
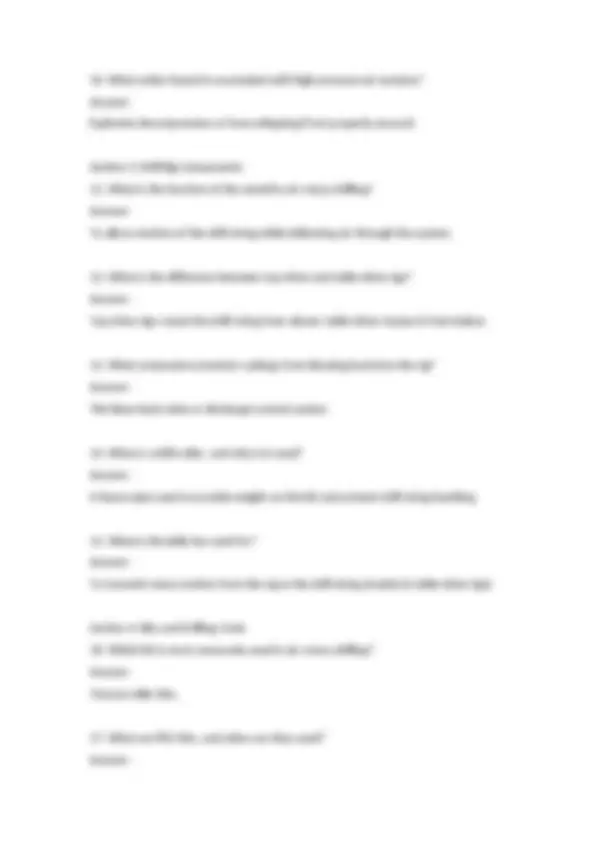
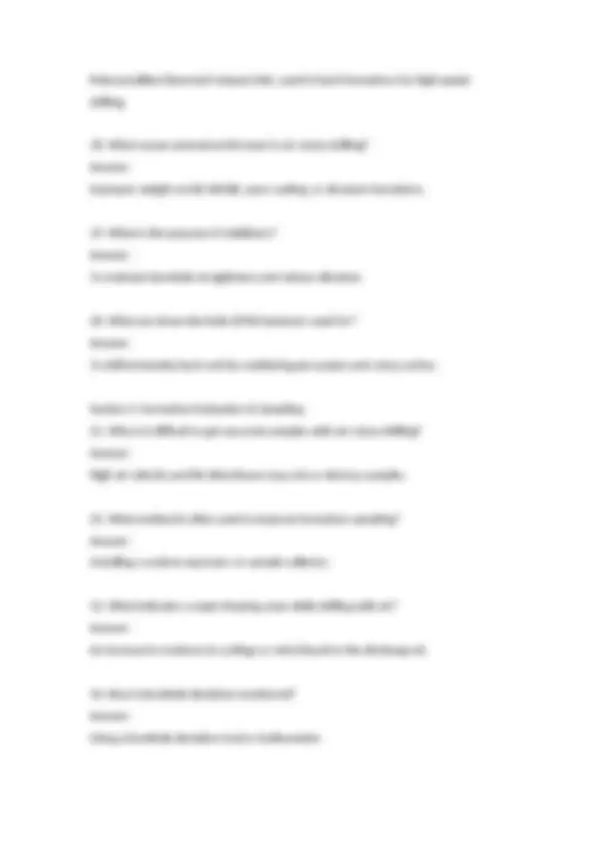
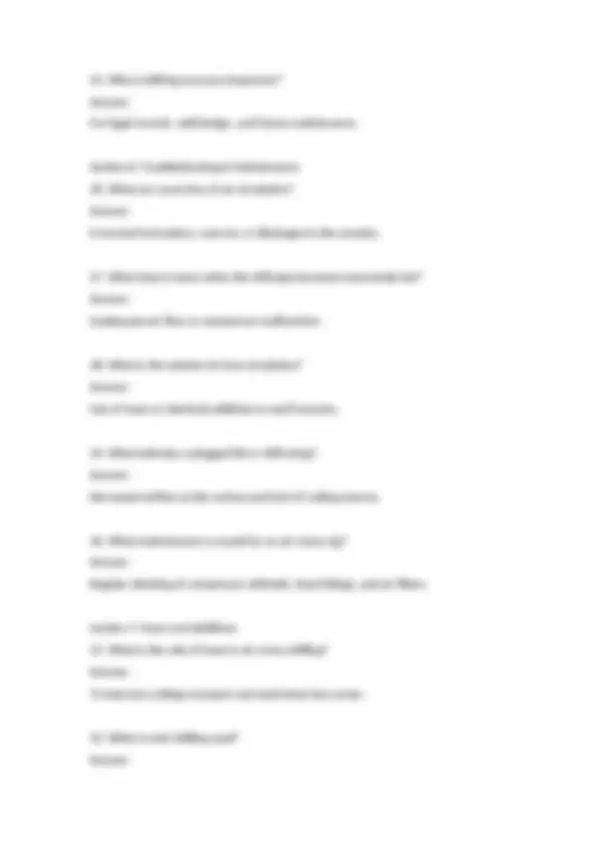
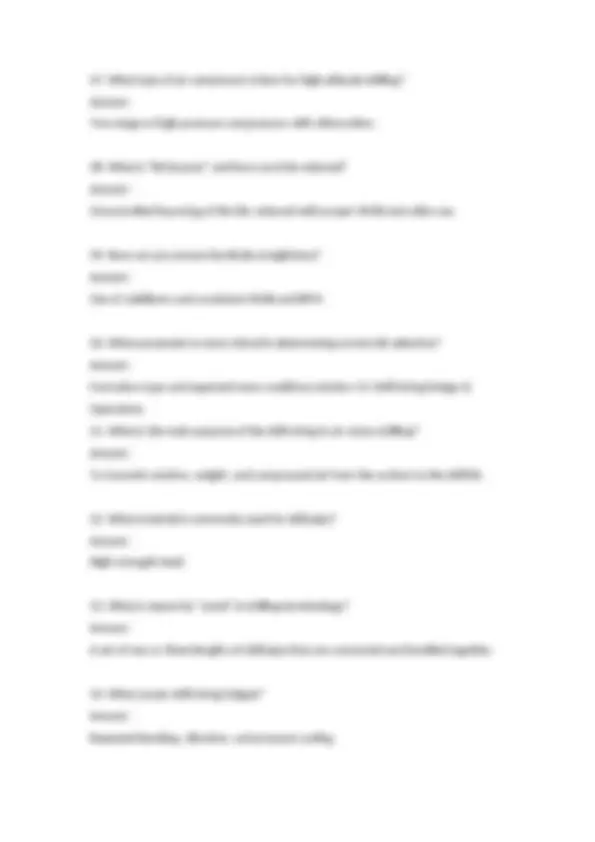
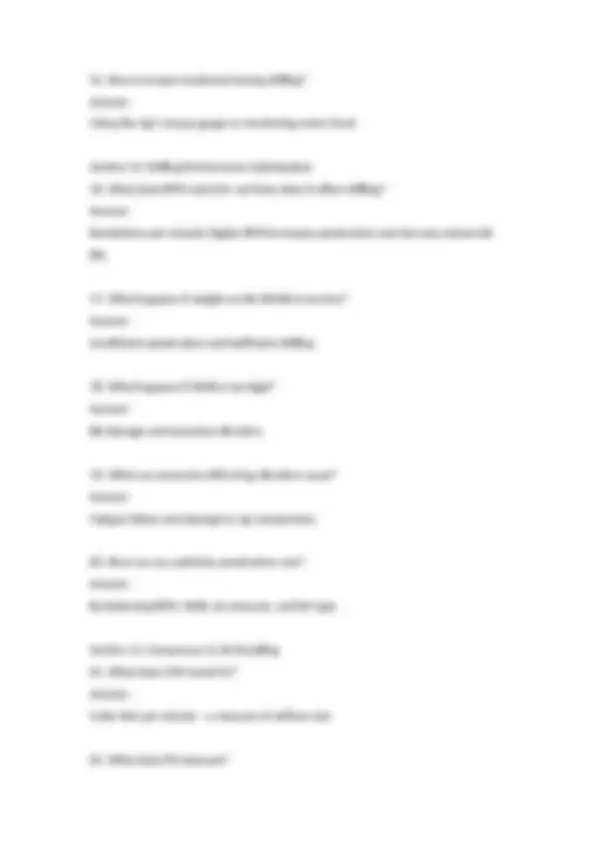
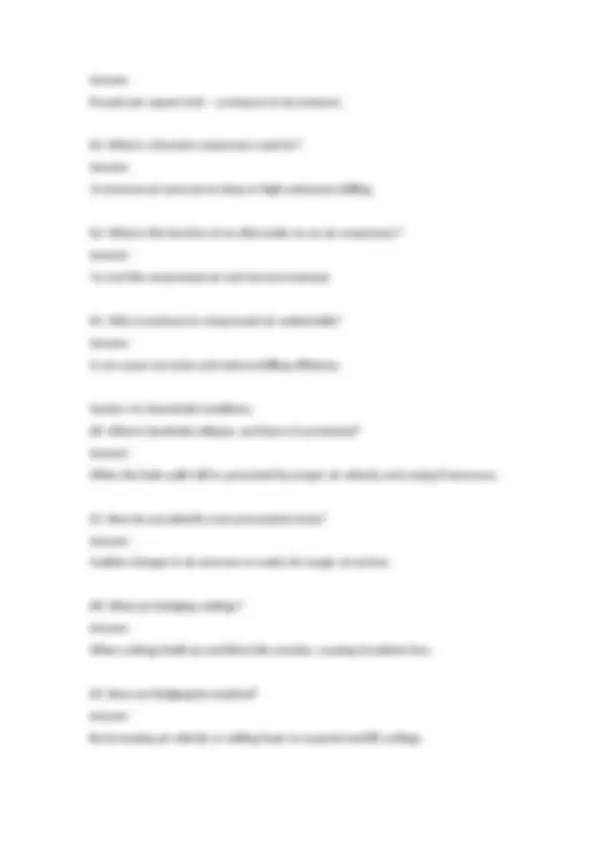
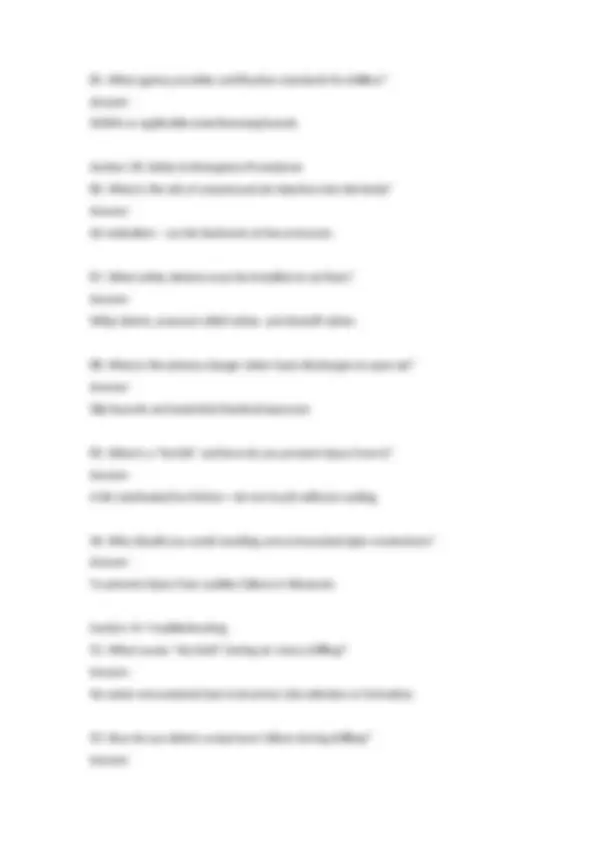
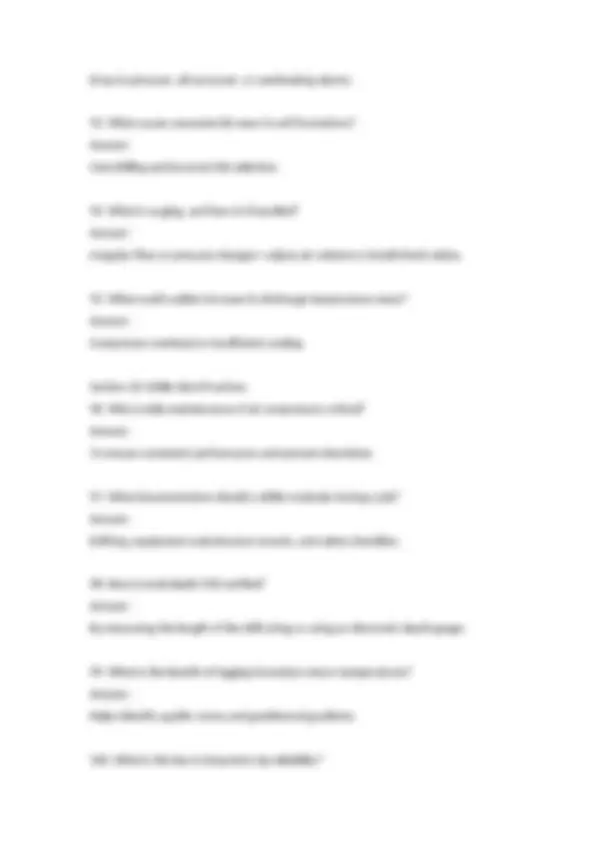
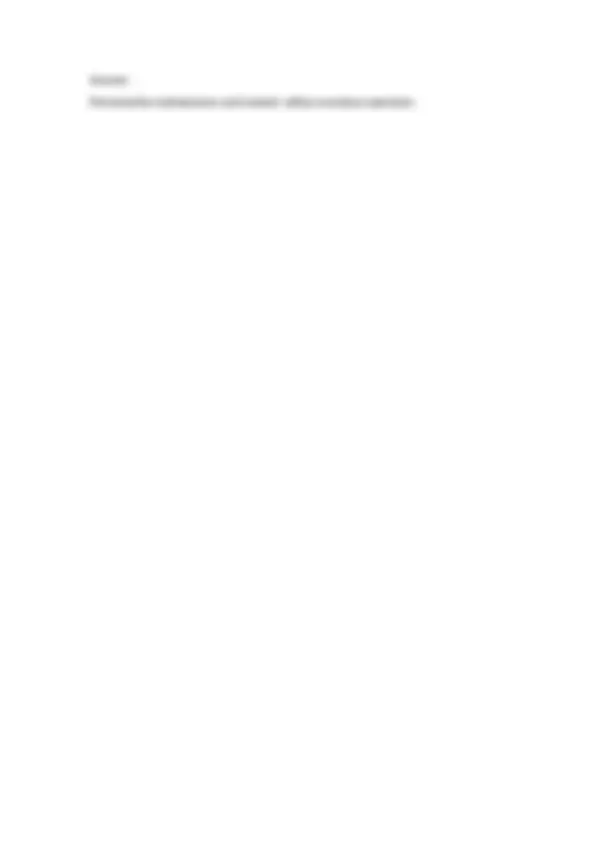
Study with the several resources on Docsity
Earn points by helping other students or get them with a premium plan
Prepare for your exams
Study with the several resources on Docsity
Earn points to download
Earn points by helping other students or get them with a premium plan
Community
Ask the community for help and clear up your study doubts
Discover the best universities in your country according to Docsity users
Free resources
Download our free guides on studying techniques, anxiety management strategies, and thesis advice from Docsity tutors
This study guide provides a comprehensive overview of air rotary drilling, covering principles, air systems, drill rig components, bits and drilling tools, formation evaluation, troubleshooting, safety, and regulations. It includes key concepts such as up-hole velocity, compressor functions, drill string design, and drilling performance optimization. The guide also addresses advanced knowledge, casing and well construction, and air drilling variants, making it a valuable resource for students and professionals in the field. It features 77 questions and answers.
Typology: Exams
1 / 15
This page cannot be seen from the preview
Don't miss anything!
Section 1: Drilling Principles
Faster drilling rates and cleaner boreholes in consolidated formations.
Polycrystalline Diamond Compact bits; used in hard formations for high-speed drilling.
Answer: Pounds per square inch – a measure of air pressure.
Drop in pressure, oil carryover, or overheating alarms.