
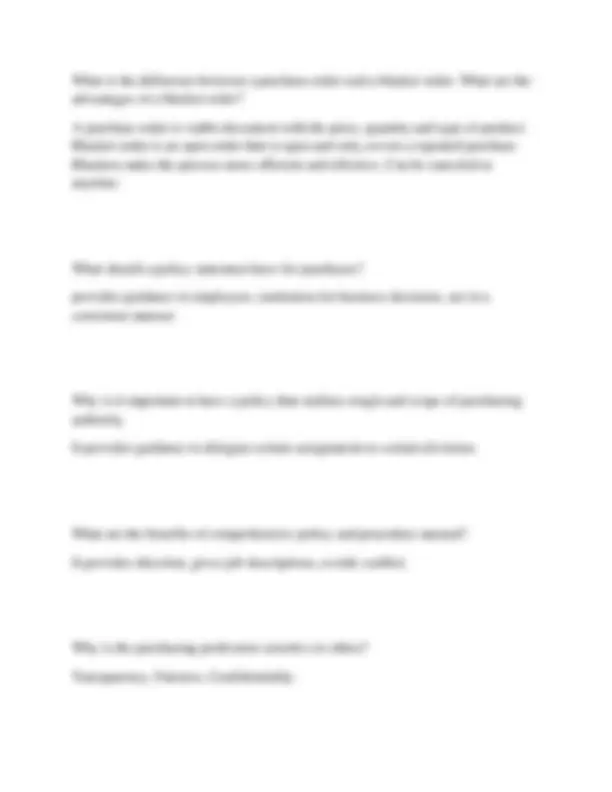
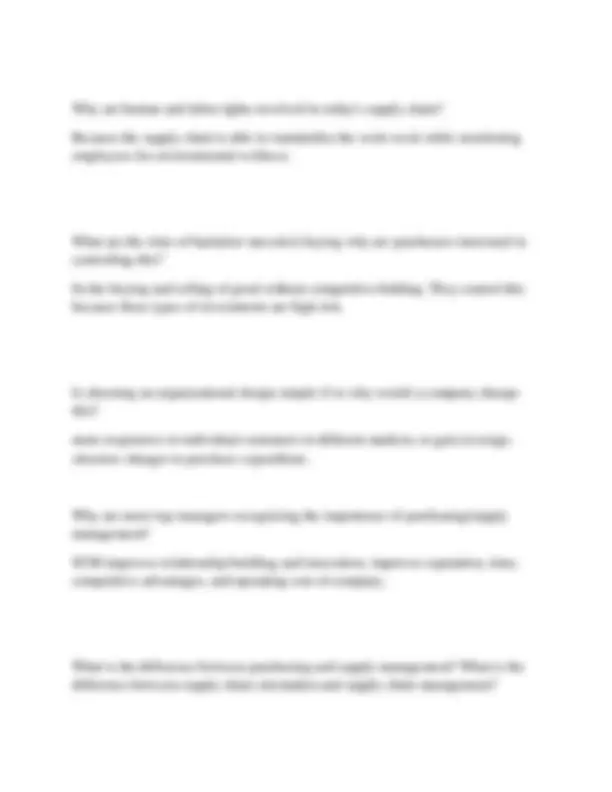
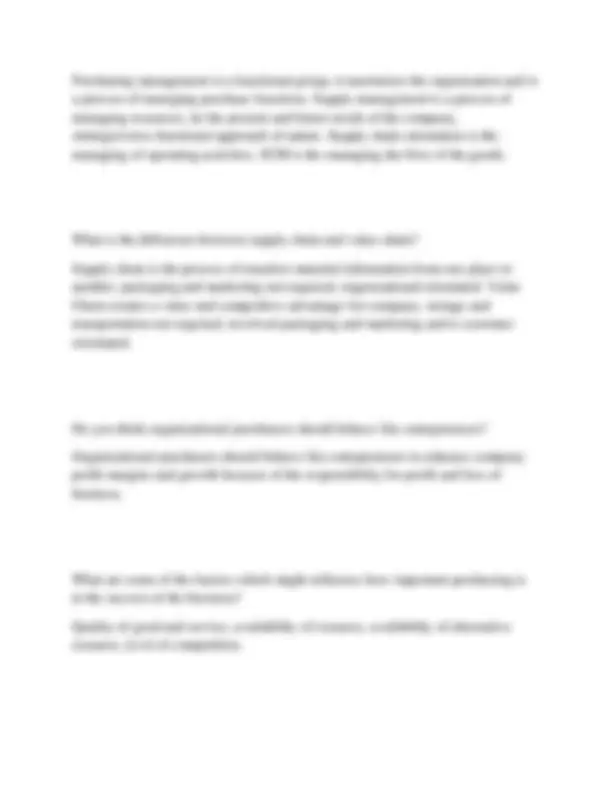
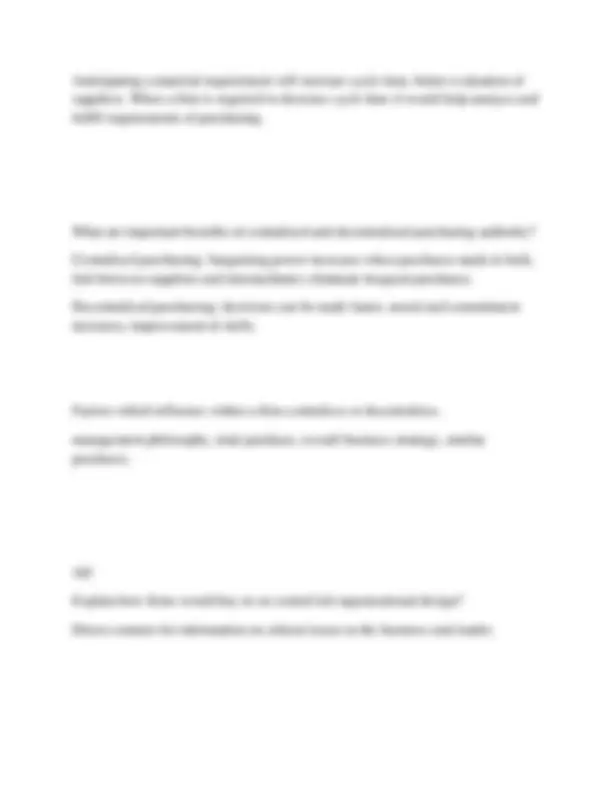
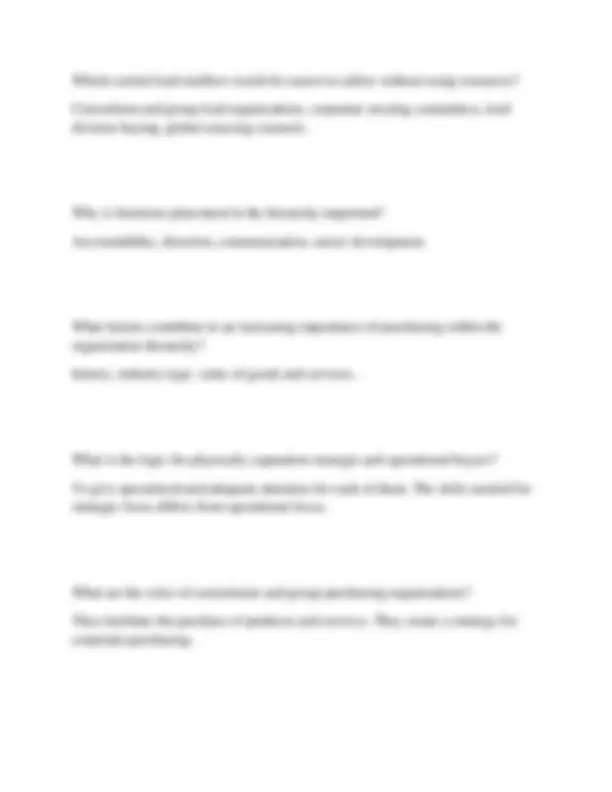
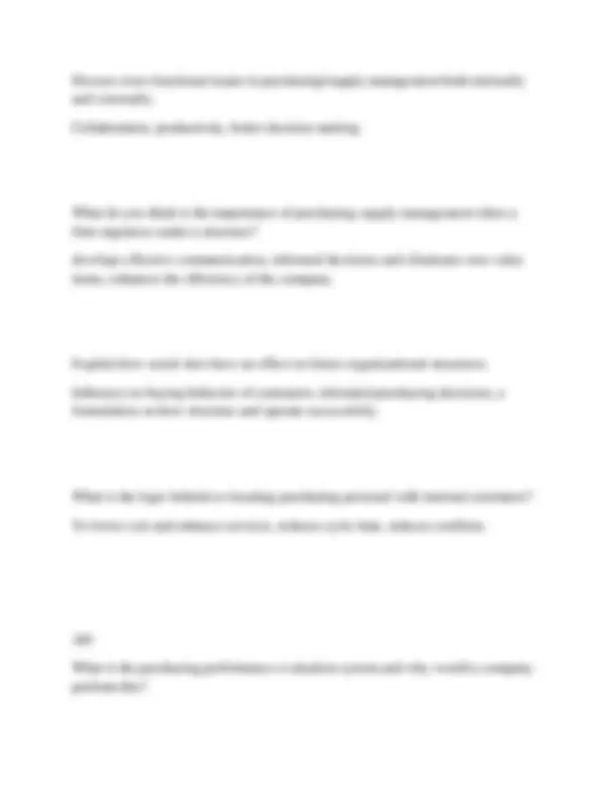
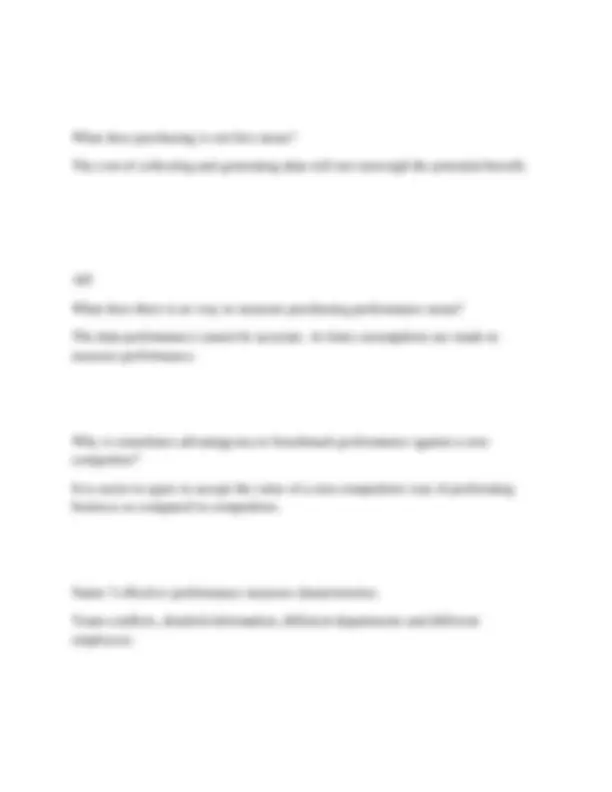
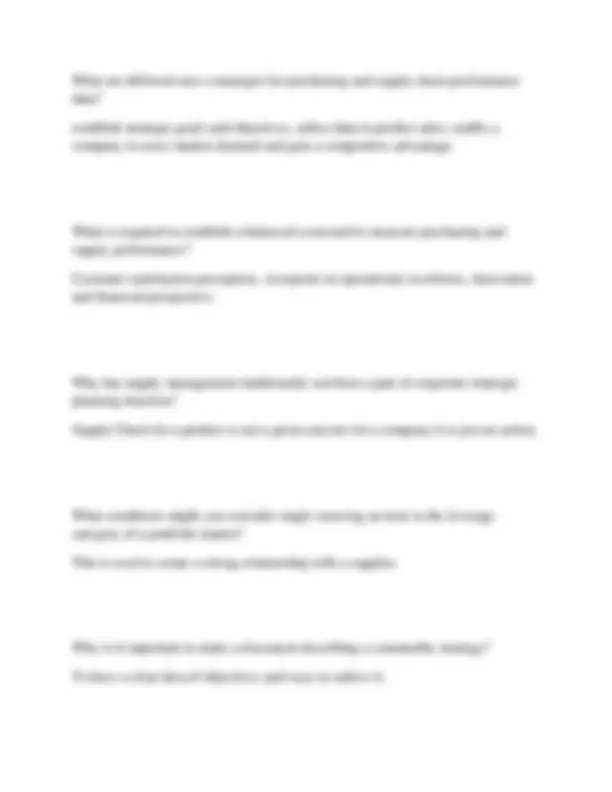
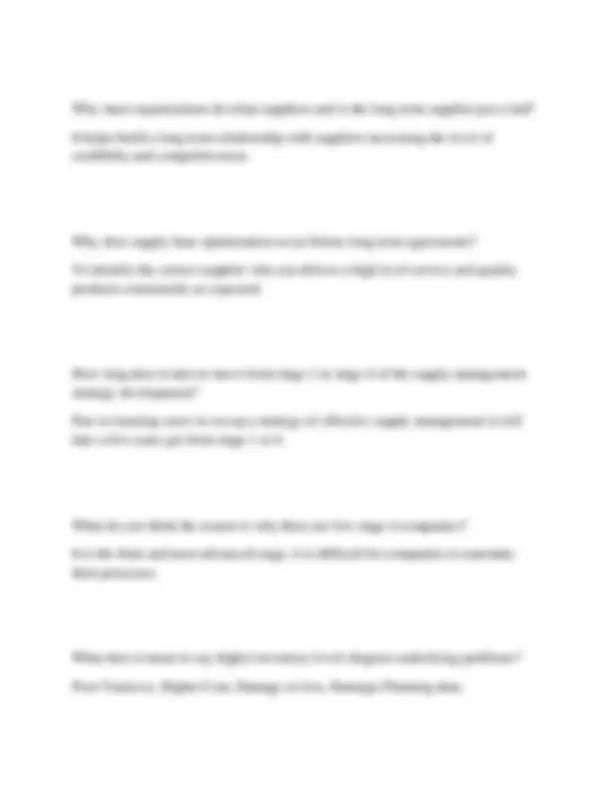
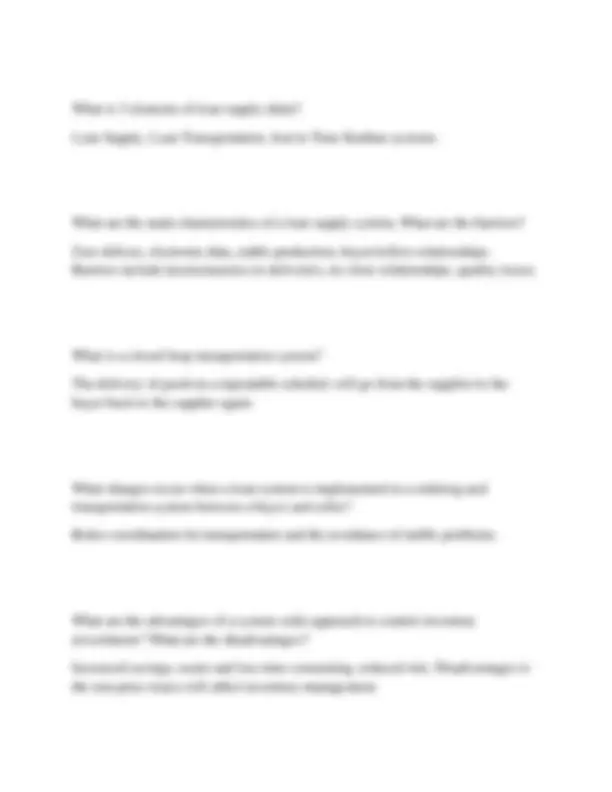
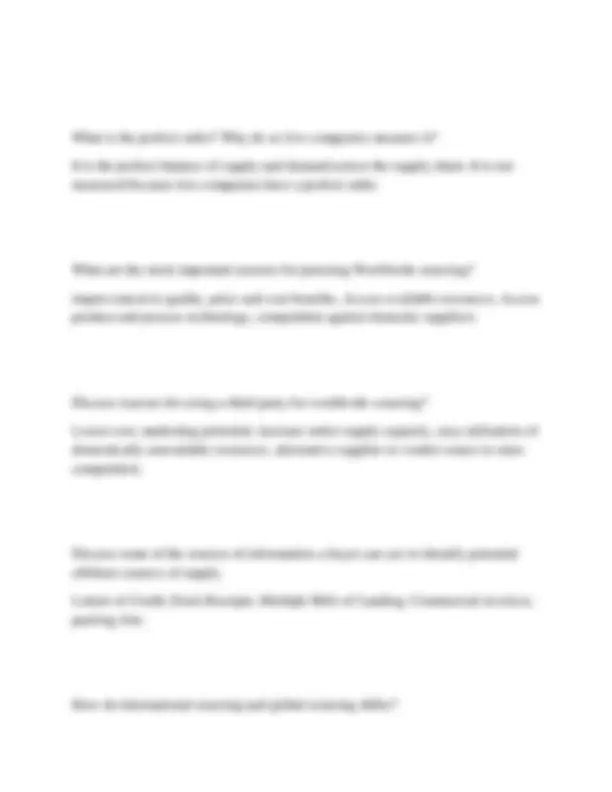
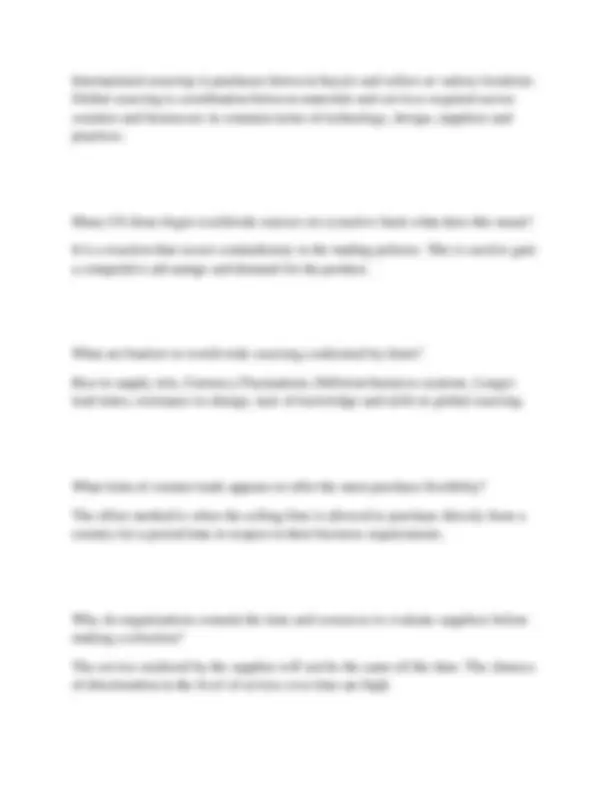
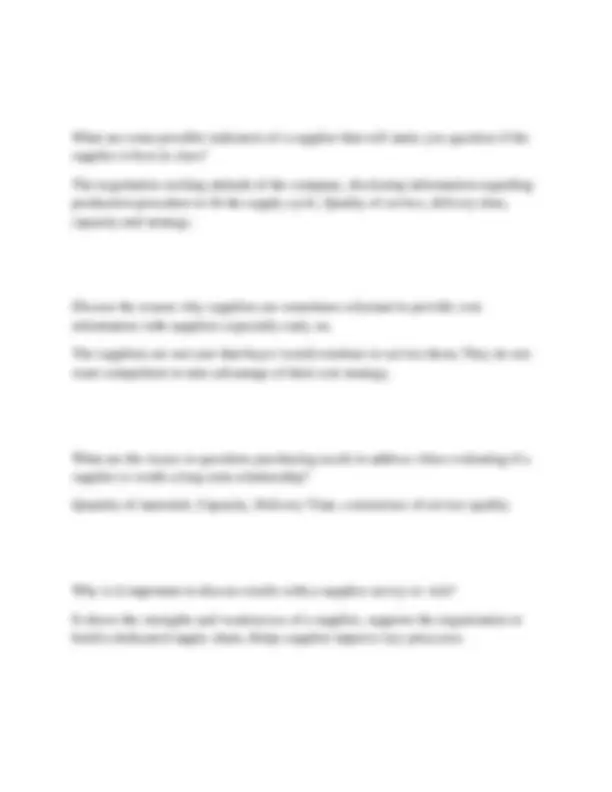
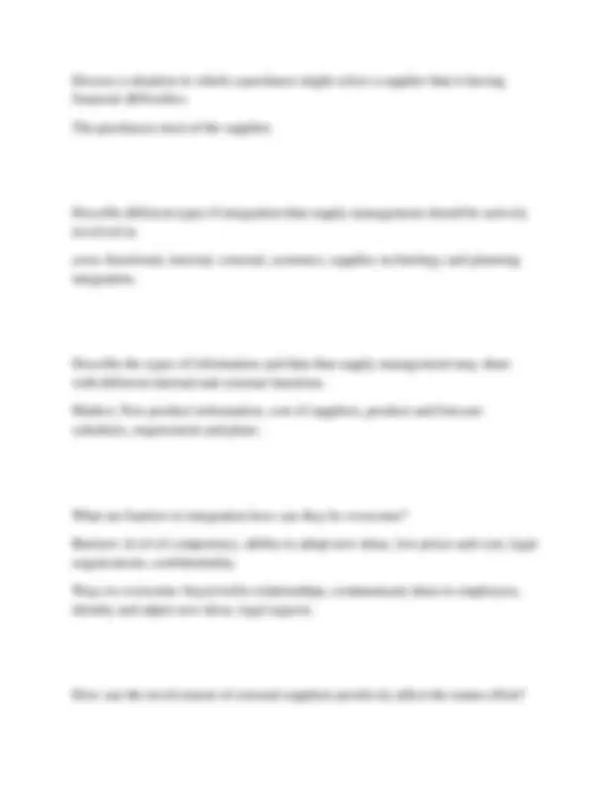
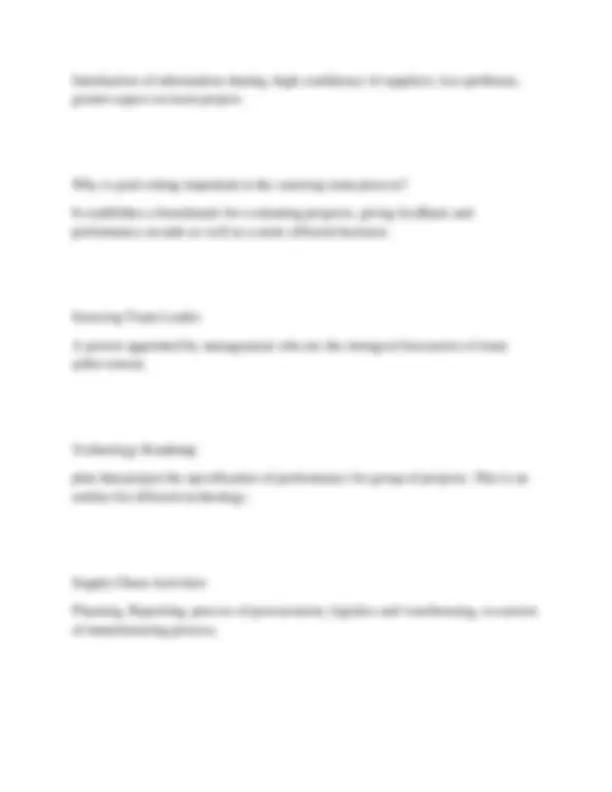
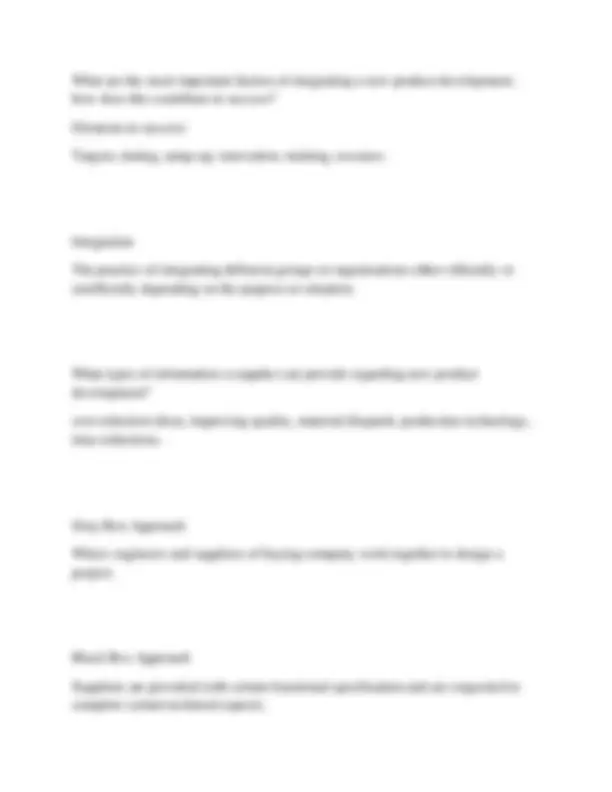

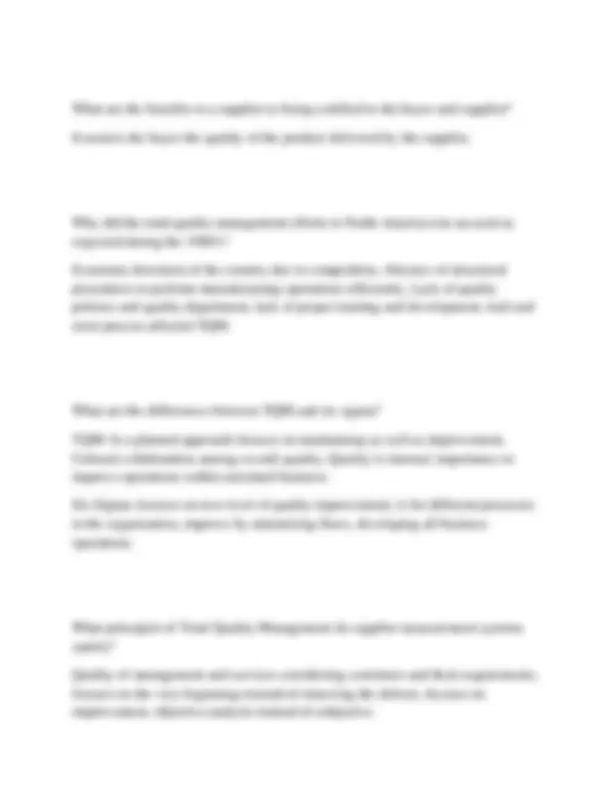
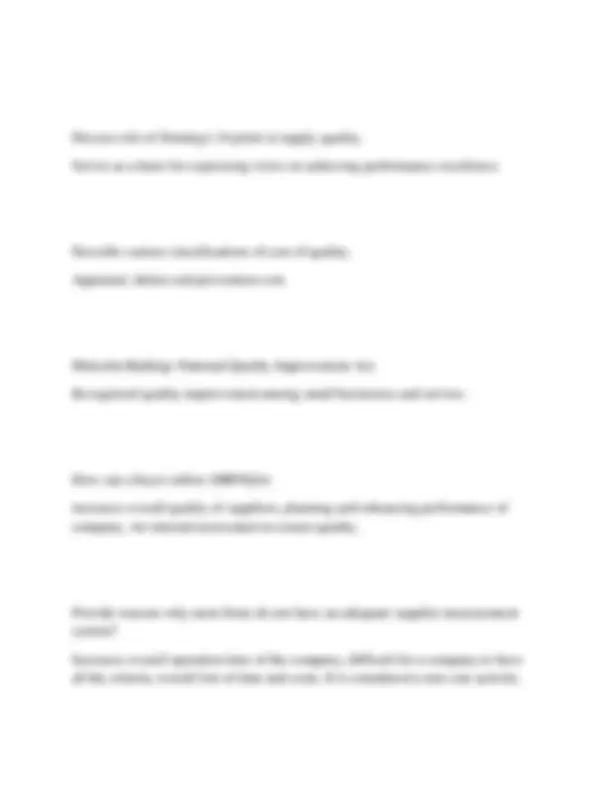
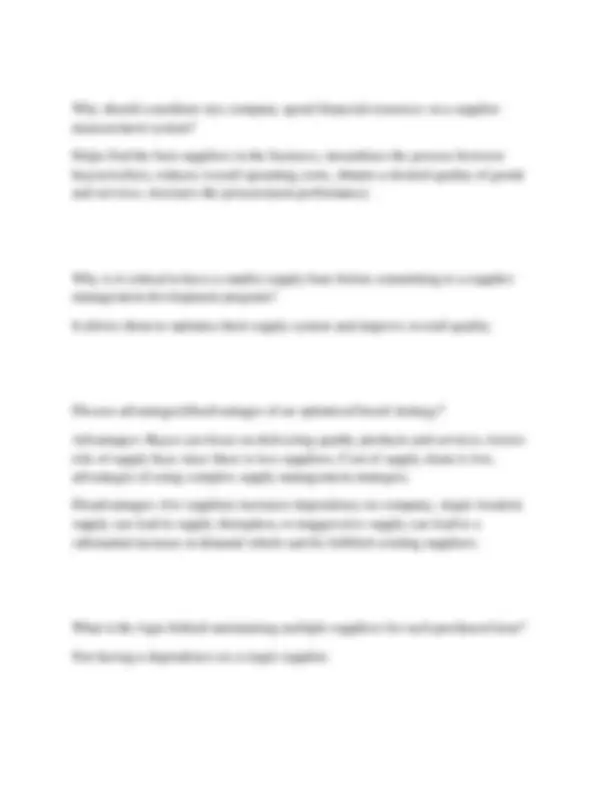
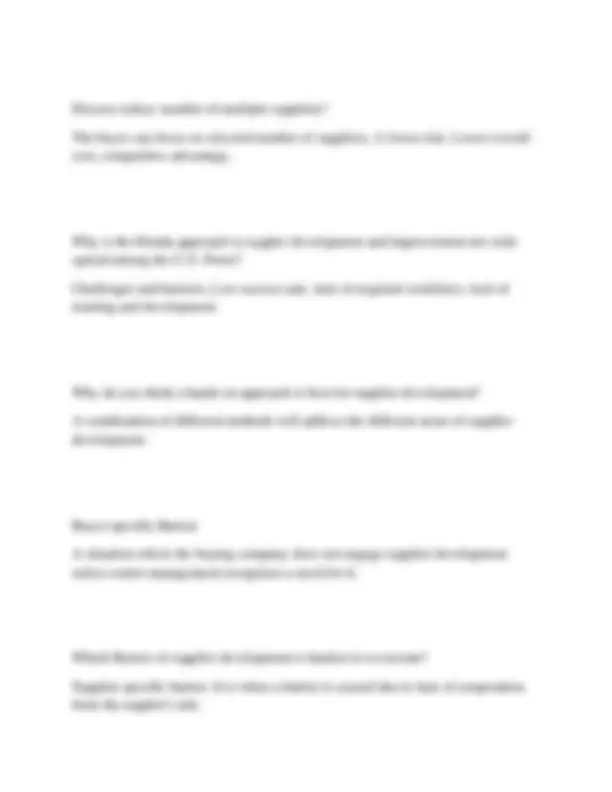
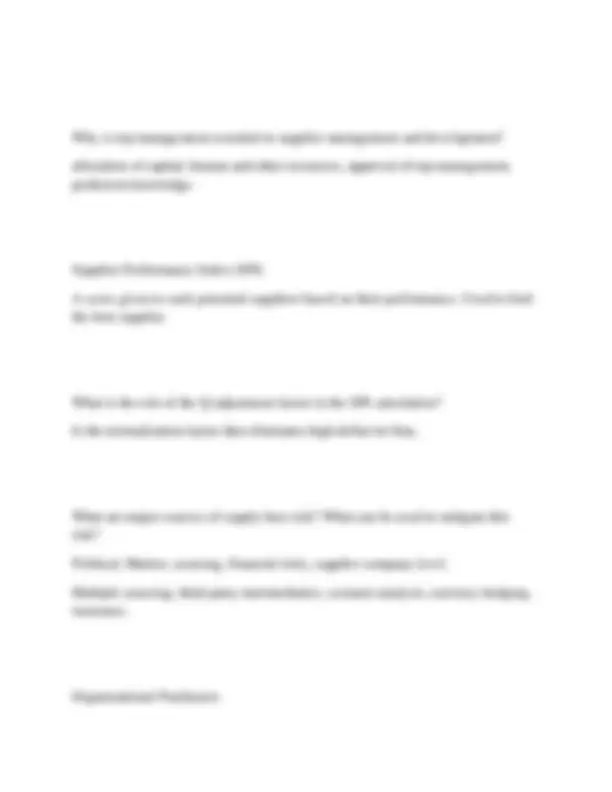
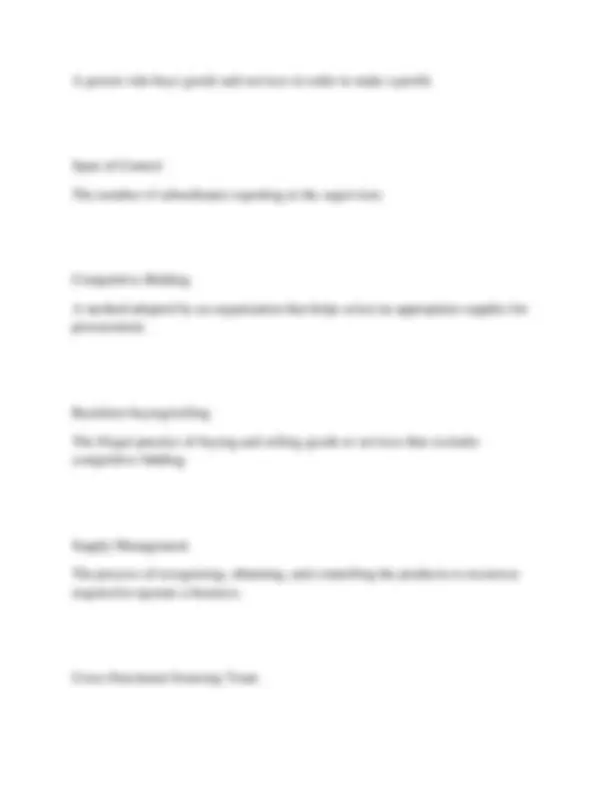
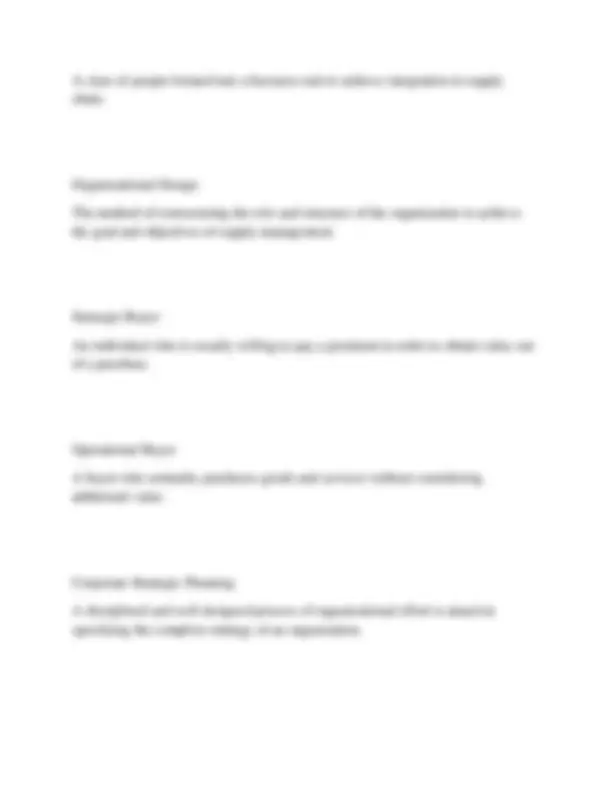
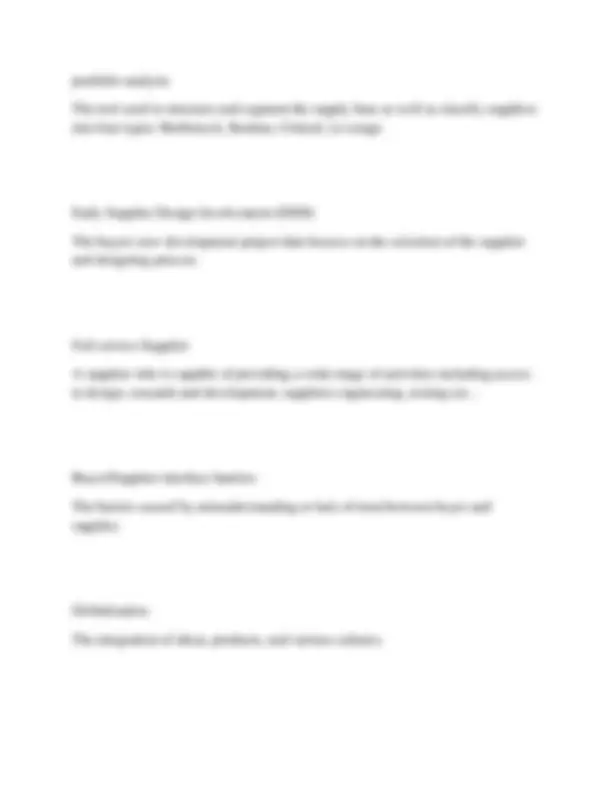
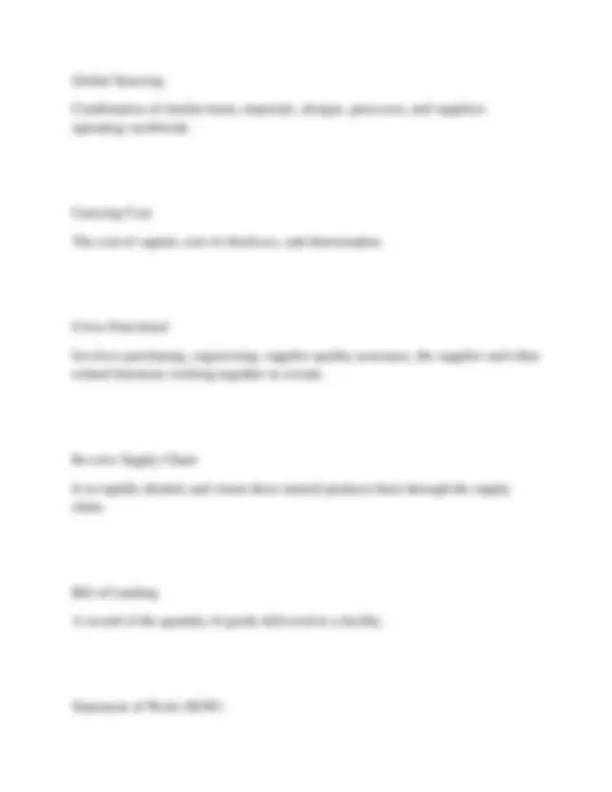
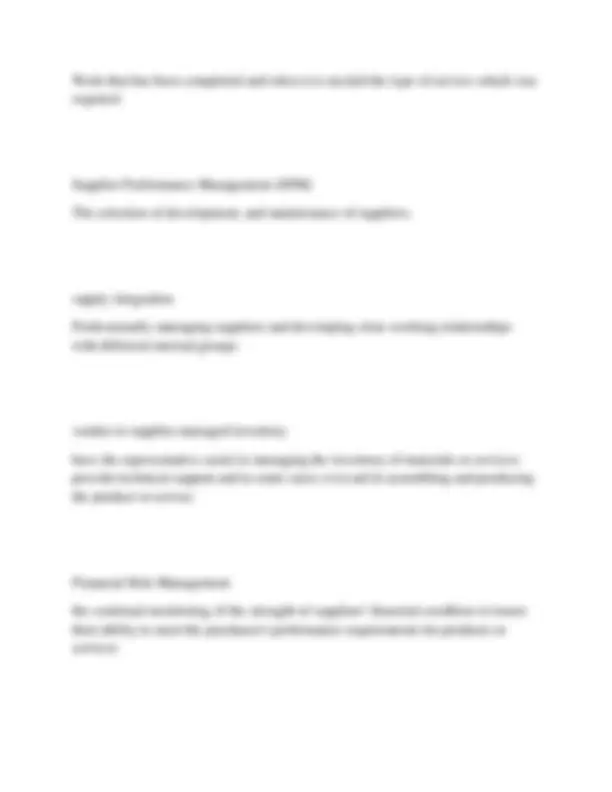
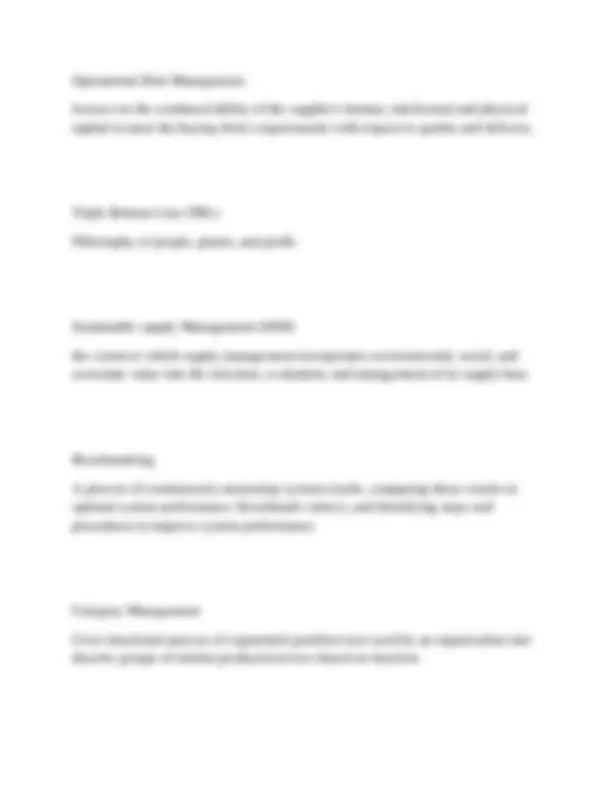

Study with the several resources on Docsity
Earn points by helping other students or get them with a premium plan
Prepare for your exams
Study with the several resources on Docsity
Earn points to download
Earn points by helping other students or get them with a premium plan
Community
Ask the community for help and clear up your study doubts
Discover the best universities in your country according to Docsity users
Free resources
Download our free guides on studying techniques, anxiety management strategies, and thesis advice from Docsity tutors
MNG 2601 PURCHASING & SUPPLY CHAIN MANAGEMENT EXAM 2025-2026 PREP QUESTIONS AND ANSWERS GRADED A+ UNISA MNG 2601 PURCHASING & SUPPLY CHAIN MANAGEMENT EXAM 2025-2026 PREP QUESTIONS AND A
Typology: Exams
1 / 37
This page cannot be seen from the preview
Don't miss anything!
Why do firms no longer rely on competitive bidding when awarding purchase contracts?
less suppliers in market, requires early procurement materials, cannot determine risks and costs.
List documents which are covered by E-procurement tools.
Proper purchasing document, cost free document, other supporting documents.
What are the advantages/disadvantages of E-Procurement tools?
Advantage: No paperwork, time reduction, error reduction, communication improvement, reductions in costs.
Disadvantage: push back from users, frictions and resistance, communication gap.
Why is it important to measure and monitor supplier performance improvement?
ensure performance initiatives, manage purchasing of good and services, identify opportunities and purchasing trends, support future purchasing decisions.
How does just in time purchasing and production system reduce the need for certain purchasing documents?
It gives a continuous amount of supply of product or inventory to reduce documentation. Documents regarding warehouse and transportation are not needed.
Why has purchasing been involved with transportation and other non-purchasing areas?
Its an important kind of buying dealing with logistics providers and suppliers. This includes assembly, packaging, and warehouse production items.
What is the difference between capital equipment and routine supplies?
Capital equipment is a capital expenditure, profits can be earned only in the future, requires lump sum to buy. Routine Supplies is a revenue expenditure profit earned immediately, requires less to purchase.
Why are human and labor rights involved in today's supply chain?
Because the supply chain is able to standardize the work week while monitoring employees for environmental wellness.
What are the risks of backdoor maverick buying why are purchasers interested in controlling this?
Its the buying and selling of good without competitive bidding. They control this because these types of investments are high risk.
Is choosing an organizational design simple if so why would a company change this?
more responsive to individual customers in different markets, to gain leverage, structure changes to purchase expenditure.
Why are more top managers recognizing the importance of purchasing/supply management?
SCM improves relationship building and innovation, improves reputation, time, competitive advantages, and operating cost of company.
What is the difference between purchasing and supply management? What is the difference between supply chain orientation and supply chain management?
Purchasing management is a functional group, it maximizes the organization and is a process of managing purchase functions. Supply management is a process of managing resources, its the present and future needs of the company, strategic/cross functional approach of nature. Supply chain orientation is the managing of operating activities. SCM is the managing the flow of the goods.
What is the difference between supply chain and value chain?
Supply chain is the process of transfers material information from one place to another, packaging and marketing not required, organizational orientated. Value Chain creates a value and competitive advantage for company, storage and transportation not required, involved packaging and marketing and is customer orientated.
Do you think organizational purchasers should behave like entrepreneurs?
Organizational purchasers should behave like entrepreneurs to enhance company profit margins and growth because of the responsibility for profit and loss of business.
What are some of the factors which might influence how important purchasing is to the success of the business?
Quality of good and service, availability of resource, availability of alternative resource, level of competition.
Who are purchasing internal customers?
The employees of the organization and internal users of the product.
Discuss the contributions a purchasing department can make to the corporate strategic planning process.
procurement of materials, price evaluation, compliance of policy.
List the areas that are typically within purchasing span of control.
Spend Analysis, demand management and specifications, category management, contract management, cost management and supplier management.
Describe how purchasing becomes aware of purchasing requirements?
Quality guarantee, reasonable pricing, on-time delivery, safety, maintenance and service.
How is anticipating a requirement or a need through purchasers involvement on new product development different than reacting to a purchase need?
Anticipating a material requirement will increase cycle time, better evaluation of suppliers. When a firm is required to decrease cycle time it would help analyze and fulfill requirements of purchasing.
What are important benefits of centralized and decentralized purchasing authority?
Centralized purchasing: bargaining power increases when purchases made in bulk, link between suppliers and intermediaries eliminate frequent purchases.
Decentralized purchasing: decisions can be made faster, moral and commitment increases, improvement of skills.
Factors which influence wither a firm centralizes or decentralizes.
management philosophy, total purchase, overall business strategy, similar purchases.
Explain how firms would buy in on central led organizational design?
Direct contacts for information on critical issues to the business unit leader.
Discuss cross functional teams in purchasing/supply management both internally and externally.
Collaboration, productivity, better decision making.
What do you think is the importance of purchasing supply management when a firm organizes under a structure?
develops effective communication, informed decisions and eliminates non-value items, enhances the efficiency of the company.
Explain how social sites have an effect on future organizational structures.
Influence on buying behavior of customers, informed purchasing decisions, a formulation on how structure and operate successfully.
What is the logic behind co-locating purchasing personal with internal customers?
To lower cost and enhance services, reduces cycle time, reduces conflicts.
What is the purchasing performance evaluation system and why would a company perform this?
A formal approach to purchaser evaluates effectiveness and efficiency measures. It helps make informed decisions, performance of the team, effectively utilizes team and motivates employees.
Why would a firm want to measure supplier performance what measures can be performed?
competitive advantage, supplier capabilities, reduced operating cost. revenue, quality, time of delivery, Technology, environmental, efficiency and performance measures.
What is performance bench-marking and why is it used for purchasing performance?
Is a process of establishing the firms target plans, action plans, and strategic plans. It determines area for opportunists, manage changes to performance, increased quality of products.
What are three types of bench-marking which is the most common?
Strategic, operational and support activity bench-marking. It will depend on the requirement of the company.
What is the difference between efficiency and effectiveness measures?
What does purchasing is not free mean?
The cost of collecting and generating data will not outweigh the potential benefit.
What does there is no way to measure purchasing performance mean?
The data performance cannot be accurate. At times assumptions are made to measure performance.
Why is sometimes advantageous to benchmark performance against a non- competitor?
It is easier to agree to accept the value of a non-competitors way of performing business as compared to competitors.
Name 3 effective performance measure characteristics.
Team conflicts, detailed information, different departments and different employees.
What are different uses a manager for purchasing and supply chain performance data?
establish strategic goals and objectives, utilize data to predict sales, enable a company to asses market demand and gain a competitive advantage.
What is required to establish a balanced scorecard to measure purchasing and supply performance?
Customer satisfaction perception, viewpoint on operational excellence, Innovation and financial perspective.
Why has supply management traditionally not been a part of corporate strategic planning function?
Supply Chain for a product is not a great concern for a company it is just an action.
What conditions might you consider single sourcing an item in the leverage category of a portfolio matrix?
This is used to create a strong relationship with a supplier.
Why is it important to make a document describing a commodity strategy?
To have a clear idea of objectives and ways to achive it.
How is purchasing directly and indirectly involved in control of a firms inventory investment?
Unit Costs, Ordering Costs, Carrying Costs, quality costs.
What are some operational problems that excessive work in process inventory might indicate?
materials waiting to be progressed to a different process, capacity bottleneck or breakdown, elongated process.
Discuss several reasons why managers neglect true cost of physical inventory? What has changed their minds?
The major impact of holding more inventories is the effect on a firms working capital. Ordering and carrying inventory has more costs with physical space mandatory for carrying excessive inventory.
Why is control for maintenance, repair and operating inventory difficult for companies?
This is difficult because it the items support production and operations. These items are not apart of the items but are critical for constant operation. Time and cost of maintenance cant be recovered.
What are the benefits of total cost associated with physical inventory?
A financial estimation that helps owners and buyers identify direct and indirect costs is total cost of ownership. Benefits are: planning and budgeting allocated funds, managing asset life cycle, prioritizing a capital acquisition proposal, selecting a vendor, and purchasing decisions.
Which function of physical inventory will purchasing be directly involved in?
Support of production requirement because the key reason is to hold up production requirements and evade supply disruptions.
What are the actions purchasing can take when reducing uncertainty?
Supply Quantity: quantity discounts, reduce inventory investment. Supplier Delivery: order cycle time, global sourcing agreements. Inaccurate demand forecasts: uncertainty affecting inventory, safety stock levels. Extended material pipelines: long distance between supply chains.
What problems do overcasting/undercasting supply chains make?
Many firms fail to recognize what inaccurate forecasting has on volume and velocity in which inventory moves. Over forecasting: High inventory volumes, High carry charges, excessive safety stock levels. Under forecasting: work in process inventory, Higher cost, poor customer service.
What is the perfect order? Why do so few companies measure it?
It is the perfect balance of supply and demand across the supply chain. It is not measured because few companies have a perfect order.
What are the most important reasons for pursuing Worldwide sourcing?
improvement in quality, price and cost benefits, Access available resources, Access product and process technology, competition against domestic suppliers.
Discuss reasons for using a third party for worldwide sourcing?
Lesser cost, marketing potential, increase entire supply capacity, easy utilization of domestically unavailable resources, alternative supplier or vendor source to raise competition.
Discuss some of the sources of information a buyer can use to identify potential offshore sources of supply.
Letters of Credit, Dock Receipts, Multiple Bills of Landing, Commercial invoices, packing lists.
How do international sourcing and global sourcing differ?
International sourcing is purchases between buyers and sellers at various locations. Global sourcing is coordination between materials and services required across counties and businesses in common terms of technology, design, suppliers and practices.
Many US firms begin worldwide sources on a reactive basis what does this mean?
It is a reaction that occurs contradictory to the trading policies. This is used to gain a competitive advantage and demand for the product.
What are barriers to world wide sourcing confronted by firms?
Rise in supply risk, Currency Fluctuations, Different business customs, Longer lead times, resistance to change, lack of knowledge and skills to global sourcing.
What form of counter trade appears to offer the most purchase flexibility?
The offset method is when the selling firm is allowed to purchase directly from a country for a period time in respect to their business requirements.
Why do organizations commit the time and resources to evaluate suppliers before making a selection?
The service rendered by the supplier will not be the same all the time. The chances of deterioration in the level of service over time are high.