
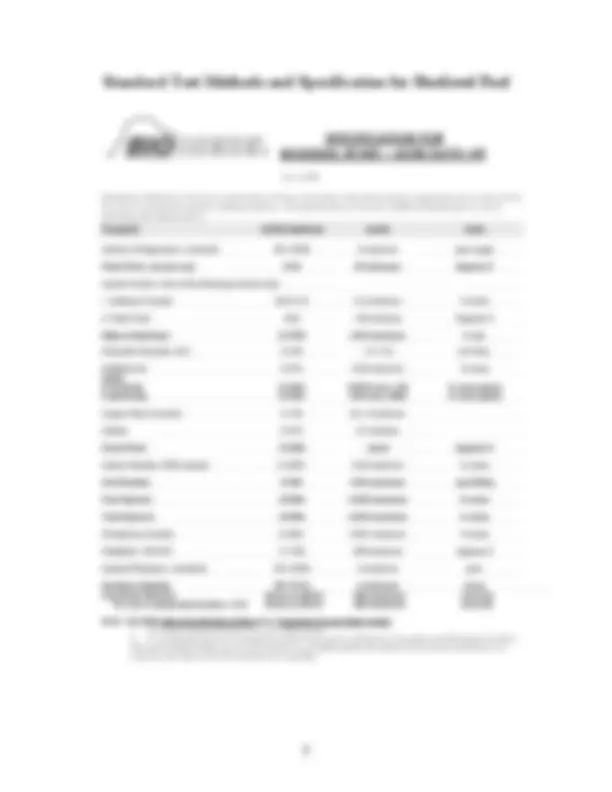
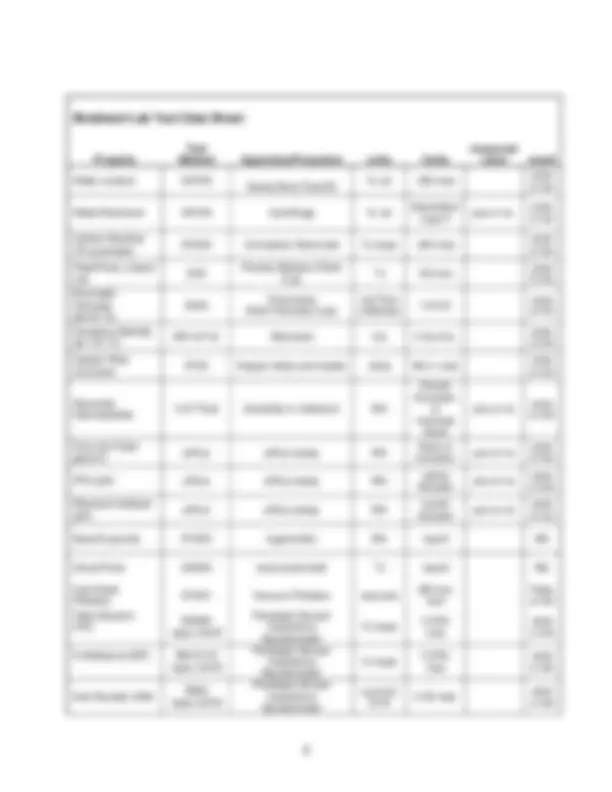
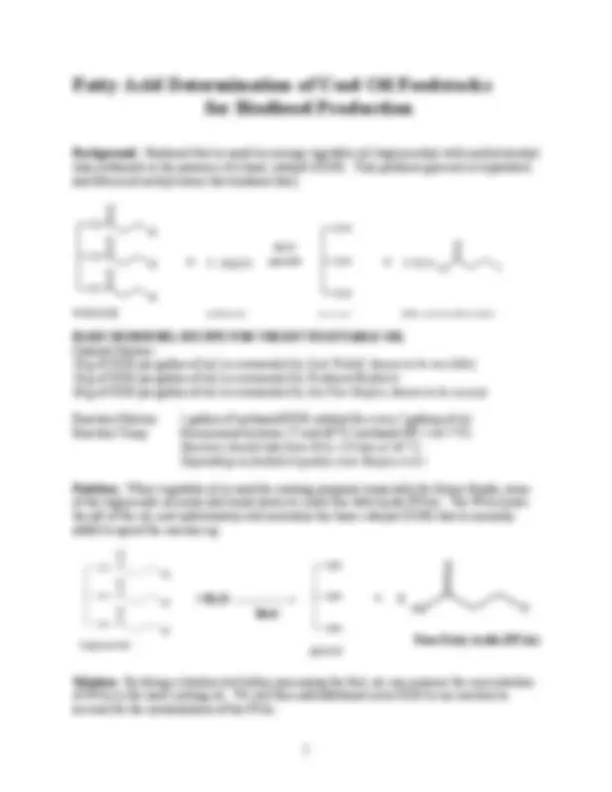
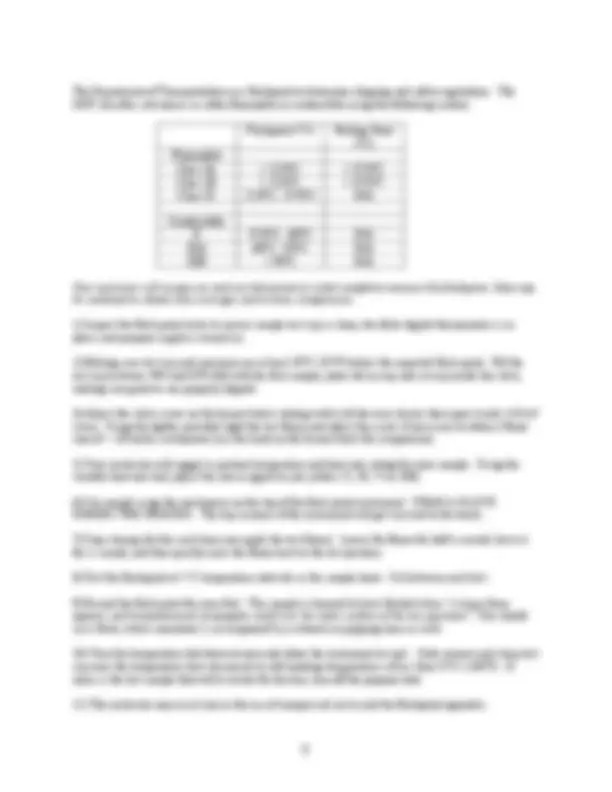
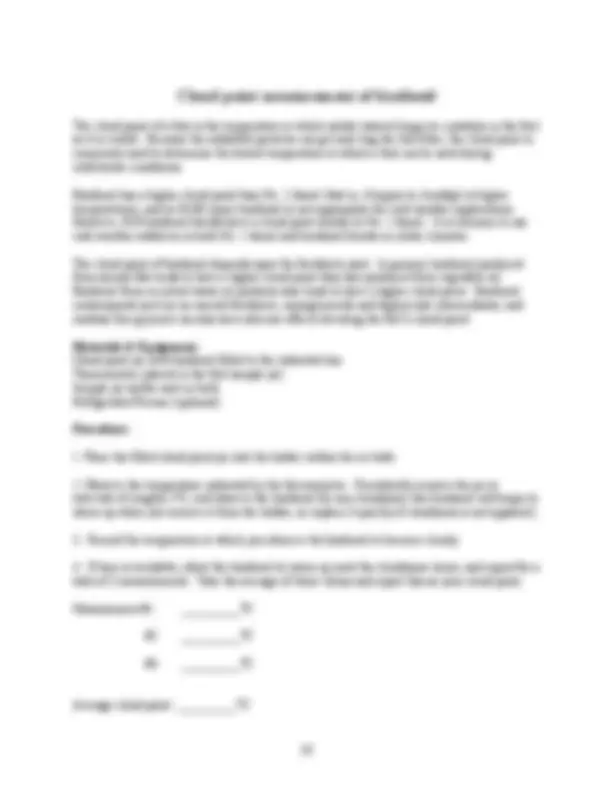
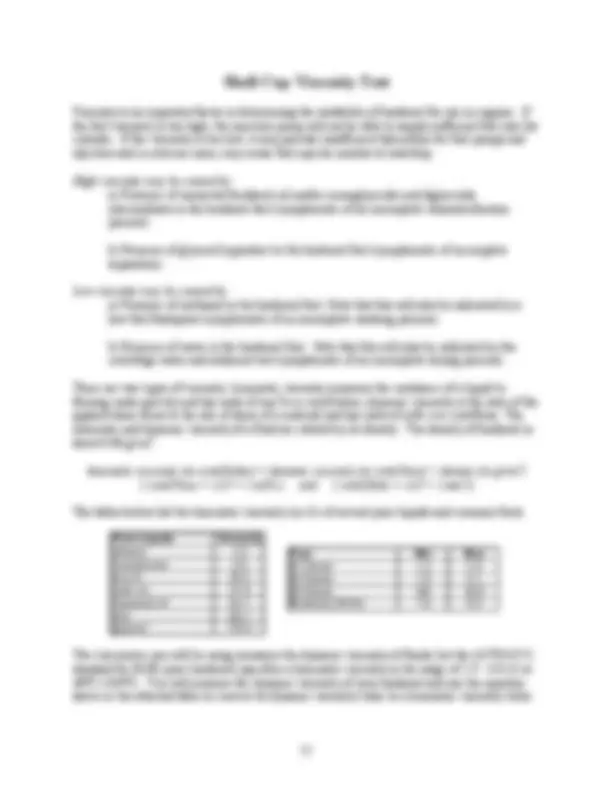
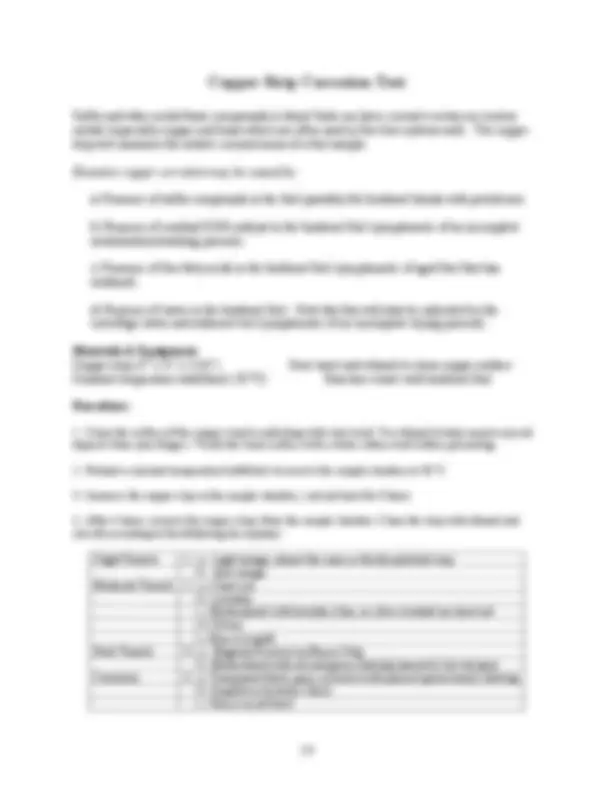
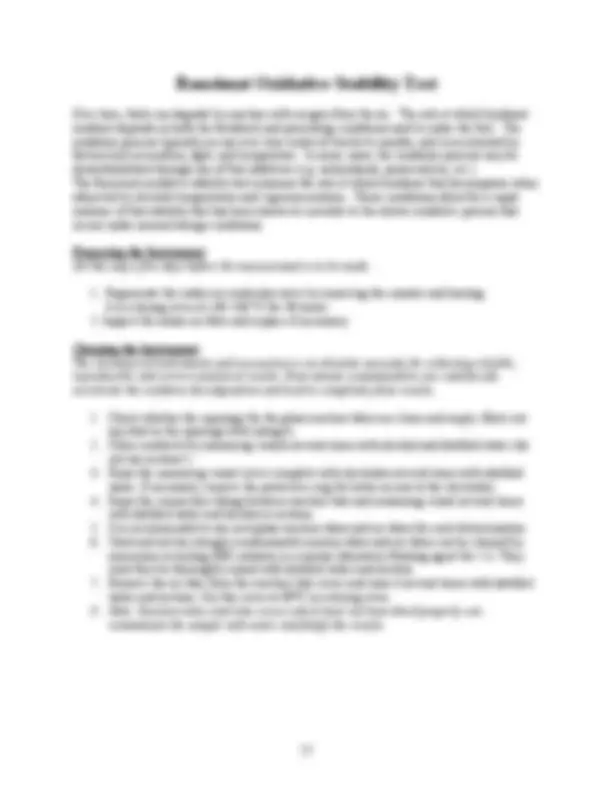
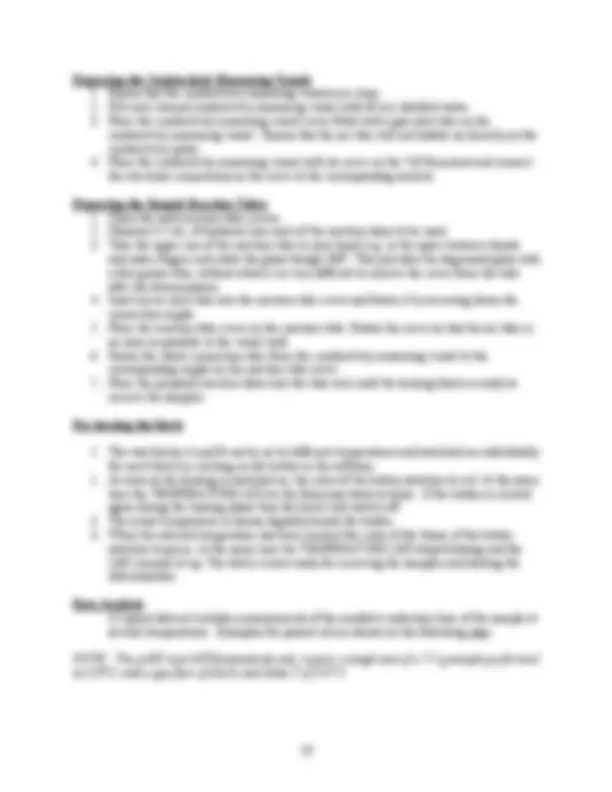
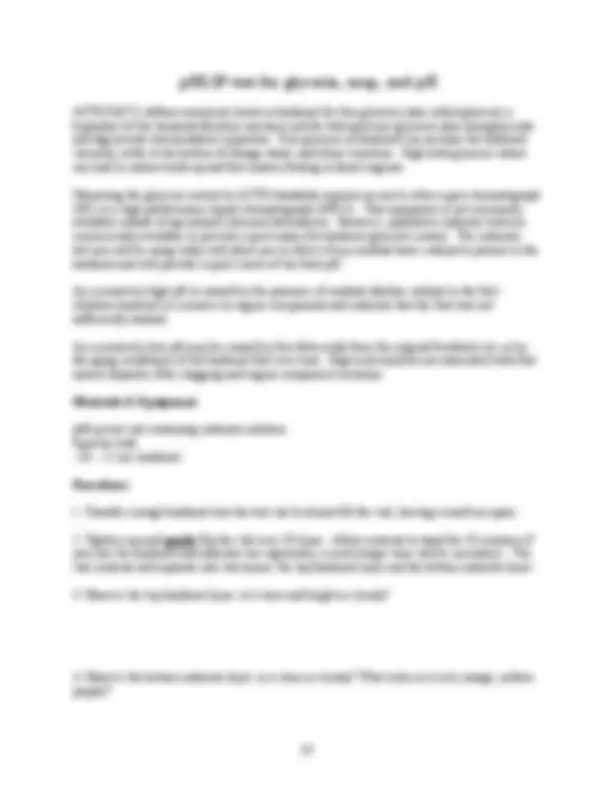
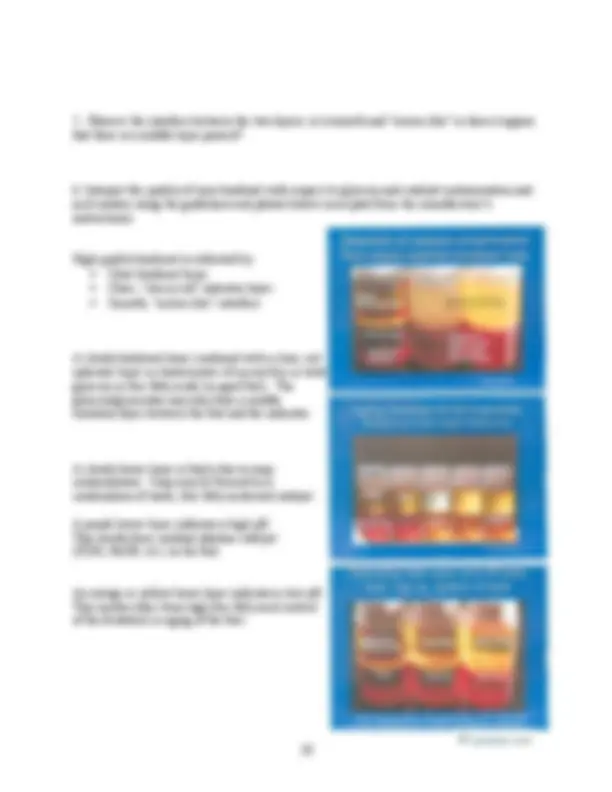
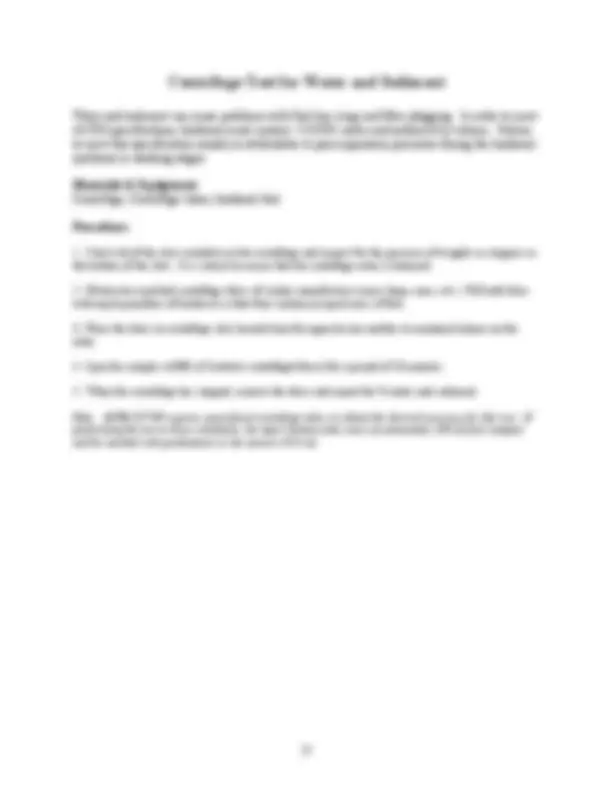
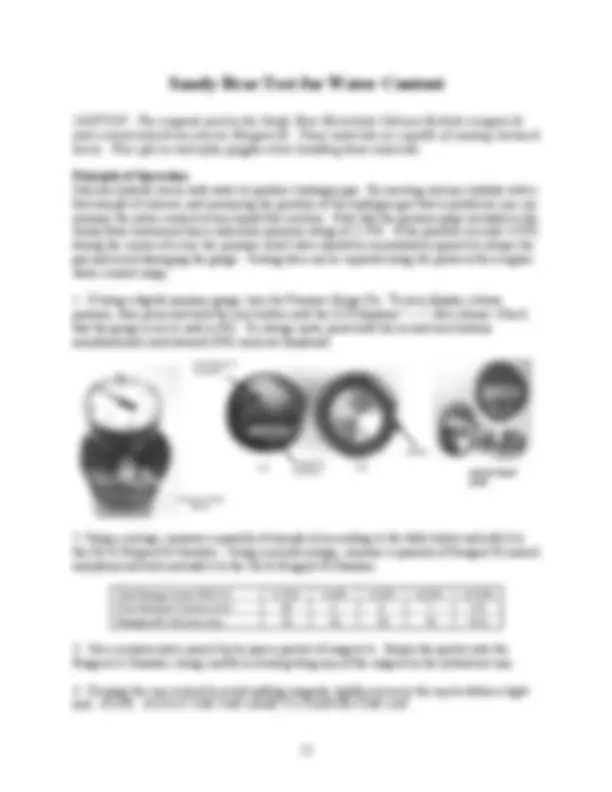
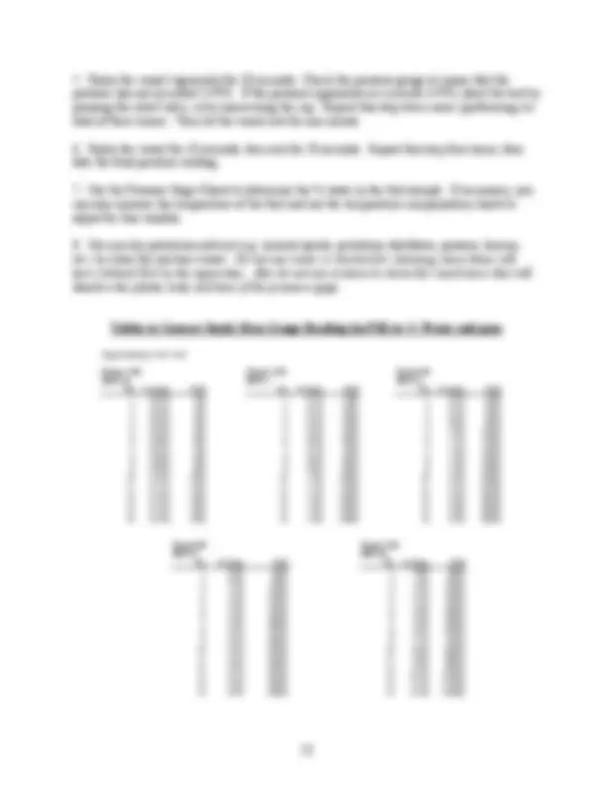
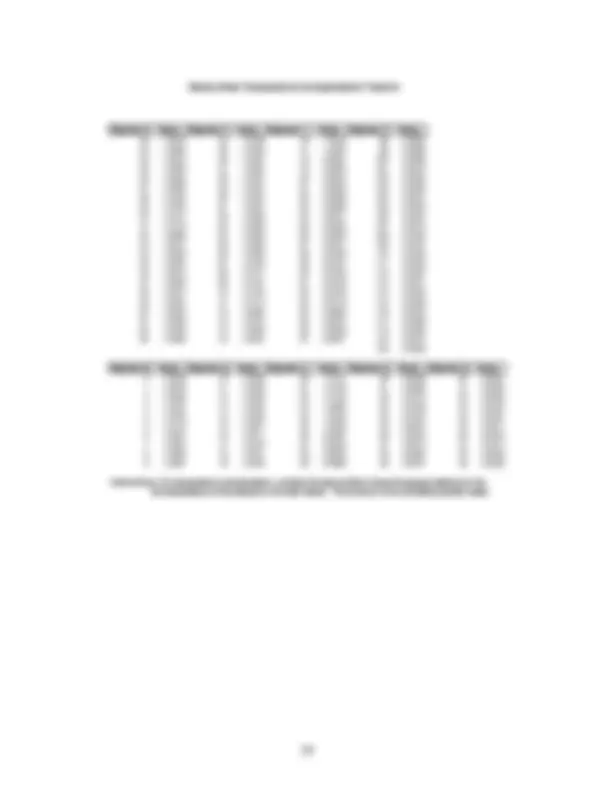
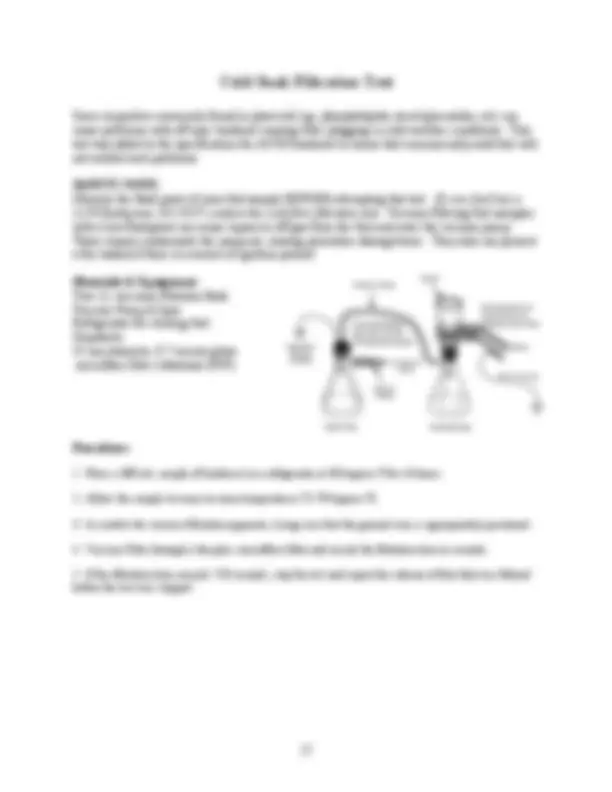
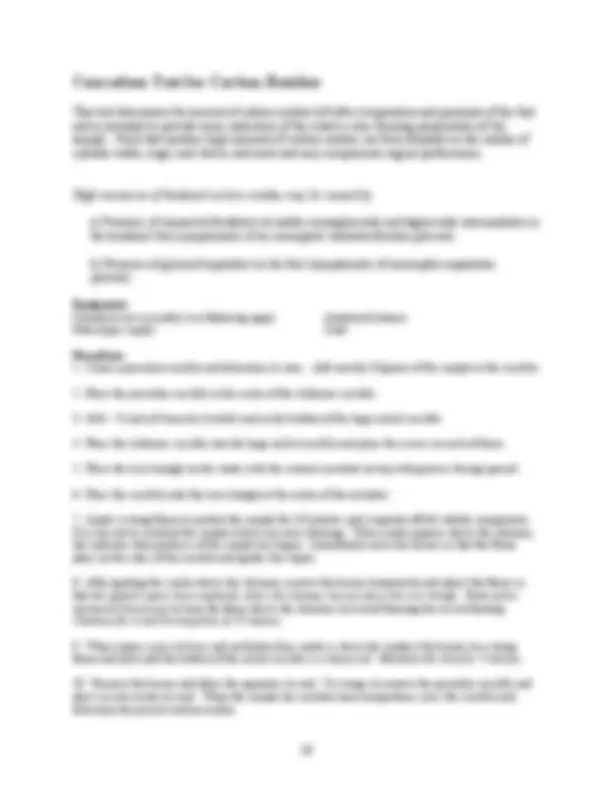
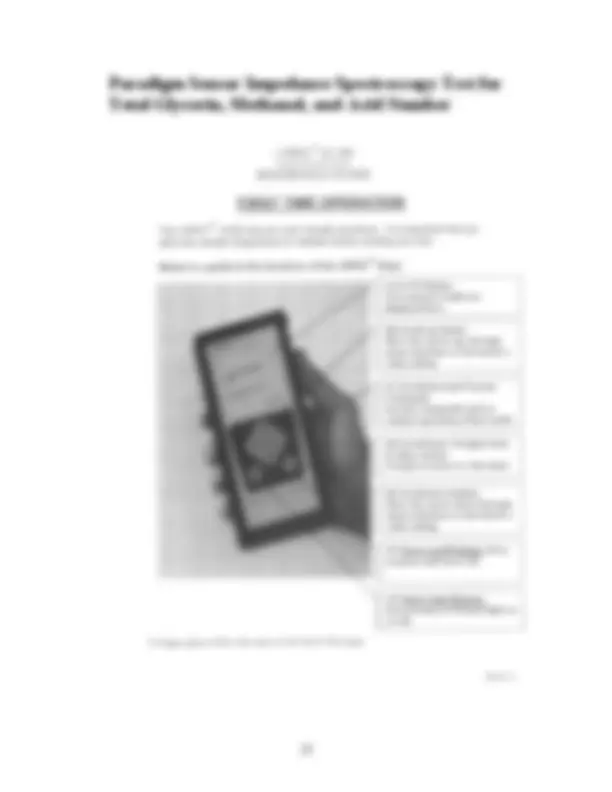
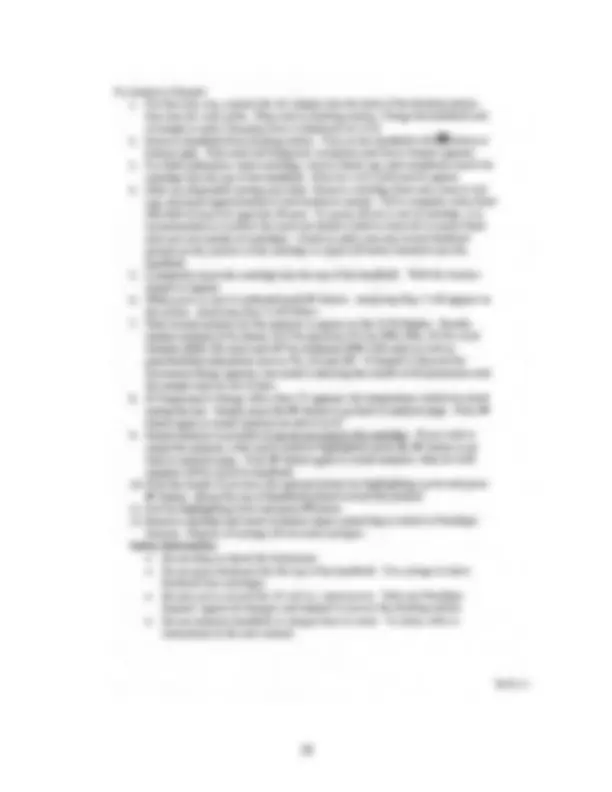
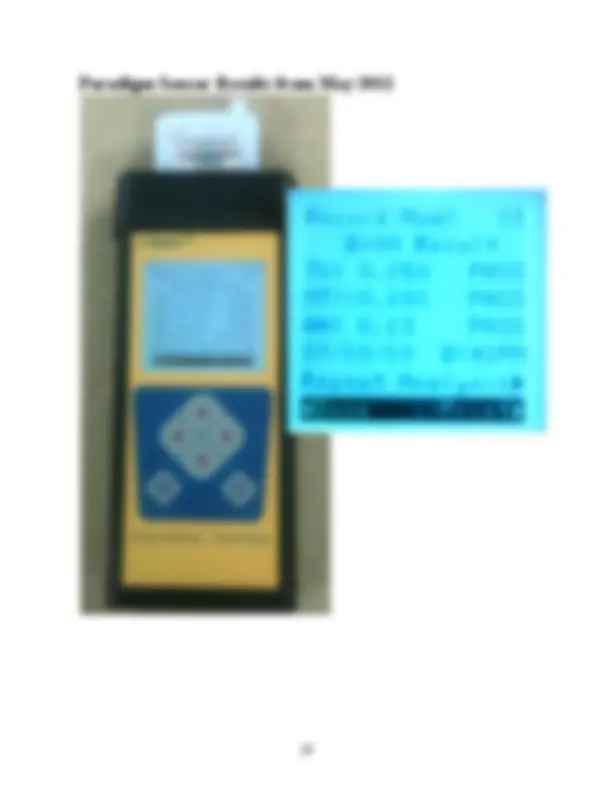
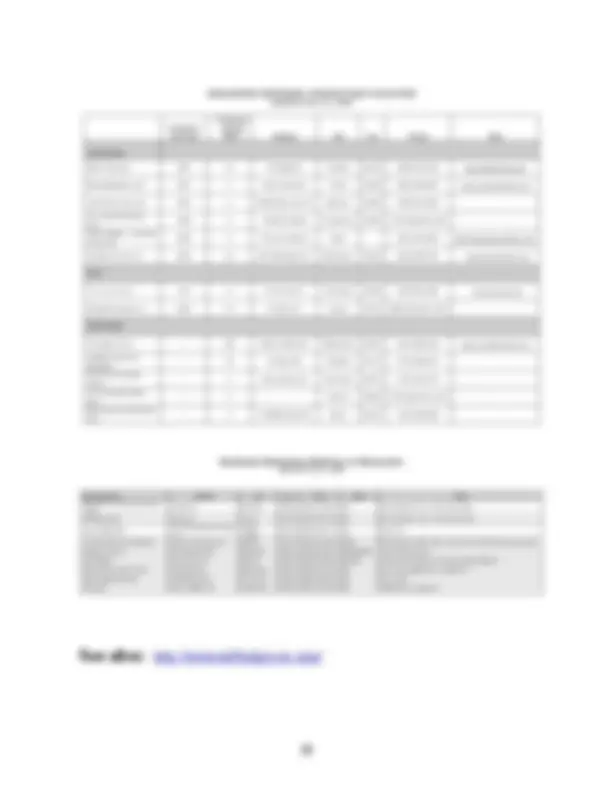
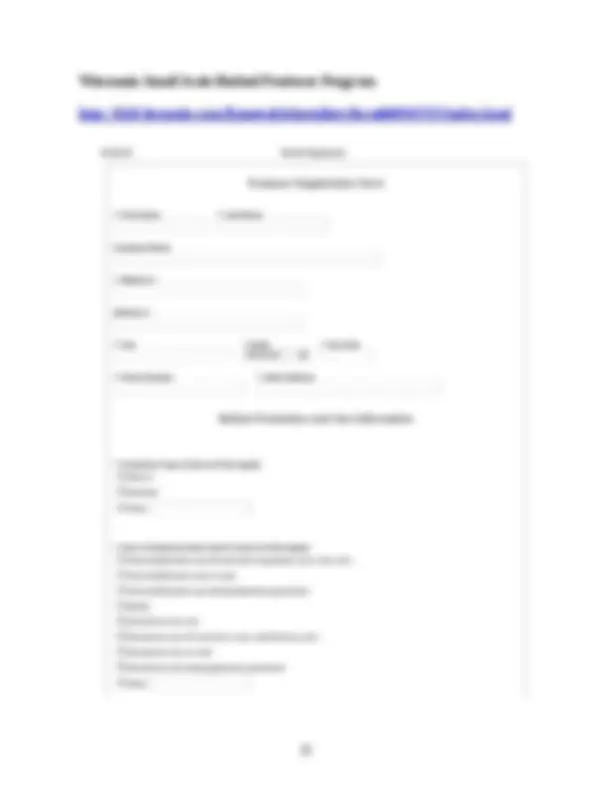
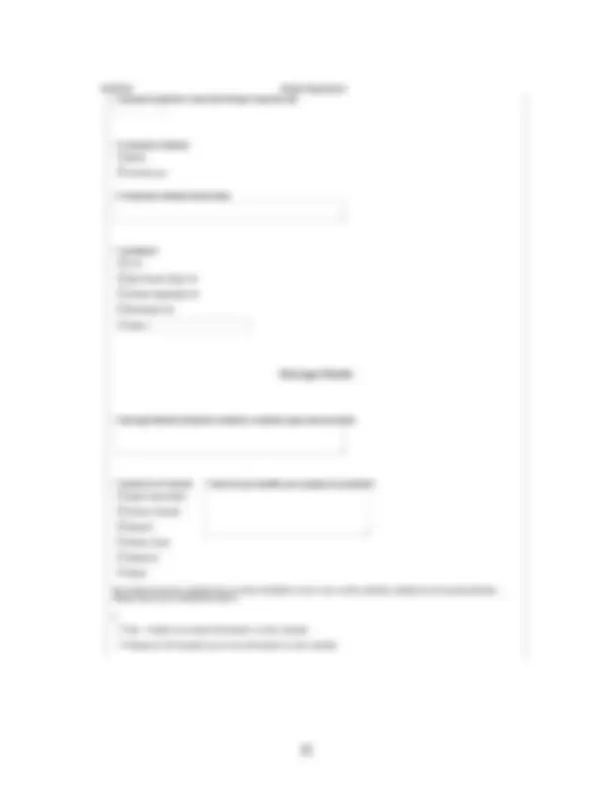
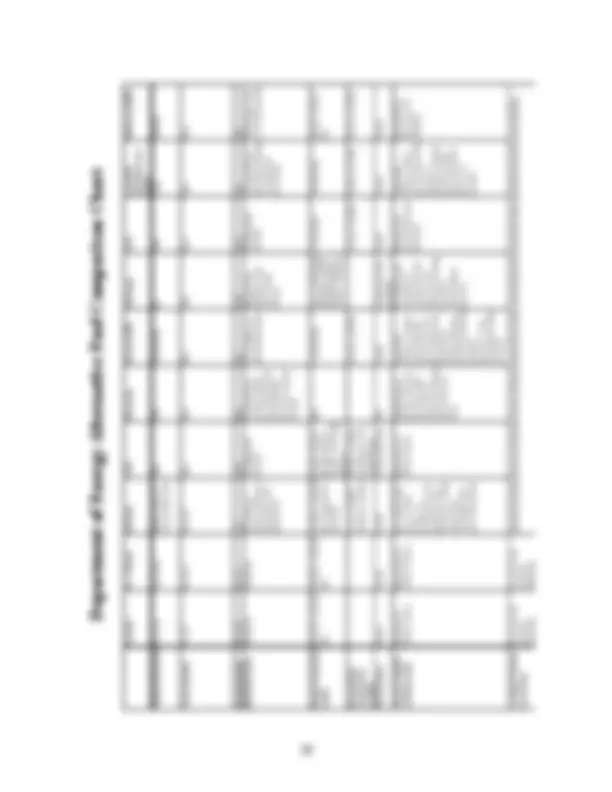
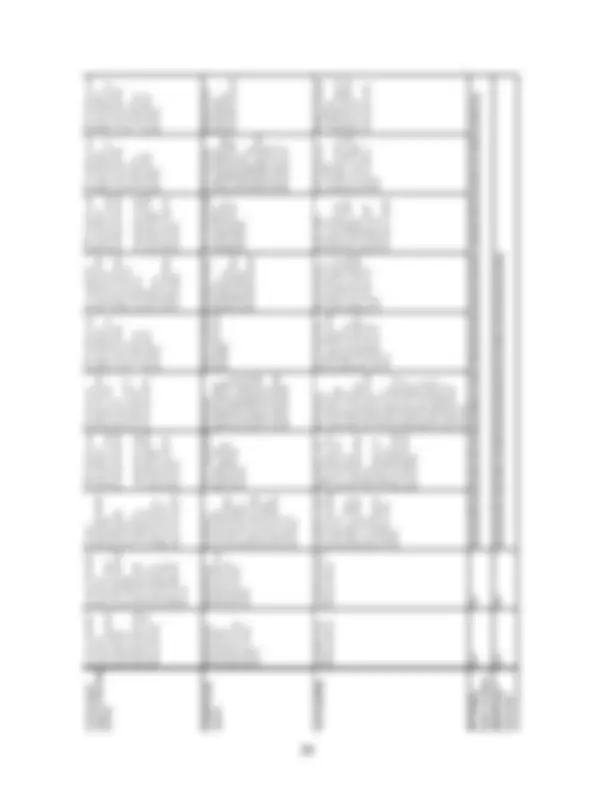
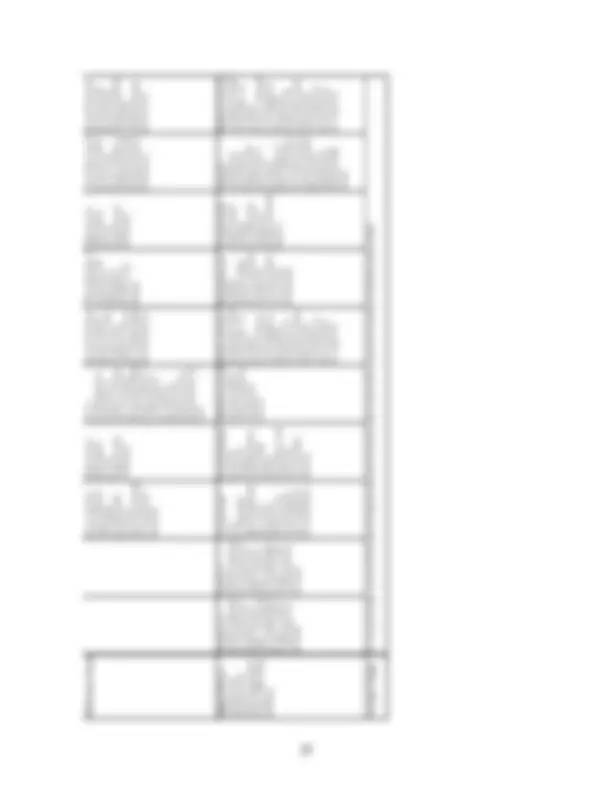
Study with the several resources on Docsity
Earn points by helping other students or get them with a premium plan
Prepare for your exams
Study with the several resources on Docsity
Earn points to download
Earn points by helping other students or get them with a premium plan
Community
Ask the community for help and clear up your study doubts
Discover the best universities in your country according to Docsity users
Free resources
Download our free guides on studying techniques, anxiety management strategies, and thesis advice from Docsity tutors
Standard Test Methods and Specification for Biodiesel Fuel
Typology: Lab Reports
1 / 34
This page cannot be seen from the preview
Don't miss anything!
Biodiesel Lab Test Data Sheet
Property
Test Method Apparatus/Procedure units limits
measured value result
Water content D2709 (^) Sandy Brae Test Kit % vol .050 max (^) or failpass
Water/Sediment D2709 Centrifuge % vol SeparationLayer? yes or no (^) or failpass
Carbon Residue (10 g sample) D4530^ Conradson flame test^ % mass^ .050 max^
pass or fail
FlashPoint, closed cup D^
Pensky Martens Flash Cup
o (^) C 130 min pass or fail Kinematic Viscosity (at 40 o^ C)
D445 (^) Shell Viscosity CupsViscometer^ mm^
(^2) /sec (cStokes) 1.9-6.^
pass or fail
Oxidative Stability (at 110 o^ C) EN 14112^ Rancimat^ hrs^ 3 hrs min.^
pass or fail
Copper Strip Corrosion D130^ Copper strips and heater^ class^ No 3. max^
pass or fail
Glyceride Intermediates 3-27 Test^ Solubility in methanol^ NA
Cloudy Emulsion or Insoluble liquid
yes or no (^) or failpass
Free and Total glycerin pHLip^ pHLip assay^ NA^
Haze or emulsion yes or no^
pass or fail
FFA (pH) pHLip pHLip assay NA (^) indicatoryellow yes or no (^) or failpass
Residual Catalyst (pH) pHLip^ pHLip assay^ NA^
purple indicator yes or no^
pass or fail
Specific gravity D1250 hygrometer NA report NA
Cloud Point D2500 cloud point bath o^ C report NA
Cold Soak Filtration D7501^ Vacuum Filtration^ seconds^
360 sec max
Pass or fail Total Glycerin (TG) (^) Ispec Q100D
Paradigm Sensor Impedance Spectormeter
% mass 0.25%max or fail^ pass
% Methanol (MT) EN Ispec Q
Paradigm Sensor Impedance Spectormeter
% mass 0.20%max or fail^ pass
Acid Number (AN) (^) Ispec Q100D
Paradigm Sensor Impedance Spectormeter
mg KOH/ g fuel 0.50 max^
pass or fail
Fatty Acid Determination of Used Oil Feedstocks
for Biodiesel Production
Background: Biodiesel fuel is made by mixing vegetable oil (triglycerides) with methyl alcohol (aka methanol) in the presence of a basic catalyst (KOH). This produces glycerol (a byproduct) and fatty acid methyl esters (the biodiesel fuel).
O H
O H
O H
O R
O H 3 C
O
O
R
O
O
R
O
O
R
CH 3 O H
KO H
triglyceride (^) methanol glycerol fatty acid methyl ester
3 3
Catalyst Mixture: 20 g of KOH per gallon of oil ( recommended by Josh Tickell, known to be too little ) 26 g of KOH per gallon of oil ( recommended by Piedmont Biofuels ) 36 g of KOH per gallon of oil ( recommended by Jon Van Gerpen , known to be excess )
Reaction Mixture: 1 gallon of methanol/KOH catalyst for every 5 gallons of oil Reaction Temp: Recommend between 55 and 60 o^ C (methanol BP = 64.7 o^ C) Reaction should take from 60 to 120 min at 60 o^ C, Depending on feedstock quality (van Gerpen et al.)
Problem: When vegetable oil is used for cooking purposes (especially for frozen foods), some of the triglyceride oil molecules break down to create free fatty acids (FFAs). The FFAs lower the pH of the oil, and unfortunately will neutralize the basic catalyst (KOH) that is normally added to speed the reaction up.
heat
Free Fatty Acids (FFAs)
Solution: By doing a titration test before processing the fuel, we can measure the concentration of FFAs in the used cooking oil. We will then add additional extra KOH to our reaction to account for the neutralization of the FFAs.
OH
OH
OH
O R
O H 3 C
O
O
R
O
O
R
O
O
R
CH 3 OH
KOH
triglyceride (^) methanol glycerol fatty acid methyl ester
3 3 HO
O
R
Pensky-Martens Closed Cup Flash Point Test
A fuel’s flashpoint is the minimum temperature at which there is a sufficient concentration of evaporated fuel vapor for combustion to propagate after an ignition source (spark or flame) has been introduced. The concentration of fuel vapor is directly related to the fuel’s vapor pressure, which in turn is dependent on temperature (see figure 1 below). Different fuels require different vapor concentrations to initiate combustion, thus flash point varies significantly between fuels (see Figure 2). In fact, the flash point differences between gasoline and diesel fuels are integral factors in the function of spark ignition versus compression ignition engines.
Figure 1. Vapor Pressure as a function of temperature for ethanol and biodiesel fuel.
Figure 2. Flashpoints of several common fuels. Fuels marked with * indicate this value is the minimum allowed by ASTM. Fuel Flashpoint (°C) Flashpoint (°F) Gasoline -43* -45* Acetone -18 0 Methanol 10 50 Ethanol 12 54 Isopropanol 12 54 Octane 13 55 Butanol 35 95 #1 (winter) diesel 38* 100* #2 (summer) diesel 52* 126* #4 (marine) diesel 55* 131* #6 bunker fuel 66* 151* Methyl stearate 110 230 Methyl laurate 113 235 Biodiesel 130* 266* Cetane 135 275 Methyl oleate 180 356 Methyl linoleate 186 367 Canola oil 192 378
The Department of Transportation uses flashpoint to determine shipping and safety regulations. The DOT classifies substances as either flammable or combustible using the following criteria:
Flashpoint (°C) Boiling Point (°C) Flammable Class IA < 22.8°C < 37.8°C Class 1B < 22.8°C > 37.8°C Class IC 22.8°C - 37.8°C N/A
Combustible II 37.8°C - 60°C N/A IIIA 60°C - 93°C N/A IIIB > 93°C N/A
Your instructor will assign you and you lab partner(s) a fuel sample)to measure the flashpoint. Data may be combined to obtain class averages and to draw comparisons.
Inspect the flash point tester to ensure sample test cup is clean, the fluke digital thermometer is in place, and propane supply is turned on.
Making sure test cup and specimen are at least 18°C (32°F) below the expected flash point. Fill the test cup between 50% and 85% full with the fuel sample, place lid on cup and set cup inside the stove, making sure grooves are properly aligned.
Adjust the valve screw on the burner block starting with it all the way closed, then open it only 1/10 of a turn. Using the lighter provided light the test flame and adjust the screw if necessary to attain a flame size of ~ 1/8 inches in diameter (use the bead on the burner block for comparison).
Your instructor will suggest a preheat temperature and heat rate setting for your sample. Using the variable heat rate dial, adjust the rate assigned to you (either 25, 50, 75 or 100).
Stir sample using the mechanism on the top of the flash point instrument. WEAR A GLOVE DURING THIS PROCESS. The top sections of the instrument will get very hot to the touch.
Stop stirring (do this each time you apply the test flame). Lower the flame for half a second, leave it for 1 second, and then quickly raise the flame back to the test position.
Test the flashpoint at 5 o^ C temperature intervals as the sample heats. Stir between each test.
Record the flash point for your fuel. The sample is deemed to have flashed when “a large flame appears and instantaneously propagates itself over the entire surface of the test specimen ". You should see a flash, which sometimes is accompanied by a whoosh or popping noise as well.
Turn the temperature dial down to zero and allow the instrument to cool. Only remove and clean test cup once the temperature have decreased to safe handing temperatures of less than 55°C (130°F). If yours is the last sample that will be tested for the day, turn off the propane tank.
The instructor may assist you in the use of compressed air to cool the flashpoint apparatus.
Viscosity is an important factor in determining the suitability of biodiesel for use in engines. If the fuel viscosity is too high, the injection pump will not be able to supply sufficient fuel into the cylinder. If the viscosity is too low, it may provide insufficient lubrication for fuel pumps and injectors and in extreme cases, may cause fuel injector nozzles to leak/drip.
High viscosity may be caused by: a) Presence of unreacted feedstock oil and/or monoglyceride and diglyceride intermediates in the biodiesel fuel (symptomatic of an incomplete transesterfication process).
b) Presence of glycerol byproduct in the biodiesel fuel (symptomatic of incomplete separation).
Low viscosity may be caused by: a) Presence of methanol in the biodiesel fuel. Note that this will also be indicated by a low fuel flashpoint (symptomatic of an incomplete washing process).
b) Presence of water in the biodiesel fuel. Note that this will also be indicated by the centrifuge water and sediment test (symptomatic of an incomplete drying process).
There are two types of viscosity: kinematic viscosity measures the resistance of a liquid to flowing under gravity and has units of mm^2 /s or centiStokes; dynamic viscosity is the ratio of the applied shear stress to the rate of shear of a material and has units of mPa·s or centiPoise. The kinematic and dynamic viscosity of a fluid are related by its density. The density of biodiesel is about 0.88 g/cm^3.
kinematic viscosity (in centiStokes) = dynamic viscosity (in centiPoise) ÷ density (in g/cm^3 ) 1 centiPoise = 1cP = 1 mPa·s and 1 centiStoke = 1cS = 1 mm^2 /s
The tables below list the kinematic viscosity (in cS) of several pure liquids and common fuels.
The viscometer you will be using measures the dynamic viscosity of fluids, but the ASTM 6751 standard for B100 (pure biodiesel) specifies a kinematic viscosity in the range of 1.9 – 6.0 cS at 40°C (104°F). You will measure the dynamic viscosity of your biodiesel and use the equation above or the attached table to convert its dynamic viscosity value to a kinematic viscosity value.
Pure Liquids Viscosity ethanol 1. hexadecane 2. soy oil 35. palm oil 47. rapeseed oil 54. lard 62. glycerol 176.
Fuel Min Max #1 Diesel 1.3 2. #2 Diesel 1.9 4. #4 Diesel NA 29. Biodiesel (B100) 1.9 6.
Materials & Equipment: Shell Viscosity Cups #1&3 Digital Thermometer Temperature Bath
Procedure:
Feedstock Dynamic viscosity: _________ cP Kinematic Viscosity:________ cS
Biodiesel Dynamic viscosity: _________ cP Kinematic Viscosity:________ cS
Dynamic viscosity (in cP) ÷ density (in g/cm^3 ) = Kinematic viscosity (in cS or mm^2 /s
Sulfur and other acidic/basic compounds in diesel fuels can have corrosive action on various metals (especially copper and brass which are often used in fuel line systems and). The copper strip test measures the relative corrosiveness of a fuel sample.
Excessive copper corrosion may be caused by:
a) Presence of sulfur compounds in the fuel (possibly for biodiesel blends with petroleum).
b) Presence of residual KOH catalyst in the biodiesel fuel (symptomatic of an incomplete neutralization/washing process).
c) Presence of free fatty acids in the biodiesel fuel (symptomatic of aged fuel that has oxidized).
d) Presence of water in the biodiesel fuel. Note that this will also be indicated by the centrifuge water and sediment test (symptomatic of an incomplete drying process).
Materials & Equipment: Copper strip (3” x ½” x 1/16”) Steel wool and ethanol to clean copper surface Constant temperature bath/block (50 oC) Reaction vessel with biodiesel fuel
Procedure:
Slight Tarnish 1 a. Light orange, almost the same as freshly polished strip b. dark orange Moderate Tarnish 2 a. Claret red b. Lavendar c. Multicolored with lavender, blue, or silver overlaid on claret red d. Silvery e. Brassy or gold Dark Tarnish 3 a. Magenta Overcast on Brassy Strip b. Multicolored with red and green showing (peacock), but not gray Corrosion 4 a. Transparent black, grey, or brown with peacock green barely showing b. Graphite or lusterless black c. Glossy or jet black
Rancimat Oxidative Stability Test
Over time, fuels can degrade by reaction with oxygen from the air. The rate at which biodiesel oxidizes depends on both the feedstock and processing conditions used to make the fuel. The oxidation process typically occurs over time scales of weeks to months, and is accelerated by factors such as aeration, light, and temperature. In some cases, the oxidation process may be slowed/inhibited through use of fuel additives (e.g. antioxidants, preservatives, etc.). The Rancimat oxidative stability test measures the rate at which biodiesel fuel decomposes when subjected to elevated temperatures and vigorous aeration. These conditions allow for a rapid measure of fuel stability that has been shown to correlate to the slower oxidative process that occurs under normal storage conditions.
Preparing the Instrument Do this step a few days before the measurement is to be made:
Cleaning the Instrument The cleanness of instruments and accessories is an absolute necessity for achieving reliable, reproducible and correct analytical results. Even minute contamination can catalytically accelerate the oxidative decomposition and lead to completely false results.
Conductivity (uS/cm) versus time (hours)
Log-Linear Extrapolation of Oxidative Stability for Peanut oil
Temperature (C) versus Time (h)
I n d u c t i o n t i m e S t a b i l i t y t i m e
6
0
. 3^
μ^ S^
/ c^
m
h
P e a n u t o i l / D B G 2 3 0 7 P e a n u t o i l / D B G 2 3 0 7 P e a n u t o i l / D B G 2 3 0 7 P e a n u t o i l / D B G 2 3 0 7
1 0
2 0
3 0
4 0
5 0
6 0
7 0
8 0
9 0
1 0 0
1 1 0
1 2 0
1 3 0
1 4 0
1 0 1 1 0 2 1 0 3
° C
h
The “3/27” Glyceride Intermediate Test
(Mono, Di, and Triglyceride content)
Biodiesel that meets ASTM specs should dissolve in the methanol solvent resulting in a single phase of clear liquid. Biodiesel that is out of spec will result in a cloudy emulsion of glyceride and methyl ester droplets suspended in the methanol.
Biodiesel that meets ASTM specs for free and total glycerol should remain dissolved in the methanol solvent as a single phase of clear liquid. After settling, biodiesel that is out of spec will typically exhibit an insoluble glyceride liquid layer at the bottom of the tube in addition to the cloudy emulsion suspended in the methanol.
For video footage, see http://www.youtube.com/watch?v=R3jGvefA4OI
High quality biodiesel is indicated by:
A cloudy biodiesel layer combined with a clear, red indicator layer is characteristic of excess free or total glycerin or free fatty acids (in aged fuel). The glycerin/glycerides may also form a middle emulsion layer between the fuel and the indicator.
A cloudy lower layer is likely due to soap contamination. Soap may be formed by a combination of water, free fatty acids and catalyst.
A purple lower layer indicates a high pH. This results from residual alkaline catalyst (KOH, NaOH, etc.) in the fuel.
An orange or yellow lower layer indicates a low pH. This results either from high free fatty acid content of the feedstock or aging of the fuel.
Water and sediment can cause problems with fuel line icing and filter plugging. In order to meet ASTM specifications, biodiesel must contain < 0.050% water and sediment by volume. Failure to meet this specification usually is attributable to poor separation processes during the biodiesel synthesis or washing stages.
Materials & Equipment: Centrifuge, Centrifuge tubes, biodiesel fuel
Procedure:
Note: ASTM D2709 requires specialized centrifuge tubes to obtain the desired accuracy for this test. If performing the test to these standards, the taper bottom tubes must accommodate 100 mL fuel samples and be marked with graduations to the nearest 0.01 mL.