
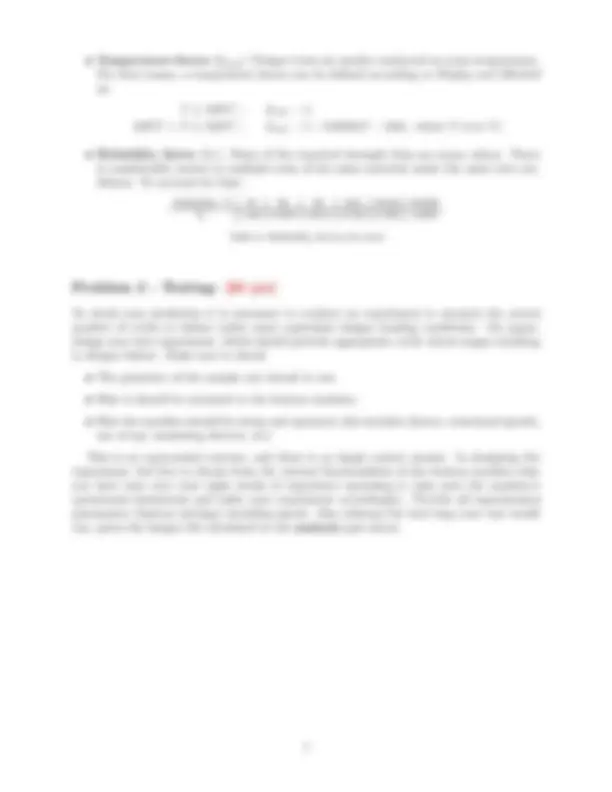
Study with the several resources on Docsity
Earn points by helping other students or get them with a premium plan
Prepare for your exams
Study with the several resources on Docsity
Earn points to download
Earn points by helping other students or get them with a premium plan
Community
Ask the community for help and clear up your study doubts
Discover the best universities in your country according to Docsity users
Free resources
Download our free guides on studying techniques, anxiety management strategies, and thesis advice from Docsity tutors
It is part of a Mechanical Systems Lab course and references J.A. Collins's textbook, *Design of Machine Elements and Machines* (section 5.6). The homework consists of two problems: (1) analyzing the fatigue life of a steel-alloy square bar under axial cyclic forces using factors such as load, size, surface finish, temperature, and reliability, and (2) designing an experiment to test fatigue failure using the Instron machine, detailing sample geometry, mounting, settings, and estimated duration. The assignment integrates analytical calculations with experimental design to reinforce theoretical knowledge through practical application. Students are expected to apply methodologies for predicting fatigue life, consider environmental and material factors, and demonstrate proficiency with mechanical testing equipment, aligning with the course's goal of bridging theoretical and experimental engineering practices.
Typology: Assignments
1 / 2
This page cannot be seen from the preview
Don't miss anything!
Note that homework#6 is graded as half of a lab report. Reading materials: “Prediction of fatigue failure” from J. A. Collins, Design of machine elements and machines, section 5.6 (Pages 241 to 281).
A 230 mm by 230 mm square bar is subjected to an axial cyclic force that ranges from 9000 kN (tension) to -6000 kN (compression). The material is a steel-alloy with hot-rolled finish, ultimate tensile strength of 600 MPa and yield strength of 300 MPa. The part is subjected to an operating environment where temperatures reach a maximum of 500oC. How many cycles of operation could be expected from this part if a reliability level of 99% is desired? Use the following set of equations to calculate the necessary knockdown factors, note that kld and ktmp are in addition o the other k’s in Collins Table 5.3.
kld = 0. 7 if instead, axial loading, kld = 1. 0 if bending.
dequiv =
r
, and
dequiv ≤ 8 mm, ksz = 1, 8 mm < dequiv ≤ 250 mm, ksz = 1. 189 d− equiv^0.^097
ksr = A(Sut)b, if ksr > 1 → 1.
Surface finish A [MPa] b Ground 1.58 -0. Machined 4.41 -0. Hot-rolled 57.7 -0. As-forged 272 -0.
Table 1: Coefficients for Shigley and Mischke surface-factor equation.
1
Table 2: Reliability factors for steel
To check your prediction it is necessary to conduct an experiment to measure the actual number of cycles to failure under some equivalent fatigue loading conditions. On paper, design your own experiment, which should provide appropriate cyclic stress ranges resulting in fatigue failure. Make sure to detail:
This is an open-ended exercise, and there is no single correct answer. In designing the experiment, feel free to choose from the various functionalities of the Instron machine that you have seen over your eight weeks of experience operating it (also note the machine’s operational limitations and tailor your experiment accordingly). Provide all experimental parameters (Instron settings) including speed. Also estimate for how long your test would run, given the fatigue life calculated in the analysis part above.
2