
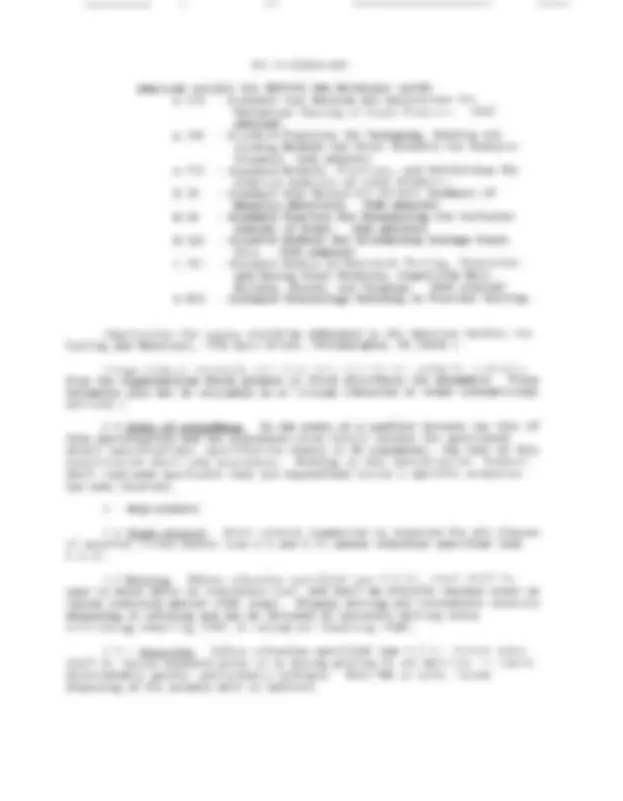
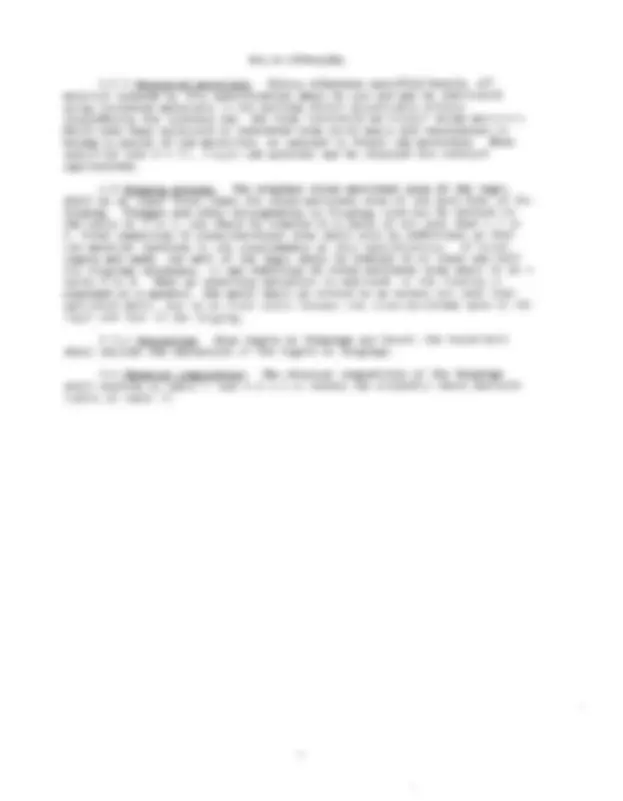
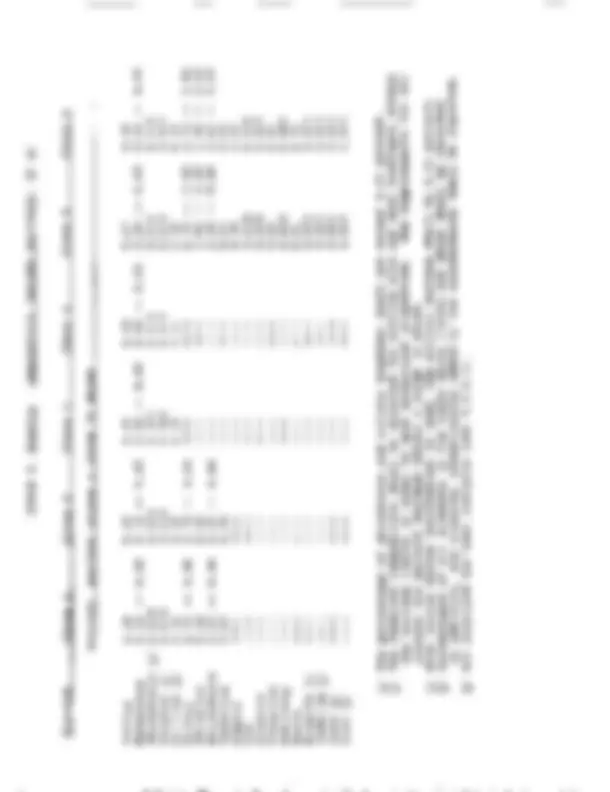
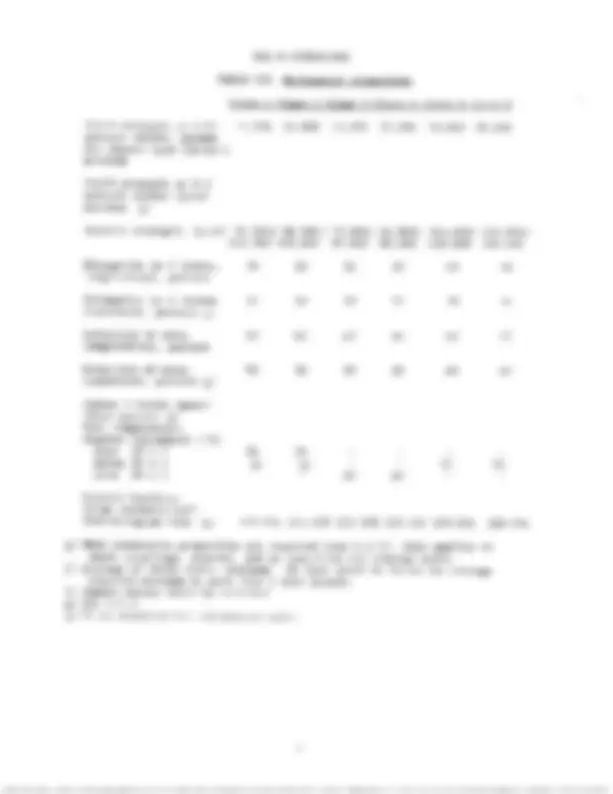
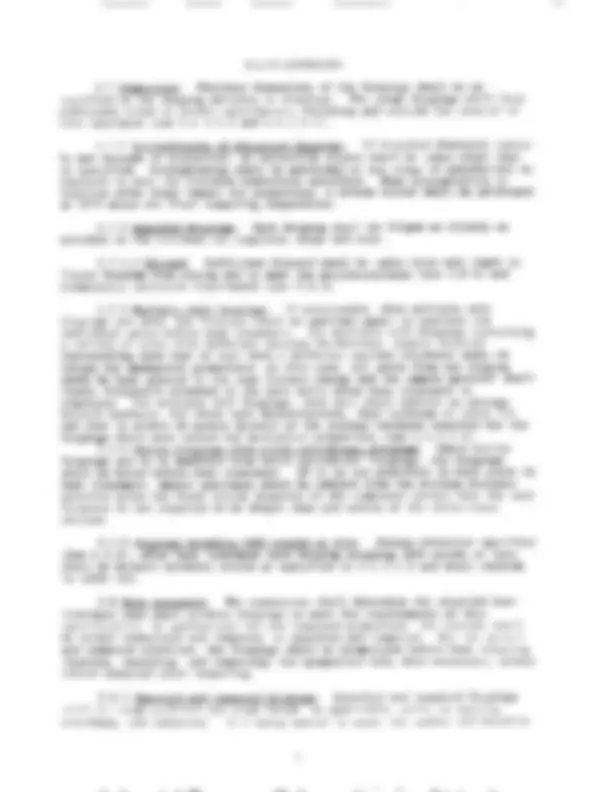
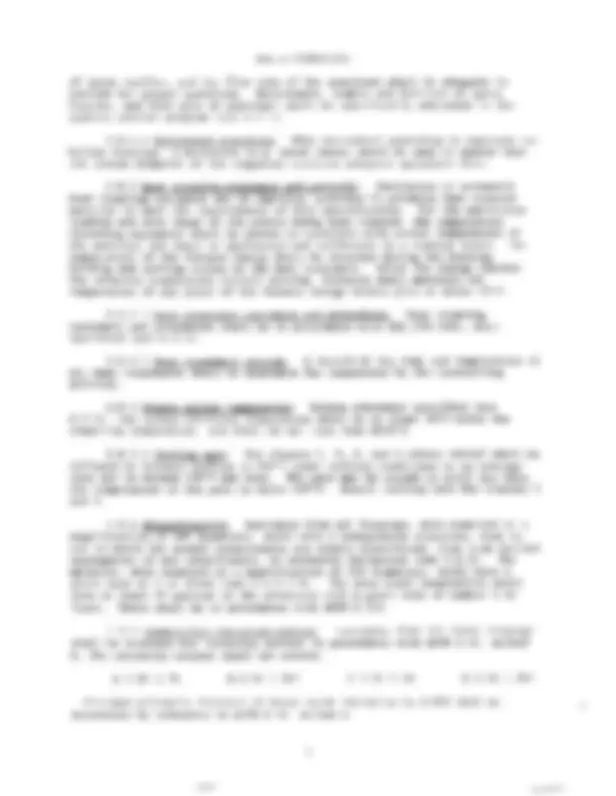
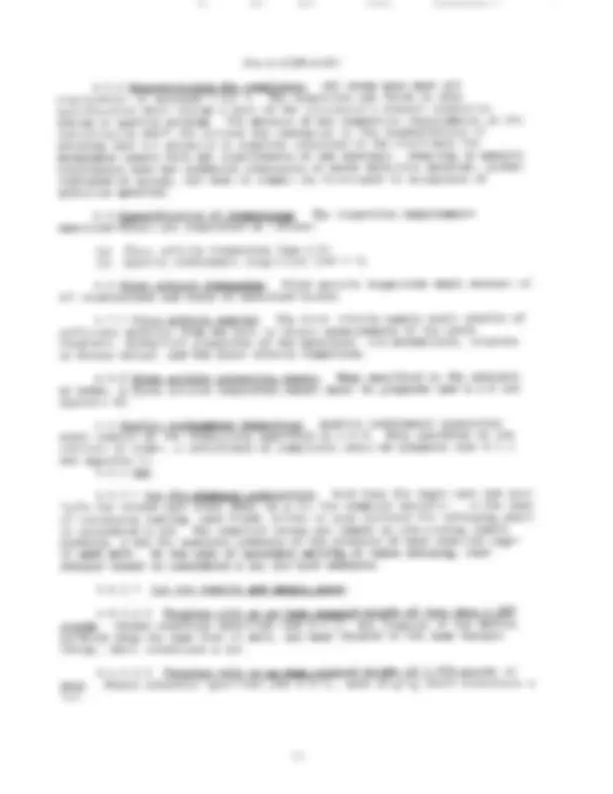
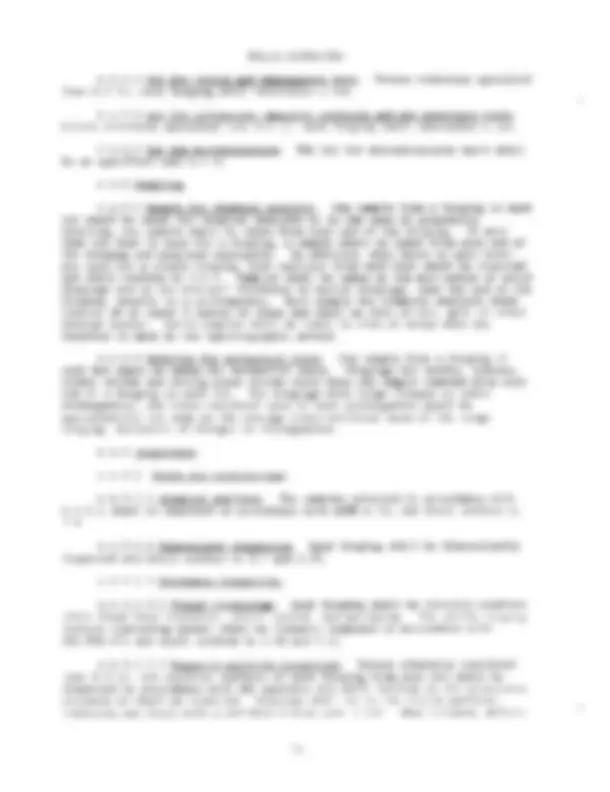
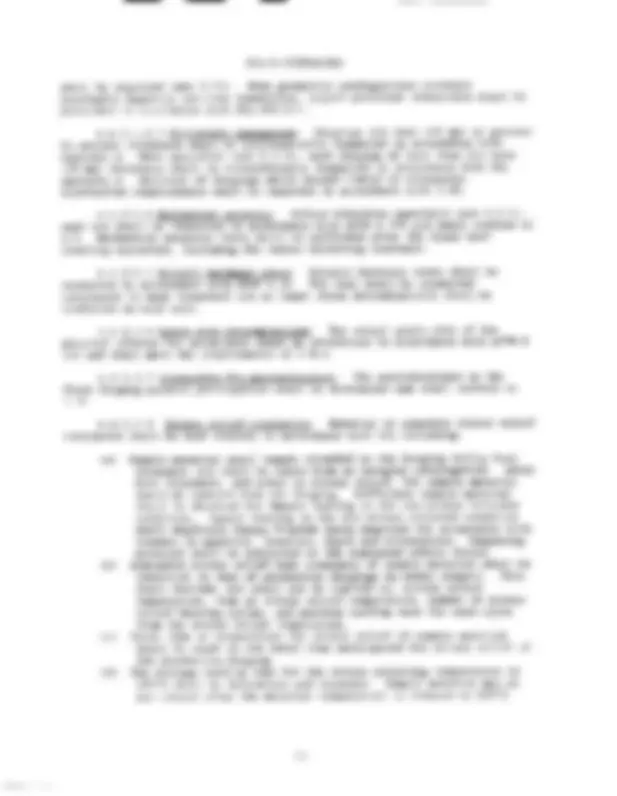
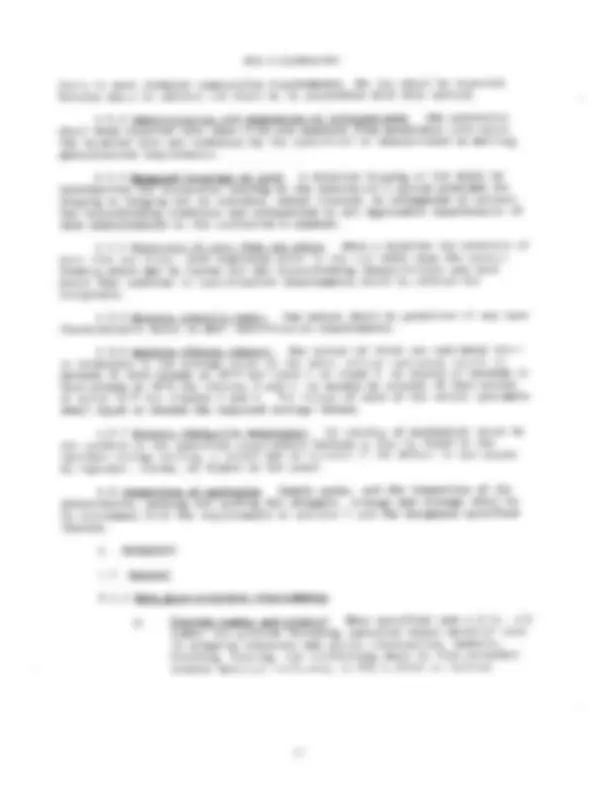
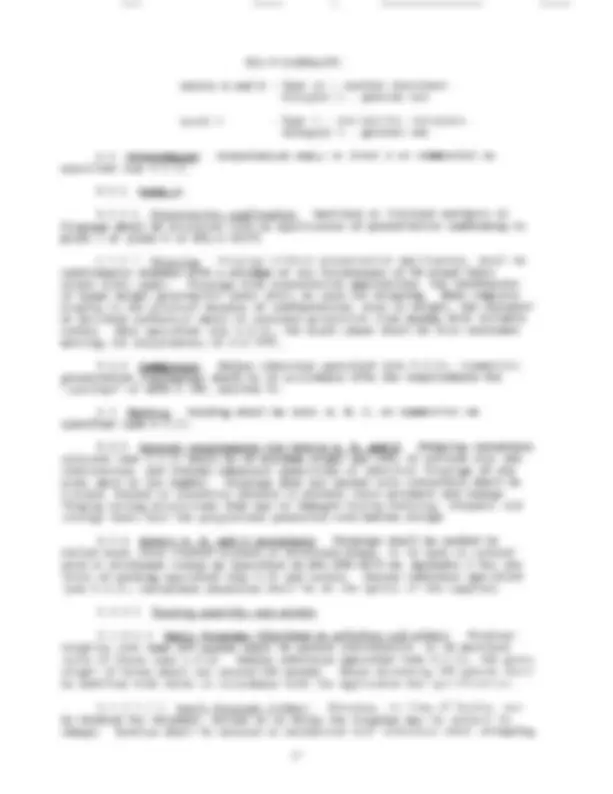
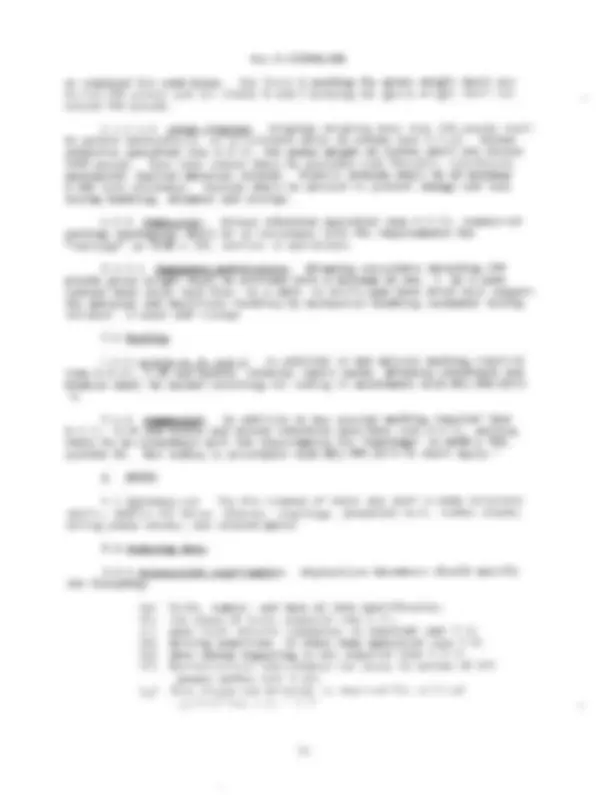
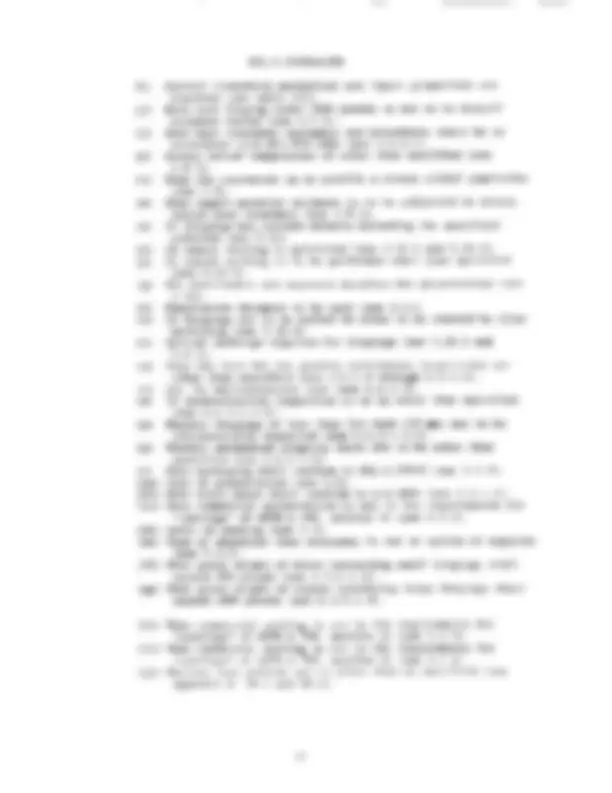
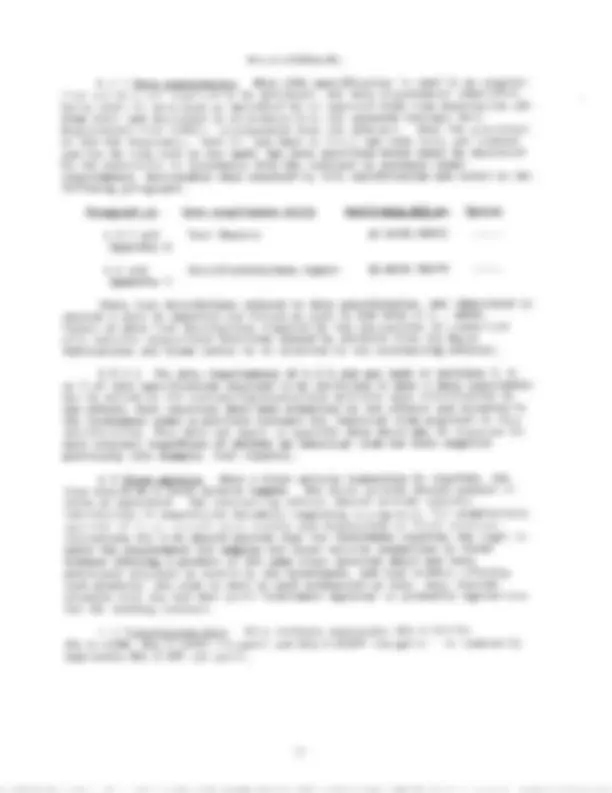
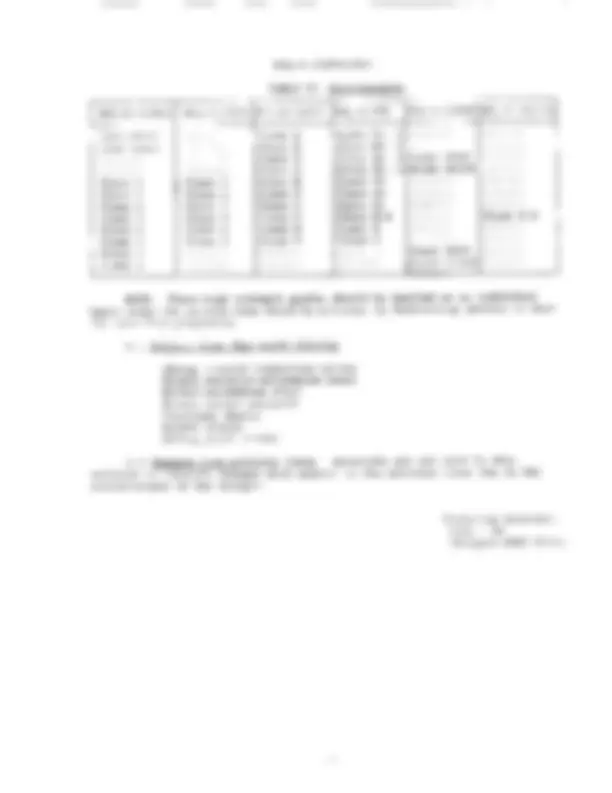
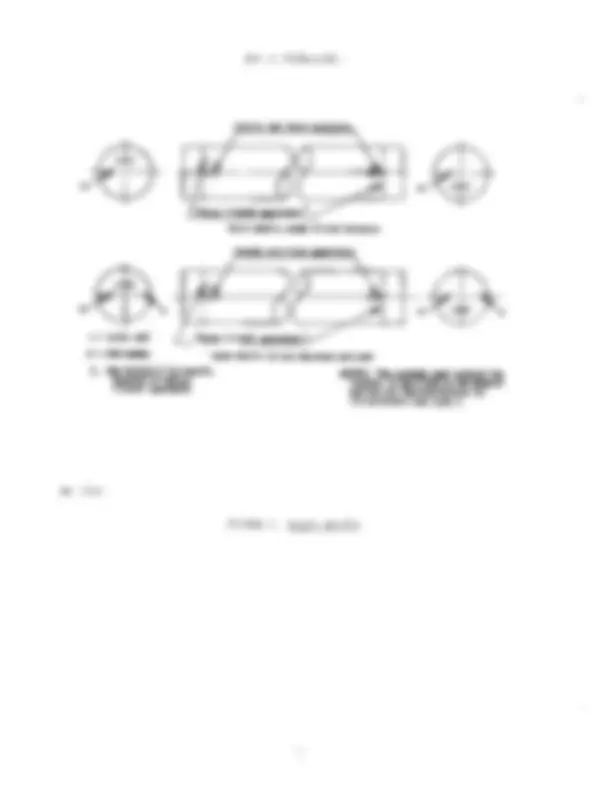
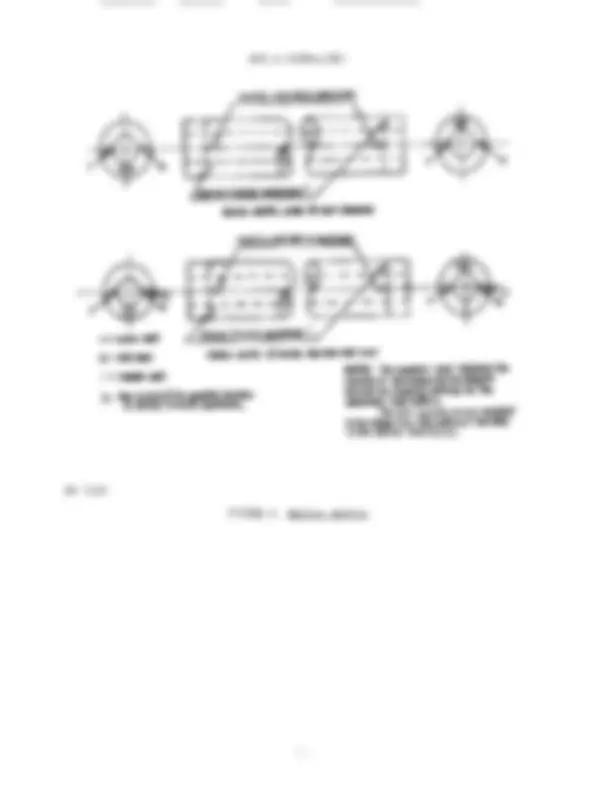
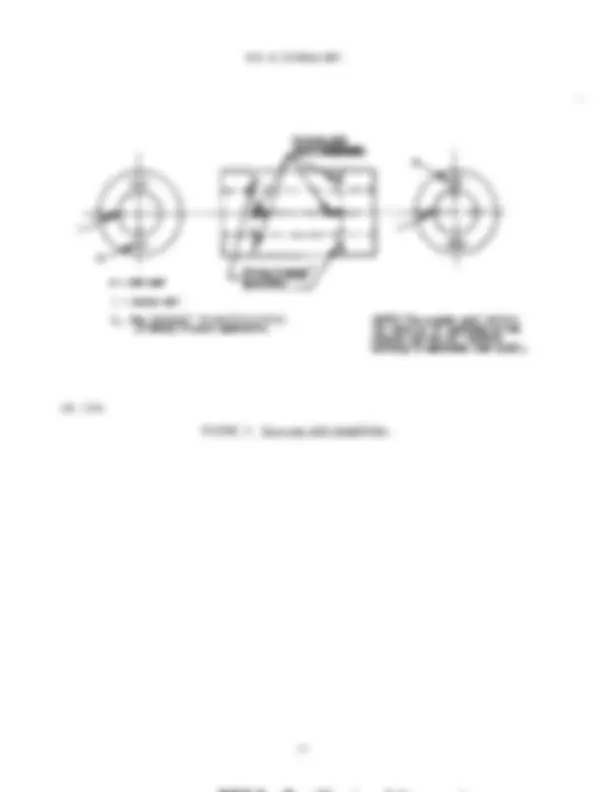
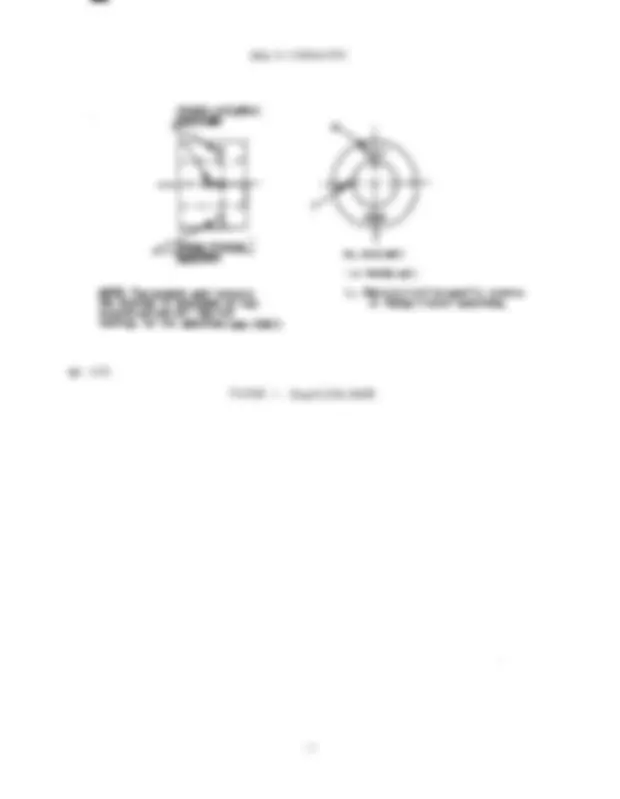
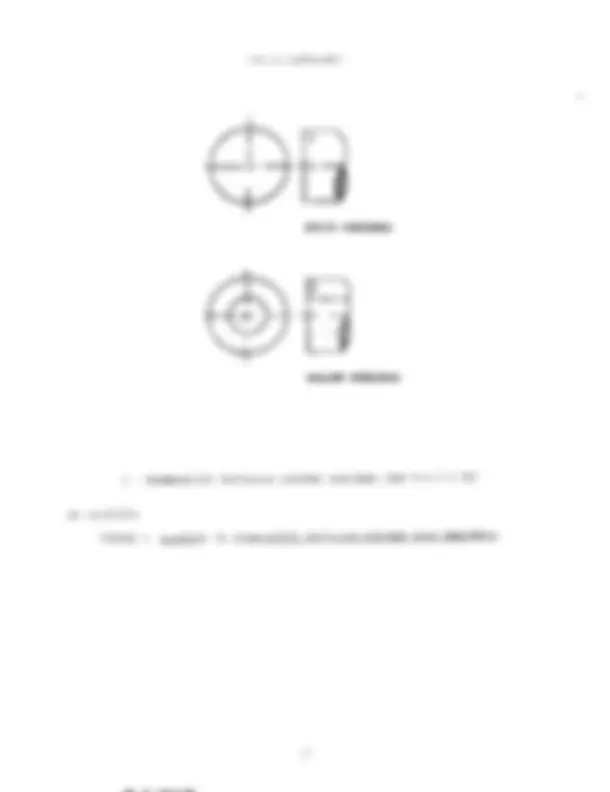
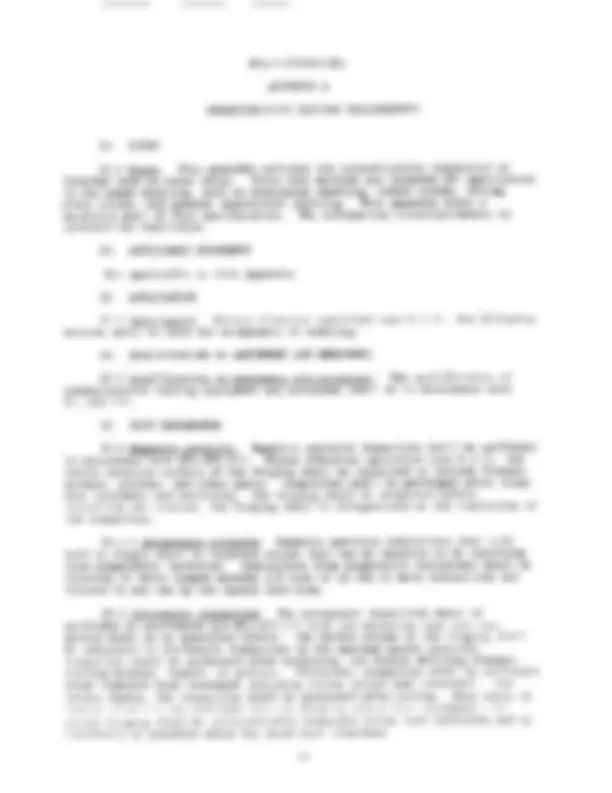
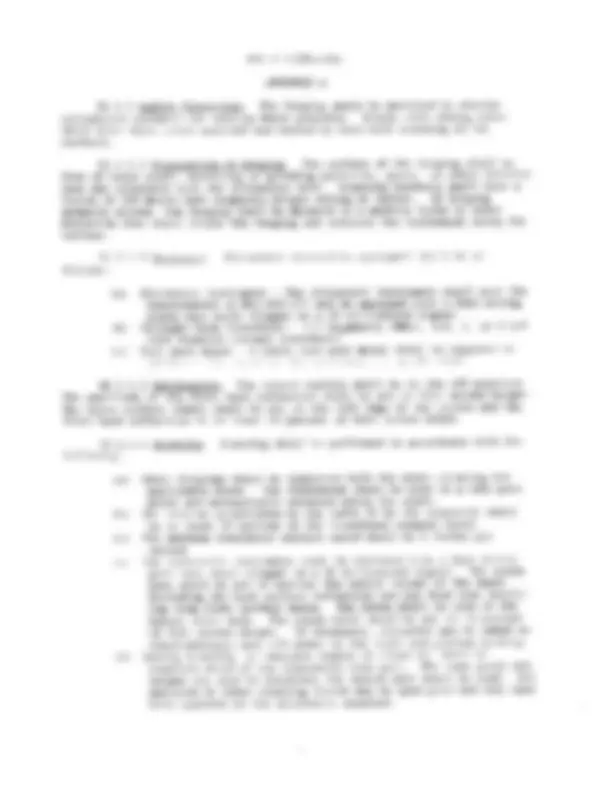
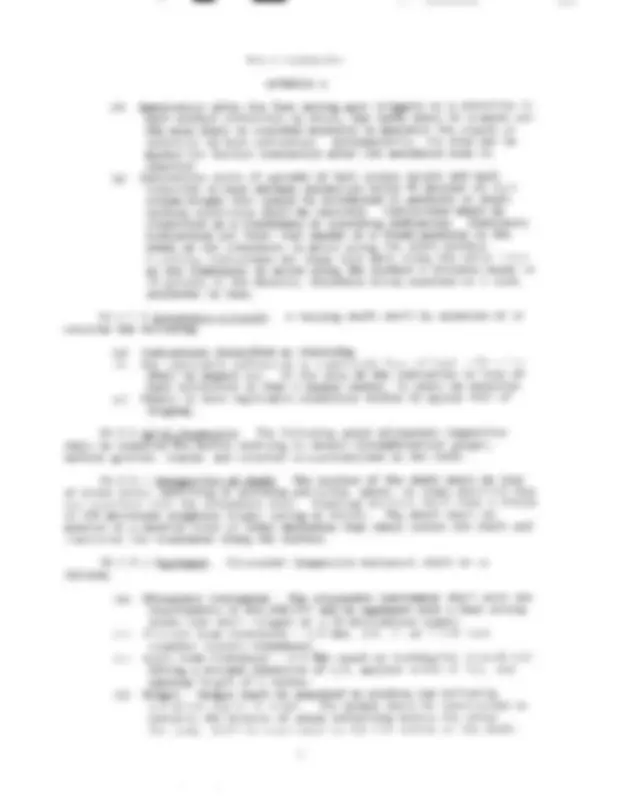
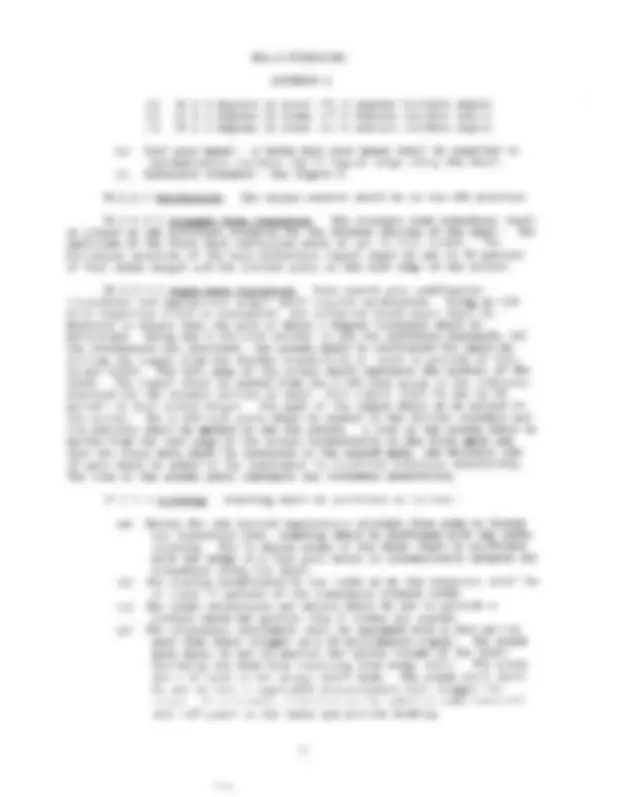
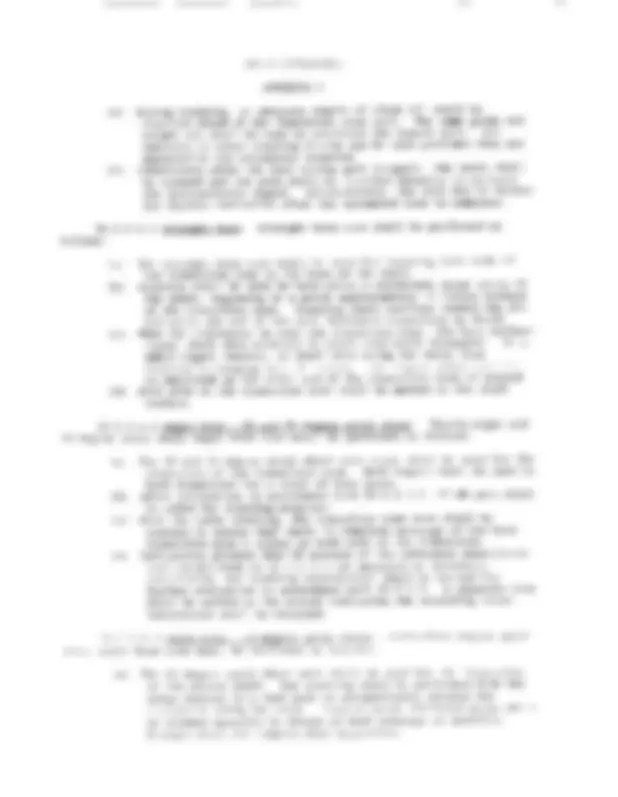
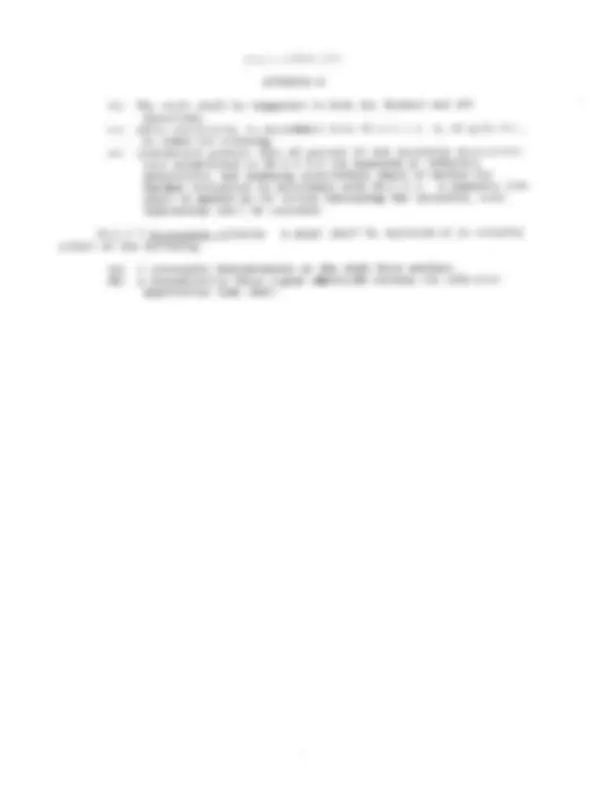
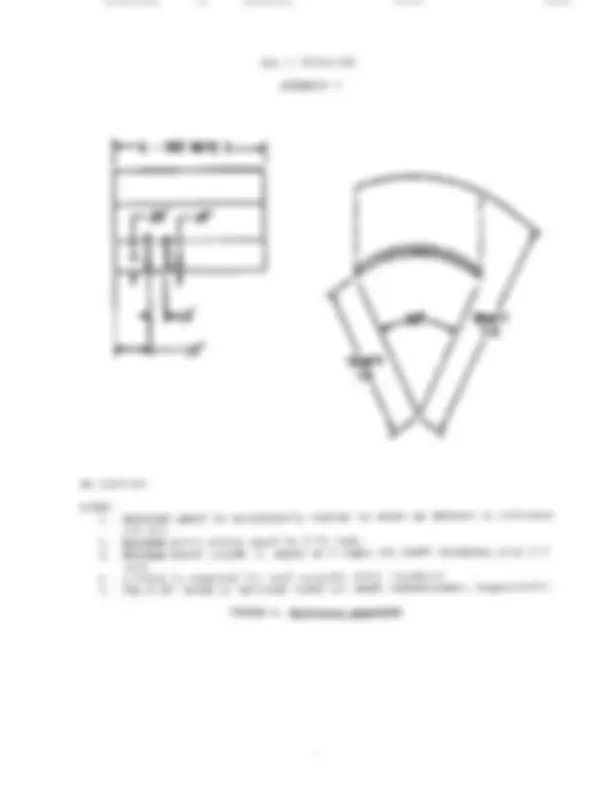
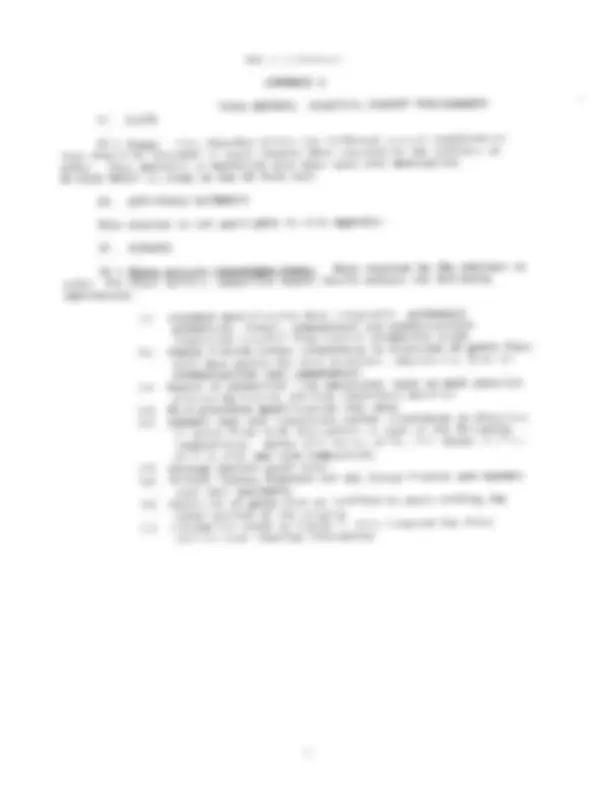
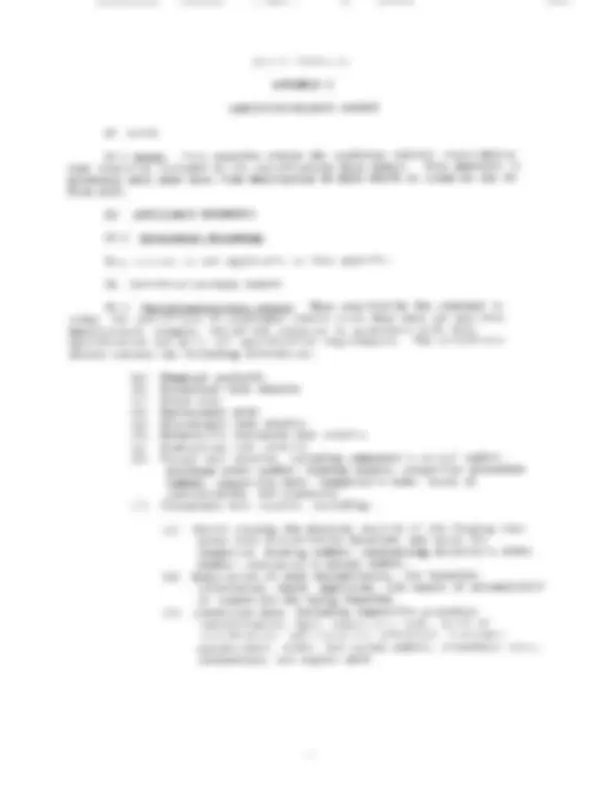
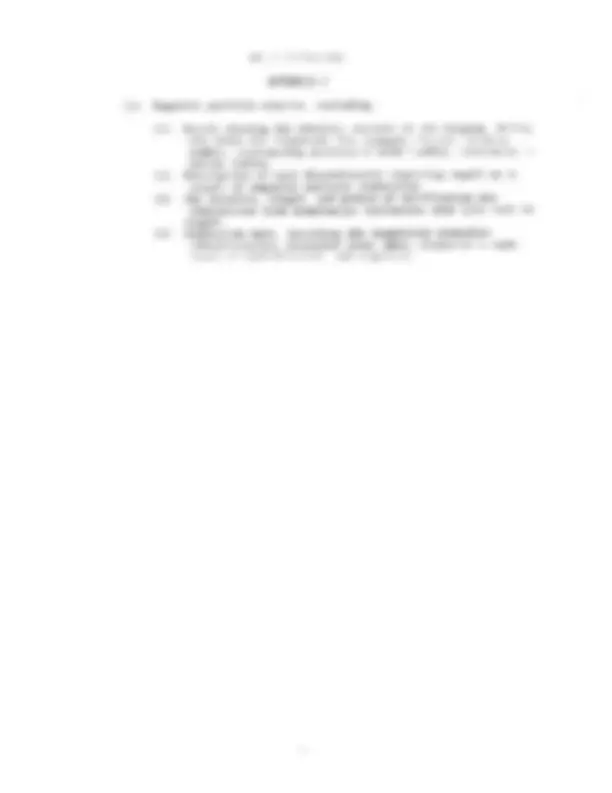
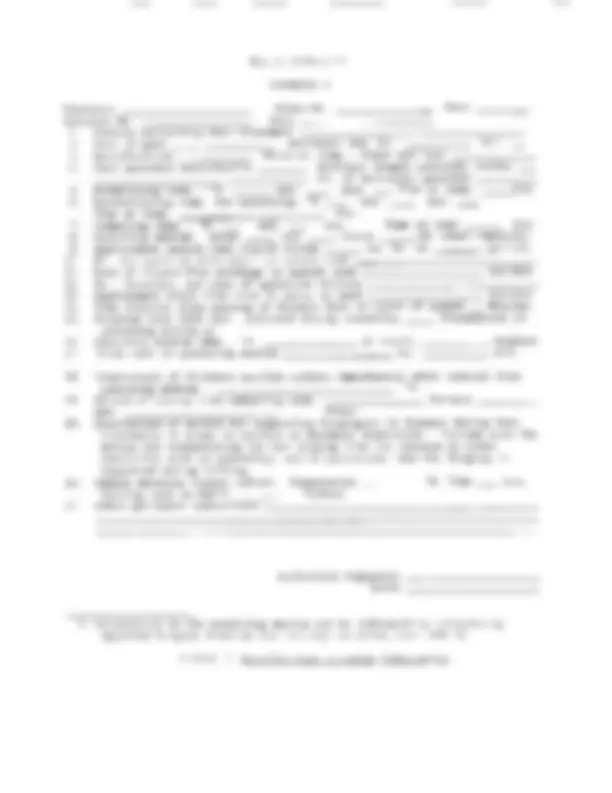
Study with the several resources on Docsity
Earn points by helping other students or get them with a premium plan
Prepare for your exams
Study with the several resources on Docsity
Earn points to download
Earn points by helping other students or get them with a premium plan
Community
Ask the community for help and clear up your study doubts
Discover the best universities in your country according to Docsity users
Free resources
Download our free guides on studying techniques, anxiety management strategies, and thesis advice from Docsity tutors
This specification covers carbon and alloy steel forgings for torsional shafts, including propulsion shafts for ships, sleeves,.
Typology: Exercises
1 / 39
This page cannot be seen from the preview
Don't miss anything!
35 June^1990 SUPERSEDING (See 6.4)
This specification is approved for use within the Naval Sea Systems Command, Department of the Navy, and is available for use by all Departments and Agencies of the Department of Defense.
1.1 Scope. This specification covers carbon and alloy steel forgings for torsional shafts, including propulsion shafts for ships, sleeves,
parts.
1.2 Classification. The forgings shall be made from the following classes of steel, (^) as specified (see 3.4 and 6.2.1):
Class 1 - Nickel-molybdenum steel Class 2 - Nickel-molybdenum steel Class 3 - Carbon steel Class 4 - Carbon steel Class 5 - Nickel-chromium molybdenum steel Class 6 - Nickel-chromium molybdenum steel
2.1 Government documents.
Beneficial comments (recommendations, additions, deletions) and any pertinent data which may be of use in improving this document should be addressed to: Commander, Naval Sea Systems Command, SEA 55Z3, Department of the Navy, Washington, (^) DC 20362-5101 by using the self-addressed Standardization Document Improvement Proposal (DD Form 1426) appearing at the end of this document or by letter.
QI_S-T~IBIJTION—----.-—-.—.STATEMENT--....—.-....... (^) .....-.A (^). ~lpproved for public release; distribution unlimited
2.1.1 Specifications and standards. The^ following^ specifications^ and standards form a part of this specification to the extent specified herein. Unless otherwise specified, the^ issues^ of^ these^ documents^ shall^ be^ those listed in the issue of the Department of Defense Index^ of^ Specifications^ and Standards (DoDISS) and supplement thereto, cited in the solicitation.
SPECIFICATIONS
FEDEIUL A-A-
MILITARY MIL-C-
MIL-L-
STANDARDS MILITARY MIL-STD- MIL-STD-
MIL-STD-
MIL-STD- MIL-STD-”
MIL-STD-
MIL-STD-
Welded Joint Design.
(Copies of specifications and standards required by contractors in connection with specific acquisition functions should be obtained from the contracting activity or as directed by the contracting activity. )
2.2 Other publications. The following documents form a part of this specification to the extent specified herein. Unless^ otherwise^ specified,^ the issues of the documents which are DoD adopted shall be those listed in the issue of the DoDISS specified in the solicitation. Unless^ othewise specified, (^) the issues of documents not listed in the DoDISS shall be the issue of the nongovernment documents which is current on tl~edate of the solicitation.
AMERICAN NATIONAL STANDARDS INSTITUTE (ANSI) B46.1 - Surface^ Texture^ (Surface^ Roughness,^ Waviness, and Lay). (DoD adopted)
(Application for copies should be addressed to the American National Standards Institute, Inc., 1430 Broadway, New york, ~ 10018”)
—
3.2.2 Recovered materials. Unless otherwise specified herein, all material covered by this specification shall be new and may be fabricated using recovered materials to the maximum extent practicable without jeopardizing the intended use. The term “recovered materials” means materials which have been collected or recovered from solid waste and reprocessed to become a source of raw materials, as opposed to virgin raw materials. When specified (see 6.2.1), virgin raw material may be required for critical applications.
3.3 For~inz vrecess. The original cross-sectional area of the ingot shall be at least three times the cross-sectional area of the main body of the forging. Flanges and other enlargements on forgings need not be reduced to the ratio of 3 to 1, but shall be reduced to a ratio of not less than 1,7 CO
3.3.1 centerline. When ingots or forgings are bored, the bored hole shall include the centerline of the ingots or forgings.
...
3.4 Chemical com~osition. The chemical composition of the forgings shall conform to table I (see 4.4.3.1. 1,)within the allowable check analysis limits of table 11,
I Ill
I Ill J 111 mm Oln In mmmm I=o!-1-imlnoommm oaolm9-loooo (-NoJoombln=rooJo 00000000
I I Om:ul! I I I I I 11 f I I I I mu)ooml I I I 1 I I I! I I I I I l III I 1 I I II I I I I I 6666011 1 I I t I I I I I I I I r+ a c)
al h J
C/i l
a mo%knl I I I I 1 I II I 1 I I I moooml I I 1 1 I t I I I I I I I “1 1 I I I I I II 1 I I II 6666011 I 1 I 1 I 1{ I I I II
ill m &
I I I I I I Oln Qlnm+u)lnou)m 1 I I I 1 I I I 1 I Ndoommlnmo I I I I I I I I I I l 1 I 1 II II I I I 66666A660 I I I I I 1 I I I i
g u & a) Q(
$ “r-l
. El f-i
‘g w &
‘cJ &
*I I I I 1 I Oln Cnlnmll+lnmomca I I 1 I 1 I I I I I (Nr-looml-lnmo I I I 1 i I I J I I I I { 1{ I I i 1 I G:&&GAG&o I I I I 1 I I I I I
& al &
22 HH
‘1 A
Y-1 d^ m^ ‘hmm
,.4^ ‘h(nm 044 “
v-l ccl
3.5 Mechanical pro~erties. After^ all^ heat^ treatments,^ including^ stress relief, the forgings shall meet the requirements for mechanical properties specified in table 111 (see 4.4.3.1.4). If it is not practical to test for mechanical properties after stress relief, a section of prolongation may be subjected to a simulated stress relief and tested (see 3.9) with the exceptior~ that all mechanical testing required for acceptance shall be performed. In the case where mechanical property data are required from each end of che forging and the manufacturer wishes to perform simulated stress relief, a section of prolongation from each end of the forging shall be subjected co simulated stress relief. It is not intended that mechanical properties be determined following stress relief of weld clad areas. — — ——_.— —
TABLE III. )4echanical DroDercies.
Class 1 Class 2 Class 3 Class 4 Class 5 Class 6
YieJd strength at 0.01. (^) 75,000 (^) 55,000 45,000 35,000 (^) 75,000 90, percent offset, pounds per square inch (lb/in’) minimum
Yield strength at 0. percent offset lb/in minimum y
Tensile strength, lb/inz (^) 95,000/ 80,000/ 75,000/ 60,000/ 105,000/ 110,000/ 115,000 100,000 95,000 80,000 130,000 140,
Elongation in 2 inches, longitudinal, percent
Elongation in 2 inches, transverse , percent ~
Reduction of area, longitudinal, percent
Reduction of area, transverse, percent ~
Charpy V-notch impact (foot pounds) ~ Test temperature, degrees Fahrenheit (’F) plus 10* minus 30 * 3 plus 28&
Brinell hardness 10-mM standard ball 3000-Kil.ogram load ~
~ When transverse properties are required (see 6,2.1), this applies to shaft couplings, sleeves, (^) and as specified for similar parts. z/ Average of three tests, minimum. No test shall be below the average required minimum by more than 5 foot-pounds. ~ Impact values shall be recorded. ~ See 3.7.3. .j~/T:)1,~1reportccl for infOrmati.0~1 0111{.*
of spray nozzles, (^) and the flow rate of the quenchant shall be adequate to provide for proper quenching. Maintenance , number and location of spray nozzles, and flow rate of quenchant shall be specifically addressed in the quality control program (see 4.1.1).
3.8.1.1 Horizontal quenching. When horizontal quenching is employed for hollow forgings, a mechanism (e.g. water lance) shall be used to ensure that the inside diameter of the component receives adequate quenchant flow.
3.8.2 Heat treating eauinment and controls. Continuous or automatic heat treating equipment may be employed, provided it produces heat treated material to meet the requirements of this specification. For the particular loading and size range of the pieces being heat treated, the temperature recording equipment shall be proven to correlate with actual temperature of the material and shall be maintained and calibrated on a regular basis. The LeLxIp~LaLuKe of che furnace cha~ge shall be recorded during the heating, holding and cooling cycles of the heat treatment. After the-charge reaches the selected temperature control setting, furnaces shall maintain the temperature of any point of the furnace charge within plus or minus 25”F.
3.8.2,1.Heat treatment eauirment and Procedures. Heat treating equipment and procedures shall be in accordance with MIL-sTD-1684, when specified (see 6.2,1),
3.8.2.2 JkaL ~reatment records. A^ record^ oi^ the^ cime^ and^ temperature^ of all heat treatments shall be available for inspection by the contracting activity.
3.8.3 Stress (^) rel ief tempera ture. Unless othemise specified (see 6.2.1), the stress relieving temperature shall be at least 50”F below the tempering temperature and shall be not less than 1.050°F.
3.8.3.1 Cooling rate. For classes 1, 2, 3, and 4 stress relief shall be followed by furnace cooling to 600”F under uniform conditions at an average rate not to exceed 150”F per hour. The part may be cooled in still air when the temperature of the part is below 600”F. Report cooling rate for classes 5 and 6.
3.8.4 Microstructure. Specimens from all forgings, when examined at a magnification of 100 diameters, shall show a homogeneous structure; that is, one in which the normal constituents are evenly distributed, free from decided segregation of any constituents, or excessive inclusions (see 3.8.5). The material, when examined at a magnification of 100 diameters, shall have a grain size of 5 or finer (see 4.4.3.1.6). The area under examination shall show at least 95 percent of the structure with a grain size of number 5 or finer. Tests shall be in accordance with ASTM E 112.
3,.9,5 NOr-metallic ir.cl’~sioncOntertt SpecimPns frOm al] final forgings shall be examined for inclusion content in accordance with ASTM E 45, rne~hod A. The inclusion con~ent shall not exceed:
A 3.Ot 1.5h B 2.5t l.Oh* C 3.Ot 1.5h D 2.ot I.Oh*
*M~yjml.]mlC)W)l~:~]jamett!l-of hea~w nxide inclusion is 0.002 inch as determined by reference to ASTM E 45,”nwthod A-
M11.-s-23284A(sl-l)
——
3.9 Stress relief simulation. (^) When specified (see 6.2.1), material to simulate stress relief treatments shall be heat treated in accordance with 4.4.3.1.8.
3.9.1 Weldment. (^) When specified (see 6.2.1), a full section integral prolongation of material shall be welded, ground flush with the surface and subjected to simulated stress relief treatment in accordance with 4.4.3.1.8, After stress relief, testing shall be performed in accordance with weld procedure qualification requirements of MIL-STD-248.
3.1O Surface finish. The surface roughness of the forging shall not exceed 250 microinches roughness height rating in accordance with ANSI B46.1. The depth of scale, pits, or other defects shall not exceed 0.015 inch (0. millimeters (mm)) and shall not result in an undergauge condition. (^) Isolated, individual pits not over 0,030 inch (0.762 mm) deep or within 6 inches ( ‘an~ Uf Lddli t3Llliii (^) slkill be wcep~d’ble pluvided L~Ie foLgiIAg Lltickness siml.1 nu~ be reduced below the specified minimum (see 4.4.3.1.2, 4.4.3:1.3.1, and 4.4.3,1.3.2).
3.11 Soundness. (^) Sufficient discard shall be taken from each ingot to ensure freedom from pipe and undue. segregation.. (^) Unless otherwise specified herein, the forgings shall be uniform in quality and shall not contain bursts, pipe, flakes, cracks, undue segregation, hard spots, porosity, SeaIIIS, laps, slivers, scabs, (^) or forged in scale. Unless otherwise specified (see 6.2.1), L1;ciu~gi~~g~ SlAdAl AAO~ ~uL~Laillcieieccs LIAdLexceed LIIeaccepLaIwe Cxlwrid o~ appendix A.
3.12 Flame cuttir.q, (^) Flame cutting in the bore or metal removal from the bore by thermal means is not permitted. (^) Flame cutting or metal removal from outer surfaces by any thermal means is not permitted after heat treatment.
3.13 $tabilitv. Material shall be furnished in a stable condition to withstand, for an indefinite time, (^) the development of external or internal cracks.
3.14 Microstructure. (^) The microstructure shall be determined for first article (see 4.4.3.1.7). (^) Deep acid etched forgings up to and including 36 square inches shall be equal to or better than S-3, R-2, and C-3 plates of ASTM E 381. Sizes over 36 and including 100 square inches shall be equal to or better than S-3, R-3 and C-3. (^) For sizes in excess of 100 square inches, microstructure requirements shall be as specified (see 6,2.1).
3.15 Repair of defects.
3.15.1 Removal of defects by (^) Er indi~ or chimzrgl. Defects may be removed by grinding or chipping provided the areas involved are well flared into the surrounding areas and sufficient stock is left to allow subsequent finishing. ‘I’heareas involved shall bE magnetic particle tested in accordance ~-ith MIL-STD-271 to ensure that the defects have been completely removed.
3.15.2 RePa~r welding. Unless otherwise specified (see 6.2.1), repair welding shall not be permitted.
MIL-s-23284 A(SN)
4.1.1 ~es~onsibilitv for complian CR.^ All^ items^ must^ meet^ all requirements of sections 3 and 5. The^ inspection^ set^ forth^ in^ this specification shall become a^ part^ of^ the^ contractor’s^ overall^ inspection system or quality program. The absence of any inspection requirements in the specification shall not relieve the contractor of the responsibility of assuring that all products or supplies submitted to the Government for acceptance comply with all requirements of the contract. Sampling^ in^ quality conformance does not authorize submission of known defective material, either indicated defective
specified
(a) (b)
or actual, nor^ does^ it^ commit^ the^ Government^ to^ acceptance^ of material.
herein are classified as follows:
First article inspection (see 4.3). Quality conformance inspection (see 4.4).
Fir st^ article^ insDection.^ First^ article^ inspection^ shall^ consist^ of all examinations and tests as specified herein.
4,3.1 First.-—— article.—.— sa~~q~,. The first article sample shall consist of sufficient ma~erial. from one heat to obtain measurements of the notch toughness, mechanical properties of the materials, its weldability, response to stress relief, and the first article inspection.
4.3.2 Firs t articl e insDection^ reDort.^ When^ specified^ in^ the^ contract or order, a first article inspection report shall be prepared (see 6.2.2 and appendix B).
4.4 Oualitv conform ante inspection. Quality^ conformance^ inspection shall consist of the inspections specified in 4,4.3. When^ specified^ in^ the contract or order, a certificate of compliance shall be prepared (see 6.2. and appendix C). 4,4.1 &@.
4.4.1.1 Lot for chemical com~osition. Each heat for ingot cast and each ladle for strand cast steel. shall be a lot for chemical analysis. In^ the^ case of continuous casting, each bloom, billet^ or^ slab^ utilized^ for^ reforging^ shall be considered a lot. For remelted vacuum arc remelt or electroslag remelt products, (^) a lot for analysis consists of the products of each remelted ingot of each melt. In the case of secondary melting or ladle refining, each charged vessel is considered a lot for heat analysis.
4.4.1.2 Lot for tensile and impact tests.
QQuDLk. unless^ otherwise^ specified^ (see^ 6.2.1),^ all^ forgings^ Of^ one^ design, produced from the same heat or melt, and heat treated in the same furnace charge , shall constitute a lot.
4.4.1.2.2 Forzi (^) QgS with an as heat treated wei~ht of 1.000 Pounds or more. Unless^ otherwise^ specified^ (see^ 6.2.1),^ each^ forging^ shall^ constitute^ a lot.
1 ‘-lA .)
4.4. 1.3 ~t for visual and dimensional test. Unless otherwise specified (see 6.2.1), (^) each forging shall constitute a lot.
4.4.1.4 Lot for ultrasonic, xnametic ~article and dve Denetrant tests. Unless otherwise specified (see 6,2.1), (^) each forging shall constitute a lot.
4.4.1.5 t f’r microstructure. The lot for inicrostruccuse tests shall be as specified (se: 6.2.1).
4.4.2 Sam~ling.
4.4.2.1 Samle (^) for chemical analv sis. One sample from a forging in each lot shall be taken for chemical analysis or in the case of propulsion shafting, one sample shall be taken from each end of the forging. (^) If more than one heat is used for a forging, a sample shall be taken from each end of the forging and analyzed separately. In addition, when three or more heats are used for a single forging, heat analyses from each heat shall be required and shall conform to 3.4.1. Samples shall be taken at the mid-radius of solid forgings and at the mid-wall thickness of hollow forgings, near the end of the forging, usually in a prolongation. (^) Each sample for chemical analysis shall consist of at least 2 ounces of chips and shall be free of oil, grit or other foreign matter, Solid samples shall be taken in lieu of chips when the analysis is made by the spectrographic method.
4.4,2.2 Sampl~nE for-mechanical tests, One sample from a forging in each lot shall be taken for mechanical tests. Forgings for shafts, sleeves, rudder stocks and diving plane stocks shall have one sample removed from each end of a forging in each lot. (^) For forgings with large flanges or other enlargements , the cross-sectional area of each prolongation shall be approximately the same as the average cross -sectional area of the rough forging, exclusive of flanges or enlargements.
4,4,3 Inspection.
4.4.3.1 Tests and examinations.
4.4.3.1.1 Chemical analysis. The samples selected in accordance with 4.4.2.1 shall be analyzed in accordance with ASTM A 751 and shall conform to 3 4,
4.4.3.1.2 J)imensional ins~ect ion. Each forging shall be dimensionally inspected and shall conform to 3.7 and 3.10.
4.4.3.1.3 Soundness inspection.
4.4,3.1.3.1 Visual insDectioQ. Each forging shall be visually examined i~ft~r final heat trparment, stress relief, and machining. The^ entire^ foI:&iI..[, surface (including bores) shall be visually examined in accordance with MIL-STD-2’71 and shall conform to 3.10 and 3,11.
4.4.3.1.3.2 MaEnetic particle inspection. Unless othemise specified (see 6.2.1), all exterior surfaces of each forging from each lot shall be inspected in accordance with the appendix and shall conform to the acceptance criteria or shall be rejected. For~jngs shall^ he^ in^ the^ finish^ machined condition and shaL1. have a suit:at)le~ir~j.sll(see 3,10). When^ 21~!.OWe(i, defects
.-
MIL-S-23284A(Sli)
4.4.3.1.8.1 Weld procedures. Welding shall be in accordance with MIL- sTD-278. Weld procedure and performance qualification shall be in accordance with MIL-STD-248.
4.4.3.1.8.1.1 (^) Bl ectrodes. Low hydrogen electrodes compatible with S- materials for class 3 and 4 base materials and with S-llA materials for class 1, 2, 5, and 6 base materials shall be used.
4.4.3.1.8.1.2 ld .Om. The weld shall be circumferential for cylindrical pieces. The weld shall conform to plate requirements for other shapes. The depth of the weld joint shall be 1 inch, or 1/2 the wall thickness of hollow forgings, or 1/2 the thickness of solid forgings, whichever is less. A weld joint design in agreement with B2J.1 of MIL-STD- shall be used except a maximum incline of 7 degrees shall be allowed on the non-beveled edge. Impact specimens shall be removed from the non-beveled edge.
4.4.3.1,8.1.3 Imuact specimens. Impact specimens shall be removed as near as practical to mid-depth of the weld joint. The longitudinal axis of heat affected zone specimens shall be perpendicular to the “non-beveled” (maximum bevel of 7 degrees) face of the weld joint. The notch opening shall face the free surface of the piece. They shall be polished and etched to define the heat affected zone prior to machining the notch. Coupons^ shall^ be cut in such a manner as to include as much as possible of the heat affected zone in the resulting fracture.
4.4.3.2 Test specimens.
4.4.3.2.1 Trees of specimens. The test specimens shall conform to the largest test specimens which can be produced from the test prolongation in accordance with ASTM A 370.
4.4.3.2.2 (^) Cation of test s~ecimen s. For solid shafts, rudder stocks, diving plane stocks and propeller nuts, the specimens shall be taken at a distance from the end of the forging equal to at least the radius. For hollow forgings, the specimens shall be taken at a distance from the end of the forging equal to at least the wall thickness.
4.4.3.2.3 n~ itudinal test sDeclulem.^. Longitudinal test specimens shall be taken from a full-size prolongation of the forging in the direction in which the material is most drawn.
4.4.3.2.4 (^) ‘Jsansverse Lest s~ecimens. Transverse test specimens shall be taken from a full-size prolongation of the forging in the direction perpendicular to which the metal is most drawn. When^ it^ is^ impractical^ to obtain transverse test specimens, longitudinal test specimens shall be taken from the appropriate locations.
4.4.3.2.5 Tensile specimens. In the case of shafts, stocks, sleeves, and couplings, tensile specimens shall be taken from each end of each forging. For solid shafts or stocks, the specimens shall be taken as shown on figure 1. For hollow shafts or stocks, the specimens shall be taken as shown on figure
v
4.4.3.2.6 Microstructure s~ecimens. The microstructure test specimens shall be in accordance wi~h ASTM E 381.
4.4.3.2.7 Charpy (^) V-notch s~ecimens. For shafts, stocks and sleeves, a group of three Charpy V-notch specimens shall be taken from each end of each forging for each test temperature, Other forgings shall have a group of three charpy V-notch specimens removed from one end of the forging. Specimens shall be taken at mid-radius for solid forgings and at mid-wall thickness for hollow forgings (see figures 1, 2, 3, and 4). Specimen and notch position shall be in accordance with the C-L orientation of ASTM E 616 for the crack plane orientation code for bars and hollow cylinders.
4.4.3.2.8 ~rinell hardness determination. At least three hardness test determinations on the outside diameter spaced 120 degrees apart shall be made on each forging in an area representing the heaviest section of each forging wilicl~is LO subsequently be mac-nined.
4.4.3.2.9 Grain size determination. Two cross-sectional grain size specimens shall be obtained from undeformed ends of two broken mechanical property acceptance test specimens from each lot and tested. When a lot consists of more than one forging the two specimens (^) (mid-wall or mid-radius specimens) shall be obtained from different forgings. (^) For those forgings with test areas provided on each end of the forging, one specimen shall be obtainecl from each test area of two forgings in the lot or from one forging if the lot uonsiscs of one forging. At the option of the contractor, samples may be taken from material adjacent to the acceptance mechanical property specimens in lieu of samples taken from broken mechanical property acceptance test specimens.
4.4.3.2.10 Macroscopic etch snecimens. (^) Cross-sectional specimens for the macroscopic etch test shall. cor.sist of material. approximately l,t2-ir.ch thick cut from each end of the forging and subject to a hot acid etch.
4.4.3.2.11 Micro scoDic specimens. One or more cross-sectional specimens shall be taken from each location where a tensile specimen is taken. When a broken tensile or Charpy impact specimen is used for this test, the microscopic specimen shall be taken from the unbroken end of the specimen.
4.4.3.2.12 Nonmetallic inclusion content specimens. One longitudinal specimen shall be taken from each end of each hollow forging as shown i.n figure 5. The specimen shall be removed a minimum of l-inch below the outside surface. In the case of propeller nuts and couplings, only one specimen shall be taken.
4.4.3.2.13 S~ecimens reauired when multiDle Darts are forzed from one
w. When^ multiple^ parts^ are^ made^ and^ heat^ treated^ as^ one^ forging,^ both ends of the forging shall be sampled, (^) Location and number of specimens f-or tlic!sampling required (^) !;hall1:)6:g<)ver”n(!(jby the largest: or pri.ncipdl t(>I”lJ,in~,s of the combined farging. (^) Tests will not be required for the individual pieces when tests are made on the forging as a whole.
4.5 Resubmittal of re~ected for~in~s or lots.
A
Levels A and B - Type 11 - weather^ resistant. Category 1 - general use.
Level C - Type 1 - non-weather resistant. Category 1 - general use.
5.2 preservation. Preservation shall be level A or commercial as specified (see 6.2.1).
5.2.1 @vel A.
5.2,1.1 Presentation application. Machined^ or^ finished^ surfaces^ of forgings shall be protected with an application of preservative conforming to grade 1 or grade 4 of MIL-C-16173.
5.2,1,2 ~rau. Forgings^ without^ presemation^ application,^ shall^ be individually wrapped with a minimum of two thicknesses of 40-pound basic weight kraft paper. (^) Forgings with preservative application, two thicknesses of equal weight greaseproof paper shall be used for wrapping. When^ complete wraping is not pratical because of configuration, size or weight, the finished or polished surface(s) shall be provided protection from damage with suitable covers. When specified (see 6.2.1), the kraft paper shall be fire resistant meeting the requirements of A-A.-1894.
(^5) .&.& 9 9 ~~~er~+a~. Unless otherwise Gpccified (see 6.2.1), commercial preservation (packaging) shall be in accordance with the requirements for “castings” of ASTM A 700, section 14.
5.3 Packing. (^) Packing shall be level A, B, C, or commercial as specified (see 6.2.1).
5.3.1 (^) General requirements for Ievels^ A. B. and^ C.^ Shipping^ containers selected (see 5.3.2) shall be of minimum weight and cube of uniform size and construction, and contain identical quantities of identical forgings of one size, melt or lot number. Forgings that are packed into containers shall be blocked, braced or otherwise secured to prevent their movement and damage. Forging having projections that may be damaged during handling, shipment and storage shall have the projections protected with batten strips.
5.3.2 Levels^ A.^ B. and^ C^ containers.^ Forgings^ shall^ be^ packed^ in nailed wood, wood cleated plywood or wirebound boxes, or in open or covered wood or wirebound crates as specified in MIL-STD-2073-lA, Appendix C for the level of packing specified (see 5.3) and herein. Unless otherwise specified (see 6.2.1), containers selection shall be at the option of the supplier.
5.3,2.1 Packin~a uantitv and weizht.
5.3.2.1.1 ~mall. fow (fini.shed or nolish ed^ and^ other>.^ Forgings weighing less than 200 pounds shall be packed individually, or in multiple units in boxes (see 5.3.2). (^) Unless otherwise specified (see 6.2.1), the gross weight of boxes shall not exceed 500 pounds. (^) Boxes exceeding 100 pounds shall be modified with skids in accordance with the applicable box specification.
5.3,2 1 1.1 k_%mll.........-.-._ for~.ggs...glgb.?.r-)-).. For:ings, in lieu of boxing, mav be bundled for shipment, unless by so doing the forgings may be subject to damage. Bundles shall be secured or reinforced with tensioned steel strapping
--s.. --------
] q
as required for wood boxes. For level A packing the gross weight shall not exceed 250 pounds and for levels B and C packing the gross weight shall not exceed 500 pounds.
5.3.2.1.2 Lar~e f.or~in~. Forgings weighing more than 500 pounds shill-l be packed individually, or in multiple units in crates (see 5.3.2). Unless otherwise specified (see 6.2.1), the gross weight of crates shall not exceed 1000 pounds. Open^ type^ crates^ shall^ be^ provided^ with^ flexible,^ reinforced, waterproof, barrier material shrouds. Plastic shrouds shall be of minimum 0.006 inch thickness. (^) Shrouds shall be secured to prevent damage and loss during handling, shipment and storage.
5.3.3 Comxnercial. Unless otherwise specified (see 6.2.1), commercial packing (packaging) shall be in accordance with the requirements for ‘castings” in ASTM A 700, section 14 and herein.
5.3.3.1 Contai ner modification. Shipping^ containers^ exceeding^100 pounds gross weight shall be provided with a minimum of two, 3- by 4-inch nominal wood skids laid flat, or^ a^ skid-^ or^ still-type^ base^ which^ will^ support the material and facilitate handling by mechanical handling equipment during shipment , srowa~e and stot-a~~
S.fiMarking.
5.4.1 J#evels A. 3. and c Irladditior~ to any special Larking required (see 6.2.1), 3.18 and herein, interior (unit) packs, shipping containers and bundles shall be marked including bar coding in accordance wtih MIL-STD-2073- 1.A.
5.4.2 Commercial. In addition to any special marking required (see 6.2,1), 3.18 and herein and unless otherwise specified (see 6.2.1), marking shall be in accordance with the requirements for “castings” in ASTM A 700, section 14. Bar coding in accordance with MIL-STD-2073-1A shall apply.”
6.1 Jntended IJst?, The six classes of steel are used to make torsional shafts, shafts for ships, sleeves, couplings, propeller nuts, rudder stocks, diving plane stocks, and related parts.
6.2 grderi.n~ data.
6.2,1 ~cauisition zeauiremen~s, Acquisi~ion documents should specify the following:
(a) Title, number, and^ date^ of^ this^ specification. (b) The class of steel required (see 1.2). (c) When first article inspection is required (see 3.1). (d) Melting practices, if other than specified (see 3.2). (e) When vacuum degassing is not required (see 3.2.1). (f) Microstructure requirements for sizes in excess of 100 square inches (see 3.14). (g) k%eTI virgin raw material is required for cririca] ;J,uplir;ilio[~c,(s+’(-?.? ?’I
;)(