
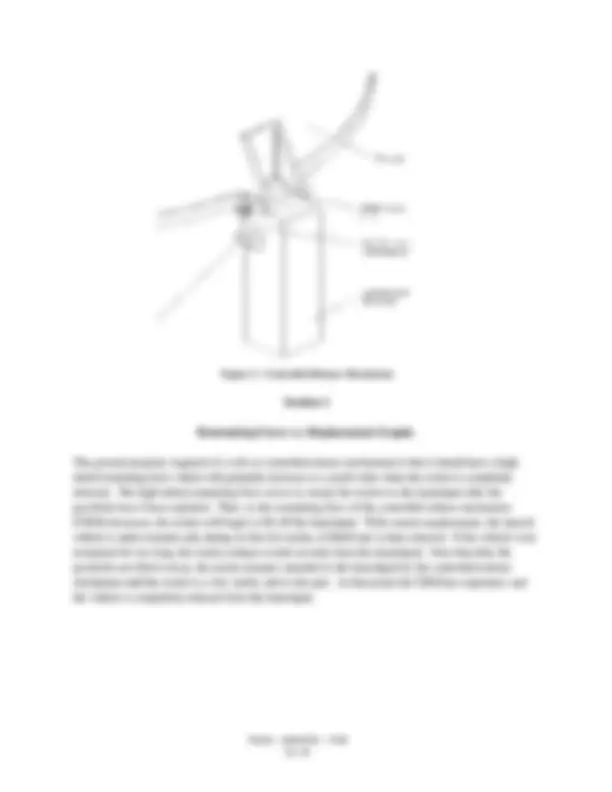
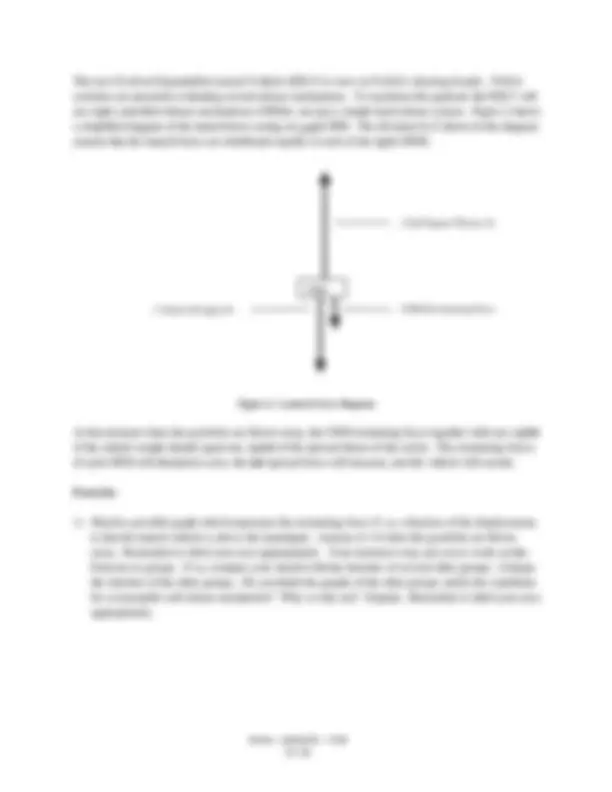
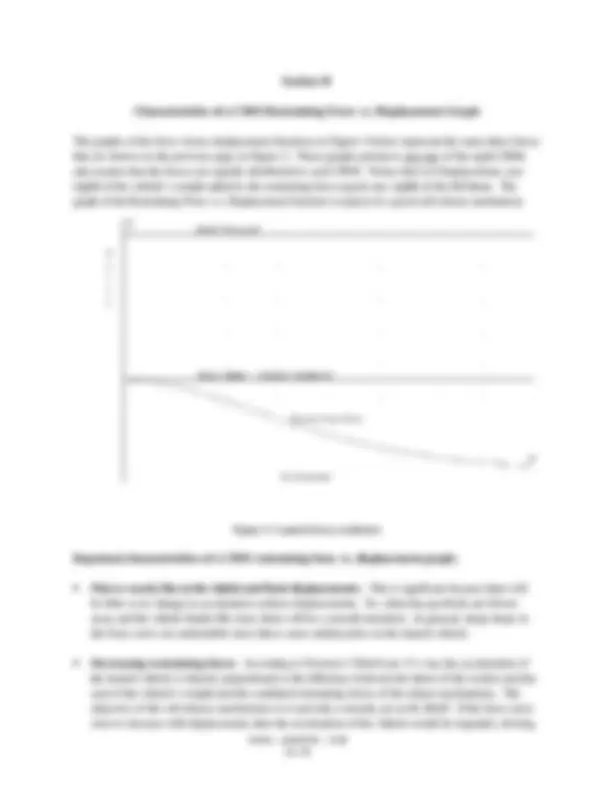
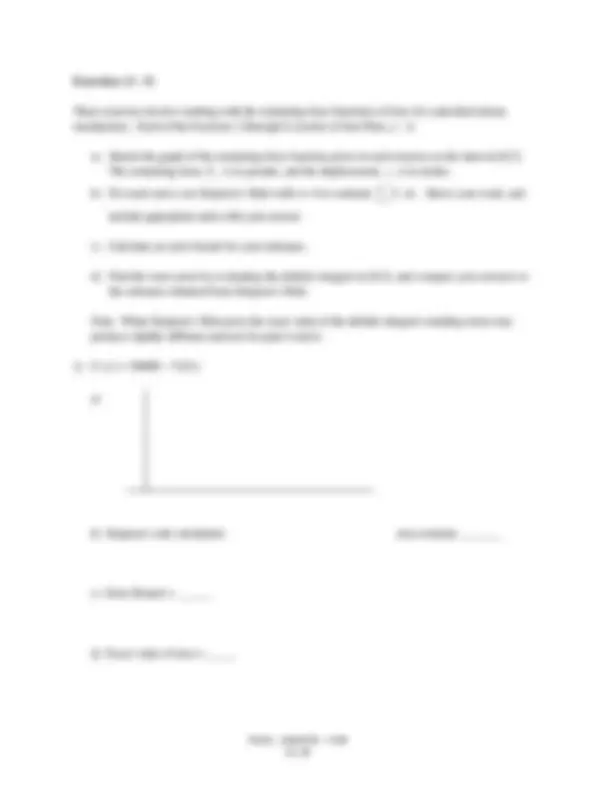
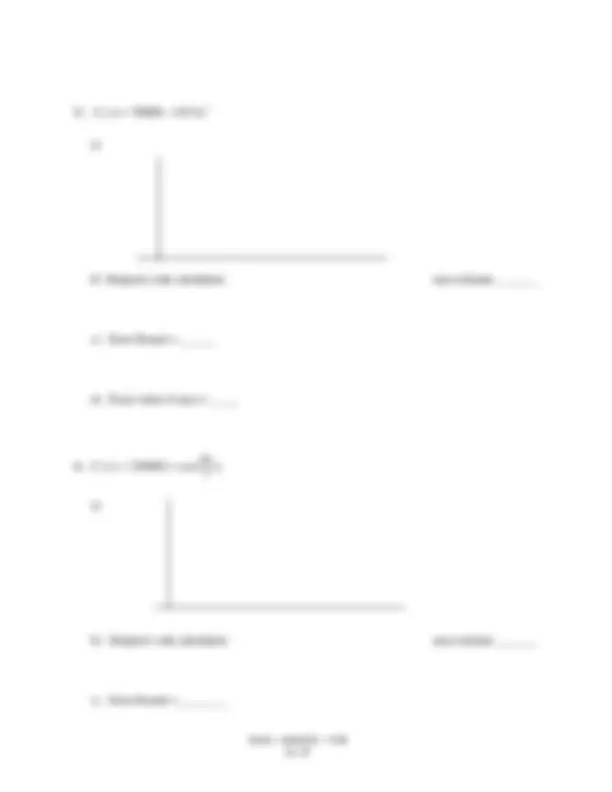
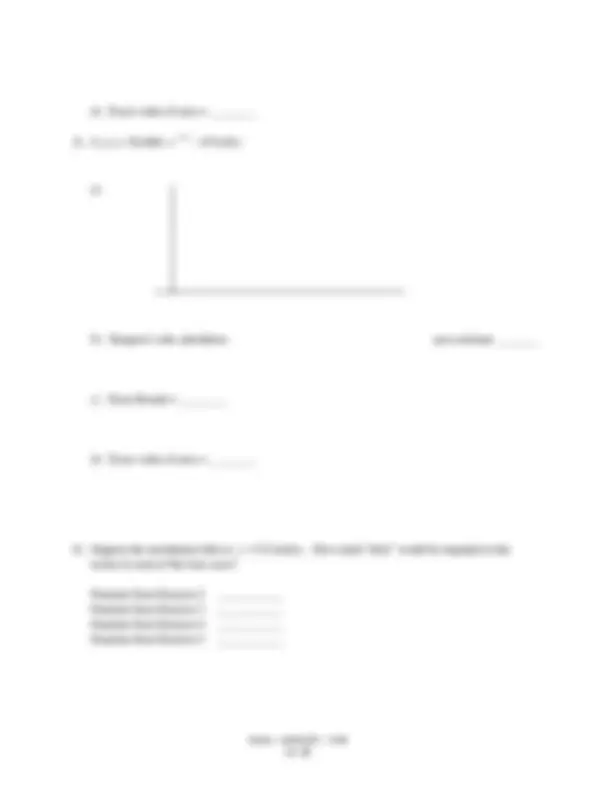
Study with the several resources on Docsity
Earn points by helping other students or get them with a premium plan
Prepare for your exams
Study with the several resources on Docsity
Earn points to download
Earn points by helping other students or get them with a premium plan
Community
Ask the community for help and clear up your study doubts
Discover the best universities in your country according to Docsity users
Free resources
Download our free guides on studying techniques, anxiety management strategies, and thesis advice from Docsity tutors
The design and analysis of controlled release mechanisms (crms) for space vehicles. Crms are used to ensure a smooth and swift liftoff by gradually decreasing the restraining force as the vehicle moves away from the launchpad. The document also covers the requirements for crms, such as load capacity and maximum displacement, and compares the advantages and disadvantages of different types of crms, including the mandrel mechanism. Exercises on calculating the area under the restraining force vs. Displacement curve using simpson's rule.
Typology: Study Guides, Projects, Research
1 / 10
This page cannot be seen from the preview
Don't miss anything!
Project Grant Team
John S. Pazdar Patricia L. Hirschy Project Director Principal Investigator Capital Community College Asnuntuck Community College Hartford, Connecticut Enfield, Connecticut
This project was supported, in part, by the Peter A. Wursthorn National Science Foundation Principal Investigator Opinions expressed are those of the authors Capital Community College and not necessarily those of the Foundation Hartford, Connecticut
Spinoffs are relatively short learning modules inspired by the LTAs. They can be easily implemented to support student learning in courses ranging from prealgebra through calculus. The Spinoffs typically give students an opportunity to use mathematics in a real world context.
Jerry Keepers - AMATYC Writing Team Member Potomac State College, Keyser, West Virginia
Cyrus McCarter - AMATYC Writing Team Member Wake Technical Community College, Raleigh, North Carolina
Eric Thaxton - NASA Scientist/Engineer Kennedy Space Center, Florida
NASA – AMATYC – NSF
Force Versus Displacement
Background
Space vehicles are expensive to launch. The rockets, which are used to lift a vehicle into space, are only able to lift a certain maximum weight. Since both the vehicle's structure and payload contribute to the total weight, any decrease in structural weight would increase the payload weight that could be launched. As a result, it is important to design a vehicle and launch system so that the vehicle's structural weight is kept to a minimum. It is also important, where possible, to keep external forces on the vehicle to a minimum. External forces include the force of winds in the atmosphere and the jerking motion encountered when the bolts, which hold the rocket in place before launch, are blown loose. If the external forces can be reduced, then the vehicle’s structure will not need to be as strong. This in turn will allow the structural weight to be reduced. In summary, to maximize the payload weight which is typically less than 10 percent of the total vehicle weight at liftoff, it is necessary to minimize the external forces encountered during launch and flight.
Just before liftoff, the rocket engines are ignited and they build up thrust to full power in about 4. seconds. During the buildup, the engines ignite at different times, so the thrust is uneven. If the vehicle were just resting on the launch pad, it would tilt and fall over while the engines were building up thrust. Therefore, the vehicle must be held down until all of the engines are balanced, working properly, and up to full power. When all the conditions are go, the vehicle is released.
Release Mechanisms
There are two general types of release mechanisms: soft and hard. A hard release is an instant release at full power. Typically, the hold down bolts of the restraining mechanism are secured by explosive nuts that are blown away to release the vehicle. A hold down bolt with an explosive nut is referred to as a pyrobolt. There is then a sudden jerk as the vehicle accelerates off the launch pad. This is analogous to what would happen at a tractor-pull contest if the cable attaching the tractor to the load suddenly broke. If the cable broke, the tractor would lurch ahead and the driver would be slammed against the back of the seat. Much more force is involved in launching a space vehicle. This sudden acceleration, or jerk, is hard on both payload and passengers. In order to mitigate the jerk, a controlled (soft) release mechanism, CRM, is added to the hard release structure. The diagram in Figure 1 on the next page shows the general components of a release mechanism and their relative positions. If a soft release mechanism is used in a launch, there would be little or no jerk. Then, it is possible that the structural weight of the vehicle could be reduced and its payload capacity increased.
NASA – AMATYC – NSF
The new Evolved Expendable Launch Vehicle (EELV) is now on NASA's drawing boards. NASA scientists are presently evaluating several release mechanisms. To maximize the payload, the EELV will use eight controlled release mechanisms (CRMs), not just a simple hard release system. Figure 2 shows a simplified diagram of the launch forces acting on each CRM. The divisions by 8 shown in the diagram assume that the launch forces are distributed equally to each of the eight CRMs.
Figure 2: Launch Force Diagram
At the moment when the pyrobolts are blown away, the CRM restraining force together with one-eighth of the vehicle weight should equal one-eighth of the upward thrust of the rocket. The restraining forces of each CRM will diminish to zero, the net upward force will increase, and the vehicle will ascend.
Exercise
( Vehicle Weight )/8 CRM Restraining Force
CRM
( Full Engine Thrust )/
NASA – AMATYC – NSF
Section II
Characteristics of a CRM Restraining Force vs. Displacement Graph
The graphs of the force versus displacement functions in Figure 3 below represent the same three forces that are shown on the previous page in Figure 2. These graphs pertain to any one of the eight CRMs and assume that the forces are equally distributed to each CRM. Notice that at 0 displacement, one- eighth of the vehicle’s weight added to the restraining force equals one-eighth of the full thrust. The graph of the Restraining Force vs. Displacement function is typical of a good soft release mechanism.
Figure 3: Launch Forces on Rocket
Important characteristics of a CRM restraining force vs. displacement graph:
F o r c e
NASA – AMATYC – NSF
Ground Side (Shaft)
Flight Side (Tube)
Section III
Controlled Release Mechanism for the Evolved Expendable Launch Vehicle (EELV)
The general requirements for the controlled release mechanism that will be used on the EELV are:
An example of one type of CRM is shown at the right. The drawing is not to scale. The flight side of the mechanism is attached to the rocket, and the ground side is attached to the launchpad and remains on the ground.
Mandrel Mechanism
Description: The flight side is a tapered 300 Series stainless steel tube. The ground side is a hardened steel shaft with a hemispherical end. At liftoff the shaft is pulled through the tube. The tube then becomes plastically deformed. The wall thickness of the tube can be designed to “tune” the Force-Displacement diagram. Narrower walls provide less restraint, thicker walls provide more restraint. The taper (decreasing wall thickness) of the steel tube creates a restraining force that decreases with displacement (shaft movement).
Advantages of the Mandrel Mechanism:
Disadvantages of the Mandrel Mechanism:
NASA – AMATYC – NSF
Exercises (2 - 5)
These exercises involve working with the restraining force functions of four (4) controlled release mechanisms. Each of the Exercises 2 through 6 consists of four Parts, a - d.
a) Sketch the graph of the restraining force function given in each exercise on the interval [0,7]. The restraining force, Fr , is in pounds, and the displacement, x , is in inches. b) For each curve, use Simpson’s Rule with n = 6 to estimate 0 F dxr
7
include appropriate units with your answer.
c) Calculate an error bound for your estimates.
d) Find the exact areas by evaluating the definite integral on [0,7], and compare your answers to the estimates obtained from Simpson’s Rule.
Note: When Simpson’s Rule gives the exact value of the definite integral, rounding errors may produce slightly different answers for parts b and d.
a)
b) Simpson’s rule calculation: area estimate _______
c) Error Bound = ______
d) Exact value of area = _____
NASA – AMATYC – NSF
d) Exact value of area = ________
a)
b) Simpson’s rule calculation: area estimate _______
c) Error Bound = ________
d) Exact value of area = ________
Function from Exercise 2 ___________ Function from Exercise 3 ___________ Function from Exercise 4 ___________ Function from Exercise 5 ___________