
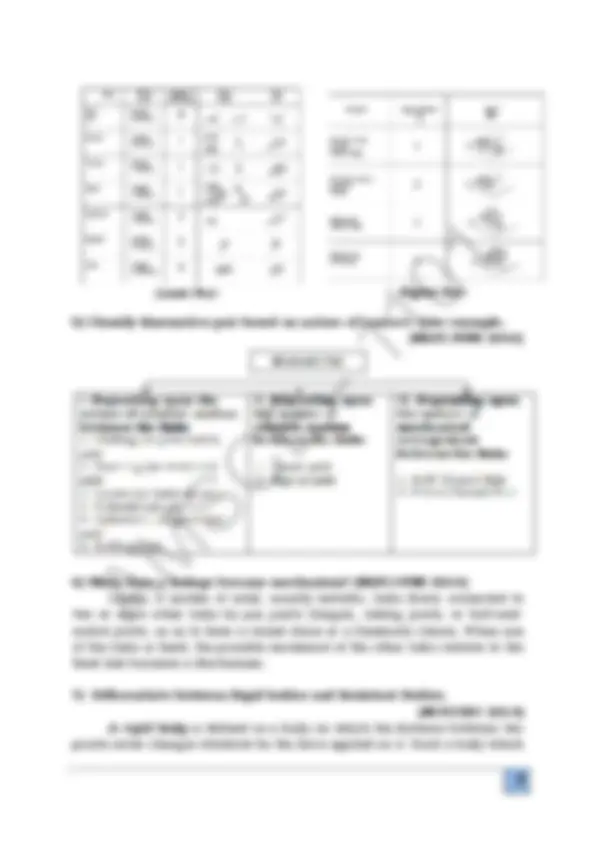
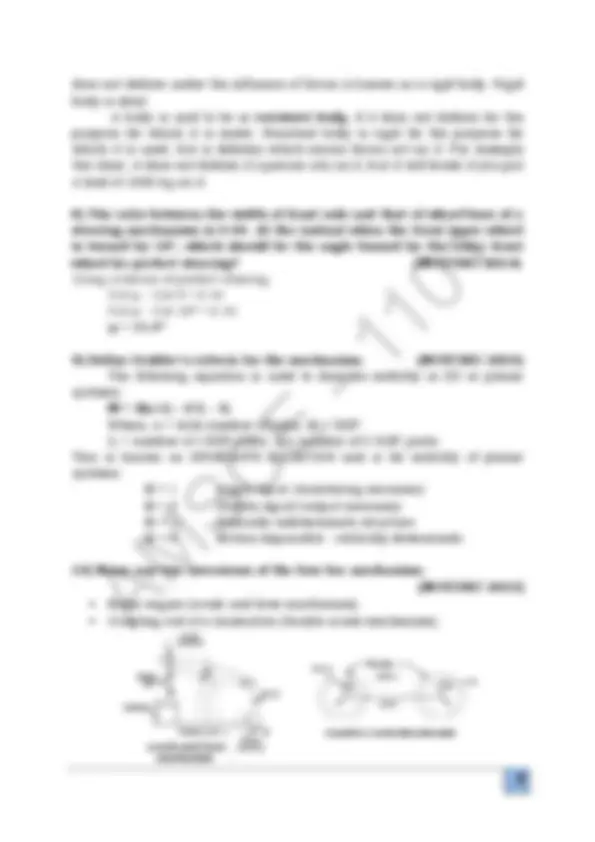
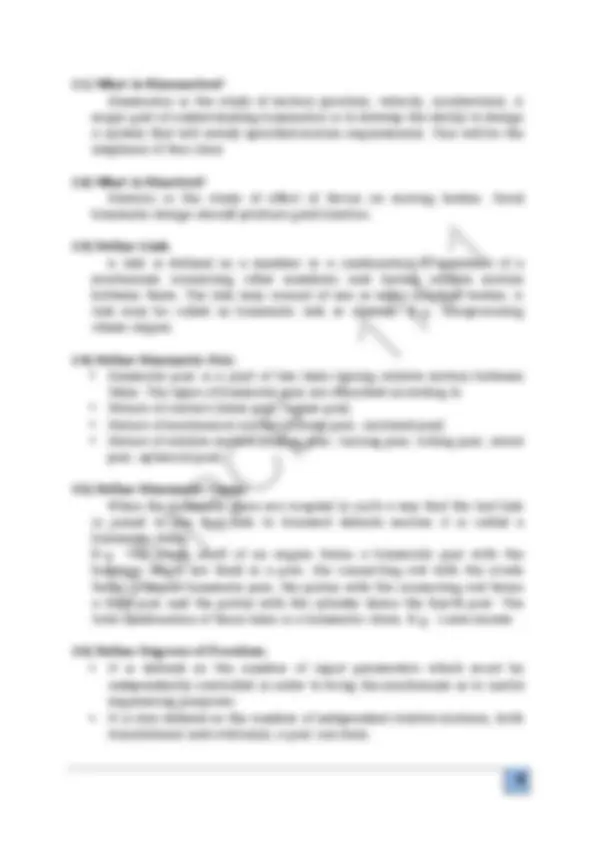
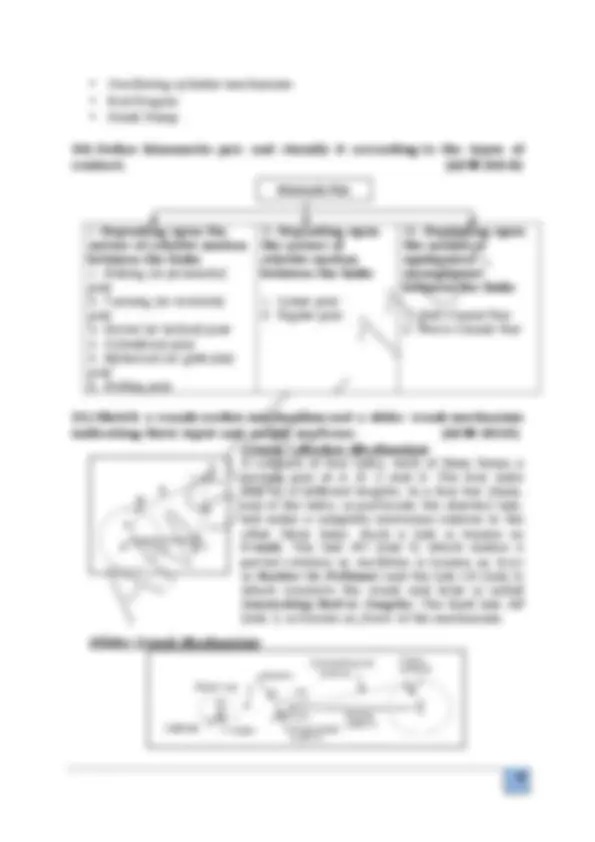
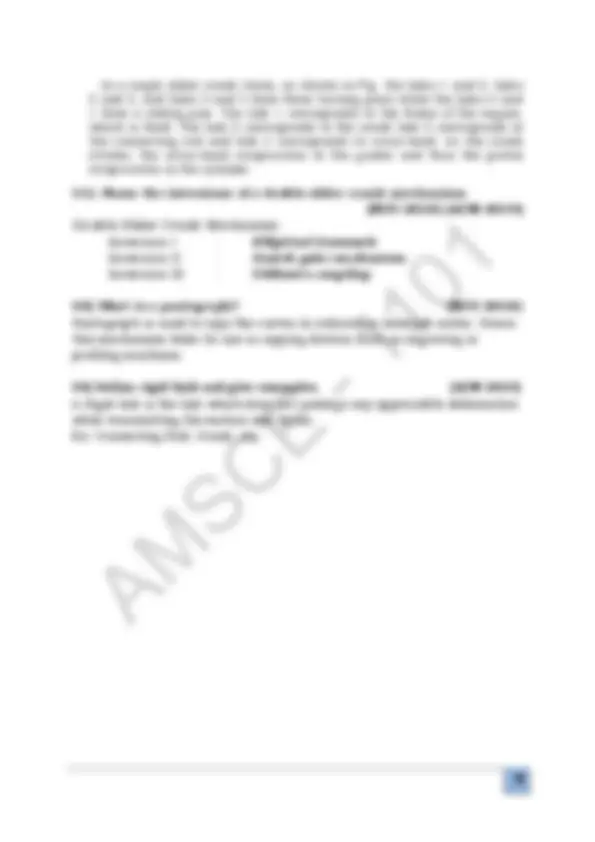
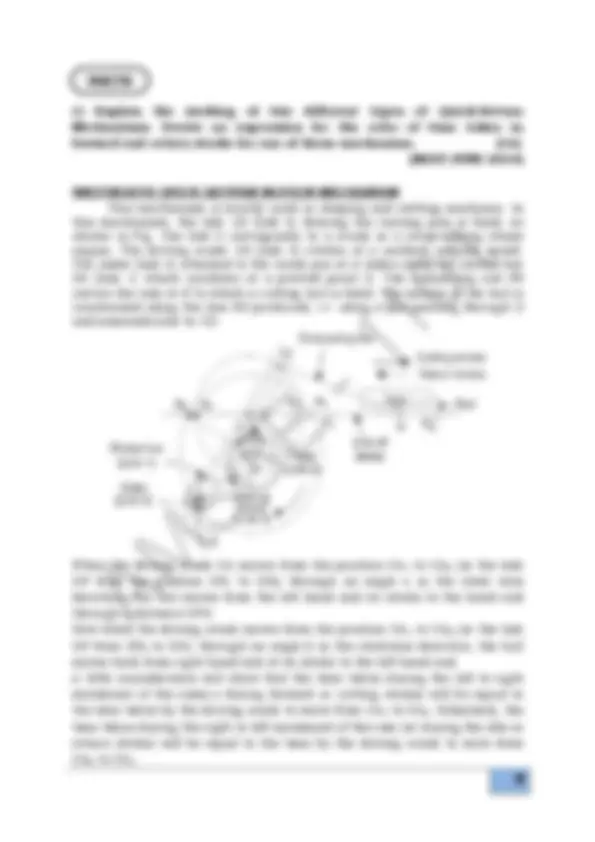
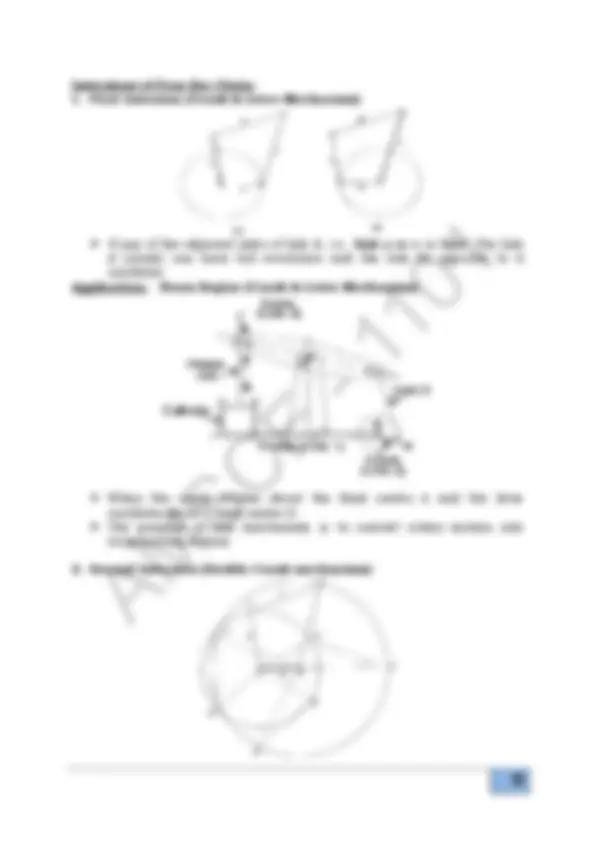
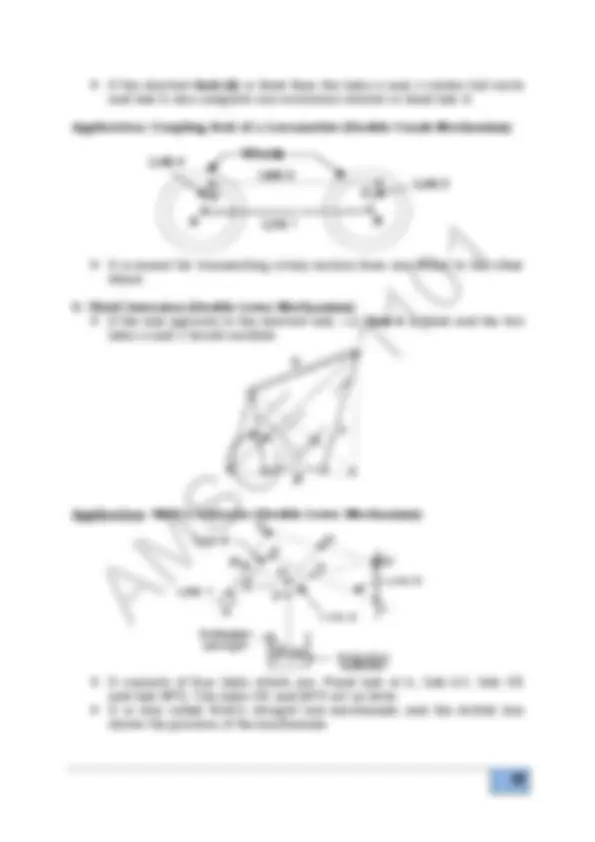
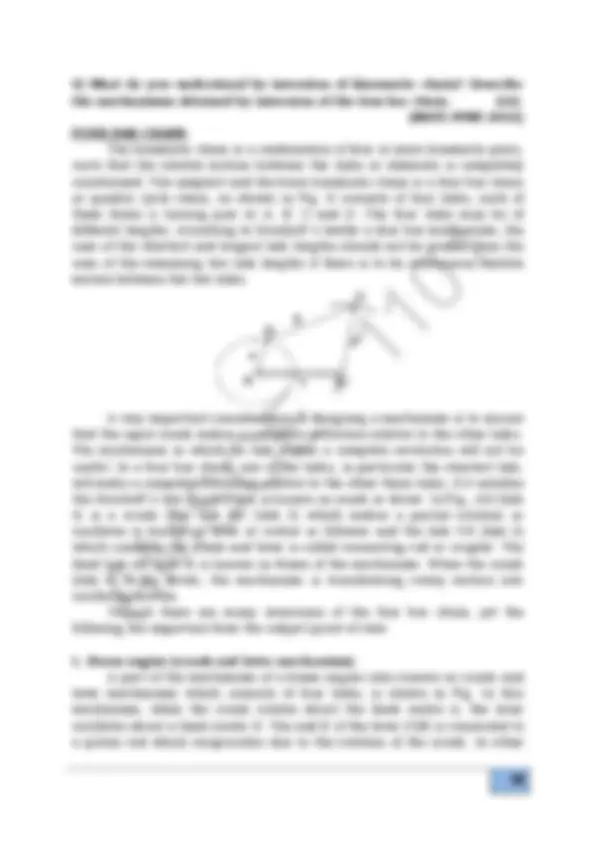
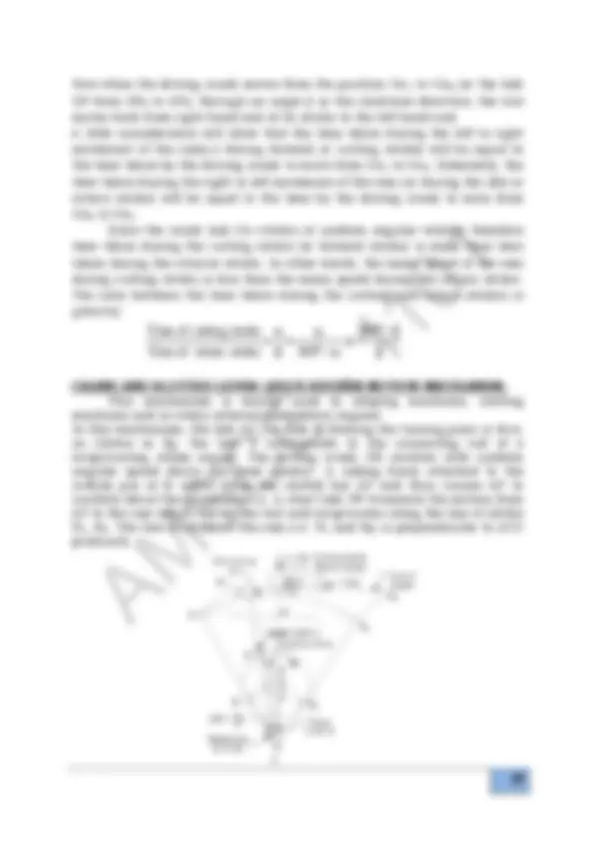
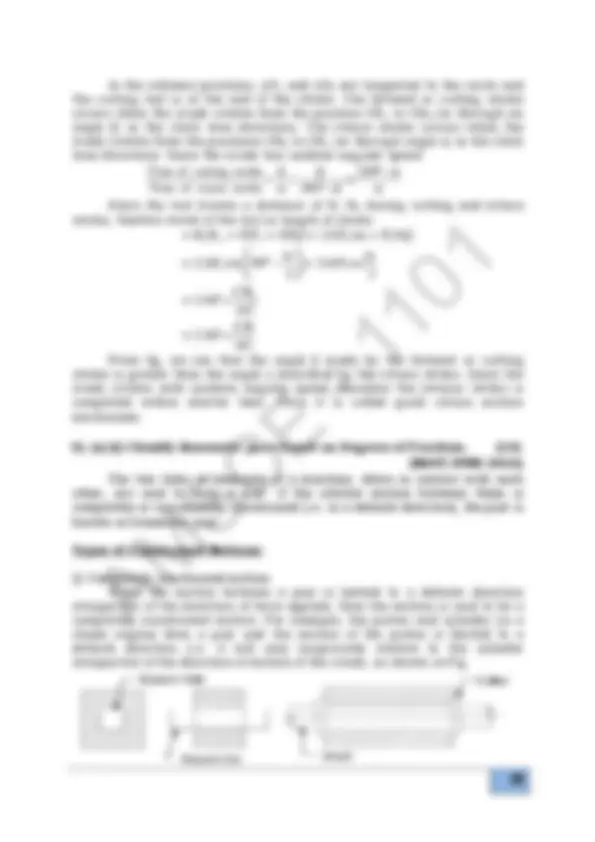
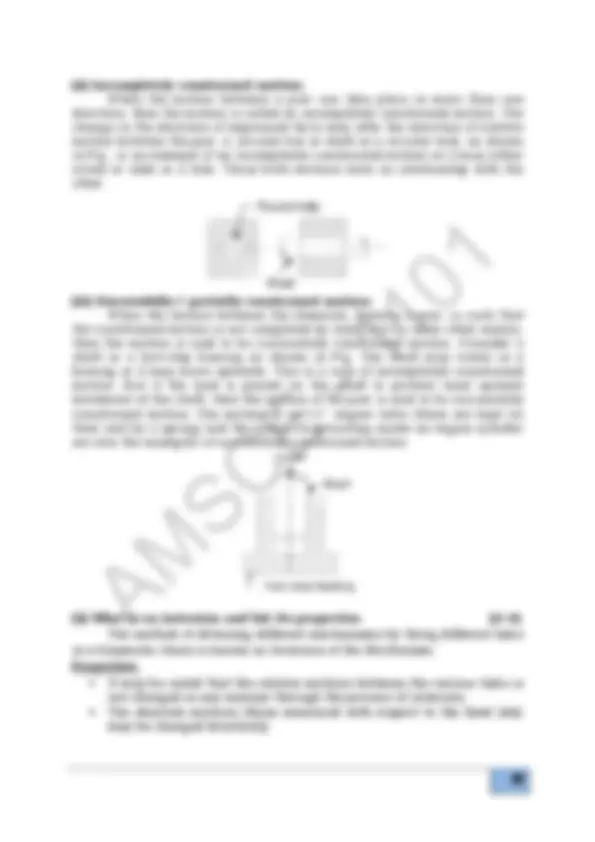
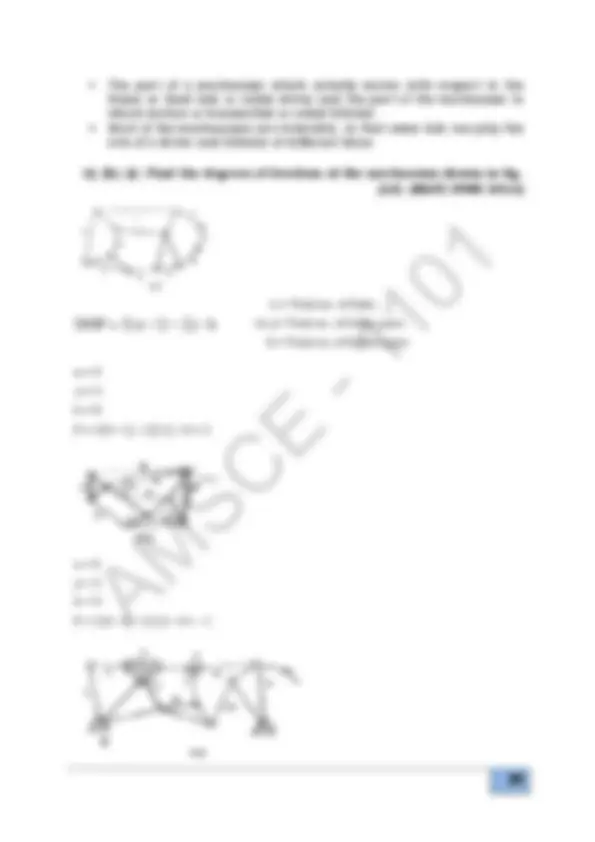
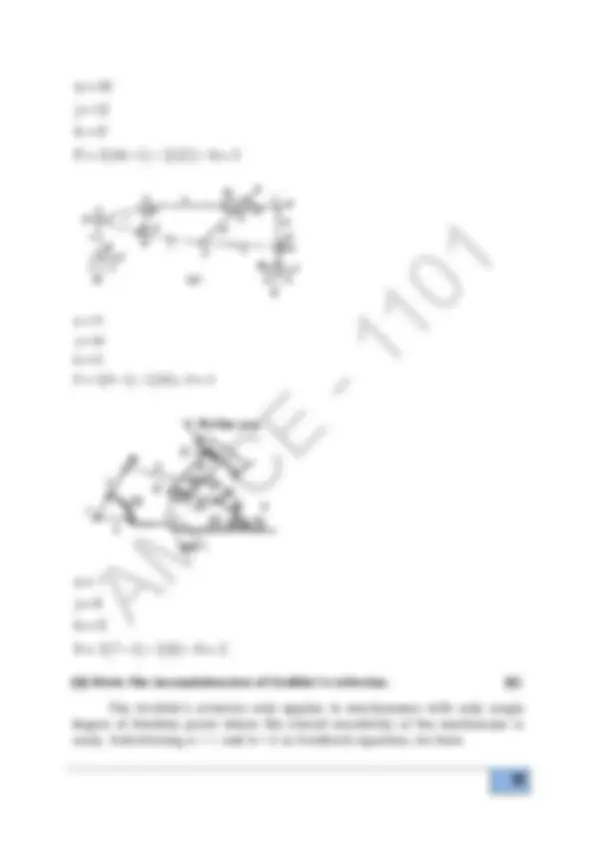
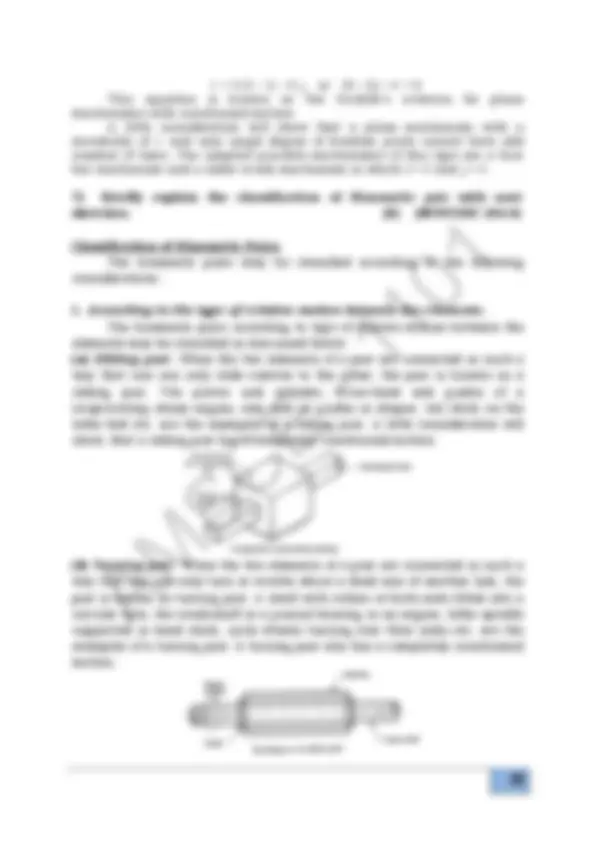
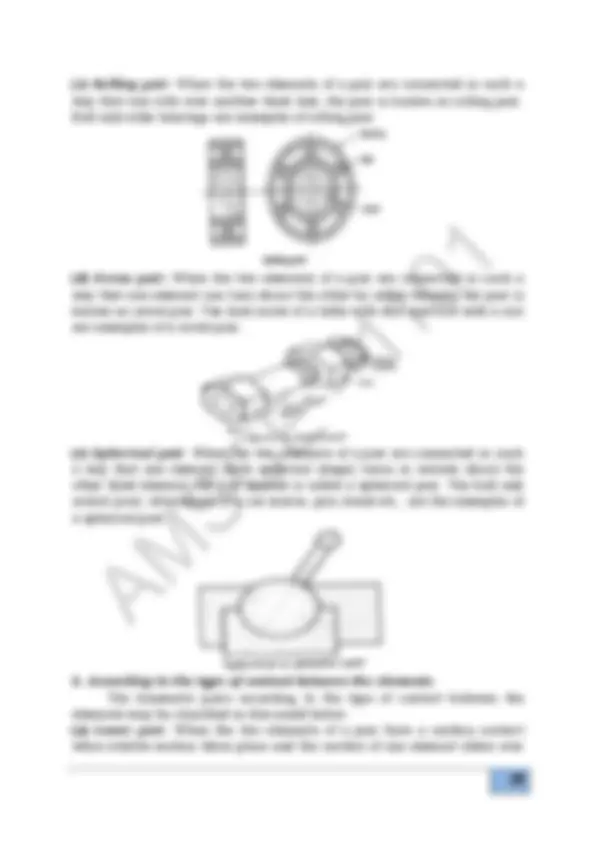
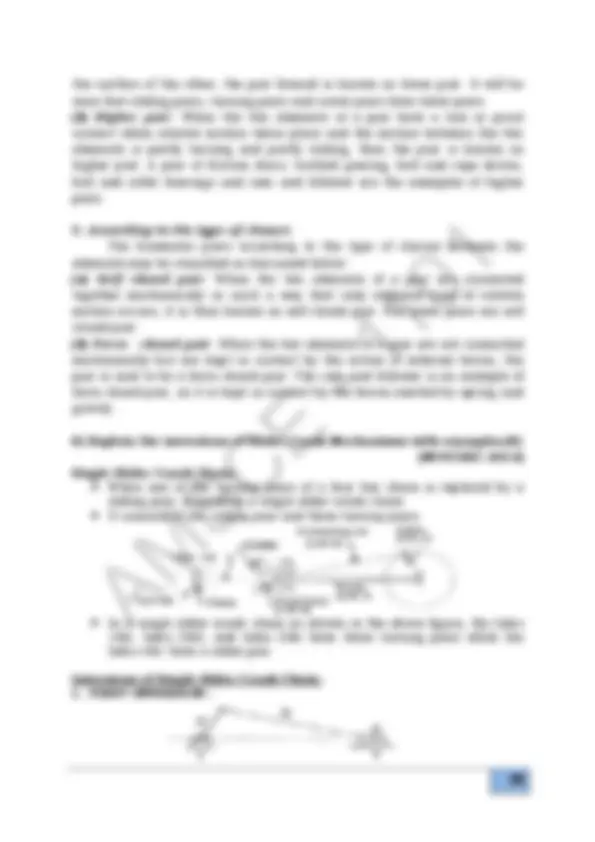
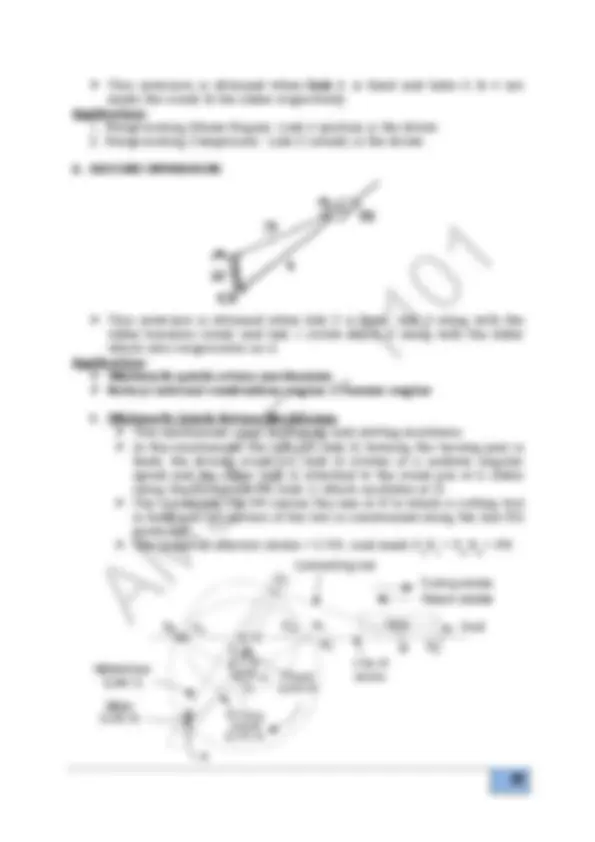
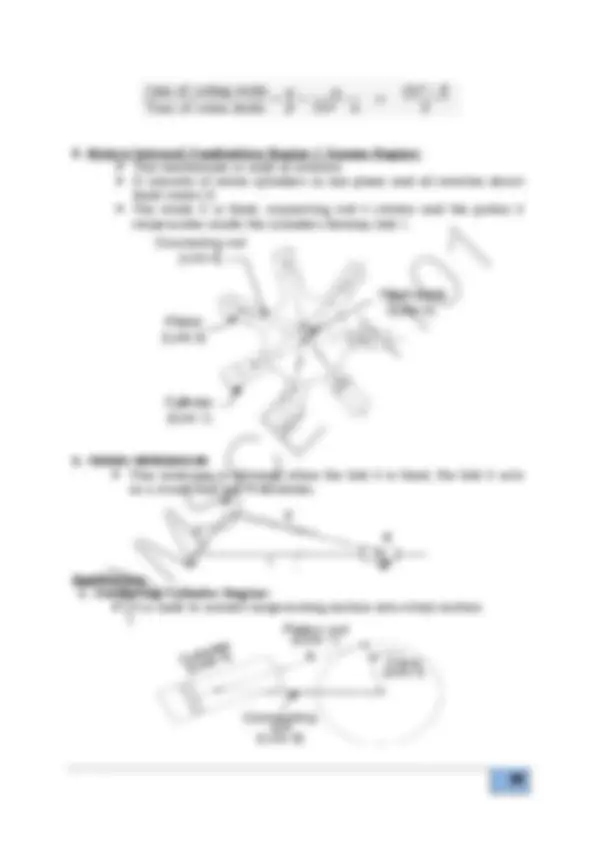
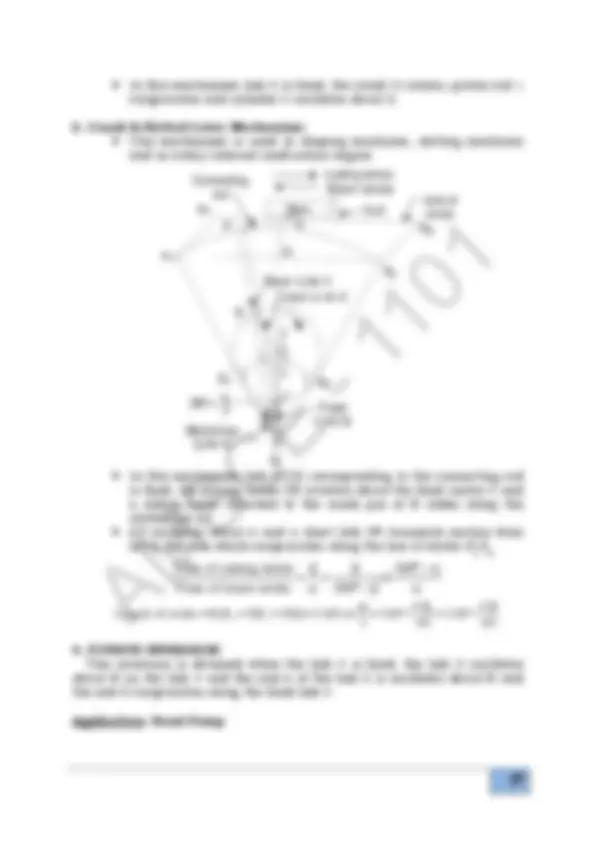
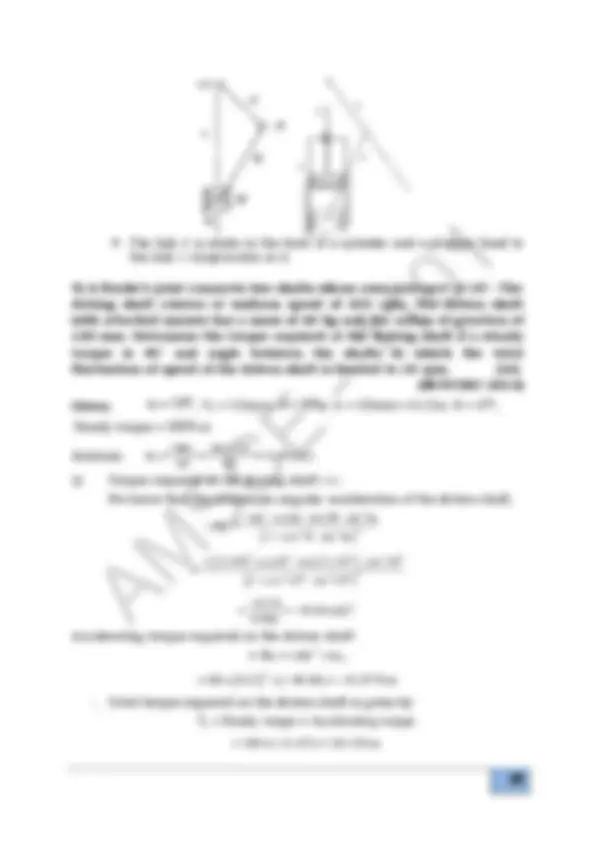
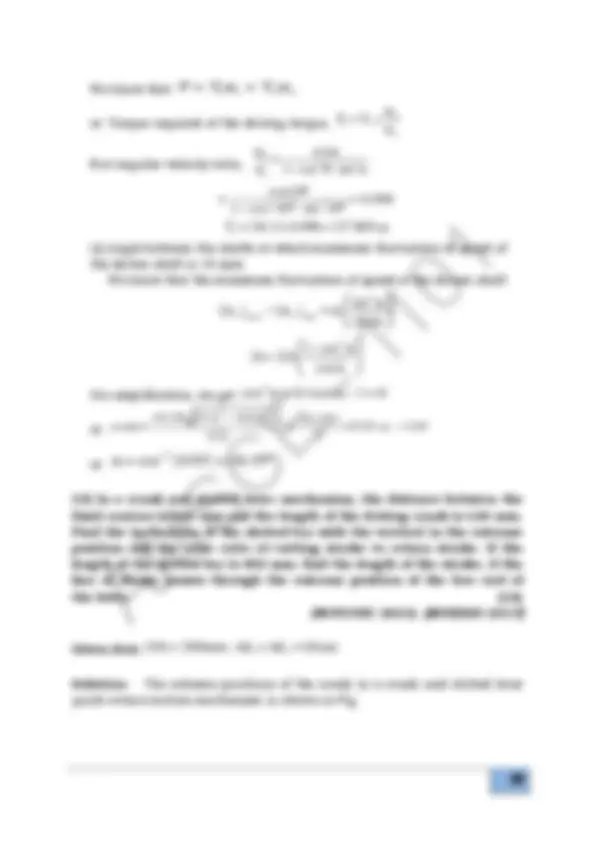
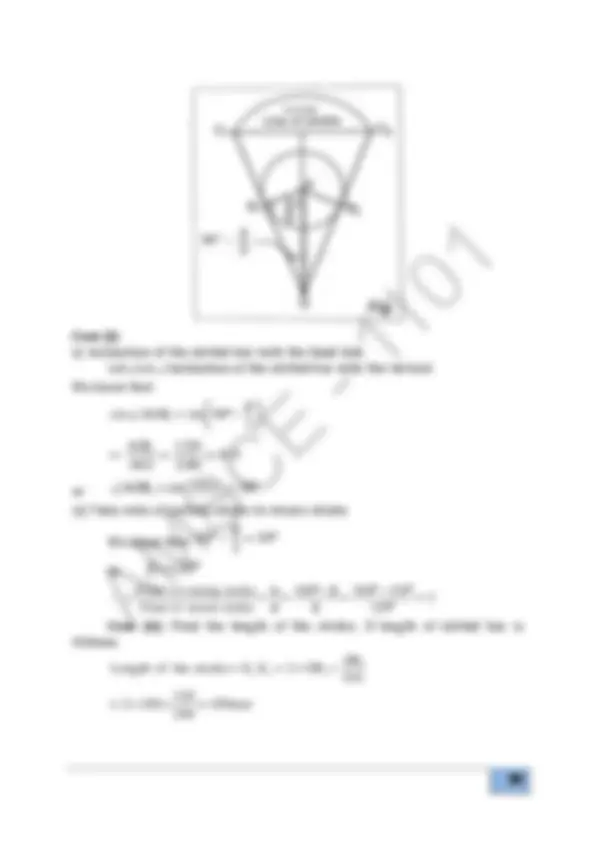
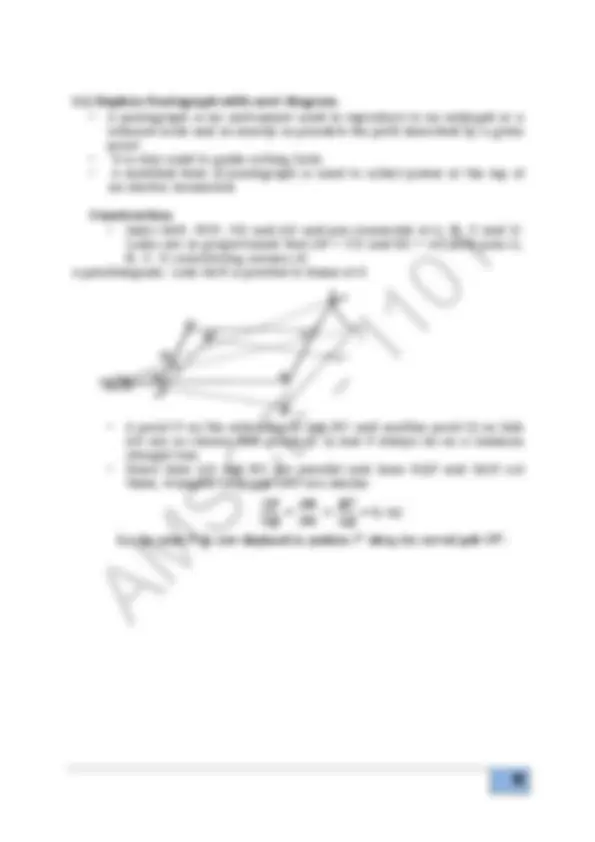
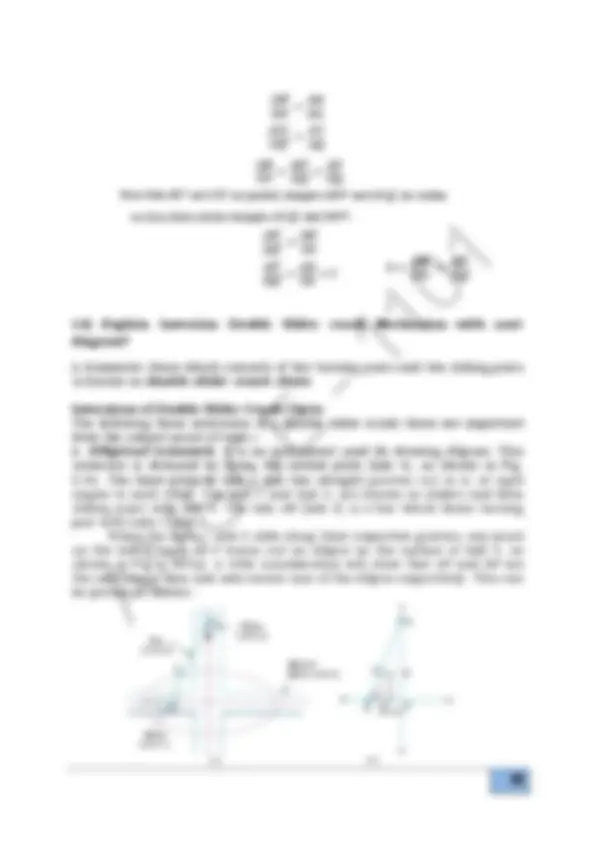
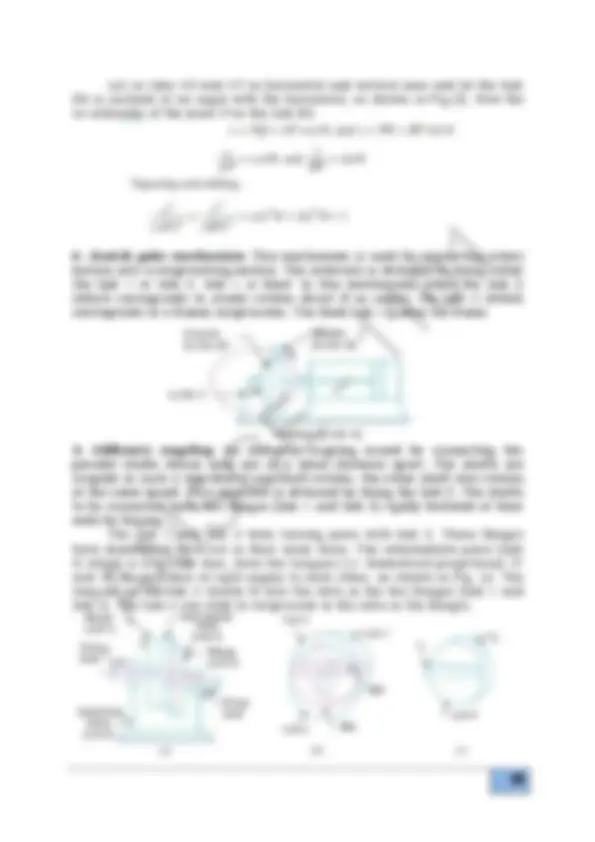
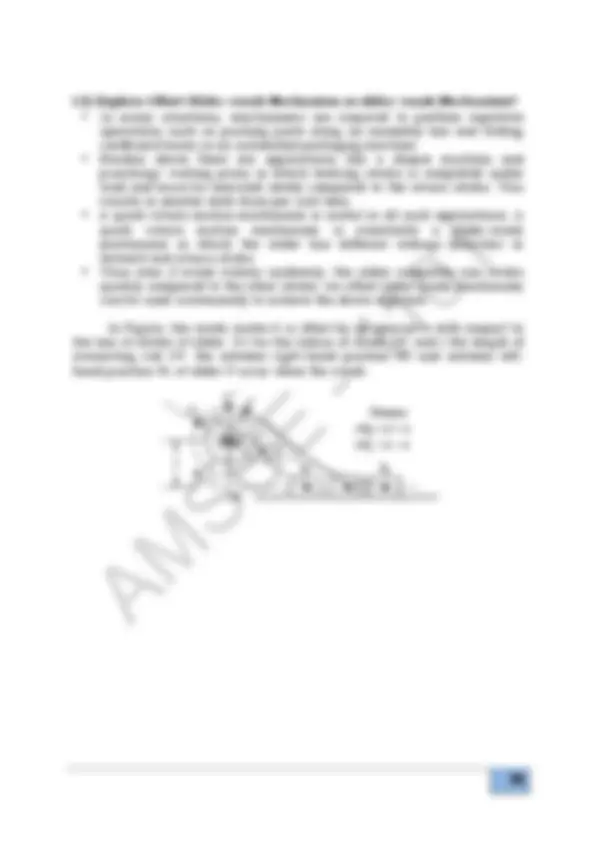
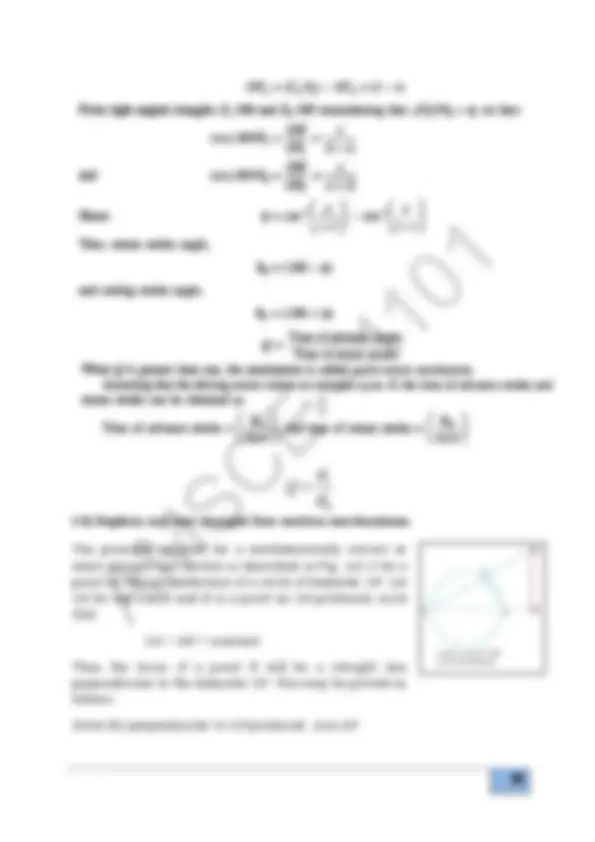
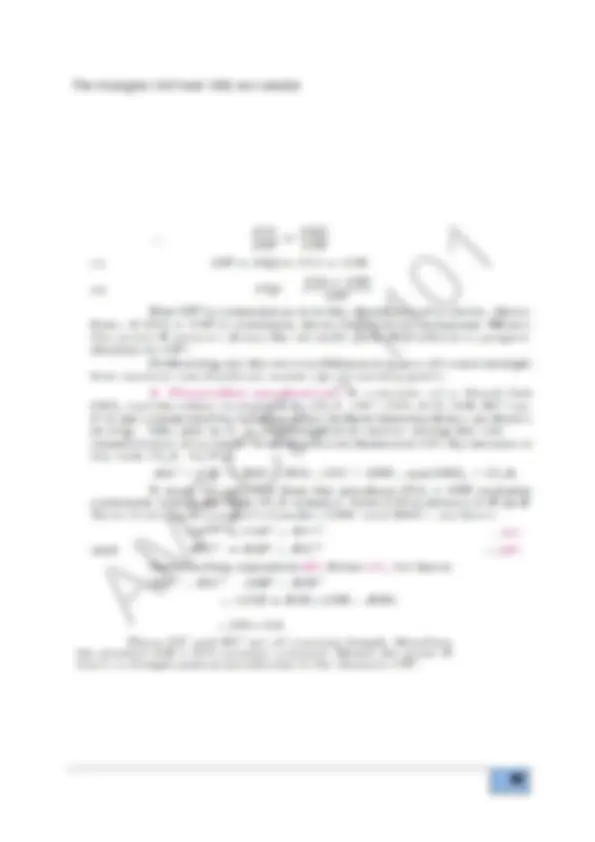
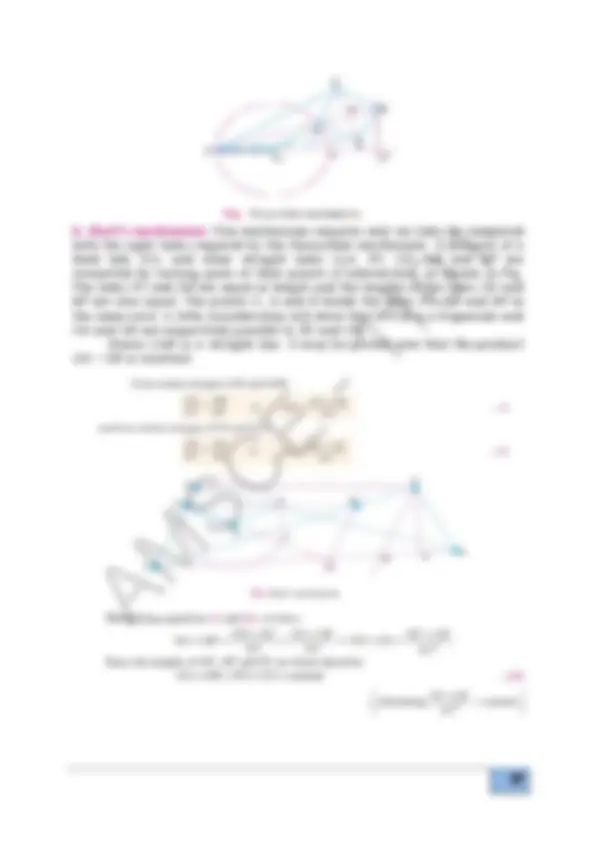
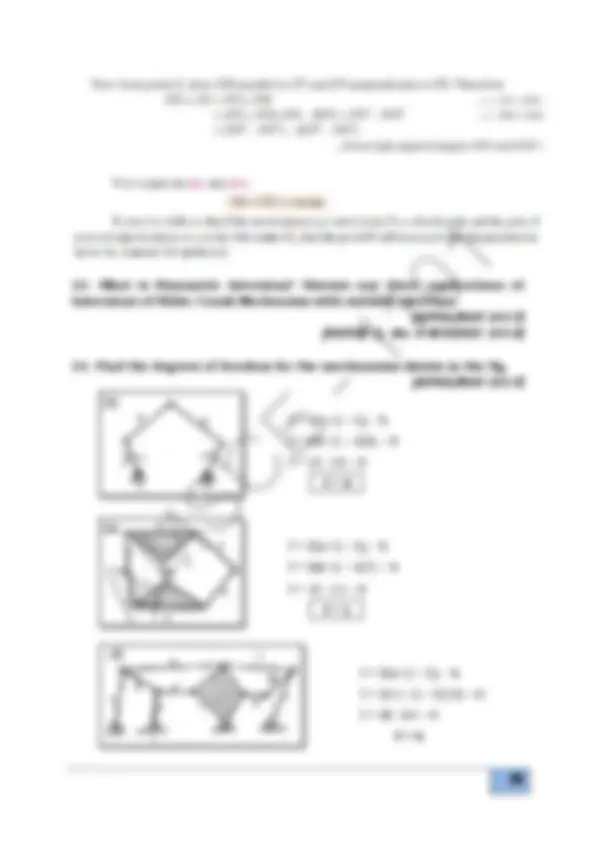
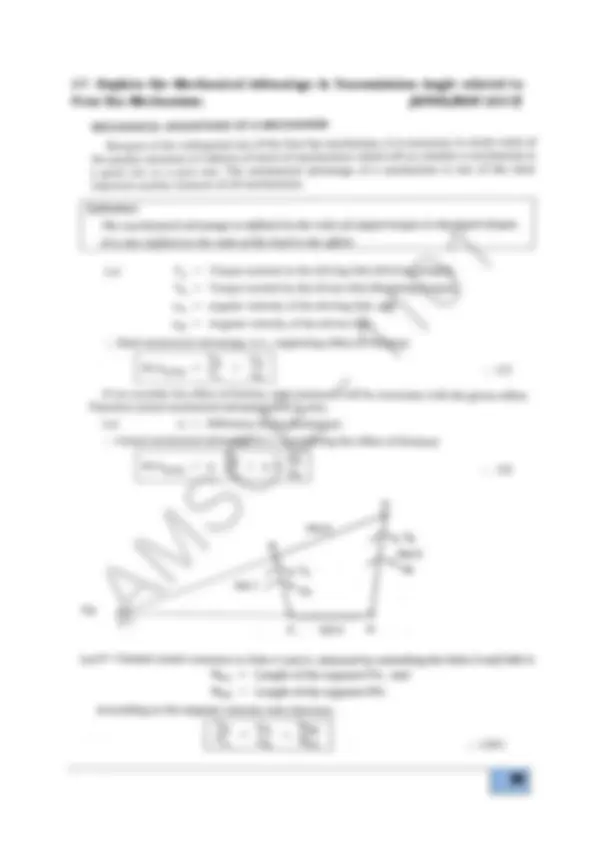
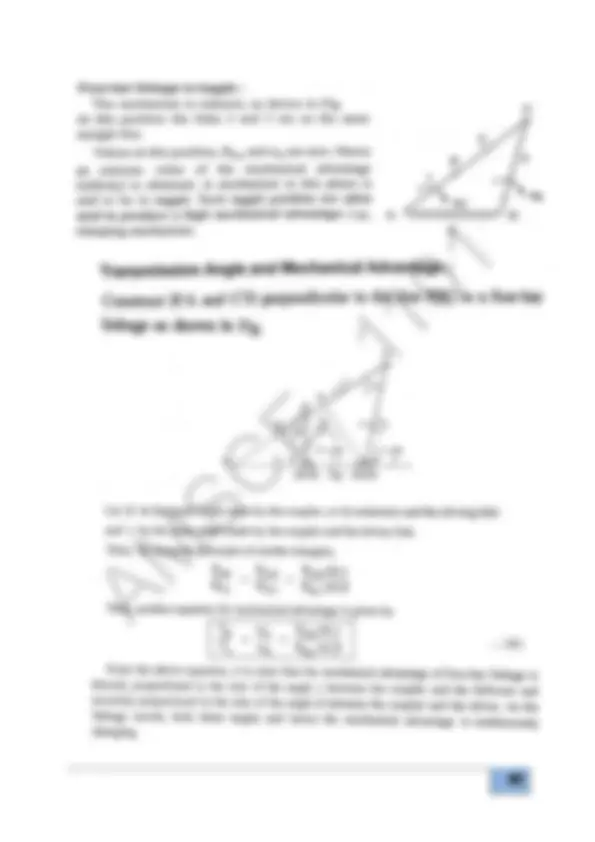
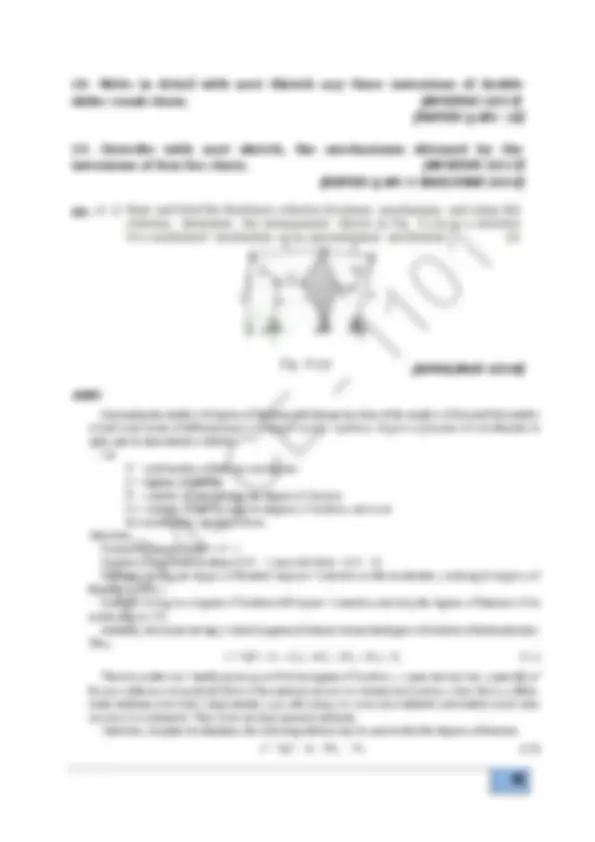
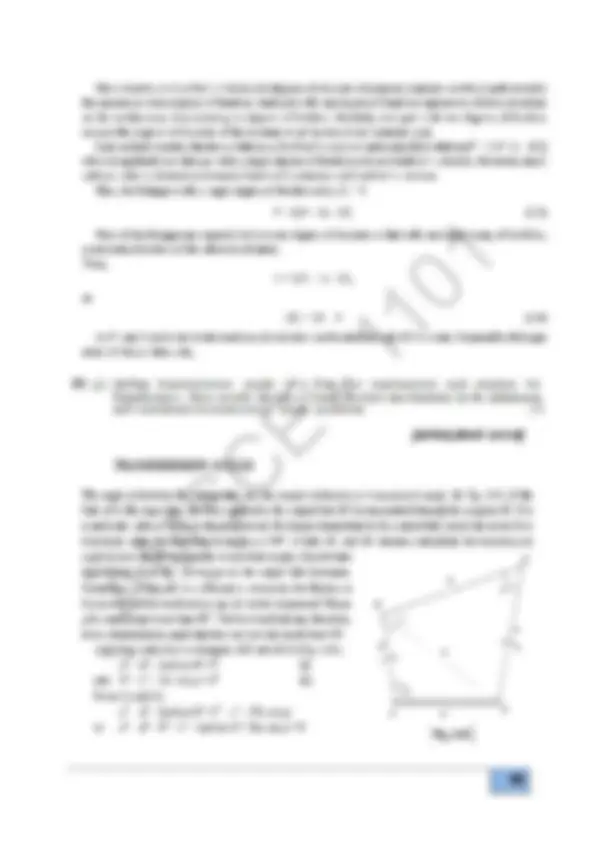
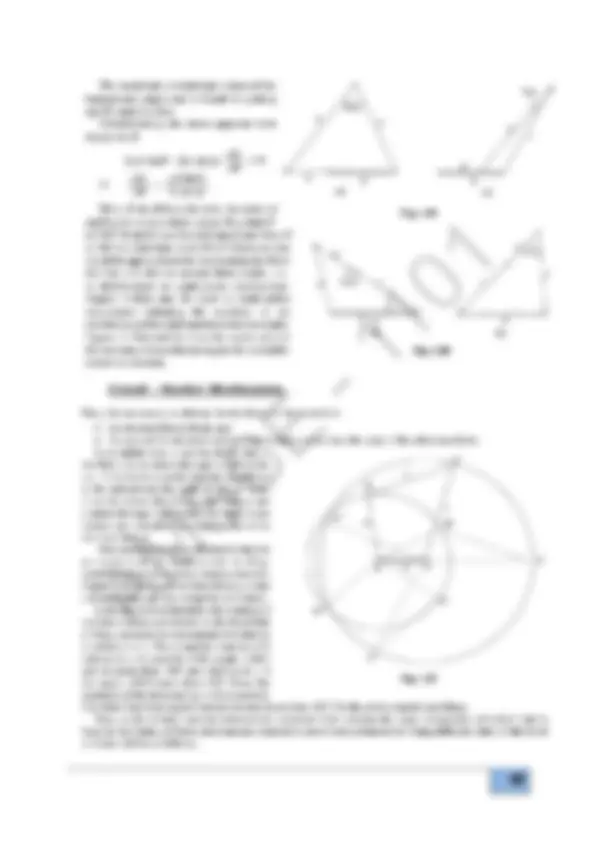
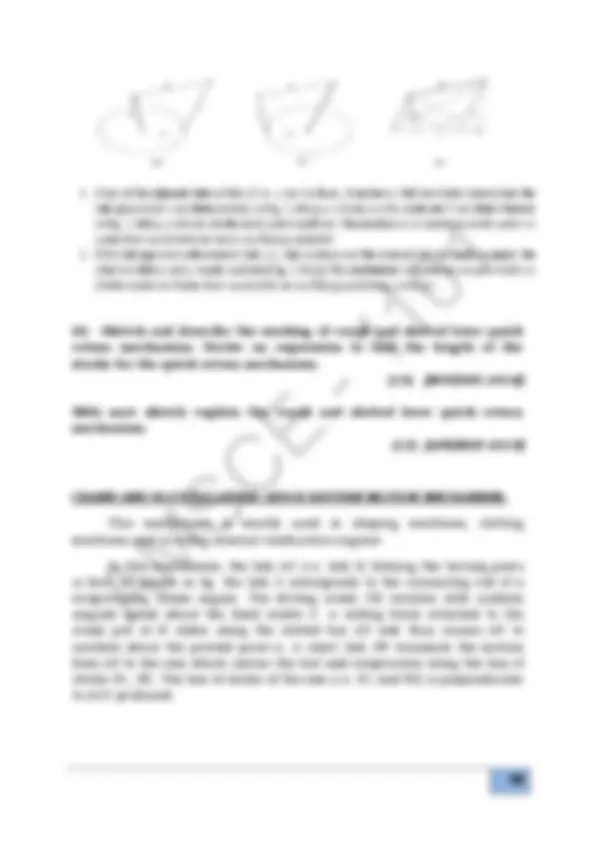
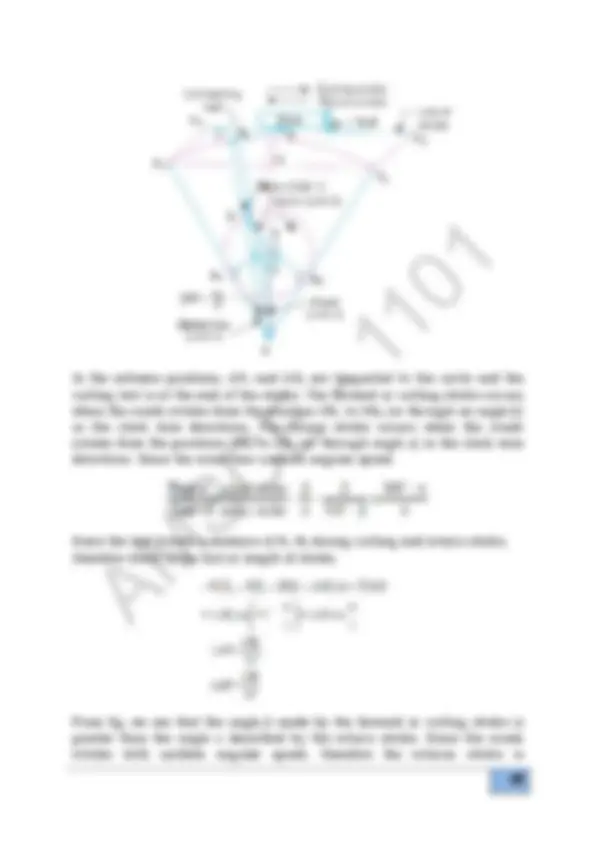
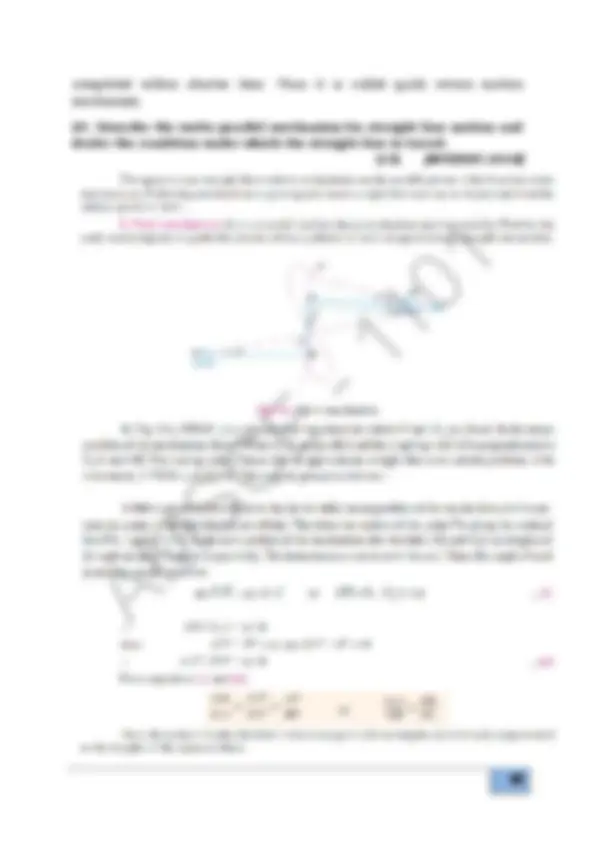
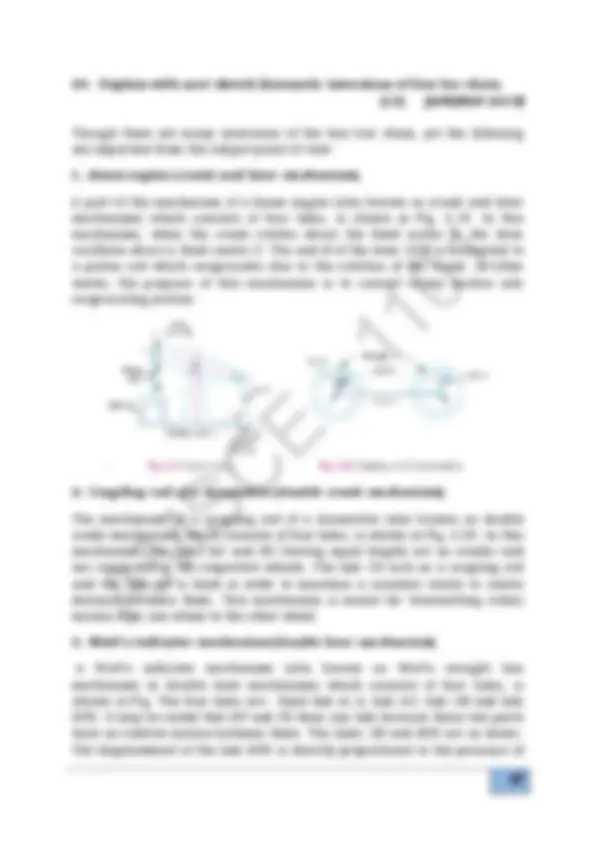
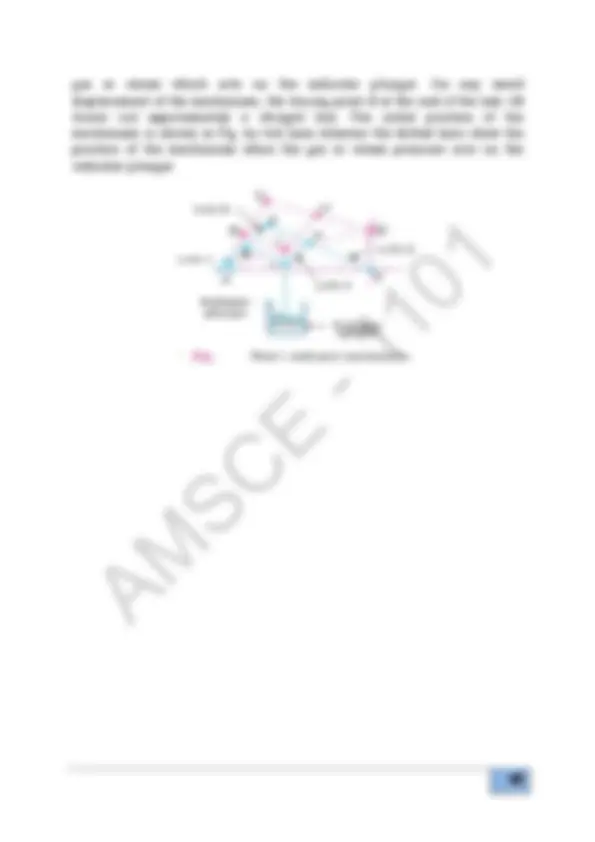
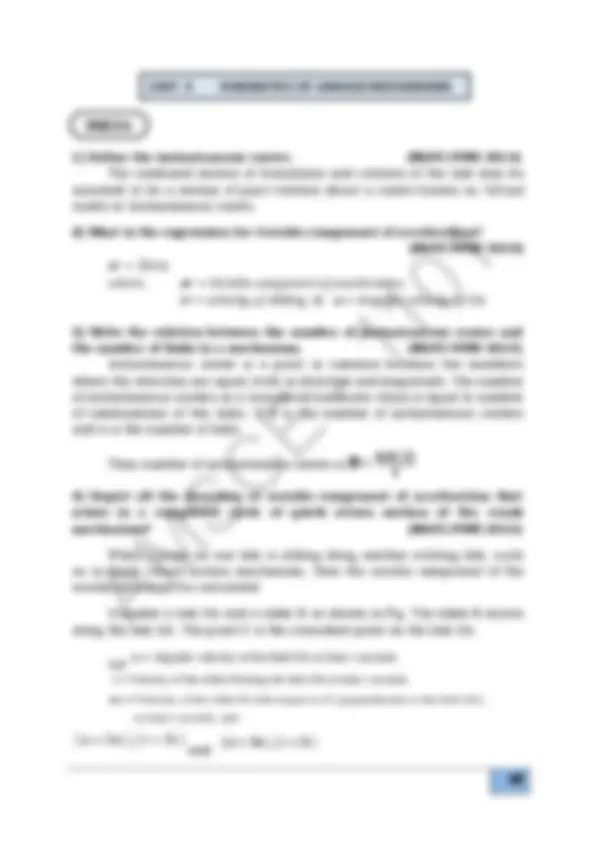
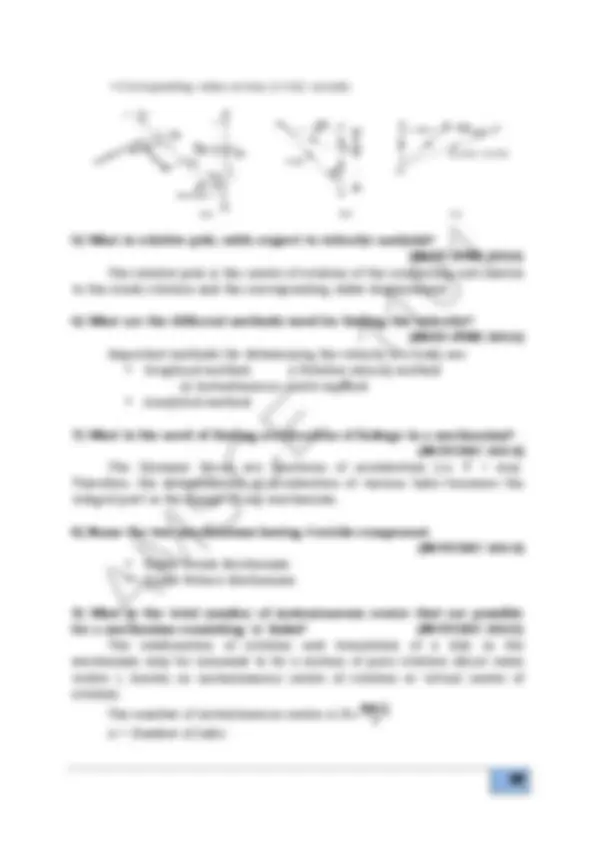
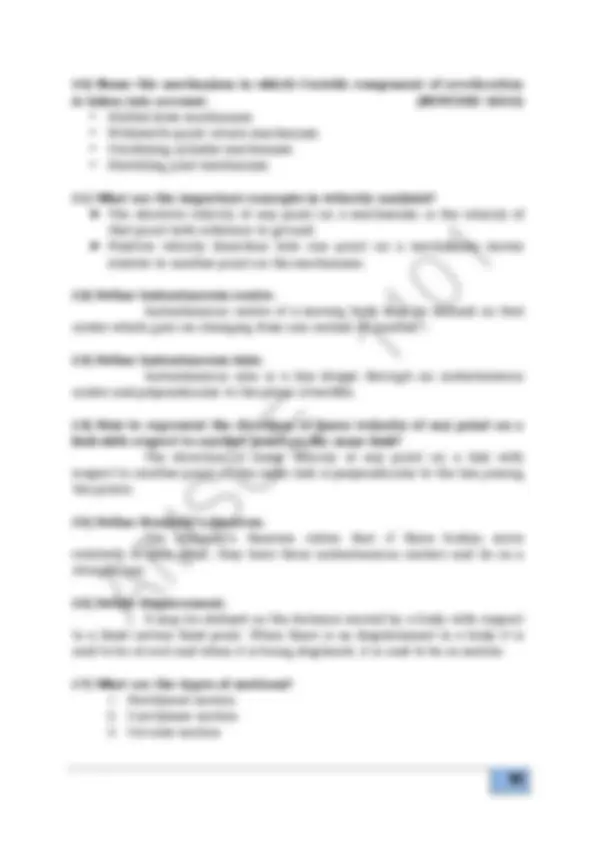
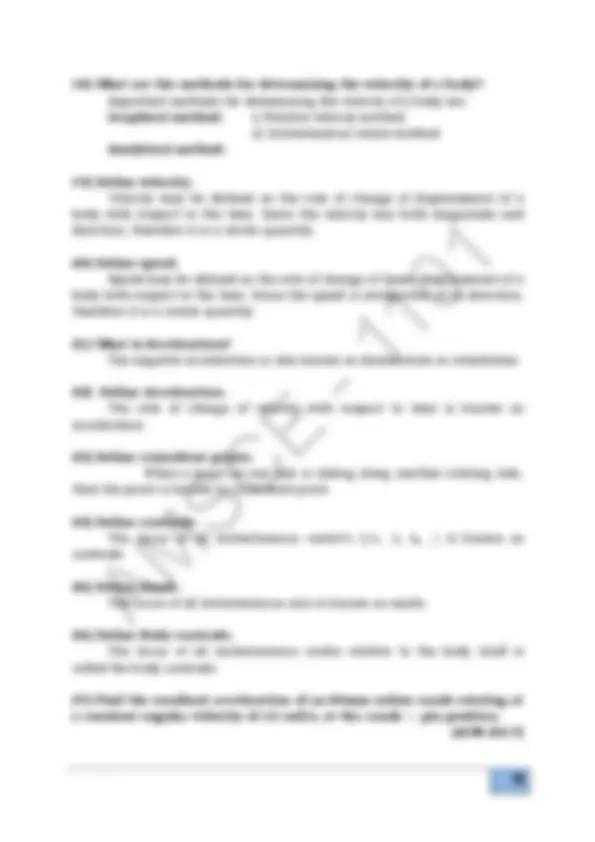
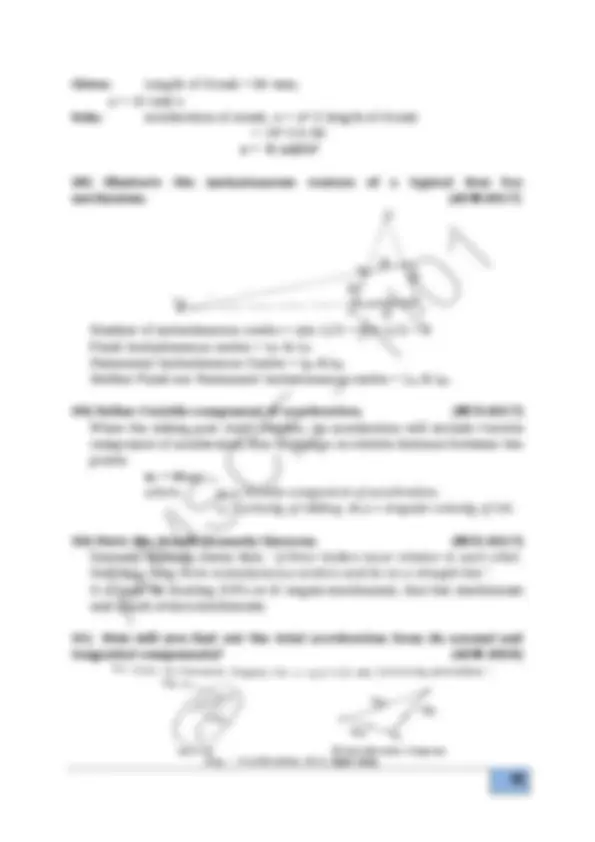
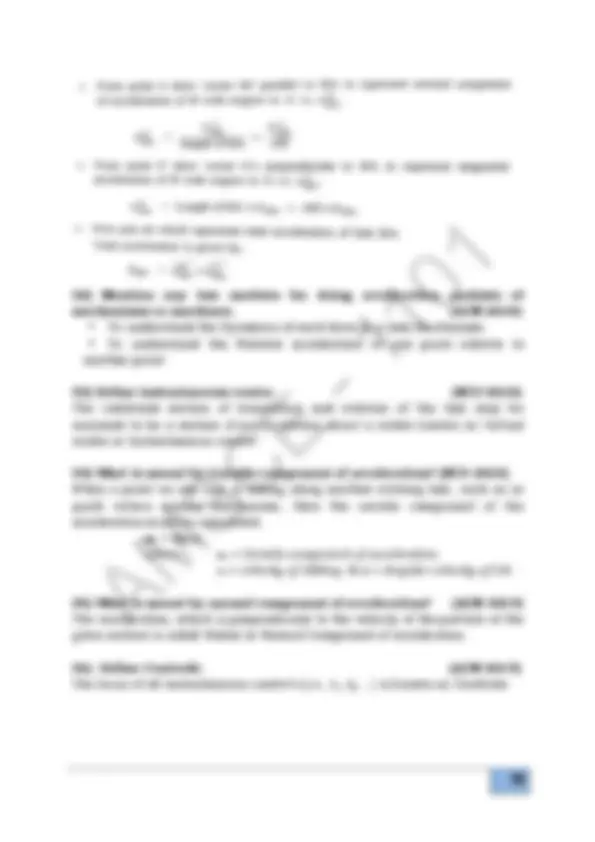
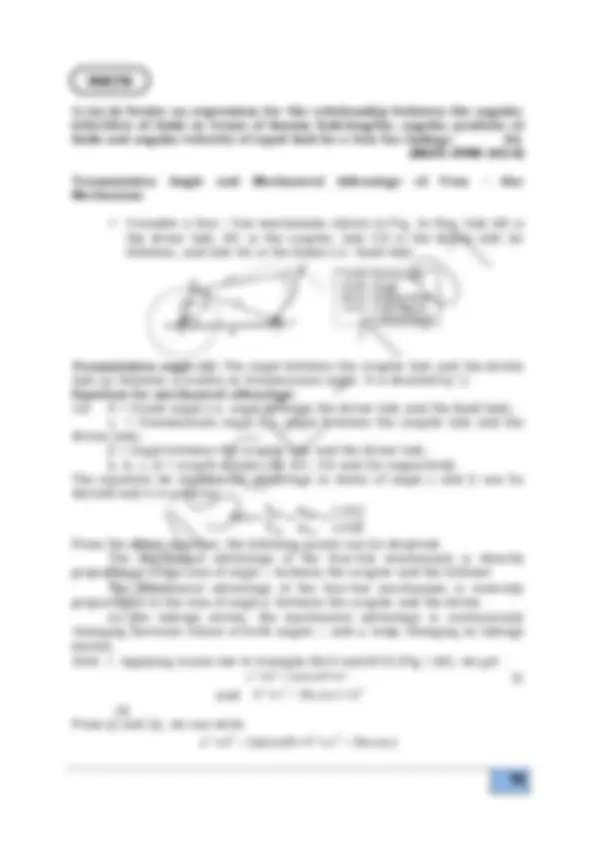
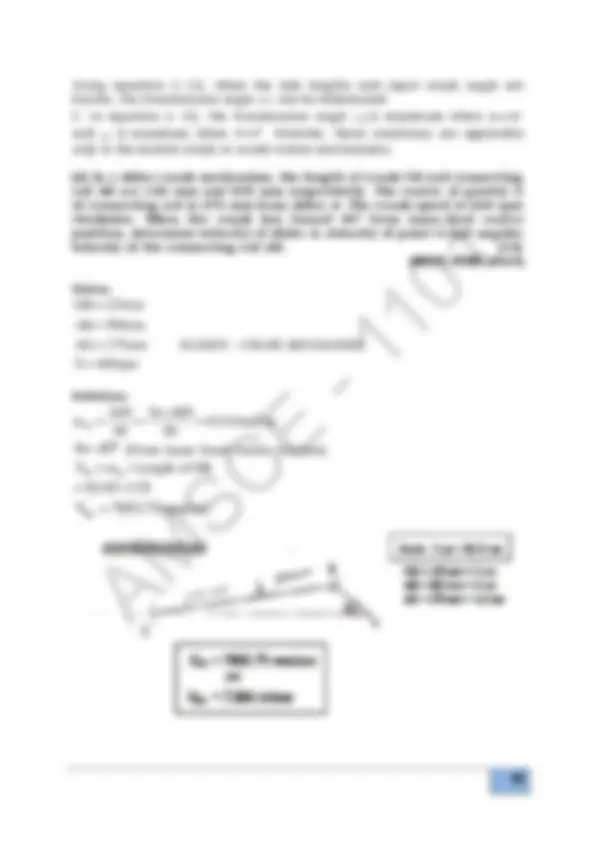
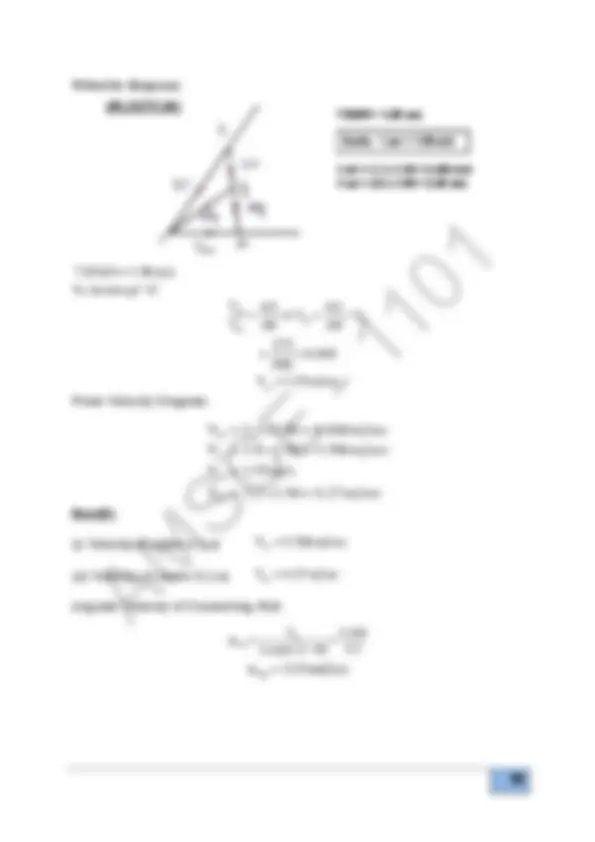
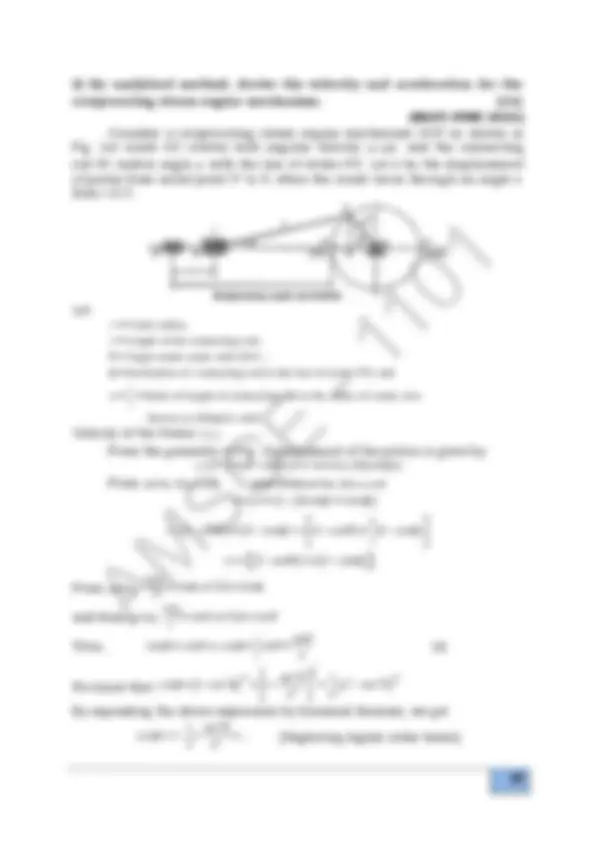
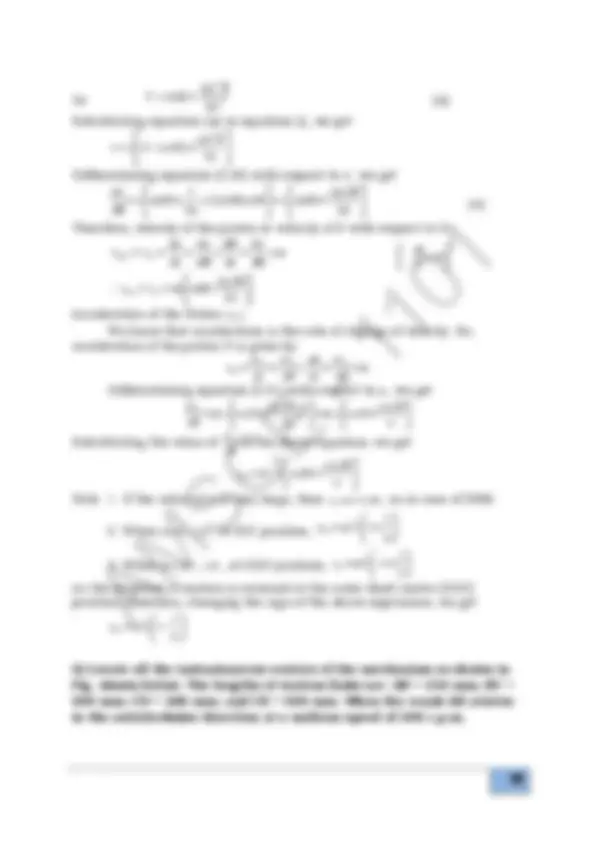
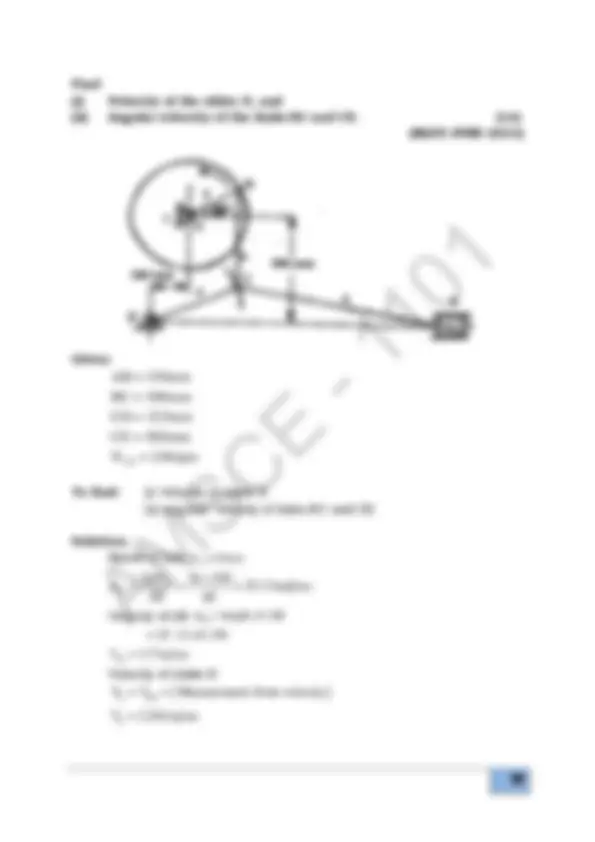
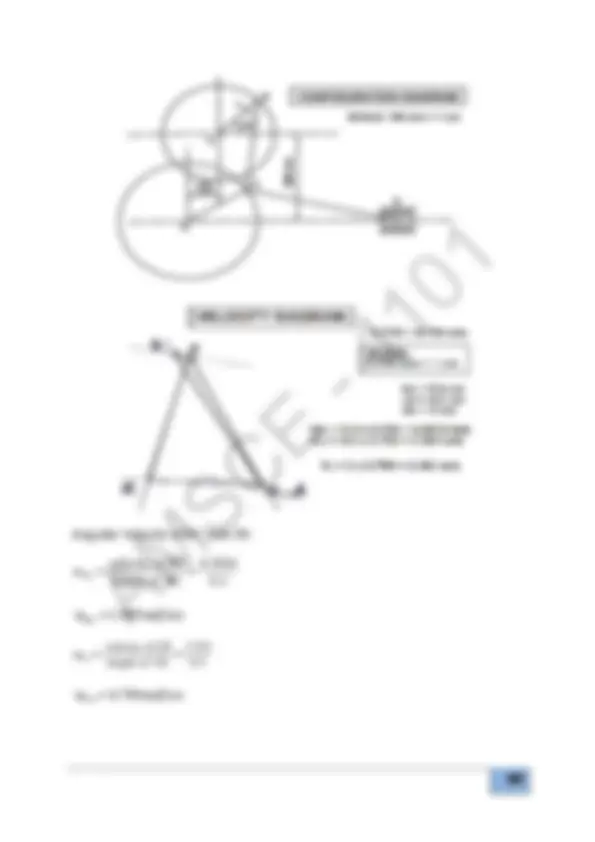
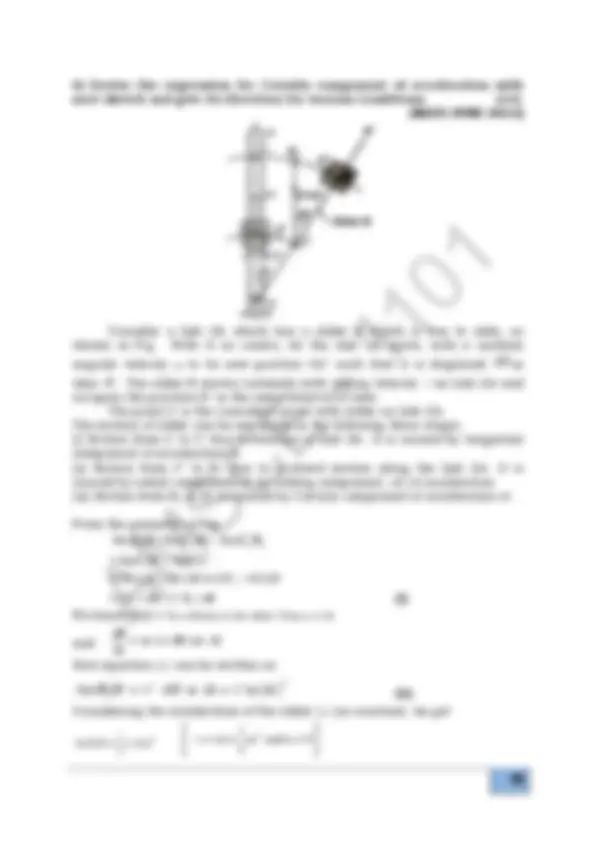

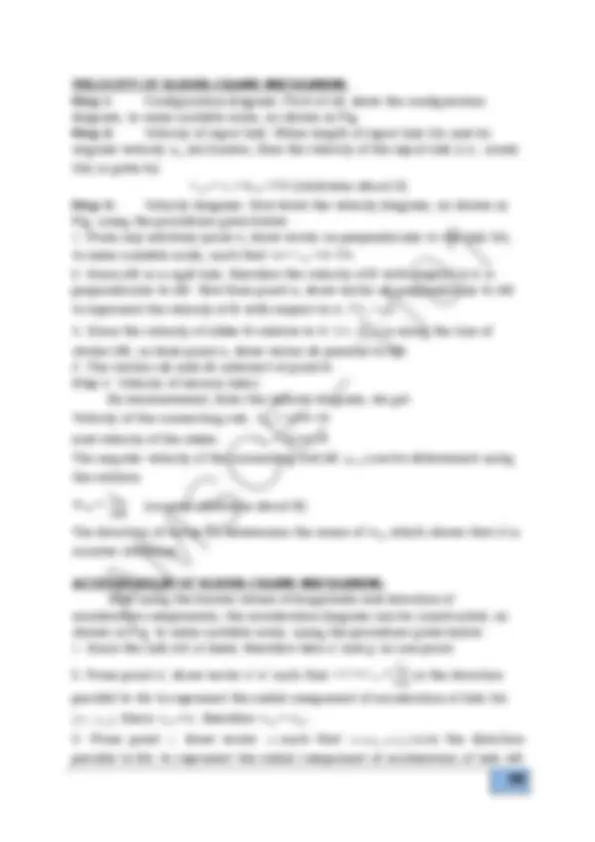
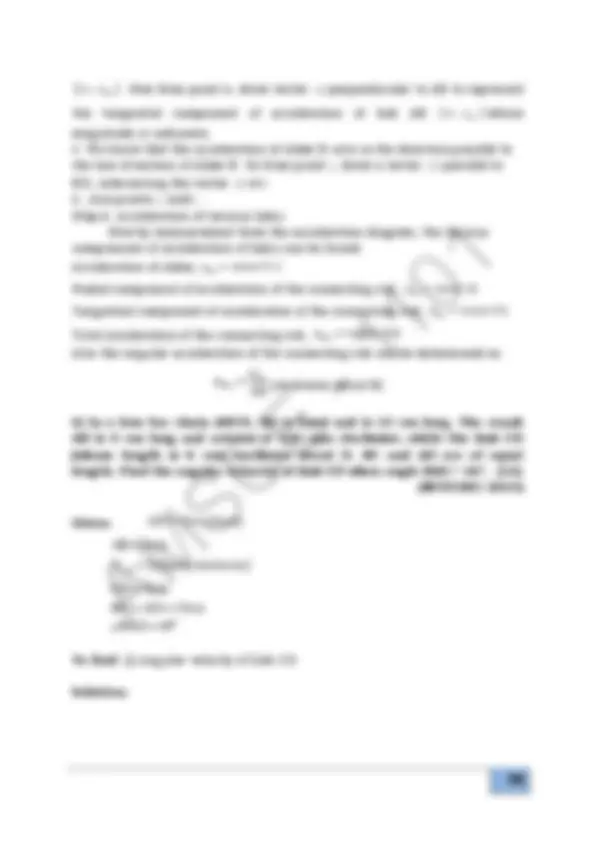
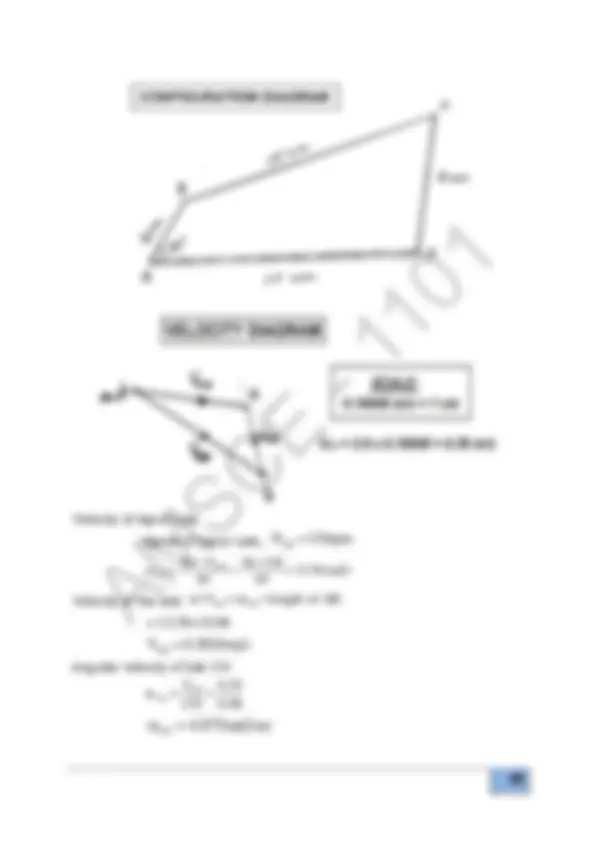
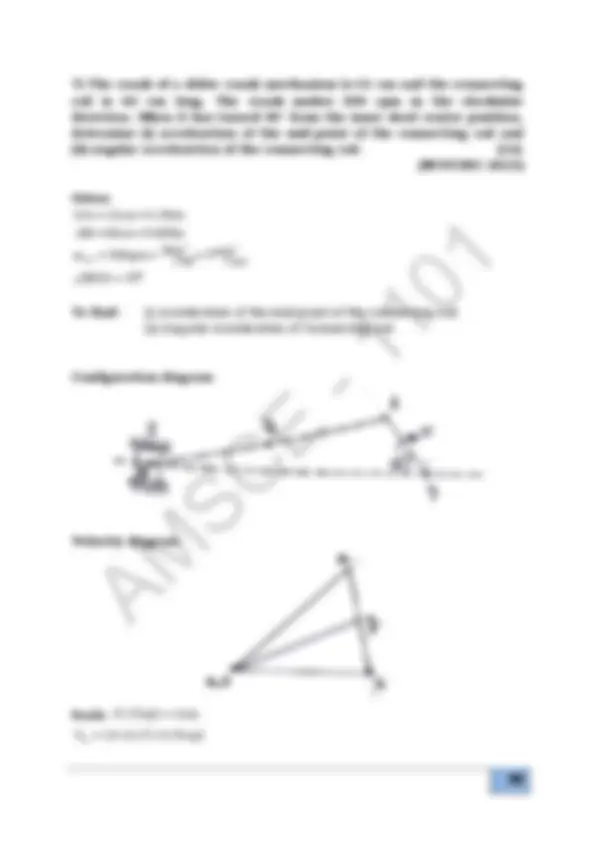
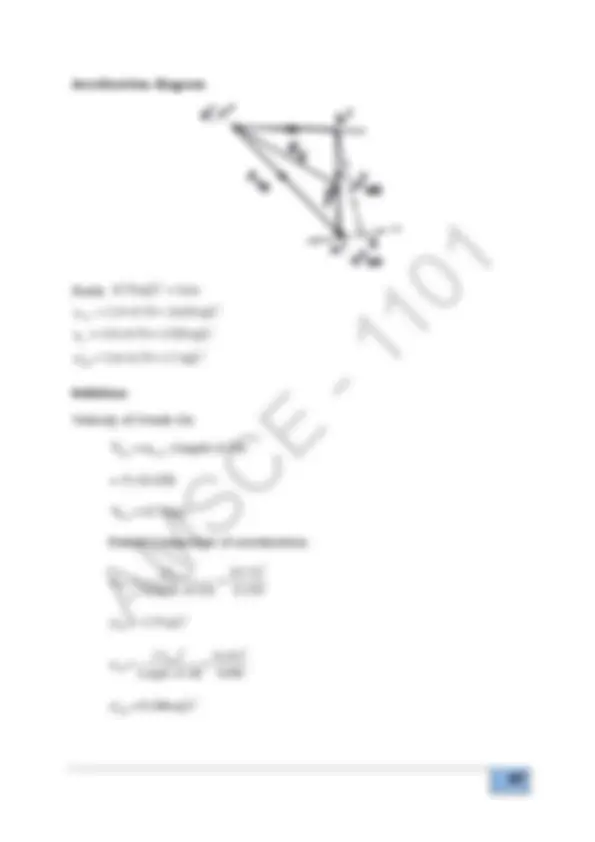
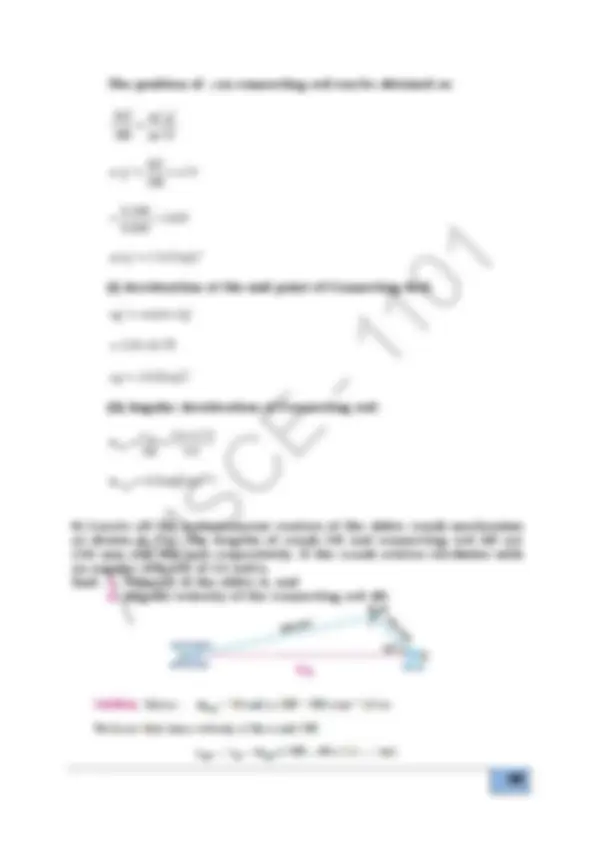
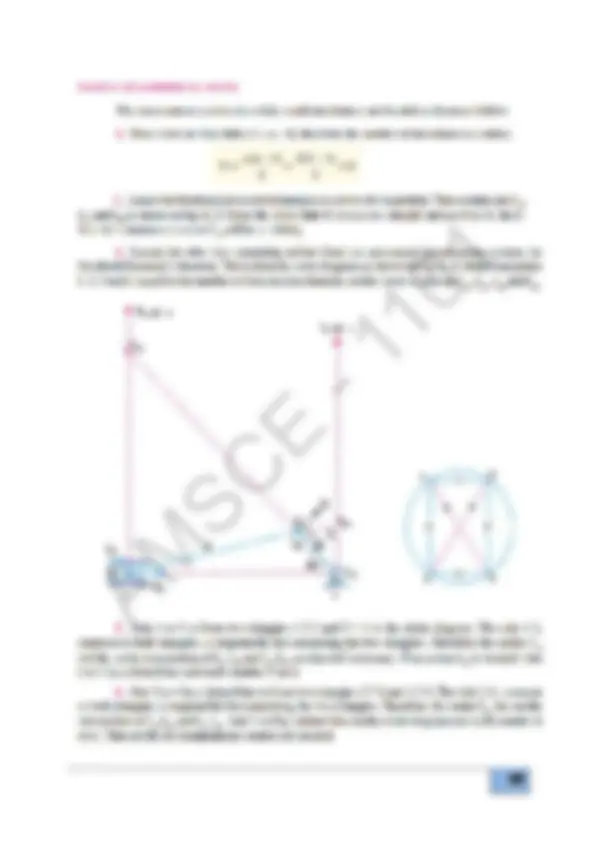
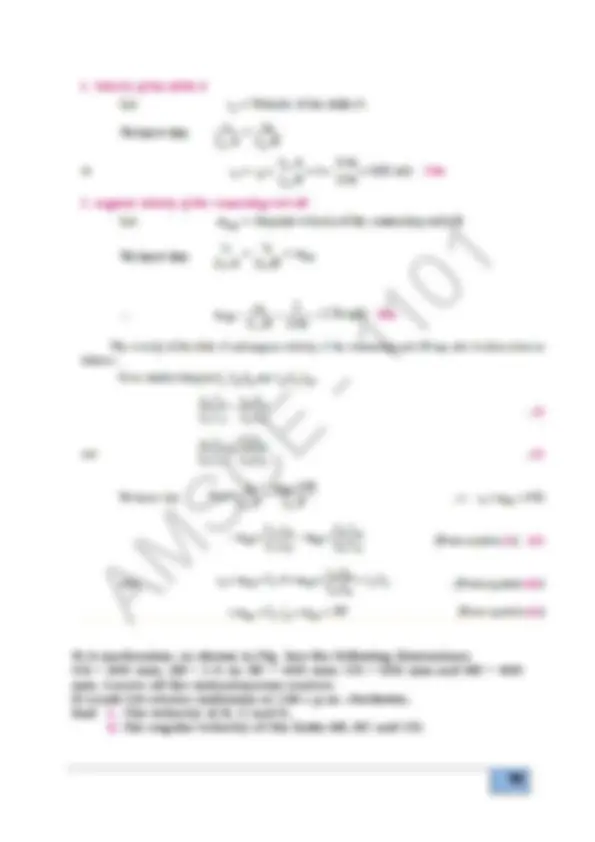
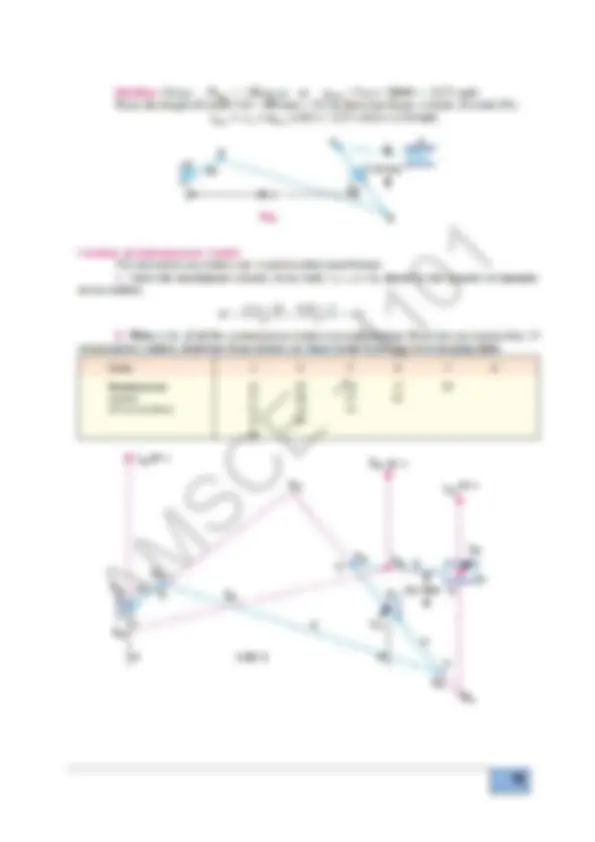
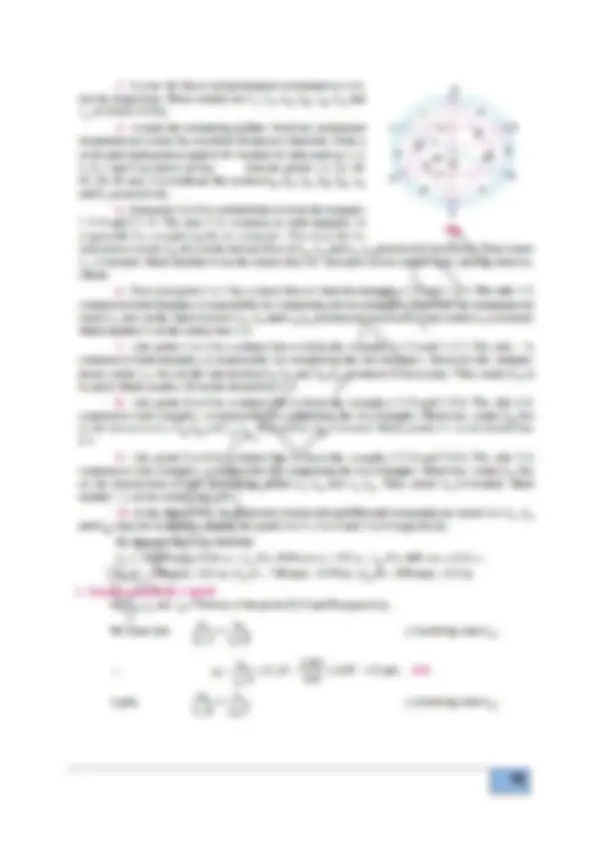
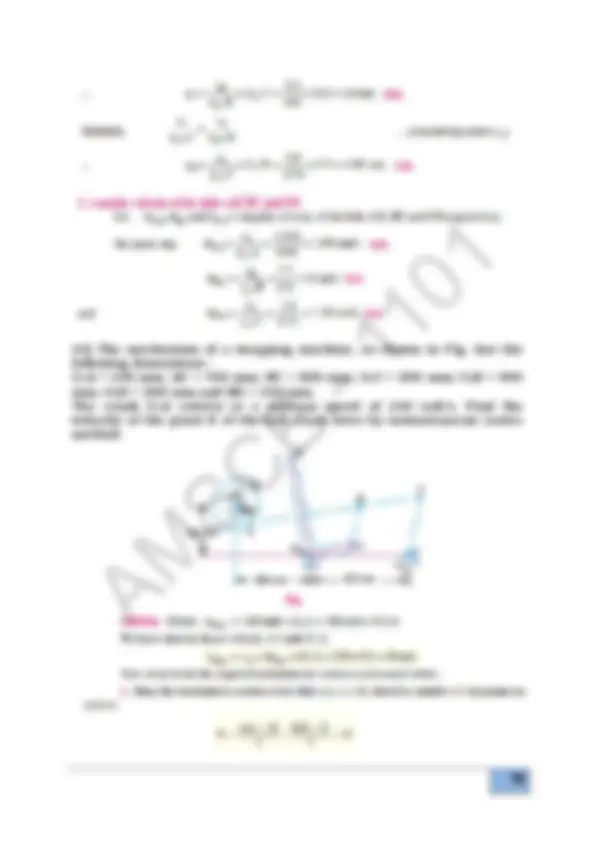
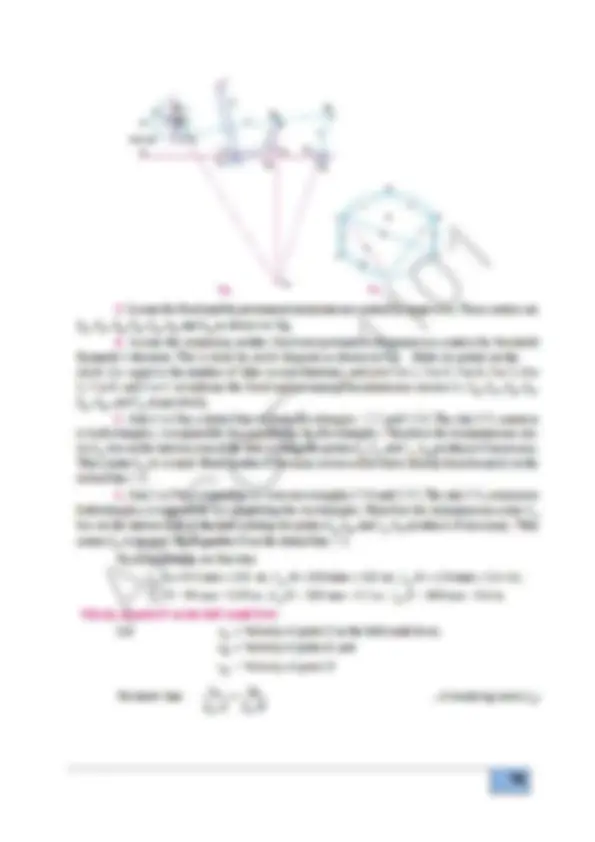
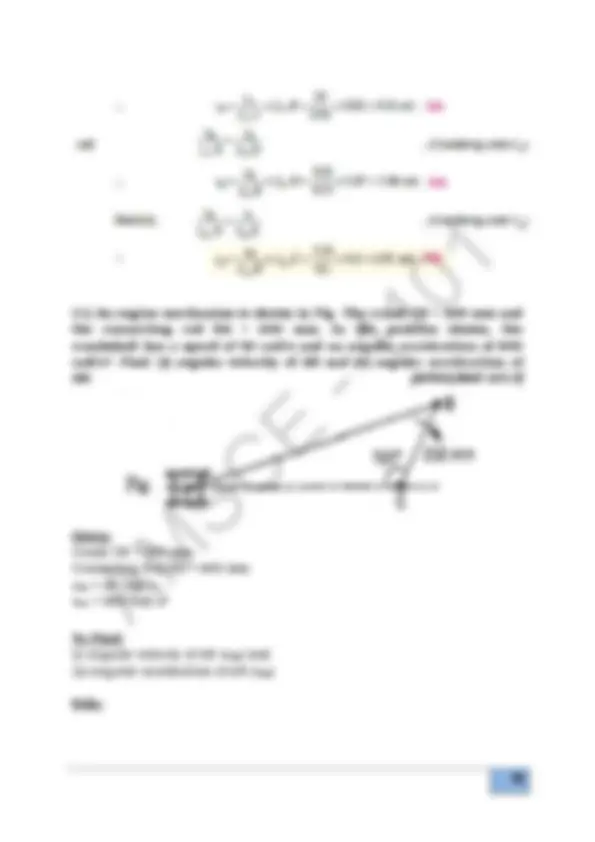
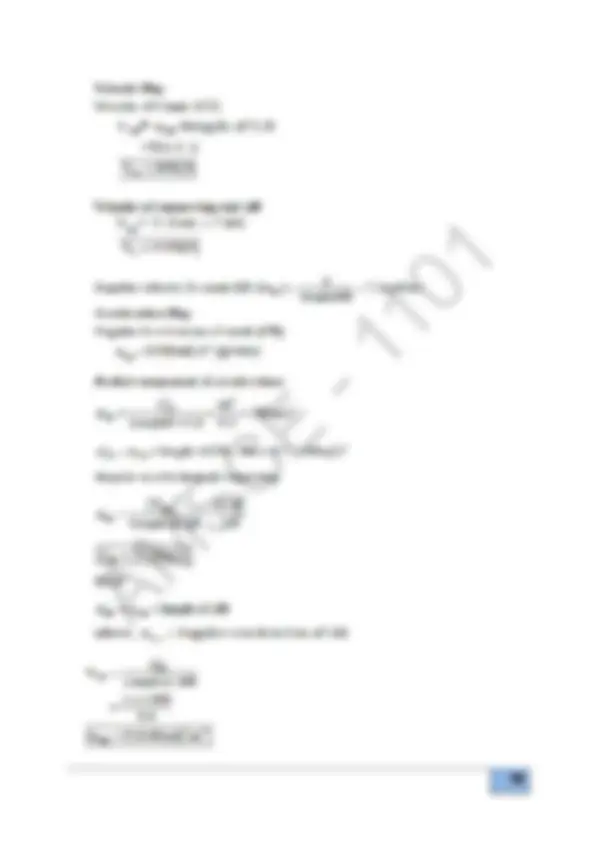
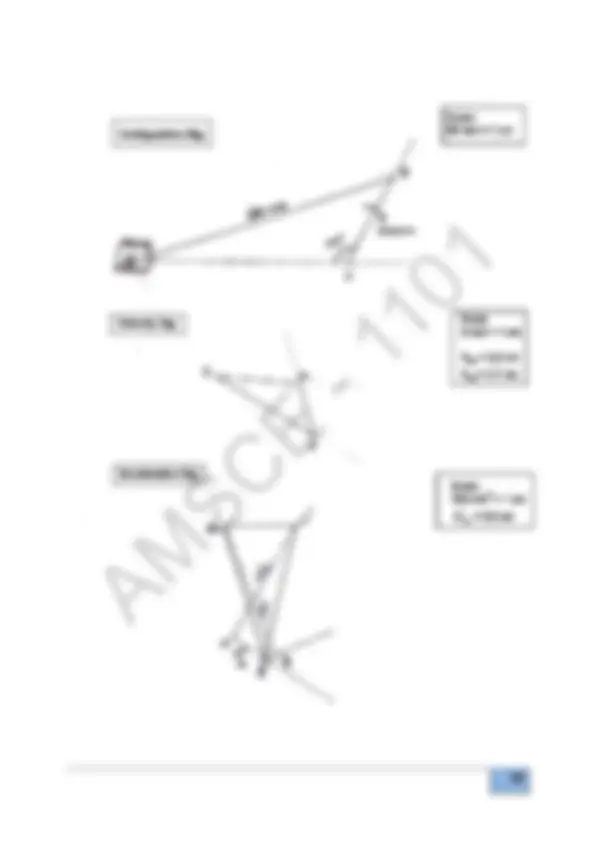
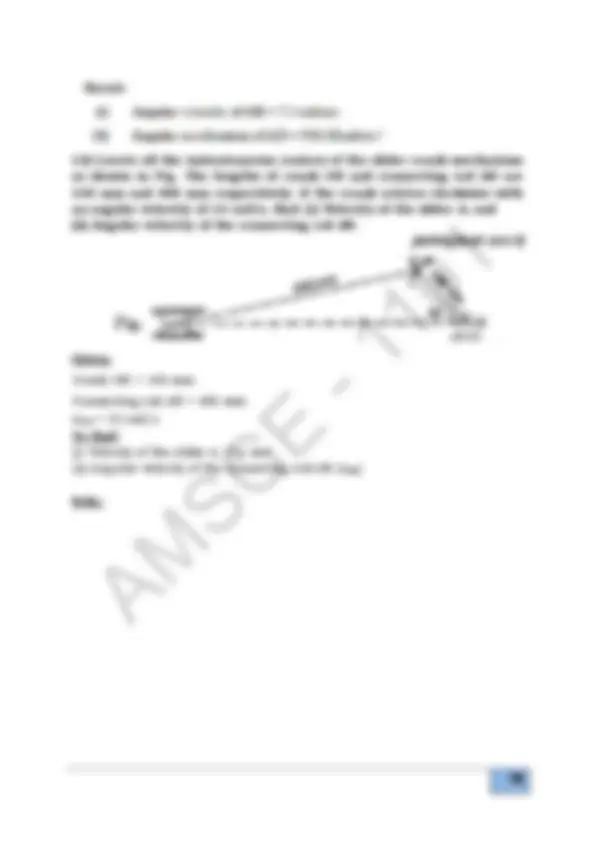
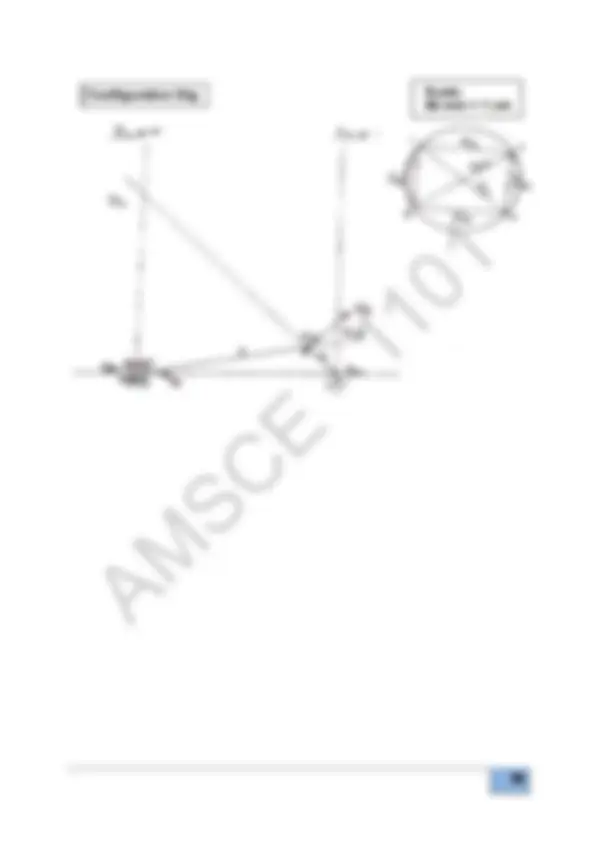
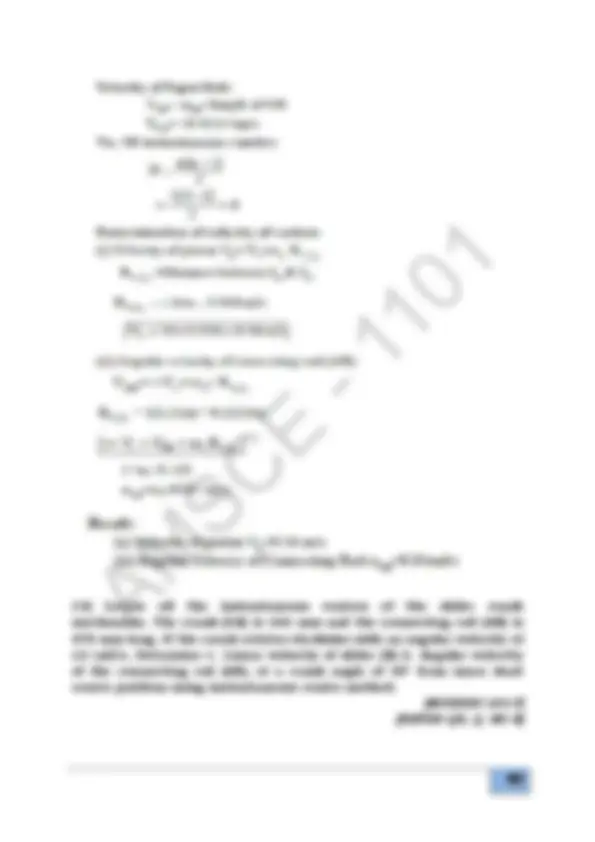
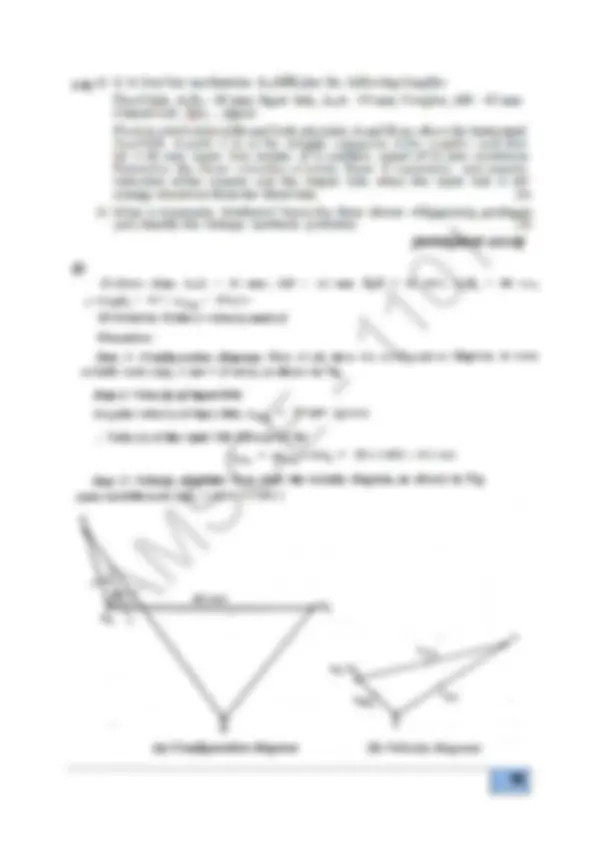
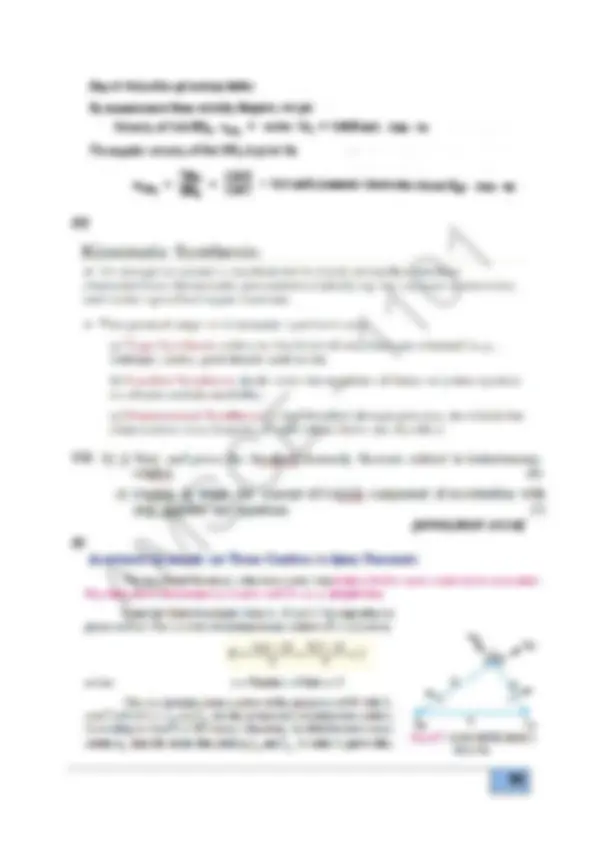
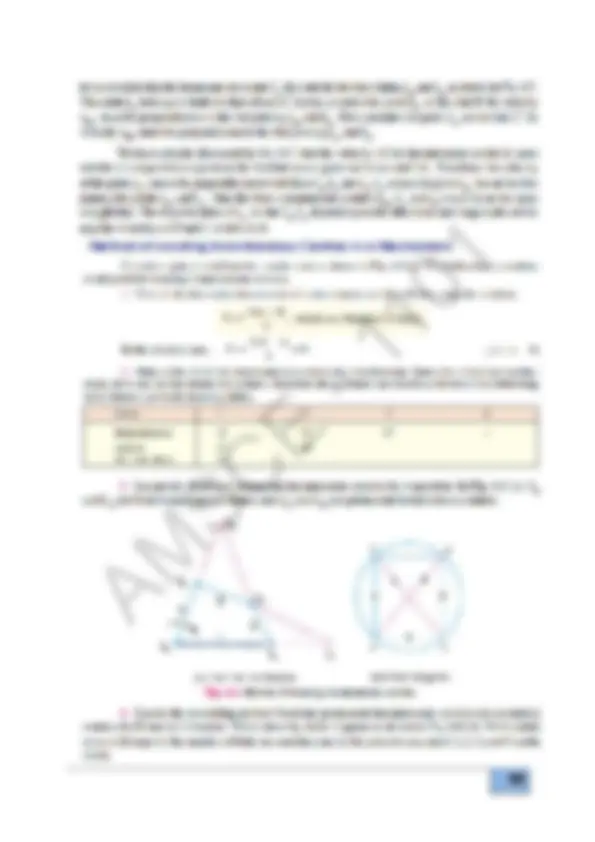
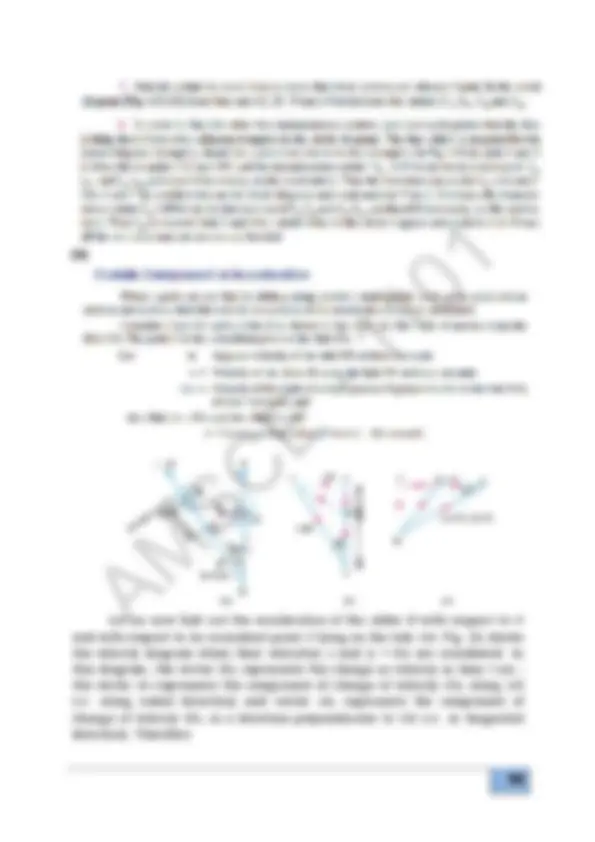
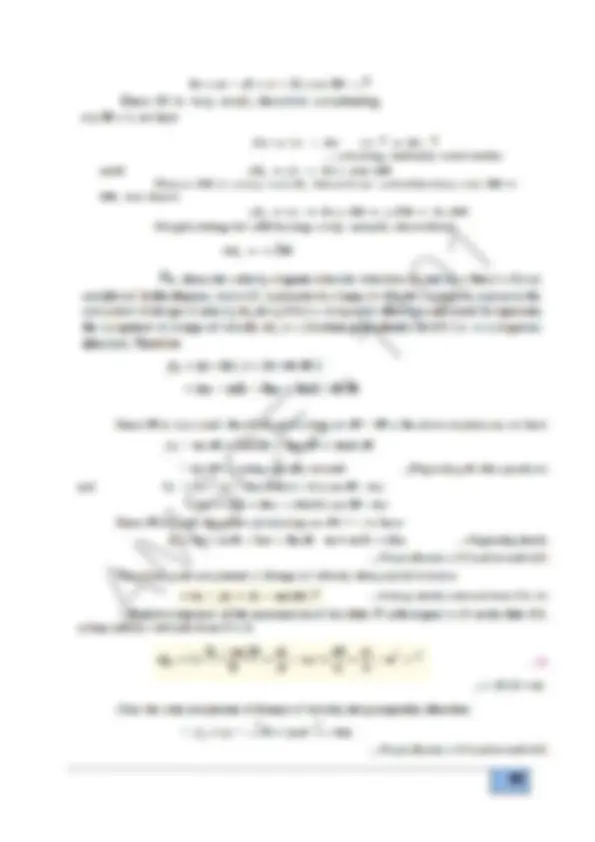
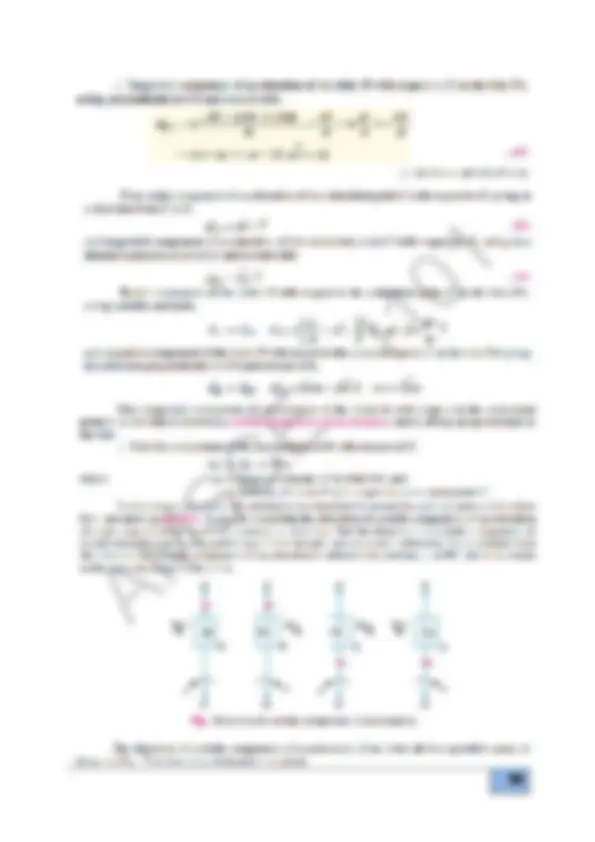
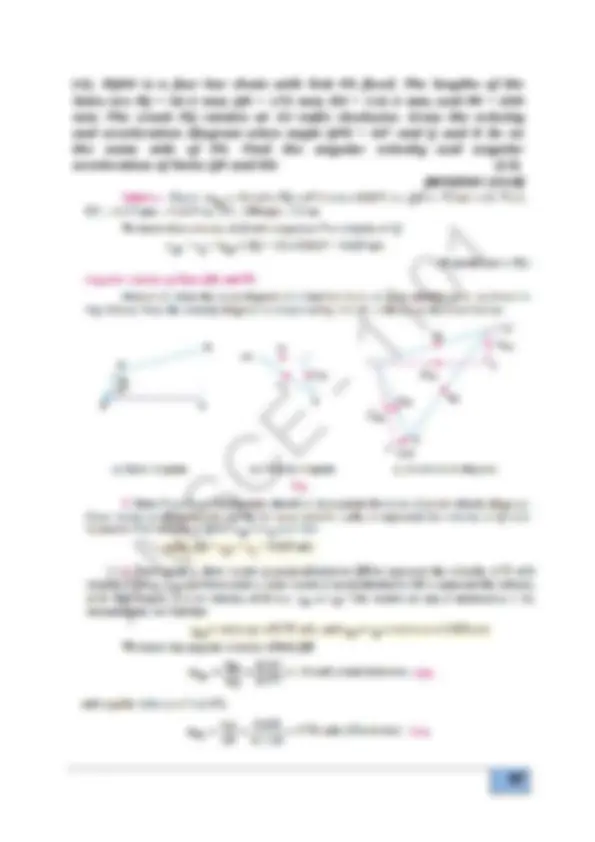
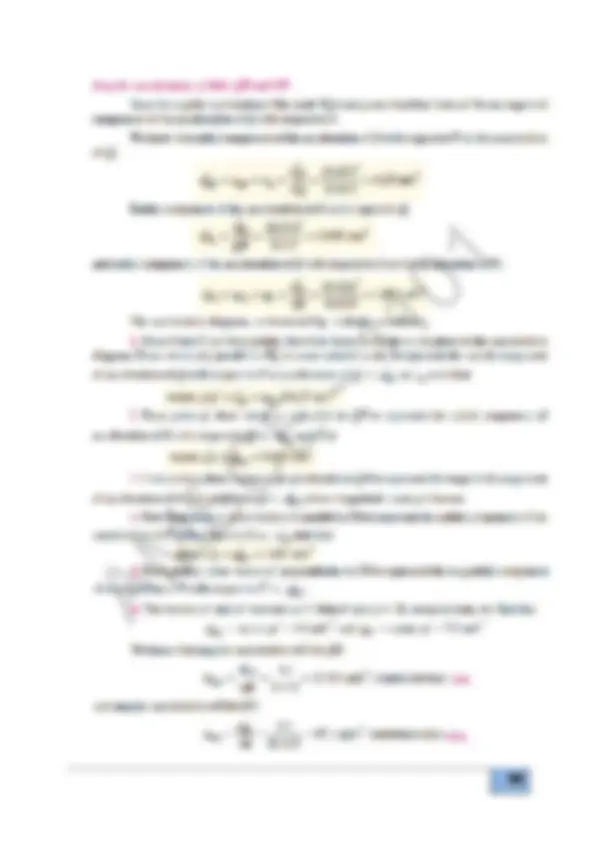
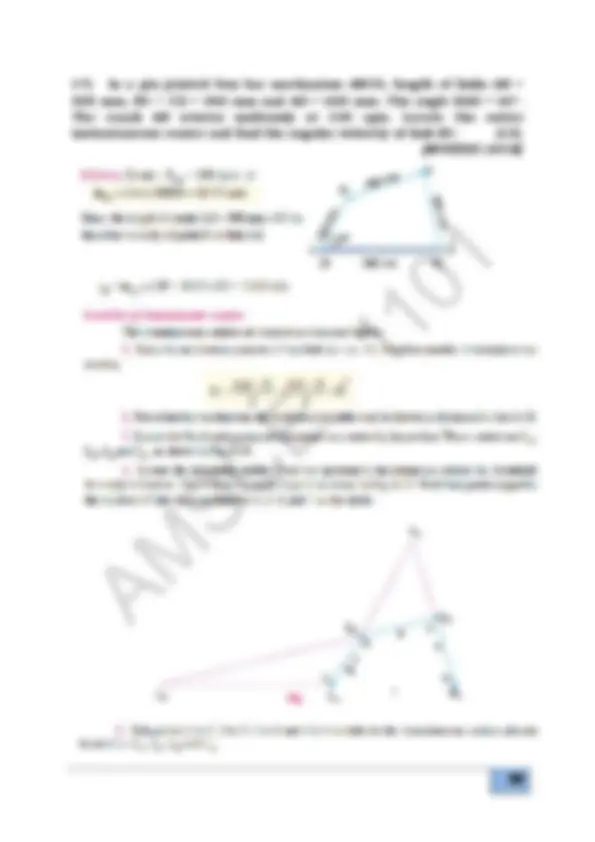
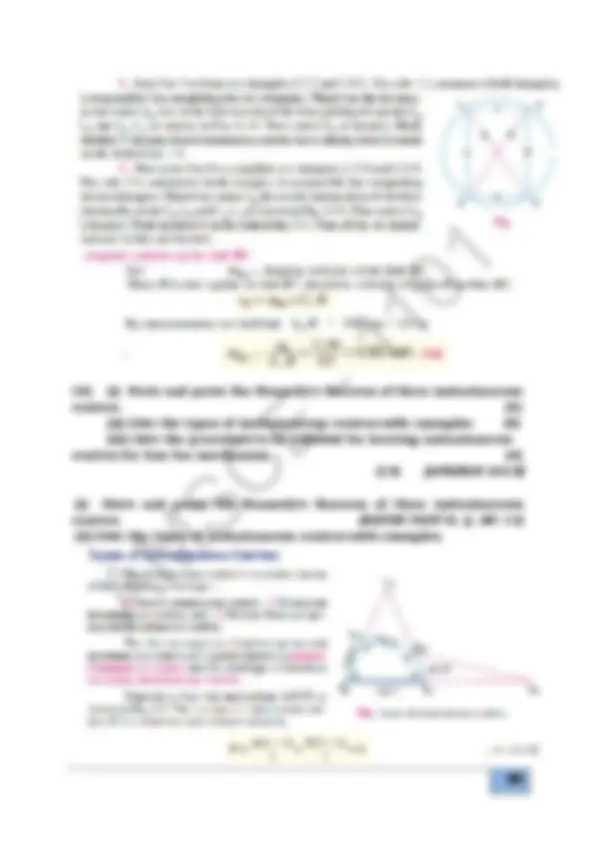
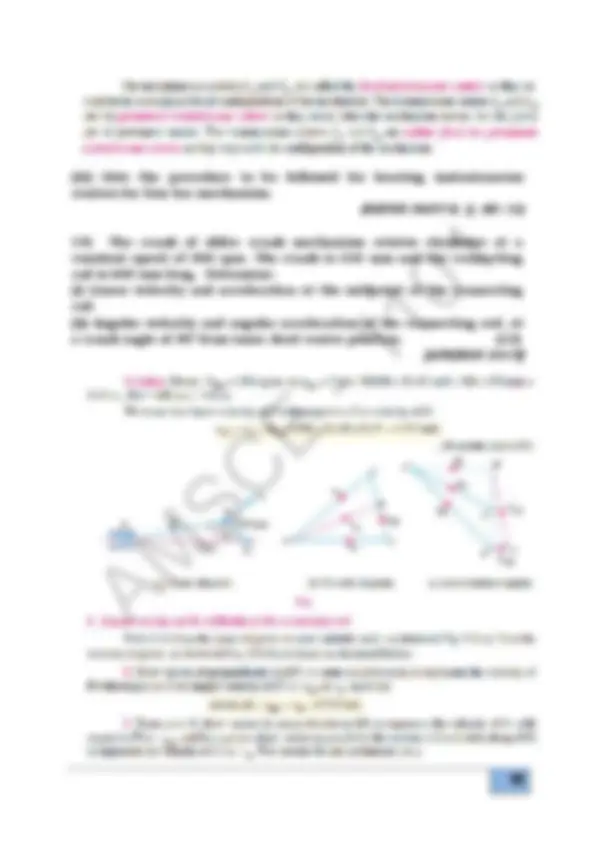
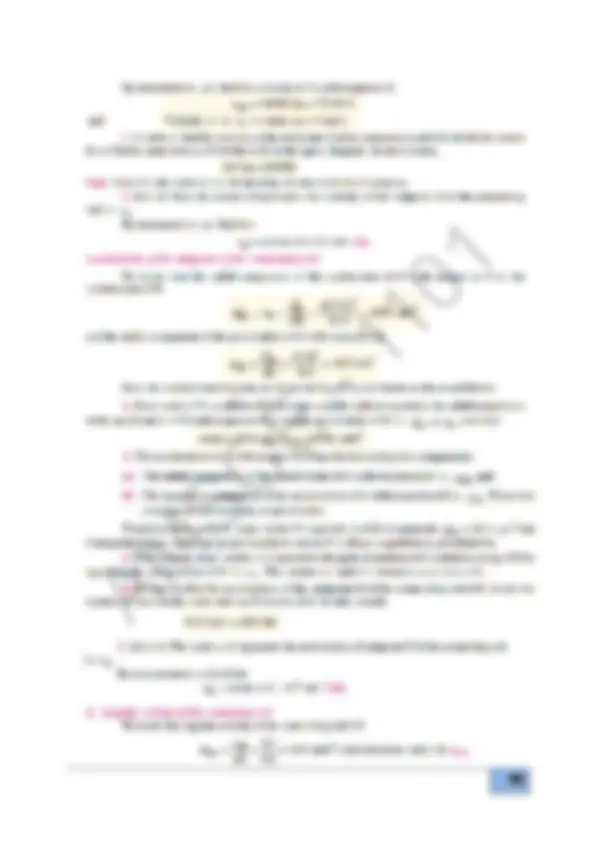
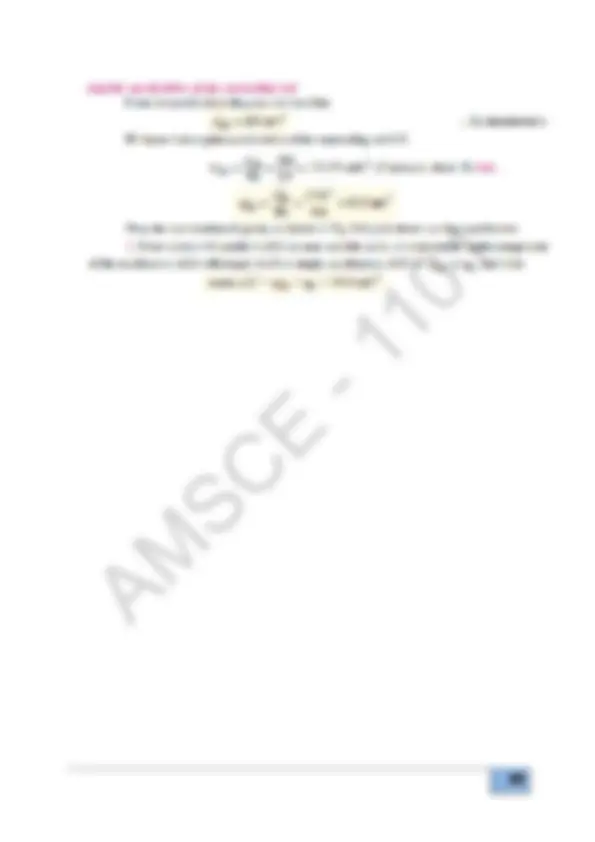
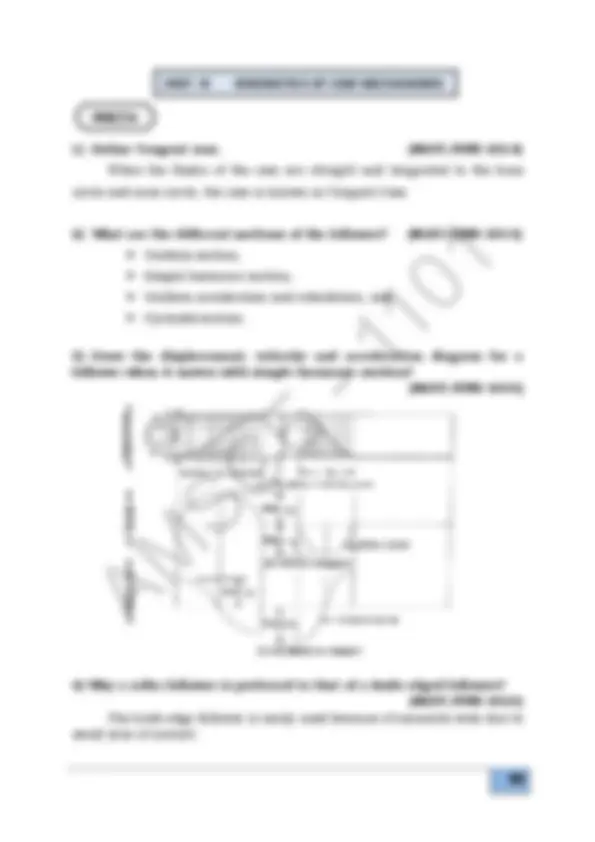
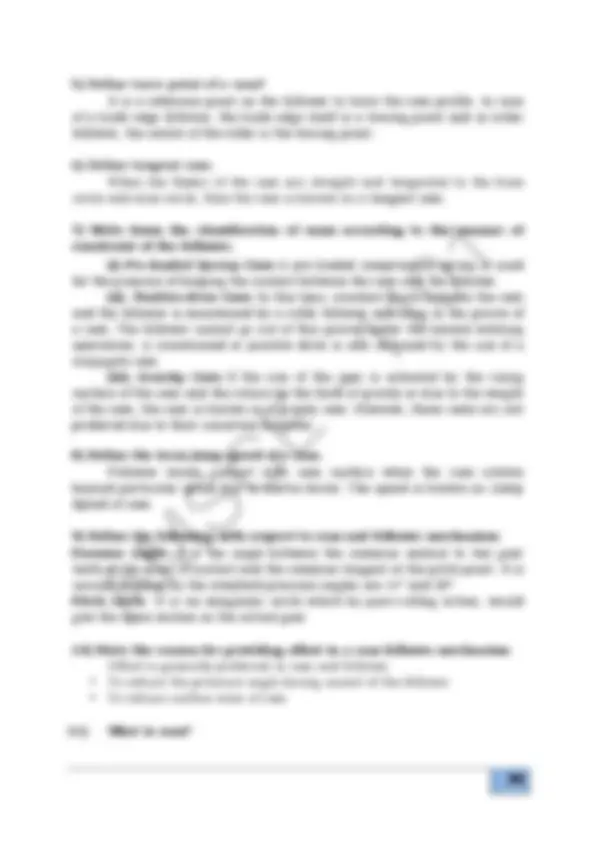

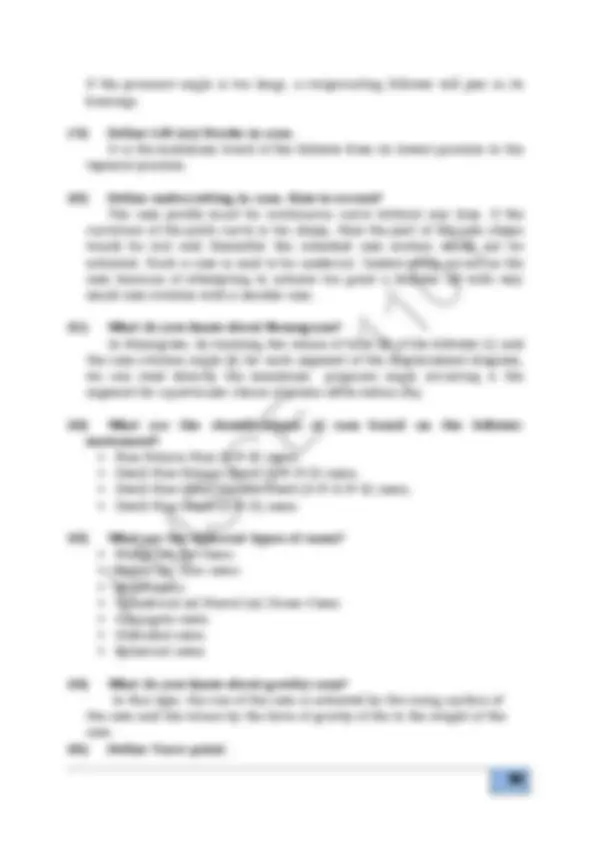
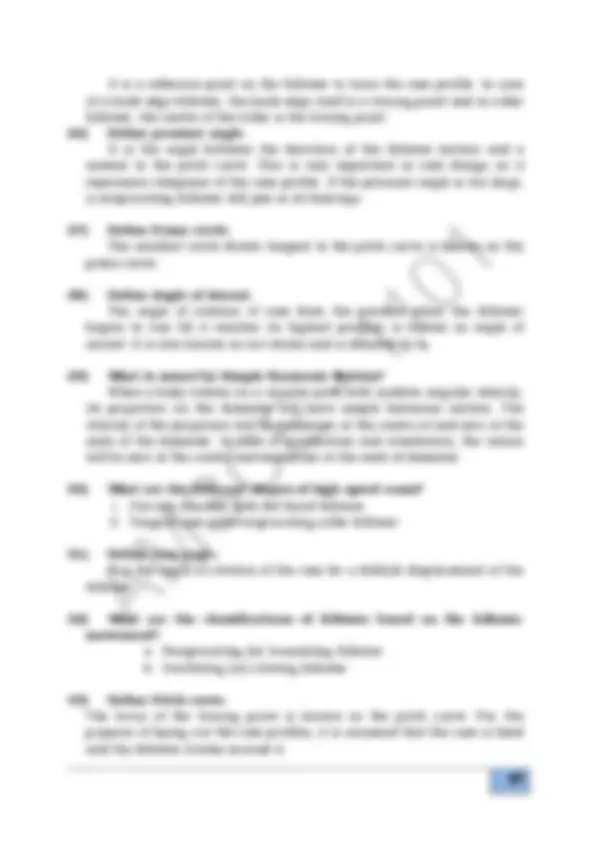
Study with the several resources on Docsity
Earn points by helping other students or get them with a premium plan
Prepare for your exams
Study with the several resources on Docsity
Earn points to download
Earn points by helping other students or get them with a premium plan
Community
Ask the community for help and clear up your study doubts
Discover the best universities in your country according to Docsity users
Free resources
Download our free guides on studying techniques, anxiety management strategies, and thesis advice from Docsity tutors
ME 8492 – KINEMATICS OF MACHINERY QUESTION BANK QUESTION PAPERS FROM 2012
Typology: Quizzes
1 / 273
This page cannot be seen from the preview
Don't miss anything!
1. Differentiate between Machine and Structure. (MAY/JUNE 2014) Machine Mechanism Machine is a mechanism or collection of mechanism which transmits force from the source of power to the resistance (load) to overcome and thus performs useful mechanical work.
Combination of rigid or resistant bodies connected that they move upon each other with definite relative motion
E.g Lathe, Shaping Machine etc. E.g single slider mechanism in IC engine All machines are mechanism All mechanisms are not Machine
2. Classify the constrained motion.(MAY/JUNE 2014)
Constrained motions are classified into three types Completely constrained motion. Incompletely constrained motion. Successfully constrained motion.
3) Determine the number of freedom of the mechanism shown in the figure below: (MAY/JUNE 2015) Using Grublers criterion: F=3(N-1)-2P 1 -P 2 We can determine the degrees of freedom to be F = 3(8-1) - (2x6) - 7 F = 2
4) Write a short notes on completed and incomplete constrains in lower and higher pairs, depict your answer with neat sketches. (MAY/JUNE 2015) A lower pair joint is one in which contact two rigid bodies occurs at every points of one or more surface segments. A higher pair joint is one which contact occurs only at isolated points or along a line segments.
does not deform under the influence of forces is known as a rigid body. Rigid body is ideal. A body is said to be a resistant body , if it does not deform for the purpose for which it is made. Resistant body is rigid for the purpose for which it is used, but is deforms which excess forces act on it. For example the chair, it does not deform if a person sits on it, but it will break if you put a load of 1000 kg on it.
8) The ratio between the width of front axle and that of wheel base of a steering mechanism is 0.44. At the instant when the front inner wheel is turned by 18^0 , which should be the angle burned by the outer front wheel for perfect steering? (NOV/DEC 2014) Using criterion of perfect steering, Cot φ - Cot θ = 0. Cot φ - Cot 18^0 = 0. φ = 15.8^0
9) Define Grubler’s criteria for the mechanism. (NOV/DEC 2015) The following equation is used to describe mobility in 2D or planar systems: M = 3(n-1) – 2 f 1 – f 2 Where, n = total number of links, M = DOF. f 1 = number of 1DOF joints. f 2 = number of 2 DOF joints. This is known as GRUBLER’S EQUATION and is for mobility of planar systems. M = 1 Single input /monitoring necessary M = 2 Double input/output necessary M = - 1 Statically indeterminate structure M = 0 Motion impossible - statically determinate
10) Name any two inversions of the four bar mechanism. (NOV/DEC 2015) Beam engine (crank and lever mechanism). Coupling rod of a locomotive (Double crank mechanism).
11) What is Kinematics? Kinematics is the study of motion (position, velocity, acceleration). A major goal of understanding kinematics is to develop the ability to design a system that will satisfy specified motion requirements. This will be the emphasis of this class.
12) What is Kinetics? Kinetics is the study of effect of forces on moving bodies. Good kinematic design should produce good kinetics.
13) Define Link. A link is defined as a member or a combination of members of a mechanism connecting other members and having relative motion between them. The link may consist of one or more resistant bodies. A link may be called as kinematic link or element. E.g.: Reciprocating steam engine.
14) Define Kinematic Pair. Kinematic pair is a joint of two links having relative motion between them. The types of kinematic pair are classified according to Nature of contact (lower pair, higher pair) Nature of mechanical contact (Closed pair, unclosed pair) Nature of relative motion (Sliding pair, turning pair, rolling pair, screw pair, spherical pair)
15) Define Kinematic Chain. When the kinematic pairs are coupled in such a way that the last link is joined to the first link to transmit definite motion it is called a kinematic chain. E.g.: The crank shaft of an engine forms a kinematic pair with the bearings which are fixed in a pair, the connecting rod with the crank forms a second kinematic pair, the piston with the connecting rod forms a third pair and the piston with the cylinder forms the fourth pair. The total combination of these links is a kinematic chain. E.g.: Lawn mower.
16) Define Degrees of Freedom. It is defined as the number of input parameters which must be independently controlled in order to bring the mechanism in to useful engineering purposes. It is also defined as the number of independent relative motions, both translational and rotational, a pair can have.
25) Write down the Grashof’s law for a four bar mechanism? Grashof’s law states that the sum of the shortest and longest links cannot be greater than the sum of the remaining two links lengths, if there is to be continuous relative motion between two members.
26) What type of kinematic pair exists between human shoulder and arm based on nature of contact and nature of relative motion? (A/M-2017) Spherical or Globular Pair. (Ball & Socket Joint)
27) Sketch and define Transmission angle of a four bar mechanism. (A/M-2017) In a four bar chain mechanism, the angle between the coupler and the follower (driven) link is called as the transmission angle.
28) Define the Grubler’s criterion for plane mechanism with mathematical expression. (N/D-2017) The following equation is used to describe mobility in 2D or planar systems: M = 3(n-1) – 2 f 1 – f 2 Where, n = total number of links, M = DOF. f 1 = number of 1DOF joints. f 2 = number of 2 DOF joints. This is known as GRUBLER’S EQUATION and is for mobility of planar systems. M = 1 Single input /monitoring necessary M = 2 Double input/output necessary M = - 1 Statically indeterminate structure M = 0 Motion impossible - statically determinate
29) Name any two inversions of single slider crank chain. (N/D-2017) Rotary or Gnome Engine Crank & Slotted lever mechanism
Oscillating cylinder mechanism Bull Engine Hand Pump
30) Define kinematic pair and classify it according to the types of contact. (A/M 2018)
I. Depending upon the nature of relative motion between the links
II. Depending upon the nature of relative motion between the links
III. Depending upon the nature of mechanical arrangement between the links
31) Sketch a crank-rocker mechanism and a slider crank mechanism indicating their input and output motions. (A/M 2018) Crank – Rocker Mechanism It consists of four links, each of them forms a turning pair at A, B, C and D. The four links may be of different lengths. In a four bar chain, one of the links, in particular the shortest link, will make a complete revolution relative to the other three links. Such a link is known as C rank. The link BC (link 2) which makes a partial rotation or oscillates is known as lever or Rocker Or Follower and the link CD (link 3) which connects the crank and lever is called Connecting Rod or Coupler. The fixed link AB (link 1) is known as frame of the mechanism. Slider Crank Mechanism
Kinematic Pair
1) Explain the working of two different types of Quick-Return Mechanisms. Derive an expression for the ratio of time taken in forward and return stroke for one of these mechanism. (16) (MAY/JUNE 2014)
This mechanism is mostly used in shaping and slotting machines. In this mechanism, the link CD (link 2) forming the turning pair is fixed, as shown in Fig. The link 2 corresponds to a crank in a reciprocating steam engine. The driving crank CA (link 3) rotates at a uniform angular speed. The slider (link 4) attached to the crank pin at A slides along the slotted bar PA (link 1) which oscillates at a pivoted point D. The connecting rod PR carries the ram at R to which a cutting tool is fixed. The motion of the tool is constrained along the line RD produced, i.e. along a line passing through D and perpendicular to CD.
When the driving crank CA moves from the position CA 1 to CA 2 (or the link DP from the position DP 1 to DP 2 ) through an angle α in the clock wise direction, the tool moves from the left hand end its stroke to the hand end through a distance 2PD. Now when the driving crank moves from the position CA 1 to CA 2 (or the link DP from DP 2 to DP 1 ) through an angle β in the clockwise direction, the tool moves back from right hand end of its stroke to the left hand end. A little consideration will show that the time taken during the left to right movement of the ram(i.e during forward or cutting stroke) will be equal to the time taken by the driving crank to move from CA 1 to CA 2. Silimilarly, the time taken during the right to left movement of the ram (or during the idle or return stroke) will be equal to the time by the driving crank to mive from CA 2 to CA 1.
PART-b
Since the crank link CA rotates at uniform angular velocity therefore time taken during the cutting stroke (or forward stroke) is more than time taken during the returns stroke. In other words, the mean speed of the ram during cutting stroke is less than the mean speed during the return stroke. The ratio between the time taken during the cutting and return strokes is given by
Time of cutting stroke 360 or Time of return stroke 360
This mechanism is mostly used in shaping machines, slotting machines and in rotary internal combustion engines. In this mechanism, the link AC (i.e. link 3) forming the turning pairs is first, as shown in fig. the link 3 corresponds to the connecting rod of a reciprocating steam engine. The driving crank CB revolves with uniform angular speed about the fixed centreC. A silding block attached to the craknk pin at B slides along the slotted bar AP and thus causes AP to oscillate about the pivotd point A. A short link PR transmits the motion from AP to the ram which carries the tool and reciprocates along the line of stroke R 1 , R 2. The line of stroke of the ram (i.e. R 1 and R 2 ) is perpendicular to ACC produced.
Inversions of Four Bar Chain:
1. First Inversion (Crank & Lever Mechanism):
If any of the adjacent links of link d, i.e., link a or c is fixed. The link d (crank) can have full revolution and the link (b) opposite to it oscillates. Application: Beam Engine (Crank & Lever Mechanism)
When the crank rotates about the fixed centre A and the lever oscillates about a fixed centre D. The purpose of this mechanism is to convert rotary motion into reciprocating motion.
2. Second Inversion (Double Crank mechanism):
If the shortest link (d) is fixed then the links a and c rotates full circle and link b also complete one revolution relative to fixed link d.
Application: Coupling Rod of a Locomotive (Double Crank Mechanism)
It is meant for transmitting rotary motion from one wheel to the other wheel.
3. Third Inversion (Double Lever Mechanism): If the link opposite to the shortest link. i.e., link b is fixed and the two links a and c would oscillate.
Application: Watt’s indicator (Double Lever Mechanism):
It consists of four links which are: Fixed link at A, link AC, link CE and link BFD. The links CE and BFD act as lever. It is also called Watt’s straight line mechanism and the dotted line shows the position of the mechanism.
words, the purpose of this mechanism is to convert rotary motion into reciprocating motion.
2. Coupling rod of a locomotive (Double crank mechanism): The mechanism of a coupling rod of a locomotive (also known as double crank mechanism) which consists of four links, is shown in Fig. In this mechanism, the links AD and BC (having equal length) act as cranks and are connected to the respective wheels. The link CD acts as a coupling rod and the link AB is fixed in order to maintain a constant centre to centre distance between them. This mechanism is meant for transmitting rotary motion from one wheel to the other wheel. 3. Watt’s indicator mechanism (Double lever mechanism): A *Watt’s indicator mechanism (also known as Watt's straight line mechanism or double lever mechanism) which consists of four links, is shown in Fig. The four links are : fixed linkat A , link AC , link CE and link BFD. It may be noted that BF and FD form one link because these two parts have norelative motion between them. The links CE and BFD actas levers. The displacement of the link BFD is directlyproportional to the pressure of gas or steam which acts onthe indicator plunger. On any small displacement of themechanism, the tracing point E at the end of the link CE traces out approximately a straight line.The initial position of the mechanism is shown inFig. by full lines whereas the dotted lines show theposition of the mechanism when the gas or steam pressureacts on the indicator plunger.
4) Sketch and describe the working of two different types of quick return mechanisms. Give examples of their applications. Derive an expression for the ratio of times taken in forward and return stroke for one of these mechanisms. (MAY/JUNE 2015)
This mechanism is mostly used in shaping and slotting machines. In this mechanism, the link CD (link 2) forming the turning pair is fixed, as shown in Fig. The link 2 corresponds to a crank in a reciprocating steam engine. The driving crank CA (link 3) rotates at a uniform angular speed. The slider (link 4) attached to the crank pin at A slides along the slotted bar PA (link 1) which oscillates at a pivoted point D. The connecting rod PR carries the ram at R to which a cutting tool is fixed. The motion of the tool is constrained along the line RD produced, i.e. along a line passing through D and perpendicular to CD.
When the driving crank CA moves from the position CA 1 to CA 2 (or the link DP from the position DP 1 to DP 2 ) through an angle α in the clock wise direction, the tool moves from the left hand end its stroke to the hand end through a distance 2PD.
In the extreme positions, AP 1 and AP 2 are tangential to the circle and the cutting tool is at the end of the stroke. The forward or cutting stroke occurs when the crank rotates from the position CB 1 to CB 2 (or through an angle β) in the clock wise directions. The return stroke occurs when the crank rotates from the positions CB 2 to CB 1 (or through angle α) in the clock wise directions. Since the crank has uniform angular speed. Time of cutting stroke 360 or Time of return stroke 360
Since the tool travels a distance of R 1 R 2 during cutting and return stroke, therfore travel of the tool or length of stroke
1 2 1 2 1 1 1
1
1
From fig, we see that the angle β made by the forward or cutting stroke is greater than the angle α described by the return stroke. Since the crank rotates with uniform angular speed, therefore the returns stroke is completed within shorter time. Thus it is called quick return motion mechanism.
5). (a) (i) Classify kinematic pairs based on Degrees of Freedom. (10) (MAY/JUNE 2016) The two links or elements of a machine, when in contact with each other, are said to form a pair. If the relative motion between them is completely or successfully constrained (i.e. in a definite direction), the pair is known as kinematic pair.
Types of Constrained Motions:
(i) Completely constrained motion: When the motion between a pair is limited to a definite direction irrespective of the direction of force applied, then the motion is said to be a completely constrained motion. For example, the piston and cylinder (in a steam engine) form a pair and the motion of the piston is limited to a definite direction (i.e. it will only reciprocate) relative to the cylinder irrespective of the direction of motion of the crank, as shown in Fig.
(ii) Incompletely constrained motion: When the motion between a pair can take place in more than one direction, then the motion is called an incompletely constrained motion. The change in the direction of impressed force may alter the direction of relative motion between the pair. A circular bar or shaft in a circular hole, as shown in Fig., is an example of an incompletely constrained motion as it may either rotate or slide in a hole. These both motions have no relationship with the other.
(iii) Successfully / partially constrained motion: When the motion between the elements, forming a pair, is such that the constrained motion is not completed by itself, but by some other means, then the motion is said to be successfully constrained motion. Consider a shaft in a foot-step bearing as shown in Fig. The shaft may rotate in a bearing or it may move upwards. This is a case of incompletely constrained motion. But if the load is placed on the shaft to prevent axial upward movement of the shaft, then the motion of the pair is said to be successfully constrained motion. The motion of an I.C. engine valve (these are kept on their seat by a spring) and the piston reciprocating inside an engine cylinder are also the examples of successfully constrained motion.
(ii) What is an inversion and list its properties. (2+4) The method of obtaining different mechanisms by fixing different links in a kinematic chain is known as Inversion of the Mechanism. Properties : It may be noted that the relative motions between the various links is not changed in any manner through the process of inversion. The absolute motions (those measured with respect to the fixed link) may be changed drastically.