
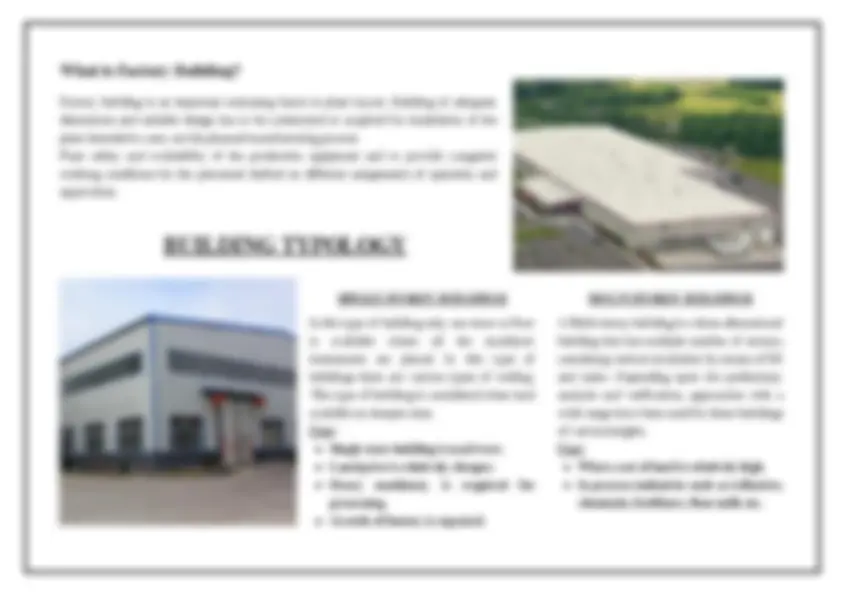
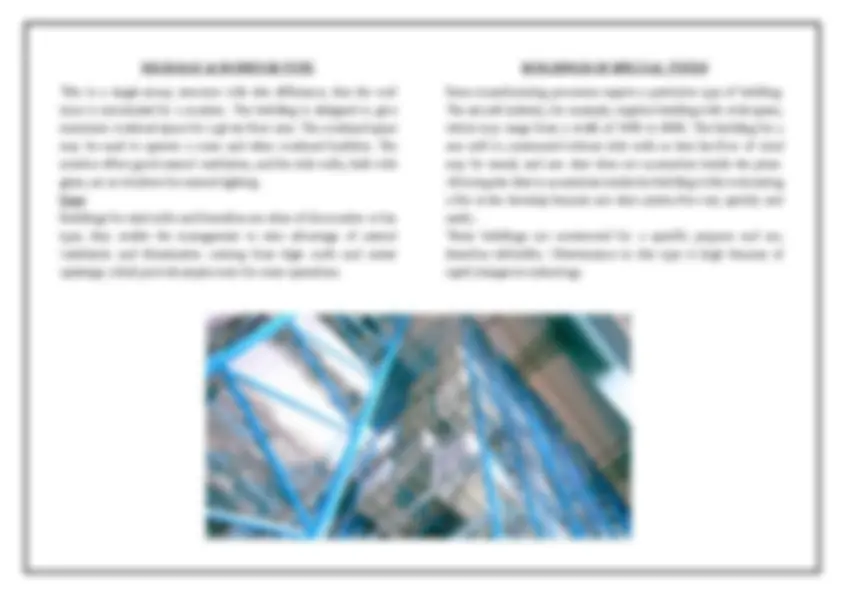
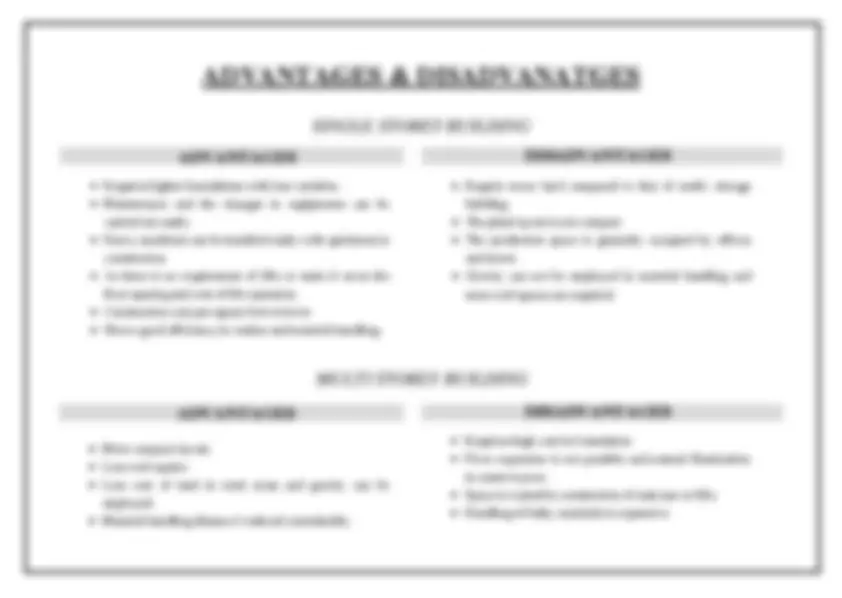
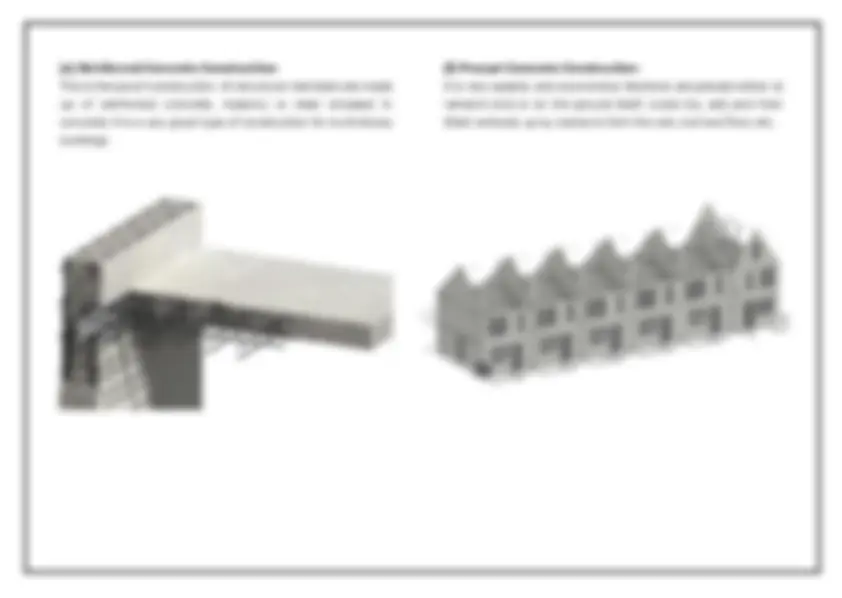
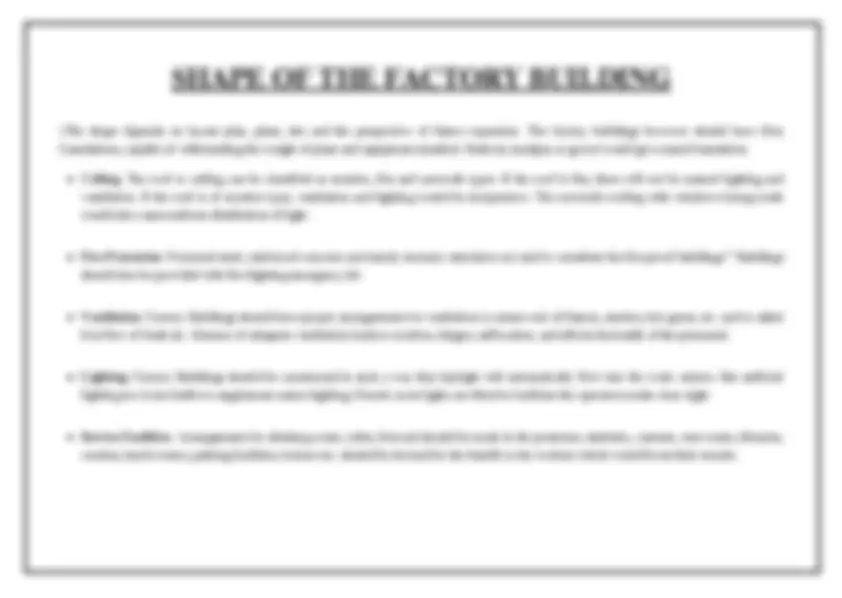
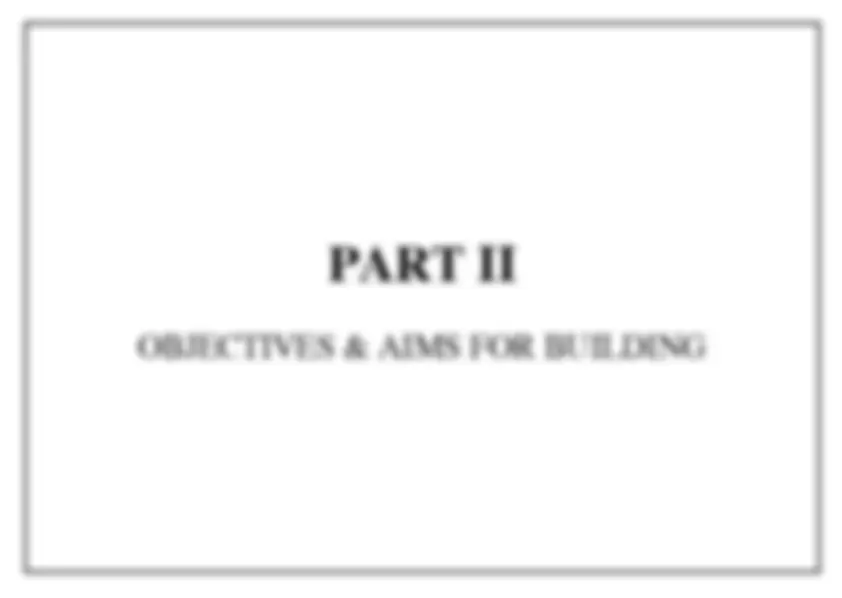
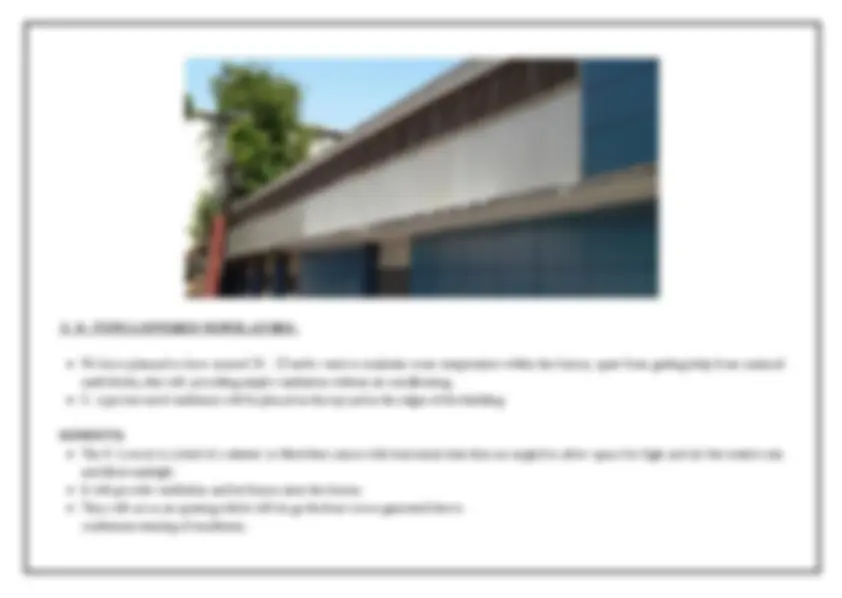
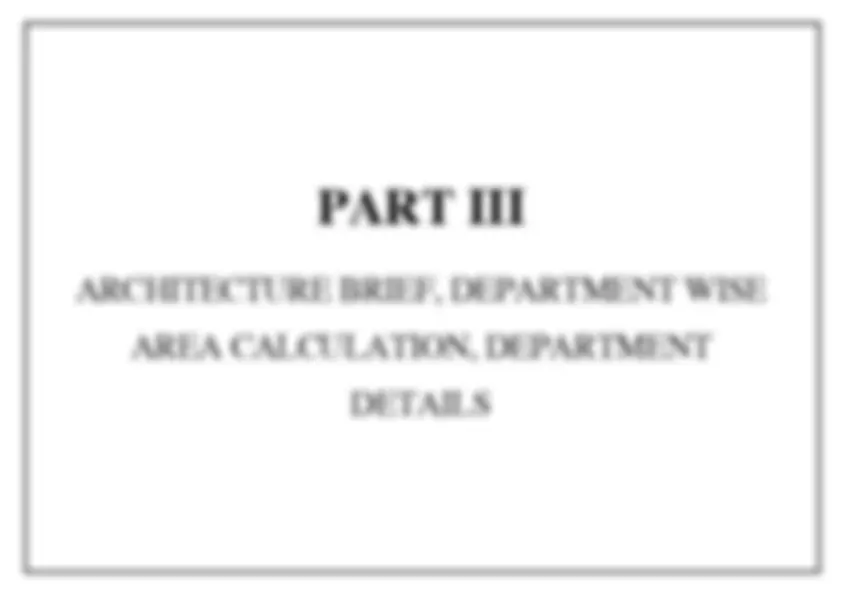
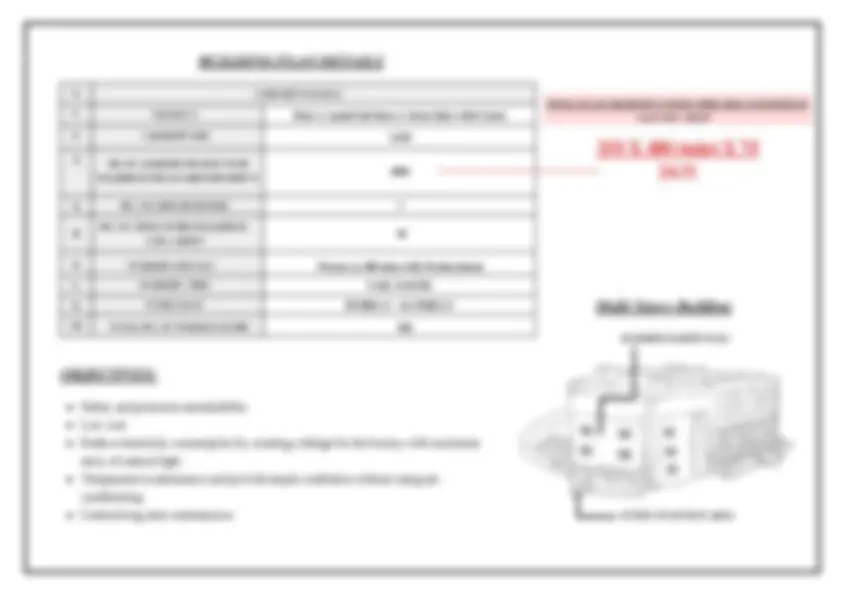
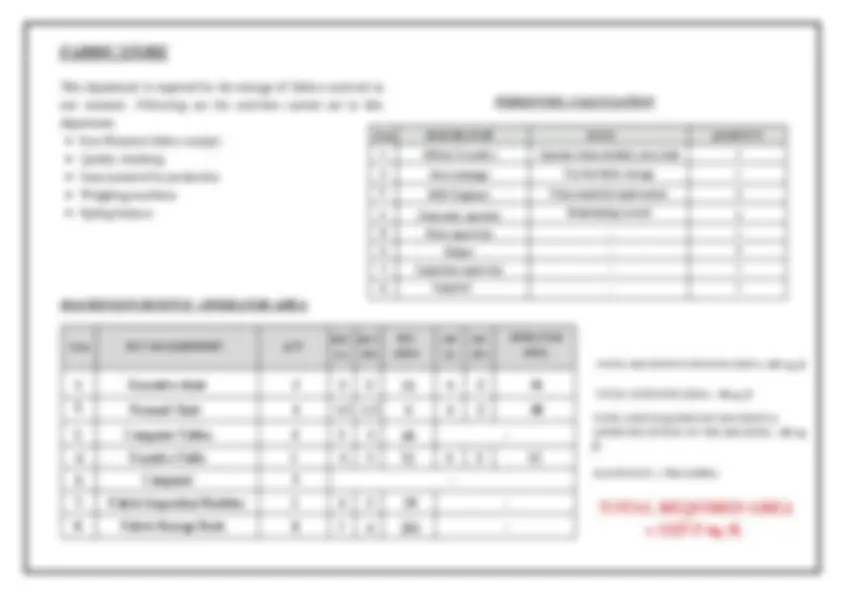
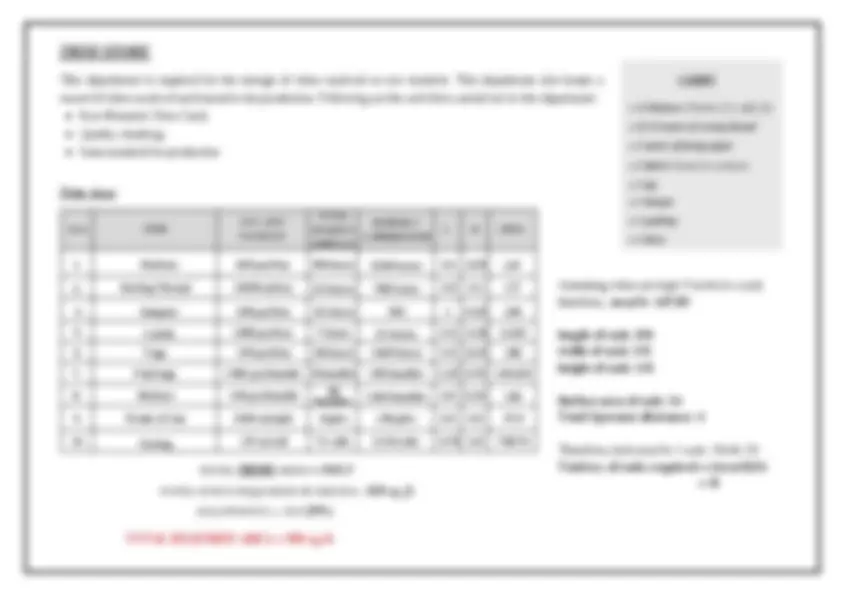
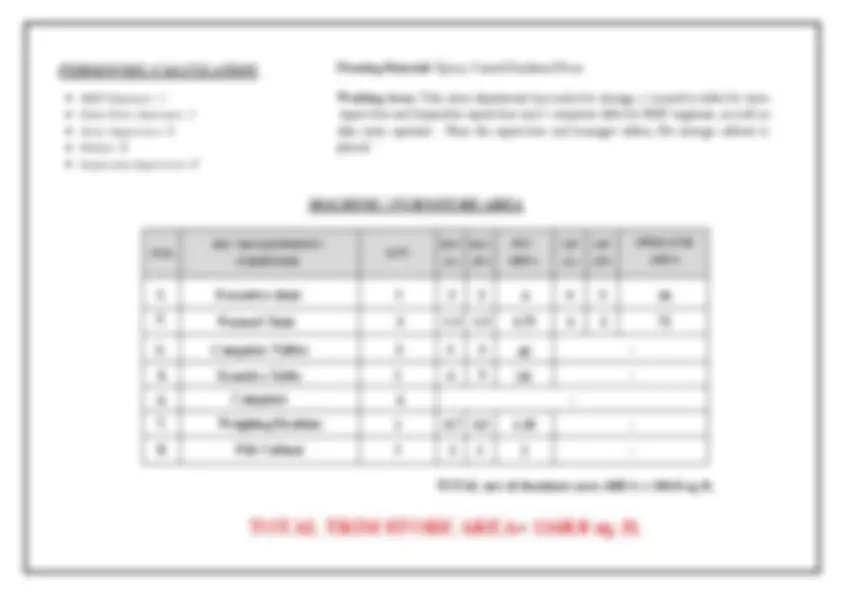
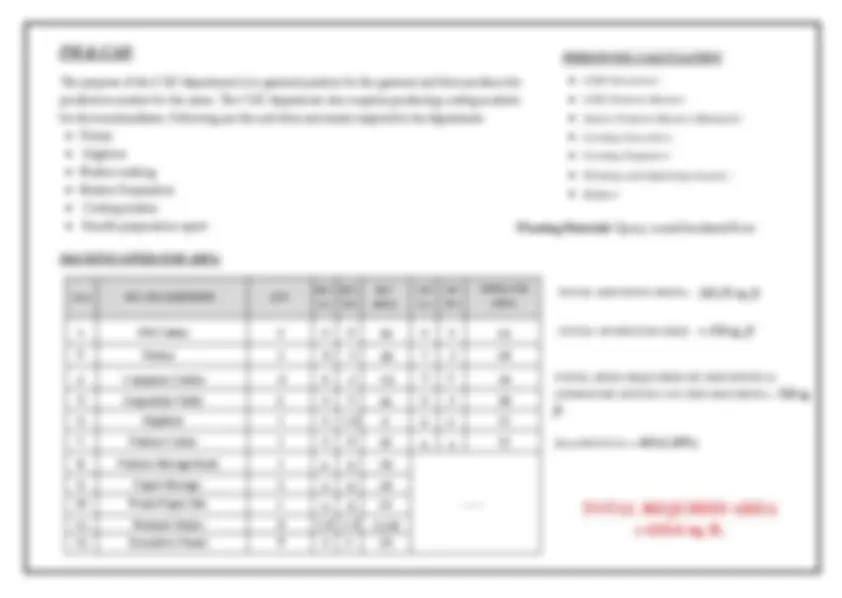
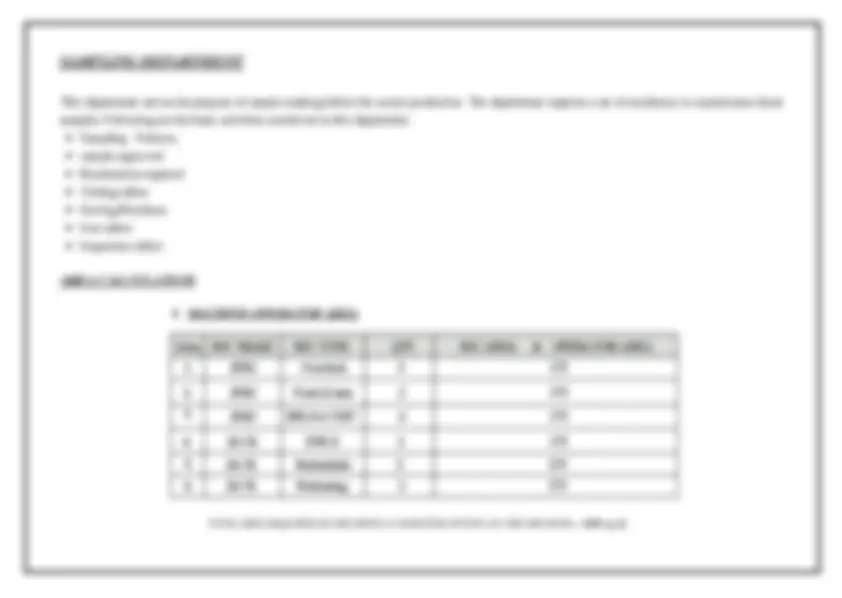
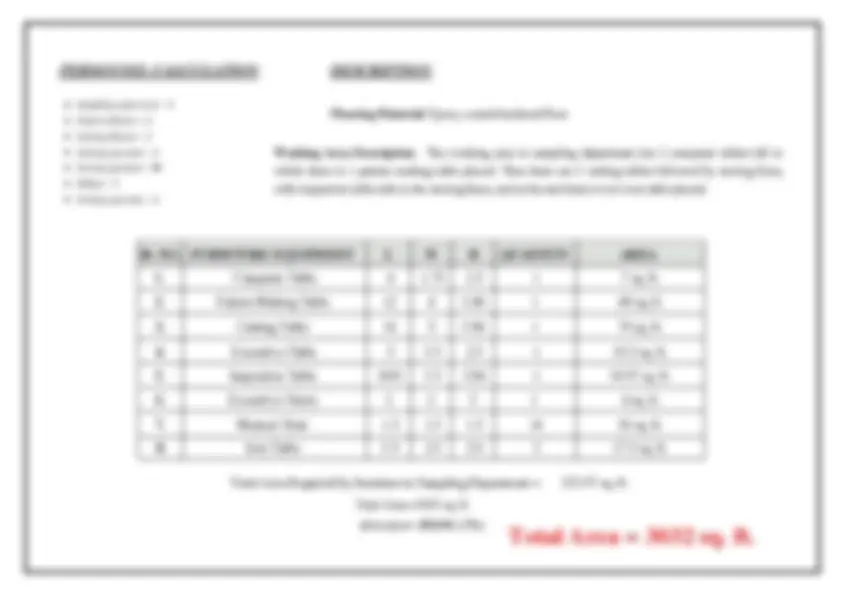
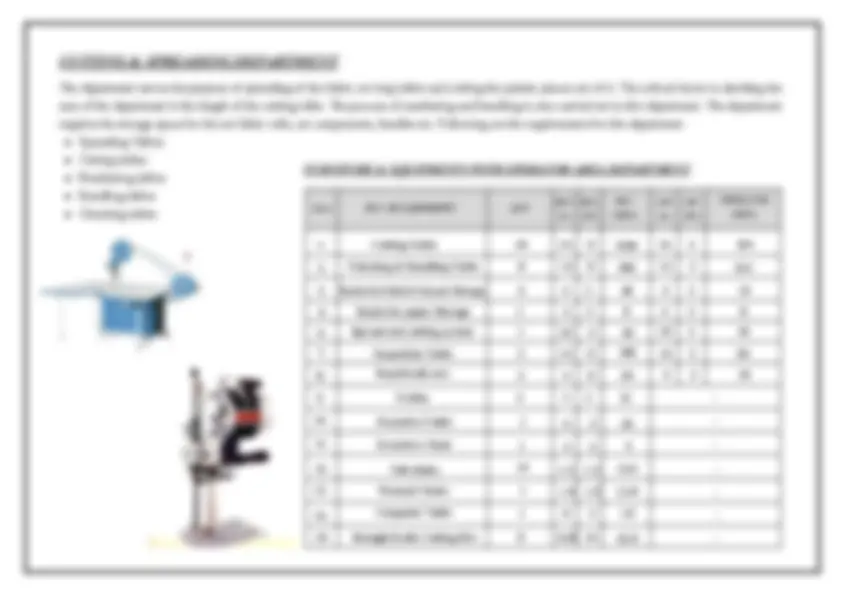
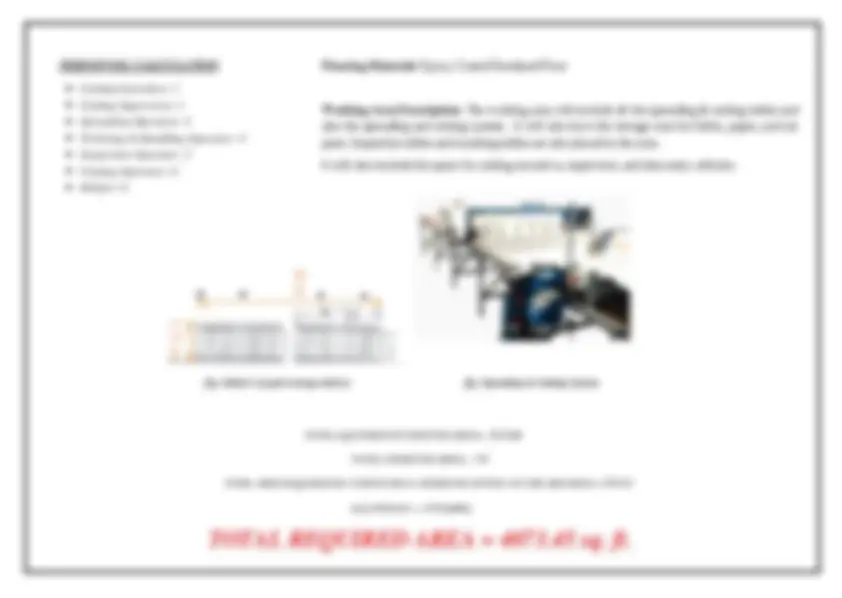
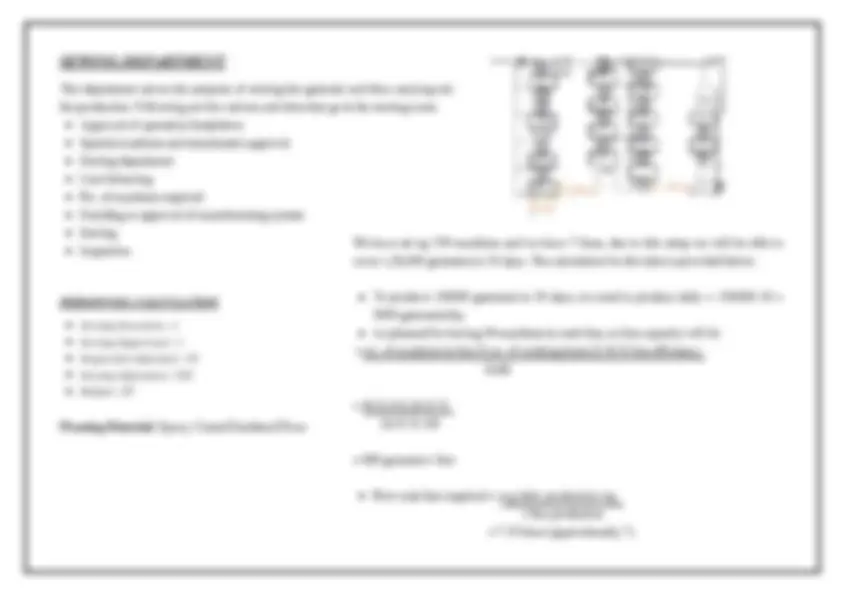
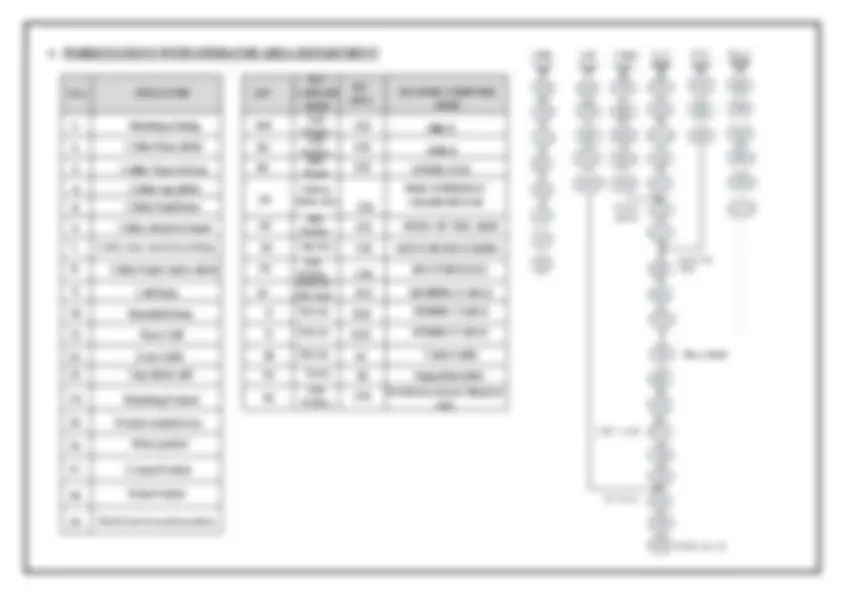
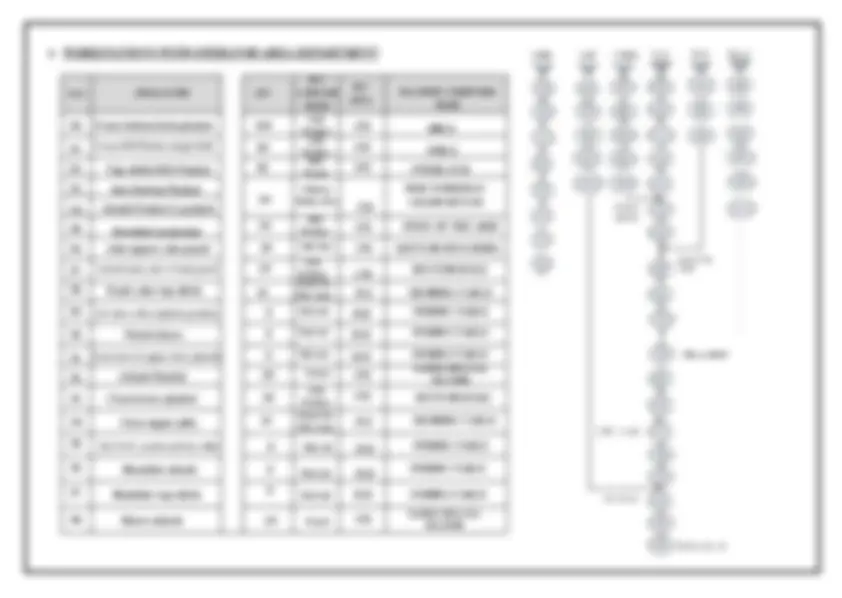
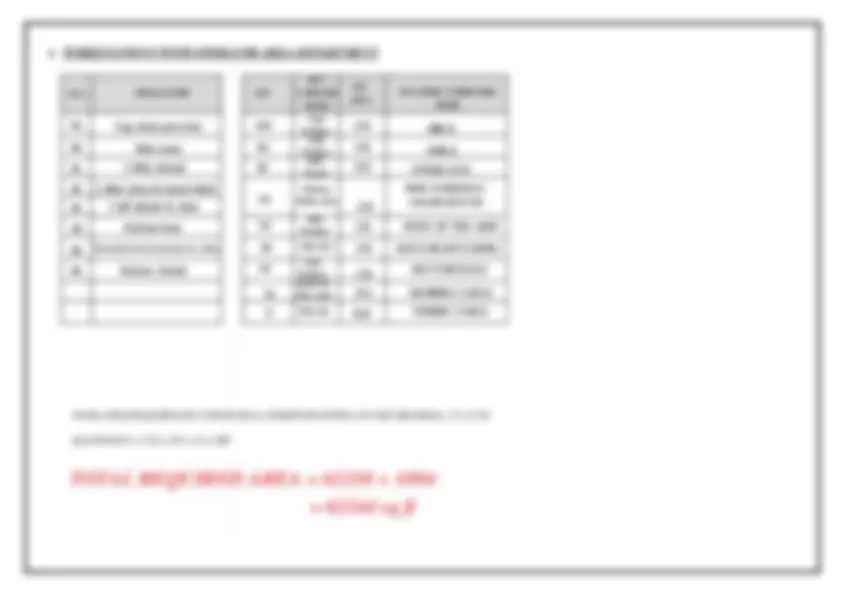
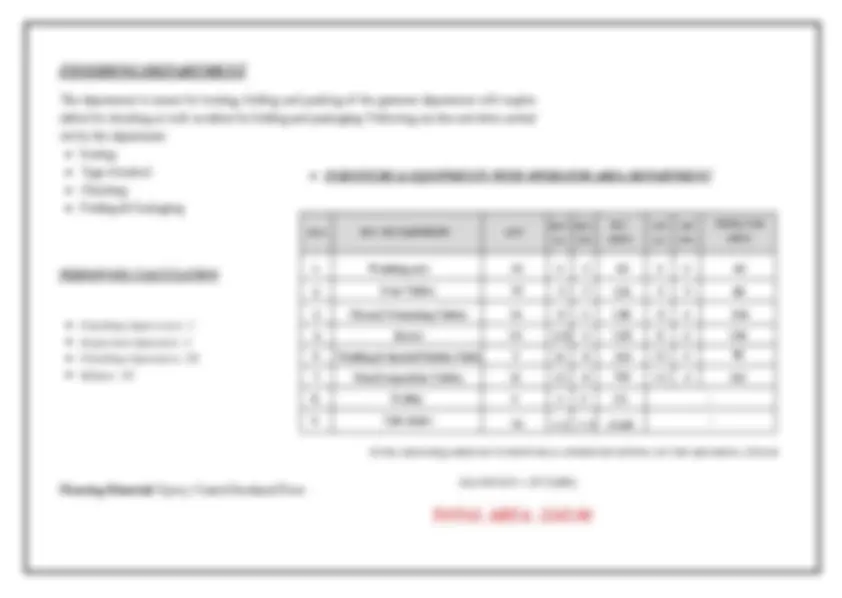
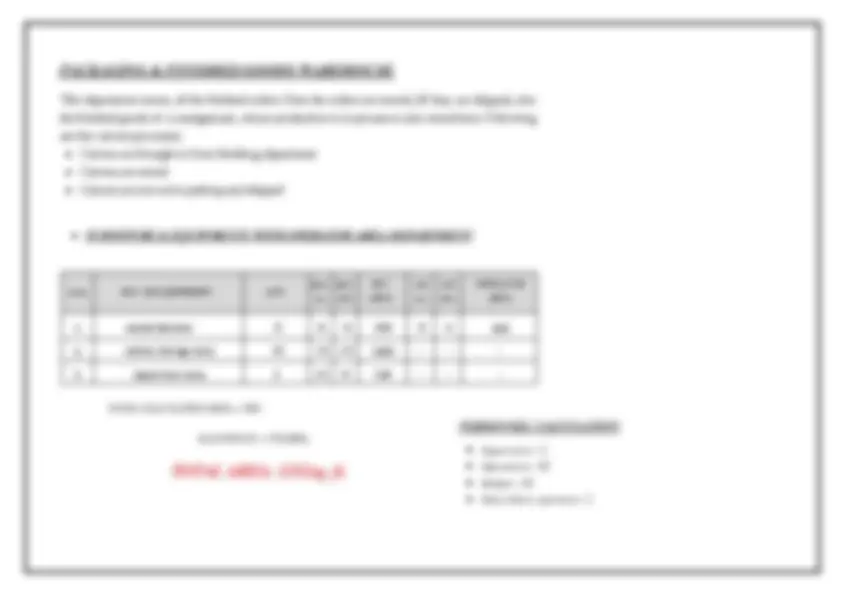
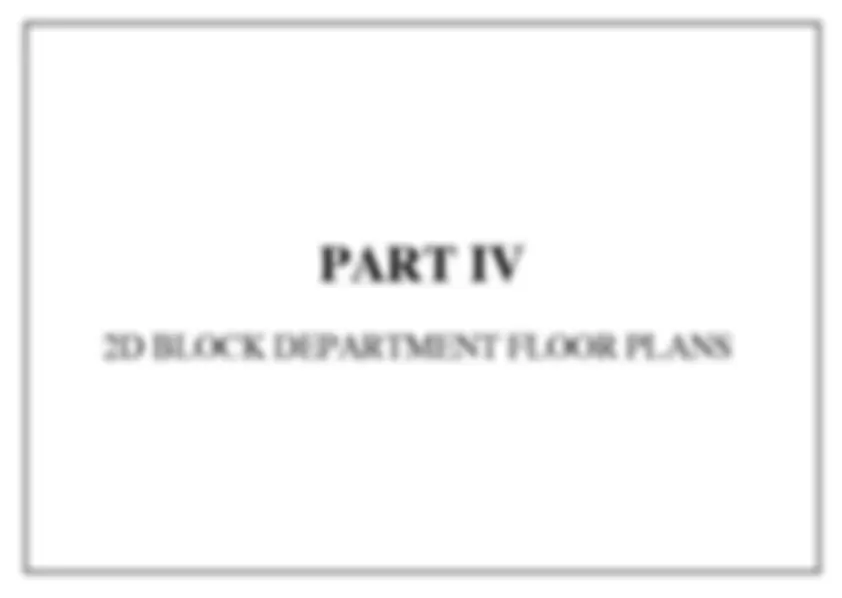
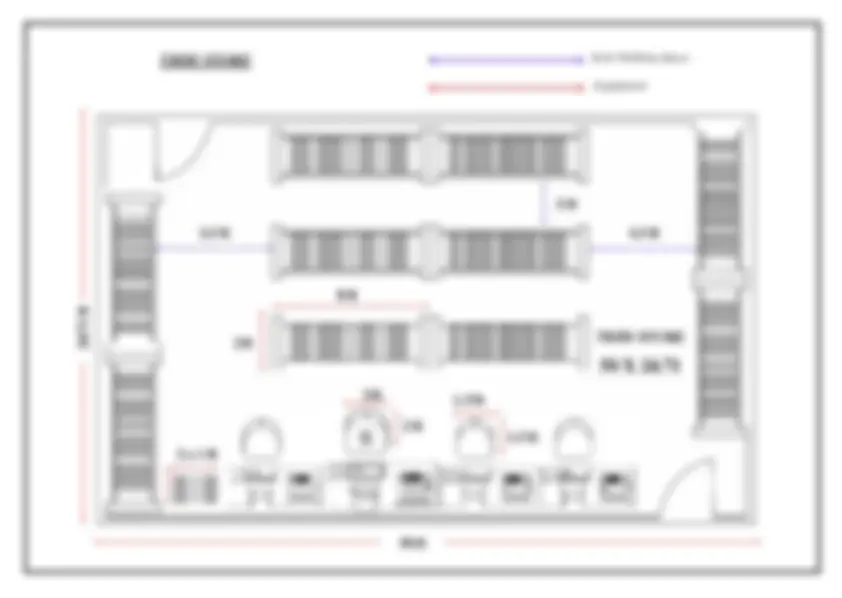
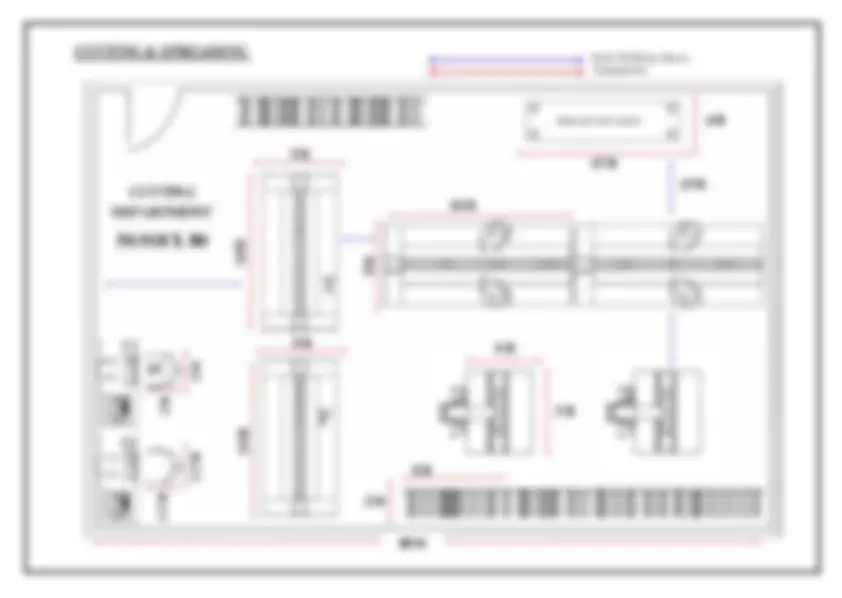
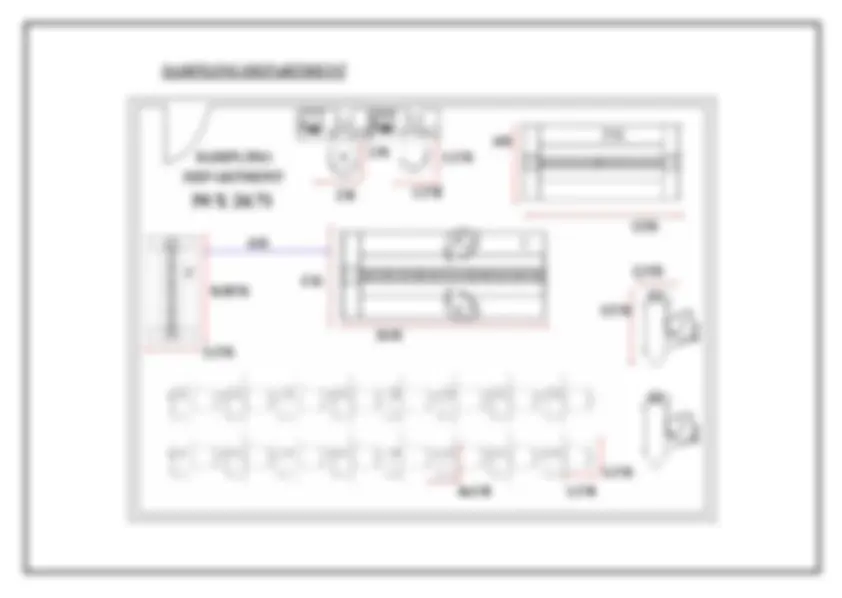
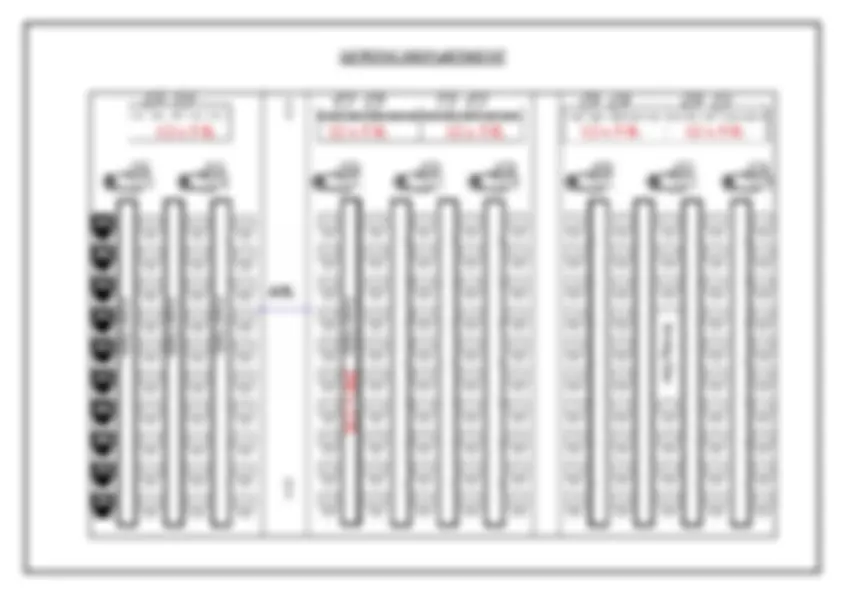
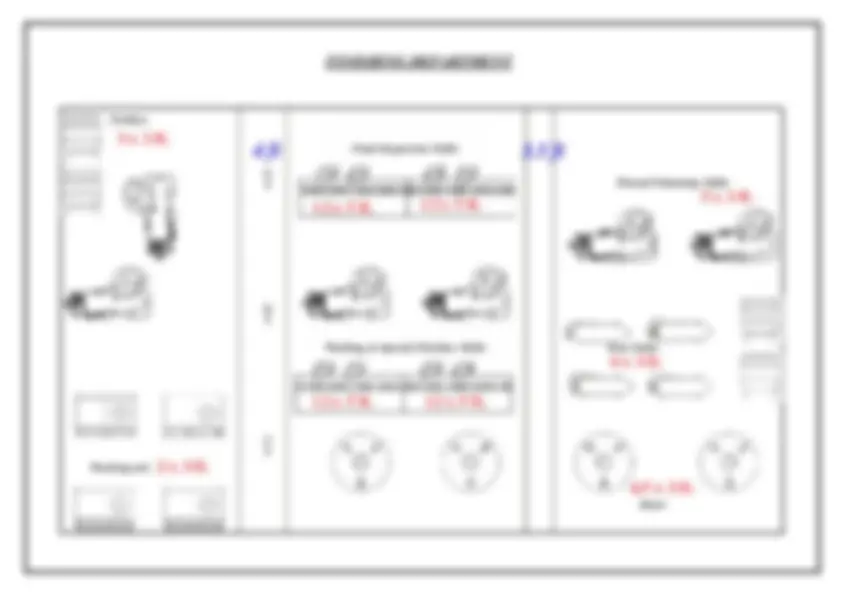
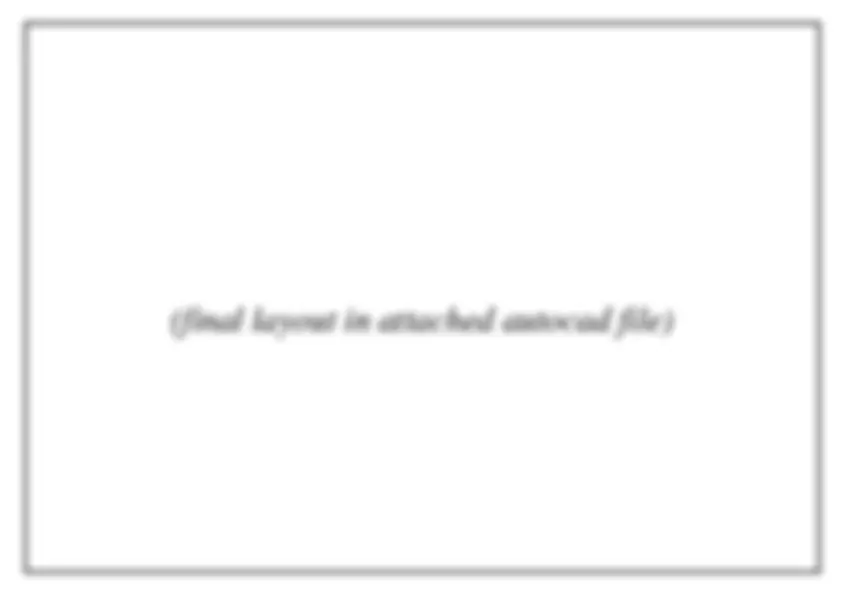
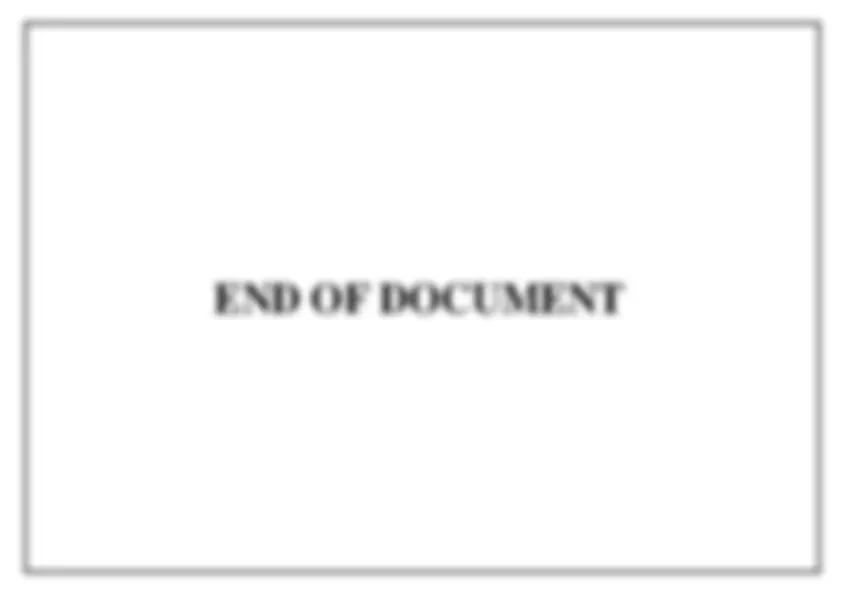
Study with the several resources on Docsity
Earn points by helping other students or get them with a premium plan
Prepare for your exams
Study with the several resources on Docsity
Earn points to download
Earn points by helping other students or get them with a premium plan
Community
Ask the community for help and clear up your study doubts
Discover the best universities in your country according to Docsity users
Free resources
Download our free guides on studying techniques, anxiety management strategies, and thesis advice from Docsity tutors
The document is a detailed work of creating Plant layout design, along with area calculations of major departments, of an apparel manufacturing factory.
Typology: Slides
1 / 39
This page cannot be seen from the preview
Don't miss anything!
On special offer
PLANT LAYOUT
This is a single-storey structure with this difference, that the roof truss is surrounded by a monitor. The building is designed to give maximum overhead space for a given floor area. The overhead space may be used to operate a crane and other overhead facilities. The monitor offers good natural ventilation, and the side walls, built with glass, act as windows for natural lighting. Uses: Buildings for steel mills and foundries are often of the monitor or bar type; they enable the management to take advantage of natural ventilation and illumination coming from high roofs and center openings, which provide ample room for crane operations.
Some manufacturing processes require a particular type of building. The aircraft industry, for example, requires building with wide spans, which may range from a width of 300ft to 400ft. The building for a saw mill is constructed without side walls so that the flow of wind may be steady and saw dust does not accumulate inside the plant. Allowing the dust to accumulate inside the building is like welcoming a fire at the doorstep because saw dust catches fire very quickly and easily. These buildings are constructed for a specific purpose and are, therefore inflexible. Obsolescence in this type is high because of rapid changes in technology.
SINGLE STOREY BUILDING
ADVANTAGES DISADVANTAGES
Requires lighter foundations with less variation. Maintenance and the changes in equipments can be carried out easily. Heavy machines can be installed easily with quickness in construction. As there is no requirement of lifts or stairs it saves the floor spacing and cost of life operation. Construction cost per square foot is lower. Shows good efficiency in routine and material handling.
Require more land compared to that of multi- storage building. The plant layout is not compact The production space is generally occupied by offices and stores. Gravity can not be employed in material handling and more roof spaces are required.
MULTI STOREY BUILDING
ADVANTAGES DISADVANTAGES
More compact layout. Less roof repairs. Less cost of land in rural areas and gravity can be employed. Material handling distance I reduced considerably.
Requires high cost for foundation Floor expansion is not possible and natural illumination in center is poor. Space is wasted in construction of staircase or lifts. Handling of bulky materials is expensive.
TYPES OF FACTORY BUILDING CONSTRUCTION
(a) Wood Frame Construction: Such a building generally is not more than two storeys in height. Floors take lighter loads only. It is highly flammable construction, therefore it is used where fire hazards are rare and are not a serious drawback.
(b) Brick Construction: Side walls and interior fire walls (i.e., the walls which separate sections of the building to prevent fire spread) are made up of bricks.
(c) Slow burning mill Construction: It is plank-on-timber building with load bearing brick siding. Owing to heavy wood members being used, the construction is fire- resistant because the members, i.e., pillars, etc., are slow to burn. Such a factory building can take moderate floor loads but involves high maintenance costs, high noise and vibration transmission and light and ventilation restricted by the load bearing walls.
(d) Steel Frame Construction: It makes use of steel girders, columns and trusses. Space between the columns is filled by bricks, etc
(e) Reinforced Concrete Construction: This is fire-proof construction. All structural members are made up of reinforced concrete, masonry or steel encased in concrete. It is a very good type of construction for multi-storey buildings.
(f) Precast Concrete Construction: It is very speedy and economical. Sections are precast either at vendor’s end or on the ground itself, cured (i.e., set) and then tilted vertically up by cranes to form the wall, roof and floor, etc.
Safety and promotes sustainability Low cost Reduce electricity consumption by creating a design for the factory with maximum entry of natural light Temperature maintenance and provide ample ventilation without using air- conditioning Limited long term maintenance
The garment industry functions on pure economical decisions. So, we want the project to be low cost. Along with being low-cost, it however has to engage and represent its world class infra- structures. The brief of our factory is generally based on work flow. We have planned to have a stream-lined work flow and processes. Lastly, the factory would employ 500 workers, special importance is to be given to them and their working conditions. All of which we hope would help in the efficiency of the factory.
MAJOR REQUIREMENTS :
OBJECTIVE OF OUR PLAN
We have planned to have around 20 - 25 turbo vents to maintain room temperature within the factory apart from getting help from rammed earth bricks, this will providing ample ventilation without air conditioning. S - type louvered ventilators will be placed on the top and ar the edges of the building
The S- Louver is a kind of a shutter or blind that comes with horizontal slats that are angled to allow space for light and air but restrict rain and direct sunlight It will provide ventilation and let breeze enter the factory They will act as an opening which will let go the heat waves generated due to
continuous running of machinery.
INDUSTRIAL SHED
This part of the site contains all the major departments, the production floor, finished goods warehouse, fabric store, trim store, etc. The multistorey building has a direct access to the industrial shed, through 6 ft and 3ft. aisles.
ENTRY TO FINISHED GOODS WAREHOUSE
SOLID POLYCARBONATE SHEETS BETWEEN METALLIC PANELS
SEWING
FINISHING
PACKING
FINISHED GOODS WAREHOUSE
SAMPLING & CAD
CUTTING & SPREADING
FABRIC HOUSE
ENTRANCE TO INDUSTRIAL SHED
PROCESS CHARTS
TRIM STORE
Raw Material (Trim Card) Quality checking Issue material for production
This department is required for the storage of trims received as raw material. This department also keeps a record of trims received and issued to the production. Following are the activities carried out in this department:
1 SHIRT
= 11 Buttons: Placket [7], cuffs [4] = 52.51 meter of sewing thread = 2 meter of fusing paper = 2 labels: brand & washcare = 1 tag = 1 hanger = 1 polybag sl no. ITEM AVG. QTY/ PACKAGE AREA
21 boxes
1440 bundles
MONTHLY CONSUMPTION
Buttons Sewing Thread
Labels
600 pcs/box 10000 m/box 150 pcs/box 1500 pcs/box 100 pcs/box
2640 boxes 780 boxes 960
247 117
Tags
Polybags 1000 pcs/bundle 100 pcs/bundle
TOTAL REQ/DAY (4800/DAY)
L
150 bundles
W
Stickers 1000 sets/pkt
Hooks & bar Fusing^ 137 m/roll
1440 boxes
150 pkts 2130 rolls
1 0.
0.5 0. 1.25 0. 0.5 0. 0.5 0. 0.75 0.
240
180
180
88 boxes 26 boxes 32 boxes 7 boxes 48 boxes 5 bundles 48 bundles 5 pkts 71 rolls
Assuming, trims are kept 3 levels in a rack therefore, area/3= 647.
length of rack: 8 ft width of rack: 2 ft height of rack: 6 ft
Surface area of rack: 16 Total Operator allowance: 4
Therefore, total area for 1 rack: 16+4= 20 Total no. of racks required = (Area/3)/ = 41
= 1.06 m
TOTAL SPACE REQUIRED BY RACKS= 820 sq. ft. ALLOWANCE = 164 (20%)
TOTAL REQUIRED AREA = 984 sq. ft.
PERSONNEL CALCULATION
MRP Engineer: 1 Data Entry Operator: 1 Store Supervisor: 1 Helper: 2 Inspection Supervisor: 1
MACHINE / FURNITURE AREA
sl no. M/C OR EQUIPMENT / FURNITURE QTY M/C AREA
OPERATOR AREA
M/C (L)
M/C (W)
O/P (W)
O/P (L)
TOTAL TRIM STORE AREA= 1168.8 sq. ft.
Flooring Material: Epoxy Coated Hardened Floor
Working Area: Trim store department has racks for storage, 1 executive table for store supervisor and inspection supervisor and 1 computer table for MRP engineer, as well as data entry operator. Near the supervisor and manager tables, file storage cabinet is placed.