

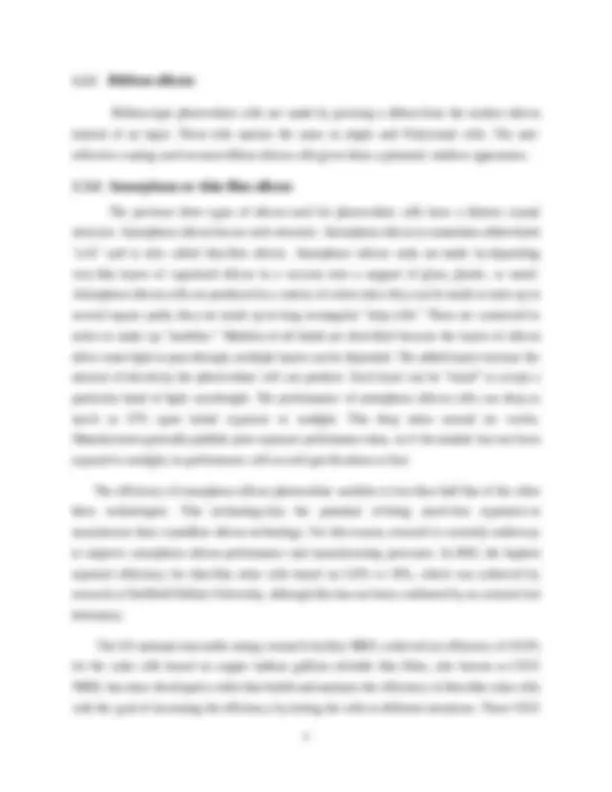
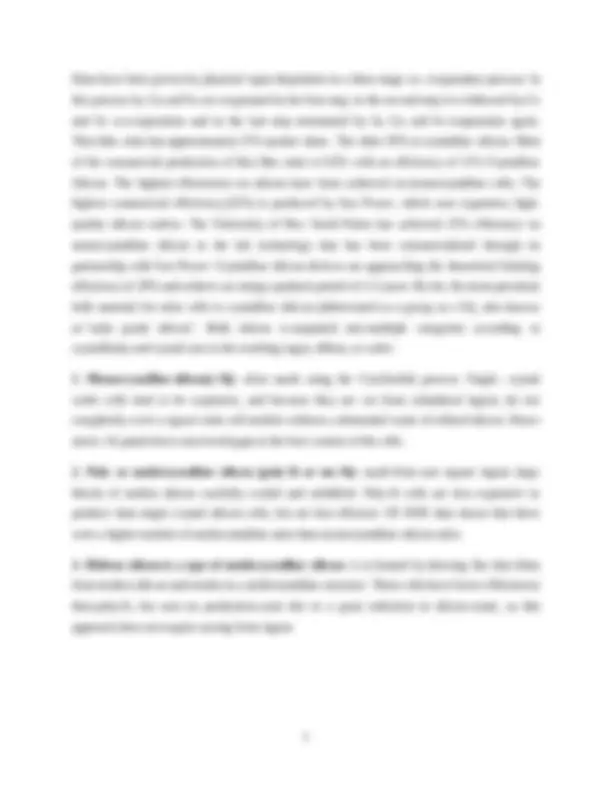
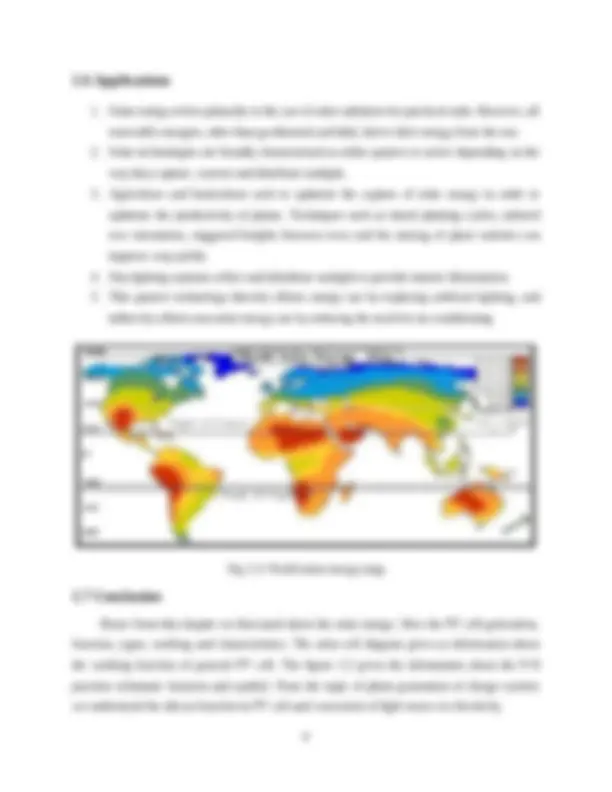
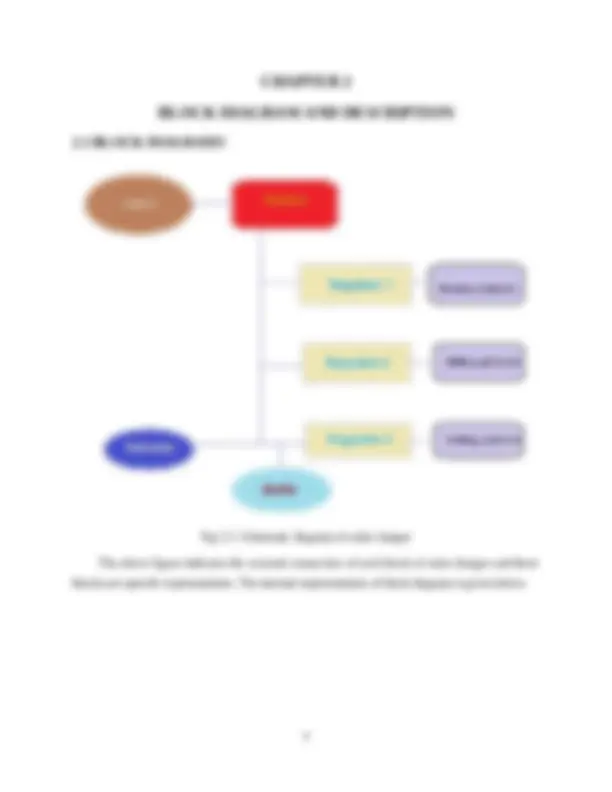
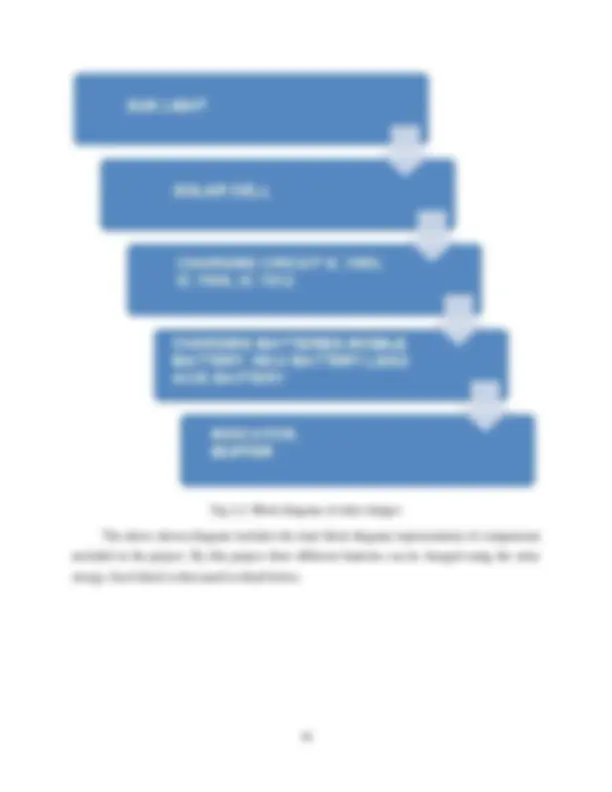
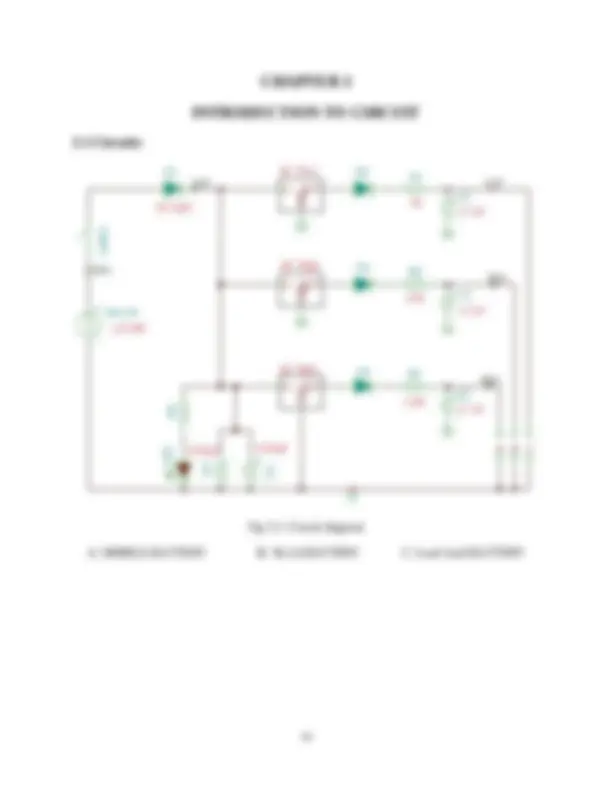
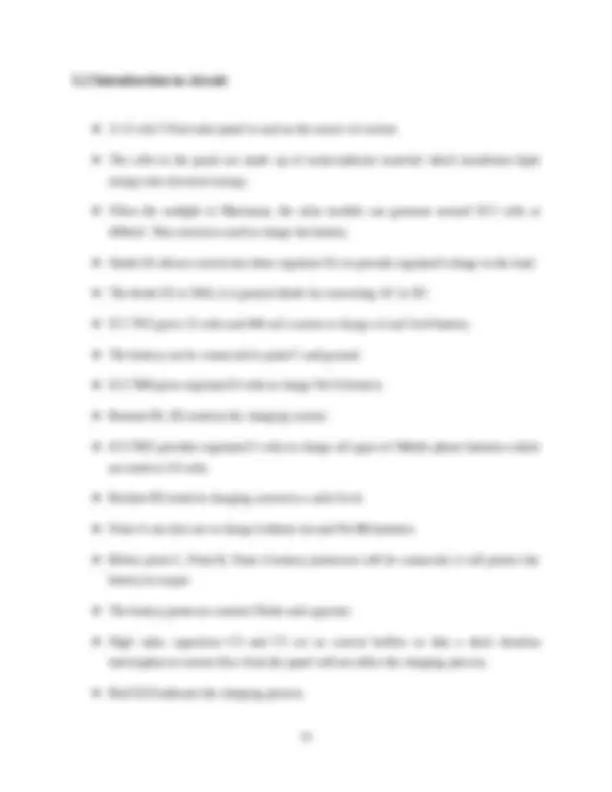
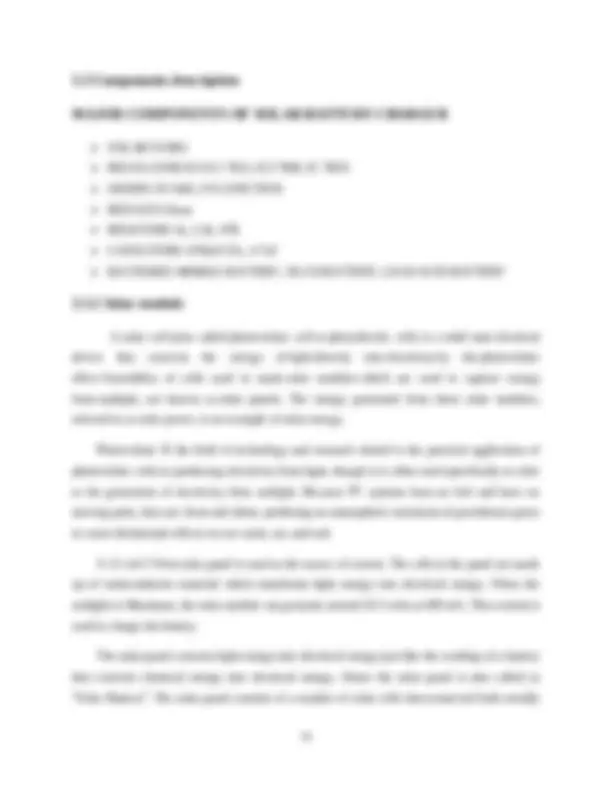
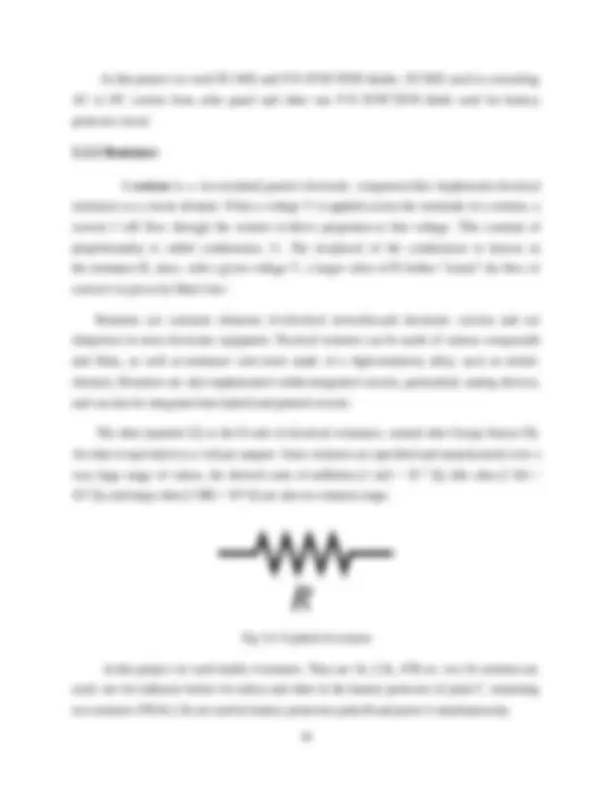
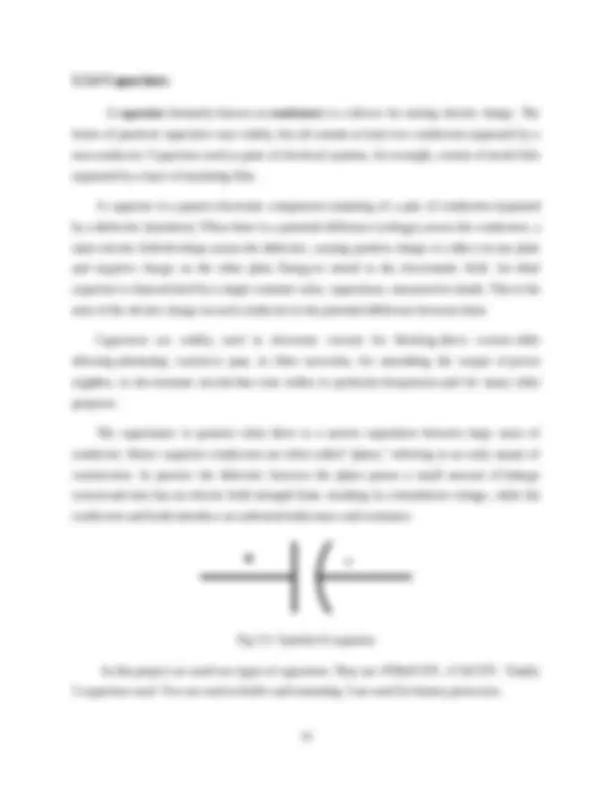
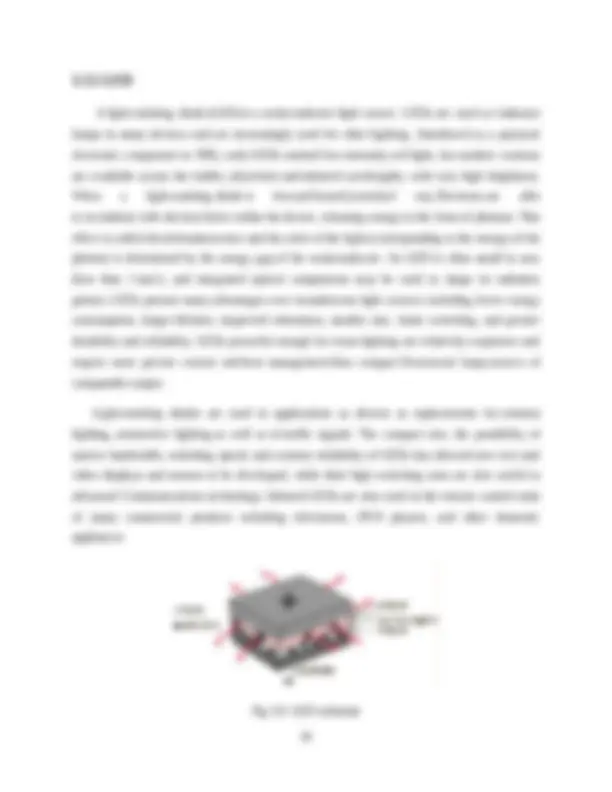
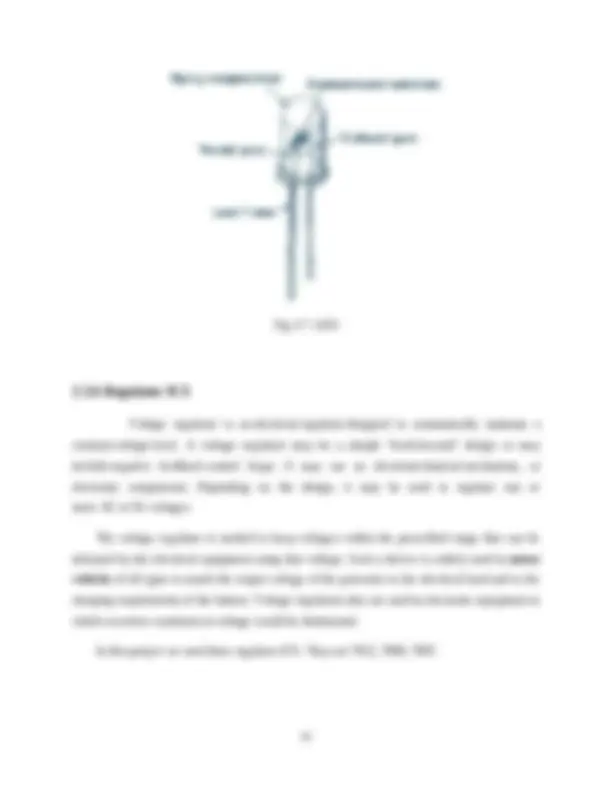
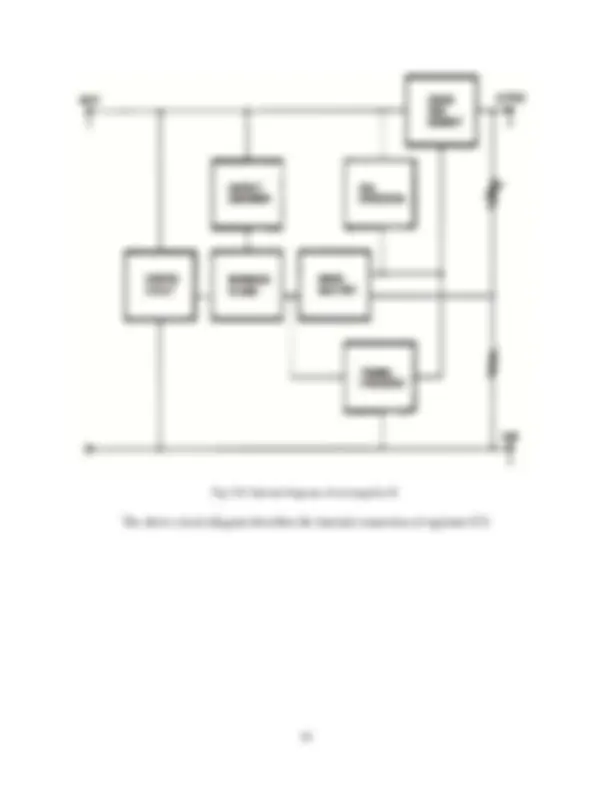
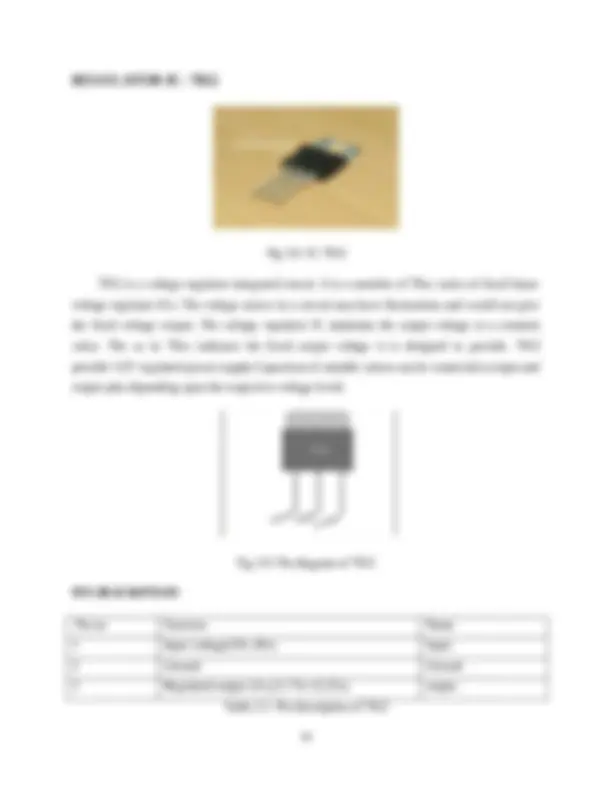
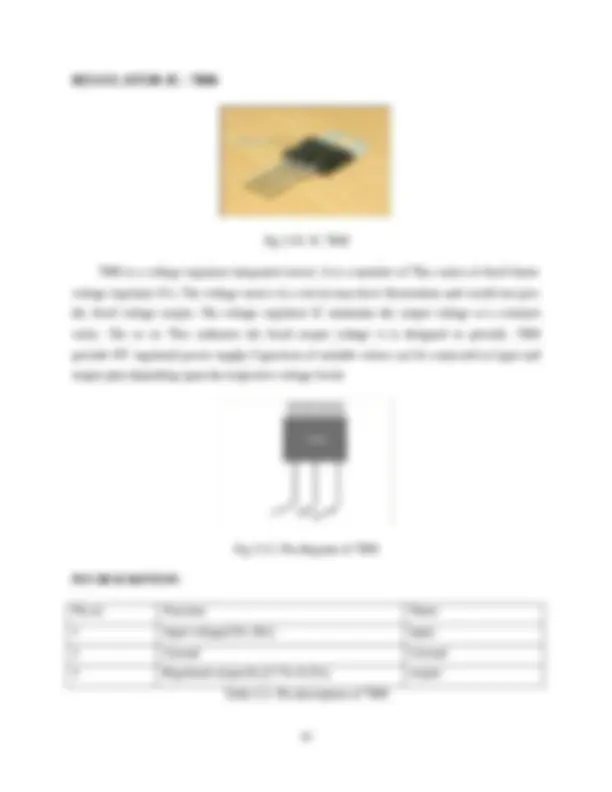
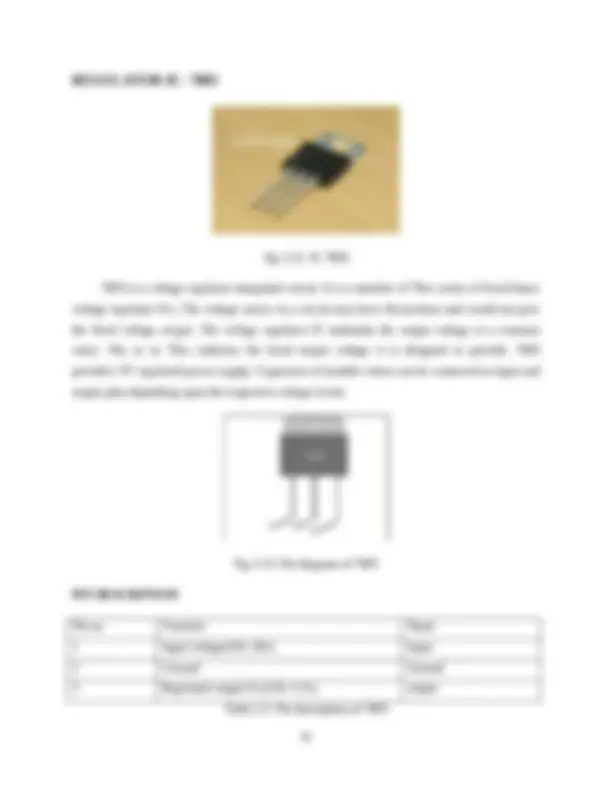
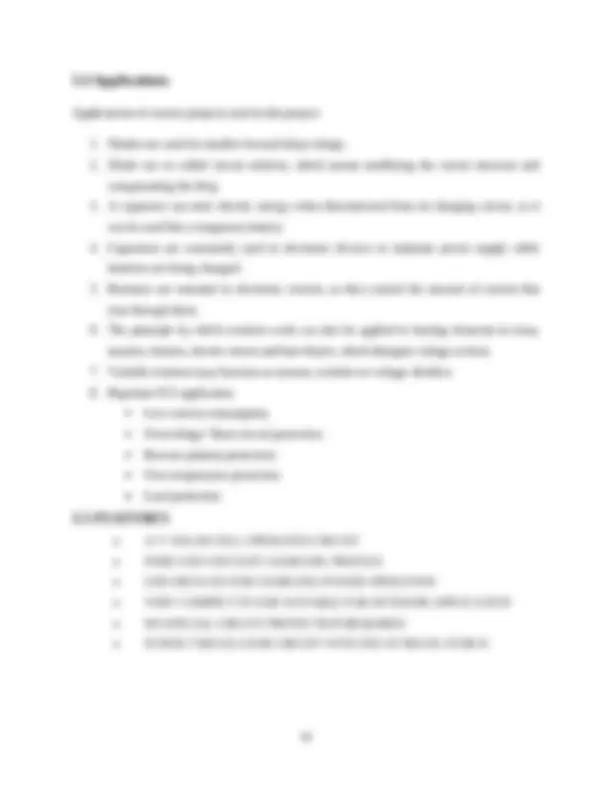
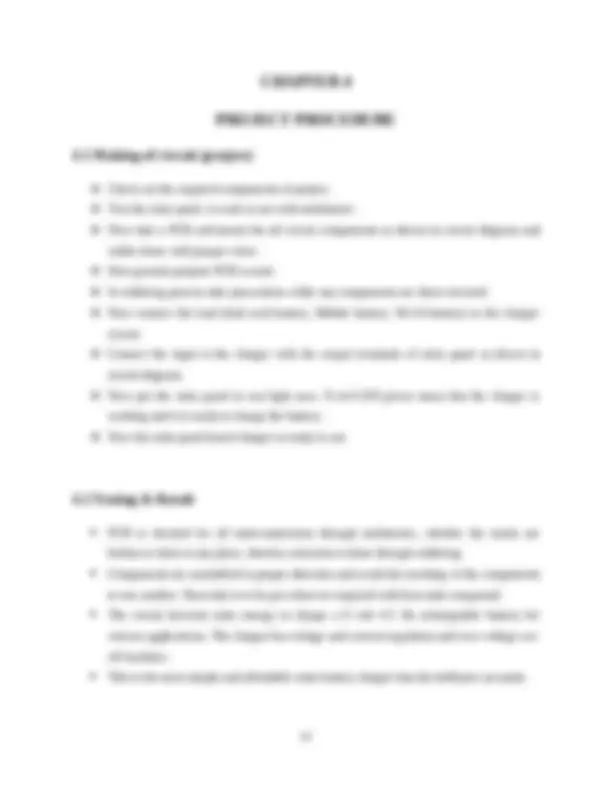
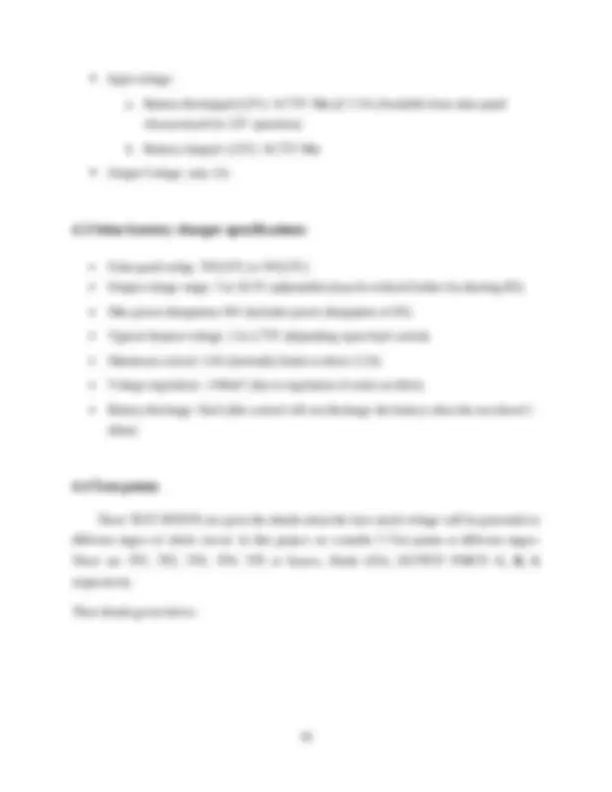
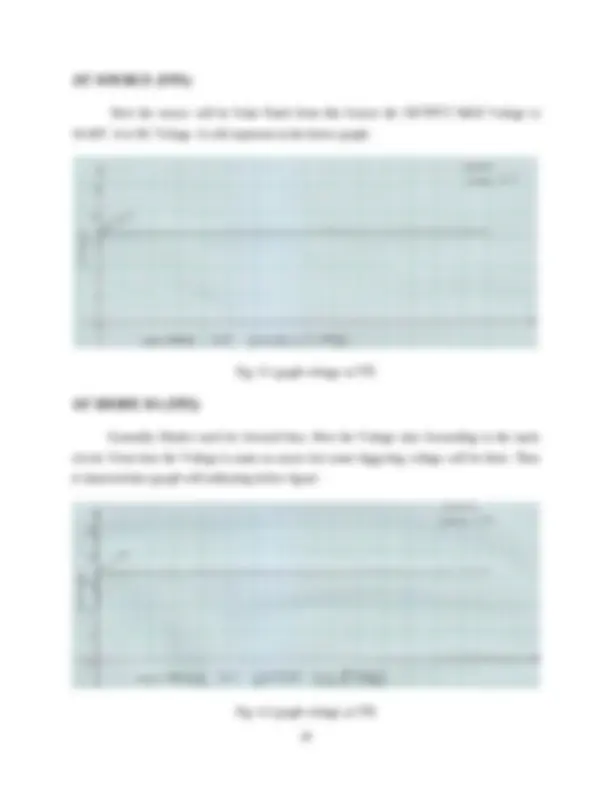
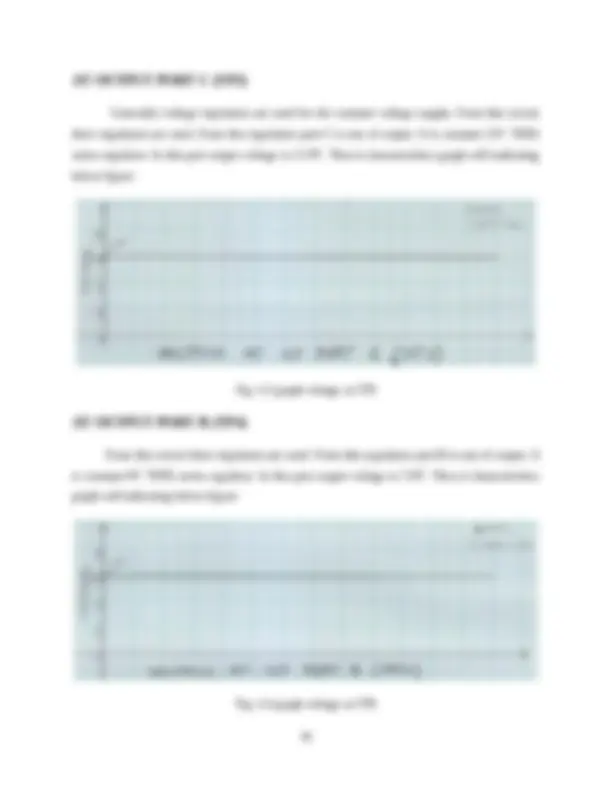
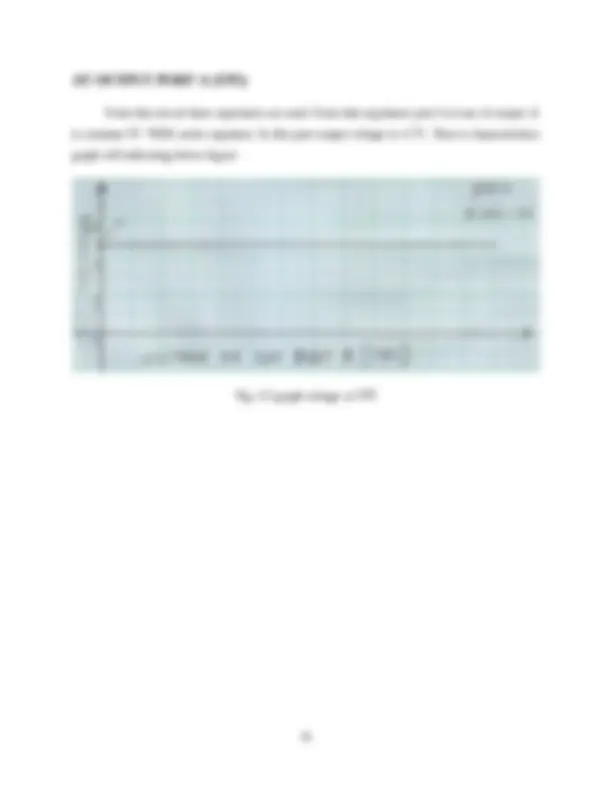
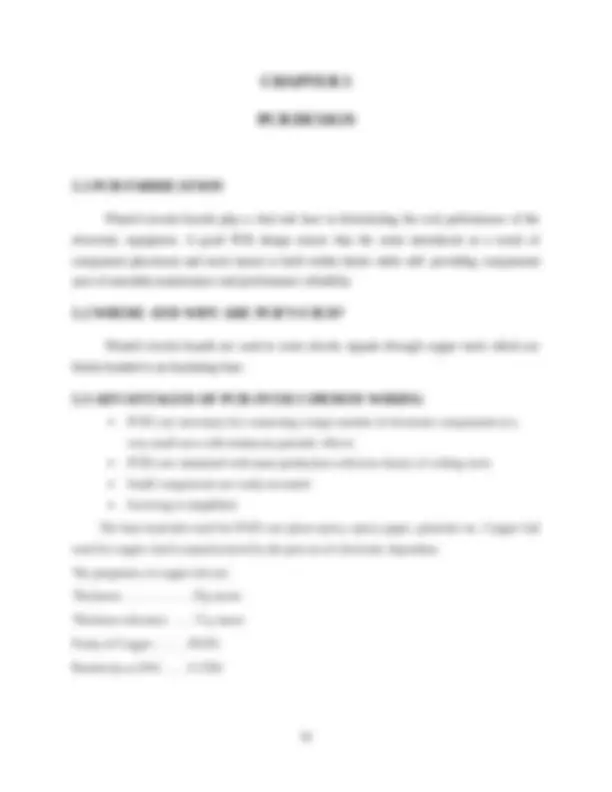
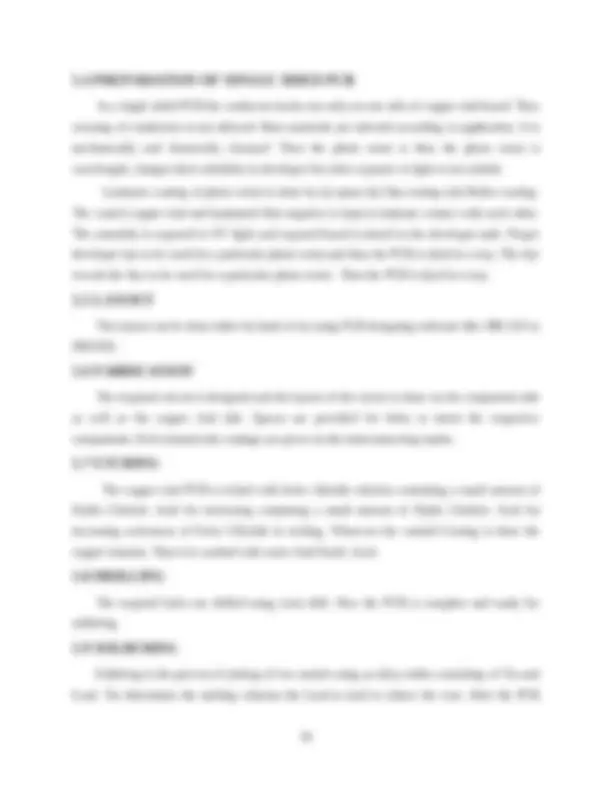
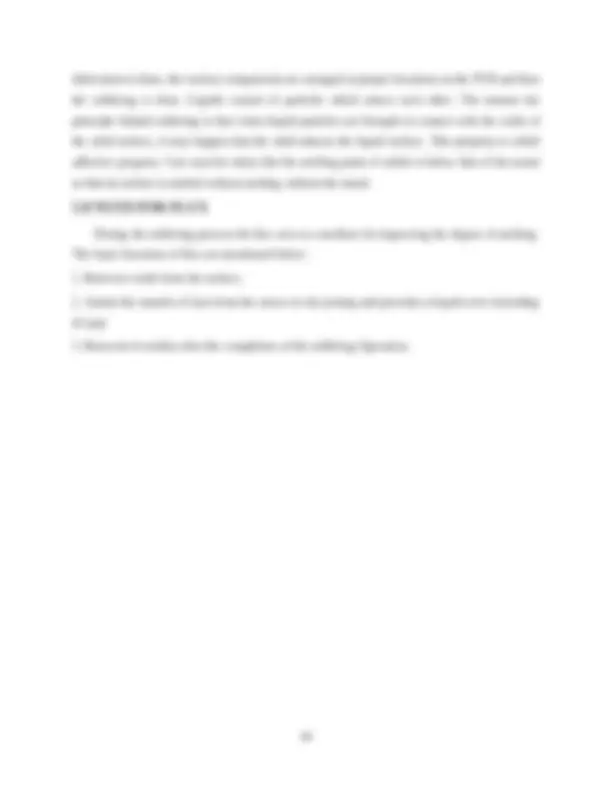
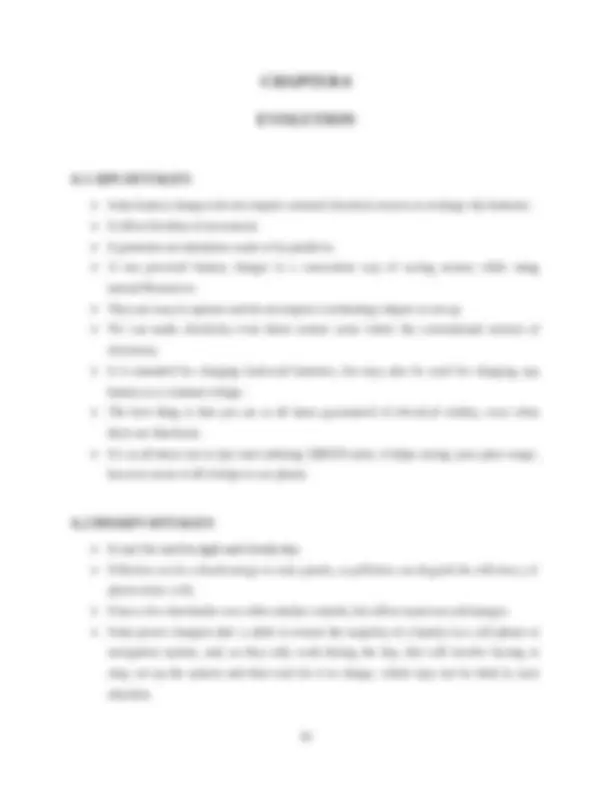
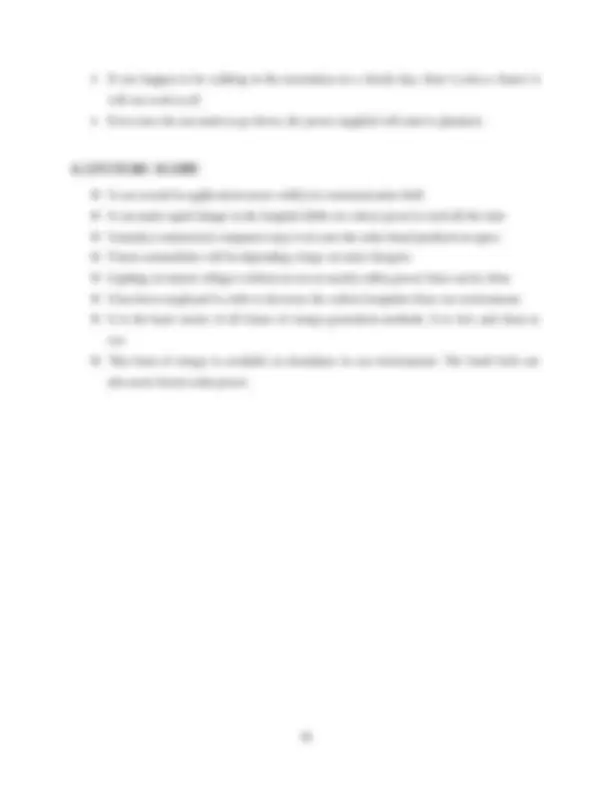
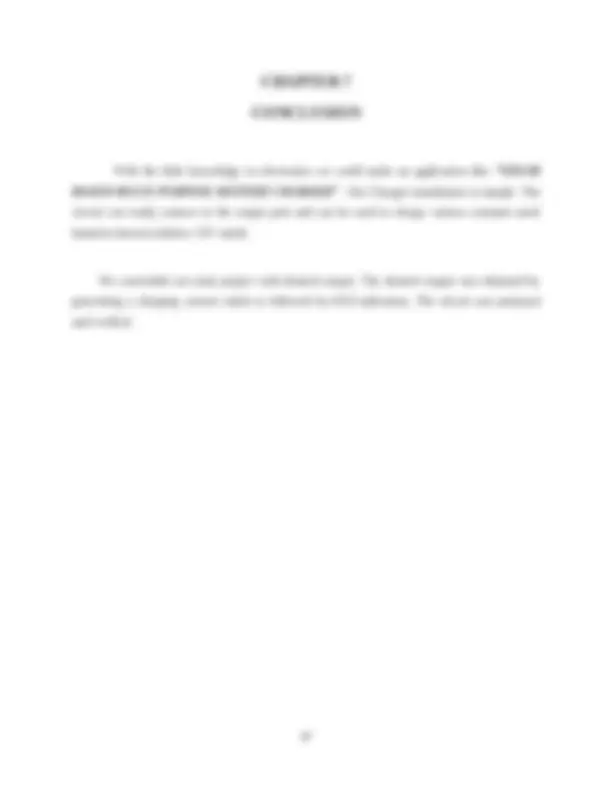
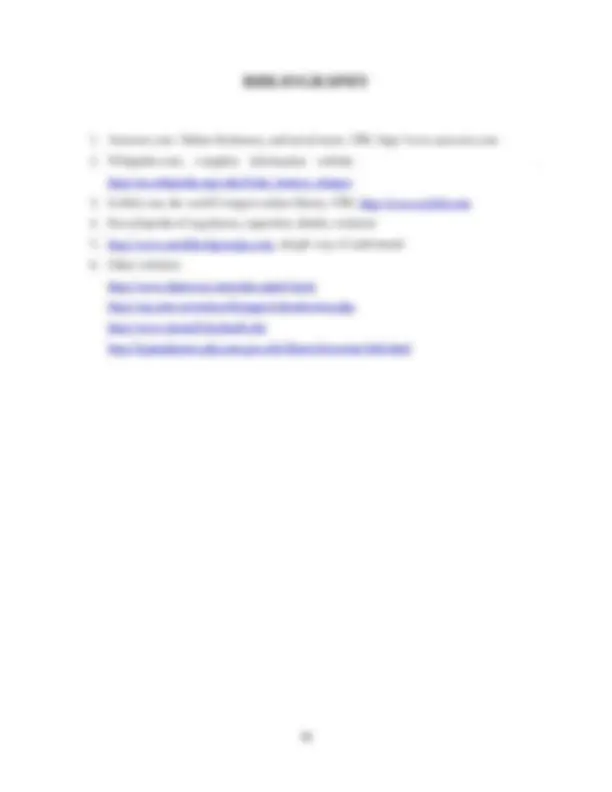
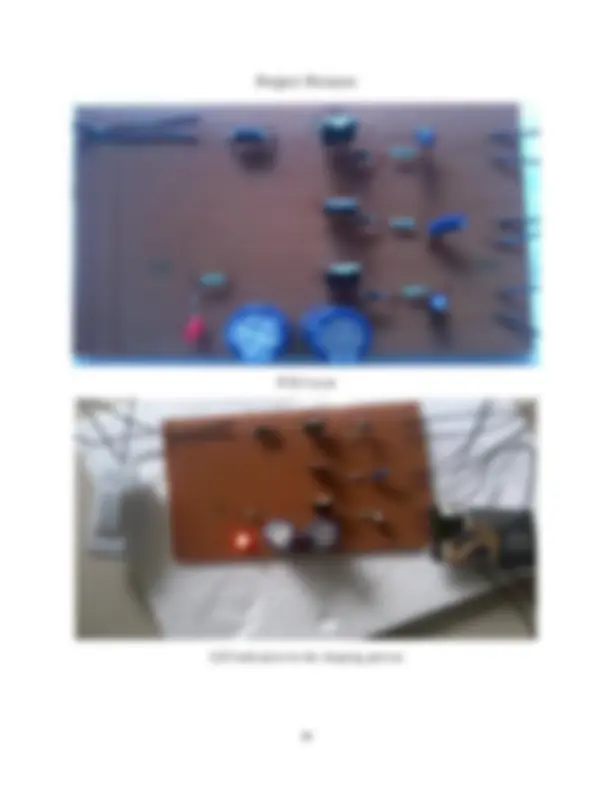
Study with the several resources on Docsity
Earn points by helping other students or get them with a premium plan
Prepare for your exams
Study with the several resources on Docsity
Earn points to download
Earn points by helping other students or get them with a premium plan
Community
Ask the community for help and clear up your study doubts
Discover the best universities in your country according to Docsity users
Free resources
Download our free guides on studying techniques, anxiety management strategies, and thesis advice from Docsity tutors
Non-conventional power generation is one of the fastest growing sectors. Globally, all countries are busy developing and implementing non-conventional power to bridge the electricity demand and power supply gap. Solar photovoltaic (PV) power is leading ahead of the other sources. In a solar power generation system, the PV cell plays a major role. The sun is the ultimate source of limitless solar energy in the form of light and heat. Light of the sun is directly converted into electrical energy.
Typology: Study Guides, Projects, Research
1 / 39
This page cannot be seen from the preview
Don't miss anything!
Non-conventional power generation is one of the fastest growing sectors. Globally, all countries are busy developing and implementing non-conventional power to bridge the electricity demand and power supply gap. Solar photovoltaic (PV) power is leading ahead of the other sources. In a solar power generation system, the PV cell plays a major role. The sun is the ultimate source of limitless solar energy in the form of light and heat. Light of the sun is directly converted into electrical energy without any inter mediate step. When the rays of the sun strike certain light-sensitive material like solar cell connected to an appropriate circuit, it exhibits a phenomenon called μphotovoltaic effect. The photovoltaic effect is the generation of an electrical current in a circuit containing a photosensitive device when the device is illuminated by visible or invisible light. In other words, light is directly converted into electricity. The photovoltaic effect can be achieved by using a variety of materials like silicon, selenium, cadmium sulphide, germanium, gallium arsenide or amorphous glass.
PV cells were invented in 1953 by Charles Fariett. A PV cell is used for converting photon into electron and with sun light incident, electrical energy is generated. The solar- based battery may be used to directly feed electricity to electronic equipment or for domestic heating. Solar batteries can also be used for satellites, communication equipment and domestic appliances. A selenium-or silicon-based solar cell exhibits open-circuit voltage of only 0.5V and short- circuit cell current of the order of 1milliampere for 6.4cm² area of the cell at 6458meter candles. Therefore a large number of such silicon or selenium solar cells need to be connected in series and parallel to provide any significant power. A telemetry system required to operate 24 hours a day requires a solar panel providing 5 watts at 12 volts used for recharging corresponding storage batteries during daylight hours.
Fig 1.1 Solar cell 1.3 TYPES OF PHOTOVOLTAIC CELL At the present time, most commercial photovoltaic cells are manufactured from silicon, the same material from which sand is made. In this case, however, the silicon is extremely pure. Other, more exotic materials such as gallium arsenide are just beginning to make their way into the field. The four general types of silicon photovoltaic cells are: Single-crystal silicon Polycrystal silicon (also known as multi crystal silicon) Ribbon silicon Amorphous silicon (abbreviated as “a Si” also known as thin film silicon)
Most photovoltaic cells are single-crystal types. To make them, silicon is purified, melted, and crystallized into ingots. The ingots are sliced into thin wafers to make individual cells. The cells have a uniform color, usually blue or black typically, most of the cell has a slight positive electrical charge.
Ribbon-type photovoltaic cells are made by growing a ribbon from the molten silicon instead of an ingot. These cells operate the same as single and Polycrystal cells. The anti- reflective coating used on most ribbon silicon cells gives them a prismatic rainbow appearance.
The previous three types of silicon used for photovoltaic cells have a distinct crystal structure. Amorphous silicon has no such structure. Amorphous silicon is sometimes abbreviated "a-Si" and is also called thin film silicon. Amorphous silicon units are made by depositing very thin layers of vaporized silicon in a vacuum onto a support of glass, plastic, or metal. Amorphous silicon cells are produced in a variety of colors since they can be made in sizes up to several square yards; they are made up in long rectangular "strip cells." These are connected in series to make up "modules." Modules of all kinds are described because the layers of silicon allow some light to pass through, multiple layers can be deposited. The added layers increase the amount of electricity the photovoltaic cell can produce. Each layer can be "tuned" to accept a particular band of light wavelength. The performance of amorphous silicon cells can drop as much as 15% upon initial exposure to sunlight. This drop takes around six weeks. Manufacturers generally publish post exposure performance data, so if the module has not been exposed to sunlight, its performance will exceed specifications at first. The efficiency of amorphous silicon photovoltaic modules is less than half that of the other three technologies. This technology has the potential of being much less expensive to manufacture than crystalline silicon technology. For this reason, research is currently underway to improve amorphous silicon performance and manufacturing processes. In 2002, the highest reported efficiency for thin film solar cells based on CdTe is 18%, which was achieved by research at Sheffield Hallam University, although this has not been confirmed by an external test laboratory. The US national renewable energy research facility NREL achieved an efficiency of 19.9% for the solar cells based on copper indium gallium selenide thin films, also known as CIGS NREL has since developed a robot that builds and analyzes the efficiency of thin-film solar cells with the goal of increasing the efficiency by testing the cells in different situations. These CIGS
films have been grown by physical vapor deposition in a three-stage co- evaporation process. In this process In, Ga and Se are evaporated in the first step; in the second step it is followed by Cu and Se co-evaporation and in the last step terminated by In, Ga and Se evaporation again. Thin film solar has approximately 15% market share. The other 85% is crystalline silicon. Most of the commercial production of thin film solar is CdTe with an efficiency of 11% Crystalline Silicon. The highest efficiencies on silicon have been achieved on monocrystalline cells. The highest commercial efficiency (22%) is produced by Sun Power, which uses expensive, high- quality silicon wafers. The University of New South Wales has achieved 25% efficiency on monocrystalline silicon in the lab technology that has been commercialized through its partnership with Sun Power. Crystalline silicon devices are approaching the theoretical limiting efficiency of 29% and achieve an energy payback period of 1-2 years. By far, the most prevalent bulk material for solar cells is crystalline silicon (abbreviated as a group as c-Si), also known as "solar grade silicon". Bulk silicon is separated into multiple categories according to crystallinity and crystal size in the resulting ingot, ribbon, or wafer.
1. Monocrystalline silicon(c-Si): often made using the Czochralski process. Single- crystal wafer cells tend to be expensive, and because they are cut from cylindrical ingots, do not completely cover a square solar cell module without a substantial waste of refined silicon. Hence most c-Si panels have uncovered gaps at the four corners of the cells. 2. Poly- or multicrystalline silicon (poly-Si or mc-Si): made from cast square ingots large blocks of molten silicon carefully cooled and solidified. Poly-Si cells are less expensive to produce than single crystal silicon cells, but are less efficient. US DOE data shows that there were a higher number of multicrystalline sales than monocrystalline silicon sales. 3. Ribbon silicon is a type of multicrystalline silicon: it is formed by drawing flat thin films from molten silicon and results in a multicrystalline structure. These cells have lower efficiencies than poly-Si, but save on production costs due to a great reduction in silicon waste, as this approach does not require sawing from ingots.
The most commonly known solar cell is configured as a large-area p-n junction made from silicon. As a simplification, one can imagine bringing a layer of n-type silicon into direct contact with a layer of p-type silicon. In practice, p-n junctions of silicon solar cells are not made in this way, but rather by diffusing an n-type do pant into one side of a p-type wafer (or vice versa).If a piece of p-type silicon is placed in intimate contact with a piece of n-type silicon, then a diffusion of electrons occurs from the region of high electron concentration (the n-type side of the junction) into the region of low electron concentration (p-type side of the junction). When the electrons diffuse across the p-n junction, they recombine with holes on the p-type side. The diffusion of carriers does not happen indefinitely, however, because charges build up on either side of the junction and create an electric field. The electric field creates a diode that promotes charge flow, known as drift current that opposes and eventually balances out the diffusion of electron and holes. This region where electrons and holes have diffused across the junction is called the depletion region because it no longer contains any mobile charge carriers. It is also known as the space charge region Fig 1.2: P-N junction characteristics
Hence from this chapter we discussed about the solar energy. How the PV cell generation, function, types, working and characteristics. The solar cell diagram gives us information about the working function of general PV cell. The figure 1.2 gives the information about the P-N junction schematic function and symbol. From the topic of photo generation of charge carriers we understood the silicon function in PV cell and conversion of light source to electricity.
Fig 2.2: Block diagram of solar charger The above shown diagram includes the total block diagram representation of components included in the project. By this project three different batteries can be charged using the solar energy. Each block is discussed in detail below.
Here a 12 volt 5 watt solar panel is used as the source of current. A solar panel (photovoltaic module or photovoltaic panel) is a packaged interconnected assembly of solar cells, also known as photovoltaic cells. The solar panel can be used as a component of a larger photovoltaic system to generate and supply electricity in commercial and residential applications. This solar panel converts the light energy in to electrical energy. The cells in the panel are made up of semiconductor material which transforms light energy into electrical energy. When the sunlight is maximum, the solar module can generate around 16.5 volts at 400 mA. This current is used to charge the battery.
A rectifier is an electrical device that converts alternating current (AC), which periodically reverses direction, to direct current (DC), which is in only one direction, a process known as rectification. Rectifiers have many uses including as components of power supplies and as detectors of radio signals. Rectifiers may be made of solid state diodes, silicon-controlled rectifiers, vacuum tube diodes, mercury arc valves, and other components. Here an IN 5492 diode is used.
Here light-emitting diode, LED is used as indicator. It indicates the charging process. It is a semiconductor light source. LEDs are used as indicator lamps in many devices and are increasingly used for other lighting.
High value capacitors act as current buffers so that a short duration interruption in current flow from the panel will not affect the charging process. It will store the Voltage from the solar panel and act as a storage box.
Fig 3.1: Circuit diagram A: MOBILE BATTERY B: Ni-Cd BATTERY C: Lead Acid BATTERY
A 12 volt 5 Watt solar panel is used as the source of current. The cells in the panel are made up of semiconductor material which transforms light energy into electrical energy. When the sunlight is Maximum, the solar module can generate around 16.5 volts at 400mA. This current is used to charge the battery. Diode D1 allows current into three regulator ICs to provide regulated voltage to the load. The diode D1 is 5402; it is general diode for converting AC to DC. IC1 7812 gives 12 volts and 400 mA current to charge a Lead Acid battery. The battery can be connected to point C and ground. IC2 7806 gives regulated 6 volts to charge Ni-Cd battery Resistor R1, R2 restricts the charging current. IC3 7805 provides regulated 5 volts to charge all types of Mobile phone batteries which are rated at 3.6 volts. Resistor R3 restricts charging current to a safer level. Point A can also use to charge Lithium ion and Ni-Mh batteries. Before point C, Point B, Point A battery protectors will be connected, it will protect the battery in output. The battery protector consists Diode and capacitor. High value capacitors C4 and C5 act as current buffers so that a short duration interruption in current flow from the panel will not affect the charging process. Red LED indicates the charging process.
and parallely. The serial connections increase the output voltage while the parallel connections increase current output. The solar cell is a semiconductor device capable of trapping solar energy and converting it into electric energy. The semiconductor in the solar panel has both electron and hole pairs, so by the influence of the external energy from sun light, electron-hole pairing occurs that leads to the generation of electric current. Electrical energy is stored in electromagnetic fields, which in turn can make a current of electrons flow. Thus a solar cell converts light, a flow of photons, to electric current, a flow of electrons. Fig 3.2: Solar panel diagram The solar cells are Photovoltaic cells (PV Cells) which has a large p-n junction doped with light sensitive semiconductor material which converts light energy into electrical energy through the Photovoltaic mechanism. In order to increase the efficiency of the system, large numbers of solar cells are used in the panel with interconnected arrangement. Each solar cell generates 1. volts.
The theory of the working of solar cell is simple. It has a p-type of silicon layer placed in contact with an n-type silicon layer and the diffusion of electrons occurs from the n-type material to the p-type material. In the p-type material, there are holes for accepting the electrons. The n- type material is rich in electrons, so by the influence of the solar energy, the electrons move from the n- type material and in the p-n junction, the combine with holes. This creates a charge on either side of the p-n junction to create an electric field. As a result of this, a diode like system develops which promotes charge flow. This is the drift current that balances the diffusion of electrons and holes. The area in which drift current occurs is the depletion zone or space charge region that lacks the mobile charge carriers.
In electronics, a diode is a two-terminal electronic component that conducts electric current in only one direction. The term usually refers to a semiconductor diode, the most common type today. This is a crystalline piece of semiconductor material connected to two electrical terminals. The most common function of a diode is to allow an electric current to pass in one direction (called the diode's forward direction), while blocking current in the opposite direction (the reverse direction). Thus, the diode can be thought of as an electronic version of a check valve. This unidirectional behavior is called rectification, and is used to convert alternating current to direct current, and to extract modulation from radio signals in radio receivers. However, diodes can have more complicated behavior than this simple on-off action. This is due to their complex non-linear electrical characteristics, which can be tailored by varying the construction of their P- N junction. Fig 3.3: Diode symbol
A capacitor (formerly known as condenser ) is a device for storing electric charge. The forms of practical capacitors vary widely, but all contain at least two conductors separated by a non-conductor. Capacitors used as parts of electrical systems, for example, consist of metal foils separated by a layer of insulating film. A capacitor is a passive electronic component consisting of a pair of conductors separated by a dielectric (insulator). When there is a potential difference (voltage) across the conductors, a static electric field develops across the dielectric, causing positive charge to collect on one plate and negative charge on the other plate. Energy is stored in the electrostatic field. An ideal capacitor is characterized by a single constant value, capacitance, measured in farads. This is the ratio of the electric charge on each conductor to the potential difference between them. Capacitors are widely used in electronic circuits for blocking direct current while allowing alternating current to pass, in filter networks, for smoothing the output of power supplies, in the resonant circuits that tune radios to particular frequencies and for many other purposes. The capacitance is greatest when there is a narrow separation between large areas of conductor. Hence capacitor conductors are often called "plates," referring to an early means of construction. In practice the dielectric between the plates passes a small amount of leakage current and also has an electric field strength limit, resulting in a breakdown voltage, while the conductors and leads introduce an undesired inductance and resistance. Fig 3.5: Symbol of capacitor In this project we used two types of capacitors. They are 4700uF/25V, 4.7uF/25V. Totally 5 capacitors used. Two are used as buffer and remaining 3 are used for battery protectors.
A light-emitting diode (LED) is a semiconductor light source. LEDs are used as indicator lamps in many devices and are increasingly used for other lighting. Introduced as a practical electronic component in 1962, early LEDs emitted low-intensity red light, but modern versions are available across the visible, ultraviolet and infrared wavelengths, with very high brightness. When a light-emitting diode is forward biased (switched on), Electrons are able to recombine with electron holes within the device, releasing energy in the form of photons. This effect is called electroluminescence and the color of the light (corresponding to the energy of the photon) is determined by the energy gap of the semiconductor. An LED is often small in area (less than 1 mm^2 ), and integrated optical components may be used to shape its radiation pattern. LEDs present many advantages over incandescent light sources including lower energy consumption, longer lifetime, improved robustness, smaller size, faster switching, and greater durability and reliability. LEDs powerful enough for room lighting are relatively expensive and require more precise current and heat management than compact fluorescent lamp sources of comparable output. Light-emitting diodes are used in applications as diverse as replacements for aviation lighting, automotive lighting as well as in traffic signals. The compact size, the possibility of narrow bandwidth, switching speed, and extreme reliability of LEDs has allowed new text and video displays and sensors to be developed, while their high switching rates are also useful in advanced Communications technology. Infrared LEDs are also used in the remote control units of many commercial products including televisions, DVD players, and other domestic appliances. Fig 3.6: LED substrate