158 3 ' 2
0'
20,
2- 0" 4-
0" 00214 3"
30,
3" 0 - 5"
40,
0' 00223
5" 0-
The values .of the constant artificial damping, based 270 m.p.h., true), are as fotlows.
K (lb ft/(md/sec))
T y p e of Control
Geared ( N = 2.5).... Normal (N = 0)....
~ = 0
960 1170
20,
1425 1730
40,
1800 2040
aircraft at a speed of about 270 ft/sec. Twill rudders were fitted, symmetrically disposed about the ends of the tailplane, and a small triangular fin was present in front of each rudder. The
Total height 165 in. Overall chord 54.7 in. Distance of main rudder hinge from leading edge 10-0 in. Chord of servo-flap 10.2 in.
Calculations in connection with the binary servo-rudder flutter of this aircraft are given in sections 8 to 1 2 o f R. & M. 15277, in section 17 of Ref. 5 and in section 3 of R. & M. 255P. The relevant numerical data, in the notation of the last two reports, are listed below. In the present case the dynamical coefficients adopted are not non-dimensional. T h e y correspond to the coefficients in Table 1 of the present report, with p, I and Co suppressed. All data given refer to a single rudder only.
Servo e, = 0.008, f , = 0. 0038, Main R u d d e r e~ : 0.09, fa = 0. 088,
j2 = 0. 025, j~ = 0.80,
k~ = 0.0013, k3 = 0.072.
Barred Aerodynamic Coefficients (N = 2.73, p = 0.002378) ~ = 1.17, ], -- 0" 344, ~,~ 0.868, k,~ = 0"0756,
The appropriate transformation formulae are given in section 17 of Ref. 5.
rudder weighed about 55 lb, and the C.G. was 12.1 in. behind the r u d d e r hinge axis. Moreover the servo-flaps were not mass-balanced. In section 17 of Ref. 5 the critical length for a servo mass-balancing arm is given as ~ = 9.26 in. The values of/$ for several representative conditions a~e as follows : - -
Standard Servo-flap statically balanced (~ == 6) Servo-flap dynamically balanced (3. =: 6) Servo-flap dynamically balanced (2 = 10:2)
= 6. 9 1 2 , fi = 7.047, = 6. 5 2 5.
Case (ii) (f~ > O, fl < 0).
* S e e :Equation (129) of R. & M. 11551.
aileron flutter the dynamical coordinates would be the wing twist at the reference section, and the aileron angle at the reference section. The inertias would then be defined as follows. Let m denote the mass at distance y from the wing root and at distance Cod behind the aileron
the ratio of the twist at section y~ to that at the reference section, the total inertial coefficients required are
Fig. 2 (a) shows the normal type of test conic diagram for torsional-aileron flutter. The stiffness point Z lies at (k,, f3), and the points M, N which are common to the test conic T, the frequency line LL, and the upper branch H,, of the divergence hyperbola, are given by,t
where
/~ - e~A (product of direct damping coefficients).
The points M, N are accordingly unreal when # exceeds the critical value (Fig. 2 (b))
The conic T then lies either wholly below H,,, or wholly above (cases of Fig. 2 (c)). In the first case flutter is either prevented absolutely or cannot occur before divergence. In the second case it is possible by further increases o f , first to shrink the test conic to a point (Fig. 2 (d)), and then make it unreal (Fig. 2 (e)). If t* is increased sufficiently, the ellipse again becomes real (Fig. 2 (f)), but is situated below H,. To determine the limiting values of/~ certain further formulae are required.
First, the condition for an imaginary test conic is§
Again, when the conic is real but M, N are unreal, the ellipse will lie below or above H, (Fig. 2 (c))
The co-ordinates of Q are found to be
XQ YQ 1
where
The four points of intersection of the two curves are given by (Fig. 3) "
4 z 4 k J ~ The tangents to f = 0 at
/ ~ = 0 , = ~3Y = ( A + = ~ 2 j
p = 0 (origin O) p = 0 (point S), 4p (k~ -- f3) = j2' -- e~' (point K ) , 4k~.f~ (k~ --f.,) p -- -- /~~' (point J ). K and J are parallel to ~, = 0, and are = (j~ + e~)~/~(tangent AA' at-point K ) , = fl~/4kJ3 (tangent B B ' at point J ). The region of the (~,, p) diagram to the right of AA' Corresponds to A = 4~ -- ( j 2 , ~ e3)~ > 0 and so to elliptic test conics. T h e region t O the right of B B ' corresponds to the cases where M, N are unreal (P- 2 < 0). Fig. 3 is the diagram appropriate to torsional-aileron flutter of the rectangular light aircraft wing (s = 9 It, Co -- 3 It) specified in section 50 of R. & M. 1155L The torsional axis is assumed to be coincident with the flexural axis (14.5 in from leading edge). As in R. & M. 11551 the reference section is chosen at the wing tip (l = s), and the appropriate derivative coefficients (converted from Table 16 of R. & M. 1155 to accord with the definitions in Table 1 of the present report) are e,,. = O" 0046, e A - - 0. 0 0 9 0 , j~ = 0. 0 0 8 7 , j, k,~ = 0"0048, k The value of the natural main damping product These data yield Point S Point K Point J Centre of f = 0 Centre of g = 0 Asymptotes of f - - 0
Asymptotes of g = 0
= 0. 0 4 5 , = 0. 0 5 4 , -- -- 0. 0 8 0. is tt - e,j2 -- 2. 484 × 10 -4.
lO -~ (2.4, 30.4) 10 -4 (1.4, 21.5)
~ - - 0 " 0 2 0 p = 1 " 7 7 × 10 - = 1 - 4 × i 0 - 4 ,, - 0. 0 5 p = 0. 3 4 x 1 0 - 4.
Points on the upper hyperbolic branch V J W of f = 0 indicate reduction of the test conic T fo a point. This degenerate ellipse lies below or above H,, (Figs. 2 (f)) and 2 (d)) according as the lower segment JV, or the upper segment J W , is taken. Hence, the safe region of the (~, p) diagram lies to the right of the composite boundary* B J W.
S u m m a r y. - - L e t / ~ 1 , ~2 denote the two roots of the equation # ~ - - ~ t { e ~ j ~ + 2p (k~ +f~)}/,~ q - p ~ ( k 2 - - f ~ ) ~ + , p f l ( j 2 - k - e 3 ) = 0. Then if ~q, #~ are real (#~ > #1) the multiplier R to be~applied to the product e~j~ is given by R =................. ( K ) If/,,, ~, are unreal R = f12/4e~ysk2/3............... (B,)
No. Author 1 R.A. Frazer and W. J. Duncan.. 2 V.M. Falkner......
3 R.A. Frazer......
4 R.A. Frazer and W. J. Duncan..
5 R.A. Frazer and W. P. Jones ..
6 W.P. Jones.... -.
7 W. J. Duncan and A. R. Collar ..
**- °
R E F E R E N C E S Title, etc. The Flutter of Aeroplane Wings. R. & M. 1155. August, 1928. Effect of Variation of Aileron Inertia and Damping on Flexural- aileron Flutter of a Typical Cantilever Wing. R. & M. 1685. October, 1935. Graphic£1 Treatment of Binary Mass-balancing Problems• R. & ~.~
T A B L E 1 D y n a m i c a l Coefficients and s u p p l e m e n t a r y Symbols (a) Class A F l u t t e r ( T y p i f i e d b y F l e x u r a l - A i l e r o n F l u t t e r ) •
Flexural Moments Aileron hinge-Moments
Non-dimensional Coefficient Significance Non-dimensionalForm^ Coefficient^ Significance^ Form
A l B C 1 P E FI
Inertia
Inertia --L~
p~3Co2a pVl3cobl pV2I~X pt%o3p pVl%o~el pV~l~cofl.
P B Ca D E~ F~
Inertia
0 In ertia
OZ2Co~p pVl%o%~ 0 plCoM pVlcoae o V 2lco~Y
X - 1 J o V 2 P , [be[ - b~e~ -- b2e~ ,
- [ b e ] - - P f l , ql' = ale2 + bfl2 - - p (e~ + b,,) ,
A =- 4b~e~ -- (e~ + b~)~.
(b) Class B F l u t t e r (Typified b y T o r s i o n a l - a i l e r o n F l u t t e r )
Aileron hinge-Moments Wing Torsional Moments Non-dimensional Non-dimensional Coefficient Significance Form Coefficient Significance Form
D 2 Eo F P ]
Inertia
h~ --H~ Inertia --Ho --Ho
pVlco3j pV~lco2k
] K
Inertia --M~ --M~ Inertia --M mo --Mo
pZco~p pVlco~ea p V2lco2f plco~ p Vlco~j pV~lco~Y
o: =- l d l - - ~ (k. + A ) , = + x / ~ ~ - 4 e ~ A k J ~ ,_
M '-....... -/'M~
Fl=xur,z- Ailcr-om FIG:b¢.~{# > O) Nor'n~l Ailm-on O~r~p;m 9 ¢~.
y (a)
Rud~l~r_Torslon F l u f f (/~ < 0.) FluP-J=¢~- P r ¢ ~ n b (W > o )
M M (~)
-!
Fl~×u~- A~l~-o~ FI~Ba~- (~ > o) FluBb*zr PP~v~nP-.~ (W > 0 ) , -
y ~-)
0 N ~ X ~ ' ~
Ruddc.r'- Torsion FIuP.P_~"(fiJ < O)_ FIMP..b.¢~ Prcv~nh.~ (M # beJow O) FIG.L1. Test Conics for_Class A Flutter.
X
FlCxur~ - Ailed-on Flul:bzr (I~ > 0 ) Flug~.r" Pr'~vmmk-~ (W=O), Formul~ AI),
y ~'F,)
~ P Z, ~ P
0 X ~ = M~=N/ :X
L Y
'F~-c.q~®me~_a.
Y P
..
Cu =H, ; Fo~mu~ ~,)
P y
~- J I /
~ 1 ° 12 - ~ I / " l~; -~ I r ~. ~ ~,. I / , / I - 7
Th~ "r,,,o c _ ¢ ~ , , F c o ,. = , ~ (p:p,/,~ f~) ~ , ~ M , N ,.,,-,,'-~l
v ~
T¢~_. Cemi~ I.Jmr'~4~l
y P
L
FIG. 2. Test Conics for Class B Flutter.
I
50
-SO
/^ I / IJ
!
I
M, N, u n r ~ l
/ / /
l /,
I I I ~ i o n eo r;ghk oF A A' I.... Je~/; o F B B ' I ,, ~ r;ghk oFBB' ,, below J V I ,, ~ v ~ J w S h ~ : l c d r~ion
M, tN u n r ~ l. 7 below H u i
T~lh'p~icM , ~^ rtz~,l.Ca>o)I M, i"t unr~z~l T I:xzlow H u T ~bovc H u T umr-~l
7"3 a Foint:.
5¢e Fiq. 2.
. o zio 3~o 4 o s-or FIG. 3. (^) I l l u s t r a t i v e (/z, p) D i a g r a m (see S e c t i o n 5).
(93004) Wt. 13/806 K. 5 ll/51 Hw. PR]NT~D IN GREA~ BRIrA[~