
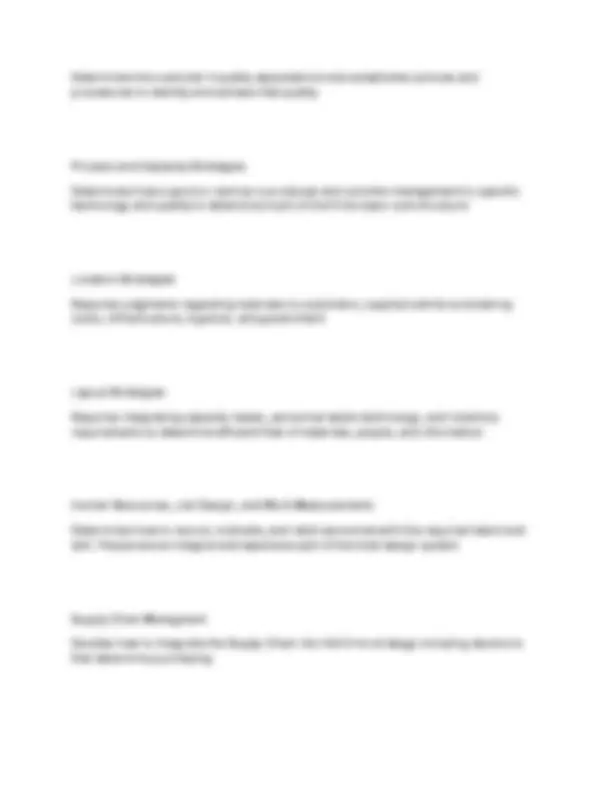
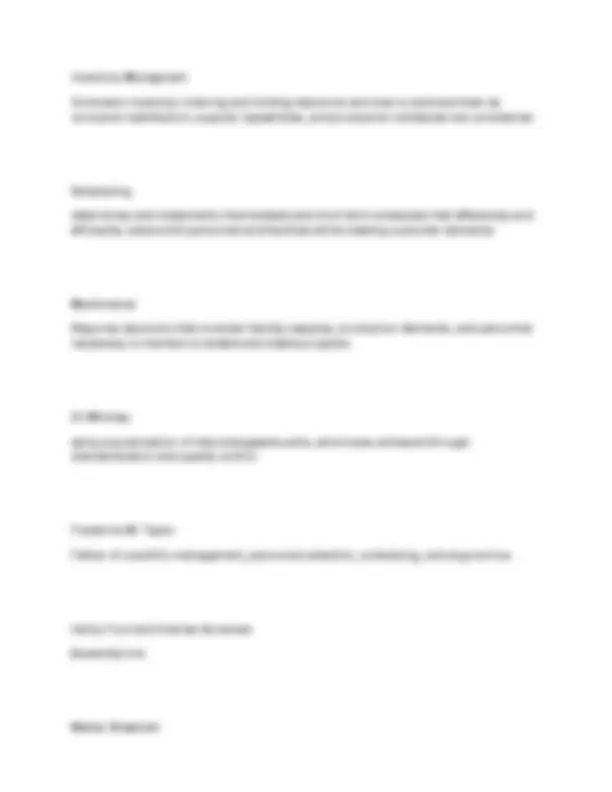
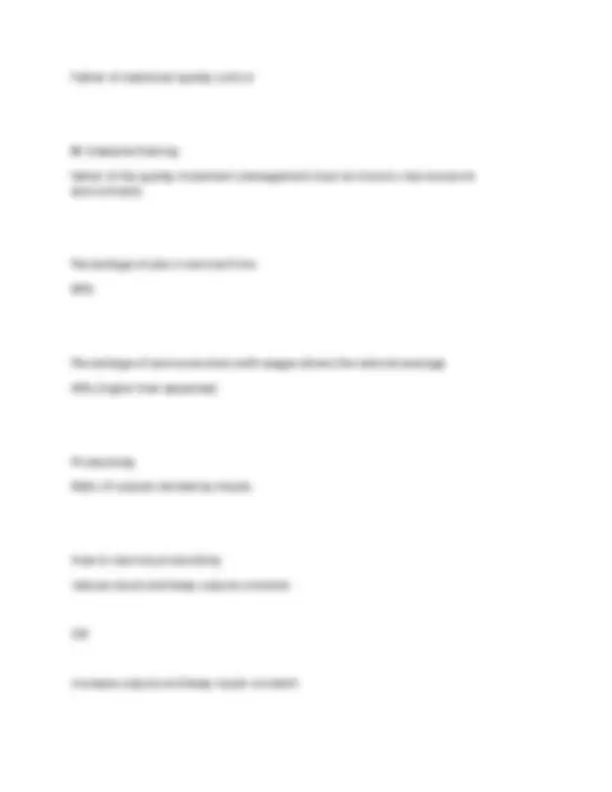
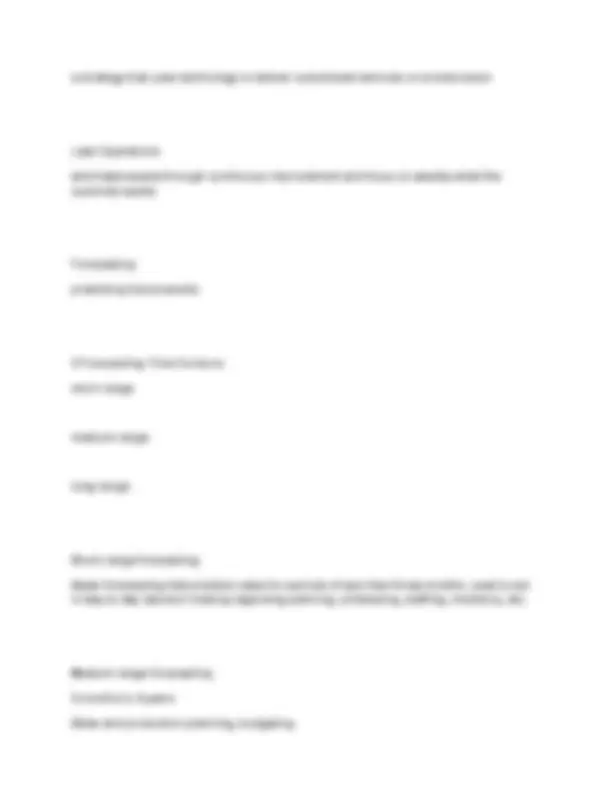
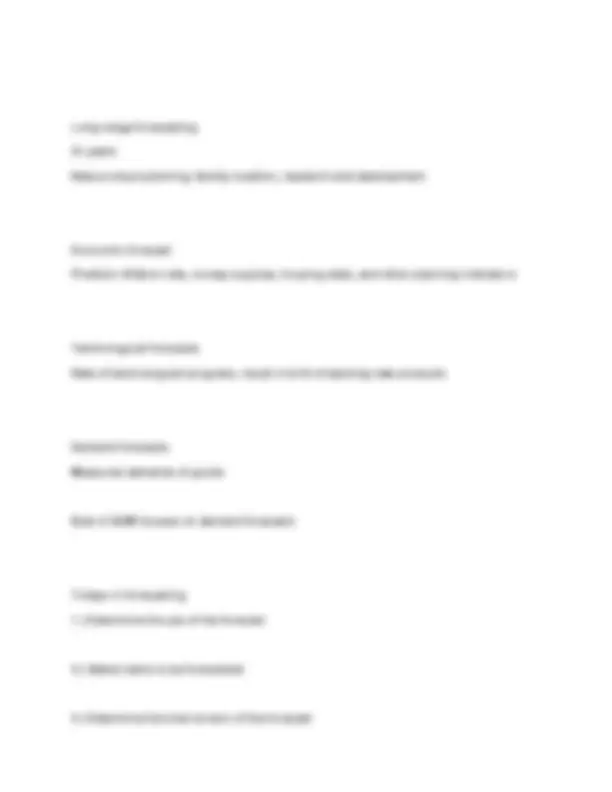
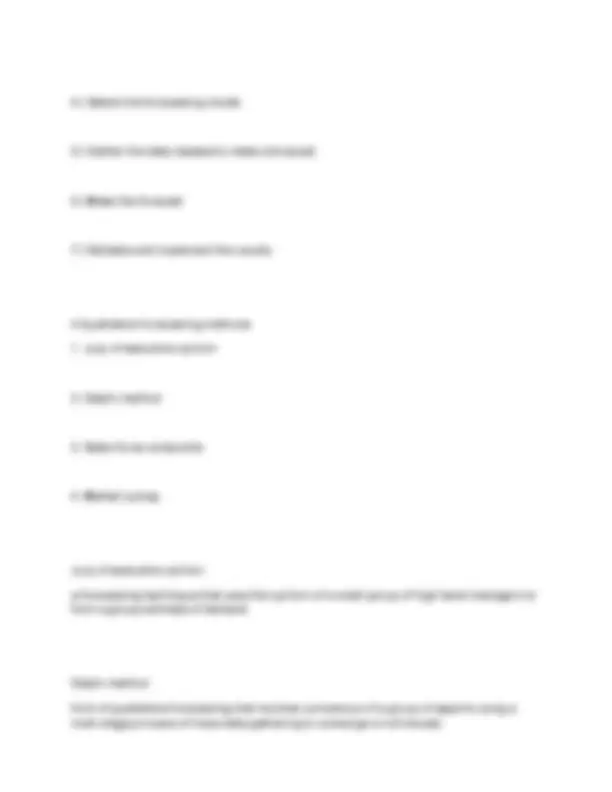
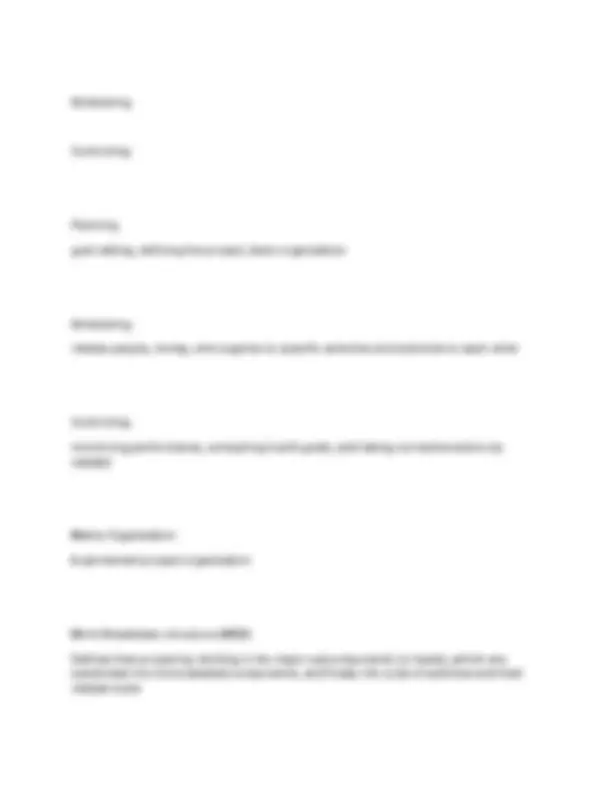
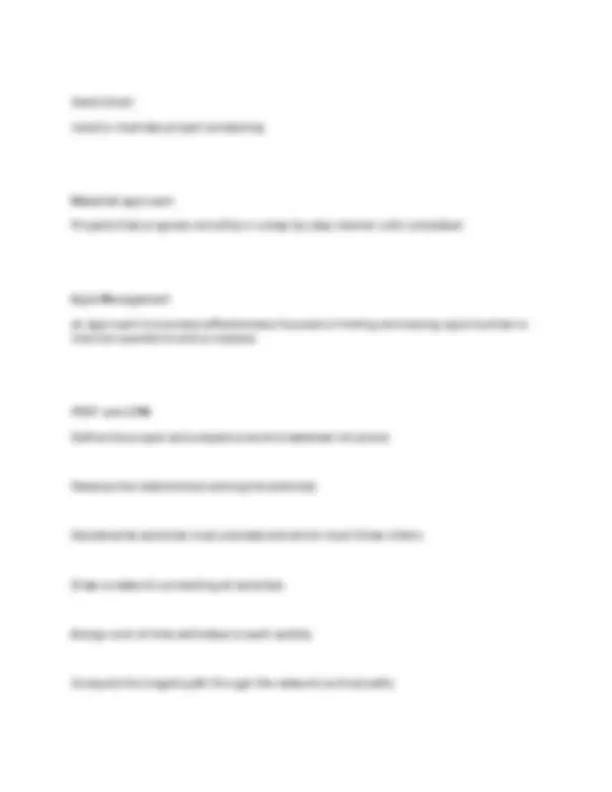
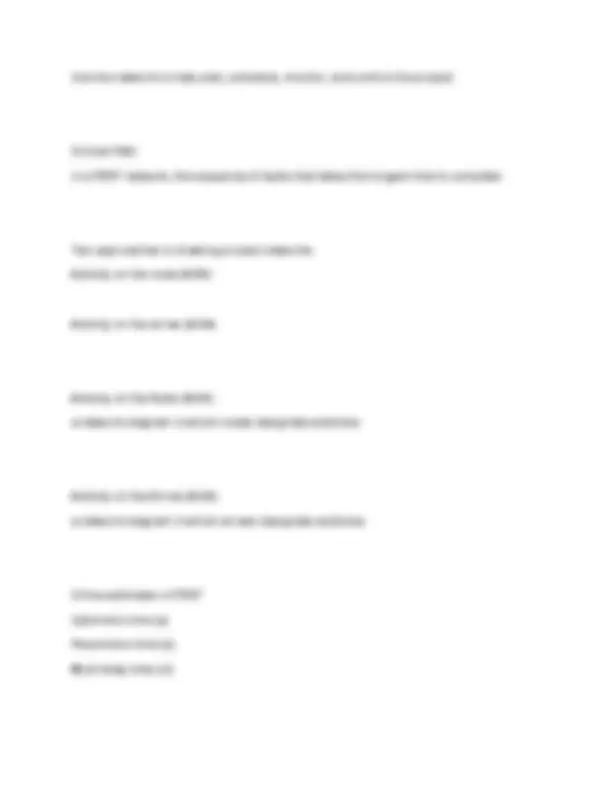
Study with the several resources on Docsity
Earn points by helping other students or get them with a premium plan
Prepare for your exams
Study with the several resources on Docsity
Earn points to download
Earn points by helping other students or get them with a premium plan
Community
Ask the community for help and clear up your study doubts
Discover the best universities in your country according to Docsity users
Free resources
Download our free guides on studying techniques, anxiety management strategies, and thesis advice from Docsity tutors
SCM 186 MIDTERM EXAM WITH COMPLETE SOLUTIONS
Typology: Exams
1 / 17
This page cannot be seen from the preview
Don't miss anything!
Operations Management the set of activities that creates value in the form of goods and services by transferring inputs into outputs
To create goods and services, all organizations perform three functions: Marketing
Production/Operations
Finance/Accounting
Marketing generates demand or at least takes order for the product
Production/Operations creates, produces, and delivers the product
Finance/Accounting tracks how well the organization is doing, pays bills, collects the money
Supply Chain Global network of organization and activities that supply a firm with goods and services
Ten Strategic Operations Management Decisions
Design of Good and Services Defines much of what is required of operations in each of the other OM decisions
Managing Quality and Statistical Process Control
Inventory Managment Considers inventory ordering and holding decisions and how to optimize them as consumer satisfaction, supplier capabilities, and production schedules are considered
Scheduling determines and implements intermediate and short term schedules that effectively and efficiently utilize both personnel and facilities while meeting customer demands
Maintinence Requires decisions that consider facility capacity, production demands, and personnel necessary to maintain a reliable and stable progress
Eli Whitney early popularization of interchangeable parts, which was achieved through standardization and quality control
Frederick W. Taylor Father of scientific management, personnel selection, scheduling, and ergonomics
Henry Ford and Charles Sorensen Assembly line
Walter Shewhart
Father of statistical quality control
W. Edwards Deming father of the quality movement (management must do more to improve work environment)
Percentage of jobs in service firms 80%
Percentage of service workers with wages above the national average 42% (higher than expected)
Productivity Ratio of outputs divided by imputs
How to improve productivity reduce inputs and keep outputs constant
OR
increase outputs and keep inputs constant
Lean operations
Globalization Actions or processes that involve the entire world and result in making something worldwide in scope.
Rapid decline in cost in international collaboration
Supply Chain Partnering shorter product life cycles, demanding customers, and fast changes in technology, materials, and processes require supply-chain partners to be in tune with the needs of end-users
Sustainability achieving a balance between society and nature that will permit both to exist in harmony
Must make sure firms are ecologically sustainabler
Rapid Product Development Technology combined with rapid international communication of news, entertainment, and lifestyles is dramatically chopping away at the life span of products
Mass customization
a strategy that uses technology to deliver customized services on a mass basis
Lean Operations eliminates waste through continuous improvement and focus on exactly what the customer wants
Forecasting predicting future events
3 Forecasting Time Horizons short-range
medium-range
long-range
Short-range forecasting Sales forecasting that predicts sales for periods of less than three months; used to aid in day-to-day decision making regarding planning, scheduling, staffing, inventory, etc.
Medium-range forecasting 3 months to 3 years Sales and production planning, budgeting
4.) Select the forecasting model
5.) Gather the data needed to make a forecast
6.) Make the forecast
7.) Validate and implement the results
4 Qualitative forecasting methods
Jury of executive opinion a forecasting technique that uses the opinion of a small group of high-level managers to form a group estimate of demand
Delphi method form of qualitative forecasting that involves consensus of a group of experts using a multi-stage process of mass data gathering to converge on a forecast.
Sales force composite a forecasting technique based on salespersons' estimates of expected sales
salespeople from several regions are combined and averaged for an estimate
Market Survey Uses consumer input
Quantitative Forecasting Methods Time-series models
Associative Model
Naive Approach a forecasting technique which assumes that demand in the next period is equal to demand in the most recent period
Scheduling
Controlling
Planning goal setting, defining the project, team organization
Scheduling relates people, money, and supplies to specific activities and activities to each other
Controlling monitoring performance, comparing it with goals, and taking corrective action as needed
Matrix Organization A permanent project organization
Work Breakdown structure (WBS) Defines then project by dividing it into major subcomponents (or tasks), which are subdivided into more detailed components, and finally into a set of activities and their related costs
Gantt Chart Used to illustrate project scheduling
Waterfall approach Projects that progress smoothly in a step-by-step manner until completed.
Agile Management an approach to business effectiveness focused on finding and seizing opportunities to improve operations and processes
PERT and CPM Define the project and prepare a work breakdown structure
Develop the relationships among the activities
Decide what activities must precede and which must follow others
Draw a network connecting all activities
Assign cost-of-time estimates to each activity
Compute the longest path through the network (critical path)
Crashing A technique used to shorten the schedule duration for the least incremental cost by adding resources.
PERT and CPM pros and cons Pros: Useful scheduling and controlling projects
Straightforward concept
Graphical networks highlight inter-project relationships
Critical path and slack analysis
Project documentation
Application to a wide variety of projects
Useful in monitoring schedules and costs
Cons: Must be a clearly defined project
Precedence relationships must be specific
Time estimates are subjective to the managers
Inherent danger in the overemphasis of the critical path
3 parts of a waiting line of queuing system Arrivals or Inputs
Que discipline
Service facility design and statistical distribution of service times
Server Number of channels
Single server vs multi serve queuing systems single versus many servers
Single vs multi-phase systems One single person does it all versus multiple stages