
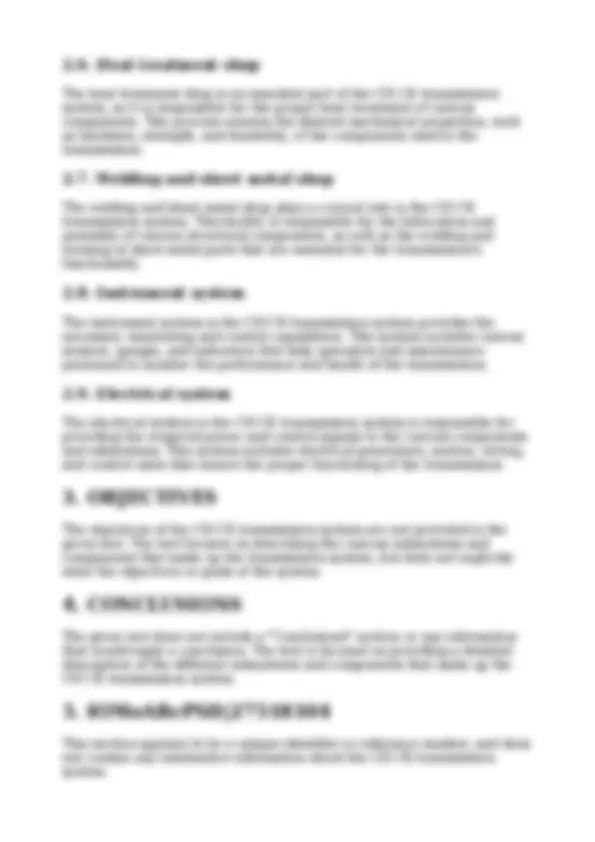
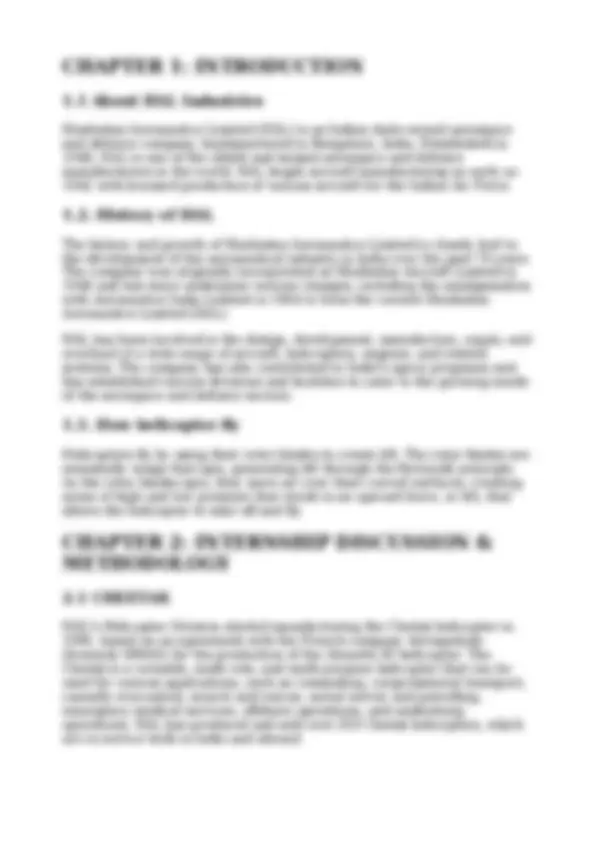
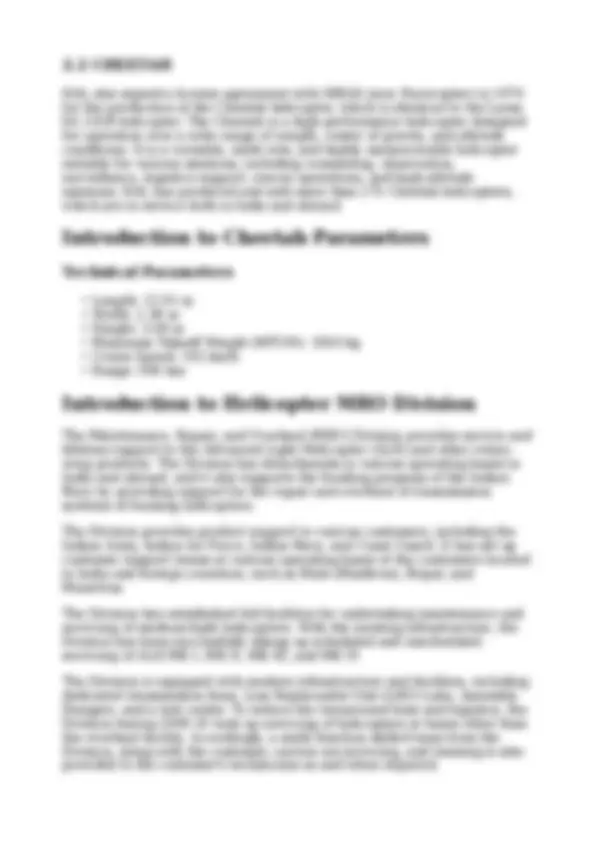
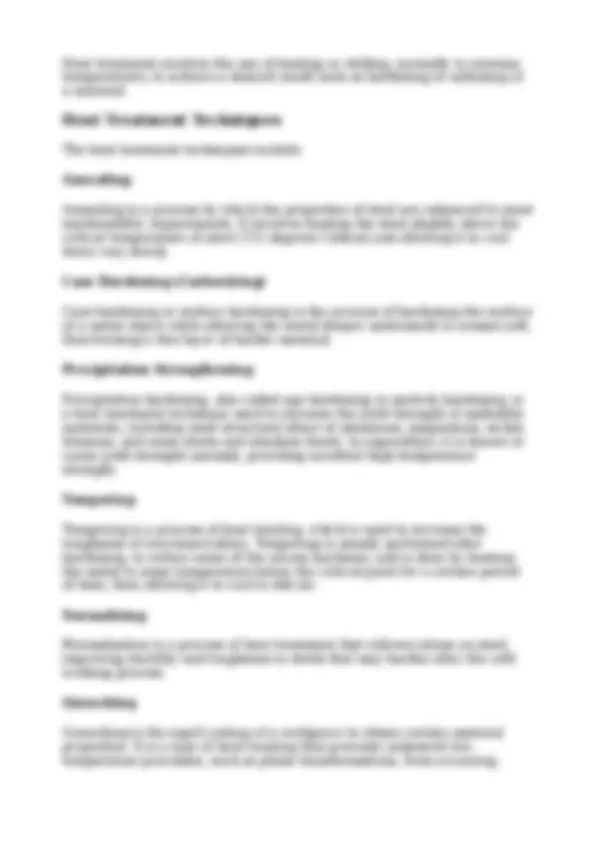
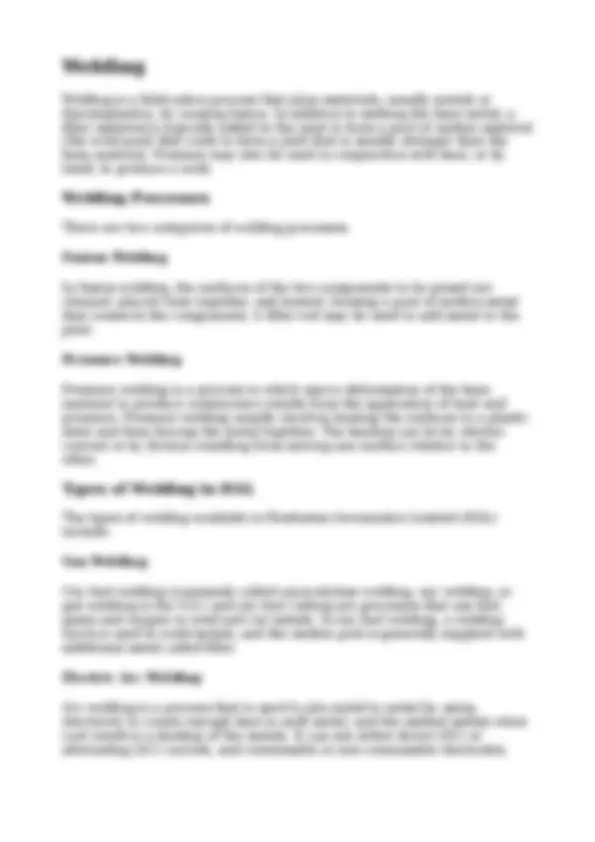
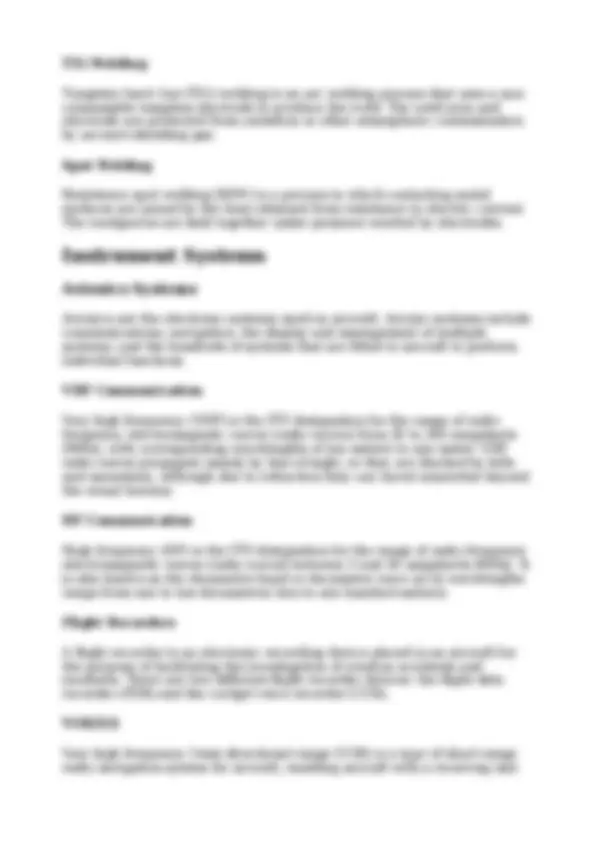
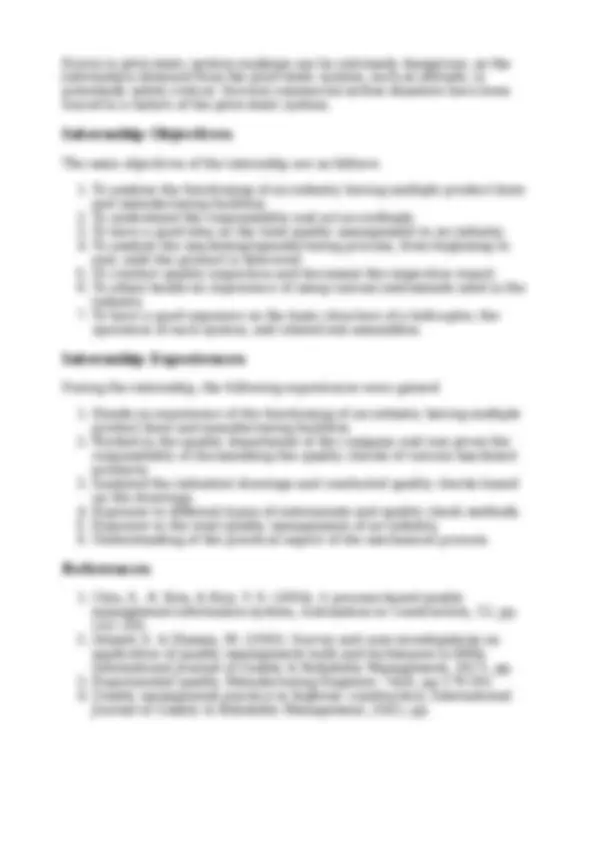
Study with the several resources on Docsity
Earn points by helping other students or get them with a premium plan
Prepare for your exams
Study with the several resources on Docsity
Earn points to download
Earn points by helping other students or get them with a premium plan
Community
Ask the community for help and clear up your study doubts
Discover the best universities in your country according to Docsity users
Free resources
Download our free guides on studying techniques, anxiety management strategies, and thesis advice from Docsity tutors
This internship report provides a detailed overview of helicopter manufacturing at hindustan aeronautics limited (hal), focusing on the cheetah and chetak models. It delves into the history of hal, its role in the indian aerospace industry, and the company's involvement in the design, development, and manufacturing of helicopters. The report also explores the maintenance, repair, and overhaul (mro) division of hal, highlighting the key aspects of the cheetah-chetak transmission system, including its hydraulic, electrical, and instrument systems. The report concludes with a discussion of welding processes and avionics systems used in helicopter manufacturing.
Typology: Lecture notes
1 / 13
This page cannot be seen from the preview
Don't miss anything!
Hindustan Aeronautics Limited (HAL) is an Indian state-owned aerospace and defense company headquartered in Bangalore, India. It is governed by the Indian Ministry of Defence. HAL is one of the oldest and largest aerospace companies in India, with over 20,000 employees. The company has been involved in the design, fabrication, and assembly of aircraft, helicopters, and their spare parts.
HAL was established on December 23, 1940, as Hindustan Aircraft Limited in Bangalore. It was founded by Walchand Hirachand, an Indian industrialist. The company was initially involved in the maintenance and repair of Willy's-Overland-made jeeps and other vehicles. During World War II, the company started manufacturing spare parts for the British Royal Air Force. In 1943, the Government of India took control of the company and renamed it Hindustan Aircraft Limited.
After India's independence in 1947, the company expanded its operations and began manufacturing aircraft. In the 1950s, HAL started producing the Hindustan Trainer HT-2, the first Indian-designed aircraft. Over the years, HAL has produced several other aircraft, including the HF-24 Marut, the first Indian-designed jet fighter, and the Dhruv, an advanced light helicopter.
Today, HAL is a major player in the Indian aerospace industry, producing a wide range of aircraft and helicopters for both military and civilian use. The company has also expanded its operations to include the maintenance, repair, and overhaul (MRO) of aircraft and helicopters.
The process of flying a helicopter involves several key steps:
Pre-flight checks: Before taking off, the pilot must perform a thorough inspection of the helicopter to ensure that all systems are functioning properly.
Engine start-up: The pilot starts the helicopter's engine(s) and checks that all systems are operating within the specified parameters.
Takeoff: The pilot lifts the helicopter off the ground, using the collective control to increase the pitch of the main rotor blades and generate lift.
Flight: The pilot uses the cyclic control to steer the helicopter in the desired direction and the anti-torque pedals to control the helicopter's yaw.
Landing: The pilot descends the helicopter and touches down gently on the ground, using the collective control to reduce the pitch of the main rotor blades and decrease lift.
Throughout the flight, the pilot must constantly monitor the helicopter's systems and make adjustments as necessary to maintain control and ensure a safe flight.
Internship Discussion and Methodology
The Cheetah is a light utility helicopter developed by HAL. It is used for a variety of roles, including reconnaissance, transport, and medical evacuation. The Cheetah is known for its high-altitude performance and is widely used in the mountainous regions of India.
The Cheetah is a light utility helicopter developed by HAL. It is used for a variety of roles, including reconnaissance, transport, and medical evacuation. The Cheetah is known for its high-altitude performance and is widely used in the mountainous regions of India.
The Maintenance, Repair, and Overhaul (MRO) division of HAL is responsible for the maintenance and repair of the company's aircraft and helicopters. This division plays a crucial role in ensuring the continued airworthiness of HAL's fleet. The MRO division is equipped with state-of-the- art facilities and employs highly skilled technicians to perform a wide range of maintenance and repair tasks.
CH-CK transmission system
The hydraulic system in the CH-CK transmission system is responsible for providing the necessary power and control for various components and mechanisms. This system includes hydraulic pumps, valves, actuators, and associated piping and fittings to ensure the smooth operation of the transmission.
CHAPTER 1: INTRODUCTION
Hindustan Aeronautics Limited (HAL) is an Indian state-owned aerospace and defence company, headquartered in Bengaluru, India. Established in 1940, HAL is one of the oldest and largest aerospace and defence manufacturers in the world. HAL began aircraft manufacturing as early as 1942 with licensed production of various aircraft for the Indian Air Force.
The history and growth of Hindustan Aeronautics Limited is closely tied to the development of the aeronautical industry in India over the past 79 years. The company was originally incorporated as Hindustan Aircraft Limited in 1940 and has since undergone various changes, including the amalgamation with Aeronautics India Limited in 1964 to form the current Hindustan Aeronautics Limited (HAL).
HAL has been involved in the design, development, manufacture, repair, and overhaul of a wide range of aircraft, helicopters, engines, and related systems. The company has also contributed to India's space programs and has established various divisions and facilities to cater to the growing needs of the aerospace and defence sectors.
Helicopters fly by using their rotor blades to create lift. The rotor blades are essentially wings that spin, generating lift through the Bernoulli principle. As the rotor blades spin, they move air over their curved surfaces, creating areas of high and low pressure that result in an upward force, or lift, that allows the helicopter to take off and fly.
CHAPTER 2: INTERNSHIP DISCUSSION &
METHODOLOGY
HAL's Helicopter Division started manufacturing the Chetak helicopter in 1965, based on an agreement with the French company Aérospatiale (formerly SNIAS) for the production of the Alouette III helicopter. The Chetak is a versatile, multi-role, and multi-purpose helicopter that can be used for various applications, such as commuting, cargo/material transport, casualty evacuation, search and rescue, aerial survey and patrolling, emergency medical services, offshore operations, and underslung operations. HAL has produced and sold over 350 Chetak helicopters, which are in service both in India and abroad.
HAL also signed a license agreement with SNIAS (now Eurocopter) in 1970 for the production of the Cheetah helicopter, which is identical to the Lama SA 315B helicopter. The Cheetah is a high-performance helicopter designed for operation over a wide range of weight, center of gravity, and altitude conditions. It is a versatile, multi-role, and highly maneuverable helicopter suitable for various missions, including commuting, observation, surveillance, logistics support, rescue operations, and high-altitude missions. HAL has produced and sold more than 275 Cheetah helicopters, which are in service both in India and abroad.
Introduction to Cheetah Parameters
Length: 12.91 m Width: 2.38 m Height: 3.09 m Maximum Takeoff Weight (MTOW): 1950 kg Cruise Speed: 192 km/h Range: 560 km
Introduction to Helicopter MRO Division
The Maintenance, Repair, and Overhaul (MRO) Division provides service and lifetime support to the Advanced Light Helicopter (ALH) and other rotary- wing products. The Division has detachments in various operating bases in India and abroad, and it also supports the Seaking program of the Indian Navy by providing support for the repair and overhaul of transmission systems of Seaking helicopters.
The Division provides product support to various customers, including the Indian Army, Indian Air Force, Indian Navy, and Coast Guard. It has set up customer support teams at various operating bases of the customers located in India and foreign countries, such as Male (Maldives), Nepal, and Mauritius.
The Division has established full facilities for undertaking maintenance and servicing of medium-light helicopters. With the existing infrastructure, the Division has been successfully taking up scheduled and unscheduled servicing of ALH MK I, MK II, MK III, and MK IV.
The Division is equipped with modern infrastructure and facilities, including dedicated transmission lines, Line Replaceable Unit (LRU) Labs, Assembly Hangars, and a test center. To reduce the turnaround time and logistics, the Division during 2009-10 took up servicing of helicopters at bases other than the overhaul facility. Accordingly, a multi-function skilled team from the Division, along with the customer, carries out servicing, and training is also provided to the customer's technicians as and when required.
Hydraulic System
The Advanced Light Helicopter (ALH) has two dedicated independent hydraulic systems referred to as the control hydraulic system for flight controls actuation. These hydraulic systems operate simultaneously and independently. When one system fails, the other system continues to operate, providing a redundant hydraulic system for flight control actuation.
In the fixed wheel version of the ALH, the hydraulic power for the operation of the wheel brakes is tapped from one of the control hydraulic systems.
The tricycle retractable wheel landing gear version of the ALH has an additional system called the utility hydraulic system to operate utility services like landing gears, wheel brakes, rescue hoist, harpoon, and sonar winch.
Each of the hydraulic systems is divided into three main modules:
Hydraulic pump Hydraulic package Operating equipment
The hydraulic pump is of the axial piston, variable delivery, and constant pressure type. It is used to supply a continuous, pressurized, and low- pulsating flow of hydraulic fluid.
The hydraulic package consists of the reservoir unit and control valves clubbed into a single unit. This also enables the pressurization of the fluid to the inlet of the hydraulic pump.
Duplex, tandem hydraulic servo actuators are used for operating the main and the tail rotor upper controls. These actuators are hydraulically powered and transmit the cockpit control input to the rotors by amplifying the efforts put by the pilot.
Heat Treating
Heat treating is a group of industrial and metal working processes used to alter the physical and sometimes chemical properties of a material. The most common application is in metallurgy, but heat treatments are also used in the manufacture of many other materials, such as glass.
Heat treatment involves the use of heating or chilling, normally to extreme temperatures, to achieve a desired result such as hardening or softening of a material.
The heat treatment techniques include:
Annealing
Annealing is a process by which the properties of steel are enhanced to meet machinability requirements. It involves heating the steel slightly above the critical temperature of steel (723 degrees Celsius) and allowing it to cool down very slowly.
Case Hardening (Carburizing)
Case-hardening or surface hardening is the process of hardening the surface of a metal object while allowing the metal deeper underneath to remain soft, thus forming a thin layer of harder material.
Precipitation Strengthening
Precipitation hardening, also called age hardening or particle hardening, is a heat treatment technique used to increase the yield strength of malleable materials, including most structural alloys of aluminum, magnesium, nickel, titanium, and some steels and stainless steels. In superalloys, it is known to cause yield strength anomaly, providing excellent high-temperature strength.
Tempering
Tempering is a process of heat treating, which is used to increase the toughness of iron-based alloys. Tempering is usually performed after hardening, to reduce some of the excess hardness, and is done by heating the metal to some temperature below the critical point for a certain period of time, then allowing it to cool in still air.
Normalizing
Normalization is a process of heat treatment that relieves stress on steel, improving ductility and toughness in steels that may harden after the cold working process.
Quenching
Quenching is the rapid cooling of a workpiece to obtain certain material properties. It is a type of heat treating that prevents undesired low- temperature processes, such as phase transformations, from occurring.
TIG Welding
Tungsten Inert Gas (TIG) welding is an arc welding process that uses a non- consumable tungsten electrode to produce the weld. The weld area and electrode are protected from oxidation or other atmospheric contamination by an inert shielding gas.
Spot Welding
Resistance spot welding (RSW) is a process in which contacting metal surfaces are joined by the heat obtained from resistance to electric current. The workpieces are held together under pressure exerted by electrodes.
Instrument Systems
Avionics are the electronic systems used on aircraft. Avionic systems include communications, navigation, the display and management of multiple systems, and the hundreds of systems that are fitted to aircraft to perform individual functions.
VHF Communication
Very high frequency (VHF) is the ITU designation for the range of radio frequency electromagnetic waves (radio waves) from 30 to 300 megahertz (MHz), with corresponding wavelengths of ten meters to one meter. VHF radio waves propagate mainly by line-of-sight, so they are blocked by hills and mountains, although due to refraction they can travel somewhat beyond the visual horizon.
HF Communication
High frequency (HF) is the ITU designation for the range of radio frequency electromagnetic waves (radio waves) between 3 and 30 megahertz (MHz). It is also known as the decametre band or decametre wave as its wavelengths range from one to ten decametres (ten to one hundred meters).
Flight Recorders
A flight recorder is an electronic recording device placed in an aircraft for the purpose of facilitating the investigation of aviation accidents and incidents. There are two different flight recorder devices: the flight data recorder (FDR) and the cockpit voice recorder (CVR).
Very high frequency Omni-directional range (VOR) is a type of short-range radio navigation system for aircraft, enabling aircraft with a receiving unit
to determine its position and stay on course by receiving radio signals transmitted by a network of fixed ground radio beacons.
A traffic collision avoidance system or traffic alert and collision avoidance system (TCAS) is an aircraft collision avoidance system designed to reduce the incidence of mid-air collision between aircraft. It monitors the airspace around an aircraft for other aircraft equipped with a corresponding active transponder, independent of air traffic control, and warns pilots of the presence of other transponder-equipped aircraft which may present a threat of mid-air collision.
In aviation, distance measuring equipment (DME) is a radio navigation technology that measures the slant range (distance) between an aircraft and a ground station by timing the propagation delay of radio signals in the frequency band between 960 and 1215 megahertz (MHz).
Radar Altimeter
A radar altimeter (RA), radio altimeter (RALT), electronic altimeter, or reflection altimeter measures altitude above the terrain presently beneath an aircraft or spacecraft by timing how long it takes a beam of radio waves to travel to ground, reflect, and return to the craft.
Identification, friend or foe (IFF) is an identification system designed for command and control. IFF systems usually use radar frequencies, but other electromagnetic frequencies, radio or infrared, may be used. It enables military and civilian air traffic control interrogation systems to identify aircraft, vehicles or forces as friendly and to determine their bearing and range from the interrogator.
IFF and Electrical Systems in Advanced Light
Helicopters
IFF was first developed during World War II, with the arrival of radar, and several friendly fire incidents. This system was designed to distinguish between friendly and enemy aircraft, helping to prevent accidental attacks on one's own forces.
Errors in pitot-static system readings can be extremely dangerous, as the information obtained from the pitot-static system, such as altitude, is potentially safety-critical. Several commercial airline disasters have been traced to a failure of the pitot-static system.
The main objectives of the internship are as follows:
To analyze the functioning of an industry having multiple product lines and manufacturing facilities. To understand the responsibility and act accordingly. To have a good idea on the total quality management in an industry. To analyze the machining/manufacturing process, from beginning to end, until the product is delivered. To conduct quality inspection and document the inspection report. To attain hands-on experience of using various instruments used in the industry. To have a good exposure on the basic structure of a helicopter, the operation of each system, and related sub-assemblies.
During the internship, the following experiences were gained:
Hands-on experience of the functioning of an industry having multiple product lines and manufacturing facilities. Worked in the quality department of the company and was given the responsibility of documenting the quality checks of various machined products. Analyzed the industrial drawings and conducted quality checks based on the drawings. Exposure to different types of instruments and quality check methods. Exposure to the total quality management of an industry. Understanding of the practical aspect of the mechanical process.
Chin, S., K. Kim, & Kim, Y.-S. (2004). A process-based quality management information system, Automation in Construction, 13, pp. 241–259. Ahmed, S. & Hassan, M. (2003). Survey and case investigations on application of quality management tools and techniques in SMIs. International Journal of Quality & Reliability Management, 20(7), pp. Experimental quality. Manufacturing Engineer, 74(4), pp.178-181. Quality management practice in highway construction, International Journal of Quality & Reliability Management, 20(5), pp.