
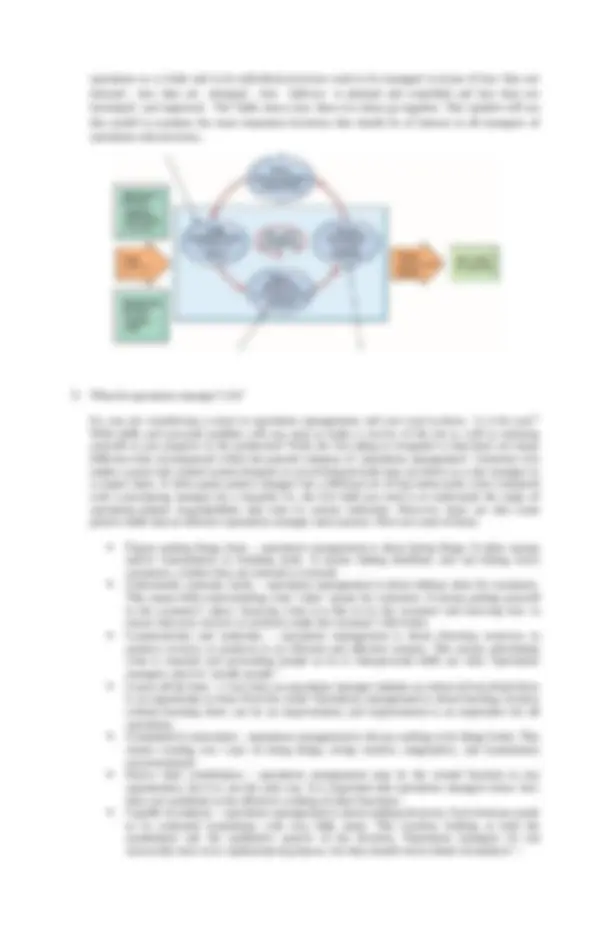
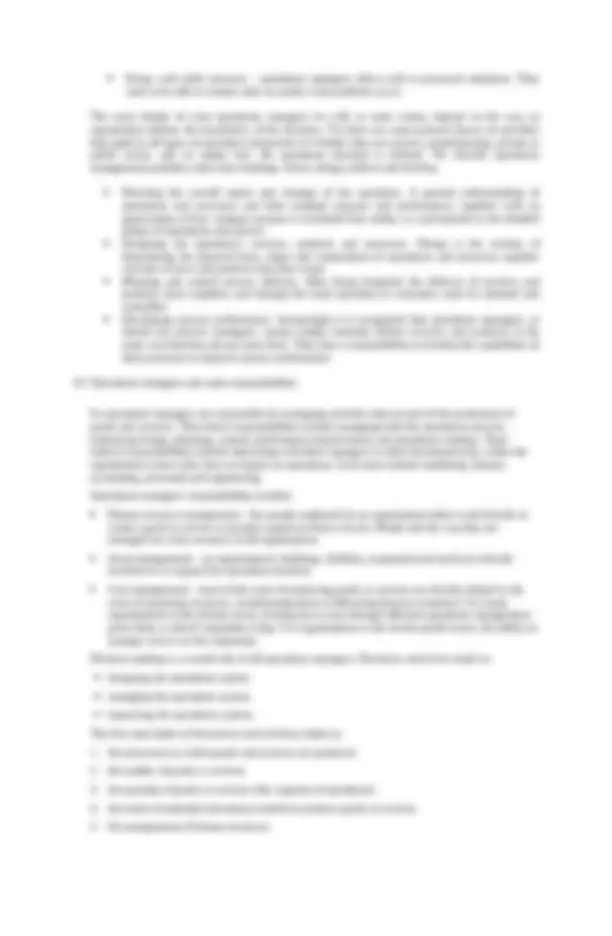
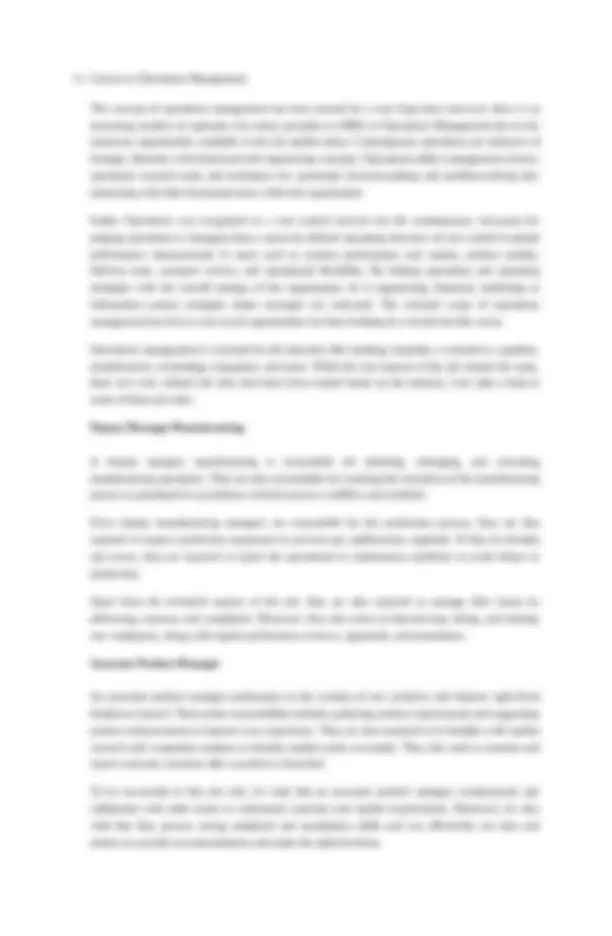
Study with the several resources on Docsity
Earn points by helping other students or get them with a premium plan
Prepare for your exams
Study with the several resources on Docsity
Earn points to download
Earn points by helping other students or get them with a premium plan
Community
Ask the community for help and clear up your study doubts
Discover the best universities in your country according to Docsity users
Free resources
Download our free guides on studying techniques, anxiety management strategies, and thesis advice from Docsity tutors
about operation management subject and managerial economics
Typology: Assignments
1 / 7
This page cannot be seen from the preview
Don't miss anything!
operations, do so to change the possession of the materials. Finally, some operations store materials, such as warehouses. ● Information – operations which process information could do so to transform their informational properties (that is the purpose or form of the information); accountants do this. Some change the possession of the information, for example market research companies sell information. Some store the information, for example archives and libraries. Finally, some operations, such as telecommunication companies, change the location of the information. ● Customers – operations which process customers might change their physical properties in a similar way to materials processors: for example, hairdressers or cosmetic surgeons. Some store (or more politely accommodate) customers: hotels, for example. Airlines, mass rapid transport systems and bus companies transform the location of their customers, while hospitals transform their physiological state. Some are concerned with transforming their psychological state, for example most entertainment services such as music, theatre, television, radio and theme parks. But customers are not always simple ‘passive’ items to be processed. They can also play a more active part in many operations and processes. For example, they create the atmosphere in a restaurant; they provide the stimulating environment in learning groups in education; they provide information at check-in desks, and so on. When customers play this role, it is usually referred to as co-production (or co-creation for new services) because the customer plays a vital part in the provision of the product/service offering. The following table gives examples of operations with their dominant transformed resources.
Keeps cool under pressure – operations managers often work in pressured situations. They need to be able to remain calm no matter what problems occur. The exact details of what operations managers do will, to some extent, depend on the way an organization defines the boundaries of the function. Yet there are some general classes of activities that apply to all types of operation irrespective of whether they are service, manufacturing, private or public sector, and no matter how the operations function is defined. We classify operations management activities under four headings: direct, design, deliver and develop. Directing the overall nature and strategy of the operation. A general understanding of operations and processes and their strategic purpose and performance, together with an appreciation of how strategic purpose is translated into reality, is a prerequisite to the detailed design of operations and process Designing the operation’s services, products and processes. Design is the activity of determining the physical form, shape and composition of operations and processes together with the services and products that they create Planning and control process delivery. After being designed, the delivery of services and products from suppliers and through the total operation to customers must be planned and controlled Developing process performance. Increasingly it is recognized that operations managers, or indeed any process managers, cannot simply routinely deliver services and products in the same way that they always have done. They have a responsibility to develop the capabilities of their processes to improve process performance
Supplier Risk Manager is expected to conduct a supplier risk assessment for Operational risk, Information security risk and reputational risk for a supplier before on-boarding. Maintain supplier compliance in terms of local regulations and company policies/processes. Partner with stakeholders to identify opportunities within the Organization for new initiatives, support the sourcing team to execute special & simplification projects based on stakeholder requirements to meet Quality standards & timelines. Gather information on the market trends and current market price points, create information repository & share the latest insights with the management, use the market benchmarks of other large organizations in order to improve current price points Functional Consultant A functional consultant may be assigned responsibility for a specific functional vertical or client- specific tasks. Given the complexity, it requires the delivery of specific capability in Technology Consulting. A functional consultant needs to understand Business Requirements and Needs and accordingly support application design, develop functional/process documents, Build, test and deliver solutions. A functional consultant is responsible for Functional specification creation, functional Unit Testing, Test Data Creation & Test scripts creation and execution. A functional consultant has to adhere to defined processes and tools while performing day-to-day operations Analyst Operations Advisory Services Analyst Operations Advisory Services is expected to support in building and executing innovative solutions for delivery excellence at an optimized delivery cost. Business operations analysts are in charge of conducting extensive, accurate analyses of their organization's existing business operations. Their main duties include gathering data and developing solutions to meet business needs. They also analyze cross-departmental business processes for efficiency. There are various specificity roles that fall under the category of operations management, and all of them are integral to an organization's success. While there is pressure to get the job done right, there is also an immense opportunity for career growth. Operations management professionals can grow to hold the position of Chief of Operations with enough experience. There are various other professions available as well, like, Logistics Manager, Warehouse Manager, Asst. Management -Quality, Vendor Development, Category Manager, etc.