
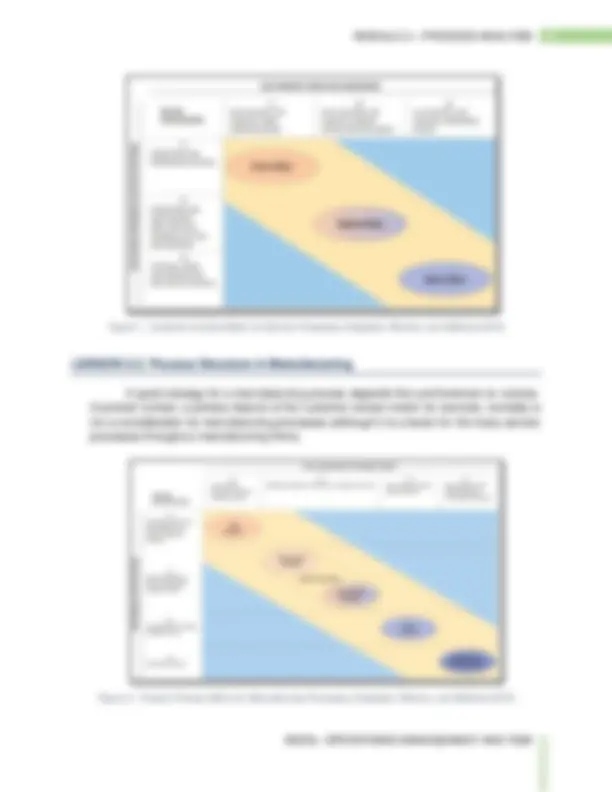

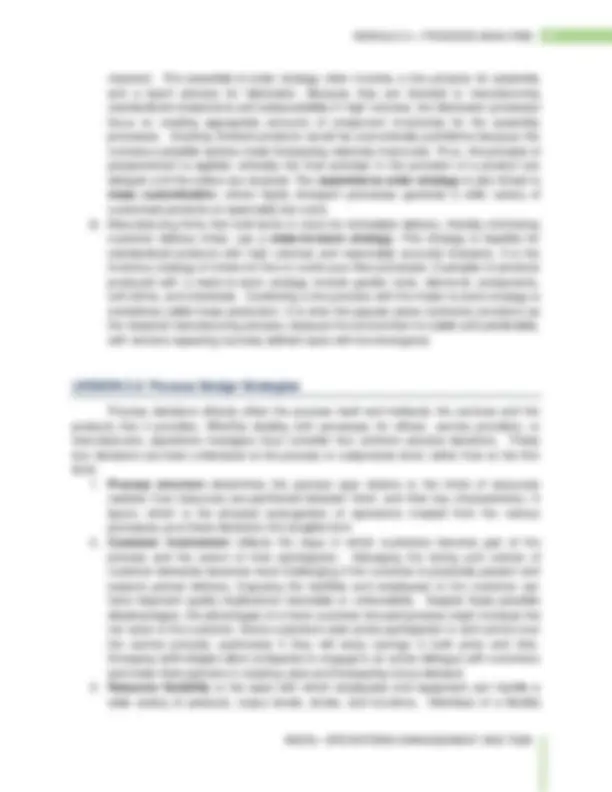
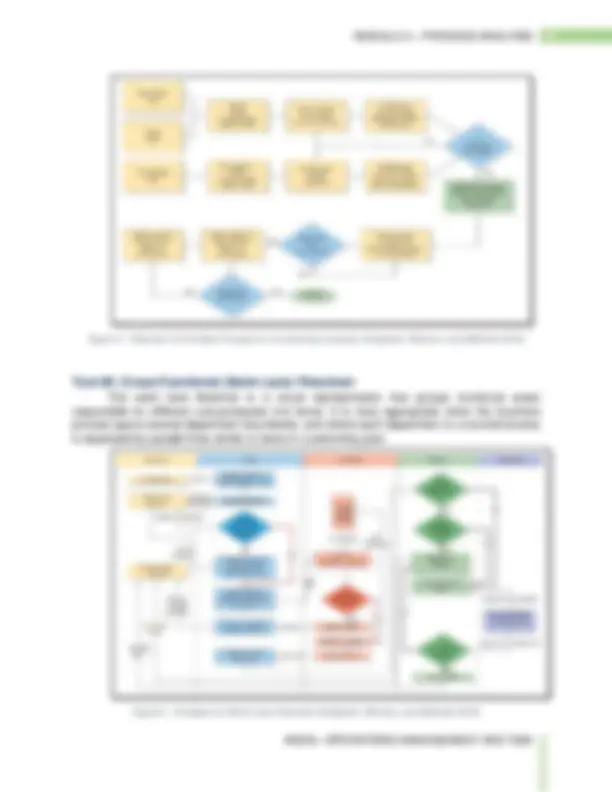
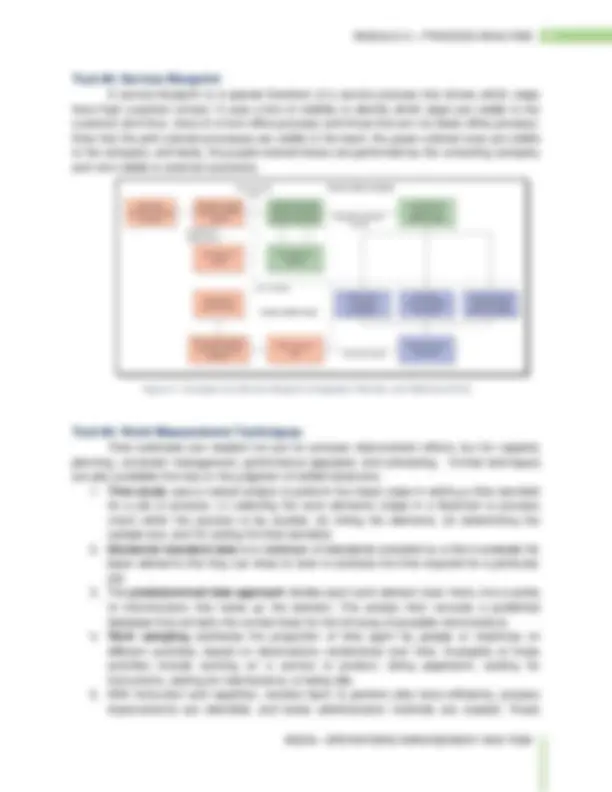
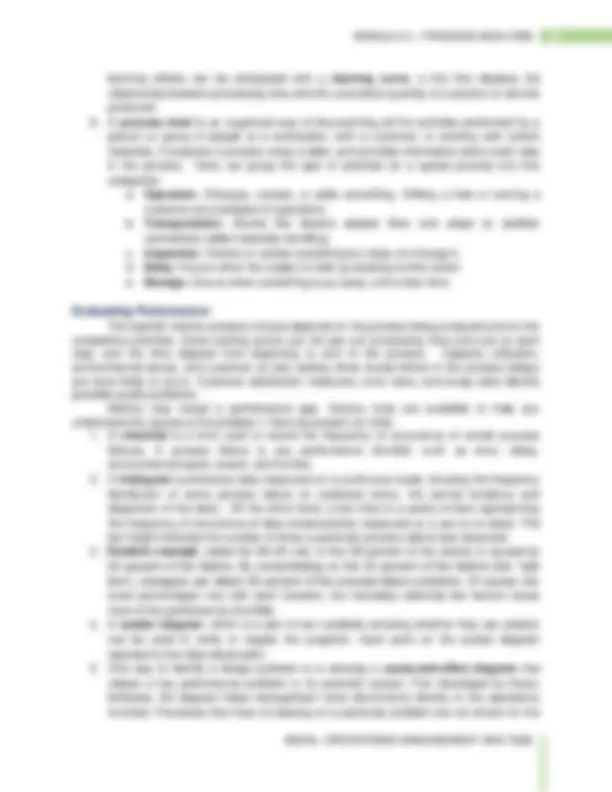
Study with the several resources on Docsity
Earn points by helping other students or get them with a premium plan
Prepare for your exams
Study with the several resources on Docsity
Earn points to download
Earn points by helping other students or get them with a premium plan
Community
Ask the community for help and clear up your study doubts
Discover the best universities in your country according to Docsity users
Free resources
Download our free guides on studying techniques, anxiety management strategies, and thesis advice from Docsity tutors
This module delves into the intricacies of process analysis, a crucial aspect of operations management and total quality management (tqm). It explores the structure of processes in both service and manufacturing contexts, highlighting the importance of customer contact and volume in process design. The module also examines process design strategies, including reengineering and process improvement, and provides a systematic approach to analyzing processes for improvement. It introduces various tools and techniques for process analysis, such as flowcharts, service blueprints, and work measurement techniques, and emphasizes the significance of benchmarking for process optimization.
Typology: Schemes and Mind Maps
1 / 12
This page cannot be seen from the preview
Don't miss anything!
Process decisions are tactical in nature. In making process decisions, managers focus on monitoring such competitive priorities as quality, flexibility, time, and cost. Process management is a continuing activity, with the identical principles applying to both first-time and redesign choices.
Furthermore, many important innovations over the past several decades include work- simplification or better-methods programs, statistical process control, optimization techniques, statistical forecasting techniques, material requirements planning, flexible automation, lean manufacturing, total quality management, reengineering, Six Sigma programs, enterprise resource planning, and e-commerce.
This module focuses on process strategy, which specifies the pattern of decisions made in managing processes so that the processes will achieve their competitive priorities. Process strategy guides a variety of process decisions, and in turn is guided by operations strategy and the organization’s ability to obtain the resources necessary to support them. This module will also discuss a systematic approach for analyzing a process that identifies opportunities for improvement, documents the current process, evaluates the process to spot performance gaps, redesigns the process to eliminate the gaps, and implements the desired changes. The goal is continual improvement.
After reading this module, the learner should be able to:
The time allotted for this module is three hours.
The participants in this module are 3rd^ year BSA and BSBA students.
Processes are found in accounting, finance, human resources, management information systems, and marketing. Organizational structure throughout the many diverse industries varies, but for the most part, all organizations perform similar business processes. All of these processes must be managed.
Furthermore, a process involves the use of an organization’s resources to provide something of value. No service can be provided and no product can be made without a process, and no process can exist without at least one service or product
Strategies for designing processes can be quite different, depending on whether a service is being provided or a product is being manufactured. We begin with service processes, given their huge implication for workforce resources in industrialized countries. Here are the types of office processes used by different kinds of businesses.
The fundamental message in the figure above is that the best choice for a manufacturing process depends on the volume and degree of customization required of the process. The process choice might apply to an entire manufacturing process or just one subprocess nested within it. Here are some of the process models of manufacturing companies.
Furthermore, strategies for manufacturing processes differ from those in services, not only because of low customer contact and involvement, but also because of the ability to use inventories:
1. Manufacturers that make products to customer specifications in low volumes tend to use the make-to-order strategy, coupling it with job or small batch processes. It is a more complex process than assembling a final product from standard components. This strategy provides a high degree of customization and typically uses job or small batch processes. The processes have high divergence. Specialized medical equipment, castings, and expensive homes are suited to the make-to-order strategy. 2. The assemble-to-order strategy is an approach to producing a wide variety of products from relatively few subassemblies and components after the customer orders are
received. The assemble-to-order strategy often involves a line process for assembly and a batch process for fabrication. Because they are devoted to manufacturing standardized components and subassemblies in high volumes, the fabrication processes focus on creating appropriate amounts of component inventories for the assembly processes. Stocking finished products would be economically prohibitive because the numerous possible options make forecasting relatively inaccurate. Thus, the principle of postponement is applied, whereby the final activities in the provision of a product are delayed until the orders are received. The assemble-to-order strategy is also linked to mass customization , where highly divergent processes generate a wide variety of customized products at reasonably low costs.
3. Manufacturing firms that hold items in stock for immediate delivery, thereby minimizing customer delivery times, use a make-to-stock strategy. This strategy is feasible for standardized products with high volumes and reasonably accurate forecasts. It is the inventory strategy of choice for line or continuous-flow processes. Examples of products produced with a make-to-stock strategy include garden tools, electronic components, soft drinks, and chemicals. Combining a line process with the make-to-stock strategy is sometimes called mass production. It is what the popular press commonly envisions as the classical manufacturing process, because the environment is stable and predictable, with workers repeating narrowly defined tasks with low divergence
Process decisions directly affect the process itself and indirectly the services and the products that it provides. Whether dealing with processes for offices, service providers, or manufacturers, operations managers must consider four common process decisions. These four decisions are best understood at the process or subprocess level, rather than at the firm level.
A stakeholder can see how a process operates, at any level of detail, and how well it is performing. Techniques for documenting the process lend themselves to finding performance gaps, generating ideas for process improvements, and documenting the look of a redesigned process. Five techniques are effective for documenting and evaluating processes:
A flowchart traces the flow of information, customers, equipment, or materials through the various steps of a process. Flowcharts are also known as flow diagrams, process maps, relationship maps, or blueprints. You can create flowcharts with several programs. Microsoft PowerPoint offers many different formatting choices for flowcharts. Other powerful software packages for flowcharting and drawing diagrams (such as organization charts and decision trees) are SmartDraw (www.smartdraw.com), Microsoft Visio (www.microsoft.com/office/visio), and Micrografx (www.micrografx.com).
Figure 3. Flowchart of the Sales Process for a Consulting Company (Krajewski, Ritzman, and Malhotra 2016)
The swim lane flowchart is a visual representation that groups functional areas responsible for different sub-processes into lanes. It is most appropriate when the business process spans several department boundaries, and where each department or a functional area is separated by parallel lines similar to lanes in a swimming pool.
Figure 4. Example of a Swim-Lane Flowchart (Krajewski, Ritzman, and Malhotra 2016)
learning effects can be anticipated with a learning curve , a line that displays the relationship between processing time and the cumulative quantity of a product or service produced.
The specific metrics analysts choose depends on the process being analyzed and on the competitive priorities. Good starting points are the per-unit processing time and cost at each step, and the time elapsed from beginning to end of the process. Capacity utilization, environmental issues, and customer (or job) waiting times reveal where in the process delays are most likely to occur. Customer satisfaction measures, error rates, and scrap rates identify possible quality problems. Metrics may reveal a performance gap. Various tools are available to help you understand the causes of the problem.1 Here we present six tools:
diagram. The cause-and-effect diagram sometimes is called a fishbone diagram. The main performance gap is labeled as the fish’s ―head,‖ the major categories of potential causes as structural ―bones,‖ and the likely specific causes as ―ribs.‖
Creativity can also be stimulated by brainstorming , letting a group of people knowledgeable about the process propose ideas for change by saying whatever comes to mind. A facilitator records the ideas on a flipchart, so that all can see. Participants are discouraged from evaluating any of the ideas generated during the session.
Benchmarking is a systematic procedure that measures a firm’s processes, services, and products against those of industry leaders. Companies use benchmarking to better understand how outstanding companies do things so that they can improve their own processes. Competitive benchmarking is based on comparisons with a direct industry competitor. On the other hand, functional benchmarking compares areas such as administration, customer service, and sales operations with those of outstanding firms in any industry. Lastly, internal benchmarking involves using an organizational unit with superior performance as the benchmark for other units. Benchmarking consists of four basic steps:
Read an article on ―A Complete Breakdown for Business Process Analysis‖ at https://kissflow.com/bpm/business-process-analysis/ Read an article about ―The Seven Steps of Business Process Analysis at https://www.businessmapping.com/blog/seven-steps-business-process-analysis/ Read an article about ―Business Process Reengineering‖ by Ben Janse at https://www.toolshero.com/quality-management/business-process-reengineering-bpr/