
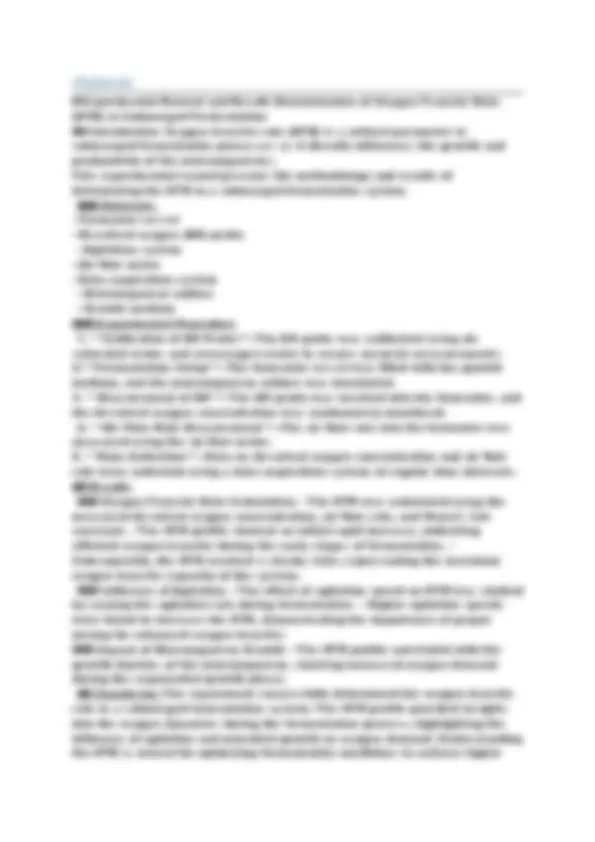
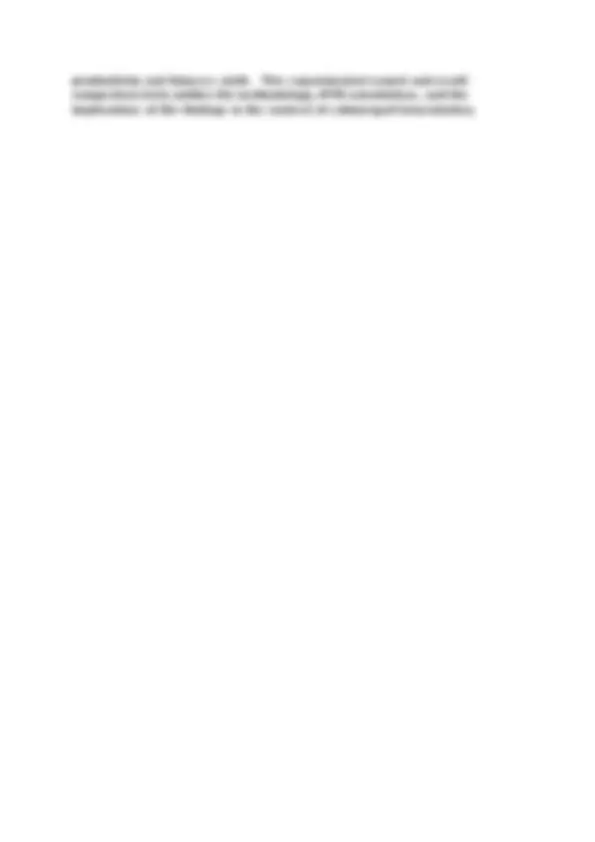
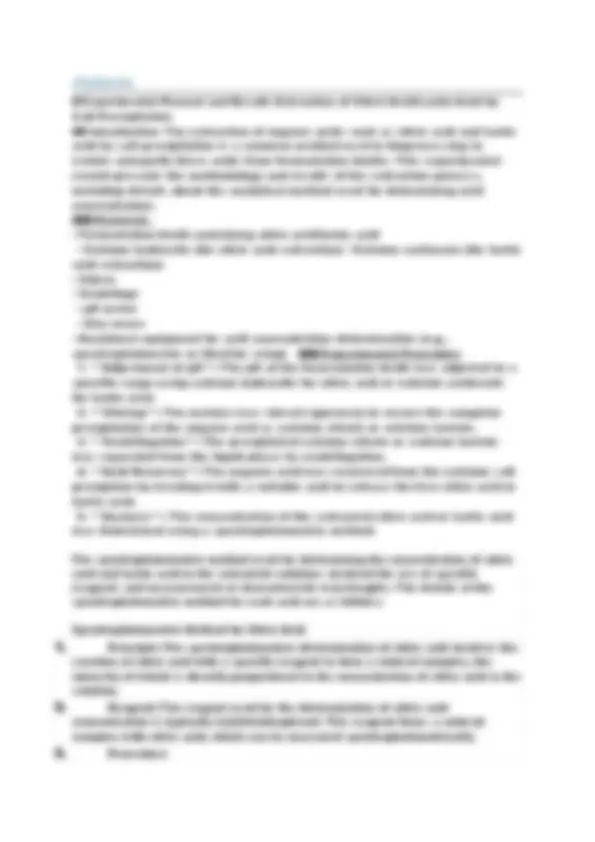
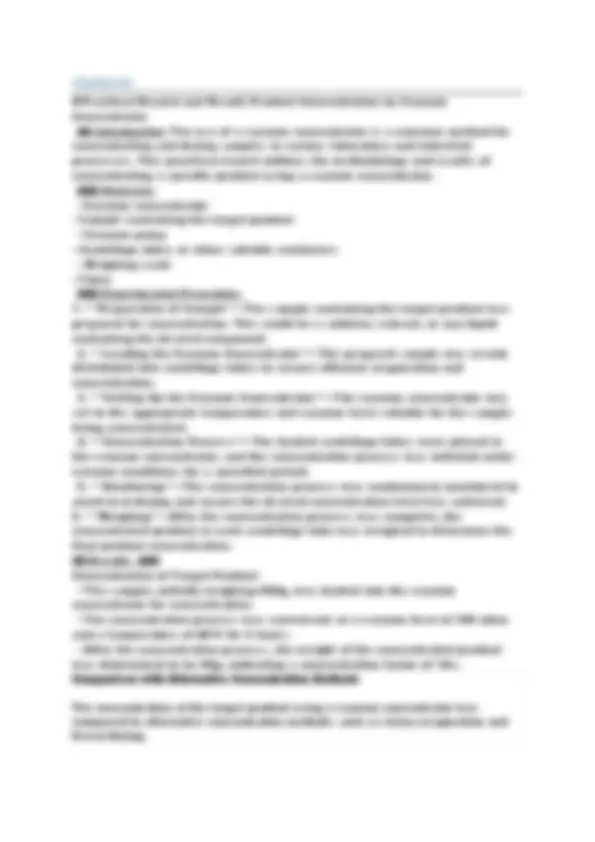
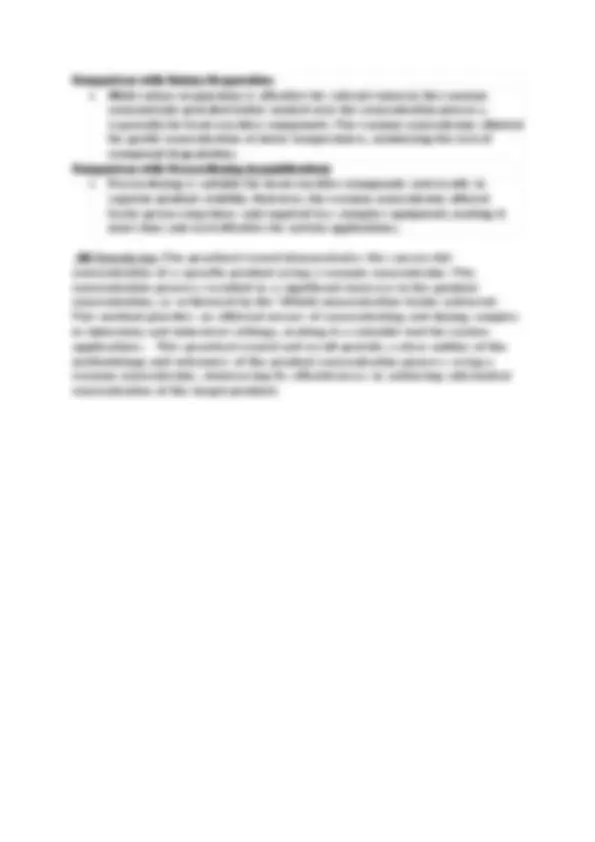
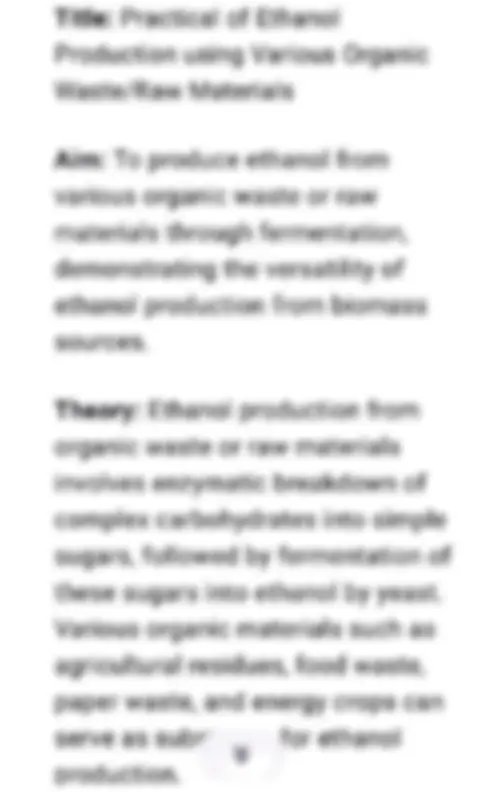
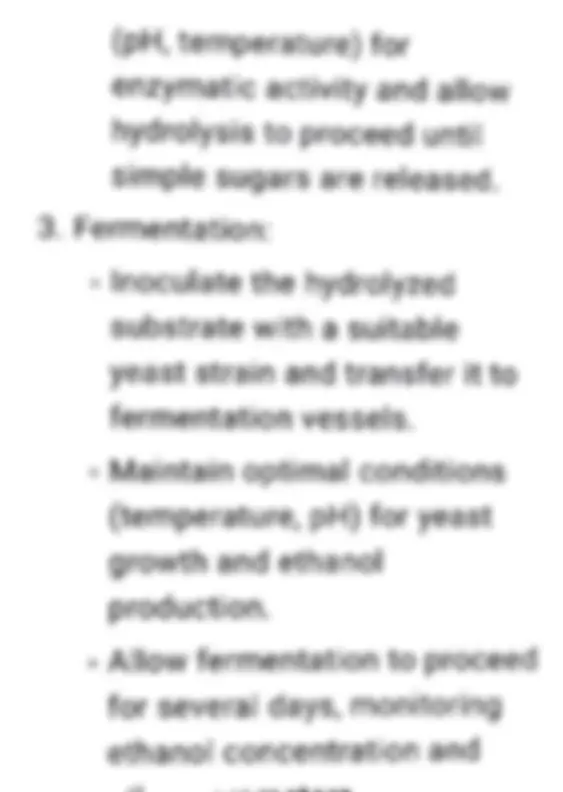
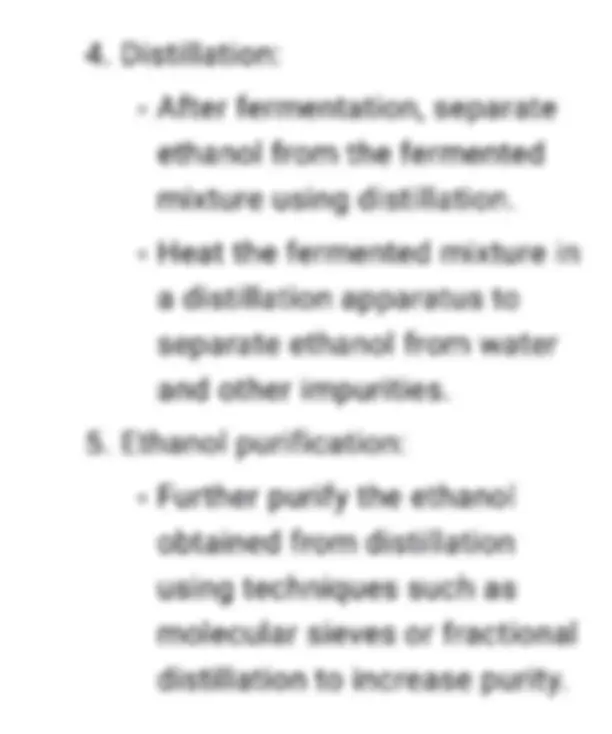
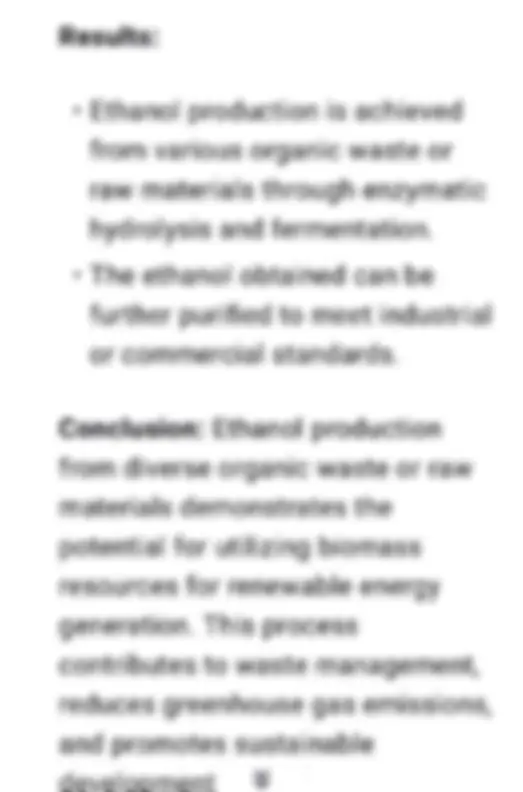
Study with the several resources on Docsity
Earn points by helping other students or get them with a premium plan
Prepare for your exams
Study with the several resources on Docsity
Earn points to download
Earn points by helping other students or get them with a premium plan
Community
Ask the community for help and clear up your study doubts
Discover the best universities in your country according to Docsity users
Free resources
Download our free guides on studying techniques, anxiety management strategies, and thesis advice from Docsity tutors
Experimental records and results of studies on microbial kinetics for the utilization of inhibitory substrates in a fed-batch bioreactor system and the extraction of citric acid and lactic acid by salt precipitation. The documents provide insights into the impact of substrate inhibition on microbial growth and product formation, as well as the successful isolation of organic acids from fermentation broths.
Typology: Study notes
1 / 17
This page cannot be seen from the preview
Don't miss anything!
Experimental Record: Determination of Microbial Kinetics for an Inhibitory Substrate in a Fed Batch Objective: The objective of this experiment was to determine the microbial kinetics for the utilization of an inhibitory substrate in a fed-batch bioreactor system, with a focus on assessing substrate inhibition and its impact on microbial growth and product formation. Materials and Equipment:
Conclusion: The experimental determination of microbial kinetics for the utilization of an inhibitory substrate in a fed-batch bioreactor provided valuable insights into the impact of substrate inhibition on microbial growth and product formation. The calculated kinetic parameters contribute to a comprehensive understanding of the substrate-microbe system and are essential for process optimization and bioreactor design in industrial applications.
productivity and biomass yield. This experimental record and result comprehensively outline the methodology, OTR calculations, and the implications of the findings in the context of submerged fermentation.
Salt Precipitation
acid by salt precipitation is a common method used in bioprocessing to isolate and purify these acids from fermentation broths. This experimental record presents the methodology and results of the extraction process, including details about the analytical method used for determining acid concentration.
reaction of citric acid with a specific reagent to form a colored complex, the intensity of which is directly proportional to the concentration of citric acid in the solution.
concentration is typically 2,4,6-trinitrophenol. This reagent forms a colored complex with citric acid, which can be measured spectrophotometrically.
spectrophotometric analysis for determining the concentration of citric acid and lactic acid in the extracted solutions.
Concentrator
concentrating and drying samples in various laboratory and industrial processes. This practical record outlines the methodology and results of concentrating a specific product using a vacuum concentrator.
Concentration of Target Product
Title: Practical of Ethanol Production usingVarious Organic Waste/Raw Materials Aim: To produce ethanol from various organic waste or raw materials through fermentation, demonstrating the versatility of ethanol production from biomass Sources. Theory: Ethanol production from organic waste or raw materials involves enzymatic breakdown of complex carbohydrates into simple sugars, followed by fermentation of these sugars intoethanol by yeast. Various organic materials such as agricultural residues, food waste, paper waste, and energy crops can serve as subs for ethanol production.
(pH, temperature) for enzymatic activity and allow hydrolysis to proceed until simple sugars are released.
biotechnology, facilitating the large-scale production of this enzyme for various industrial applications. This practical record outlines the methodology, experimental setup, and results of the fermentative production of amylase using Bacillus subtilis as the amylase-producing microorganism.
Statistical Analysis: If multiple replicates were performed, statistical analysis such as calculating mean enzyme activity and standard deviation was conducted to assess the reproducibility of the fermentative production process
amylase was carried out using Bacillus subtilis as the amylase-producing microorganism. - The fermentation process was conducted in a 10-liter bioreactor with a fermentation medium containing starch as the carbon source. - Over a 48- hour fermentation period, the amylase activity steadily increased, reaching a peak of 3000 U/mL. - The harvested culture broth was found to contain a significant concentration of amylase, demonstrating the successful fermentative production of this enzyme.
The practical record demonstrates the successful fermentative production of amylase using Bacillus subtilis and provides insight into the methodology, experimental setup, and outcomes of the fermentation process. The results indicate the efficient production of amylase through fermentation, highlighting the potential for industrial-scale enzyme production using microbial fermentation. This practical record and result provide a clear outline of the methodology, experimental setup, and outcomes of the fermentative production of amylase, showcasing the successful utilization of microbial fermentation for the efficient production of this important enzyme. This practical record serves as an essential reference for understanding the fermentative production of amylase and its implications in industrial enzyme production and biotechnological applications.