
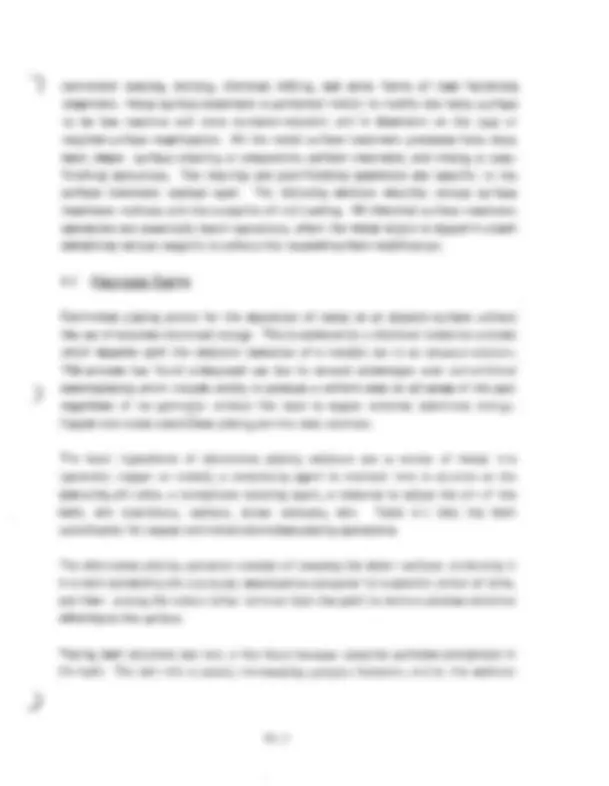
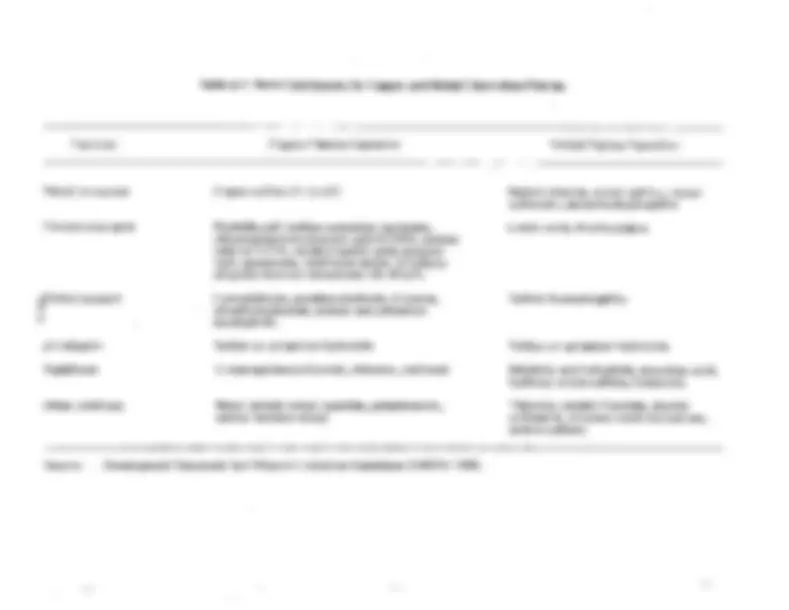
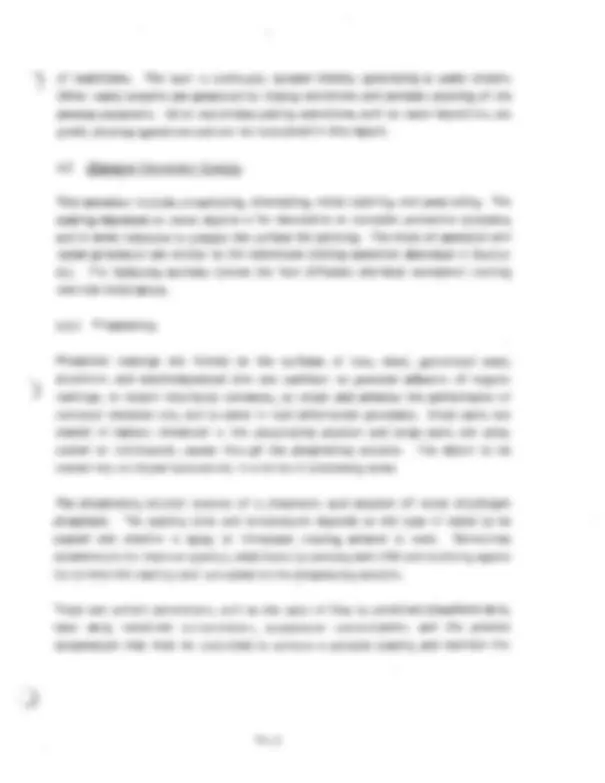
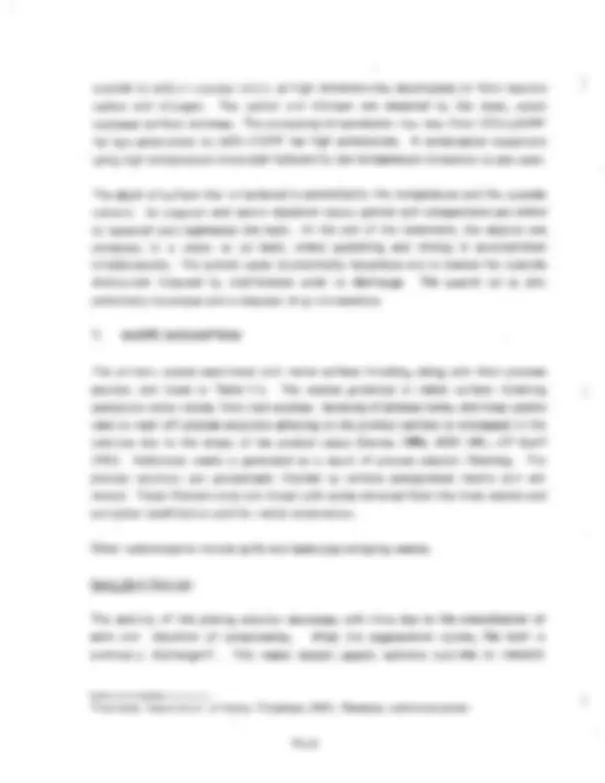
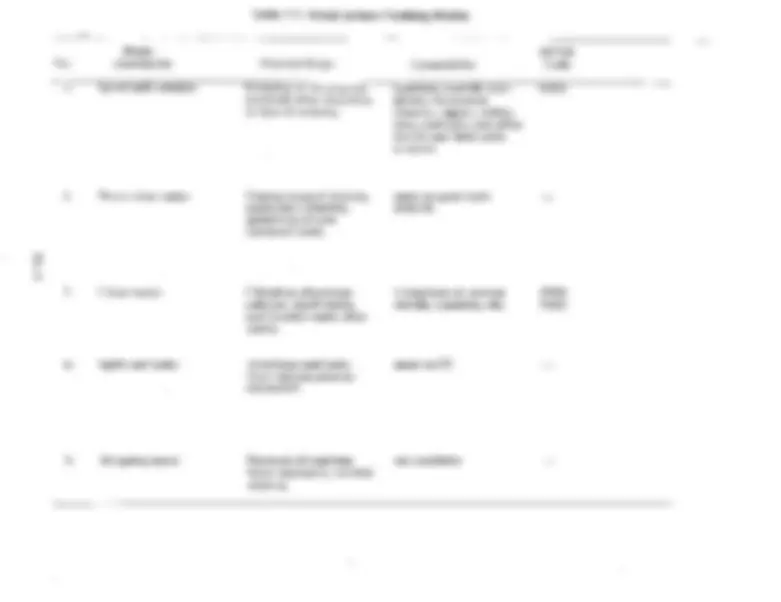
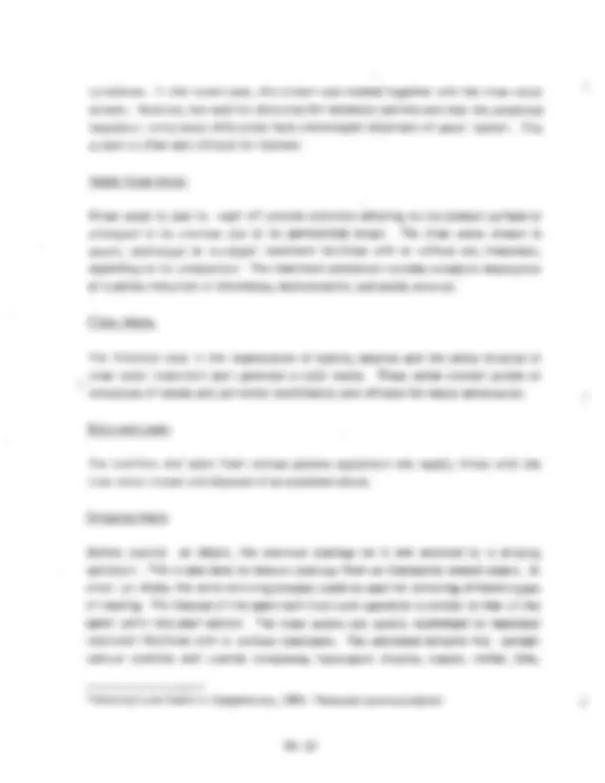
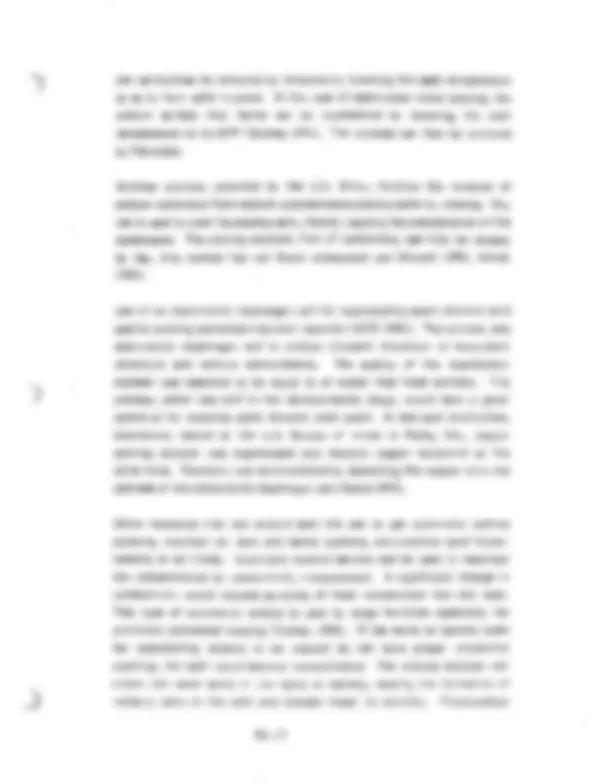
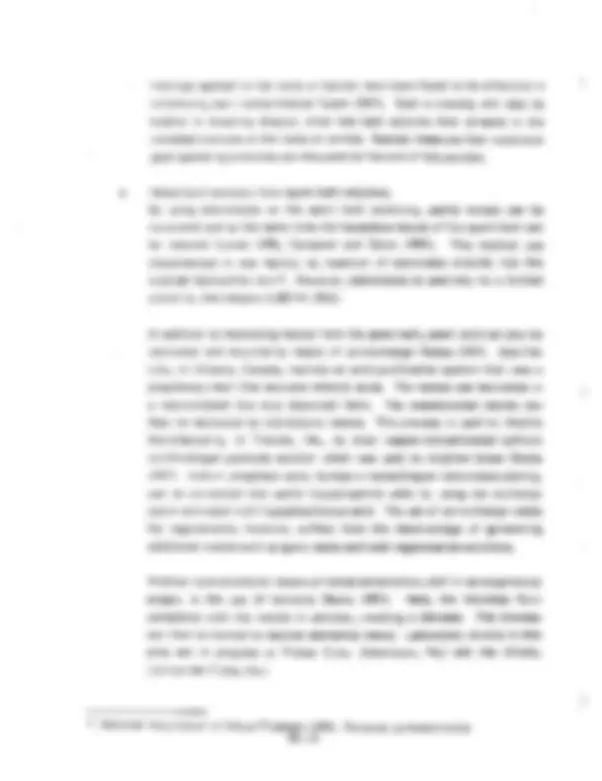
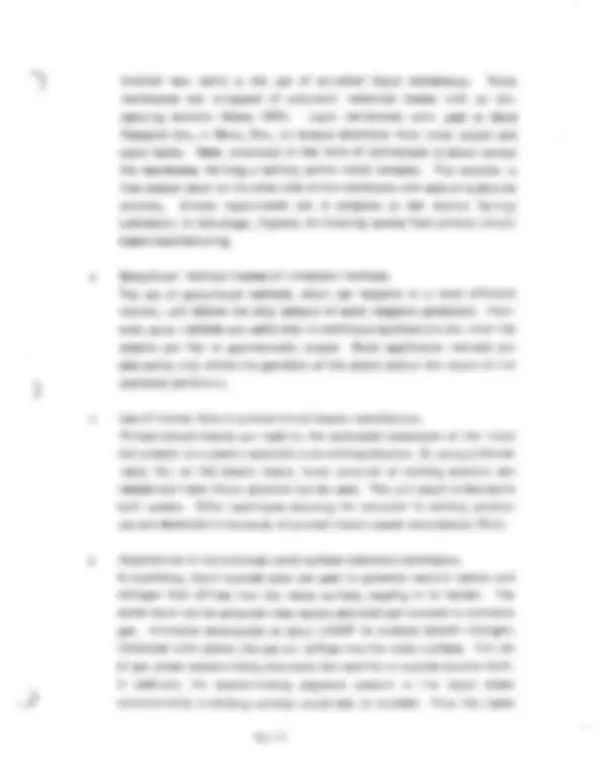
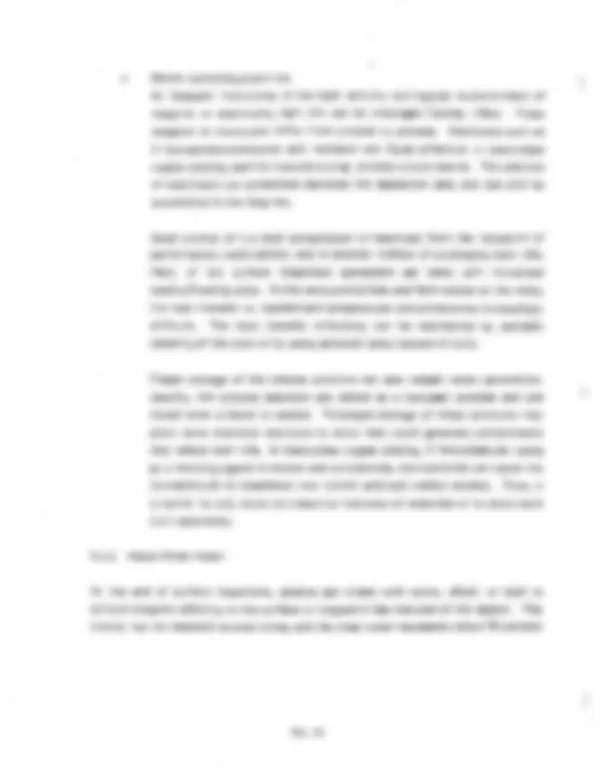
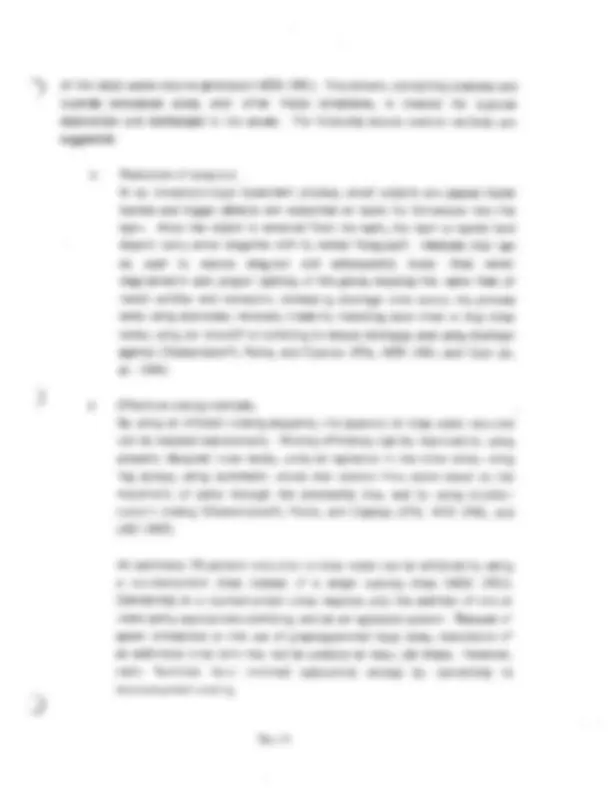
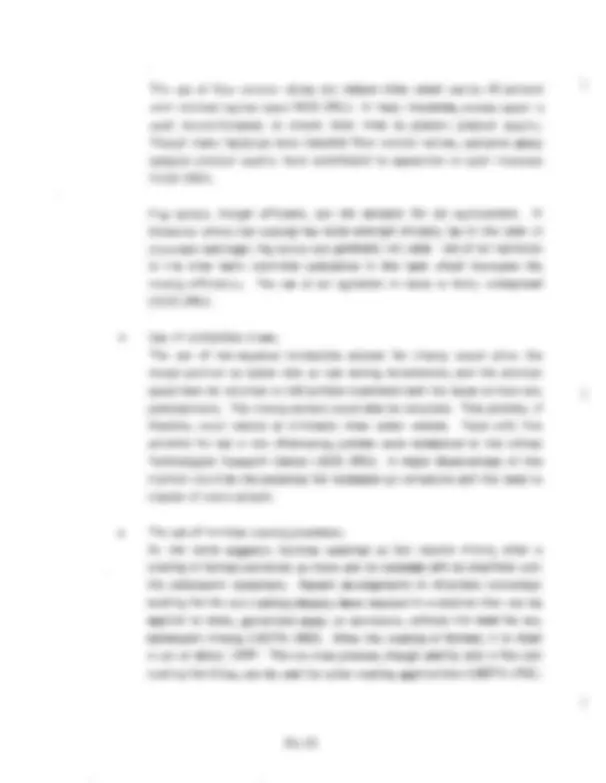
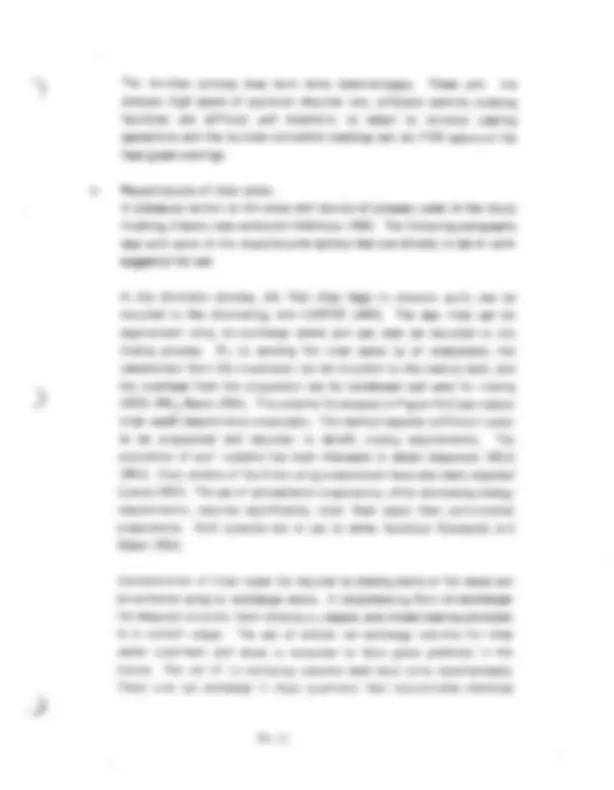
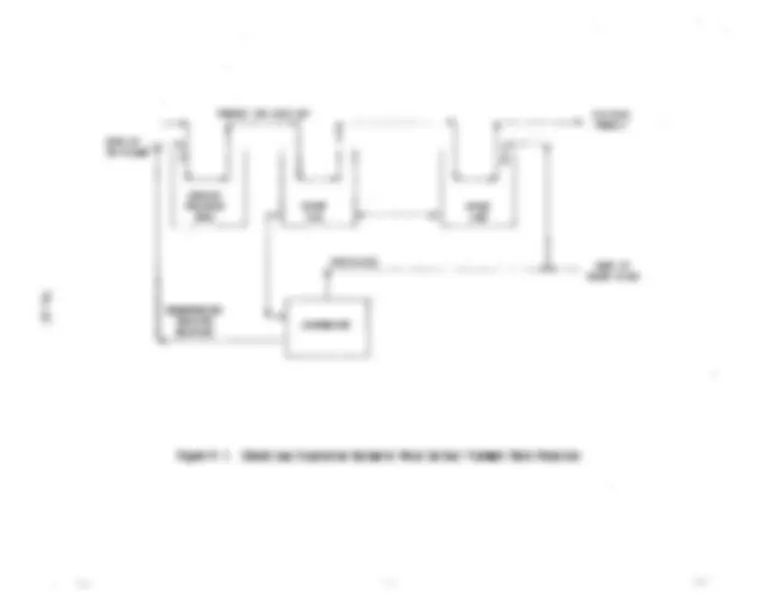
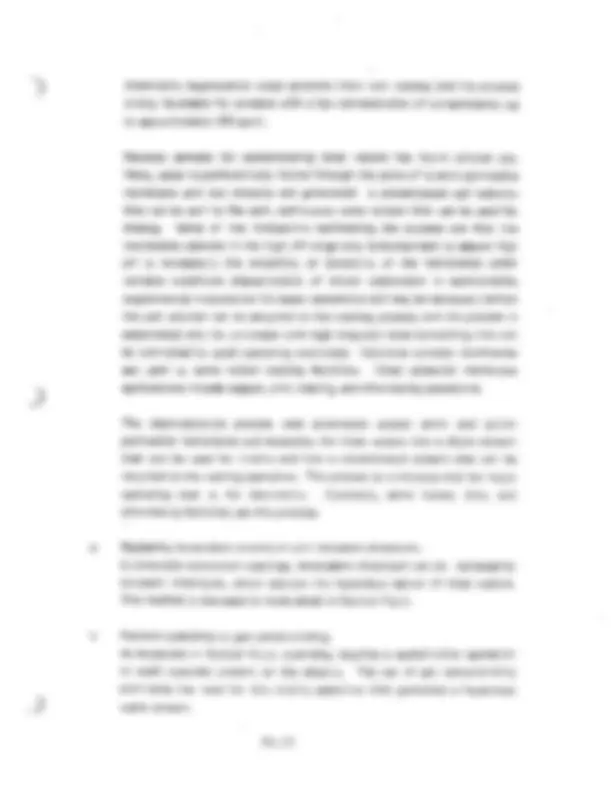
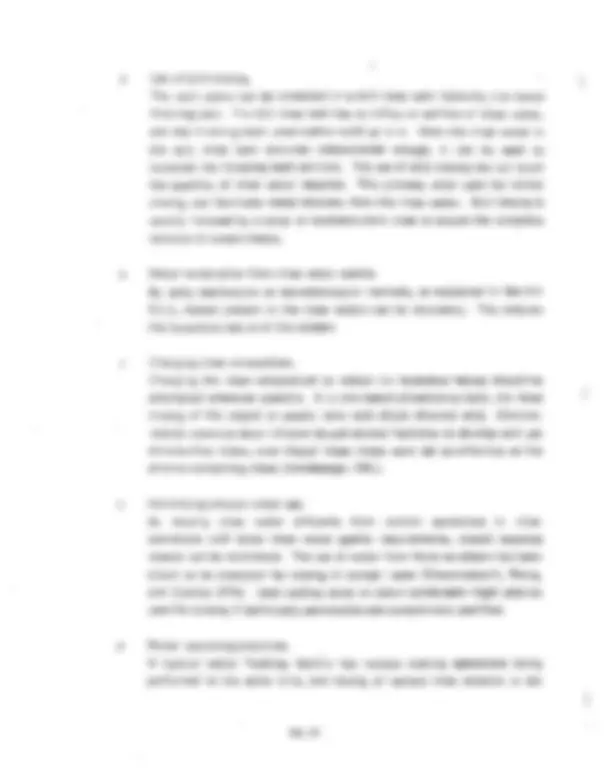
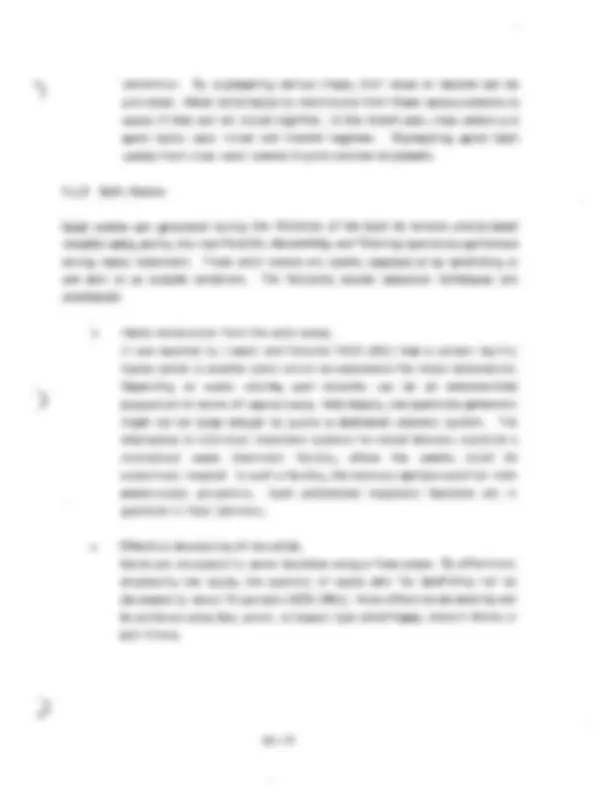
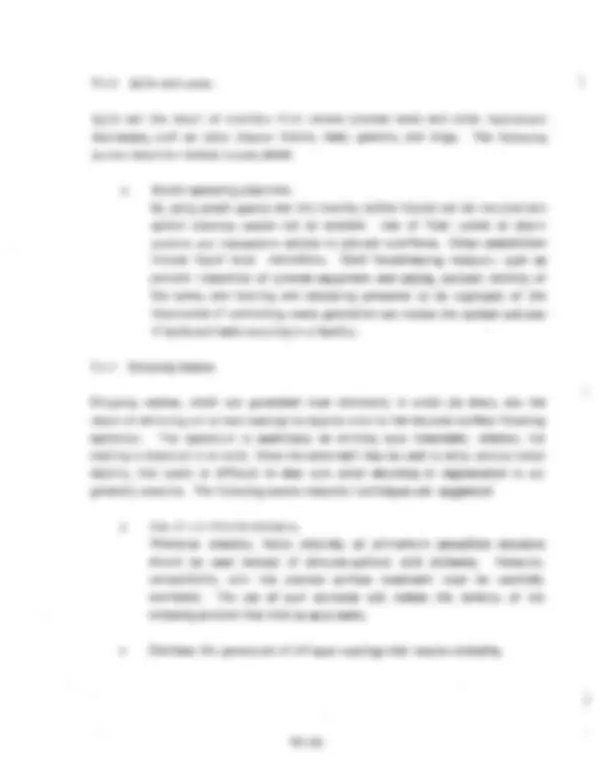
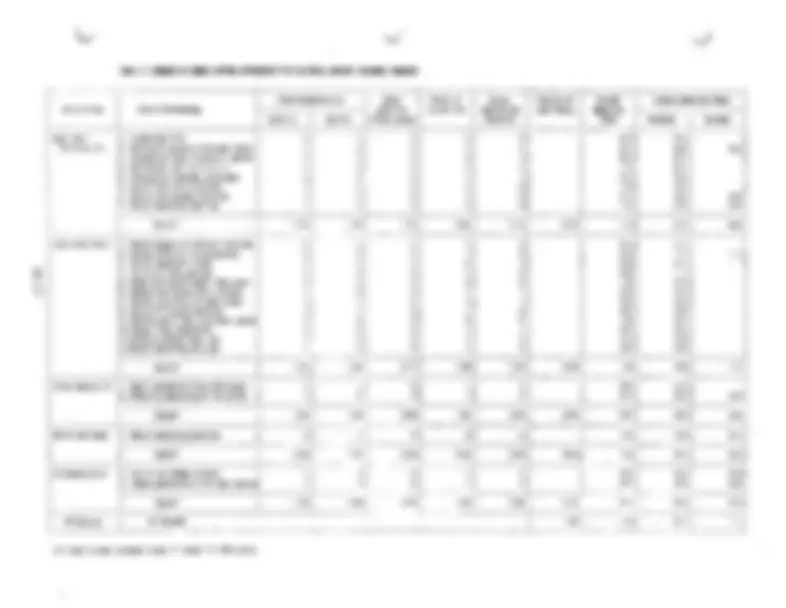
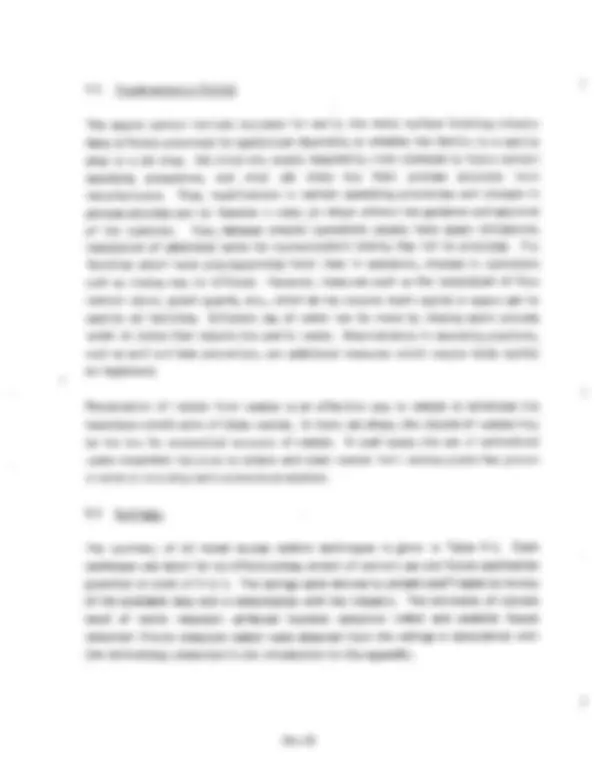
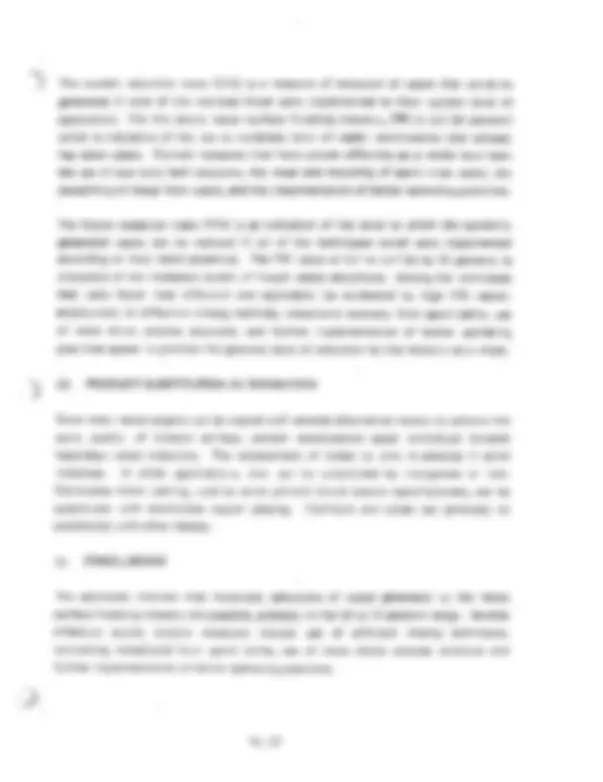

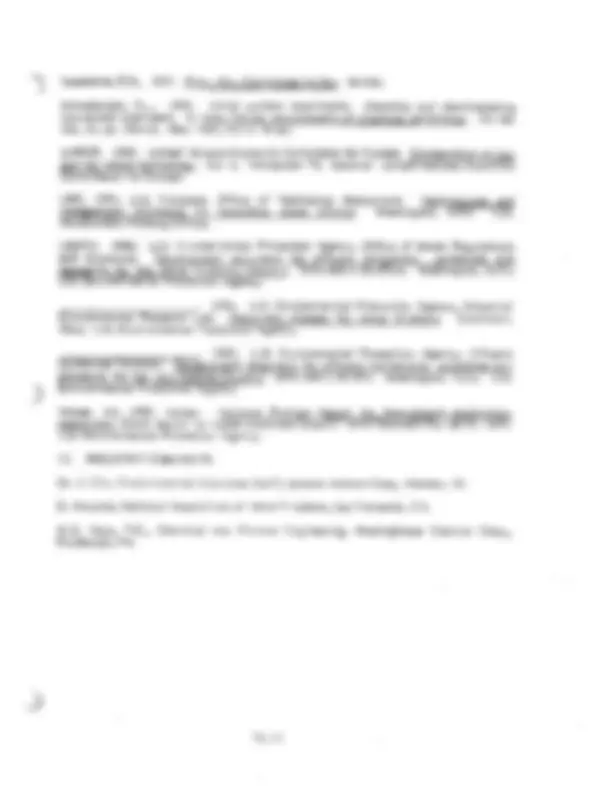
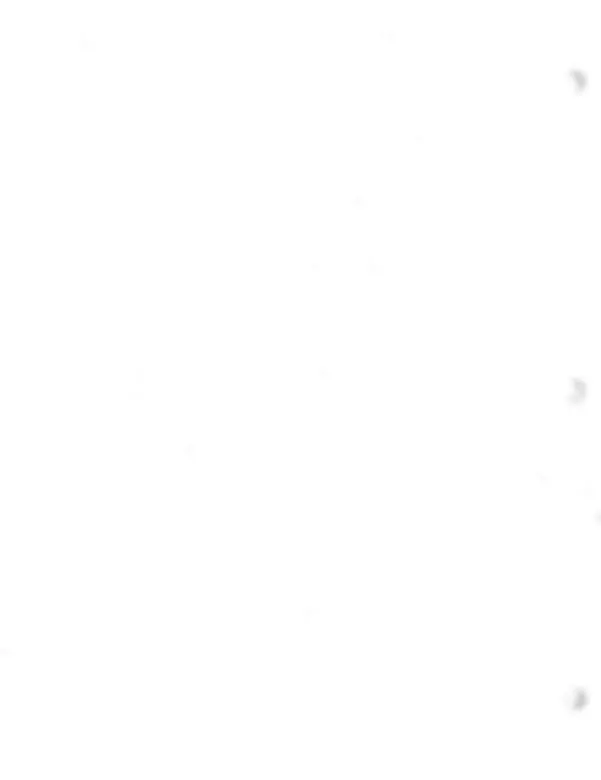
Study with the several resources on Docsity
Earn points by helping other students or get them with a premium plan
Prepare for your exams
Study with the several resources on Docsity
Earn points to download
Earn points by helping other students or get them with a premium plan
Community
Ask the community for help and clear up your study doubts
Discover the best universities in your country according to Docsity users
Free resources
Download our free guides on studying techniques, anxiety management strategies, and thesis advice from Docsity tutors
An overview of metal surface finishing processes, including electroless plating and waste generation. It discusses the basic steps of metal surface treatment, the chemicals used, and the primary wastes produced. The document also explores methods for reducing waste and improving sustainability in metal finishing operations.
What you will learn
Typology: Study notes
1 / 32
This page cannot be seen from the preview
Don't miss anything!
Metal finishing is a p a r t of t h e plating and polishing industry classified under Standard
primarily engaged in all types of electroplating, plating, anodizing, coloring, and finishing of m e t a l and formed products f o r t h e trade. Most of t h e work performed by this industry is done on materials owned by others. Though m e t a l surface finishing is
operations t h a t use chemical means a r e discussed in this report.
3.1 Company Size Distribution
Since metal s u r f a c e finishing operations a r e performed by various industries classified
industry was not separately available. In 1980, t h e r e were approximately 160, manufacturing facilities in t h e U.S. which were covered by t h e metal finishing category (USEPA 1980). These facilities varied greatly in size, age, and number of employees. They ranged from very small independent job shops with less than ten employees, t o small shops within large corporations, t o large facilities employing large work forces.
3.2 Principal Producers
The m e t a l surface finishing industry is dominated by small job shops employing less than 20 employees each. There a r e no major producers who control a large share of t h e market.
3.3 Geoqraphical Distribution
The geographical distribution of t h e m e t a l surface finishing industry was not available due t o the reasons s t a t e d above.
The m e t a l surface finishing industry deals mostly w i t h the treatment o f m e t a l l i c or non-metallic products manufactured by others. Each product requires a specific
desired by the user. The principal products of the m e t a l surface finishing industry include:
Printed c i r c u i t boards C o i l coating Automotive parts
K i t c h e n utensils Jewelry Mechanical (non-automotive) parts
5. RAW MATERIALS
Reagents phosphoric acid, secondary or t e r t i a r y m e t a l phosphates, sodium dichromate, sodium nitrate, sodium cyanide, barium chloride, sodium chloride, sodium carbonate, sodium cyanate, ammonia, silicon t e t r a - chloride, zinc oxide, chromic acid (^) )
Accelerators quinoline, toluidine, nitrophenols, various oxidizing agents such as peroxides, and sulfites
Metals zinc, aluminum, chromium, cadmium, magnesium, iron, nickel, copper, silver, molybdenum, vanadium, tungsten
Alloys tin, lead-tin alloys, bronze, brass
M e t a l surface treatment consists of various processes such as electroplating, electroless plating, anodizing, chemical conversion coating, cleaning, etc. (USEPA 1980, BCL 1976, Schneberger 1981, Durney 1984). Since electroplating and m e t a l surface cleaning are discussed in separate studies in this appendix, this study considers only chemical surface treatments such as electroless plating, chemical
Table 6-1 B a t h Constituents for Capper and Nickel Electroless P l a t i n q
~~ Function Copper P l a t i n q Operation N i c k e l P l a t i n q Operation
M e t a l ion source
Complexinq agent
S e d u c i n q agent o
c^ I
pH adjustor S tabil izers
0 ther additives
Cupric sulfate (3-15 9/11 N i c k e l chloride, nickel sulfate, nickel sulfarnate, nickel hydmphosphite Rochelle s a l t (sodium potassium tartarate, eth ylenedi aminetetracetic acid (EDTA), sodium salts of EDTA, n i t r i l o t r i a c e t i c acid, qluconic acid, gluconates, triethanol amine, n-hydroxy ethylene diamine tetracetate (20-50 q/l).
L a c t i c acid, dicarhoxylates
Formaldehyde, paraformaldehyde, t ri oxene, dimethylhydantoin, sodium and potassium borohydride.
Sodium hyposphosphi t e
Sodium or potassium hydroxide Sodi urn or potassium hydroxi de 2 -mercaptobenzo thiazole, thiourea, methanol Molybdic acid'anhydride,^ arsenious acid, hydroxyl amino sulfate, hvdrazine. Water soluble m e t a l cyanides, polysiloxanes, m e t h y l dichloro silane
Thiourea, soluble fluorides, elcohol sulfonates, ethylene oxide derivatives, sodium sulfate. ~~ Source: Development Document^ for^ E f f l u e n t L i m i t a t i o n Guidelines^ (USEPA^1980 ).
-) of^ stabilizers.^ The bath^ is^ eventually^ dumped^ thereby^ generating a^ waste^ stream. Other waste s t r e a m s a r e generated by rinsing operations and periodic cleaning o f t h e process equipment. Other electroless plating operations, such as vapor deposition, a r e purely physical operations and are not considered in this report.
6.2 Chemical Conversion Coating
This operation includes phosphating, chromating, m e t a l coloring, and passivating. The coating deposited on metal objects is for decorative or corrosion protection purposes, and in some instances t o prepare t h e surface for painting. The mode of operation and waste generation a r e similar t o t h e electroless plating operation described in Section 6.1. The following sections discuss t h e four different chemical conversion coating methods listed above.
6. 2. 1 Phosphating
Phosphate coatings a r e formed on t h e surfaces of iron, steel, galvanized s t e e l , aluminum, and electrodeposited zinc and cadmium t o p r o m o t e adhesion of organic coatings, t o r e t a r d interfacial corrosion, t o retain and enhance t h e performance of corrosion resistant oils, and t o assist in cold deformation processes. Small p a r t s a r e coated in barrels immersed in t h e phosphating solution a n d ā l a r g e p a r t s a r e spray c o a t e d or continuously passed through t h e phosphating solution. The object t o b e coated may b e dipped successively in a series o f processing tanks.
3
The phosphating solution consists of a phosphoric acid solution of m e t a l dihydrogen phosphate. The coating t i m e and t e m p e r a t u r e depends on t h e t y p e o f metal t o b e c o a t e d and whether a spray or immersion coating s c h e m e is used. Sometimes a c c e l e r a t o r s ( t o improve quality), stabilizers ( t o prolong bath life) and oxidizing a g e n t s ( t o control the coating r a t e ) a r e added t o t h e phosphating solution.
There a r e c e r t a i n parameters, such a s t h e r a t i o of free t o combined phosphoric acid, t o t a l acid, metal-ion concentration, a c c e l e r a t o r concentration, and t h e process t e m p e r a t u r e t h a t must be controlled t o achieve a suitable coating and maintain t h e
-3 Many^ formulations^ a r e^ available^ for^ t h e^ coloring^ of^ m e t a l s and^ most^ of^ t h e m^ a r e proprietary. The major coloring process f o r steel uses a t r e a t m e n t solution of sodium hydroxide and sodium n i t r a t e in water. The processing t e m p e r a t u r e may vary from 275-320OF, and t h e immersion t i m e may vary f r o m 5 t o 30 minutes. The coating color and characteristics are largely a function of t h e alloy being treated, s u r f a c e characteristics, concentration o f t h e bath, t e m p e r a t u r e , and immersion time.
6.2.4 Passivation
Passivation r e f e r s t o forming a protective film on metal, particularly stainless s t e e l and copper, by immersion in an acid solution. Stainless s t e e l is passivated t o dissolve embedded iron particles and t o form a thin oxide film on its surface. A typical
dichromate. Copper is passivated using a solution of ammonium s u l f a t e and copper sulfate.
6. 3 Chemical Etchinq
Chemical etcMng is used t o produce specific design configurations and tolerances on metallic or metal-clad plastic (printed circuit boards) by controlled dissolution of t h e m e t a l with chemical etchants. Typical etching solutions are f e r r i c chloride, nitric acid, ammonium persulfate, chromic acid, cupric chloride, hydrochloric acid, etc. "Bright dipping" is a special form of chemical etching used t o remove oxide layers from ferrous and non-ferrous materials.
1
6.4 Cyaniding
Cyaniding is a type of c a s e hardening t h a t produces a hard surface on a m e t a l whose c o r e remains relatively soft. The product is a hard, wear-resistant surface backed by a strong, ductile, and tough core. Carbon and alloy s t e e l s a r e usually immersed in t h e cyaniding bath f o r a specific period of t i m e t o achieve t h e required degree of s u r f a c e hardening.
The most common cyaniding solution consists of 30 percent sodium cyanide, 40 percent sodium carbonate, and 30 p e r c e n t sodium chloride. Baths containing 97,^ 75,^ and^^45 percent sodium cyanide a r e also used. Oxygen f r o m t h e a i r oxidizes the sodium
cyanide t o sodium c y a n a t e which, a t high temperatures, decomposes to form nascent carbon and nitrogen. The carbon and nitrogen a r e absorbed by the steel, which increases surface hardness. The processing temperatures may vary from 1200-135OOF f o r low penetration t o 1650-1725OF for high penetration. A combination t r e a t m e n t using high t e m p e r a t u r e immersion followed by low t e m p e r a t u r e immersion is also used.
The depth of surface t h a t is hardened is controlled by t h e t e m p e r a t u r e and t h e cyanide content. As drag-out and carbon depletion occur, special s a l t compositions a r e added t o replenish and r e g e n e r a t e t h e bath. At the end of the t r e a t m e n t , t h e objects are immersed in a w a t e r or oil bath, where quenching and rinsing is accomplished simultaneously. The quench w a t e r is potentially hazardous and is t r e a t e d for cyanide destruction followed by clarification prior t o discharge. The quench oil is also potentially hazardous and is disposed of by incineration.
7. WASTE DESCRIPTiON
The primary wastes associated with metal surface finishing, along with t h e i r process sources, are listed in Table 7-1. The wastes produced in m e t a l surface finishing operations come mainly f r o m two sources: dumping of process tanks, and rinse w a t e r s used to wash off process solutions adhering to t h e product surface or entrapped in t h e crevices due to t h e shape of t h e product piece (Durney 1984, AESI 1981, CP S t a f f 1984). The process solutions a r e periodically filtered t o remove precipitated m e t a l s and a r e reused. These filtered solids a r e mixed with solids.removed from t h e rinse w a t e r s and a r e either landfilled or sold for m e t a l reclamation.
Additional w a s t e is generated a s a result of process solution filtering.
O t h e r wastestreams include spills and leaks plus stripping wastes.
Spent Bath Solution
The activity of t h e plating solution decreases with time due t o t h e precipitation of salts and depletion o f constituents. A f t e r 3-6 regeneration cycles, t h e b a t h is eventually discharged*. This waste s t r e a m usually contains cyanides or m e t a l l i c
~ ~~~ *National Association of Metal Finishers 1985: Personal communication.
I complexes. I n the recent past, this stream was treated together w i t h the rinse water stream. However, the need for obtaining the necessary p e r m i t s and also the perceived regulatory compliance d i f f i c u l t i e s have discouraged treatment o f spent baths*. This stream i s often sent off-site f o r disposal.
Waste Rinse Water
Rinse water i s used to wash o f f process solutions adhering t o the product surface or entrapped in i t s crevices due to i t s geometrical shape. The rinse water stream is usually discharged to municipal treatment facilities w i t h or without any treatment, depending on i t s^ composition.^ The treatment procedure includes oxidative destruction of cyanides reduction o f chromates, neutralization, and solids removal.
F i l t e r Waste.
The f i l t r a t i o n step in the regeneration o f plating solution and the solids removal in rinse water treatment each generate a solid waste. These solids contain oxides or complexes o f metals and are either landfilled or sent off-site f o r m e t a l reclamation.
S p i l l s and Leaks
The overflow and leaks f r o m various process equipment are usually mixed w i t h the rinse water stream and disposed o f as explained above.
Strippinq Waste
Before coating an object, the previous coatings on it are removed by a striping operation. This i s also done t o remove coatings f r o m an improperly coated object. In small job shops, the same stripping solution could be used f o r removing d i f f e r e n t types o f coating. The disposal o f the spent b a t h f r o m such operation is similar t o t h a t o f the spent baths discussed earlier. The rinse waters are usually discharged t o municipal treatment facilities w i t h or^ without treatment.^ The untreated streams may^ contain various cyanides and cyanide complexes, hexavalent chrome, copper, nickel, zinc,
I
3 cadmium and other metals. The t r e a t m e n t includes oxidative destruction of cyanides, The t r e a t m e n t sludge is Spills and overflows t h a t occur c a n be mixed and t r e a t e d
reduction of chromates, neutralization, and solids removal. expected t o be landfilled. with o t h e r liquid wastes and t r e a t e d as discussed.
8. WASTE GENERATION RATES
Since metal finishing operations a r e o f t e n performed along with electroplating and o t h e r operations, the waste generation r a t e s specifically attributable t o m e t a l finishing a r e difficult t o determine. N o waste generation d a t a were in evidence a t t h e t i m e of t h e final document preparation. While no specific waste generation r a t e s were reported, fractional r a t e s were e s t i m a t e d by project s t a f f based on t h e available information and engineering judgements. These values a r e shown in Table 9-1.
9. WASTE REDUCTION THROUGH SOURCE CONTROL
9.1 Description of Techniques
The list of individual waste s t r e a m s and sources and their corresponding source reduction methods is presented in Table 9-1. The following sections discuss t h e various waste reduction methods based on a l i t e r a t u r e survey and industry contacts.
In addition t o the waste reduction measures classified a s being process changes or material/product substitutions, a variety of waste reducing measures labeled as "good operating practices" has also been included. Good operating practices a r e defined a s being procedural or institutional policies which result in a reduction of waste. The following items highlight t h e scope of good operating practice: o Waste s t r e a m segregation o Personnel practices
material tracking and inventory control
can s o m e t i m e s be removed by temporarily lowering t h e b a t h t e m p e r a t u r e so as t o f o r m solid crystals. In t h e c a s e of electroless nickel plating, t h e sodium s u l f a t e t h a t forms can be crystallized by lowering t h e bath t e m p e r a t u r e t o 41-500F (Durney 1984). The crystals c a n then be removed by filtration.
Another process, patented by t h e U.S.^ Army,^ involves^ t h e^ removal^ of sodium c a r b o n a t e f r o m sodium cyanide-based plating b a t h s by cooling. Dry ice is used t o cool t h e plating bath, thereby causing t h e precipitation of t h e carbonates. The plating solution, free of carbonates, c a n then b e reused. So f a r , t h i s method has not found widespread use (Arienti 1985, Versar 1985).
Use o f a n e l e c t r o l y t i c diaphragm cell for regenerating spent chromic acid used in etching operations has been reported (AESI 1981). The process uses electrolytic diaphragm cell t o oxidize trivalent chromium t o hexavalent chromium and remove contaminants. The quality of t h e regenerated e t c h a n t was reported t o b e equal t o or b e t t e r than fresh etchant. This process, which was still in t h e developmental stage, would have a g r e a t potential f o r reducing spent chromic acid waste. In one such application, extensively t e s t e d a t t h e U.S. Bureau o f Mines in Rolla, Mo., copper etching solution was regenerated and metallic copper recovered a t t h e s a m e time. Recovery was accomplished by depositing t h e copper onto t h e cathode of t h e e l e c t r o l y t i c diaphragm cell (Basta 1983).
O t h e r measures t h a t can extend bath life a r e t o use a u t o m a t i c control systems, maintain a l l rack and barrel systems, and p r a c t i c e good house- keeping a t all times. Automatic control devices can b e used t o maintain t h e concentration by conductivity measurement. A significant change in conductivity would i n i t i a t e pumping of fresh c o n c e n t r a t e into t h e tank. This type of a u t o m a t i c control is used by large facilities especially f o r c h r o m a t e conversion coating (Durney 1984). If t h e racks or barrels (used for transferring objects t o be coated) do not have proper protective coatings, t h e bath could become contaminated. The process solution c a n a t t a c k t h e weak spots in t h e racks or barrels, causing t h e formation of metallic s a l t s in t h e bath and thereby lower its activity. Fluorocarbon
coatings applied t o the racks or barrels have been found t o b e e f f e c t i v e in (^1) minimizing such contamination (Lane 1985). Such a coating will also be helpful in lowering dragout since less bath solution t h a t remains in t h e corroded crevices on the racks or barrels. Special measures t h a t c o n s t i t u t e good operating practices a r e discussed a t t h e end of this section.
o Metal/acid recovery from spent bath solutions. By using electrolysis on t h e spent bath solutions, useful m e t a l s c a n be recovered and a t the s a m e time t h e hazardous n a t u r e of t h e spent b a t h c a n be reduced (Lewis 1980, Campbell and Glenn 1982). This method was implemented in one facility by insertion of electrodes directly into t h e cyanide destruction tank*. However, electrolysis is used only t o a limited e x t e n t by t h e industry (USEPA 1982).
In addition t o recovering metals from t h e spent bath, spent acid can also b e recovered and recycled by means of ion-exchange (Basta 19831. Eco-Tec Ltd., in Ontario, Canada, markets an acid purification s y s t e m t h a t uses a proprietary resin t h a t recovers mineral acids. The m e t a l s are recovered in a concentrated (but still dissolved) form. The c o n c e n t r a t e d m e t a l s c a n than be recovered by electrolytic means. This process is used by Modine Manufacturing, in Trenton, Mo., t o t r e a t copper-contaminated sulfuric acid/hydrogen peroxide solution which was used t o brighten brass (Basta 1983). Sodium phosphate salts, formed in nickel/copper electroless plating, can be converted into useful hypophosphite salts by using ion exchange resins activated with hypophosphorous acid. The use of ion exchange resins for regeneration, however, suffers from t h e disadvantage of generating additional wastes such a s spent resins and resin regenera tion solutions.
1
Another nonelectrolytic means of m e t a l reclamation, still in developmental stages, is t h e use of b a c t e r i a (Basta 1983). Here, t h e microbes form complexes with t h e metals in solution, creating a biomass. The biomass c a n then b e burned t o recover e l e m e n t a l metal. Laboratory studies in this a r e a a r e in progress a t Polbac Corp. (Allentown, Pa.) and t h e O'Kelly Companies (Tulsa, Ok.).
generated by spent bath solutions can be eliminated totally. Zyaniding, however, does have several advantages over gas carboni triding (Schneberger 1981). These include more flexible opera tion illustrated b y the ability t o simultaneously t r e a t many small batches which require different cycle times, and a higher heating rate. This is important for cases where t h e t i m e needed f o r t h e object t o reach the conditioning temperature may b e a large f r a c t i o n of t h e t o t a l cycle time.
Vacuum evaporation methods for coating nickel, aluminum, and o t h e r metals have been developed. Here, m e t a l s a r e evaporated a t l o w pressure using an electron beam and the vapor condenses, a s a coating, onto t h e substrate. This method could be a viable a l t e r n a t i v e t o electroless nickel plating, which generates spent bath wastes. However, the vacuum evaporation method has several disadvantages, e.g., it requires relatively expensive equipment which becomes effective only when a large number of substrates a r e t o be coated, and the uniformity of coating thickness is generally very difficult t o control.
Chromium and cadmium can b e ,deposited on s t e e l using ion plating methods instead of electrodeposition. Ion plating uses high-energy ions t h a t bombard the depositing m e t a l which e v a p o r a t e s and then condenses on the substrate. In t h e U.S., this method is used only when other techniques a r e found inadequate. However, ion plating is in wide use in Japan where it successfully competes with electrodeposition (Durney 1984).
Chemical vapor deposition (where a chemical reaction decomposes t h e r e a c t a n t gases t o produce t h e desired coating material which then condenses on t h e substrate) c a n b e used for almost any coating operation (Durney 1984). However, its use has been limited t o t h e semiconductor industry, and commercial systems for o t h e r applications are not available a t the present time.
Ion beam processing techniques, s t i l l in t h e development stage, will b e a n excellent alternative t o case-hardening t r e a t m e n t s (Anon 1984). Here, a high energy ion beam is used to harden t h e s u r f a c e by implanting t h e ions in the material. 1
1 ) o Use o f less t o x i c solutions. Whenever possible, the use of less t o x i c solutions for m e t a l finishing w i l l lower the hazard o f spent solutions. In the case of electroless copper plating, water soluble cyanide compounds of many metals are added t o eliminate or minimize the internal stress of the deposit. It was found t h a t polysiloxanes, such as General E l e c t r i c silicon f l u i d SF-96, are also e f f e c t i v e stress relievers (Durney 1984). B y substituting cyanides w i t h polysiloxanes, the hazardous nature o f the spent b a t h solution can be reduced, Use o f trivalent chrome instead o f hexavalent chrome in chromate conversion coating can eliminate the t o x i c i t y o f the spent electroplating baths. Though some manufacturers use t r i v a l e n t chrome+, i t s use i s not growing rapidly because the quality o f t r i v a l e n t chromium coatings i s not as good as t h a t o f hexavalent coatings in many applications.+ Currently, there were a t least f i v e companies t h a t o f f e r t r i v a l e n t systems (Chementator 1982). Trivalent chromium baths can also use lower m e t a l concentrations. One such solution, developed by W. Canning Materials Ltd. in Birmingham, England, uses only 3. 5 gms/liter of t o t a l chromium compared t o the level o f 130 gms/ l i t e r s used in traditional hexavalent baths.
o More dilute process solutions. The use o f dilute bath solutions, whenever possible, would also reduce the hazardous nature of the dumped bath. In the case o f cyaniding, a t y p i c a l b a t h solution composition i s 30 percent sodium cyanide, though some f a c i l i t i e s use 45, 7 5 , and 92 percent solutions. By using a 30 percent solution instead o f a solution o f higher concentration, substantial reduction in the cyanide content o f the spent bath solution can be achieved. In electroless copper plating for printed c i r c u i t board manufacture, dilute solutions have been tried successfully by many manufacturers (USEP 1981). The use o f dilute b a t h solution could also lower subsequent rinse water requirements and m e t a l dragout i n t o rinsewater.
J * Nationa! Association o f fvletai Finishers 1985: Personal communication.
B 6 - 1 7
3
cyanide complexes along with o t h e r m e t a l complexes, is t r e a t e d for cyanide destruction and discharged t o the sewer. The following source control methods a r e suggested:
In an immersion-type t r e a t m e n t process, small objects a r e placed inside barrels and bigger objects are supported on racks for immersion into t h e bath. When t h e object is removed from t h e bath, t h e rack or barrel (and object) c a r r y s o m e r e a g e n t s with it, called "drag-out". Methods t h a t c a n b e used t o reduce drag-out and subsequently lower rinse w a t e r requirements are: proper racking o f t h e parts; keeping t h e racks free of m e t a l buildup and corrosion; increasing drainage t i m e above t h e process tank; using stationary recovery rinses by installing save rinse or drip rinse tanks; using air blowoff or^ tumbling t o ensure drainage; and using drainage agents (Cheremisinoff, Peina, and Ciancia 1976, AESI 1981, and Cook et. al. 1984).
1 o Effective rinsing methods. By using an e f f i c e n t rinsing sequence, t h e quantity of rinse water required can be reduced substantially. Rinsing efficiency can be improved by using properly designed rinse tanks, using a i r agitation in t h e rinse tanks, using f o g sprays, using a u t o m a t i c valves t h a t control flow r a t e s based on t h e movement of p a r t s through t h e processing line, and by using counter- c u r r e n t rinsing (Cheremisinoff, Peina, and Ciancia 1976, AESI 1981, and
An e s t i m a t e d 90 p e r c e n t reduction in rinse water c a n b e achieved by using a countercurrent rinse instead of a single running rinse (AESI 1981). Converting t o a c o u n t e r c u r r e n t rinse requires only t h e addition of one or more tanks, appropriate plumbing, and an a i r agitation system. Because of space limitations or t h e use of preprogrammed hoist lines, installation of an additional rinse tank may not be possible a t many job shops. However, many facilities have reported substantial savings by converting t o countercurrent rinsing.
The use of f l o w control valves can reduce rinse water use by 50 percent w i t h m i n i m a l capital costs (AESI 1981). I n many instances, excess water i s used indiscriminately t o ensure t o t a l rinse to p r o t e c t product quality. Though many facilities have installed flow control valves, concerns about reduced product quality have contributed t o opposition t o such measures (AESI 1981).
F o g sprays, though efficient, are not suitable f o r a l l applications. In instances where the coating has l i t t l e strength i n i t i a l l y (as in the case o f chromate coatings), fog sprays are generally not used. Use o f a i r agitation in the rinse tanks promotes turbulence in the tank which increases the rinsing efficiency. The use o f a i r agitation in tanks is f a i r l y widespread (AESI 1981).
o Use o f immiscible rinses. The use o f non-aqueous immiscible solvent f o r rinsing would allow the rinsed solution t o either sink or rise during decantation, and the solution could then be returned t o the surface t r e a t m e n t b a t h f o r reuse without any pretreatment. The rinsing solvent could also be recycled. This process, i f feasible, could reduce or eliminate rinse water wastes. Tests w i t h f i v e solvents f o r use in the chromatin9 process were conducted a t the U n i t e d Technologies Research Center (AESI 1981). A major disadvantage of this method would be the potential f o r increased a i r emissions and the need t o dispose of spent solvent.
o The use of no-rinse coating processes. As the name suggests, no-rinse coatings do n o t require rinsing a f t e r a coating is formed and dried, as there are no residuals l e f t t o i n t e r f e r e w i t h the subsequent treatment. Recent developments in chromate conversion coating f o r the c o i l coating industry have resulted in a solution t h a t can be applied t o steel, galvanized steel, or aluminum, without the need for any subsequent rinsing (USEPA 1982). A f t e r the coating is formed, it is dried in a i r a t about 15OoF. This no-rinse process, though used by only a f e w c o i l coating facilities, can be used f o r other coating applications (USEPA 1982).