
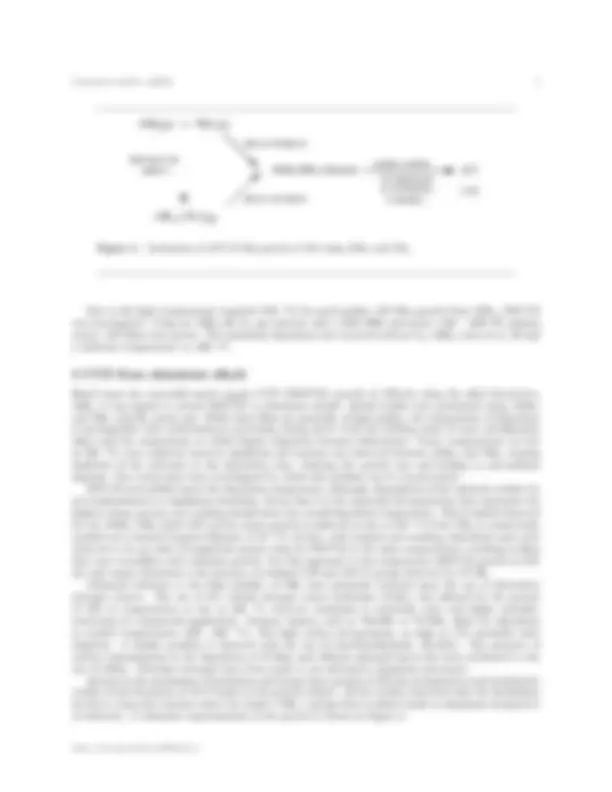
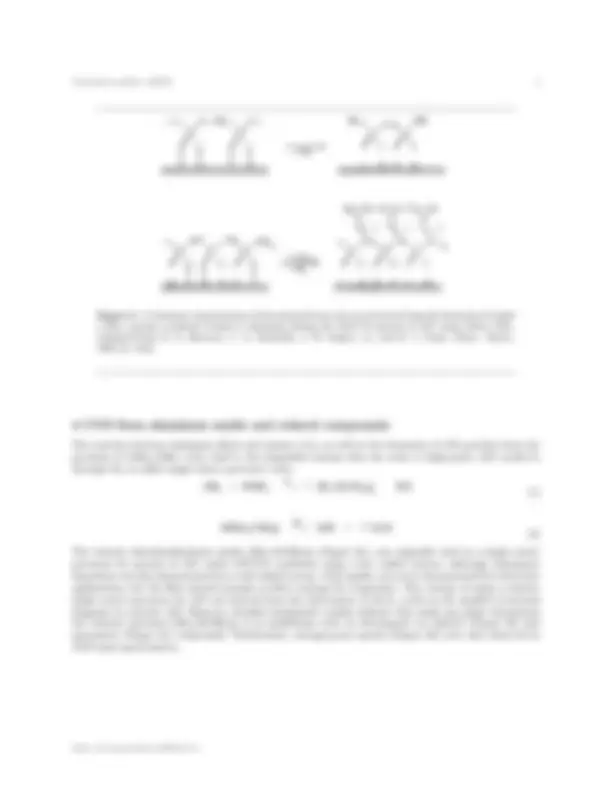
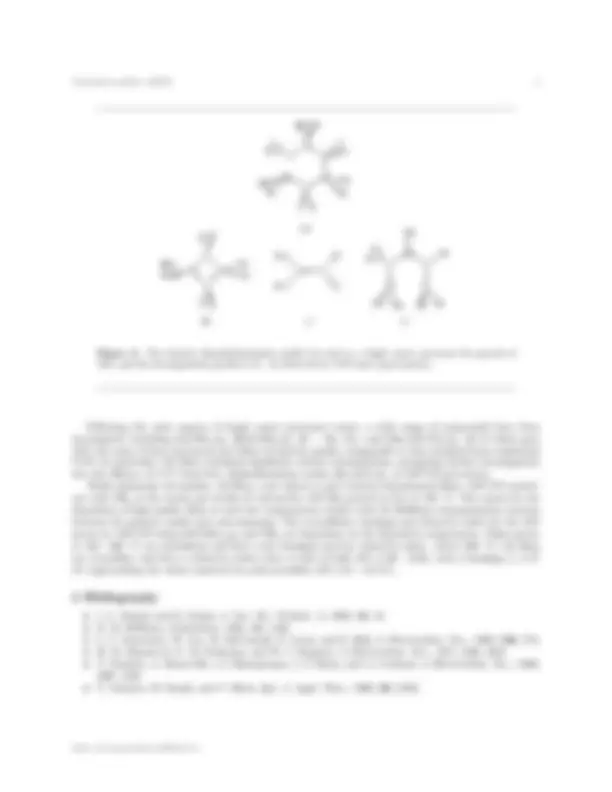
Study with the several resources on Docsity
Earn points by helping other students or get them with a premium plan
Prepare for your exams
Study with the several resources on Docsity
Earn points to download
Earn points by helping other students or get them with a premium plan
Community
Ask the community for help and clear up your study doubts
Discover the best universities in your country according to Docsity users
Free resources
Download our free guides on studying techniques, anxiety management strategies, and thesis advice from Docsity tutors
Study Material. Interest in the mechanism of nucleation and atomic layer growth of AlN has prompted several mechanistic studies of the formation of Al-N bonds on the growth surface. Chemical Vapor Deposition of Aluminum Nitride, Connexions Web site. http://cnx.org/content/m26132/1.1/, Jun 27, 2009. Chemical, Vapor, Deposition, Aluminum, Nit ride, Microelectronic, Optical, Band gap, AIN, Material, Complex, Packages, Dielectric, Coefficient.
Typology: Study notes
1 / 5
This page cannot be seen from the preview
Don't miss anything!
This work is produced by The Connexions Project and licensed under the Creative Commons Attribution License †
Aluminum nitride (AlN) has potential for signicant applications in microelectronic and optical devices. It has a large direct bandgap (Eg,dir = 6.28 eV), extremely high melting point (3000 ◦C), high thermal conductivity (2.6 W/cm.K), and a large dielectric constant (ε = 9.14). In present commercial microelectronic devices, AlN is used most often as a packaging material, allowing for the construction of complex packages with many signal, ground, power, bonding, and sealing layers. Aluminum nitride is especially useful for high power applications due to its enhanced thermal conductivity. Chemical vapor deposition (CVD) grown thin lms of AlN have been centered upon its use as a high gate-insulation layer for MIS devices, and a dielectric in high-performance capacitors. One additional property of AlN that makes it a promising insulating material for both Si and GaAs devices is that its thermal expansion coecient is almost identical to both of these semiconductors. The lack of a suitably volatile homoleptic hydride for aluminum (AlH 3 is an involatile polymeric species) led to the application of aluminum halides and organometallic compounds as precursors. A summary of selected precursor combinations is given in Table 1.
Aluminum precursor
Nitrogen source
Carrier gas CVD method
Deposition temp. ( ◦C)
Comments
AlCl 3 (NH 3 ) - N 2 LPCVD 700 - 1400 NH 4 Cl present AlBr 3 NH 3 N 2 APCVD 400 - 900 Br present AlBr 3 N 2 N 2 LPCVD 520 - 560 oriented growth AlMe 3 NH 3 H 2 LPCVD 1200 AlMe 3 NH 3 He APCVD 350 - 400 continued on next page
∗Version 1.1: Jun 27, 2009 7:32 am GMT- †http://creativecommons.org/licenses/by/3.0/
AlMe 3 pre-cracked NH 3
H 2 /He APCVD 310 - 460 N-H and AlN- N bonds de- tected AlMe 3 tBuNH 2 or iPrNH 2
H 2 APCVD 400 - 600 high C content, low N AlMe 3 Me 3 SiN 3 H 2 APCVD 300 - 450 very high C content [R 2 Al(NH 2 )] 3 (R = Me, Et)
H 2 LPCVD 400 - 800 poor lm qual- ity, high C con- tent [R 2 AlN 3 ] 3 (R = Me, Et)
Table 1: Precursors and deposition conditions for AlN CVD.
The observation that AlN powder may be produced upon the thermal decomposition of the AlCl 3 (NH 3 ) complex, prompted initial studies on the use of AlCl 3 /NH 3 for the CVD of AlN lms. Initially, the low volatility of AlCl 3 (a polymeric chain structure) required that the AlCl 3 (NH 3 ) complex to be used as a single precursor. Low pressure CVD (LPCVD) at 5 -10 Torr resulted in deposition of AlN lms, although lms deposited below 1000 ◦C were contaminated with NH 4 Cl, and all the lms contained chlorine. Films with reasonable electrical properties were prepared by the use of the more volatile tris-ammonia complex, AlCl 3 (NH 3 ) 3. The dielectric constant for lms grown at 800 - 1000 ◦C (11.5) is higher than bulk AlN (9.14) and also than that of the lms grown at 1100 ◦C (8.1). All the lms were polycrystalline with the grain size increasing with increasing deposition temperatures and preferred orientation was observed only for the lms grown below 1000 ◦C. Aluminum bromide is a dimeric volatile compound, [Br 2 Al(μ-Br)] 2 , and is more attractive as a CVD source, than AlCl 3. Deposition of AlN lms can be accomplished using AlBr 3 and NH 3 in an APCVD system with H 2 as the carrier gas. The mechanism of lm growth has been proposed (Figure 1).
Figure 2: A schematic representation of the proposed step-wise reaction involving the formation of amide (-NH 2 -) groups covalently bound to aluminum during the MOCVD growth of AlN using AlMe 3 /NH 3. (Adapted from M. E. Bartram, T. A. Michalske, J. W. Rogers, Jr., and R. T. Paine, Chem. Mater., 1993, 5 , 1424).
The reaction between aluminum alkyls and amines ((1)), as well as the formation of AlN powders from the pyrolysis of AlMe 3 (NH 3 ) ((2)), lead to the misguided concept that the route to high-purity AlN would be through the so-called single source precursor route.
(1)
The trimeric dimethylaluminum amide, [Me 2 Al(NH 2 )] 3 (Figure 3a), was originally used as a single source precursor for growth of AlN under LPCVD conditions using a hot walled reactor, although subsequent deposition was also demonstrated in a cold walled system. Film quality was never demonstrated for electronic applications, but the lms showed promise as ber coatings for composites. The concept of using a trimeric single source precursor for AlN was derived from the observation of Al 3 N 3 cycles as the smallest structural fragment in wurtzite AlN. However, detailed mechanistic studies indicate that under gas phase thermolysis the trimeric precursor [Me 2 Al(NH 2 )] 3 is in equilibrium with (or decomposes to) dimeric (Figure 3b) and monomeric (Figure 3c) compounds. Furthermore, nitrogen-poor species (Figure 3d) were also observed by TOF-mass spectrometry.
Figure 3: The trimeric dimethylaluminum amide (a) used as a single source precursor for growth of AlN, and the decomposition products (b - d) observed by TOF-mass spectrometry.
Following the early reports of single source precursor routes, a wide range of compounds have been investigated, including [Al(NR 2 ) 3 ] 2 , [HAl(NR 2 ) 2 ] 2 (R = Me, Et), and [Me 2 AlN(iPr) 2 ] 2 , all of which gave AlN, but none of these precursors give lms of superior quality comparable to that obtained from traditional CVD. In particular, the lms contained signicant carbon contamination, prompting further investigations into the ecacy of, N-C bond free, dialkylaluminum azides, [R 2 Al(N 3 )] 3 , as LPCVD precursors. While aluminum tris-amides, Al(NR 2 ) 3 were shown to give carbon-contaminated lms, APCVD carried- out with NH 3 as the carrier gas results in carbon-free AlN lm growth as low as 100 ◦C. The reason for the deposition of high quality lms at such low temperatures resides with the Homan transamination reaction between the primary amido unit and ammonia. The crystallinity, bandgap and refractive index for the AlN grown by APCVD using [Al(NMe 2 ) 3 ] 2 and NH 3 are dependent on the deposition temperature. Films grown at 100 - 200 ◦C are amorphous and have a low bandgap and low refractive index. Above 300 ◦C, the lms are crystalline, and have a refractive index close to that of bulk AlN (1.99 - 2.02), with a bandgap (≤ 5. eV) approaching the values reported for polycrystalline AlN (5.8 - 5.9 eV).