
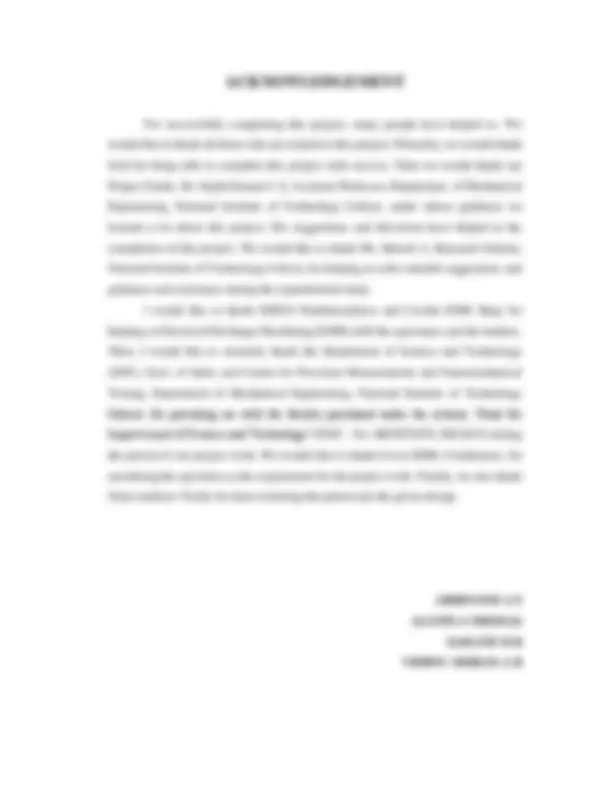
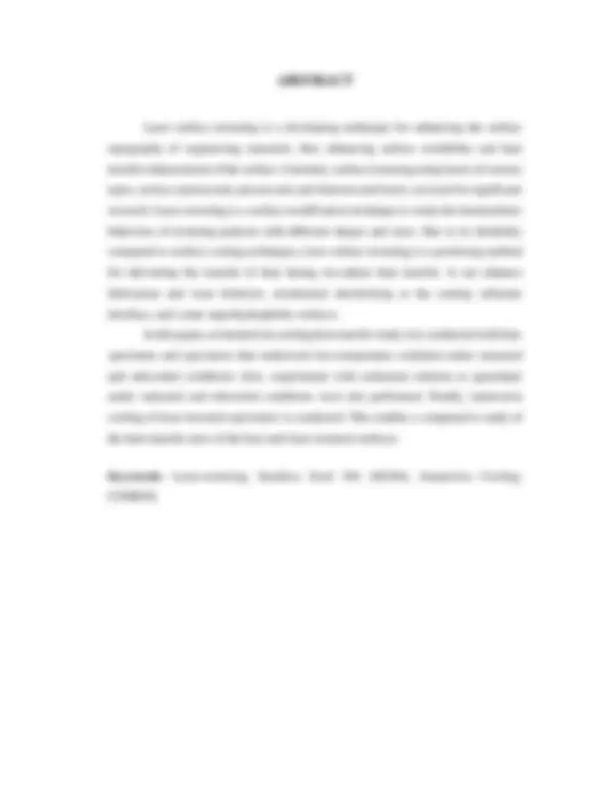
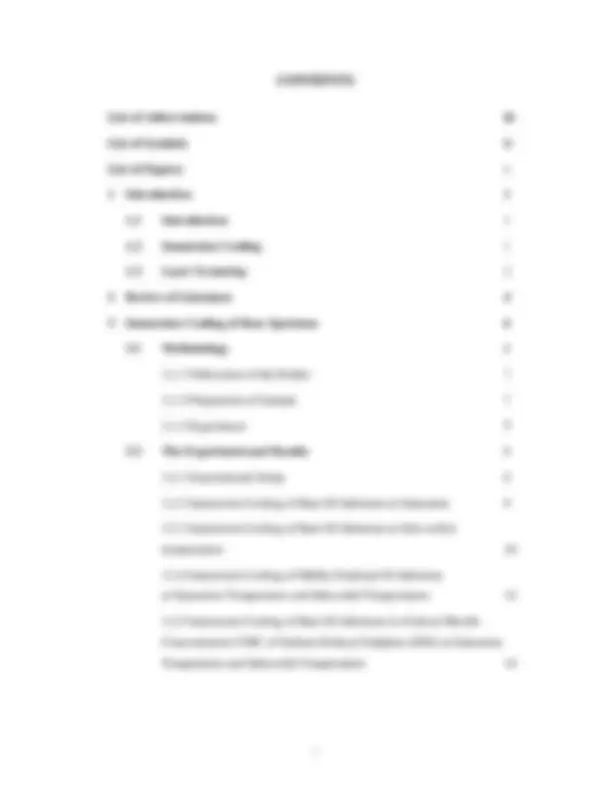
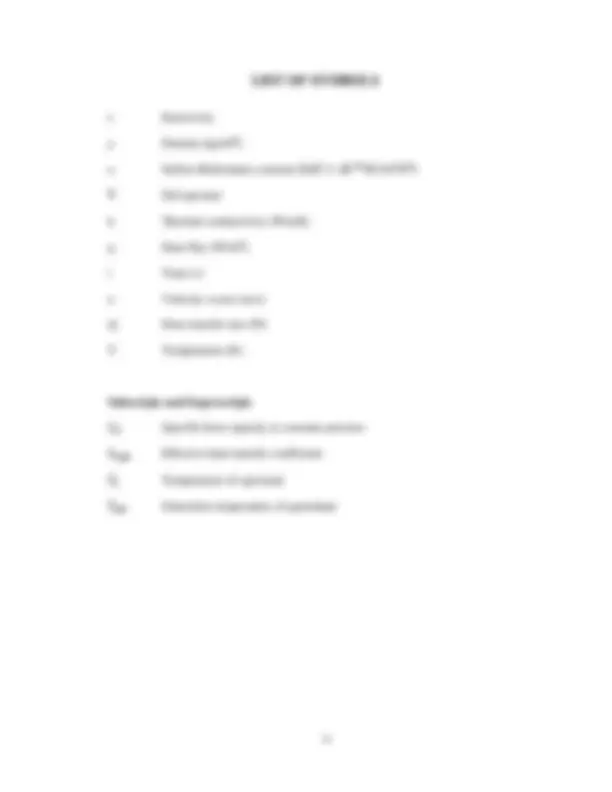
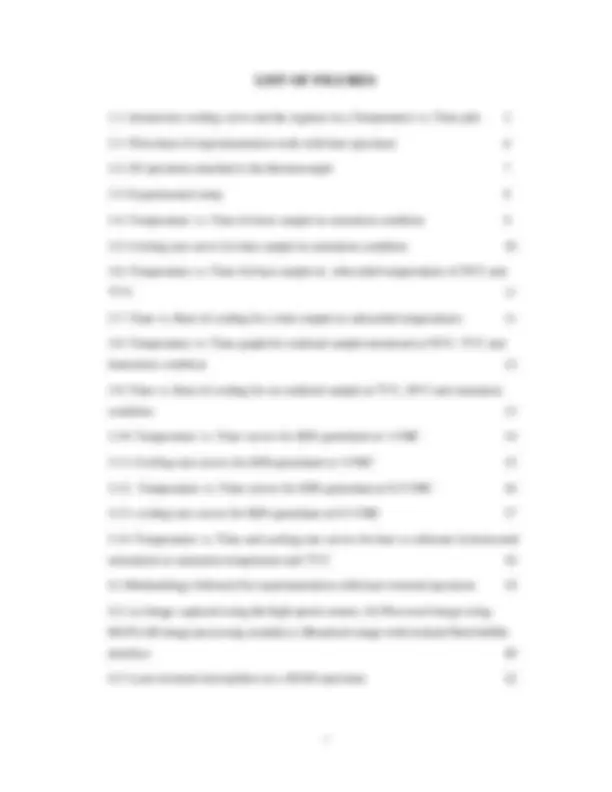
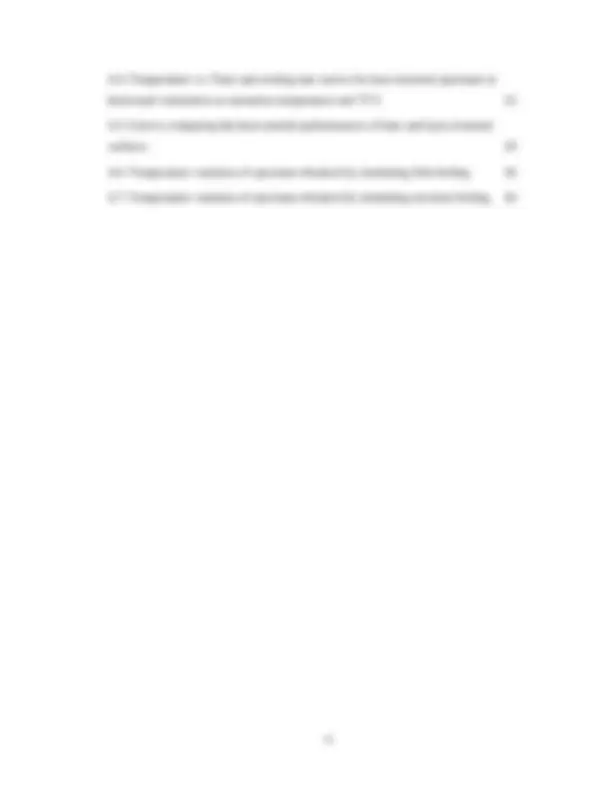
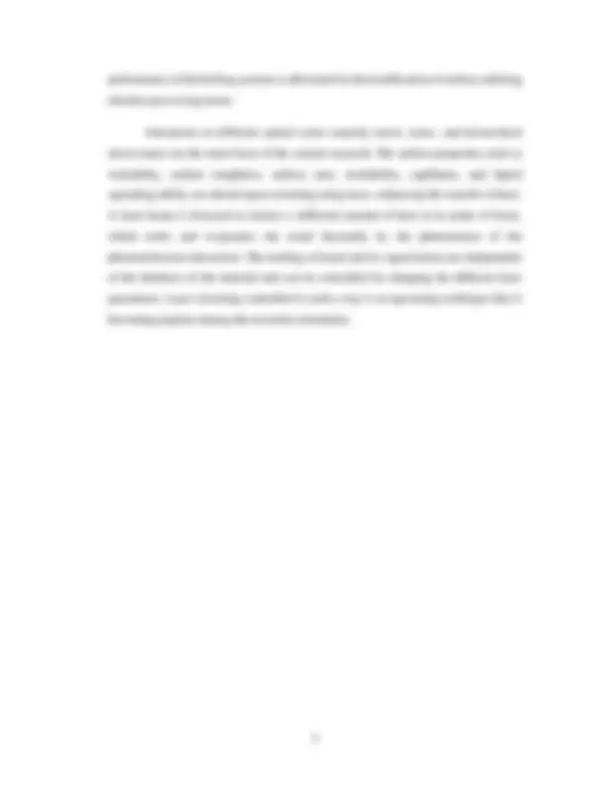
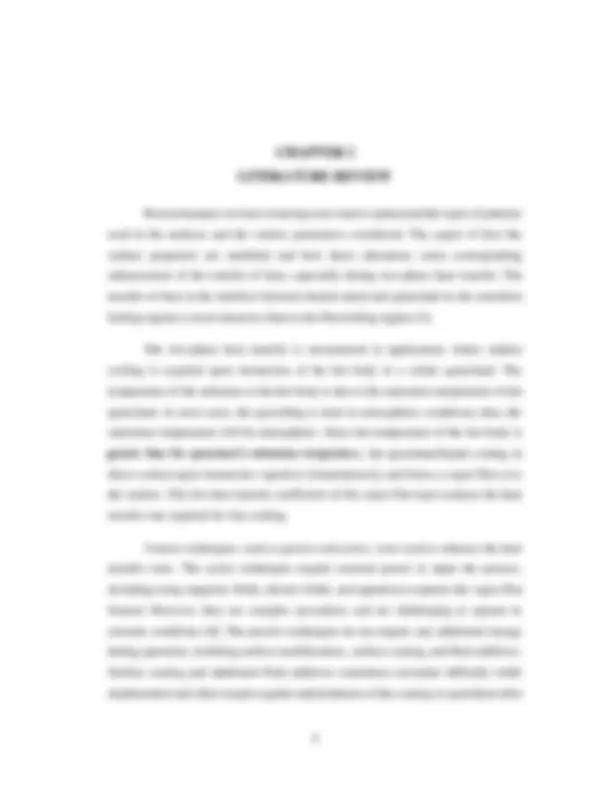
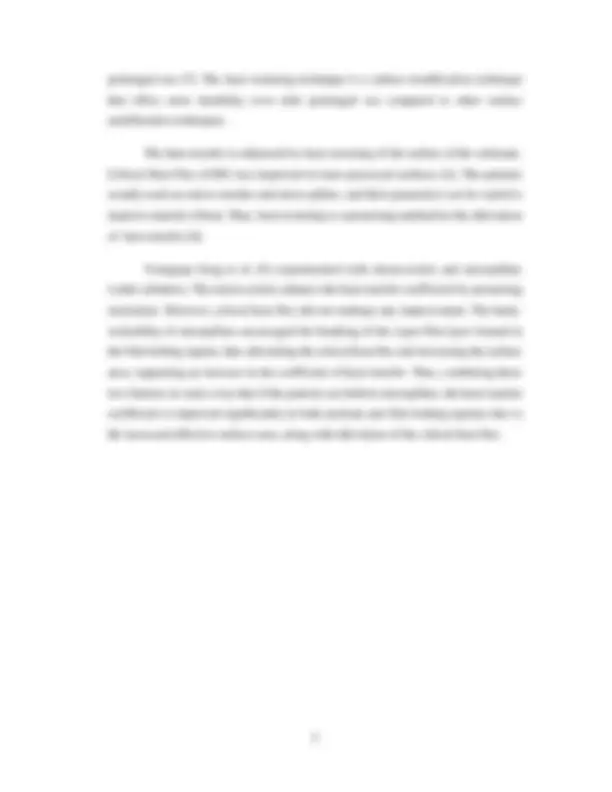
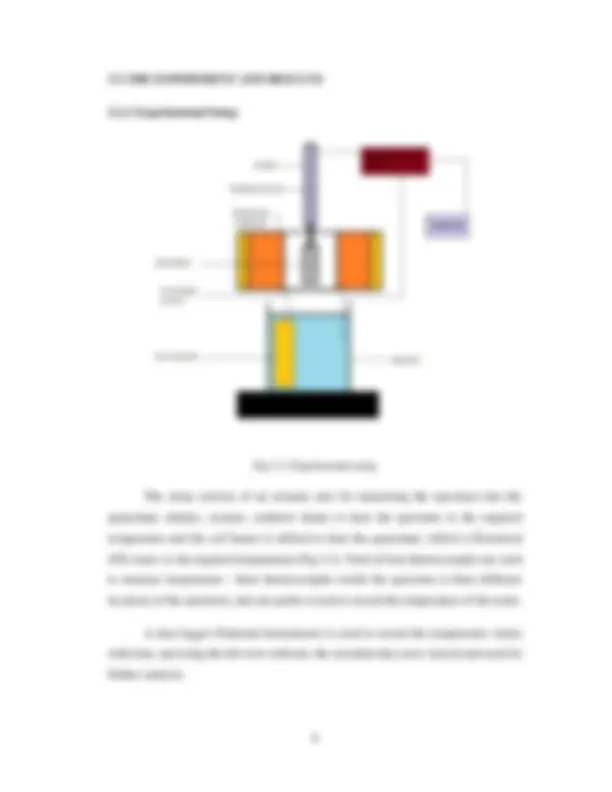
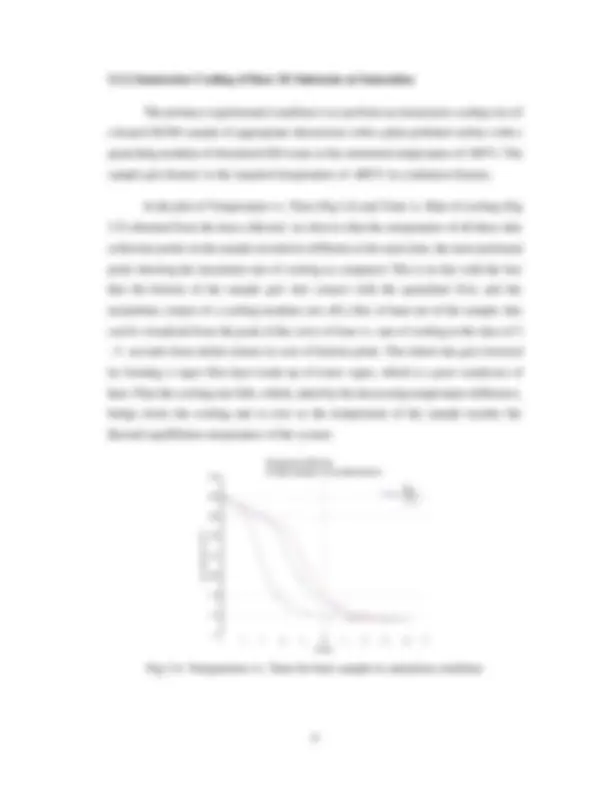
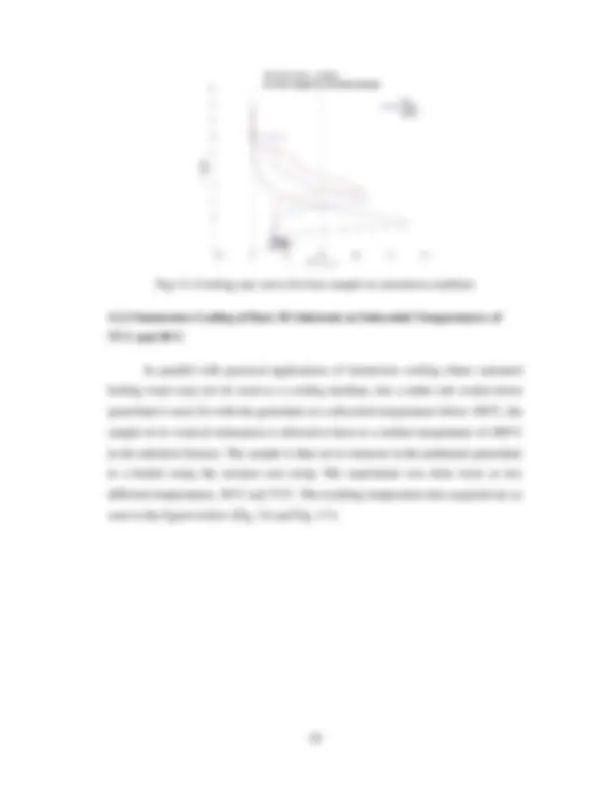
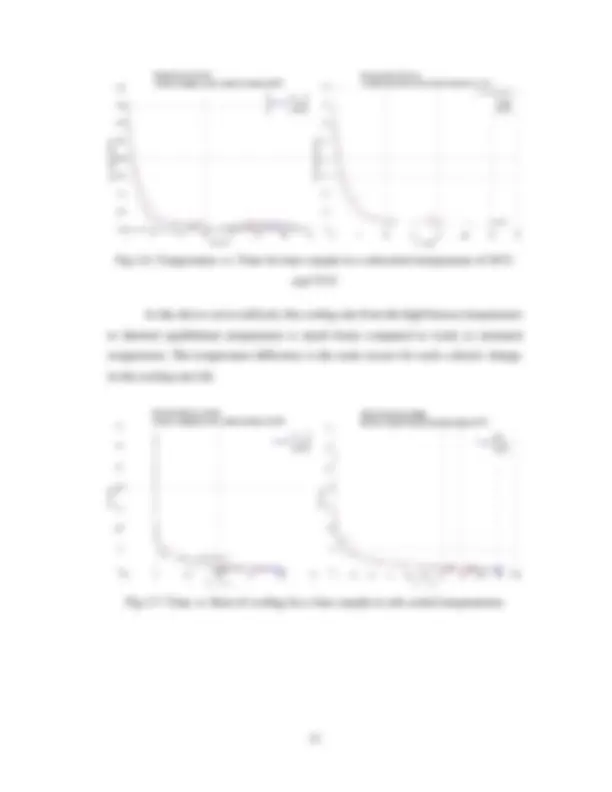
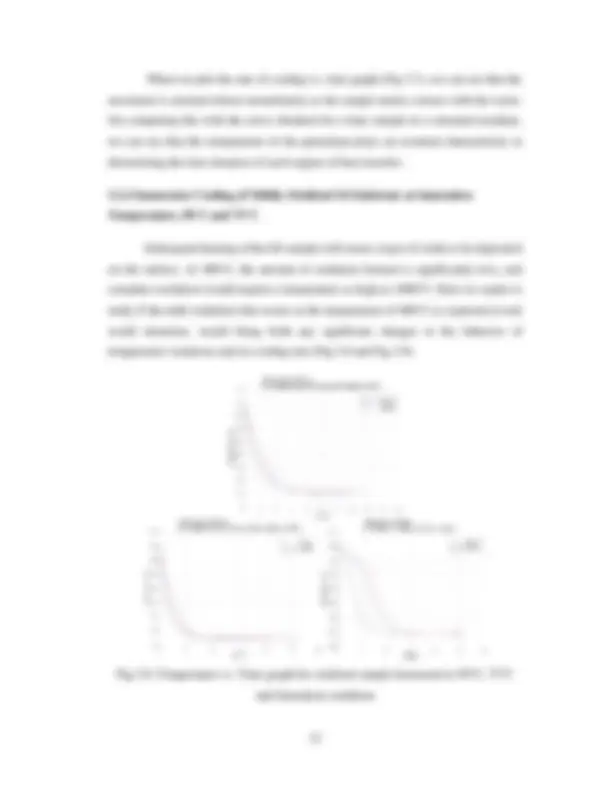
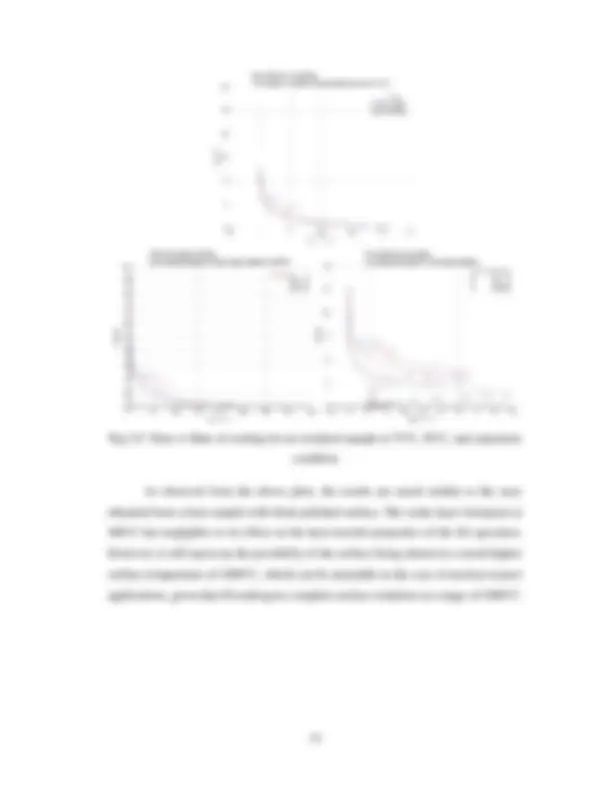
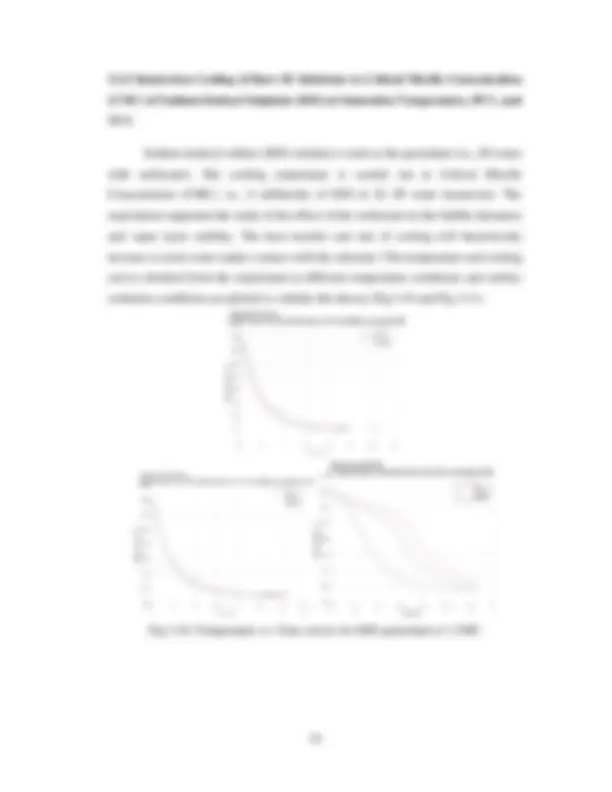
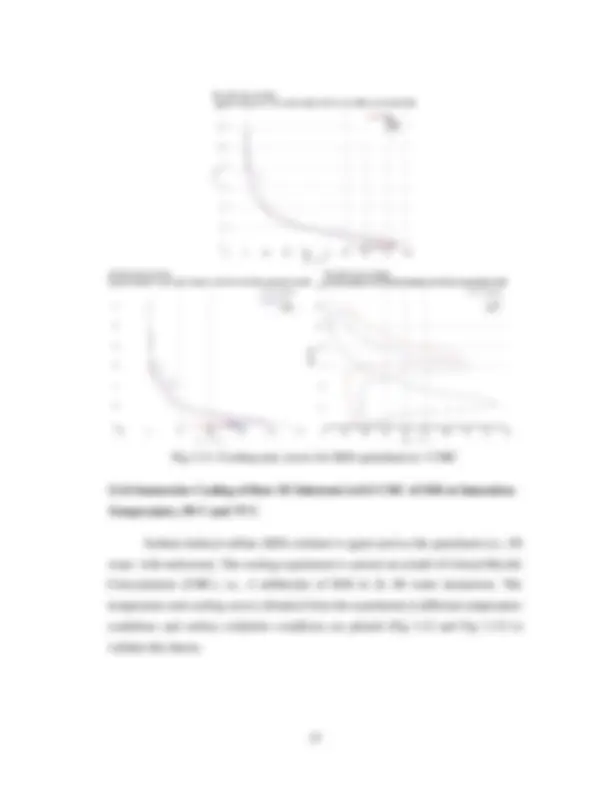
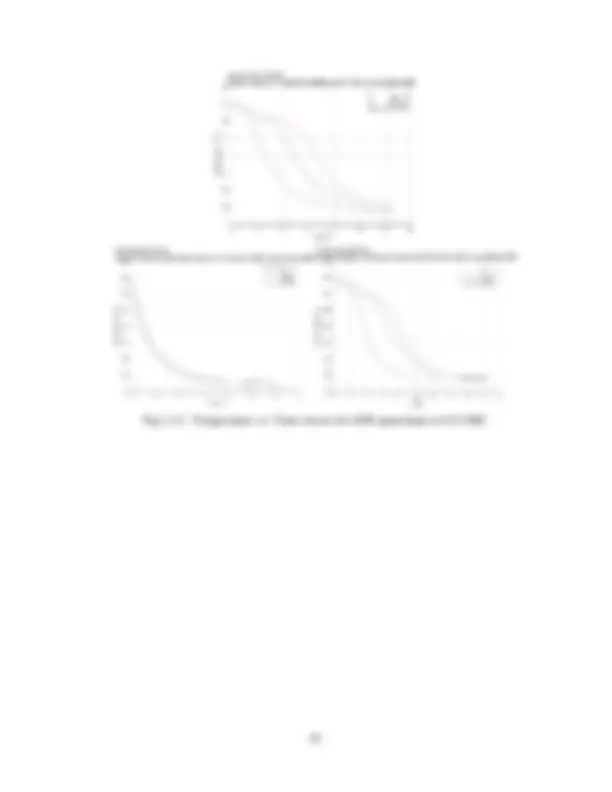
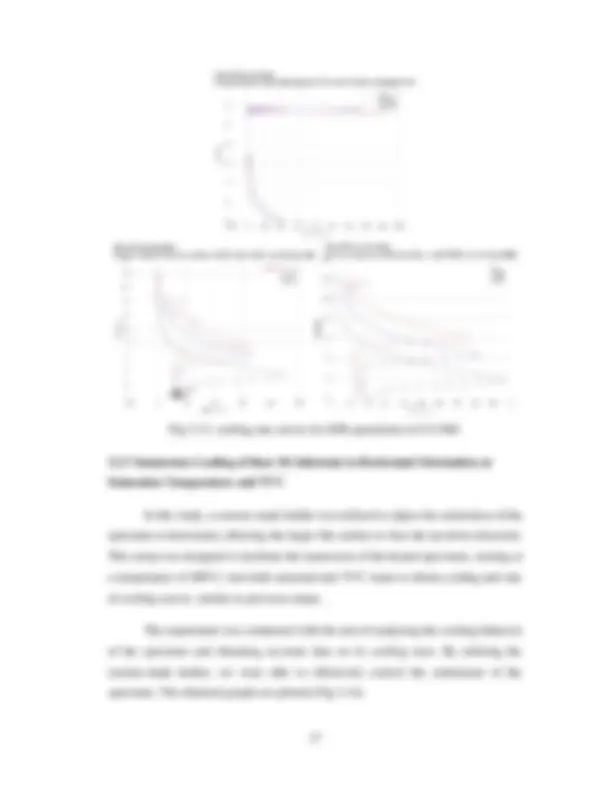
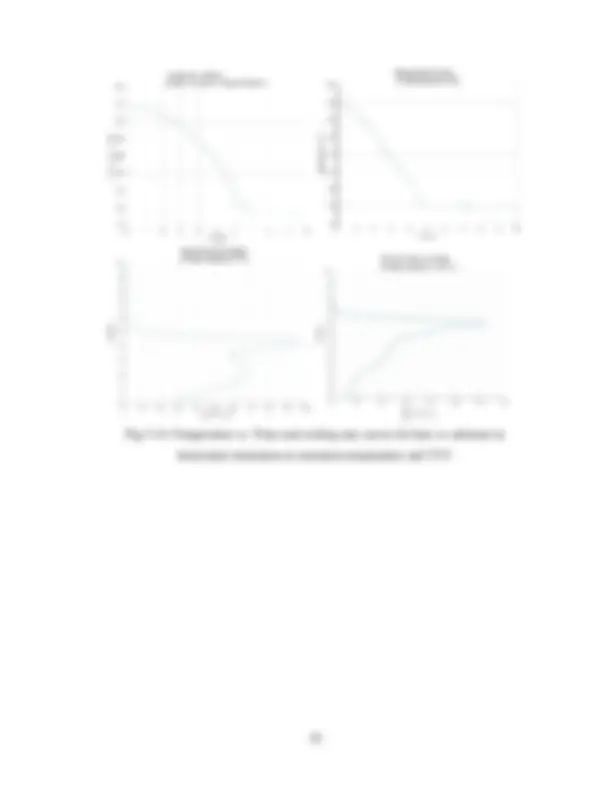
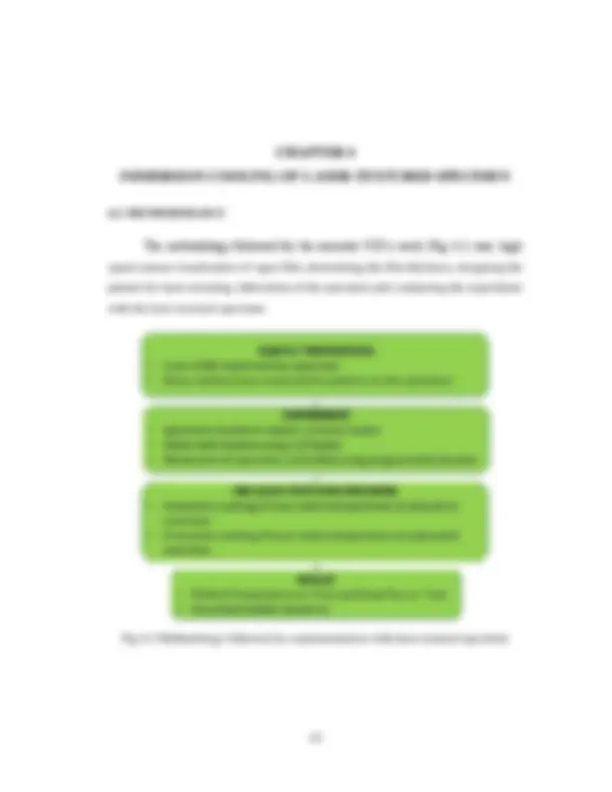
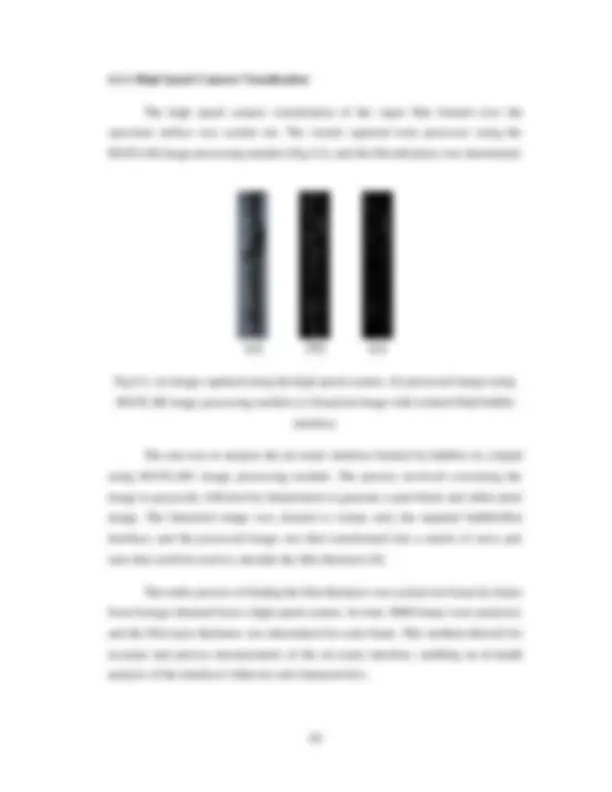
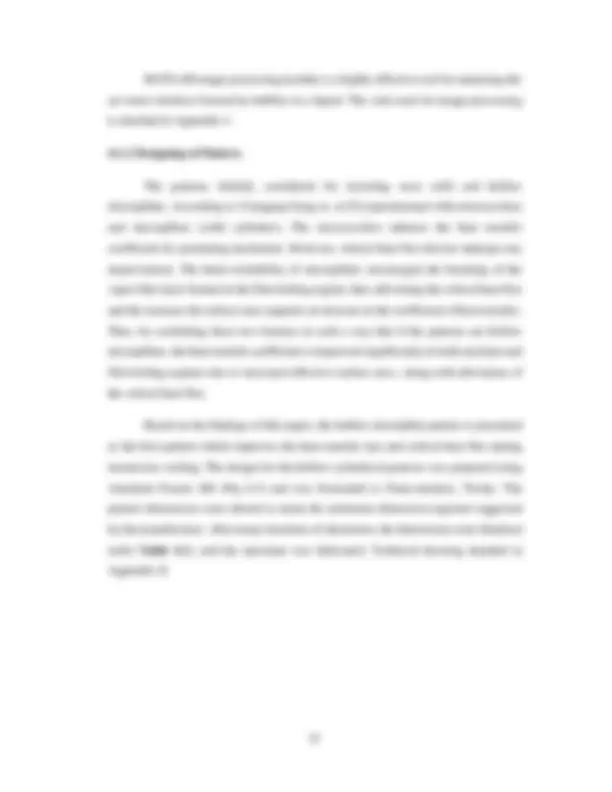
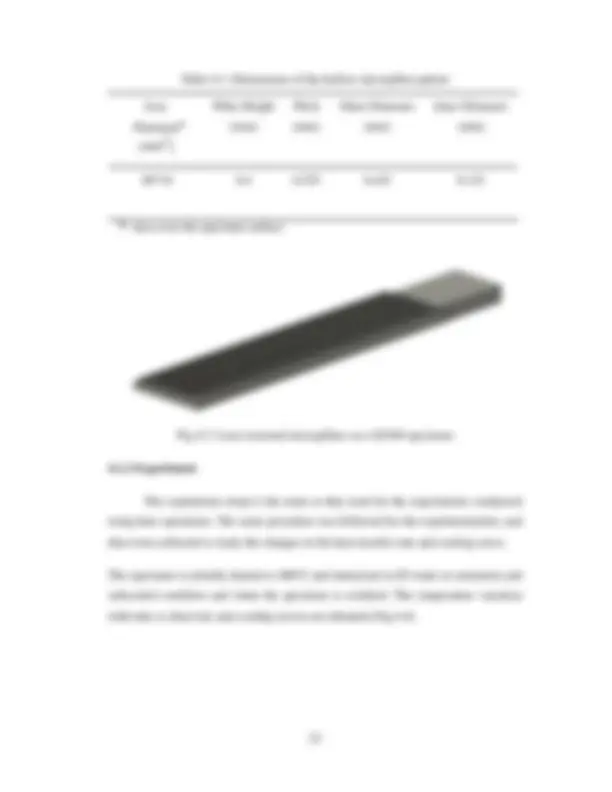
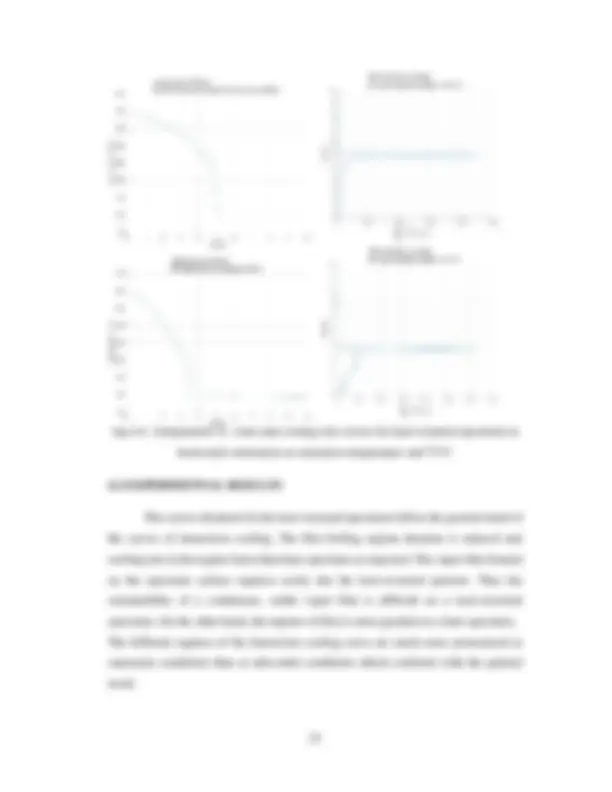
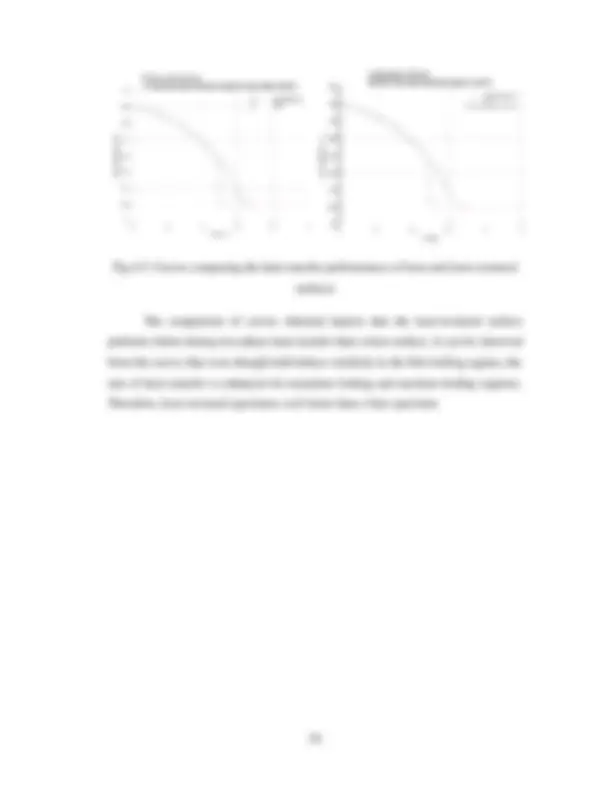
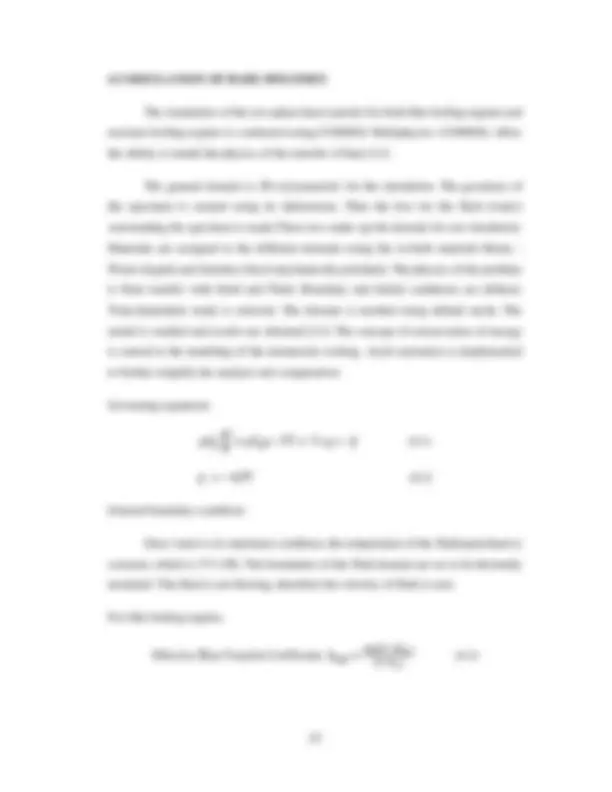
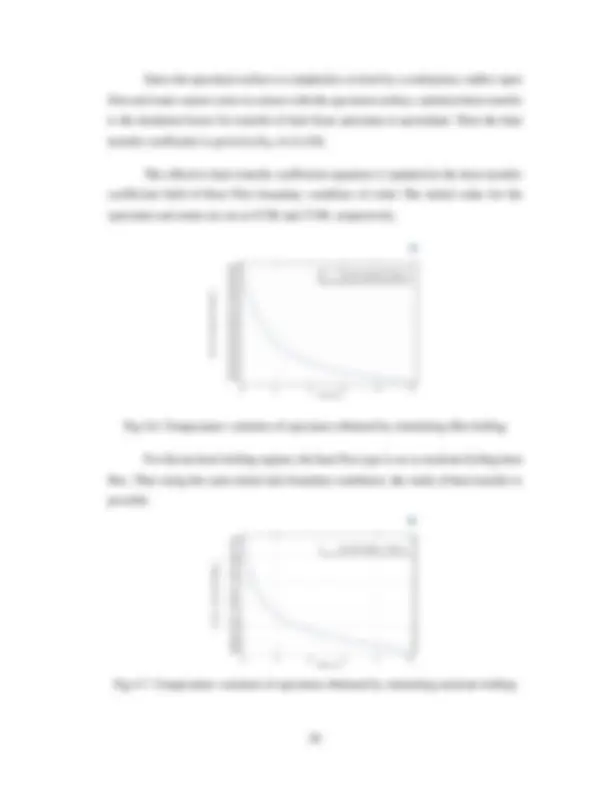
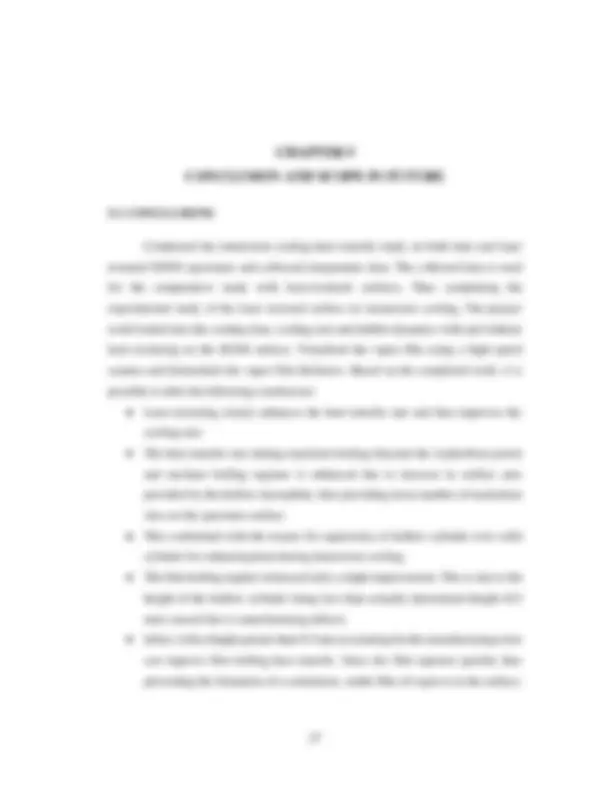
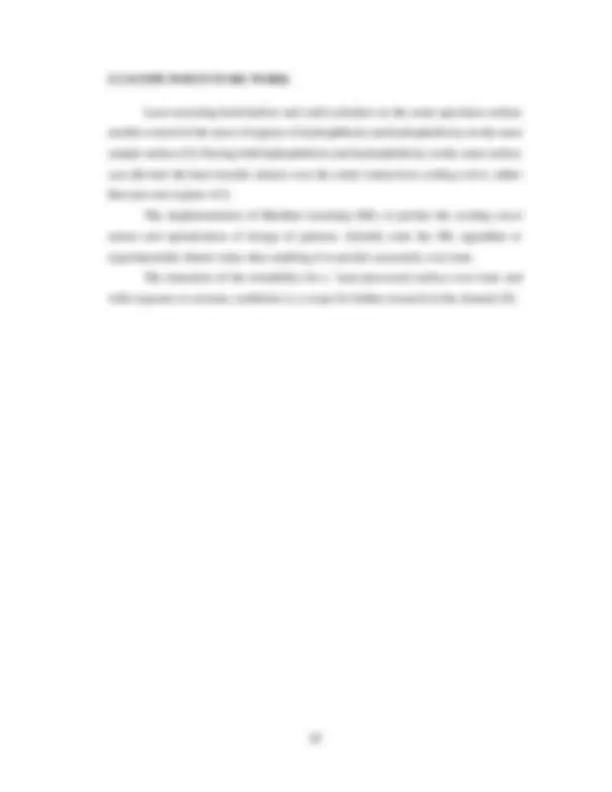
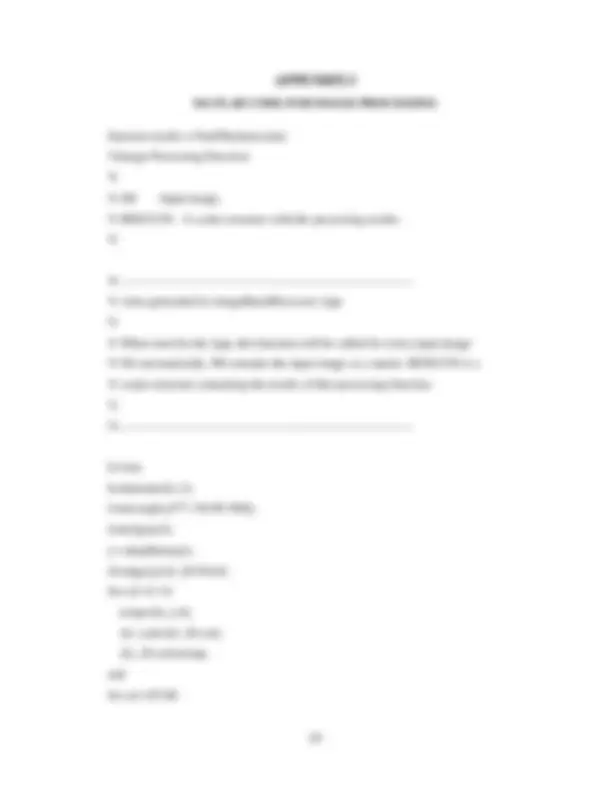
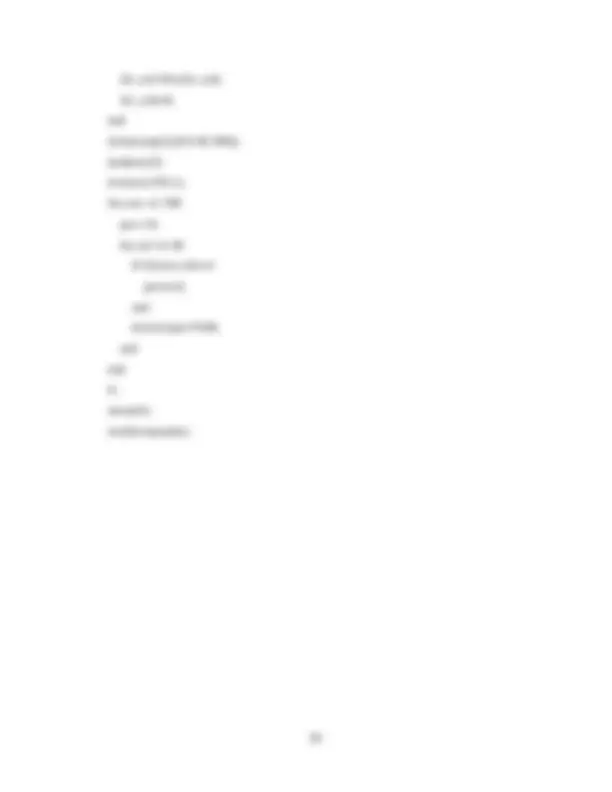
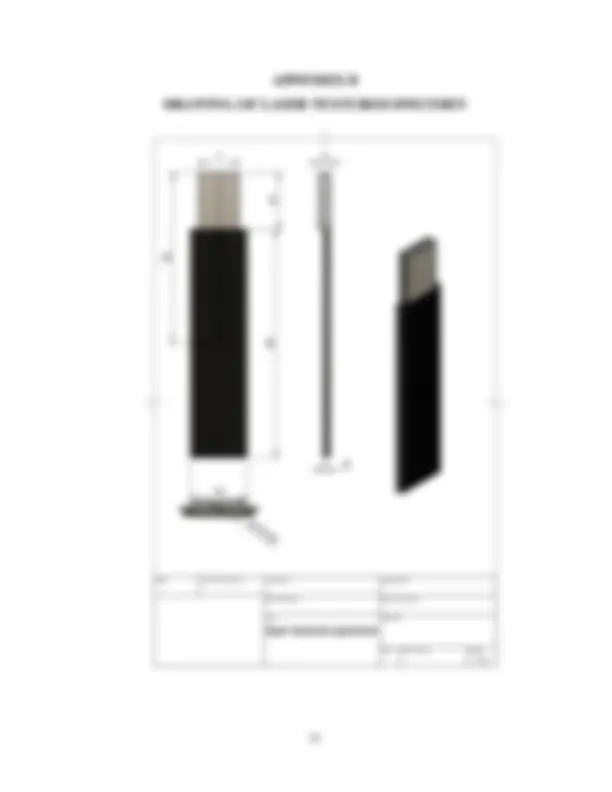
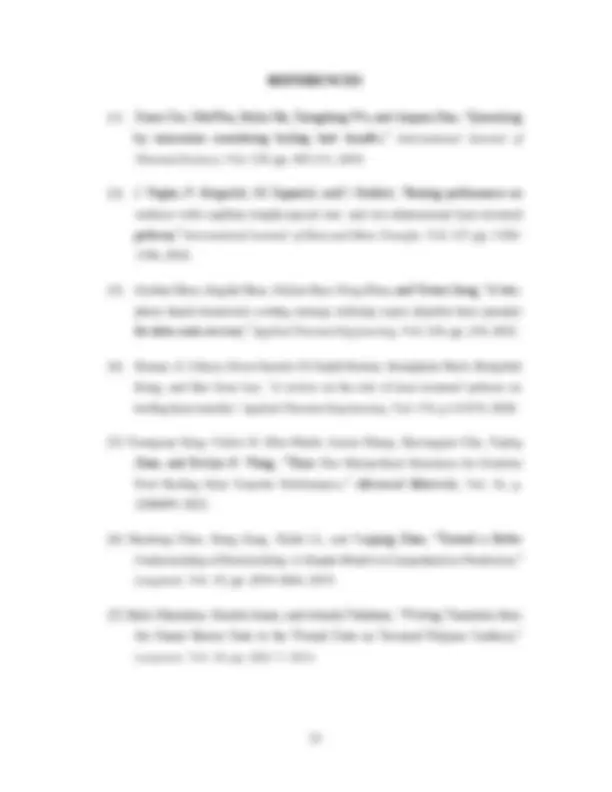
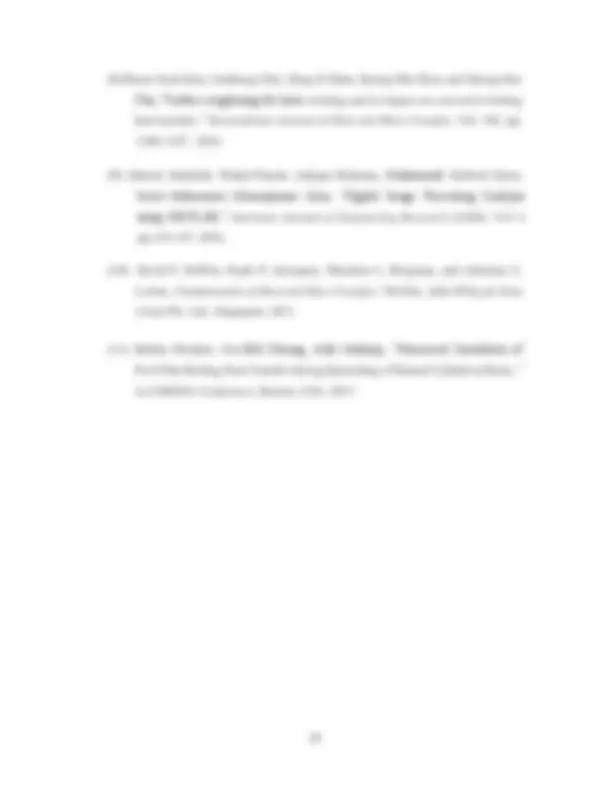
Study with the several resources on Docsity
Earn points by helping other students or get them with a premium plan
Prepare for your exams
Study with the several resources on Docsity
Earn points to download
Earn points by helping other students or get them with a premium plan
Community
Ask the community for help and clear up your study doubts
Discover the best universities in your country according to Docsity users
Free resources
Download our free guides on studying techniques, anxiety management strategies, and thesis advice from Docsity tutors
This research paper investigates the effectiveness of laser surface texturing in improving heat transfer during immersion cooling. The study focuses on the application of laser-textured surfaces in two-phase heat transfer, specifically examining the impact of different surface patterns on the cooling rate and heat transfer coefficient. The paper presents experimental results and simulations to demonstrate the advantages of laser texturing in enhancing heat transfer performance compared to conventional bare surfaces.
Typology: Study Guides, Projects, Research
1 / 43
This page cannot be seen from the preview
Don't miss anything!
Submitted in partial fulfillment of the requirements for the award of the degree of
Bachelor of Technology in Mechanical Engineering by
This is to certify that the report entitled “ EXPERIMENTAL INVESTIGATION ON EFFECT OF LASER-TEXTURED SURFACES IN IMMERSION COOLING ” is a bonafide record of the Project done by ABHINAND A S ( Roll No .: B190030ME), AUSTIN S THOMAS ( Roll No .: B190018ME) , SARATH M B ( Roll No .: B190043ME) and VISHNU MOHAN A B ( Roll No.: B190052ME ) under my supervision, in partial fulfillment of the requirements for the award of the degree of Bachelor of Technology in Mechanical Engineering from National Institute of Technology Calicut , and this work has not been submitted elsewhere for the award of a degree.
(Guide) Assistant Professor Dept. of Mechanical Engineering
Dept. of Mechanical Engineering
Place: NIT Calicut Date: 08-May- 2023
Laser surface texturing is a developing technique for enhancing the surface topography of engineering materials, thus enhancing surface wettability and heat transfer enhancement of the surface. Currently, surface texturing using lasers of various types, such as nanosecond, picosecond, and femtosecond lasers, are used for significant research. Laser texturing is a surface modification technique to study the deterministic behaviors of texturing patterns with different shapes and sizes. Due to its durability compared to surface coating techniques, laser surface texturing is a promising method for alleviating the transfer of heat during two-phase heat transfer. It can enhance lubrication and wear behavior, mechanical interlocking at the coating substrate interface, and create superhydrophobic surfaces. In this paper, an immersion cooling heat transfer study was conducted with bare specimens and specimens that underwent low-temperature oxidation under saturated and subcooled conditions Also, experiments with surfactant solution as quenchant under saturated and subcooled conditions were also performed. Finally, immersion cooling of laser-textured specimens is conducted. This enables a comparative study of the heat transfer rates of the bare and laser-textured surfaces.
Keywords: Laser-texturing, Stainless Steel 304 (SS304), Immersion Cooling, COMSOL
i
List of Abbreviations iii
List of Symbols iv
List of Figures v
1 Introduction 1
1.1 Introduction 1 1.2 Immersion Cooling 1 1.3 Laser Texturing 2
2 Review of Literature 4
3 Immersion Cooling of Bare Specimen 6
3.1 Methodology 6 3 .1.1 Fabrication of the Holder 7 3.1.2 Preparation of Sample 7 3.1.3 Experiment 7 3.2 The Experiment and Results 8 3.2.1 Experimental Setup 8 3.2.2 Immersion Cooling of Bare SS Substrate at Saturation 9 3.2.3 Immersion Cooling of Bare SS Substrate at Sub-cooled temperatures 10 3.2.4 Immersion Cooling of Mildly Oxidized SS Substrate at Saturation Temperature and Subcooled Temperatures 12 3.2.5 Immersion Cooling of Bare SS Substrate in (Critical Micelle Concentration) CMC of Sodium Dodecyl Sulphate (SDS) at Saturation Temperature and Subcooled Temperatures 14
iii
CMC Critical Micelle Concentration DI Deionized EDM Electrical Discharge Machining SDS Sodium Dodecyl Sulphate
SS Stainless Steel
𝜖 Emissivity
𝜌 Density (kg/𝑚^3 )
𝜎 Stefan–Boltzmann constant ( 5. 67 × 10 −^8 𝑊/𝑚^2 𝐾^4 )
∇ Del operator
k Thermal conductivity (W/mK)
q Heat flux (W/𝑚^2 )
t Time (s)
u Velocity vector (m/s)
Q Heat transfer rate (W)
T Temperature (K)
Subscripts and Superscripts
𝐶𝑃 Specific heat capacity at constant pressure
ℎ𝑟𝑎𝑑 Effective heat transfer coefficient
𝑇𝑠 Temperature of specimen
𝑇𝑠𝑎𝑡 Saturation temperature of quenchant
iv
4.4: Temperature vs. Time and cooling rate curves for laser textured specimen in horizontal orientation at saturation temperature and 75°C 23
4.5: Curves comparing the heat transfer performances of bare and laser-textured surfaces 24
4.6: Temperature variation of specimen obtained by simulating film boiling 26
4.7: Temperature variation of specimen obtained by simulating nucleate boiling 26
vi
Laser texturing is a process by which the surface properties of a material are altered by changing the surface texture and roughness. A beam of laser having sufficient power creates micropatterns on the material surface through laser ablation or by removing layers with micrometer precision and perfect repeatability. The most commonly experimented patterns are dimples, grooves, and free forms.
In the two-phase heat transfer, the formation of vapor film over the surface during film boiling restricts the rate of heat transfer since heat transfer coefficient is low compared to that of the quenchant. So, laser-textured surfaces provide provision to overcome the difficulty formed by the vapor film. These patterns can either accommodate the vapor layer within them such that the main surface for heat transfer is in contact with the liquid quenchant and not its vapor form or they can support the rupturing of the vapor film. The stability of the vapor film formed is what determines the heat transfer rate. If it is highly stable, the film boiling sustains for a longer time, and if it is not that stable, it ruptures easily and exposes the surface to the liquid quenchant.
1.2 IMMERSION COOLING
Immersion cooling is a process in which direct cooling of the metal, generally by quenching or immersing of the metal in a liquid (quechant), from the austenitizing temperature to, or at least near, the surrounding temperature. So, substrate, which is a metal, is heated to a particular temperature or due to the application in which it is used
performance of the boiling systems is alleviated by the modification of surface utilizing ultrafast processing lasers.
Alterations on different spatial scales (namely micro, nano-, and hierarchical micro-nano) are the main focus of the current research. The surface properties such as wettability, surface roughness, surface area, wickability, capillarity, and liquid spreading ability are altered upon texturing using laser, enhancing the transfer of heat. A laser beam is focussed to ensure a sufficient amount of heat at its point of focus, which melts and evaporates the metal thermally by the phenomenon of the phonon/electron interaction. The melting of metal and its vaporization are independent of the hardness of the material and can be controlled by changing the different laser parameters. Laser texturing controlled in such a way is an upcoming technique that is becoming popular among the research community.
Research papers on laser texturing were read to understand the types of patterns used in the surfaces and the various parameters considered. The aspect of how the surface properties are modified and how those alterations cause corresponding enhancement of the transfer of heat, especially during two-phase heat transfer. The transfer of heat at the interface between heated metal and quenchant in the transition boiling regime is more intensive than in the film boiling regime [1].
The two-phase heat transfer is encountered in applications where sudden cooling is required upon immersion of the hot body in a colder quenchant. The temperature of the substrate or the hot body is above the saturation temperature of the quenchant. In most cases, the quenching is done in atmospheric conditions; thus, the saturation temperature will be atmospheric. Since the temperature of the hot body is greater than the quenchant’s saturation temperature, the quenchant/liquid coming in direct contact upon immersion vaporizes instantaneously and forms a vapor film over the surface. The low heat transfer coefficient of the vapor film layer reduces the heat transfer rate required for fast cooling.
Various techniques, such as passive and active, were used to enhance the heat transfer rates. The active techniques require external power to input the process, including using magnetic fields, electric fields, and agitation to rupture the vapor film formed. However, they are complex procedures and are challenging to operate in extreme conditions [6]. The passive techniques do not require any additional energy during operation, including surface modifications, surface coating, and fluid additives. Surface coating and additional fluid additives sometimes encounter difficulty while implemented and often require regular replenishment of the coating or quenchant after
The methodology followed for experimentation with bare specimen (Fig 3.1) was: fabrication of holder, preparation of the specimen, conducting the immersion cooling heat transfer experiment, and finally, performing cooling curve analysis, heat transfer analysis, and visualization of film thickness.
Fig 3.1: Flowchart of Experimentation work with bare specimen
3.1.1 Fabrication of the Holder
The holder was fabricated with mild steel at the Central Workshop. The cylindrical tubes were machined outside and welded to the primary holder body, enabling the main holder body to be attached to the actuator arm. Holes of 3 mm diameter were drilled by Electrical Discharge Machining (EDM) wire drilling on the holder for the probes to pass through.
3.1.2 Preparation of the Sample
EDM wire drilling was done on bare specimens for holes of 1mm diameter to hold the thermocouple probes. In the sample for vertical orientation, three holes of different depths were drilled lengthwise. The specimens’ surfaces were polished using different grades of sandpaper-like 400,800,1200 and 2000 to obtain a mirror finish. Finally, surfaces are prepared by ultrasonication in acetone at the Thermal Science Lab for removing contaminants (Fig 3.2). The contact angle analysis of the bare specimen showed that it is hydrophilic.
3.1.3 Experiment
Various experiments were conducted with the bare specimens in such saturated and subcooled conditions. Subcooled conditions include temperatures of 50°C and 75°C. Such experiments will also be conducted with specimens with laser-textured surfaces.
Fig 3.2: Stainless Steel (SS) 304 specimen attached to thermocouple
3.2.2 Immersion Cooling of Bare SS Substrate at Saturation
The primary experimental condition is to perform an immersion cooling test of a heated SS304 sample of appropriate dimensions with a plain polished surface with a quenching medium of deionized (DI) water at the saturation temperature of 100°C. The sample gets heated to the required temperature of 400°C in a radiation furnace.
In the plot of Temperature vs. Time (Fig 3.4) and Time vs. Rate of cooling (Fig 3.5) obtained from the data collected, we observe that the temperature of all three data collection points in the sample recorded is different at the same time. the most profound point showing the maximum rate of cooling as compared. This is in line with the fact that the bottom of the sample gets into contact with the quenchant first, and the immediate contact of a cooling medium sets off a flux of heat out of the sample; this can be visualized from the peak of the curve of time vs. rate of cooling at the time of 3
Fig 3.4: Temperature vs. Time for bare sample in saturation condition
Fig 3.5: Cooling rate curve for bare sample in saturation condition
3.2.3 Immersion Cooling of Bare SS Substrate at Subcooled Temperatures of 75°C and 50°C
In parallel with practical applications of immersion cooling where saturated boiling water may not be used as a cooling medium, but a rather sub cooled down quenchant is used. So with the quenchant at a subcooled temperature below 100°C, the sample in its vertical orientation is allowed to heat to a similar temperature of 400°C in the radiation furnace. The sample is then set to immerse in the preheated quenchant in a beaker using the actuator arm setup. The experiment was done twice at two different temperatures, 50°C and 75°C. The resulting temperature data acquired are as seen in the figures below (Fig. 3.6 and Fig. 3.7).