
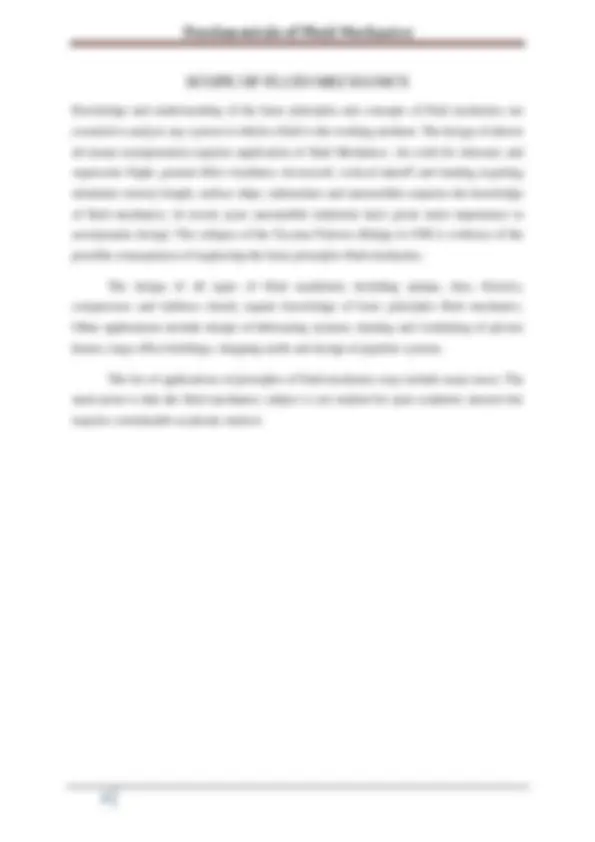
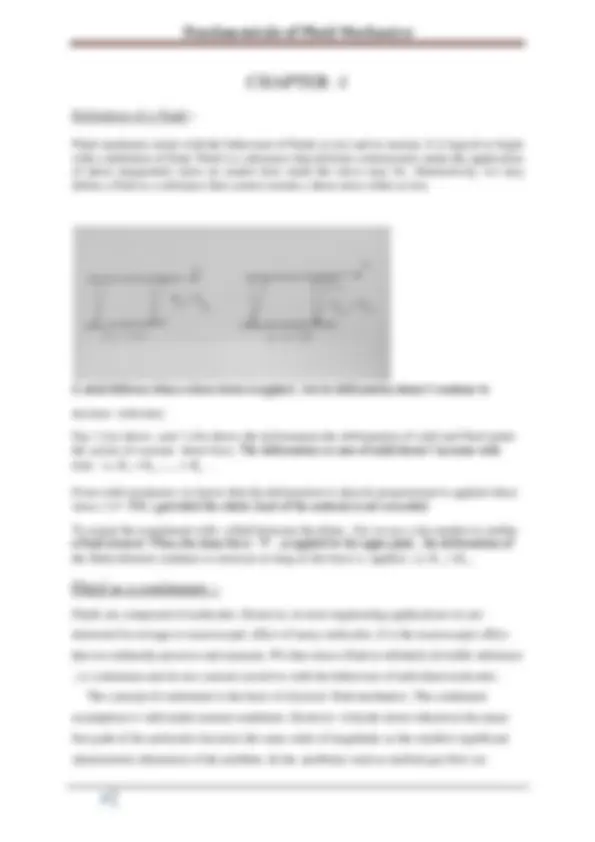
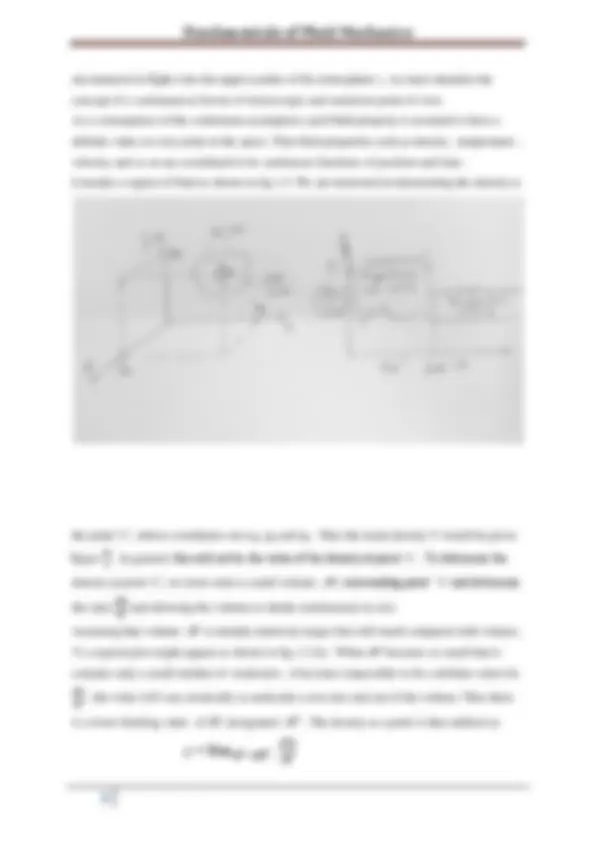
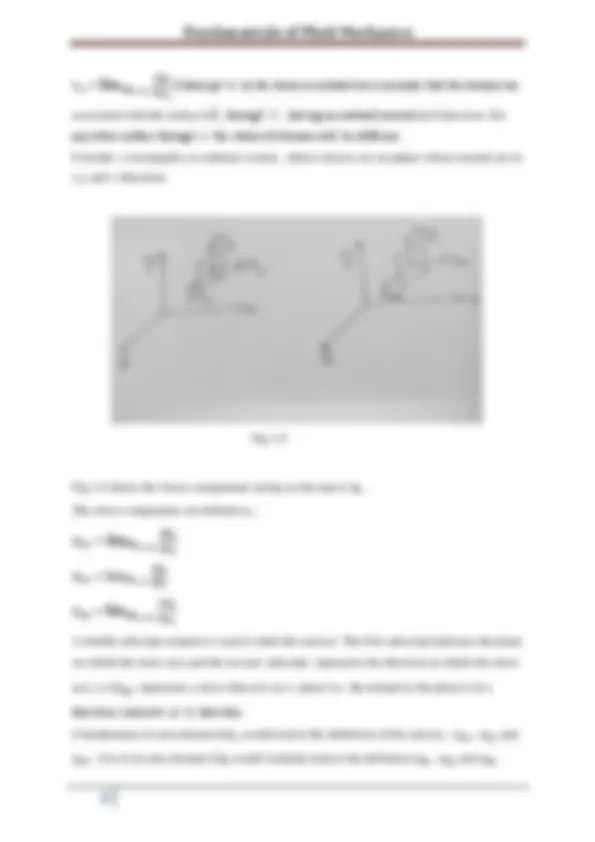
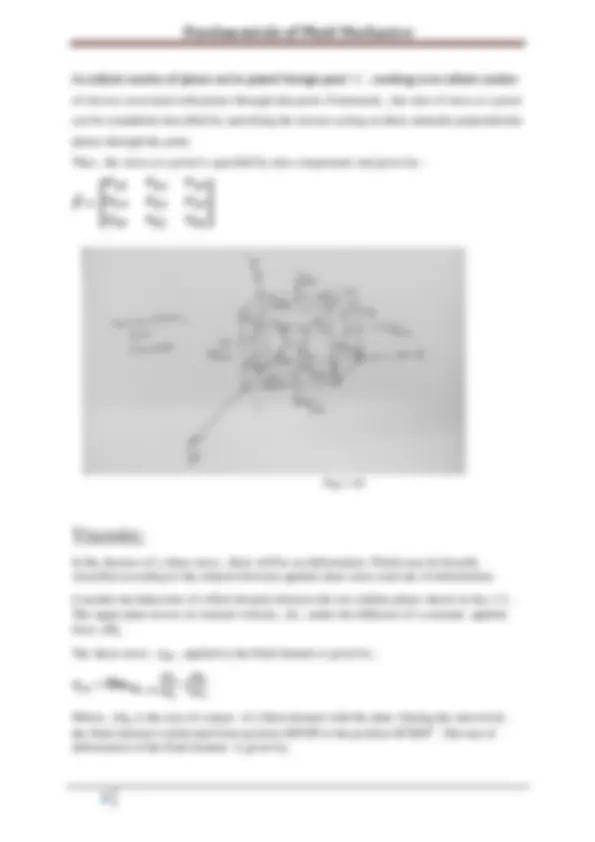
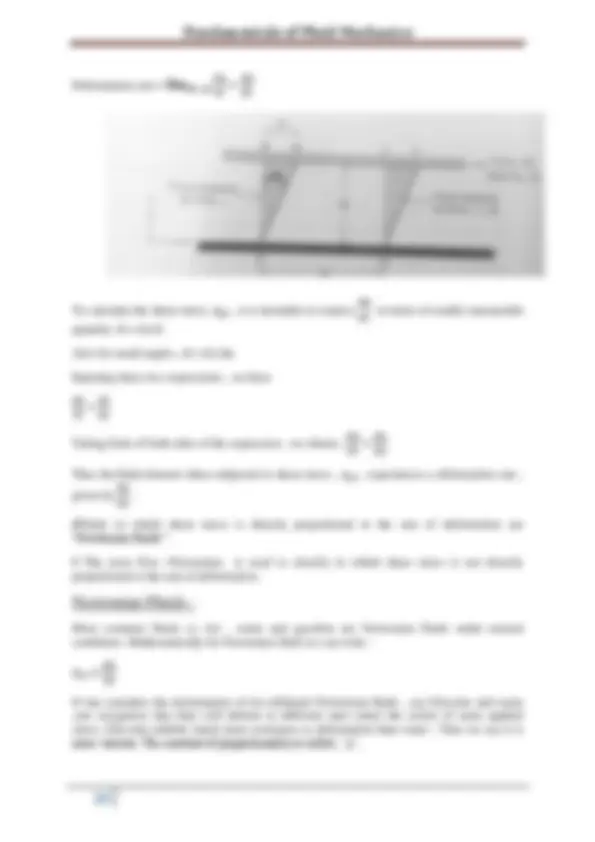
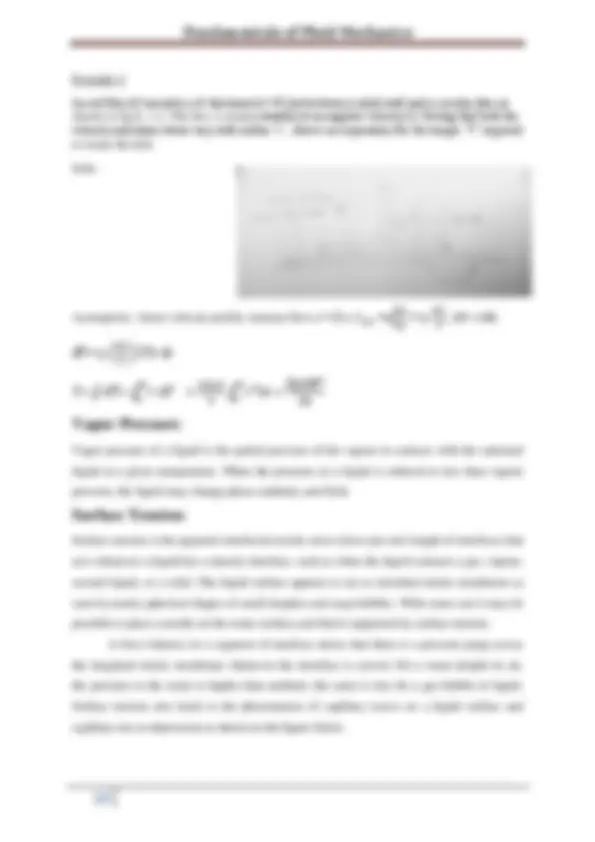
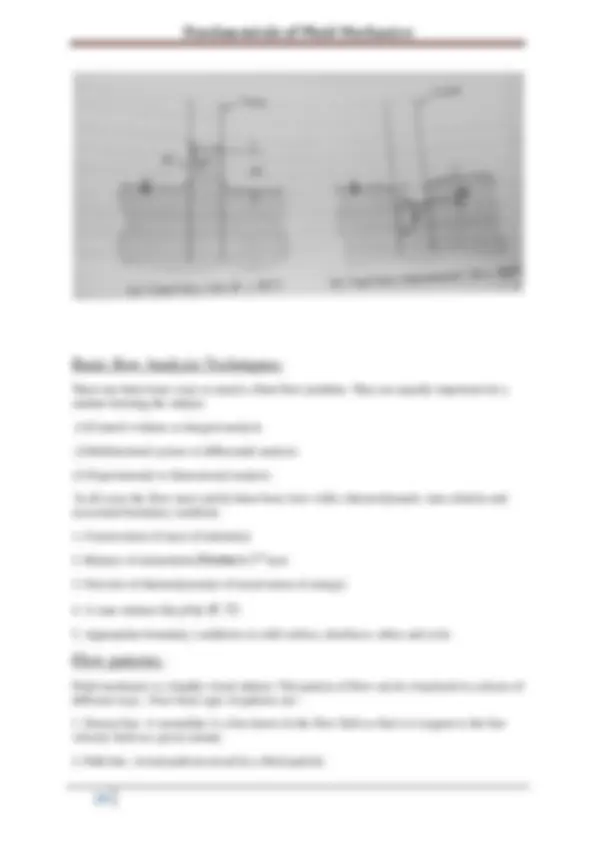
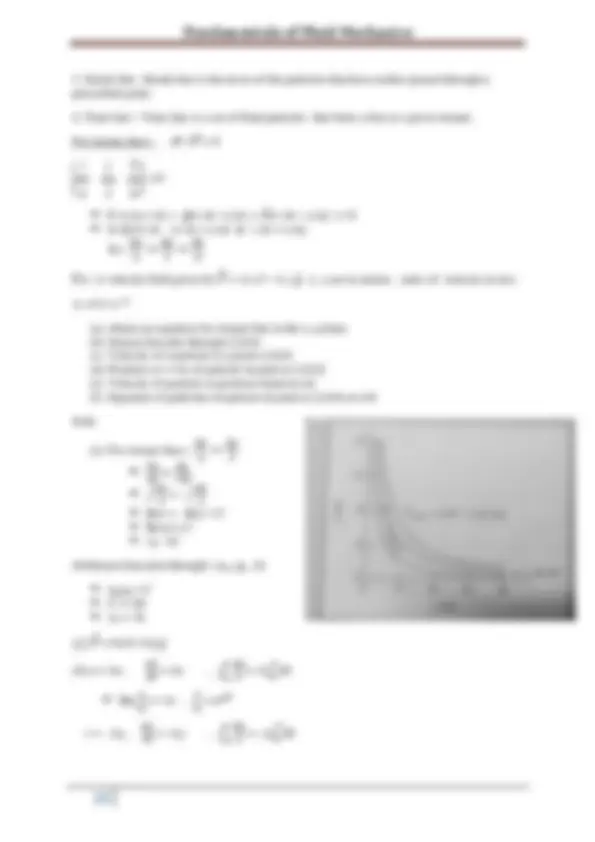
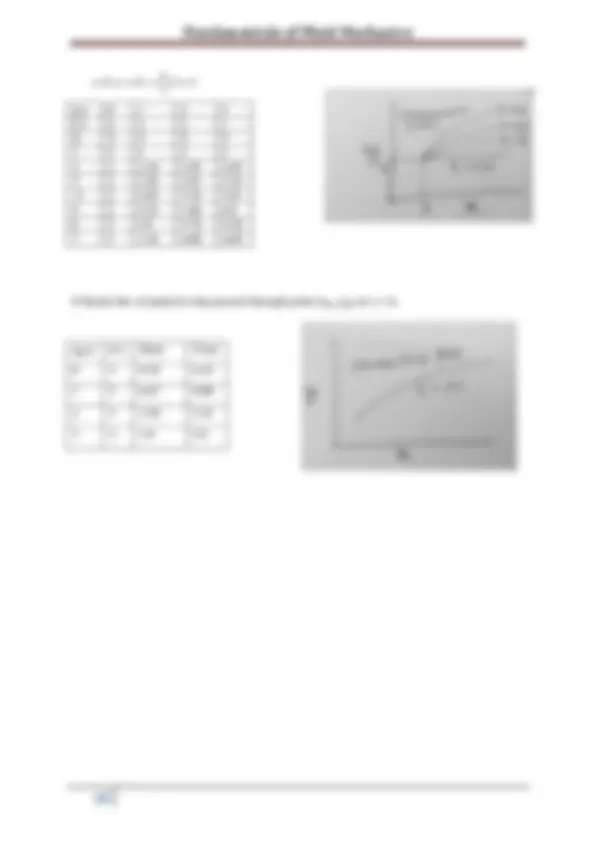
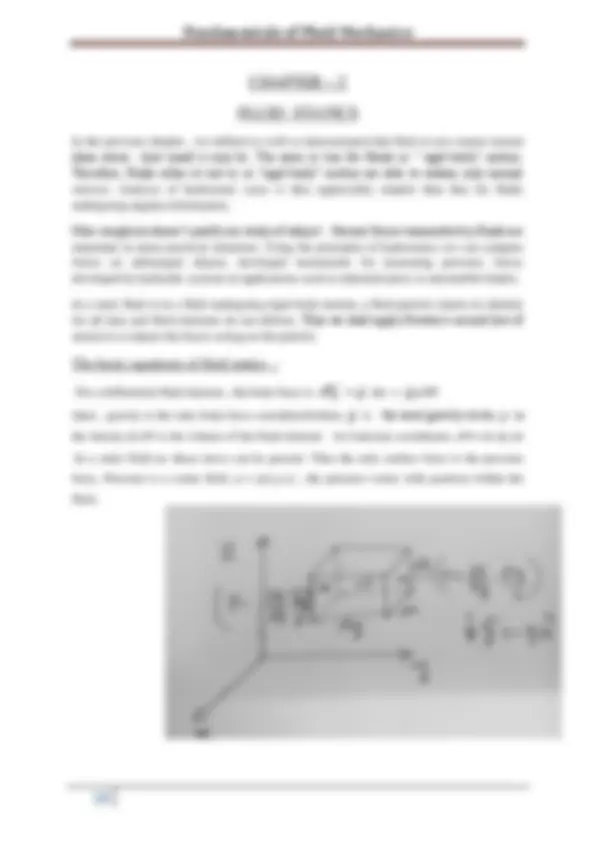
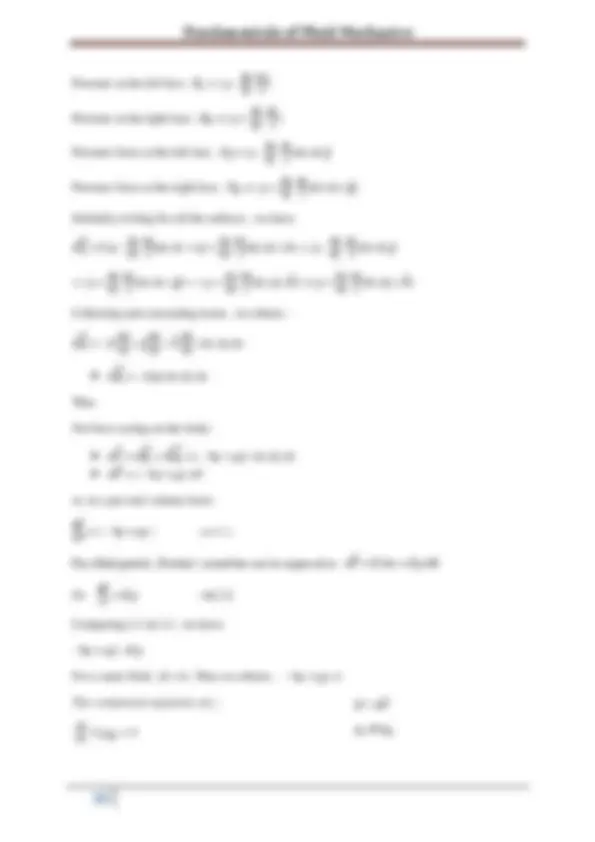
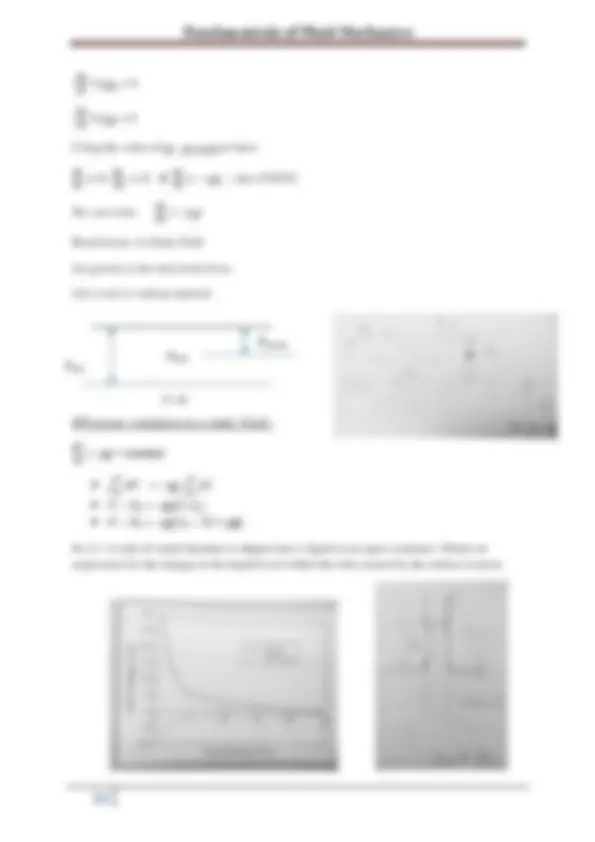
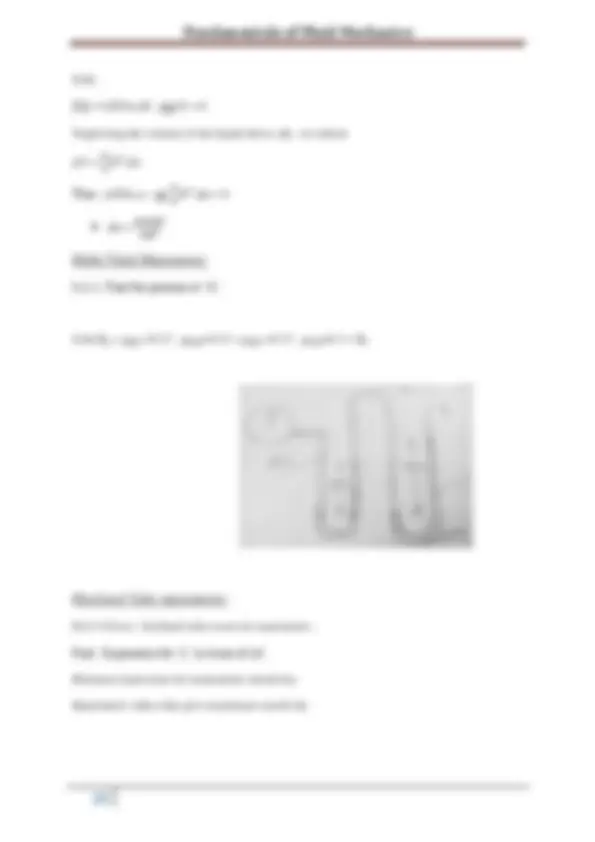
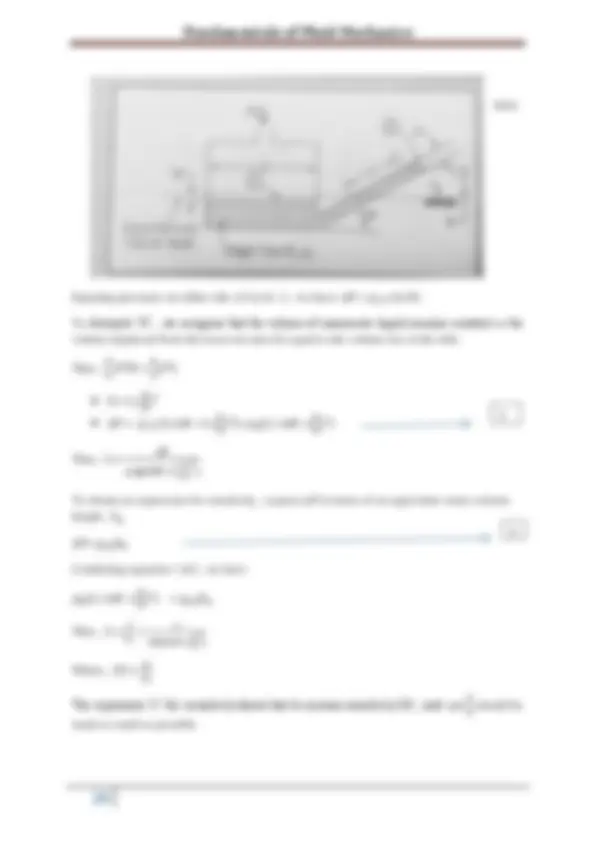
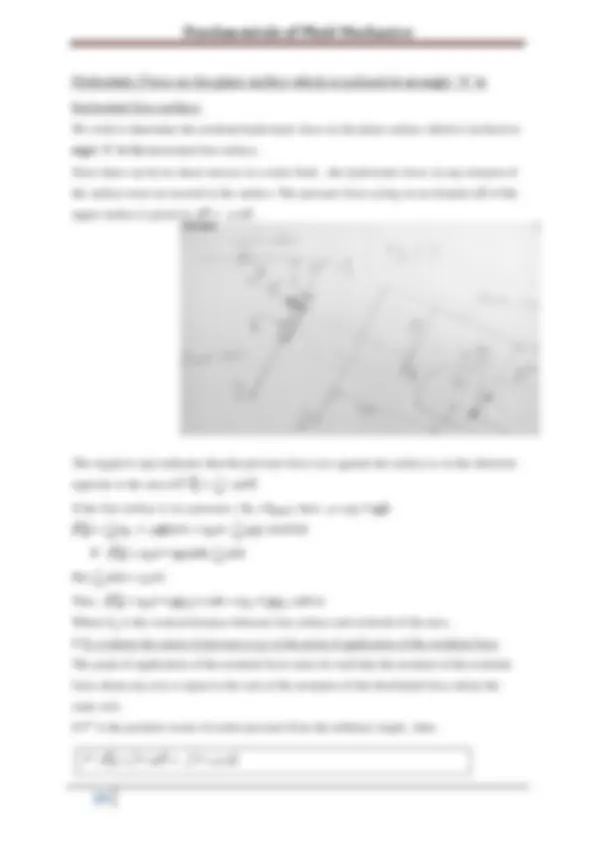
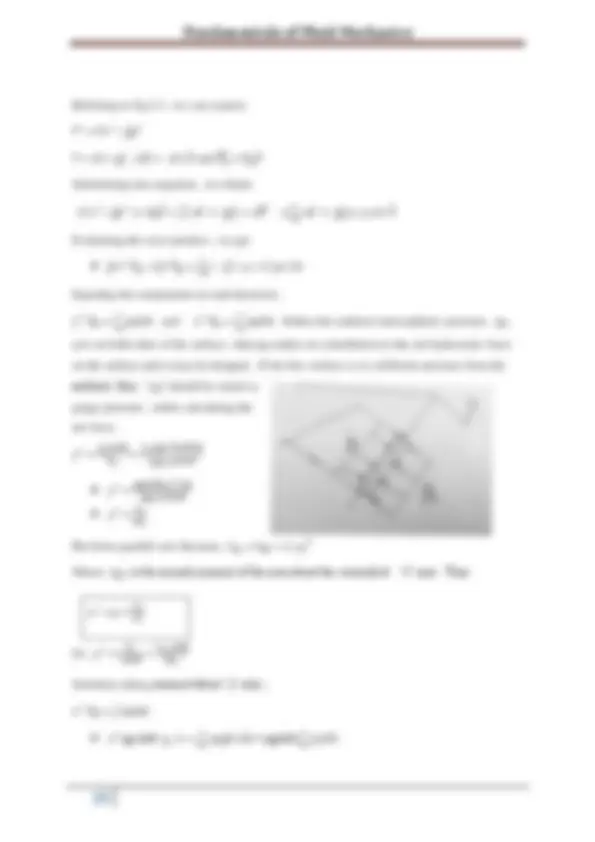
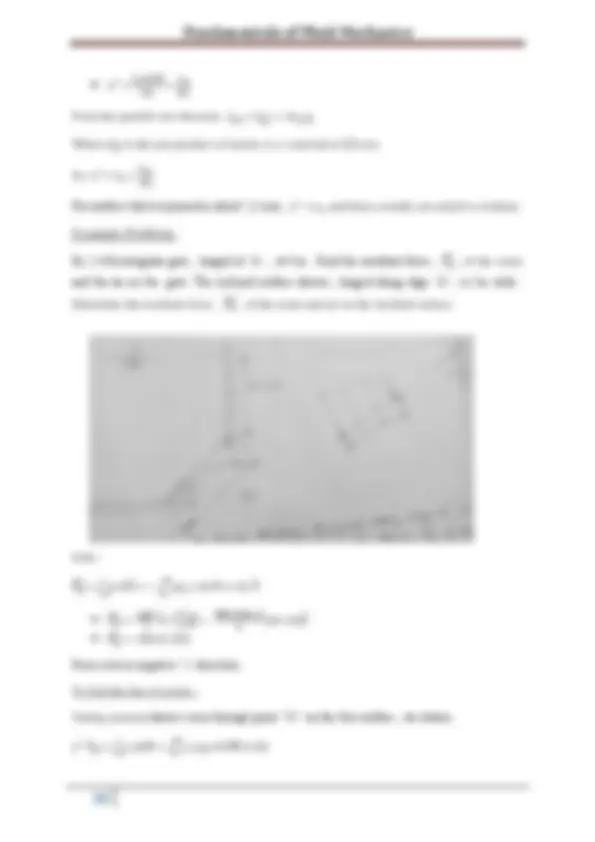
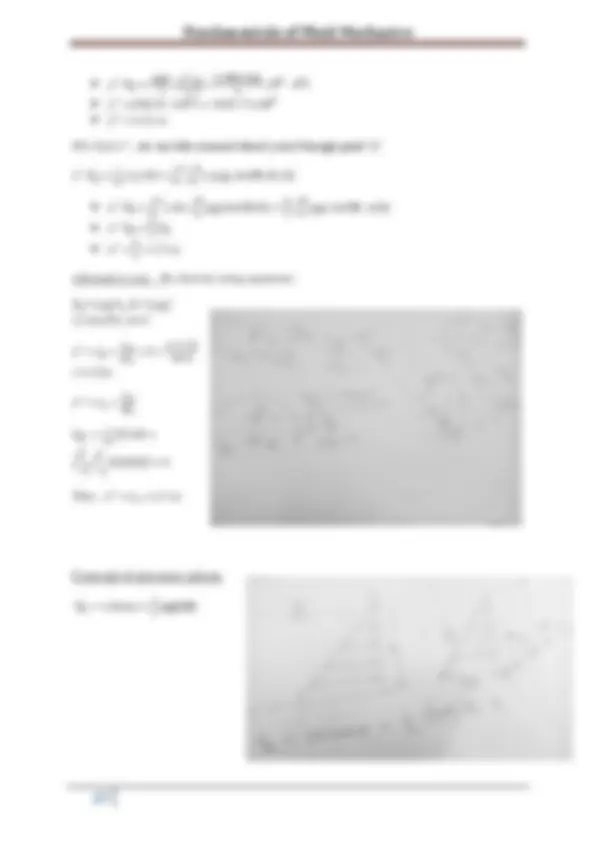
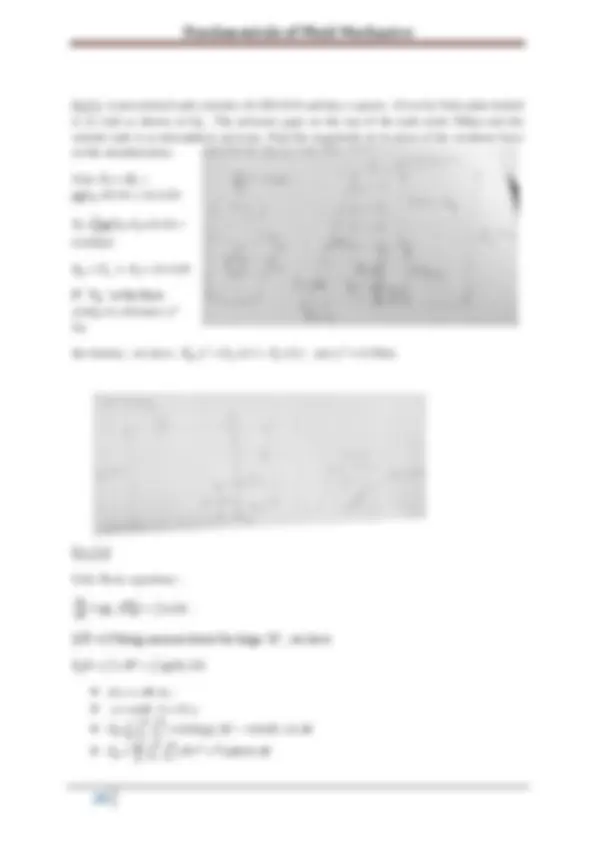
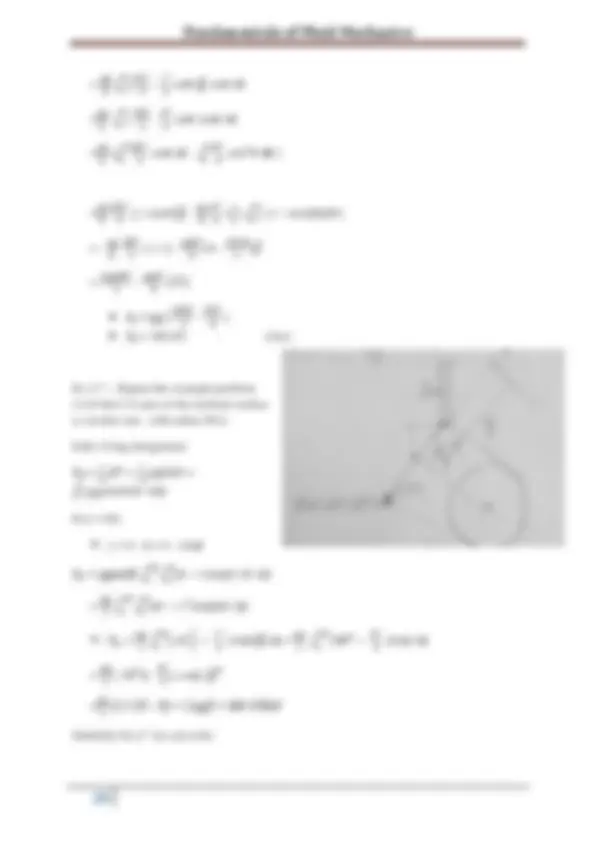
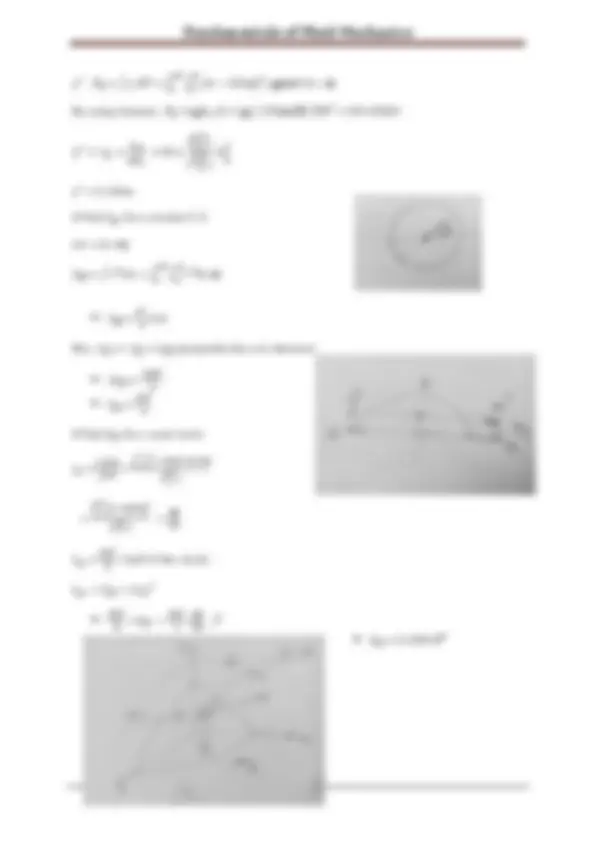
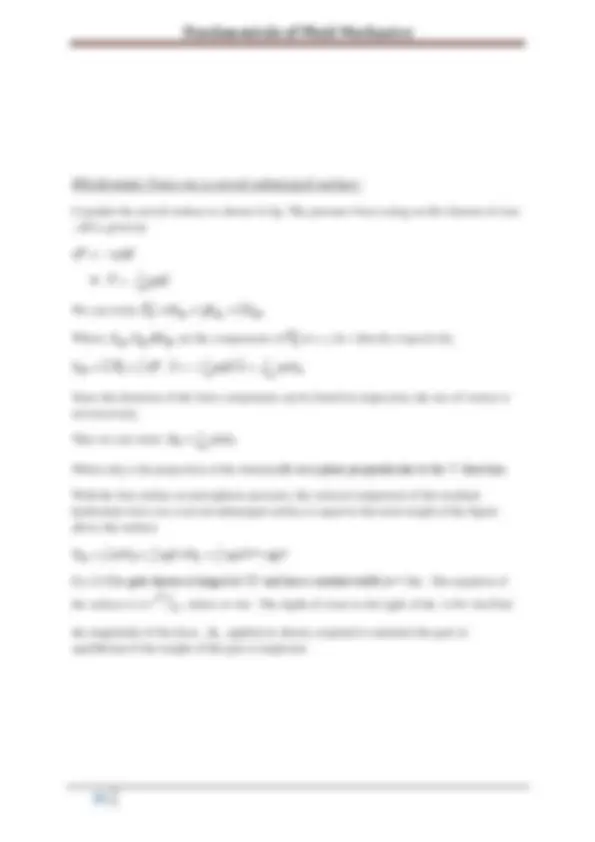
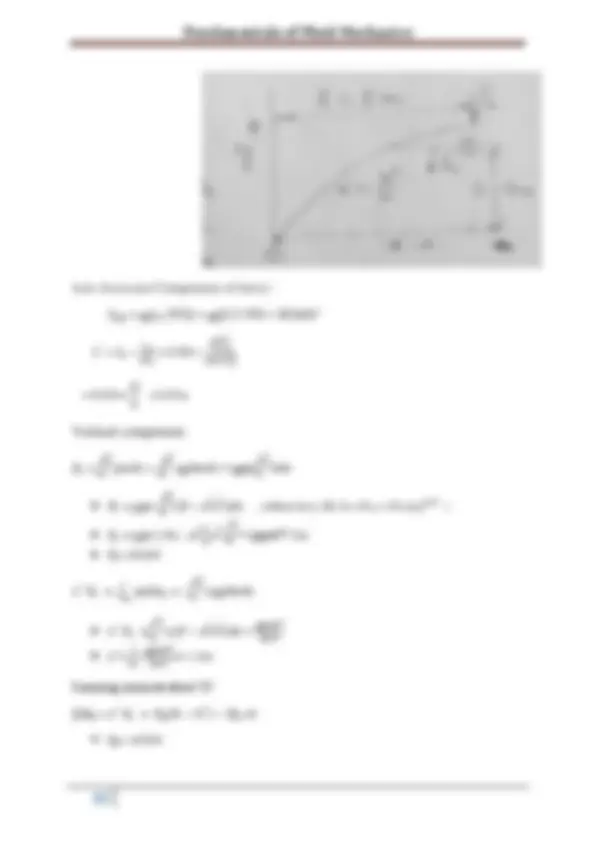
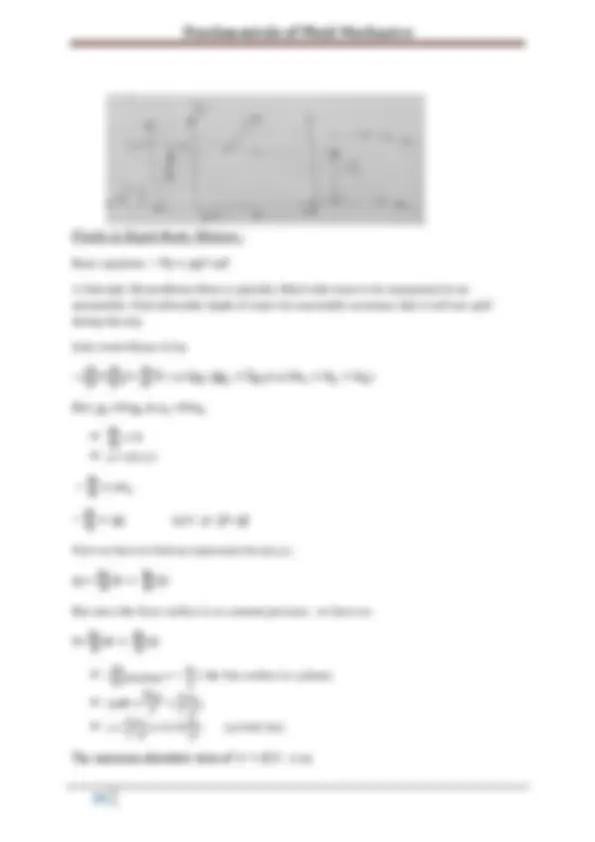
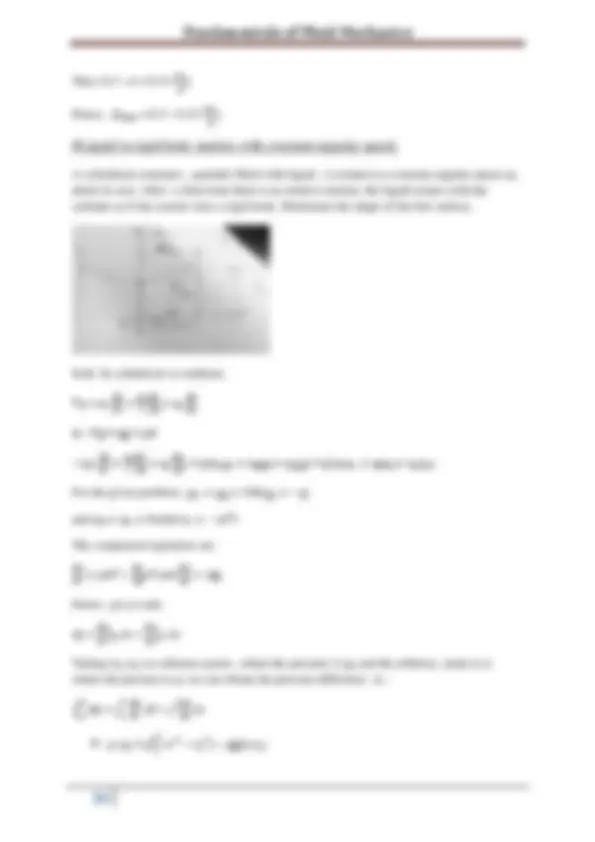
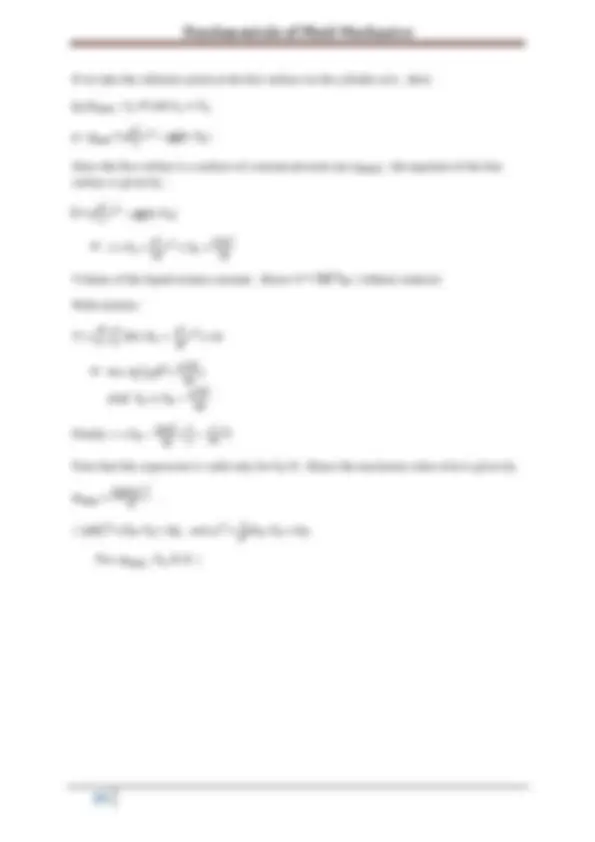
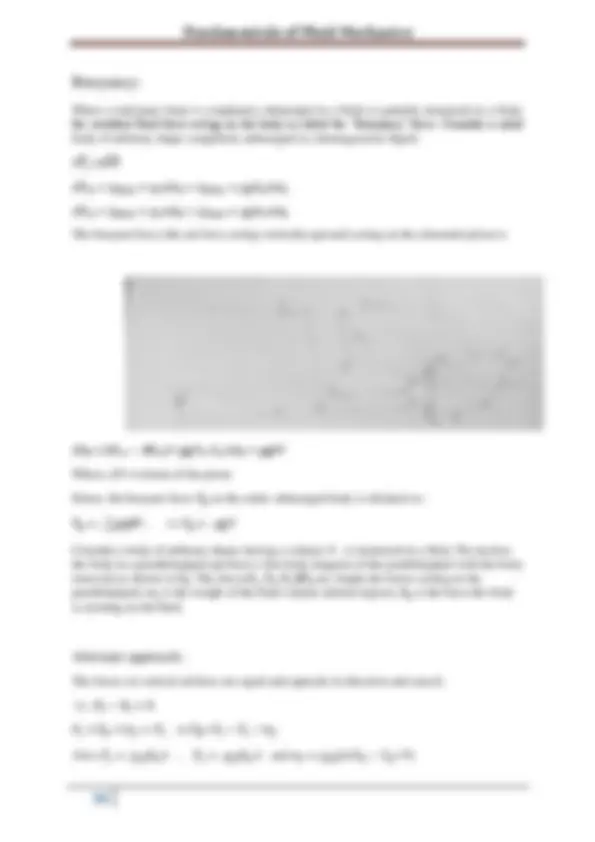
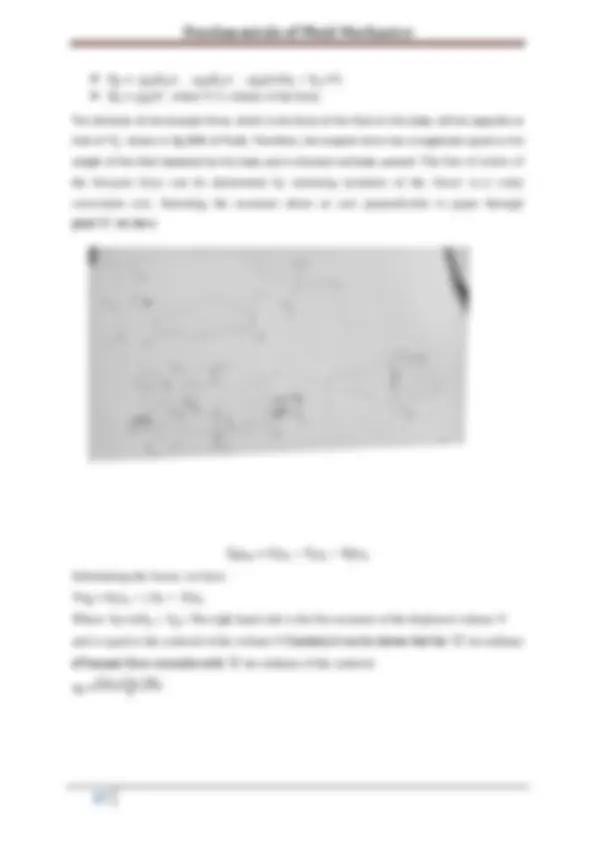
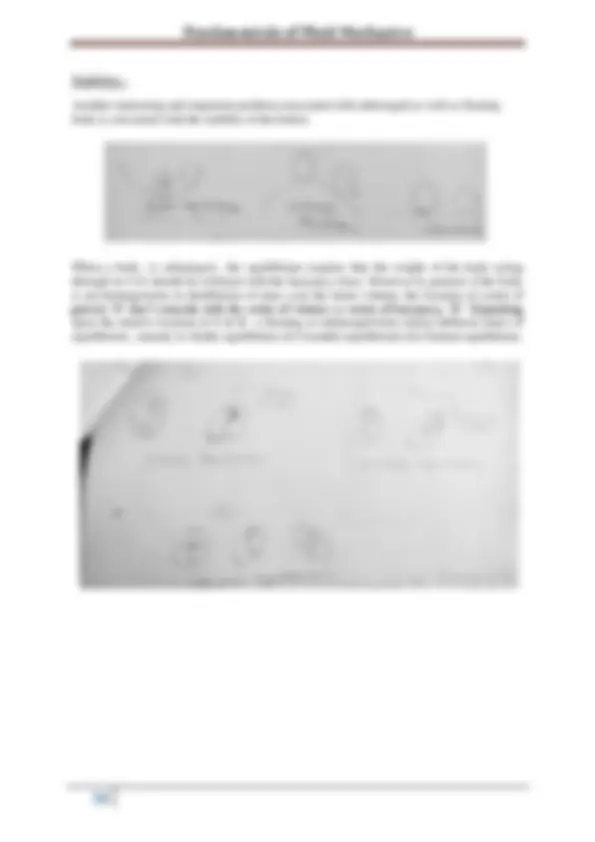
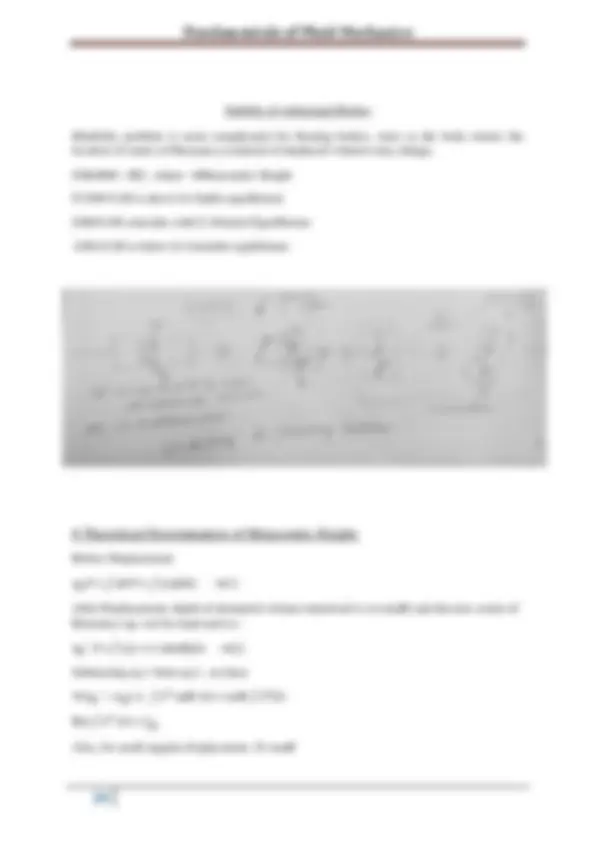
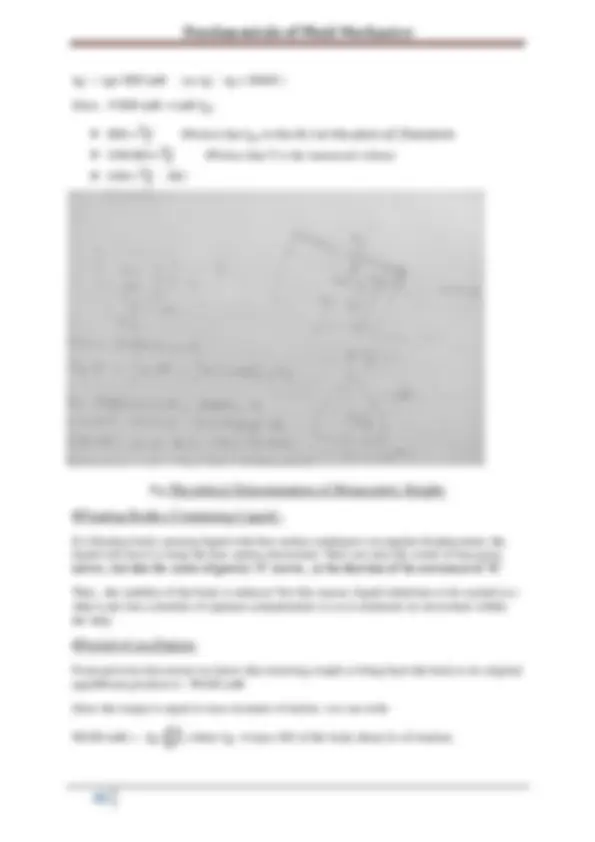
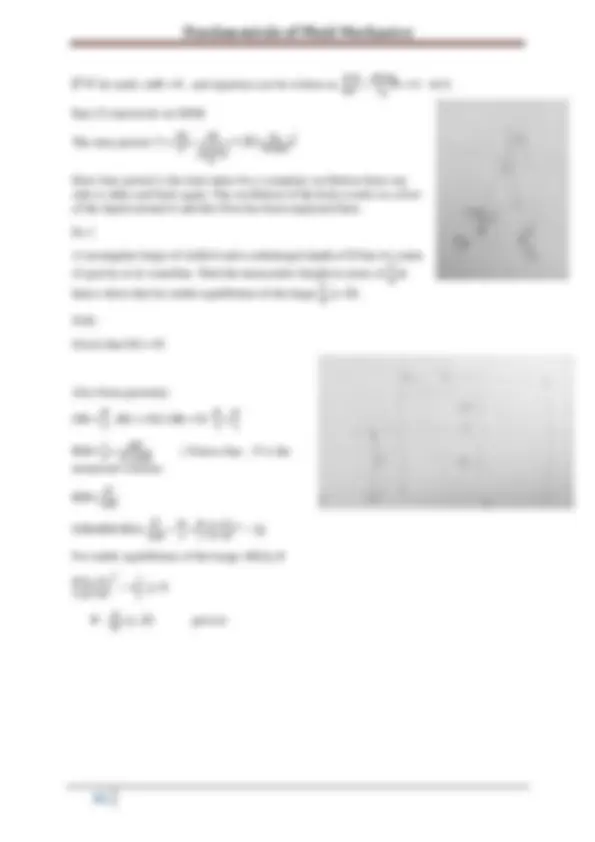
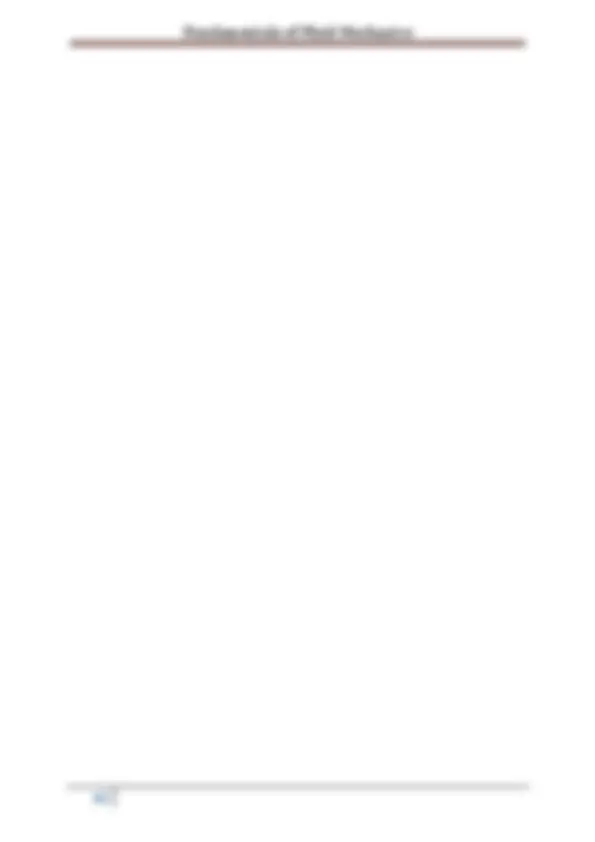
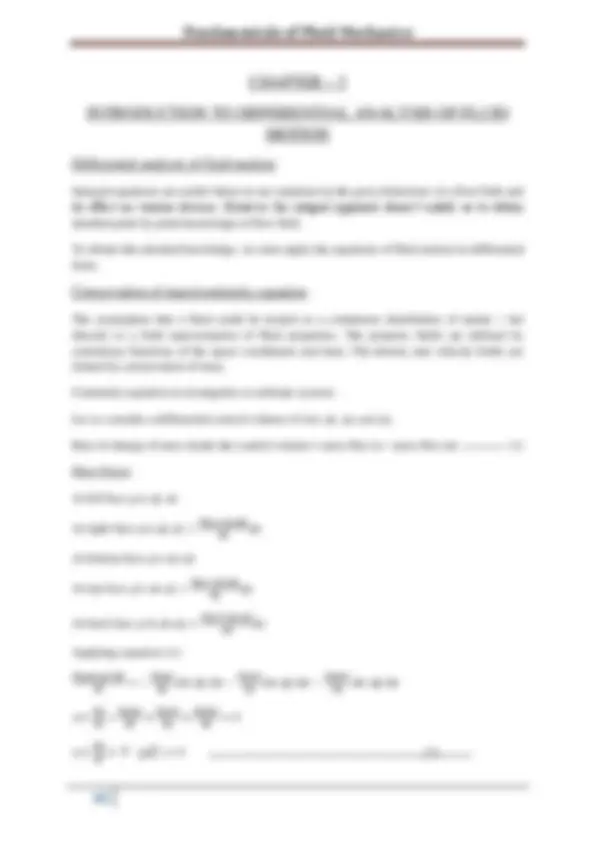
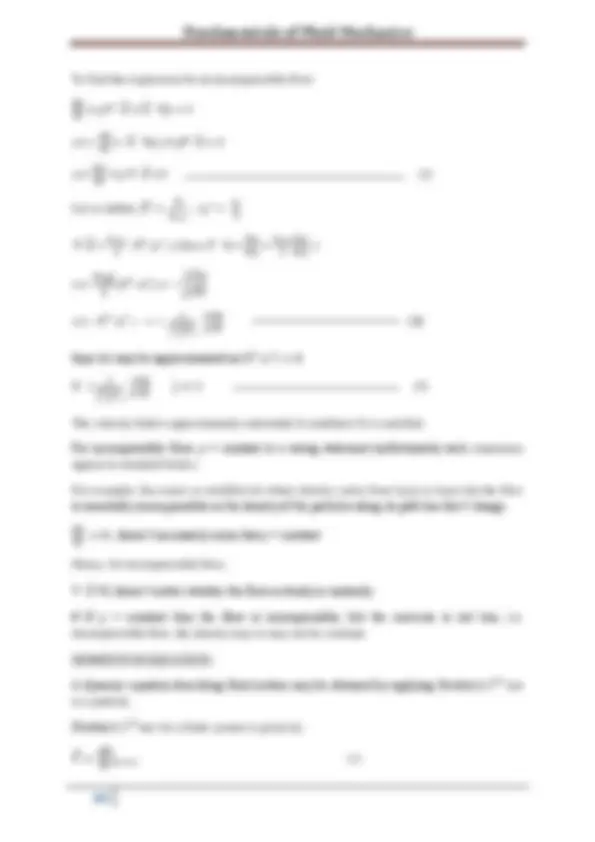
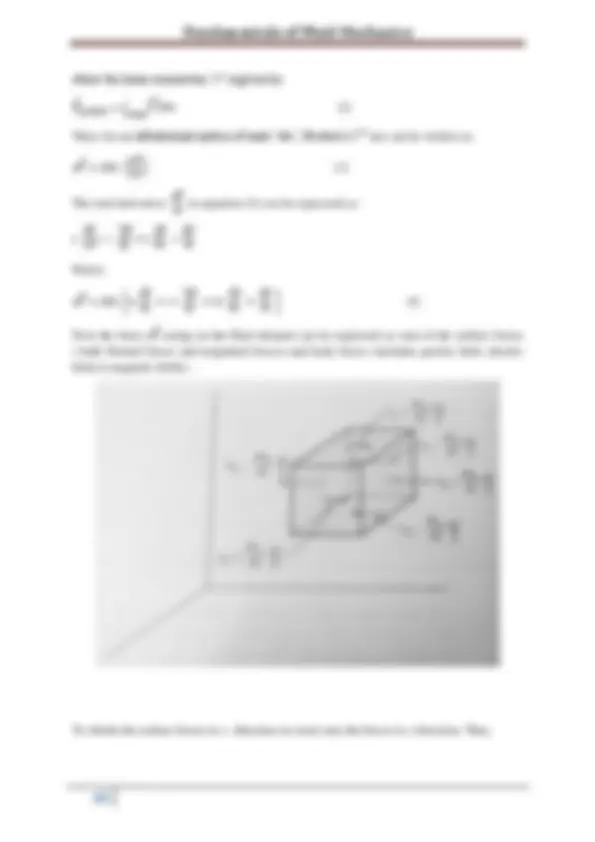
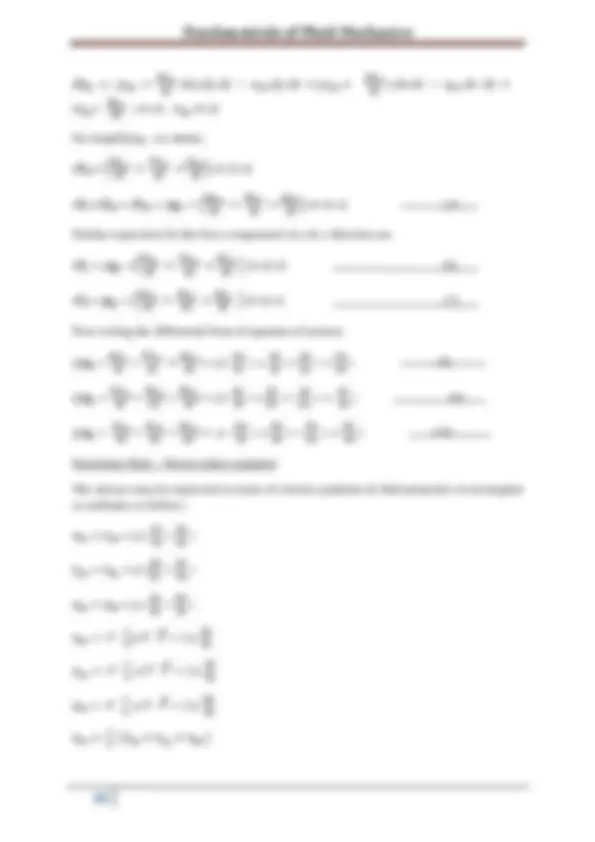
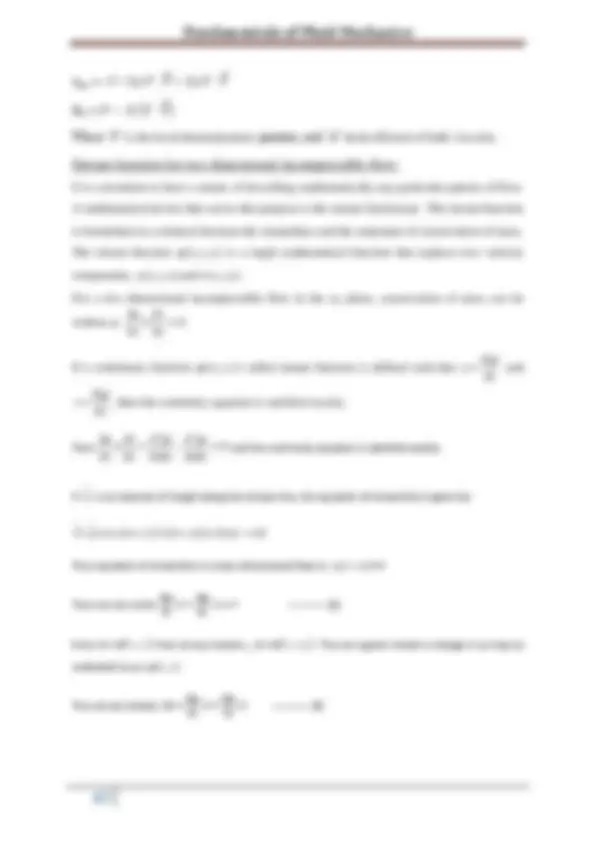
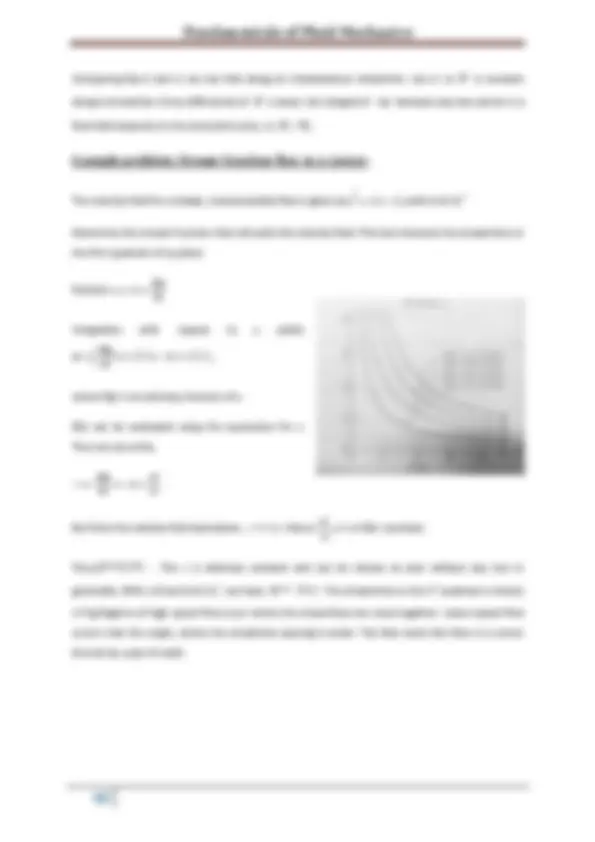
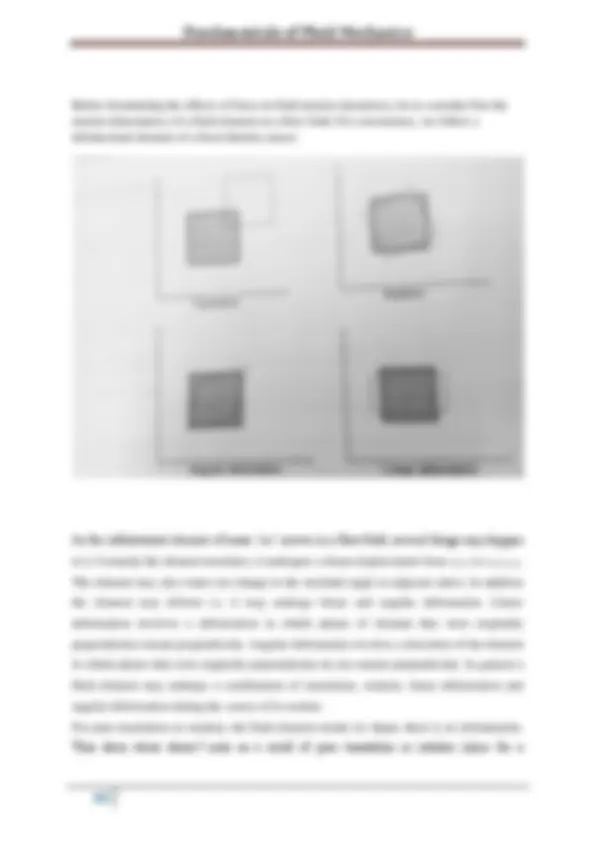
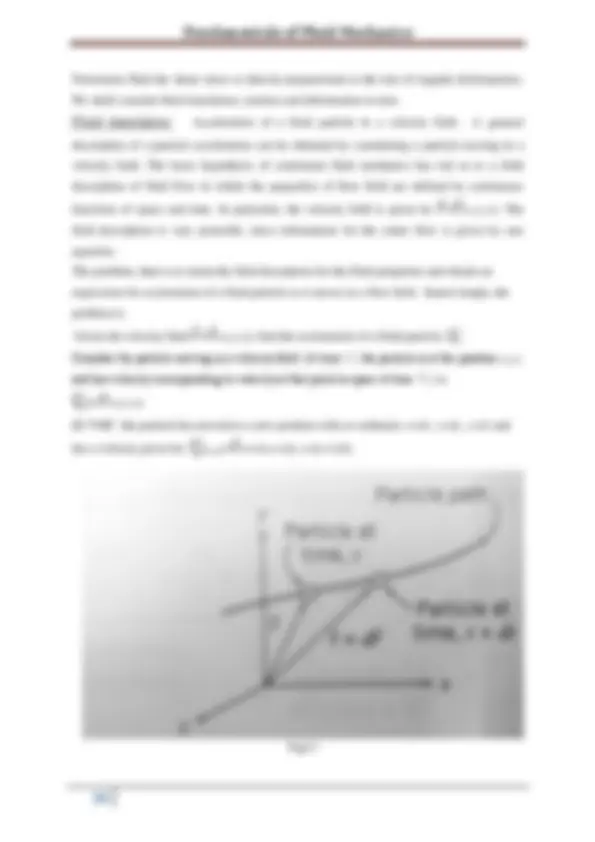
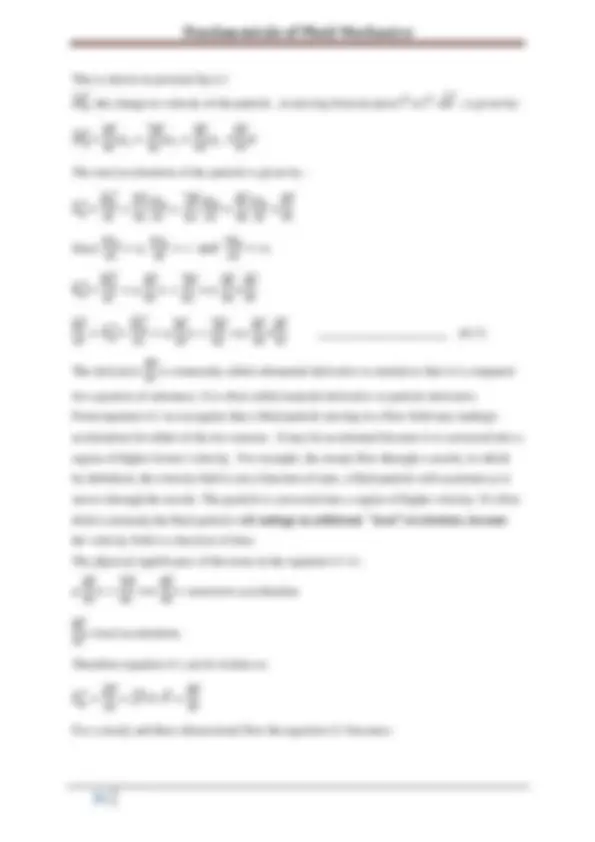
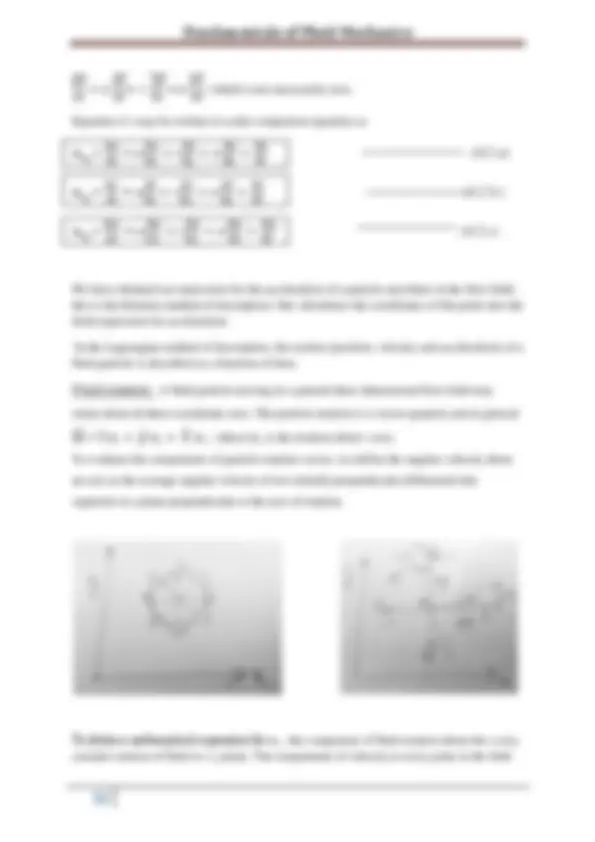
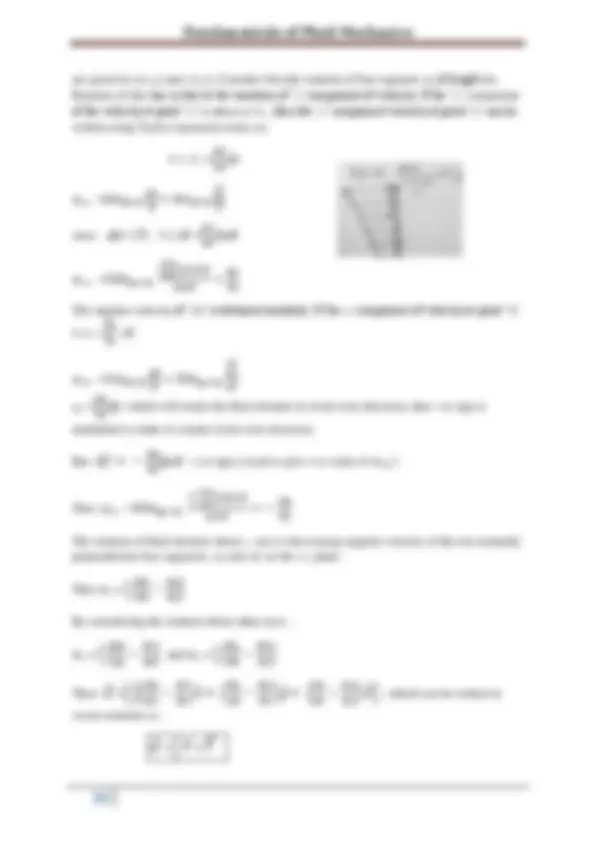
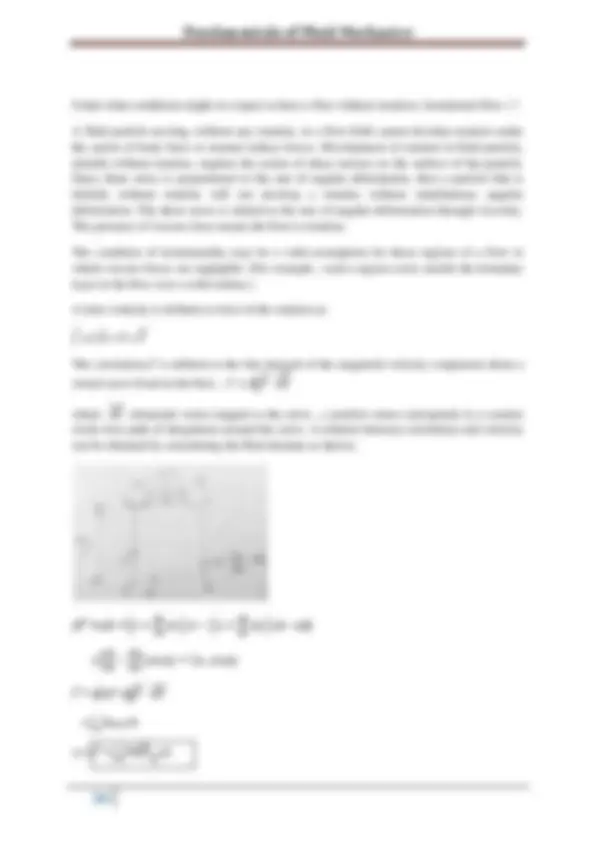
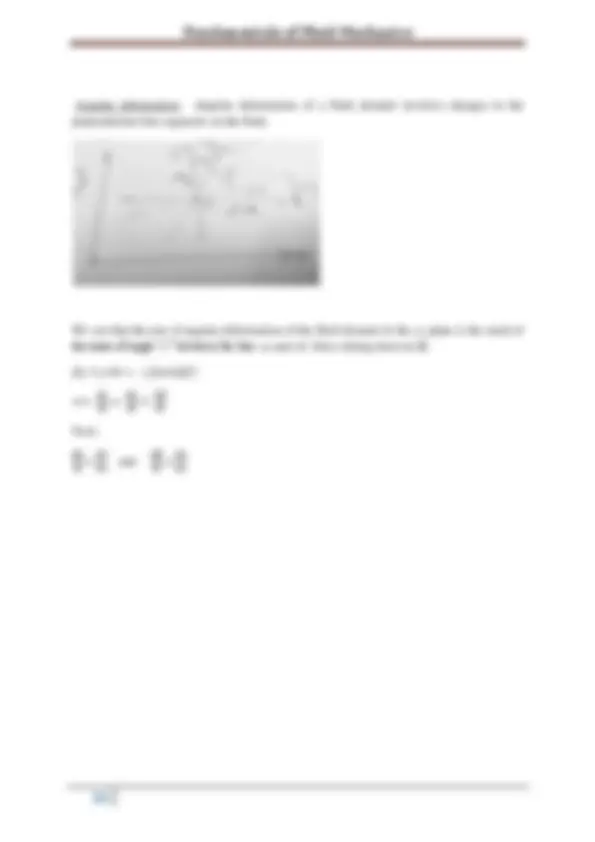
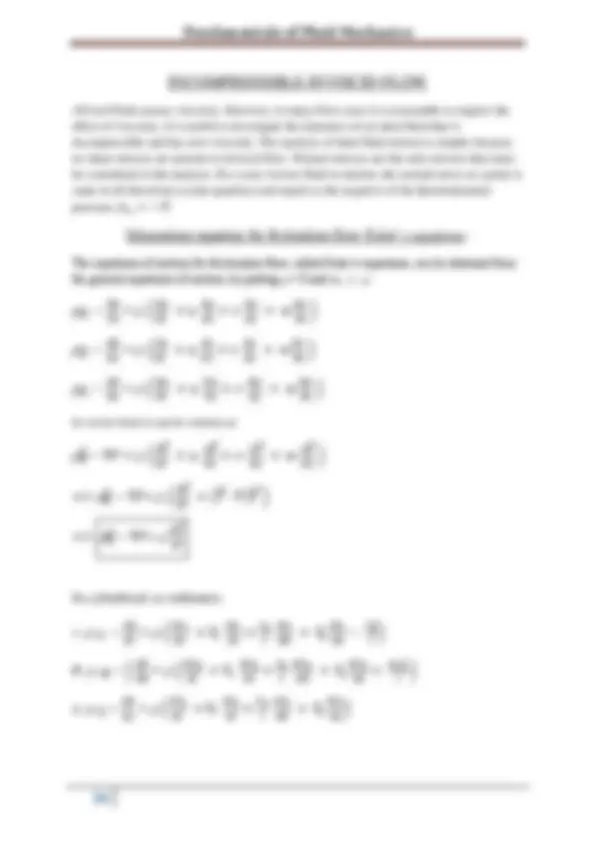
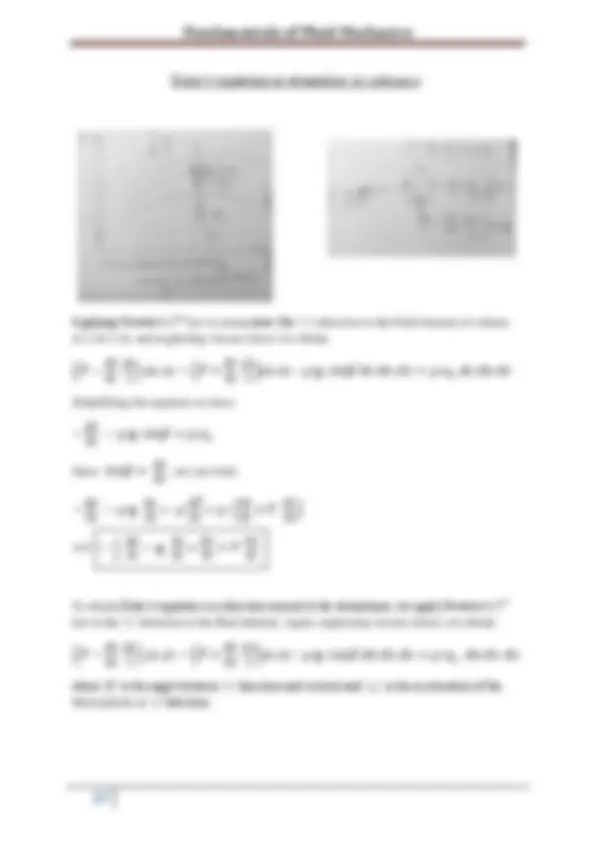
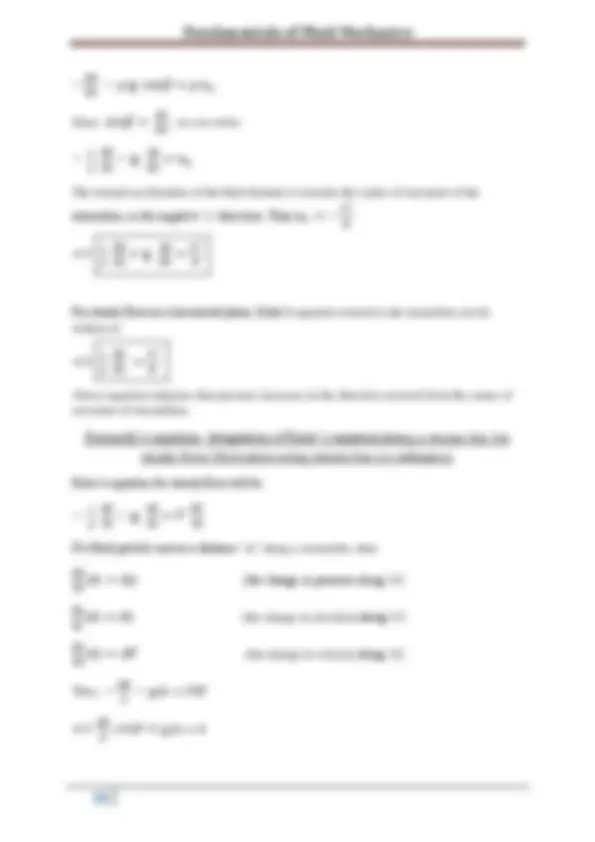
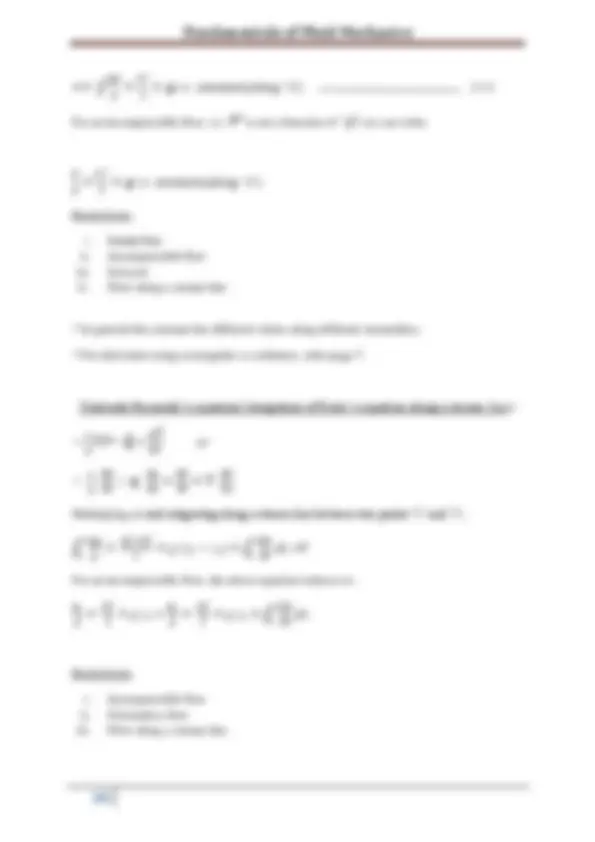
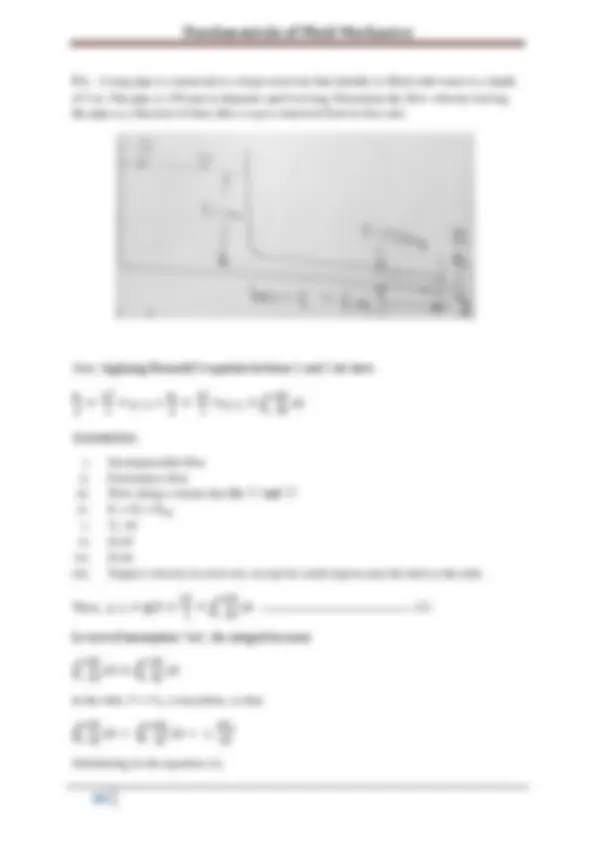
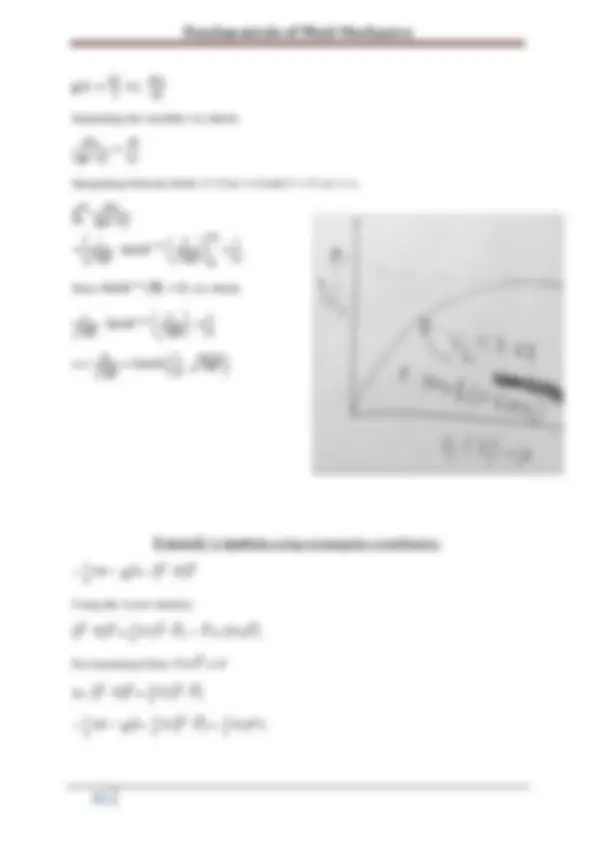
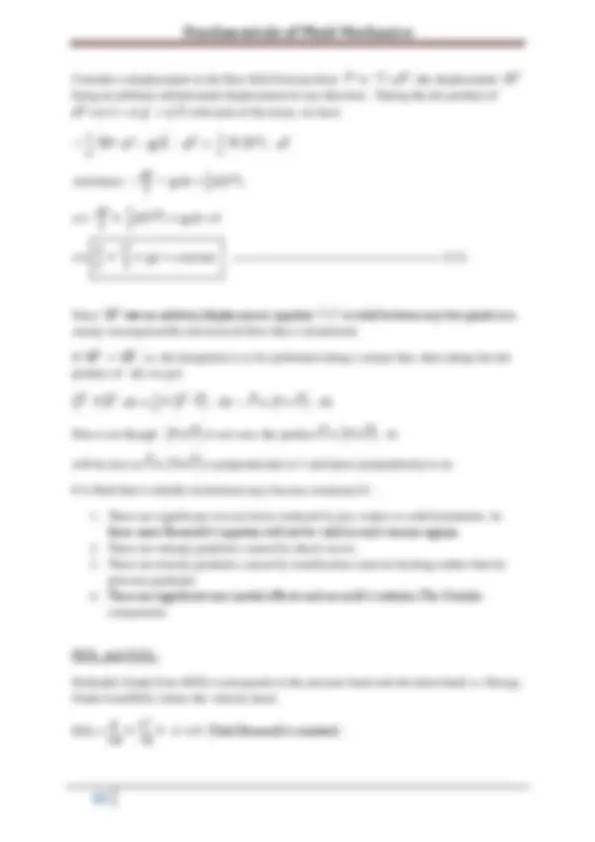
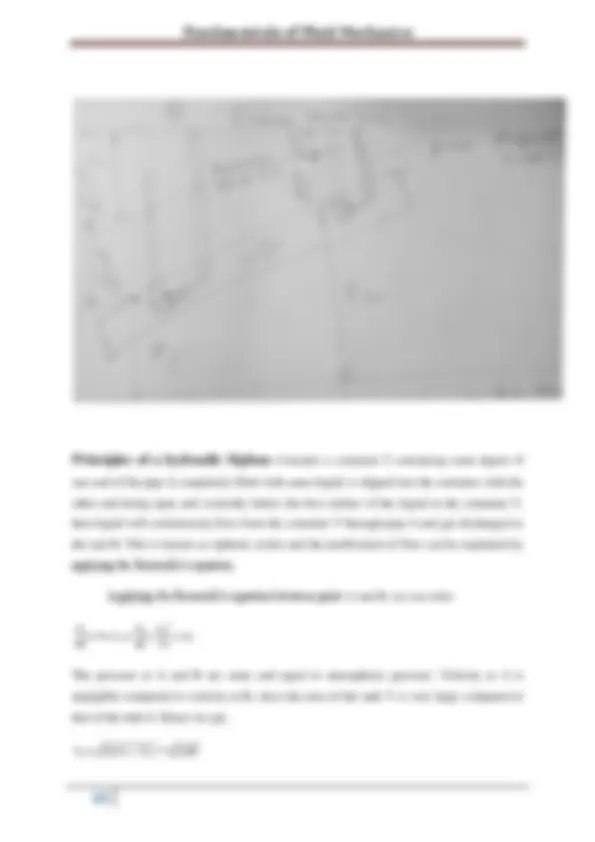
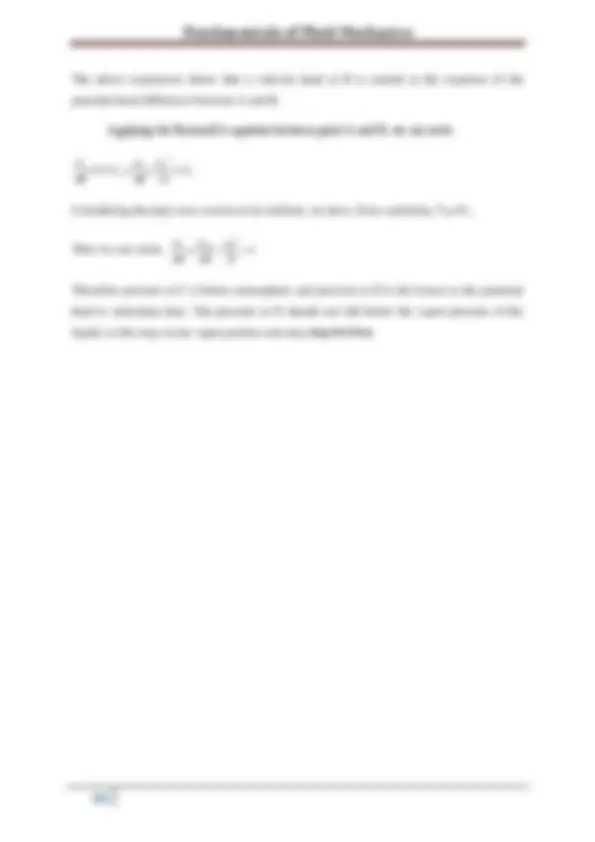
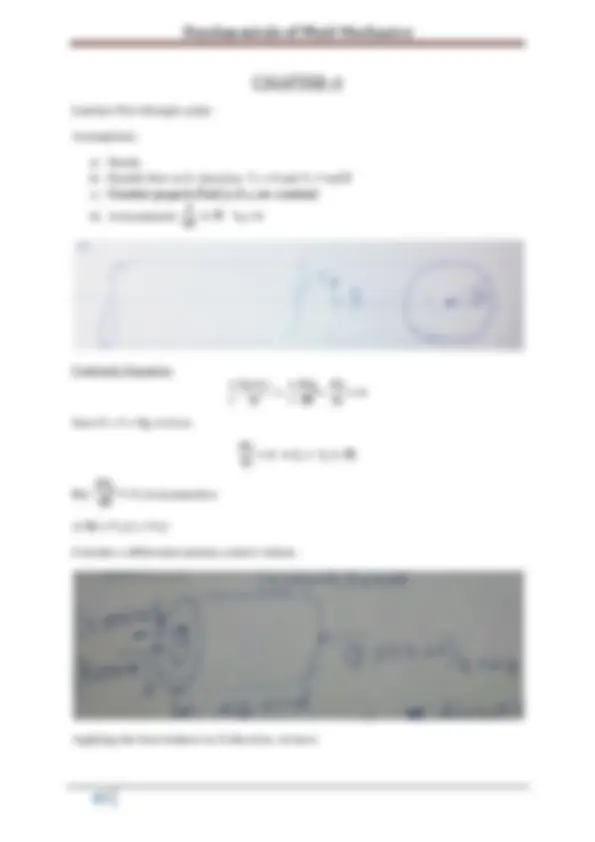
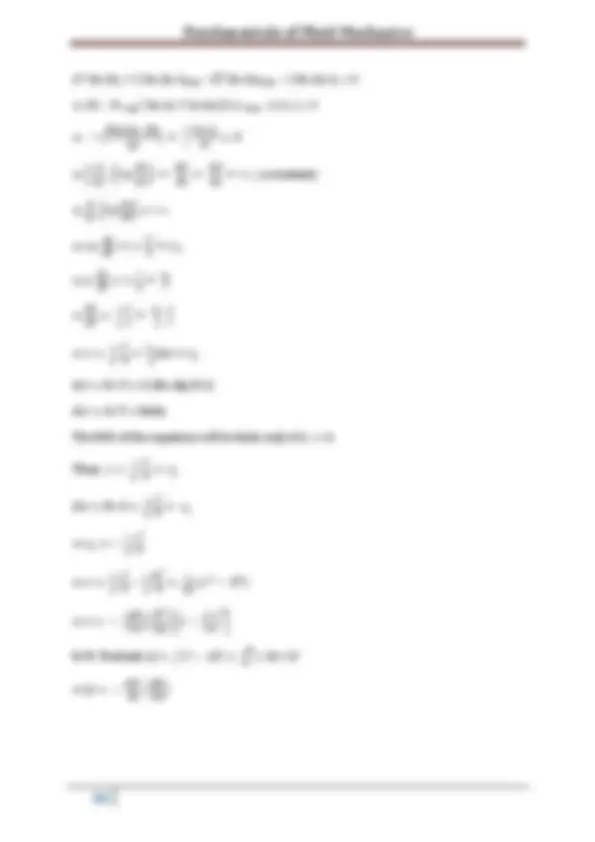
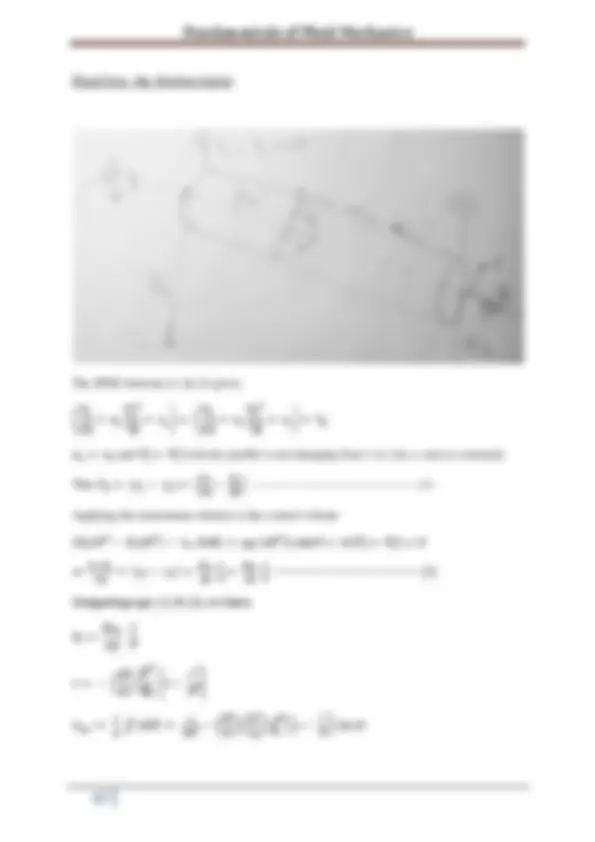
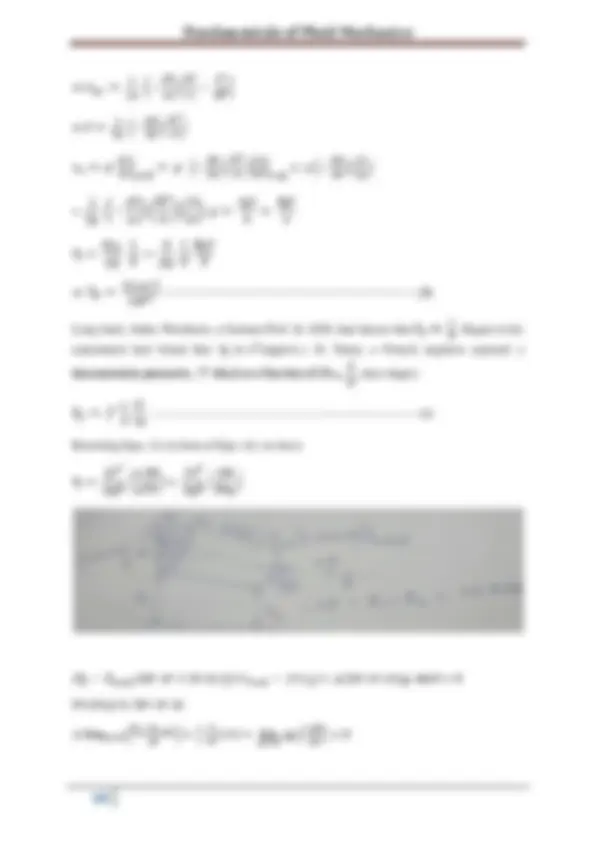
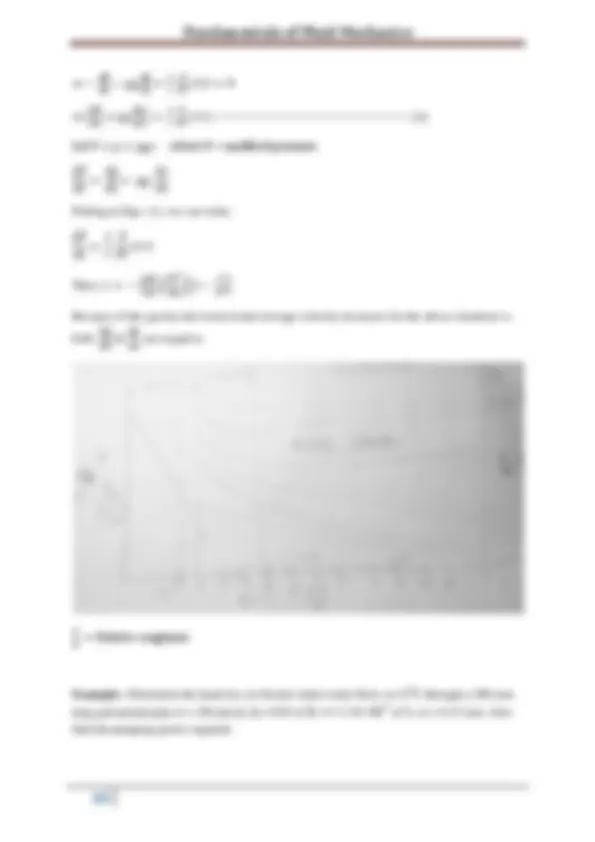
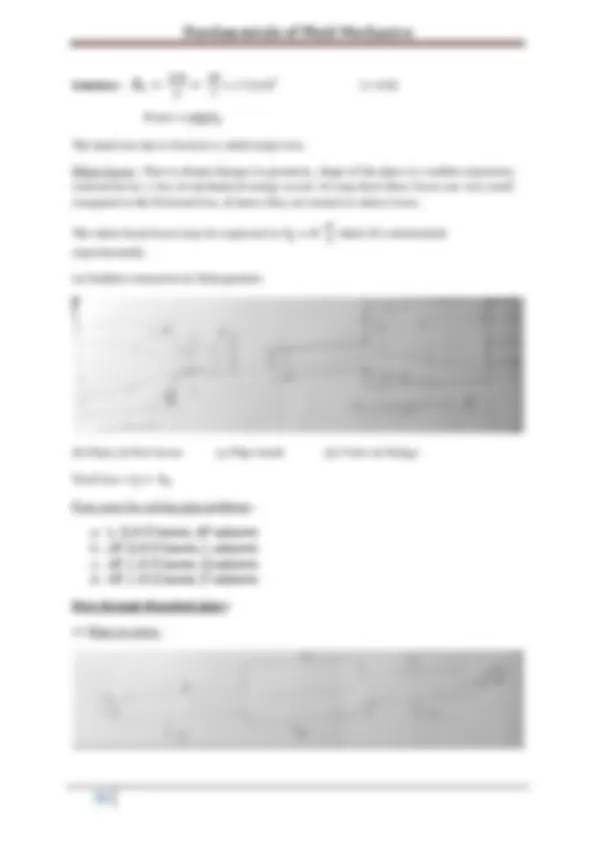
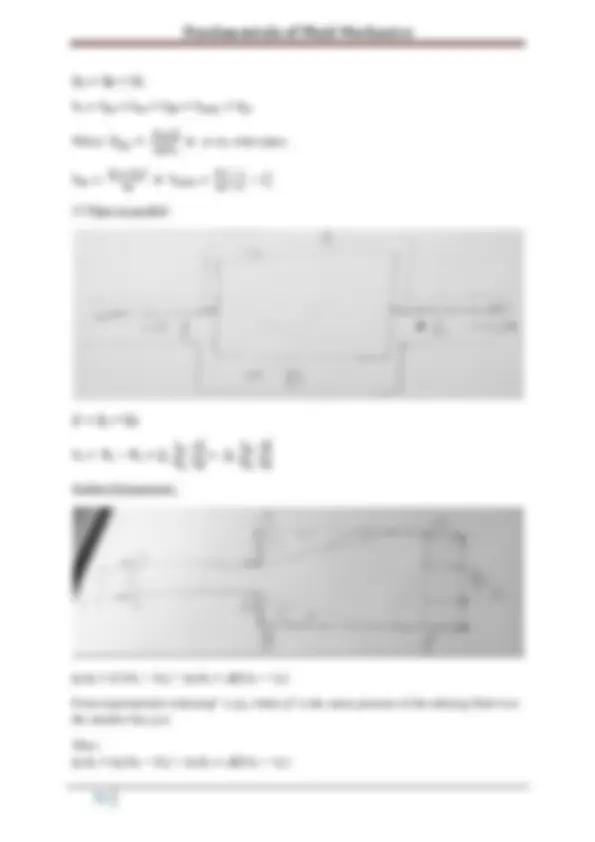
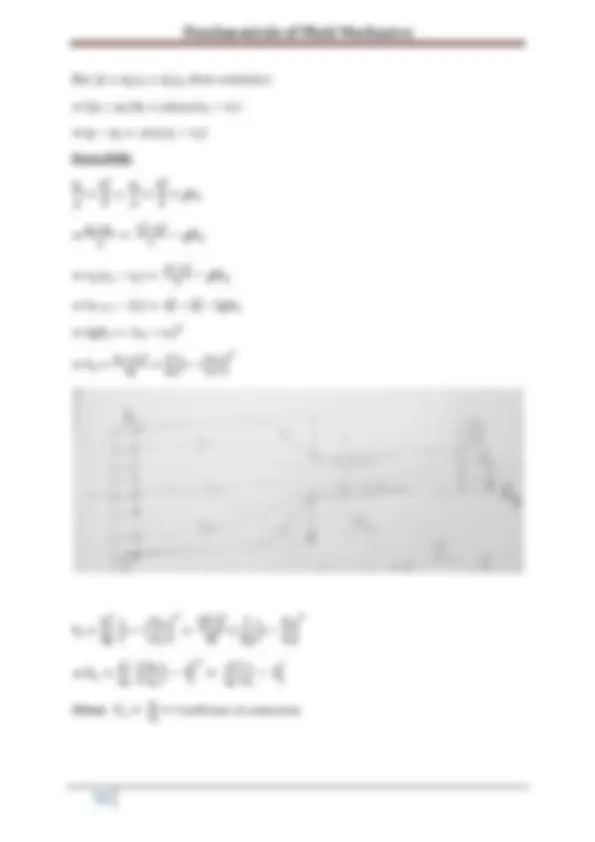
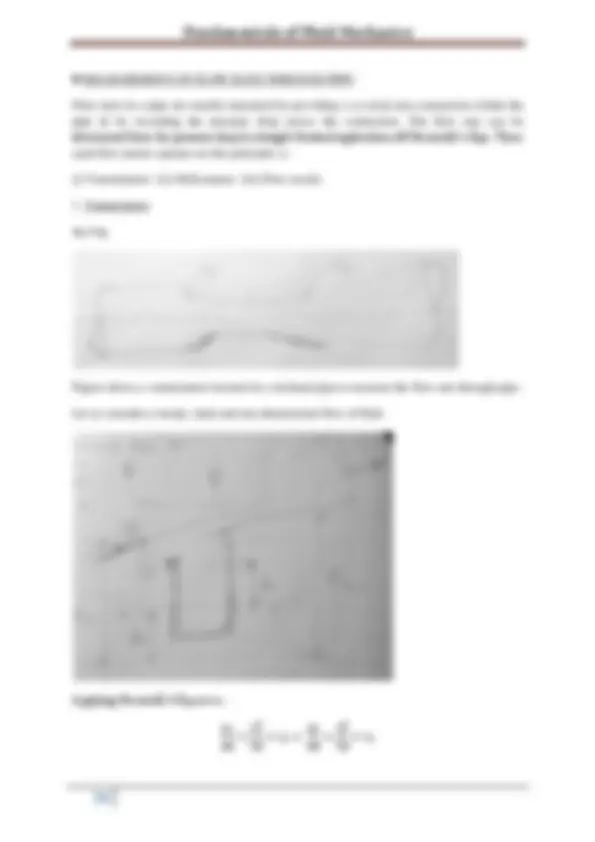
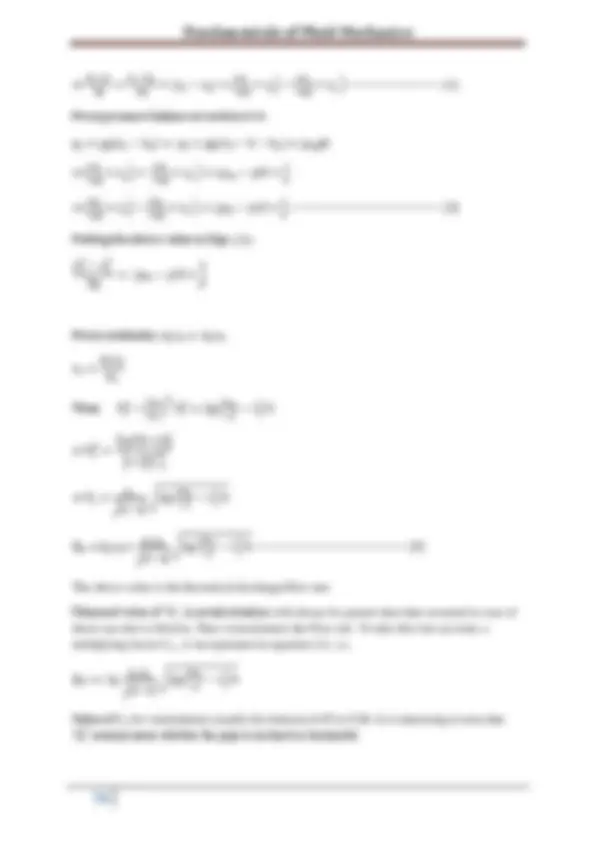
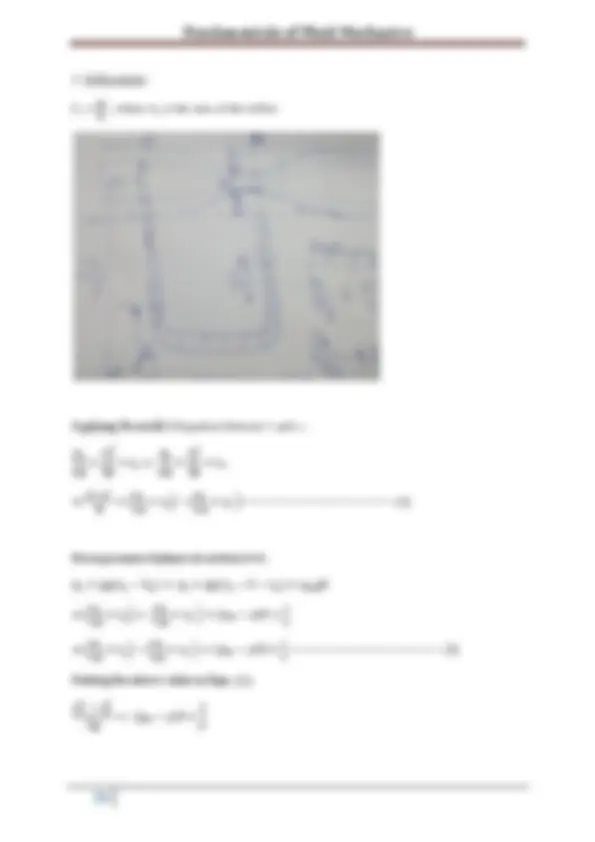
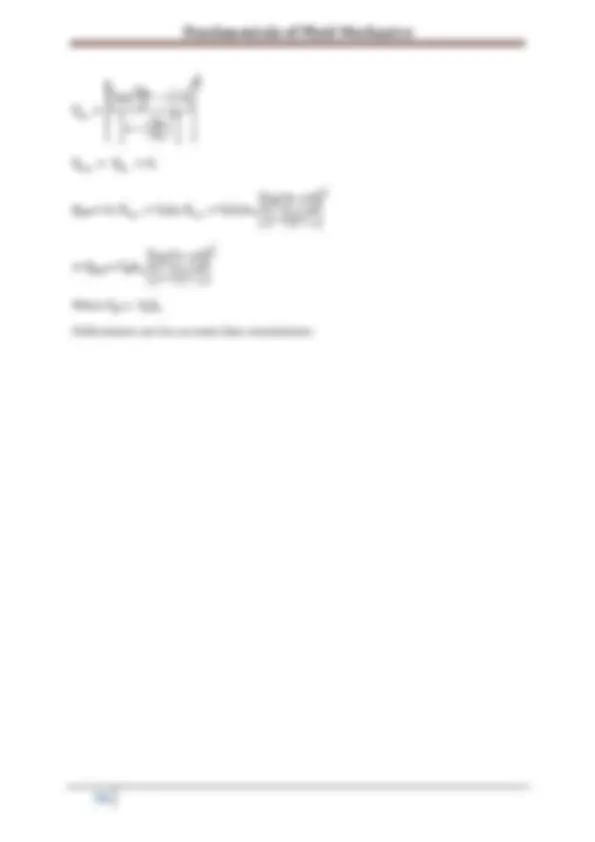
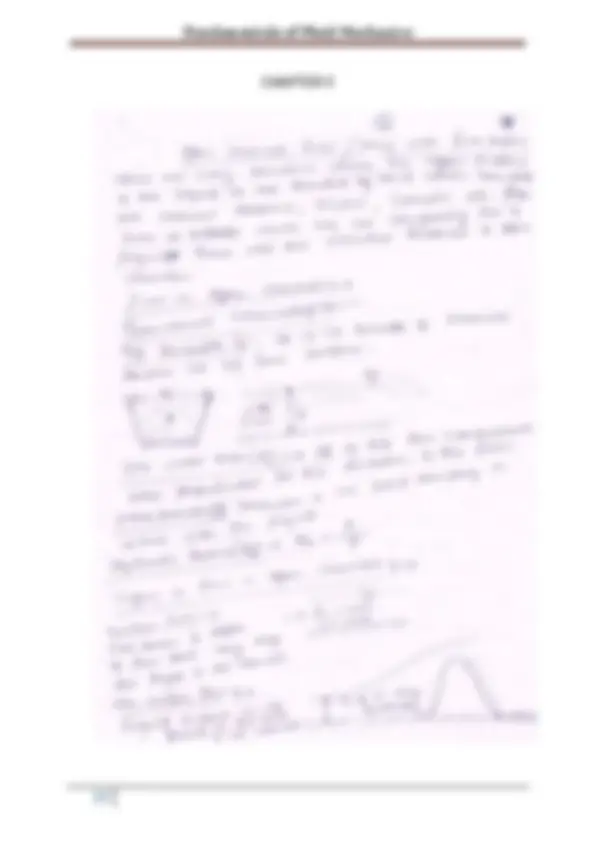
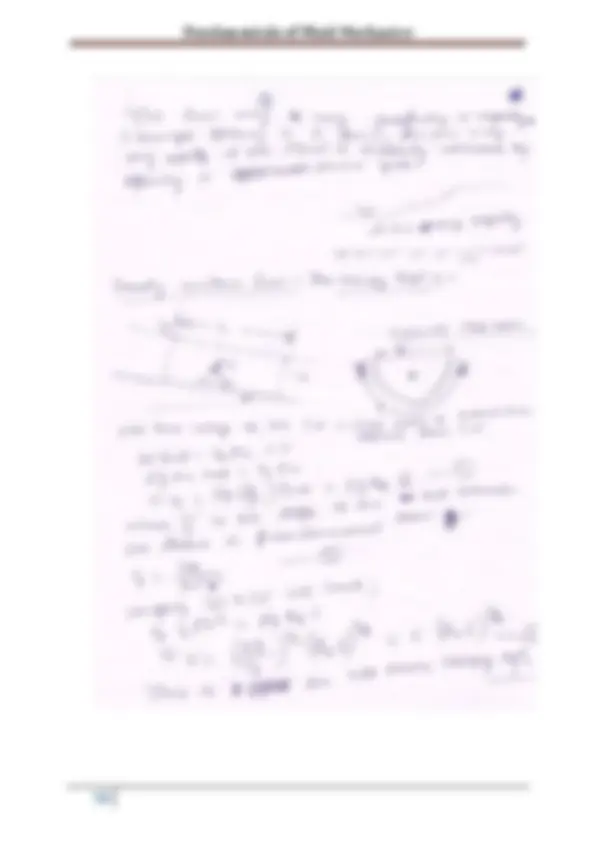
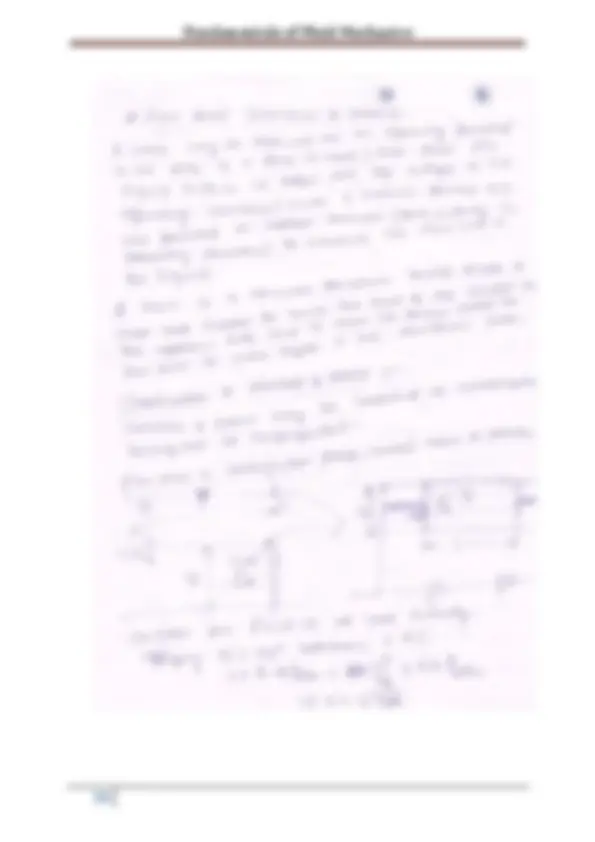
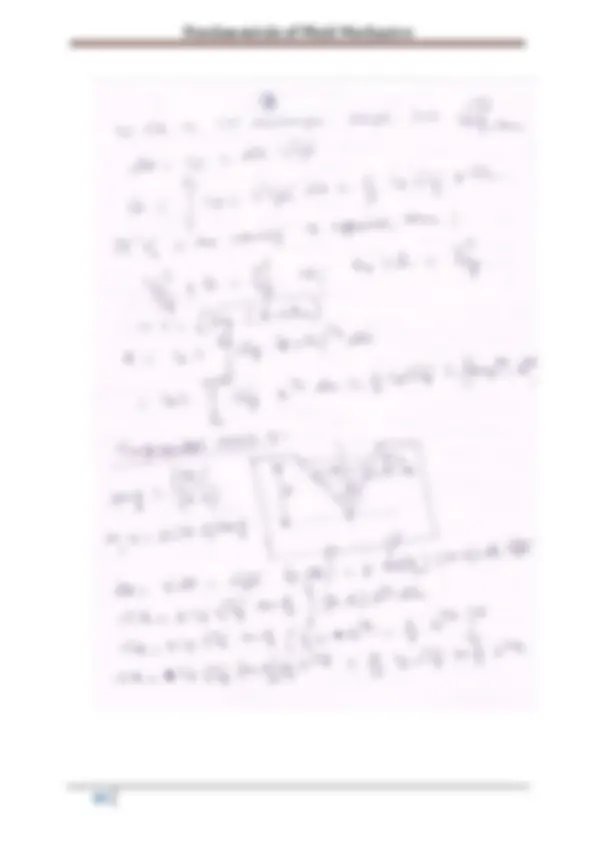
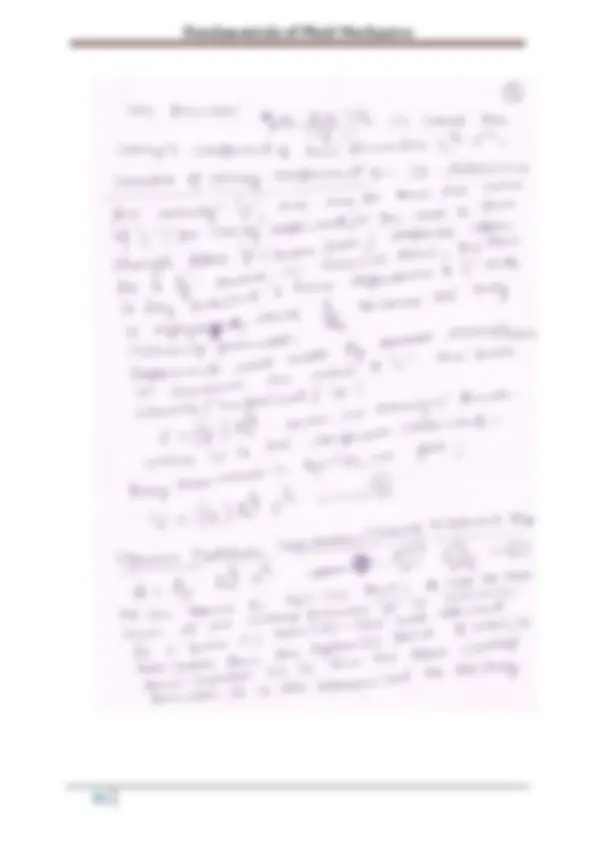
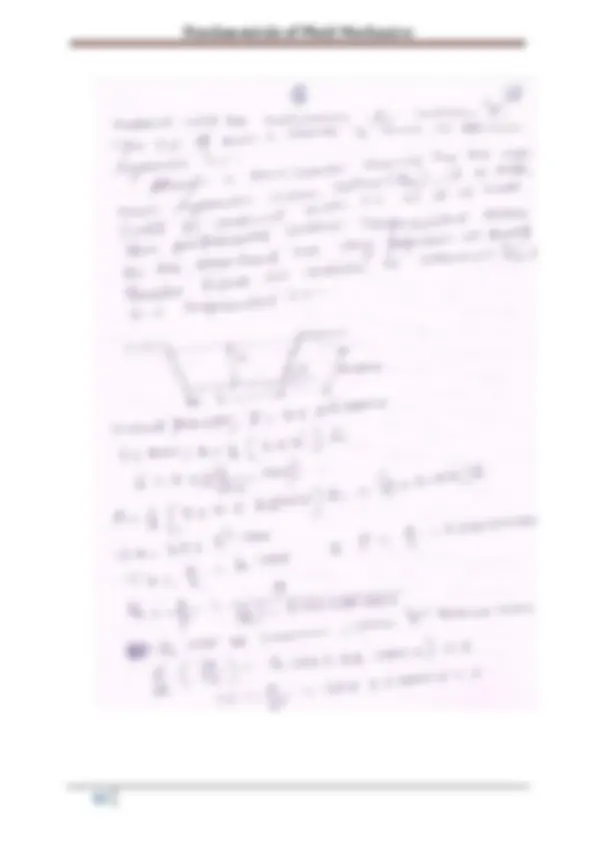
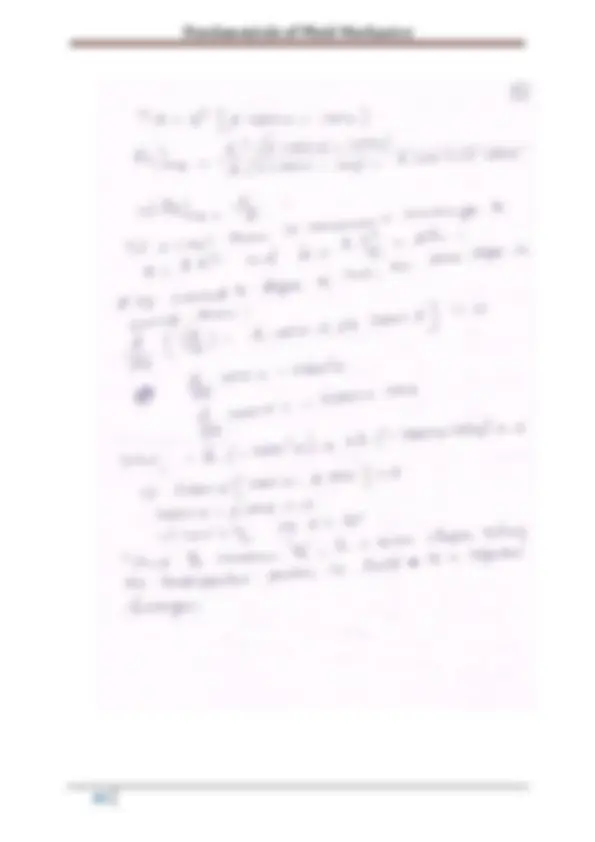
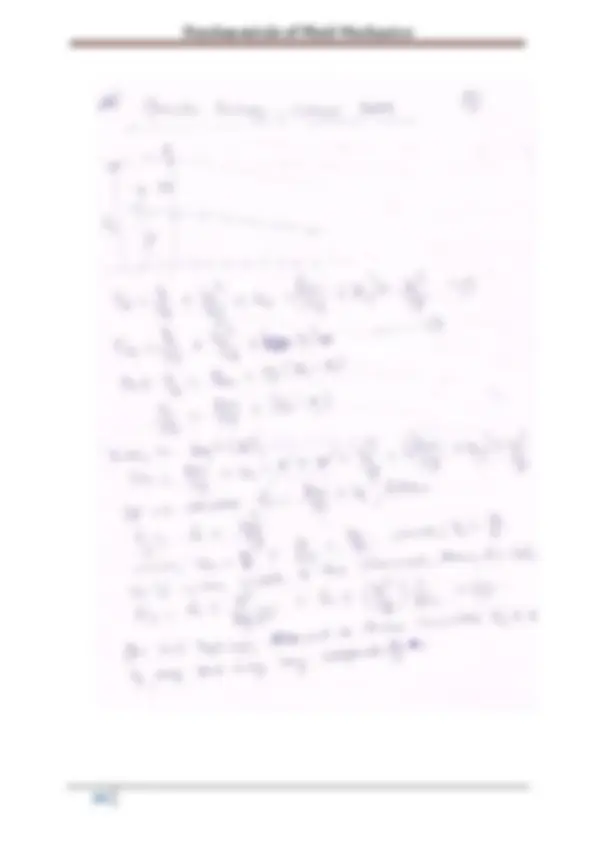
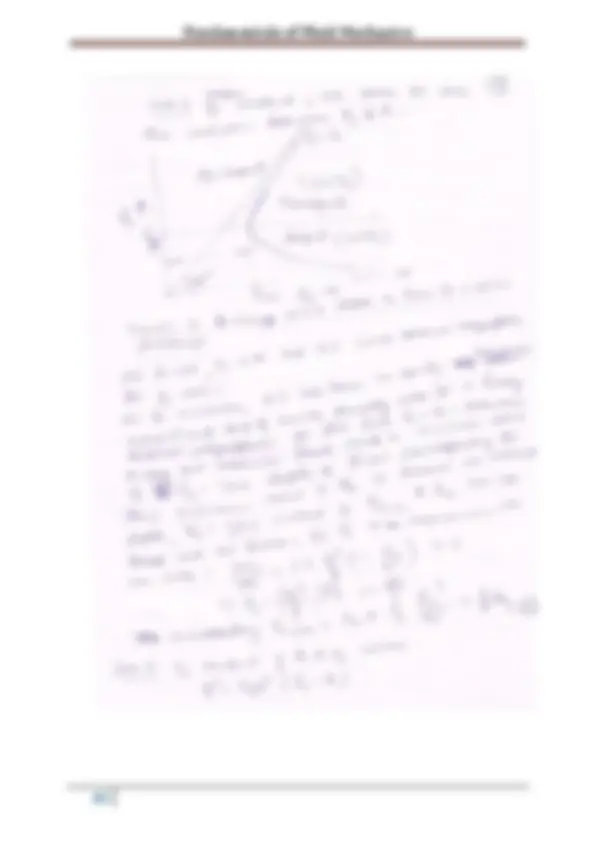
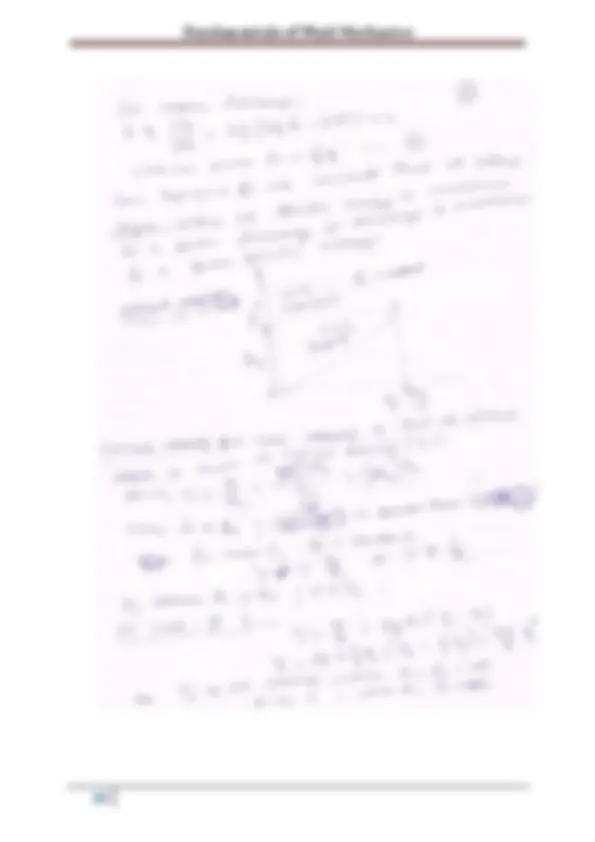
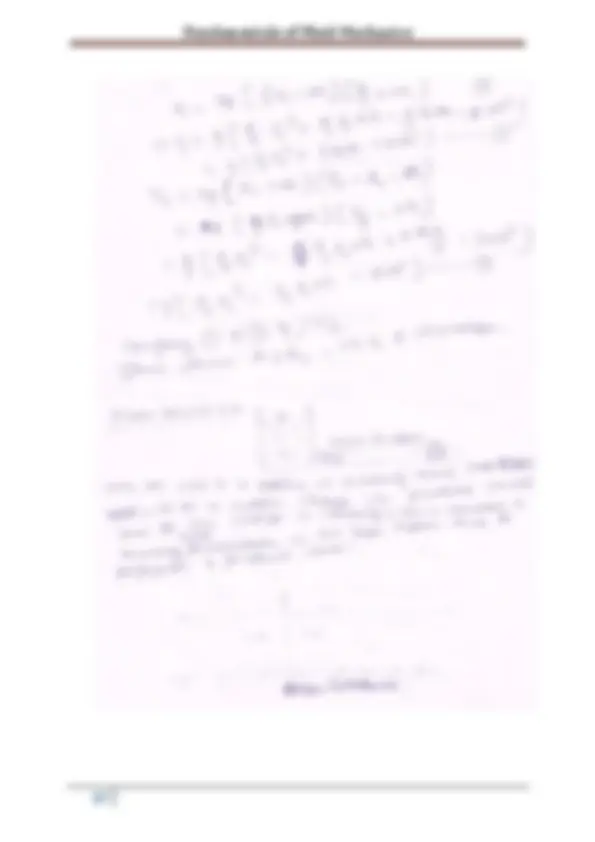
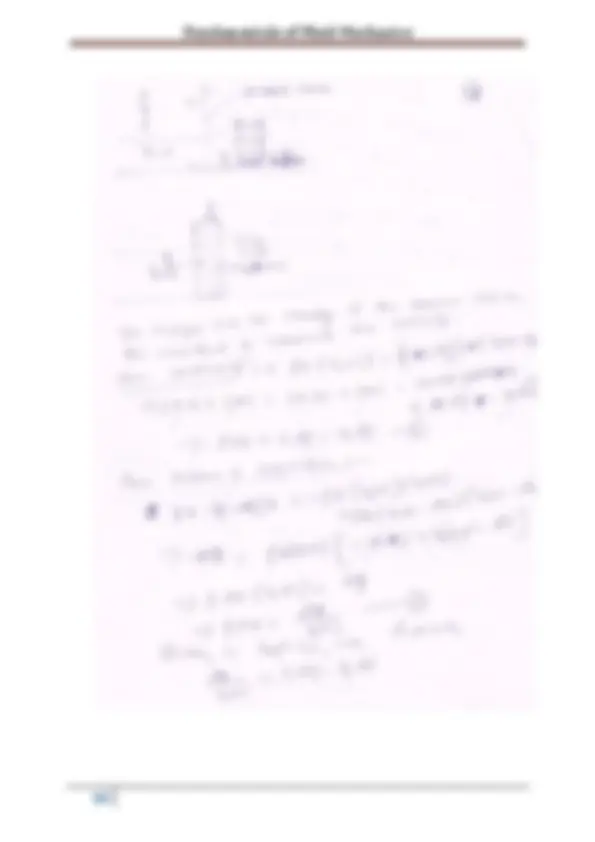
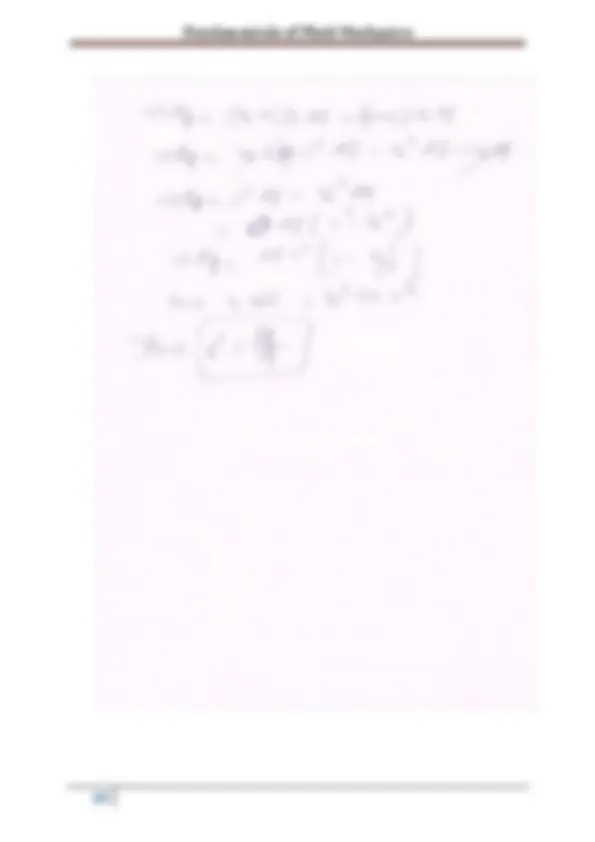
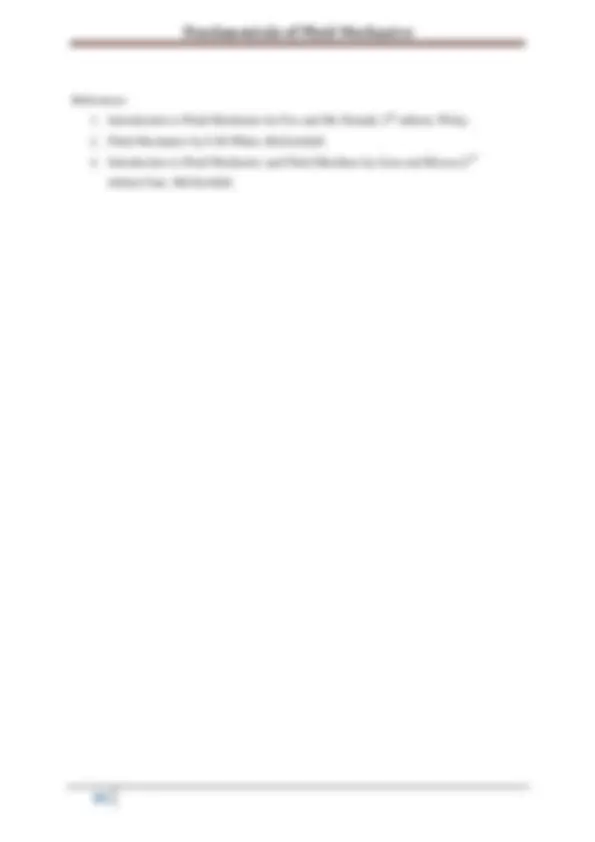
Study with the several resources on Docsity
Earn points by helping other students or get them with a premium plan
Prepare for your exams
Study with the several resources on Docsity
Earn points to download
Earn points by helping other students or get them with a premium plan
Community
Ask the community for help and clear up your study doubts
Discover the best universities in your country according to Docsity users
Free resources
Download our free guides on studying techniques, anxiety management strategies, and thesis advice from Docsity tutors
An introduction to the fundamentals of fluid mechanics. It covers topics such as the continuum assumption, fluid properties, density, and velocity fields. not intended to be used as a substitute for prescribed textbooks and is not for commercial use. The accuracy and completeness of the contents are not guaranteed. prepared by Aurovinda Mohanty, an Asst. Prof. in the Mechanical Engg. Dept at VSSUT Burla.
Typology: Lecture notes
1 / 90
This page cannot be seen from the preview
Don't miss anything!
This document does not claim any originality and cannot be used as a substitute for prescribed textbooks. The information presented here is merely a collection by the committee members for their respective teaching assignments. Various sources as mentioned at the reference of the document as well as freely available material from internet were consulted for preparing this document. The ownership of the information lies with the respective authors or institutions. Further, this document is not intended to be used for commercial purpose and the committee members are not accountable for any issues, legal or otherwise, arising out of use of this document. The committee members make no representations or warranties with respect to the accuracy or completeness of the contents of this document and specifically disclaim any implied warranties of merchantability or fitness for a particular purpose.
Fluid mechanics deals with the behaviour of fluids at rest and in motion. It is logical to begin with a definition of fluid. Fluid is a substance that deforms continuously under the application of shear (tangential) stress no matter how small the stress may be. Alternatively, we may define a fluid as a substance that cannot sustain a shear stress when at rest.
A solid deforms when a shear stress is applied , but its deformation doesn’t continue to
increase with time.
Fig 1.1(a) shows and 1.1(b) shows the deformation the deformation of solid and fluid under the action of constant shear force. The deformation in case of solid doesn’t increase with
From solid mechanics we know that the deformation is directly proportional to applied shear stress ( τ = F/A ),provided the elastic limit of the material is not exceeded.
To repeat the experiment with a fluid between the plates , lets us use a dye marker to outline a fluid element. When the shear force ‘F’ , is applied to the upper plate , the deformation of
Fluids are composed of molecules. However, in most engineering applications we are interested in average or macroscopic effect of many molecules. It is the macroscopic effect that we ordinarily perceive and measure. We thus treat a fluid as infinitely divisible substance , i.e continuum and do not concern ourselves with the behaviour of individual molecules. The concept of continuum is the basis of classical fluid mechanics .The continuum assumption is valid under normal conditions .However it breaks down whenever the mean free path of the molecules becomes the same order of magnitude as the smallest significant characteristic dimension of the problem .In the problems such as rarefied gas flow (as
encountered in flights into the upper reaches of the atmosphere ) , we must abandon the concept of a continuum in favour of microscopic and statistical point of view. As a consequence of the continuum assumption, each fluid property is assumed to have a definite value at every point in the space .Thus fluid properties such as density , temperature , velocity and so on are considered to be continuous functions of position and time. Consider a region of fluid as shown in fig 1.5. We are interested in determining the density at
the point ‘c’, whose coordinates are , and. Thus the mean density V would be given
by ρ=. In general, this will not be the value of the density at point ‘c’. To determine the
density at point ‘c’, we must select a small volume , , surrounding point ‘c’ and determine
the ratio and allowing the volume to shrink continuously in size.
Assuming that volume is initially relatively larger (but still small compared with volume , V) a typical plot might appear as shown in fig 1.5 (b). When becomes so small that it contains only a small number of molecules , it becomes impossible to fix a definite value for
; the value will vary erratically as molecules cross into and out of the volume. Thus there
is a lower limiting value of , designated ꞌ. The density at a point is thus defined as
ρ = (^) ꞌ
Fig1.6a and Fig1.6b
An example of a two-dimensional flow is illustrated in Fig1.6b.The velocity distribution is depicted for a flow between two diverging straight walls that are infinitely large in z direction. Since the channel is considered to be infinitely large in z the direction, the velocity will be identical in all planes perpendicular to z axis. Thus the velocity field will be only function of x and y and the flow can be classified as two dimensional. Fig 1.
For the purpose of analysis often it is convenient to introduce the notion of uniform flow at a given cross-section. Under this situation the two dimensional flow of Fig 1.6 b is modelled as one dimensional flow as shown in Fig1.7, i.e. velocity field is a function of x only. However, convenience alone does not justify the assumption such as a uniform flow assumption at a cross section, unless the results of acceptable accuracy are obtained.
Surface and body forces are encountered in the study of continuum fluid mechanics. Surface forces act on the boundaries of a medium through direct contact. Forces developed without physical contact and distributed over the volume of the fluid, are termed as body forces. Gravitational and electromagnetic forces are examples of body forces. Consider an area , that passes through ‘c’ .Consider a force acting on an area through point ‘c’ .The normal stress and shear stress
associated with the surface , through ‘c’ , having an outward normal in direction .For any other surface through ‘c’ the values of stresses will be different. Consider a rectangular co-ordinate system , where stresses act on planes whose normal are in x,y and z directions.
Fig 1.
Fig 1.9 shows the forces components acting on the area.
The stress components are defined as ;
A double subscript notation is used to label the stresses. The first subscript indicates the plane on which the stress acts and the second subscript represents the direction in which the stress
acts, i.e represents a stress that acts on x- plane (i.e the normal to the plane is in x
direction ) and acts in ‘y’ direction. Consideration of area element would lead to the definition of the stresses , , and
. Use of an area element would similarly lead to the definition , and.
To calculate the shear stress, , it is desirable to express in terms of readily measurable quantity. l = u t
Also for small angles , l = y
Equating these two expressions , we have
Thus the fluid element when subjected to shear stress , , experiences a deformation rate ,
#Fluids in which shear stress is directly proportional to the rate of deformation are “Newtonian fluids “.
proportional to the rate of deformation.
Newtonian Fluids :
Most common fluids i.e Air , water and gasoline are Newtonian fluids under normal conditions. Mathematically for Newtonian fluid we can write :
∝
If one considers the deformation of two different Newtonian fluids , say Glycerin and water ,one recognizes that they will deform at different rates under the action of same applied stress. Glycerin exhibits much more resistance to deformation than water. Thus we say it is more viscous. The constant of proportionality is called , ‘μ’.
Thus , =μ
Non-Newtonian Fluids :
=k , ‘n’ is flow behaviour index and ‘k’ is consistency index.
To ensure that has the same sign as that of , we can express
=k = η
Where ‘η’ = k is referred as apparent viscosity.
are called pseudoplastic (shear thining) fluids. Most Non – Newtonian fluids fall into this category. Examples include : polymer solutions , colloidal suspensions and paper pulp in water.
as dilatant( shear thickening). Suspension of starch and sand are examples of dilatant fluids.
exhibits a linear relation between stress and deformation rate.
= + μ
Examples are : Clay suspension , drilling muds & tooth paste.
Example-
An oil film of viscosity μ & thickness h<<R lies between a solid wall and a circular disc as shown in fig E .1.2. The disc is rotated steadily at an angular velocity Ω. Noting that both the velocity and shear stress vary with radius ‘r’ , derive an expression for the torque ‘T’ required to rotate the disk.
Soln:
Vapor Pressure :
Vapor pressure of a liquid is the partial pressure of the vapour in contacts with the saturated liquid at a given temperature. When the pressure in a liquid is reduced to less than vapour pressure, the liquid may change phase suddenly and flash.
Surface Tension :
Surface tension is the apparent interfacial tensile stress (force per unit length of interface) that acts whenever a liquid has a density interface, such as when the liquid contacts a gas, vapour, second liquid, or a solid. The liquid surface appears to act as stretched elastic membrane as seen by nearly spherical shapes of small droplets and soap bubbles. With some care it may be possible to place a needle on the water surface and find it supported by surface tension. A force balance on a segment of interface shows that there is a pressure jump across the imagined elastic membrane whenever the interface is curved. For a water droplet in air, the pressure in the water is higher than ambient; the same is true for a gas bubble in liquid. Surface tension also leads to the phenomenon of capillary waves on a liquid surface and capillary rise or depression as shown in the figure below.
Basic flow Analysis Techniques:
There are three basic ways to attack a fluid flow problem. They are equally important for a student learning the subject.
(1)Control–volume or integral analysis (2)Infinitesimal system or differential analysis
(3) Experimental or dimensional analysis.
In all cases the flow must satisfy three basic laws with a thermodynamic state relation and associated boundary condition.
Flow patterns:
Fluid mechanics is a highly visual subject. The pattern of flow can be visualized in a dozen of different ways. Four basic type of patterns are :
) = -At , =
At t = 6s ; x=2 = 12.1 m
; y=8 = 1.32 m
(e) = 0.3 ×12.1 - 0.3 × 1.32 = 3.63 – 0.
(f) To determine the equation of the path line , we use the parametric equation :
x = and y = and eliminate ‘t’ xy =
Remarks :
(a)The equation of stream line through ( ) and equation of the path line traced out by particle passing through ( )are same as the flow is steady.
(b) In following a particle ( Lagrangian method of description ) , both the coordinates of the particle (x,y) and the component ( ) are functions of time.
A flow is described by velocity field, =ay + bt , where a = 1 , b= 0.5 m/. At t=2s , what are the coordinates of the particle that passed through (1,2) at t=0? At t=3s , what are the coordinates of the particle that passed through the point (1,2) at t= 2s.
Plot the path line and streak line through point (1,2) and compare with the stream lines through the same point ( 1,2) at instant , t = 0,1,2 & 3 s.
Soln:
Path line and streak line are based on parametric equations for a particle.
v = = bt , so, dy = bt dt
y - = ( )
& u = = ay = a [ + ( ) ]
= + ( ) ]}dt ) = a (t- ) + ( t + a (t - ) + { ( - (t- ) } (a) For = 0 and ( , ) = (1,2) , at t = 2s , we have y-2 = (4) y =3 m x = 1 + 2 (2-0) + [ – 0] = 5.67 m
(b)For = 2s and ( , ) = ( 1,2). Thus at t = 3s
We have , y -2 = ( ) = (9-4) = 1. y = 3.25 m
& x = 1+ 2 (3-2) + { ( - (3-2) }
x = 1 + 2 (3-2) + { ( - 4(1 ) }= 3.58 m
(c) The streak line at any given ‘t’ may be obtained by varying ‘ ’.
(s) t^ X(m)^ Y(m) 0 0 1 2 0 1 3.08 2. 0 2 5.67 3. 0 3 9.25 4.
#part (b): path lines of a particle located at ( , ) at = 2s
(s) t(s)^ X^ Y 2 2 1 2 2 3 3.58 3. 2 4 7.67 5.
#part (c) : =
dx = ) dy y dy = dx = ( ) x + c
Thus , c = – ( )
For ( , ) = (1,2) , for different value of ‘t’.
For t =0 ; c = ( = 4
t = 1 ;c = 4 – ( )1 = 3 t = 2 ;c = 4 – ( )1 = 2
CHAPTER – 2 FLUID STATICS
In the previous chapter , we defined as well as demonstrated that fluid at rest cannot sustain shear stress , how small it may be. The same is true for fluids in “ rigid body” motion. Therefore, fluids either at rest or in “rigid body” motion are able to sustain only normal stresses. Analysis of hydrostatic cases is thus appreciably simpler than that for fluids undergoing angular deformation.
Mere simplicity doesn’t justify our study of subject. Normal forces transmitted by fluids are important in many practical situations. Using the principles of hydrostatics we can compute forces on submerged objects, developed instruments for measuring pressure, forces developed by hydraulic systems in applications such as industrial press or automobile brakes.
In a static fluid or in a fluid undergoing rigid-body motion, a fluid particle retains its identity for all time and fluid elements do not deform. Thus we shall apply Newton’s second law of motion to evaluate the forces acting on the particle.
(here , gravity is the only body force considered)where, is the local gravity vector ,ρ is the density & d is the volume of the fluid element. In Cartesian coordinates, d= dx dy dz .In a static fluid no shear stress can be present. Thus the only surface force is the pressure force. Pressure is a scalar field, p = p(x,y,z) ; the pressure varies with position within the fluid.
Pressure at the left face : = ( p - )
Pressure at the right face : = ( p + )
Pressure force at the left face : = ( p - )dx dz
Pressure force at the right face : ( p + )dx dz (- )
Similarly writing for all the surfaces , we have
d = (p - )dy dz + (p + )dy dz (- ) + ( p - )dx dz
Collecting and concealing terms , we obtain :
d = - ( + + ) dx dy dz
d = - (∇p dx dy dz
Thus
Net force acting on the body:
d = d + d = ( - ∇p + ρ ) dx dy dz d = ( - ∇p + ρ )d
or, in a per unit volume basis:
= (^ -^ ∇p +^ ρ^ )^ (2.1)
For a fluid particle , Newton’s second law can be expressed as : d = dm = ρ dv
Or (^) = ρ (2.2)
Comparing 2.1 & 2.2 , we have
For a static fluid , = 0 ; Thus we obtain ; - ∇p + ρ =
The component equations are ;
= - g =0=