
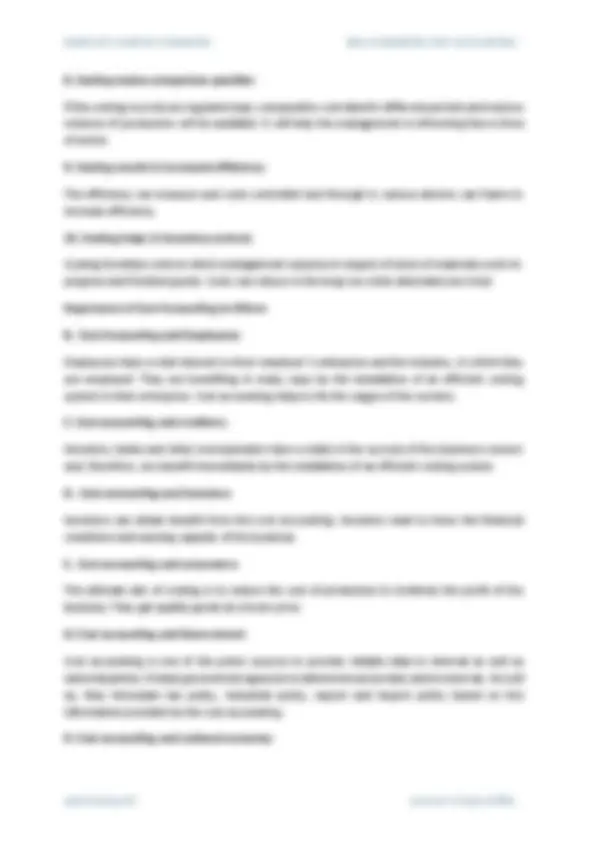
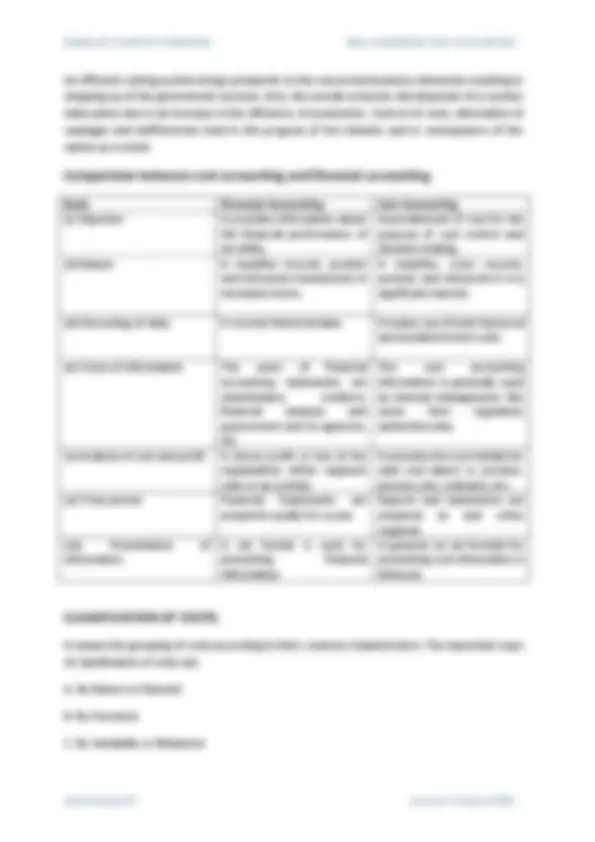
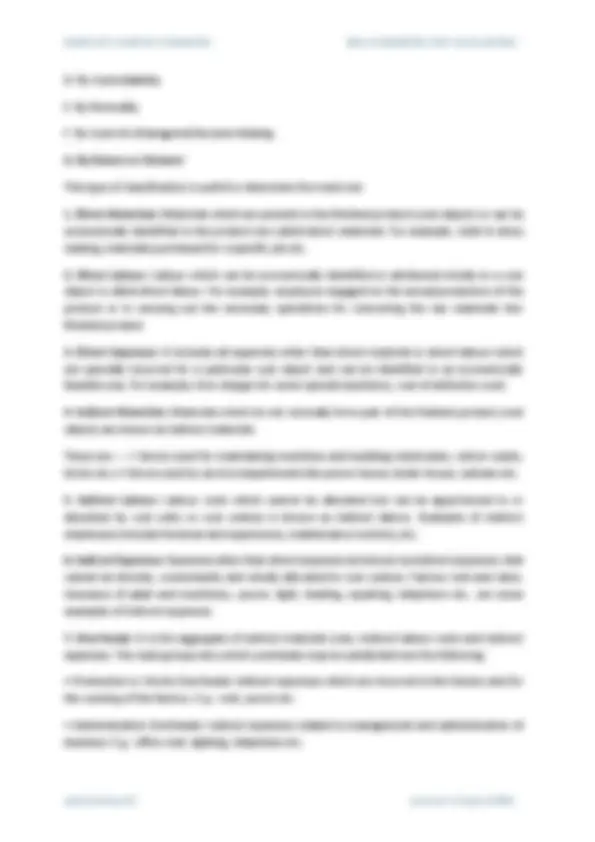
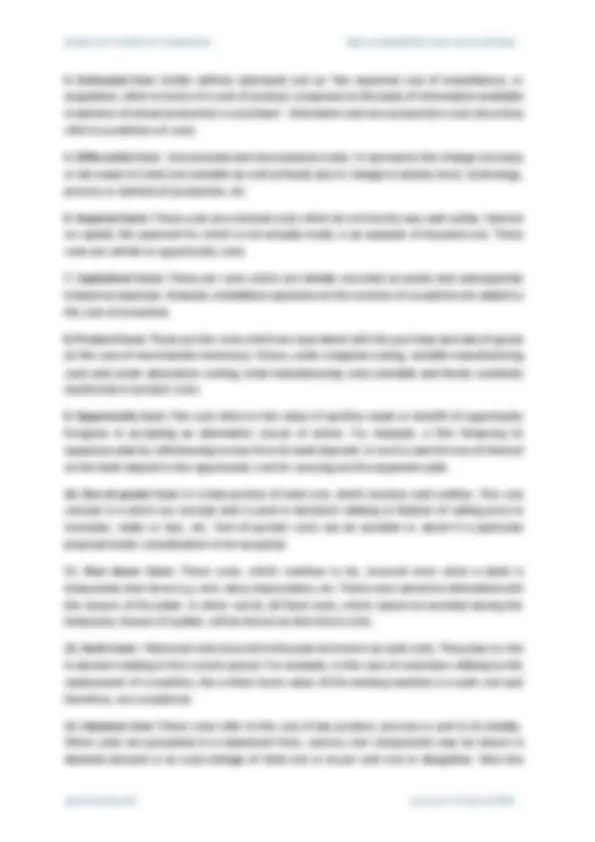
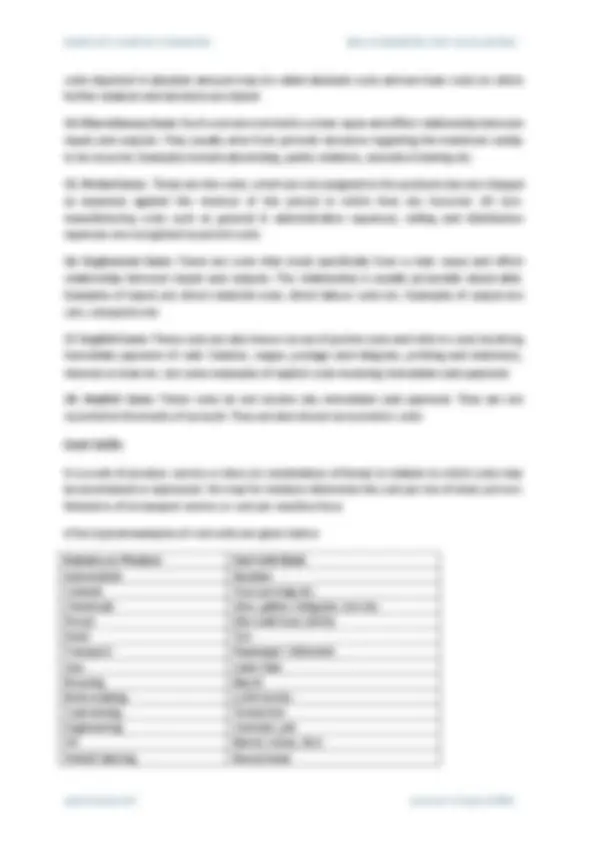
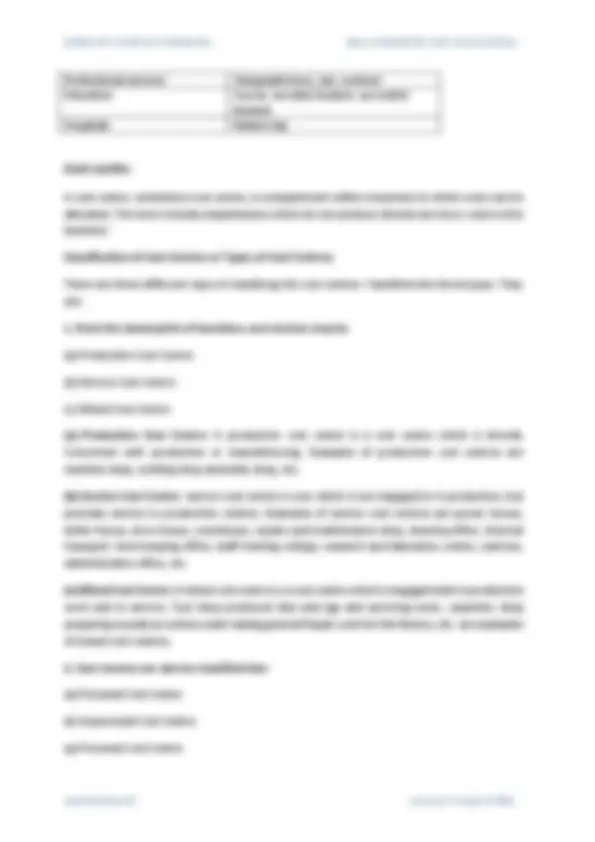
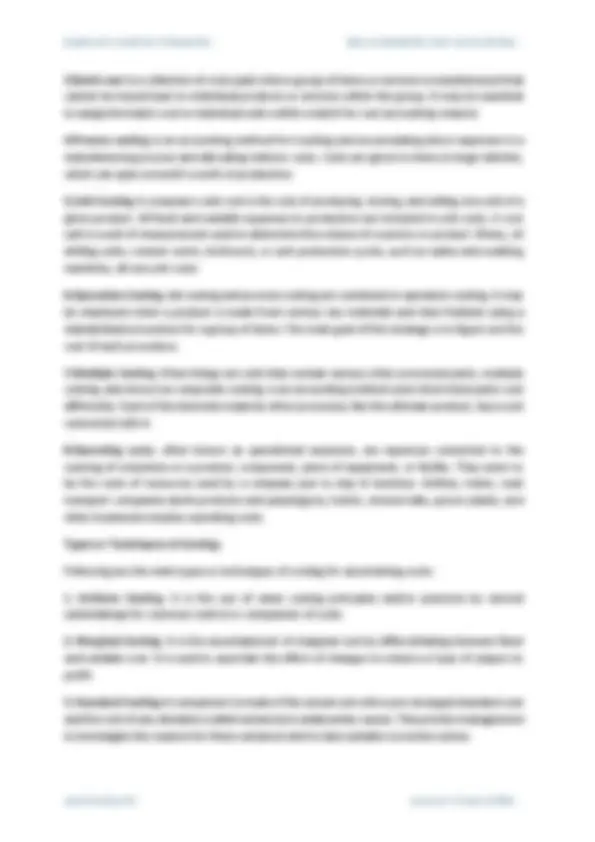
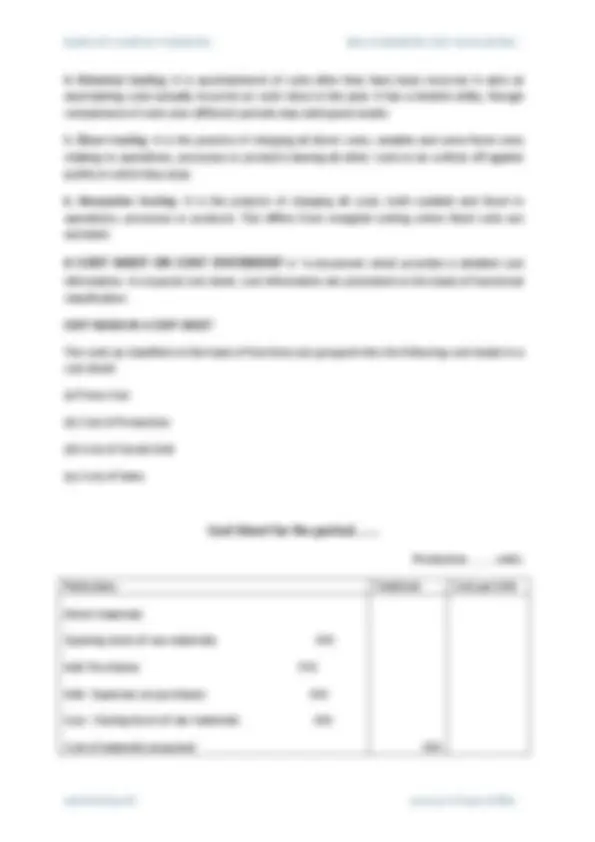
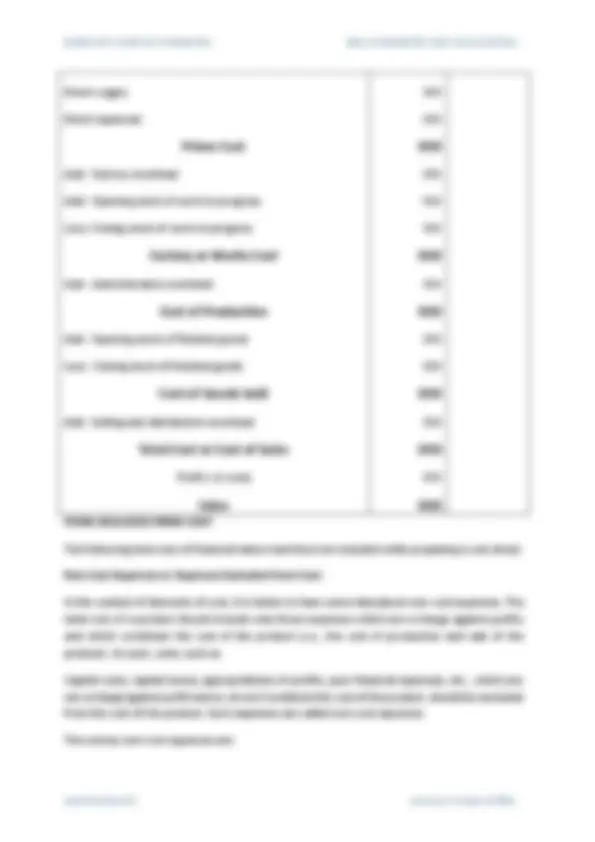
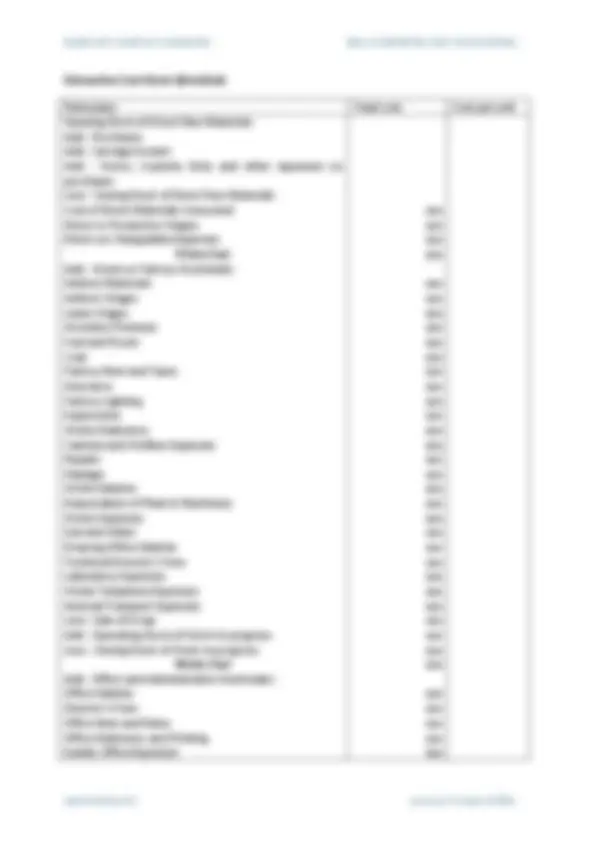
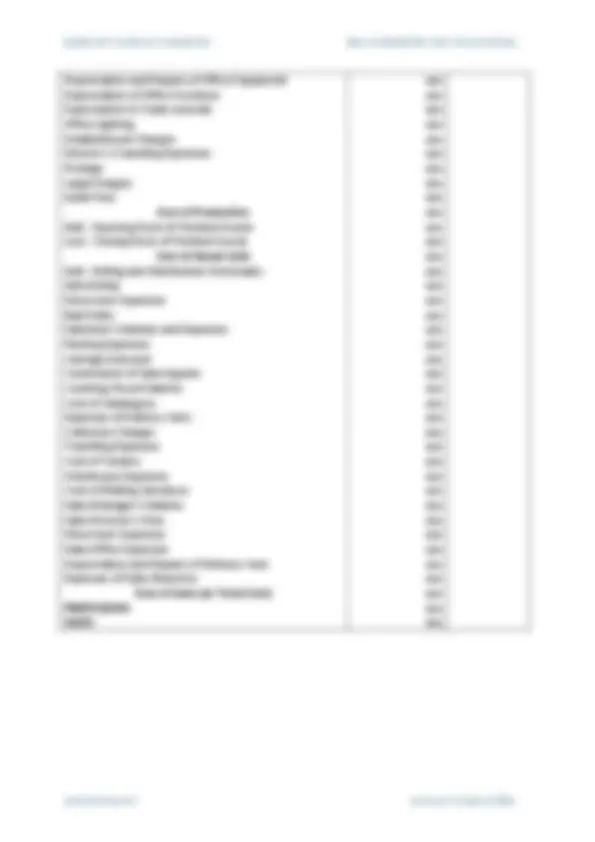
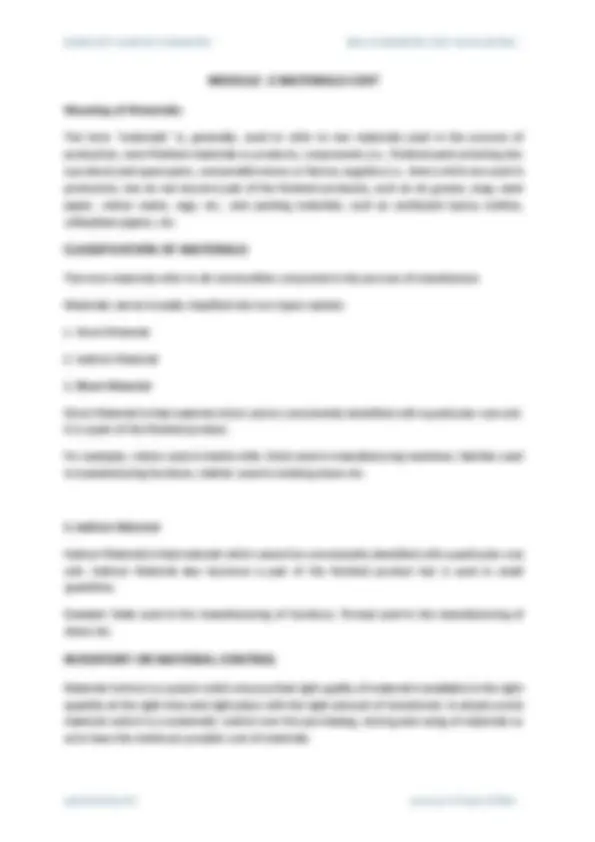
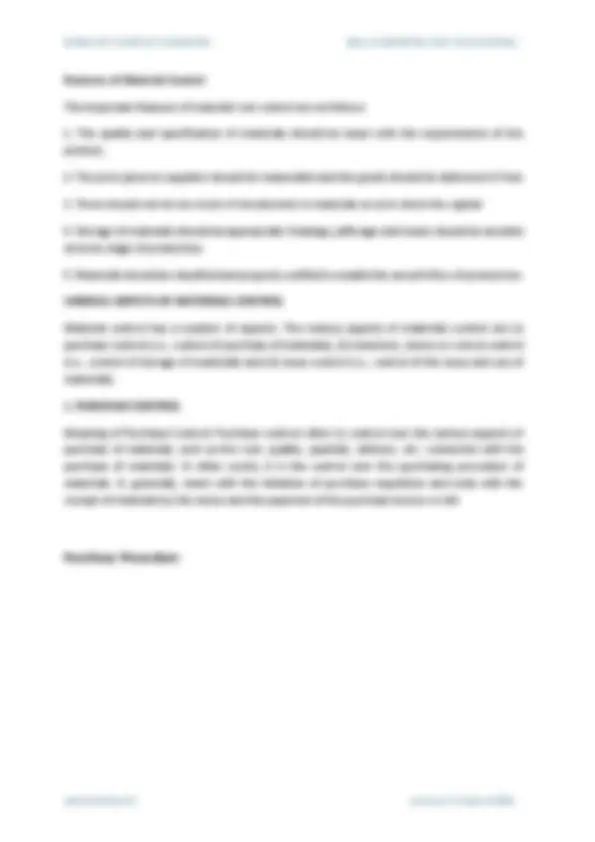
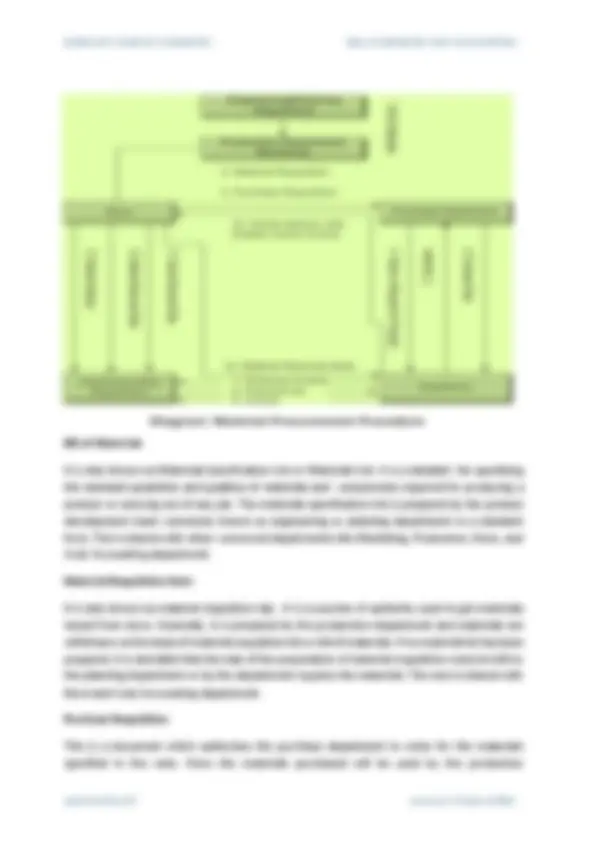
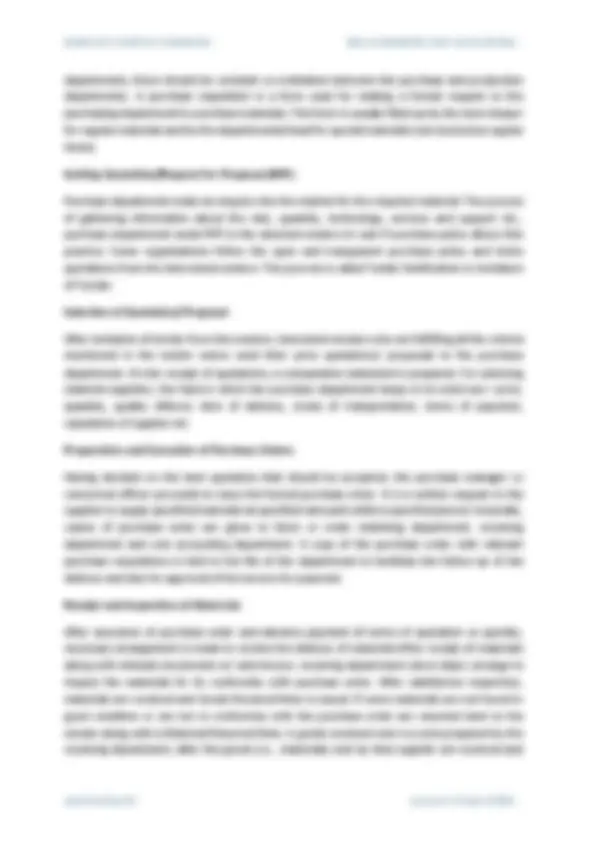

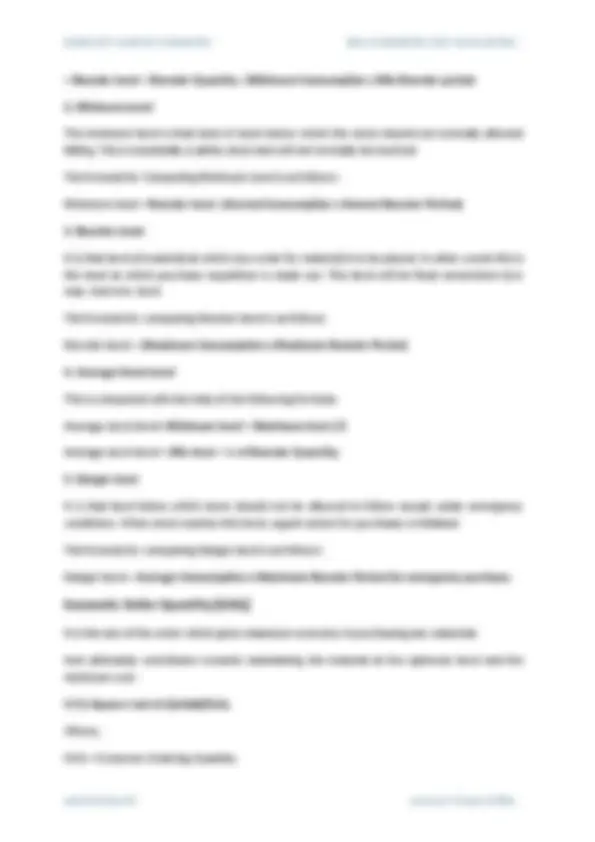
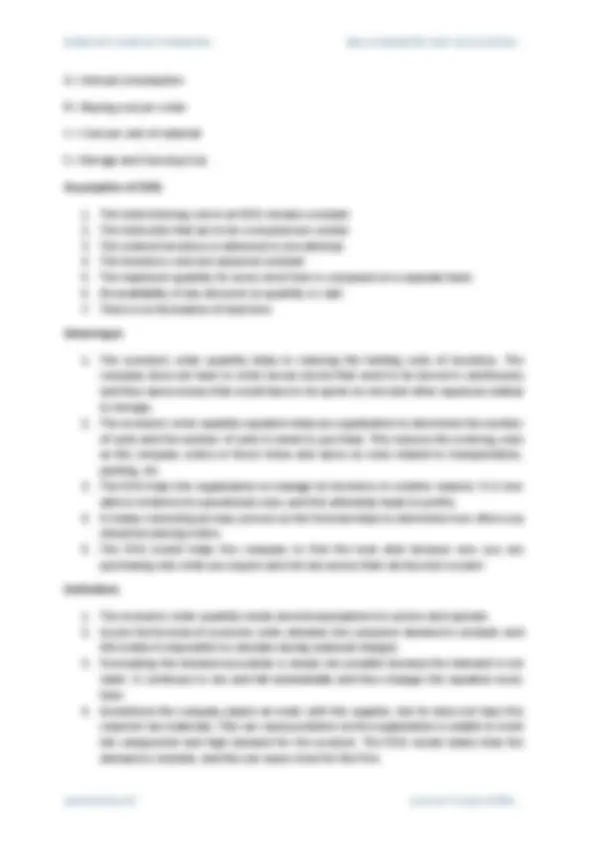
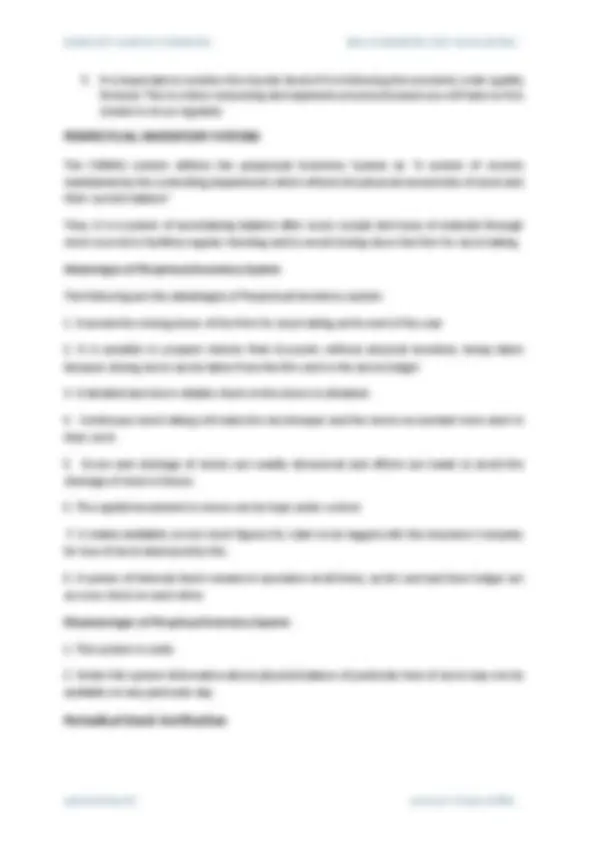
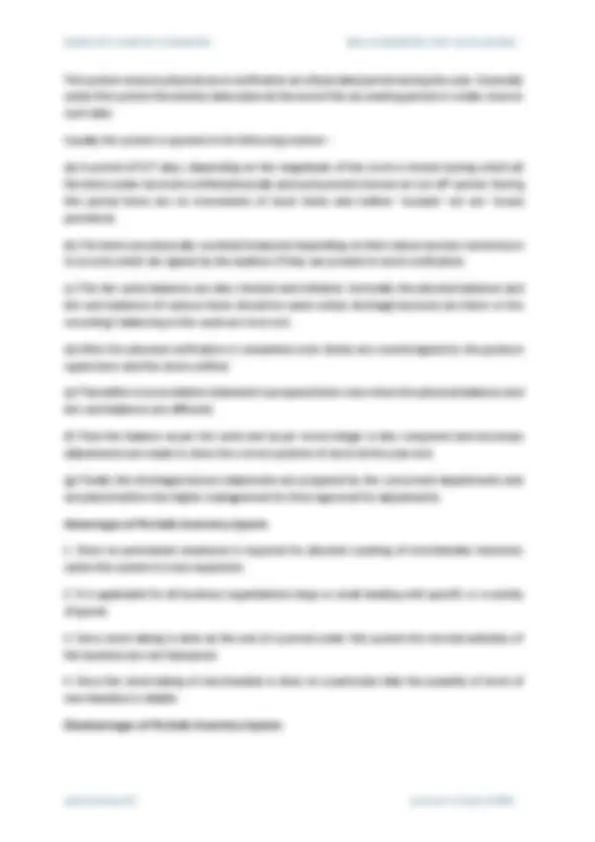
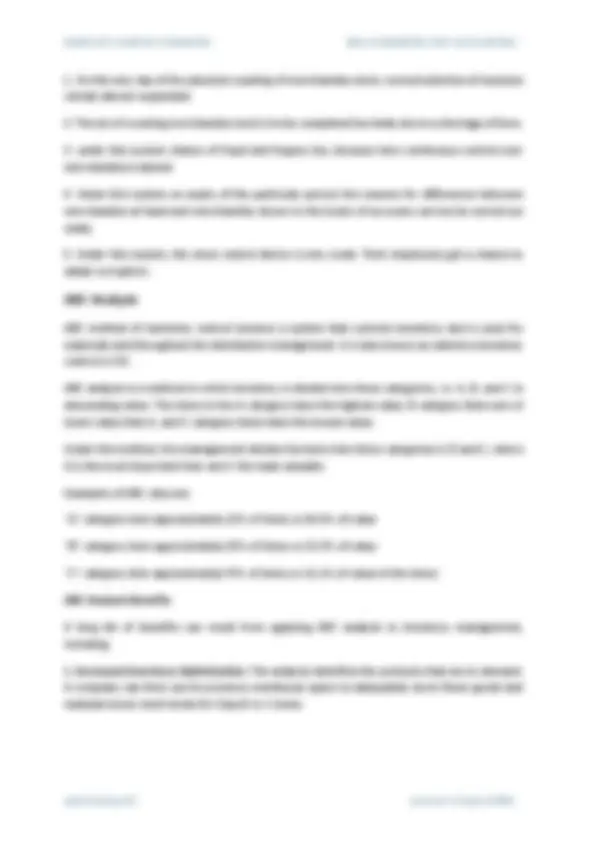
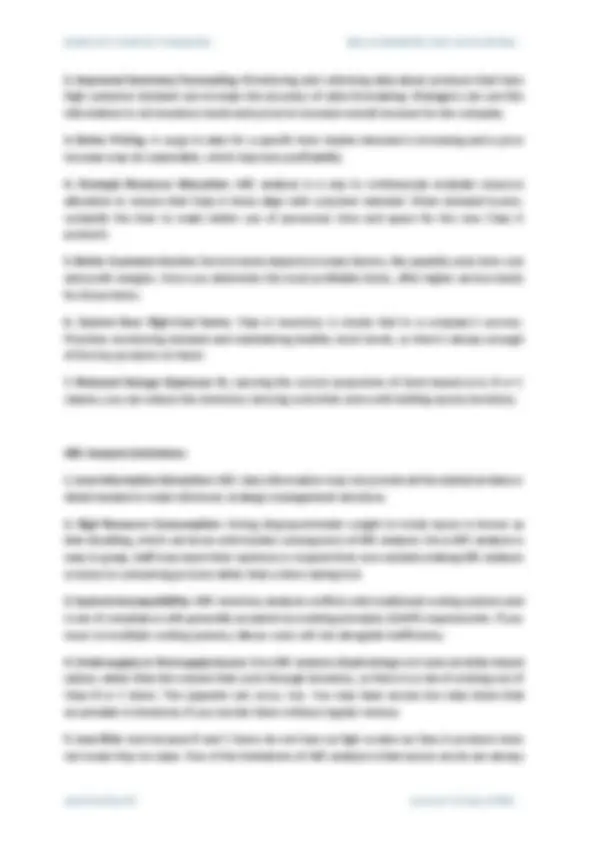
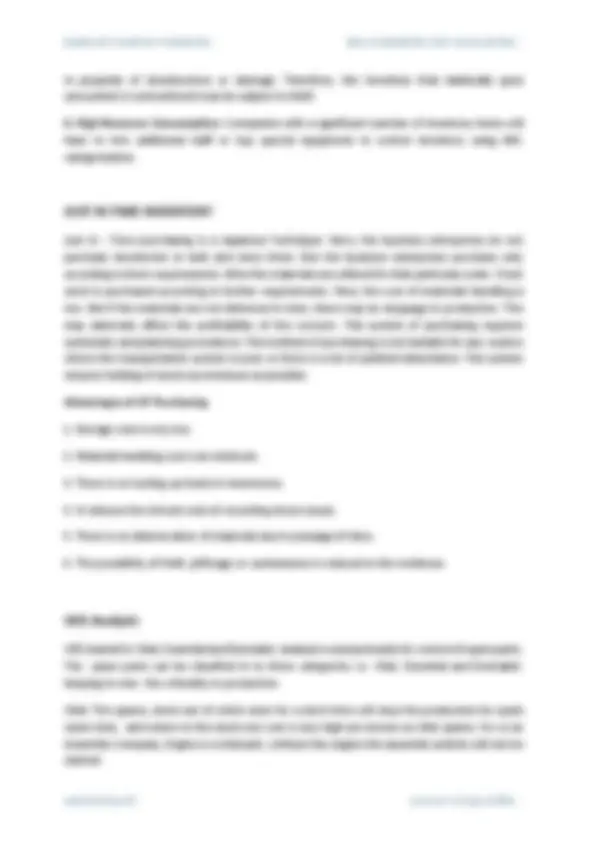
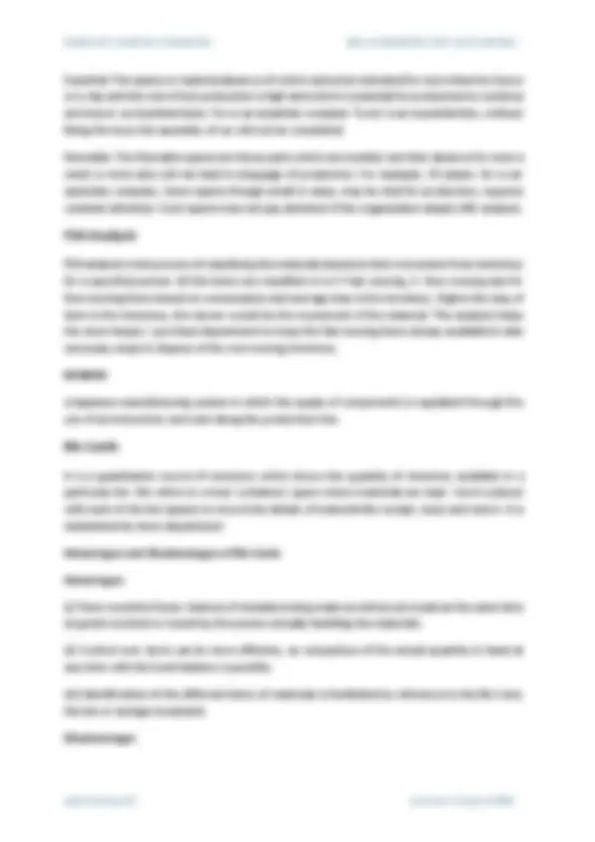
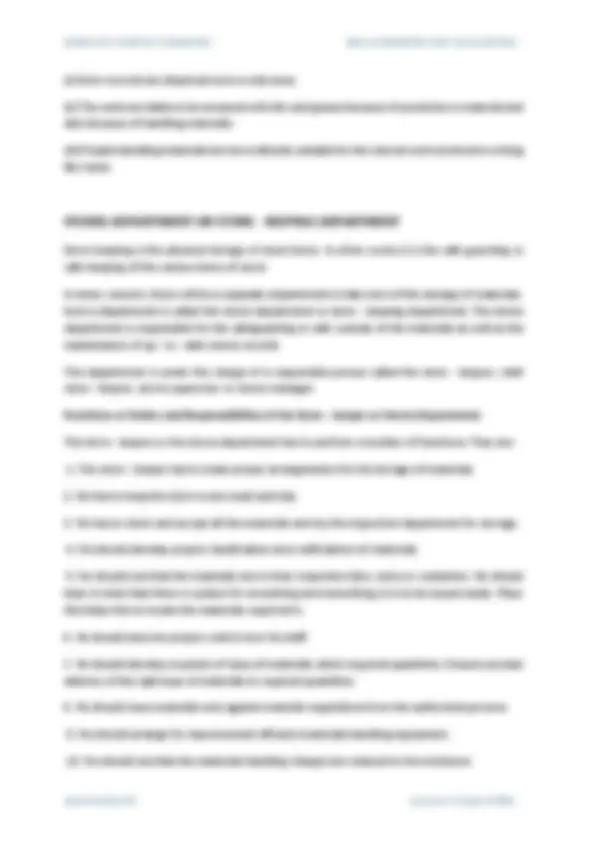
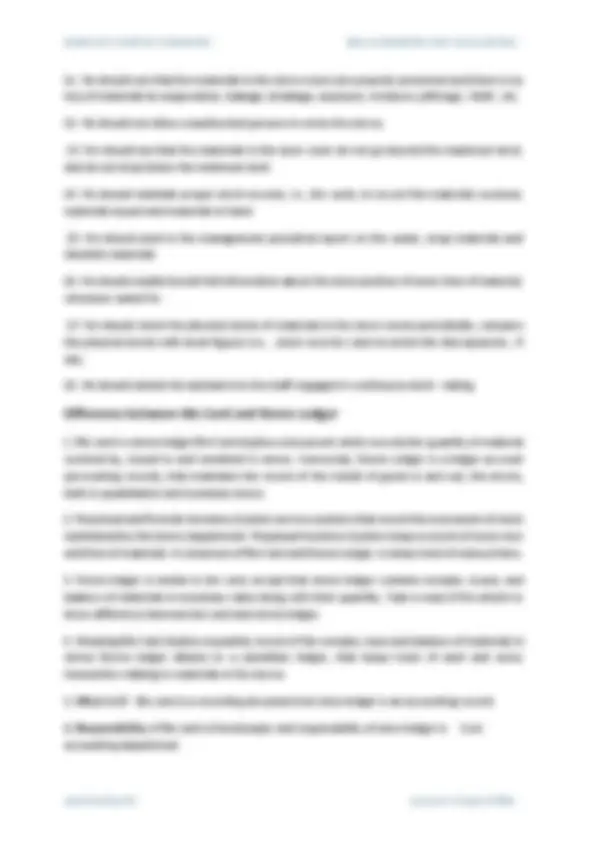
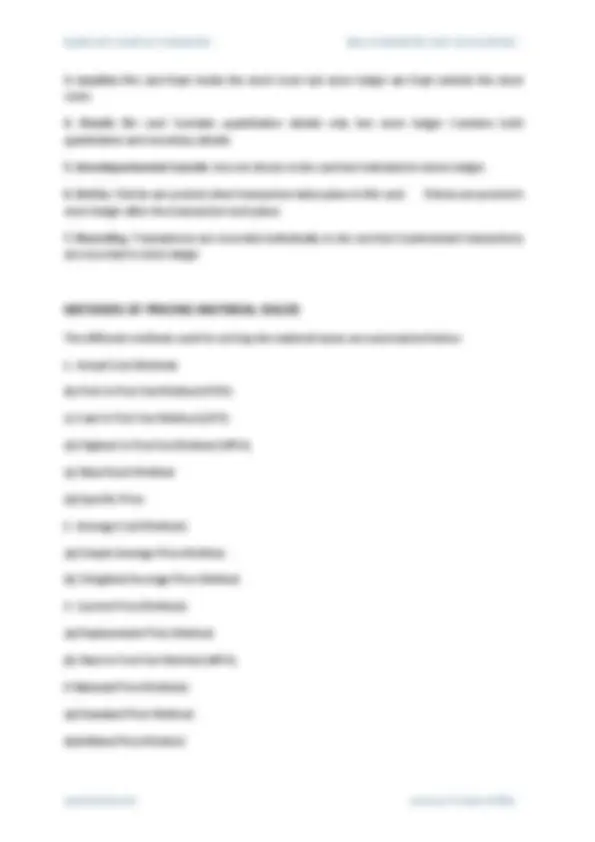
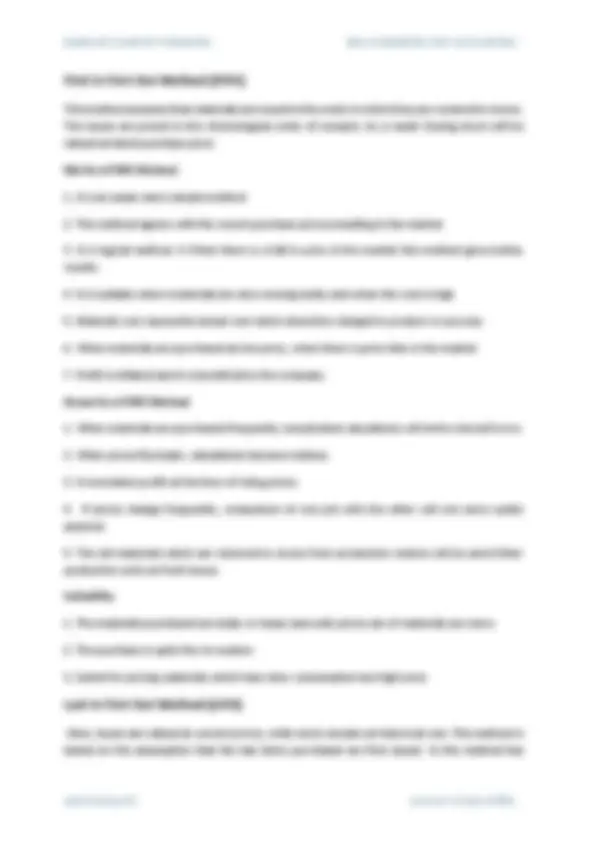
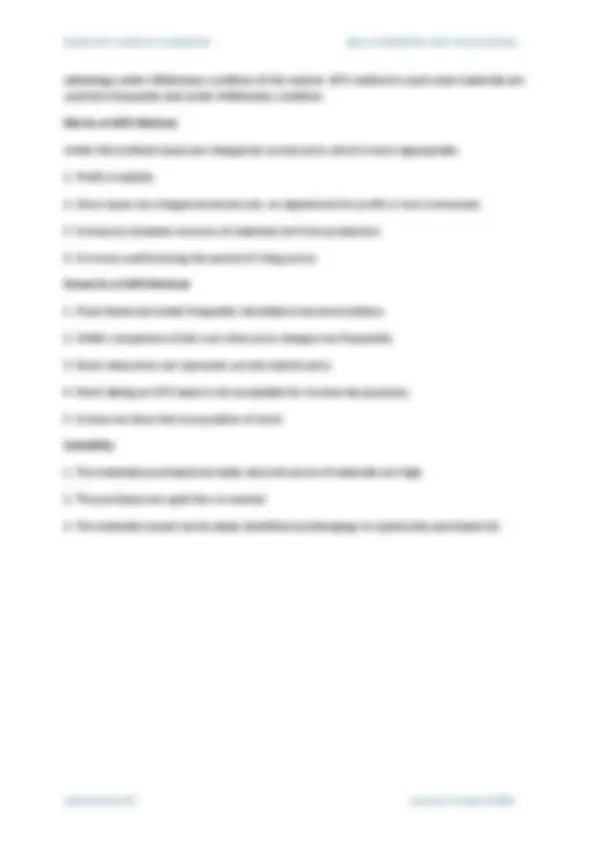
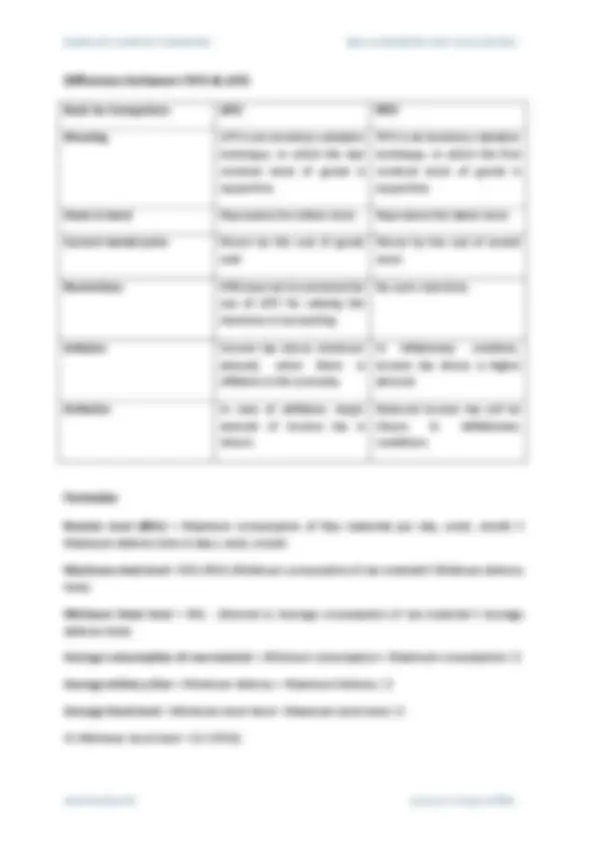
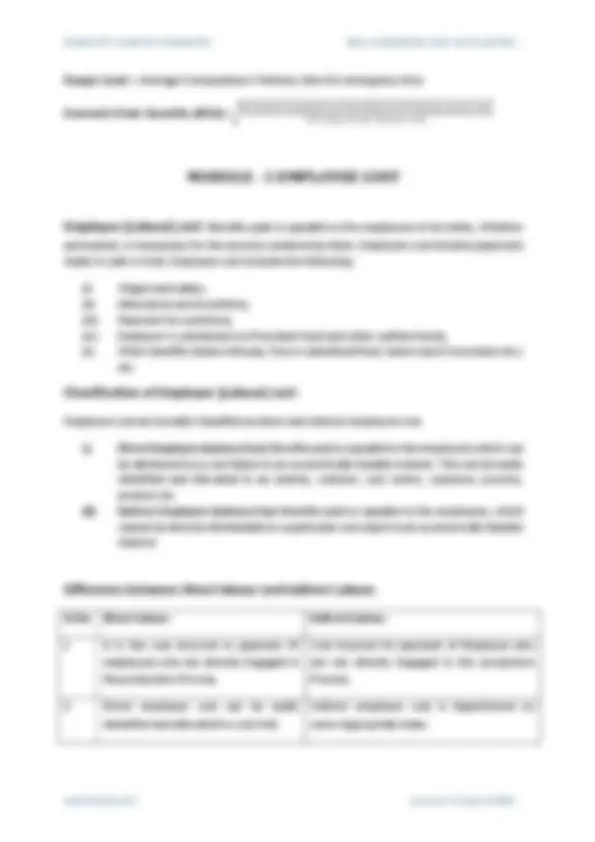
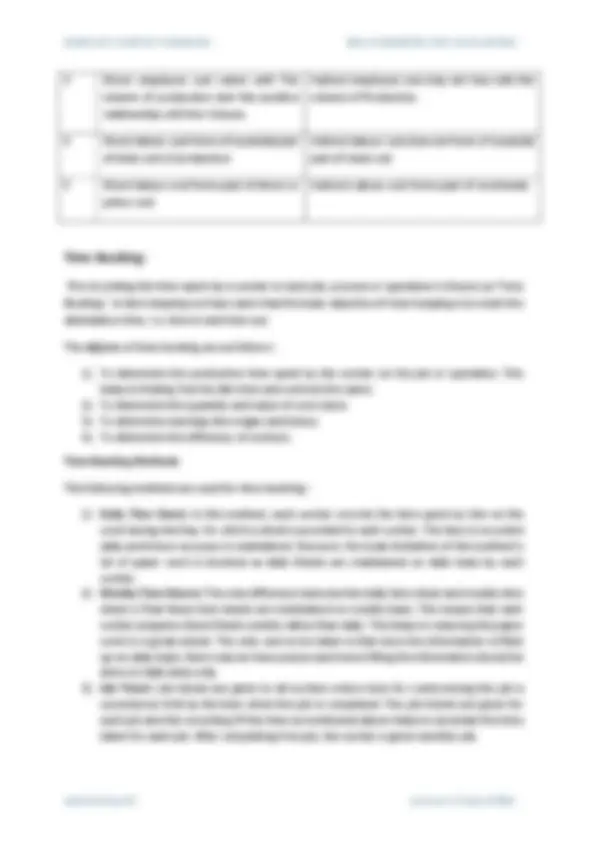
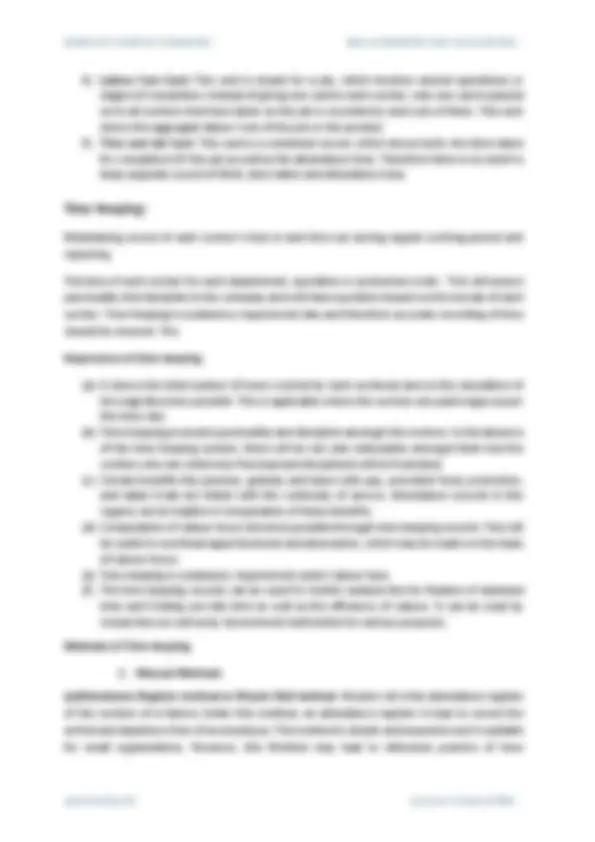
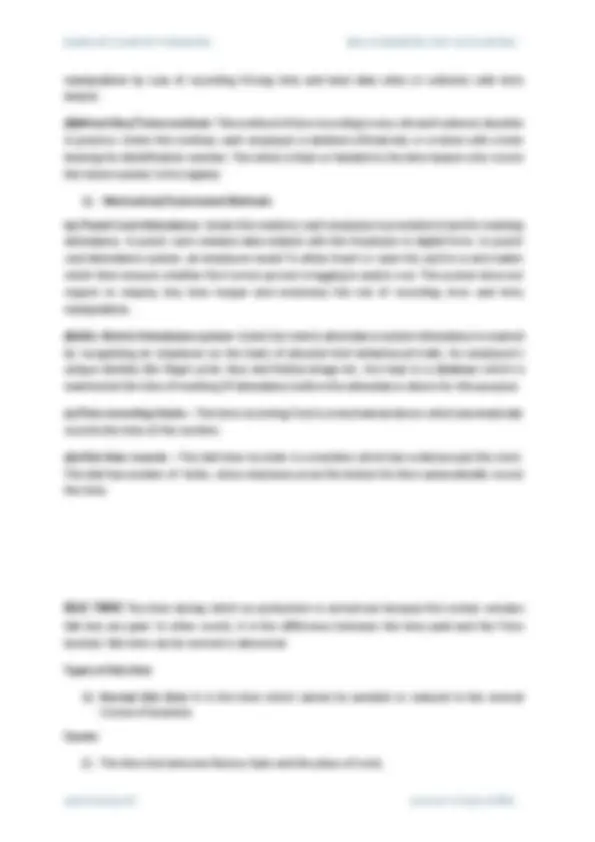
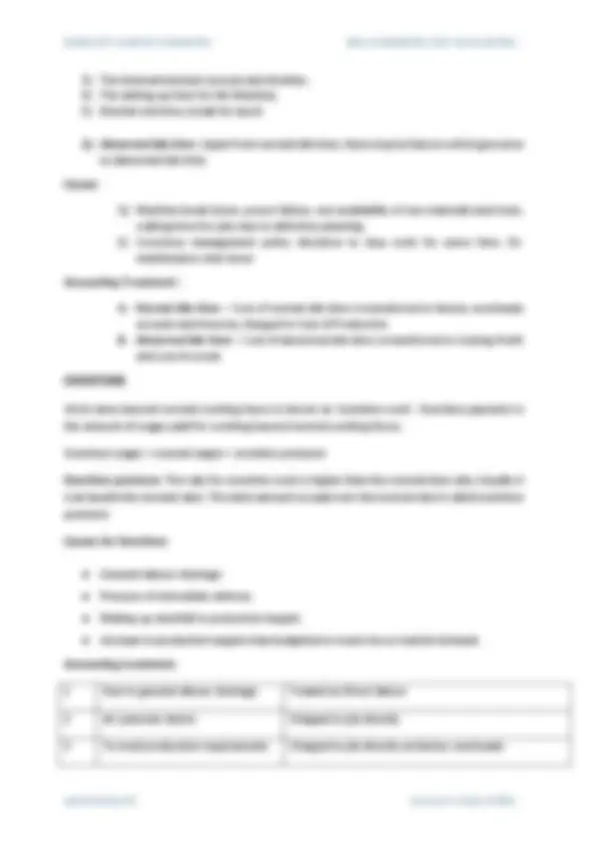
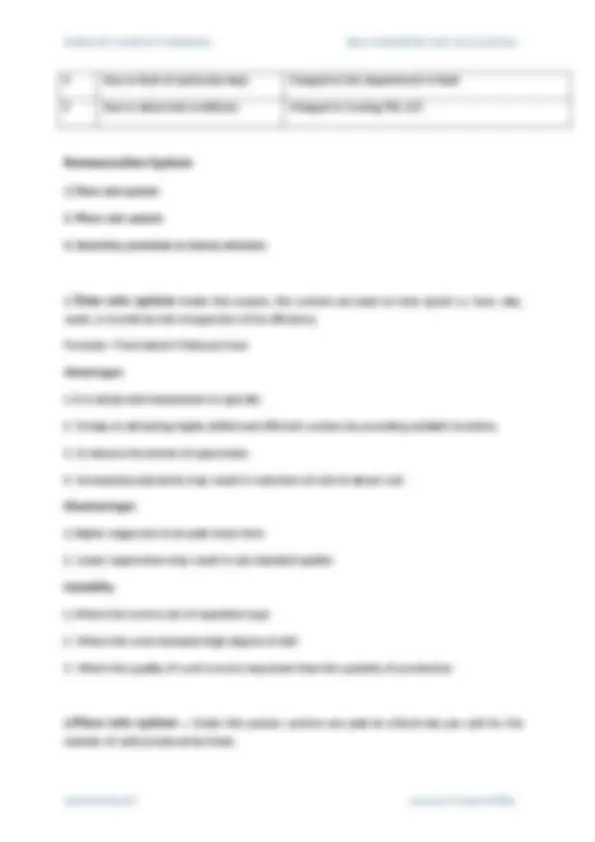
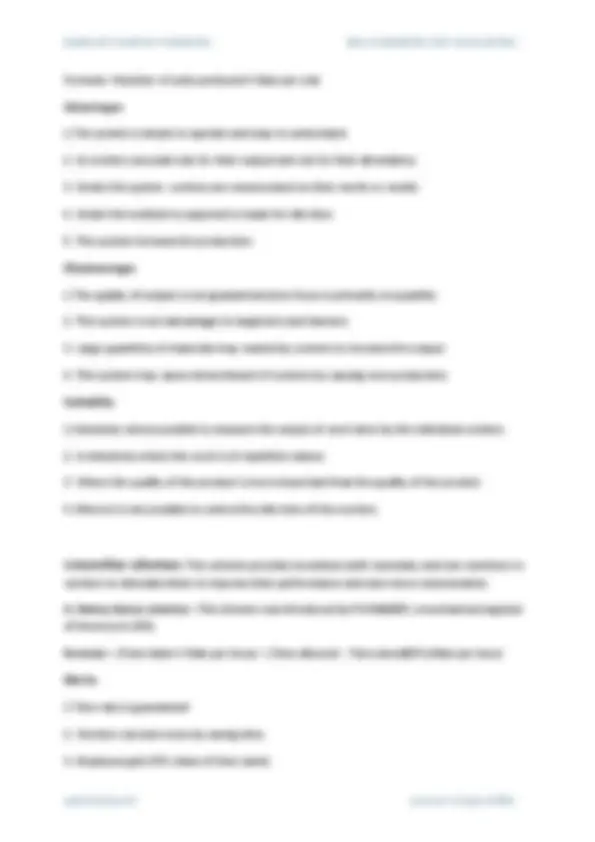
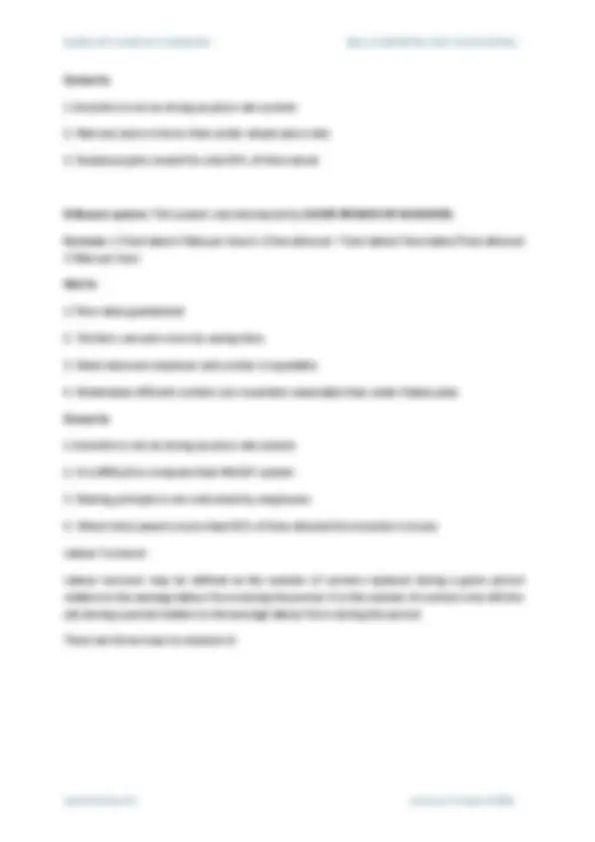
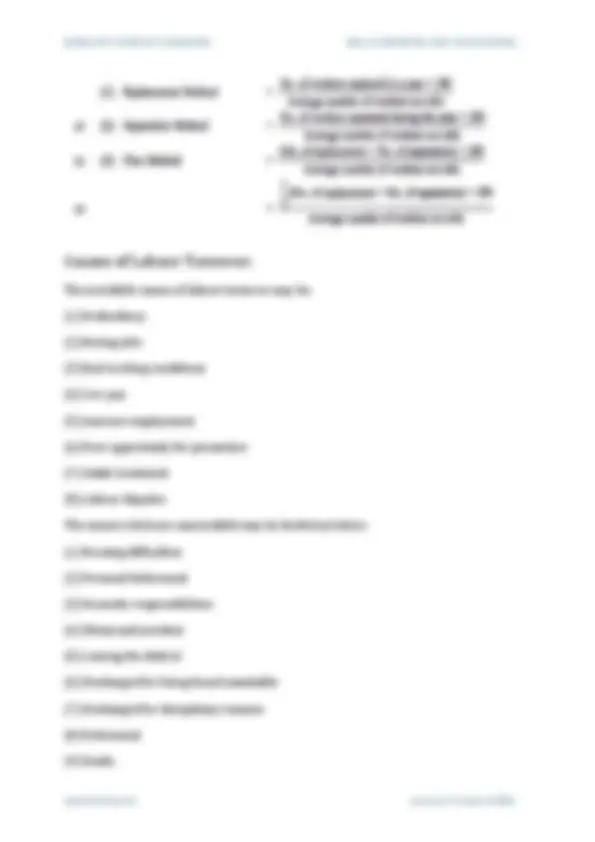
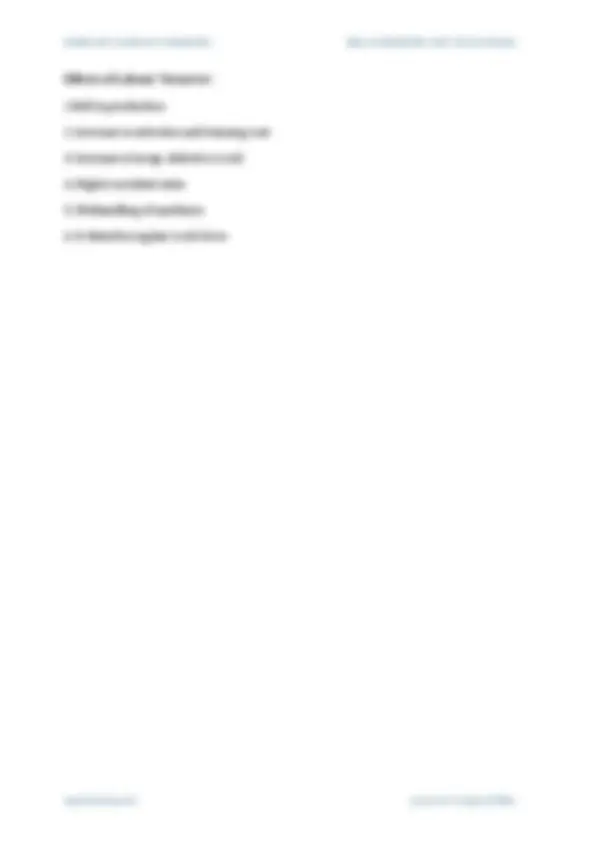

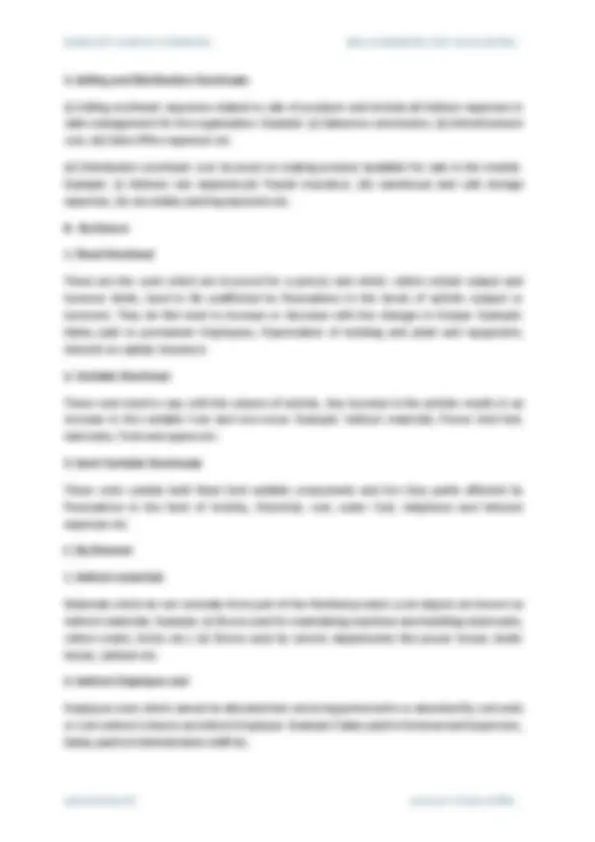
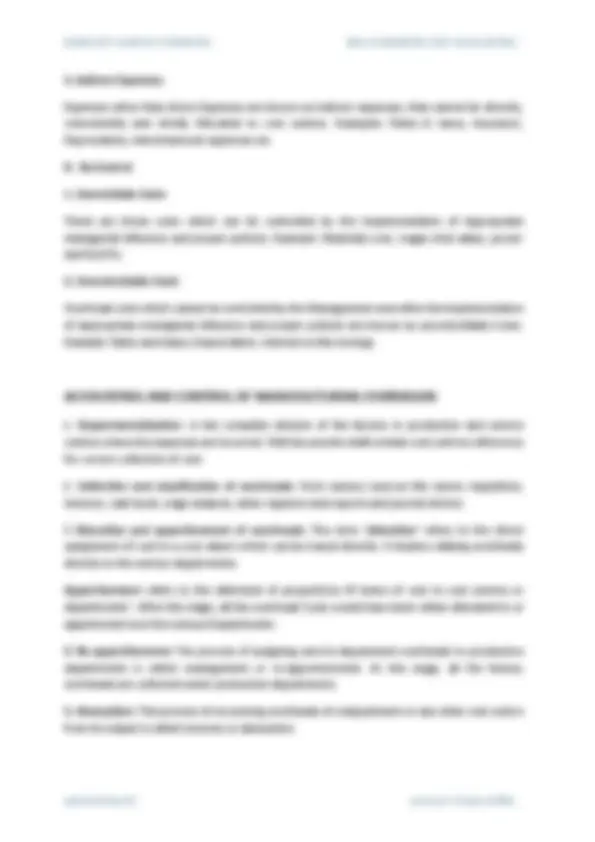
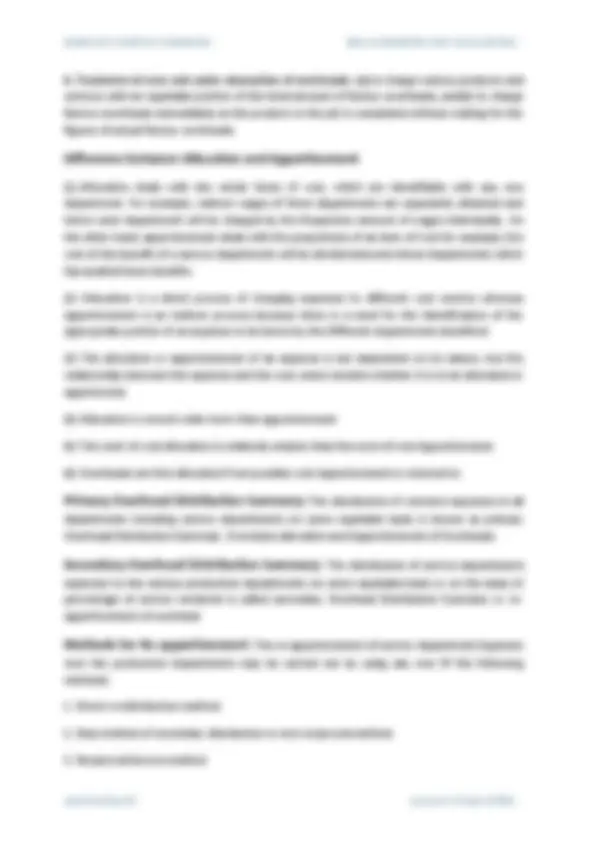
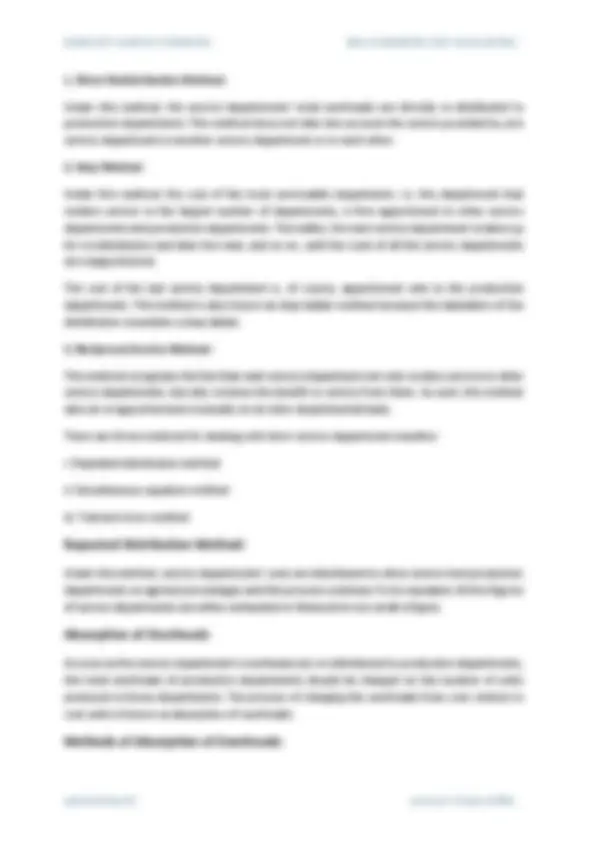
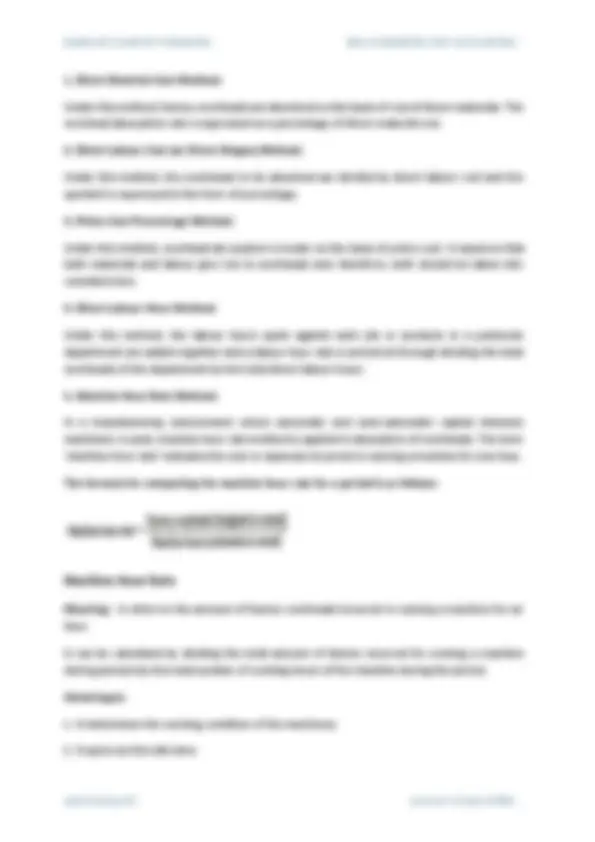
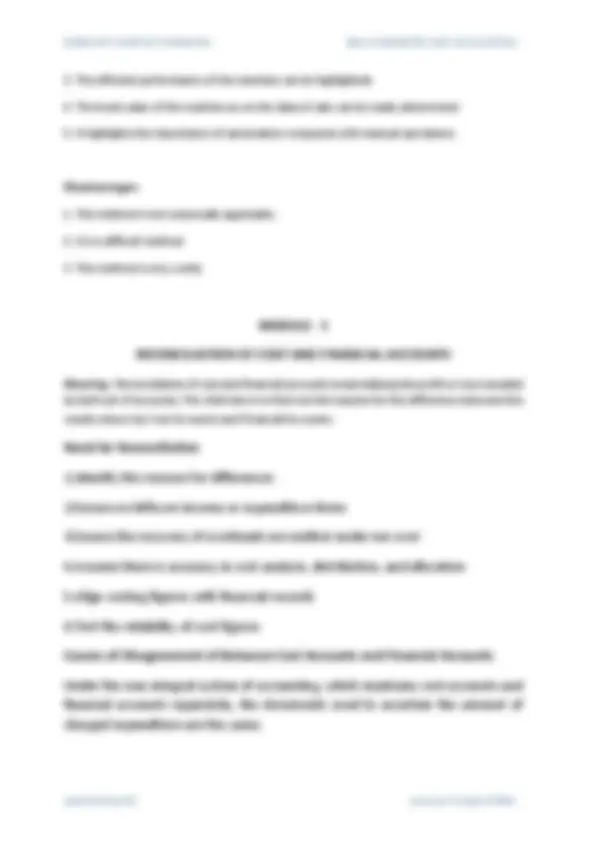

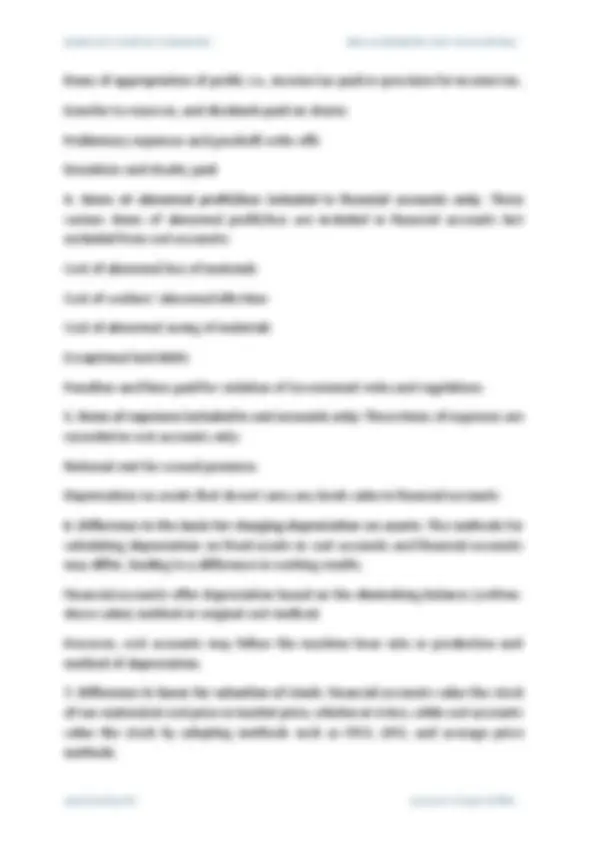
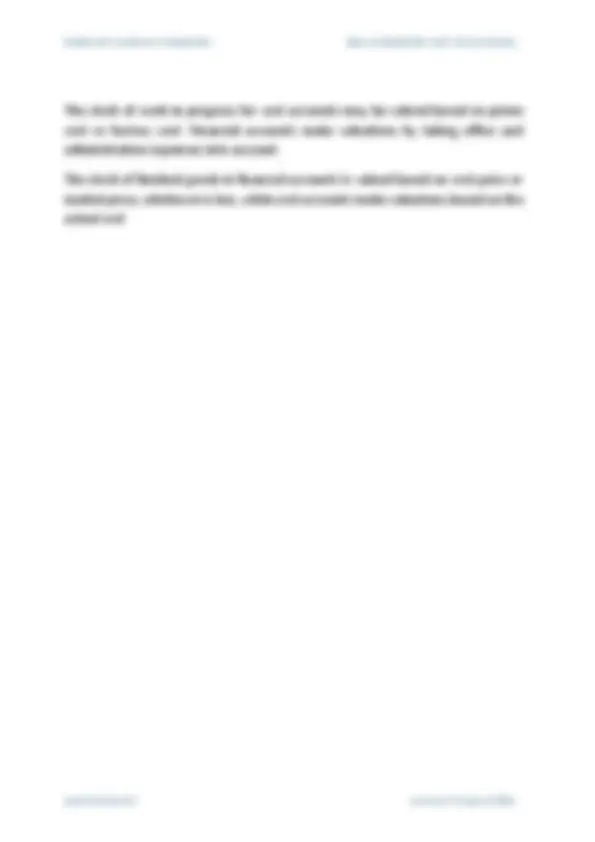
Study with the several resources on Docsity
Earn points by helping other students or get them with a premium plan
Prepare for your exams
Study with the several resources on Docsity
Earn points to download
Earn points by helping other students or get them with a premium plan
Community
Ask the community for help and clear up your study doubts
Discover the best universities in your country according to Docsity users
Free resources
Download our free guides on studying techniques, anxiety management strategies, and thesis advice from Docsity tutors
Cost accounting information about the latest class notes
Typology: Lecture notes
1 / 58
This page cannot be seen from the preview
Don't miss anything!
Cost - As a noun-The amount of expenditure (actual or notional) incurred on or attributable to a specified article, product or activity. As a verb- To ascertain the cost of a specified thing or activity. Costing - Costing is defined as “the technique and process of ascertaining costs”. According to CIMA “an organisation’s costing system is the foundation of the internal financial information system for managers. It provides the information that management needs to plan and control the organisation’s activities and to make decisions about the future.” Cost Accounting - Cost Accounting is defined as "the process of accounting for cost which begins with the recording of income and expenditure or the bases on which they are calculated and ends with the preparation of periodical statements and reports for ascertaining and controlling costs." OBJECTIVES OF COST ACCOUNTING The main objectives of cost and management accounting are explained as below: (i) Ascertainment of Cost: The main objective of cost accounting is accumulation and ascertainment of cost. Costs are accumulated, assigned and ascertained for each cost object. (ii) Determination of Selling Price and Profitability: The cost accounting system helps in determination of selling price and thus profitability of a cost object. (iii) Cost Control: Maintaining discipline in expenditure is one of the main objective of a good cost accounting system. It ensures that expenditures are in consonance with predetermined set standard and any variation from these (iv) Cost Reduction : It may be defined "as the achievement of real and permanent reduction in the unit cost of goods manufactured or services standards is noted and reported on continuous basis. Rendered without impairing their suitability for the use intended or diminution in the quality of the product." v) Assisting management in decision making: Cost and Management accounting by providing relevant information, assist management in planning, implementing, measuring, controlling and evaluation of various activities.
Let us look at some of the importance of cost accounting to the management of an organization,
1. Classification of Costs Some costs are prime cost, direct cost, factory cost, selling cost etc. Such classification allows the management to control the costs and ascertain the profitability of any such processes and activities. It also helps in calculating efficiency. 2. Cost Control An efficient business focuses on controlling the cost of inventory, labor, and various other overhead costs. Cost accounting allows them to do so. For example to achieve maximum efficiency in their inventory management the can adopt the EOQ technique which is a costing technique. 3. Price Determination Cost accounting makes the basic distinction between fixed and variable costs. This is then used by management to fix the prices of products, according to the costs of the product. 4. Fixing of Standards Organizations use standards to make estimates and budgets for the future. They use these as a basis to measure the actual efficiency of the process or department. 5. Helps in estimates: Ascertained costs provide a measure for estimates, a guide to policy, and control over current production. 6. Cost Accounting helps in channelizing production on the right lines: Costing makes possible for the management to distinguish between profitable and non- profitable activities. Profits can maximize by concentrating or profitable operations and eliminating non-profitable ones. 7. Helps in reducing wastage: As it is possible to know the cost of the article at every stage, it becomes possible to check various forms of waste, such as time, expense, etc., or in the use of machinery, equipment, and tools.
An efficient costing system brings prosperity to the concerned business enterprise resulting in stepping up of the government revenue. Also, the overall economic development of a country takes place due to an increase in the efficiency of production. Control of costs, elimination of wastages and inefficiencies lead to the progress of the industry and in consequence of the nation as a whole.
Basis Financial Accounting Cost Accounting (i) Objective It provides information about the financial performance of an entity. Ascertainment of cost for the purpose of cost control and decision making. (ii) Nature It classifies records, present and interprets transactions in monetary terms. It classifies, costs records, present, and interprets it in a significant manner. (iii) Recording of data It records Historical data. It makes use of both historical and predetermined costs. (iv) Users of information The users of financial accounting statements are shareholders, creditors, financial analysts and government and its agencies, etc. The cost accounting information is generally used by internal management. But some time regulatory authorities also. (v) Analysis of cost and profit It shows profit or loss of the organization either segment wise or as a whole. It provides the cost details for each cost object i.e. product, process, job, contracts, etc. (vi) Time period. Financial Statements are prepared usually for a year. Reports and statements are prepared as and when required (vii) Presentation of information A set format is used for presenting financial information. In general, no set formats for presenting cost information is followed
It means the grouping of costs according to their common characteristics. The important ways of classification of costs are: A. By Nature or Element B. By Functions C. By Variability or Behaviour
D. By Controllability E. By Normality F. By Costs for Managerial Decision Making A. By Nature or Element This type of classification is useful to determine the total cost
1. Direct Materials: Materials which are present in the finished product (cost object) or can be economically identified in the product are called direct materials. For example, cloth in dress making; materials purchased for a specific job etc. 2. Direct Labour: Labour which can be economically identified or attributed wholly to a cost object is called direct labour. For example, employee engaged on the actual production of the product or in carrying out the necessary operations for converting the raw materials into finished product 3. Direct Expenses: It includes all expenses other than direct material or direct labour which are specially incurred for a particular cost object and can be identified in an economically feasible way. For example, hire charges for some special machinery, cost of defective work. 4. Indirect Materials: Materials which do not normally form part of the finished product (cost object) are known as indirect materials. These are — • Stores used for maintaining machines and buildings (lubricants, cotton waste, bricks etc.) • Stores used by service departments like power house, boiler house, canteen etc. 5. Indirect Labour: Labour costs which cannot be allocated but can be apportioned to or absorbed by cost units or cost centres is known as indirect labour. Examples of indirect employees includes foreman and supervisors; maintenance workers; etc. 6. Indirect Expenses: Expenses other than direct expenses are known as indirect expenses, that cannot be directly, conveniently and wholly allocated to cost centres. Factory rent and rates, insurance of plant and machinery, power, light, heating, repairing, telephone etc., are some examples of indirect expenses. 7. Overheads: It is the aggregate of indirect material costs, indirect labour costs and indirect expenses. The main groups into which overheads may be subdivided are the following:
(a) Graphical method (b) High points and low points method (c) Analytical method (d) Comparison by period or level of activity method (e) Least squares method D. By Controllability Costs here may be classified into controllable and uncontrollable costs.
1. Controllable Costs: Cost that can be controlled, typically by a cost, profit or investment centre manager is called controllable cost. For example, direct costs comprising direct labour, direct material, direct expenses and some of the overheads are generally controllable by the shop level management. 2. Uncontrollable Costs: Costs which cannot be influenced by the action of a specified member of an undertaking are known as uncontrollable costs. E. By Normality According to this basis cost may be categorised as follows: 1. Normal Cost: It is the cost which is normally incurred at a given level of output under the conditions in which that level of output is normally attained. 2. Abnormal Cost: It is the cost which is not normally incurred at a given level of output in the conditions in which that level of output is normally attained. It is charged to Costing Profit and loss Account. F. By Costs for Managerial Decision Making According to this basis cost may be categorised as follows: 1. Pre-determined Cost: A cost which is computed in advance before production or operations start, on the basis of specification of all the factors affecting cost, is known as a pre-determined cost. 2. Standard Cost: A pre-determined cost, which is calculated from managements ‘expected standard of efficient operation’ and the relevant necessary expenditure. It may be used as a basis for price fixation and for cost control through variance analysis. 3. Marginal Cost: The amount at any given volume of output by which aggregate costs are changed if the volume of output is increased or decreased by one unit.
4. Estimated Cost: Kohler defines estimated cost as “the expected cost of manufacture, or acquisition, often in terms of a unit of product computed on the basis of information available in advance of actual production or purchase”. Estimated costs are prospective costs since they refer to prediction of costs. 5. Differential Cost: (Incremental and decremental costs). It represents the change (increase or decrease) in total cost (variable as well as fixed) due to change in activity level, technology, process or method of production, etc. 6. Imputed Costs: These costs are notional costs which do not involve any cash outlay. Interest on capital, the payment for which is not actually made, is an example of imputed cost. These costs are similar to opportunity costs. 7. Capitalized Costs: These are costs which are initially recorded as assets and subsequently treated as expenses. Example, installation expenses on the erection of a machine are added to the cost of a machine. 8. Product Costs: These are the costs which are associated with the purchase and sale of goods (in the case of merchandise inventory). Hence, under marginal costing, variable manufacturing costs and under absorption costing, total manufacturing costs (variable and fixed) constitute inventorial or product costs. 9. Opportunity Cost: This cost refers to the value of sacrifice made or benefit of opportunity foregone in accepting an alternative course of action. For example, a firm financing its expansion plan by withdrawing money from its bank deposits. In such a case the loss of interest on the bank deposit is the opportunity cost for carrying out the expansion plan. 10. Out-of-pocket Cost: It is that portion of total cost, which involves cash outflow. This cost concept is a short-run concept and is used in decisions relating to fixation of selling price in recession, make or buy, etc. Out–of–pocket costs can be avoided or saved if a particular proposal under consideration is not accepted. 11. Shut down Costs: Those costs, which continue to be, incurred even when a plant is temporarily shut-down e.g. rent, rates, depreciation, etc. These costs cannot be eliminated with the closure of the plant. In other words, all fixed costs, which cannot be avoided during the temporary closure of a plant, will be known as shut down costs. 12. Sunk Costs: Historical costs incurred in the past are known as sunk costs. They play no role in decision making in the current period. For example, in the case of a decision relating to the replacement of a machine, the written down value of the existing machine is a sunk cost and therefore, not considered. 13. Absolute Cost: These costs refer to the cost of any product, process or unit in its totality. When costs are presented in a statement form, various cost components may be shown in absolute amount or as a percentage of total cost or as per unit cost or altogether. Here the
Professional services Chargeable hour, job, contract Education Course, enrolled student, successful Student Hospitals Patient day
A cost centre, sometimes cost centre, is a department within a business to which costs can be allocated. The term includes departments which do not produce directly but incur costs to the business.’ Classification of Cost Centres or Types of Cost Centres: There are three different ways of classifying the cost centres. Classified into three types. They are:
1. From the stand point of functions, cost centres may be (a) Production Cost Centre (b) Service Cost Centre (c) Mixed Cost Centre (a) Production Cost Centre: A production cost centre is a cost centre which is directly Concerned with production or manufacturing. Examples of production cost centres are machine shop, welding shop assembly shop, etc. (b) Service Cost Centre: service cost centre is one which is not engaged in A production, but provides service to production centres. Examples of service cost centres are power house, boiler house, store house, warehouse, repairs and maintenance shop, drawing office, internal transport, time-keeping office, staff training college, research and laboratory centre, canteen, administrative office, etc. (c) Mixed Cost Centre: A mixed cost centre 1s a cost centre which is engaged both in production work and in service. Tool shop produced dies and jigs and servicing tools, carpentry shop preparing moulds as well as under-taking general Repair work for the factory, etc. are examples of mixed cost centres, 2. Cost centres can also be classified into: (a) Personal Cost Centre. (b) Impersonal Cost Centre. (a) Personal Cost Centre:
(a) A personal cost centre is one which consists of a person or group of persons, such as works manager, foreman, store keeper, sales manager, salesman, Customer, etc. in respect which costs are collected and charged for the purpose of Cost ascertainment and cost control. (b) Impersonal Cost Centre: An impersonal cost centre refers to a cost centre which consists of a location, i.e., an area, such as a department or store yard, or an item of machine or equipment, or a group of machines or equipment’s, for which costs are collected for cost ascertainment and cost control.
3. Cost centres can also be classified into: (a) Operation Cost Centre. (b) Process Cost Centre. a) Operation Cost Centre: An operation cost centre is a cost centre which consists of machines and or persons carrying out similar operations for ascertainment and cost control. Examples of operation cost Centres are persons and machines engaged in welding which costs are accumulated (i.e., collected) for cost turning machining, etc. b) Process Cost Centre: A process cost centre is one which consists of machines and or persons carrying out a specific process or a continuous sequence of operations for which costs are accumulated or collected for cost ascertainment and cost control.
There are a number of differences between a cost centre and a cost unit. The main differences between the two are as follows:
3.Batch cost is a collection of costs paid when a group of items or services is manufactured that cannot be traced back to individual products or services within the group. It may be essential to assign the batch cost to individual units within a batch for cost accounting reasons. 4.Process costing is an accounting method for tracking and accumulating direct expenses in a manufacturing process and allocating indirect costs. Costs are given to items in huge batches, which can span a month’s worth of production. 5.Unit Costing A company’s unit cost is the cost of producing, storing, and selling one unit of a given product. All fixed and variable expenses in production are included in unit costs. A cost unit is a unit of measurement used to determine the volume of a service or product. Mines, oil drilling units, cement works, brickwork, or unit production cycles, such as radios and washing machines, all use unit costs. 6.Operation Costing Job costing and process costing are combined in operation costing. It may be employed when a product is made from various raw materials and then finished using a standardised procedure for a group of items. The main goal of this strategy is to figure out the cost of each procedure. 7.Multiple Costing When things are sold that contain various other processed parts, multiple costing, also known as composite costing, is an accounting method used when these parts cost differently. Each of the elements made by other processes, like the ultimate product, has a cost connected with it. 8.Operating costs , often known as operational expenses, are expenses connected to the running of a business or a product, component, piece of equipment, or facility. They seem to be the costs of resources used by a company just to stay in business. Airlines, trains, road transport companies (both products and passengers), hotels, cinema halls, power plants, and other businesses employ operating costs. Types or Techniques of Costing: Following are the main types or techniques of costing for ascertaining costs:
1. Uniform Costing : It is the use of same costing principles and/or practices by several undertakings for common control or comparison of costs. 2. Marginal Costing : It is the ascertainment of marginal cost by differentiating between fixed and variable cost. It is used to ascertain the effect of changes in volume or type of output on profit. 3. Standard Costing: A comparison is made of the actual cost with a pre-arranged standard cost and the cost of any deviation (called variances) is analysed by causes. This permits management to investigate the reasons for these variances and to take suitable corrective action.
4. Historical Costing : It is ascertainment of costs after they have been incurred. It aims at ascertaining costs actually incurred on work done in the past. It has a limited utility, though comparisons of costs over different periods may yield good results. 5. Direct Costing : It is the practice of charging all direct costs, variable and some fixed costs relating to operations, processes or products leaving all other costs to be written off against profits in which they arise. 6. Absorption Costing : It is the practice of charging all costs, both variable and fixed to operations, processes or products. This differs from marginal costing where fixed costs are excluded.
information. In a typical cost sheet, cost information are presented on the basis of functional classification COST HEADS IN A COST SHEET The costs as classified on the basis of functions are grouped into the following cost heads in a cost sheet: (i) Prime Cost (ii) Cost of Production (iii) Cost of Goods Sold (iv) Cost of Sales
Production ........ units. Particulars TotalCost Cost per Unit Direct materials Opening stock of raw materials XXX Add: Purchases XXX Add : Expenses on purchases XXX Less : Closing stock of raw materials XXX Cost of material consumed XXX
9 Subsidy received on exports. Treatment of Scrap In certain manufacturing industries, scrap arises in the form of cuttings, trimmings, borings from metals or timber, etc. Scrap generally can be sold at a price. The realisable value of scrap is deducted from factory overheads or factory cost while preparing the cost sheet. Advantages of Cost sheet or Cost Statements The main advantages of a Cost Sheet are as follows: (i) It provides the total cost figure as well as cost per unit of production. (ii) It helps in cost comparison. (iii) It facilitates the preparation of cost estimates required for submitting tenders. (iv) It provides sufficient help in arriving at the figure of selling price. (v) It facilitates cost control by disclosing operational efficiency
Depreciation and Repairs of Office Equipment Depreciation of Office Furniture Subscription to Trade Journals Office Lighting Establishment Charges Director’s Travelling Expenses Postage Legal Charges Audit Fees Cost of Production Add : Opening Stock of Finished Goods Less : Closing Stock of Finished Goods Cost of Goods Sold Add : Selling and Distribution Overheads : Advertising Showroom Expenses Bad Debts Salesmen’s Salaries and Expenses Packing Expenses Carriage Outward Commission of Sales Agents Counting House Salaries Cost of Catalogues Expenses of Delivery Vans Collection Charges Travelling Expenses Cost of Tenders Warehouse Expenses Cost of Mailing Literature Sales Manager’s Salaries Sales Director’s Fees Showroom Expenses Sales Office Expenses Depreciation and Repairs of Delivery Vans Expenses of Sales Branches Cost of Sales (or Total Cost) PROFIT/LOSS SALES xxx xxx xxx xxx xxx xxx xxx xxx xxx xxx xxx xxx xxx xxx xxx xxx xxx xxx xxx xxx xxx xxx xxx xxx xxx xxx xxx xxx xxx xxx xxx xxx xxx xxx xxx xxx xxx xxx
The term "materials" is, generally, used to refer to raw materials used in the process of production, semi-finished materials or products, components (i.e., finished parts entering into a product) and spare parts, consumable stores or factory supplies (i.e., items which are used in production, but do not become part of the finished products), such as oil, grease, soap, sand paper, cotton waste, rags, etc., and packing materials, such as cardboard boxes, bottles, cellophane papers, etc.
The term materials refer to all commodities consumed in the process of manufacture. Materials can be broadly classified into two types namely:
Material Control is a system which ensures that right quality of material is available in the right quantity at the right time and right place with the right amount of investment. In simple words material control is a systematic control over the purchasing, storing and using of materials so as to have the minimum possible cost of materials.