
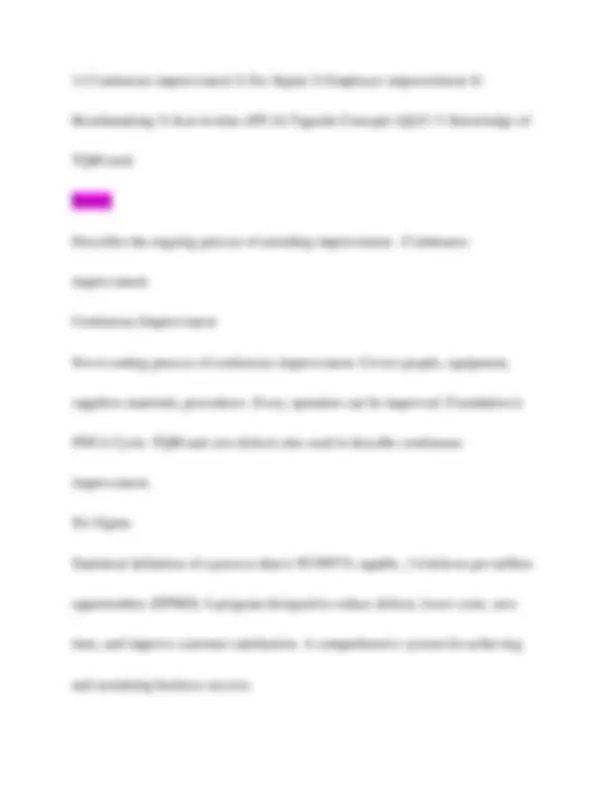
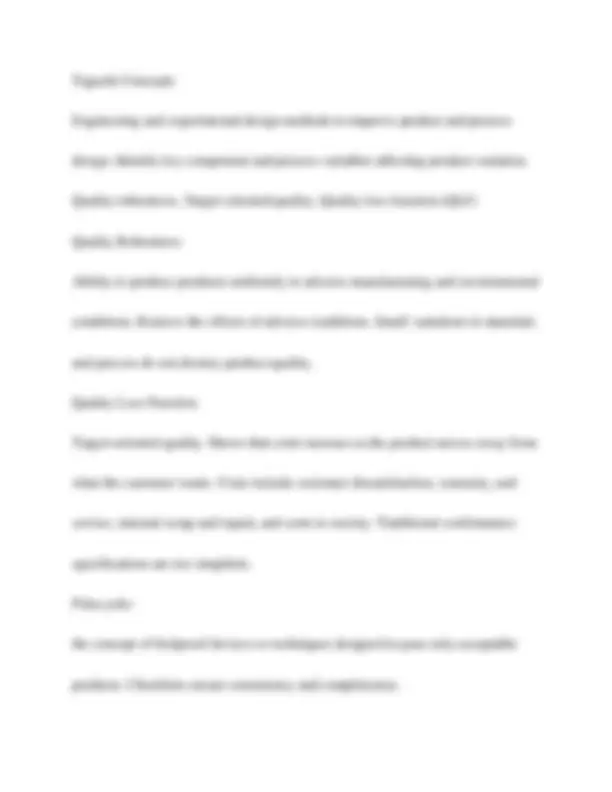
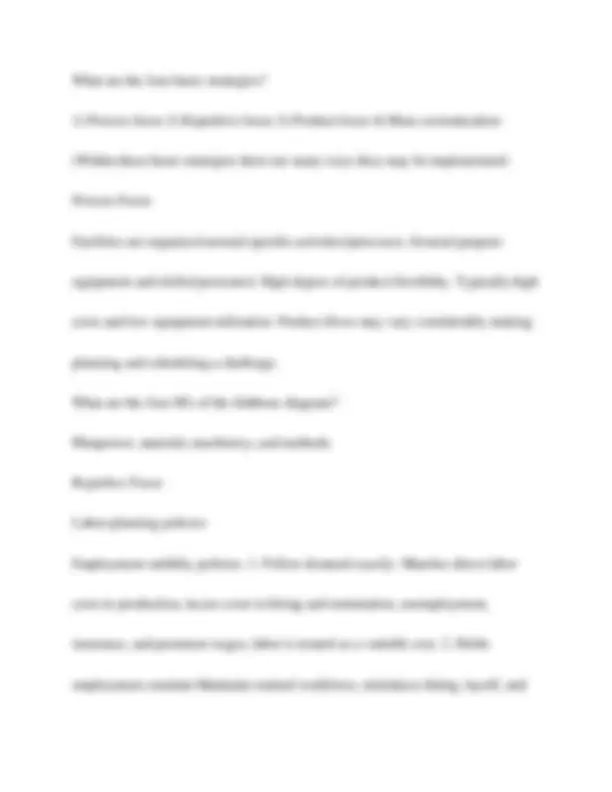
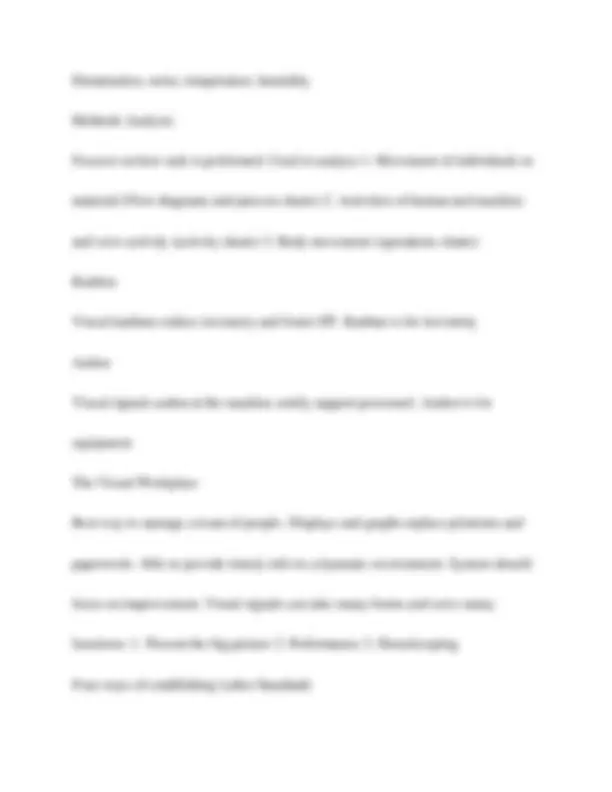
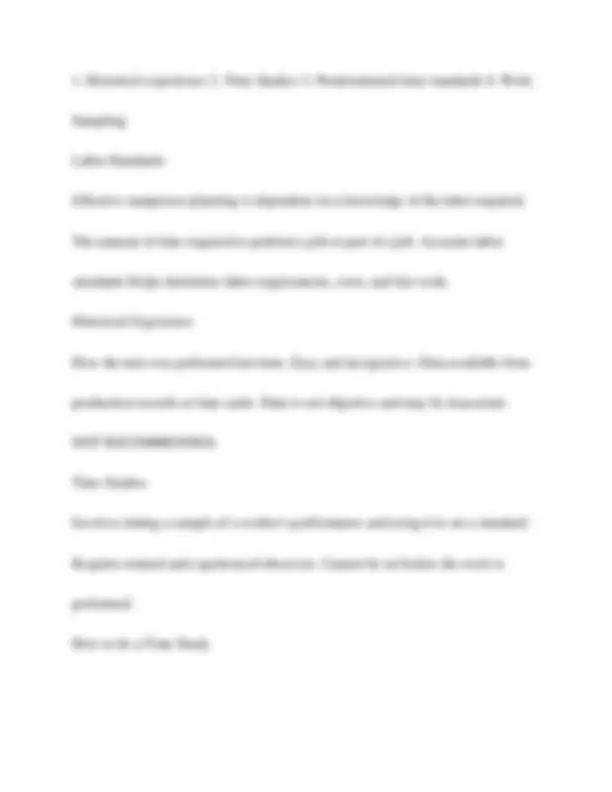
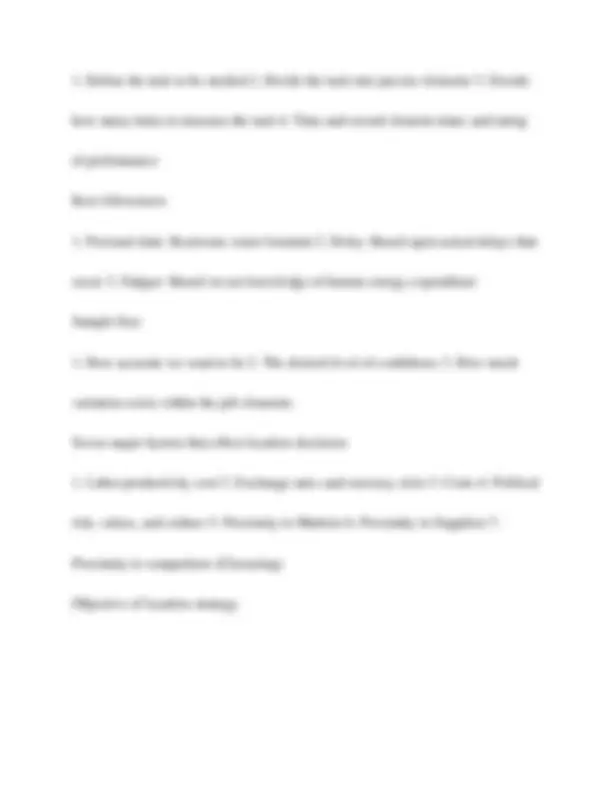
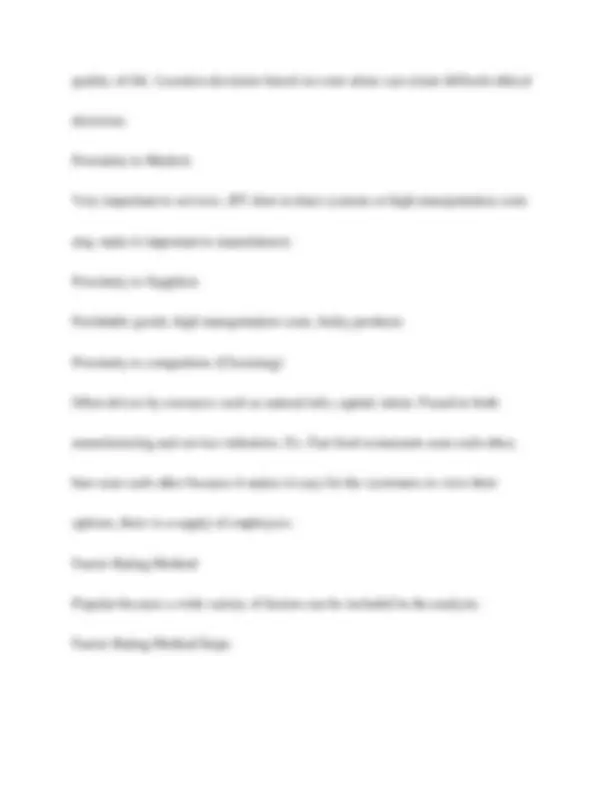
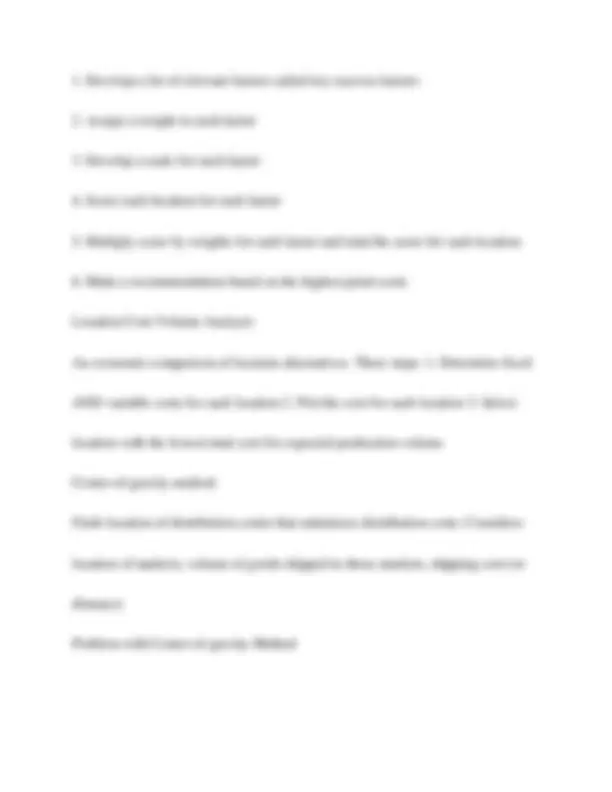
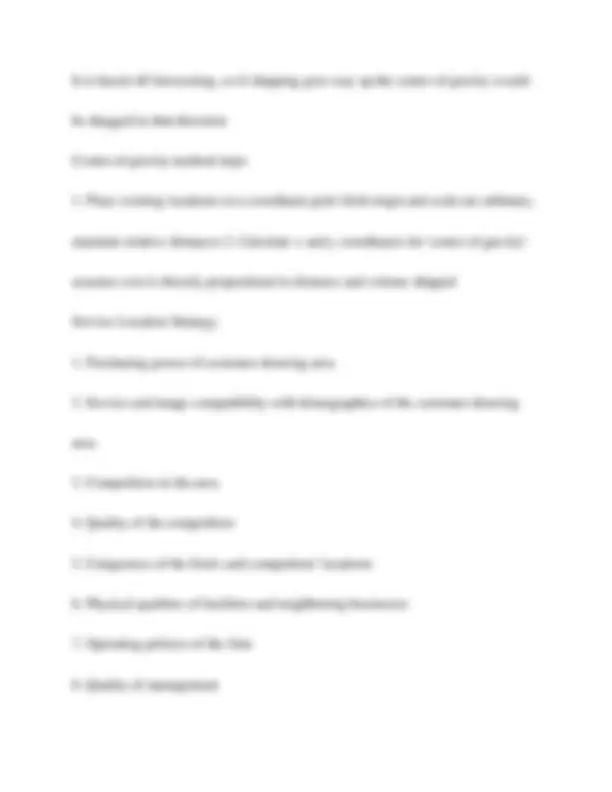
Study with the several resources on Docsity
Earn points by helping other students or get them with a premium plan
Prepare for your exams
Study with the several resources on Docsity
Earn points to download
Earn points by helping other students or get them with a premium plan
Community
Ask the community for help and clear up your study doubts
Discover the best universities in your country according to Docsity users
Free resources
Download our free guides on studying techniques, anxiety management strategies, and thesis advice from Docsity tutors
OM 300- Chilcutt Exam Two| Questions and 100% Correct Answers Managing quality supports ____________, ____________, and ____________ strategies differentiation, low cost, and response What is an operations manager's objective? To build a total quality management system that identifies and satisfies customer needs American Society for Quality The totality of features and characteristics of a product or service that bears on its ability to satisfy stated or implied needs User based view Better performance, more features Manufacturing-based view conformance to standards, making it right the first time Product based view Specific and measurable attributes of the product Prevention costs (Costs of Quality) Reducing the potential for defects (training, quality improvement programs) Appraisal costs (Costs of Quality) Evaluating products, parts, and services Internal failure costs (Costs of Quality) Producing defective parts or service before delivery External failure costs (Costs of Quality)
Typology: Exams
1 / 16
This page cannot be seen from the preview
Don't miss anything!
Managing quality supports ____________, ____________, and ____________ strategies differentiation, low cost, and response What is an operations manager's objective? To build a total quality management system that identifies and satisfies customer needs American Society for Quality The totality of features and characteristics of a product or service that bears on its ability to satisfy stated or implied needs User based view Better performance, more features Manufacturing-based view conformance to standards, making it right the first time Product based view
Specific and measurable attributes of the product Prevention costs (Costs of Quality) Reducing the potential for defects (training, quality improvement programs) Appraisal costs (Costs of Quality) Evaluating products, parts, and services Internal failure costs (Costs of Quality) Producing defective parts or service before delivery External failure costs (Costs of Quality) Defects discovered after delivery (recalls) Implications of Quality
Taguchi Concepts Engineering and experimental design methods to improve product and process design. Identify key component and process variables affecting product variation. Quality robustness, Target-oriented quality, Quality loss function (QLF) Quality Robustness Ability to produce products uniformly in adverse manufacturing and environmental conditions. Remove the effects of adverse conditions. Small variations in materials and process do not destroy product quality. Quality Loss Function Target-oriented quality. Shows that costs increase as the product moves away from what the customer wants. Costs include customer dissatisfaction, warranty, and service, internal scrap and repair, and costs to society. Traditional conformance specifications are too simplistic. Poka-yoke the concept of foolproof devices or techniques designed to pass only acceptable products. Checklists ensure consistency and completeness.
What are the four basic strategies?
Human resource strategy requires consideration of the psychological components of job design Human Resource Strategy The objective is to manage labor and design jobs so people are effectively and efficiently utilized. Ensures that people: 1. Are efficiently utilized within the constraints of other operations management decisions 2. Have a reasonable quality of work life in an atmosphere of mutual commitment and trust Core Job Characteristics
Illumination, noise, temperature, humidity Methods Analysis Focuses on how task is performed. Used to analyze 1. Movement of individuals or material (Flow diagrams and process charts) 2. Activities of human and machine and crew activity (activity charts) 3. Body movement (operations charts) Kanban Visual kanbans reduce inventory and foster JIT. Kanban is for inventory Andon Visual signals andon at the machine notify support personnel. Andon is for equipment. The Visual Workplace Best way to manage a team of people. Displays and graphs replace printouts and paperwork. Able to provide timely info in a dynamic environment. System should focus on improvement. Visual signals can take many forms and serve many functions: 1. Present the big picture 2. Performance 3. Housekeeping Four ways of establishing Labor Standards
To maximize the benefit of location to the firm. Options include: 1. Expanding existing facilities 2. Maintain existing and relocating 3. Closing existing and relocating Drivers of globalization Market economics, communication, rapid/ reliable transportation, ease of capital flow, differing labor costs Location Country Decision Key Success Factors ( KSF's)
quality of life. Location decisions based on costs alone can create difficult ethical decisions. Proximity to Markets Very important to services. JIT (Just in time) systems or high transportation costs may make it important to manufaturers Proximity to Suppliers Perishable goods, high transportation costs, bulky products Proximity to competitors (Clustering) Often driven by resources such as natural info, capital, talent. Found in both manufacturing and service industries. Ex. Fast food restaurants near each other, bars near each other because it makes it easy for the customers to view their options, there is a supply of employees. Factor-Rating Method Popular because a wide variety of factors can be included in the analysis. Factor-Rating Method Steps
Service Sector Location Analysis REVENUE FOCUSED Process Strategy objective To create a process to produce offerings that meet customer requirements within cost and other managerial constraints Process focus Facilities are organized around specific activities or processes. General purpose equipment and skilled personnel. High degree of product flexibility. Typically high costs and low equipment utilization. Product flows may vary considerably making planning and scheduling a challenge.