
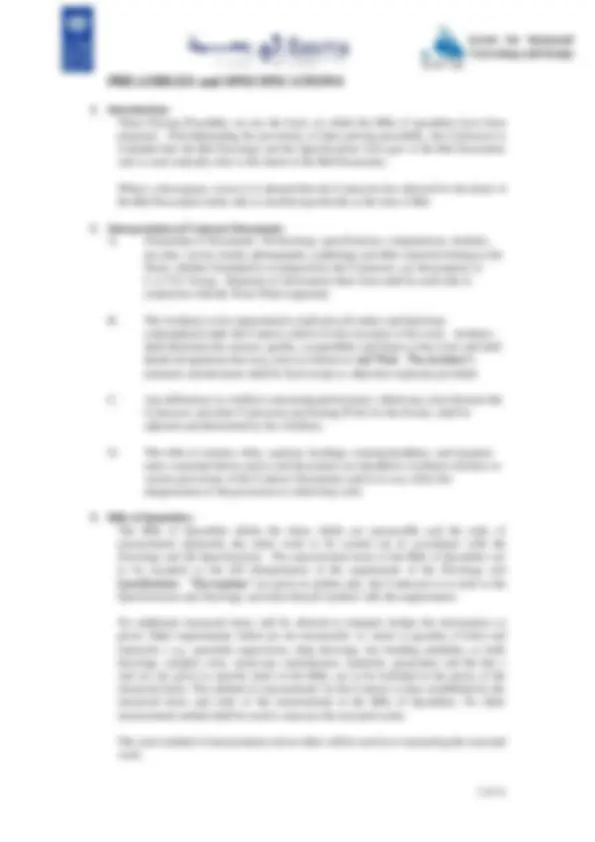
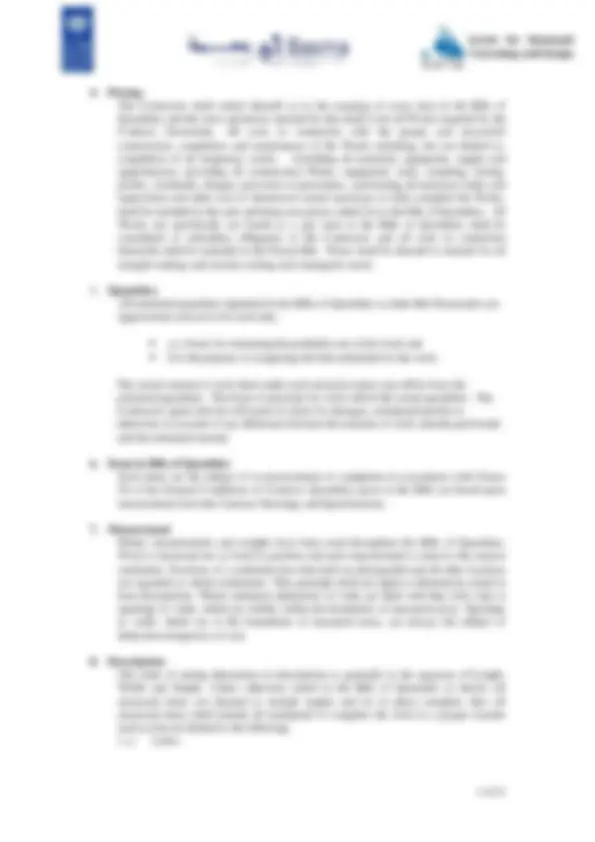
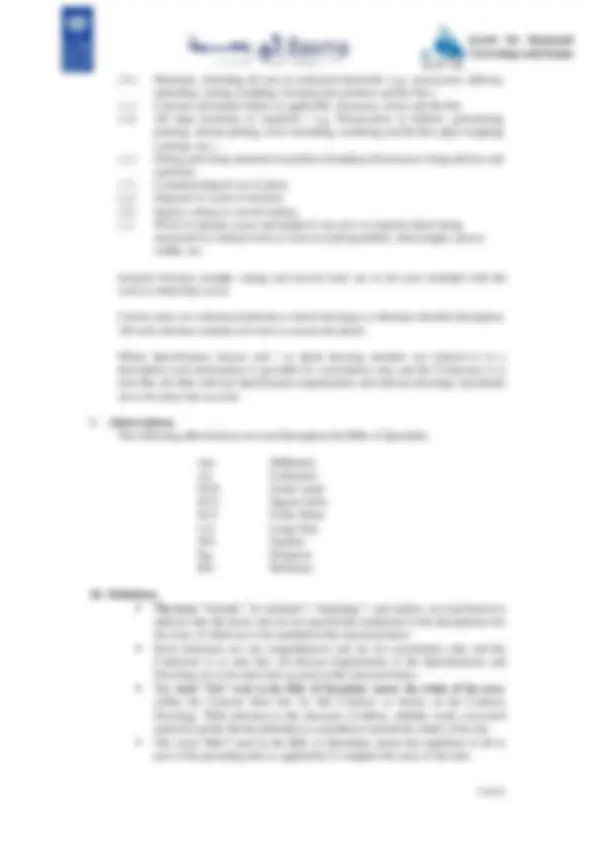
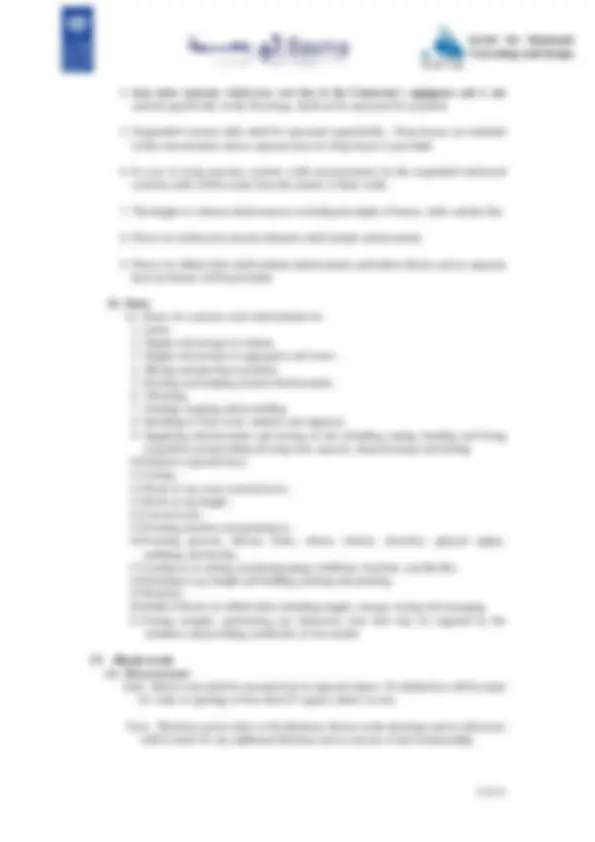
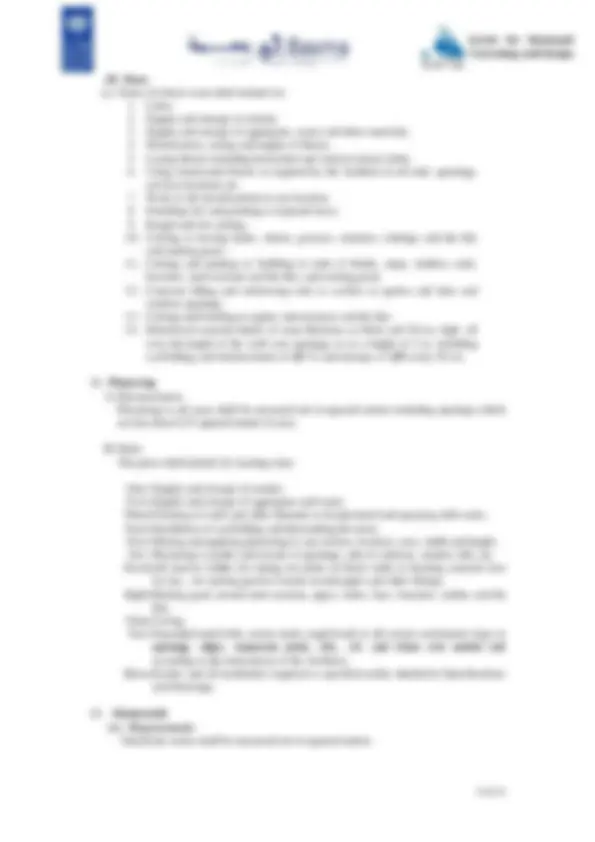
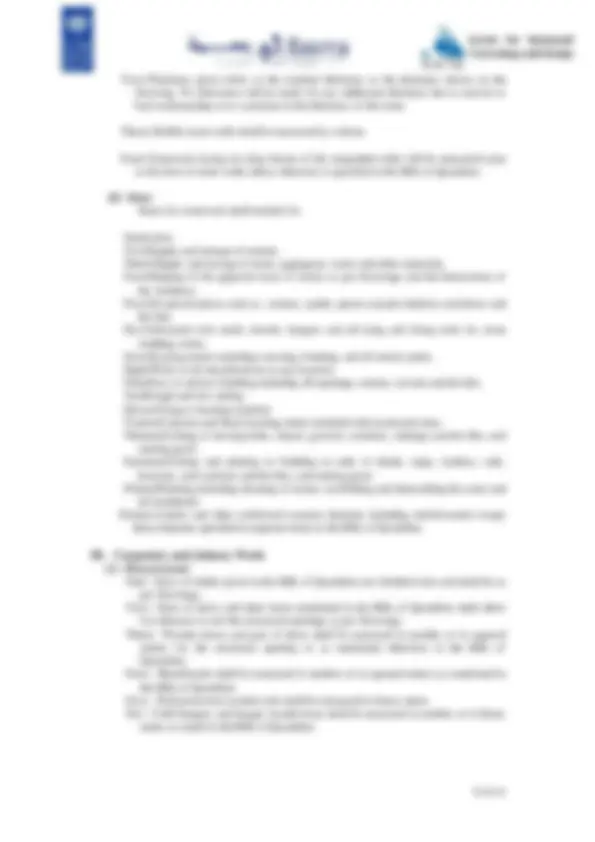
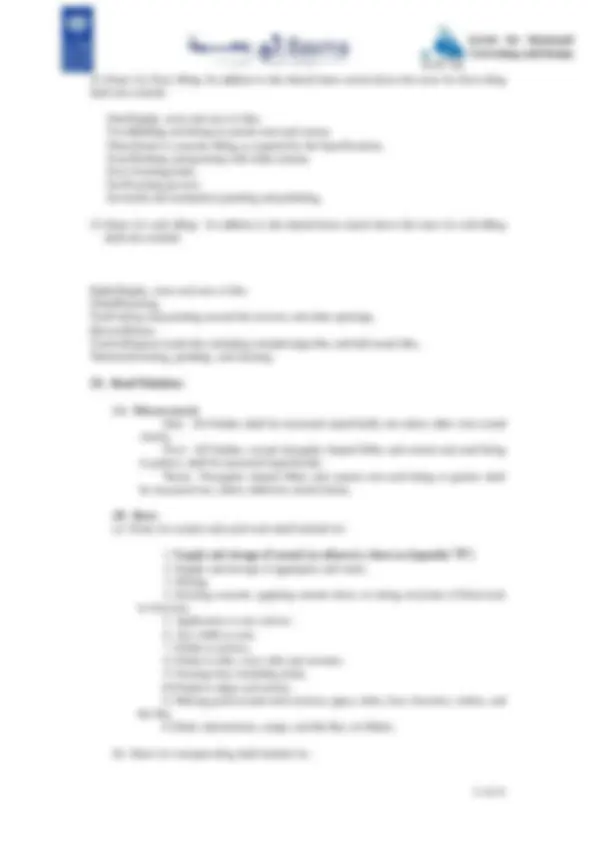
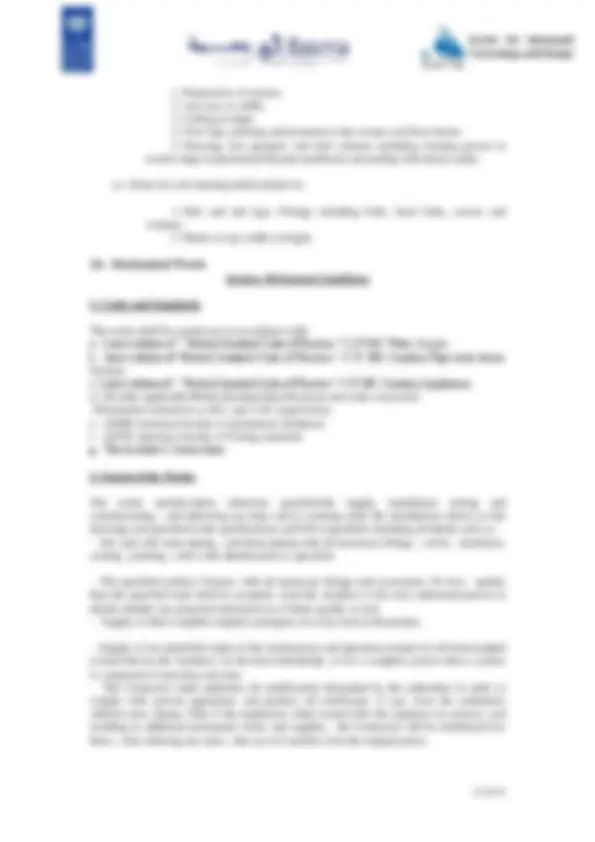
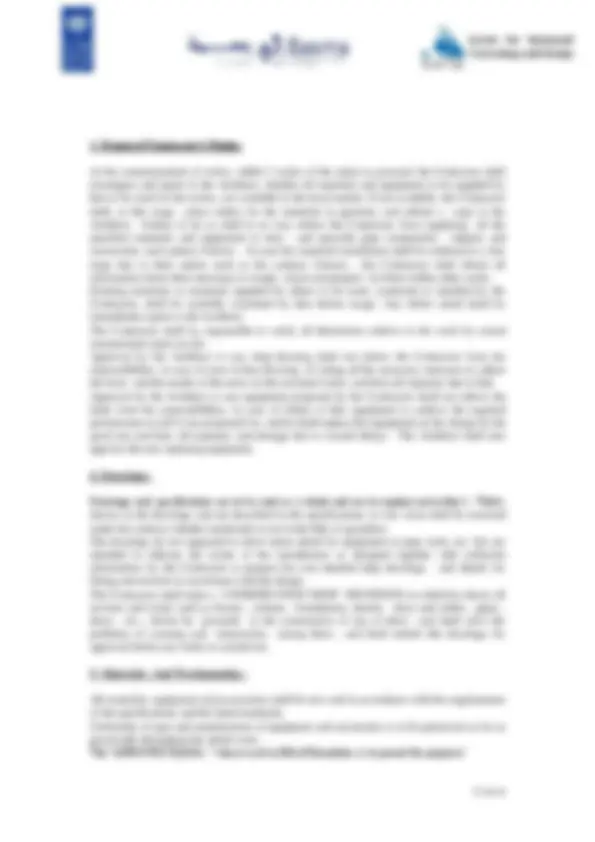

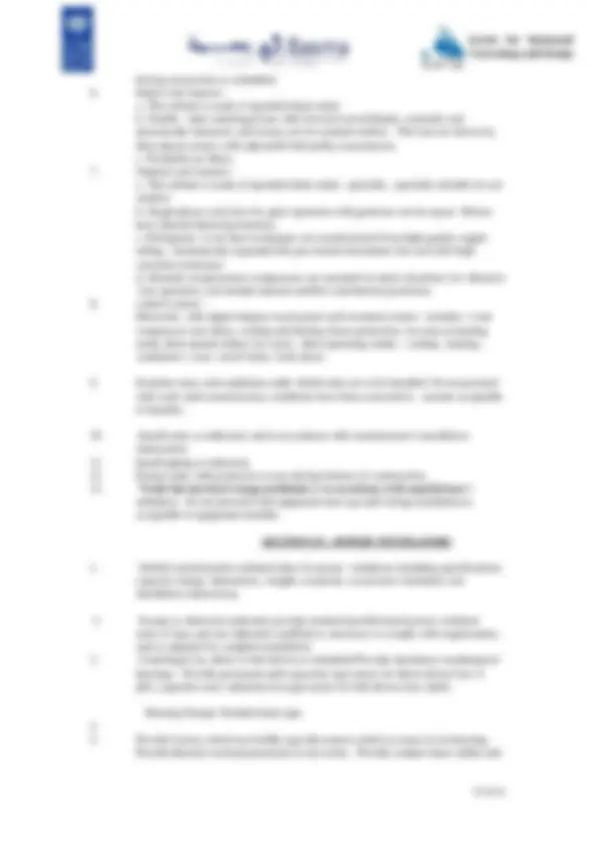
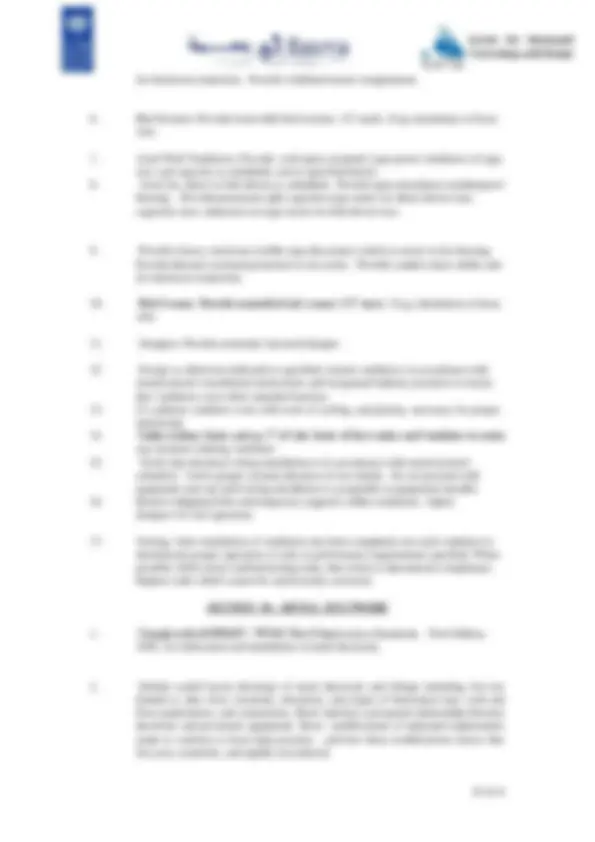
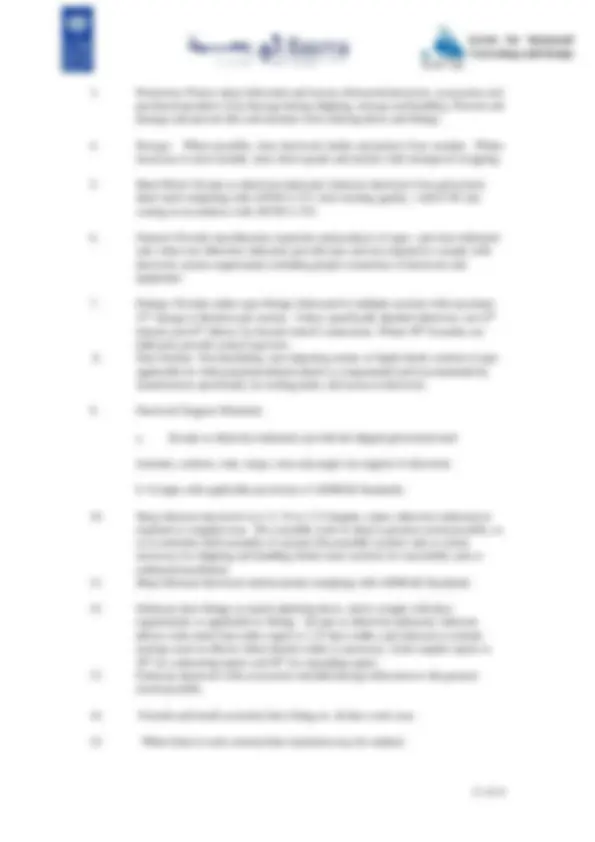
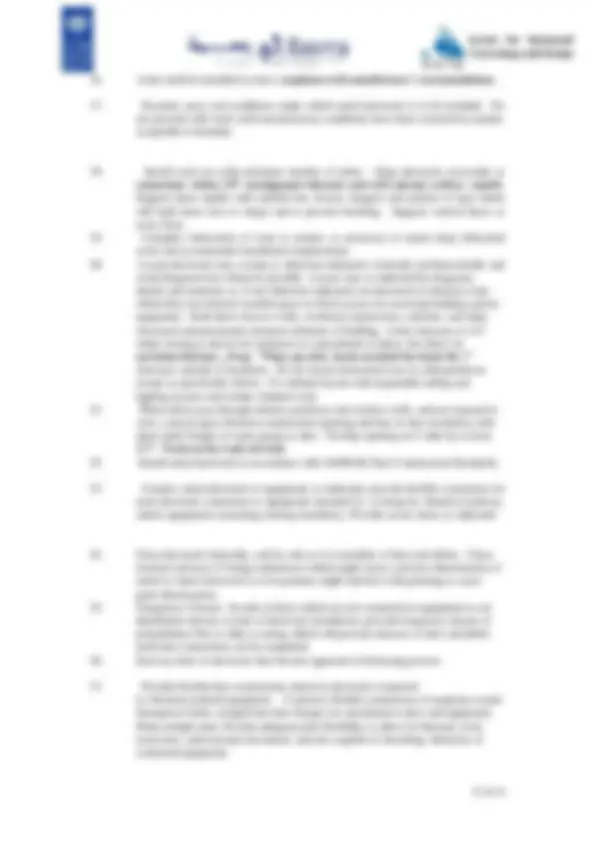
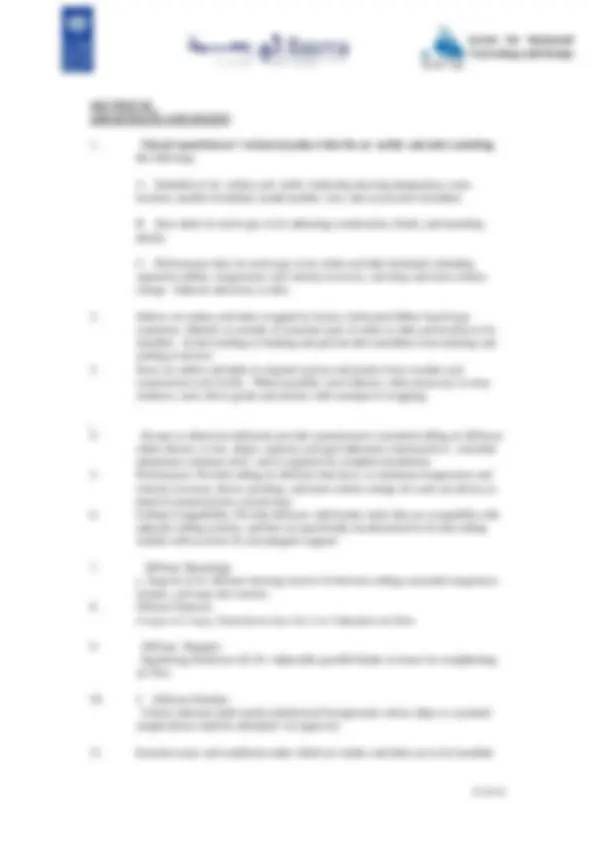

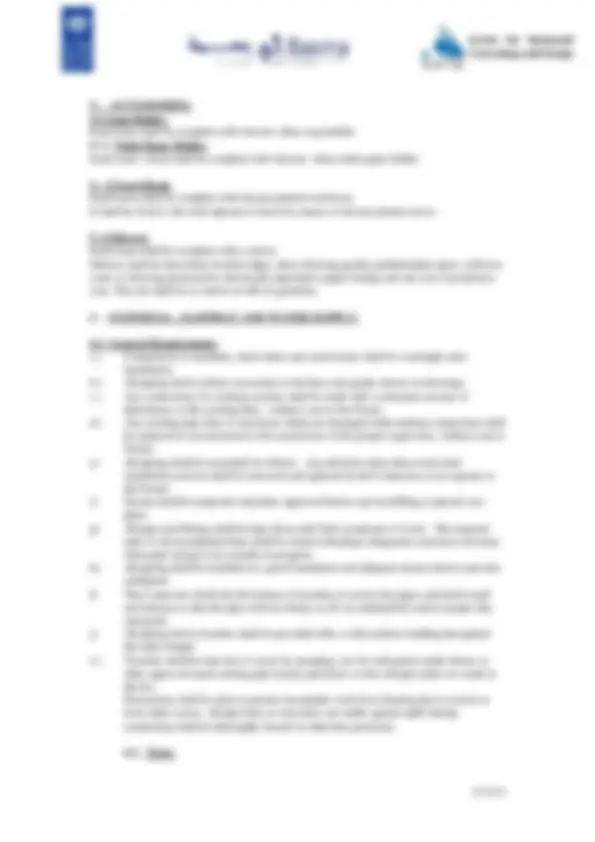
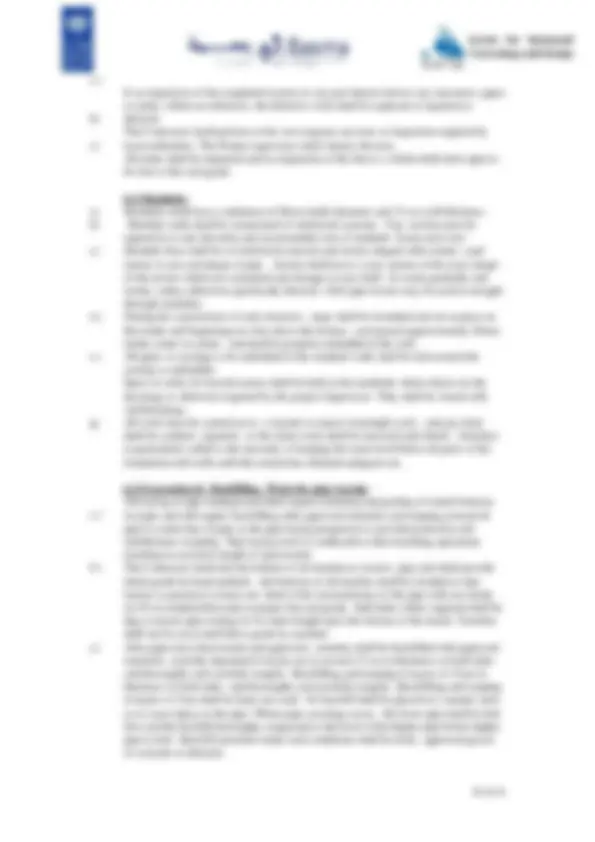
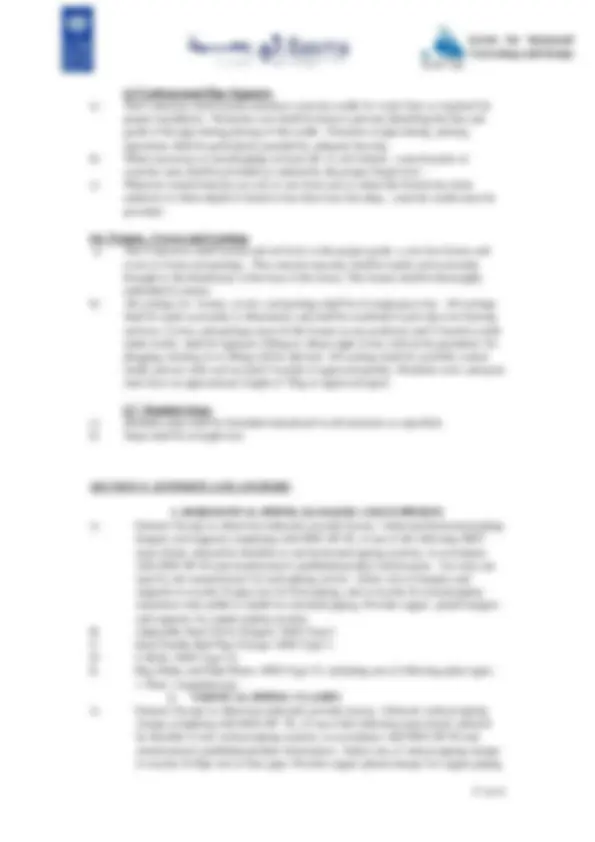
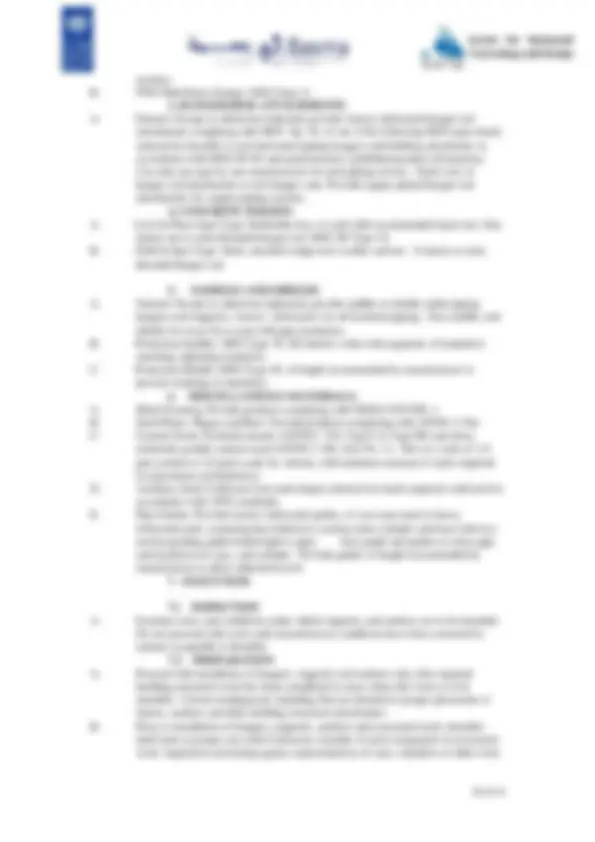
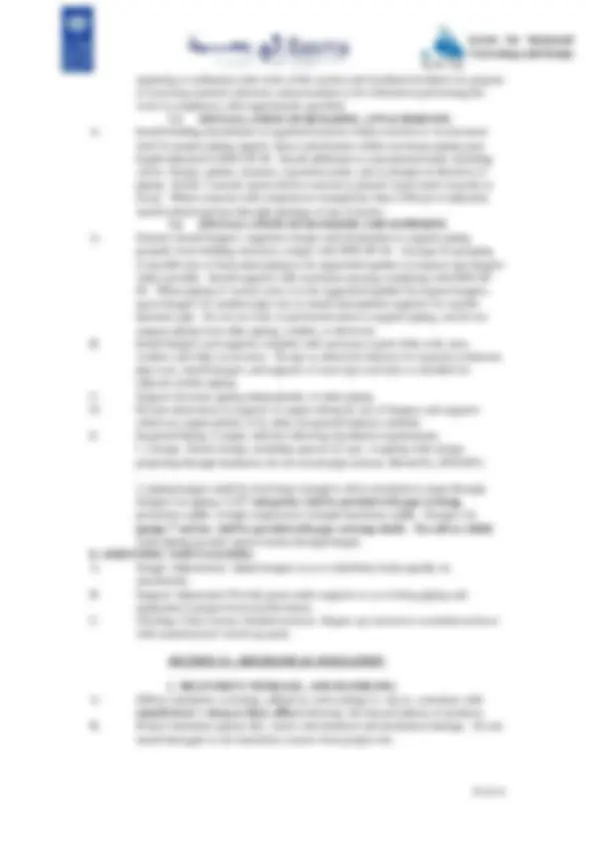
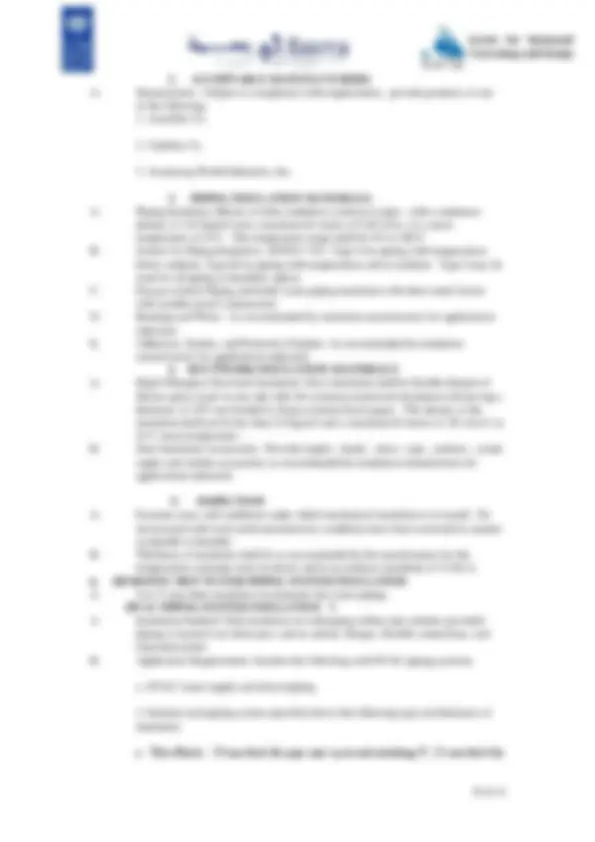
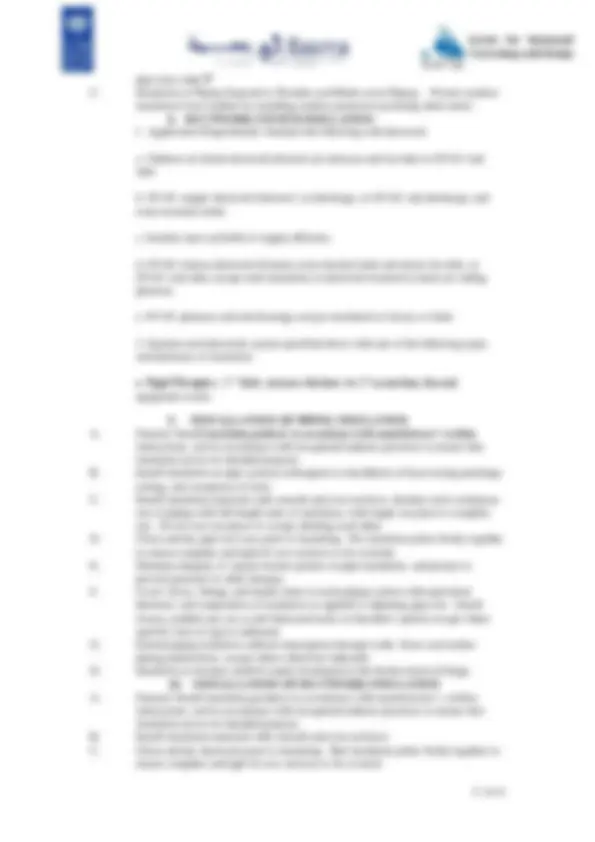
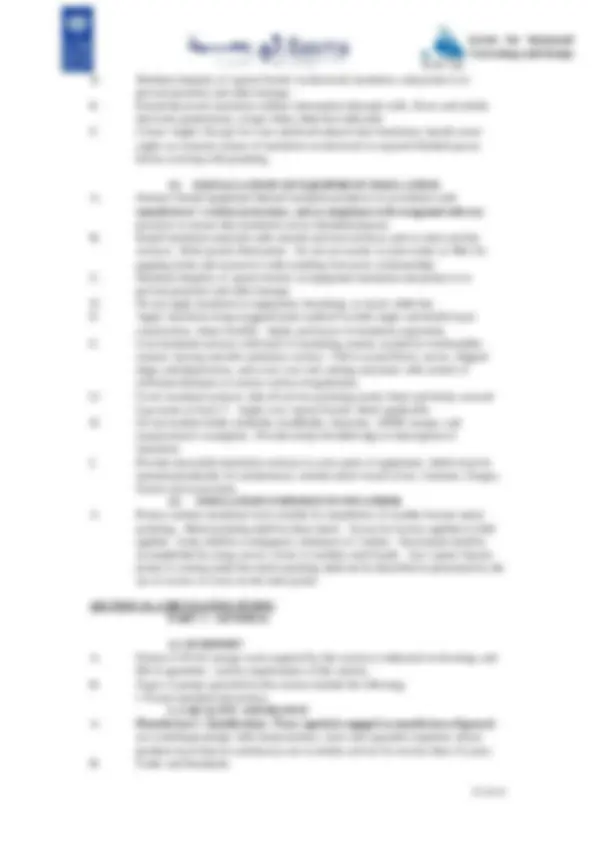
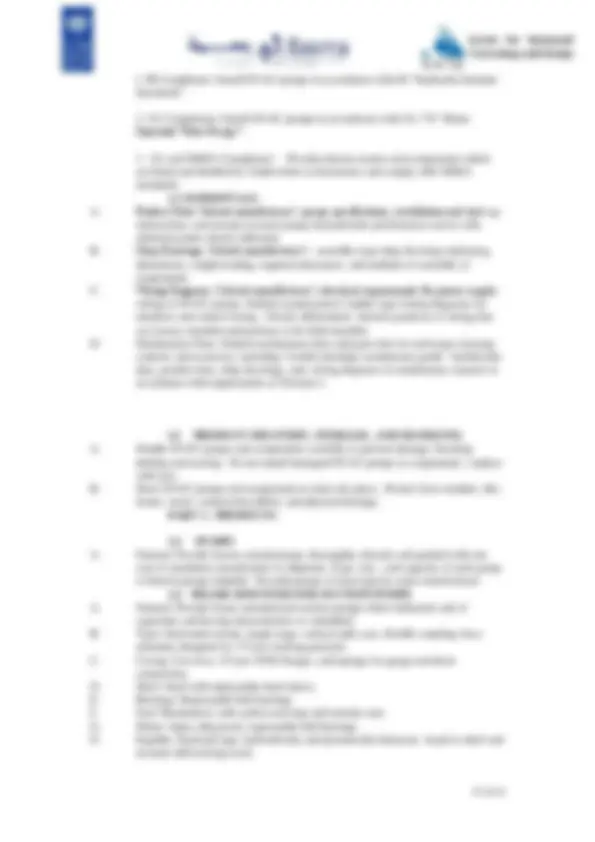
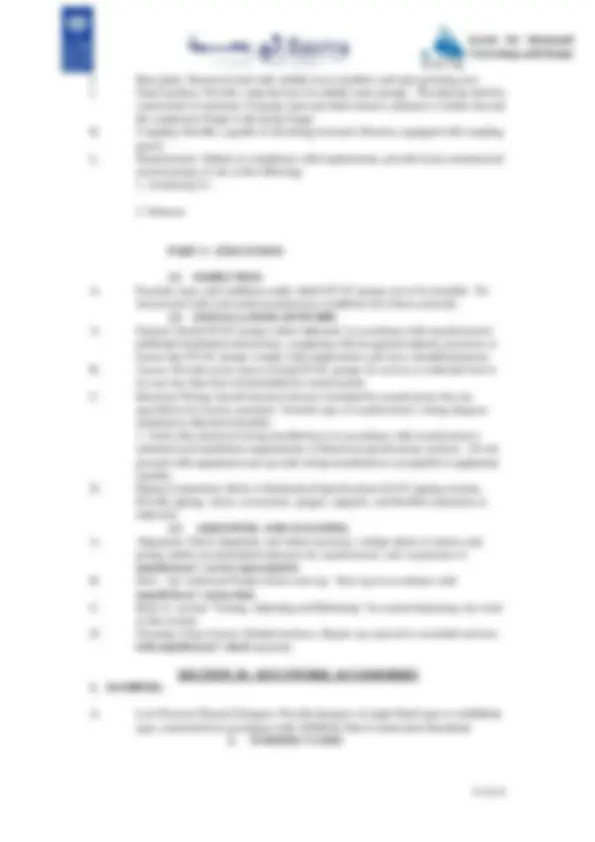
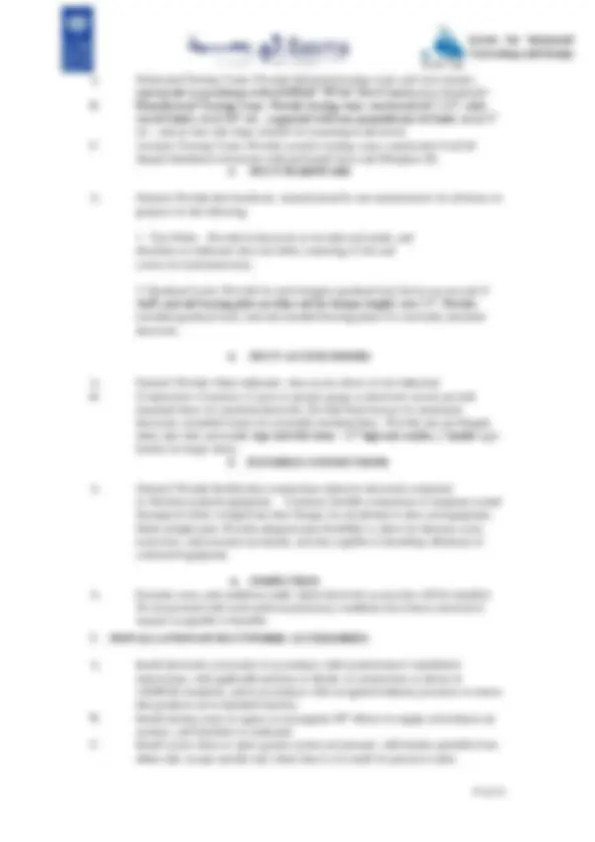
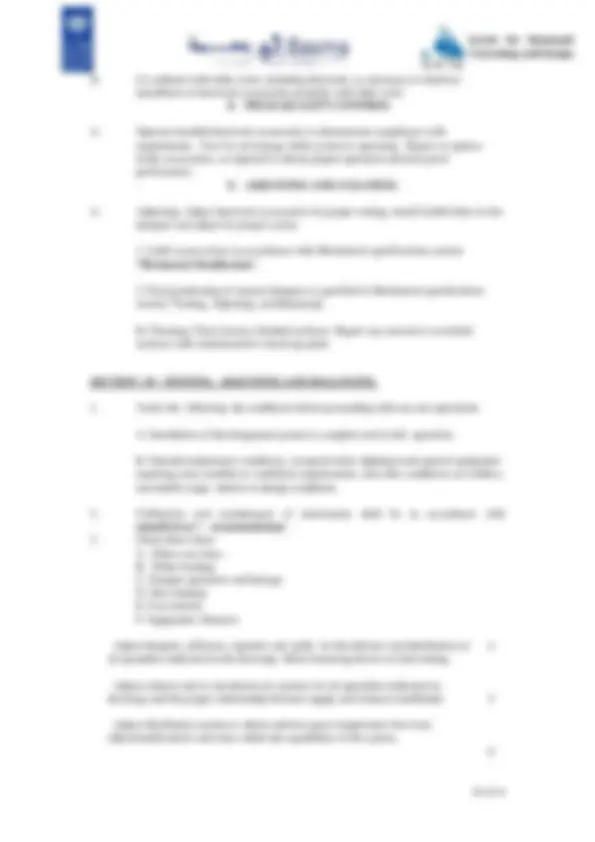
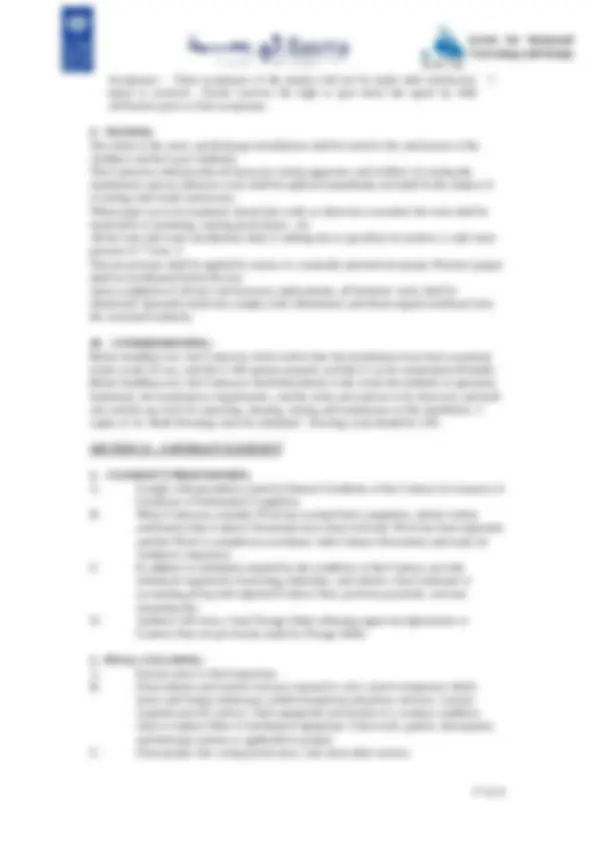
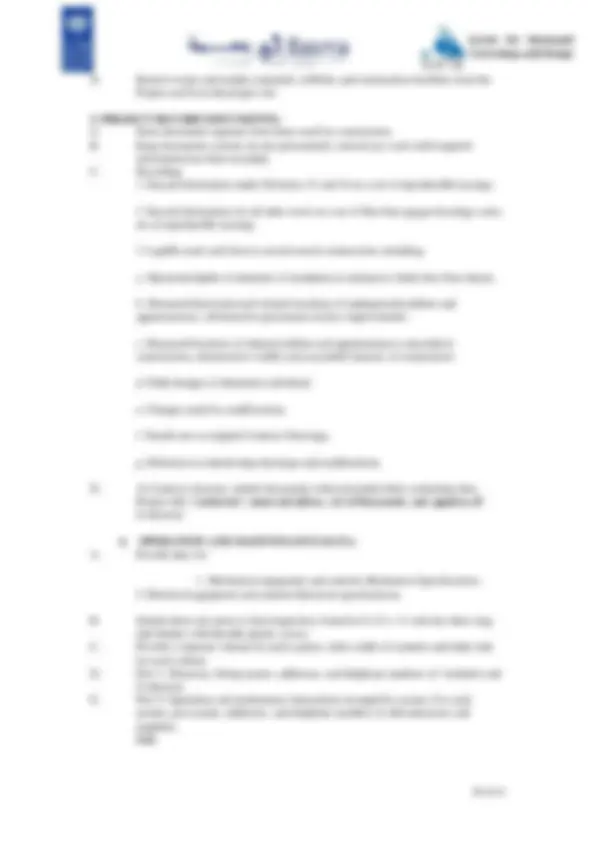
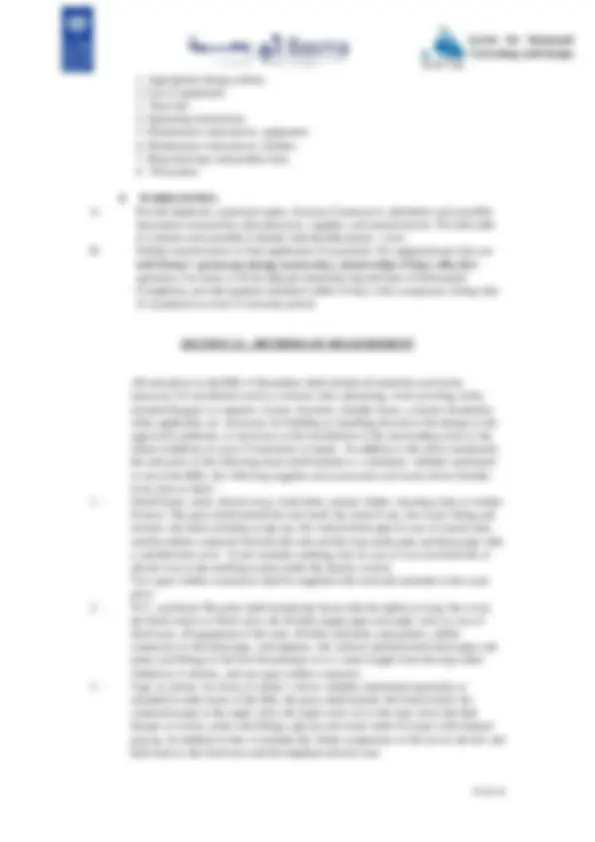
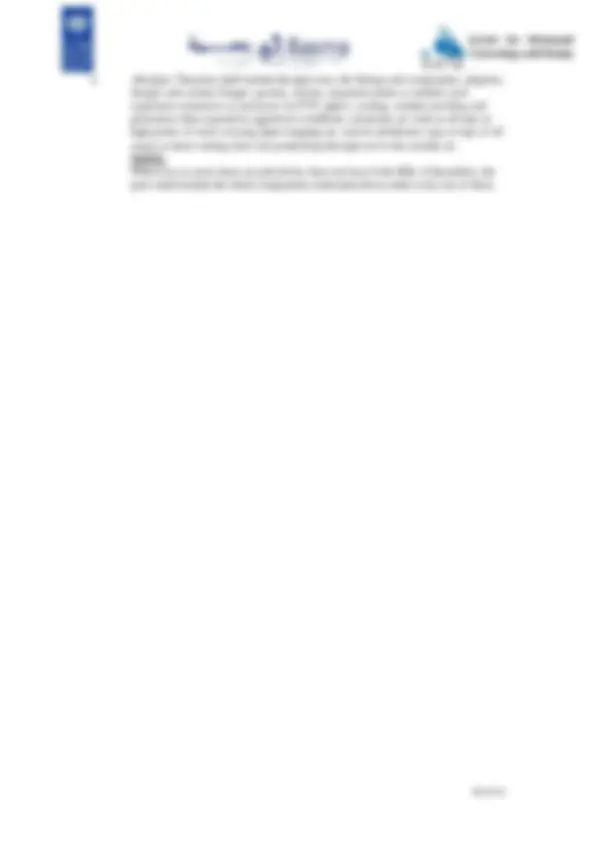
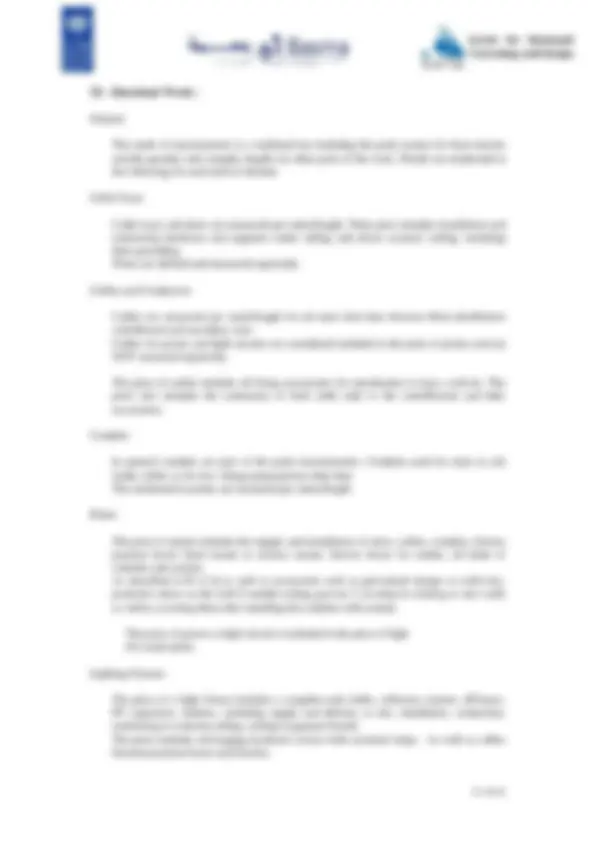
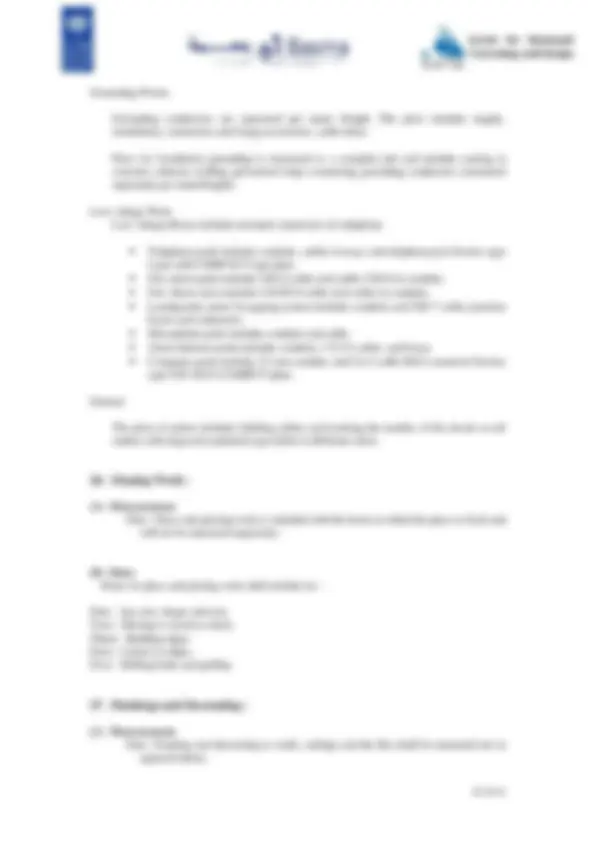
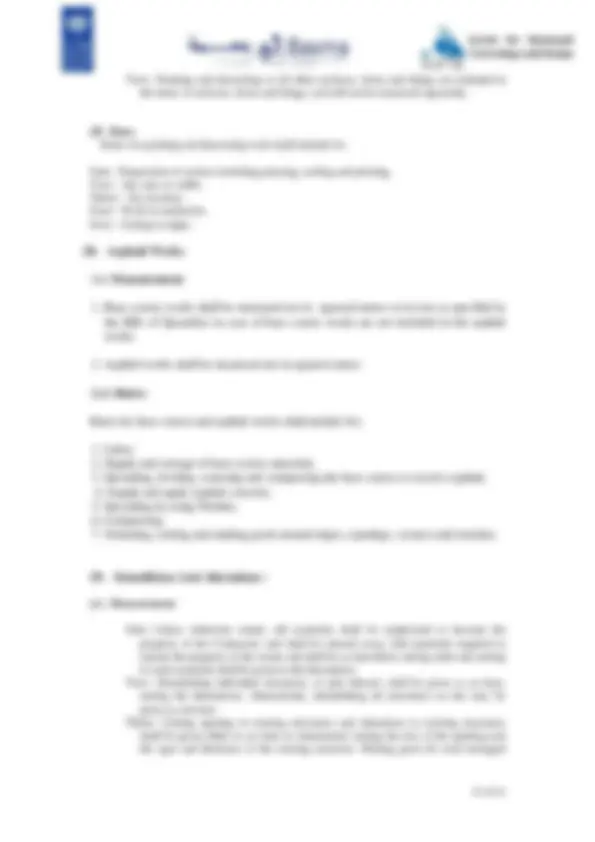
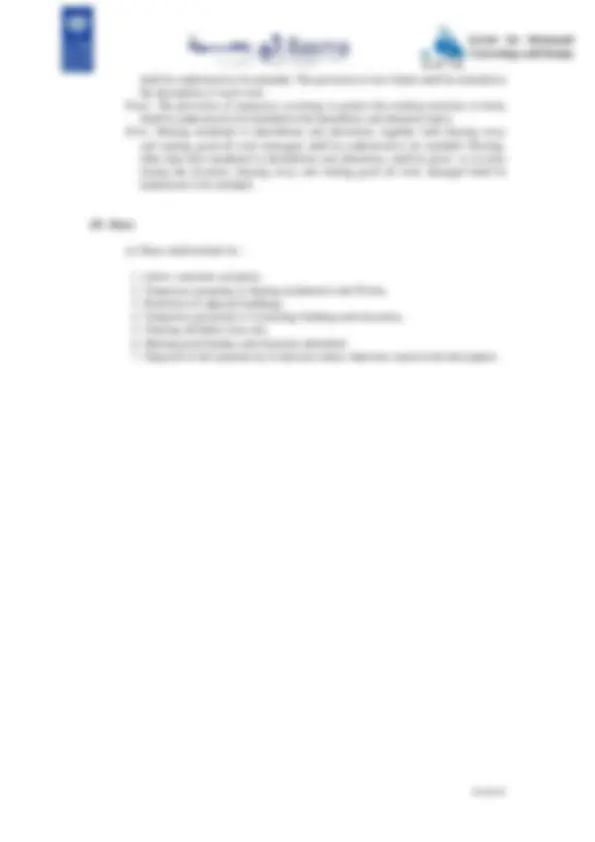
Study with the several resources on Docsity
Earn points by helping other students or get them with a premium plan
Prepare for your exams
Study with the several resources on Docsity
Earn points to download
Earn points by helping other students or get them with a premium plan
Community
Ask the community for help and clear up your study doubts
Discover the best universities in your country according to Docsity users
Free resources
Download our free guides on studying techniques, anxiety management strategies, and thesis advice from Docsity tutors
The roles and responsibilities of an architect in a construction contract, including determining the amount and quality of work, deciding disputes, and the inclusion of various costs in the unit and lump sum prices. The document also provides rates for concrete work, block work, stonework, and carpentry and joinery work, detailing what is included in each rate.
Typology: Study Guides, Projects, Research
1 / 44
This page cannot be seen from the preview
Don't miss anything!
GENERAL CONDITIONS OF CONTRACT
In relation to tender No. (CATD-A150401)
4. Pricing: The Contractor shall satisfy himself as to the meaning of every item in the Bills of Quantities and the rates and prices inserted by him shall cover all Works required by the Contract Documents. All costs in connection with the proper and successful construction, completion and maintenance of the Works including, but not limited to, completion of all temporary works, furnishing all materials, equipment, supply and appurtenance, providing all construction Plants, equipment, tools, sampling, testing, profits, overheads, charges, provision of guarantees, performing all necessary labor and supervision and other cost of whatsoever nature necessary to fully complete the Works, shall be included in the unit and lump sum prices called for in the bills of Quantities. All Works not specifically set fourth as a pay item in the Bills of Quantities shall be considered as subsidiary obligation of the Contractor and all costs in connection therewith shall be included in the Priced Bid. Prices shall be deemed to include for all straight ranking and circular cutting and consequent waste.
as a basis for estimating the probable cost of the work and For the purpose of comparing the bids submitted for the work.
The actual amount of work done under each unit price items may differ from the estimated quantities. The basis of payment for work will be the actual quantities. The Contractor agrees that he will make no claim for damages, anticipated profits or otherwise on account of any difference between the amounts of work actually performed and the estimated amount.
6. Items in Bills of Quantities Such items are the subject of re-measurement of completion in accordance with Clause 56 of the General Conditions of Contract. Quantities given in the Bills are based upon measurement from the Contract Drawings and Specifications. 7. Measurement Metric measurements and weights have been used throughout the Bills of Quantities. Work is measured net as fixed in position and each measurement is taken to the nearest centimeter. Fractions of a centimeter less than half are disregarded and all other fractions are regarded as whole centimeters. This principle shall not apply to dimensions stated in item descriptions. Where minimum deductions of voids are dealt with they refer only to openings or voids, which are wholly within the boundaries of measured areas. Openings or voids, which are at the boundaries of measured areas, are always the subject of deduction irrespective of size. 8. Descriptions The order of stating dimensions in descriptions is generally in the sequence of Length, Width and Height. Unless otherwise stated in the Bills of Quantities or herein, all measured items are deemed to include supply and fix in place complete, thus all measured items shall include all incidentals to complete the work in a proper manner such as but not limited to the following: ( a ) Labor.
( b ) Materials, including all cost in connection herewith ( e.g. conveyance, delivery, unloading, storing, handling, lowering into position and the like ). ( c ) Customs and import duties as applicable, insurance, levies and the like. ( d ) All shop treatment of materials ( e.g. Preservation of timbers, galvanizing, priming, chrome plating, stove enameling, anodizing and the like, pipe wrapping, coatings, etc.). ( e ) Fitting and fixing materials in position including all necessary fixing devices and materials. ( f ) Commissioning & use of plant. ( g ) Disposal of waste of material. ( h ) Square, raking or curved cutting. ( i ) Work in volumes, areas and length of any size, no separate items being measured for isolated work or work in small quantities, short length, narrow widths, etc.
Junction between straight, raking and curved work are in all cases included with the work in which they occur.
Certain items are referenced directly to detail drawings to eliminate detailed description. All such reference includes all work to execute the detail.
Where Specification clauses and / or detail drawing numbers are referred to in a description such information is provided for convenience only and the Contractor is to note that all other relevant Specification requirements and relevant drawings and details are to be taken into account.
mm Millimeter cm Centimeter M.R. Linear meter M.S. Square meter M.C Cubic Meter L.S. Lump Sum NO. Number Kg. Kilogram Ref. Reference
10. Definitions The terms “include", “is included “, “including “, and similar, are used herein to indicate that the items and are not specifically mentioned in the descriptions but the costs of which are to be included in the measured items. Such references are not comprehensive and are for convenience only and the Contractor is to note that all relevant requirements of the Specifications and Drawings are to be taken into account in the measured items. The word “Site” used in the Bills of Quantities means the whole of the areas within the Contract limit lies for this Contract as shown on the Contract Drawings. With reference to the clearance of debris, rubbish, trash, excavated material and the like the definition is extended to include the whole of the site. The word “ditto” used in the Bills of Quantities means the repetition of all or part of the preceding item as applicable to complete the sense of the item.
B) Rates:
(2) Rates for hard-core beds shall include for: (a) Trimming and leveling ground under. (b) Watering, ramming and consolidation. (c) Loss of bulk in consolidation. (d) Finishing top surface to receive concrete, paving and the like.
(a) Measurements
(b) Rates (1) Rates for concrete work shall include for:
(A) Measurements One) Block work shall be measured net in squared meters. No deductions will be made for voids or openings of less than 0.5 square meters in area.
Two) Thickness given refers to the thickness shown on the drawings and no allowance will be made for any additional thickness due to uneven or bad workmanship.
Two) Thickness given refers to the nominal thickness or the thickness shown on the Drawing. No allowance will be made for any additional thickness due to uneven or bad workmanship or to variations in the thickness of the stone.
Three) Rubble stone walls shall be measured by volume.
Four) Stonework facing for drop beams of the suspended slabs will be measured same as the item of stone walls unless otherwise is specified in the Bills of Quantities.
(B) Rates Rates for stonework shall include for:
One)Labor, Two)Supply and storage of cement, Three)Supply and storage of stone, aggregates, water and other materials, Four)Shaping of the apparent faces of stones as per Drawings and the Instructions of the Architect, Five)All special pieces such as corners, jambs, pieces around windows and doors and the like, Six) Fabricated wire mesh, dowels, hangers and all tying and fixing tools for stone cladding works, Seven)Laying stones including coursing, bonding, and all mortar joints, Eight)Work of all classifications in any location, Nine)Face or surface finishing including all openings, returns, reveals and the like, Ten)Rough and fair cutting, Eleven)Tying to backing material, Twelve)Concrete and block backing where included with stonework item, Thirteen)Cutting or leaving holes, chases, grooves, mortices, sinkings and the like, and making good , Fourteen)Cutting and pinning or building in ends of lintels, steps, timbers, rails, brackets, steel sections and the like, and making good. Fifteen)Pointing including cleaning of stones, scaffolding and dismantling the same and all incidentals. Sixteen) Lintels and other reinforced concrete elements including reinforcement except those elements specified in separate items in the Bills of Quantities.
(A) Measurements One) Sizes of timber given in the Bills of Quantities are finished sizes and shall be as per Drawings, Two) Sizes of doors and other items mentioned in the Bills of Quantities shall allow for tolerance to suit the structural openings as per Drawings, Three) Wooden doors and pair of doors shall be measured in number or in squared meters for the structural opening or as mentioned otherwise in the Bills of Quantities, Four) Blackboards shall be measured in number or in squared meters as mentioned in the Bills of Quantities. Five) Wall protection wooden rails shall be measured in linear meter, Six) Cloth hangers and hanger wooden base shall be measured in number or in linear meter as stated in the Bills of Quantities.
(B) Rates Rates for carpentry and joinery work shall include for:
One) Labor, Two) Shop drawings, Three)Any length of timber , Four) Joints in the running length of timber , Five) Raking, curved or circular work and labors , Six) Frames, architrave, chalk holders and other holders and kick plates, Seven)Allowance for plastering and tiling and the like, Eight) Forming holes, angles, ends, mitres, rebates, splayed edges, grooves, chamfers, scribed edges, rounded edges, rounded corners, notches, sinkings, fitted ends, far ends and the like, Nine) Cutting and fitting around obstructions, Ten) Forming moldings, Eleven)Nosing, bed moulds, margins, and the like, Twelve)Facing and edging to blackboard , Thirteen)Bedding and painting, Fourteen)Grounds, blockings and backings, Fifteen)Plugging concrete, blockwork, and stonework , and making good, Sixteen)Ironmongery including cylindrical locks, handles, stoppers, screws, temporarily fixing, re-fixing, oiling and adjusting, Seventeen)Providing two keys for each lock including tagging, Eighteen)Hardware including nails, screws, dowels, cramps and the like , Nineteen)Steel legs, brackets, bearers and other supports including painting, Twenty)Glass and glazing including cutting to size and putty, Twenty-one)Preparing surfaces to receive finishes, Twenty-two)Painting, varnishing, polishing, oiling, and the like, to any area or width in any location including work in multicolor and cutting in edges.
(A) Measurements Metal works shall be measured in number or in squared meters as stated in the Bills of Quantities.
(B) Rates (a) Rates for metalwork shall include for :
One)Labor, Two)Preparing shop drawings, Three)Cutting, Four)Assembling, Five)Welding grinding and joining, Six)Drilling, countersinking, screwing, bolting and riveting, Seven)Bedding and pinting, Eight)Frames, including galvanized steel frames for Aluminum windows and architrave, Nine)Lugs, plugs, holdfasts and the like, Ten)Gaskets, sashes, double weather strips and external and internal silicon filling around frames,
(2) Rates for floor tilling: In addition to the related items stated above the rates for floor tiling shall also include:
One)Supply, store and cure of tiles, Two)Bedding and lining in cement and sand mortar Three)Sand or concrete filling as required by the Specifications, Four)Pointing and grouting with white cement, Five) Forming holes, Six)Forming grooves. Seven)On site mechanical grinding and polishing.
(3) Rates for wall tilling: In addition to the related items stated above the rates for wall tilling shall also include:
Eight)Supply, store and cure of tiles Nine)Plastering, Ten)Cutting and patching around the services and other openings, Eleven)Mortar, Twelve)Purpose made tiles including rounded edge tiles and bull nosed tiles, Thirteen)Grouting, grinding, and cleaning.
(A) Measurements One) All finishes shall be measured superficially net unless other wise stated clearly. Two) All finishes, except triangular shaped fillets and cement and sand lining to gutters, shall be measured superficially. Three) Triangular shaped fillets and cement and sand lining to gutters shall be measured run, unless otherwise stated clearly.
(B) Rates (a) Rates for cement and sand work shall include for:
(b) Rates for waterproofing shall include for :
(c) Rates for roof sheeting shall include for:
Section 00-General Conditions
1- Codes and Standards
The works shall be carried out in accordance with: a. Latest edition of “ British Standard Code of Practice “ C,P.310: Water Supply. b. latest edition of “British Standard Code of Practice “ C.P. 304: Sanitary Pipe work above Ground. c. Latest edition of “ British Standard Code of Practice “ C.P.305 Sanitary Appliances. d. All other applicable British Standard Specifications and codes of practice (Hereinafter referred to as B.S. and C.B. respectively). e. ASME American Society of mechanical Architects. f. ASTM American Society of Testing materials g. The Architect’s Instructions.
2- Extent of the Works
The works include-unless otherwise specified-the supply, installation, testing and commissioning , and delivering up clean and in working order the installations shown on the drawings and specified in the specifications and bill of quantities including all details such as :
of another manufacturer’s products for the work, and the Architect’s decision concerning equal product is final.
6. CONTRACTOR PRICE INCLUDED IN UNIT PRICE : A. Delivery to the Site. B. Product handling at site, including unloading, uncrossing and storage. C.. Protection of product from elements and damage. D. Labor for installation and finishing including the removal of waste material to approved sites by local Authorities. E. Other expenses required to complete installation. F. All Required Testing , Adjusting , and Calibration. G. All Documents Required in mechanical specifications. H. Architecting and Administrative Work. I. All works required in section ( 01 ). J. Contractor overhead and profit.
disconnecting, with minimum of interference with other installations.
B. Remove and replace defective Work;
C. Remove and replace Work not confirming to requirements of the Contract Documents;
D. Remove samples of installed Work as specified for testing;
E. Install equipment and materials in existing structures;
F. Upon written instructions from the Architect, uncover and restore Work to provide for Architect observation of concealed Work.
having accessories as scheduled.
Centrifugal fan, direct or belt driven as scheduled Provide aluminium weatherproof housings. Provide permanent split capacitor type motor for direct driven fans ( pH); capacitor start, induction run type motor for belt driven fans (3pH).
Housing Design: Hooded dome type.
for electrical connection. Provide ventilated motor compartment.
Bird Screens: Provide removable bird screens, 1/2' mesh, 16 ga aluminium or brass wire.
Axial fan, direct or belt driven as scheduled. Provide spun aluminium weatherproof housing. Provide permanent split capacitor type motor for direct driven fans, capacitor start, induction run type motor for belt driven fans.
Provide factory wired non-fusible type disconnect switch at motor in fan housing. Provide thermal overload protection in fan motor. Provide conduit chase within unit for electrical connection.
Bird Screens: Provide removable bird screens 1/2” mesh, 16 ga aluminium or brass wire.
Dampers: Provide automatic louvered damper.