
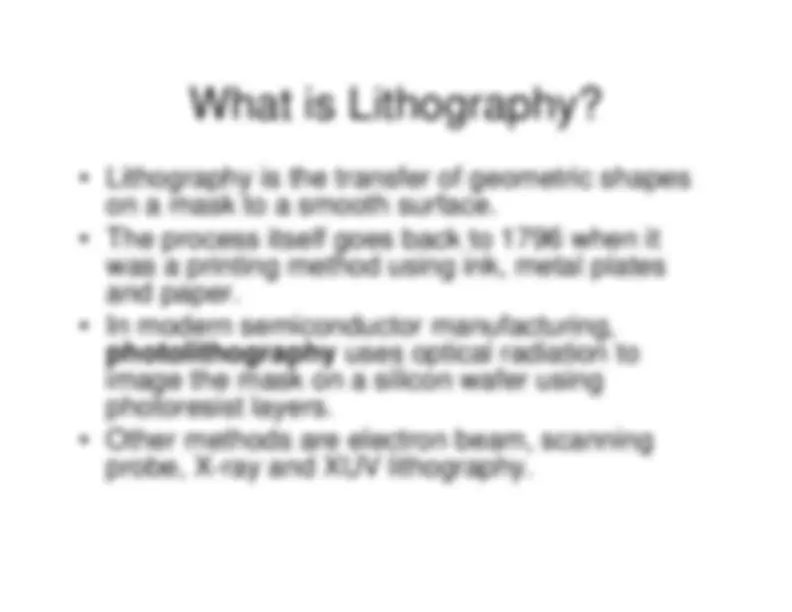
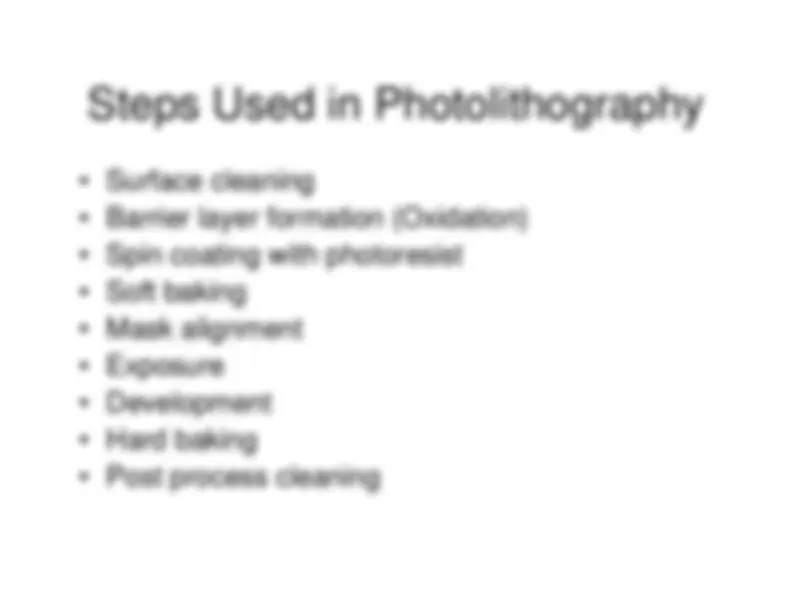
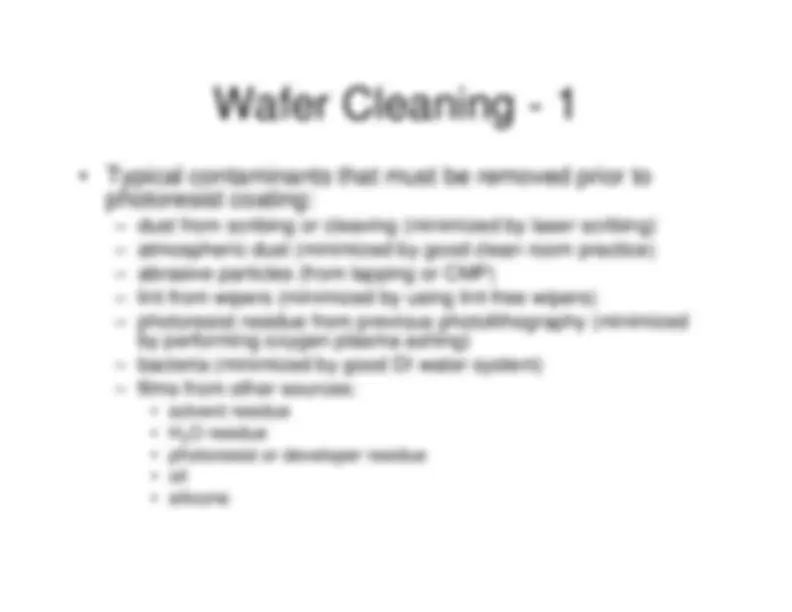
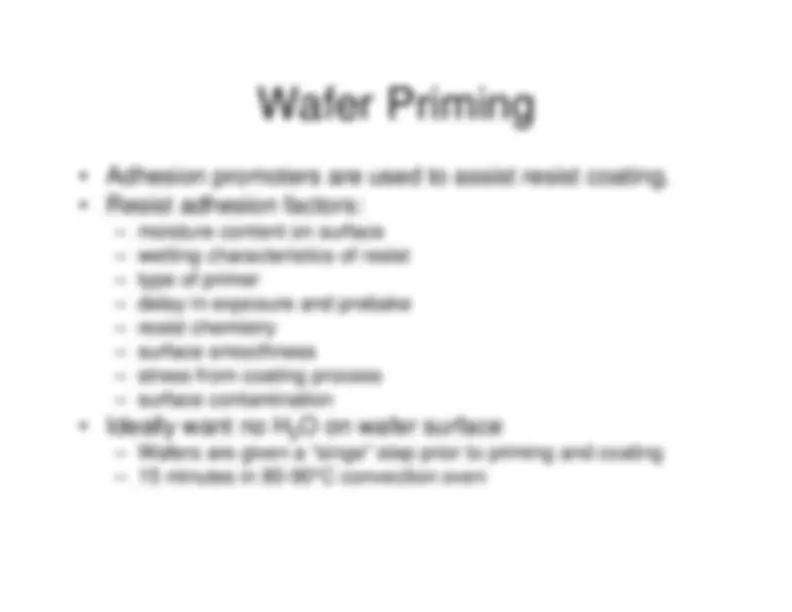
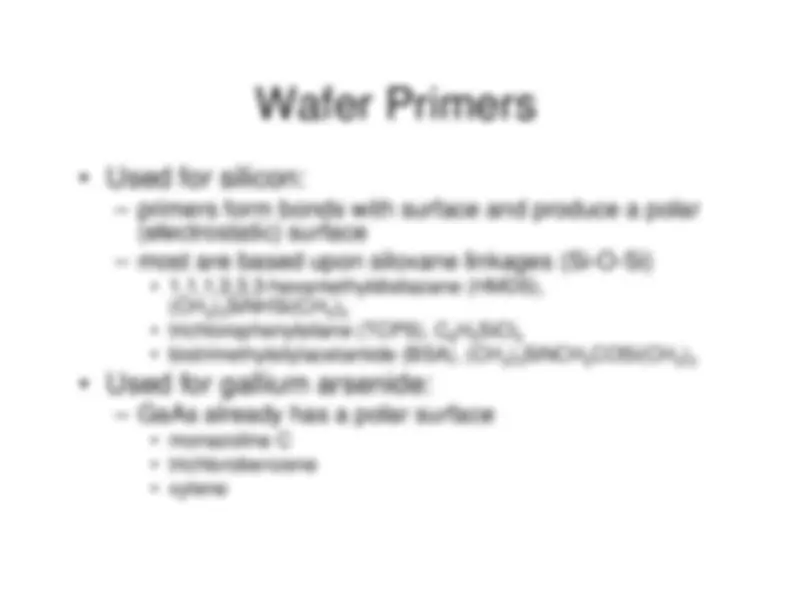
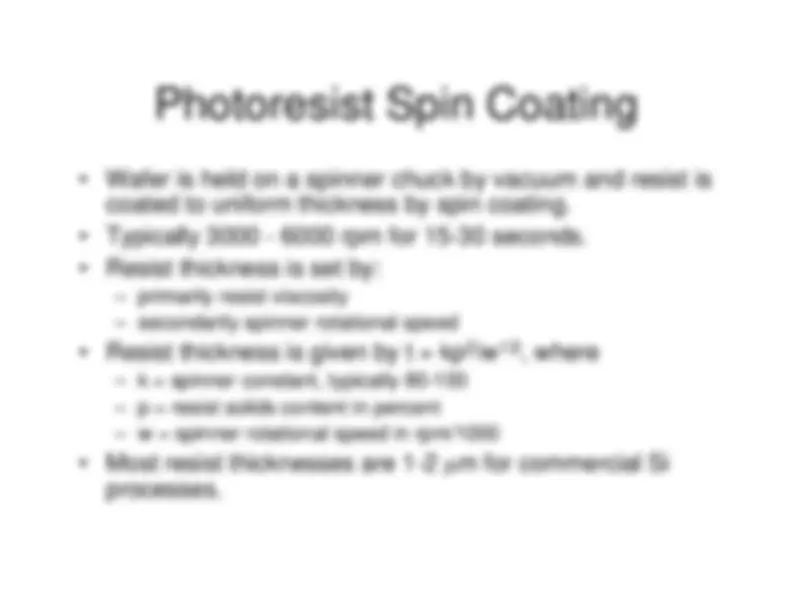
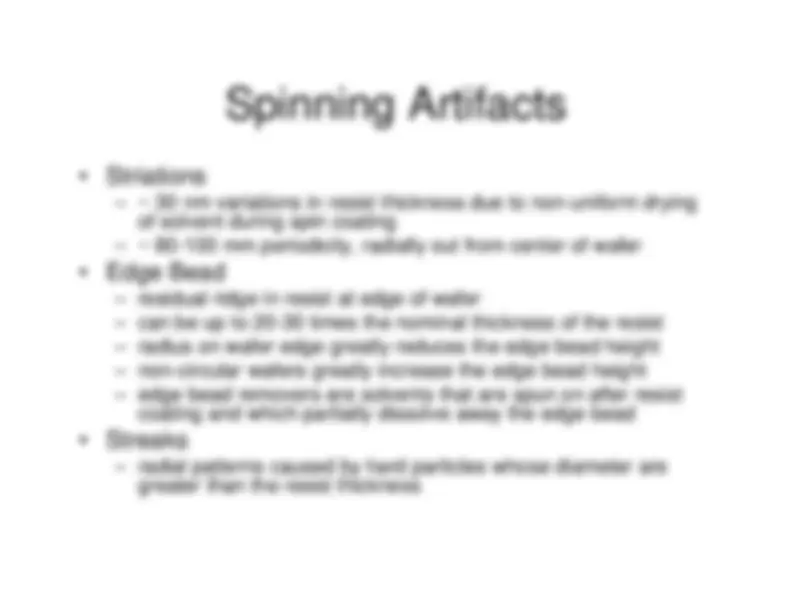
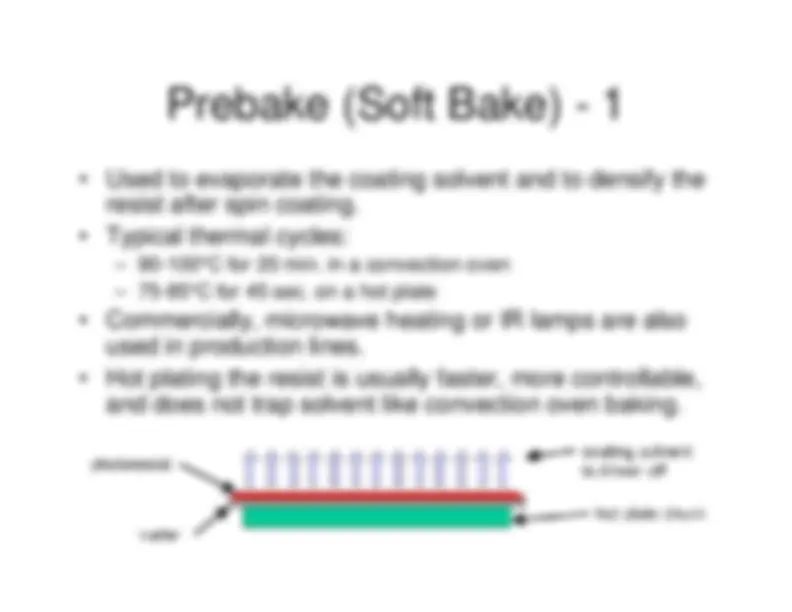
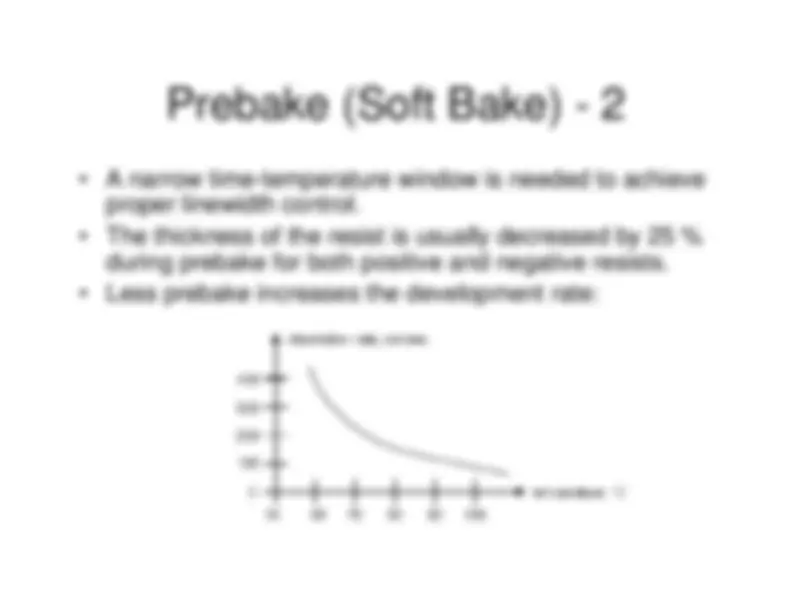
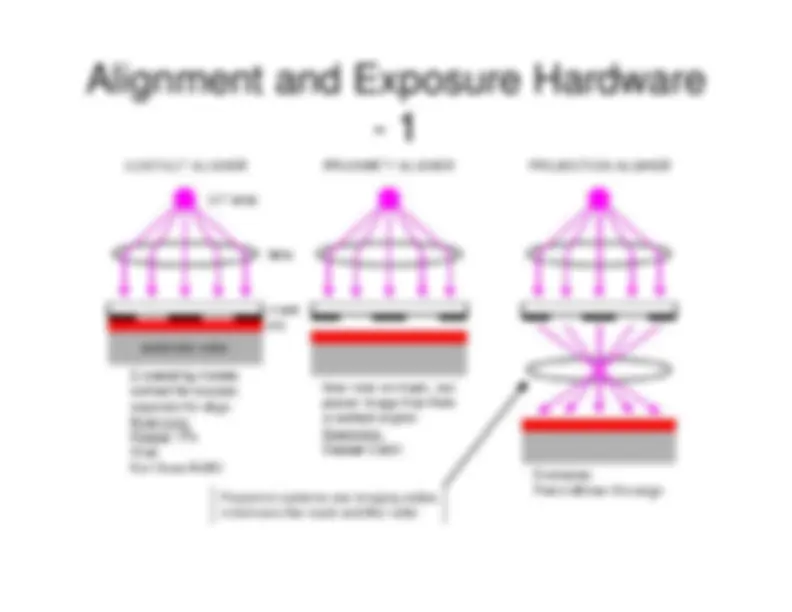
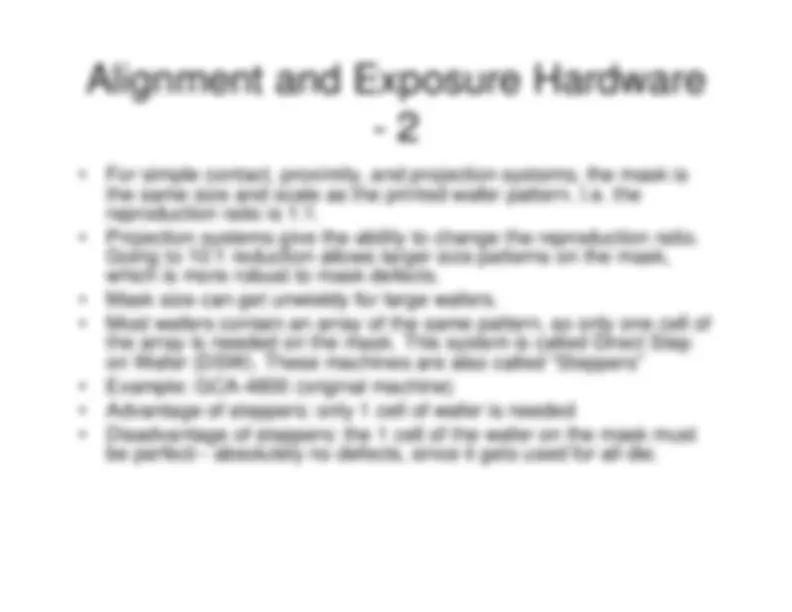
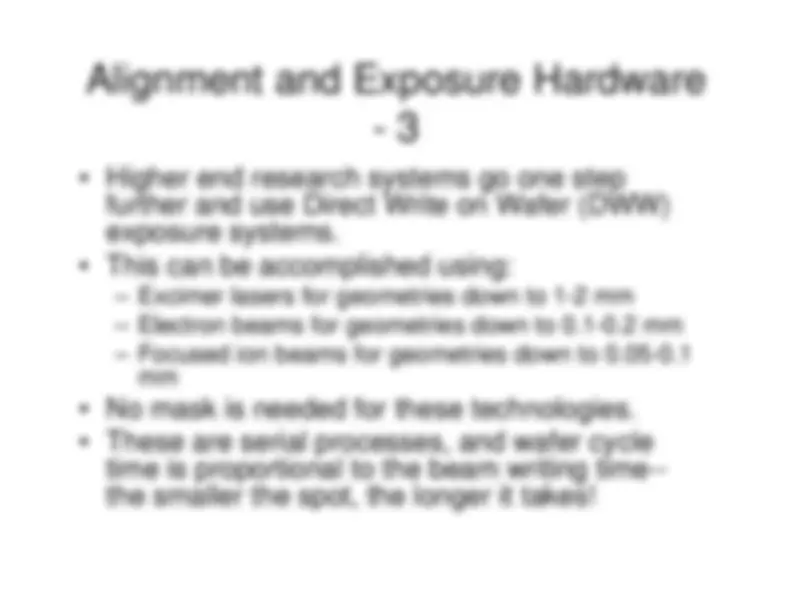
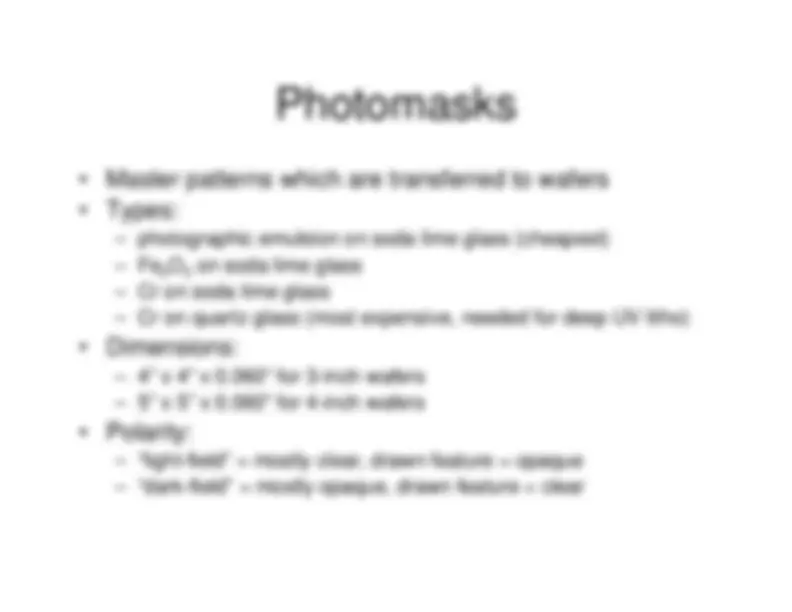
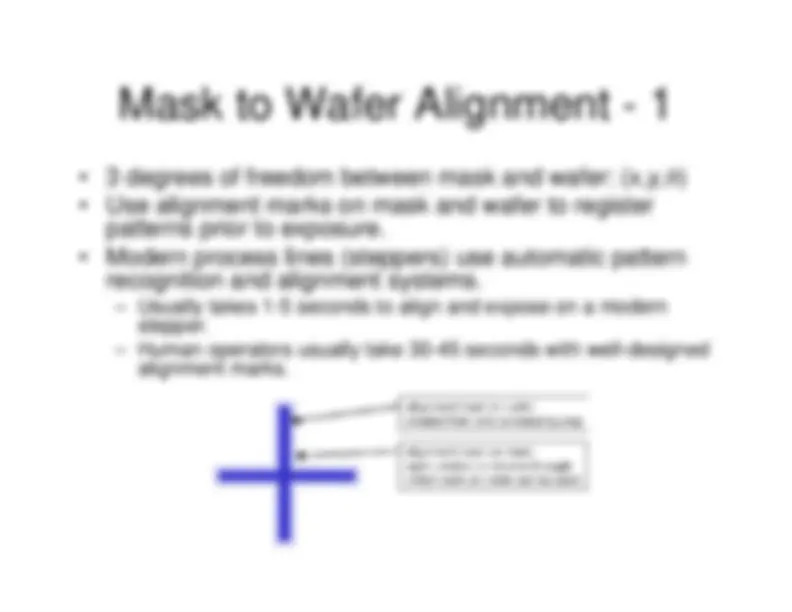
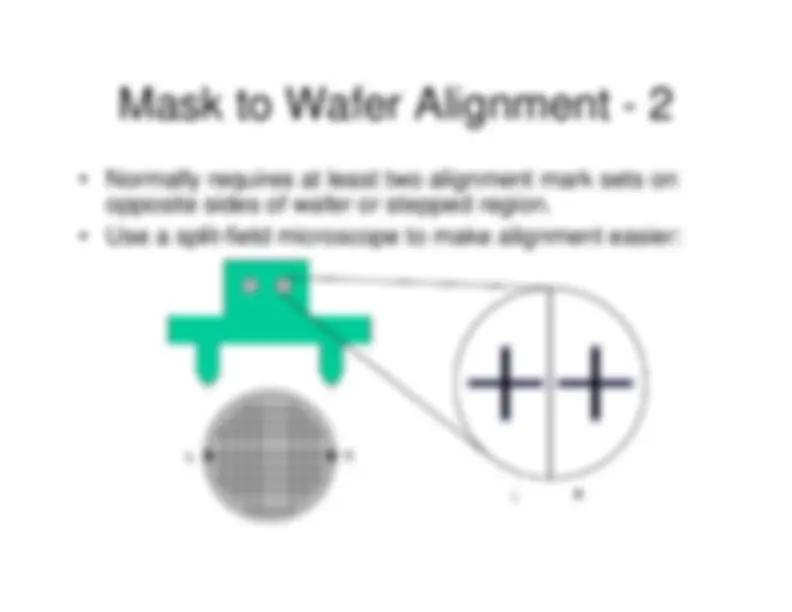
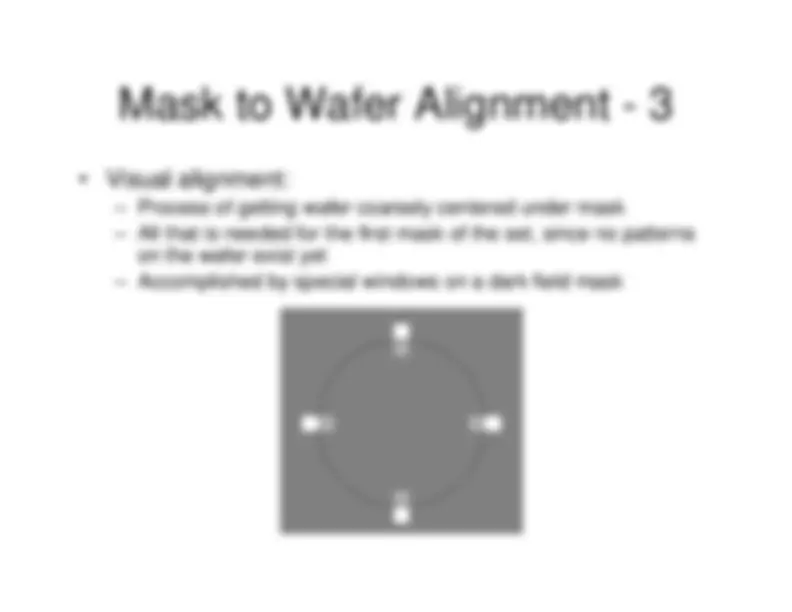
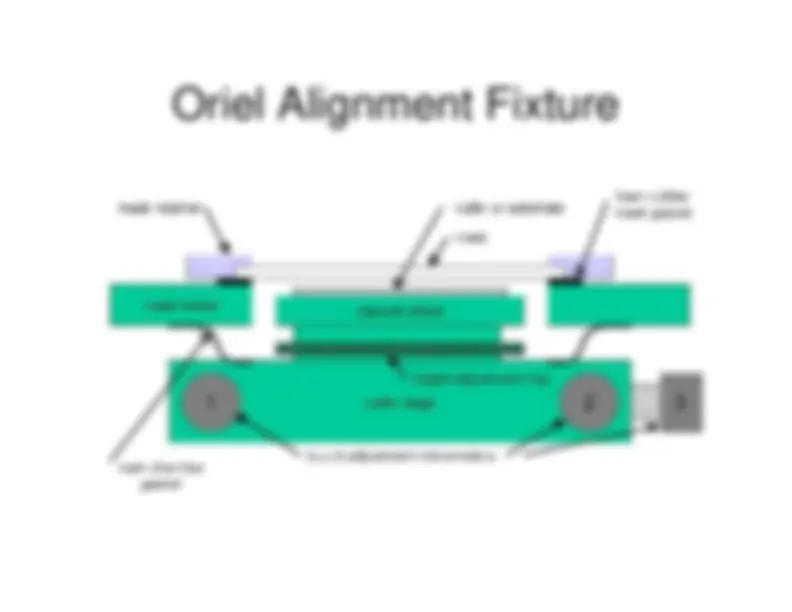
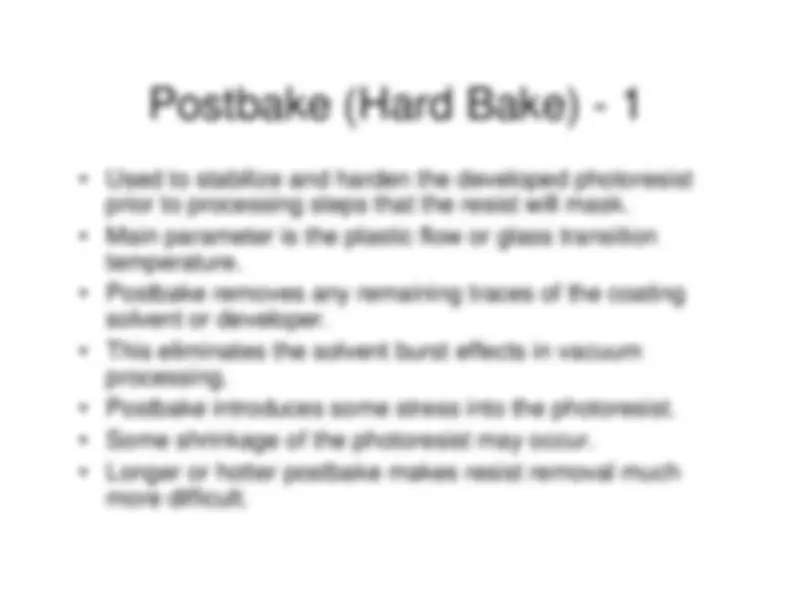
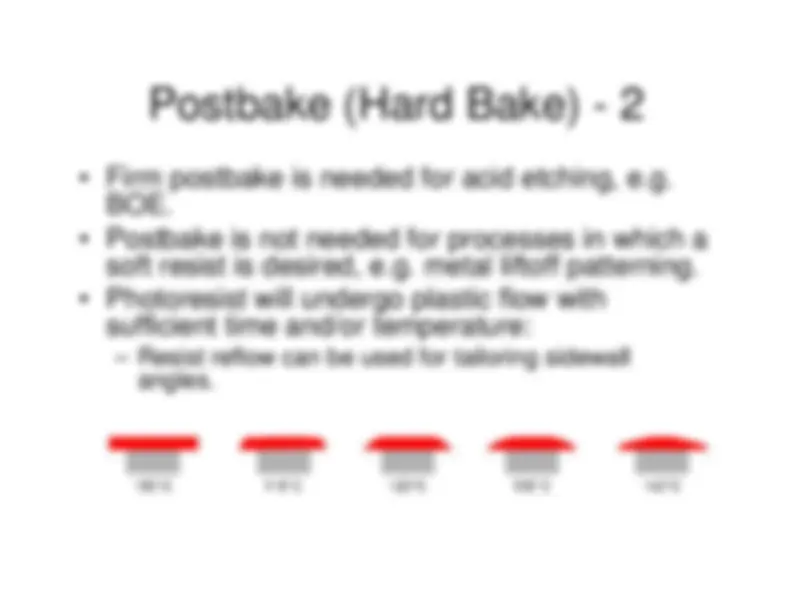
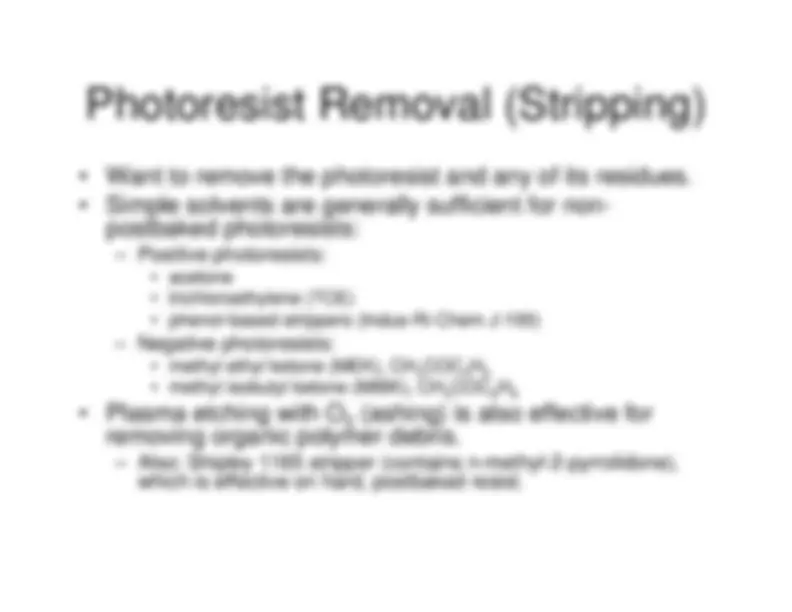
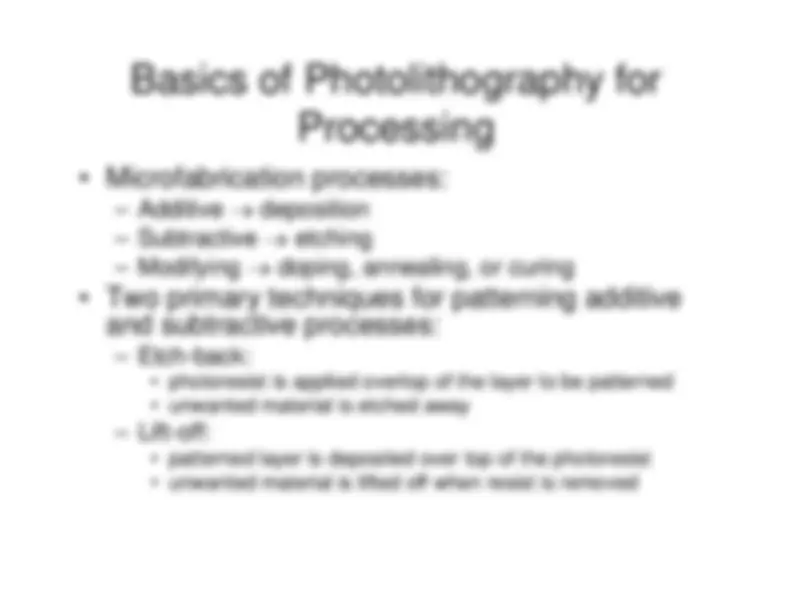
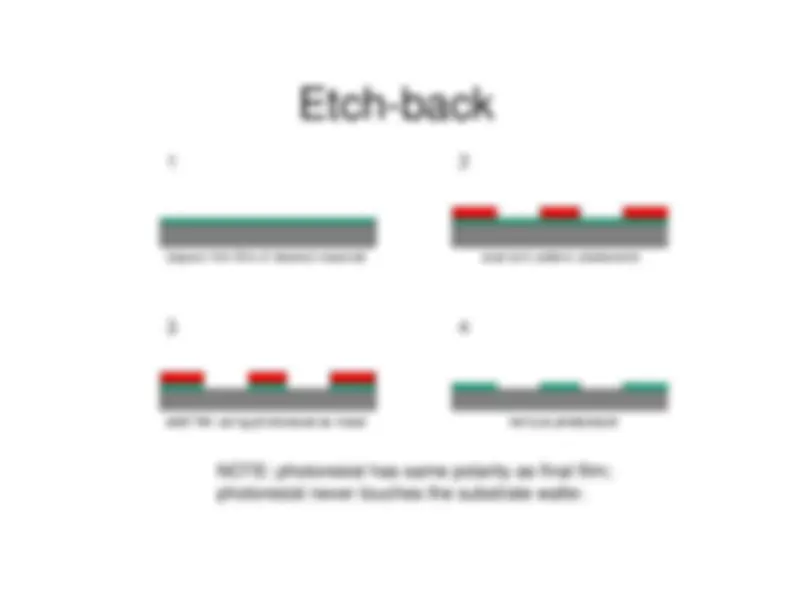
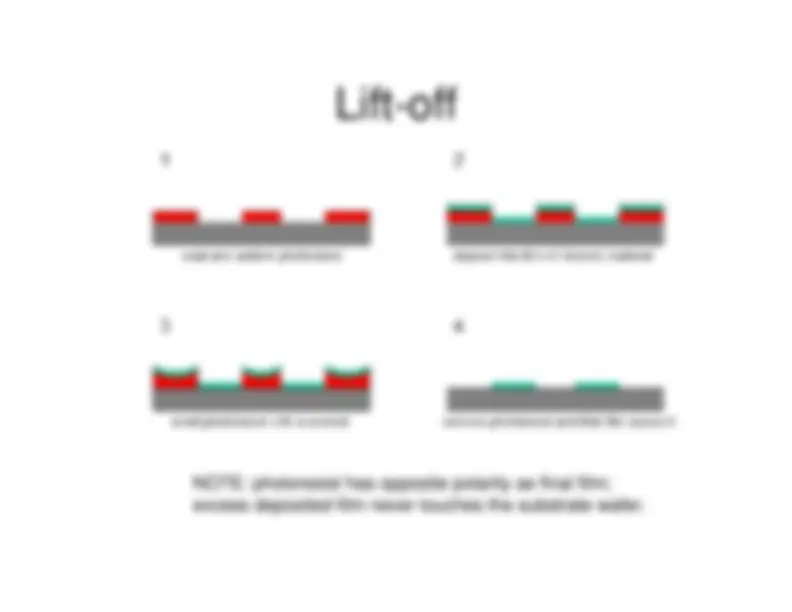
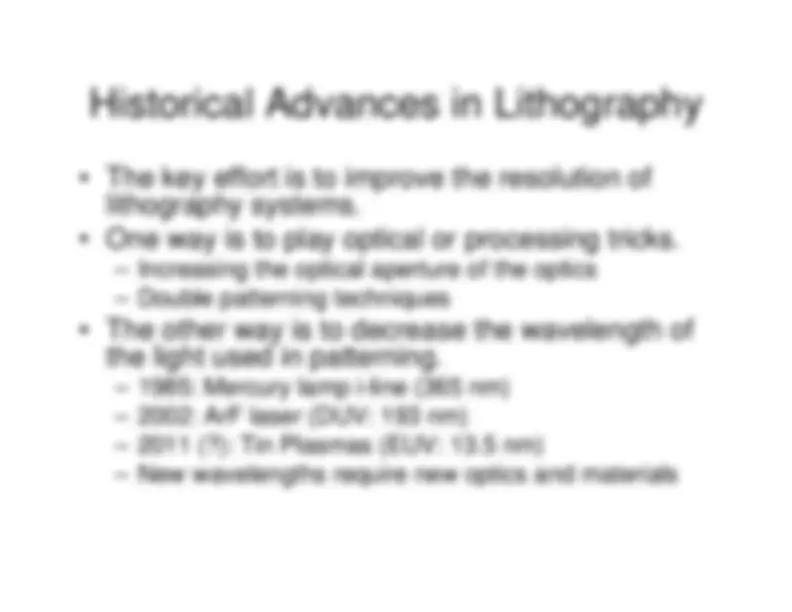
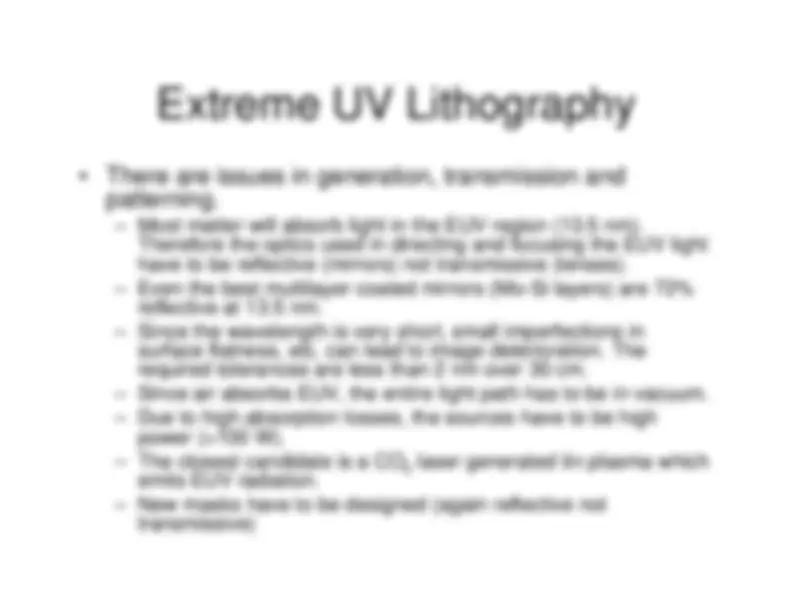
Study with the several resources on Docsity
Earn points by helping other students or get them with a premium plan
Prepare for your exams
Study with the several resources on Docsity
Earn points to download
Earn points by helping other students or get them with a premium plan
Community
Ask the community for help and clear up your study doubts
Discover the best universities in your country according to Docsity users
Free resources
Download our free guides on studying techniques, anxiety management strategies, and thesis advice from Docsity tutors
photolitography is one of the most important part of vlsi ic desing process
Typology: Lecture notes
1 / 33
This page cannot be seen from the preview
Don't miss anything!
A MOSFET Device The MOSFET as patterned on a wafer
dust from scribing or cleaving (minimized by laser scribing)
atmospheric dust (minimized by good clean room practice) - abrasive particles (from lapping or CMP) - lint from wipers (minimized by using lint-free wipers) - photoresist residue from previous photolithography (minimizedby performing oxygen plasma ashing) - bacteria (minimized by good DI water system) - films from other sources: - solvent residue - H 2 O residue - photoresist or developer residue - oil - silicone
4
2
2
2
2
2
2
2
2
2
moisture content on surface
wetting characteristics of resist - type of primer - delay in exposure and prebake - resist chemistry - surface smoothness - stress from coating process - surface contamination
2
Wafers are given a “singe” step prior to priming and coating
15 minutes in 80-90°C convection oven
primarily resist viscosity
secondarily spinner rotational speed
2
1/
k = spinner constant, typically 80-
p = resist solids content in percent - w = spinner rotational speed in rpm/
~ 30 nm variations in resist thickness due to non-uniform dryingof solvent during spin coating
~ 80-100 mm periodicity, radially out from center of wafer
residual ridge in resist at edge of wafer
can be up to 20-30 times the nominal thickness of the resist - radius on wafer edge greatly reduces the edge bead height - non-circular wafers greatly increase the edge bead height - edge bead removers are solvents that are spun on after resistcoating and which partially dissolve away the edge bead
radial patterns caused by hard particles whose diameter aregreater than the resist thickness
90-100°C for 20 min. in a convection oven
75-85°C for 45 sec. on a hot plate
Overview of Align/Expose/Develop Steps
Alignment and Exposure Hardware
Alignment and Exposure Hardware
No mask is needed for these technologies. - These are serial processes, and wafer cycletime is proportional to the beam writing time--the smaller the spot, the longer it takes!