
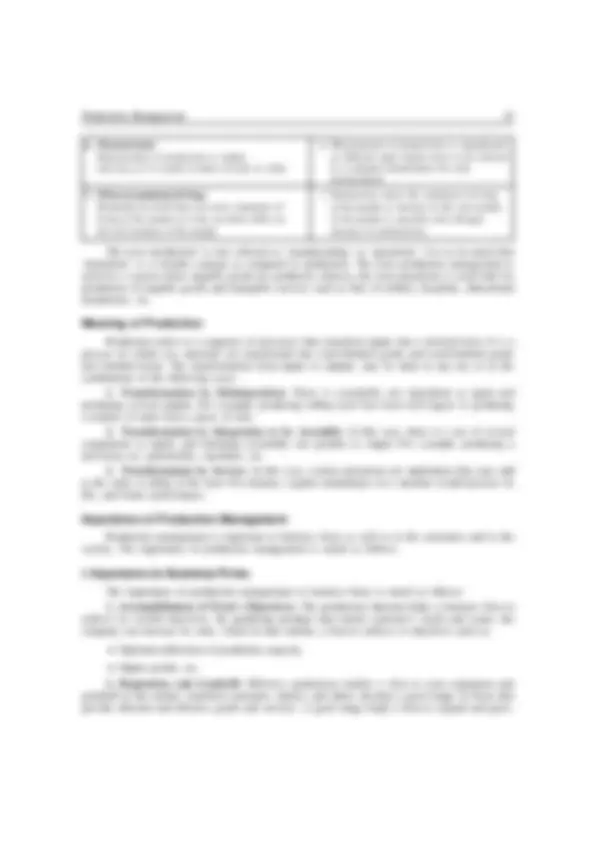
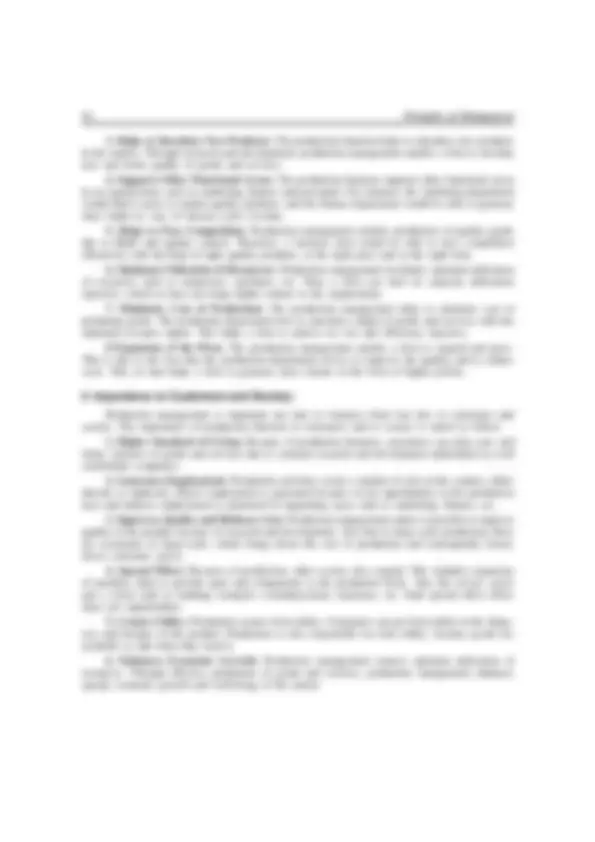
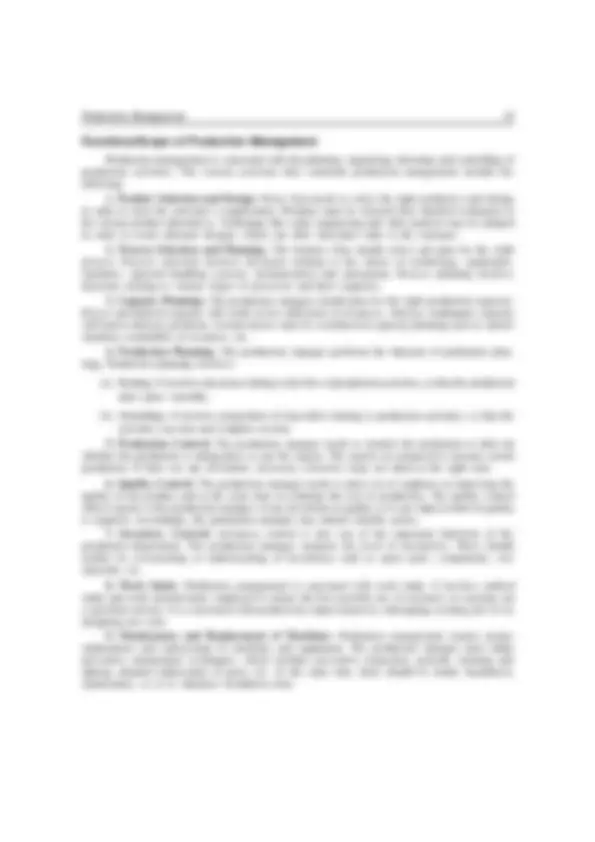
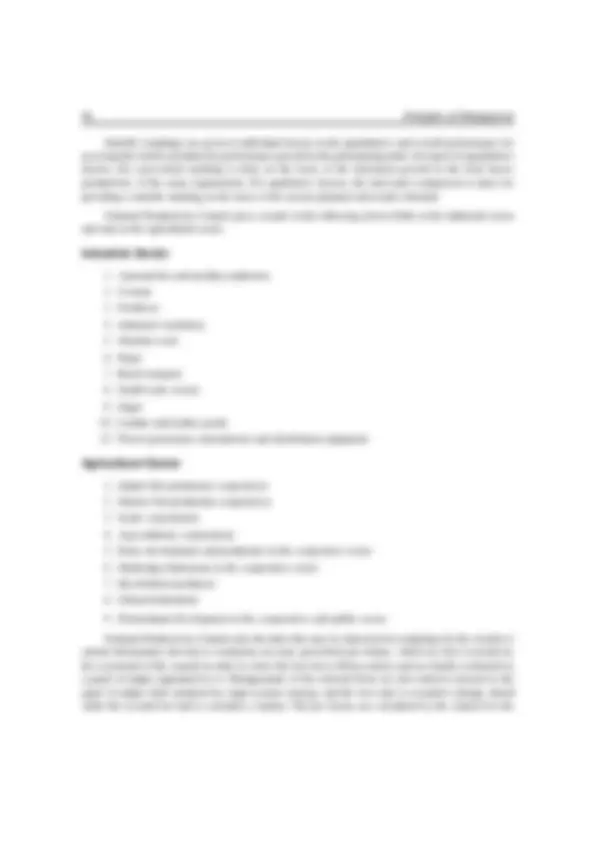
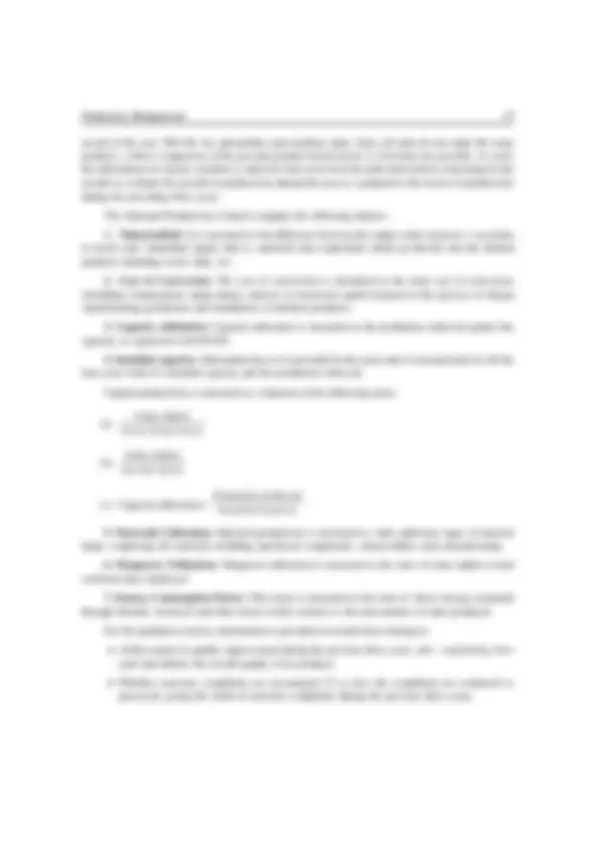
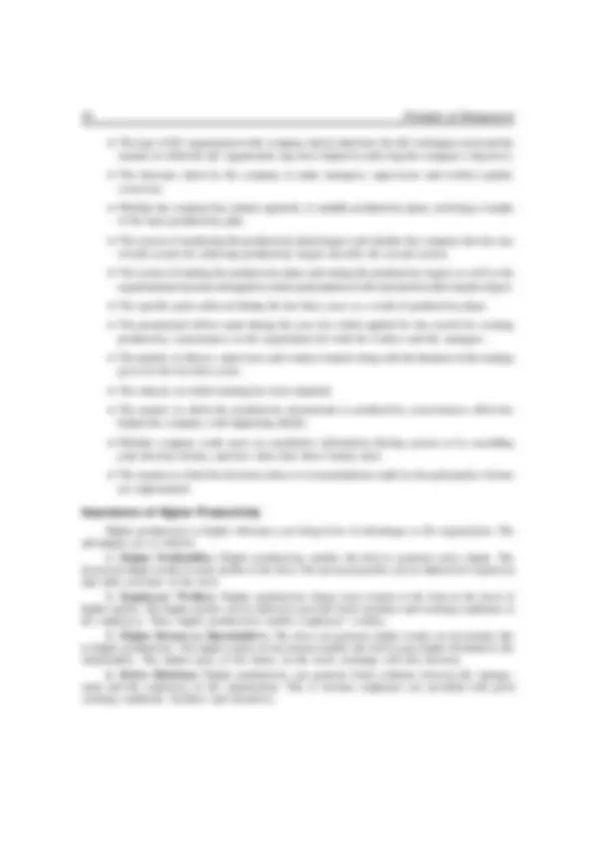
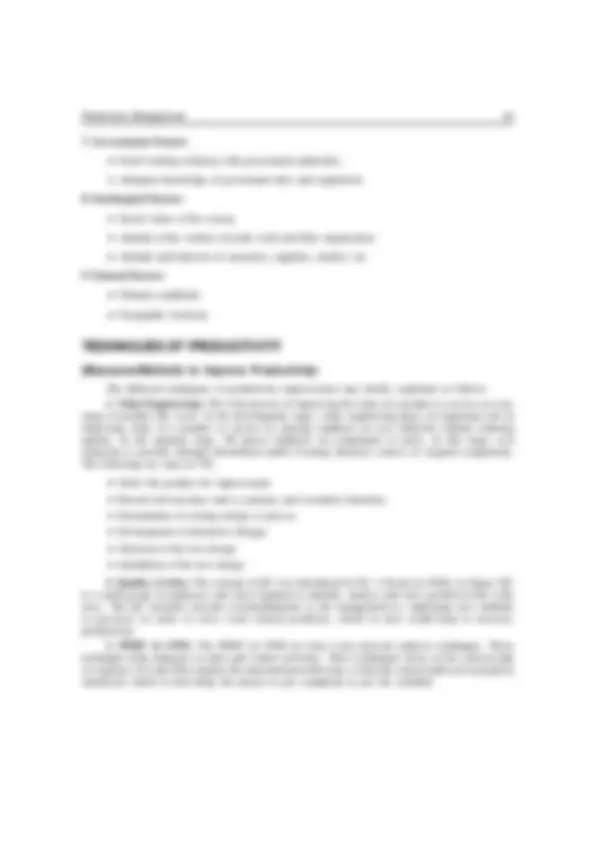
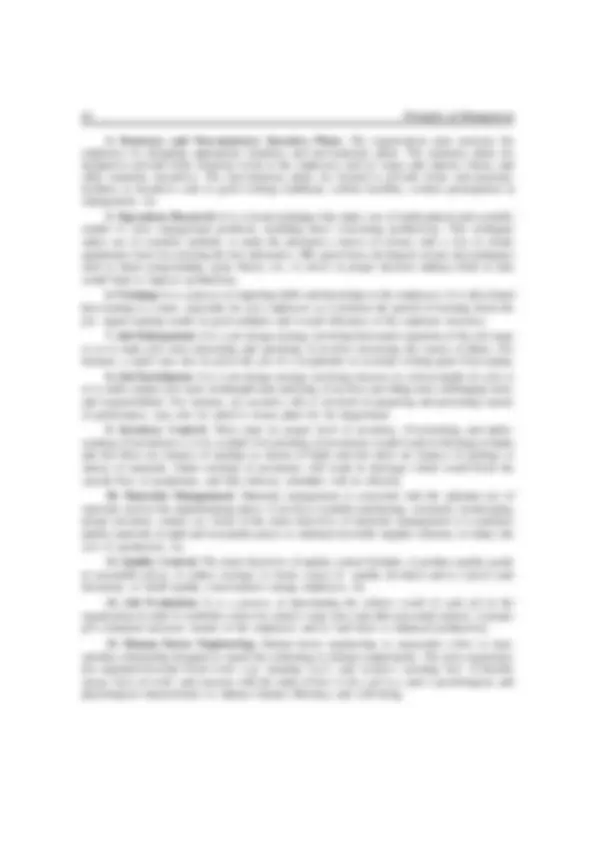
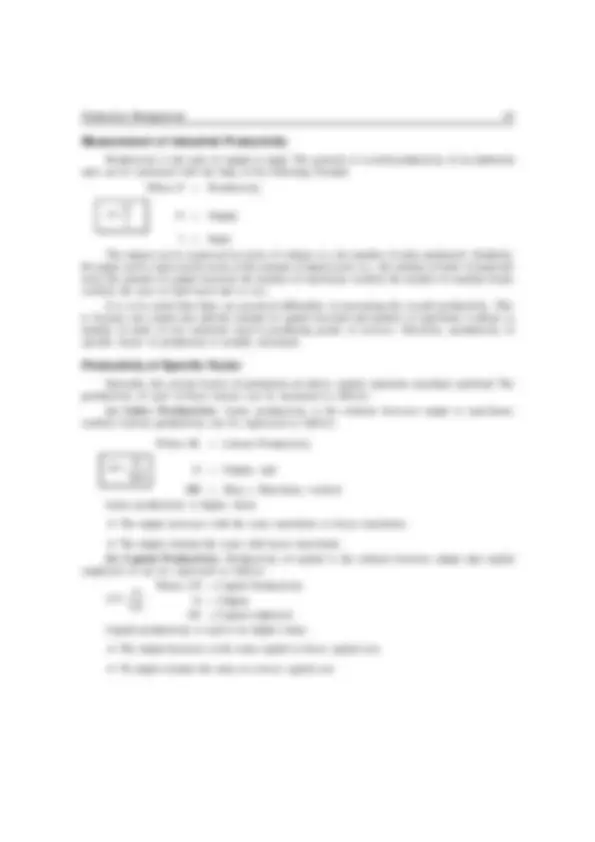
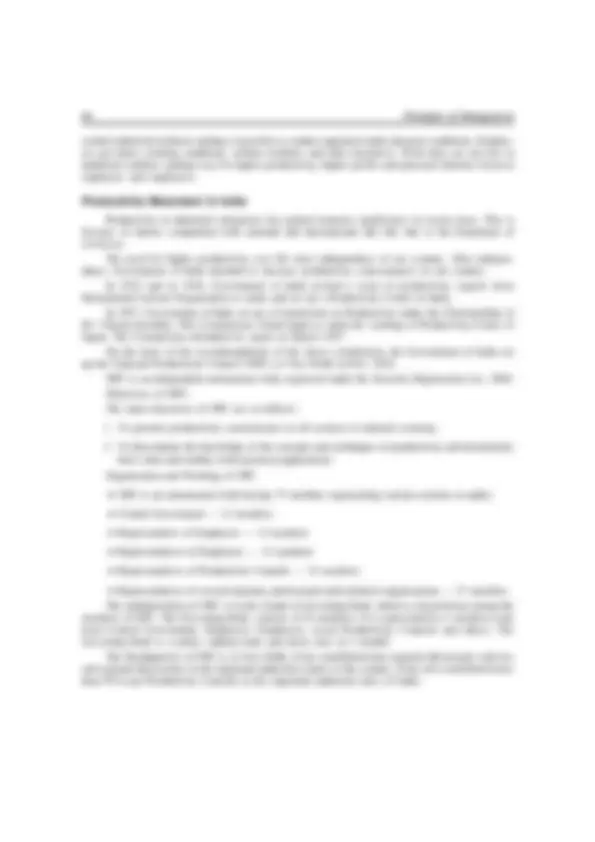
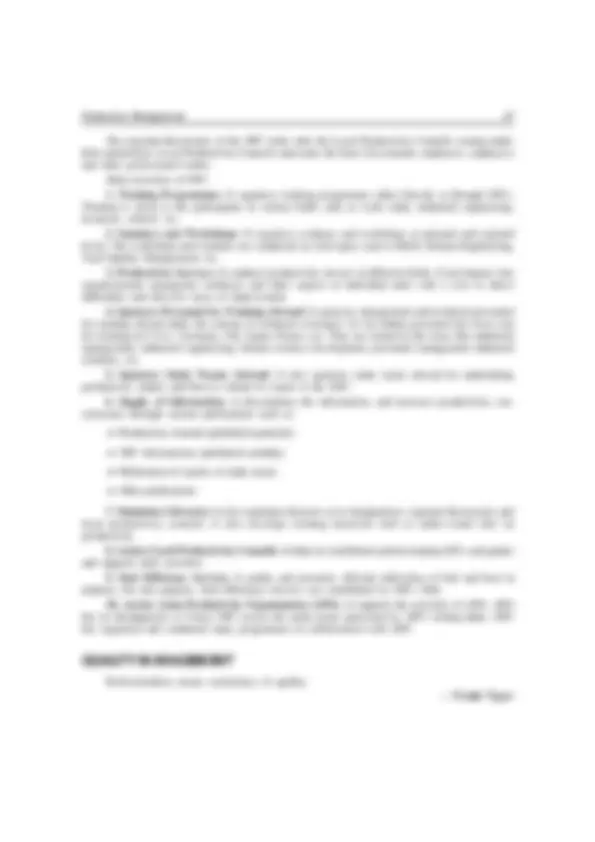
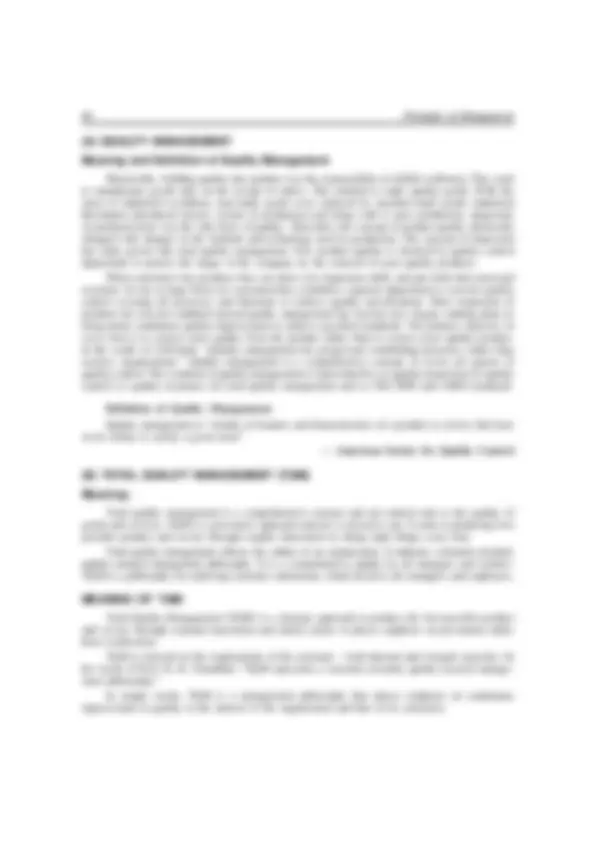
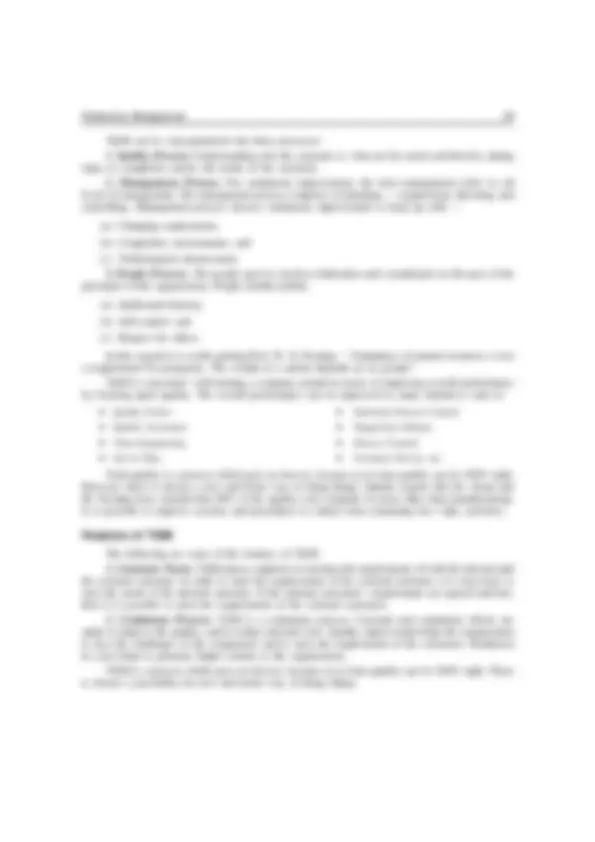
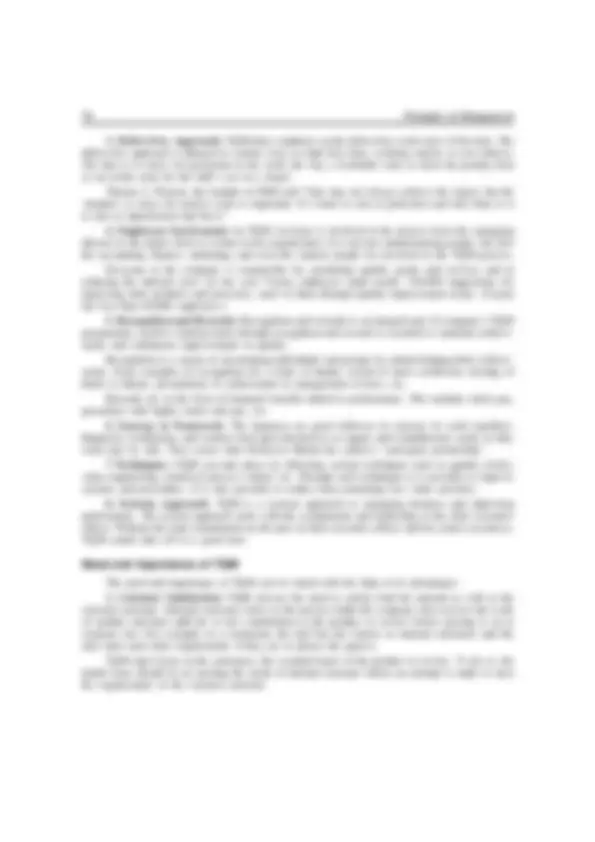
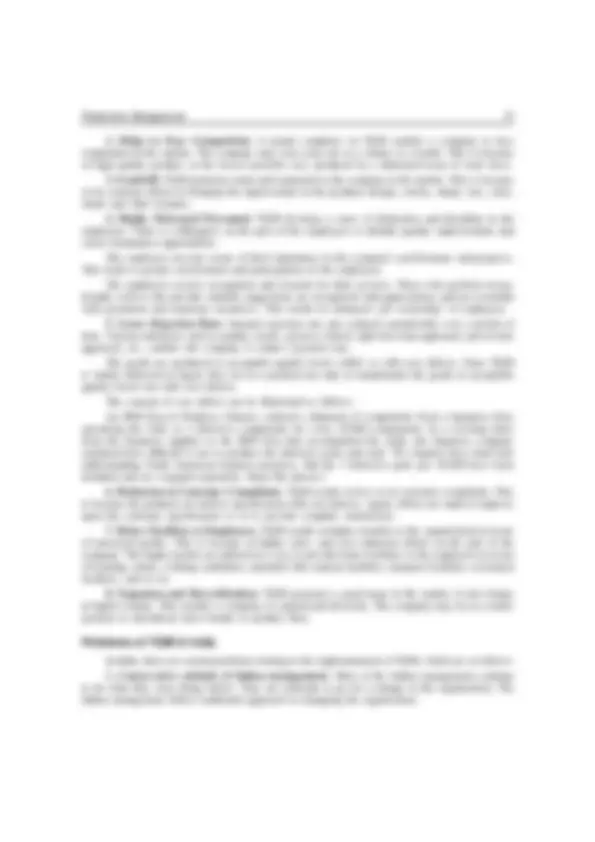
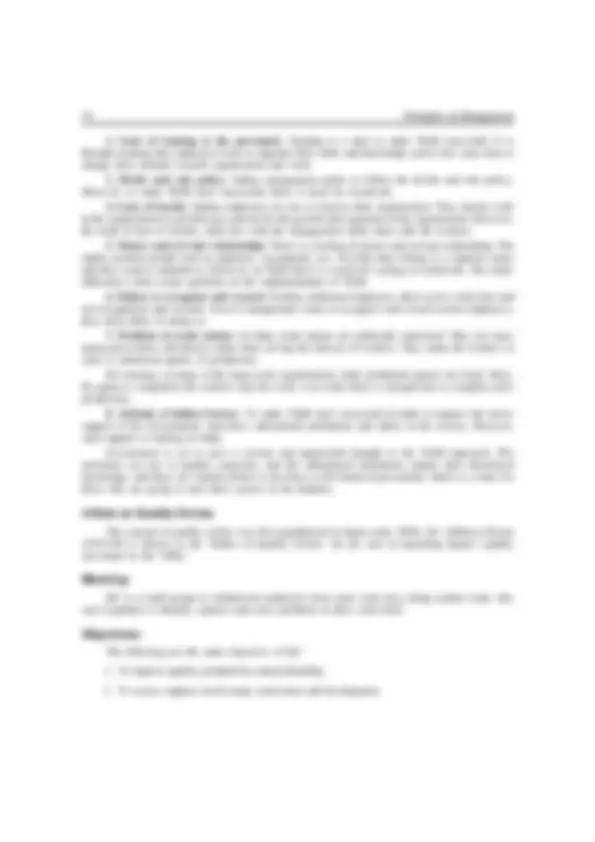
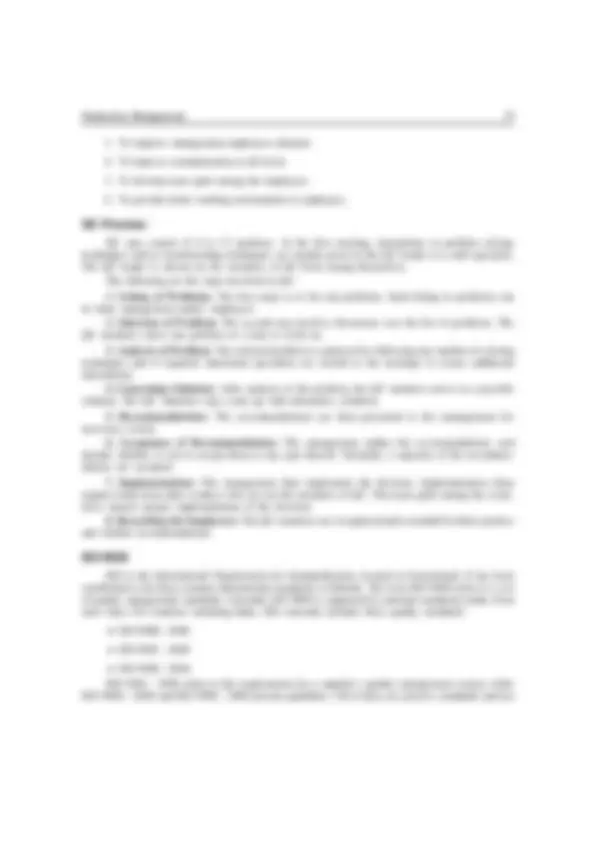
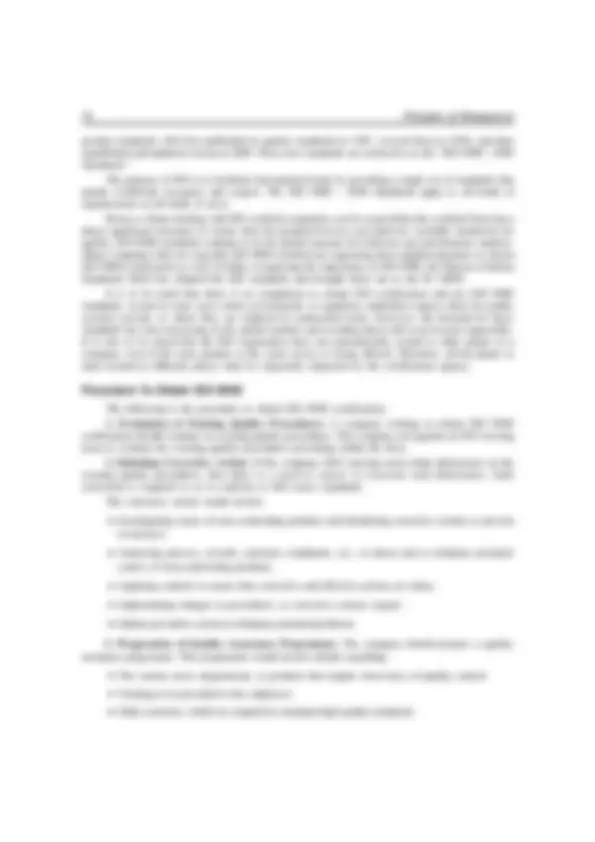
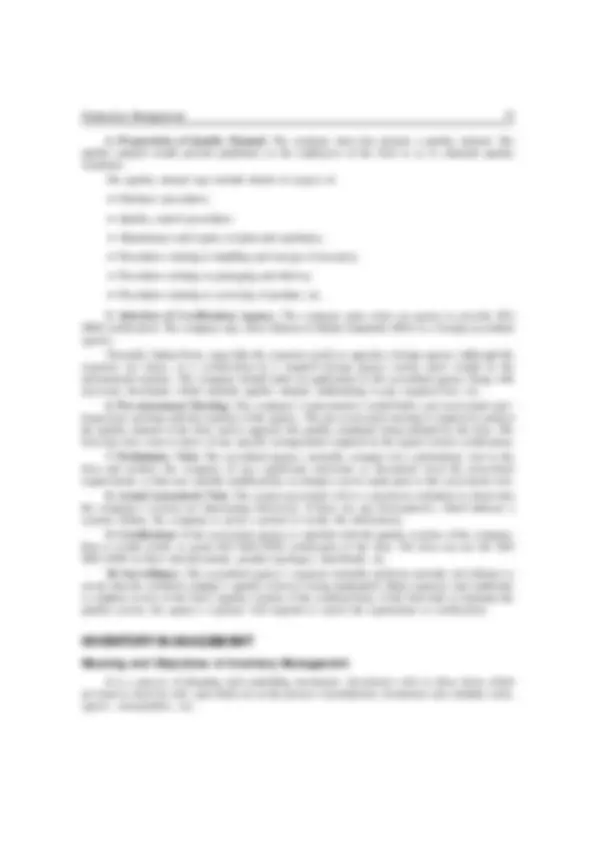
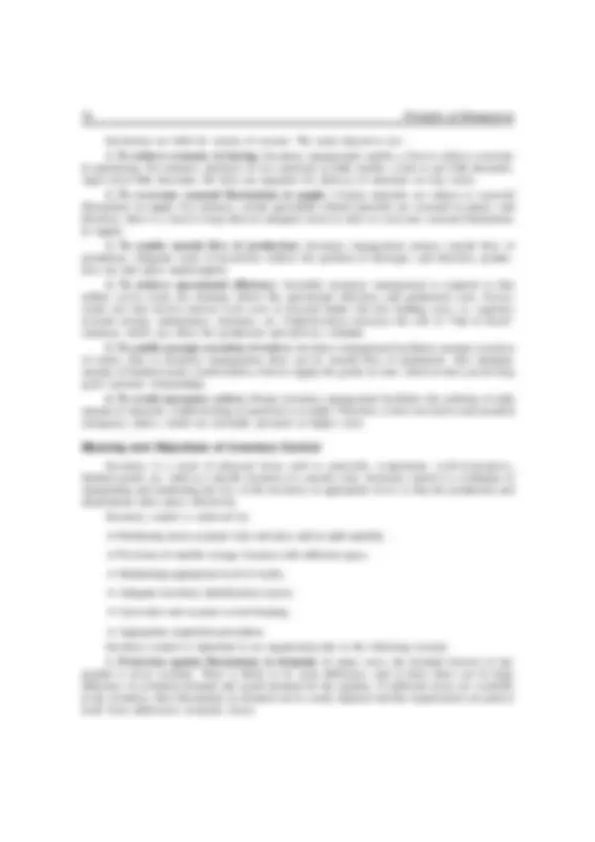
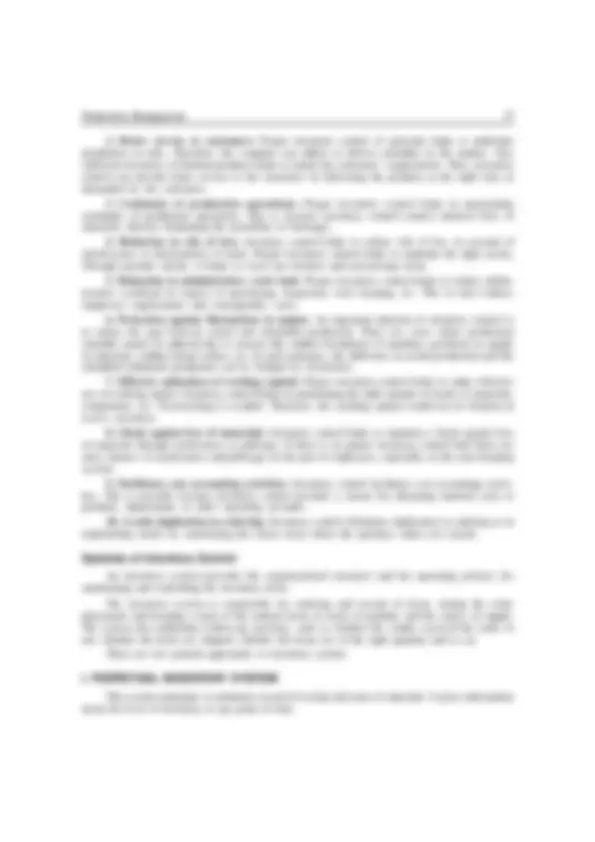
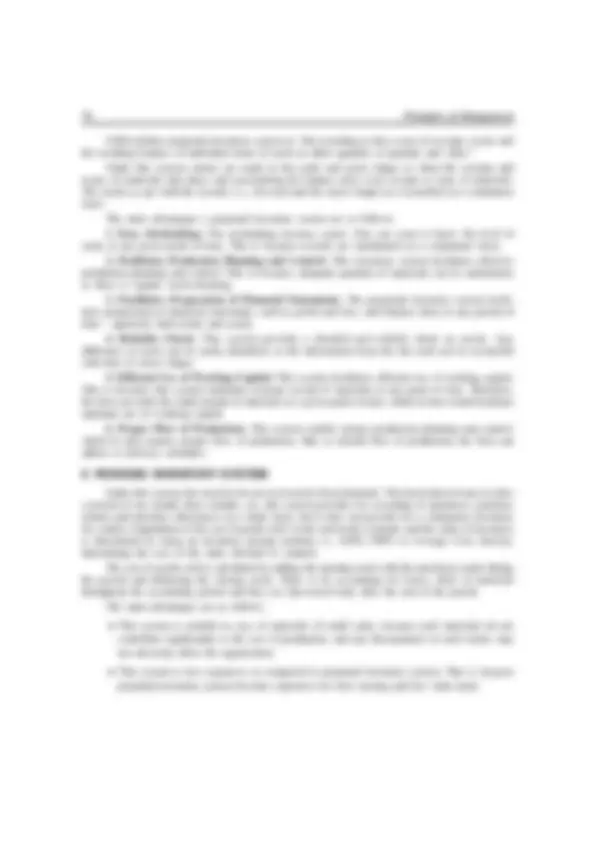
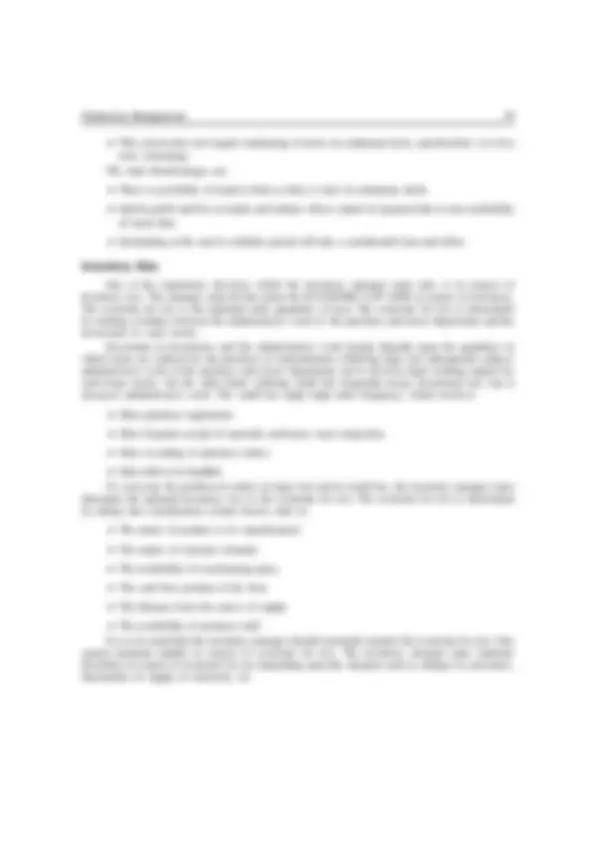
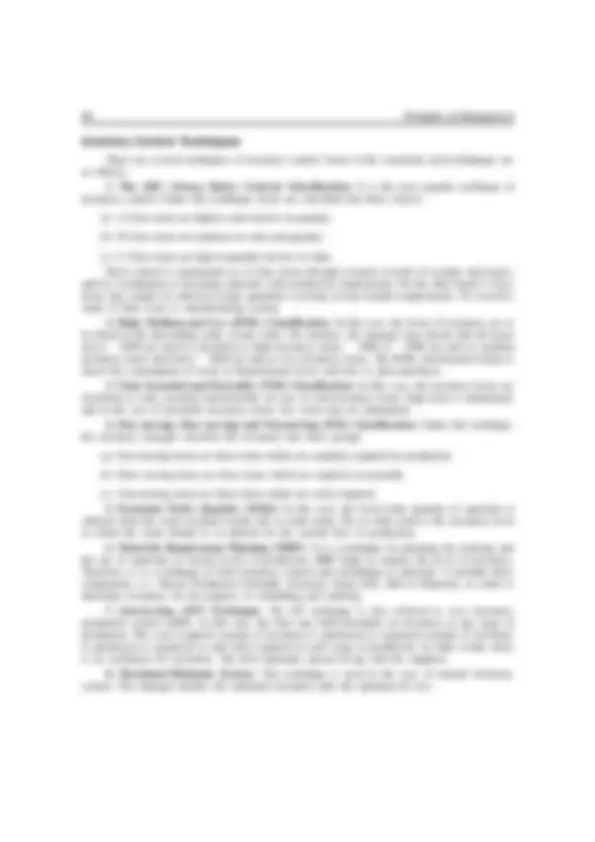
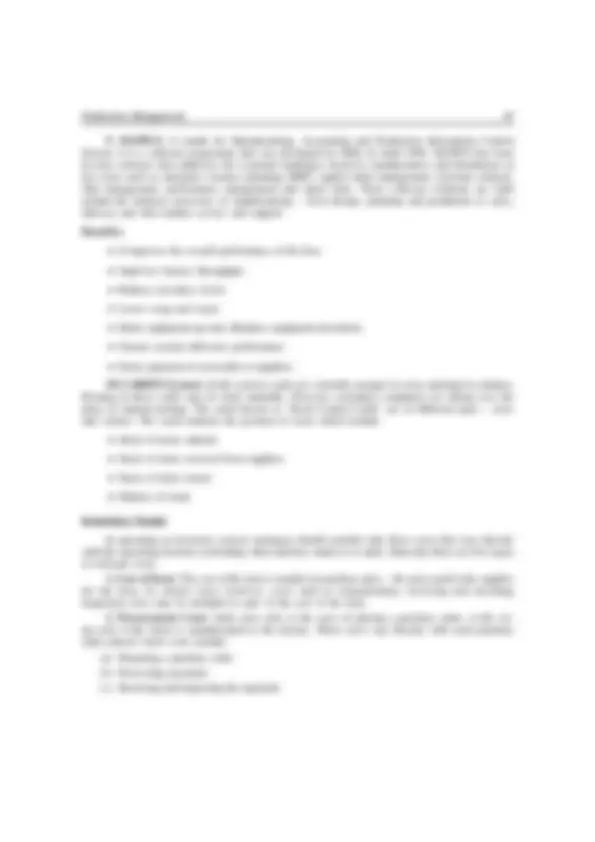
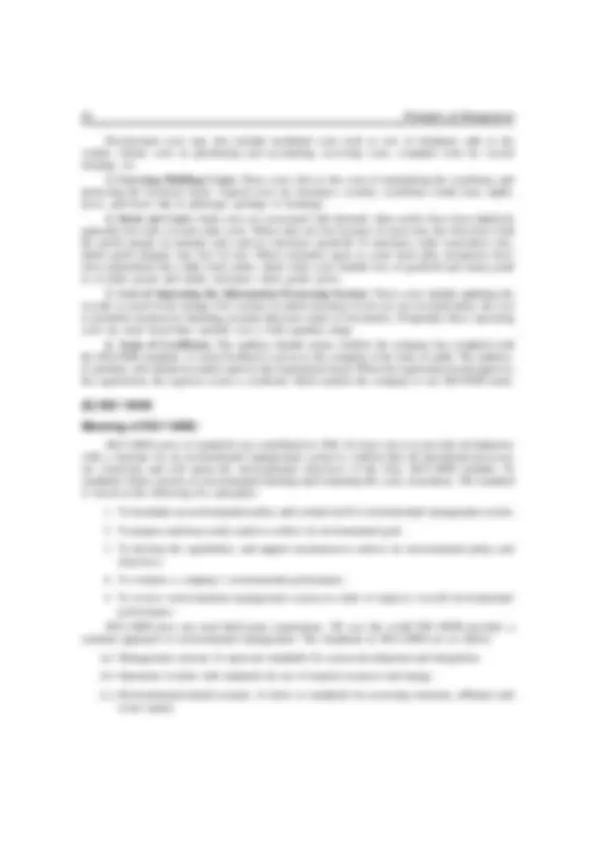
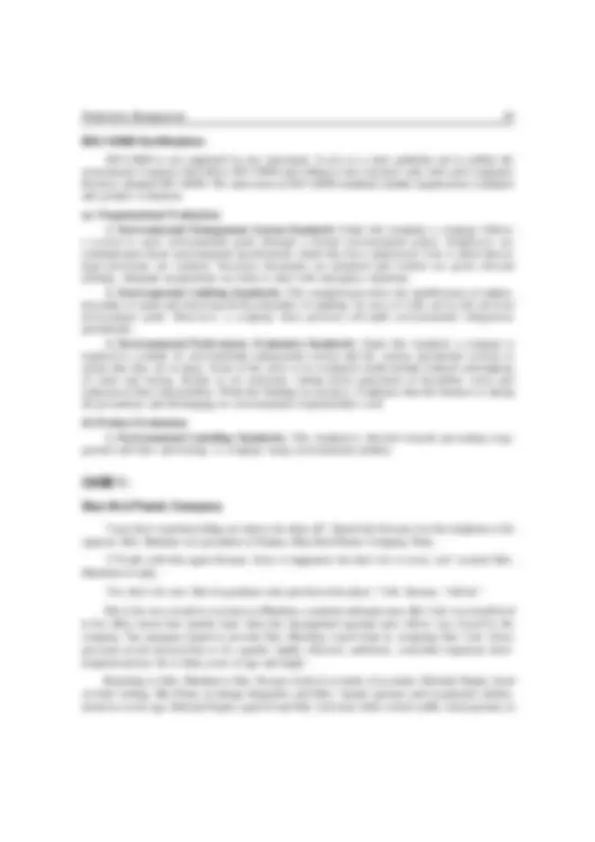
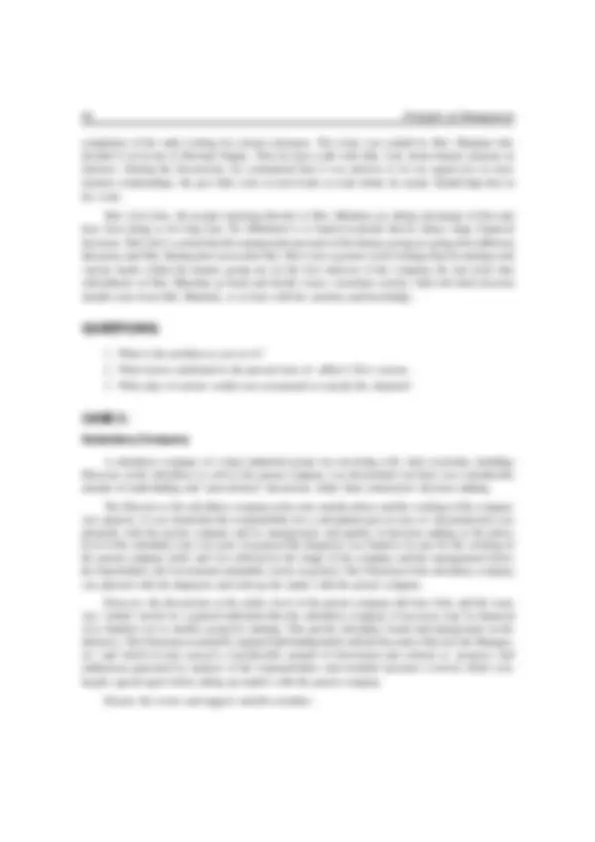
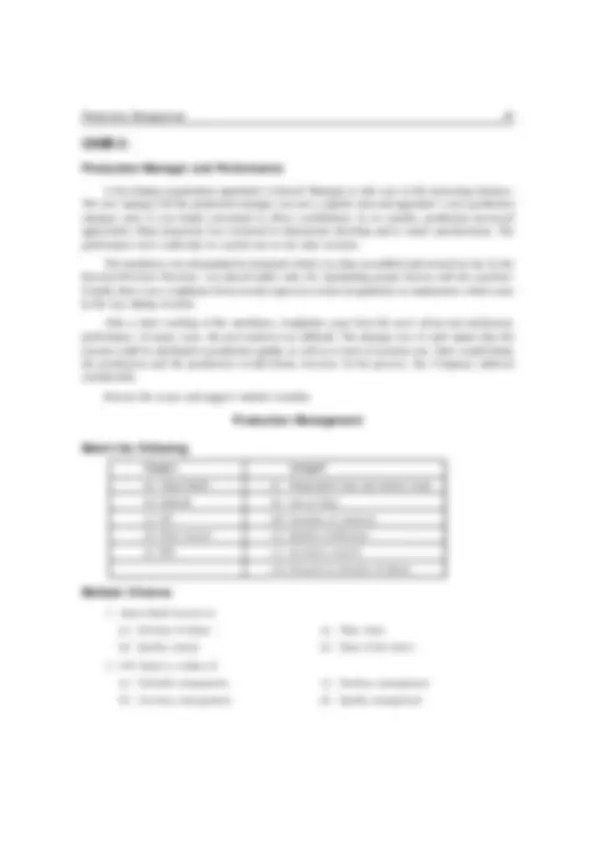
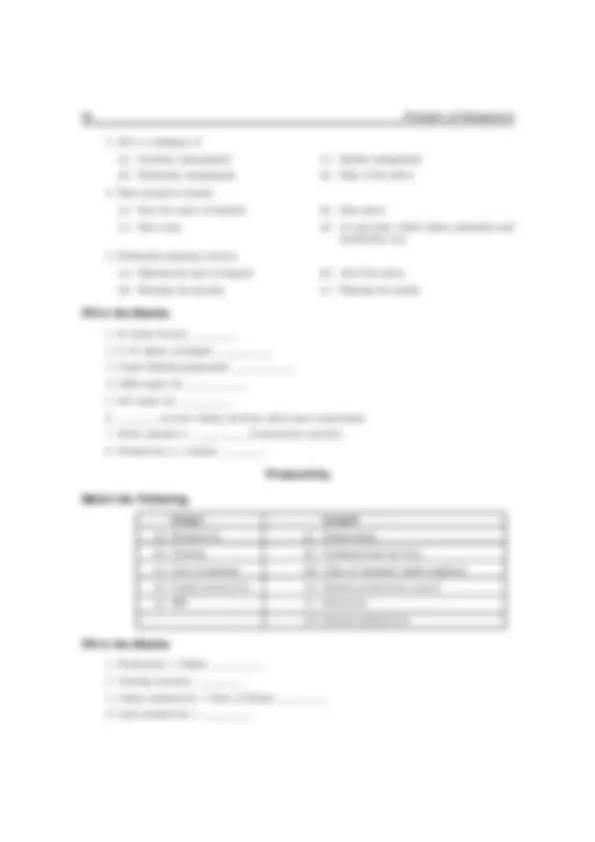
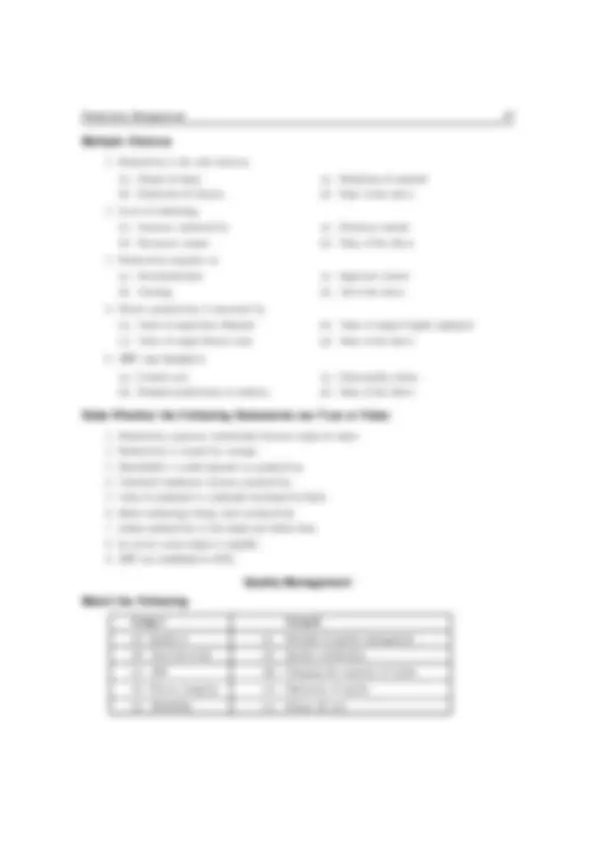
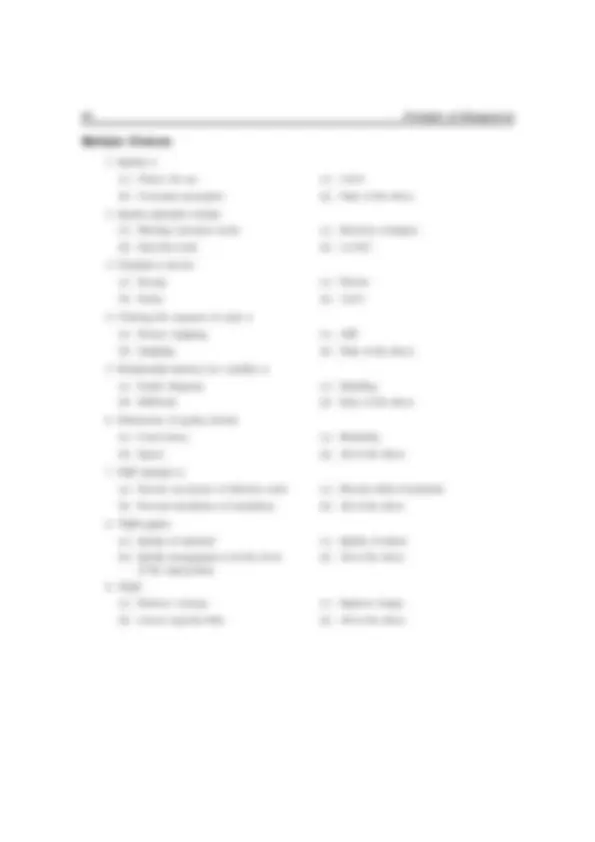
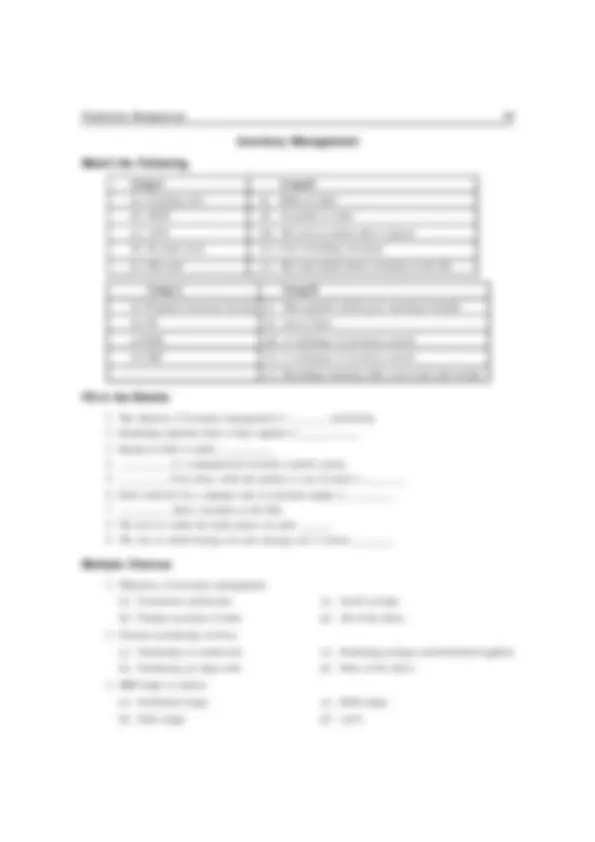
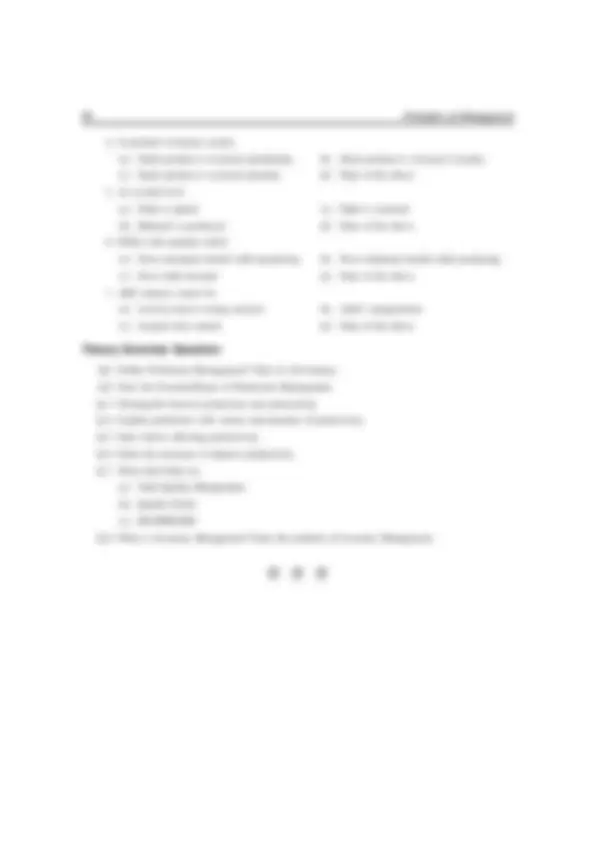
Study with the several resources on Docsity
Earn points by helping other students or get them with a premium plan
Prepare for your exams
Study with the several resources on Docsity
Earn points to download
Earn points by helping other students or get them with a premium plan
Community
Ask the community for help and clear up your study doubts
Discover the best universities in your country according to Docsity users
Free resources
Download our free guides on studying techniques, anxiety management strategies, and thesis advice from Docsity tutors
Production is the creation of utilities for meeting human wants. Here, men, material and equipment are used for the creation of goods which can be used for ...
Typology: Exams
1 / 42
This page cannot be seen from the preview
Don't miss anything!
Production Management 49
MEANING OF PRODUCTION MANAGEMENT (WHAT IS PRODUCTION MANAGEMENT?) Production is the creation of utilities for meeting human wants. Here, men, material and equipment are used for the creation of goods which can be used for different purposes. According to Carl Heyel, “Production is the process of transforming raw materials or purchased components into finished products for sale”. In the production process, raw materials and other inputs are converted into finished goods for actual use. There is creation of utilities through the process of production. Satisfaction of human wants is the guiding principle of all production activities. Thus, production is a process by which goods and services are manufactured or brought into existence. Production and production management are closely related concepts. Production is the creation of goods and services. Production management refers to the application of management principles to the production function/ activity in a factory. The application of management functions to production activity was necessary due to the introduction of factory system of production, growing popularity of joint-stock companies and application of principles of scientific management to production activities. Production process is also described as an act of transformation, i.e., inputs are processed and transferred into some tangible output. Such transformation is possible by assembling or by disinte- gration. In assembling, the components are integrated (e.g., assembling of an automobile) and in disintegration, the parts are separated (e.g., small bars from a big steel bar). Thus, managing productive system involves controlling the conversion process and all the variables that affect its performance. This process of production/productive system is made clear in the following chart:
50 Principles of Management Definition of Production Management
52 Principles of Management
3. Helps to Introduce New Products: The production function helps to introduce new products in the market. Through research and development, production management enables a firm to develop new and better quality of goods and services. 4. Supports Other Functional Areas: The production function supports other functional areas in an organization, such as marketing, finance and personnel. For instance, the marketing department would find it easier to market quality products, and the finance department would be able to generate more funds by way of increase sales revenue. 5. Helps to Face Competition: Production management enables production of quality goods due to R&D and quality control. Therefore, a business firm would be able to face competition effectively with the help of right quality products, at the right price and at the right time. 6. Optimum Utilization of Resources: Production management facilitates optimum utilization of resources such as manpower, machines, etc. Thus, a firm can meet its capacity utilization objective, which in turn can bring higher returns to the organization. 7. Minimizes Cost of Production: The production management helps to minimize cost of producing goods. The production department tries to maximize output of goods and services with the minimum resource inputs. This helps a firm to achieve its cost and efficiency objective. 8 Expansion of the Firm: The production management enables a firm to expand and grow. This is due to the fact that the production department strives to improve the quality and to reduce costs. This, in turn helps a firm to generate more returns in the form of higher profits. II. Importance to Customers and Society: Production management is important not only to business firms but also to customers and society. The importance of production function to customers and to society is stated as follow: 1. Higher Standard of Living: Because of production function, consumers can enjoy new and better varieties of goods and services due to constant research and development undertaken by well established companies. 2. Generates Employment: Production activities create a number of jobs in the country, either directly or indirectly. Direct employment is generated because of job opportunities in the production area and indirect employment is generated in supporting areas such as marketing, finance, etc. 3. Improves Quality and Reduces Cost: Production management makes it possible to improve quality of the product because of research and development. Also due to large-scale production, there are economies of large-scale, which brings down the cost of production and consequently lowers down consumer prices. 4. Spread Effect: Because of production, other sectors also expand. This includes expansion of ancillary units to provide parts and components to the production firms. Also the service sector gets a boost such as banking, transport, communications, insurance, etc. Such spread effect offers more job opportunities. 5. Creates Utility: Production creates form utility. Consumers can get form utility in the shape, size and designs of the product. Production is also responsible for time utility, because goods are available as and when they need it. 6. Enhances Economic Growth: Production management ensures optimum utilization of resources. Through effective production of goods and services, production management enhances speedy economic growth and well-being of the nation.
Production Management 53 Functions/Scope of Production Management Production management is concerned with the planning, organizing, directing and controlling of production activities. The various activities that constitute production management include the following:
1. Product Selection and Design: Every firm needs to select the right product(s) and design in order to meet the customer’s requirements. Products must be selected after detailed evaluation of the various product alternatives. Techniques like value engineering and value analysis may be adopted in order to create alternate designs, which can offer maximum value to the customer. 2. Process Selection and Planning: The business firm should select and plan for the right process. Process selection involves decisions relating to the choice of technology, equipment, machines, material handling systems, mechanization and automation. Process planning involves decisions relating to various stages of processes and their sequence. 3. Capacity Planning: The production manager should plan for the right production capacity. Excess and utilized capacity will result in low utilization of resources, whereas, inadequate capacity will lead to delivery problems. Certain factors must be considered in capacity planning such as market situation, availability of resources, etc. 4. Production Planning: The production manager performs the function of production plan- ning. Production planning involves: (a) Routing: It involves decisions relating to the flow of production activities, so that the production takes place smoothly. (b) Scheduling: It involves preparation of time-table relating to production activities, so that the activities can start and complete on time. 5. Production Control: The production manager needs to monitor the production to find out whether the production is taking place as per the targets. The reports are prepared to measure actual production. If there are any deviations, necessary corrective steps are taken at the right time. 6. Quality Control: The production manager needs to place lot of emphasis in improving the quality of the product and at the same time in reducing the cost of production. The quality control officer reports to the production manager of any deviations in quality or if any improvement in quality is required. Accordingly, the production manager may initiate suitable action. 7. Inventory Control: Inventory control is also one of the important functions of the production department. The production manager monitors the level of inventories. There should neither be overstocking or understocking of inventories such as spare parts, components, raw materials, etc. 8. Work Study: Production management is concerned with work study. It involves method study and work measurement, employed to ensure the best possible use of resources in carrying out a specified activity. It is concerned with productivity improvement by redesigning existing jobs or by designing new jobs. 9. Maintenance and Replacement of Machines: Production management ensures proper maintenance and replacement of machines and equipment. The production manager must adopt preventive maintenance techniques, which includes preventive inspection, periodic cleaning and upkeep, planned replacement of parts, etc. At the same time, there should be timely breakdown, maintenance, so as to minimize breakdown time.
Production Management 55 For an organization involved in selling raw materials, improvements in productivity helps in lowering the selling prices of more and more products and checking inflation. Efficient maintenance of productivity helps in boosting product reliability, quality improvement methodologies and thus, keeps a competitive edge over others. Productivity of each and every industry helps the consumerism, i.e., buying of various commodities at a country level. Lower price increases the purchasing power of consumers enabling a better standard of living. Thus, every nation strives to achieve higher productivity to improve its per capita gross national product (GNP). When the productivity of an organization in a particular industry is raised, others too have to adopt measures to increase their productivity in: order to remain competitive. It is thus very important for every organization to plan a systematic approach towards achieving a higher productivity. Increase in productivity concepts such as Total Productivity and Organisational Productivity are very useful for company and helps in moving towards its object. NATIONAL PRODUCTIVITY COUNCIL The National Productivity Council of India has instituted awards for productivity performance in order to encourage productivity improvement programmes at the units’ level through a process of recognition for sustained and high productivity improvement. For this purpose, it has evolved a system of evaluating growth in the total ,factor productivity index. For instance, in automobile and ancillary units, it goes by the average total factor productivity index of the three consecutive previous years, besides the year for which the award is to be given, using the following pattern of weightage system to calculate the index: Item Weightage (a) Overall Managerial Effectiveness
56 Principles of Management Suitable weightage are given to individual factors in the quantitative and overall performance for assessing the relative productivity performance growth by the participating units. In respect of quantitative factors, the assessment marking is done on the basis of the maximum growth in the total factor productivity of the same organisation. For qualitative factors, the inter-unit comparison is done for providing a suitable marking on the basis of the actions planned and results obtained. National Productivity Council gives awards in the following eleven fields in the industrial sector and nine in the agricultural sector. Industrial Sector
58 Principles of Management The type of QC organisation in the company and its functions, the QC techniques used and the manner in which the QC organisation may have helped in achieving the company’s objectives. The measures taken by the company to make managers, supervisors and workers quality conscious. Whether the company has annual, quarterly or monthly productivity plans, enclosing a sample of the latest productivity plan. The system of monitoring the productivity plans / targets and whether the company also has any reward system for achieving productivity targets describe the reward system. The system of making the productivity plans and setting the productivity targets as well as the organisational measures designed to ensure participation of all concerned in achieving the targets. The specific gains achieved during the last three years as a result of productivity plans. The promotional efforts made during the year (for which applied for the award) for creating productivity consciousness in the organisation for both the workers and the managers. The number of officers, supervisors and workers trained, along with the duration of the training given for the last three years. The subjects on which training has been imparted. The manner in which the productivity promotional or productivity consciousness effort has helped the company, with supporting details. Whether company works more on consultative information sharing systems or by consulting joint decision forums, and how often does these forums meet. The manner in which the decisions taken or recommendations made by the participative forums are implemented. Importance of Higher Productivity Higher productivity or higher efficiency can bring in lot of advantages to the organization. The advantages are as follows:
1. Higher Profitability: Higher productivity enables the firm to generate more output. The increased output results in more profits to the firm. The increased profits can be utilized for expansion and other activities of the firm. 2. Employees’ Welfare: Higher productivity brings more returns to the firm in the form of higher profits. The higher profits can be utilized to provide better facilities and working conditions to the employees. Thus, higher productivity enables employees’ welfare. 3. Higher Return to Shareholders: The firm can generate higher return on investment due to higher productivity. The higher return on investment enables the firm to pay higher dividend to the shareholders. The market price of the shares on the stock exchange will also increase. 4. Better Relations: Higher productivity can generate better relations between the manage- ment and the employees in the organization. This is because employees are provided with good working conditions, facilities and incentives.
Production Management 59
5. Customer Satisfaction: Higher productivity can generate better customer satisfaction. This is because customers are provided with quality products at good prices. Customer satisfaction will result into customer loyalty towards the organization. 6. Higher Credit Rating: Higher productivity can generate higher credit rating by financial institutions and rating agencies like CRISIL and CARE. This will enable the firm to obtain cheap funds from the market to meet working capital requirements as well as fixed capital requirements. 7. Corporate Image: The firm can enjoy a good corporate image in the minds of various sections of the society. This includes: (a) The shareholders (b) The suppliers (c) The financial institutions (d) The customers, etc. 8. Better Terms from Suppliers: Higher productivity can enable the firm to obtain better terms form the suppliers. The suppliers may provide higher credit period due to the goodwill enjoyed by the firm. 9. Less Employees Turnover: Higher productivity enables the firm to provide better facilities and working conditions to the employees. Therefore, this will generate employees loyalty towards the firm and they may not leave the organization. FACTORS AFFECTING PRODUCTIVITY There are several factors affecting industrial productivity. Overall productivity can be increased by improving these factors and attaining a balance between them, The factors are: Technical Factors Sociological & Other Factors Govern- mental Factors Production Factors (^) Organi- sational Factors Manangerial Factors Labour Factors Financial Factors Factors Affecting Productivity 1. Labour Factors Scientific recruitment and selection of employees. Proper placement of employees throughout the organization
Production Management 61
7. Government Factors Good working relations with government authorities. Adequate knowledge of government rules and regulations. 8. Sociological Factors Social values of the society. Attitude of the workers towards work and their organization Attitude and behavior of customers, suppliers, dealers, etc. 9. Natural Factors Climatic conditions Geographic locations TECHNIQUES OF PRODUCTIVITY (Measures/Methods to Improve Productivity) The different techniques of productivity improvement may briefly explained as follows: 1. Value Engineering: VE is the process of improving the value of a product or service at every stage of product life cycle. At the development stage, value engineering plays an important role in improving value of a product or service by placing emphasis on cost reduction without reducing quality. At the maturity stage, VE places emphasis on components or parts. At this stage, cost reduction is possible through substitution and/or locating alternate sources of original components. The following are steps in VE: Select the product for improvement Record relevant data such as primary and secondary functions. Examination of existing design or process Development of alternative designs Selection of the best design Installation of the new design. 2. Quality Circles: The concept of QC was introduced by Dr. I. Kaoru in 1960s, in Japan. QC is a small group of employees who meet regularly to identify, analyst, and solve problem in the work area.. The QC members provide recommendations to the management to, implement new methods or practices in order to solve work related problems, which in turn would help to increase productivity. 3. PERT & CPM: The PERT & CPM are time event network analysis techniques. These techniques help managers to plan and control activities. These techniques focus on the critical path or sequence of events that requires the maximum possible time, so that the critical path can be properly monitored, which in turn helps the project to get completed as per the schedule.
62 Principles of Management
4. Monetary and Non-monetary Incentive Plans: The organization must motivate the employees by designing appropriate monetary and non-monetary plans. The monetary plans are designed to provide better monetary terms to the employees such as wages and salaries, bonus, and other monetary incentives. The non-monetary plans are framed to provide better non-monetary facilities or incentives such as good working conditions, welfare facilities, workers participation in management, etc. 5. Operations Research: It is a broad technique that makes use of mathematical and scientific models to solve management problems, including those concerning productivity. This technique makes use of scientific methods, to study the alternative courses of actions with a view to obtain quantitative basis for selecting the best alternative. OR experts have developed various sub-techniques such as linear programming, game theory, etc., to arrive at proper decision making which in turn would help to improve productivity. 6. Training: It is a process of imparting skills and knowledge to the employees. It is often found that training is a must, especially for new employees as it shortens the period of learning about the job. Again training results in good attitudes and overall efficiency of the employee increases. 7. Job Enlargement: It is a job design strategy involving horizontal expansion of the job range so as to make jobs more interesting and satisfying. It involves increasing the variety of duties. For instance, a typist may also be given the job of a receptionist or accounts writing apart from typing. 8. Job Enrichment: It is a job design strategy involving increase in vertical depth of a job so as to make routine jobs more meaningful and satisfying. It involves providing more challenging tasks, and responsibilities. For instance, an executive who is involved in preparing and presenting reports of performance, may also be asked to frame plans for his department. 9. Inventory Control: There must be proper level of inventory. Overstocking and under- stocking of inventories is to be avoided. Overstocking of inventories would result in blocking of funds and also there are chances of spoilage or misuse of funds and also there are chances of spoilage or misuse of materials. Under stocking of inventories will result in shortages which would block the smooth flow of production, and thus delivery schedules will be affected. 10. Materials Management: Materials management is concerned with the optimum use of materials used in the manufacturing prices. It involves scientific purchasing, systematic storekeeping, proper inventory control, etc. Some of the main objectives of materials management is to purchase quality materials at right and reasonable prices, to maintain favorable supplier relations, to reduce the cost of production, etc. 11. Quality Control: The main objectives of quality control includes, to produce quality goods at reasonable prices, to reduce wastage, to locate causes of quality deviation and to correct such deviations, to instill quality consciousness among employees, etc. 12. Job Evaluation: It is a process of determining the relative worth of each job in the organization in order to establish a basis for relative wage rates and other personnel matters. A proper job evaluation increases morale of the employees and as such there is enhanced productivity. 13. Human Factor Engineering: Human factor engineering or ergonomics refers to man- machine relationship designed to match the technology to human requirements. The term ergonomics has originated from the Greek work ‘ergs’ meaning ‘work’, and ‘nomikos’ meaning ‘law’. It literally means ‘laws of work’ and concerns with the study of how to fit a job to a man’s psychological, and physiological characteristics to enhance human efficiency and well-being.
64 Principles of Management (c) Raw Materials Productivity: The productivity of raw materials is the relations between output to raw materials consumed. It can be expressed as follows: Where RMP = Raw materials productivity O RMP = RMC O = Output RMC = Raw materials consumed It is to be noted that the raw materials productivity can be measured in terms of number of units of raw materials consumed as well as the cost of raw materials. (d) Machines Productivity: The productivity of machines is the relation between output to machine-hours worked. It can be expressed as follows: Where MP = Machines productivity O PL = MHW O = Output MHW = Machine-hours worked (e) Productivity of Land: The productivity of land is the relation between output to area of land used. It can be expressed as follows: Where PL = Productivity of land O PL = AL O = Output AL = Area of land used Difficulties in Measuring Productivity
1. Difficulty in Measuring Output: Output can be measured either in terms of physical volume or in terms of money value. If measured in physical volume the problem will arise when physical units of different size, shape, color, etc., are produced as such physical units cannot be totalled up. Further, certain by-products may arise during the manufacturing process, whose evaluation becomes arbitrary. If output is measured in terms of money value then the firm will have certain difficulties in measuring productivity, especially, when the firm manufactures a wide variety of items and where inter-company comparison has to be made. 2. Difficulty in Measuring Labour Productivity: It is difficult to measure and compare the labour productivity. This is because one cannot easily compare the labour productivity of one firm with that of another. For instance, the labour of one firm may be more trained and capable as that of the other and therefore the productivity of labour in the first firm may be higher. 3. Difficulty in Measuring Capital Productivity: It is difficult to measure and compare the capital productivity of two different firms. This is because one firm may employ capital obtained from sources at low rate of interest as compared to the other firm. 4. Difficulty in Measuring Land Productivity: It is difficult to measure and compare the land productivity at two different locations. The land may differ in various respects such as rent, locational advantages, etc.
Production Management 65
5. Difficulty in Measuring Machines Productivity: It is difficult to measure the productivity of machines employed by two different firms. For instance, one firm may employ latest machines as compared to the other. Therefore, the productivity of machines employed by the firm may be higher as compared to the other firm. 6. Difficulty in Measuring Materials Productivity: It is difficult to measure the productivity of materials employed by two different firms. For instance, one firm may make use of good quality materials as compared to that of another firm. Therefore, the productivity of materials used by the first firm may be higher as compared to the other firm. 7. Difficulty in Measurement of Man-hours: It is difficult to figure out the exact figures of productive man-hours. Wages paid to labour includes cost of idle time also. 8. War and Peace Periods: Comparison during war and peace periods also becomes difficult, because the value of inputs and outputs varies according to conditions prevailing in the country. 9. Technology Changes: Change in Technology also poses a problem as it would cause a change in the nature and quality of output. 10. Service Institutions: In service Institutions like banks, insurance companies, etc,. it is difficult to work out productivity ratios. Output figures in physical terms for intangible services are difficult to compute. 11. Price Changes: Value comparison over a period of time does not give a correct picture due to inflation. There arises a problem of reducing prices to proper base price. Productivity vs Performance Appraisal Productivity: Productivity is the quantitative relation between what we produce and what we use as a resource to produce them. Productivity also indicates the efficiency of production manage- ment. It is an indicator to show how well the factors of production land, labour, capital and enterprise are utilized. Productivity leads to better utilization of resources at the enterprise level. Higher productivity provides improved wages to employees. Productivity cuts down wastage along with cost and improves margin of profits. Higher productivity earns improved credit rating for the enterprise from the rating agencies. Performance Appraisal: Performance appraisal is an objective assessment of an individual’s performance against well defined standards. Performance is essentially what an employee does and does not do. On the other hand, at the organizational level performance appraisal is a systematic evaluation of performance of employees at work by their superiors. Performance appraisal is conducted mainly on traits such as quality and quantity of output, presence at work. Cooperativeness, timely work, etc. Performance appraisal is useful for guiding the employees for self-improvement and self-development. Linking Productivity with Performance Appraisal: Productivity and performance appraisal are closely linked to one another. High productivity raises the competitive capacity of an enterprise and enables it to remain in the business with reasonable stability and an opportunity to move further towards prosperity. Quality improvement and cost reduction are also possible through productivity improvement. The benefits of higher productivity goes down to individual employees whose positions and remuneration show marked improvement. Performance appraisal develops a spirit of healthy competition among the employees who aim to contribute in increasing productivity. Performance appraisal helps the employees in their development through their performance feedback. Productivity contributes in improving individual efficiency resulting in better performance appraisal report. Employees contribute more and get better financial benefits due to higher productivity. This ensures
Production Management 67 The regional directorates of the NPC looks after the Local Productivity Councils coming under their jurisdiction. Local Productivity Councils represents the State Government, employers, employees and other professional bodies. Main Activities of NPC:
1. Training Programmes: It organizes training programmes either directly or through LPCs. Training is given to the participants in various fields such as work study, industrial engineering, inventory control, etc. 2. Seminars and Workshops: It organizes seminars and workshops at national and regional levels. The workshops and seminars are conducted on vital topics such as R&D, Human Engineering, Total Quality Management, etc. 3. Productivity Surveys: It conducts productivity surveys in different fields. It investigates into organizational, managerial, technical, and other aspects of individual units with a view to detect difficulties and discover areas of improvement. 4. Sponsors Personnel for Training Abroad: It sponsors management and technical personnel for training abroad under the scheme of technical assistance. So far Indian personnel has been sent for training in U.S.A., Germany, UK, Japan, France, etc. They are trained in the areas like industrial management, industrial engineering, human resource development, personnel management industrial relations, etc. 5. Sponsors Study Teams Abroad: It also sponsors study teams abroad for undertaking productivity studies and then to submit its report to the NPC. 6. Supply of Information: It disseminates the information, and increases productivity con- sciousness through various publications such as: Productivity Journal (published quarterly) NPC Informations (published monthly) Publication of reports of study teams Other publications 7. Maintains Libraries: It also maintains libraries at its headquarters, regional directorates and local productivity councils. It also develops training materials such as audio-visual aids on productivity. 8. Assists Local Productivity Councils: It helps in established and developing LPCs and guides and supports their activities. 9. Fuel Efficiency Service: It guides and promotes efficient utilization of fuel and heat in industry. For this purpose, Fuel Efficiency Service was established by NPC 1964. 10. Assists Asian Productivity Organization (APO): It supports the activities of APO. APO has its Headquarters at Tokyo NPC assists the study teams sponsored by APO visiting India. NPC has organized and conducted many programmes in collaboration with APO. QUALITY MANAGEMENT Professionalism means consistency of quality. — Frank Tyger
68 Principles of Management (A) QUALITY MANAGEMENT Meaning and Definition of Quality Management Historically, building quality into product was the responsibility of skilled craftsmen. They used to manufacture goods only on the receipt of orders. This enabled to make quality goods. With the onset of industrial revolution, man-made goods were replaced by machine-made goods. Industrial Revolution introduced factory system of production and along with it mass production. Inspection of produced items was the only basis of quality. Thereafter, the concept of product quality drastically changed with changes in the methods and technology used in production. The concept of inspection has today grown into total quality management. Now product quality is checked by quality control department to protect the image of the company by the removal of poor quality products. When customers buy products they use their own inspection skills and put forth their personal reactions. So far as large firms are concerned they establish a separate department to exercise quality control covering all processes and functions to achieve quality specifications. Mere inspection of products has become outdated instead quality management has become new slogan; making plans to bring about continuous quality improvement to achieve specified standards. The primary objective of every firm is to remove poor quality from the product rather than to remove poor quality product. In the words of J.M.Juran, “Quality management has progressed establishing proactive rather than reactive organizations.” Quality management is a comprehensive concept. It covers all aspects of quality control. The evolution of quality management is represented by (a) quality inspection (b) quality control (c) quality assurance (d) total quality management and (e) ISO 9000 and 14000 standards. Definition of Quality Management: Quality management is “totality of features and characteristics of a product or service that bear on its ability to satisfy a given need.” — American Society for Quality Control (B) TOTAL QUALITY MANAGEMENT (TQM) Meaning: Total quality management is a comprehensive concept and not related only to the quality of goods and services. TQM is a preventive approach and not a corrective one. It aims at producing best possible product and service through regular innovation by doing right things every time. Total quality management reflects the culture of an organization. It indicates consumer-oriented, quality-oriented management philosophy. It is a commitment to quality by all managers and workers. TQM is a philosophy for achieving customer satisfaction, which involves all, managers and employees. MEANING OF TQM Total Quality Management (TQM) is a strategic approach to produce the best possible product and service through constant innovation and timely action. It places emphasis on prevention rather than rectification. TQM is focused on the requirements of the customer – both internal and external customer. In the words of Prof. K. K. Chaudhari “TQM represents a customer-oriented, quality focused manage- ment philosophy.” In simple words, TQM is a management philosophy that places emphasis on continuous improvement in quality in the interest of the organization and that of its customers.