
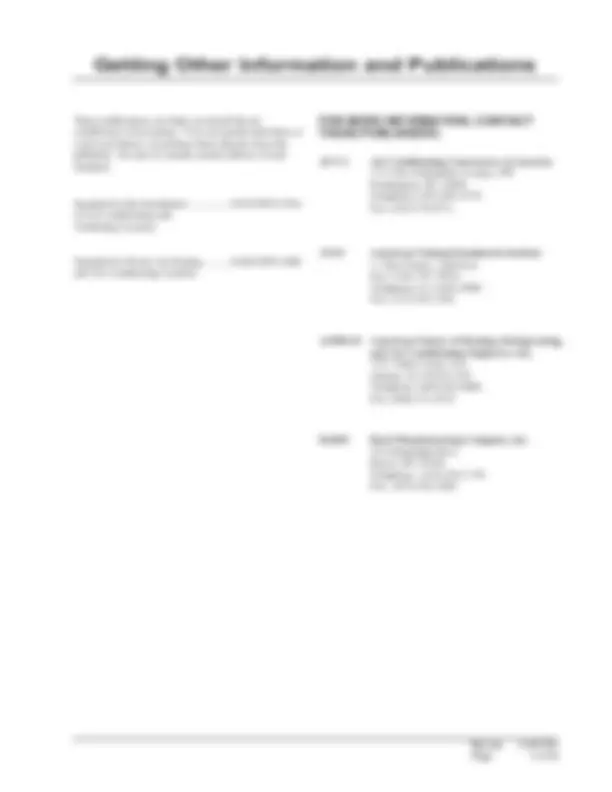
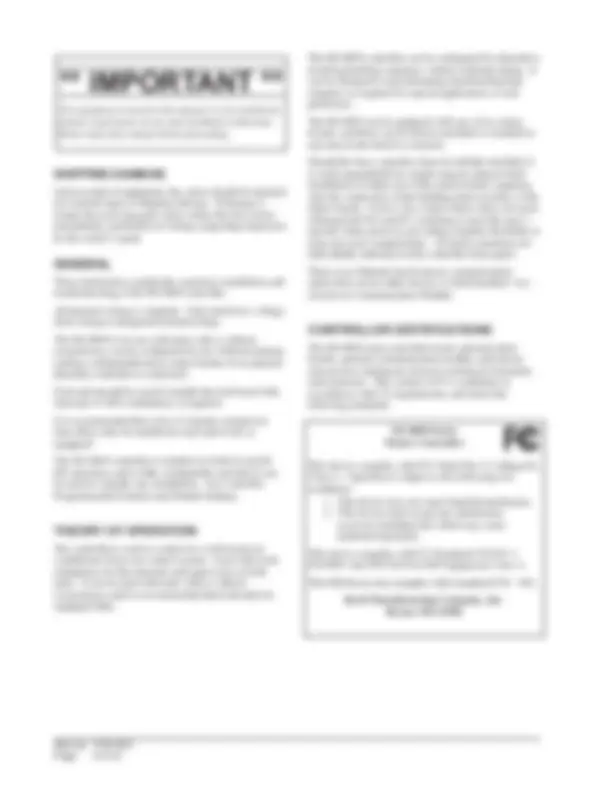
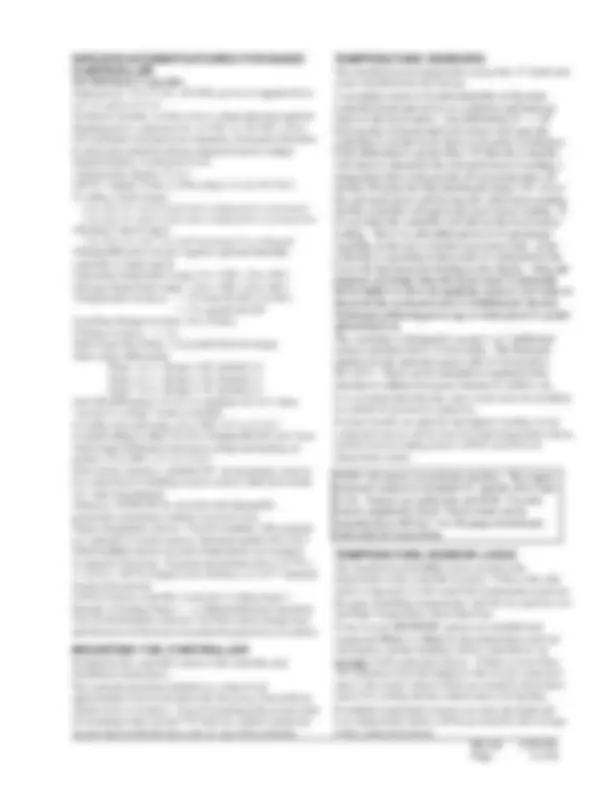
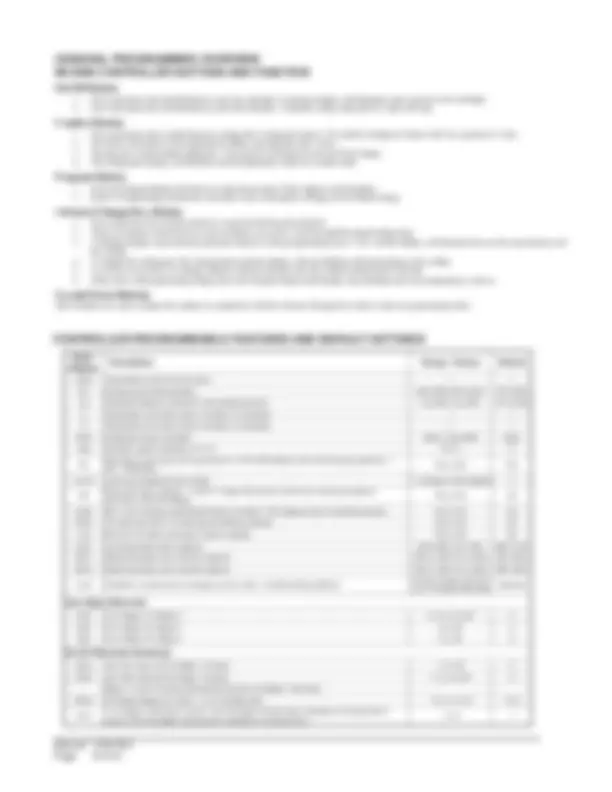
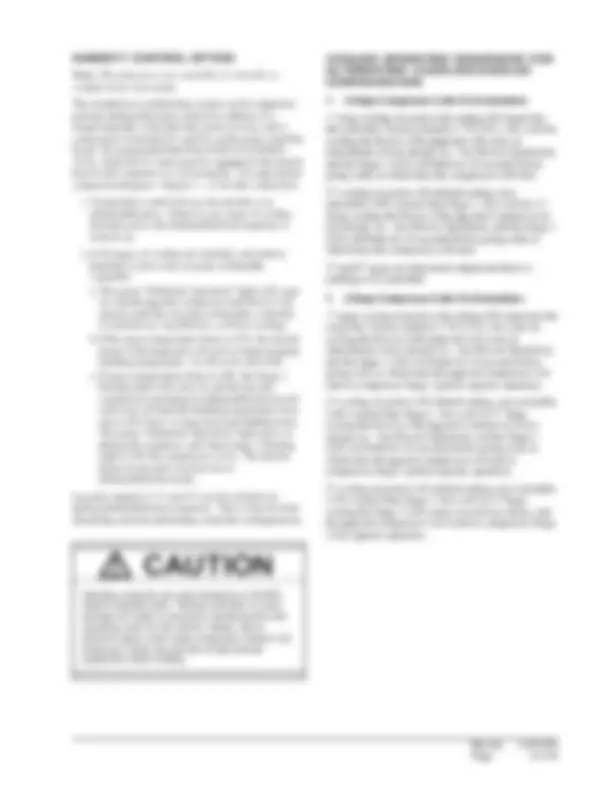
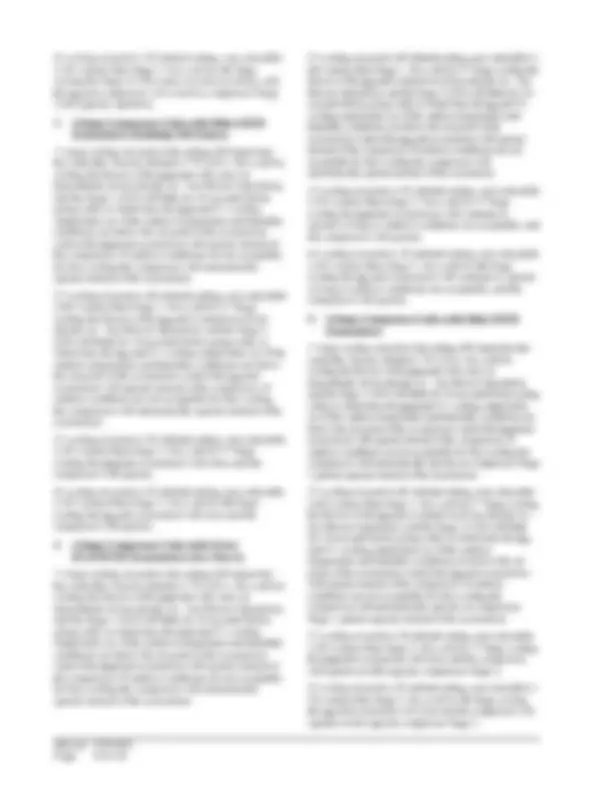
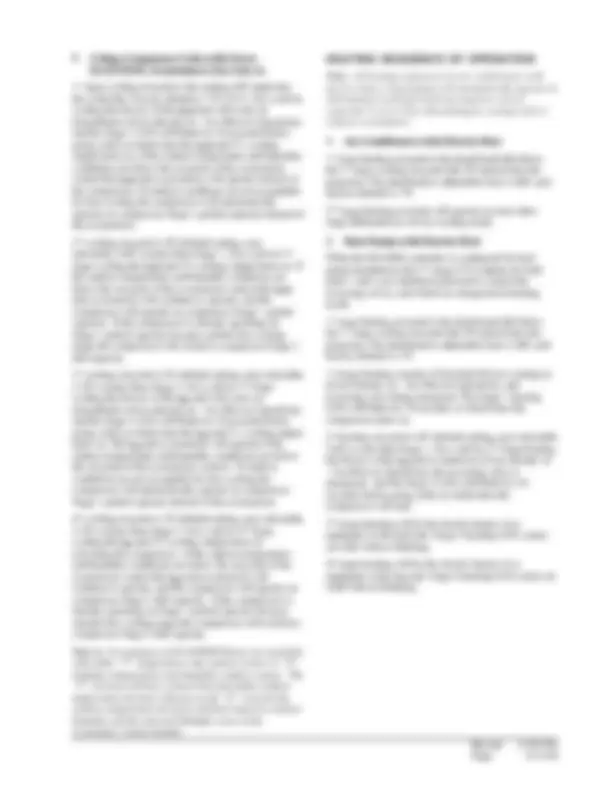

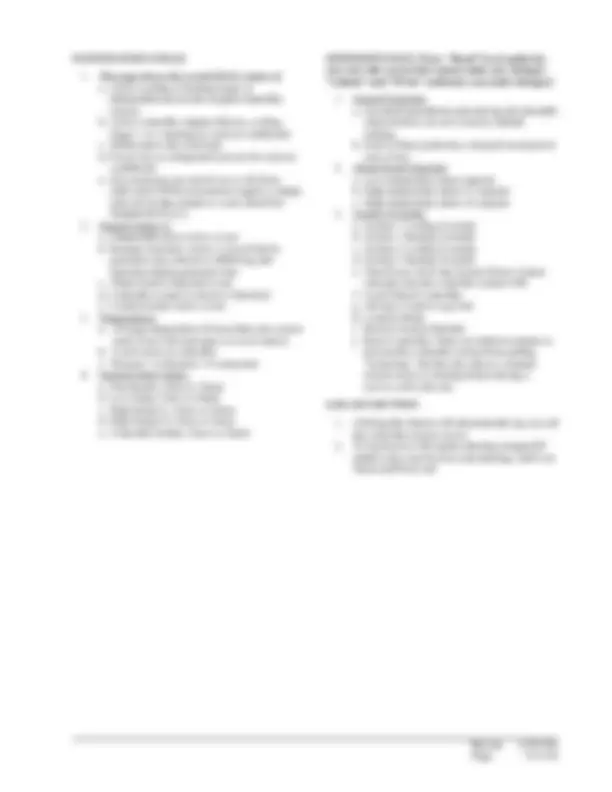
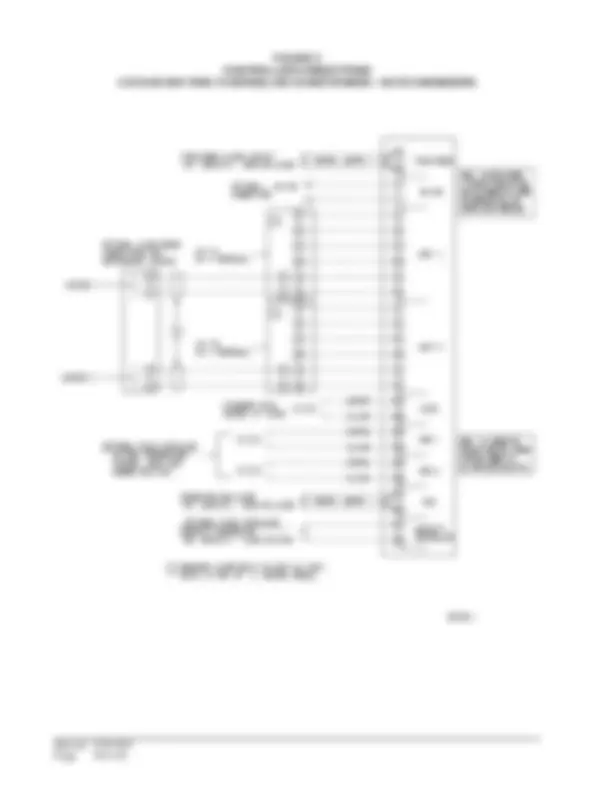
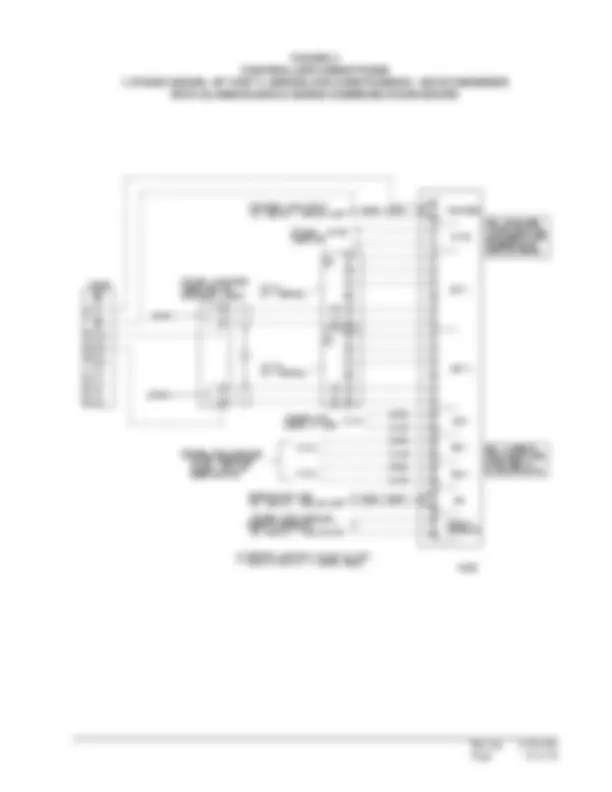
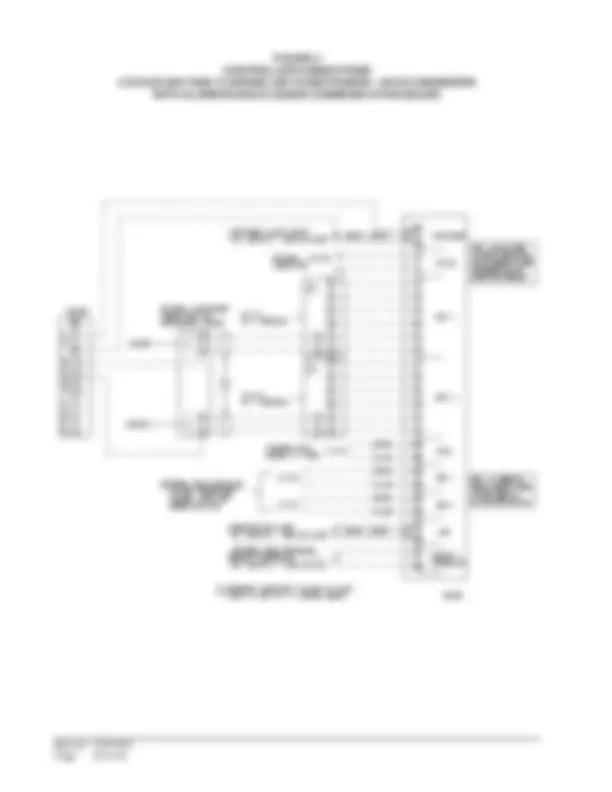
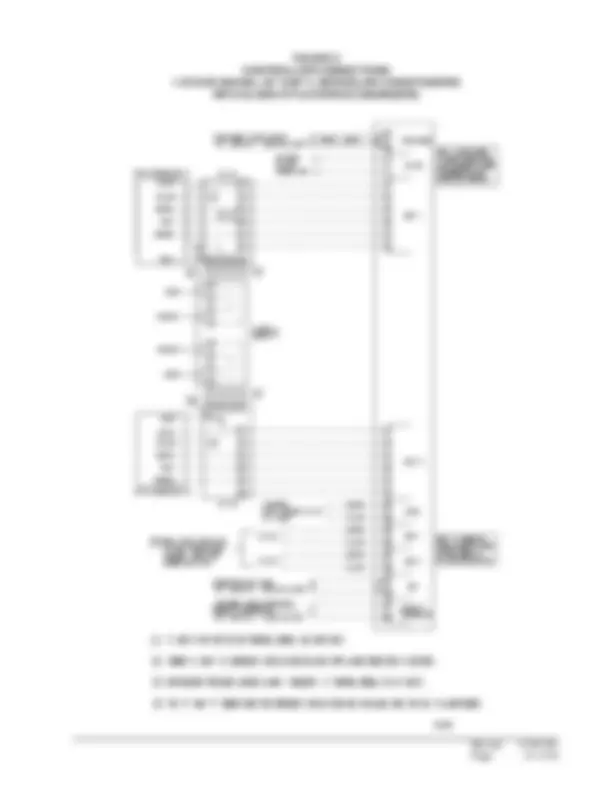
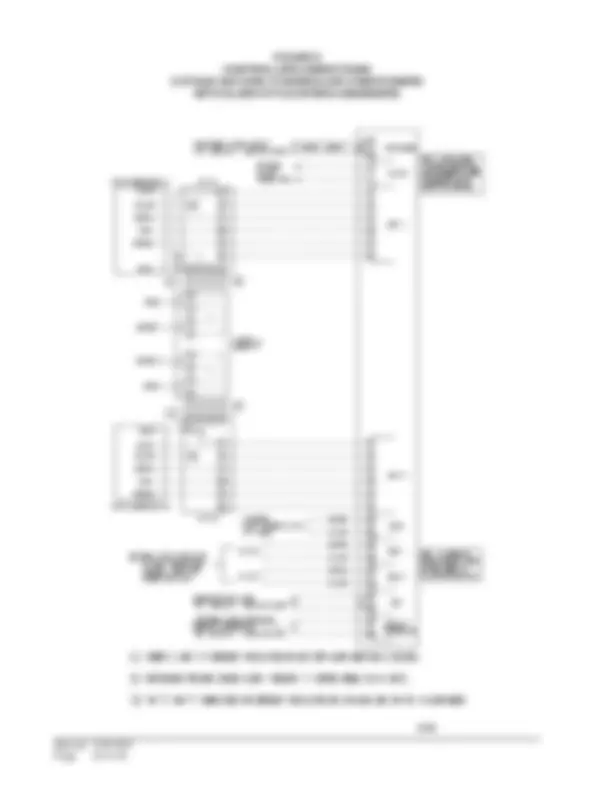
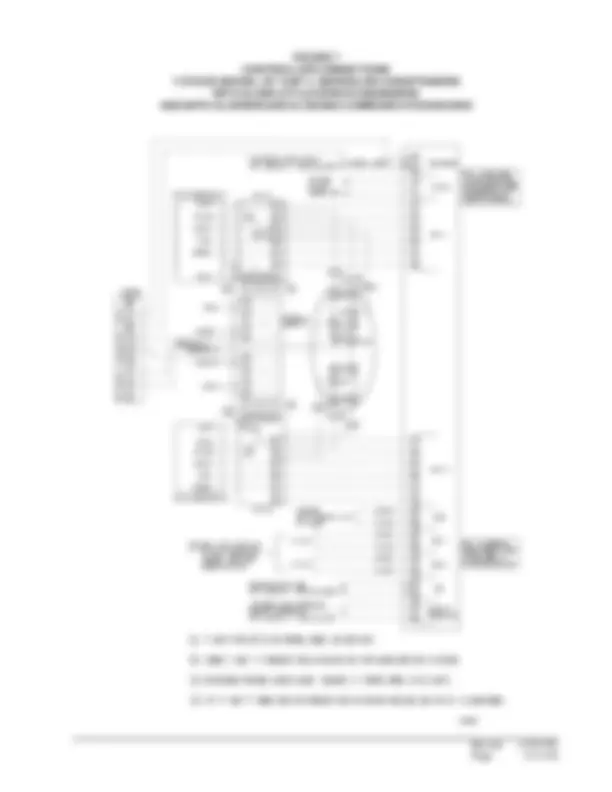
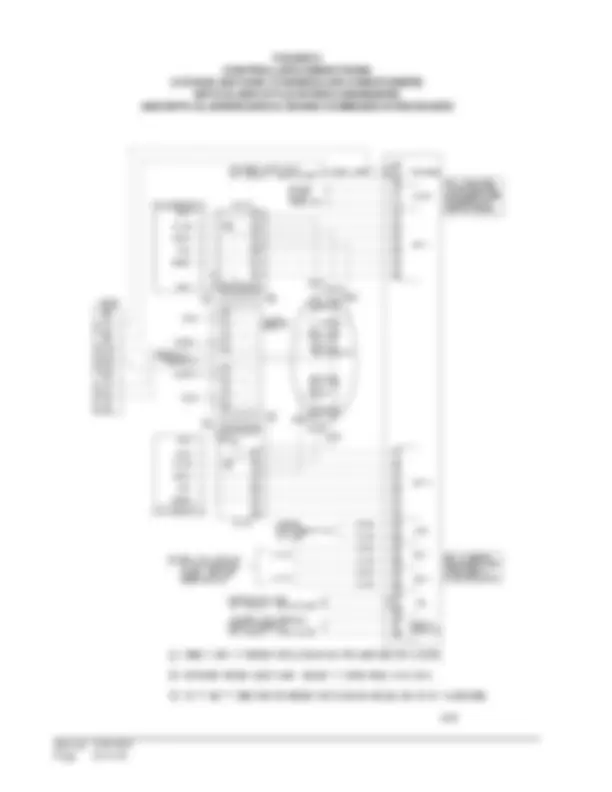
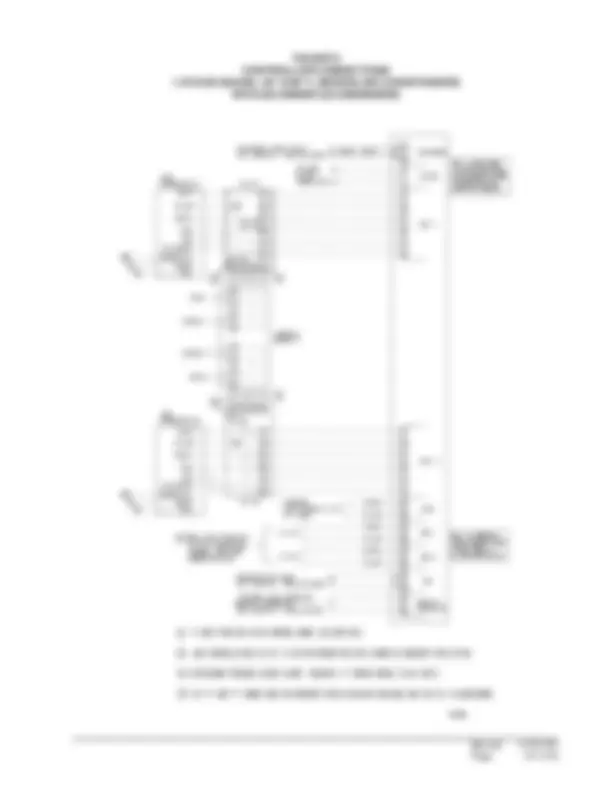
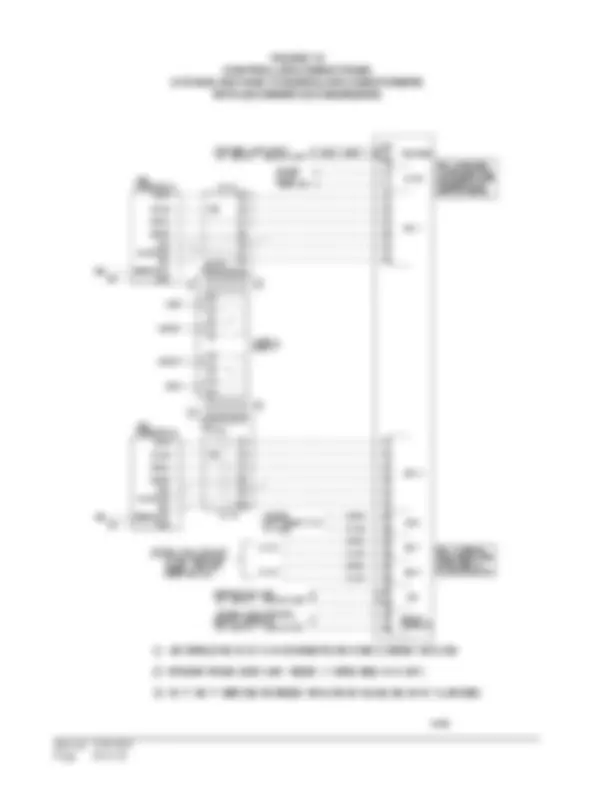
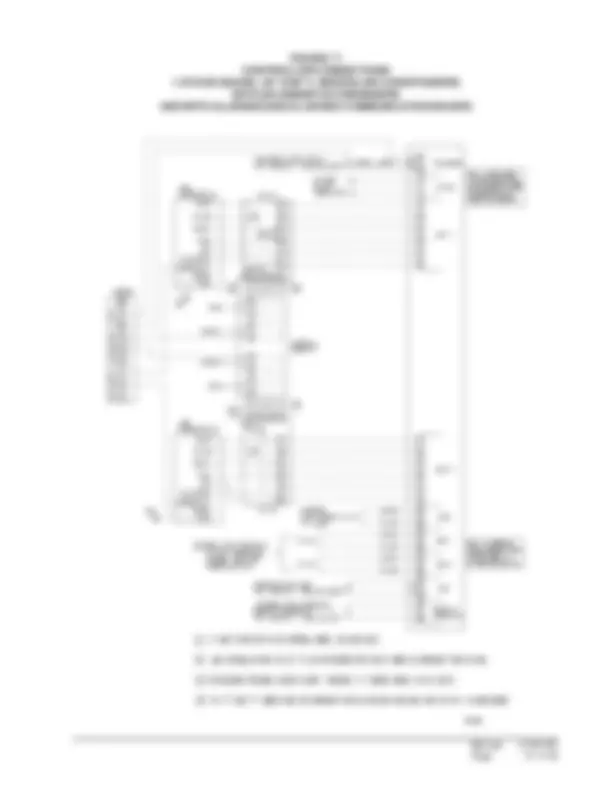
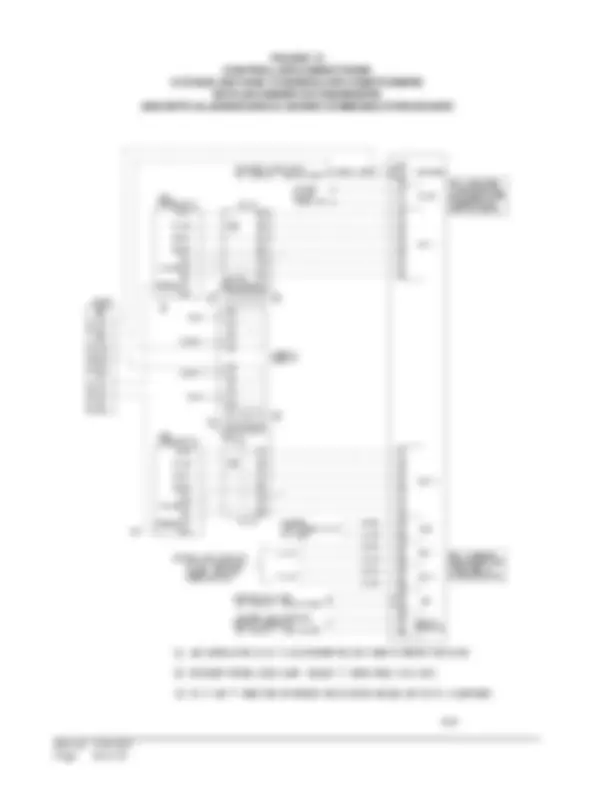
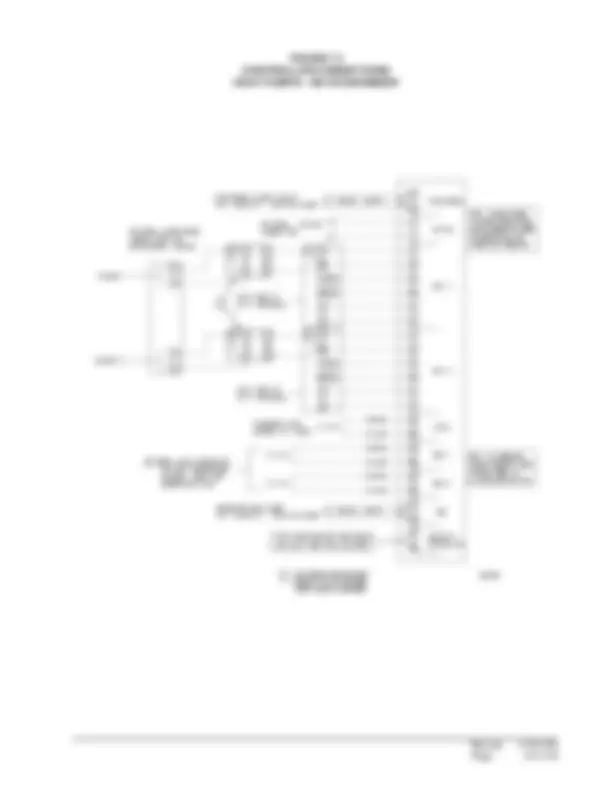
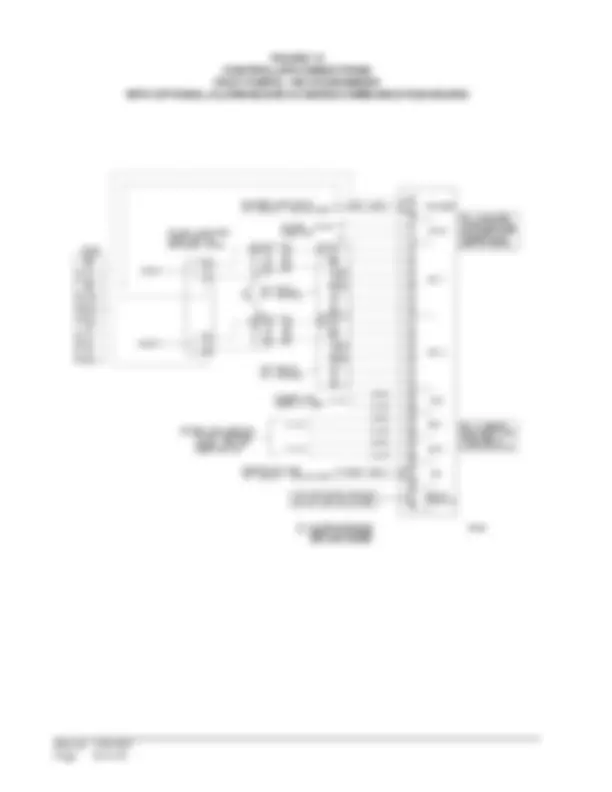
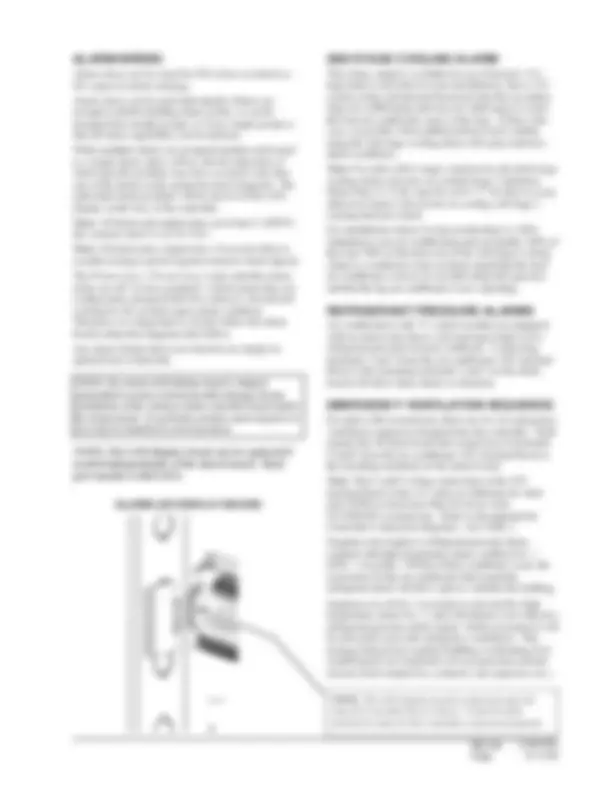
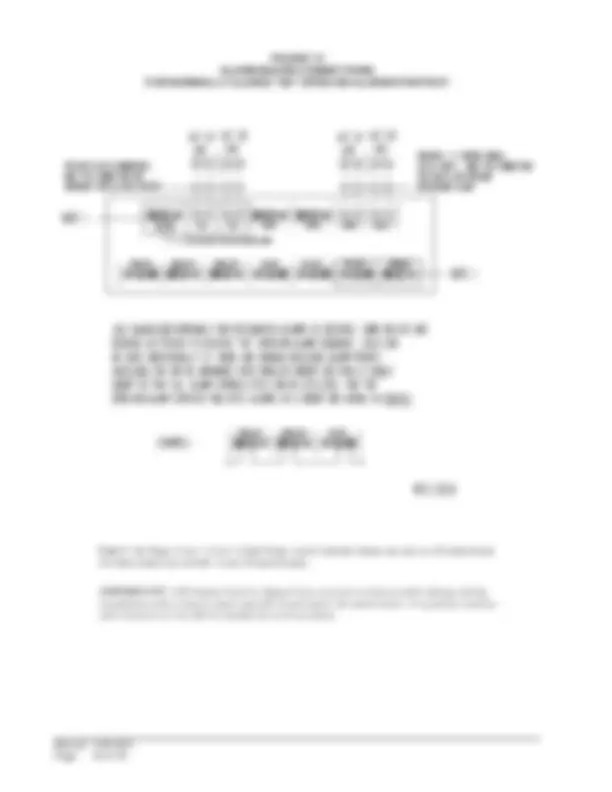
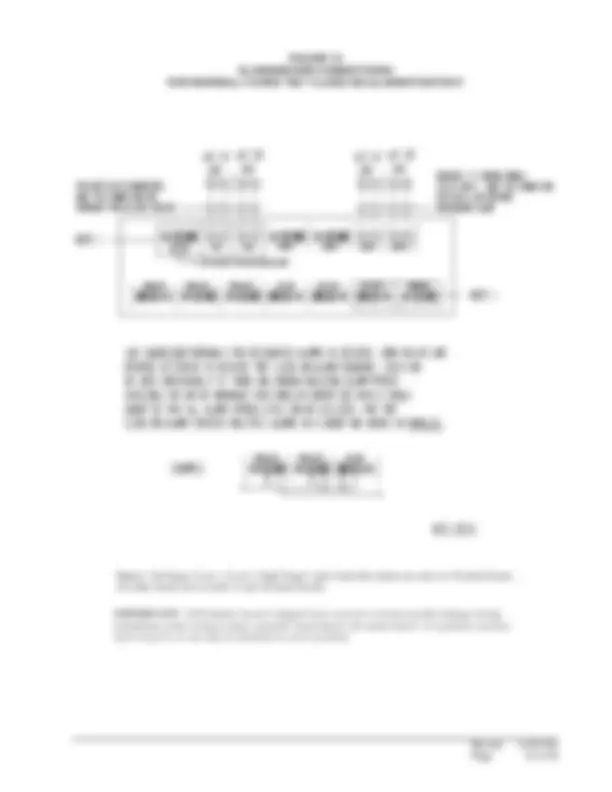
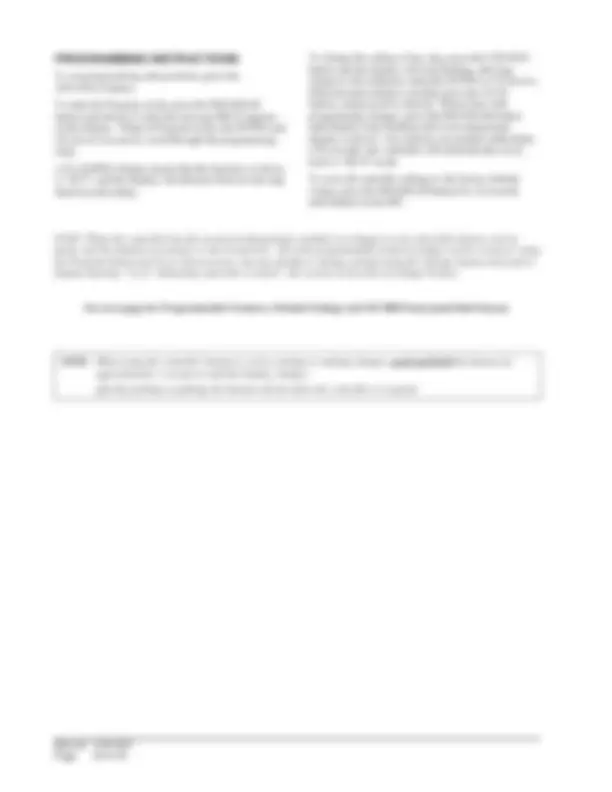
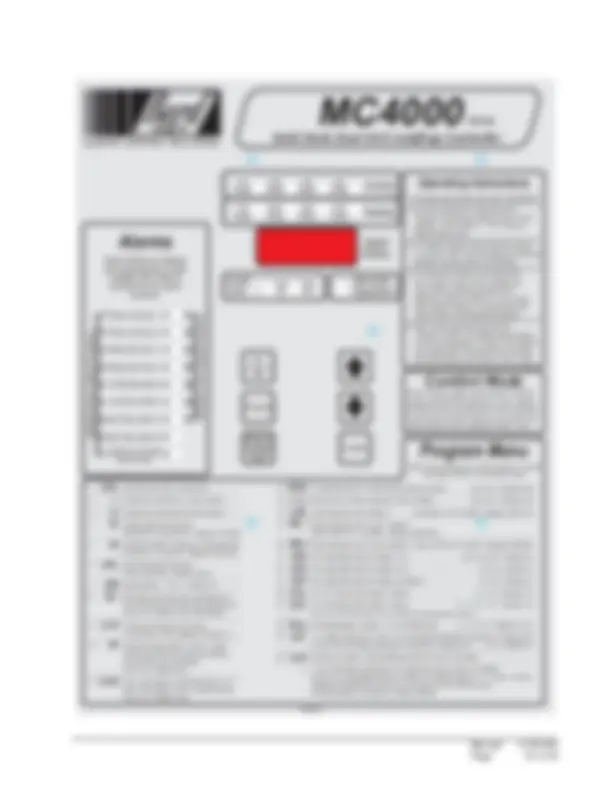
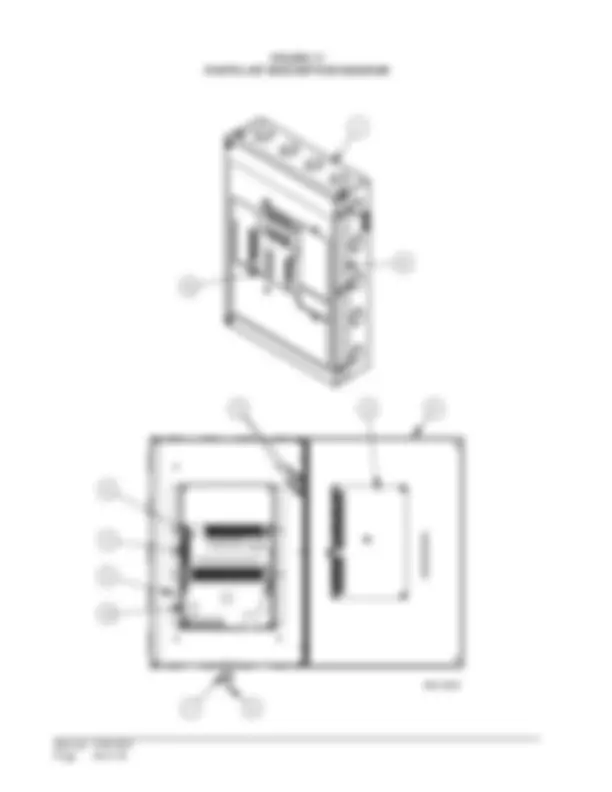
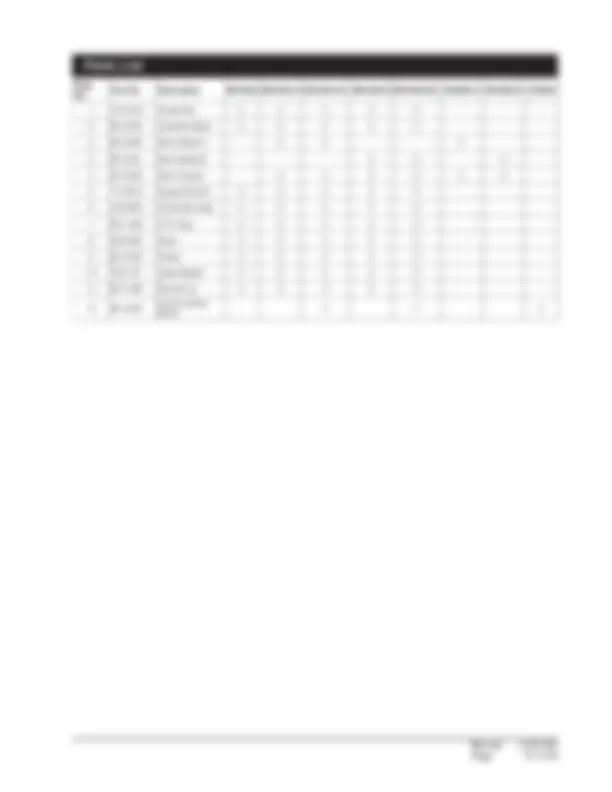
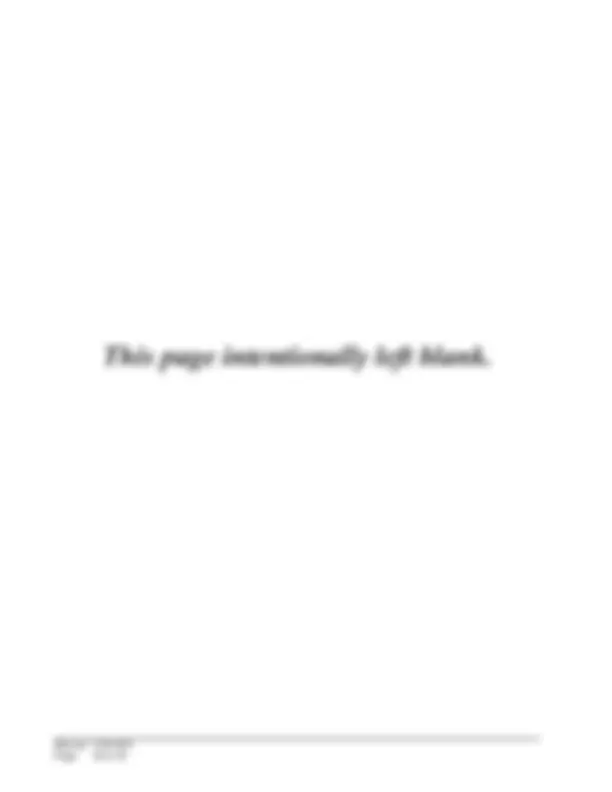
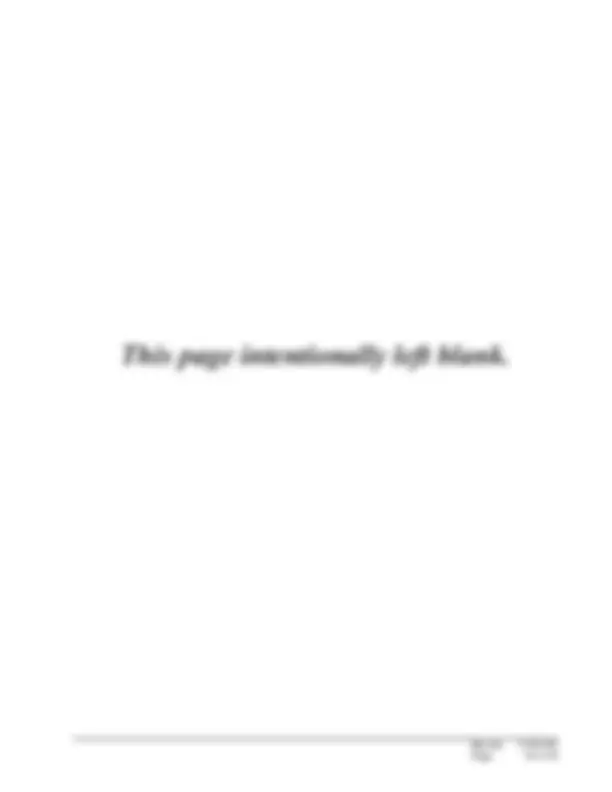
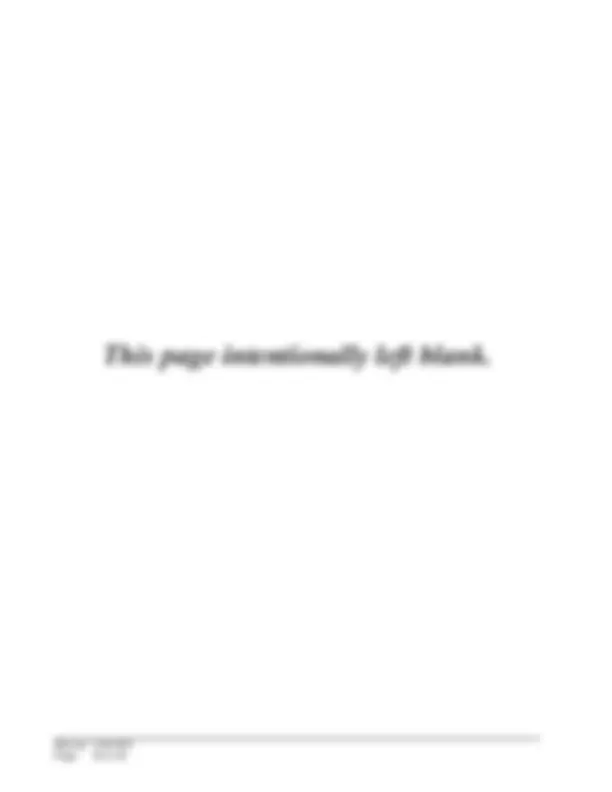
Study with the several resources on Docsity
Earn points by helping other students or get them with a premium plan
Prepare for your exams
Study with the several resources on Docsity
Earn points to download
Earn points by helping other students or get them with a premium plan
Community
Ask the community for help and clear up your study doubts
Discover the best universities in your country according to Docsity users
Free resources
Download our free guides on studying techniques, anxiety management strategies, and thesis advice from Docsity tutors
Shows how to get accepted in college
Typology: Cheat Sheet
1 / 40
This page cannot be seen from the preview
Don't miss anything!
MC4000 SERIES SOLID STATE
DUAL UNIT LEAD/LAG CONTROLLER
INSTALLATION INSTRUCTIONS
& REPLACEMENT PARTS LIST
Bard Manufacturing Company, Inc. Bryan, Ohio 43506
CONTENTS
Figures Figure 1 Controller Connections 1-Stage (WA/WL, WA/ WL Series) A/C w/No Economizers ..... 17 Figure 2 Controller Connections 2-Stage (WAS/WLS Series) A/C - No Economizers ................ 18 Figure 3 Controller Connections 1-Stage (WA/WL, WA/ WL Series) A/C - No Econo with Alarm Board & CB4000 Comm. Board ........................... 19 Figure 4 Controller Connections 2-Stage (WAS/WLS Series) A/C - No Econo with Alarm Board & CB4000 Comm. Board ........................... 20 Figure 5 Controller Connections 1-Stage (WA/WL, WA/ WL Series) A/C-Older EIFM Econo ..... 21 Figure 6 Controller Connections 2-Stage (WAS/WLS Series) A/C-Older Style EIFM Econo ...... 22 Figure 7 Controller Connections 1-Stage (WA/WL, WA/ WL Series) A/C w/Older Style EIFM Econo & w/Alarm Board/CB4000 Comm. Board ... 23 Figure 8 Controller Connections 2-Stage (WAS/WLS Series) A/C w/Older Style EIFM Econo & w/Alarm Board/CB4000 Comm. Board ................. 24 Figure 9 Controller Connections 1-Stage (WA/WL, WA/ WL Series) A/C w/ECONWMT Econo .. 25 Figure 10 Controller Connections 2-Stage (WAS/WLS Series) A/C w/ECONWMT Econo .......... 26 Figure 11 Controller Connections 1-Stage (WA/WL, WA/ WL Series) A/C w/ECONWMT Econo & w/Alarm Board/CB4000 Comm. Board ................. 27 Figure 12 Controller Connections 2-Stage (WAS/WLS Series) A/C w/ECONWMT Econo & w/Alarm Board/CB4000 Comm. Board ................. 28 Figure 13 Controller Connections Heat Pumps - No Economizers ..................................... 29 Figure 14 Controller Connections Heat Pumps - No Economizers w/Opt. Alarm Board & CB4000 Communication Board .............. 30 — — — Alarm LED Display Board ...................... 31 Figure 15 Alarm Board Connections for Normally Closed "NC" Open-On-Alarm Strategy ............... 32 Figure 16 Alarm Board Connections for Normally Open "NO" Close-On-Alarm Strategy .............. 33 — — — MC4000 Label ........................................ 35 Figure 17 Parts List Description Diagram ............... 36
Tables Table 1 Hook-Up Diagram Selection ................... 17 Table Parts List ................................................ 37
Getting Other Information and Publications 3 MC4000 General Information Shipping Damage .................................................. 4 General .................................................................. 4 Theory of Operation ............................................... 4 Controller Certifications ......................................... 4 Specifications/Features for Basic Controller MC4000 Basic Controller ....................................... 5 Mounting the Controller Installation Instructions .......................................... 5 Temperature Sensors Two Optional Sensor Inputs ................................... 5 Temperature Sensor Logic Using Multiple Sensors .......................................... 5 Controller Input/Output Specifications MC4000 Controller Connections ............................ 6 Specifications/Features for Alarm Boards MC4000-A with Optional Base Alarm ..................... 6 MC4000-B with Enhanced Version Alarm .............. 6 Low Voltage Field Wiring Circuitry in the MC4000 ......................................... 7 Controller Grounding Earth ground .......................................................... 7 Controller Power-Up Time Delay on Power-Up ....................................... 7 Fire Suppression Circuit Disabling the MC4000 ........................................... 7 Staging Delay Periods Stages 1 - 4 ............................................................ 7 Blower Operation Various Blower Options ......................................... 7 Advance (Swap) Lead/Lag Unit Feature Manual Switching of Units ..................................... 7 Accelerate Timer Feature Testing the Timer Function ..................................... 7 General Programming Overview Buttons & Function ................................................ 8 Humidity Control Option Adding Optional Humidity Control .......................... 9 Cooling Operating Sequences for Alternating Lead/Lag/Lead/Lag Config ........ 9- Cooling Operating Sequences for Non-Alt Lead/Lead/Lag/Lag Config ........... 11- Heating Sequence of Operation ........................... 13 Specifications Opt. Remote Comm. Board .... 14- Controller Wiring Refer to Connection Diagram .............................. 16 Security (Locking) Feature Locking and Unlocking the MC4000 .................... 16 Generator Run Feature Standby Generator Disable Operation ................. 16 Backup DC Power Connection Input Connections Available ................................ 16 Alarm Wiring .......................................................... 31 2nd Stage Cooling Alarm ...................................... 31 Refrigerant Pressure Alarms ................................ 31 Emergency Ventilation Sequence ........................ 31 Programming Instructions ................................... 34
SHIPPING DAMAGE
Upon receipt of equipment, the carton should be checked for external signs of shipping damage. If damage is found, the receiving party must contact the last carrier immediately, preferably in writing, requesting inspection by the carrier’s agent.
GENERAL
These instructions explain the operation, installation and troubleshooting of the MC4000 controller.
All internal wiring is complete. Only attach low voltage field wiring to designated terminal strips.
The MC4000 is for use with units with or without economizers, can be configured for use with heat pumps, and has a dehumidification control feature if an optional humidity controller is connected.
Each unit should be sized to handle the total load of the structure if 100% redundancy is required.
It is recommended that a five (5) minute compressor time delay relay be installed in each unit if not so equipped.
The MC4000 controller is suitable for both 50 and 60 HZ operation, and is fully configurable such that it can be used in virtually any installation. See Controller Programmable Features and Default Settings.
THEORY OF OPERATION
The controller is used to control two wall mount air conditioners from one control system. It provides total redundancy for the structure and equal wear on both units. It can be used with units with or without economizers and it is recommended that both units be equipped alike.
The MC4000 controller can be configured for alternative (lead/lag/lead/lag) sequence, which is default setting. It can be changed to non-alternating (lead/lead/lag/lag) sequence as required for special applications or user preference. The MC4000 can be equipped with one of two alarm boards, and these can be factory-installed or installed at any time in the field if so desired. Should the base controller alone be initially installed, it is easily upgradeable by simple snap-in, plug-in field installation of either one of the alarm boards, requiring only the connection of the building alarm circuitry to the alarm boards. Form C dry contact alarm relays are used, offering both NO and NC switching to meet the user’s specific alarm protocol, providing complete flexibility to meet any user's requirements. All alarm actuations are individually indicated on the controller front panel. There is an Ethernet based remote communication option that can be either factory or field installed. See section on Communication Module.
CONTROLLER CERTIFICATIONS The MC4000 main controller board, optional alarm boards, optional communication module, and remote sensors have undergone extensive testing for immunity and emissions. This system is FCC-compliant, in accordance with CE requirements, and meets the following standards:
MC4000 Series Master Controller
This device complies with FCC Rule Part 15, Subpart B, Class A. Operation is subject to the following two conditions:
The equipment covered in this manual is to be installed by trained, experienced service and installation technicians. Please read entire manual before proceeding.
SPECIFICATIONS/FEATURES FOR BASIC CONTROLLER MC4000 Basic Controller •Input power: 18-32 VAC, 60/50Hz, power is supplied from A/C #1 and/or A/C # •Isolation circuitry: no line or low voltage phasing required •Backup power: connection for -24 VDC or -48 VDC (-20 to - 56V) maintains microprocessor operation, front panel indication & alarm relay operation during commercial power outages. •Digital display: 4-character LCD •Temperature display: F or C •HVAC outputs: Form A (NO) relays (1A @ 24 VAC) •Cooling control stages:
•Heating Control stages:
•Dehumidification circuit: requires optional humidity controller as input signal •Operating temperature range: 0 to 120F (-18 to 49C) •Storage temperature range: -20 to 140F (-29 to 60C) •Temperature accuracy: +/- 1F from 60-85F (16-30C) +/- 1% outside 60-85F •Lead/lag changeover time: 0 to 30 days •Timing accuracy: +/- 1% •Inter-stage time delay: 10 seconds between stages •Inter-stage differential: Stage 1 to 2 - Range 2-6F, default is 4 Stage 2 to 3 - Range 2-3F, default is 2 Stage 3 to 4 - Range 2-3F, default is 2 •On-Off differential: 2F (1C) is standard, 4F (3C) when “excessive cycling” mode is enabled •Cooling set point range: 65 to 90F (18.3 to 32.2C) •Comfort setting-Cooling 72F (22C), Heating 68F(20C), for 1 hour •Dead band (difference between cooling and heating set points): 2F to 40F (1.1C to 22.2C) •Fire/smoke interface: standard NC circuit jumper, remove for connection to building system control, shuts down both A/C units immediately •Memory: EEPROM for set point and changeable parameters (maintains settings on power loss) •Space temperature sensors: 1 local is standard, will accept up to 2 optional 25' remote sensors, Bard part number 8612-023. When multiple sensors are used, temperatures are averaged •Controller Enclosure: 20-gauge pre-painted steel, 9.25"W x 13.50"H x 3.00"D, hinged cover, thirteen (13) .875" diameter electrical knockouts •LEDs for basic controller: Lead unit, Cooling stages 1 through 4, Heating Stages 1 – 4, Dehumidification operation •Six (6) Push-button controls: On/Off switch-Change lead unit-Increase & Decrease set points-Program/Save-Comfort.
MOUNTING THE CONTROLLER Included in the controller carton is the controller and installation instructions. The controller should be installed on a vertical wall approximately four (4) feet above the floor-away from drafts & outside doors or windows. Four (4) mounting holes are provided for mounting to the wall and 7/8" holes for conduit connections are provided in both the base, sides & top of the controller.
TEMPERATURE SENSORS The standard (local) temperature sensor has 12" leads and comes installed from the factory. A secondary sensor is located internally on the main controller board and serves as a reference and back-up sensor to the local sensor. Any differential of +/- 12F between the on-board and local sensor will cause the controller to use the local sensor as its point of reference. If the differential is greater than 12F then the controller will check to determine the on-board sensor is reading a temperature that is between the SP (set-point) plus 12F and the SP minus the DB (dead-band) minus 12F. If it is the on-board sensor will become the valid sensor reading and the controller will ignore the local sensor reading. If it is not then the controller will still use the local sensor reading. This is to add additional level of operational capability in the rare event the local sensor fails. If the controller is operating in this mode it is indicated by the lower left decimal point flashing in the display. Note: for purposes of testing when the local sensor is manually driven higher or lower by applying warm or cool water to the probe the on-board sensor is inhibited for the first 30-minutes following power up, or when power is cycled off and back on. The controller is designed to accept 1 or 2 additional sensors and those have 25-foot leads. The Bard part number for the optional sensor with 25-foot leads is 8612-023. These can be installed as required in the structure to address hot spots, barriers to airflow, etc. It is recommended that the sensor lead wires be installed in conduit for protective purposes. If alarm boards are utilized, the highest reading of any connected sensor will be used for high temperature alarm and the lowest reading sensor will be used for low temperature alarm.
TEMPERATURE SENSOR LOGIC The standard local (LSEn) sensor monitors the temperature at the controller location. If this is the only sensor connected, it will control the temperature read-out, the space (building) temperature, and also be used for Low and High Temperature alarm functions. If one or more REMOTE sensors are installed and connected (Rem 1 or Rem 2), the temperature read-out will display and the building will be controlled to an average of all connected sensors. If there is more than 10F difference from the highest to the lowest connected sensor, the actual control will be governed by the hottest sensor for cooling and the coldest sensor for heating. If multiple temperature sensors are used, the High and Low temperature alarms will be governed by the average of the connected sensors.
NOTE: All sensors are polarity sensitive. The copper lead must connect to terminal CU, and the silver lead to AG. Sensors are solid state, not RTD. Use only sensors supplied by Bard. Sensor leads can be extended up to 200 feet. Use 18-gauge twisted pair with soldered connections.
LOW VOLTAGE FIELD WIRING
The MC4000 is powered from the air conditioners that it is controlling, 24 VAC (18-32V) low voltage only.
Circuitry in the MC4000 isolates the power supplies of the two air conditioners so that no back feeds or phasing problems can occur. Additionally, if one air conditioner loses power, the MC4000 and the other air conditioner are unaffected and will continue to operate normally.
Connect the low voltage field wiring from each unit per the low voltage field wiring diagrams in Section on “Controller Wiring”. NOTE: Maximum of 18-gauge control wiring should be used. Using heavier gauge wiring can create excessive stress on the control board as door is opened and closed. Create a wiring loop so the door can open and close without stressing terminal blocks.
CONTROLLER GROUNDING A reliable earth ground must be connected in addition to any grounding from conduit. Grounding lugs are supplied for this purpose.
CONTROLLER POWER-UP
Whenever power is first applied to the controller, there is a twenty (20) second time-delay prior to any function (other than display) becoming active. This time-delay is in effect if the controller On/Off button is used when 24VAC from air conditioners is present, and also if controller is in “ON” position and 24VAC from air conditioners is removed and then restored.
FIRE SUPPRESSION CIRCUIT
To disable the MC4000 and shut down both air conditioners, terminals F1 and F2 may be used. The F and F2 terminals must be jumpered together for normal operation. A normally closed (nc) set of dry contacts may be connected across the terminals and the factory jumper removed for use with a field-installed fire suppression system. The contacts must open if a fire is detected. See appropriate connection diagram - Figures 1, 2 or 3 for this connection. Contacts should be rated for pilot duty operation at 2 amp 24VAC minimum. Shielded wire (22-gauge minimum) must be used, and the shield must be grounded to the controller enclosure.
IMPORTANT NOTE: Older Bard R-22 models employ an electronic blower control that has a 60-second blower off-delay. Current production R-410A models do not use a blower off-delay device and the remainder of this (paragraph) does not apply. In order to have immediate shutdown of the blower motor, in addition to disabling the run function of the air conditioners will require a simple wiring modification at the blower control located in the electrical control panel of the air conditioners being controlled by the lead/lag controller. To eliminate the 60-second blower off-delay, disconnect and isolate the wire that is factory-connected to the “R” terminal on the electronic blower control, and then connect a jumper from the “G” terminal on the blower
control to the “R” terminal on the blower control. The electronic blower control will now function as an on-off relay with no off-delay, and the blower motor will stop running immediately when the F1-F2 fire suppression circuit is activated (opened).
STAGING DELAY PERIODS The following delays are built in for both cooling & heating: Stage 1 – 0 seconds for blower (if not already on as
Stage 2 – 10 seconds after Stage 1 for blower
Stage 3 – 10 seconds after Stage 2 Stage 4 – 10 seconds after Stage 3 Note: For cooling Stages 1 and 2, the stage LED will blink for 10 seconds while the cooling output is delayed after that stage is called for. There is also a delay after the stage is satisfied, and after the LED stops blinking, the stage will turn off. There is a minimum 10-second delay between stages 2 & 3, and 3 & 4, but no delayed output when stage is turned on or off, and LED for those stages will not blink.
BLOWER OPERATION The controller can be configured to have main HVAC blowers cycle on and off on demand; have all blowers run continuously; or have the lead unit blower run continuously with the lag unit blower cycling on demand. Default setting is the blower(s) start and stop on demand. There is also an option to have all blowers cycle on if one remote sensor is connected, and a temperature difference of more than 5F between any two sensors is observed. This helps to redistribute the heat load within the structure and should reduce compressor operating time. When any of the stages are satisfied, the stage LED will blink for ten (10) seconds before the stage is actually turned off.
ADVANCE (SWAP) LEAD/LAG UNIT FEATURE Pressing the Advance button for one (1) second will cause the lead and lag units to change positions. This may be useful during service and maintenance procedures.
ACCELERATE TIMER FEATURE Pressing the UP arrow button for five (5) seconds will activate an accelerate (speed-up) mode, causing the normal changeover time increments of days to be reduced to seconds. Example: 7 days becomes 7 seconds. When “ACC” displays, release button. Whichever LED is on, indicating lead unit will blink over for each second until the controller switches. This is a check for the timer functionality.
GENERAL PROGRAMMING OVERVIEW MC4000 CONTROLLER BUTTONS AND FUNCTION On/Off Button
Comfort Button
Program Button
Advance/Change/Save Button
Up and Down Buttons
CONTROLLER PROGRAMMABLE FEATURES AND DEFAULT SETTINGS
LS E n Te mperatureatlocal(main)sensor — — SP C oolingsetpointtemperature 65 to 90 F( 18 to 32 C) 77 F( 25 C) db D eadbandbetweencoolingSPandheatingsetpoint 2 to 40 F( 1 to 24 C) 17 F( 9. 4 C) r 1 Te mperatureatremotesensor 1 location,ifconnected — — r 2 Te mperatureatremotesensor 2 location,ifconnected — — cF An C ontinuousbloweroperation No ne,Lead,Both None de g C ontrollersystemoperatesinForC F orC F Al t AYel tesrn=aAtinltegrnLaetaindg-Lag-Lead-LagsequenceorNon-AlternatingLead-Lead-Lag-Lagsequence— Ye sorNo Yes LL CO Le ad-Lagchangeovertime(Days) 1 - 30 days,or 0 fordisabled 7 HP H(o evaetrrpidumespaloNgoicn-eAnlatbseletdtin—g)onlyfor^1 - stageheatpumpsandforcesLead-Lagsequence Ye sorNo No Cb d 5 Un it 1 and 2 blowersautomaticallybothrunifdeltaT> 5 Fbetweenany 2 connectedsensors Ye sorNo Yes OF de 3 - minuteleadunit& 4 - minutelagunitoff-delayenabled Ye sorNo No cr un Mi nimum 3 - minutecompressorruntimeenabled Ye sorNo No Lo AL Lo wtemperaturealarmsetpoint 28 to 65 F(- 2 to 18 C) 45 F( 7. 2 C) HA L 1 Hi ghtemperaturealarmlevel# 1 setpoint 70 Fto 120 F( 21 to 49 C) 90 F( 32 C) HA L 2 Hi ghtemperaturealarmlevel# 2 setpoint 70 Fto 120 F( 21 to 49 C) 95 F( 35 C) Lo cd C ontrollerislockedandnochangescanbemade.Consultbuildingauthority. ILfo loccdkiefdc,hdainsgpelasyawttiellmshpotewd Unlocked
IS d 2 Fr omStage 1 toStage 2 2 , 3 , 4 , 5 or 6 F 4 IS d 3 Fr omStage 2 toStage 3 2 or 3 F 2 IS d 4 Fr omStage 3 toStage 4 2 or 3 F 2
CS o n Tu rn"On"aboveSPforStage 1 Cooling + 1 or 2 F 2 CS oF Tu rn"Off"belowSPforStage 1 Cooling - 1 , 2 , 3 or 4 F - 2 Stage 2 , 3 and 4 CoolingautomaticallysetsameasStage 1 decisions HS oo Al lHeatingStagesareequal-/+on&offdifferential - 1 /+ 1 or- 2 /+ 2 - 2 /+ 2 C oPr^1 if osert^2 t-osta 2 gtehec 2 onmdpsretasgseor,CiofoselintgtoA^1 latrhme^2 anctdivsattaegseoCnoCoolionlginAglaCramlla 3 ctivatesonCoolingCall^2 , 1 or 2 1
4 th^ cooling set point is 2F (default setting, user selectable 2-3F) warmer than Stage 3. On a call for 4th Stage cooling the Stage 4 LED comes on solid (no delay), and the lag unit compressor will switch to compressor Stage 2 full capacity operation.
1 st^ stage cooling set point is the setting (SP) input into the controller. Factory default is 77F (25C). On a call for cooling the blower of the lead unit will come on immediately (if not already on – See Blower Operation), and the Stage 1 LED will blink for 10-seconds before going solid, at which time the lead unit Y1 cooling output turns on. If the outdoor temperature and humidity conditions are below the set point of the economizer control the lead unit economizer will operate instead of the compressor. If outdoor conditions are not acceptable for free cooling the compressor will automatically operate instead of the economizer.
2 nd^ cooling set point is 4F (default setting, user selectable 2-6F) warmer than Stage 1. On a call for 2nd^ Stage cooling the blower of the lag unit is turned on (if not already on – See Blower Operation), and the Stage 2 LED will blink for 10-seconds before going solid, at which time the lag unit Y1 cooling output turns on. If the outdoor temperature and humidity conditions are below the set point of the economizer control the lag unit economizer will operate instead of the compressor. If outdoor conditions are not acceptable for free cooling the compressor will automatically operate instead of the economizer.
3 rd^ cooling set point is 2F (default setting, user selectable 2-3F) warmer than Stage 2. On a call for 3rd^ Stage cooling the lead unit economizer will close and the compressor will operate.
4 th^ cooling set point is 2F (default setting, user selectable 2-3F) warmer than Stage 3. On a call for 4th Stage cooling the lag unit economizer will close and the compressor will operate.
1 st^ stage cooling set point is the setting (SP) input into the controller. Factory default is 77F (25C). On a call for cooling the blower of the lead unit will come on immediately (if not already on – See Blower Operation), and the Stage 1 LED will blink for 10-seconds before going solid, at which time the lead unit Y1 cooling output turns on. If the outdoor temperature and humidity conditions are below the set point of the economizer control the lead unit economizer will operate instead of the compressor. If outdoor conditions are not acceptable for free cooling the compressor will automatically operate instead of the economizer.
2 nd^ cooling set point is 4F (default setting, user selectable 2- 6F) warmer than Stage 1. On a call for 2nd^ Stage cooling the blower of the lag unit is turned on (if not already on – See Blower Operation), and the Stage 2 LED will blink for 10- seconds before going solid, at which time the lag unit Y cooling output turns on. If the outdoor temperature and humidity conditions are below the set point of the economizer control the lag unit economizer will operate instead of the compressor. If outdoor conditions are not acceptable for free cooling the compressor will automatically operate instead of the economizer. 3 rd^ cooling set point is 2F (default setting, user selectable 2-3F) warmer than Stage 2. On a call for 3rd^ Stage cooling the lead unit economizer will continue to operate as long as outdoor conditions are acceptable, and the compressor will operate. 4 th^ cooling set point is 2F (default setting, user selectable 2-3F) warmer than Stage 3. On a call for 4th Stage cooling the lag unit economizer will continue to operate as long as outdoor conditions are acceptable, and the compressor will operate.
1 st^ stage cooling set point is the setting (SP) input into the controller. Factory default is 77F (25C). On a call for cooling the blower of the lead unit will come on immediately (if not already on – See Blower Operation), and the Stage 1 LED will blink for 10- seconds before going solid, at which time the lead unit Y1 cooling output turns on. If the outdoor temperature and humidity conditions are below the set point of the economizer control the lead unit economizer will operate instead of the compressor. If outdoor conditions are not acceptable for free cooling the compressor will automatically operate on compressor Stage 1 partial capacity instead of the economizer.
2 nd^ cooling set point is 4F (default setting, user selectable 2-6F) warmer than Stage 1. On a call for 2nd Stage cooling the blower of the lag unit is turned on (if not already on – See Blower Operation), and the Stage 2 LED will blink for 10-seconds before going solid, at which time the lag unit Y1 cooling output turns on. If the outdoor temperature and humidity conditions are below the set point of the economizer control the lag unit economizer will operate instead of the compressor. If outdoor conditions are not acceptable for free cooling the compressor will automatically operate on compressor Stage 1 partial capacity instead of the economizer.
3 rd^ cooling set point is 2F (default setting, user selectable 2-3F) warmer than Stage 2. On a call for 3rd Stage cooling the lead unit economizer will continue to operate as long as outdoor conditions are acceptable, and the compressor will operate on compressor Stage 1 partial capacity. If outdoor conditions are not acceptable for free cooling the lead unit compressor will automatically be operating on compressor Stage 1 partial capacity and will go to Stage 2 full capacity operation.
4 th^ cooling set point is 2F (default setting, user selectable 2-3F) warmer than Stage 3. On a call for 4th Stage cooling the lag unit economizer will continue to operate as long as outdoor conditions are acceptable, and the compressor will operate on compressor Stage 1 partial capacity. If outdoor conditions are not acceptable for free cooling the lag unit compressor will automatically be operating on compressor Stage 1 partial capacity and will go to Stage 2 full capacity operation.
COOLING OPERATING SEQUENCES FOR NON-ALTERNATING LEAD/LEAD/LAG/ LAG CONFIGURATION Note: Heat pumps cannot be operated in Non-Alternating Lead/Lead/Lag/Lag sequence. Selecting Heat Pump = Yes will override a Non-Alternating selection and force system to Alternating Lead/Lag/Lead/Lag sequence.
1 st^ stage cooling set point is the setting (SP) input into the controller. Factory default is 77F (25C). On a call for cooling the blower of the lead unit will come on immediately (if not already on – See Blower Operation), and the Stage 1 LED will blink for 10-seconds before going solid, at which time the lead unit Y1 cooling output turns on. If the outdoor temperature and humidity conditions are below the set point of the economizer control the lead unit economizer will operate instead of the compressor. If outdoor conditions are not acceptable for free cooling the compressor will automatically operate on compressor Stage 1 partial capacity instead of the economizer.
2 nd^ cooling set point is 4F (default setting, user selectable 2-6F) warmer than Stage 1. On a call for 2nd stage cooling the lead unit Y2 cooling output turns on. If the outdoor temperature and humidity conditions are below the set point of the economizer control the lead unit economizer will continue to operate, and the compressor will operate on compressor Stage 1 partial capacity. If the compressor is already operating on Stage 1 partial capacity because outside free cooling range the compressor will switch to compressor Stage 2 full capacity.
3 rd^ cooling set point is 2F (default setting, user selectable 2-3F) warmer than Stage 2. On a call for 3rd^ Stage cooling the blower of the lag unit will come on immediately (if not already on – See Blower Operation), and the Stage 3 LED will blink for 10-seconds before going solid, at which time the lag unit Y1 cooling output turns on. The lag unit economizer will operate if the outdoor temperature and humidity conditions are below the set point of the economizer control. If outdoor conditions are not acceptable for free cooling the compressor will automatically operate on compressor Stage 1 partial capacity instead of the economizer.
4 th^ cooling set point is 2F (default setting, user selectable 2-3F) warmer than Stage 3. On a call for 4th^ Stage cooling the lag unit Y2 cooling output turns on activating the compressor. If the outdoor temperature and humidity conditions are below the set point of the economizer control the lag unit economizer will continue to operate, and the compressor will operate on compressor Stage 2 full capacity. If the compressor is already operating on Stage 1 partial capacity because outside free cooling range the compressor will switch to compressor Stage 2 full capacity.
Note A: Economizers in ECONWMT-Series are available with either “T” temperature only outdoor sensor or “E” enthalpy (temperature and humidity) outdoor sensor. The “T” versions will have a fixed (but selectable) outdoor temperature decision whereas on the “E” versions the outdoor temperature decision will float based on outdoor humidity and the selected Enthalpy curve in the economizer control module.
HEATING SEQUENCE OF OPERATION Note: All heating sequences for air conditioners with electric heat or heat pumps will automatically operate in Alternating Lead/Lag/Lead/Lag sequence even if controller is set to Non-Alternating for cooling with or without economizers.
SPECIFICATIONS FOR OPTIONAL REMOTE COMMUNICATION BOARD
CB4000 COMMUNICATION BOARD
Note: If this communication board was not originally factory installed it can be field-installed at anytime. Bard part number is CB4000. Either the –A or –B alarm board is required for CB4000 to operate properly. It allows remote access via Ethernet, depending upon level of authority assigned, to all functions of the controller system the same as it one was in the building where the controller system is physically installed.
Required Input Connections to the CB4000 (these are all internal connections from either the alarm board or main controller board):
OPERATING SYSTEM
No special software is required to access the system. The CB4000 has a default address, simply follow these instructions:
TO ACCESS THE SYSTEM
For XP or Windows 2000:
For Vista or Windows 7:
LOG IN PAGE
USER PAGE
CONTROLLER WIRING
The MC4000 can be used for controlling two (2) air conditioners with or without economizers. It can also be configured for two (2) heat pumps without economizers. Units with economizers will connect differently than units without economizers; therefore, it is important to use the correct connection diagram.
There are older style EIFM economizers and newer style ECONWMT economizers that the MC4000 controller system can work with, and also an option for a remote Ethernet communication board. Therefore, it is important to select the correct low voltage hook-up diagram. See Table 1 — Hook-Up Diagram Selection on Page 17.
SECURITY (LOCKING) FEATURE
The MC4000 controller can be locked such that unauthorized persons cannot make any changes to temperature set points or any other selectable parameters of the controller system.
The ON/OFF and Comfort buttons remain fully active for their normal intent. The Advance/Change/Save button remains active for the Advance feature only, which allows the position of the lead and lag air conditioners to be swapped (reversed). The Program button remains partially active - allowing the review of temperature sensor(s) actual reading of temperature, and the current settings/choices that have been chosen. However, no changes can be made when the controller is locked, and if the change button is pressed when in the Program mode, the display will come up showing “Locd” instead of flashing the selectable choices for that parameter. The default (DEF) reset capability is also disabled when the controller is in locked mode.
Locking and Unlocking the MC4000 Controller:
GENERATOR RUN FEATURE If desired, the MC4000 controller can be signaled from a standby generator system to lockout (disable operation) of the lag air conditioning system. This is sometimes mandated if the generator size is not sufficient to handle the building load (amperage) and that of both air conditioning systems. A normally closed (NC) dry contact as part of generator controls is required. These contacts must open when the generator is started, and such action will signal the MC4000 controller to this condition and disable lag air conditioner run function. A wire jumper is factory-installed across the G1 and G terminals or main controller board. To utilize the generator run feature, remove the jumper from G1 and G2, and connect the generator normally closed (NC) contacts that will open-on-run generator condition to the G1 and G2 terminals.
BACKUP DC POWER CONNECTION There are input connections available for -24VDC or -48VDC (-20 to -56V) backup power connection. Making this connection will maintain microprocessor operation, front panel display, LED signaling, and alarm relay operation during periods of commercial power outages and when no standby generator is available. This circuit is protected by a replaceable .5A (500mA) 250V fuse.
IMPORTANT: The shelter DC battery power must be connected to the controller and wired as shown in controller wiring diagrams. The backup DC power connection is polarity sensitive. If polarity is reversed, the controller will not function on backup power, no display and no alarm functions will be evident.
A/Cwith 1 - Stage Compressor
A/Cwith 2 - Stage Co mpressor WA^ S/WLS^2 4 6 8 10
He atPump WSHH //WS****HH 1 3 14 N/ A N/ A N/ A N/A
TABLE 1 HOOK-UP DIAGRAM SELECTION TABLE — REFERENCE FIGURE 1 SHOWN
FIGURE 1 CONTROLLER CONNECTIONS 1-STAGE (WA/WL, WA/WL SERIES) AIR CONDITIONERS – NO ECONOMIZER
FIGURE 3 CONTROLLER CONNECTIONS 1-STAGE (WA/WL, WA/WL SERIES) AIR CONDITIONERS – NO ECONOMIZER WITH ALARM BOARD & CB4000 COMMUNICATION BOARD
FIGURE 4 CONTROLLER CONNECTIONS 2-STAGE (WAS/WLS SERIES) AIR CONDITIONERS – NO ECONOMIZERS WITH ALARM BOARD & CB4000 COMMUNICATION BOARD