
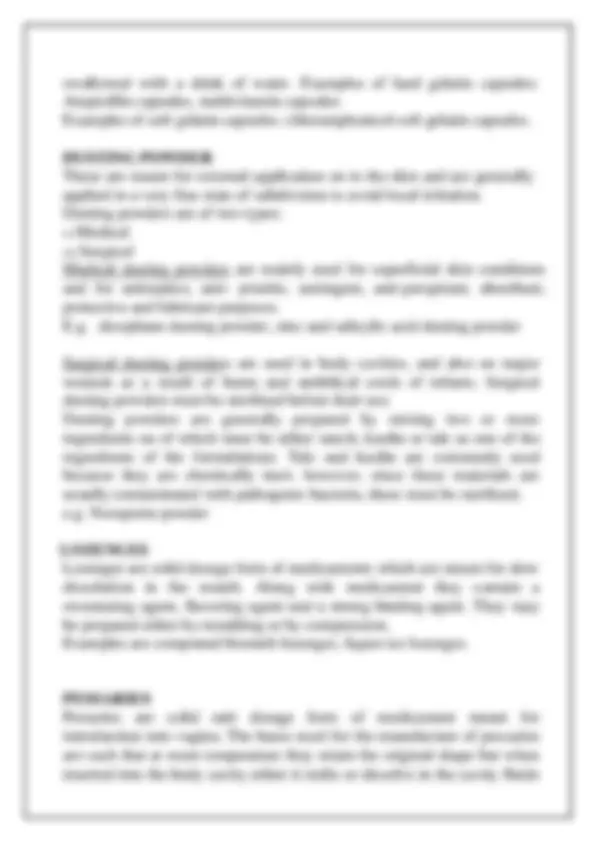
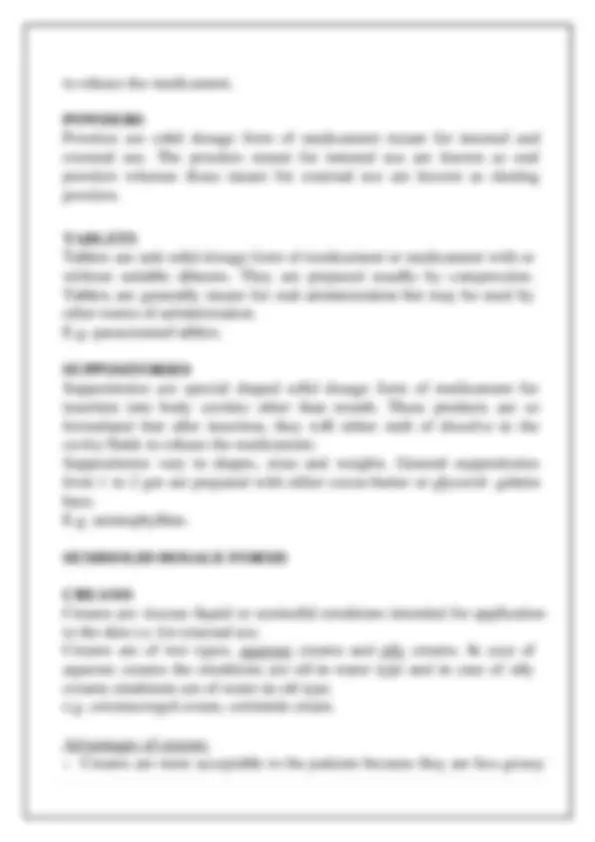
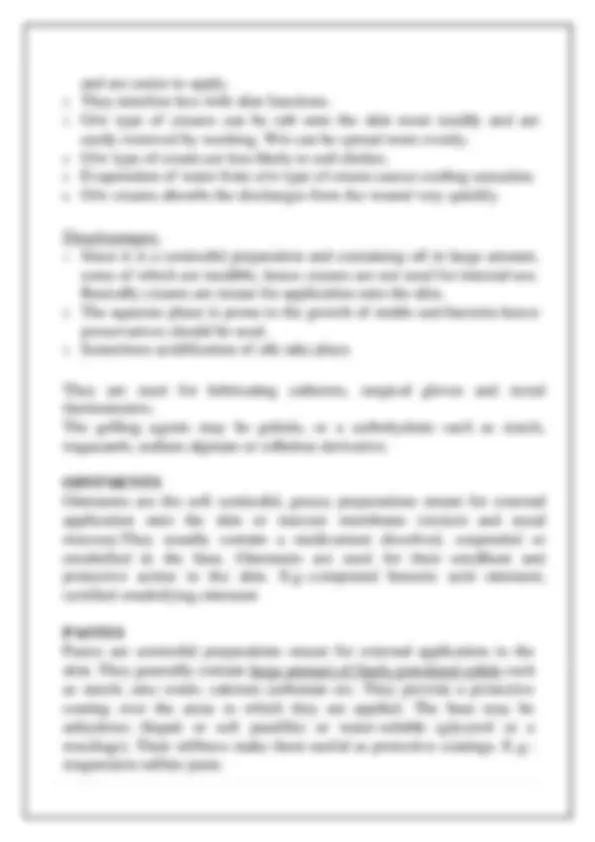
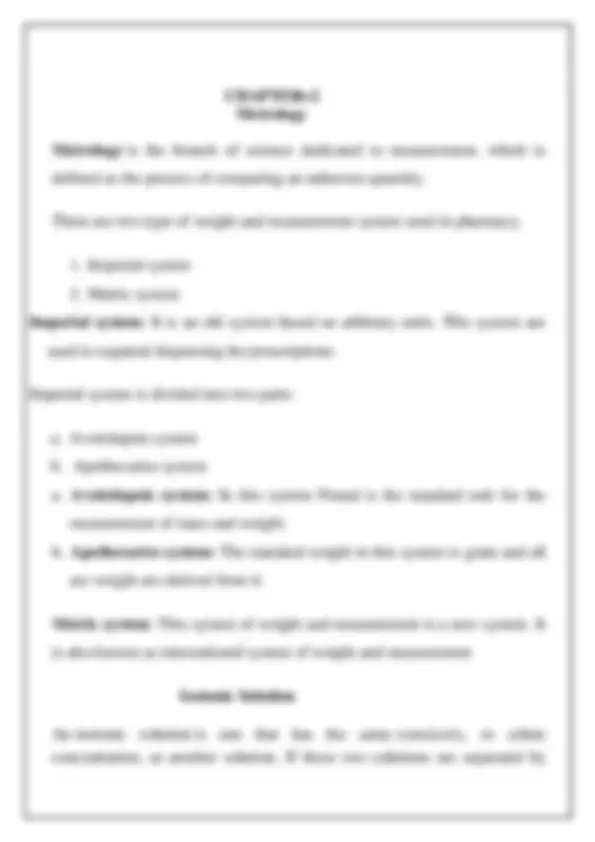
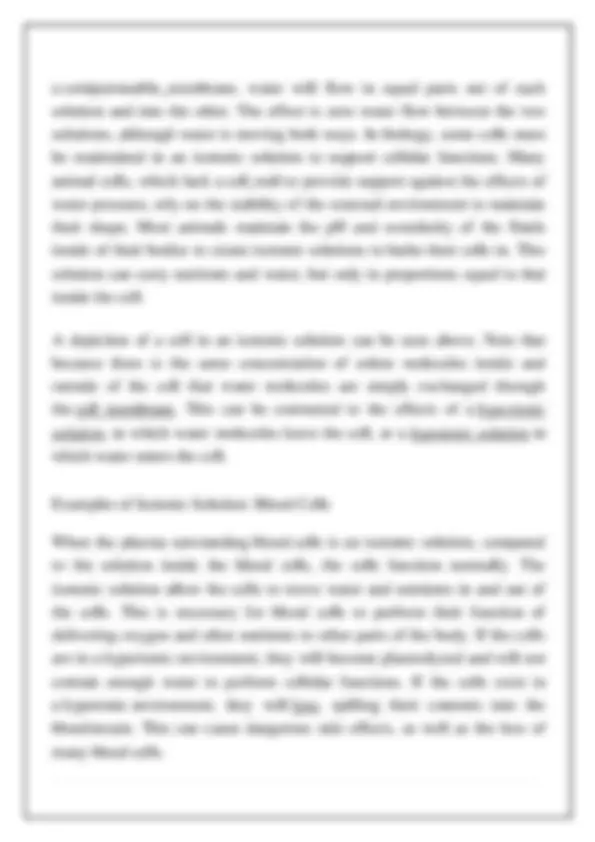

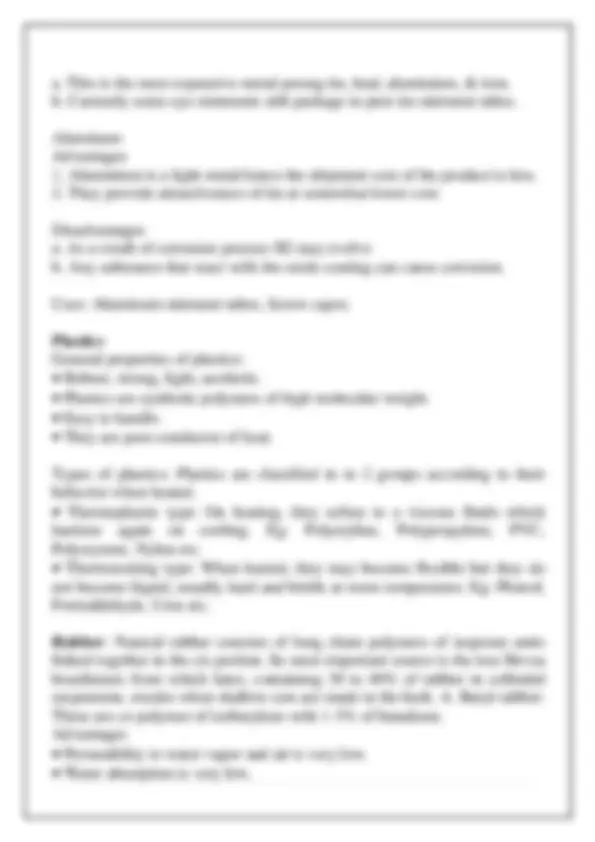
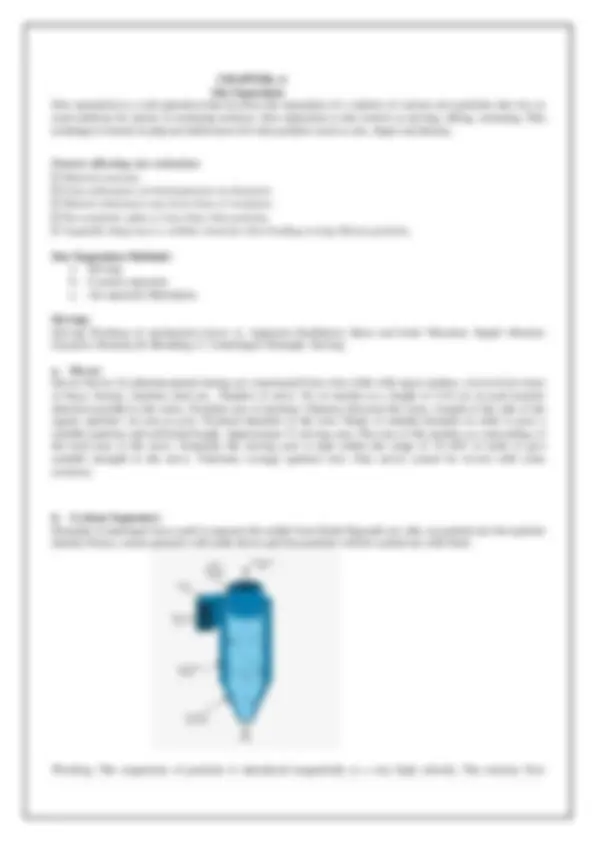
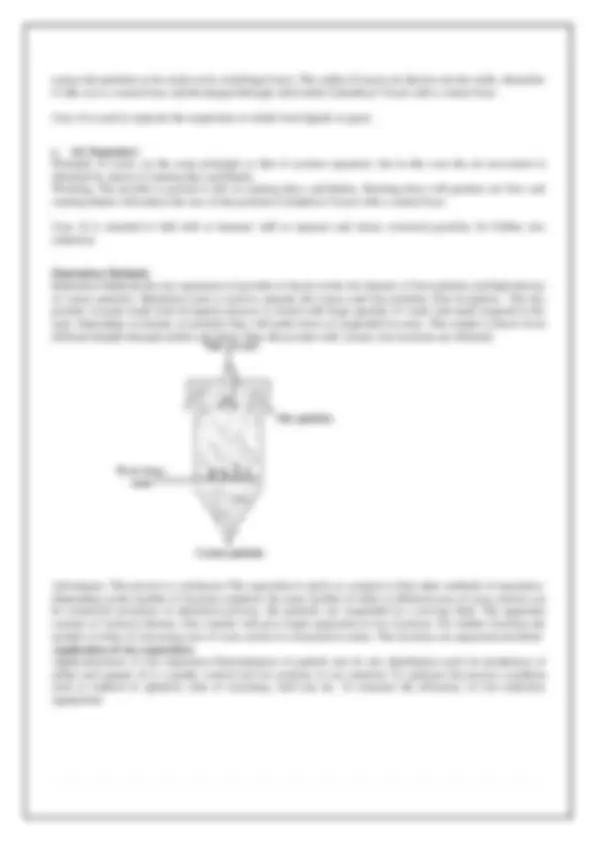
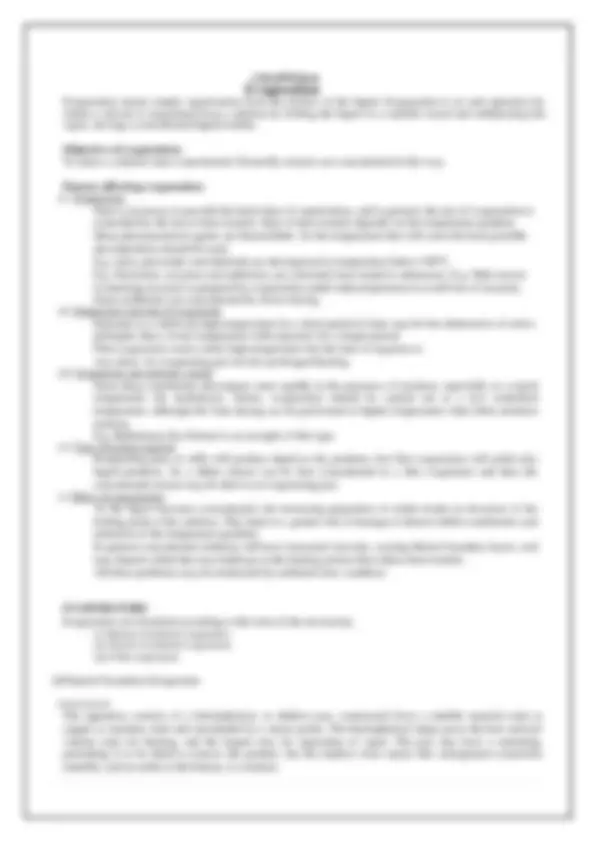
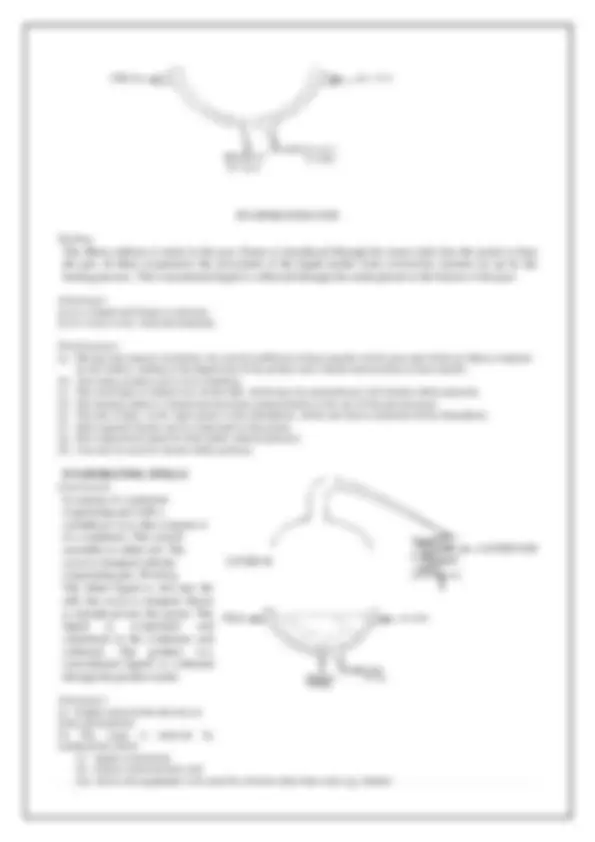
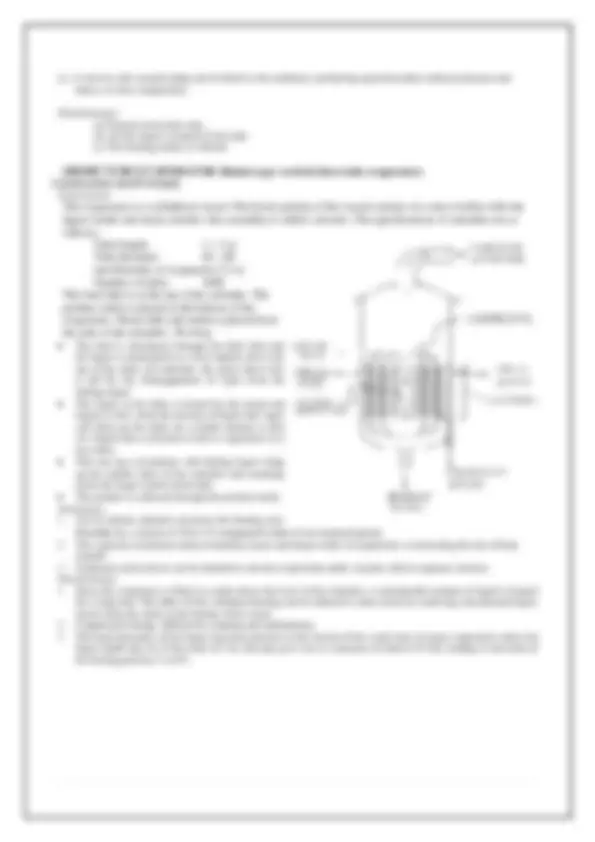
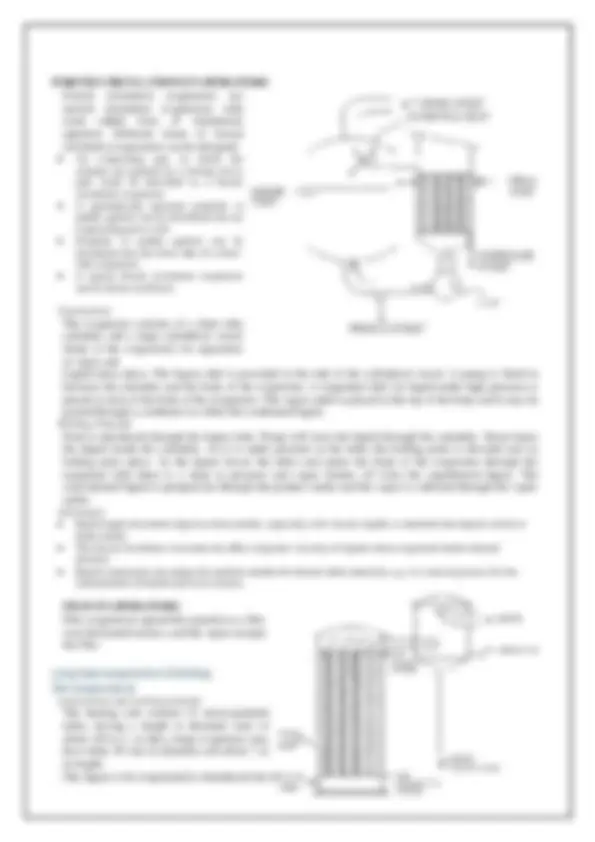
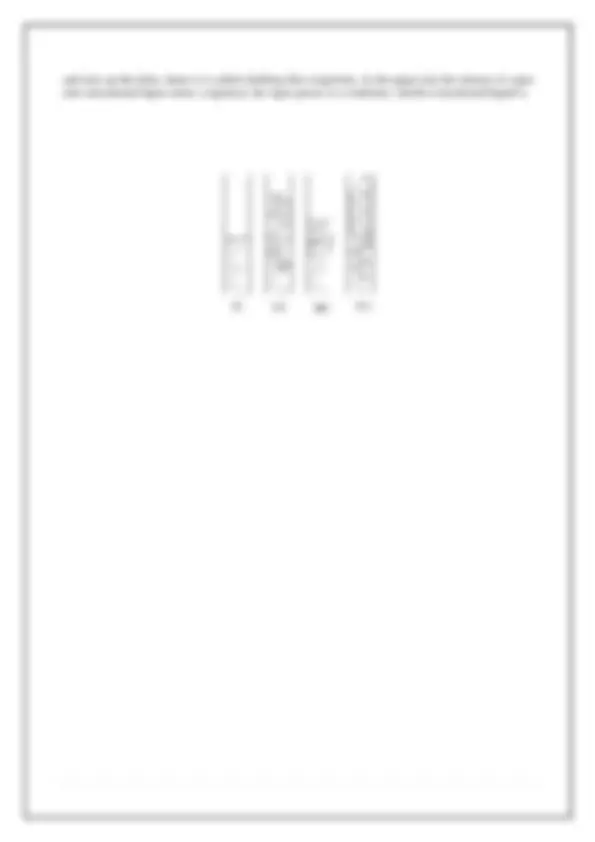

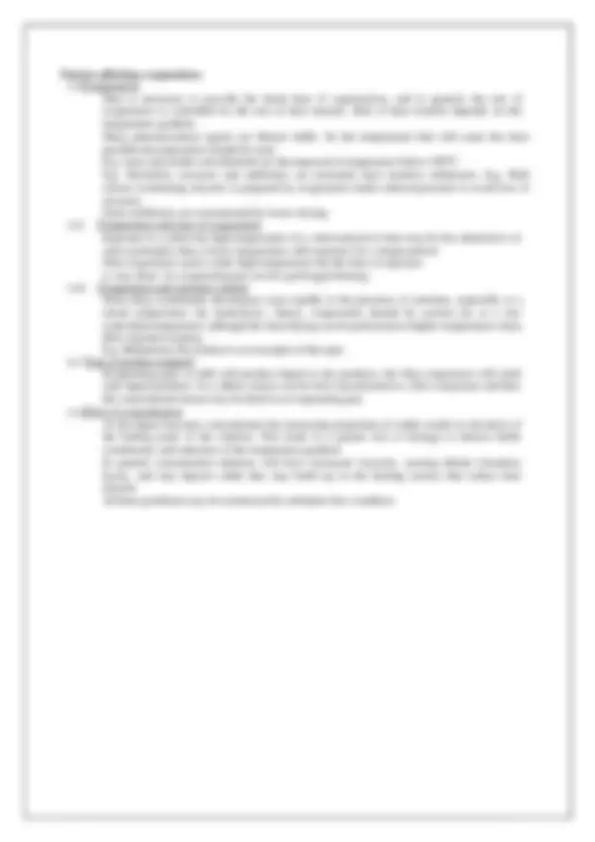
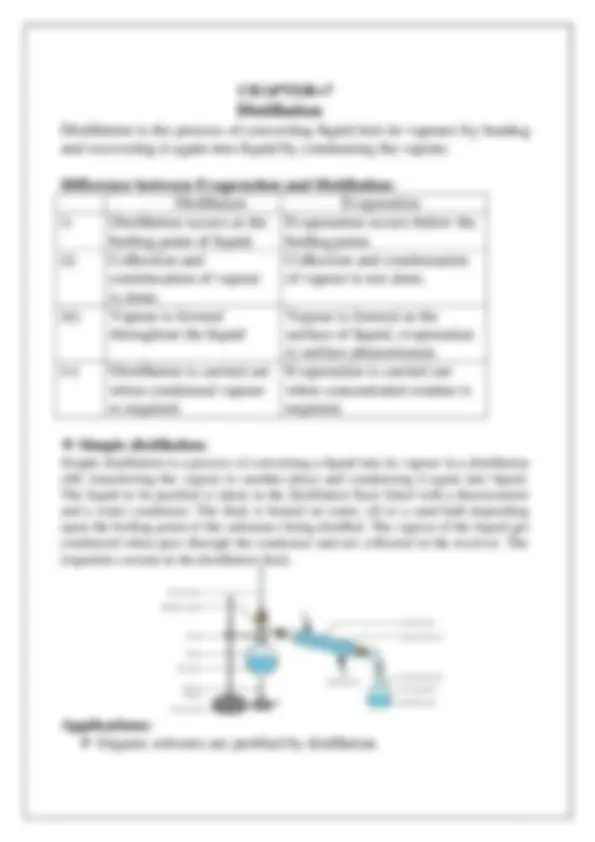
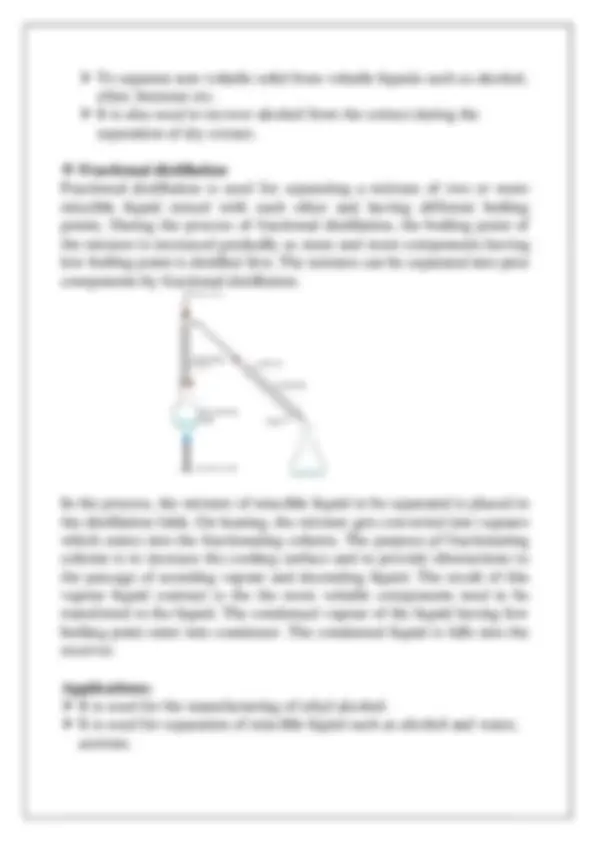
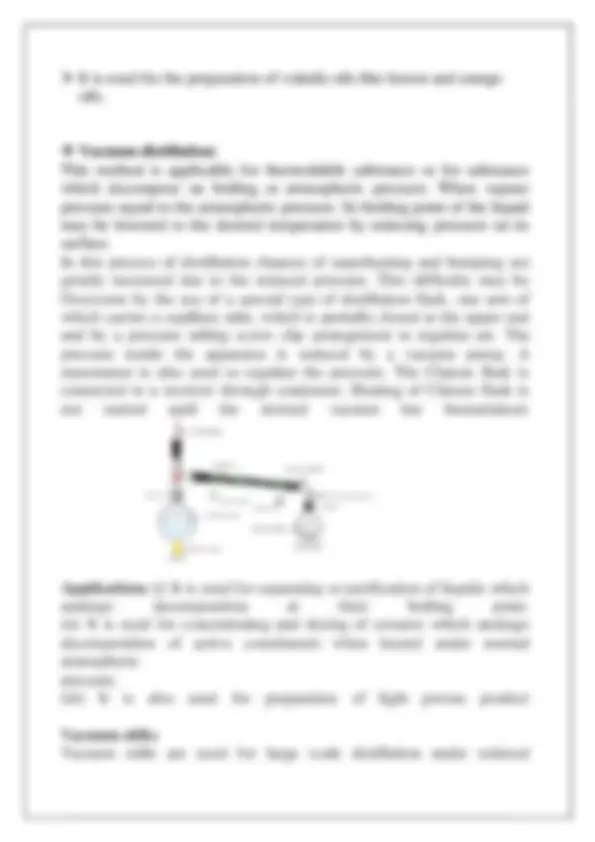
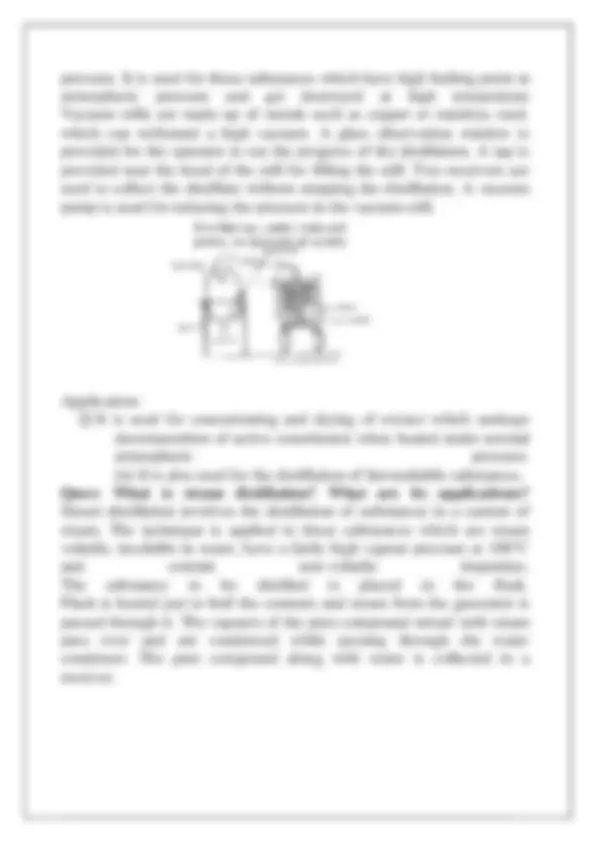
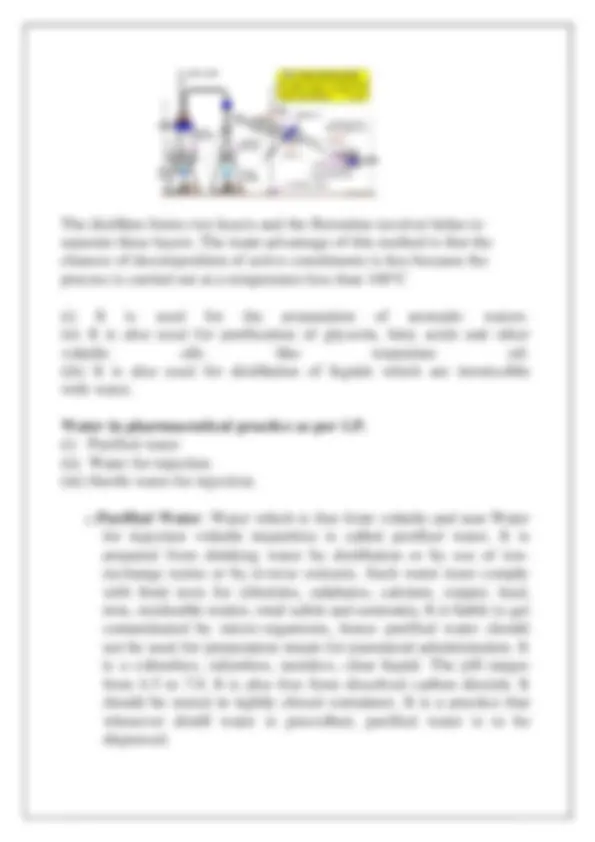
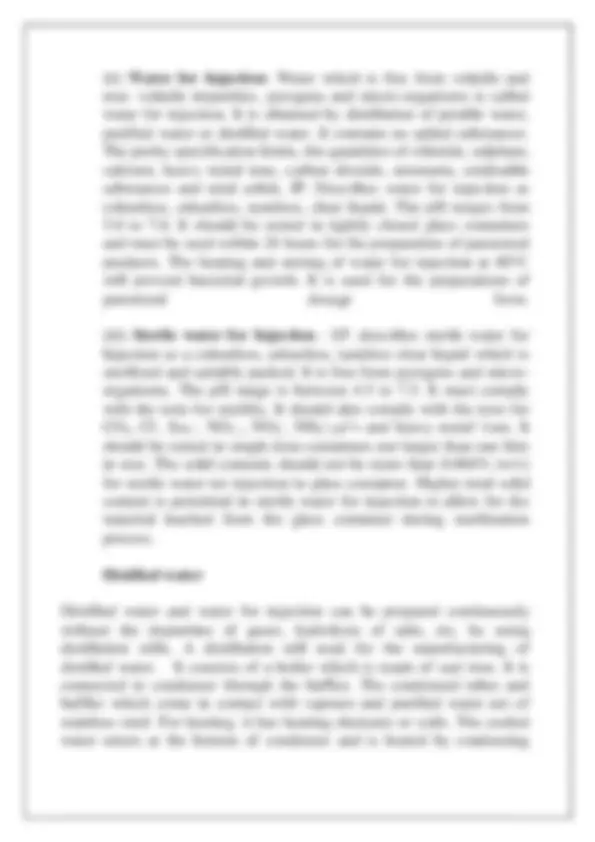
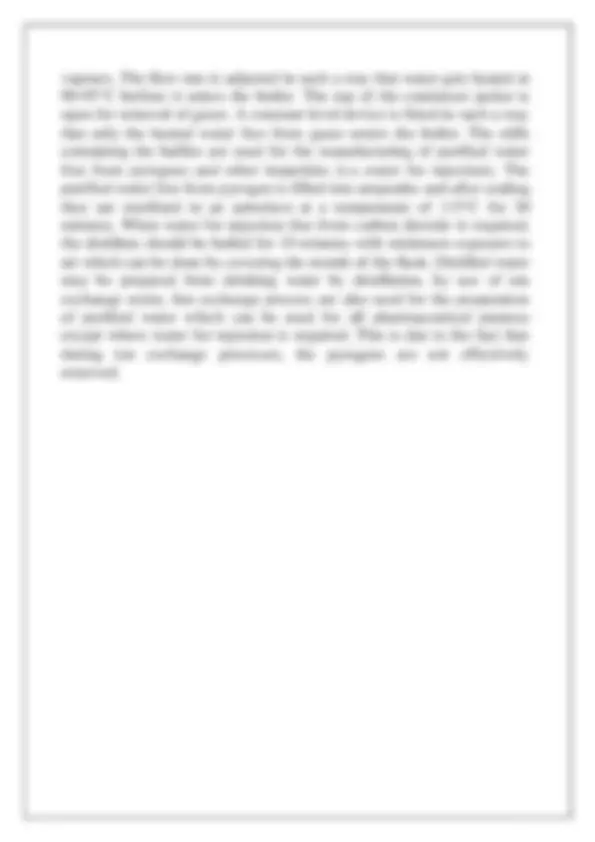
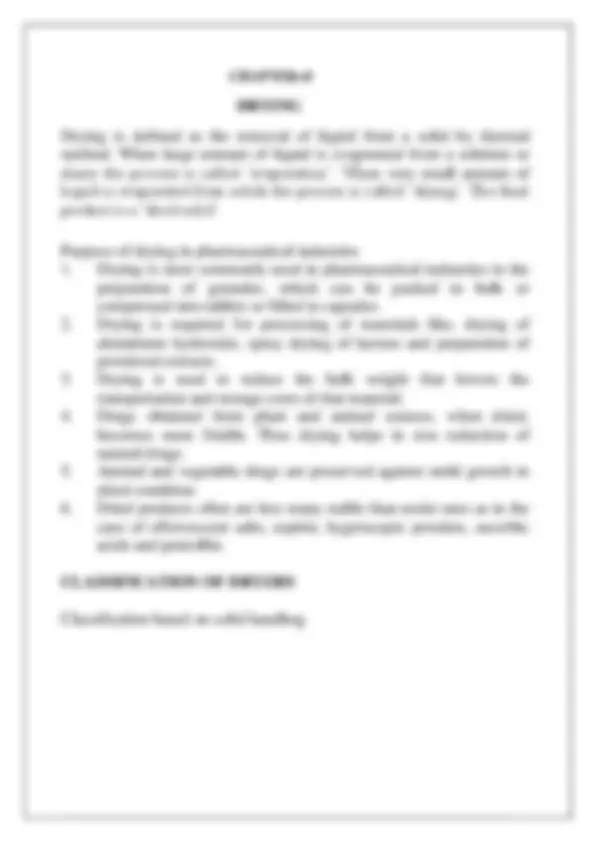
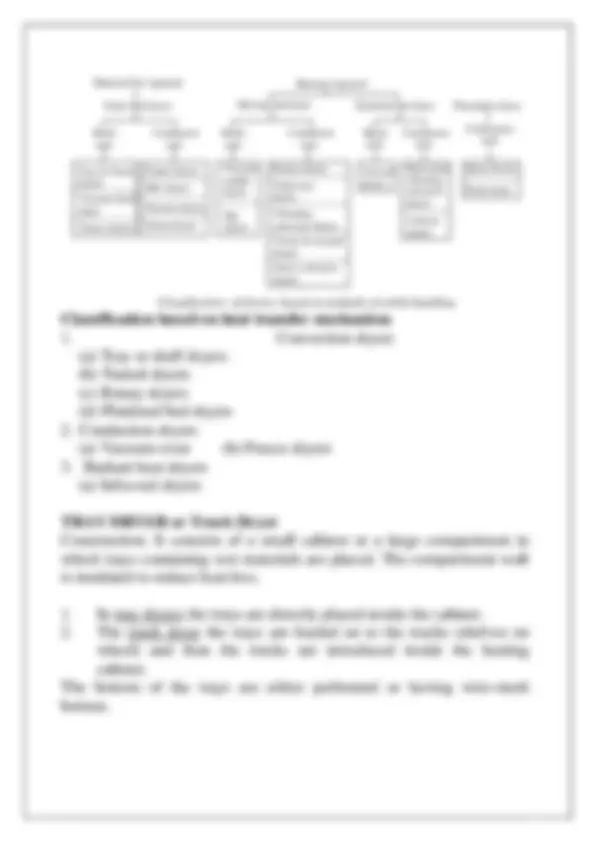
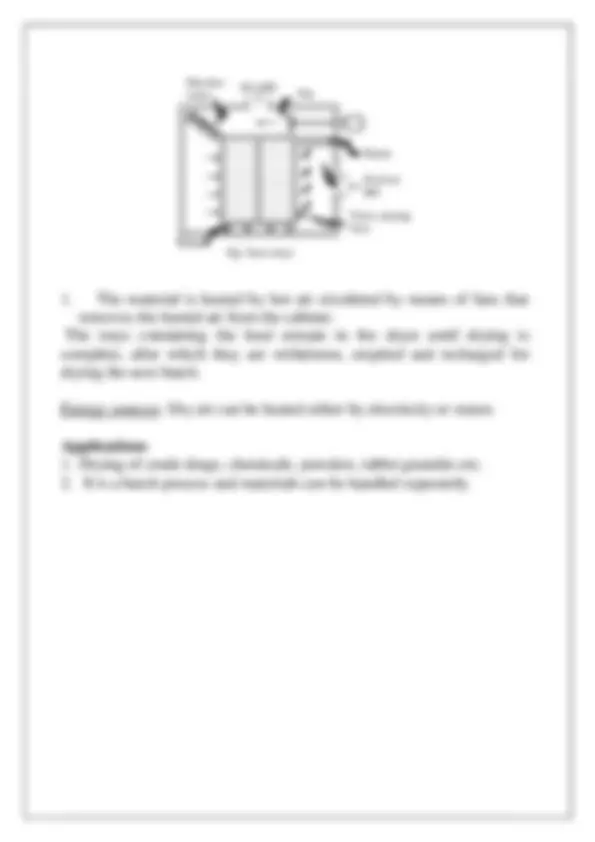
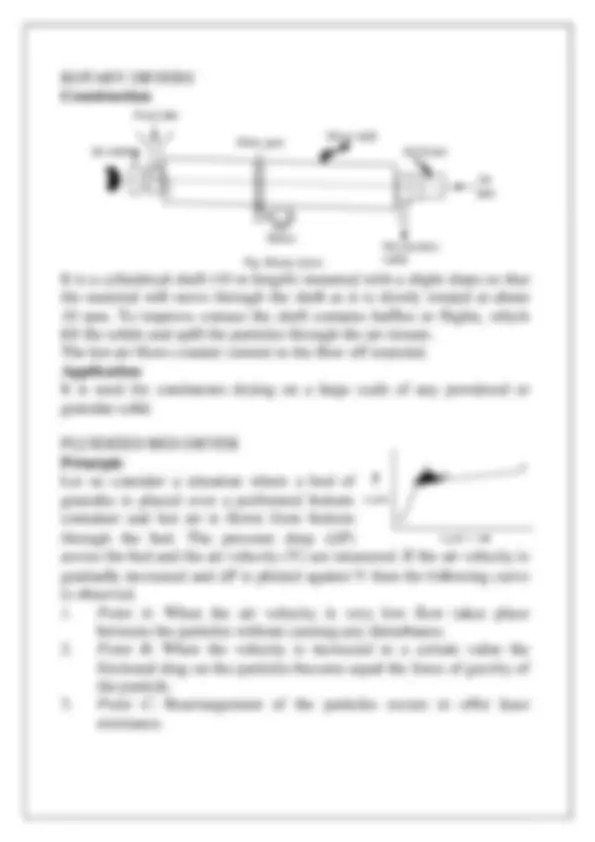
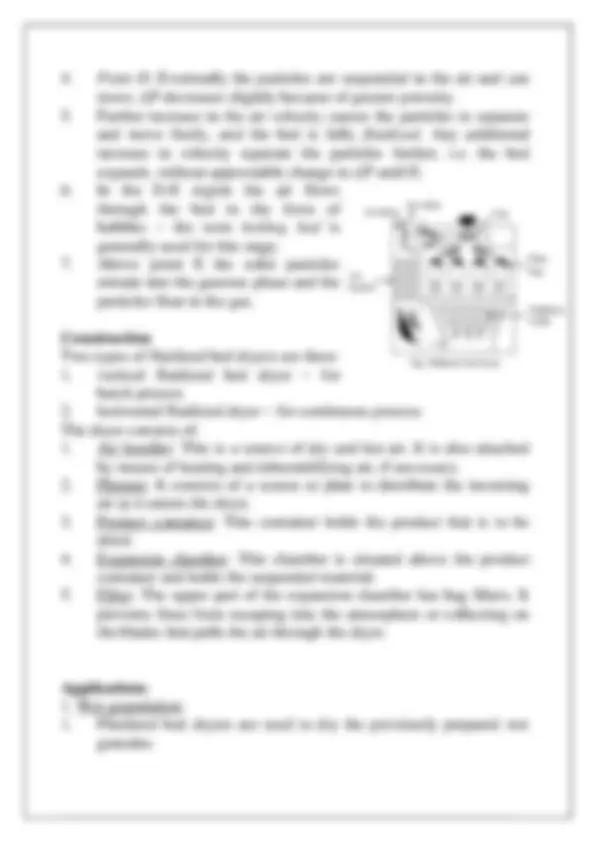
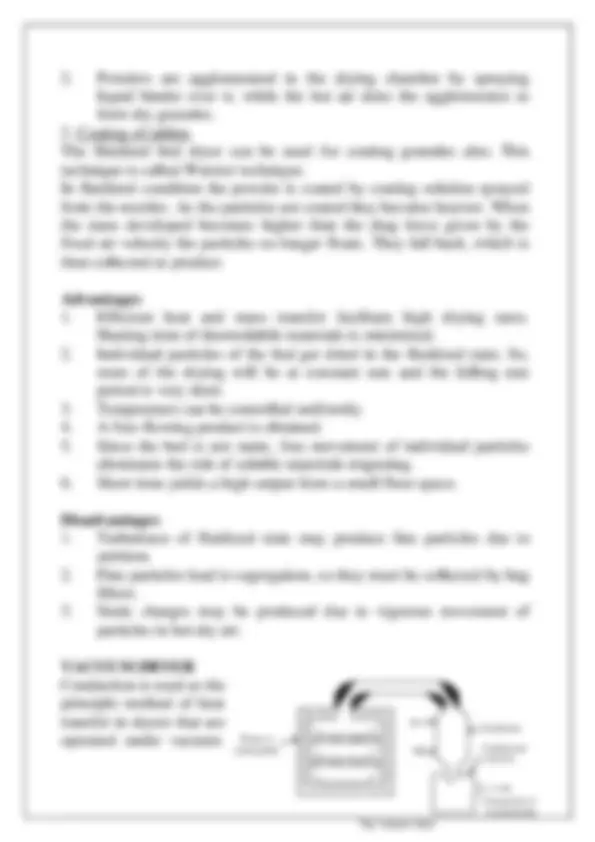
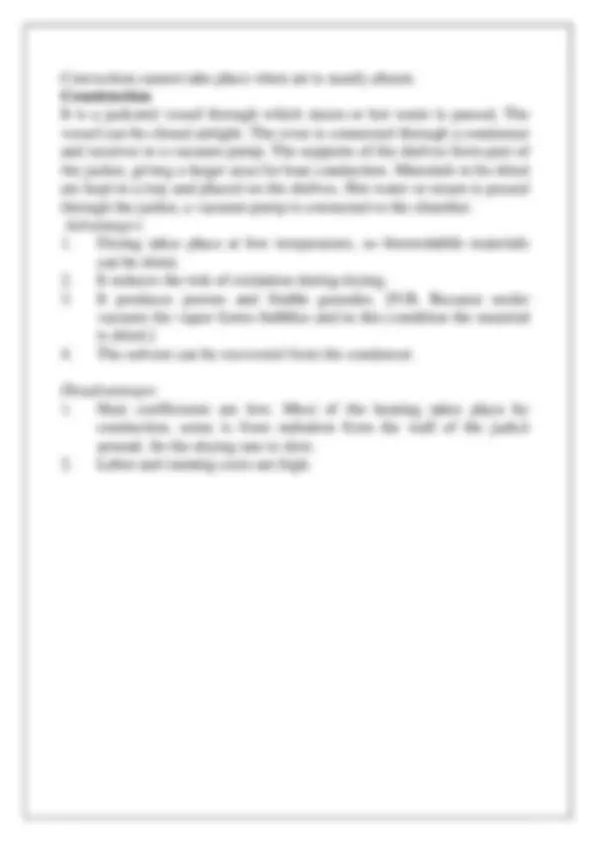
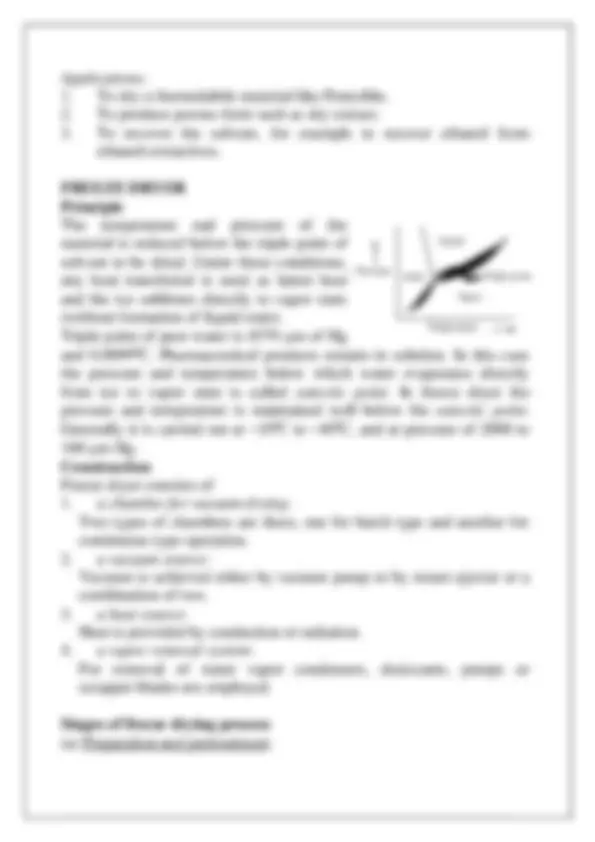
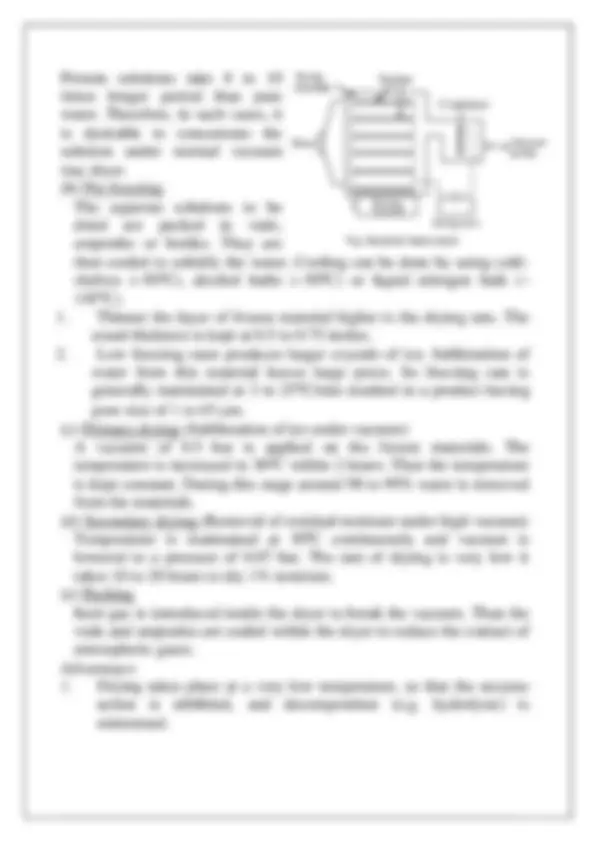
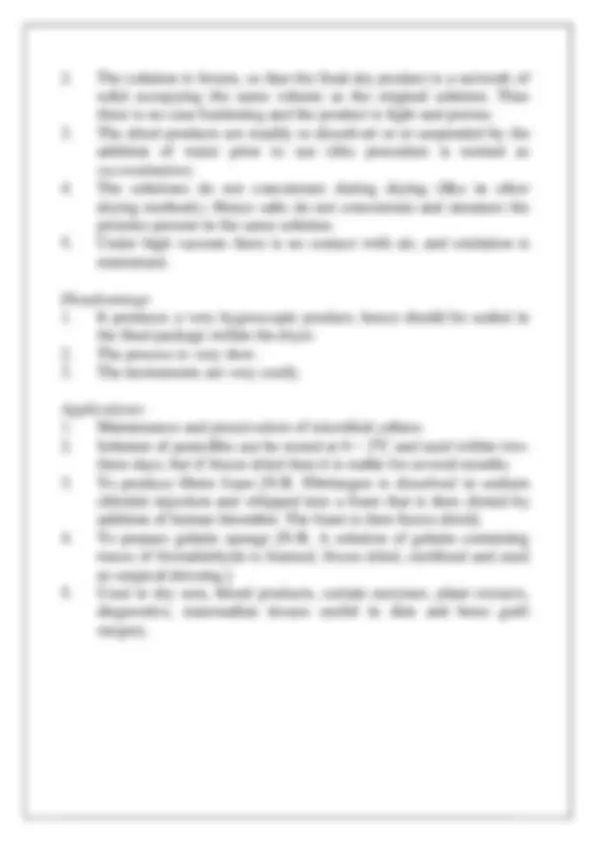
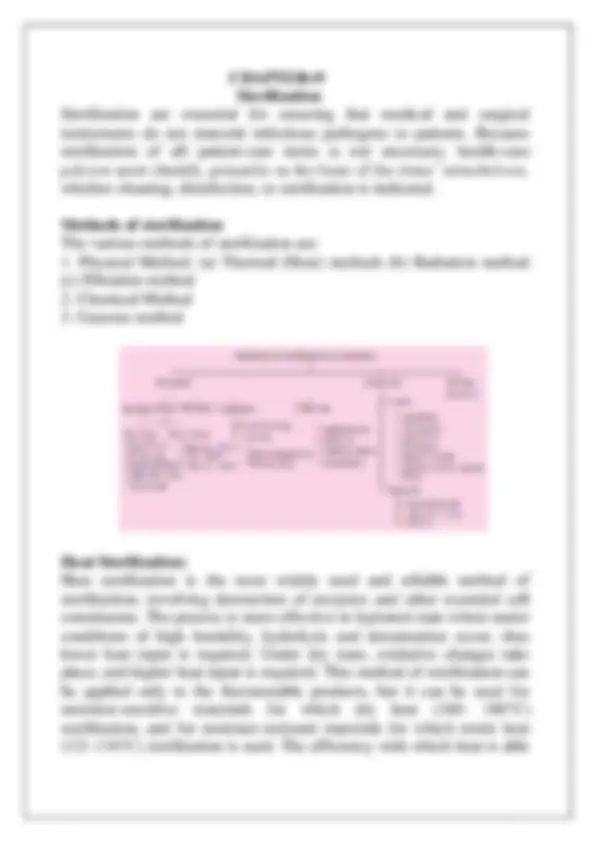
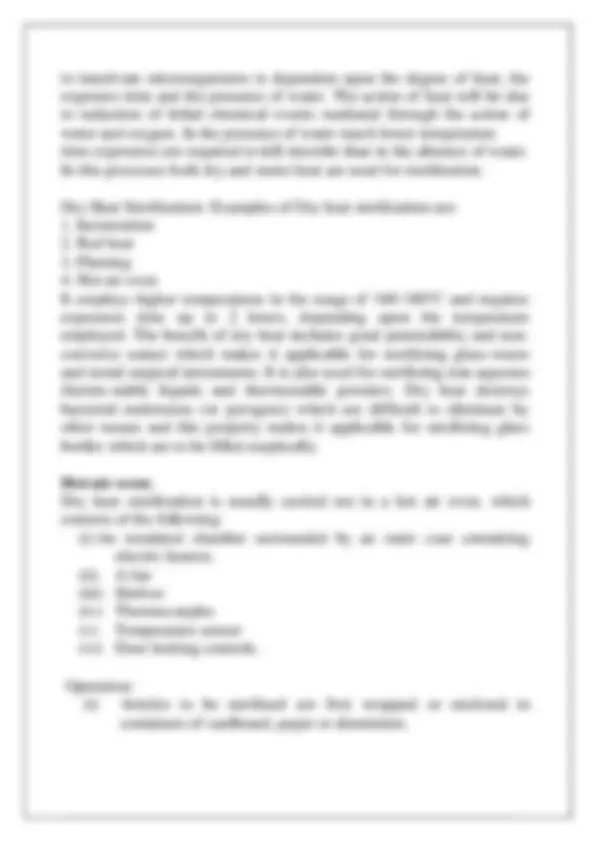
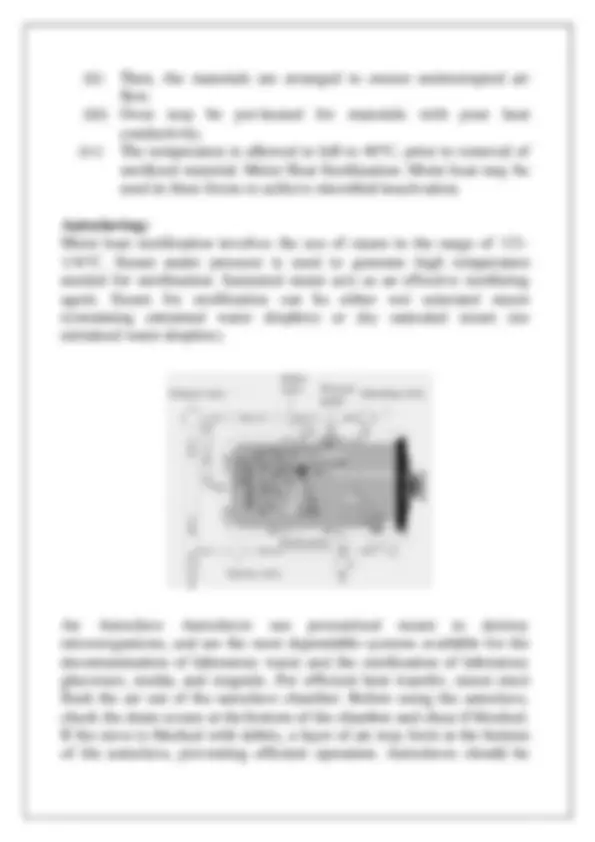
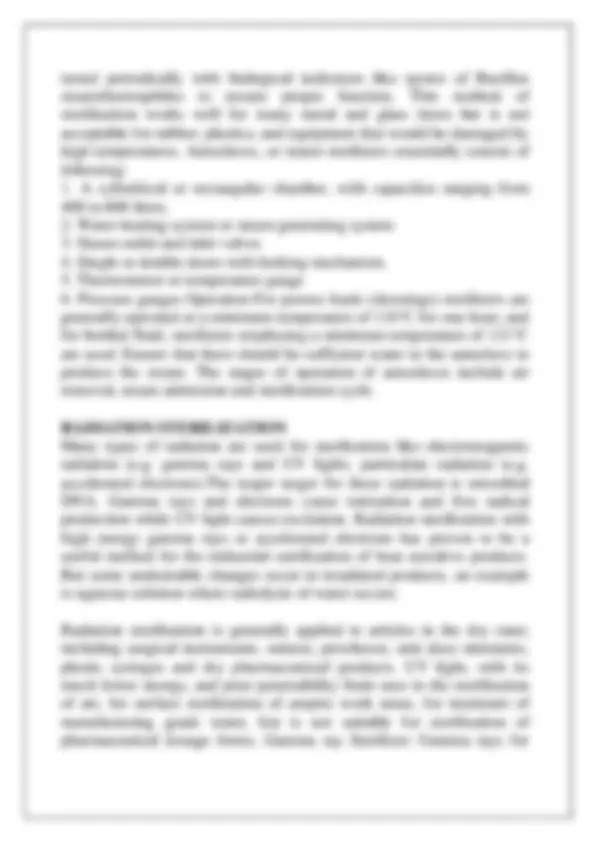
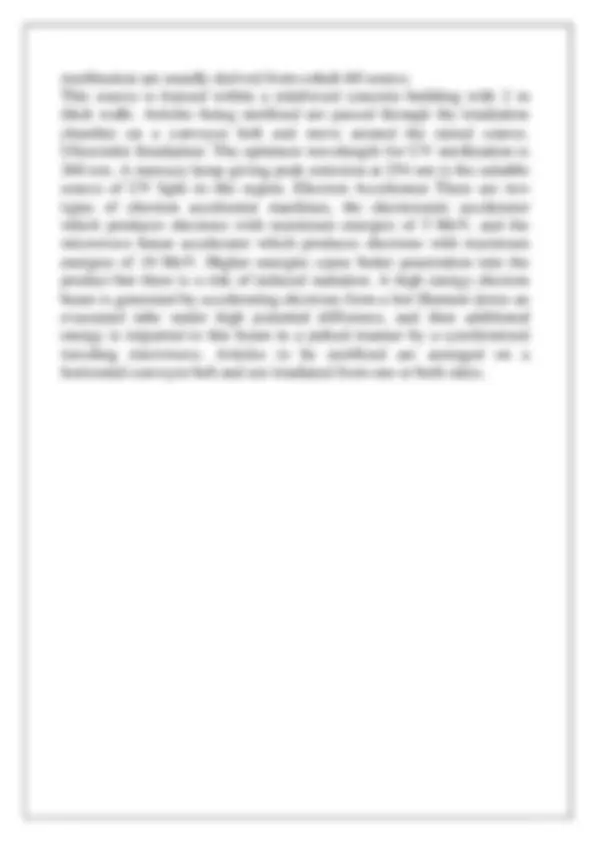
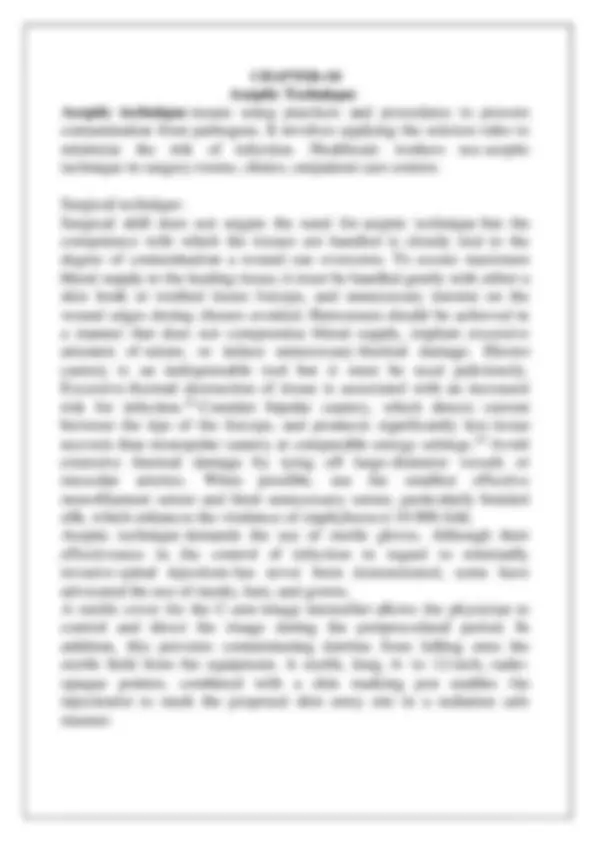
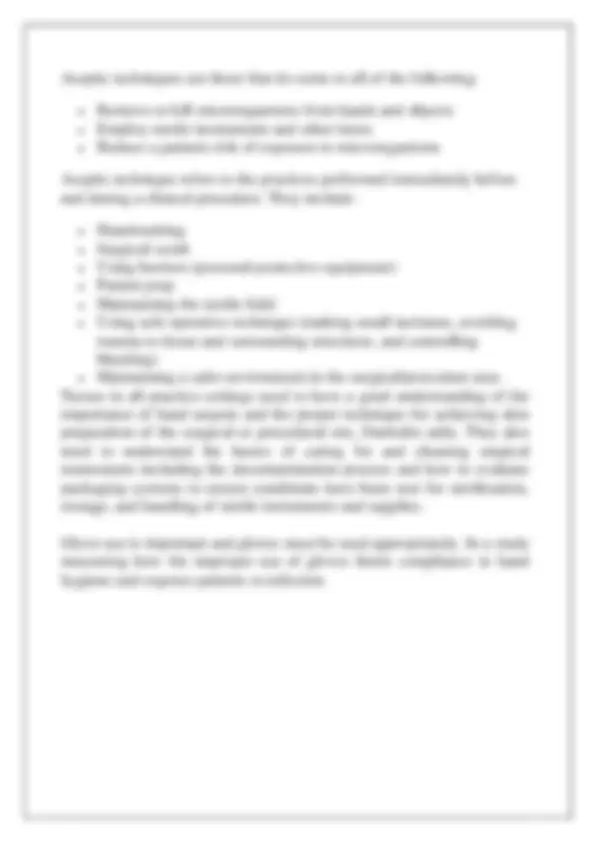
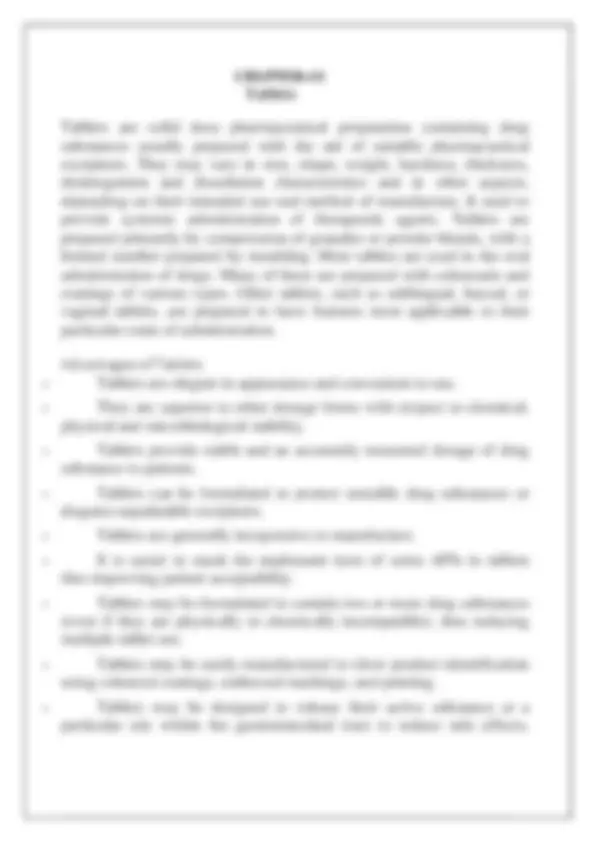
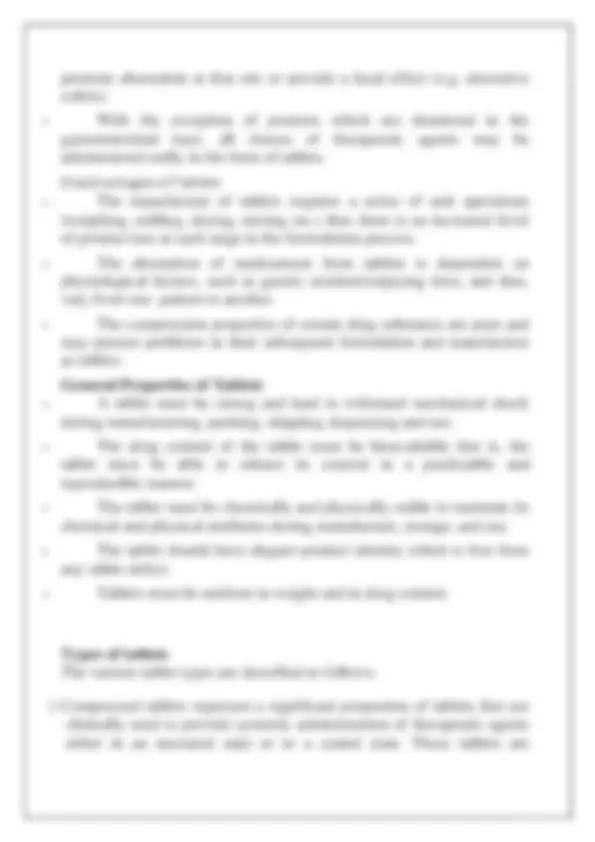
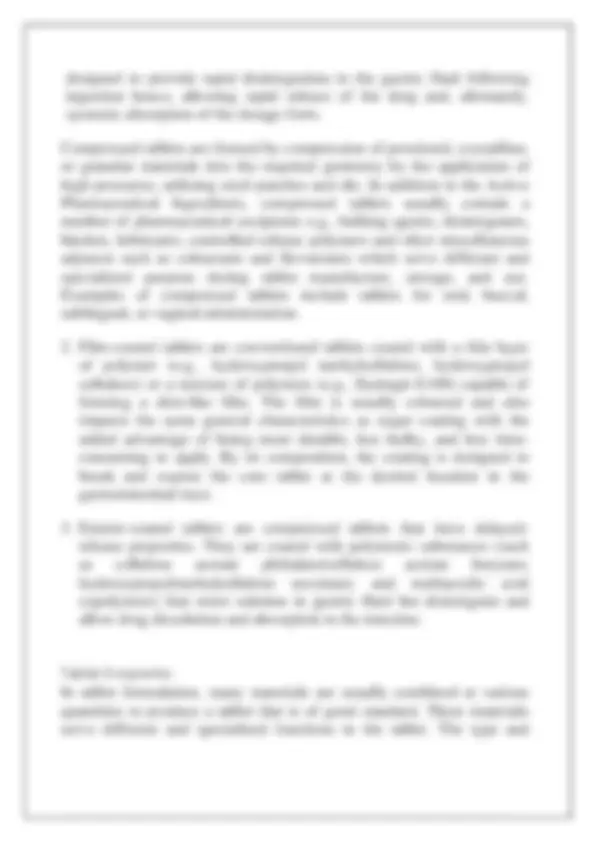
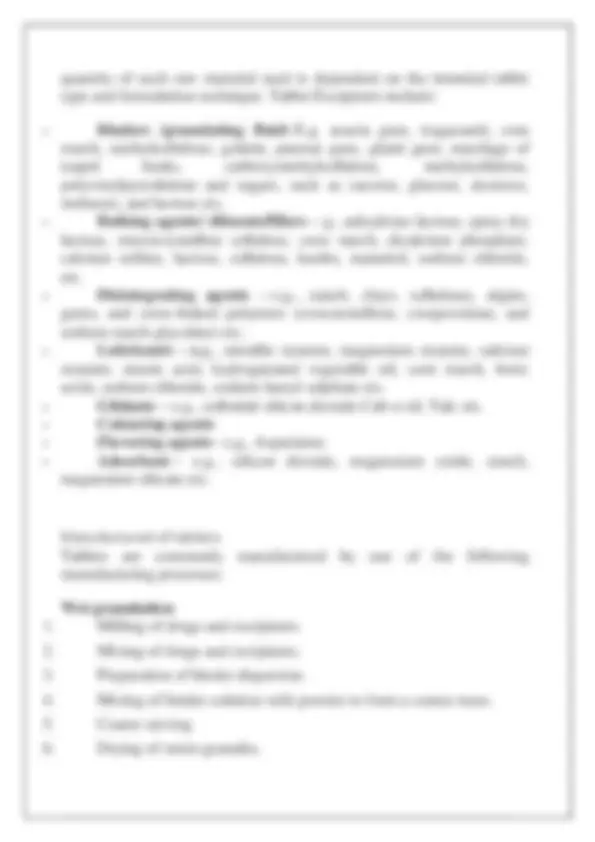
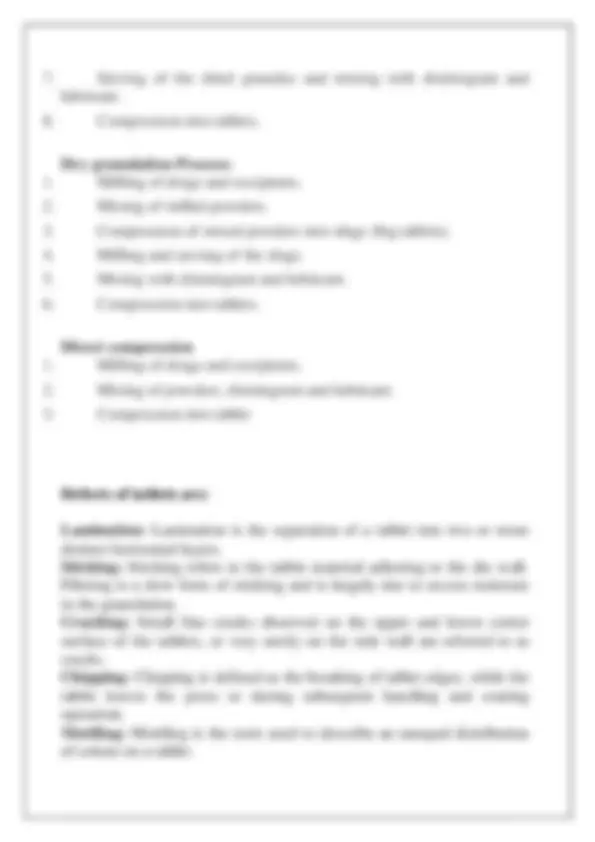
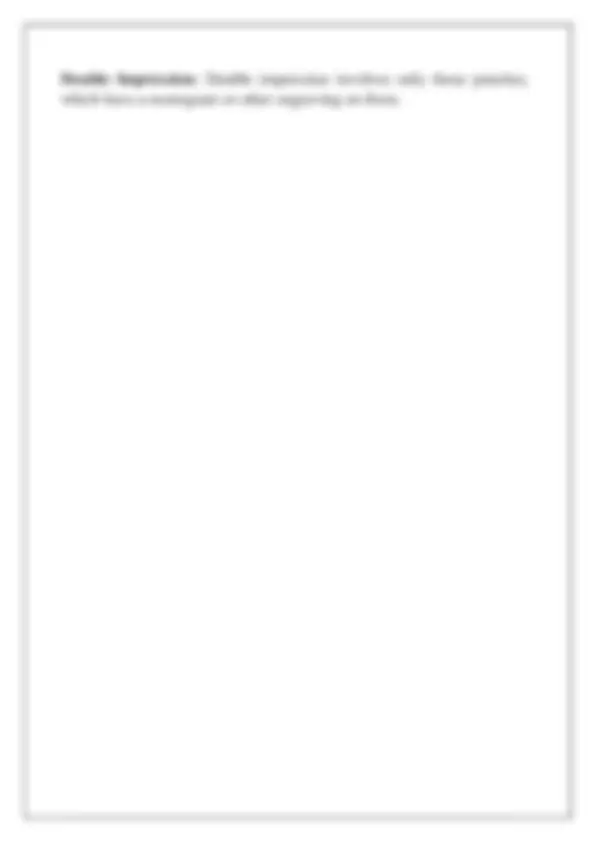
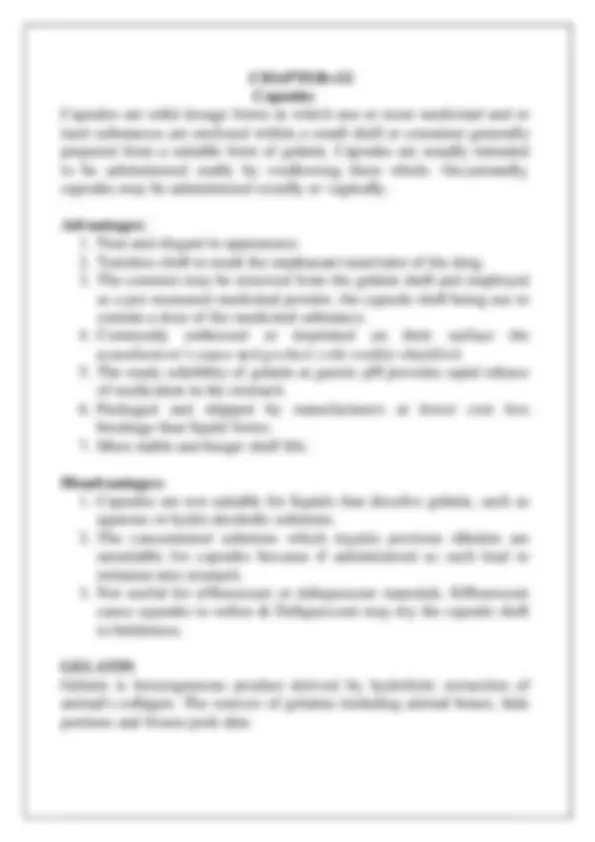
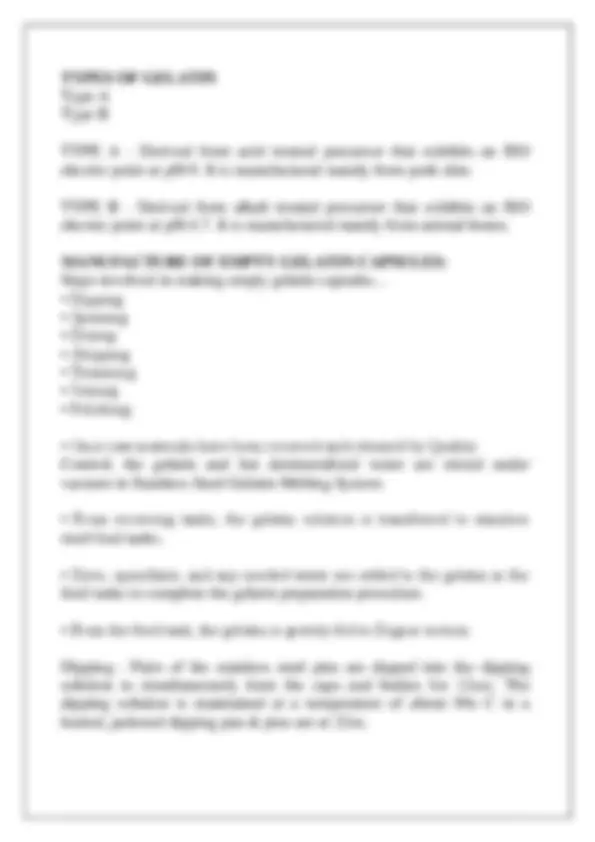

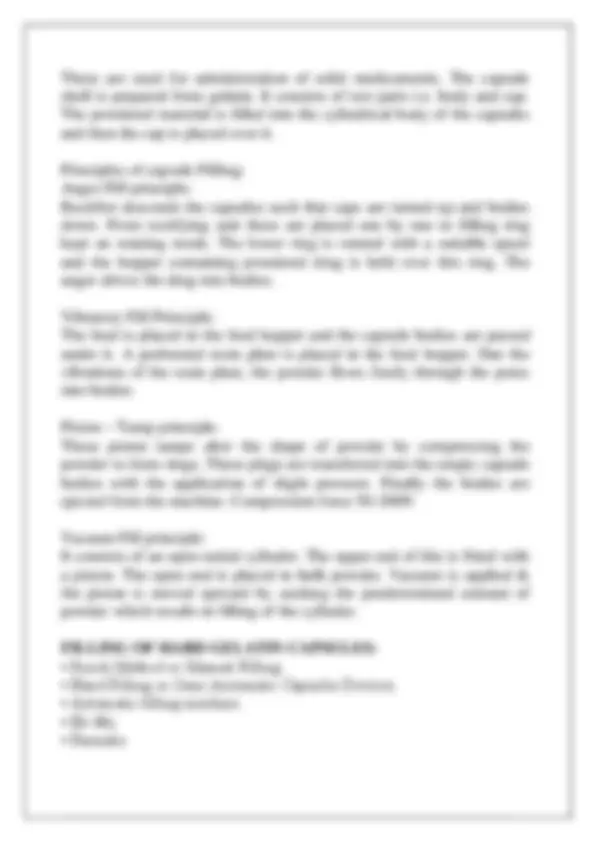
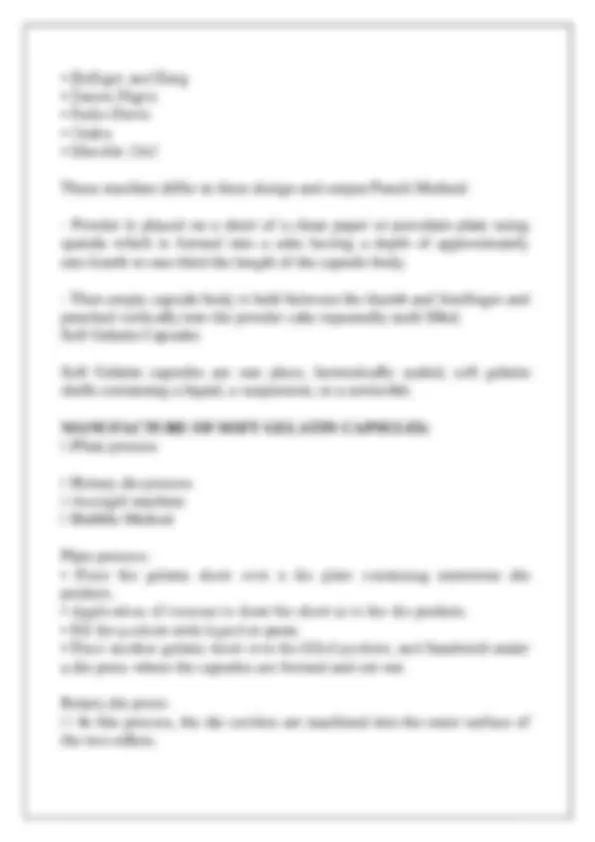
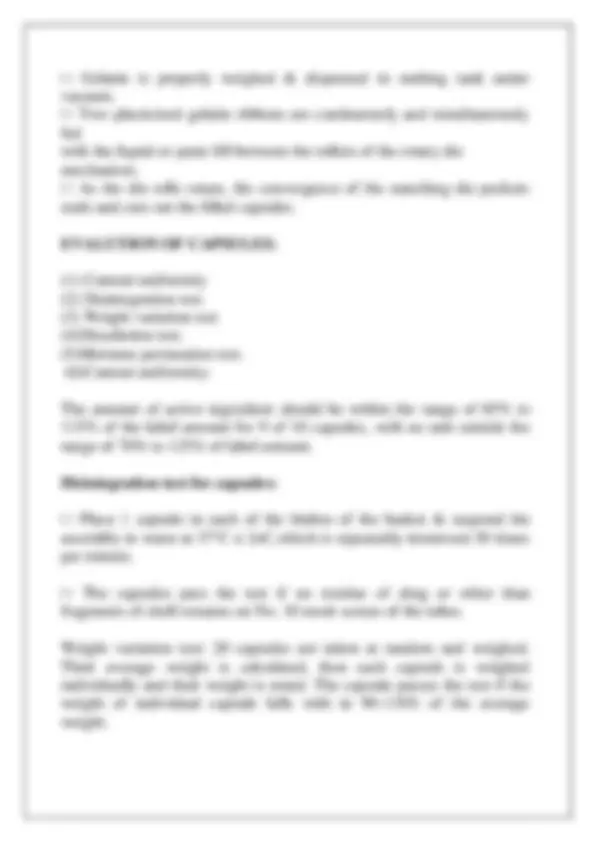
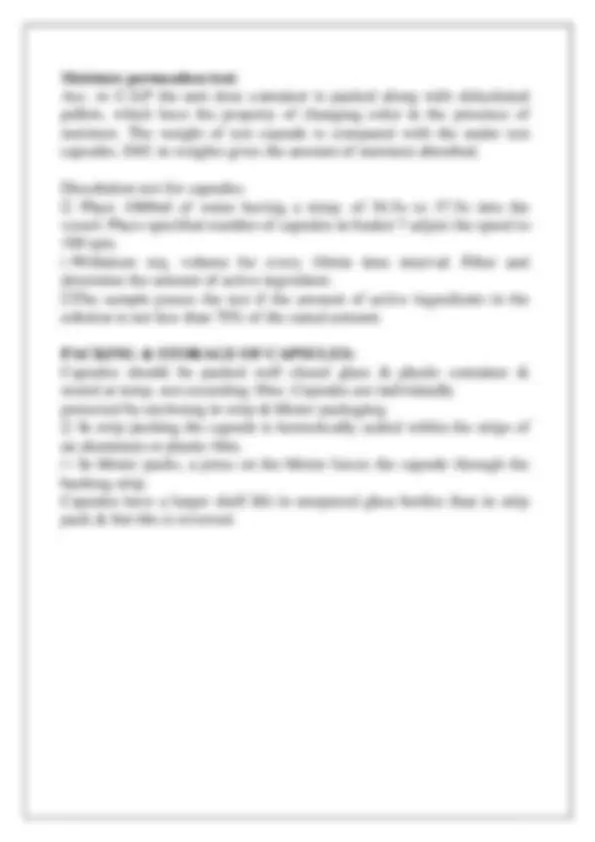
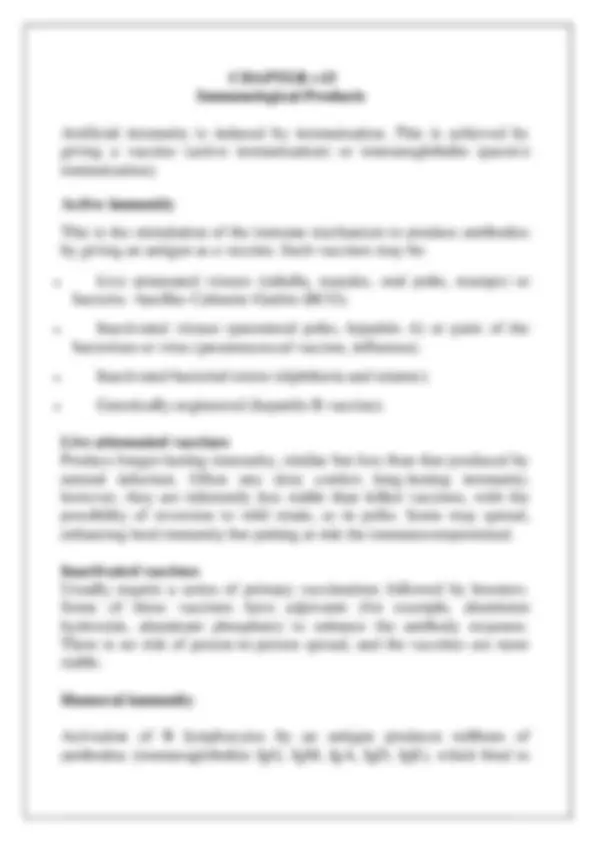
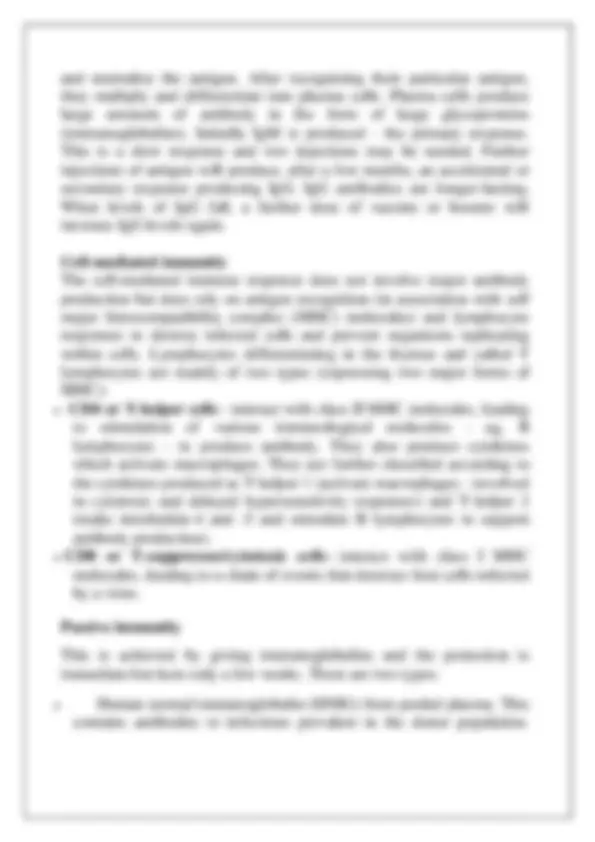
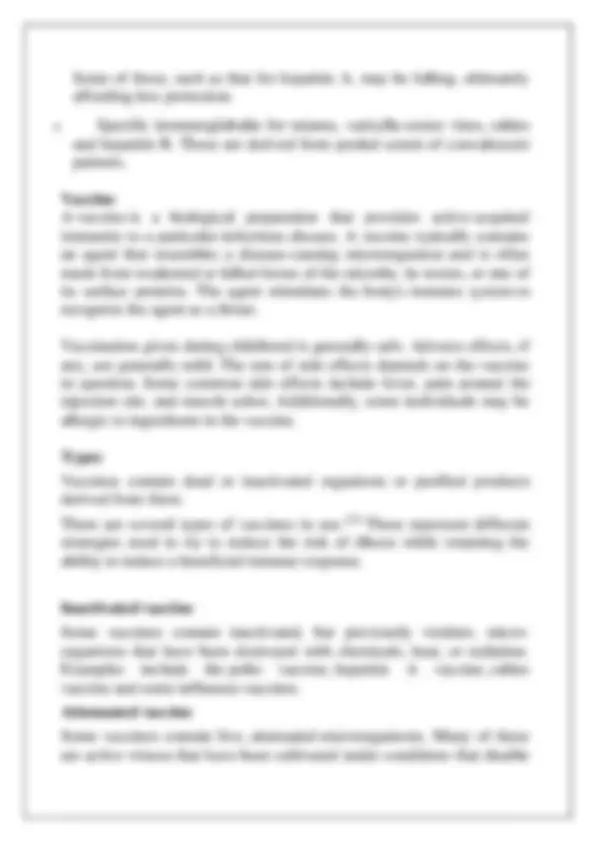
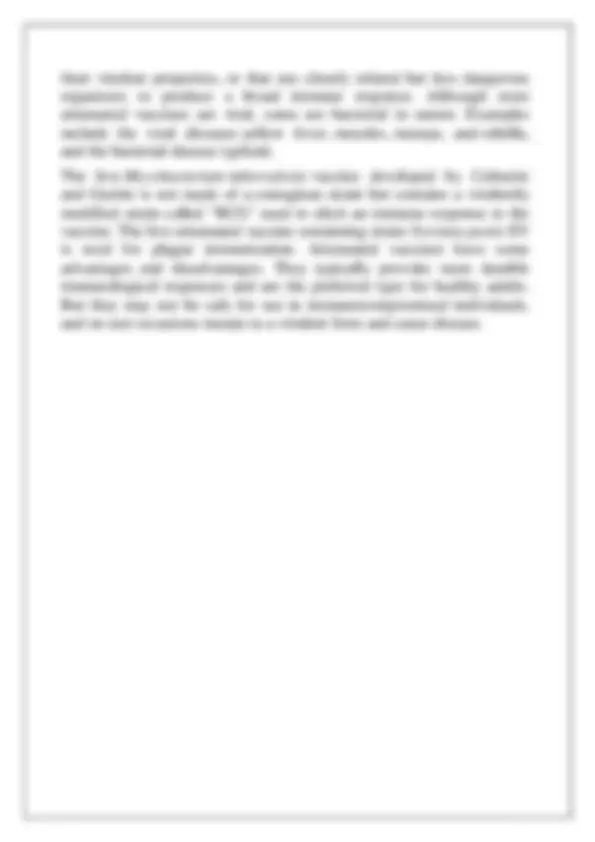
Study with the several resources on Docsity
Earn points by helping other students or get them with a premium plan
Prepare for your exams
Study with the several resources on Docsity
Earn points to download
Earn points by helping other students or get them with a premium plan
Community
Ask the community for help and clear up your study doubts
Discover the best universities in your country according to Docsity users
Free resources
Download our free guides on studying techniques, anxiety management strategies, and thesis advice from Docsity tutors
A basic overview of pharmaceutical dosage forms, including capsules, creams, and powders. It also discusses various manufacturing processes, such as mixing, separation, and sterilization, used in the pharmaceutical industry. The document highlights the importance of particle size and distribution in tablet and capsule production, as well as the different types of evaporators used for liquid processing. It also covers the different types of water used in pharmaceutical practice, including purified water, water for injection, and sterile water for injection. The document concludes with a brief discussion on sterilization methods, including heat sterilization, radiation sterilization, and uv sterilization.
Typology: Schemes and Mind Maps
1 / 65
This page cannot be seen from the preview
Don't miss anything!
Route of administration Physical state
DRUG: “ A drug may be defined as an agent, intended for use in the diagnosis, mitigation, treatment, cure or prevention of disease in man or in animals”. DOSAGE FORM: Drugs are rarely administered in their original pure state. They are converted into suitable formulation which are called dosage forms. Every dosage form is a combination of the drug and other non-drug components. CLASSIFICATION OF DOSAGE FORMS (i) Solid (i) Oral (i) Skin (i) Internal (ii) Semisolid (ii) Parenteral (ii) Eye (ii) External (iii) Liquid (iii) Rectal (iii) Tooth (iv) Gaseous (iv) Nasal (iv) Hand (v) Foot (vi) Hair (vii) Nose Route of administration Dosage forms Oral Powders, tablets, capsules, solutions, emulsions, syrups, elixirs, magmas, gels, cachets, pills. Parenteral Solutions, suspensions, emulsions. Transdermal Ointments, creams, powders, pastes, lotions, plaster Rectal Suppositories, tablets, ointments, creams, douches, foams. Site of Application DOSAGE FORM Use
Urethral Suppositories Sublingual Lozenges, tablets Intranasal Solutions, sprays, inhalations. Conjunctival Ointments Intra-ocular Solutions Intra-respiratory Aerosols CACHETS Cachets consists of a dry powder enclosed in a shell. The shell is prepared from a mixture of rice flour and water by moulding into suitable shape and then dried. Two types of cachets are there: (i) Wet seal cachets: Lower half of the cachet is filled with powdered drug. Then the flange of the empty upper half of the cachet is moistened with water, and pressed over the lower half. The cachet is dried for 15 minutes. (ii) Dry seal cachets: Drug powder is filled in the lower half and the upper half is pressed over it just like a capsule. Use: They are used for administering the drug with unpleasant taste and a large dose. Before administration, a cachet should be immersed in water for few seconds and then placed on the tongue and swallowed with water. e.g. - Sodium aminosalicylate cachets, Sodium aminosalicylate and isoniazid cachets. CAPSULES Capsule are the solid unit dosage form of medicament in which the drug or drugs are enclosed in a practically tasteless, hard or soft soluble container of shell made up of gelatin. Hard gelatin capsules are made up of two cylindrical halves, one slightly larger in diameter but shorter in length known as cap and the other slightly shorter in diameter but longer in length known as base. Soft gelatin capsules are flexible in nature. They may be spherical, ovoid cylindrical or tubes. The small spherical capsules are also known as ‘pearls’. Soft gelatin capsules are used to enclose solids, semisolids or liquids for oral administration the capsule is placed on the tongue and
to release the medicament. POWDERS Powders are solid dosage form of medicament meant for internal and external use. The powders meant for internal use are known as oral powders whereas those meant for external use are known as dusting powders. TABLETS Tablets are unit solid dosage form of medicament or medicament with or without suitable diluents. They are prepared usually by compression. Tablets are generally meant for oral administration but may be used by other routes of administration. E.g.-paracetamol tablets. SUPPOSITORIES Suppositories are special shaped solid dosage form of medicament for insertion into body cavities other than mouth. These products are so formulated that after insertion, they will either melt of dissolve in the cavity fluids to release the medicament. Suppositories vary in shapes, sizes and weights. General suppositories from 1 to 2 gm are prepared with either cocoa-butter or glycerol- gelatin base. E.g. aminophylline. SEMISOLID DOSAGE FORMS CREAMS Creams are viscous liquid or semisolid emulsions intended for application to the skin i.e. for external use. Creams are of two types, aqueous creams and oily creams. In case of aqueous creams the emulsions are oil-in-water type and in case of oily creams emulsions are of water-in-oil type. e.g. cetomacrogol cream, cetrimide cream. Advantages of creams:
and are easier to apply.
inflamed mucous membrane preventing contact with air in the surroundings), sedative or expectorant action. The viscous vehicle soothes the sore membrane of the throat. The usual dose is 5 ml. Linctus’s should be taken in small doses, sipped and swallowed slowly without diluting it with water in order to have the maximum and prolonged effect of medicaments. Simple Syrup is generally used as a vehicle. For diabetic patients Sorbitol solution is used instead of Simple Syrup.
Metrology Metrology is the branch of science dedicated to measurement, which is defined as the process of comparing an unknown quantity. There are two type of weight and measurement system used in pharmacy.
Indian Pharmacopoeia: The Indian Pharmacopoeia Commission (IPC) is an Autonomous Body under Ministry of Health & Family Welfare, Govt, of India primarily with the objectives of regularly updating the Indian Pharmacopoeia by publishing new edition and its addenda, National Formulary of India and other related tasks such as preparing, certification and distribution of reference substances & functions as National Coordination Centre (NCC) for Pharmacovigilance Programme of India (PvPI).
Packaging of Pharmaceuticals A Pharmaceutical Package container is an article or device which contains the Pharmaceutical Product and the container may or may not in direct contact with the product. The container which is designed for pharmaceutical purpose must be stable. Ideal Qualities of a Pharmaceutical Package.
a. This is the most expensive metal among tin, lead, aluminium, & iron. b. Currently some eye ointments still package in pure tin ointment tubes. Aluminum Advantages
CHAPTER= 4 Size Separation Size separation is a unit operation that involves the separation of a mixture of various size particles into two or more portions by means of screening surfaces. Size separation is also known as sieving, sifting, screening. This technique is based on physical differences b/w the particles such as size, shape and density. Factors affecting size reduction Material structure. Some substances are homogeneous in character. Mineral substances may have lines of weakness. The materials splits to form flake-like particles. Vegetable drugs have a cellular structure often leading to long fibrous particles. Size Separation Methods: a. Sieving b. Cyclone separator c. Air separator Elutriation. Sieving: Sieving Working of mechanical sieves A. Agitation Oscillation: Back and froth Vibration: Rapid vibration Gyration: Rotatory B. Brushing: C. Centrifugal: Principle: Sieving a. Sieves: Sieves Sieves for pharmacopeial testing are constructed from wire cloth with sqare meshes, woven from wires of brass, bronze, stainless steel etc., Number of sieve: No of meshes in a length of 2.54 cm in each transfer direction parallel to the wires. Nominal size of aperture: Distance between the wires. Length of the side of the square aperture. (in mm or μm). Nominal diameter of the wire: Made of suitable diameter in order to give a suitable aperture and sufficient length. Approximate % sieving area: The area of the meshes as a percentage of the total area of the sieve. Generally the sieving area is kept within the range of 35-40% in order to give suitable strength to the sieve. Tolerance average aperture size: Fine sieves cannot be woven with same accuracy. b. Cyclone Separator: Principle: Centrifugal force used to separate the solids from fluids Depends not only on particle size but particle density Hence, coarse particles will settle down and fine particles will be carried out with fluid. Working: The suspension of particles is introduced tangentially at a very high velocity. The rotatory flow
CHAPTER= Mixing Mixing may be defined as the process in which two or more than two components in a separate or roughly mixed condition are treated in such a way so that each particle of any one ingredient lies as nearly as possible to the adjacent particles of other ingredients or components. This process may involve the mixing of gases, liquids or solids in any possible combination and in any possible ratio of two or more components. Mixing of a gas with another gas, mixing of miscible low viscosity liquids and mixing of a highly soluble solid with a low viscosity liquid to effect dissolution are relatively simple as compared to the mixing of gases with liquids, mixing of liquids of high viscosity though miscible, mixing of two immiscible liquids such as aqueous and oily solutions to form emulsions, mixing of solids with liquids when the proportion of solids is high and mixing of solids with solids, specialized equipments are required for these operations. Some of the examples of large scale mixing practiced in pharmacy are: Mixing of powders in varying proportions prior to granulation or tableting. Dry mixing of the materials for direct compression in tablets. Dry blending of powders in capsules and compound powders (insufflations). Blending of powders in cosmetics in the preparation of face powders, tooth powders Dissolution of soluble solids in viscous liquids for dispensing in soft capsules and in the preparation of syrups Mixing of two immiscible liquids for preparation of emulsions. Objectives of mixing To ensure that there is uniformity of composition between the mixed ingredients which may be determined by taking samples from the bulk material and analyzing them, which should represent overall composition of the mixture. To initiate or to enhance the physical or chemical reactions e.g. diffusion, dissolution etc. When two or more than two miscible liquids are mixed together, this results in to a solution known as true solution. When two immiscible liquids are mixed in the presence of an emulsifying agent, an emulsion is produced. When a solid is dissolved in a vehicle, a solution is obtained. When an insoluble solid is mixed with a vehicle, a suspension is obtained. When a solid or liquid is mixed with a semisolid base, an ointment or a suppository is produced. When two or more than two solid substances are mixed together, a powder is obtained which when filled into capsule shell is known as capsules and when compressed under heavy pressure is called tablet. Types of Mixtures : Mixtures may be classified as follows:
on the surface can decrease aggregation, for e.g. addition of colloidal silica to a strongly aggregating zinc oxide can make it a fine dusting powder which can be easily mixed. ™ Particle size – Variation in particle size leads to separation as the small particles move downward through the spaces between the bigger particles. As the particle size increases, flow properties also increases due to the influence of gravitational force on the size. It is easier to mix two powders having approximately the same particle size. ™ Particle shape – For uniform mixing, the particles should be spherical in shape. The irregular shapes can become inter-locked and there are less chances of separation of particles once these are mixed together. ™ Particle charge – Some particles exert attractive forces due to electrostatic charges on them. This results to separation or segregation. Mechanism of Mixing In all type of mixers, mixing is achieved by applying one or more of the following mechanisms: Convective mixing – During convective mixing transfer of groups of particles in bulk take place from one part of powder bed to another. Convective mixing is referred to as macromixing. Shear mixing – During shear mixing, shear forces are created within the mass of the material by using agitator arm or a blast of air. Diffusive mixing – During this mixing, the materials are tilted so that the gravitational forces cause the upper layers to slip and diffusion of individual particles take place over newly developed surfaces. Diffusion is also sometimes referred to as micromixing. Powder mixers Dry mixer (stationary container): For batch work the dry mixer which is the stationary shell type is often used. This consists of a semi-cylindrical trough, usually covered and provided with two or more ribbon spirals. One spiral is right-handed and the other left-handed. So that the material is worked back and forth in the trough. Ribbon cross section and pitch and number of spirals on the ribbon are varied for different materials varying from low density, finely divided materials to fibrous or sticky materials. It may be centre discharge or end discharge. Another variation is the mounting of cutting blades on the central shaft. A broad ribbon lifts and conveys the materials while a narrow one will cut through the materials while conveying. Ribbon blenders are often used on the large scale and may be adapted for continuous mixing. Dry Mixer: The paddle mixer has a stationary outer vessel and the powders are agitated by paddles rotating within. The equipment is suitable to heating, by jacketing the vessel, and also permits a kneading effect by the use of appropriately shaped paddles or beaters. In the bowl mixer the paddle is mounted vertically and in the trough mixer (e.g., dry mixer) a number of vanes are mounted horizontally. Vertical screw mixer: In these types of mixers, the screw rotates about its own axis while orbiting around the centre axis of the conical tank. In another variation, the screw does not orbit but remains in the centre of the conical tank and is tapered so that the swept area steadily increases with increasing height. This type of mixer is mainly used for free flowing solids.
EVAPORATING PAN Working The dilute solution is taken in the pan. Steam is introduced through the steam inlet into the jacket to heat the pan. In these evaporators the movement of the liquid results from convection currents set up by the heating process. The concentrated liquid is collected through the outlet placed at the bottom of the pan. Advantages: (a) It is simple and cheap to construct. (b) It is easy to use, clean and maintain. Disadvantages: (a) Having only natural circulation, the overall coefficient of heat transfer will be poor and solids are likely to deposit on the surface, leading to decomposition of the product and a further deterioration in heat transfer. (b) Also many products give rise to foaming. (c) The total liquor is heated over all the time, which may be unsatisfactory with thermo labile materials. (d) The heating surface is limited and decreases proportionally as the size of the pan increases. (e) The pan is open, so the vapor passes to the atmosphere, which can lead to saturation of the atmosphere. (f) Only aqueous liquids can be evaporated in these pans. (g) Pan evaporation cannot be done under reduced pressure. (h) Can only be used for thermo labile products. EVAPORATING STILLS Construction It consists of a jacketed- evaporating pan with a cylindrical cover that connects it to a condenser. The overall assembly is called still. The cover is clamped with the evaporating pan. Working The dilute liquid is fed into the still, the cover is clamped. Steam is introduced into the jacket. The liquid is evaporated and condensed in the condenser and collected. The product (i.e. concentrated liquid) is collected through the product outlet. Advantages : (a) Simple construction and easy to clean and maintain. (b) The vapor is removed by condensation which (i) speeds evaporation (ii) reduces inconvenience and (iii) Allows the equipment to be used for solvents other than water e.g. ethanol.
(c) A receiver and vacuum pump can be fitted to the condenser, permitting operation under reduced pressure and, hence, at lower temperature. Disadvantages : (a) Natural convection only (b) All the liquor is heated all the time (c) The heating surface is limited. SHORT TUBE EVAPORATOR (Basket type vertical short tube evaporator) Construction and Principle Construction The evaporator is a cylindrical vessel. The lower portion of the vessel consists of a nest of tubes with the liquor inside and steam outside– this assembly is called calendar. The specifications of calendric are as follows: Tube length: 1 – 2 m Tube diameter: 40 – 80 mm Diameter of evaporator:2.5 m Number of tubes: 1000 The feed inlet is at the top of the calendar. The product outlet is placed at the bottom of the evaporator. Steam inlet and outlet is placed from the side of the calendric. Working The feed is introduced through the feed inlet and the liquor is maintained at a level slightly above the top of the tubes (of calendar), the space above this is left for the disengagement of vapor from the boiling liquor. The liquor in the tubes is heated by the steam and begins to boil, when the mixture of liquid and vapor will shoot up the tubes (in a similar manner to that of a liquid that is allowed to boil to vigorously in a test-tube). This sets up a circulation, with boiling liquor rising up the smaller tubes of the calendric and returning down the larger central down take. The product is collected through the product outlet. Advantages