
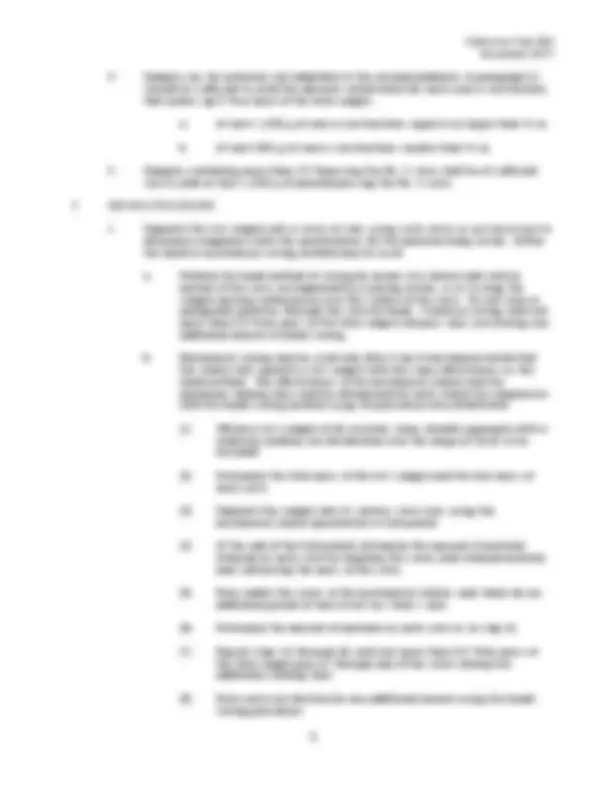
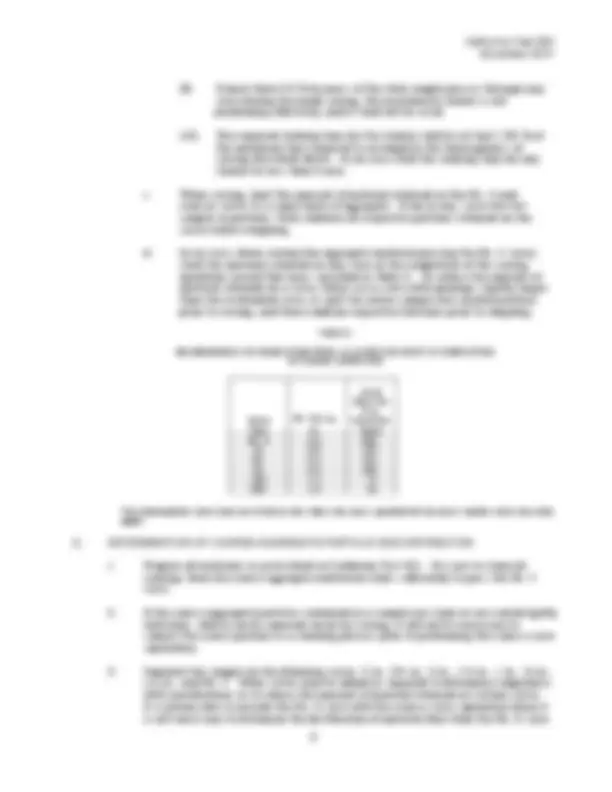
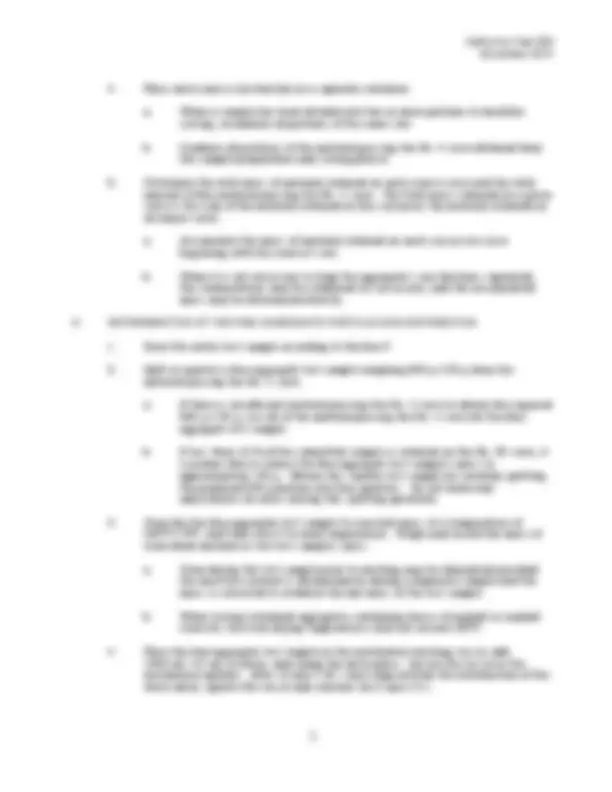
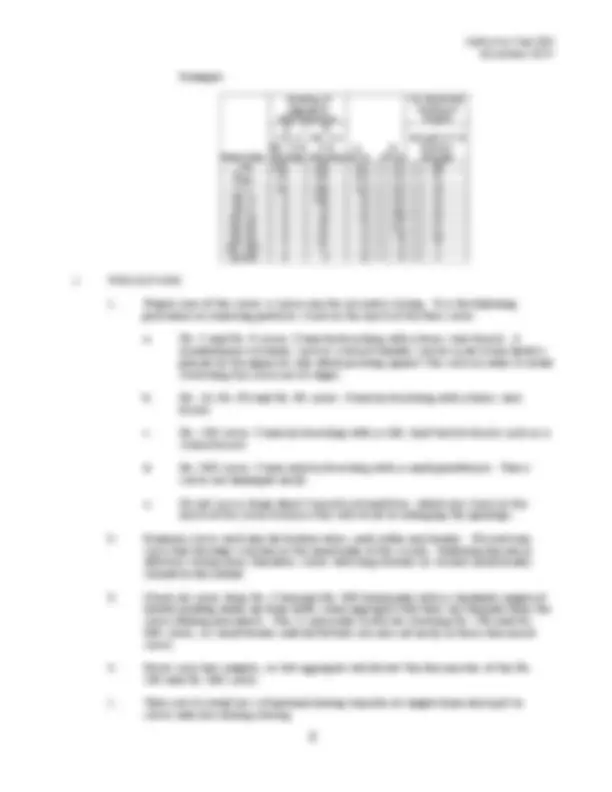
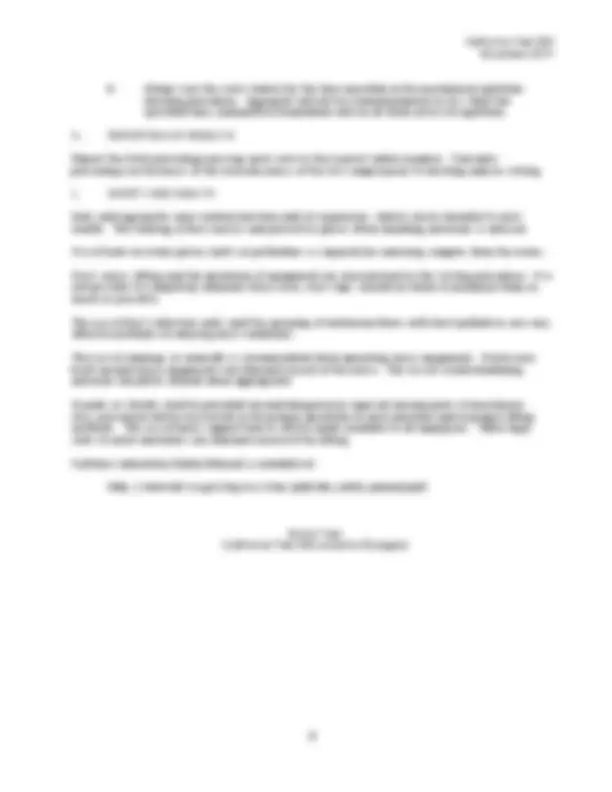
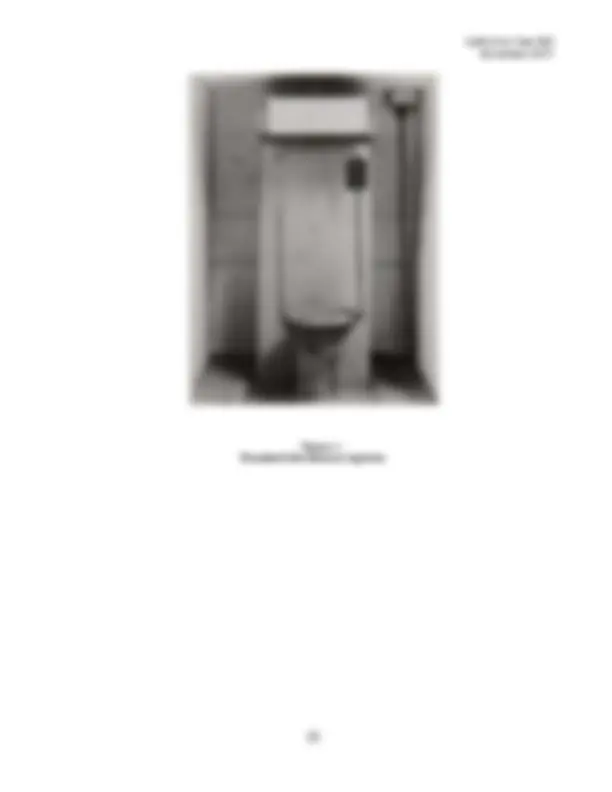
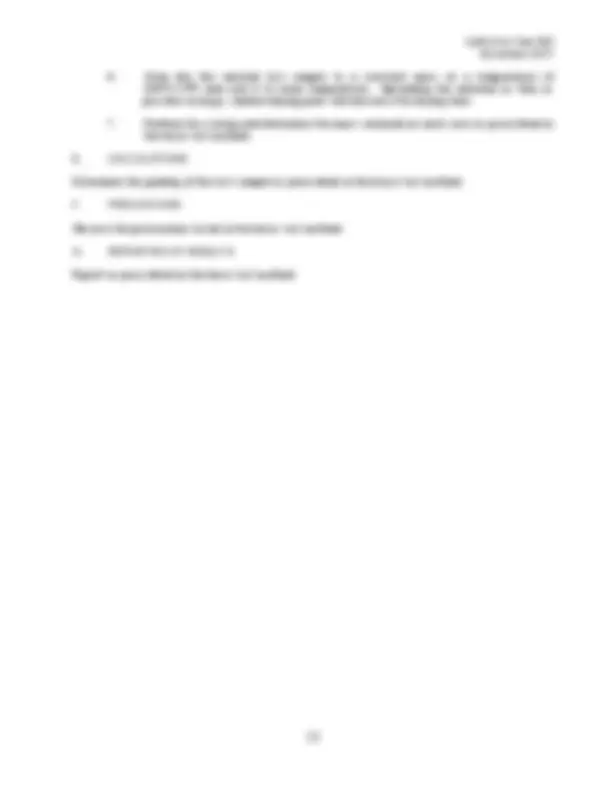
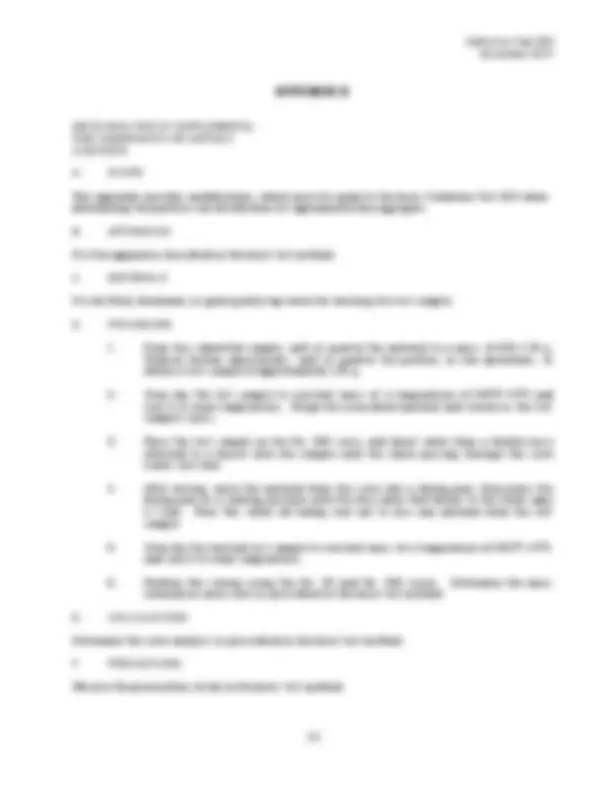
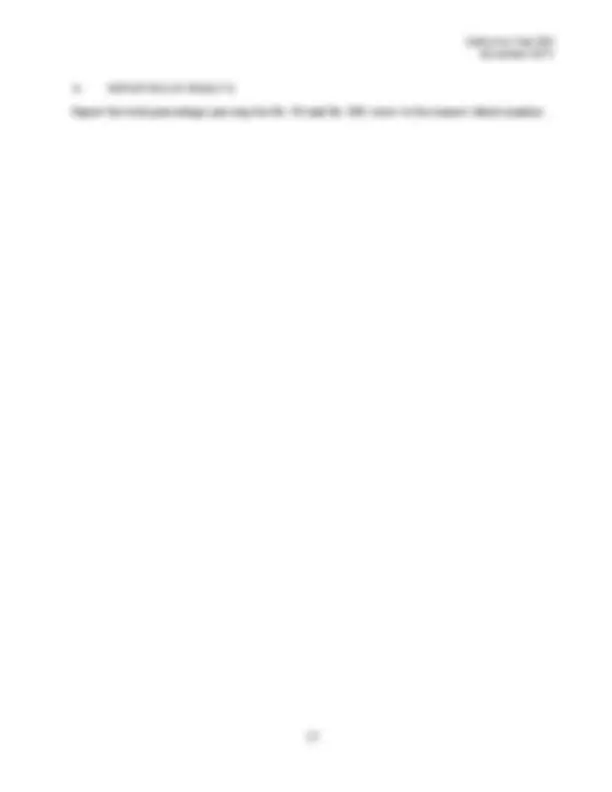

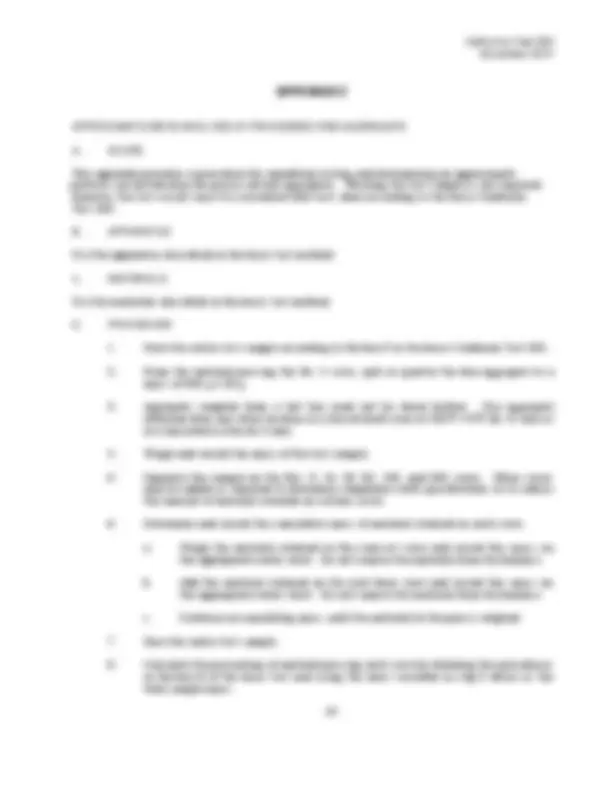
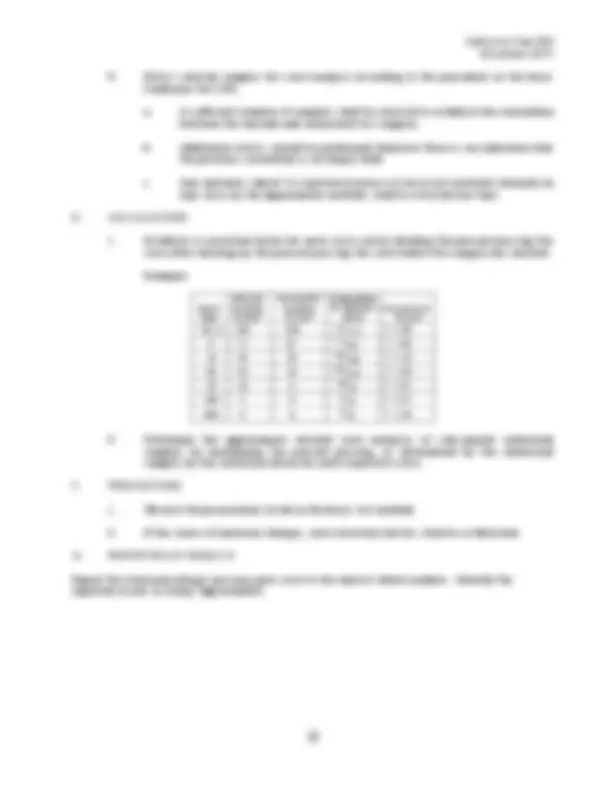
Study with the several resources on Docsity
Earn points by helping other students or get them with a premium plan
Prepare for your exams
Study with the several resources on Docsity
Earn points to download
Earn points by helping other students or get them with a premium plan
Community
Ask the community for help and clear up your study doubts
Discover the best universities in your country according to Docsity users
Free resources
Download our free guides on studying techniques, anxiety management strategies, and thesis advice from Docsity tutors
Method of Test for Sieve Analysis of Fine and Coarse Aggregates.
Typology: Summaries
1 / 20
This page cannot be seen from the preview
Don't miss anything!
STATE OF CALIFORNIA—BUSINESS, TRANSPORTATION AND HOUSING AGENCY November 2011
DIVISION OF ENGINEERING SERVICES Transportation Laboratory 5900 Folsom Boulevard Sacramento, California 95819-
This method, which includes modifications of AASHTO Designations T 11, T 27, T 30, and T 37, specifies the procedures for determining the particle-size distribution of fine and coarse aggregates.
Special procedures for testing aggregate from extracted bituminous mixtures, supplemental fine aggregate, glass spheres, and granular quicklime are included in Appendices A, B, C, and D, respectively. A procedure for expediting testing and providing an approximate particle-size distribution for processed fine aggregate is included in Appendix E.
B. REFERENCES
California Test 201- Soil and Aggregate Sample Preparation AASHTO M 92 - Standard Specification for Wire-Cloth Sieves for Testing Purposes AASHTO T 11 - Test for Materials Finer Than 75-μm (No. 200) Sieve in Mineral Aggregates by Washing AASHTO T 27 - Test for Sieve Analysis of Fine and Coarse Aggregates AASHTO T 30 - Test for Mechanical Analysis of Extracted Aggregate AASHTO T 37 - Test for Sieve Analysis of Mineral Filler for Hot Mix Asphalt (HMA)
C. APPARATUS
a. Each sieve shall be inspected visually for bent or distorted wires after each use. Replace any damaged or nonconforming sieves.
a. It is essential that the sieve shaker be designed so that its motion includes a bumping or bouncing action sufficient to keep the aggregate particles in motion on the surface of the sieves.
November 2011
b. Refer to Section F.1.b of this method for procedures to verify shaker efficiency.
D. MATERIALS
Distilled, deionized, or good-quality tap water shall be used for washing the fine-aggregate test sample.
E. SIZE OF SAMPLE
TABLE 1
Maximum Nominal Aggregate Size
Recommended Mass of Portion Retained on No. 4 Sieve Over 2 ½ in. 30,000 g 2 ½ in. 25,000 g 2 in. 20,000 g 1 ½ in. 15,000 g 1 in. 10,000 g 3/4 in. 5,000 g ½ in. 2,500 g 3/8 in. 1,000 g
November 2011
(9) If more than 0.5 % by mass of the total sample passes through any sieve during the hand sieving, the mechanical shaker is not performing effectively, and it shall not be used.
(10) The required shaking time for the shaker shall be at least 125 % of the minimum time required to accomplish the thoroughness of sieving described above. In no case shall the shaking time for any shaker be less than 5 min.
c. When sieving, limit the amount of material retained on the No. 4 and coarser sieves to a single layer of aggregate. If necessary, sieve the test sample in portions; then combine all respective portions retained on the sieves before weighing.
d. In no case, when sieving fine aggregate (material passing the No. 4 sieve), shall the material retained on any sieve at the completion of the sieving operation exceed that mass specified in Table 2. To reduce the amount of material retained on a sieve, either use a sieve with openings slightly larger than the overloaded sieve, or split the entire sample into smaller portions prior to sieving, and then combine respective fractions prior to weighing.
TABLE 2
MAXIMUM MASS IN GRAMS OF MATERIAL ALLOWED ON SIEVE AT COMPLETION OF SIEVING OPERATION*
Sieve Size
Wt. Per sq. in.
Total Mass for 8 in. Diameter Sieve No. 8 4.0 200 16 3.0 150 30 2.5 125 50 2.0 100 100 1.5 75 200 1.0 50
*For intermediate sieve sizes not listed in this table, the mass specified for the next smaller sieve size shall apply.
G. DETERMINATION OF COARSE-AGGREGATE PARTICLE-SIZE DISTRIBUTION
November 2011
a. When a sample has been divided into two or more portions to facilitate sieving, recombine all portions of the same size.
b. Combine all portions of the material passing the No. 4 sieve obtained from the sample preparation and sieving phases.
a. Accumulate the mass of material retained on each successive sieve beginning with the coarsest size.
b. When it is not necessary to keep the aggregate’s size fractions separated, the sized portions may be combined in succession, and the accumulated mass may be determined directly.
H. DETERMINATION OF THE FINE-AGGREGATE PARTICLE-SIZE DISTRIBUTION
a. If there is insufficient material passing the No. 4 sieve to obtain the required 500 g ± 25 g, use all of the material passing the No. 4 sieve for the fine- aggregate test sample.
b. If less than 10 % of the submitted sample is retained on the No. 30 sieve, it is permissible to reduce the fine-aggregate test sample’s mass to approximately 125 g. Obtain this smaller test sample by carefully splitting the prepared 500 g portion into four quarters. Do not make any adjustments for mass during this splitting operation.
a. Oven-drying the test sample prior to washing may be eliminated provided the moisture content is determined by drying a duplicate sample and the mass is corrected to establish the dry mass of the test sample.
b. When testing reclaimed aggregates containing traces of asphalt or asphalt concrete, the oven-drying temperature shall not exceed 100˚F.
November 2011
b. Compute the percentage of material passing each sieve as follows:
P = 100 – R
Where:
P = Percentage of test sample passing the sieve.
R = Percentage of test sample retained on the sieve.
a. Compute the percentage, by mass, represented by each aggregate-size fraction based on the total sample mass as received.
Example:
Fraction
Aggregate Size (^) Percent of Total Pass Retained Sample
Mass in Grams A 1 in. No. 4 6,600 66 % B No. 4 -- 3,400 34 % Total Sample -- -- 10,000 100 %
b. Then, take each aggregate size in turn and multiply the percent passing each sieve (as determined by the sieve analysis on the test sample) by the percentage of that aggregate size found to be present in the “as-received” sample.
Example:
Sieve Size
1 Grading of Aggregate Size Fraction “A”
2 Percent of Total Sample
3 Products of Items 1 and 2 1 in. 100 66 % 66 ¾ in. 94 66 % 62 3/8 in. 24 66 % 16 No. 4 3 66 % 2 No. 8 3 66 % 2 No. 16 3 66 % 2 No. 30 2 66 % 1 No. 50 2 66 % 1 No. 100 1 66 % 1 No. 200 0 66 % 0
c. Add the products thus obtained on corresponding sieve sizes as shown in the following example. These sums, as shown in the last column of the example, constitute the “as received” grading of the original sample.
November 2011
Example:
Sieve Size
Grading of Aggregate Size Fractions
A 66 %
B 34 %
"As Received" Grading of Original A 1 in. x No. 4 % Passing
B No. 4 x 0 % Passing
Sample A + B Percent Passing 1 in. 100 100 66 + 34 = 100 ¾ in. 94 100 62 +^34 =^96 3/8 in. 24 100 16 + 34 = 50 No. 4 3 100 2 + 34 = 36 No. 8 3 70 2 + 24 = 26 No. 16 3 56 2 + 19 =^21 No. 30 2 41 1 + 14 =^15 No. 50 2 27 1 + 9 =^10 No. 100 1 17 1 + 6 = 7 No.200 0 8 0 + 3 = 3
J. PRECAUTIONS
a. No. 4 and No. 8 sieves: Clean by brushing with a brass wire brush. A rounded piece of wood, such as a brush handle, can be used if one hand is placed on the opposite side when pushing against the sieve in order to avoid stretching the sieve out of shape.
b. No. 16, No. 30 and No. 50 sieves: Clean by brushing with a brass wire brush.
c. No. 100 sieves: Clean by brushing with a stiff, short bristle brush such as a stencil brush.
d. No. 200 sieves: Clean only by brushing with a small paintbrush. These sieves are damaged easily.
e. Do not use a sharp object to push out particles, which are stuck in the mesh of the sieves because this will result in enlarging the openings.
November 2011
Figure 1 Standard Mechanical Agitator
November 2011
Figure 2 Mechanical Washing Vessel
November 2011
E. CALCULATIONS
Determine the grading of the test sample as prescribed in the basic test method.
F. PRECAUTIONS
Observe the precautions listed in the basic test method.
G. REPORTING OF RESULTS
Report as prescribed in the basic test method.
November 2011
This appendix specifies modifications, which must be made to the basic California Test 202 when determining the particle-size distribution of supplemental fine aggregate.
B. APPARATUS
Use the apparatus described in the basic test method.
C. MATERIALS
Use distilled, deionized, or good-quality tap water for washing the test sample.
D. PROCEDURE
E. CALCULATIONS
Determine the sieve analysis as prescribed in the basic test method.
F. PRECAUTIONS
Observe the precautions listed in the basic test method.
November 2011
This appendix specifies the modifications, which must be made to the basic California Test 202 when determining the particle-size distribution of glass spheres (beads), for reflectorizing paint markings on pavements.
B. APPARATUS
Use the apparatus described in the basic test method, except that the balance shall read to 0.1 g.
C. MATERIALS
No special materials are required for this test.
D. SIZE OF SAMPLE
E. PROCEDURE
a. Do not wash glass spheres.
F. CALCULATIONS
Determine the grading of the test sample as prescribed in the basic test method.
G. PRECAUTIONS
Observe the precautions listed in the basic test method.
H. REPORTING OF RESULTS
Report as prescribed in the basic test method.
November 2011
This appendix specifies modifications that must be made to the basic California Test 202 when determining the particle-size distribution of granular quicklime.
B. APPARATUS
C. MATERIALS
No special materials are required for this test.
D. SIZE OF SAMPLE
The total mass of quicklime submitted for testing shall be not less than 5 lb.
E. PROCEDURE
a. Test the granular quicklime in its “as-received” condition. Do not wash or oven dry.
a. Use the sieves necessary to determine compliance with the specifications and additional intermediate sieves as needed to prevent overloading.
b. Sieving shall be accomplished by the mechanical sieving method. The sieving time shall be 10 min ± 30 s.
c. Take care that the quicklime particles are not crushed or abraded by excessive handling.
F. CALCULATIONS
Determine the grading of the test sample as prescribed in the basic test method.
G. PRECAUTIONS
Observe the precautions listed in the basic test method and these special precautions:
November 2011
This appendix provides a procedure for expediting testing and determining an approximate particle-size distribution for processed fine aggregates. Washing the test sample is not required; however, the test results must be correlated with tests done according to the basic California Test 202.
B. APPARATUS
Use the apparatus described in the basic test method.
C. MATERIALS
Use the materials described in the basic test method.
D. PROCEDURE
a. Weigh the material retained on the coarsest sieve and record this mass on the appropriate work sheet. Do not remove the material from the balance.
b. Add the material retained on the next finer sieve and record this mass on the appropriate work sheet. Do not remove the material from the balance.
c. Continue accumulating mass until the material in the pan is weighed.
November 2011
a. A sufficient number of samples shall be retested to establish the correlation between the washed and unwashed test samples.
b. Additional retests should be performed whenever there is an indication that the previous correlation is no longer valid.
c. Any material subject to rejection because of excessive material retained on any sieve, by the approximate method, shall be retested one time.
E. CALCULATIONS
Example:
Sieve Size
Washed Grading % Pass
Unwashed Grading % Pass
% By Wash % Without Wash
=Correction Factor No. 4 (^100 100 100) /100 = 1. 8 71 67 71 / 67 = 1. 16 56 50 56 / 50 = 1. 30 25 18 25 / 18 = 1. 50 10 6 10 / 6 = 1. 100 5 3 5 / 3 = 1. 200 3 2 3 / 2 = 1.
F. PRECAUTIONS
G. REPORTING OF RESULTS
Report the total percentages passing each sieve to the nearest whole number. Identify the reported results as being "approximate".