
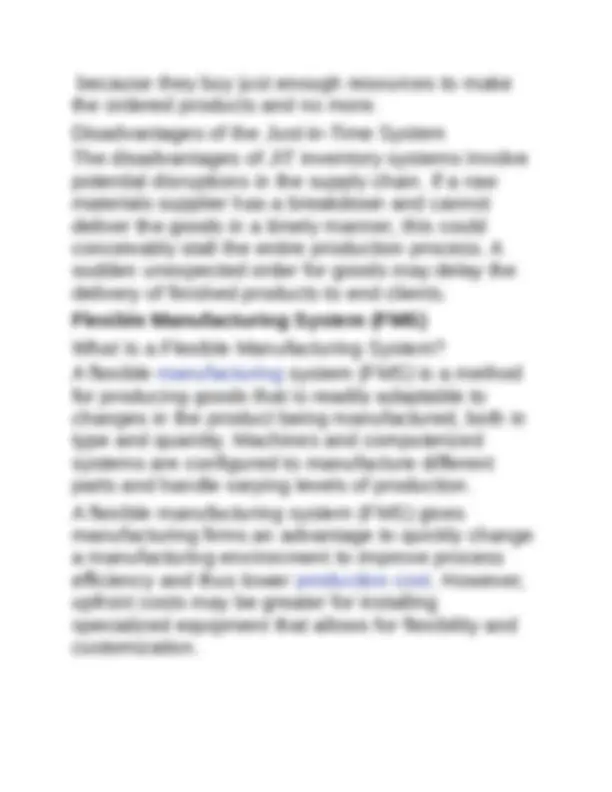
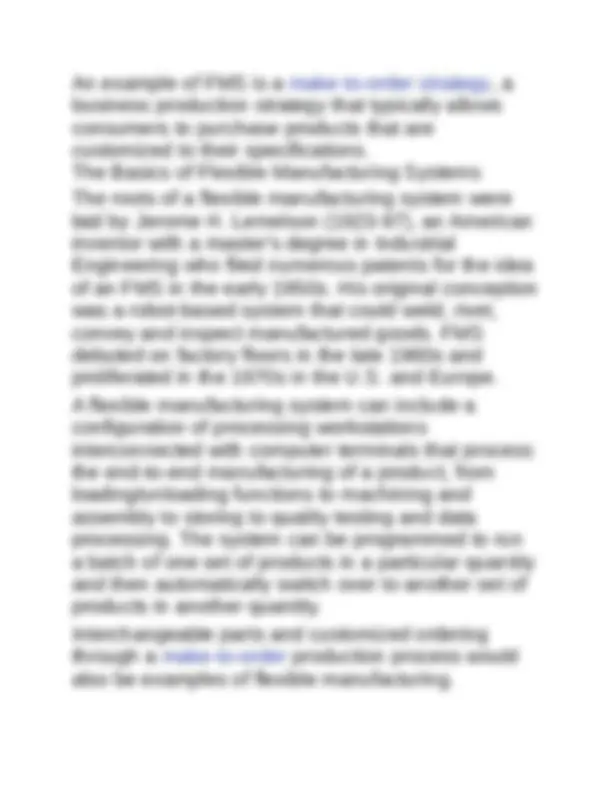
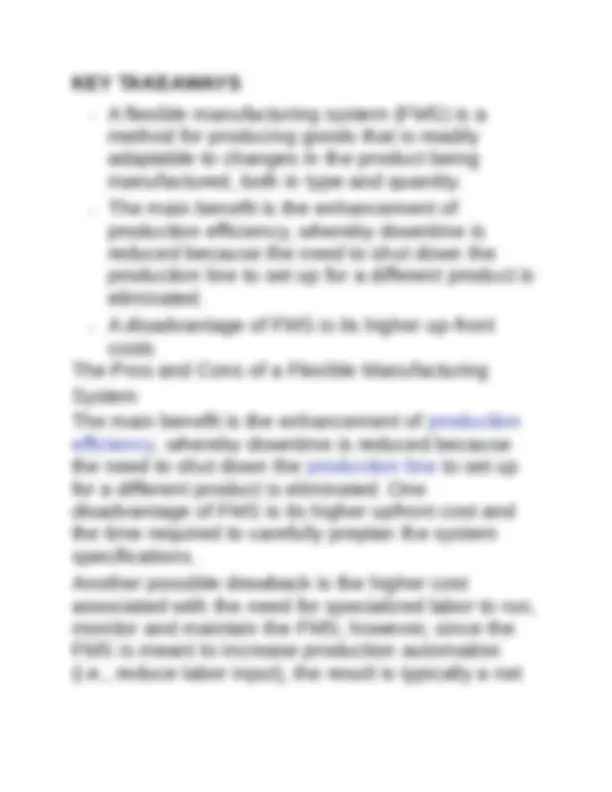
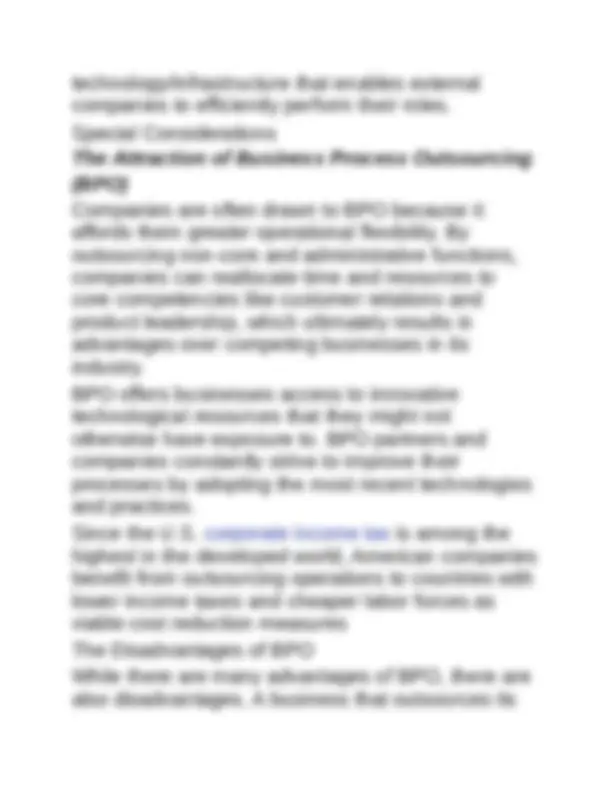
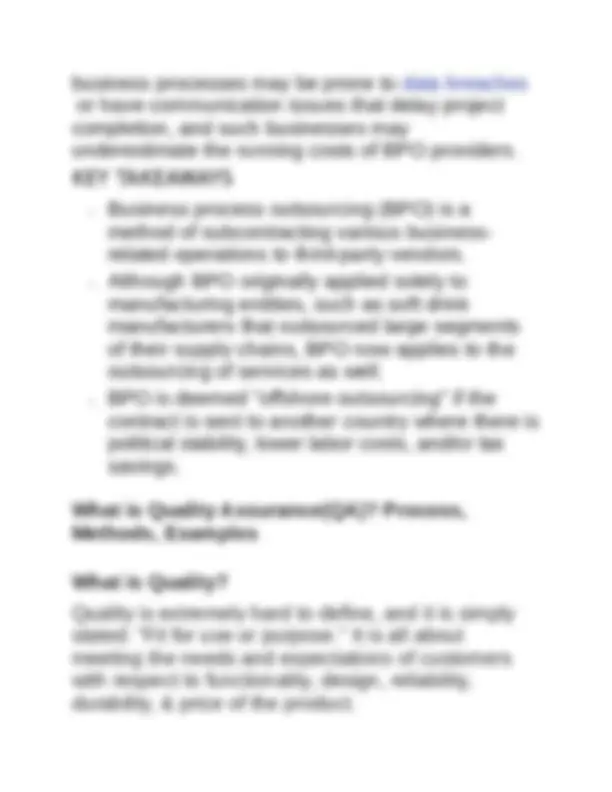
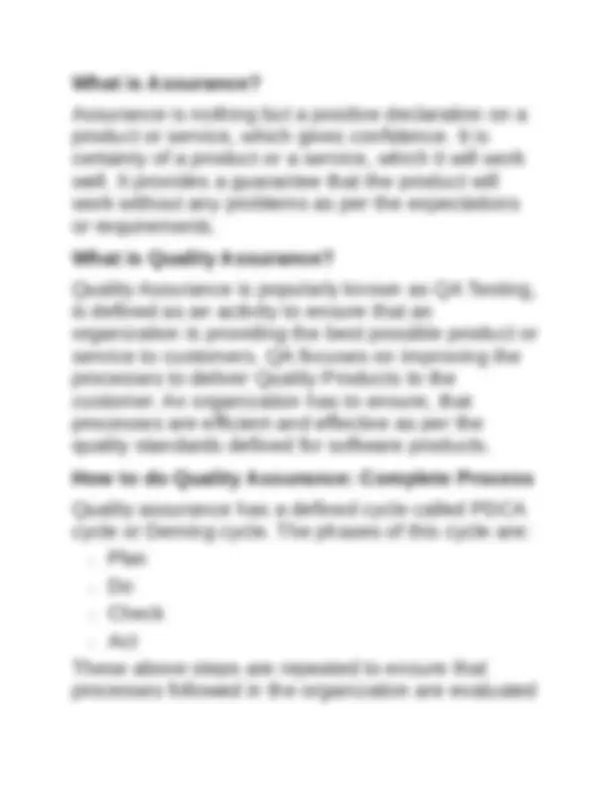
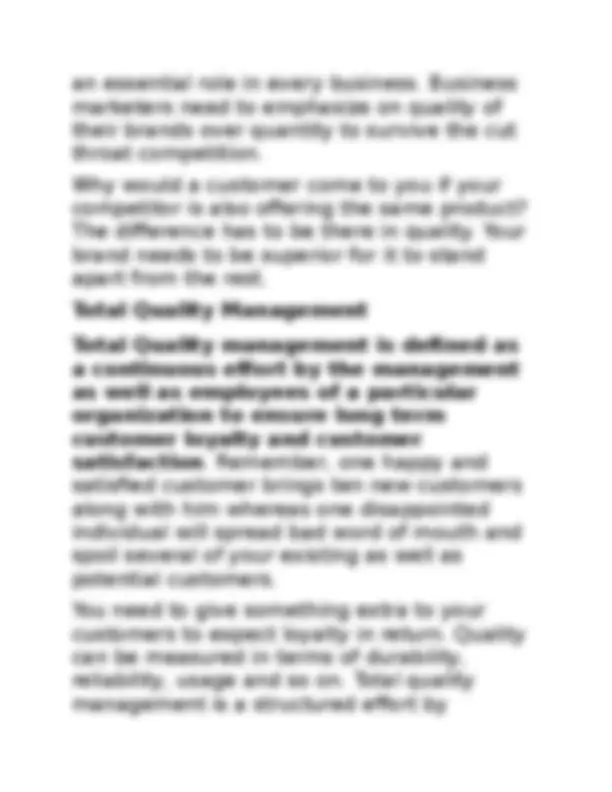
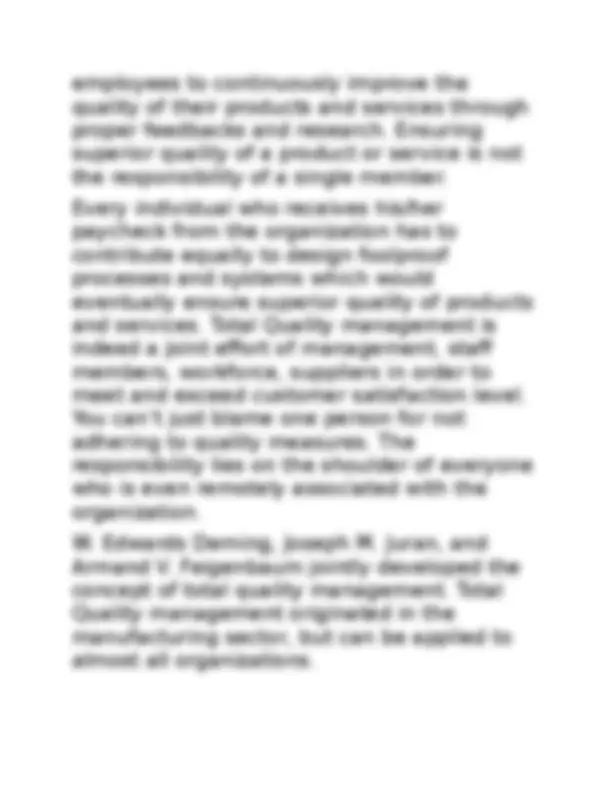
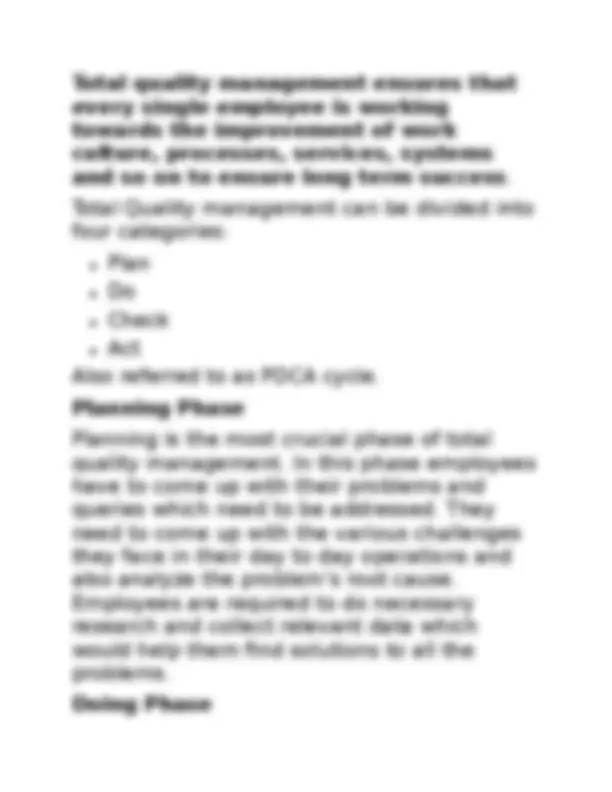
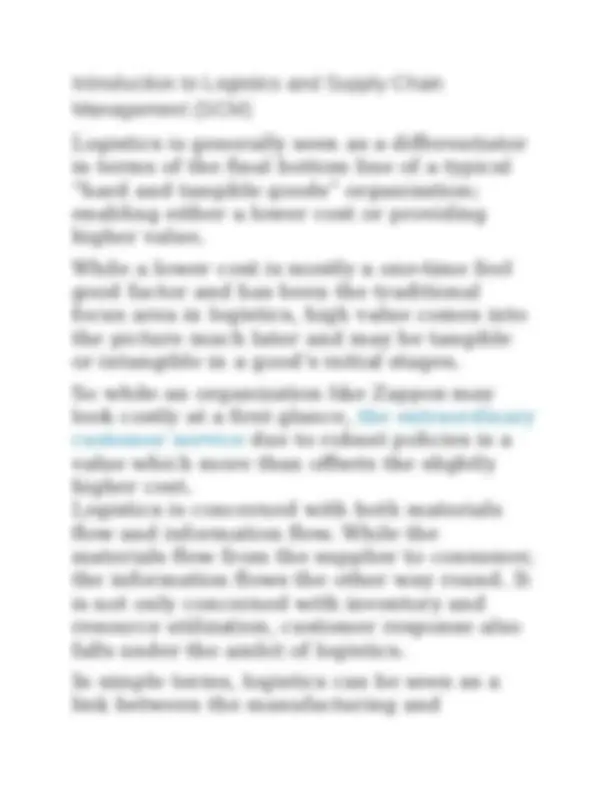
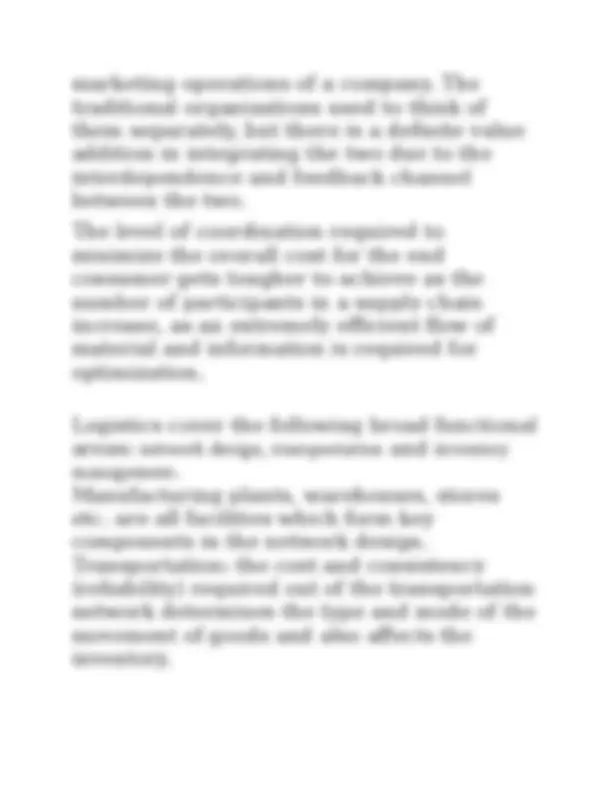
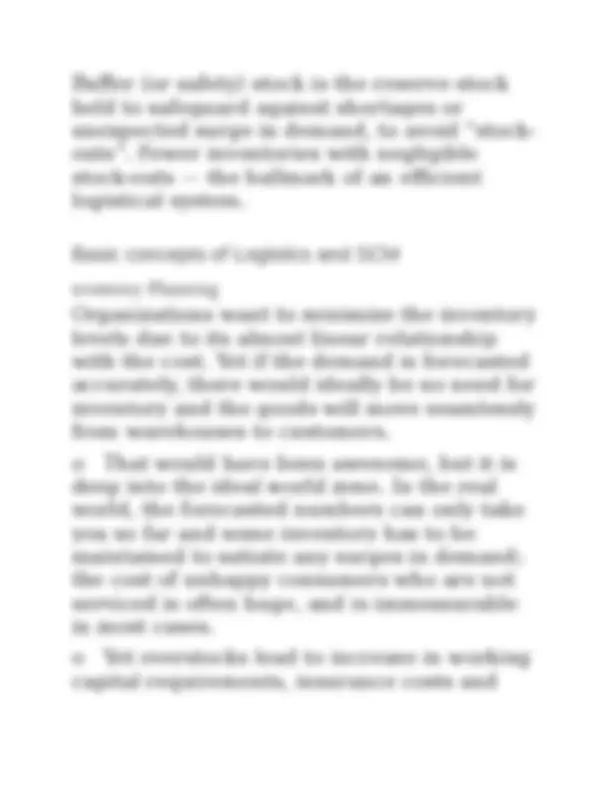
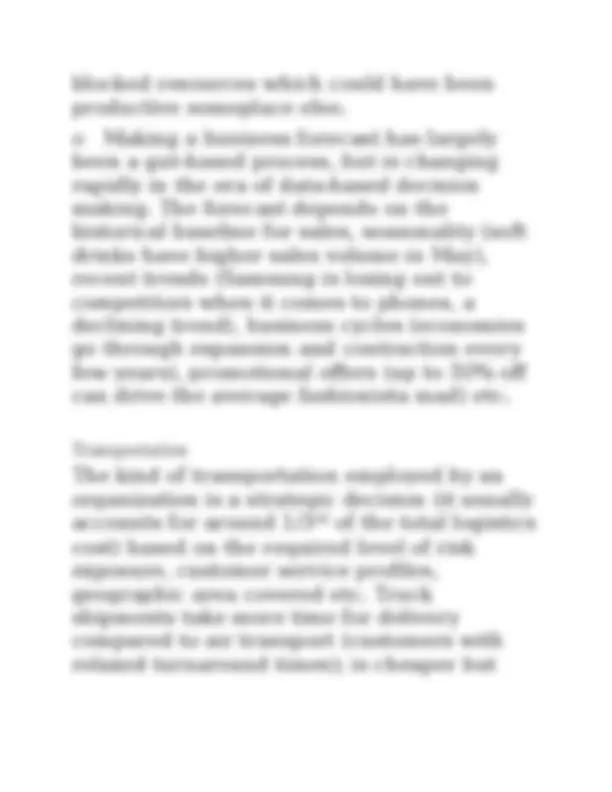

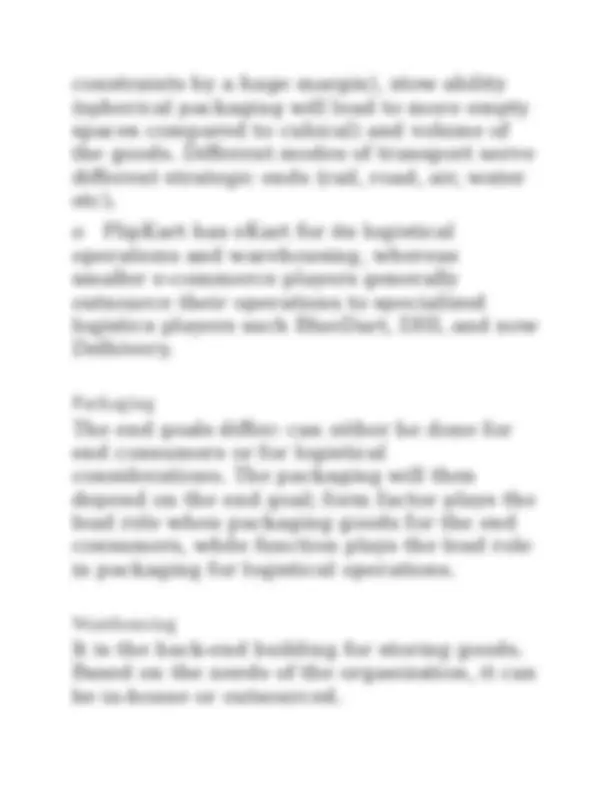
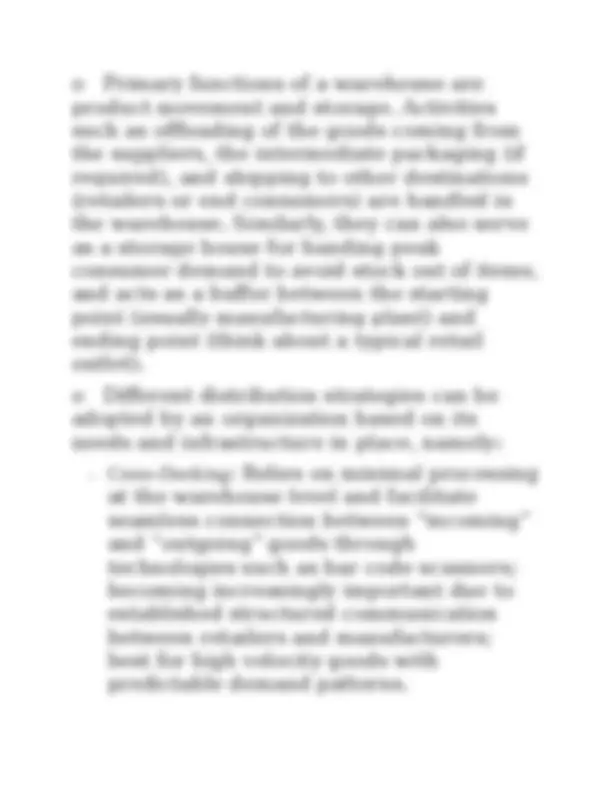
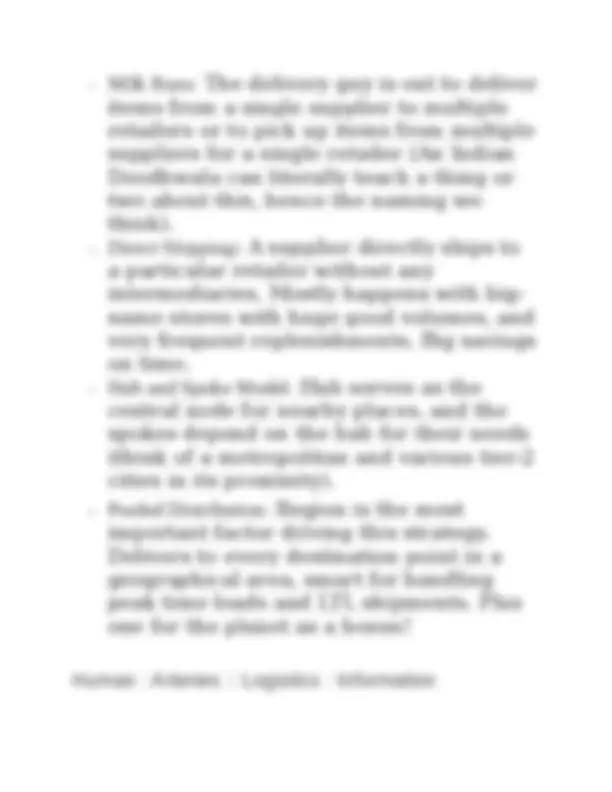
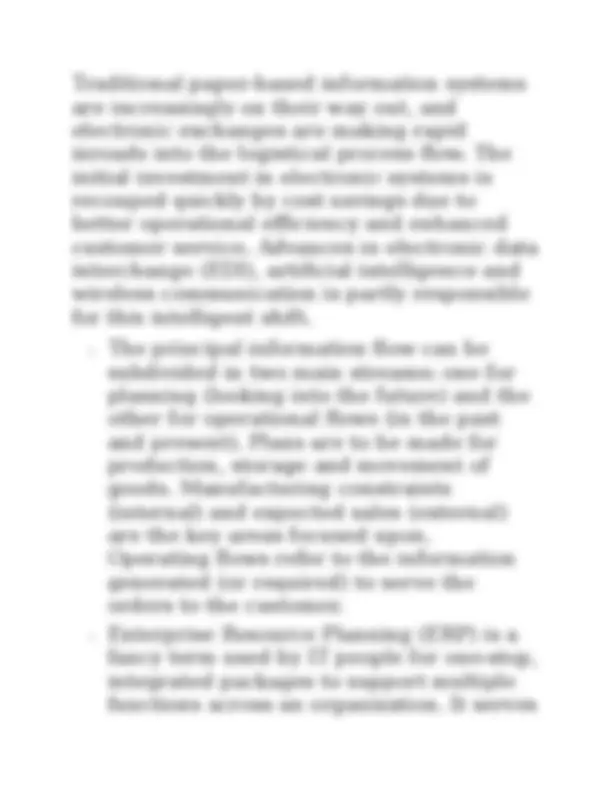
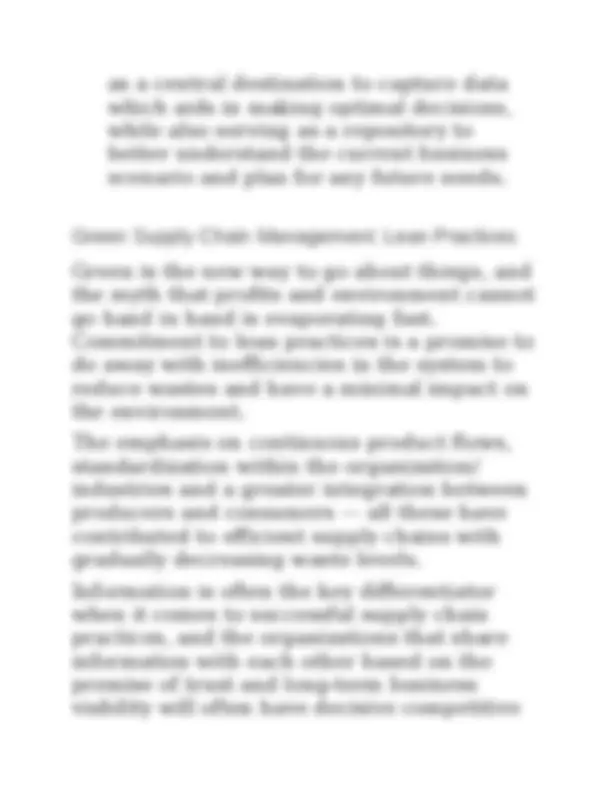
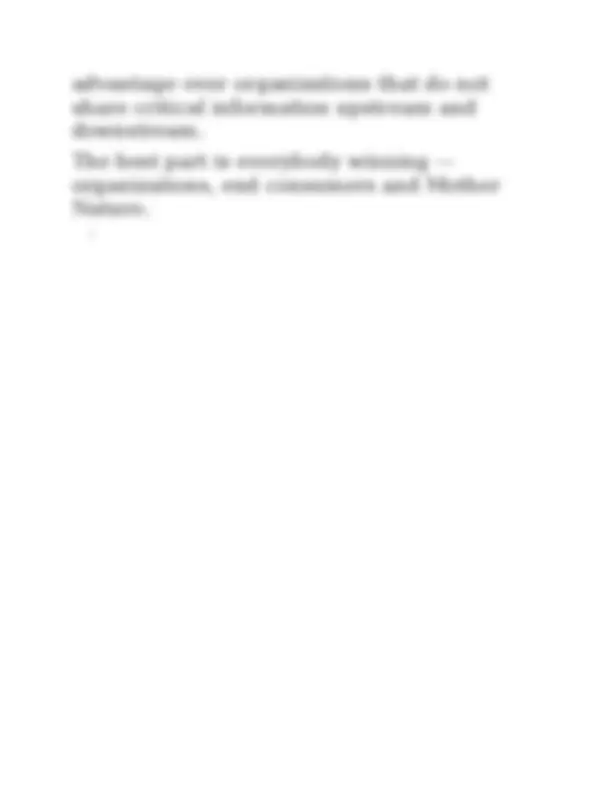
Study with the several resources on Docsity
Earn points by helping other students or get them with a premium plan
Prepare for your exams
Study with the several resources on Docsity
Earn points to download
Earn points by helping other students or get them with a premium plan
Community
Ask the community for help and clear up your study doubts
Discover the best universities in your country according to Docsity users
Free resources
Download our free guides on studying techniques, anxiety management strategies, and thesis advice from Docsity tutors
just in time for theory purpose
Typology: Lecture notes
1 / 28
This page cannot be seen from the preview
Don't miss anything!
Just in Time (JIT)
What Is Just in Time (JIT)?
The just-in-time (JIT) inventory system is a management strategy that aligns raw-material orders from suppliers directly with production schedules. Companies employ this inventory strategy to increase efficiency and decrease waste by receiving goods only as they need them for the production process, which reduces inventory costs. This method requires producers to forecast demand accurately.
The JIT inventory system contrasts with just-in- case strategies, wherein producers hold sufficient inventories to have enough product to absorb maximum market demand.
KEY TAKEAWAYS
One example of a JIT inventory system is a car manufacturer that operates with low inventory levels but heavily relies on its supply chain to deliver the parts it requires to build cars, on an as-needed basis. Consequently, the manufacturer orders the parts required to assemble the cars, only after an order is received.
For JIT manufacturing to succeed, companies must have steady production, high-quality workmanship, glitch-free plant machinery, and reliable suppliers.
JIT production systems cut inventory costs because manufacturers do not have to pay storage costs. Manufacturers are also not left with unwanted inventory if an order is canceled or not fulfilled. Just-in-Time (JIT) Inventory System Advantages
JIT inventory systems have several advantages over traditional models. Production runs are short, which means that manufacturers can quickly move from one product to another. Furthermore, this method reduces costs by minimizing warehouse needs. Companies also spend less money on raw materials
An example of FMS is a make-to-order strategy, a business production strategy that typically allows consumers to purchase products that are customized to their specifications. The Basics of Flexible Manufacturing Systems
The roots of a flexible manufacturing system were laid by Jerome H. Lemelson (1923-97), an American inventor with a master's degree in Industrial Engineering who filed numerous patents for the idea of an FMS in the early 1950s. His original conception was a robot-based system that could weld, rivet, convey and inspect manufactured goods. FMS debuted on factory floors in the late 1960s and proliferated in the 1970s in the U.S. and Europe.
A flexible manufacturing system can include a configuration of processing workstations interconnected with computer terminals that process the end-to-end manufacturing of a product, from loading/unloading functions to machining and assembly to storing to quality testing and data processing. The system can be programmed to run a batch of one set of products in a particular quantity and then automatically switch over to another set of products in another quantity.
Interchangeable parts and customized ordering through a make-to-order production process would also be examples of flexible manufacturing.
System
The main benefit is the enhancement of production efficiency, whereby downtime is reduced because the need to shut down the production line to set up for a different product is eliminated. One disadvantage of FMS is its higher upfront cost and the time required to carefully preplan the system specifications.
Another possible drawback is the higher cost associated with the need for specialized labor to run, monitor and maintain the FMS; however, since the FMS is meant to increase production automation (i.e., reduce labor input), the result is typically a net
By contrast, front office BPO tasks commonly include customer-related services such as tech support, sales, and marketing.
[Important: Business process outsourcing is on the climb, evidenced by the fact that in 2017, the estimated global market size of outsourced services was 88.9 billion U.S. dollars, which was up $ billion from the previous year.]
The breadth of a business' BPO options depends on whether it contracts its operations within or outside the borders of its home country. BPO is deemed "offshore outsourcing" if the contract is sent to another country where there is political stability, lower labor costs, and/or tax savings. A U.S. company using an offshore BPO vendor in Singapore is one such example of offshore outsourcing.
BPO is referred to as "nearshore outsourcing" if the job is contracted to a neighboring country. Such would be the case if a U.S. company partnered with a BPO vendor located in Canada.
A third option, known as "onshore outsourcing" or "domestic sourcing," occurs when BPO is contracted within the companyās own country, even if its vendor partners are located in different cities or states.
BPO is often referred to as information technology- enabled services (ITES) because it relies on
technology/infrastructure that enables external companies to efficiently perform their roles.
Special Considerations
The Attraction of Business Process Outsourcing
(BPO)
Companies are often drawn to BPO because it affords them greater operational flexibility. By outsourcing non-core and administrative functions, companies can reallocate time and resources to core competencies like customer relations and product leadership, which ultimately results in advantages over competing businesses in its industry.
BPO offers businesses access to innovative technological resources that they might not otherwise have exposure to. BPO partners and companies constantly strive to improve their processes by adopting the most recent technologies and practices.
Since the U.S. corporate income tax is among the highest in the developed world, American companies benefit from outsourcing operations to countries with lower income taxes and cheaper labor forces as viable cost reduction measures
The Disadvantages of BPO
While there are many advantages of BPO, there are also disadvantages. A business that outsources its
What is Assurance?
Assurance is nothing but a positive declaration on a product or service, which gives confidence. It is certainty of a product or a service, which it will work well. It provides a guarantee that the product will work without any problems as per the expectations or requirements.
What is Quality Assurance?
Quality Assurance is popularly known as QA Testing, is defined as an activity to ensure that an organization is providing the best possible product or service to customers. QA focuses on improving the processes to deliver Quality Products to the customer. An organization has to ensure, that processes are efficient and effective as per the quality standards defined for software products.
How to do Quality Assurance: Complete Process
Quality assurance has a defined cycle called PDCA cycle or Deming cycle. The phases of this cycle are:
These above steps are repeated to ensure that processes followed in the organization are evaluated
and improved on a periodic basis. Let's look into the above steps in detail -
An organization must use Quality Assurance to ensure that the product is designed and implemented with correct procedures. This helps reduce problems and errors, in the final product.
Quality control popularly abbreviated as QC. It is a Software Engineering process used to ensure quality in a product or a service. It does not deal with the processes used to create a product; rather it examines the quality of the "end products" and the final outcome.
The main aim of Quality control is to check whether the products meet the specifications and requirements of the customer. If an issue or problem
an essential role in every business. Business marketers need to emphasize on quality of their brands over quantity to survive the cut throat competition.
Why would a customer come to you if your competitor is also offering the same product? The difference has to be there in quality. Your brand needs to be superior for it to stand apart from the rest.
Total Quality Management
Total Quality management is defined as a continuous effort by the management as well as employees of a particular organization to ensure long term customer loyalty and customer satisfaction. Remember, one happy and satisfied customer brings ten new customers along with him whereas one disappointed individual will spread bad word of mouth and spoil several of your existing as well as potential customers.
You need to give something extra to your customers to expect loyalty in return. Quality can be measured in terms of durability, reliability, usage and so on. Total quality management is a structured effort by
employees to continuously improve the quality of their products and services through proper feedbacks and research. Ensuring superior quality of a product or service is not the responsibility of a single member.
Every individual who receives his/her paycheck from the organization has to contribute equally to design foolproof processes and systems which would eventually ensure superior quality of products and services. Total Quality management is indeed a joint effort of management, staff members, workforce, suppliers in order to meet and exceed customer satisfaction level. You canāt just blame one person for not adhering to quality measures. The responsibility lies on the shoulder of everyone who is even remotely associated with the organization.
W. Edwards Deming, Joseph M. Juran, and Armand V. Feigenbaum jointly developed the concept of total quality management. Total Quality management originated in the manufacturing sector, but can be applied to almost all organizations.
In the doing phase, employees develop a solution for the problems defined in planning phase. Strategies are devised and implemented to overcome the challenges faced by employees. The effectiveness of solutions and strategies is also measured in this stage.
Checking Phase
Checking phase is the stage where people actually do a comparison analysis of before and after data to confirm the effectiveness of the processes and measure the results
Acting Phase
In this phase employees document their results and prepare themselves to address other problems
Introduction to Logistics and Supply Chain Management
The term āSupply Chain Managementā was coined in 1982 by Keith Oliver of Booz, Allen and Hamilton Inc. But the discipline and practice has been in existence for centuries.
The terms Logistics and Supply Chain Management are used interchangeably these days, but there is a subtle difference that exists between the two.
āLogisticsā has a military origin, and used to be associated with the movement of troops and their supplies in the battlefield. But like so many other technologies and terminologies, it entered into the business lexicon gradually and has now become synonymous with the set of activities ranging from procurement of raw materials, to the delivery of the final polished good to the end consumer.
In a typical business scenario, many organizations work in tandem (knowingly or unknowingly) to get the final product in hand of the end consumer. The supply chain is a network of these organizations that coalesce with each other (downstream or upstream) to make the final shipment successful.
A group of farmers, a cotton mill, a designer and a tailor is the least number of stakeholders you can expect from a regular shirt you wear every day.
marketing operations of a company. The traditional organizations used to think of them separately, but there is a definite value addition in integrating the two due to the interdependence and feedback channel between the two.
The level of coordination required to minimize the overall cost for the end consumer gets tougher to achieve as the number of participants in a supply chain increase, as an extremely efficient flow of material and information is required for optimization.
Logistics cover the following broad functional areas: network design, transportation and inventory management. Manufacturing plants, warehouses, stores etc. are all facilities which form key components in the network design. Transportation: the cost and consistency (reliability) required out of the transportation network determines the type and mode of the movement of goods and also affects the inventory.
Buffer (or safety) stock is the reserve stock held to safeguard against shortages or unexpected surge in demand, to avoid āstock- outsā. Fewer inventories with negligible stock-outs ā the hallmark of an efficient logistical system.
Basic concepts of Logistics and SCM
nventory Planning
Organizations want to minimize the inventory levels due to its almost linear relationship with the cost. Yet if the demand is forecasted accurately, there would ideally be no need for inventory and the goods will move seamlessly from warehouses to customers.
o That would have been awesome, but it is deep into the ideal world zone. In the real world, the forecasted numbers can only take you so far and some inventory has to be maintained to satiate any surges in demand; the cost of unhappy consumers who are not serviced is often huge, and is immeasurable in most cases.
o Yet overstocks lead to increase in working capital requirements, insurance costs and