
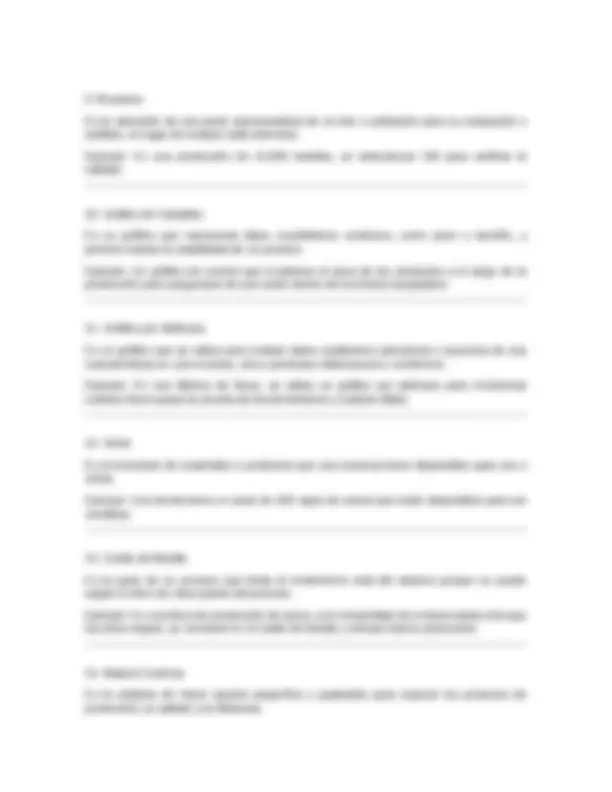
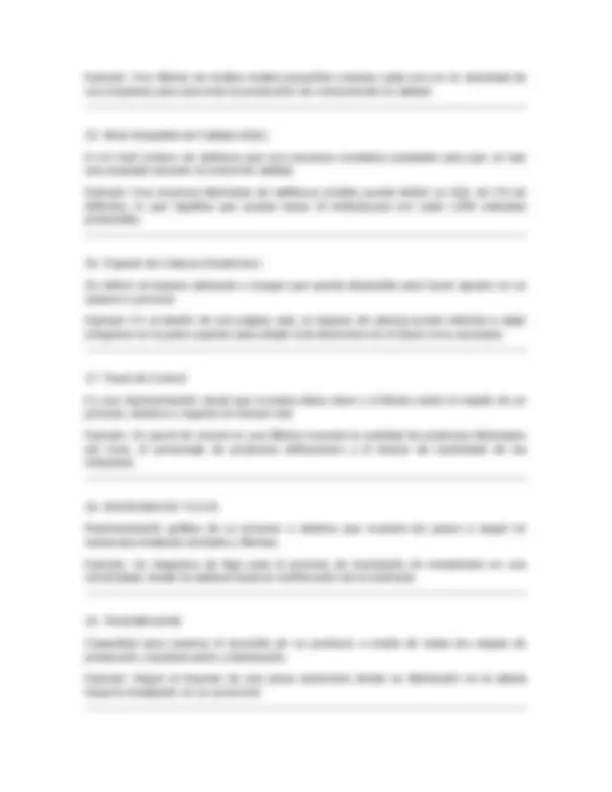
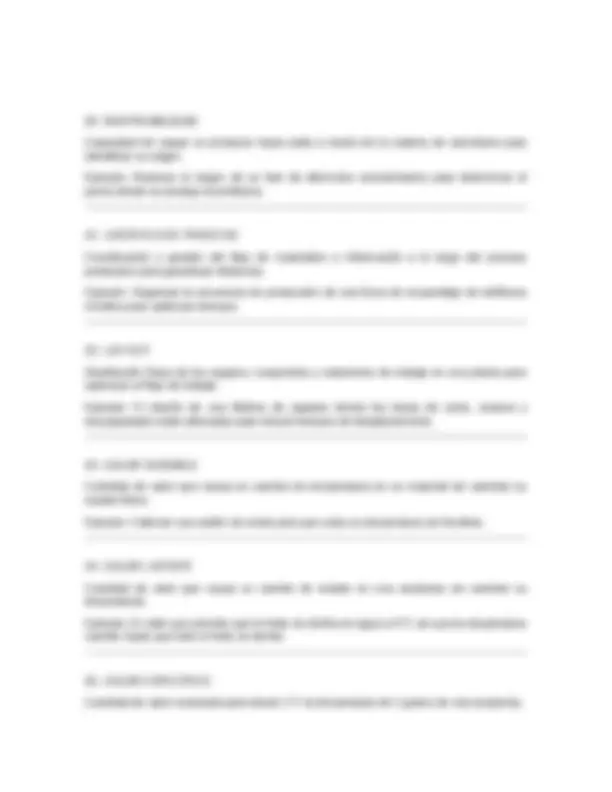
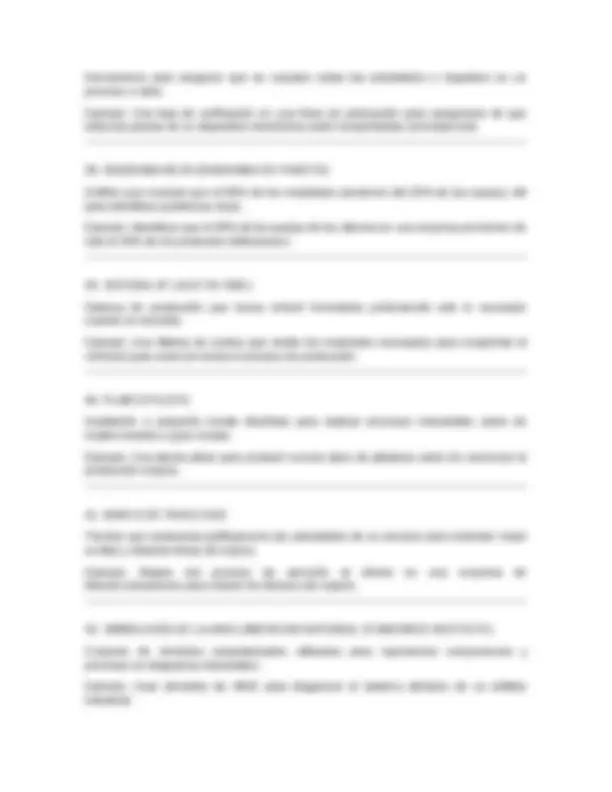
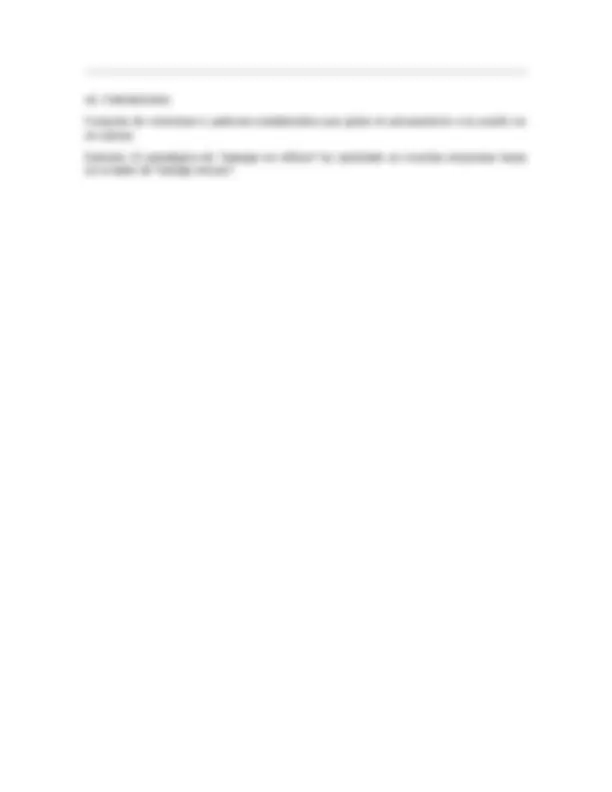
Study with the several resources on Docsity
Earn points by helping other students or get them with a premium plan
Prepare for your exams
Study with the several resources on Docsity
Earn points to download
Earn points by helping other students or get them with a premium plan
Community
Ask the community for help and clear up your study doubts
Discover the best universities in your country according to Docsity users
Free resources
Download our free guides on studying techniques, anxiety management strategies, and thesis advice from Docsity tutors
Una amplia gama de conceptos y herramientas esenciales para la gestión de procesos, incluyendo el ciclo de deming (pdca), la mejora continua, el análisis de costos de calidad, la optimización paramétrica y estructural, la simulación, la estratificación, el diagrama 80-20 (diagrama de pareto), la logística de proceso, el mapeo de procesos y la simbología de la ansi. Se ilustran estos conceptos con ejemplos prácticos que facilitan la comprensión de su aplicación en diferentes contextos.
Typology: Cheat Sheet
1 / 9
This page cannot be seen from the preview
Don't miss anything!
Ejemplo: Diseñar sillas de oficina ajustables en altura para evitar problemas de espalda en los empleados que pasan muchas horas sentados.
Ejemplo: Una fábrica de textiles realiza pequeñas mejoras cada mes en la velocidad de sus máquinas para aumentar la producción sin comprometer la calidad.
Capacidad de seguir un producto hacia atrás a través de la cadena de suministro para identificar su origen. Ejemplo: Rastrear el origen de un lote de alimentos contaminados para determinar el punto donde se produjo el problema.
Ejemplo: Simular el tráfico en una ciudad con un nuevo sistema de semáforos para ver cómo afecta los tiempos de desplazamiento.
Herramienta para asegurar que se cumplan todas las actividades o requisitos en un proceso o tarea. Ejemplo: Una lista de verificación en una línea de producción para asegurarse de que todas las piezas de un dispositivo electrónico estén ensambladas correctamente.