
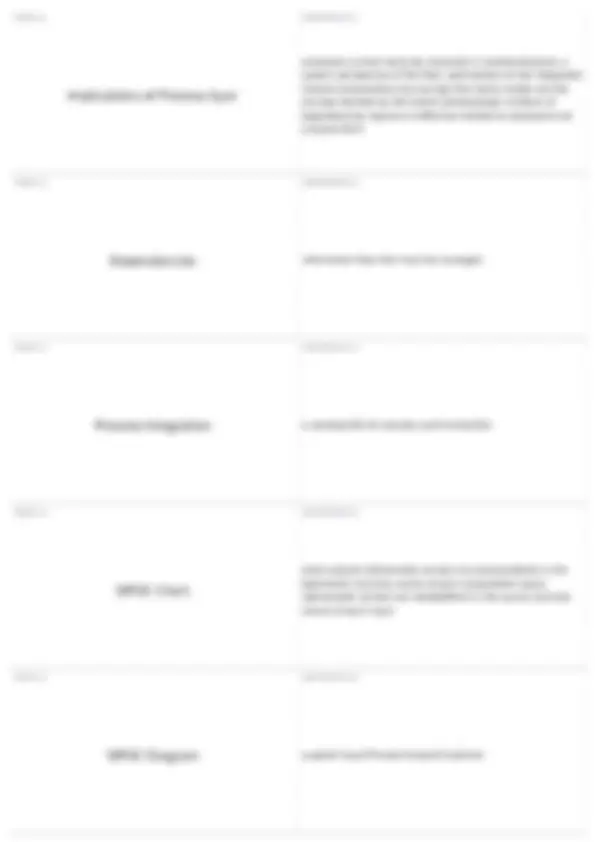
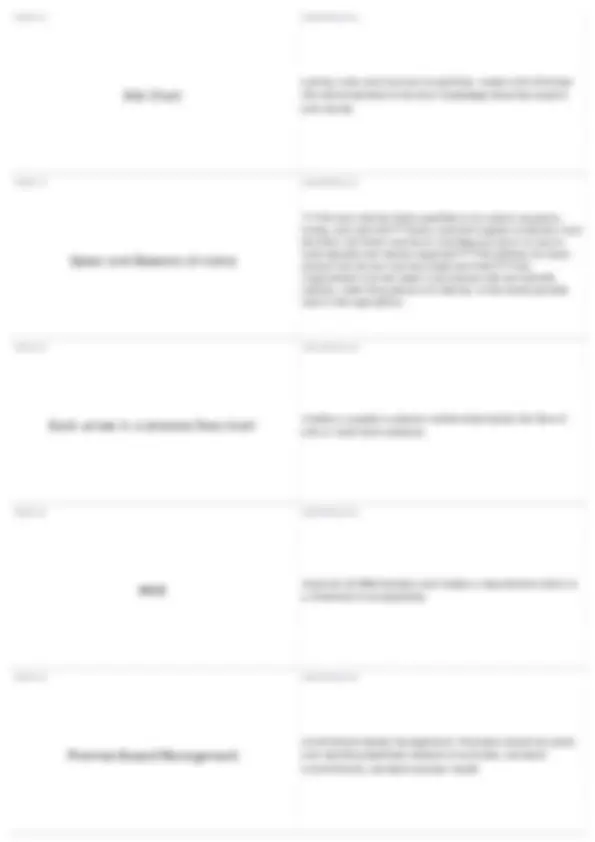
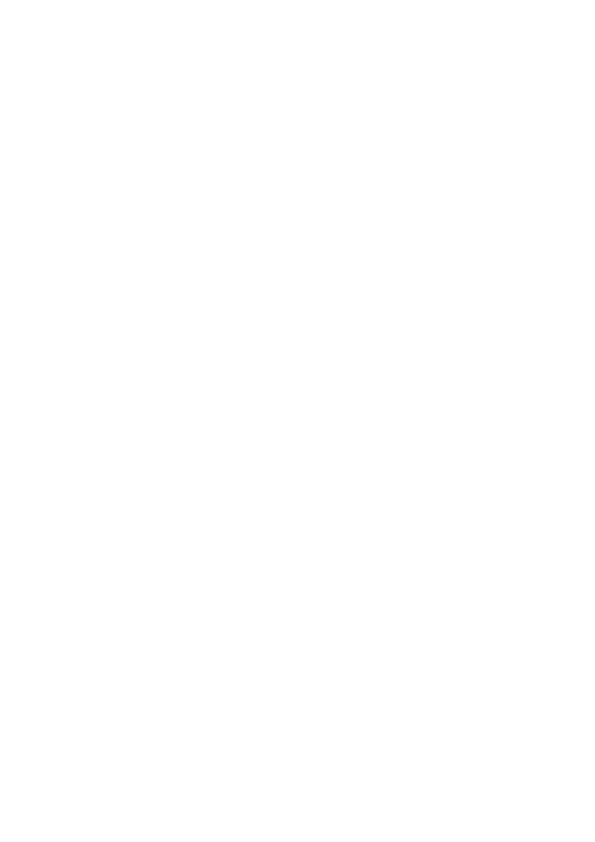
Study with the several resources on Docsity
Earn points by helping other students or get them with a premium plan
Prepare for your exams
Study with the several resources on Docsity
Earn points to download
Earn points by helping other students or get them with a premium plan
Community
Ask the community for help and clear up your study doubts
Discover the best universities in your country according to Docsity users
Free resources
Download our free guides on studying techniques, anxiety management strategies, and thesis advice from Docsity tutors
Class: MGMT - Operations Management; Subject: Management; University: Texas Christian University; Term: Forever 1989;
Typology: Quizzes
1 / 5
This page cannot be seen from the preview
Don't miss anything!
to ensure that all elements of the organization are working in harmony (synchronously) towards the goalto emphasize total system performance and not local measures such as labor or machine utilization or efficiency TERM 2
DEFINITION 2 when activities take variable amounts of time we can't find the bottleneckthe average capacity of each activity is less than the average capacity of the process. may not know what it is exactlyaverage capacity of the process is the numbers divided by two so for dice it is 3. TERM 3
DEFINITION 3 implies the need to balance the flow through the process rather than the capacities of the activities TERM 4
DEFINITION 4 can be a bad the bottleneck is indeterminable TERM 5
DEFINITION 5 smaller flow at non bottleneck activities to keep flow balanced in the system
quality control earlyoutsourceoff line set upsensure all items need itload for max utilization TERM 7
DEFINITION 7 infinite for an assembly line because it is continuous TERM 8
DEFINITION 8 one because one unit is moved at a time TERM 9
DEFINITION 9 Do not balance capacity; balance flow utilization of a non bottleneck resource is not determined by its own potential but by other system constraints Utilization and activation of resources are not the same An hour lost at the bottleneck is lost for the whole system an hour saved at a non bottleneck is a mirage transfer batch and process batch size are different TERM 10
DEFINITION 10 A-wait-B-wait-Cby eliminating one constraint another may pop up.by working before ready then re-work may occurlean synchronization (coordinate in time) external process to ensure right information in the right place at the right time.
overlay rows and columns to optimize. reveal and eliminate the disconnectstacit and local knowledge becomes explicit and shared TERM 17
DEFINITION 17 *****all work shall be highly specified as to content, sequence, timing, and outcome*****every customer-supplier connection must be direct, and there must be an unambiguous yes-or-no way to send requests and receive responses*****The pathway for every product and service must be simple and direct*****Any improvement must be made in accordance with the scientific method, under the guidance of a teacher, at the lowest possible level in the organization TERM 18
DEFINITION 18 implies a supplier-customer relationshipimplies the flow of one or more work products TERM 19
DEFINITION 19 measure of effectiveness and implies a requirement which is a threshold of acceptability TERM 20
DEFINITION 20 commitment based management. Promises should be public and realisticpredefined network of activities, standard commitments, standard process model