
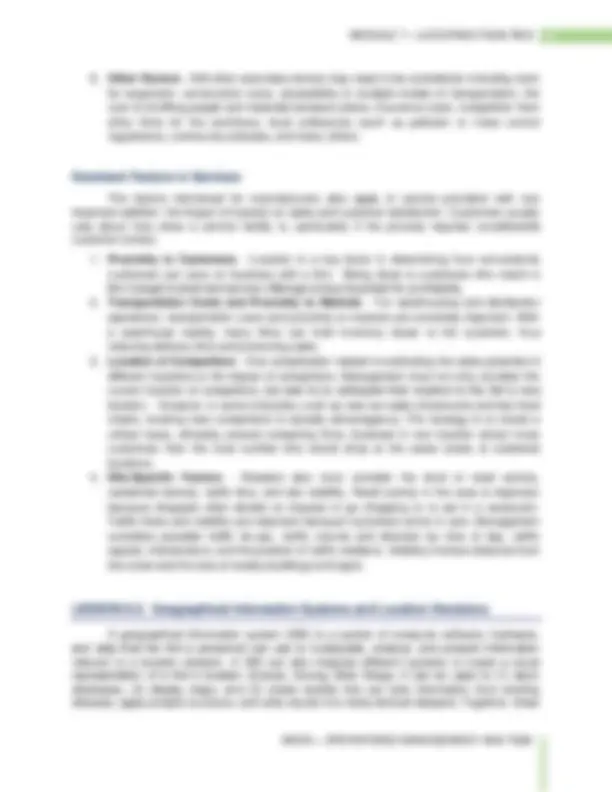
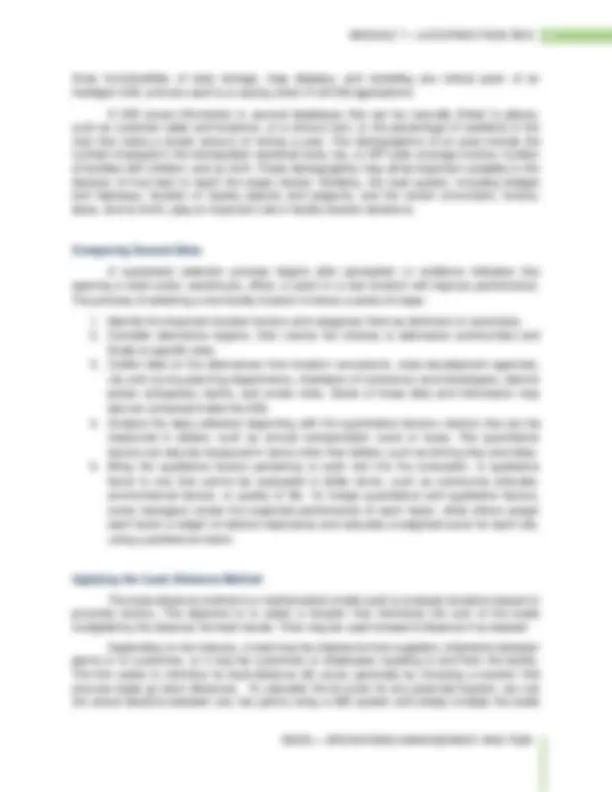
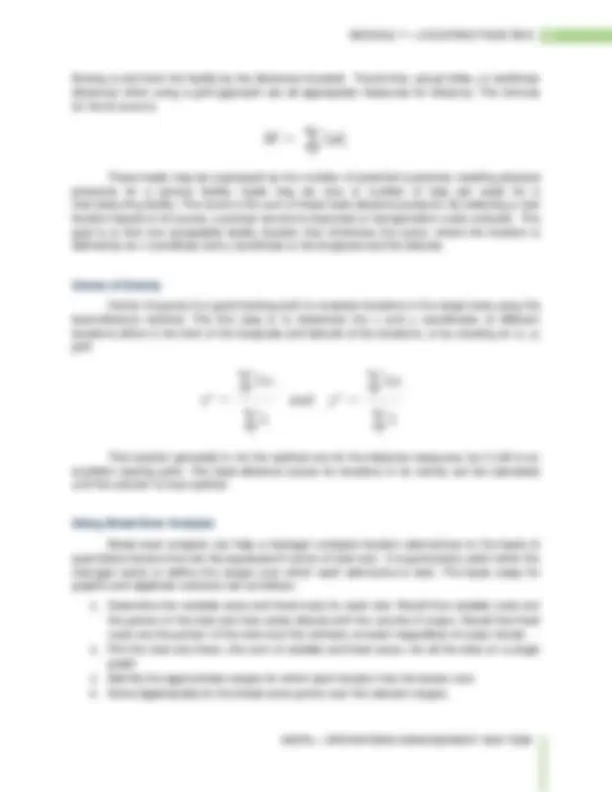
Study with the several resources on Docsity
Earn points by helping other students or get them with a premium plan
Prepare for your exams
Study with the several resources on Docsity
Earn points to download
Earn points by helping other students or get them with a premium plan
Community
Ask the community for help and clear up your study doubts
Discover the best universities in your country according to Docsity users
Free resources
Download our free guides on studying techniques, anxiety management strategies, and thesis advice from Docsity tutors
This module explores the critical process of facility location in operations management and total quality management (tqm). It delves into the factors influencing location decisions, including proximity to markets, environmental impact, quality of life, and transportation costs. The module also introduces the use of geographical information systems (gis) for analyzing location patterns and identifying optimal sites. It further examines the load-distance method, break-even analysis, and the transportation method for evaluating and selecting facility locations.
Typology: Schemes and Mind Maps
1 / 7
This page cannot be seen from the preview
Don't miss anything!
Facility location is the process of determining geographic sites for a firm’s operations, which could include a manufacturing plant, a distribution center, and a customer service center. Distribution center is a warehouse or a stocking point where goods are stored for subsequent distribution to manufacturers, wholesalers, retailers, and customers. Location choices can be critically important for firms, and have a profound impact on its supply chains. For example, they can affect the supplier relationship process.
Analyzing location patterns to discover a firm’s underlying strategy is fascinating. Recognizing the strategic impact location decisions have on implementing a firm’s strategy and supply chain design, we first consider the qualitative factors that influence location choices and their implications across the organization. Subsequently we examine an important trend in location patterns: the use of geographical information systems (GIS) to identify market segments and how serving each segment can profitably affect the firm’s location decisions.
After reading this module, the learner should be able to:
Location decisions affect processes and departments throughout the organization. Relocating all or part of an organization can significantly affect the attitudes of the firm’s
workforce and the organization’s ability to operate effectively across departmental lines. Location also has implications for a firm’s human resources department, which must be attuned to the firm’s hiring and training needs. Locating new facilities or relocating existing facilities is usually costly; therefore, these decisions must be carefully evaluated by the organization’s accounting and finance departments.
Managers of both service and manufacturing organizations must weigh many factors when assessing the desirability of particular locations, including their proximity to customers and suppliers, labor costs, and transportation costs.
The following seven groups of factors dominate the decisions firms, including BMW, make about the location of new manufacturing plants or distribution centers. Often there is a trade-off among factors.
three functionalities of data storage, map displays, and modeling are critical parts of an intelligent GIS, and are used to a varying extent in all GIS applications.
A GIS stores information in several databases that can be naturally linked to places, such as customer sales and locations, or a census tract, or the percentage of residents in the tract that make a certain amount of money a year. The demographics of an area include the number of people in the metropolitan statistical area, city, or ZIP code; average income; number of families with children; and so forth. These demographics may all be important variables in the decision of how best to reach the target market. Similarly, the road system, including bridges and highways, location of nearby airports and seaports, and the terrain (mountains, forests, lakes, and so forth), play an important role in facility location decisions.
Comparing Several Sites
A systematic selection process begins after perception or evidence indicates that opening a retail outlet, warehouse, office, or plant in a new location will improve performance. The process of selecting a new facility location involves a series of steps.
Applying the Load–Distance Method
The load–distance method is a mathematical model used to evaluate locations based on proximity factors. The objective is to select a location that minimizes the sum of the loads multiplied by the distance the load travels. Time may be used instead of distance if so desired.
Depending on the industry, a load may be shipments from suppliers, shipments between plants or to customers, or it may be customers or employees traveling to and from the facility. The firm seeks to minimize its load–distance (ld) score, generally by choosing a location that ensures loads go short distances. To calculate the ld score for any potential location, we use the actual distance between any two points using a GIS system and simply multiply the loads
flowing to and from the facility by the distances traveled. Travel time, actual miles, or rectilinear distances when using a grid approach are all appropriate measures for distance. The formula for the ld score is
These loads may be expressed as the number of potential customers needing physical presence for a service facility; loads may be tons or number of trips per week for a manufacturing facility. The score is the sum of these load–distance products. By selecting a new location based on ld scores, customer service is improved or transportation costs reduced. The goal is to find one acceptable facility location that minimizes the score, where the location is defined by its x coordinate and y coordinate or the longitude and the latitude.
Center of Gravity
Center of gravity is a good starting point to evaluate locations in the target area using the load–distance method. The first step is to determine the x and y coordinates of different locations either in the form of the longitude and latitude of the locations, or by creating an (x, y) grid.
This location generally is not the optimal one for the distance measures, but it still is an excellent starting point. The load–distance scores for locations in its vicinity can be calculated until the solution is near optimal.
Using Break-Even Analysis
Break-even analysis can help a manager compare location alternatives on the basis of quantitative factors that can be expressed in terms of total cost. It is particularly useful when the manager wants to define the ranges over which each alternative is best. The basic steps for graphic and algebraic solutions are as follows:
Stevenson, William (2018), Project Management; the managerial process 7th^ ed. Stevenson, William (2018), Operations Management 13th^ Edition Zani, Rosliza (2018), Operation management Krajewski, Lee J. (2016) Operation management: sustainability and supply chain management 12 th^ ed. Verma, A.P. (2016). Industrial Engineering and Management