
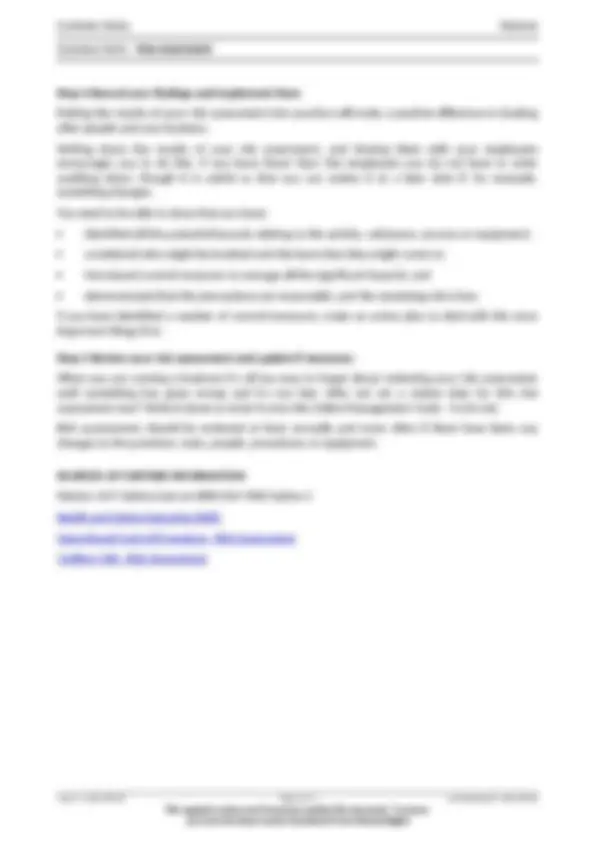
Study with the several resources on Docsity
Earn points by helping other students or get them with a premium plan
Prepare for your exams
Study with the several resources on Docsity
Earn points to download
Earn points by helping other students or get them with a premium plan
Community
Ask the community for help and clear up your study doubts
Discover the best universities in your country according to Docsity users
Free resources
Download our free guides on studying techniques, anxiety management strategies, and thesis advice from Docsity tutors
Risk Assessment fillable forms etc
Typology: Cheat Sheet
1 / 3
This page cannot be seen from the preview
Don't miss anything!
This Guidance Note should be read in conjunction with the Risk Assessment Operational Control Procedure. INTRODUCTION A risk assessment is a careful examination of anything, in your work and environment that could cause harm to people, taking into account its severity. It enables you to decide whether you have taken enough precautions or should do more to prevent harm. It is an important step in protecting employees and your business, as well as complying with the law. Risk assessments help you focus on the issues that really matter in the workplace, the ones with the potential to cause harm. In many instances risks can be easily controlled. The law does not expect the elimination of all risk, but you are required to protect people as far as is reasonably practicable. Accidents and ill health can ruin lives and affect business if output is lost, machinery is damaged, insurance costs increase or you have to go to court, then the cost is very high. There is a legal requirement to carry out suitable and sufficient risk assessments for all hazardous activities. If there are five or more employees the risk assessment must be recorded. PROCEDURAL STEPS You need to ensure that any person required to undertake risk assessments has been provided with suitable training. Training may include the use of external providers such as Mentor. Training may also include on the job training in the process or activity to be assessed. Risk assessment has 5 steps: Step 1 Identify the hazards You need to work out how people could be harmed. When you work in a place every day it is easy to overlook some hazards: walk around your workplace and look at what could reasonably be expected to cause harm; ask your employees what they think. They may have noticed things that are not immediately obvious to you; check manufacturers' instructions or data sheets for chemicals and equipment as they can be helpful in identifying hazards; look back at your accident and ill health records as these often help to identify the less obvious hazards; and remember to think about health hazards, for example, high noise levels or exposure to harmful substances, as well as safety hazards. If it looks dangerous, it probably is. Issue: 3 2021-08-18 Page 1 of 3 Last Reviewed: 2021-08- We regularly review and if necessary update this document. To ensure
Step 2 Decide who might be harmed and how For each hazard you need to be clear about who might be harmed, it will help you to identify the best way of managing the risk. That doesn't mean listing everyone by name, but rather identifying groups of people, for example, people working in the storeroom or factory. In each case, identify how they might be harmed, that is, what type of injury or ill health might occur, for example, store room employees may suffer back injuries from the repeated lifting of equipment or items. Some individuals have special requirements and may be at particular risk: new and young employees; new or expectant mothers; and people with disabilities/existing health issues. Extra thought will be needed for some people: cleaners, visitors, contractors, maintenance employees etc. who may not be in the workplace all the time; and members of the public, if they could be harmed by your activities. Step 3 Evaluate the risks and decide on precautions Having identified the hazards, you then need to decide what, if anything you can do about them. The law requires you to do everything reasonably practicable to protect people from harm. Compare what you are doing with good practice. Take into account the controls you have in place and how your workplace risks are managed. To achieve this you could: try a less hazardous option, for example, switch to using a different chemical or process; prevent access to the hazard, for example, by guarding it; organise work to reduce exposure to the hazard, for example you could put barriers between pedestrians and traffic; develop safe systems of work, if people understand how important it is to work safely, it’s more likely they will do; issue personal protective equipment (PPE), such as clothing, footwear, goggles etc. and ensure it is worn where required; and provide welfare facilities, for example, first aid and washing facilities for the removal of contamination. Improving health and safety need not cost a lot. For instance, placing a mirror on a dangerous blind corner to help prevent vehicle accidents is a low-cost precaution, considering the risks. Failure to take simple precautions can cost a lot more if an accident does happen. Involve employees so that you can be sure that what you propose to do will work in practice and won't introduce any new hazards Issue: 3 2021-08-18 Page 2 of 3 Last Reviewed: 2021-08- We regularly review and if necessary update this document. To ensure