
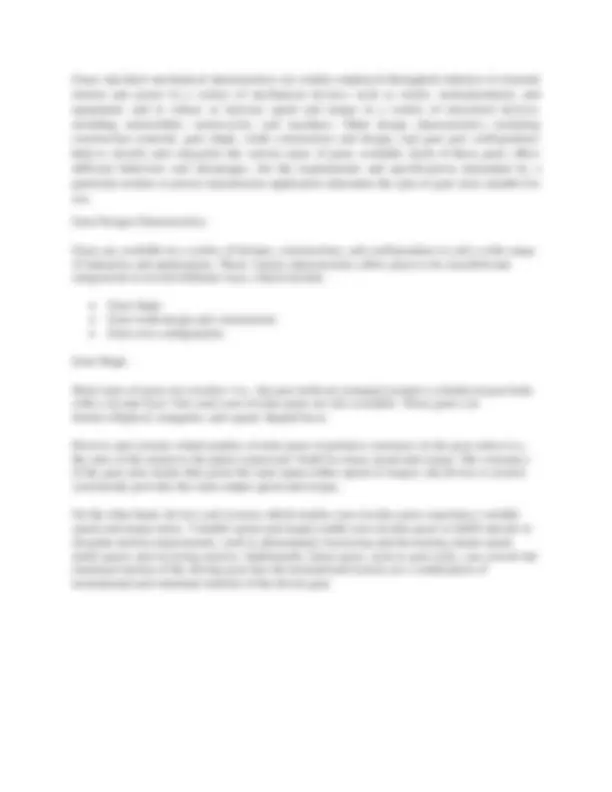
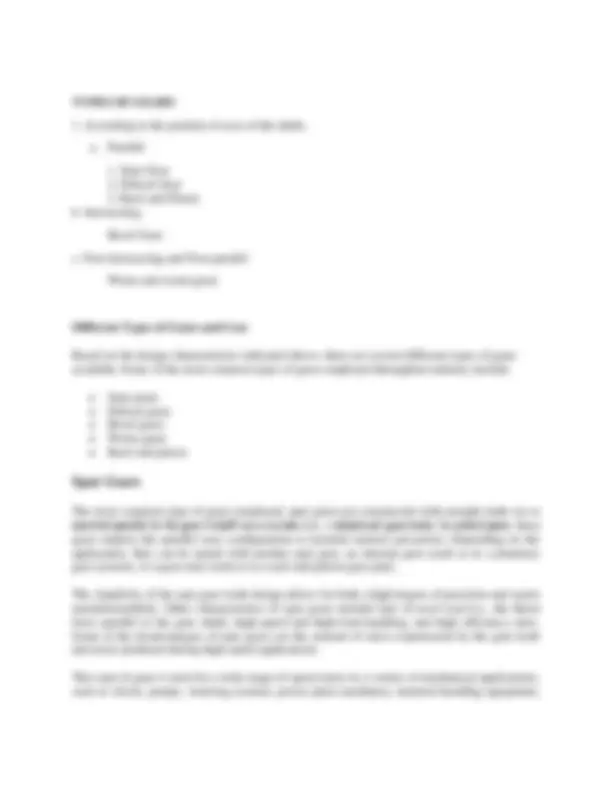
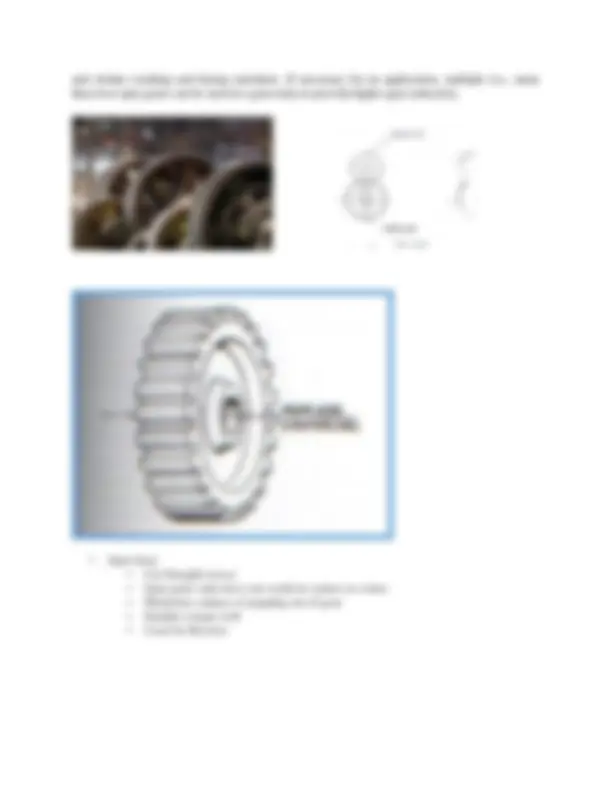
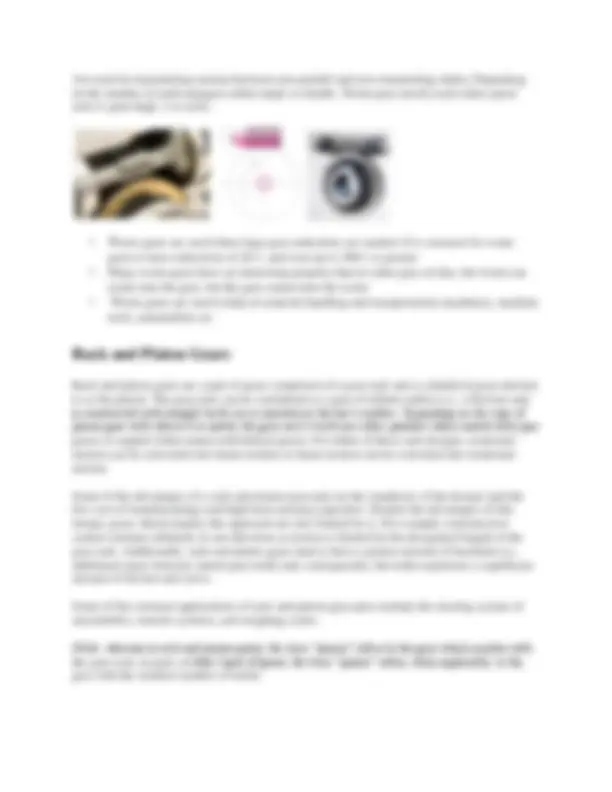
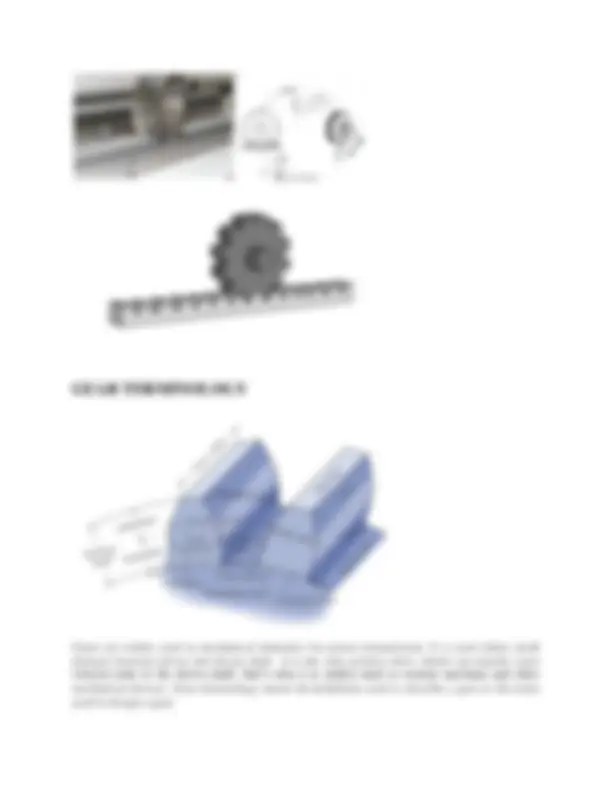
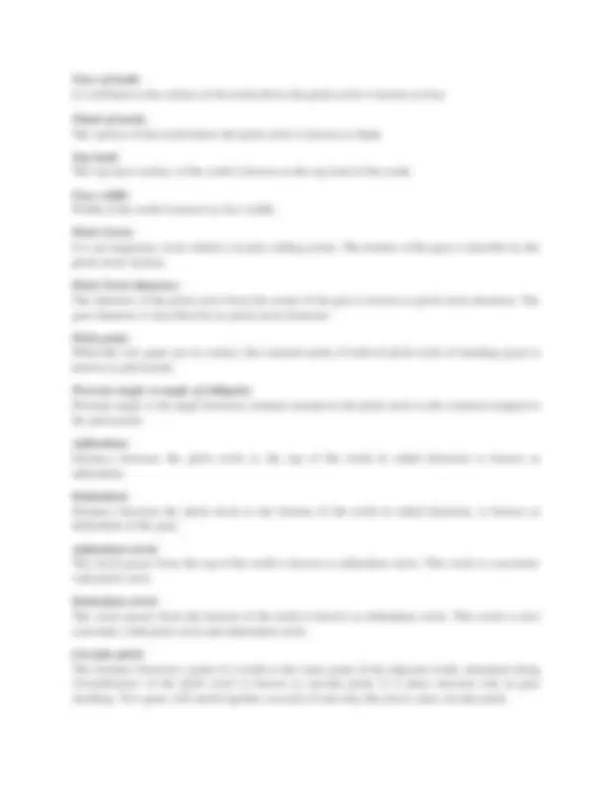
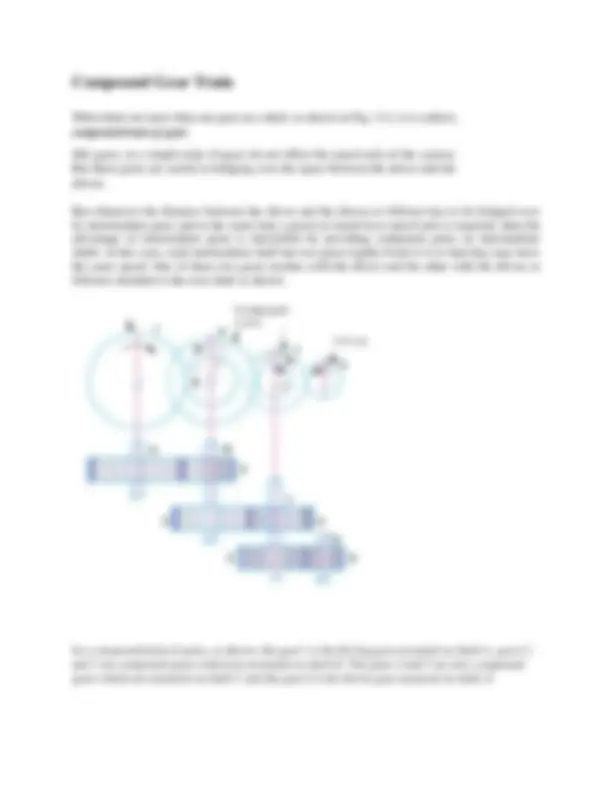
Study with the several resources on Docsity
Earn points by helping other students or get them with a premium plan
Prepare for your exams
Study with the several resources on Docsity
Earn points to download
Earn points by helping other students or get them with a premium plan
Community
Ask the community for help and clear up your study doubts
Discover the best universities in your country according to Docsity users
Free resources
Download our free guides on studying techniques, anxiety management strategies, and thesis advice from Docsity tutors
This pdf will help you out in understanding the concept of gears, drives and bearings with neat diagram. I hope that you will like it
Typology: Lecture notes
1 / 13
This page cannot be seen from the preview
Don't miss anything!
Syllabus:
Rotating elements which possess mechanical energy has to be utilized at required place by transmitting.
The system that is used to transmit power from one mechanical element to another mechanical element
Gears are toothed, mechanical transmission elements used to transfer motion and power between machine components, and in this article, we discuss the different types of gears available and how gears work. Operating in mated pairs, gears mesh their teeth with the teeth of another corresponding gear or toothed component which prevents slippage during the transmission process. Each gear or toothed component is attached to a machine shaft or base component, therefore when the driving gear (i.e., the gear that provides the initial rotational input) rotates along with its shaft component, the driven gear (i.e., the gear or toothed component which is impacted by the driving gear and exhibits the final output) rotates or translates its shaft component. Depending on the design and construction of the gear pair, the transference of motion between the driving shaft and the driven shaft can result in a change of the direction of rotation or movement. Additionally, if the gears are not of equal sizes, the machine or system experiences a mechanical advantage which allows for a change in the output speed and torque (i.e., the force which causes an object to rotate).
a. Parallel
Bevel Gear
c. Non-intersecting and Non-parallel
Worm and worm gears
Different Types of Gears and Uses
Based on the design characteristics indicated above, there are several different types of gears available. Some of the more common types of gears employed throughout industry include:
Spur gears Helical gears Bevel gears Worm gears Rack and pinion
The most common type of gears employed, spur gears are constructed with straight teeth cut or inserted parallel to the gear’s shaft on a circular (i.e., cylindrical) gear body. In mated pairs, these gears employ the parallel axes configuration to transmit motion and power. Depending on the application, they can be mated with another spur gear, an internal gear (such as in a planetary gear system), or a gear rack (such as in a rack and pinion gear pair).
The simplicity of the spur gear tooth design allows for both a high degree of precision and easier manufacturability. Other characteristics of spur gears include lack of axial load (i.e., the thrust force parallel to the gear shaft), high-speed and high-load handling, and high efficiency rates. Some of the disadvantages of spur gears are the amount of stress experienced by the gear teeth and noise produced during high-speed applications.
This type of gear is used for a wide range of speed ratios in a variety of mechanical applications, such as clocks, pumps, watering systems, power plant machinery, material handling equipment,
and clothes washing and drying machines. If necessary for an application, multiple (i.e., more than two) spur gears can be used in a gear train to provide higher gear reduction.
Bevel Gears are used to transmit rotary motion between intersecting shafts
Bevel gears are cone-shaped gears with teeth placed along the conical surface. These gears are used to transmit motion and power between intersecting shafts in applications which require changes to the axis of rotation. Typically, bevel gears are employed for shaft configurations placed at 90-degree angles, but configurations with lesser or greater angles are also manageable.
Teeth are formed on conical surfaces, the teeth could be straight or spiral.
Worm gear pairs are comprised of a worm wheel—typically a cylindrical gear—paired with a worm—i.e., a screw-shaped gear. These gears are used to transmit motion and power between non-parallel, non-intersecting shafts. They offer large gear ratios and capabilities for substantial speed reduction while maintaining quiet and smooth operation.
One distinction of worm gear pairs is that the worm can turn the worm wheel, but, depending on the angle of the worm, the worm wheel may not be able to turn the worm. This characteristic is employed in equipment requiring self-locking mechanisms. Some of the disadvantages of worm gears are the low transmission efficiency and the amount of friction generated between the worm wheel and worm gear which necessitates continuous lubrication.
Are used for transmitting motion between non parallel and non-transmitting shafts, Depending on the number of teeth engaged called single or double. Worm gear mostly used when speed ratio is quiet high, 3 or more.
Rack and pinion gears are a pair of gears comprised of a gear rack and a cylindrical gear referred to as the pinion. The gear rack can be considered as a gear of infinite radius (i.e., a flat bar) and is constructed with straight teeth cut or inserted on the bar’s surface. Depending on the type of pinion gear with which it is mated, the gear rack’s teeth are either parallel (when mated with spur gears) or angled (when mated with helical gears). For either of these rack designs, rotational motion can be converted into linear motion or linear motion can be converted into rotational motion.
Some of the advantages of a rack and pinion gear pair are the simplicity of the design (and the low cost of manufacturing) and high load carrying capacities. Despite the advantages of this design, gears which employ this approach are also limited by it. For example, transmission cannot continue infinitely in one direction as motion is limited by the designated length of the gear rack. Additionally, rack and pinion gears tend to have a greater amount of backlash (i.e., additional space between mated gear teeth) and, consequently, the teeth experience a significant amount of friction and stress.
Some of the common applications of rack and pinion gear pairs include the steering system of automobiles, transfer systems, and weighing scales.
(Note: whereas in rack and pinion gears, the term ―pinion‖ refers to the gear which meshes with the gear rack, in pairs of other types of gears, the term ―pinion‖ refers, when applicable, to the gear with the smallest number of teeth)
Face of tooth: It is defined as the surface of the tooth above the pitch circle is known as face.
Flank of tooth: The surface of the tooth below the pitch circle is known as flank.
Top land: The top most surface of the tooth is known as the top land of the tooth.
Face width: Width of the tooth is known as face width.
Pitch Circle: It is an imaginary circle which is in pure rolling action. The motion of the gear is describe by the pitch circle motion.
Pitch Circle diameter: The diameter of the pitch circle from the center of the gear is known as pitch circle diameter. The gear diameter is described by its pitch circle diameter.
Pitch point: When the two gears are in contact, the common point of both of pitch circle of meshing gears is known as pitch point.
Pressure angle or angle of obliquity: Pressure angle is the angle between common normal to the pitch circle to the common tangent to the pitch point.
Addendum: Distance between the pitch circle to the top of the tooth in radial direction is known as addendum.
Dedendum: Distance between the pitch circle to the bottom of the tooth in radial direction, is known as dedendum of the gear.
Addendum circle: The circle passes from the top of the tooth is known as addendum circle. This circle is concentric with pitch circle.
Dedendum circle: The circle passes from the bottom of the tooth is known as dedendum circle. This circle is also concentric with pitch circle and addendum circle.
Circular pitch: The distance between a point of a tooth to the same point of the adjacent tooth, measured along circumference of the pitch circle is known as circular pitch. It is plays measure role in gear meshing. Two gears will mesh together correctly if and only they have same circular pitch.
Diametrical pitch: The ratio of the number of teeth to the diameter of pitch circle in millimeter is known as diametrical pitch.
Module: The ratio of the pitch circle diameter in millimeters to the total number of teeth is known as module. It is reciprocal of the diametrical pitch.
Clearance: When two gears are in meshing condition, the radial distance from top of a tooth of one gear to the bottom of the tooth of another gear is known as clearance. The circle passes from the top of the tooth in meshing condition is known as clearance angle.
Total depth: The sum of the addendum and dedendum of a gear is known as total depth. It is the distance between addendum circle to the dedendum circle measure along radial direction.
Working depth: The distance between addendum circle to the clearance circle measured along radial direction is known as working depth of the gear.
Tooth thickness: Distance of the tooth measured along the circumference of the pitch circle is known as tooth thickness.
Tooth space: Distance between the two adjacent tooth measured along the circumference of the pitch circle is known as the tooth space.
Backlash: It is the difference between the tooth thickness and the tooth space. It prevents jamming of the gears in meshing condition.
Profile: It is the curved formed by the face and flank is known as profile of the tooth. Gear tooth are generally have cycloidal or involute profile.
When there are more than one gear on a shaft, as shown in Fig. 13.2, it is called a compound train of gear****.
Idle gears, in a simple train of gears do not effect the speed ratio of the system. But these gears are useful in bridging over the space between the driver and the driven.
But whenever the distance between the driver and the driven or follower has to be bridged over by intermediate gears and at the same time a great (or much less) speed ratio is required, then the advantage of intermediate gears is intensified by providing compound gears on intermediate shafts. In this case, each intermediate shaft has two gears rigidly fixed to it so that they may have the same speed. One of these two gears meshes with the driver and the other with the driven or follower attached to the next shaft as shown.
In a compound train of gears, as shown, the gear 1 is the driving gear mounted on shaft A , gears 2 and 3 are compound gears which are mounted on shaft B. The gears 4 and 5 are also compound gears which are mounted on shaft C and the gear 6 is the driven gear mounted on shaft D