
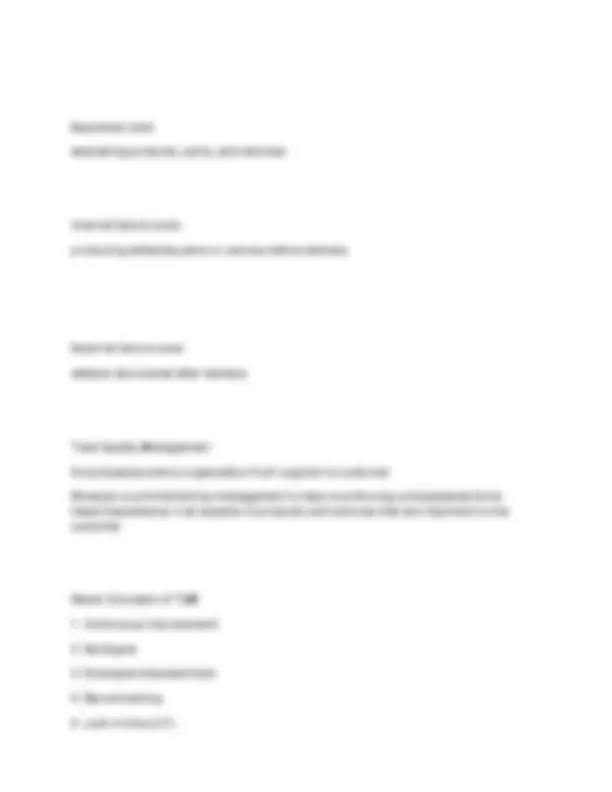
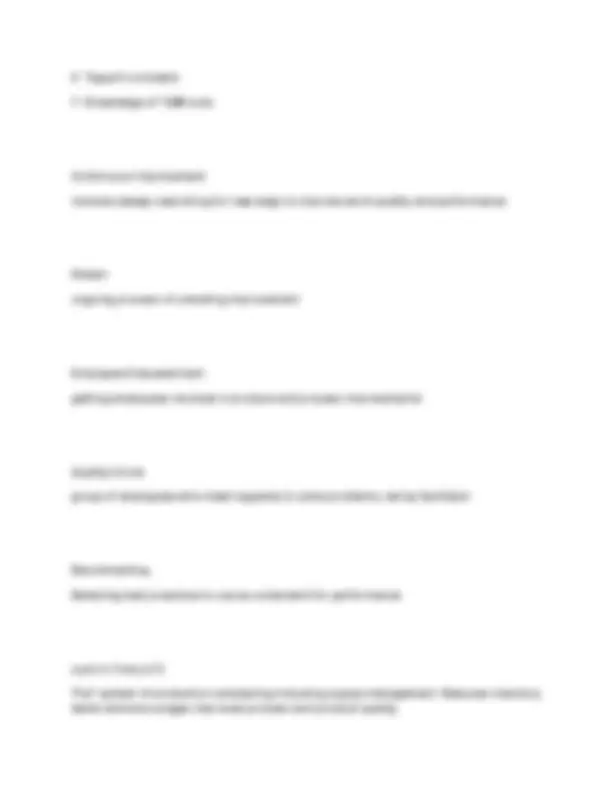
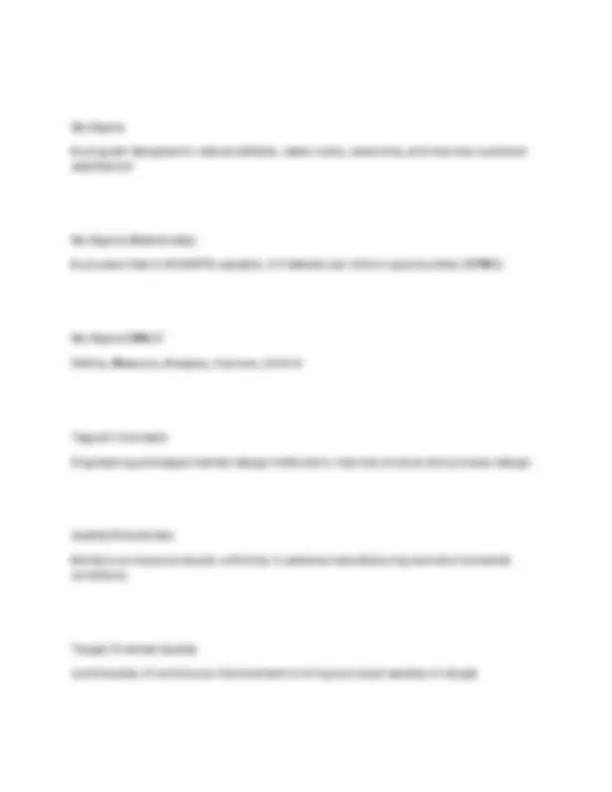
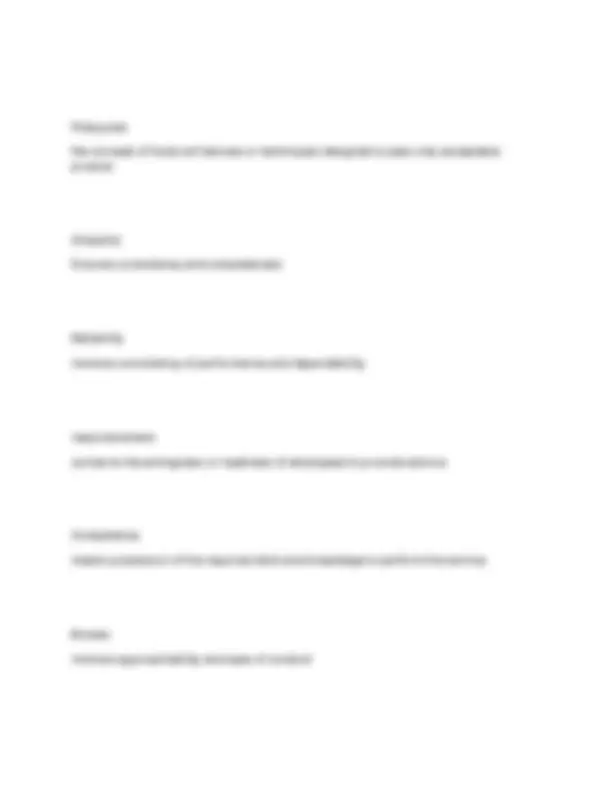
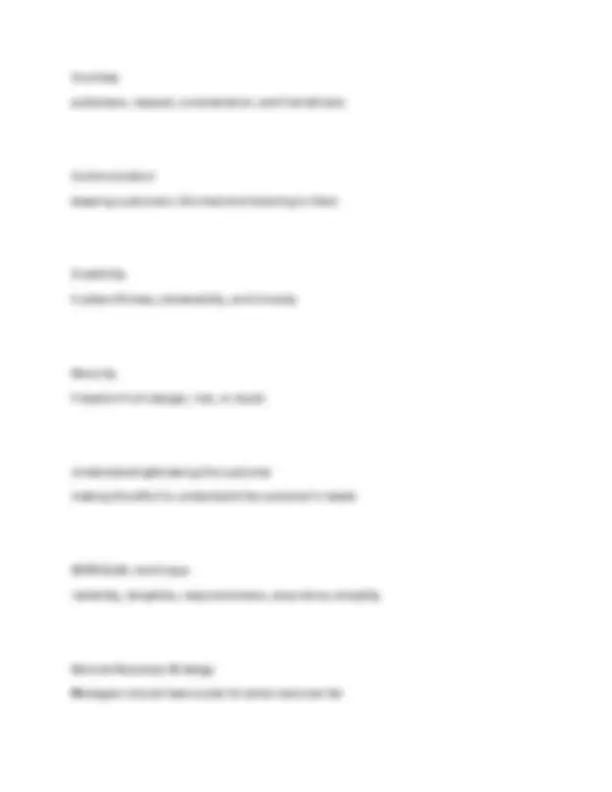
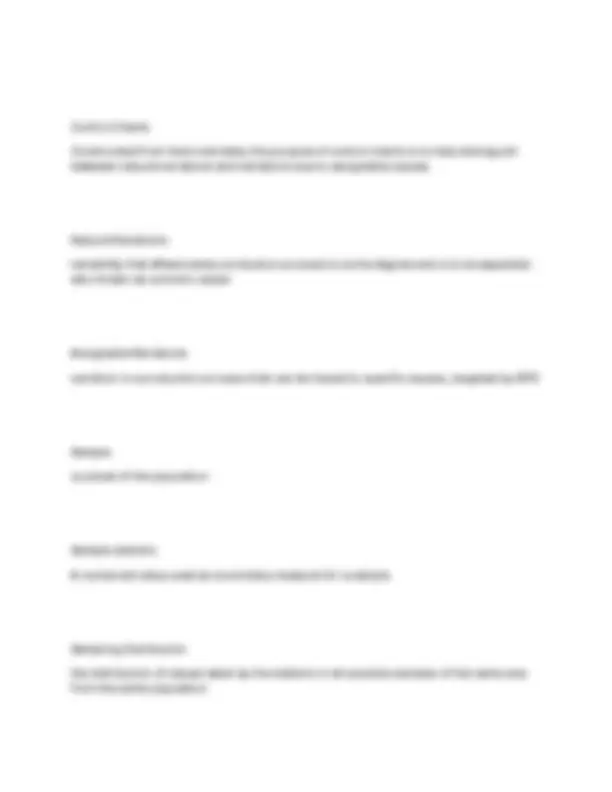

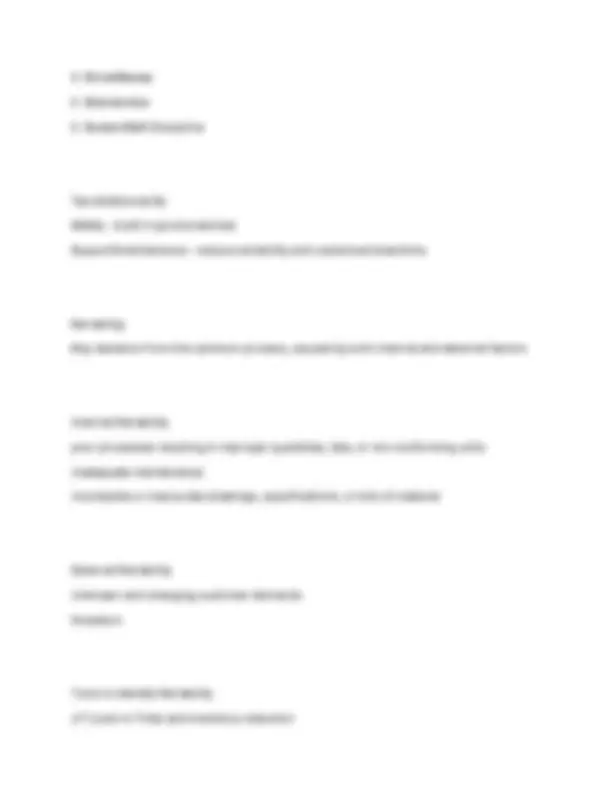
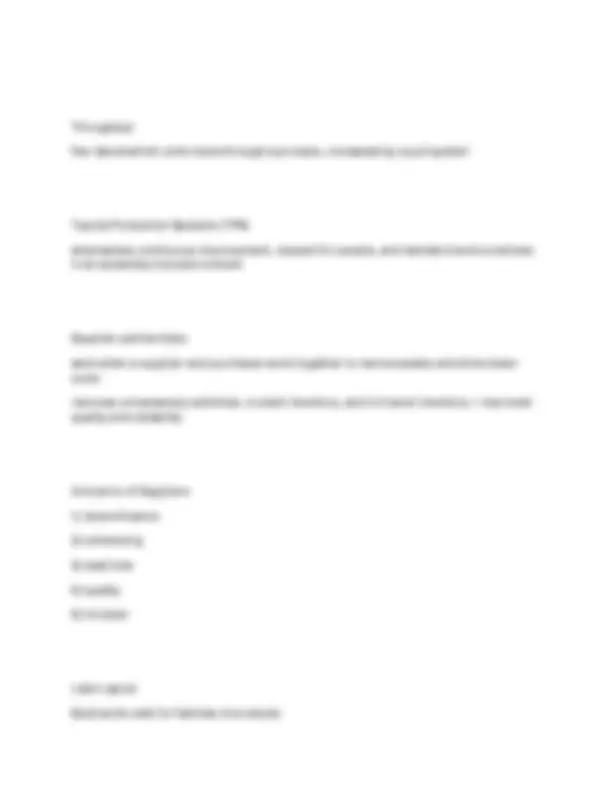
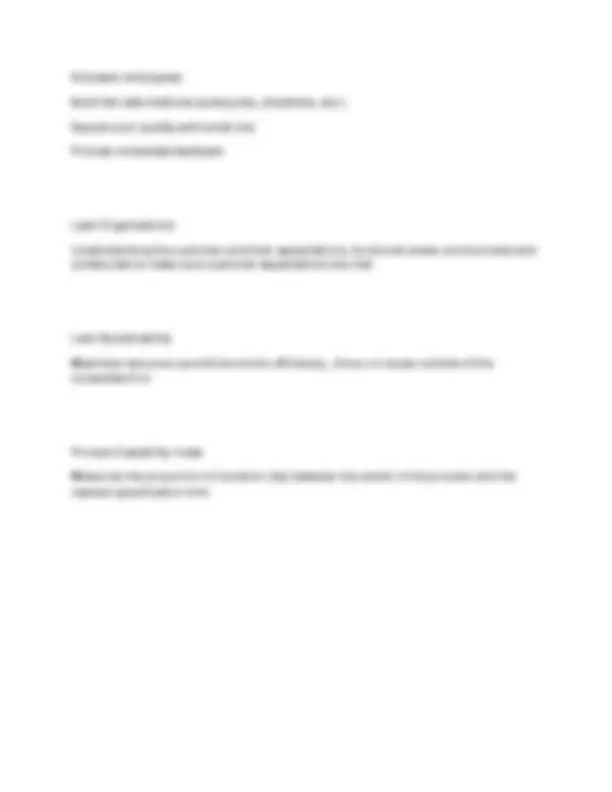
Study with the several resources on Docsity
Earn points by helping other students or get them with a premium plan
Prepare for your exams
Study with the several resources on Docsity
Earn points to download
Earn points by helping other students or get them with a premium plan
Community
Ask the community for help and clear up your study doubts
Discover the best universities in your country according to Docsity users
Free resources
Download our free guides on studying techniques, anxiety management strategies, and thesis advice from Docsity tutors
SCM186 Lehigh Exam 3 Questions And Accurate Answers 100% Verified
Typology: Exams
1 / 18
This page cannot be seen from the preview
Don't miss anything!
Quality the totality of features and characteristics of a product or service that bears on its ability to satisfy stated or implied needs
Managing Quality Supports differentiation, low cost, and response strategies
Organizational Practices Leadership, Mission statement, Effective operating procedures, Staff support, Training Yields: What is important and what is to be accomplished.
User Based Quality Management better performance, more features
Manufacturing Based Quality Management conformance to standards, making it right the first time
Product Based Quality Management
Precise and measurable attributes of the product
Quality Implies
ISO 9000 International Quality Standards Internationally recognized set of standards that encourage quality management procedures, detailed documentation, work instructions, and record keeping.
8 Management Principles
Prevention Costs reducing the potential for defects
Continuous Improvement involves always searching for new ways to improve work quality and performance
Kaizen ongoing process of unending improvement
Employee Empowerment getting employees involved in product and process improvements
Quality Circle group of employees who meet regularly to solve problems, led by facilitator
Benchmarking Selecting best practices to use as a standard for performance
Just-In-Time (JIT) 'Pull' system of production scheduling including supply management. Reduces inventory levels and encourages improved process and product quality
Six Sigma A program designed to reduce defects, lower costs, save time, and improve customer satisfaction
Six Sigma (Statistically) A process that is 99.9997% capable, 3.4 defects per million opportunities (DPMO)
Six Sigma DMAIC Define, Measure, Analyze, Improve, Control
Taguchi Concepts Engineering and experimental design methods to improve product and process design
Quality Robustness Ability to produce products uniformly in adverse manufacturing and environmental conditions
Target-Oriented Quality a philosophy of continuous improvement to bring a product exactly on target
a chart that describes the steps in a process
Histogram a distribution showing the frequency of occurrences of a variable
Statistical Process Control Chart a chart with time on the horizontal axis to plot values of a statistic
Statistical Process Control (SPC) Uses statistics and control charts to tell when to take corrective action, and drives process improvement. Types: Natural and Assignable
Inspection Involves examining items to see if an item is good or defective
Attributes Items are either good or bad, acceptable or unacceptable, does not address degree of failure
Variables Measures dimensions such as weight, speed, height, or strength
Poka-yoke the concept of foolproof devices or techniques designed to pass only acceptable product
Checklist Ensures consistency and completeness
Reliability involves consistency of performance and dependability
responsiveness concerns the willingness or readiness of employees to provide service
Competence means possession of the required skills and knowledge to perform the service
Access involves approachability and ease of conduct
Control Charts Constructed from historical data, the purpose of control charts is to help distinguish between natural variations and variations due to assignable causes
Natural Variations variability that affects every production process to some degree and is to be expected; also known as common cause
Assignable Variations variation in a production process that can be traced to specific causes, targeted by SPC
Sample a subset of the population
Sample statistic A numerical value used as a summary measure for a sample
Sampling Distribution the distribution of values taken by the statistic in all possible samples of the same size from the same population
Central Limit Theorem Regardless of the distribution of the population, the distribution of sample means drawn from the population will tend to follow a normal curve
μ = x bar (mean sampling distribution)
The mean of the sampling distribution will be the same as the population mean m
σ(x bar) =(σ)/√n The standard deviation of the sampling distribution will equal the population standard deviation divided by the square root of the sample size, n
Range (ri) the difference between the largest and smallest items in one sample
Steps in Building Control Charts
Lean Operations supply the customer with exactly what the customer wants when the customer wants it, without waste, through continuous improvement
Fundamental operation Issues Eliminate waste, remove variability, improve throughput
Eliminate Waste Waste is anything that does not add value from the customer point of view
Ohno's Seven Wastes
The 5Ss
Two Additional Ss Safety - build in good practices Support/maintenance - reduce variability and unplanned downtime
Variability Any deviation from the optimum process, caused by both internal and external factors
Internal Variability poor processes resulting in improper quantities, late, or non-conforming units inadequate maintenance incomplete or inaccurate drawings, specifications, or bills of material
External Variability Unknown and changing customer demands Disasters
Tools to Identify Variability JIT (Just-in-Time) and inventory reduction
Distance Reduction Large lots and long production lines with single-purpose machinery are being replaced by smaller flexible cells, often U-shaped and using group technology concepts
Flexible or Moveable Equipment cells designed to be rearranged as volume or designs change
Lean Layout-Impact on Employees employees may be cross-trained for flexibility and efficiency, improved communications facilitate the passing of important information about the process
Reduced Space and Inventory With reduced space, inventory must be in very small lots Units are always moving because there is no storage
Lean Inventory When Inventory is at the minimum level necessary to keep operations running
Reduce Lot Sizes Ideal situation is to have lot sizes of one pulled from one process to the next, use EOQ analysis to calculate desired setup time
Reduce Setup Costs Reducing setup costs reduces lot size and reduces average inventory and setup time can be reduced through preparation prior to shutdown and changeover
Lean Scheduling schedules must be communicated inside and outside the organization
Kanban Signals used in a pull-system (JIT) The card is an authorization for the next container of materials to be produced
Advantages of Kanban Small containers require tight schedules, smooth operations, little variability, shortages create an immediate impact. emphasis on meeting schedules, reducing lead time and setups, and economic material handling
Lean Quality Lean cuts the cost of obtaining good quality because Lean exposes poor quality
Lean Quality Tactics Use statistical process control