
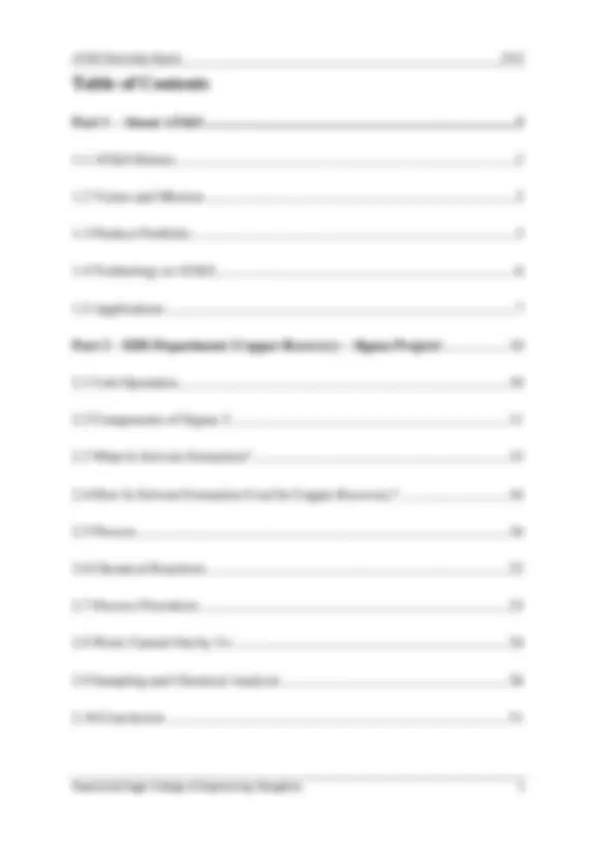
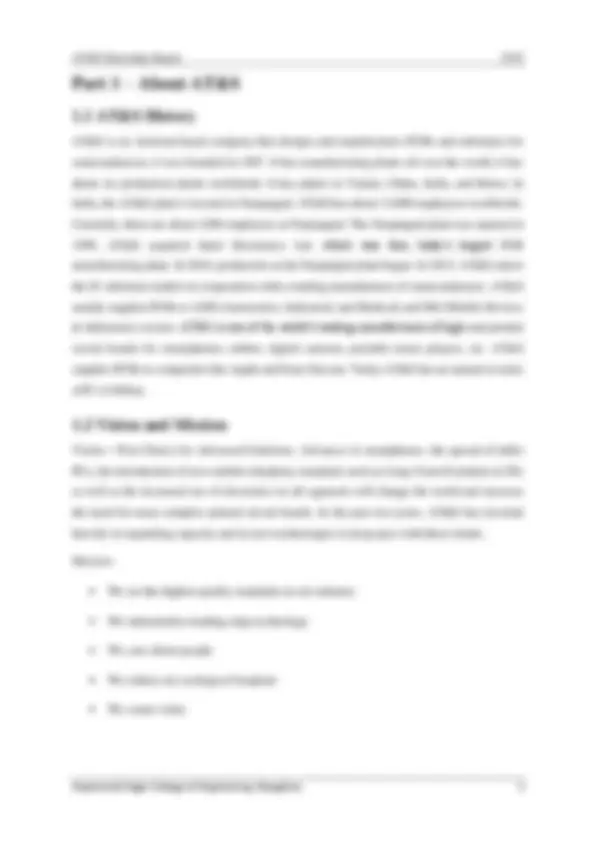
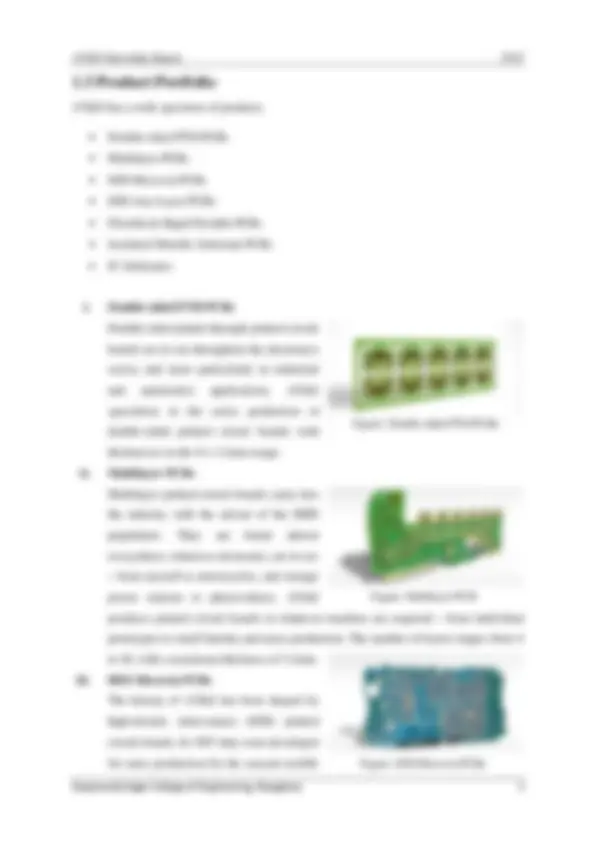
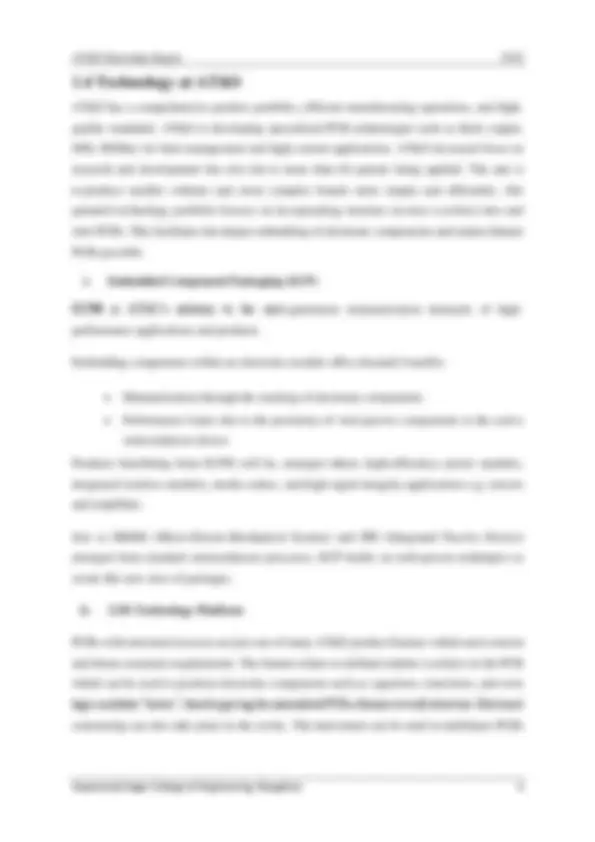
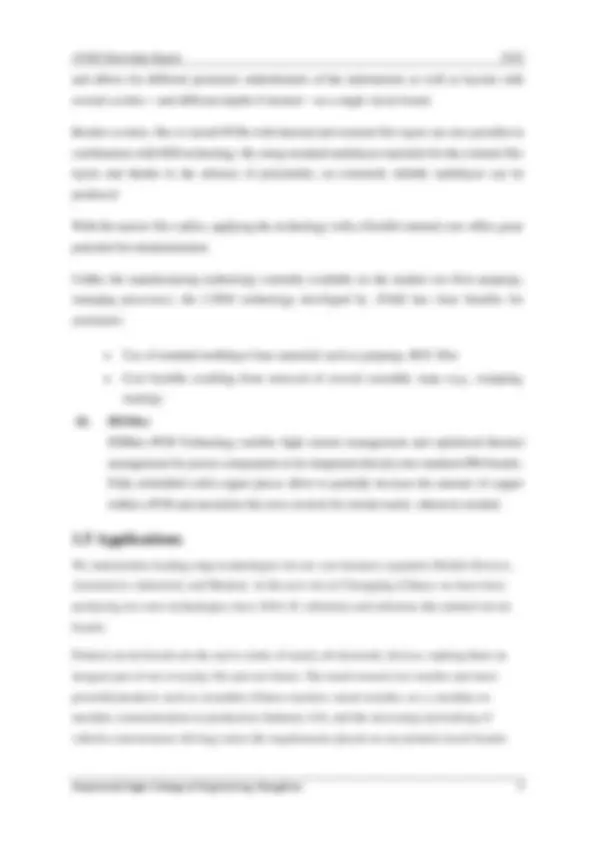
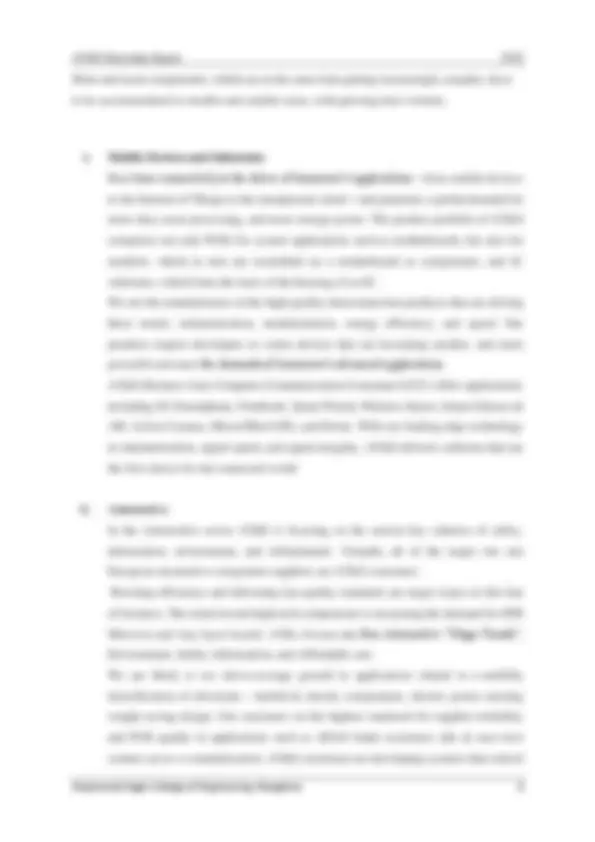
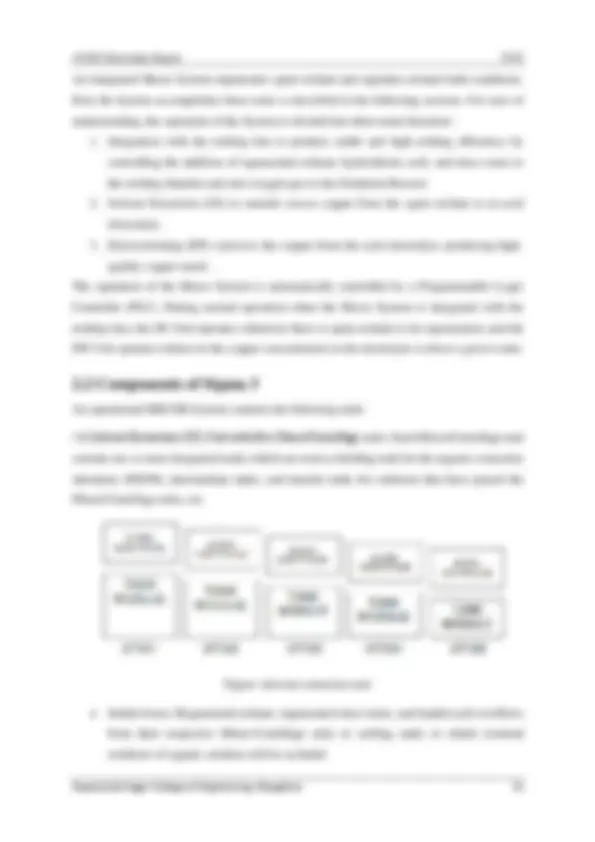
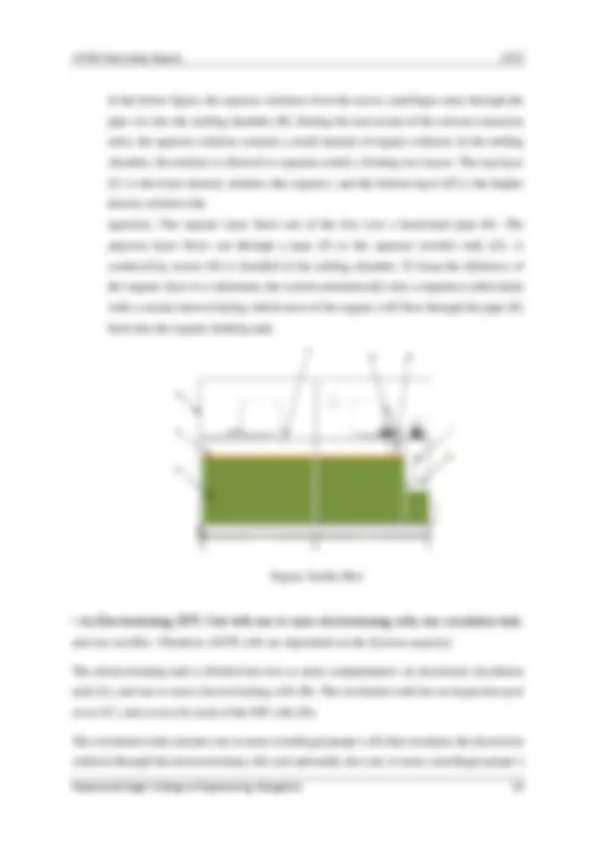
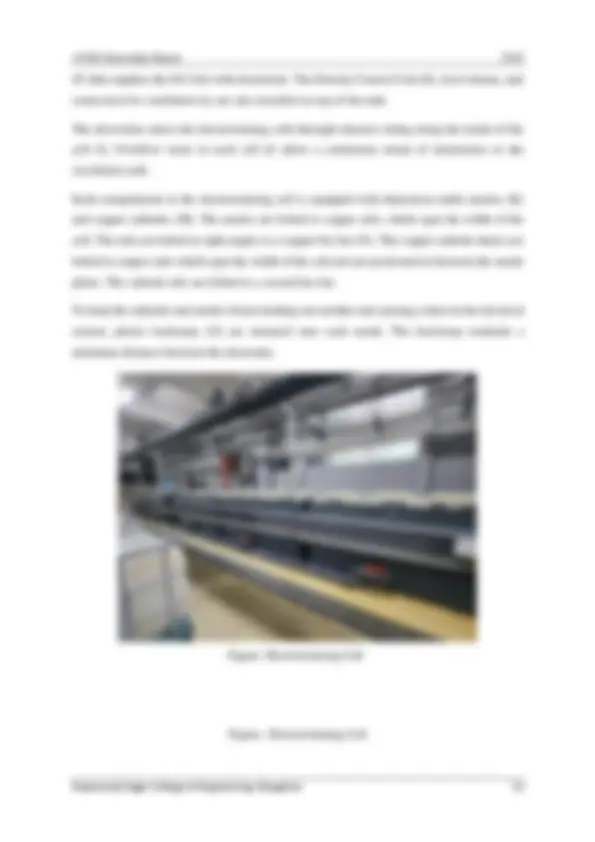
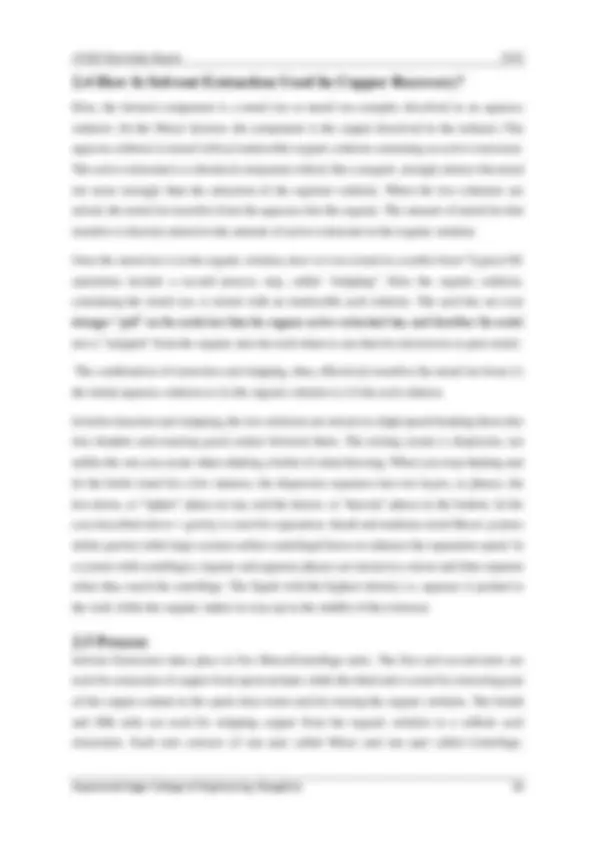
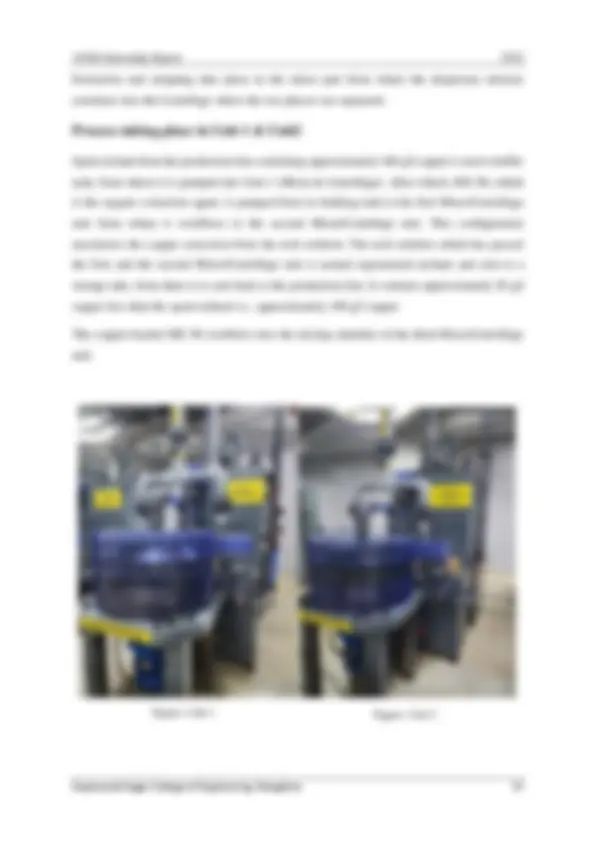
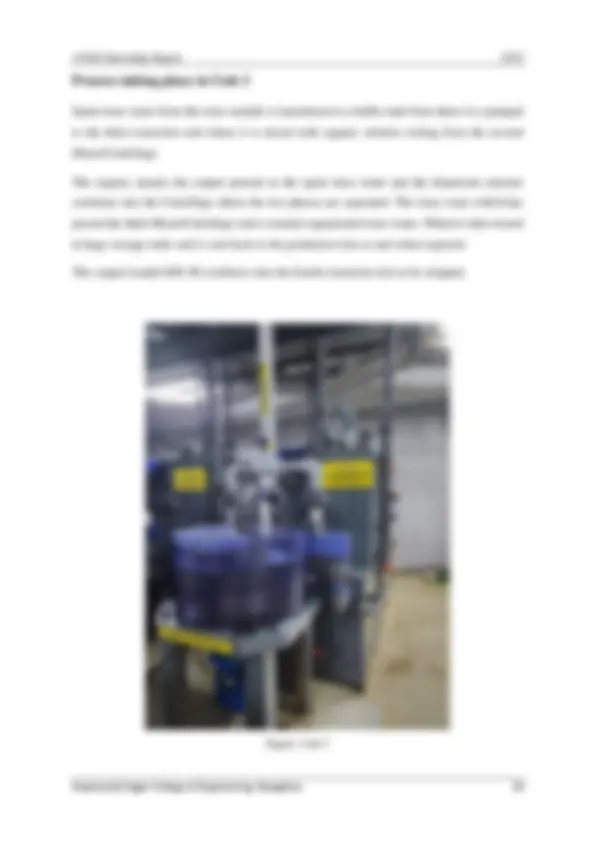
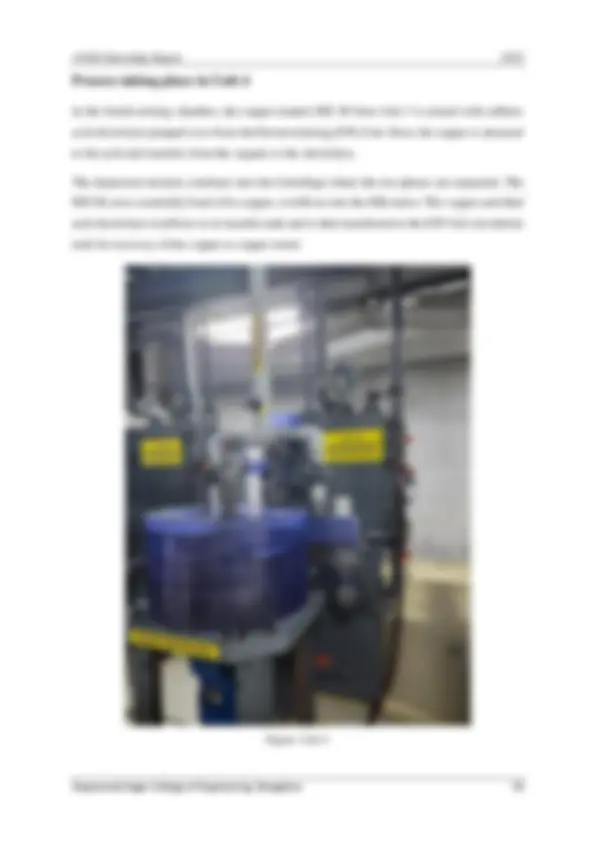
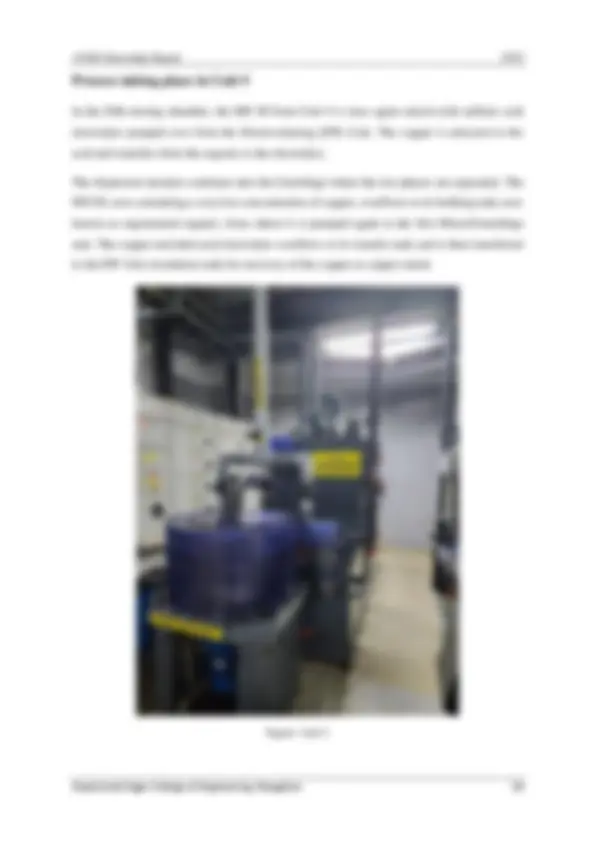
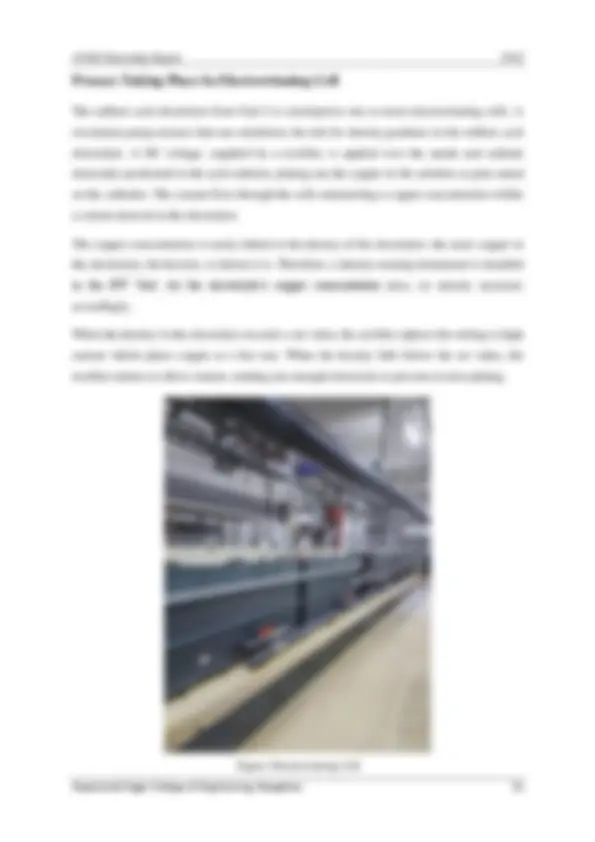
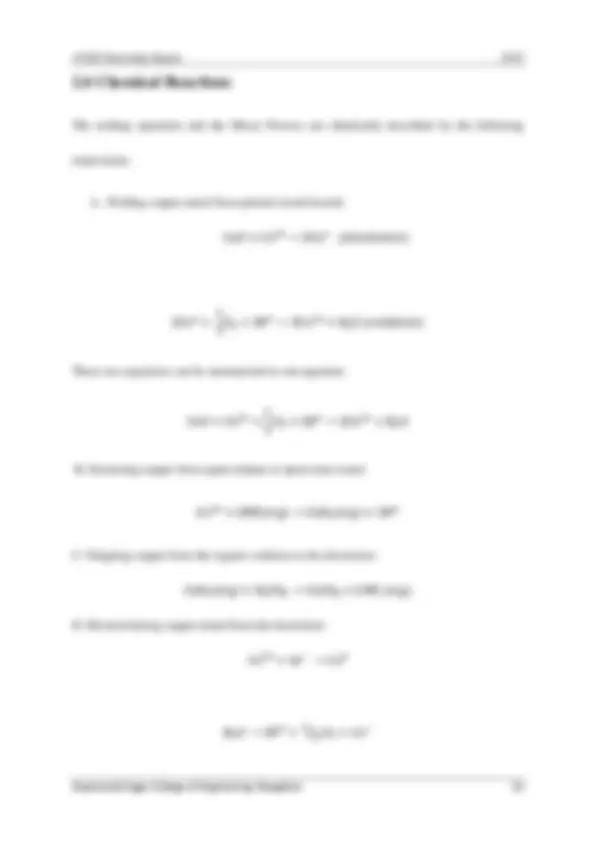
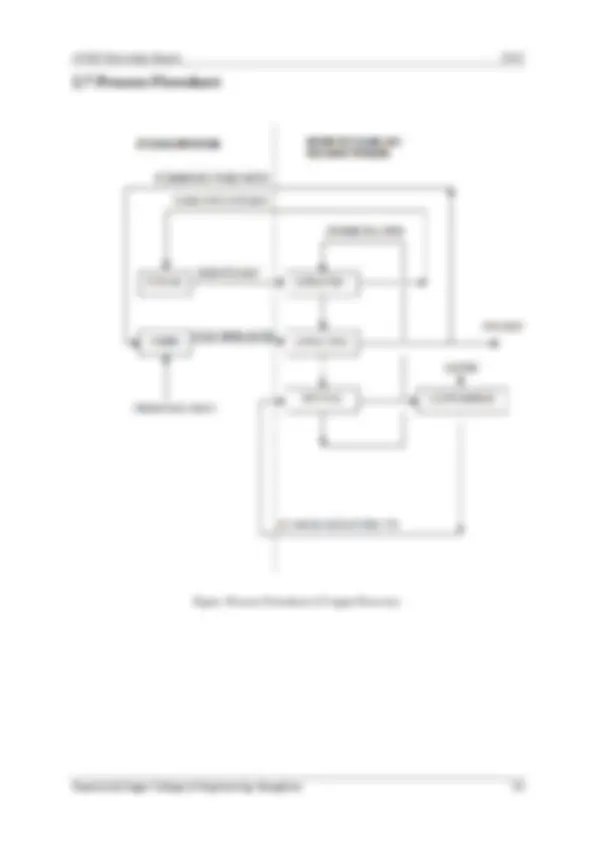
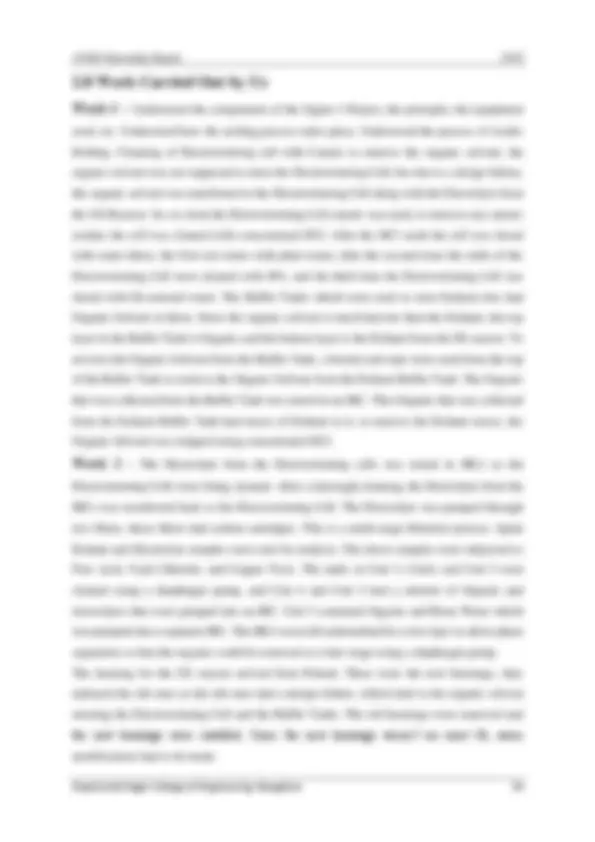
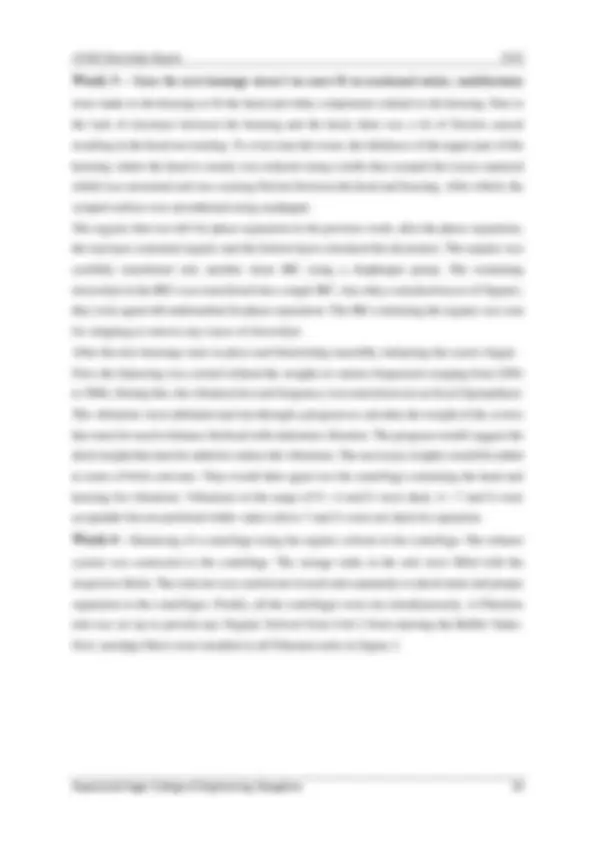
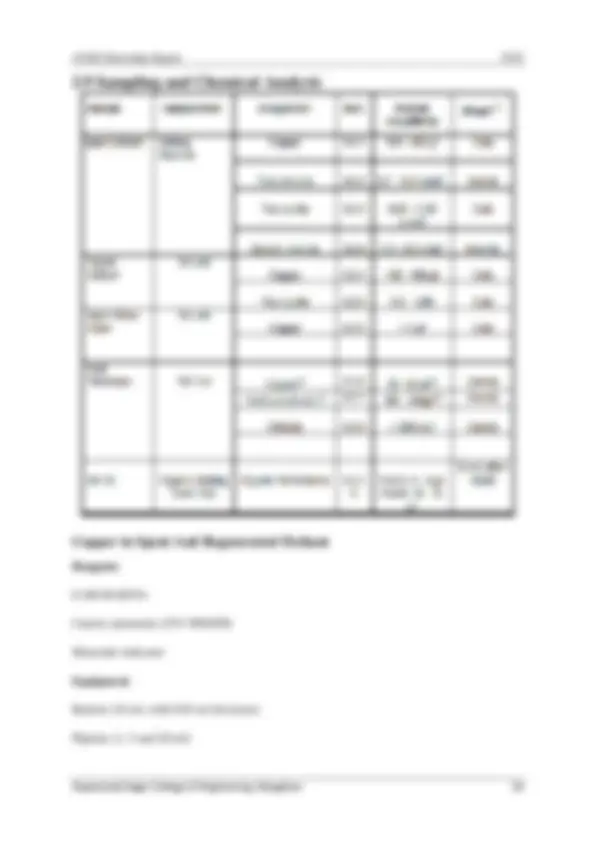
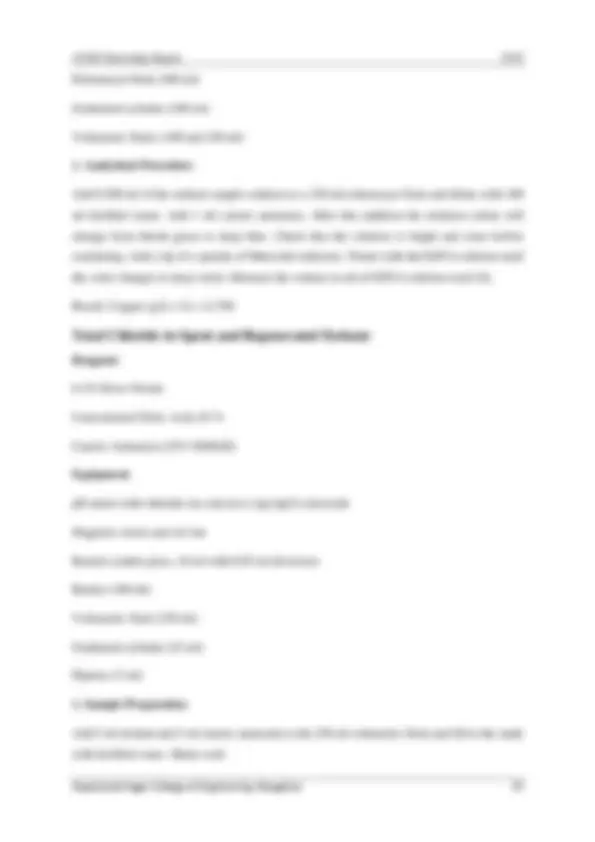
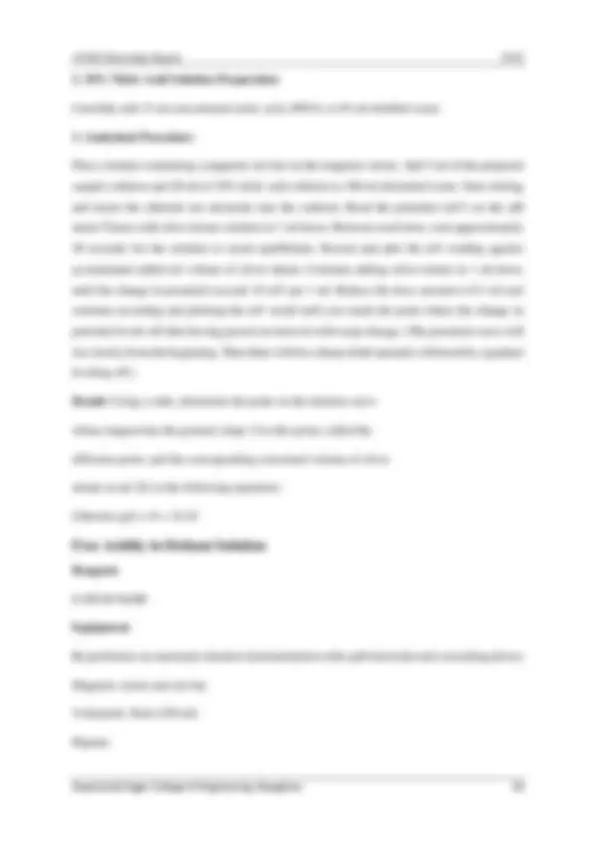
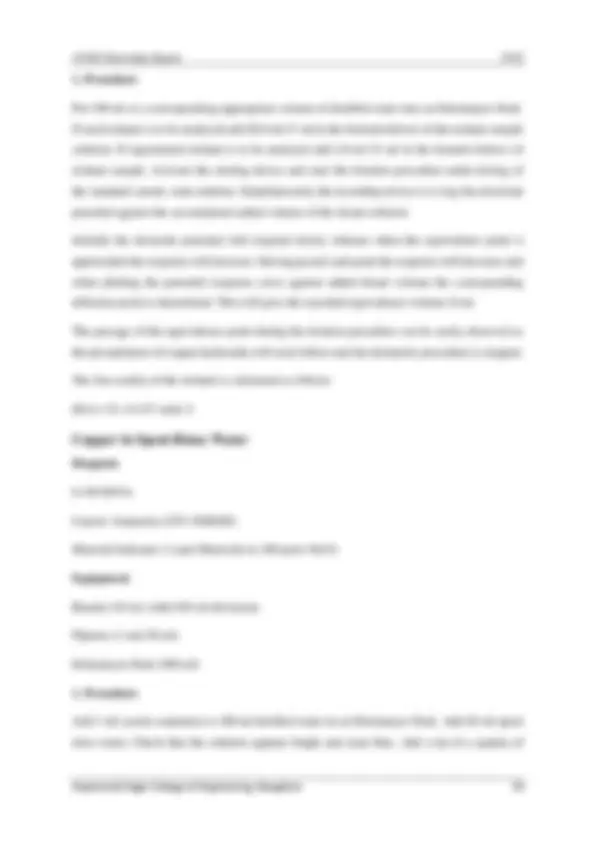
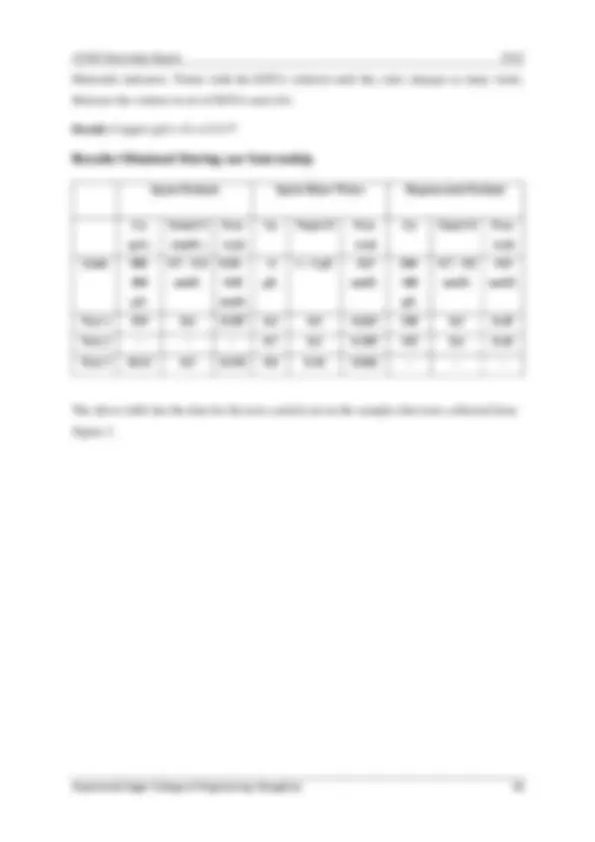
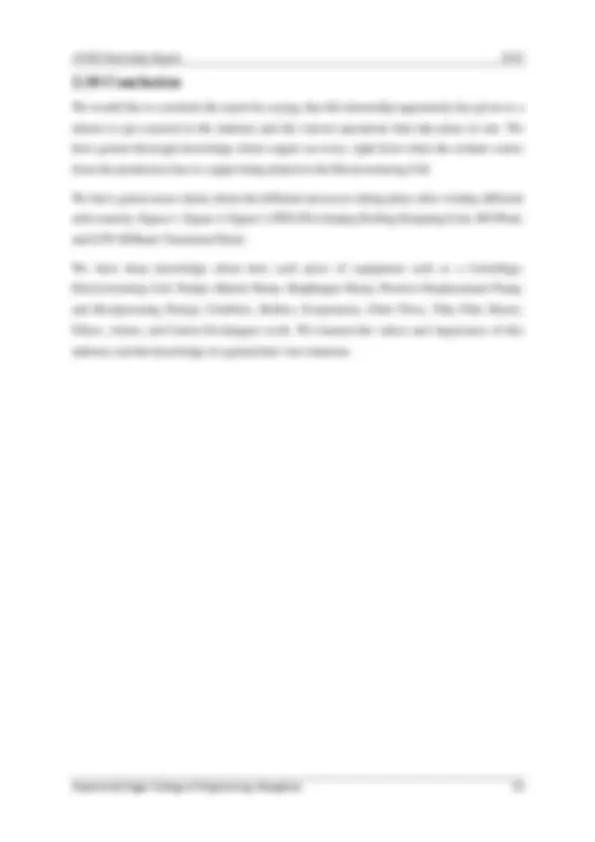
Study with the several resources on Docsity
Earn points by helping other students or get them with a premium plan
Prepare for your exams
Study with the several resources on Docsity
Earn points to download
Earn points by helping other students or get them with a premium plan
Community
Ask the community for help and clear up your study doubts
Discover the best universities in your country according to Docsity users
Free resources
Download our free guides on studying techniques, anxiety management strategies, and thesis advice from Docsity tutors
HI, THIS IS THE INTERNSHIP REOPRT ON THE BASED ON THE ABOVE UPLOADED
Typology: Schemes and Mind Maps
1 / 33
This page cannot be seen from the preview
Don't miss anything!
Department of Chemical Engineering , Shavige Malleshwara Hills, 91st^ Main Road, 1st^ Stage, Kumaraswamy Layout, Bangalore, Karnataka - 560111
Submitted By: Eldho Manoj (1DS19CH007) Karthikeyan. T (1DS19CH014)
ACKNOWLEDGEMENT The Internship opportunity we had at AT&S Ltd. was a great chance for learning and professional development. Therefore, we consider ourselves very lucky individuals as we were provided with an opportunity to be a part of it. We are also grateful for having a chance to meet so many wonderful people and professionals who led us through this internship period. We would like to take this opportunity to express our deepest gratitude to Dr. B R Veena for referring us for this Internship Program and Mr. Santosh Gundapi, MD, who heartily welcomed us into AT&S for the internship. We would like to thank the Head of the EHS department Mr. A Ravi for his constant guidance and support throughout our internship. We would also like to convey our heartiest thanks to Dr. Suru Vivian John-Denk, Mr. Jagadeesh, Mr. Mohammed Musaddiq, and Ms. Rithika Cheruka despite being extraordinarily busy with their duties, took time out to guide and educate us throughout the program and also for arranging all facilities to make the training experience easier. We choose this moment to acknowledge their contribution gratefully. We would also like to thank Mr.Raghavendra from the HR Department for guiding us through the Internship. Finally, we would like to thank all the department heads and the staff at the unit, for their careful and precious guidance which was extremely valuable for our study both theoretically and practically.
Part 1 – About AT&S 1.1 AT&S History AT&S is an Austrian-based company that designs and manufactures PCBs and substrates for semiconductors, it was founded in 1987. It has manufacturing plants all over the world, it has about six production plants worldwide. It has plants in Vienna, China, India, and Korea. In India, the AT&S plant is located in Nanjangud. AT&S has about 1 3 ,000 employees worldwide. Currently, there are about 1200 employees at Nanjangud. The Nanjangud plant was opened in 1999, AT&S acquired Indal Electronics Ltd. which was then India’s largest PCB manufacturing plant. In 2010, production at the Nanjangud plant began. In 2013, AT&S enters the IC substrate market in cooperation with a leading manufacturer of semiconductors. AT&S mainly supplies PCBs to AIM (Automotive, Industrial, and Medical) and MS (Mobile Devices & Substrates) sectors. AT&S is one of the world’s leading manufacturers of high-end printed circuit boards for smartphones, tablets, digital cameras, portable music players, etc. AT&S supplies PCBs to companies like Apple and Sony Ericson. Today AT&S has an annual revenue of € 1.6 billion. 1.2 Vision and Mission Vision – First Choice for Advanced Solutions. Advances in smartphones, the spread of tablet PCs, the introduction of new mobile telephony standards such as Long-Term Evolution (LTE) as well as the increased use of electronics in all segments will change the world and increase the need for more complex printed circuit boards. In the past two years, AT&S has invested heavily in expanding capacity and in new technologies to keep pace with these trends. Mission -
1.3 Product Portfolio AT&S has a wide spectrum of products,
vi. Insulated Metallic Substrate PCBs In the single-side printed circuit board business, AT&S focuses on IMS boards. These are used primarily as heat sinks for LEDs and power components. To enable heat dissipation, the base material used has one side that is an aluminum or copper layer either 1.0mm or 1.6mm thick. vii. IC Substrates Flip Chip technology is the foundation for packaging high-performance Integrated Circuits used in applications from consumer-level smartphones, tablets, and PCs to high-performance graphics workstations, servers, and IT infrastructure equipment. AT&S provides IC substrates for Flip Chip packaging in a variety of single and multi- chip, BGA, and LGA form factors for high I/O, high-performance applications, with micro bumps for C4 or TCB die to attach. Substrates may have surface-mounted passive devices on one or both sides and delivered as array strips or singulated fabs in JEDEC trays. Our advanced build-up process, highly automated, contact-free, and contained in cleanrooms, starts with the formation of a reinforced core board with filled core or copper-filled buried vias that provide a platform to build up multiple layers of unreinforced dielectric film alternating with copper circuits formed by a Semi Additive Process (SAP). This versatile system provides the best balance of performance, reliability, and value for the high-density interconnect products leading the industry. Figure: IC Substrate Figure: Insulated Metallic Substrate PCB
1.4 Technology at AT&S AT&S has a comprehensive product portfolio, efficient manufacturing operations, and high- quality standards. AT&S is developing specialized PCB technologies such as thick copper, IMS, HSMtec for heat management and high-current applications. AT&S increased focus on research and development has also led to more than 64 patents being applied. The aim is to produce smaller volumes and more complex boards more simply and efficiently. Our patented technology portfolio focuses on incorporating structure recesses (cavities) into and onto PCBs. This facilitates the deeper embedding of electronic components and makes thinner PCBs possible. i. Embedded Component Packaging (ECP) ECP® is AT&S’s solution to the next-generation miniaturization demands of high- performance applications and products. Embedding components within an electronic module offers dramatic benefits:
More and more components, which are at the same time getting increasingly complex, have to be accommodated in smaller and smaller areas, with growing data volumes. i. Mobile Devices and Substrates Real-time connectivity is the driver of tomorrow’s applications – from mobile devices to the Internet of Things to the omnipresent cloud – and generates a global demand for more data, more processing, and more storage power. The product portfolio of AT&S comprises not only PCBs for system applications such as motherboards, but also for modules, which in turn are assembled on a motherboard as components, and IC substrates, which form the basis of the housing of an IC. We are the manufacturers of the high-quality interconnection products that are driving these trends: miniaturization, modularization, energy efficiency, and speed. Our products inspire developers to create devices that are becoming smaller, and more powerful and meet the demands of tomorrow’s advanced applications. AT&S Business Line Computer-Communication-Consumer (CCC) offers applications including 5G Smartphone, Notebook, Smart Watch, Wireless Stereo, Smart Glasses & AR, Action Camera, Micro/Mini LED, and Drone. With our leading-edge technology in miniaturization, signal speed, and signal integrity, AT&S delivers solutions that are the first choice for the connected world. ii. Automotive In the Automotive sector AT&S is focusing on the current key schemes of safety, information, environment, and infotainment. Virtually all of the major tier one European automotive component suppliers are AT&S customers. Boosting efficiency and delivering top-quality standards are major issues in this line of business. The trend toward high-tech components is increasing the demand for HDI Microvia and Any layer boards. AT&s focuses on four Automotive “Mega-Trends”, Environment, Safety, Information, and Affordable cars. We are likely to see above-average growth in applications related to e-mobility electrification of drivetrain – hybrid & electric components, electric power steering weight-saving design. Our customers set the highest standards for supplier reliability and PCB quality in applications such as ADAS brake assistance side & rear-view camera car-to-x communication. AT&S customers are developing systems that control
the information flow to the driver, such as head-up tachygraphs cockpit modules navigation multimedia. The auto electronics market is expected to grow faster than the automotive market as a whole. There is a need for small & compact seized vehicles for cost-efficient solutions. iii. Industrial The Industrial business is characterized by a multitude of customers with widely diversified technological requirements. The products supplied range from multilayer PCBs with up to 22 layers through to single- and double-sided, flexible and semi- flexible as well as rigid-flex boards. The industrial segments include electronics, measurement and control technology, medicine, computing, and white and brown goods. Applications in the Lighting industry are the illumination of buildings, rooms, professional working lights, and signals. Their PCBs are used in architecture, Safety Systems Lighting/Electronic signals. Applications in the Power Segment comprise equipment to generate, convert, transmit, and distribute power. Our PCBs are used in Power Generation, Power Inverters, Smart Grids/Homes, and Smart Meters. Our PCBs are used in Sensoric, Process and Manufacturing Control, and Human Machine Interface. The Transportation Segment includes commercial and passenger transport, Signalling, Rolling Stocks, etc. Our PCBs are used in braking Systems, Intrain communication, Tracking, Control Devices, etc. Our PCBs are used in Infrastructure, Building, Commercial/Consumer Appliances, HVACm Payment Terminals. iv. Medical - AT&S is one of the few European PCB manufacturers to have obtained certification under the EN ISO 13485 Medical Devices Standard. AT&S consequently enlarges its portfolio to all fields of medical technology. Applications are Diagnostic Instruments that provide high-resolution pictures of structures inside the body. Our PCBs are used in MRI, X-ray, Ultrasound Diagnostic & Imaging. The equipment is used in the treatment of specific medical conditions. Our PCBs are used in Defibrillator, Pacemaker, and Hearing Aids. Instruments are used to measure and monitor a patient’s vital signs and other functions. Their PCBs are used in blood glucose and ECG. All other electronics are used for specific medical applications. Their PCBs are used in surgical tools, test & analytical IT, Biochips, RFID.
An integrated Mecer System regenerates spent etchant and regulates etchant bath conditions. How the System accomplishes these tasks is described in the following sections. For ease of understanding, the operation of the System is divided into three main functions:
In the below figure, the aqueous solutions from the mixer centrifuges enter through the pipe (A) into the settling chamber (B). During the start mode of the solvent extraction units, the aqueous solution contains a small amount of organic solution. In the settling chamber, the mixture is allowed to separate (settle), forming two layers. The top layer (C) is the lower density solution (the organic), and the bottom layer (D) is the higher density solution (the aqueous). The organic layer flows out of the box over a horizontal pipe (E). The aqueous layer flows out through a pipe (F) to the aqueous transfer tank (G). A conductivity sensor (H) is installed in the settling chamber. To keep the thickness of the organic layer to a minimum, the system automatically runs a sequence called drain with a certain interval during which most of the organic will flow through the pipe (E) back into the organic holding tank.
Liquid transfer from the buffer tank is accomplished by one or more pumps connected to one or more outlets at the bottom of the tank (A). The tanks are equipped with centrifugal pumps and flow control devices. If the liquid level in the buffer tank has the potential to exceed the liquid level in the tank to which the liquid is pumped, an anti-siphon pipe is installed from the outlet side of the pump to the top of the buffer tank (B). The top of each tank supports one or more liquid inlet/-s (C), a ventilation port (D), and a level sensor connection (E) Figure: Top and Side view of Buffer Tank 2.3 What Is Solvent Extraction? Solvent extraction (SX) is a process, which can be used when you wish to selectively transfer (or "extract") a component from one solution to another. For solvent extraction to work, the solution containing the component and the solution into which the component is to be extracted must be immiscible, i.e., the two solutions won't mix and stay mixed, but will separate into layers.
Extraction and stripping take place in the mixer part from where the dispersion mixture continues into the Centrifuge where the two phases are separated. Process taking place in Unit 1 & Unit Spent etchant from the production line containing approximately 180 g/l copper is sent to buffer tank, from where it is pumped into Unit 1 (Mixer & Centrifuge). After which, MX 90, which is the organic extraction agent, is pumped from its holding tank to the first Mixer/Centrifuge unit from where it overflows to the second Mixer/Centrifuge unit. This configuration maximizes the copper extraction from the etch solution. The etch solution which has passed the first and the second Mixer/Centrifuge unit is named regenerated etchant and sent to a storage take, from there it is sent back to the production line. It contains approximately 20 g/l copper less than the spent etchant i.e., approximately 160 g/l copper. The copper-loaded MX 90 overflows into the mixing chamber of the third Mixer/Centrifuge unit. Figure: Unit 1 (^) Figure: Unit 2
Process taking place in Unit 3 Spent rinse water from the rinse module is transferred to a buffer tank from there it is pumped to the third extraction unit where it is mixed with organic solution exiting from the second Mixer/Centrifuge. The organic attacks the copper present in the spent rinse water and the dispersion mixture continues into the Centrifuge where the two phases are separated. The rinse water which has passed the third Mixer/Centrifuge unit is named regenerated rinse water. Which is then stored in huge storage tanks and is sent back to the production line as and when required. The copper-loaded MX 90 overflows into the fourth extraction unit to be stripped. Figure: Unit 3