
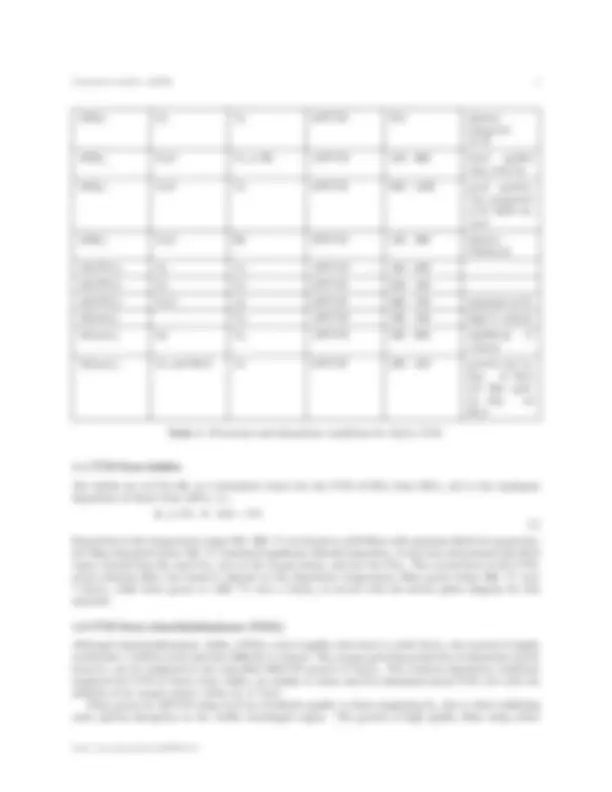
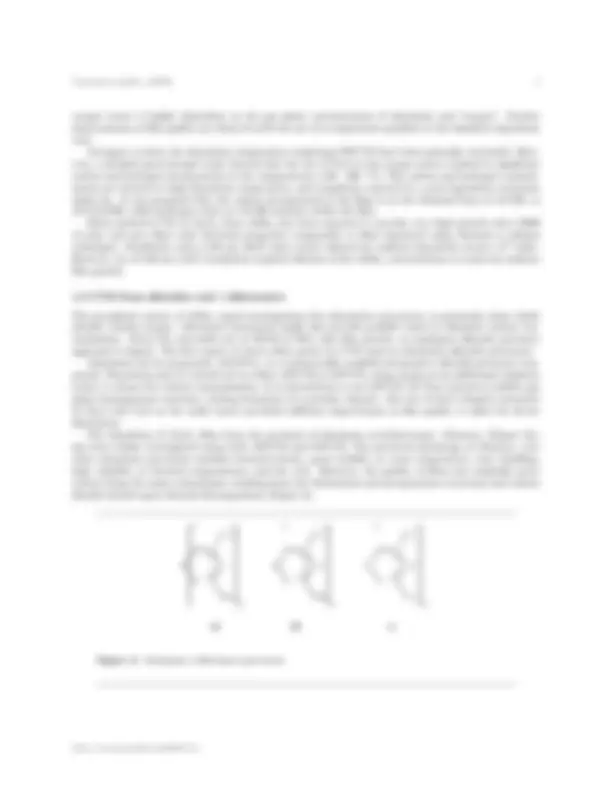
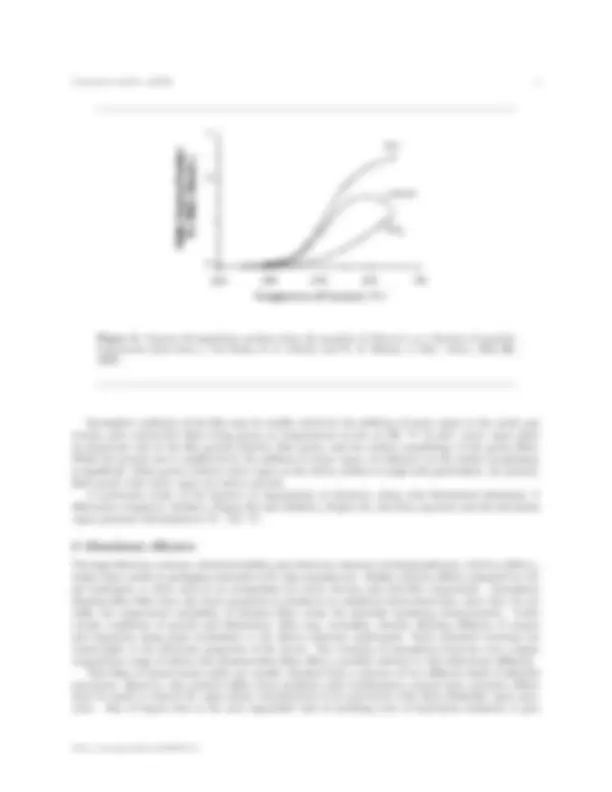
Study with the several resources on Docsity
Earn points by helping other students or get them with a premium plan
Prepare for your exams
Study with the several resources on Docsity
Earn points to download
Earn points by helping other students or get them with a premium plan
Community
Ask the community for help and clear up your study doubts
Discover the best universities in your country according to Docsity users
Free resources
Download our free guides on studying techniques, anxiety management strategies, and thesis advice from Docsity tutors
An in-depth analysis of the chemical vapor deposition (cvd) process for the growth of alumina (al2o3) thin films. Various precursors such as alcl3, alme3, al(acac)3, and their corresponding deposition conditions, growth mechanisms, and challenges. The document also discusses the role of oxygen sources, temperature gradients, and gas phase concentrations in improving film quality. Additionally, the document touches upon the use of water vapor, carbon contamination, and the comparison of different deposition techniques such as apcvd, lpcvd, and pecvd.
Typology: Study notes
1 / 7
This page cannot be seen from the preview
Don't miss anything!
This work is produced by The Connexions Project and licensed under the Creative Commons Attribution License †
Alumina, Al 2 O 3 , exists as multiple crystalline forms, however, the two most important are the α and γ forms. α-Al 2 O 3 (corundum) is stable at high temperatures and its structure consists of a hexagonal close-packed array of oxide (O2-) ions with the Al3+^ ions occupying octahedral interstices. In contrast, γ-Al 2 O 3 has a defect spinel structure, readily takes up water and dissolves in acid. Despite the potential disadvantages of γ-Al 2 O 3 there is a preference for its deposition on silicon substrates because of the two dierent lattice- matching relationships of γ-Al 2 O 3 (100) on Si(100). These are shown as schematic diagrams in Figure 1. A summary of CVD precursor systems for Al 2 O 3 is given in Table 1.
∗Version 1.5: Jan 25, 2010 4:45 pm US/Central †http://creativecommons.org/licenses/by/3.0/
Figure 1: Schematic diagram of the crystallographic relations of γ-Al 2 O 3 on Si(100): (a) γ-Al 2 O 3 (100)||Si(100), and (b) γ-Al 2 O 3 (100)||Si(110). Adapted from A. R. Barron, CVD of Non-Metals, W. S. Rees, Jr., Ed. VCH, New York (1996).
Aluminum precursor
Oxygen source
Carrier gas CVD method
Deposition temp. ( ◦C)
Comments
AlCl 3 CO 2 /H 2 H 2 or N 2 APCVD 700 - 900 amorphous (700), crys- talline (850 -
AlMe 3 O 2 N 2 or He APCVD 350 - 380 dep. rate highly de- pendent on gas-phase conc. Al and O 2 continued on next page
oxygen source is highly dependent on the gas phase concentrations of aluminum and oxygen. Further improvements in lm quality are observed with the use of a temperature gradient in the chambers deposition zone. Attempts to lower the deposition temperature employing PECVD have been generally successful. How- ever, a detailed spectroscopic study showed that the use of N 2 O as the oxygen source resulted in signicant carbon and hydrogen incorporation at low temperatures (120 - 300 ◦C). The carbon and hydrogen contami- nation are lowered at high deposition temperature, and completely removed by a post-deposition treatment under O 2. It was proposed that the carbon incorporated in the lms is in the chemical form of Al-CH 3 or Al-C(O)OH, while hydrogen exists as Al-OH moieties within the lm. Photo-assisted CVD of Al 2 O 3 from AlMe 3 has been reported to provide very high growth rates ( Å/min) and give lms with electrical properties comparable to lms deposited using thermal or plasma techniques. Irradiation with a 248 nm (KrF) laser source allowed for uniform deposition across a 3" wafer. However, use of 193 nm (ArF) irradiation required dilution of the AlMe 3 concentration to avoid non-uniform lm growth.
1.3 CVD from alkoxides and β-diketonates
The pyrophoric nature of AlMe 3 urged investigations into alternative precursors, in particular those which already contain oxygen. Alternative precursors might also provide possible routes to eliminate carbon con- tamination. Given the successful use of TEOS in SiO 2 thin lm growth, an analogous alkoxide precursor approach is logical. The rst report of Al 2 O 3 lms grown by CVD used an aluminum alkoxide precursors. Aluminum tris-iso-propoxide, Al(OiPr) 3 , is a commercially available inexpensive alkoxide precursor com- pound. Deposition may be carried-out by either APCVD or LPCVD, using oxygen as an additional oxidation source to ensure low carbon contamination. It is adventitious to use LPCVD (10 Torr) growth to inhibit gas phase homogeneous reactions, causing formation of a powdery deposit. The use of lower chamber pressures (3 Torr) and N 2 O as the oxide source provided sucient improvement in lm quality to allow for device fabrication. The deposition of Al 2 O 3 lms from the pyrolysis of aluminum acetylacetonate, Al(acac) 3 (Figure 2a), has been widely investigated using both APCVD and LPCVD. The perceived advantage of Al(acac) 3 over other aluminum precursors includes lowered-toxicity, good stability at room temperature, easy handling, high volatility at elevated temperatures, and low cost. However, the quality of lms was originally poor; carbon being the main contaminant resulting from the thermolysis and incorporation of acetone and carbon dioxide formed upon thermal decomposition (Figure 3).
Figure 2: Aluminum β-diketonate precursors.
Figure 3: Gaseous decomposition products from the pyrolysis of Al(acac) 3 as a function of pyrolysis temperature (Data from J. Von Hoene, R. G. Charles, and W. M. Hickam, J. Phys. Chem., 1958, 62 , 1098).
Incomplete oxidation of the lm may be readily solved by the addition of water vapor to the carrier gas stream; pure carbon-free lms being grown at temperatures as low as 230 ◦C. In fact, water vapor plays an important role in the lm growth kinetics, lm purity, and the surface morphology of the grown lms. While the growth rate is unaected by the addition of water vapor, its inuence on the surface morphology is signicant. Films grown without water vapor on the Al 2 O 3 surface is rough with particulates. In contrast, lms grown with water vapor are mirror smooth. A systematic study of the kinetics of vaporization of Al(acac) 3 along with uorinated aluminum β- diketonate complexes, Al(tfac) 3 (Figure 2b) and Al(hfac) 3 (Figure 2c), has been reported, and the saturation vapor pressures determined at 75 - 175 ◦C.
The high dielectric constant, chemical stability and refractory character of aluminosilicates, (Al 2 O 3 )x(SiO 2 )y, makes them useful as packaging materials in IC chip manufacture. Mullite (3Al 2 O 3 .2SiO 2 ) prepared by sol- gel techniques, is often used as an encapsulant for active devices and thin-lm components. Amorphous alumina-silica lms have also been proposed as insulators in multilevel interconnections, since they do not suer the temperature instability of alumina lms retain the desirable insulating characteristics. Under certain conditions of growth and fabrication, silica may crystallize, thereby allowing diusion of oxygen and impurities along grain boundaries to the silicon substrate underneath. Such unwanted reactions are catastrophic to the electronic properties of the device. The retention of amorphous structure over a larger temperature range of silicon rich alumina-silica lms oers a possible solution to this deleterious diusion. Thin lms of mixed metal oxides are usually obtained from a mixture of two dierent kinds of alkoxide precursors. However, this method suers from problems with stoichiometry control since extensive eorts must be made to control the vapor phase concentration of two precursors with often dissimilar vapor pres- sures. Also of import here is the near impossible task of matching rates of hydrolysis/oxidation to give