
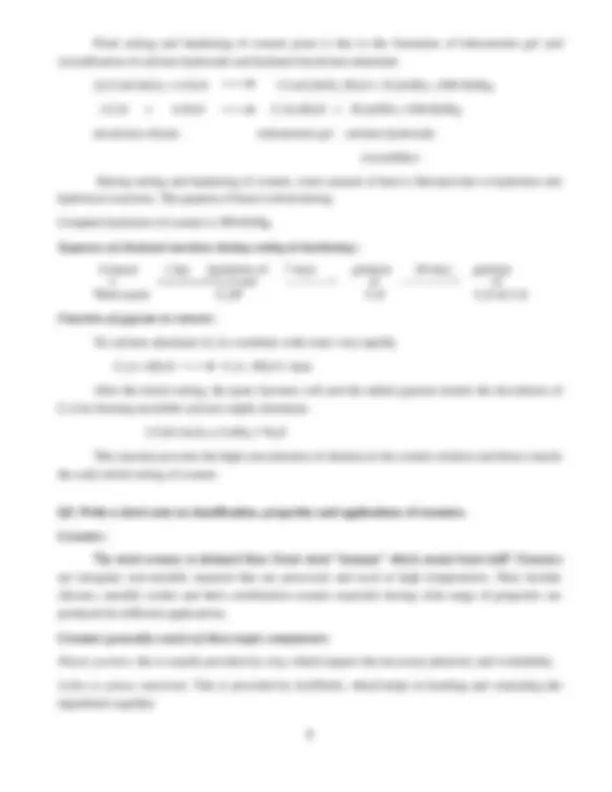
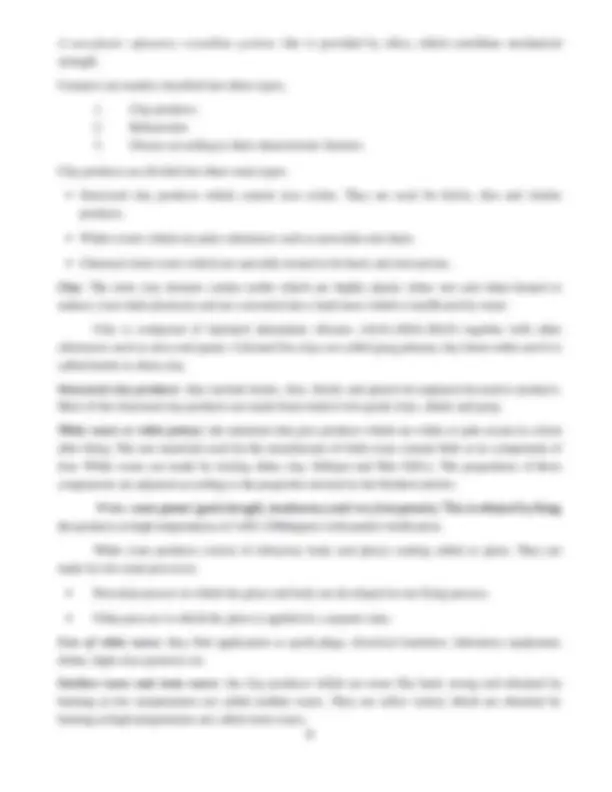
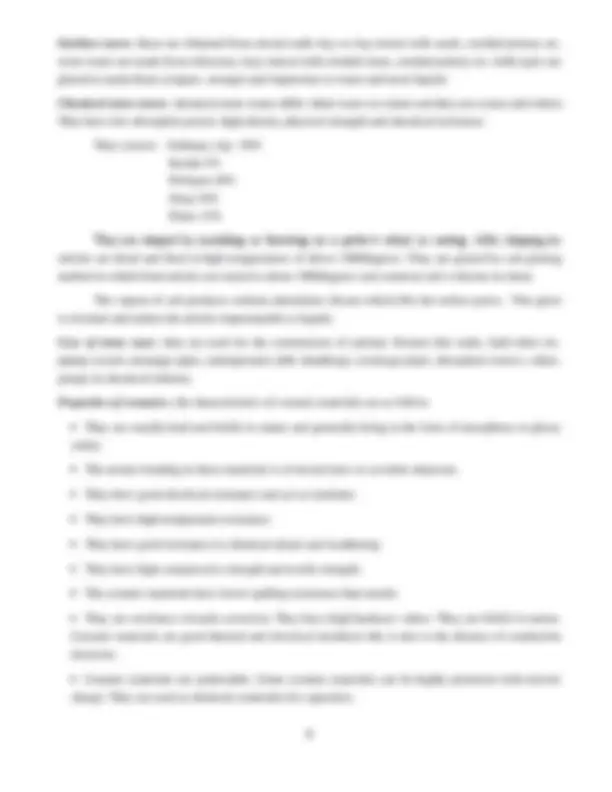
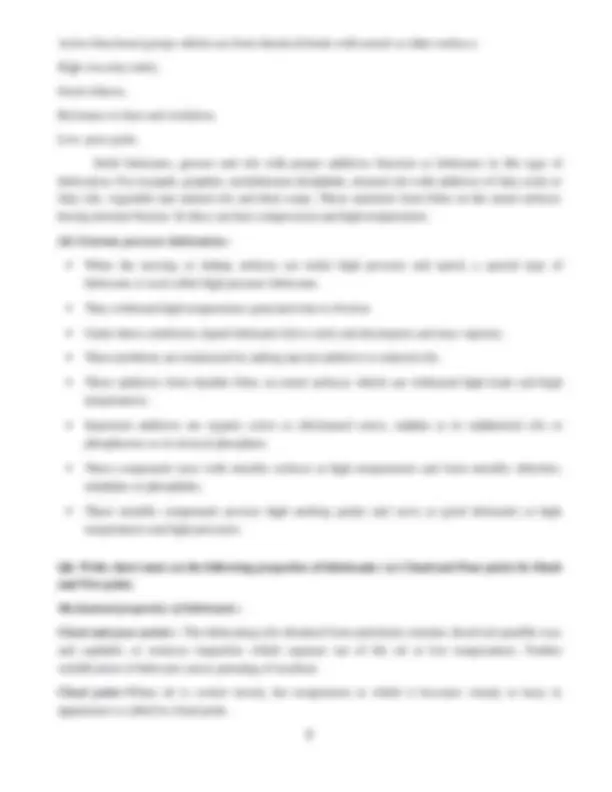
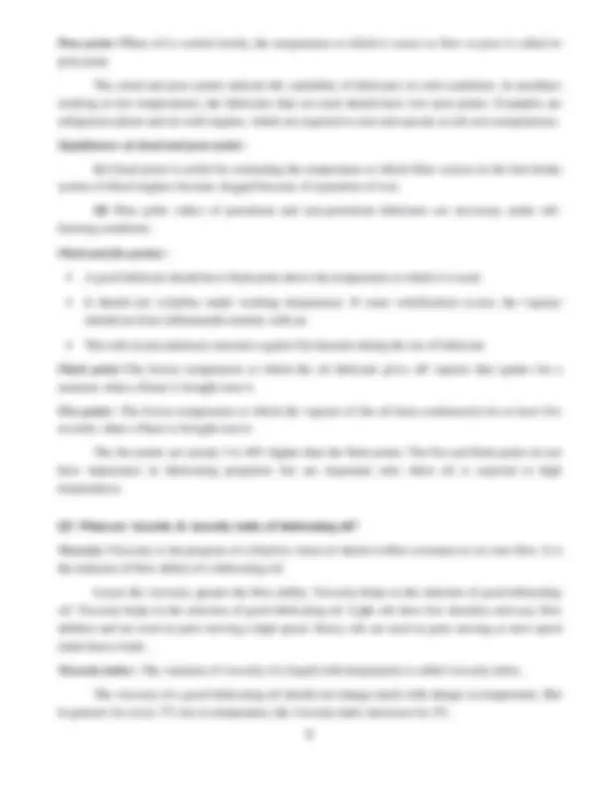
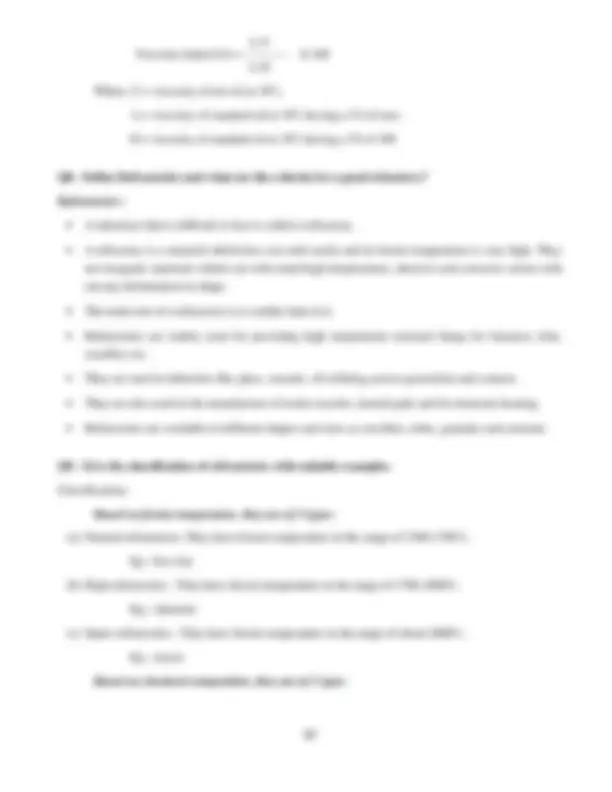
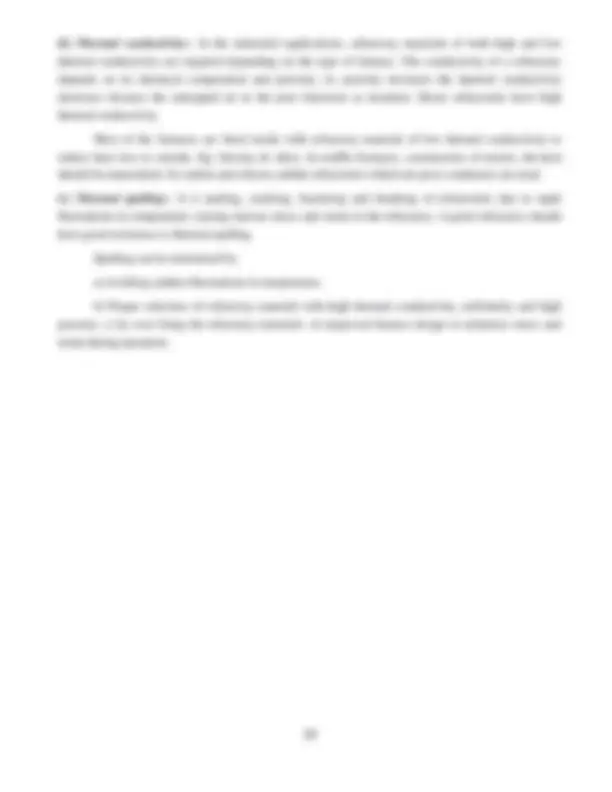
Study with the several resources on Docsity
Earn points by helping other students or get them with a premium plan
Prepare for your exams
Study with the several resources on Docsity
Earn points to download
Earn points by helping other students or get them with a premium plan
Community
Ask the community for help and clear up your study doubts
Discover the best universities in your country according to Docsity users
Free resources
Download our free guides on studying techniques, anxiety management strategies, and thesis advice from Docsity tutors
A basic overview of cement, ceramics, and refractories, highlighting their properties, applications, and classifications. It explains the chemical reactions involved in cement setting and hardening, discusses the different types of ceramics and their uses, and explores the characteristics and properties of refractory materials. Suitable for introductory courses in materials science or engineering.
Typology: Summaries
1 / 13
This page cannot be seen from the preview
Don't miss anything!
Q1. Write a brief account on composition and classification of cement. Cement: Concrete is most widely used non-metallic material in construction of buildings, dams, bridges, high ways etc. In concrete, cement is the essential bonding material which binds sand and rock when mixed with water. Cement is a dirty greenish heavy powder and finds its importance as a building material. It can be described as material possessing adhesive and cohesive properties and capable of bonding materials like stones, bricks, building blocks etc. Cement has the property of setting and hardening in the presence of water. So it is called as hydraulic cement. The essential constituents of cement used for constructional purposes are compounds of calcium (calcareous) and Al +Si (argillaceous). Classification: - Cement is classified into four types, based on the chemical composition.
Q2. Write a brief account on setting and hardening of cement. Setting and Hardening of cement:- Cement when mixed with water forms a plastic mass called cement paste. During hydration reaction, gel and crystalline products are formed. The inter-locking of the crystals binds the inert particles of the aggregates into a compact rock like material. This process of solidification comprises of (i) setting and then (ii) hardening Setting is defined as stiffening of the original plastic mass due to initial gel formation. Hardening is development of strength, due to crystallisation. Due to the gradual progress of crystallisation in the interior mass of cement, hardening starts after setting. The strength developed by cement paste at any time depends upon the amount of gel formed and the extent of crystallisation. The setting and hardening of cement is due to the formation of inter locking crystals reinforced by rigid gels formed by the hydration and hydrolysis of the constitutional compounds. Reactions involved in setting and hardening of cement:- When cement is mixed with water, the paste becomes rigid within a short time which is known as initial setting. This is due to the hydration of tricalcium aluminate and gel formation of tetra calcium alumino ferrite. 3 CaO.Al 2 O 3 + 6 H 2 O 3 CaO.Al 2 O 3 .6 H 2 O + 880 KJ/Kg C 3 A + 6 H 2 O C 3 A. 6 H 2 O + 880 KJ/Kg tricalcium aluminate hydrated tricalcium aluminate (crystalline) 4 CaO.Al 2 O 3 .Fe 2 O 3 + 7 H 2 O 3 CaO.Al 2 O 3 .6 H 2 O+ Cao.Fe 2 O 3 .H 2 O + 420 KJ/Kg C 4 AF + 7 H 2 O C 3 A. 6 H 2 O + CF.H 2 O + 420 KJ/Kg tetracalcium alumino ferrite (crystalline) gel Dicalcium silicate also hydrolyses to tobermonite gel which contributes to initial setting. 2(2 CaO.SiO 2 ) + 4 H 2 O 3 CaO.2SiO 2 .6H 2 O + Ca(OH) 2 +250 KJ/Kg 2 C 2 S + 4 H 2 O C 3 S 2 .6H 2 O + Ca(OH) 2 +250 KJ/Kg Dicalcium silicate tobermonite gel
A non-plastic refractory crystalline portion: this is provided by silica, which contribute mechanical strength. Ceramics are mainly classified into three types:
Earthen wares: these are obtained from mixed earth clay or clay mixed with sands, crushed pottery etc. stone wares are made from refractory clays mixed with crushed stone, crushed pottery etc. both types are glazed to made them compact, stronger and impersions to water and most liquids. Chemical stone wares: chemical stone wares differ white wares in colour and they are coarse and robust. They have low absorption power, high density, physical strength and chemical resistance. They consist: Ordinary clay - 50% Kaolin-5% Feldspar- 2 0% Grog-10% Flints-15% They are shaped by moulding or throwing on a potter’s wheel or casting. After shaping,the articles are dried and fired at high temperatures of above 1000degrees. They are glazed by salt glazing method in which fired articles are raised to about 1000degrees and common salt is thrown on them. The vapour of salt produces sodium aluminium silicate which fills the surface pores. This glaze is resistant and makes the articles impermeable to liquids. Uses of stone ware : they are used for the construction of sanitary fixtures like sinks, bath tubes etc. piping vessels, drainage pipes, underground cable sheathings, sewerage pipes, absorption towers, values, pumps in chemical industry. Properties of ceramics: the characteristics of ceramic materials are as follow: They are usually hard and brittle in nature and generally being in the form of amorphous or glassy solids. The atomic bonding in these materials is of mixed ionic or covalent character. They have good electrical resistance and act as insulator. They have high temperature resistance. They have good resistance to chemical attack and weathering. They have high compressive strength and textile strength. The ceramic materials have lower spalling resistance than metals. They are resistance towards corrosion. They have high hardness values. They are brittle in nature. Ceramic materials are good thermal and electrical insulators this is due to the absence of conduction electrons. Ceramic materials are polarizable. Some ceramic materials can be highly polarized with electric charge. They are used as dielectric materials for capacitors.
The lubricant film covers the irregularities of the surfaces and reduces friction and wear and tear. The resistance to movement of sliding or moving parts is due to internal resistance between the particles of the lubricant moving over each other. For this, the lubricant should have minimum viscosity under working conditions. It should remain in place and separate the surfaces. The coefficient of friction which is a ratio of force required to cause motion to the applied load is as low as 0.001 to 0.03. Delicate instruments, light machines like watches, clocks, guns, sewing machines etc. are provided with fluid film lubrication. The fluid film lubrication is done by hydrocarbon oils. These are blended with selected long chain polymers to maintain the viscosity of oil as constant in all seasons. The viscosity of hydrocarbon oils increases with increasing molecular weight. Hence appropriate fractions are blended from petroleum refining to meet the requirement for different applications.These fractions contain small quantities of unsaturated hydrocarbons which get oxidised under operating conditions and form gummy products. So antioxidants like amino phenols are used in hydrocarbon oils. (ii)Boundary lubrication:- This type of lubrication occurs when a continuous film of lubricant cannot persist and direct metal to metal is possible. In these conditions, the space between the moving or sliding surfaces is lubricated so that a thin layer of lubricant is adsorbed on the metallic surfaces due to physical or chemical forces. This adsorbed layer helps to avoid the direct metal to metal contact between the rubbings surfaces. This load is carried by the layers of adsorbed lubricant on both thre metal surfaces. The coefficient of friction varies from 0.05 to 0.15. For boundary lubrication, the lubricant molecules should have Long hydrocarbon chains, Polar groups to promote wetting or spreading over the surface, Lateral attraction between the chains,
Active functional groups which can form chemical bonds with metals or other surface,s High viscosity index, Good oiliness, Resistance to heat and oxidation, Low pour point. Solid lubricants, greases and oils with proper additives function as lubricants in this type of lubrication. For example, graphite, molybdenum disulphide, mineral oils with additives of fatty acids or fatty oils, vegetable and animal oils and their soaps. These materials form films on the metal surfaces having internal friction. So they can bear compression and high temperatures. (iii) Extreme pressure lubrication:- When the moving or sliding surfaces are under high pressure and speed, a special type of lubricants is used called high pressure lubricants. They withstand high temperatures generated due to friction. Under these conditions, liquid lubricants fail to stick and decompose and may vaporise. These problems are minimised by adding special additives to mineral oils. These additives form durable films on metal surfaces which can withstand high loads and high temperatures. Important additives are organic esters as chlorinated esters, sulphur as in sulphurised oils or phosphorous as in tricresyl phosphate. These compounds react with metallic surfaces at high temperatures and form metallic chlorides, sulphides or phosphides. These metallic compounds possess high melting points and serve as good lubricants at high temperatures and high pressures. Q6. Write short notes on the following properties of lubricants: (a) Cloud and Pour point (b) Flash and Fire point. Mechanical properties of lubricants:- Cloud and pour points:- The lubricating oils obtained from petroleum contains dissolved paraffin wax and asphaltic or resinous impurities which separate out of the oil at low temperatures. Further solidification of lubricant causes jamming of machine. Cloud point:- When oil is cooled slowly, the temperature at which it becomes cloudy or hazy in appearance is called its cloud point.
Viscosity Index(VI) = ----------- X 100 L-H Where, U = viscosity of test oil at 3 8 o c. L = viscosity of standard oil at 38 o c having a VI of zero. H = viscosity of standard oil at 38 o c having a VI of 100. Q8. Define Refractories and what are the criteria for a good refractory? Refractories:- A substance that is difficult to fuse is called a refractory. A refractory is a material which does not melt easily and its fusion temperature is very high. They are inorganic materials which can with stand high temperatures, abrasive and corrosive action with out any deformation in shape. The main role of a refractory is to confine heat in it. Refractories are widely used for providing high temperature resistant lining for furnaces, kiln, crucibles etc. They are used in industries like glass, ceramic, oil-refining, power generation and cement. They are also used in the manufacture of rocket nozzles, launch pads and for domestic heating. Refractories are available in different shapes and sizes as crucibles, tubes, granules and cements. Q9. Give the classification of refractories with suitable examples. Classification:- Based on fusion temperature, they are of 3 types: (a) Normal refractories:-They have fusion temperature in the range of 1580- 1780 oc. Eg:- fire clay (b) High refractories:- They have fusion temperature in the range of 1780- 2000 oc. Eg;- chromite (c) Super refractories:- They have fusion temperature in the range of about 2000oc. Eg:- zircon Based on chemical composition, they are of 3 types:
(a) Acidic refractories:- They consists of acidic materials like alumina and silica. These refractory materials are resistant to acid slags and are readily attacked by basic slags. Eg:- Alumina, silica and fire clay refractories. (b) Basic refractories:- They consist of basic materials like CaO, MgO etc. and are resistant to basic slags. They are widely used in steel making open hearth furnaces. Eg:- magnesite and dolomite bricks (c) Neutral refractories:- They are made from weakly basic or acidic materials like carbon, zirconia and chromite. Neutral refractories show resistance to the action of basic and acidic materials. They show good chemical stability. Eg:-graphite, zirconia and carborundum Based on oxide content, the refractories are classified in to 3 types. (a) Single oxide refractories:- Eg:- alumina, magnesia and zirconia (b) Mixed oxide refractories:- Eg:- zircon, spinel. (c) Non oxide refractories:- Eg:- Borides, carbides, silicides etc. Q10. Write short notes on characteristics and properties of refractories. Characteristics of refractory materials:- A good refractory material should have a softening temperature higher than operating temperatures. They should be chemically inert. The refractoriness should be high for a good refractory. The refractories should not crack at operating temperatures. They should have low permeability. They should have low thermal coefficient of expansion and should expand and contract uniformly with increase and decrease of temperatures. They should with stand heavy loads. They should possess good physical, chemical and mechanical properties. Properties of refractories:- (i)Refractoriness:- It is the ability of a material to with stand high temperature without deformation under working conditions.
iii) Thermal conductivity:- In the industrial applications, refractory materials of both high and low thermal conductivity are required depending on the type of furnace. The conductivity of a refractory depends on its chemical composition and porosity. As porosity increases the thermal conductivity decreases because the entrapped air in the pore functions as insulator. Dense refractories have high thermal conductivity. Most of the furnaces are lined inside with refractory material of low thermal conductivity to reduce heat loss to outside. Eg: fireclay & silica. In muffle furnaces, construction of retorts, the heat should be transmitted. So carbon and silicon carbide refractories which are poor conductors are used. iv) Thermal spalling:- It is peeling, cracking, fracturing and breaking of refractories due to rapid fluctuations in temperature causing uneven stress and strain in the refractory. A good refractory should have good resistance to thermal spalling. Spalling can be minimised by: a) Avoiding sudden fluctuations in temperature. b) Proper selection of refractory material with high thermal conductivity, uniformity and high porosity. c) by over firing the refractory materials. d) improved furnace design to minimise stress and strain during operation.