
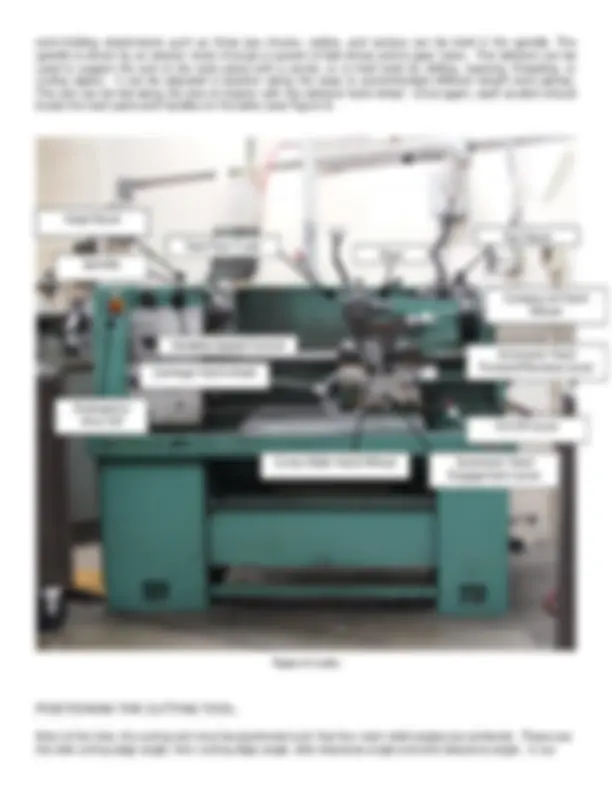
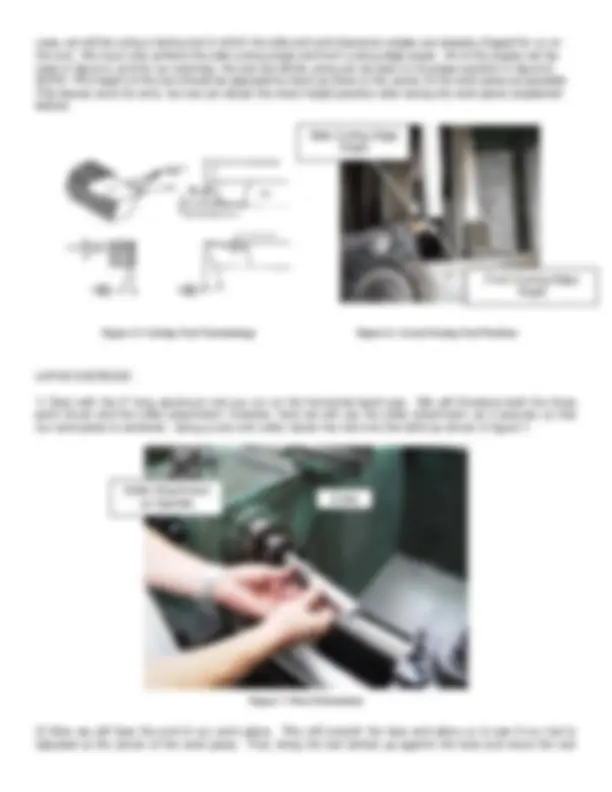
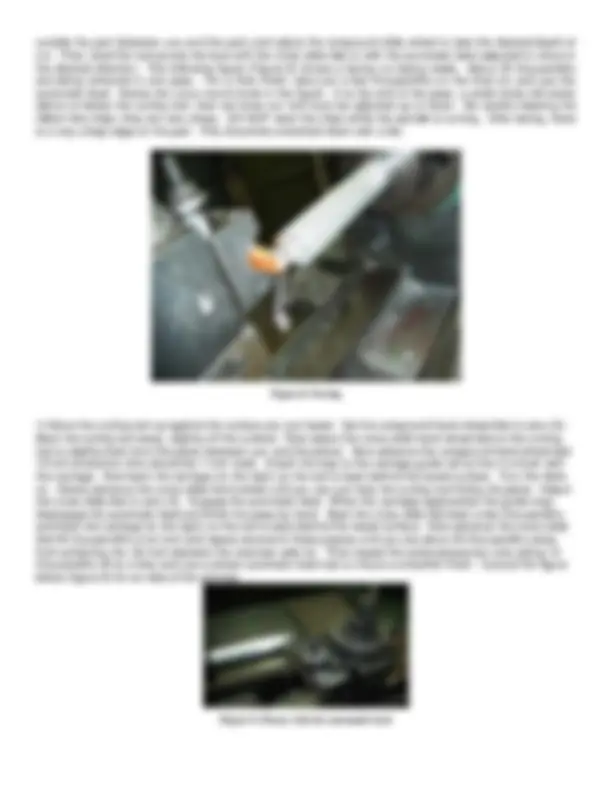
Study with the several resources on Docsity
Earn points by helping other students or get them with a premium plan
Prepare for your exams
Study with the several resources on Docsity
Earn points to download
Earn points by helping other students or get them with a premium plan
Community
Ask the community for help and clear up your study doubts
Discover the best universities in your country according to Docsity users
Free resources
Download our free guides on studying techniques, anxiety management strategies, and thesis advice from Docsity tutors
Material Type: Project; Class: 650 - DESIGN OF MECH SYS I; Subject: MECHANICAL AND AEROSPACE ENGINEERING; University: Rutgers University; Term: Fall 2004;
Typology: Study Guides, Projects, Research
1 / 6
This page cannot be seen from the preview
Don't miss anything!
Department of Mechanical and Aerospace Engineering 650:486 Design of Mechanical Systems Fall 2004
Instructor 1: Vasilije Jovanovic Office: Eng. Bldg. D-117, Phone: 732.445.5769, e-mail: vasilije@rci.rutgers.edu
Instructor 2: Jeffrey Ippolito Office: Eng. Bldg. D-123-D, Phone: 732.445.2770, e-mail: jeffipp@eden.rutgers.edu
The goal of this exercise is to demonstrate a basic set of instructions for the lathe and horizontal band saw. In order to obtain a passing grade in the Machine Shop instruction part of the course and to be approved to use the Machine Shop for the design project, a student has to be able to machine the part in Figure 1.
Figure 1: Part Drawing (All units in inches)
The horizontal band saw is useful for cutting long stock to a desired length. Like the vertical band saw, it contains a serrated blade that forms one continuous loop. Before starting the horizontal band saw, each student should locate the main parts and handles on the machine (see Figure 2).
Drilled Hole, 1 inch deep, 0.14 inch dia.
Figure 2: Horizontal Band Saw
Each group starts the exercise with a 12” long aluminum rod. Using the horizontal band saw, each student should cut one 3” piece off of the original. Obviously the 4th^ cut will not have to be made.
Before starting the band saw, students should adjust the stock into the vice and pull the blade arm down close to the stock to verify correct positioning of stock. NEVER ADJUST THE STOCK IN THE VICE WITH BAND SAW ON!
With the blade arm in the up position, start the band saw. Make sure there is sufficient water flowing onto the blade from the water nozzle. If too little or too much, SHUT OFF the saw and adjust the nozzle.
Pull the blade arm down slowly onto the stock. There is no need to apply much pressure downward as the saw will cut its way through the stock by itself, DON’T FORCE IT. The student needs only to assure the saw does not over-vibrate, which could cause the saw to jam. Simply apply a light amount of downward pressure to prevent the saw from jumping.
After cutting the 4 pieces, deburr the rough edges using the belt sander shown in Figure 3.
Figure 3: Belt Sander
Be sure to keep hands away from the belt at all times. Be careful, as the belt does not instantly stop when the power is shut off.
The purpose of a lathe is to rotate a part against a tool whose position it controls. It is useful for fabricating parts and/or features that have a circular cross section. The spindle is the part of the lathe that rotates. Various
Start/Stop
Motor
Water hose and nozzle
Blade down
Blade Guide/Guard
Vice
Vice Blade up tightening wheel
case, we will be using a facing tool in which the side and end clearance angles are already shaped for us on the tool. We must only achieve the side cutting angle and front cutting edge angle. All of the angles can be seen in figure 5, and for our exercise, the tool we will be using can be seen in its proper position in figure 6. NOTE: The height of the tool should be adjusted by hand as close to the center of the work piece as possible. This leaves room for error, but we can obtain the exact height position after facing the work piece (explained below).
Figure 5: Cutting Tool Terminology Figure 6: Actual Facing Tool Position
Figure 7: Part Orientation
Collet Attachment on Spindle Collet
Side Cutting Edge Angle
Front Cutting Edge Angle
outside the part (between you and the part) and adjust the compound slide wheel to take the desired depth of cut. Then, feed the tool across the face with the cross slide dial or with the automatic feed adjusted to move in the desired direction. The following figure (Figure 8) shows a facing cut being made. About 20 thousandths are being removed in one pass. For a finer finish, take just a few thousandths on the final cut and use the automatic feed. Notice the uncut round circle in the figure. If at the end of the pass, a small circle still exists above or below the cutting tool, then we know our tool must be adjusted up or down. Be careful clearing the ribbon-like chips; they are very sharp. DO NOT clear the chips while the spindle is turning. After facing, there is a very sharp edge on the part. This should be smoothed down with a file.
Figure 8: Facing
Back the cutting tool away, slightly off the surface. Now adjust the cross slide hand wheel dial so the cutting tool is slightly back from the piece (between you and the piece). Now advance the compound hand wheel dial 10 full revolutions (this should be 1 inch total). Attach the stop to the carriage guide rail so that it is flush with the carriage. Now back the carriage (to the right) so the tool is back behind the faced surface. Turn the lathe on. Slowly advance the cross slide hand wheel until you can just hear the cutting tool hitting the piece. Adjust the cross slide dial to zero (0). Engage the automatic feed. When the carriage approaches the guide stop, disengage the automatic feed and finish the pass by hand. Back the cross slide dial back a few thousandths and back the carriage (to the right) so the tool is back behind the faced surface. Now advance the cross slide dial 40 thousandths of an inch and repeat several of these passes until you are about 20 thousandths away from achieving the .50 inch diameter the exercise calls for. Then repeat the same passes but only taking 10 thousandths off at a time and use a slower automatic feed rate to insure a smoother finish. Consult the figure below (figure 9) for an idea of the process.
Figure 9: Passes with the automatic feed