
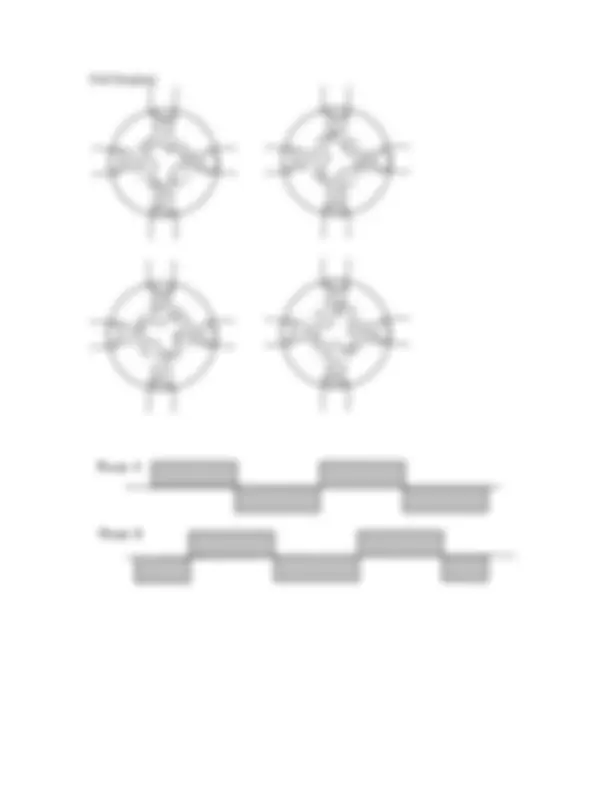
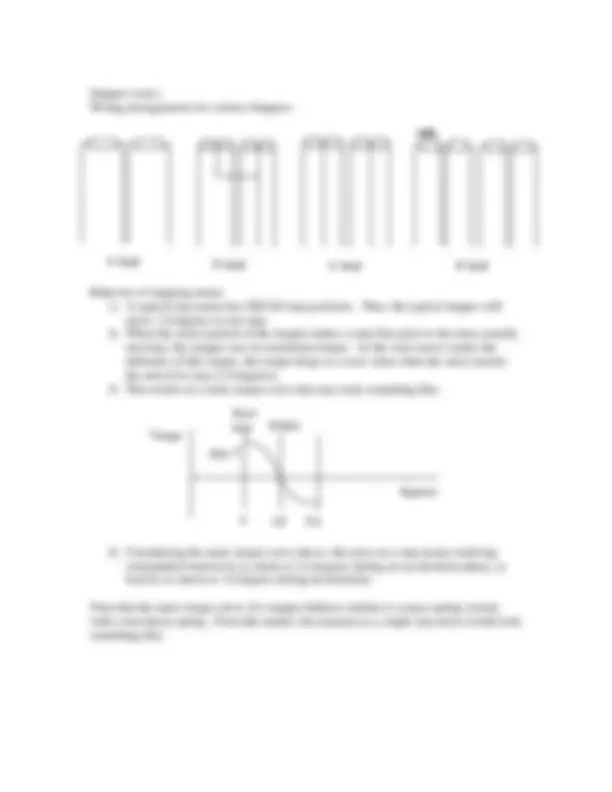
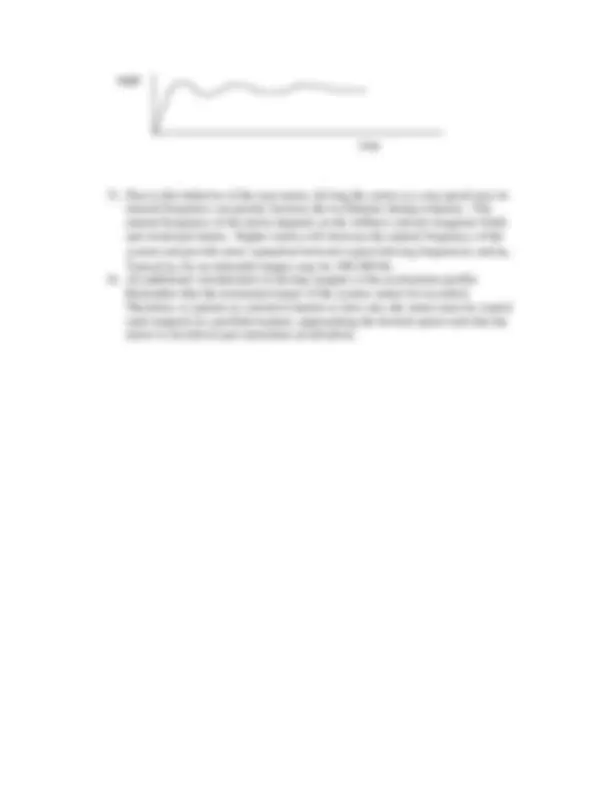
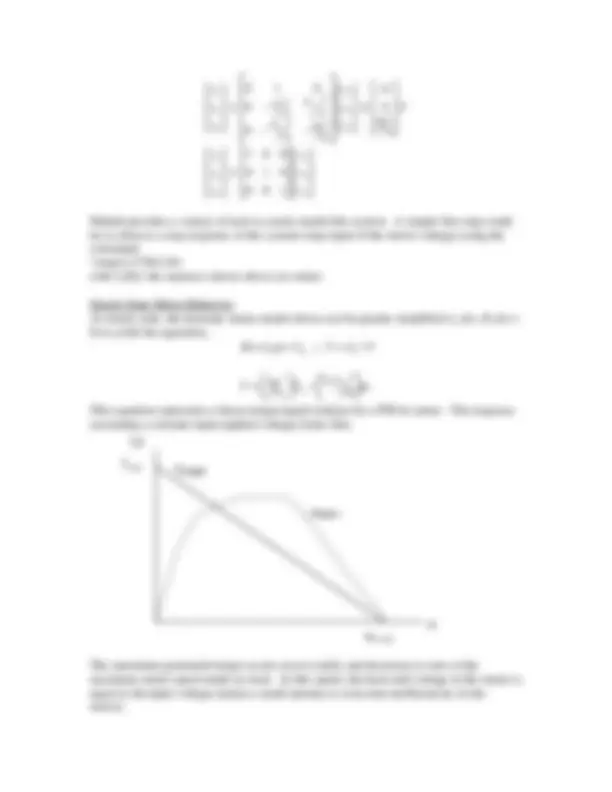
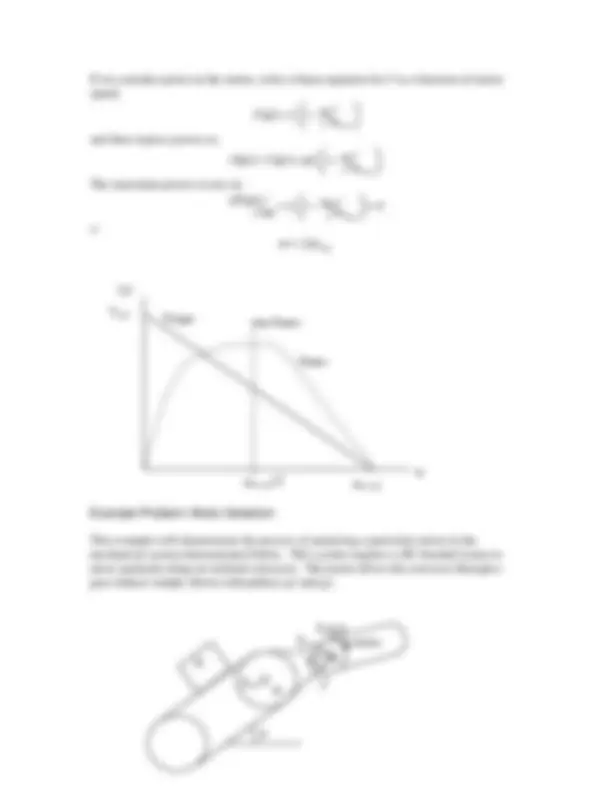
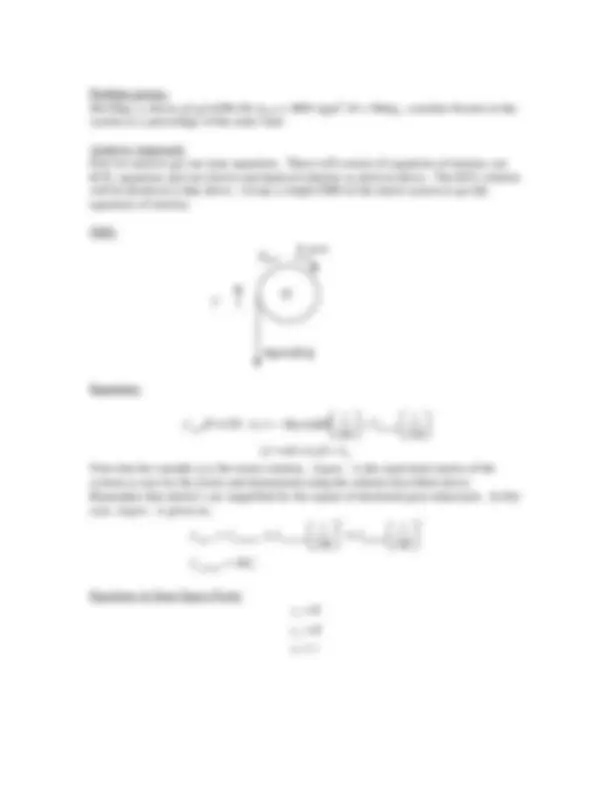
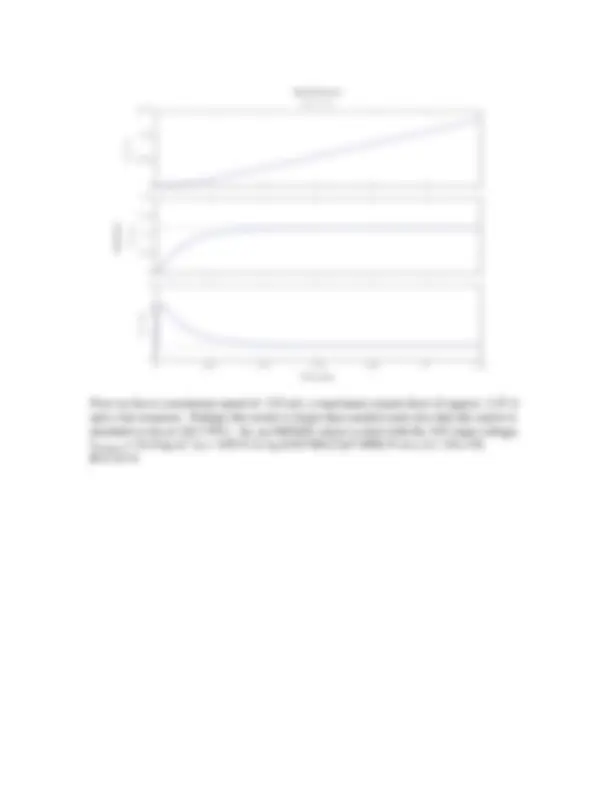
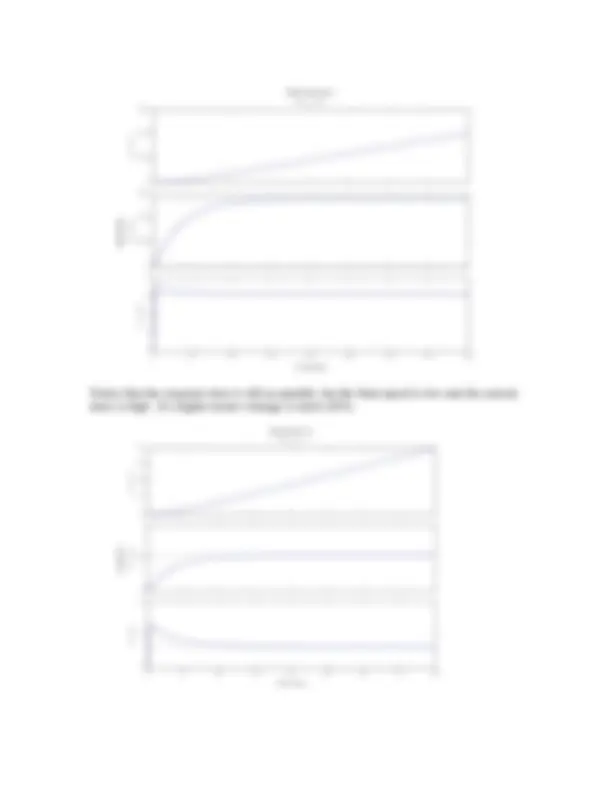
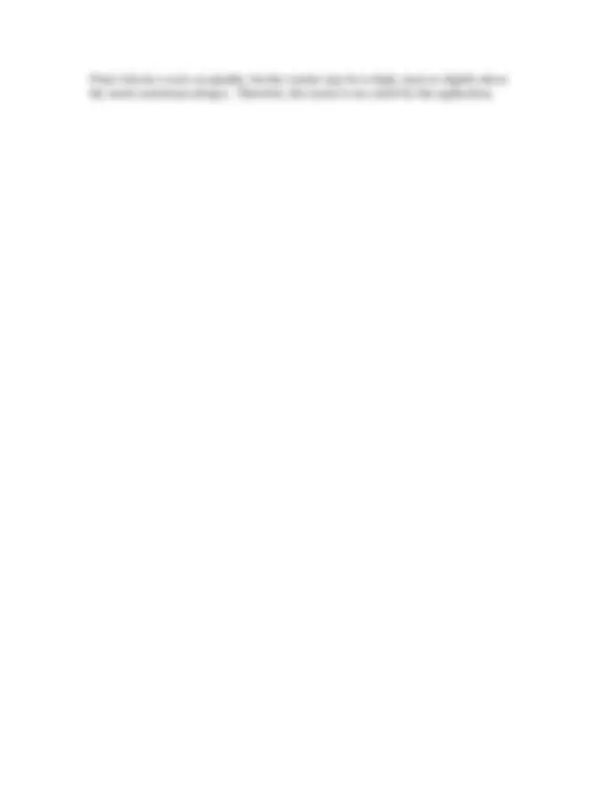
Study with the several resources on Docsity
Earn points by helping other students or get them with a premium plan
Prepare for your exams
Study with the several resources on Docsity
Earn points to download
Earn points by helping other students or get them with a premium plan
Community
Ask the community for help and clear up your study doubts
Discover the best universities in your country according to Docsity users
Free resources
Download our free guides on studying techniques, anxiety management strategies, and thesis advice from Docsity tutors
An overview of various types of motors, including brushed dc motors, stepper motors, brushless dc motors, and brushless ac motors. It discusses their characteristics, such as torque, reliability, and suitability for different environments. The document also includes equations for motor dynamics and control, as well as an example problem for motor selection.
Typology: Exams
1 / 15
This page cannot be seen from the preview
Don't miss anything!
Overview of motors and motion control
High-level controller
Low-level controller
Driver
Power Supply
Motor
Brushed, PM DC Motors
Stepper Motors Brushless DC Motors
Brushless AC Motors Cheap, rugged, high-reliability
Cheap, rugged, high-reliability
No brushes, suitable for any environment
No brushes, suitable for any environment Low Torque ripple No brushes, suitable for any environment Do not require feedback At low speeds, provide up to 5x torque of brushed motor, 2x torque of brushless motor Suffers from resonance and long settling times Consume current regardless of load or motion, run hot Losses at speed are high Undetected position loss as a result of open loop operation
Stepper Motors
Half Stepping
N
S N
N
S S
S N
N
S S
Phase A
Phase B
Stepper (cont.) Wiring arrangements for various Steppers
∼6Ω
4-lead (^) 5-lead (^) 6-lead 8-lead
Behavior of stepping-motor
(^0) 1.8 3.
degrees
Torque Max T.
Start step Stable
Note that the static torque curve of a stepper behaves similar to a mass-spring system with a non-linear spring. From this model, the response to a single step move would look something like;
angle
time
a first order ODE in current, i, with L , R the motor inductance and resistance, ke the electric constant, Vemf the back emf and ω the rotational speed of the motor (rad/s).
Motor Mechanics:
The rotational inertia, J as seen by the motor is, 2
2
1 ⎟
g
g motor load d
d J J J ,
accounting for motor inertia (rotor) as well as gear train and load inertia. Motor Dynamics:
torque and Tfriction the friction torque describes the motor dynamics.
Finally, the electro-mechanical relation is approximately given as an equation that describes motor torque as a linear function of current in the motor, T = kt i
where kt the motor torque constant.
These equations can be combined to result in two equations, a 1st^ and 2nd^ order ODE with two unknowns, i and q ;
These will be cast in state-space form to result in a system of three 1st^ order DE’s’
x i
x
x
3
2
1
x V L x R L x k
x CJx k J x T
x x
b in
t friction
3 2 3
2 2 3
1 2
or;
Jload (^) g 2
Jmotor g 1
motor
T
θ, ω, α
3
2
1
3
2
1
3
2
1
3
2
1
x
x
x
y
y
y
x R
x
x
k
k J
x
x
x
b
t &
Matlab provides a variety of tools to easily model this system. A simple first step could be to observe a step response of this system (step input of the motor voltage) using the command;
step(A,V*B,C,D) with A,B,C the matrices shown above (in order).
Steady-State Motor Behavior:
V k k k T R in e t t
,
This equation represents a linear torque/speed relation for a PM dc motor. The response (assuming a constant input applied voltage) looks like;
Torque
Power
T,P Tstall
ωno load
ω
The maximum generated torque occurs at rest (stall), and decreases to zero at the maximum motor speed under no load. At this speed, the back-emf voltage in the motor is equal to the input voltage (minus a small amount to overcome inefficiencies in the motor).
Problem givens; M=10kg; rw=8cm; g2:g1=GR=50; Jload = .0001 kgm^2 ; θ = 30deg., consider friction in the system as a percentage of the static load.
Analysis Approach; First we need to get our state equations. These will consist of equations of motion, our KVL equations and our electro-mechanical relations as derived above. The KVL relation will be identical to that above. Create a simple FBD of the motor system to get the equations of motion;
FBD:
Jequiv
Equations:
J (^) equiv C kti Mg friction
Note that the variable q is the motor rotation. Jequiv. is the equivalent inertia of the system as seen by the motor and determined using the relation described above. Remember that inertia’s are magnified by the square of intermedi gear reductions. In this case, Jequiv. is given as;
2
2 2 1 1
payload w
equiv armature conveyor payload
J Mr
Equations in State-Space Form:
x i
x
x
3
2
1
T
θ, ω, α
Mgsin(θ)/g
3
2
1
3
2
1
3
2
1
3
2
1
sin
x
x
x
GR
r
r
y
y
y
Mg
x
x
x
k
k J
x
x
x
w
w
friction
b
Note that in describing that observers or outputs, y a conversion is made to output displacement and velocity in meters and m/s respectively, y 3 still represents current.
Solution approach: Implement using the step function in Matlab. In this case, the system will be described in state space form with the matrices A, B, C (D=[]) as above.
Example: Consider the SM233A motor from Parker automation (page 188 in ’99 computmotor catalog). The specifications on this motor are as follows; Jarmature = 1.3e-4 kg m^2 ; kt = .415 N.A; kb=50.6860/(2pi*1000) N m s; L= 4.8e-3 H, R = 9.65O, V=
Matlab code: M=10; %Payload mass g=9.81; %gravity Jconv=.0001; %Conveyor inertia rw=.08; %Wheel radius dg1=1;dg2=25;GR=dg2/dg1; J_motor=1.3e-4; %Motor inertia J=J_motor+Jconv(1/GR)^2+Mrw^2(1/GR)^2; %Total inertia at motor C=1.0791e-5; %Viscous damping theta=30pi/180; kt=.415; % torque constant kb=50.6860/(2pi1000); %Back emf constant L=4.81e-3; %Inductance R=9.65; %Resistance V=12; %Input voltage Tf=.5; %frictional torque as a percent of dead load A=[0,1, 0,-C/J,kt/J 0,-kb/L,-R/L]; B=[0;(-Mgrwsin(theta)/GR)(1+Tf)/J;V/L]; C=[rw/GR,0,0;0,rw/GR,0;0,0,1]; D=[0;0;0]; step(A,B,C,D)
Step R es pons e
Tim e (s ec)
Am plitude
0
From : U (1)
To: Y(1)
0
To: Y(2)
0 0.02 0.04 0.06 0.08 0.1 0. 0
1
2
3
To: Y(3)
Now we have a maximum speed of .125 m/s, a maximum current draw of approx. 2.25 A and a fast response. Perhaps this motor is larger than needed (note also that this motor is intended to run at 120-170V). So, an SM160A motor is tried with the 24V input voltage; Jarmature = 5e-6 kg m^2 ; kt = .038 N.A; kb=4.0260/(2pi*1000) N m s; L= .53e-3 H, R=3.43 O
Step R es pons e
Tim e (s ec)
Am plitude
0
From : U (1)
To: Y(1)
0
To: Y(2)
(^00) 0.1 0.2 0.3 0.4 0.5 0.6 0.7 0.
1
2
3
4
To: Y(3)
Notice that the response time is still acceptable, but the final speed is low and the current draw is high. If a higher motor volatage is tried (24V):
Step R es pons e
Tim e (s ec)
Am plitude
0
From : U (1)
To: Y(1)
0
1
To: Y(2)
(^00) 0.1 0.2 0.3 0.4 0.5 0.6 0.7 0.
5
10
To: Y(3)