
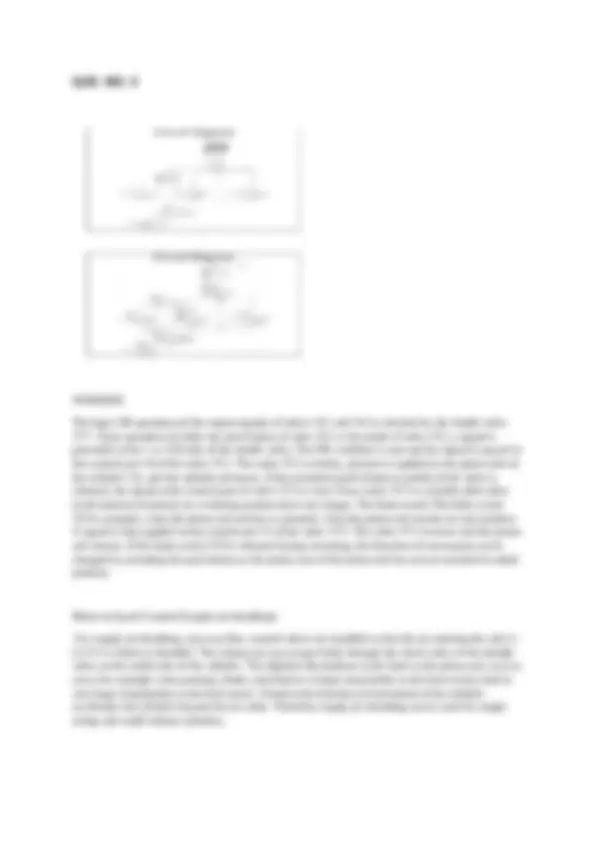
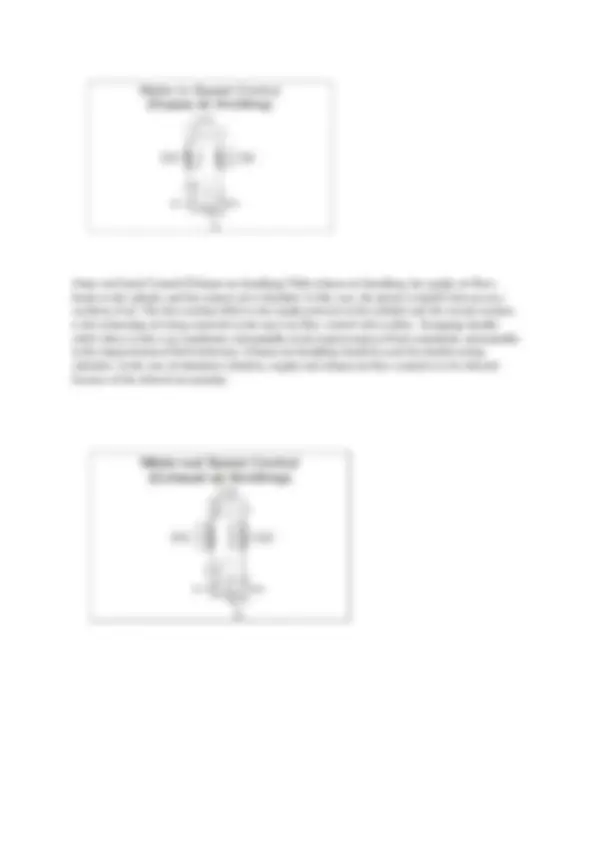
Study with the several resources on Docsity
Earn points by helping other students or get them with a premium plan
Prepare for your exams
Study with the several resources on Docsity
Earn points to download
Earn points by helping other students or get them with a premium plan
Community
Ask the community for help and clear up your study doubts
Discover the best universities in your country according to Docsity users
Free resources
Download our free guides on studying techniques, anxiety management strategies, and thesis advice from Docsity tutors
The concept of low-cost automation using pneumatic systems and control valves. It covers the working of various valves, their logic functions (or and and), and how they are used to control the movement of cylinders. The document also explains the concepts of meter-in and meter-out speed control.
What you will learn
Typology: Cheat Sheet
1 / 4
This page cannot be seen from the preview
Don't miss anything!
For controlling cylinders at high speed or of large diameter, the air flow required determines that a large size control valve should be used. The operating force to actuate the valve may be relatively large and in this case indirect control is preferable. The valve 1S when operated by a push button supplies a pilot signal to the 14 port of the control valve 1V. The valve 1V reverses, the piston rod of the cylinder is pressurised and the piston rod of cylinder 1A advances. If the push button is released, the control port of valve 1V exhausts to atmosphere. The valve 1V then reverses and the cylinder retracts. If the push button is released, the direction of movement is immediately reversed and the direction of movement is immediately reversed and the piston rod retracts. A change in the direction of movement is therefore possible without the piston rod reaching its initial or end position. Since the valve 1V is without memory function, it changes its switching position immediately after the push button of valve 1S has been pressed.
The pneumatic shuttle valve and the dual pressure valve have logic functions. Both have two inputs and one output each.The shuttle valve has the and one output each. The shuttle valve has the characteristic of an OR function, whereby at least either of two inputs 1 or 1(3) are required to generate an output at port 2 of the valve. In the case of the dual pressure valve, the characteristic is th f h A f i h b b hi hat of the AND function, whereby both inputs 1 and 1(3) are required to initiate an output 2.
The logic AND operation of the output signals of valves 1S1, 1S2 and 1S3 is checked by the dual- pressure valves 1V1 and 1V2. If the valves are actuated, i.e. 1S2 (via the workpiece), 1S3 (via the guard) and (via the guard) and 1S1 (via the operator) a signal is (via the operator), a signal is applied at output A of the dual-pressure valve 1V2. This signal is passed on to the control port 14 of the control element 1V3. The valve 1V3 reverses, pressure is applied at the piston side of the cylinder 1A and the piston rod advances. If the push button is released or the guard opened, this means that the AND conditions are no longer met. The control port 14 of the valve 1V3 is unpressurised. The valve 1V3 switches and the piston rod retracts.
Meter-out Speed Control (Exhaust air throttling) With exhaust air throttling, the supply air flows freely to the cylinder and the exhaust air is throttled. In this case, the piston is loaded between two cushions of air. The first cushion effect is the supply pressure to the cylinder and the second cushion is the exhausting air being restricted at the one-way flow control valve orifice. Arranging throttle relief valves in this way contributes substantially to the improvement of feed contributes substantially to the improvement of feed behaviour. Exhaust air throttling should be used for double-acting cylinders. In the case of miniature cylinders, supply and exhaust air flow control is to be selected because of the reduced air quantity.