
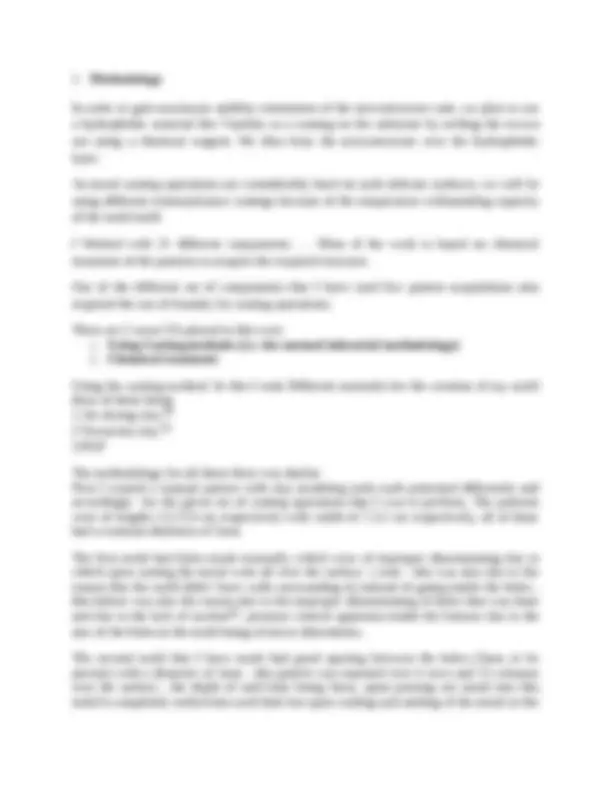
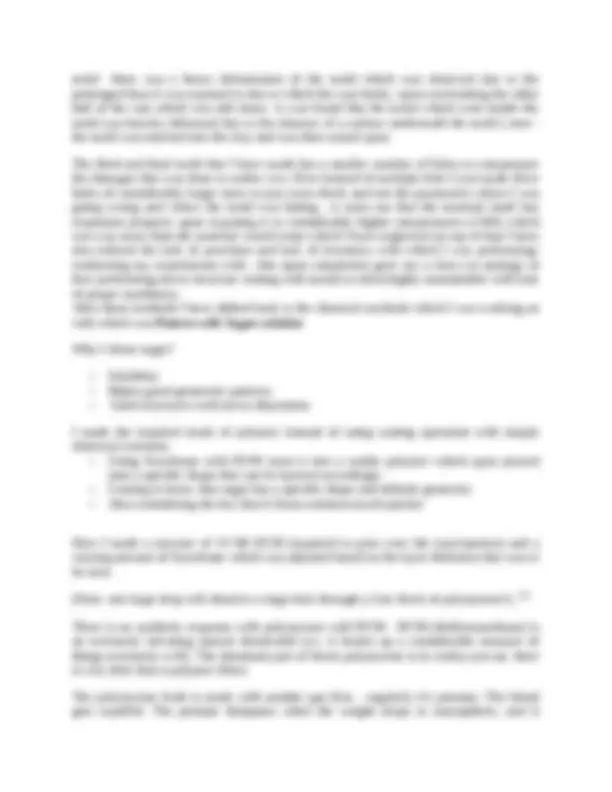
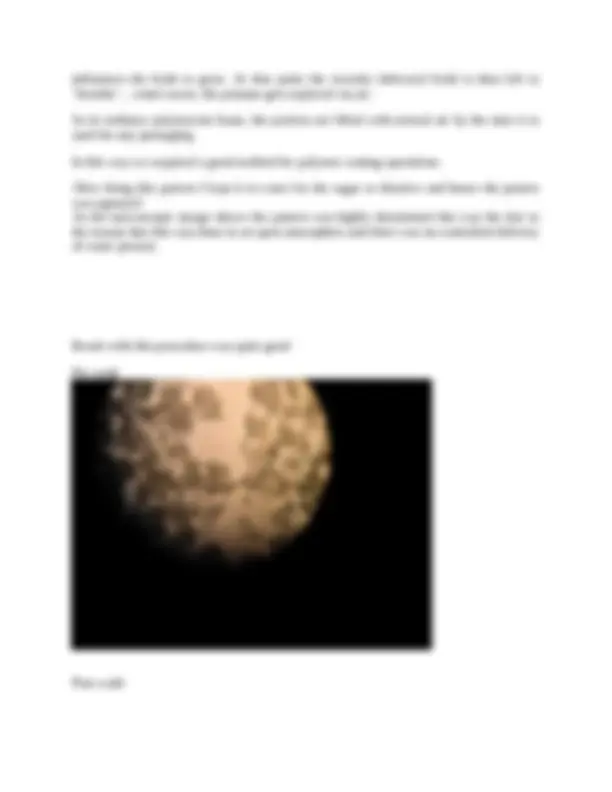

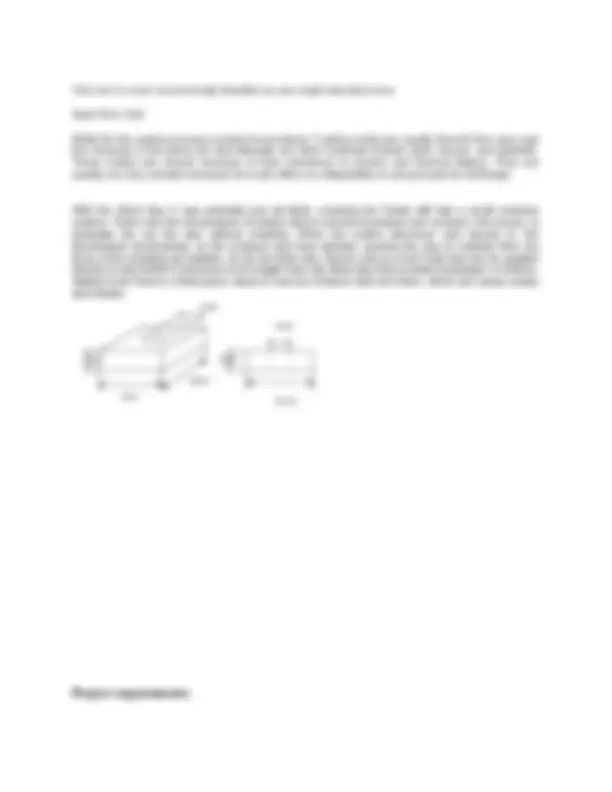
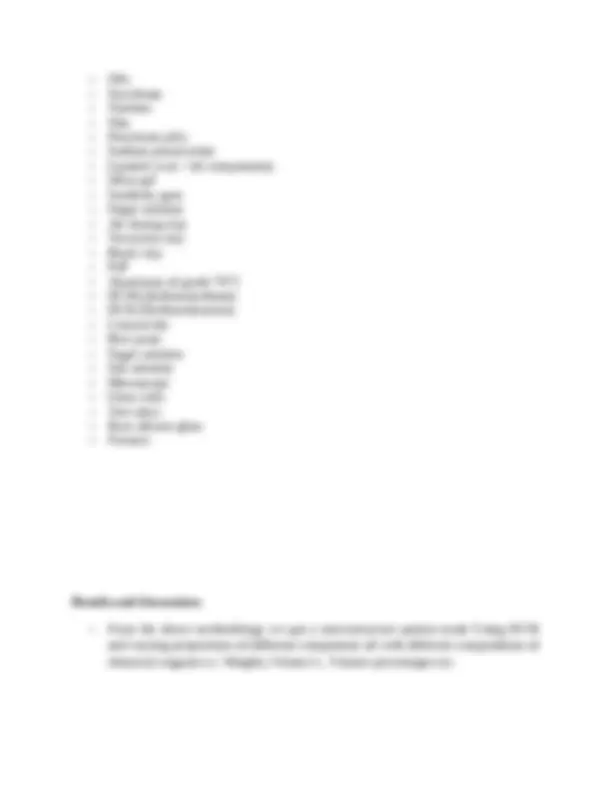
Study with the several resources on Docsity
Earn points by helping other students or get them with a premium plan
Prepare for your exams
Study with the several resources on Docsity
Earn points to download
Earn points by helping other students or get them with a premium plan
Community
Ask the community for help and clear up your study doubts
Discover the best universities in your country according to Docsity users
Free resources
Download our free guides on studying techniques, anxiety management strategies, and thesis advice from Docsity tutors
This document details a student's project on microstructure fabrication using casting and chemical methods. The student discusses their experience with various materials, including clay and sugar solution, and shares the challenges and results of their experiments. The document also includes references.
Typology: Study Guides, Projects, Research
1 / 12
This page cannot be seen from the preview
Don't miss anything!
Microstructures have shown tremendous applications primarily in the field of medicine
ever since the onset of its usage. Technologies like ultra-high precision needles and micro
cameras have been possible due to the controlled microstructure manufacturing. [1][2]^ The
present state of manufactured objects has shown an attribute of high wear with every
usage.[3]^ This reduces the feasibility of such structures in various applications and
production while also limiting the field’s potential. In this project, I worked with an
efficient and affordable way to produce microstructure via casting and chemical methods.
The aim of this project is to suggest, test and verify a method to fabricate and design
stronger, durable and precise microstructures to replace or augment the current method of
manufacturing a microstructure.
mold there was a heavy deformation of the mold which was observed due to the prolonged heat it was exposed to due to which the cast broke, upon overlooking the other half of the cast which was still intact it was found that the metal which went inside the mold was heavily deformed due to the absence of a surface underneath the mold ( note : the mold was inserted into the clay and was then casted upon.
The third and final mold that I have made has a smaller number of holes to compensate the damages that was done to earlier two. Here instead of multiple hole I just made three holes of considerably larger sizes to just cross check and test the parameters where I was going wrong and where the mold was failing , it turns out that the material itself has expansion property upon exposing it to considerably higher temperatures (1300) which was way more than the material would resist which I have neglected on top of that I have also noticed the lack of precision and lack of inventory with which I was performing/ conducting my experiments with , this upon completion gave me a clear cut analogy of how performing micro structure casting with metals is often highly unattainable with lack of proper machinery. After these methods I have shifted back to the chemical methods which I was working on with which was Pattern with Sugar solution
Why I chose sugar?
I made the required mask of polymer instead of using casting operation with simple chemical reactions
Here I made a mixture of 10 Ml DCM (required to pour over the layer/pattern) and a varying amount of Styrofoam which was adjusted based on the layer thickness that was to be seen
(Note: one large drop will dissolve a large hole through a 2cm block of polystyrene!) .[7]
There is no synthetic response with polystyrene with DCM. DCM (dichloromethane) is an extremely solvating natural dissolvable (i.e. it breaks up a considerable measure of things extremely well). The dominant part of block polystyrene is in reality just air, there is very little that is polymer fibers
The polystyrene froth is made with another gas first... regularly it's pentane. The blend gets expelled. The pentane dissipates when the weight drops to atmospheric, and it
influences the froth to grow. At that point the recently delivered froth is then left to "breathe"... what's more, the pentane gets replaced via air.
So in ordinary polystyrene foam, the pockets are filled with normal air by the time it is used for any packaging.
In this way we acquired a good method for polymer casting operations.
After doing this pattern I kept it in water for the sugar to dissolve and hence the pattern was appeared As the microscopic image shows the pattern was highly disoriented this was the due to the reason that this was done in an open atmosphere and there was no controlled delivery of water present
Result with this procedure was quite good
Pre wash
Post wash
Note: When adding in concentrated form it with rather dissolve or eat away the whole aluminum but in very mild amounts it can be used for controlled cleaning of the surface.
Al⁰ - 3e = Al³⁺
Cations of hydrochloric acid take electrons, reducing to molecular hydrogen:
2H⁺ + 2e = H₂⁰
Complete reaction equation:
2Al⁰ + 6H⁺ + 6Cl⁻ = 2Al³⁺ + 6Cl⁻ + 3H₂⁰
In abbreviated ionic form:
2Al⁰ + 6H⁺ = 2Al³⁺ + 3H₂⁰
In molecular form the reaction looks as follows:
2Al + 6HCl = 2AlCl₃ + 3H₂
H20 when treated with silica
This was unintentional as I was dealing with silica for layering upon dissolution with high amounts of water for turning it into a layer on which I could cast my impression upon (once done it was powdery)
Si + 2H2O SiO 2 + 2H 2
Hcl on lipstick
Hcl in this case did eat away most of the impression that I have made with the lipstick Leaving behind few residual oils in this the pattern was quite clear to view but the pathing of the pattern was not continuous this was due to the fact that I used the lipstick all in all and Hcl tends to eat away the wax leaving the oils behind in the pattern.
This was the result
Aluminum on clay mold
Aluminum melts at around 1200 degrees and be cast into most clay or sand. You don’t risk any pressure explosions unless you’re casting iron or steel into wet sand. For casting anything larger than a Lego made mold I would suggest building a small charcoal forge (considering the amount of money would go exponentially low ) with a steel crucible for melting aluminum but as it wasn’t available I had to go with the regular one
Using of clay mold
Results and discussions
Future uses :
References
[1] https://pdfs.semanticscholar.org/ee15/f5fe92176faa8204cfced7eb7c2c4842f59d.pdf
[2] R. C. Jaeger, Introduction to microelectronic fabrication, Prentice; Hall, 2002
[3] https://www.reddit.com/r/pics/comments/m68u6/ head_of_a_needle_under_a_microscope/
[4] https://www.thesprucecrafts.com/air-dry-clay-
[7] https://www.scienceforums.net/topic/55930-dcm-and-polystyrene/