
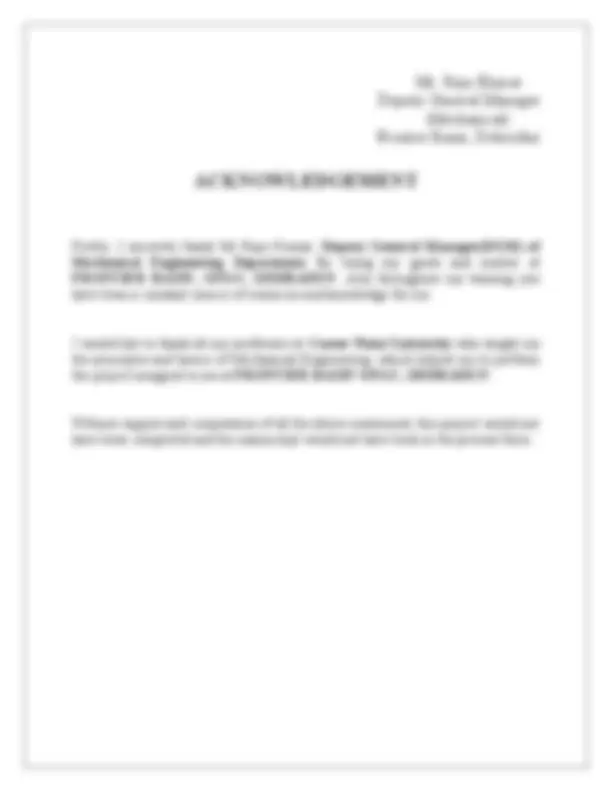
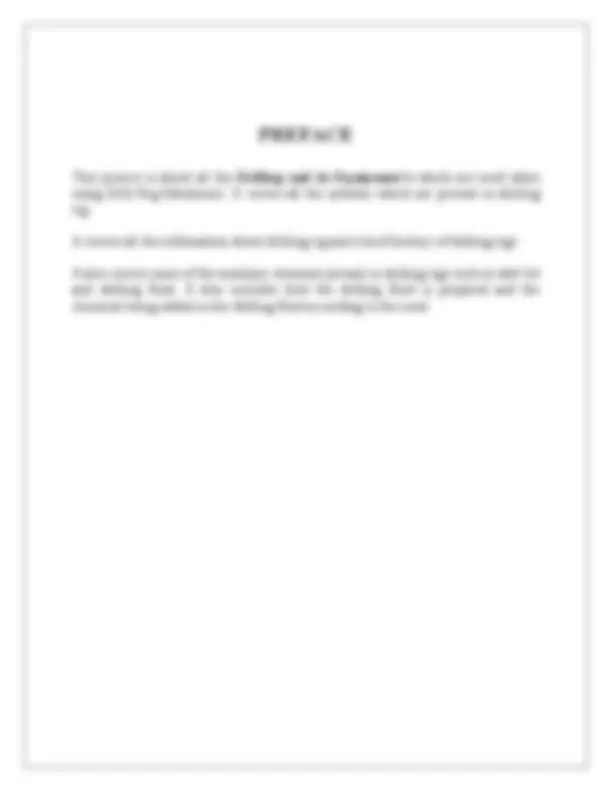
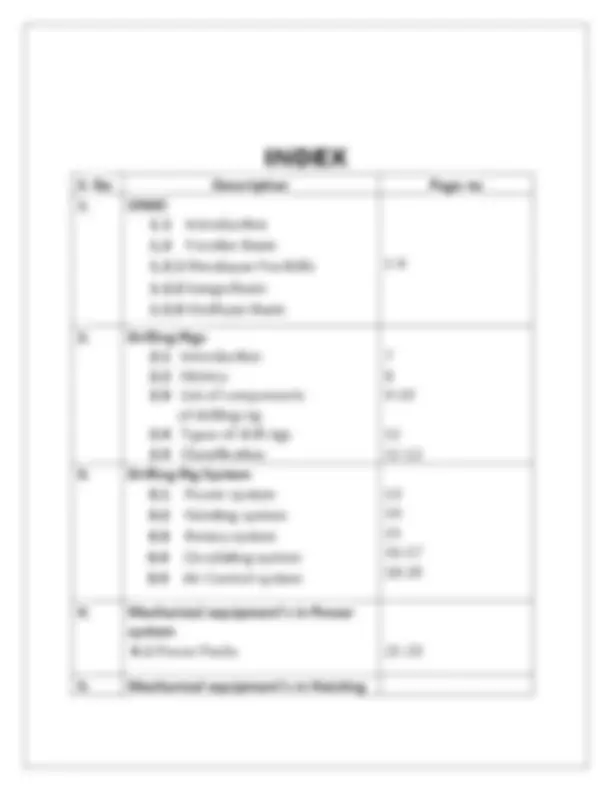
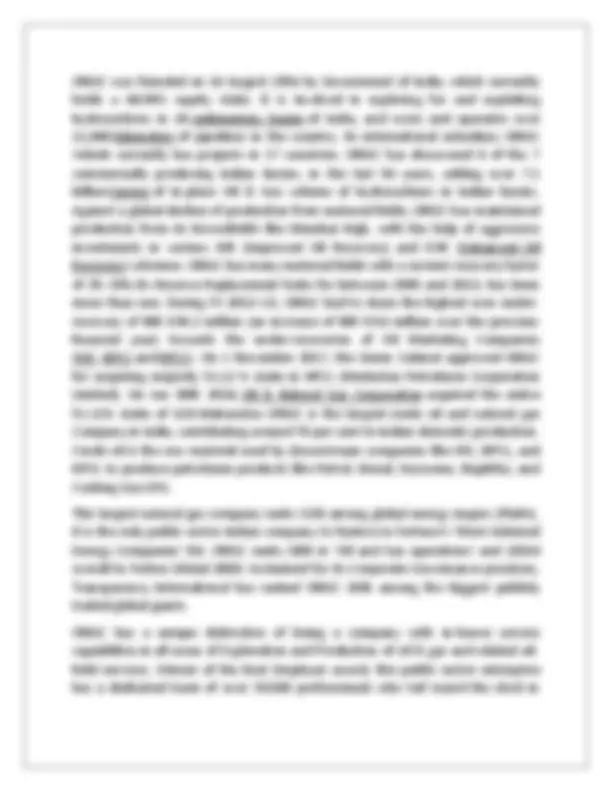
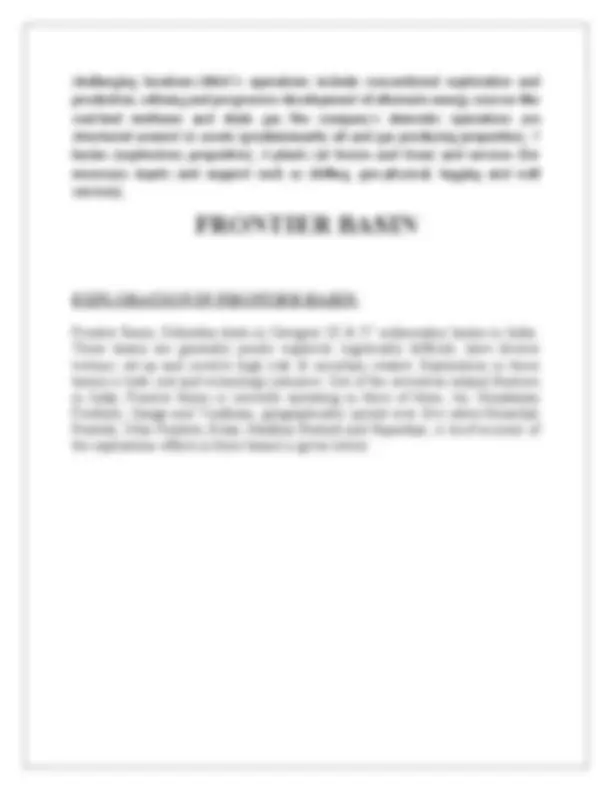
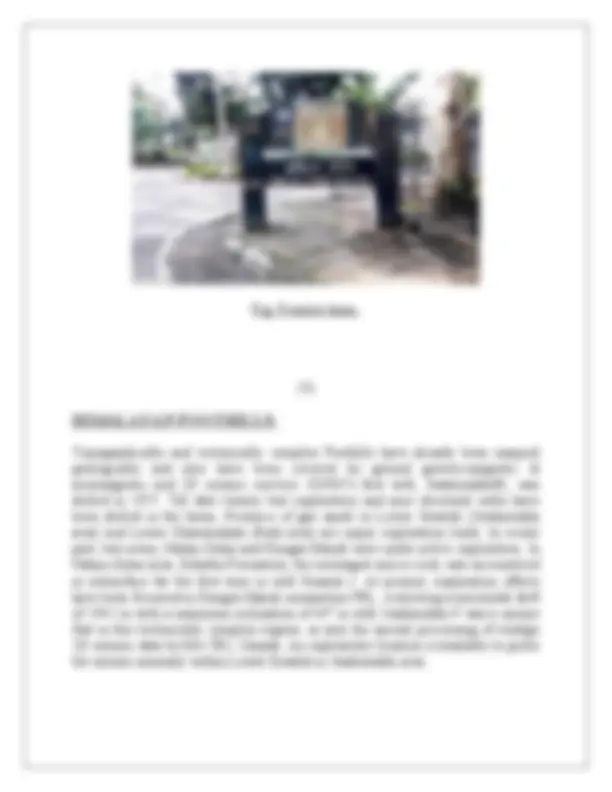
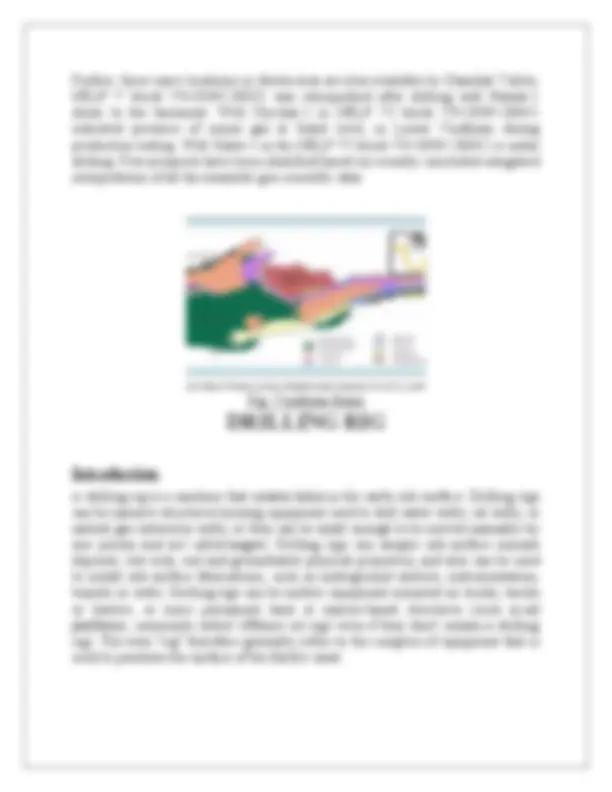
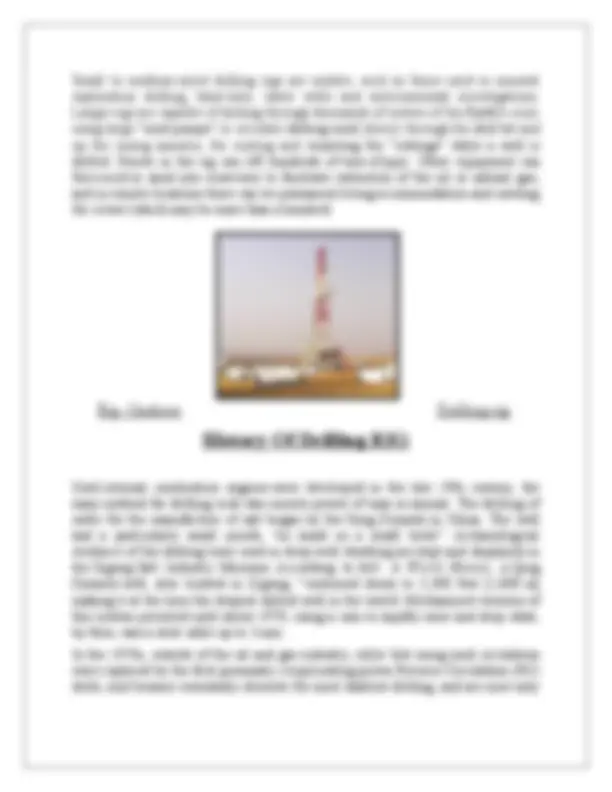
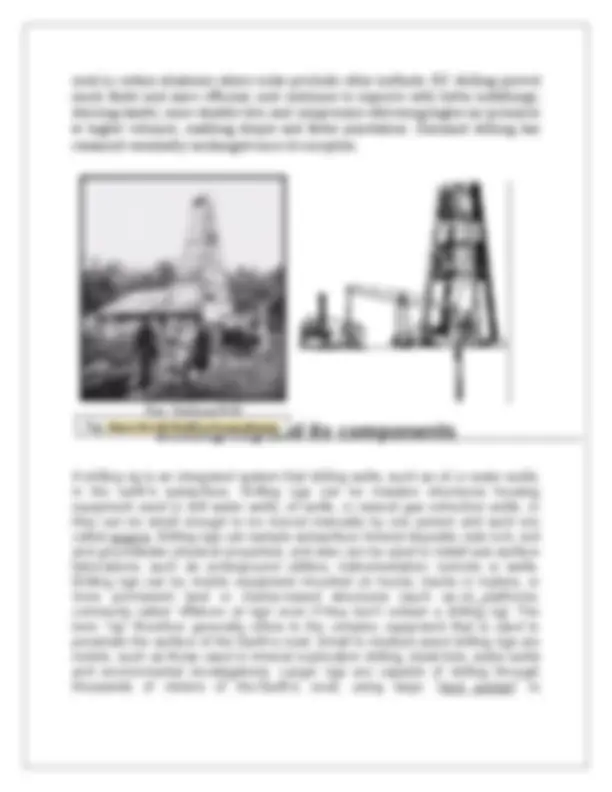
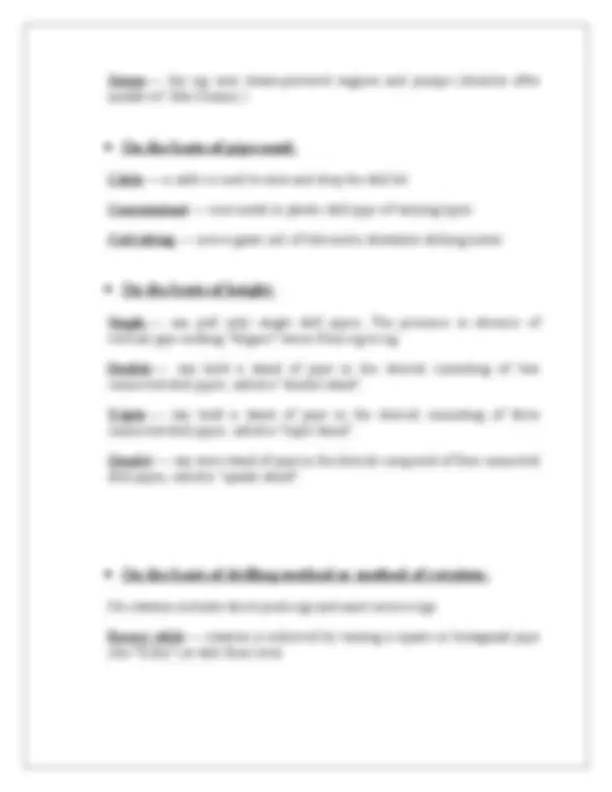
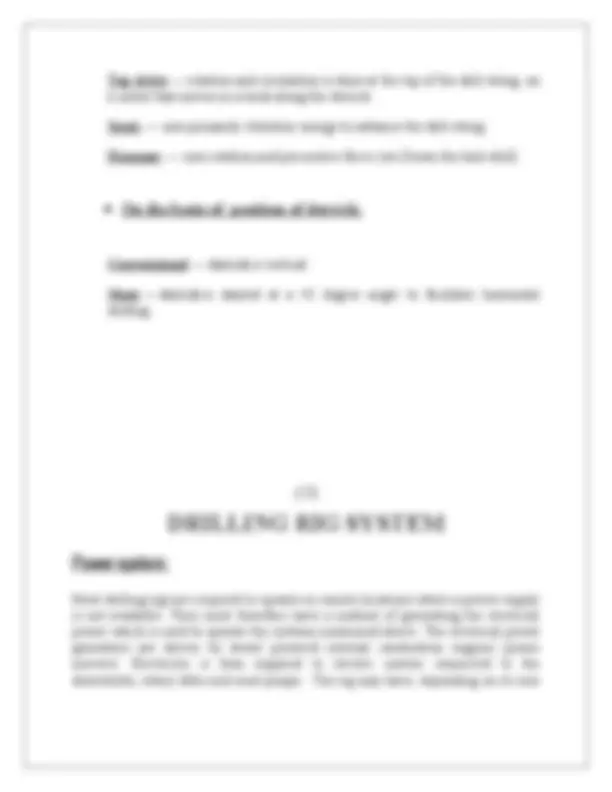
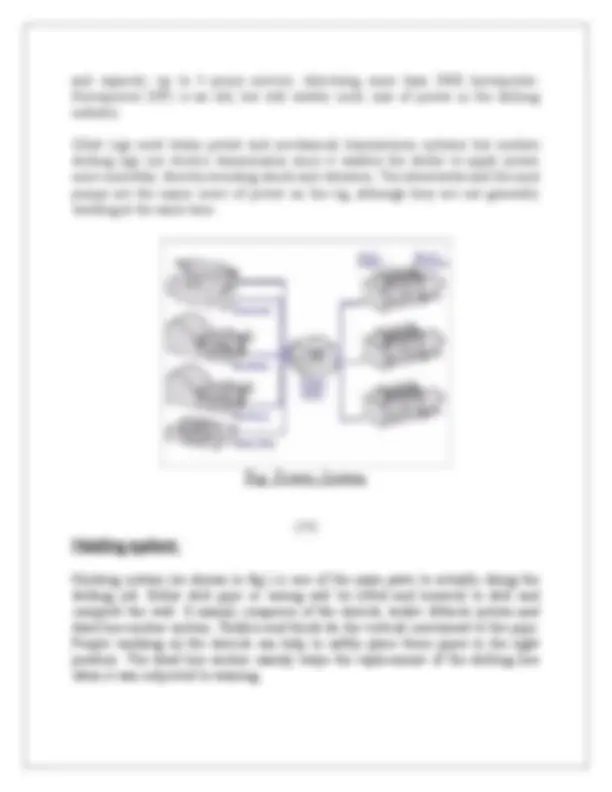
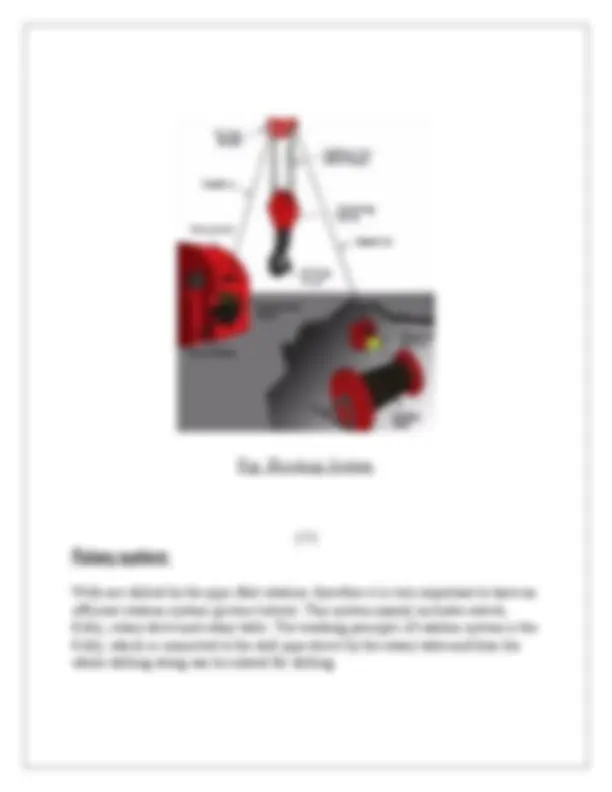
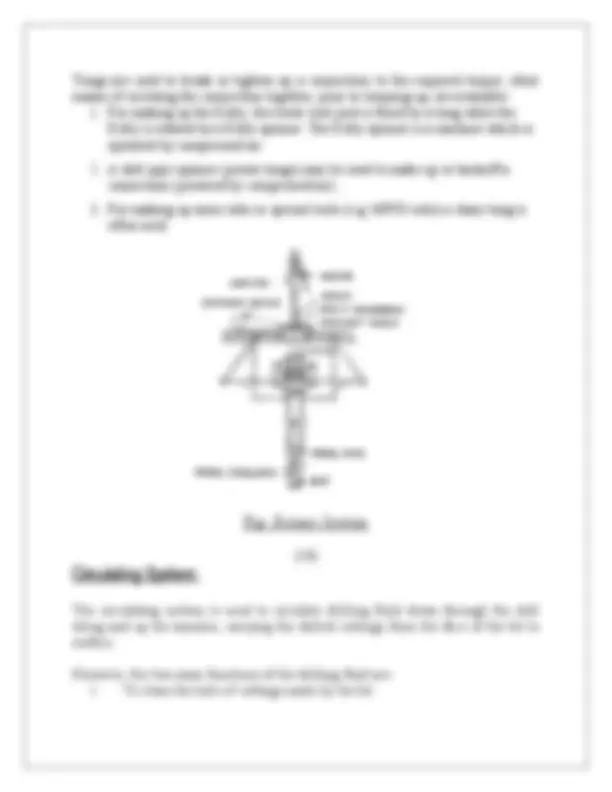
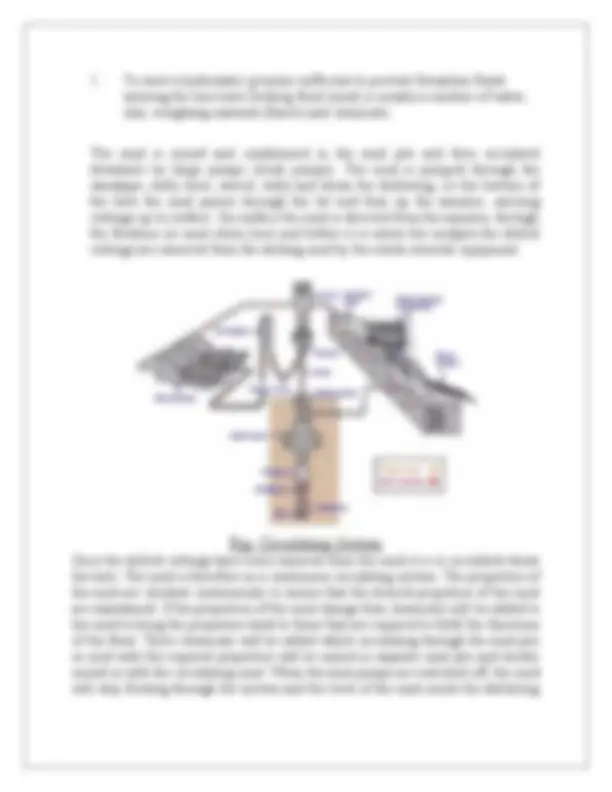
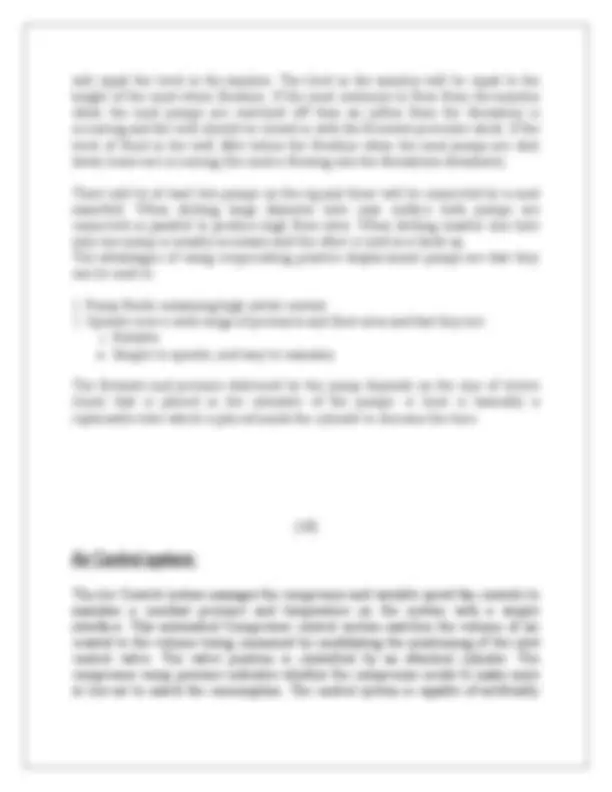
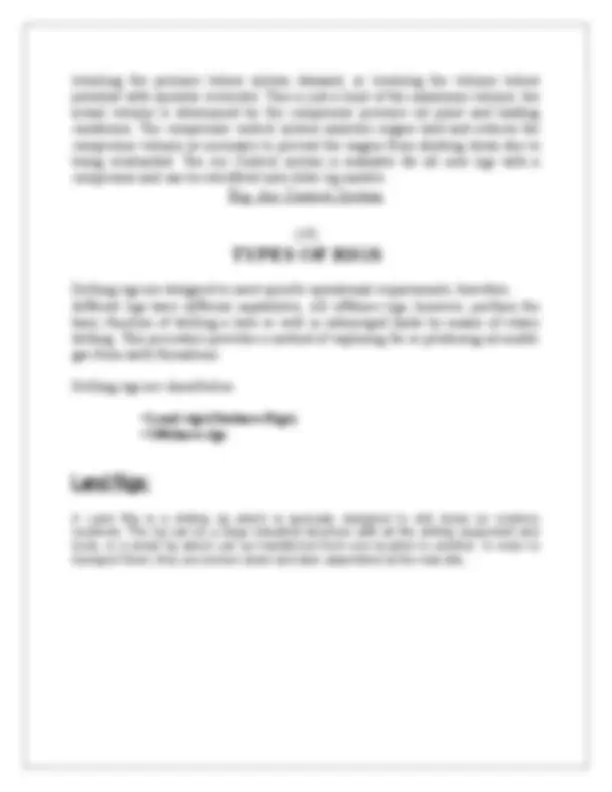
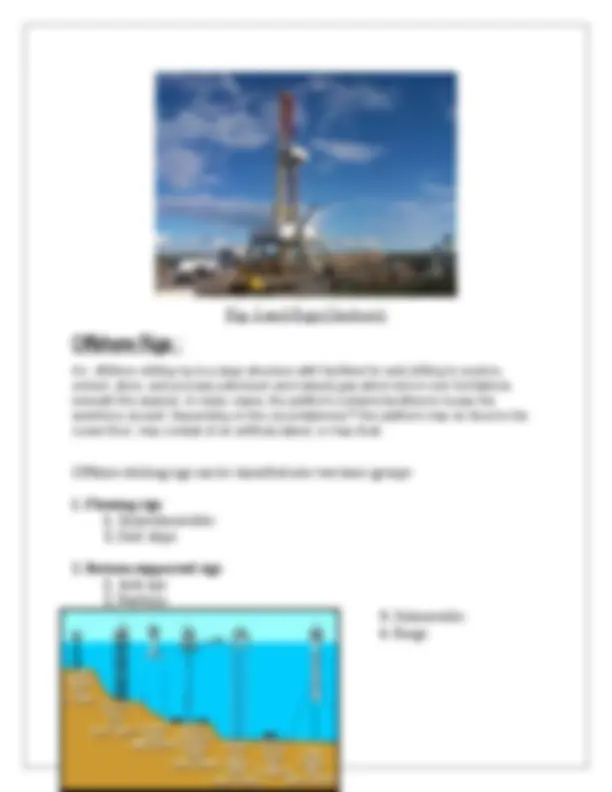
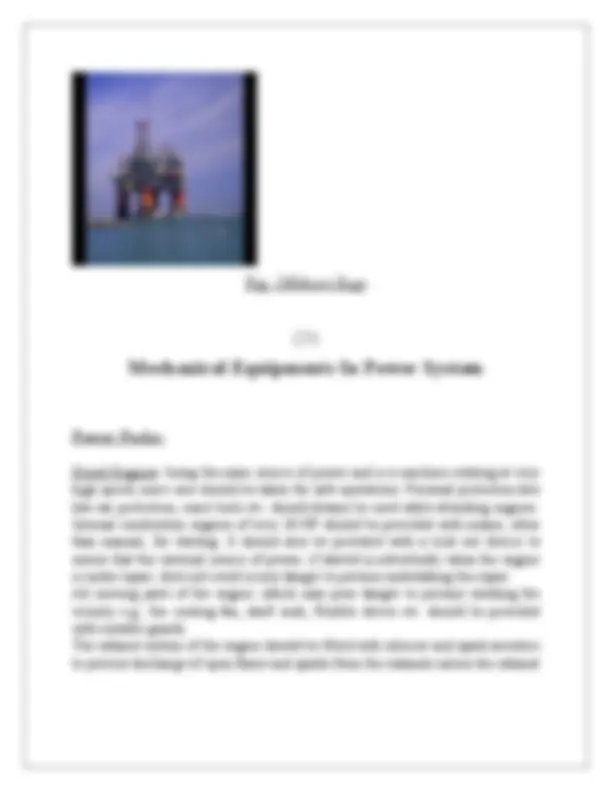
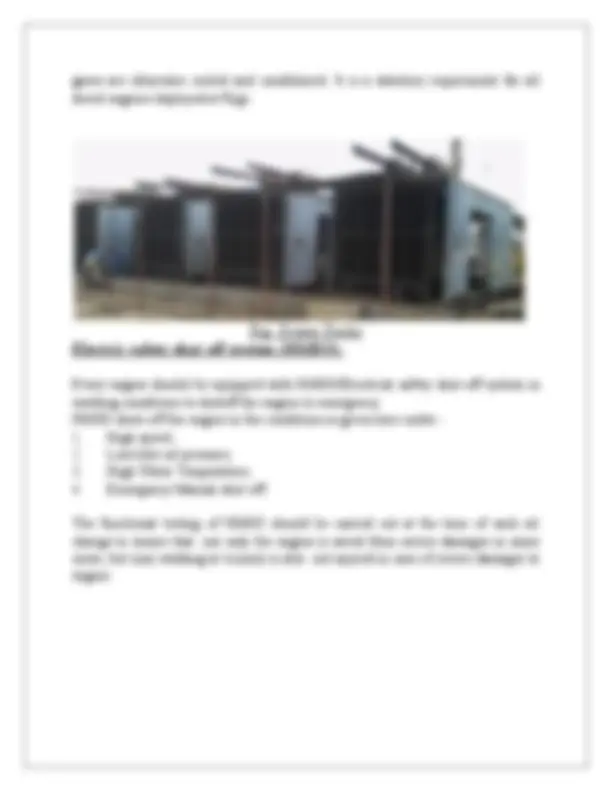
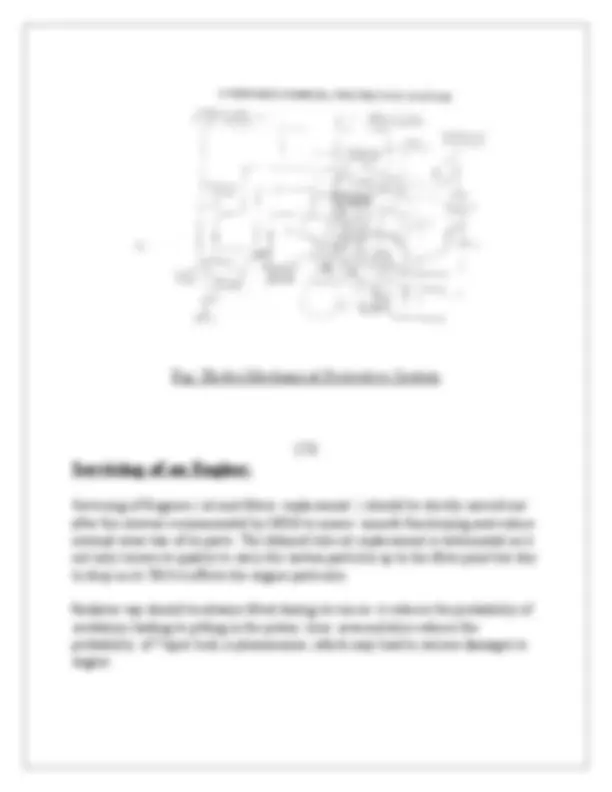
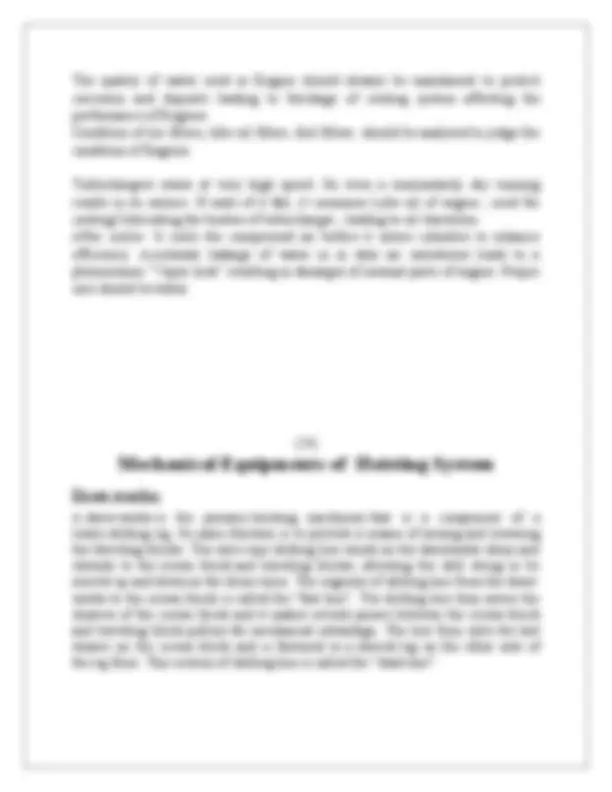
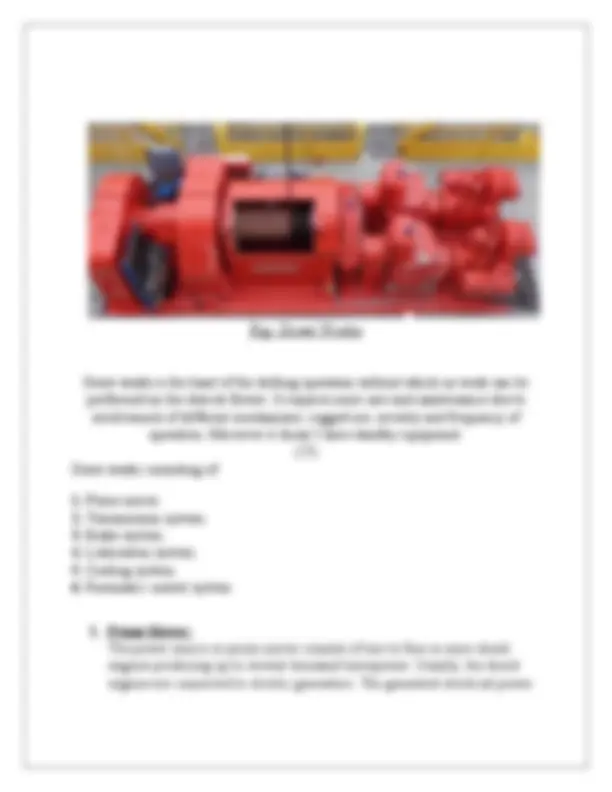
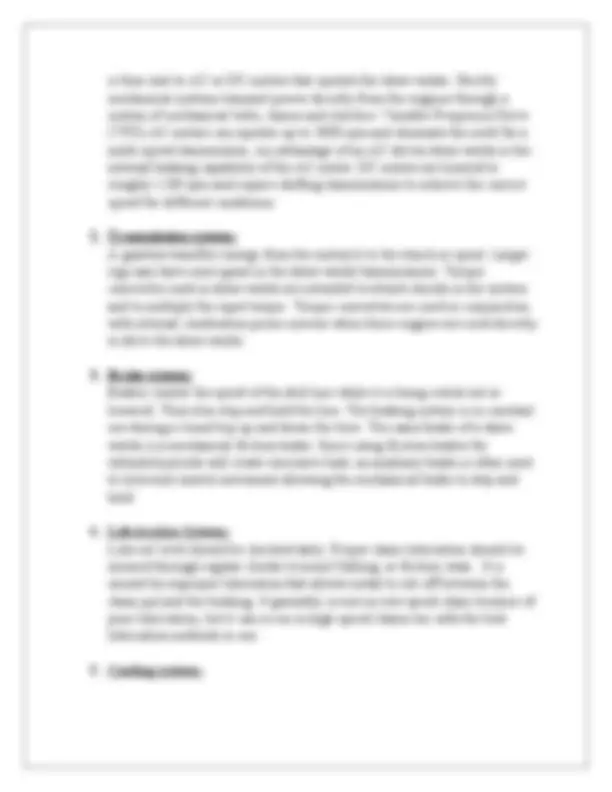
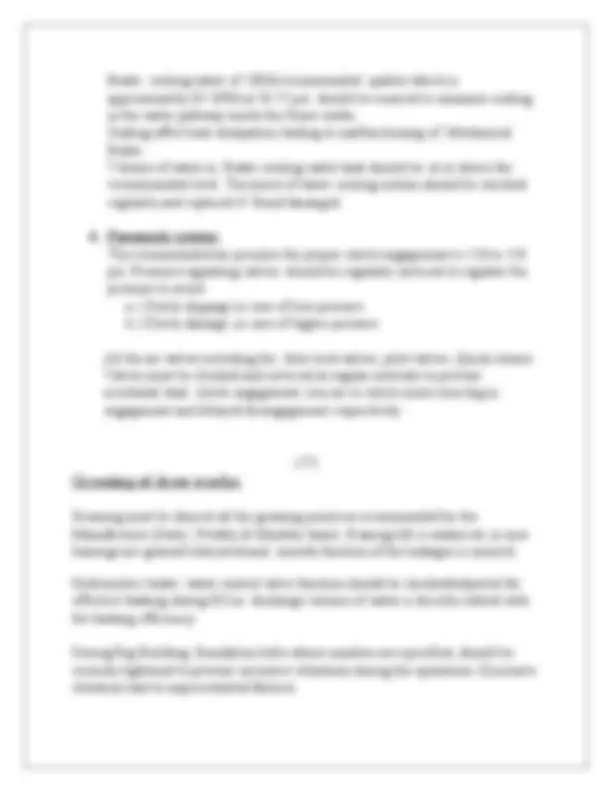
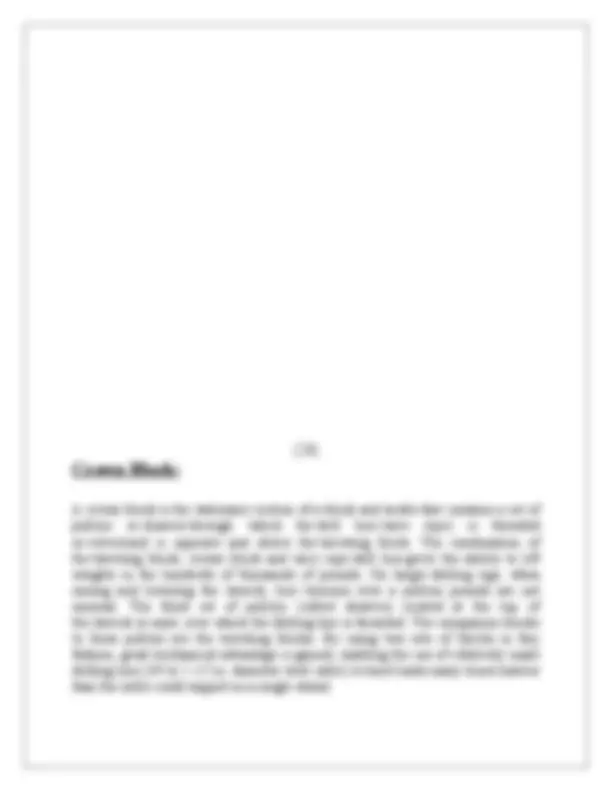
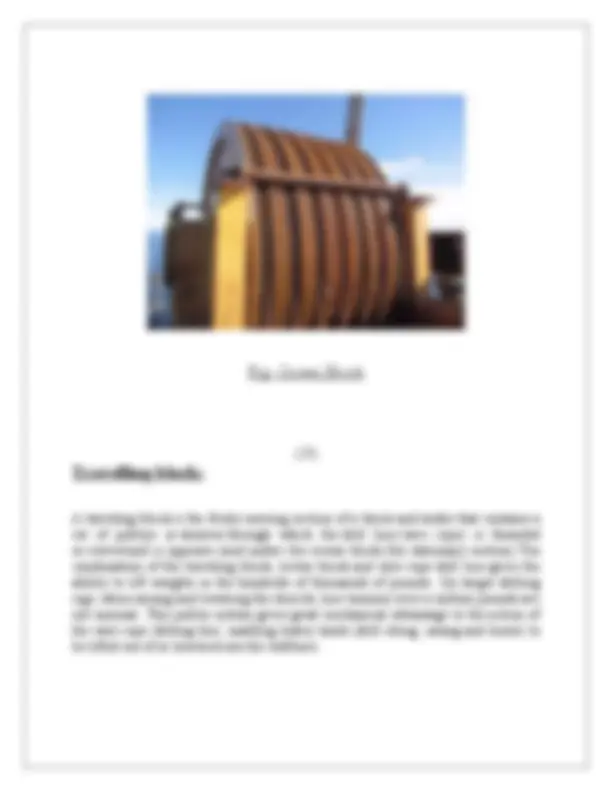
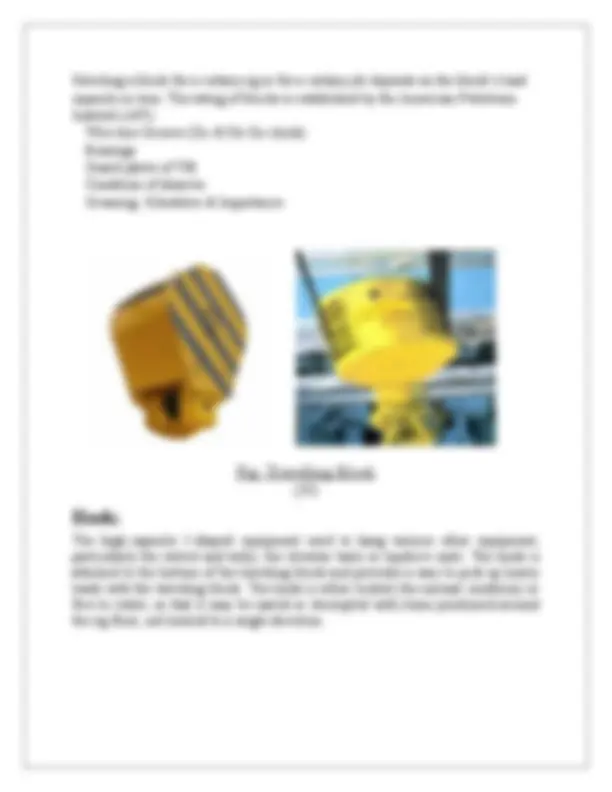
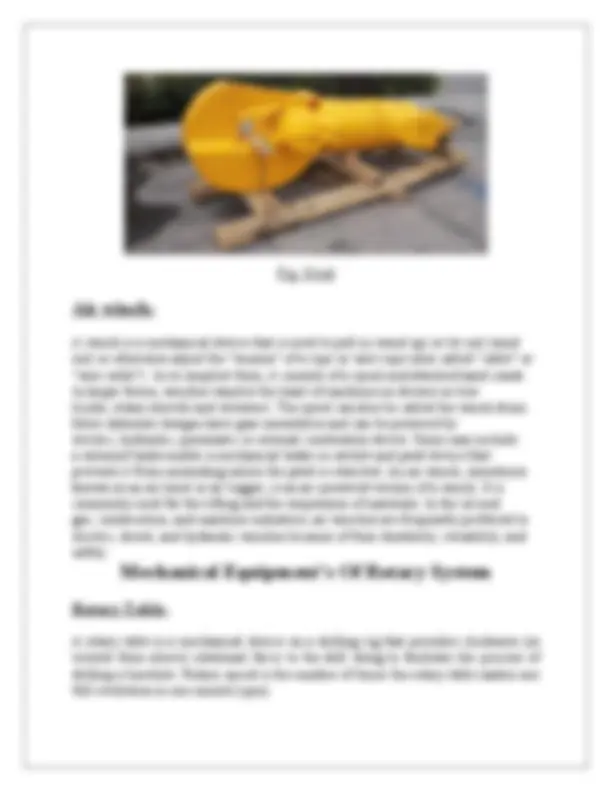

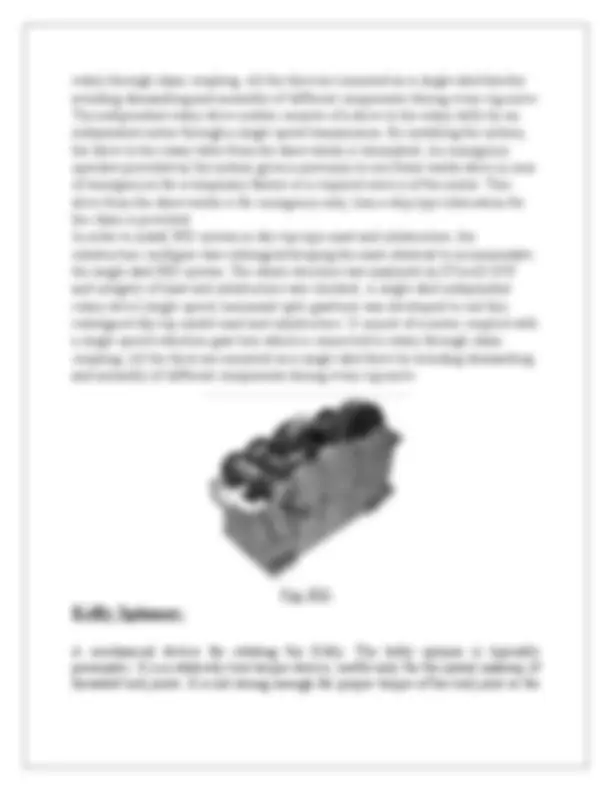
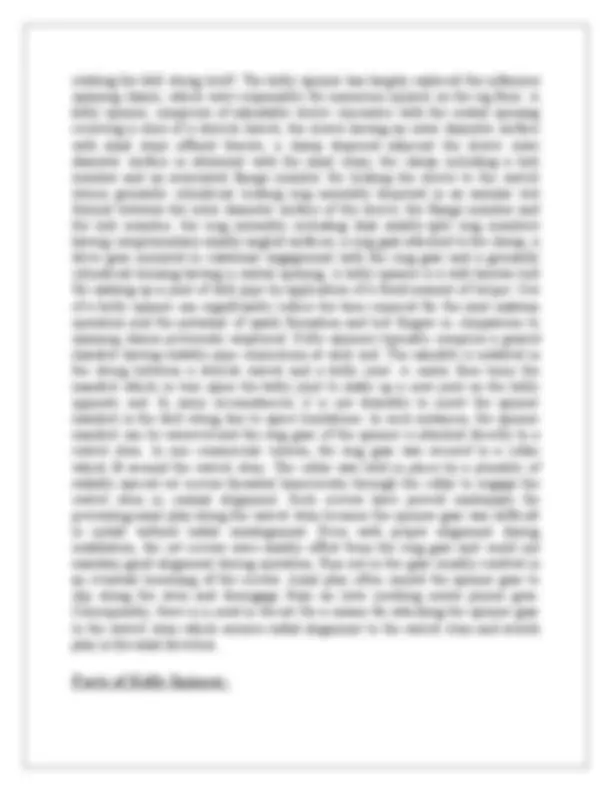
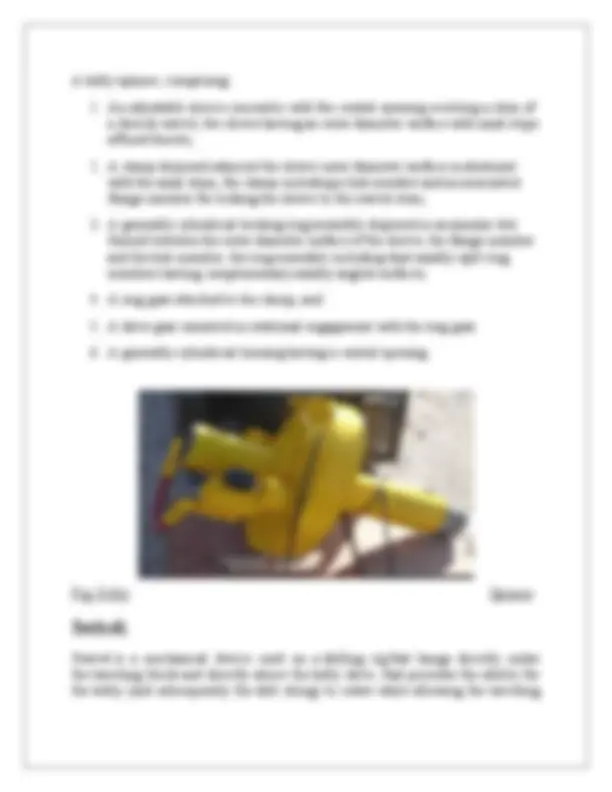
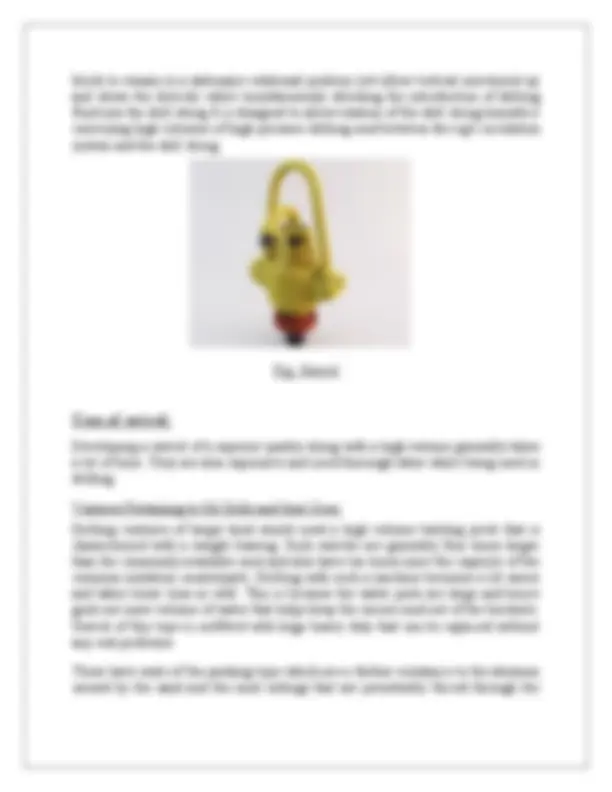
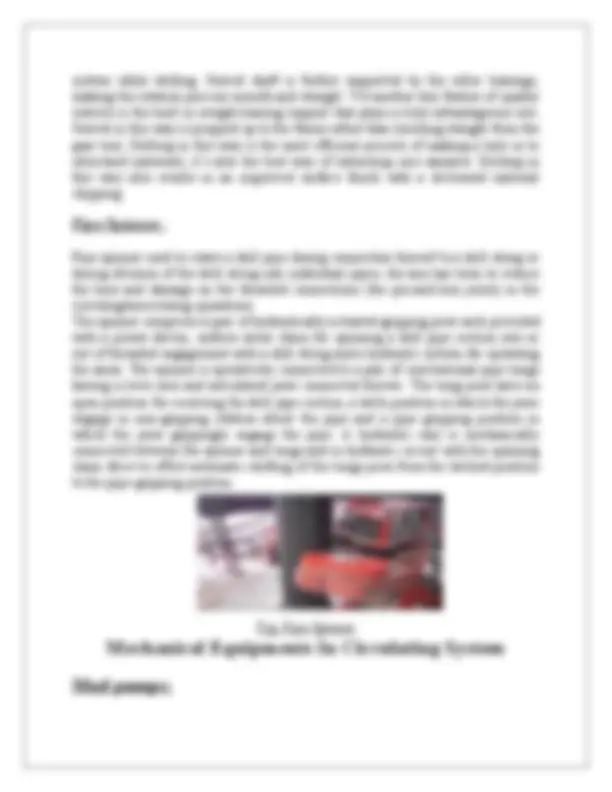
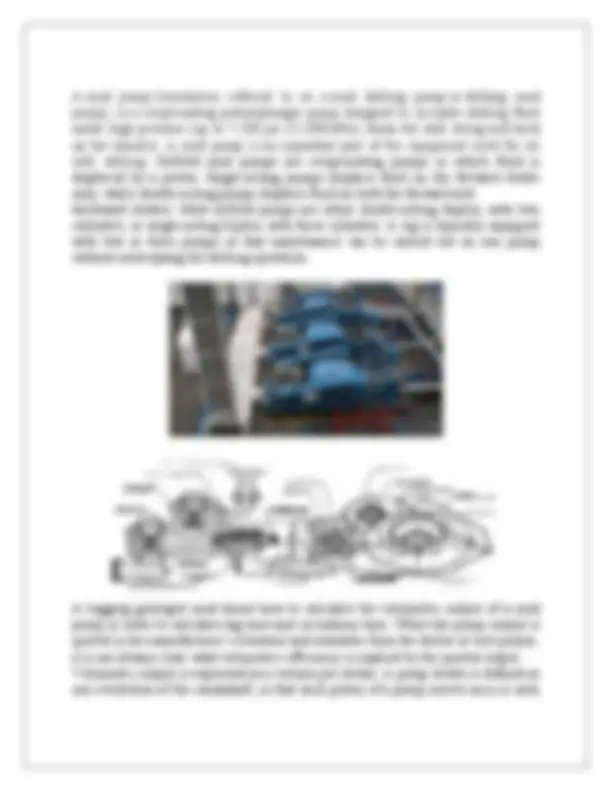
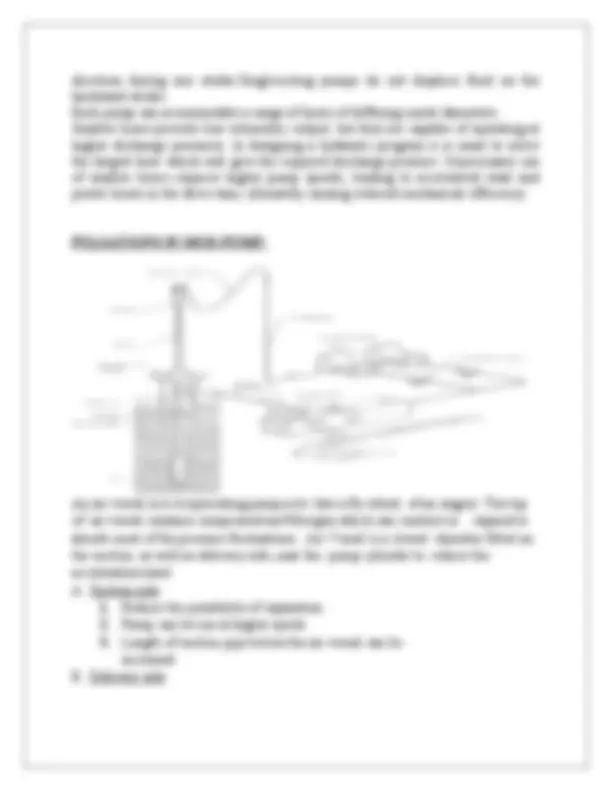
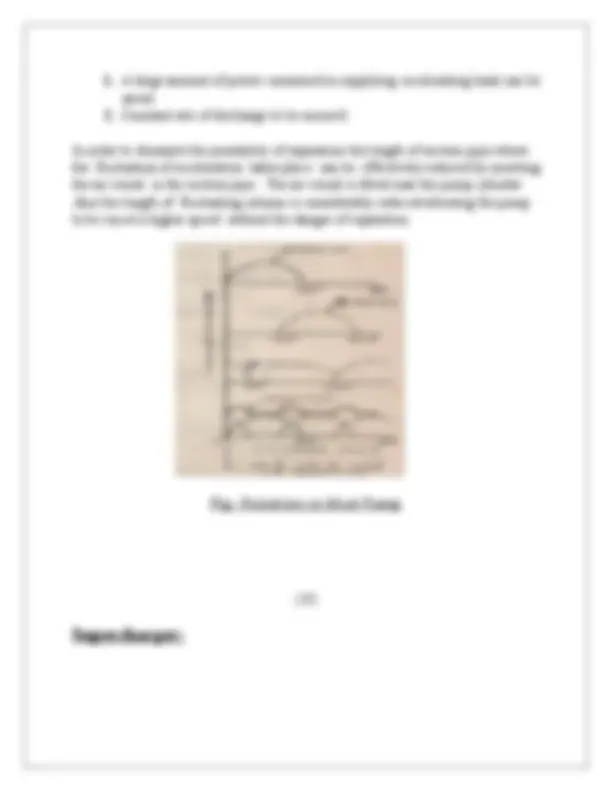
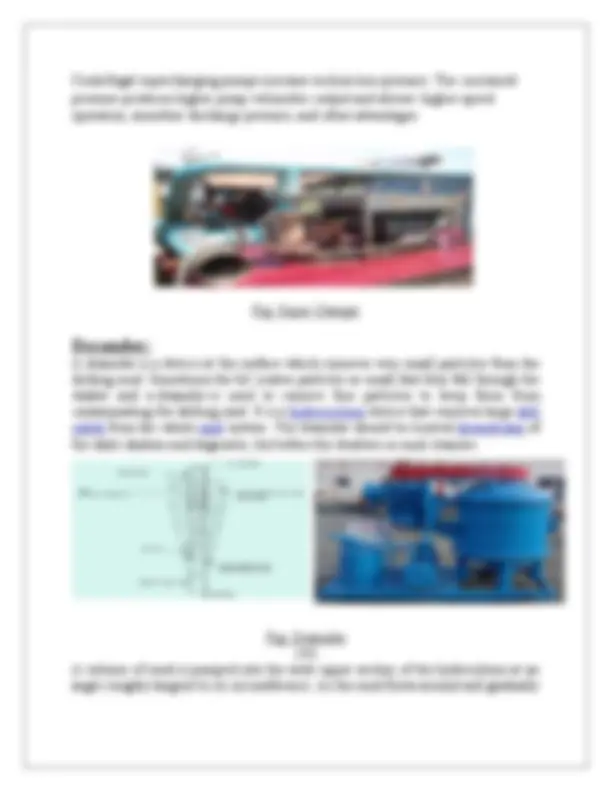
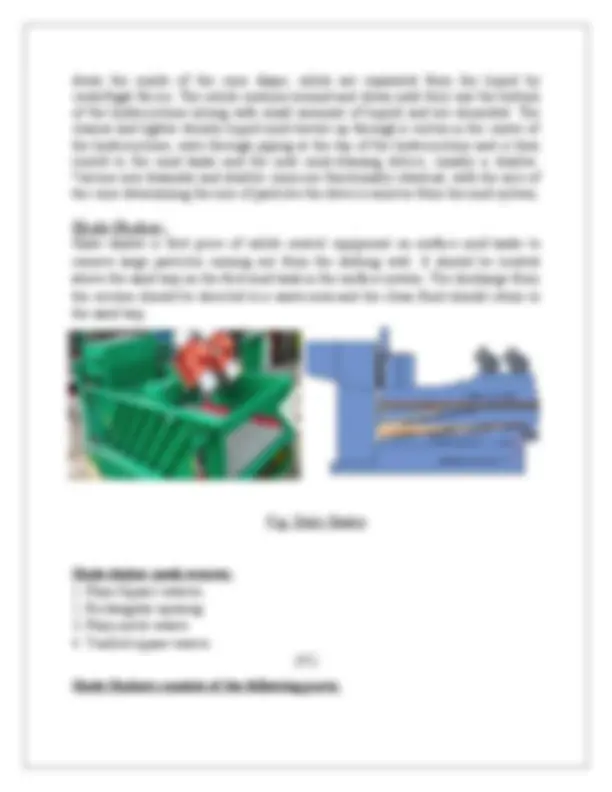
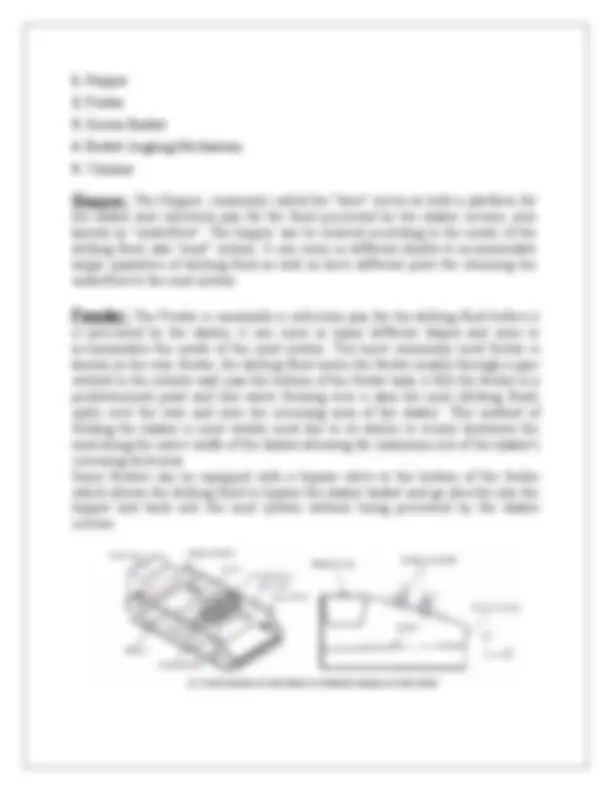
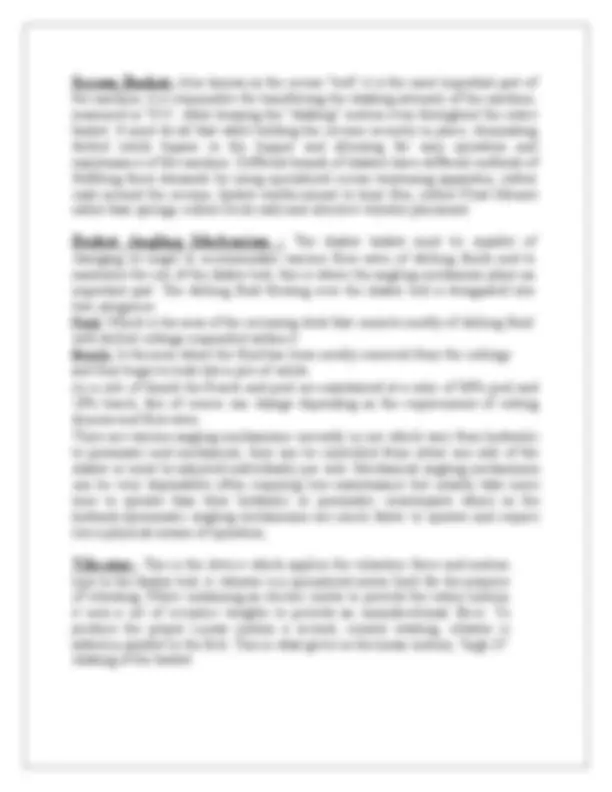
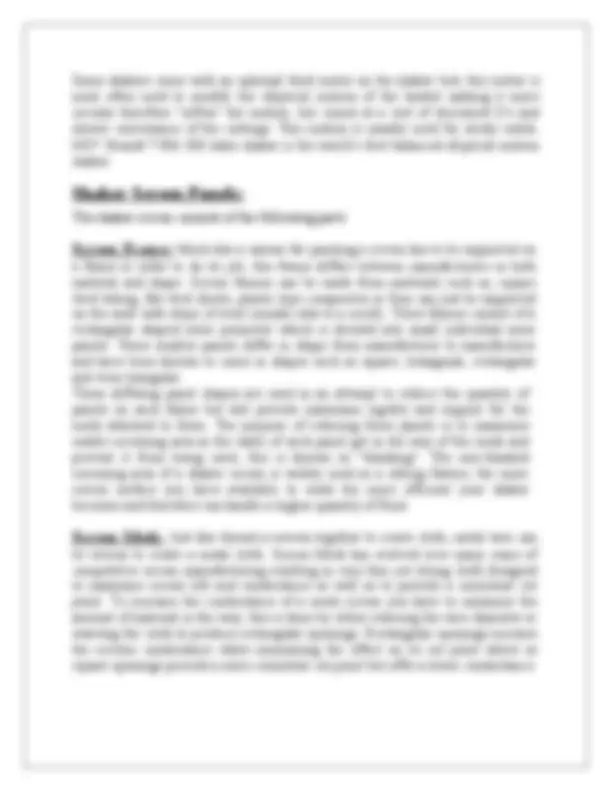
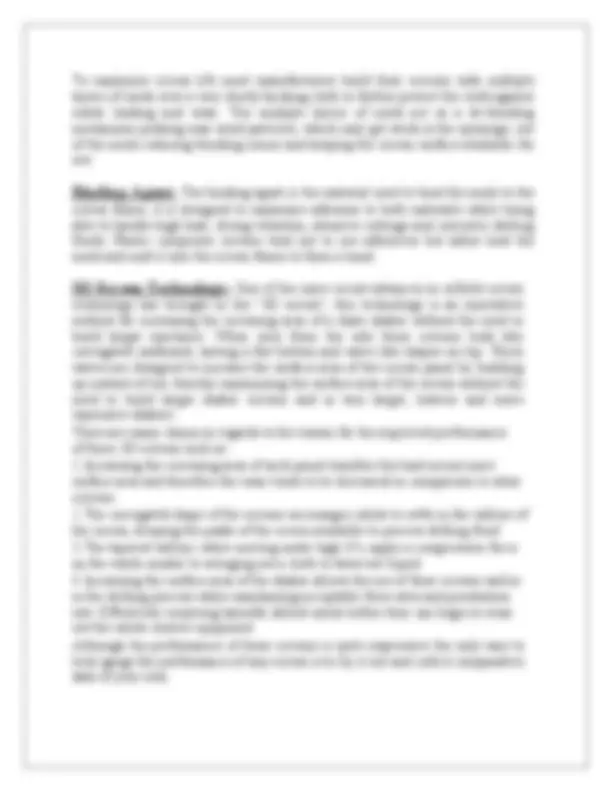
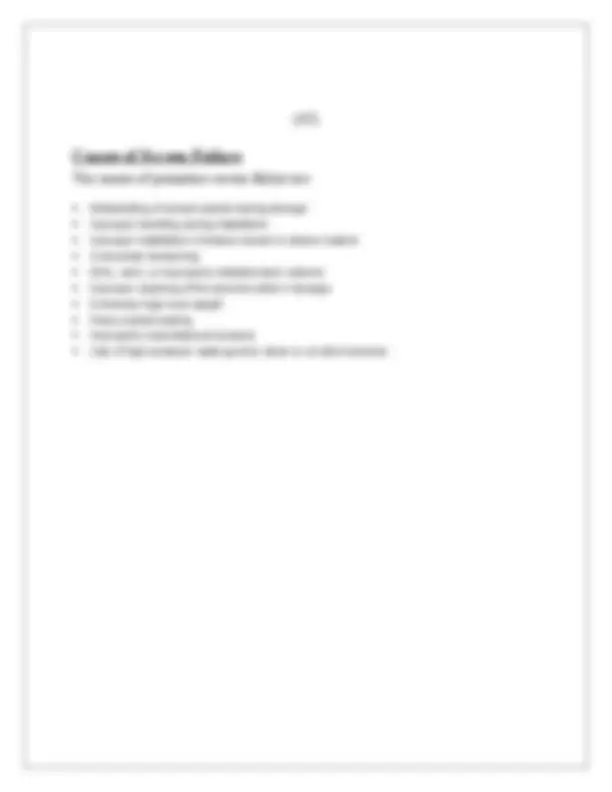
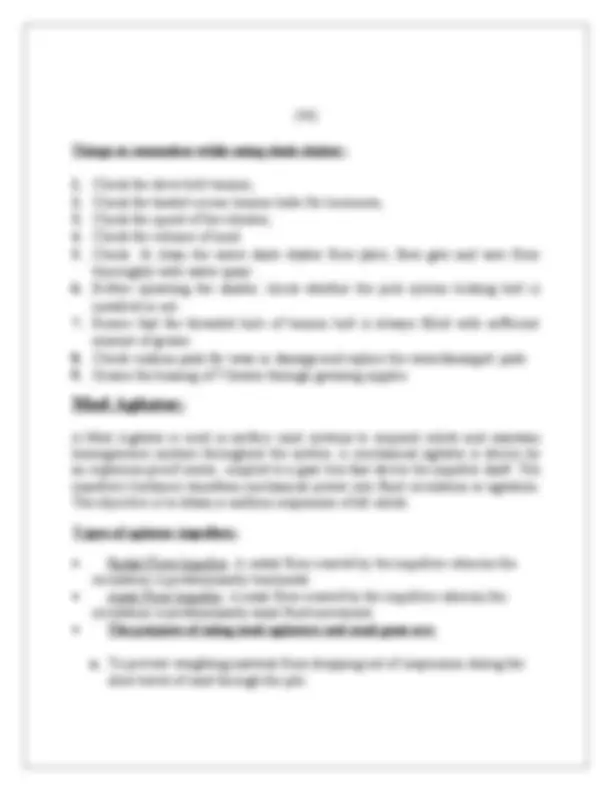
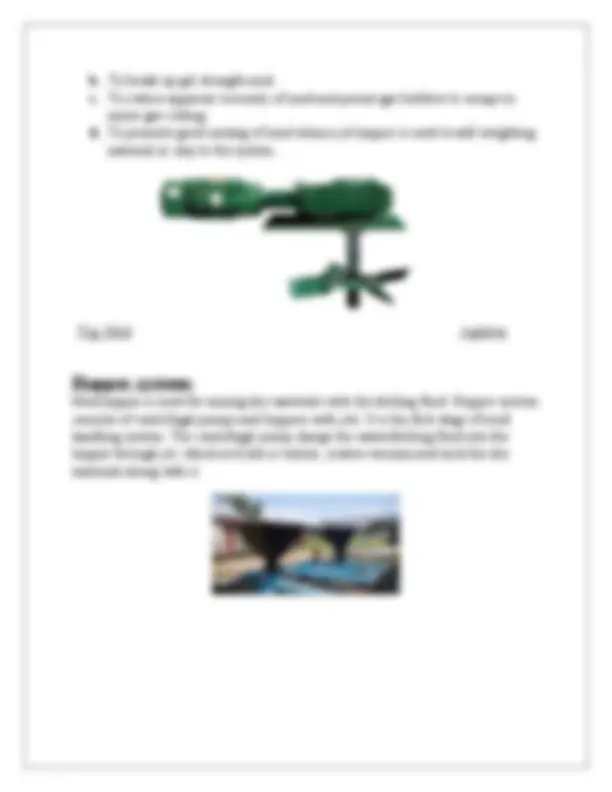
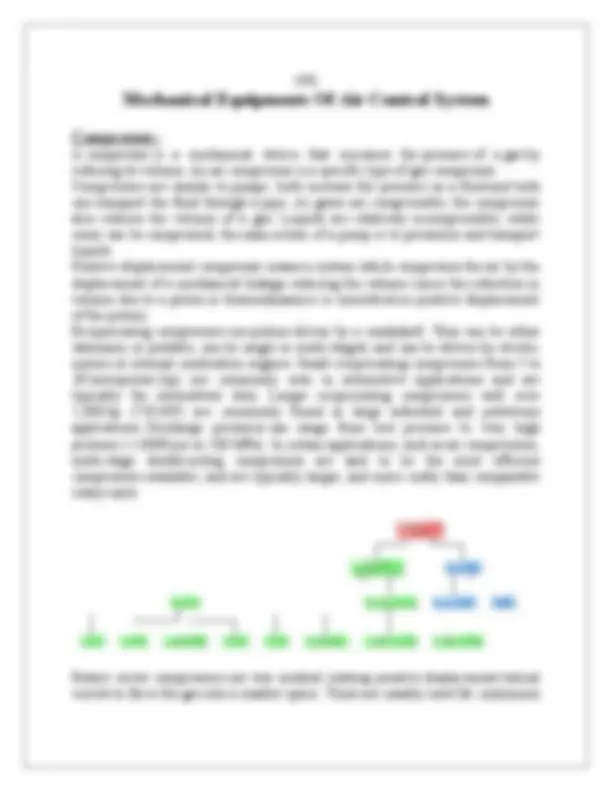
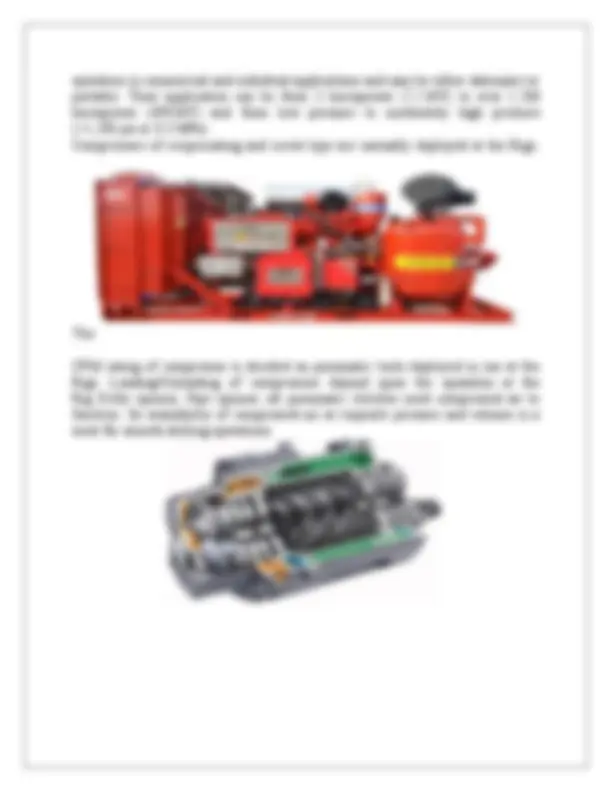
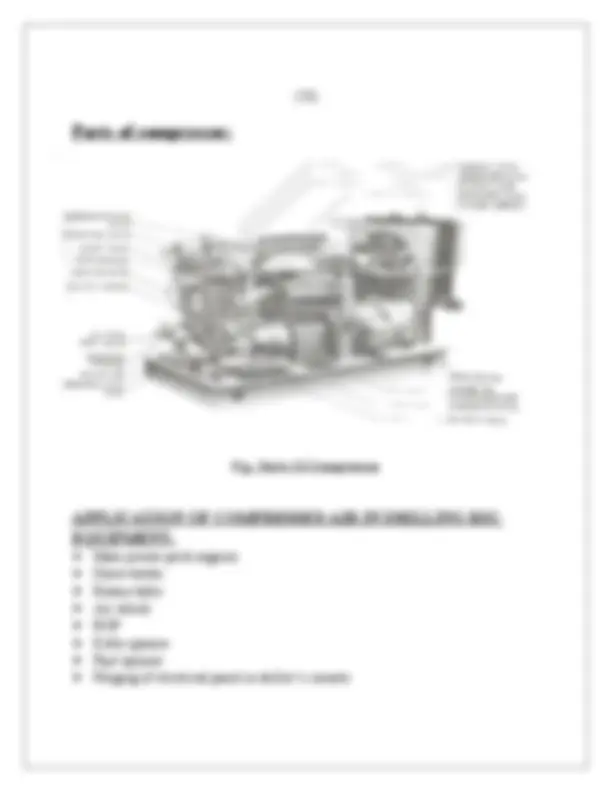

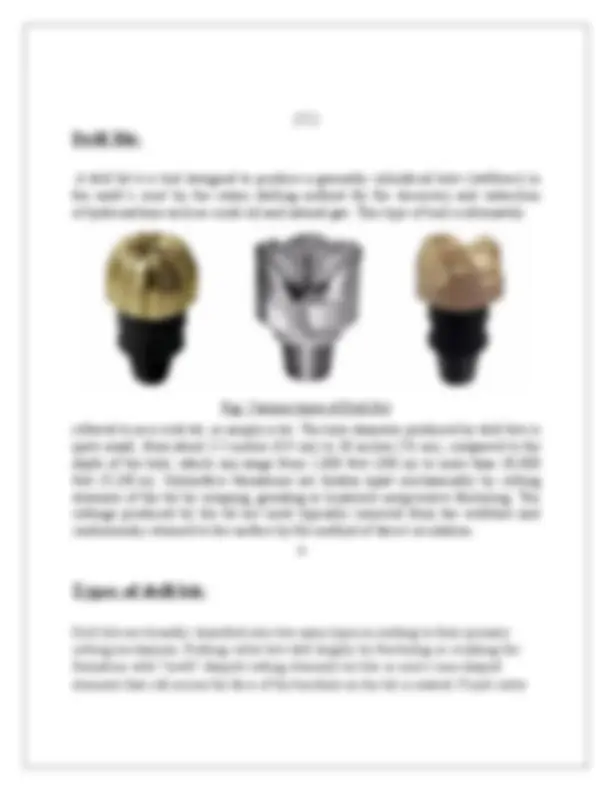

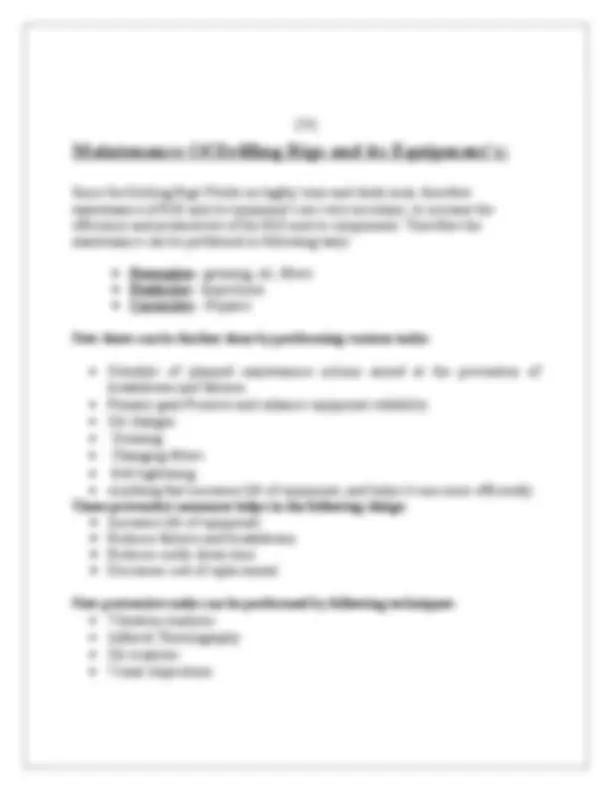
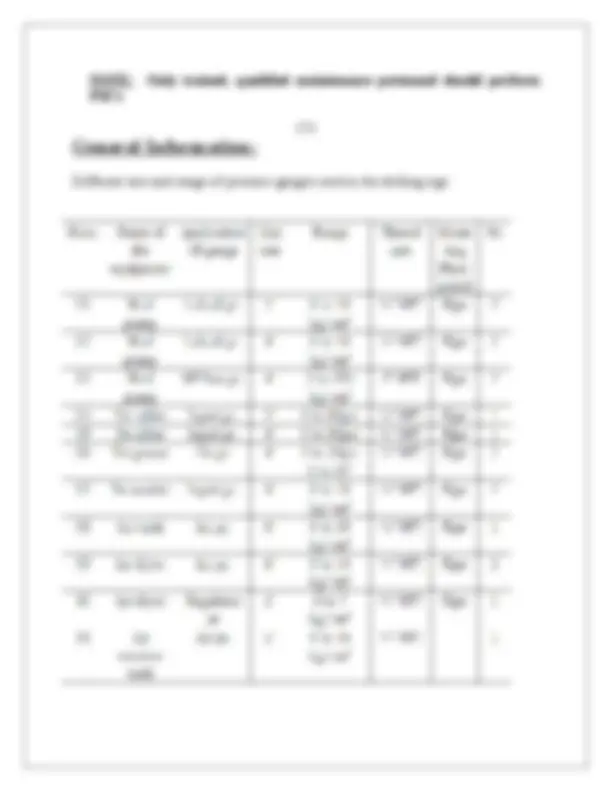
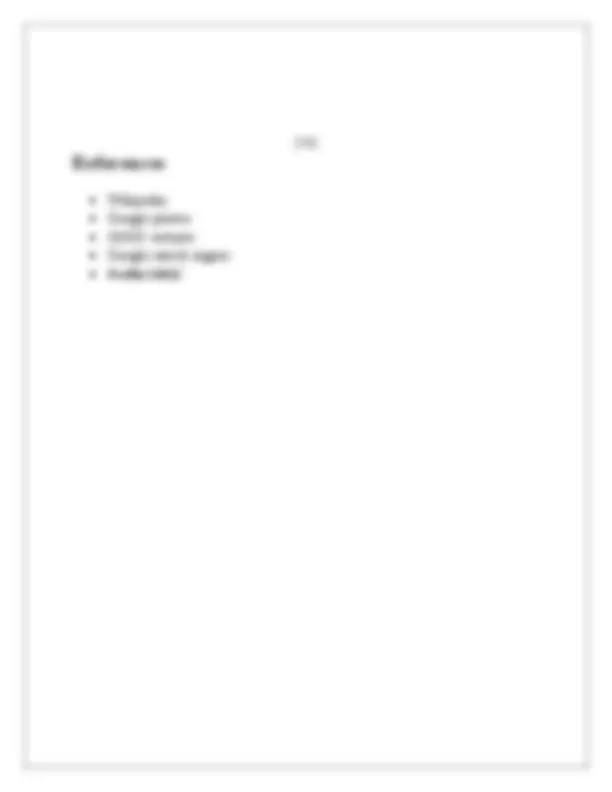
Study with the several resources on Docsity
Earn points by helping other students or get them with a premium plan
Prepare for your exams
Study with the several resources on Docsity
Earn points to download
Earn points by helping other students or get them with a premium plan
Community
Ask the community for help and clear up your study doubts
Discover the best universities in your country according to Docsity users
Free resources
Download our free guides on studying techniques, anxiety management strategies, and thesis advice from Docsity tutors
A comprehensive overview of drilling rigs, covering their history, classification, and the various mechanical equipment and systems that make up a drilling rig. It delves into the power system, rotary system, and circulating system, including detailed information on components such as the draw works, rotary table, mud pumps, and shale shakers. The document also discusses the drilling fluid and drill bits used in the drilling process. This in-depth coverage of the technical aspects of drilling rigs and their associated equipment makes this document a valuable resource for understanding the complex machinery and processes involved in oil and gas exploration and extraction.
Typology: Schemes and Mind Maps
1 / 64
This page cannot be seen from the preview
Don't miss anything!
Kartik Sharma Mr. Raju Kumar B.Tech(ME) Deputy General Manager Career Point University(Mechanical) Frontier Basin, ONGC Hamirpur,(H.P.) Dehradun(U.K.)
CERTIFICATE I hereby declare that the project work Drill Rig Equipment’s is an authentic record of my own my work carried out at FRONTIER BASIN ONGC Dehradun as requirements Internship Projects for the award of degree of B.tech , Career Point University Hamirpur, under the guidance of Mr. Raju Kumar during June to July
PREFACE This project is about all the Drilling and its Equipment’s which are used while using Drill Rig Machinery. It covers all the systems which are present in drilling rig. It covers all the information about drilling rig and a brief history of drilling rigs. It also covers some of the auxiliary elements present in drilling rigs such as drill bit and drilling fluid. It also includes how the drilling fluid is prepared and the chemical being added in the drilling fluid according to the need.
INDEX
equipment’s
Oil and Natural Gas Corporation Limited (ONGC) is an Indian multinational oil and gas company headquartered in Dehradun, Uttarakhan d, India. It is a Public Sector Undertaking (PSU) of the Government of India, under the administrative control of the Ministry of Petroleum and Natural Gas. It is India's largest oil and gas exploration and production company. It produces around 69% of India's crude oil (equivalent to around 30% of the country's total demand) and around 62% of its natural gas.On 31 March 2013, its market capitalization was INR 2.6 trillion (US$48.98 billion), making it India's second largest publicly traded company. In a government survey for FY 2011–12, it was ranked as the largest profit making PSU in India. ONGC has been ranked 357th in the Fortune Global 500 list of the world's biggest corporations for the year 2012. Figure 1: ONGC Building in Dehradun GEOPIC
ONGC was founded on 14 August 1956 by Government of India, which currently holds a 68.94% equity stake. It is involved in exploring for and exploiting hydrocarbons in 26 sedimentary basins of India, and owns and operates over 11,000 kilometers of pipelines in the country. Its international subsidiary ONGC Videsh currently has projects in 17 countries. ONGC has discovered 6 of the 7 commercially producing Indian Basins, in the last 50 years, adding over 7. billion tonnes of In-place Oil & Gas volume of hydrocarbons in Indian basins. Against a global decline of production from matured fields, ONGC has maintained production from its brownfields like Mumbai High, with the help of aggressive investments in various IOR (Improved Oil Recovery) and EOR (Enhanced Oil Recovery) schemes. ONGC has many matured fields with a current recovery factor of 25–33%.Its Reserve Replacement Ratio for between 2005 and 2013, has been more than one. During FY 2012–13, ONGC had to share the highest ever under- recovery of INR 494.2 million (an increase of INR 49.6 million over the previous financial year) towards the under-recoveries of Oil Marketing Companies (IOC, BPCL and HPCL). On 1 November 2017, the Union Cabinet approved ONGC for acquiring majority 51.11 % stake in HPCL (Hindustan Petroleum Corporation Limited). On Jan 30th 2018, Oil & Natural Gas Corporation acquired the entire 51.11% stake of GOI.Maharatna ONGC is the largest crude oil and natural gas Company in India, contributing around 70 per cent to Indian domestic production. Crude oil is the raw material used by downstream companies like IOC, BPCL, and HPCL to produce petroleum products like Petrol, Diesel, Kerosene, Naphtha, and Cooking Gas-LPG. This largest natural gas company ranks 11th among global energy majors (Platts). It is the only public sector Indian company to feature in Fortune’s ‘Most Admired Energy Companies’ list. ONGC ranks 18th in ‘Oil and Gas operations’ and 183rd overall in Forbes Global 2000. Acclaimed for its Corporate Governance practices, Transparency International has ranked ONGC 26th among the biggest publicly traded global giants. ONGC has a unique distinction of being a company with in-house service capabilities in all areas of Exploration and Production of oil & gas and related oil- field services. Winner of the Best Employer award, this public sector enterprise has a dedicated team of over 33,500 professionals who toil round the clock in
Fig: Frontier basin. (4)
Topographically and tectonically complex Foothills have already been mapped geologically and also have been covered by ground gravity-magnetic & aeromagnetic and 2D seismic surveys. ONGC's first well, Jwalamukhi#1, was drilled in 1957. Till date twenty two exploratory and nine structural wells have been drilled in the basin. Presence of gas sands in Lower Siwalik (Jwalamukhi area) and Lower Dharamshala (Balh area) are major exploration leads. In recent past, two areas, Nahan-Solan and Kangra-Mandi were under active exploration. In Nahan-Solan area, Subathu Formation, the envisaged source rock, was encountered in subsurface for the first time in well Kasauli-1. At present, exploration efforts have been focussed in Kangra-Mandi nomination PEL. Achieving a horizontal drift of 1942 m with a maximum inclination of 44° in well Jwalamukhi-9 was a unique feat in this tectonically complex regime, so also the special processing of vintage 2D seismic data by M/s TBI, Canada. An exploratory location is available to probe the seismic anomaly within Lower Siwalik in Jwalamukhi area.
Fig: Himalayan Basin.
Ganga Basin is a wide, relief-less alluvium covered tract, occupying major part of Indo-Gangetic plain in the northern Indian states of Uttarakhand, Uttar Pradesh and Bihar, encompassing an area of approx. 3,00,000 Sq. Km. The basin is bound in north by Himalayan Frontal Thrust (HFT) and Delhi Aravali-ridge, in south by Bundelkhand Massif and Vindhyan Basin, in west by The Great Boundary Fault (GBF) and in east by Munger-Sahrsa subsurface ridge. From west to east, the basin is divided into four sub-basins namely, Sahaspur, Sarda, Gandak and Madhubani depressions separated by ridges. Geological, Gravity-Magnetic, 2D & 3D Seismic surveys and surface geochemical surveys have been carried out in the basin besides drilling of 16 exploratory and four structural wells. Although, some wells have given hydrocarbon indications, commercial discovery is yet to be realized.
Further, three more locations in Jabera area are also available.In Chambal Valley, NELP V block VN-ONN-2003/1 was relinquished after drilling well Palaita- down to the basement. Well Chechat-1 in NELP VI block VN-ONN-2004/ indicated presence of minor gas at Suket level, in Lower Vindhyan during production testing. Well Suket-1 in the NELP VI block VN-ONN-2004/2 is under drilling. Few prospects have been identified based on recently concluded integrated interpretation of all the available geo-scientific data. Fig: Vindhyan Basin
A drilling rig is a machine that creates holes in the earth sub-surface. Drilling rigs can be massive structures housing equipment used to drill water wells, oil wells, or natural gas extraction wells, or they can be small enough to be moved manually by one person and are called augers. Drilling rigs can sample sub-surface mineral deposits, test rock, soil and groundwater physical properties, and also can be used to install sub-surface fabrications, such as underground utilities, instrumentation, tunnels or wells. Drilling rigs can be mobile equipment mounted on trucks, tracks or trailers, or more permanent land or marine-based structures (such as oil platforms, commonly called 'offshore oil rigs' even if they don't contain a drilling rig). The term "rig" therefore generally refers to the complex of equipment that is used to penetrate the surface of the Earth's crust.
Small to medium-sized drilling rigs are mobile, such as those used in mineral exploration drilling, blast-hole, water wells and environmental investigations. Larger rigs are capable of drilling through thousands of meters of the Earth's crust, using large "mud pumps" to circulate drilling mud (slurry) through the drill bit and up the casing annulus, for cooling and removing the "cuttings" while a well is drilled. Hoists in the rig can lift hundreds of tons of pipe. Other equipment can force acid or sand into reservoirs to facilitate extraction of the oil or natural gas; and in remote locations there can be permanent living accommodation and catering for crews (which may be more than a hundred.
History Of Drilling RIG Until internal combustion engines were developed in the late 19th century, the main method for drilling rock was muscle power of man or animal. The drilling of wells for the manufacture of salt began by the Song Dynasty in China. The well had a particularly small mouth, "as small as a small bowl." Archaeological evidence of the drilling tools used in deep-well dwelling are kept and displayed in the Zigong Salt Industry Museum. According to Salt: A World History , a Qing Dynasty well, also located in Zigong, "continued down to 3,300 feet [1,000 m] making it at the time the deepest drilled well in the world. Mechanized versions of this system persisted until about 1970, using a cam to rapidly raise and drop what, by then, was a steel cable up to 3 mm In the 1970s, outside of the oil and gas industry, roller bits using mud circulation were replaced by the first pneumatic reciprocating piston Reverse Circulation (RC) drills, and became essentially obsolete for most shallow drilling, and are now only
circulate drilling mud(slurry) through the drill bit and up the casing annulus, for cooling and removing the "cuttings" while a well is drilled. Hoists in the rig can lift hundreds of tons of pipe. Other equipment can force acid or sand into reservoirs to facilitate extraction of the oil or natural gas; and in remote locations there can be permanent living accommodation and catering for crews (which may be more than a hundred). Marine rigs may operate thousands of miles distant from the supply base with infrequent crew rotation or cycle. (10) Fig: Drilling RIG and its Components
1. Mud tank 18. Swivel (May be replaced by a top drive) 2. Shale shakers 19. Kelly Drive
3. Suction line (mud pump) 20. Rotary Table 4. Mud pump 21. Drill Floor 5. Motor or power source 22. Bell Nipple 6. Hose 23. Blowout preventer (BOP) Annular type 7. Draw-works 24. Blowout preventer (BOP) Pipe ram & blind ram 8. Standpipe 25. Drill String 9. Kelly hose 26. Drill bit 10. Goose-neck 27. Casing head or Wellhead 11. Traveling block 28. Flow line 12. Drill line 13. Crown block 14. Derrick 15. Racking Board (Sometimes referred to as the Monkey Board) 16. Stand (of drill pipe) 17. Setback (floor) (11) DRILLING RIG CLASSIFICATION
Mechanical — the rig uses torque converters, clutches, and transmissions powered by its own engines, often diesel Electric — the major items of machinery are driven by electric motors, usually with power generated on-site using internal combustion engines Hydraulic — the rig primarily uses hydraulic power Pneumatic — the rig is primarily powered by pressurized air
Top drive — rotation and circulation is done at the top of the drill string, on a motor that moves in a track along the derrick. Sonic — uses primarily vibratory energy to advance the drill string Hammer — uses rotation and percussive force (see Down-the-hole drill)
Conventional — derrick is vertical Slant — derrick is slanted at a 45 degree angle to facilitate horizontal drilling. (13) DRILLING RIG SYSTEM Power system: Most drilling rigs are required to operate in remote locations where a power supply is not available. They must therefore have a method of generating the electrical power which is used to operate the systems mentioned above. The electrical power generators are driven by diesel powered internal combustion engines (prime movers). Electricity is then supplied to electric motors connected to the drawworks, rotary table and mud pumps. The rig may have, depending on its size
and capacity, up to 4 prime movers, delivering more than 3000 horsepower. Horsepower (HP) is an old, but still widely used, unit of power in the drilling industry. Older rigs used steam power and mechanical transmission systems but modern drilling rigs use electric transmission since it enables the driller to apply power more smoothly, thereby avoiding shock and vibration. The drawworks and the mud pumps are the major users of power on the rig, although they are not generally working at the same time.
Hoisting system: Hoisting system (as shown in fig.) is one of the main parts to actually doing the drilling job. Either drill pipe or casing will be lifted and lowered to drill and complete the well. It mainly composes of the derrick, tackle &block system and dead line anchor system. Tackles and block do the vertical movement to the pipe. People working on the derrick can help to safely place these pipes to the right position. The dead line anchor mainly helps the replacement of the drilling line when it was subjected to wearing.