
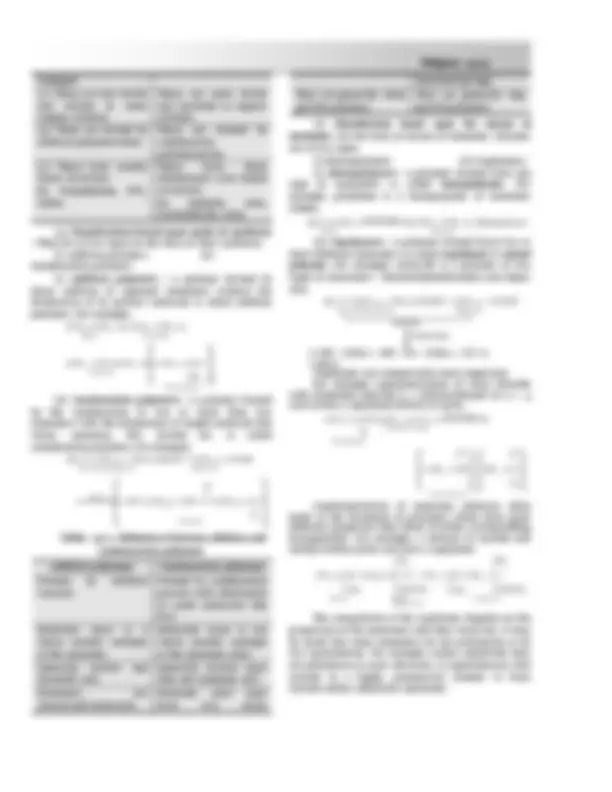
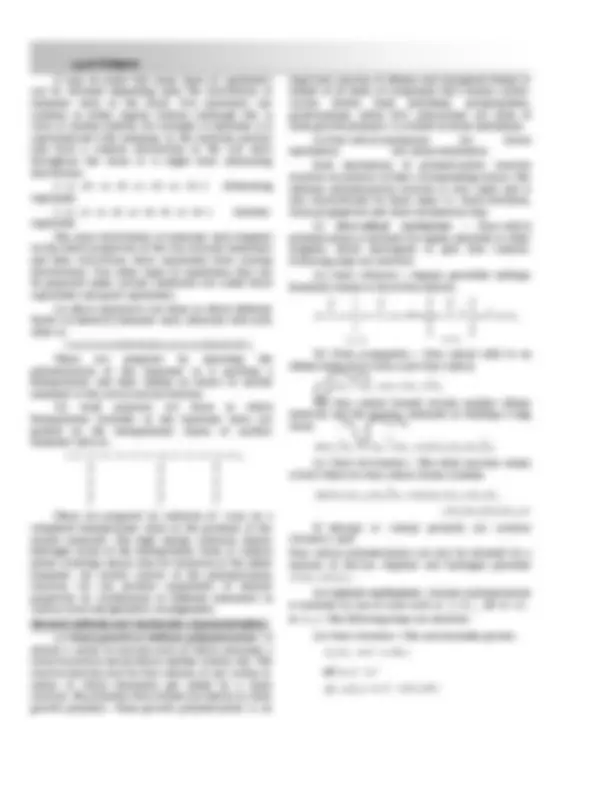
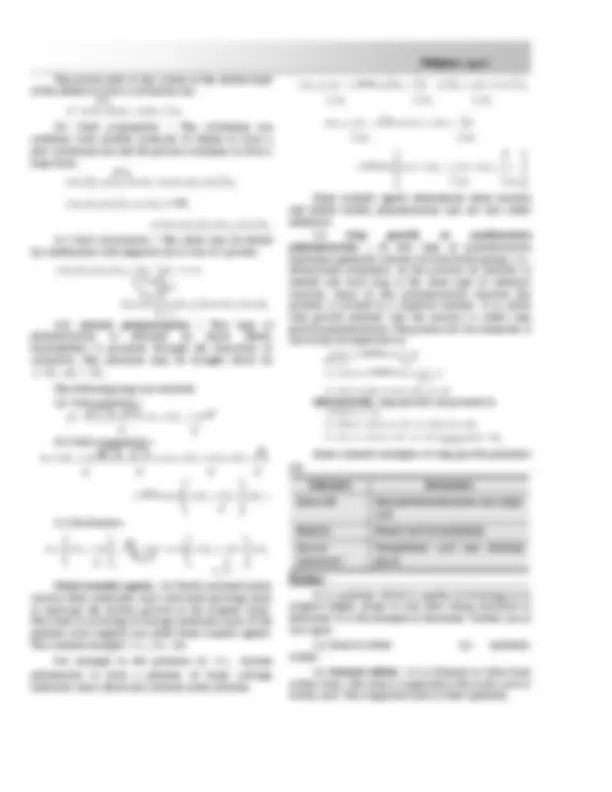
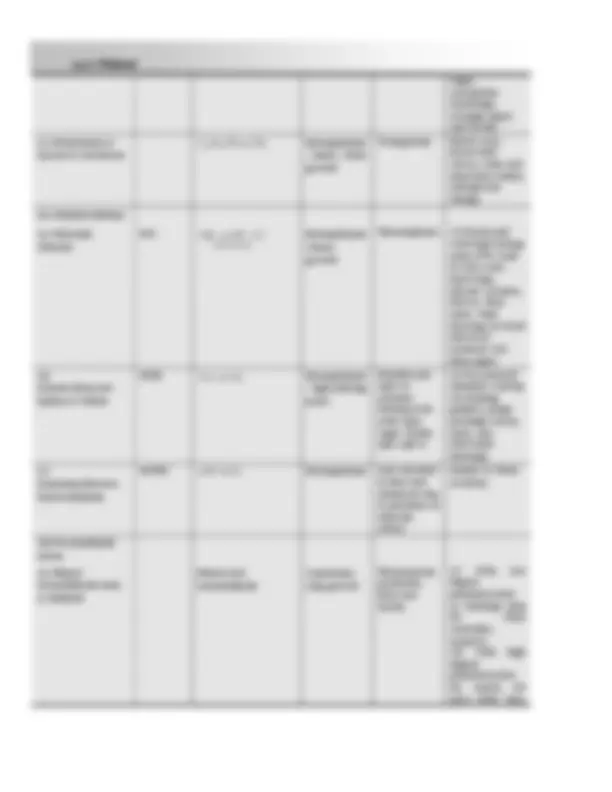
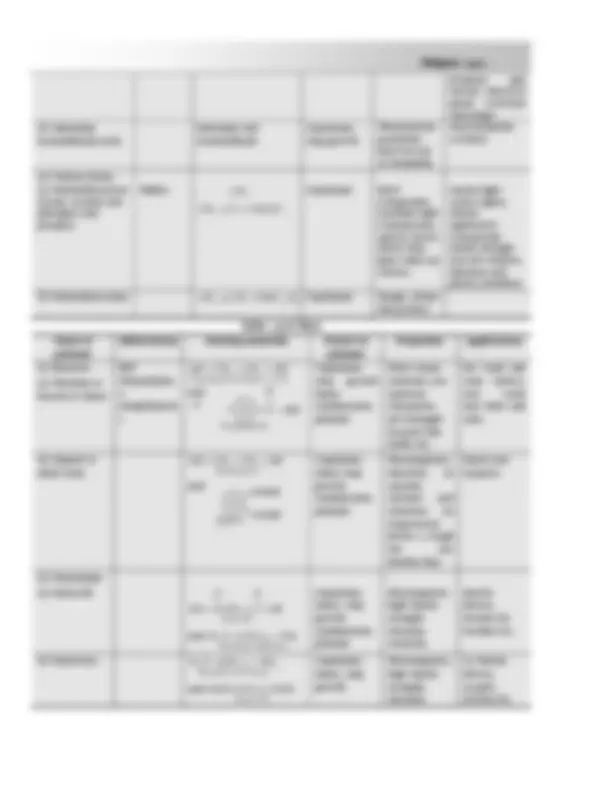
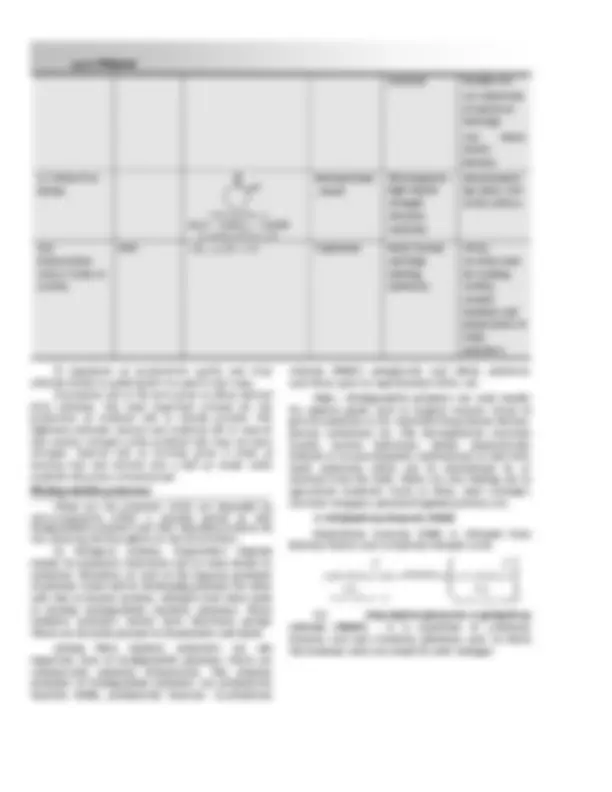
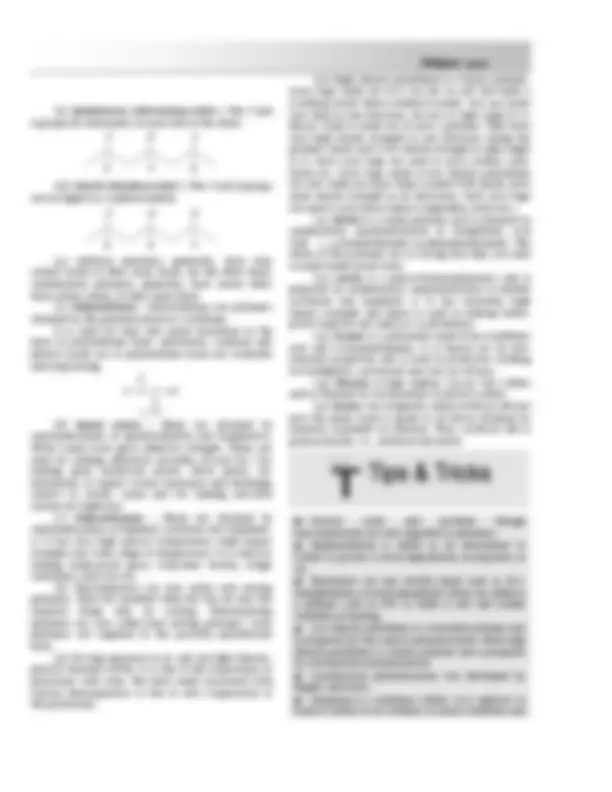
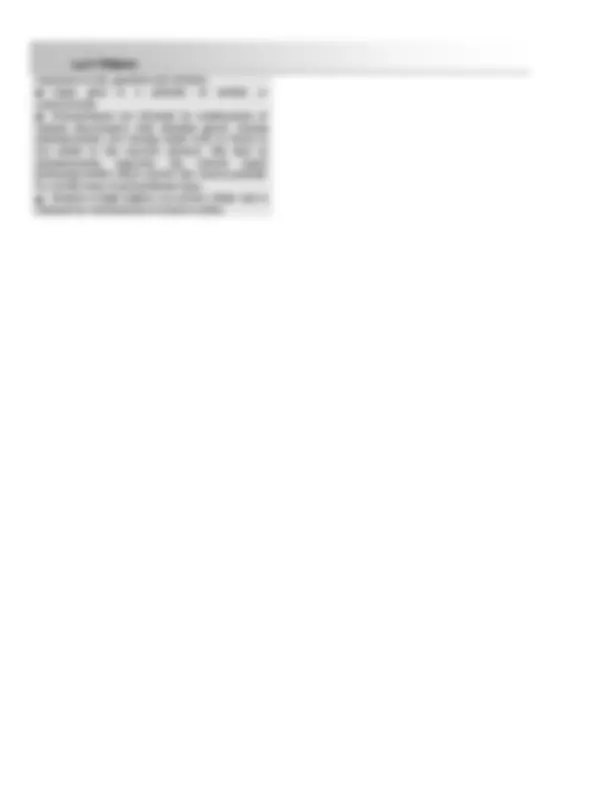
Study with the several resources on Docsity
Earn points by helping other students or get them with a premium plan
Prepare for your exams
Study with the several resources on Docsity
Earn points to download
Earn points by helping other students or get them with a premium plan
Community
Ask the community for help and clear up your study doubts
Discover the best universities in your country according to Docsity users
Free resources
Download our free guides on studying techniques, anxiety management strategies, and thesis advice from Docsity tutors
Simple and lucid explanation of the topic with diagrams, tables, tips etc.
Typology: Study notes
1 / 14
This page cannot be seen from the preview
Don't miss anything!
Polymers are compound of very high molecular masses formed by the combination of a large number of simple molecules. The simple molecules which combine to give polymers are called monomers. The process by which the simple molecule (i.e. monomers) are converted into polymers is called polymerisation. Example : Polyethylene All polymers are macromolecule but all macromolecules are not polymers because polymer consist repeating unit of monomer e.g., chlorophyll is a macromolecule but not a polymer.
(1) Classification based on source of availability : They are classified as (i) Natural polymers (ii) Synthetic polymers (iii) Semi-synthetic polymers (i) Natural polymers : The polymers obtained from nature (plants and animals) are called natural polymers. These polymers are very essential for life. They are as under. (a) Starch : It is polymer of glucose and it is food reserve of plant. (b) Cellulose : It is also a polymer of glucose. It is a chief structural material of the plant both starch and cellulose are made by plants from glucose produced during photosynthesis. (c) Proteins : These are polymers of -amino acids, they have generally 20 to 1000 amino acid joined together in a highly organized arrangement. These are building blocks of animal body and constitute an essential part of our food.
(d) Nucleic acids : These are polymers of various nucleotides. For example RNA and DNA are common nucleotides. It may be noted that polymers such as polysaccharides (starch, cellulose), proteins and nucleic acids etc. which control various life processes in plants and animals are also called biopolymers. (ii) Synthetic polymers : The polymers which are prepared in the laboratories are called synthetic polymers. These are also called man made polymers. For example polyethene, PVC nylon, teflon, bakelite terylene, synthetic rubber etc. (iii) Semisynthetic polymers : These polymers are mostly derived from naturally occurring polymers by chemical modifications. For example cellulose is naturally occurring polymers, cellulose on acetylation with acetic anhydride in the presence of sulphuric acid forms cellulose diacetate polymers. It is used in making thread and materials like films glasses etc. Vulcanized rubber is also an example of semisynthetic polymers used in making tyres etc. gun cotton which is cellulose nitrate used in making explosive. Semi-synthetic polymers : Rayon and other cellulose derivatives like cellulose nitrate, cellulose acetate etc., are semi-synthetic polymers. These are thermoplastic polymers. Viscose rayon in the form of a thin transparent film is known as cellophane. Cellophane is softened with glycerol. Unlike plastic sheets it absorbs water. Rayon : Rayon is a man made material which consists of purified cellulose in the form of long fibres. Cellulose is treated with cold NaOH solution to purify it and then treated with CS 2 to form a viscose solution.
Chapter
This is why rayon is sometimes called viscose rayon. This solution is allowed to pass through fine pores in metal cylinder, into a dilute solution of H 2 SO 4. This results in the formation of long fibres. Rayon fibre is chemically identical to cotton but has a shine like silk. As such rayon is also known as artificial silk. Rayon is used on a large scale for making textiles, tyre-chord, carpets and surgical dressings. Unlike fully synthetic polymers, it absorbs moisture and is bio-degradable. (2) Classification based upon structure : On the basis of structure of polymers these can be classified as (i) Linear polymers (ii) Branched chain polymers (iii) Cross linked polymers (i) Linear polymers : These are polymers in which monomeric units are linked together to form linear chain. These linear polymers are well packed and have high magnitude of intermolecular forces of attraction and therefore have high densities, high tensil (pulling) strength and high melting points. Some common example of linear polymers are high density polyethylene nylon, polyester, PVC, PAN etc. (ii) Branched chain polymers : These are polymers in which the monomers are joined to form long chains with side chains or branches of different lengths. These branched chain polymers are irregularly packed and therefore, they have low tensile strength, low density, boiling point and melting points than linear polymers. Some common examples are low density polythene, glycogen, starch etc. (Amylopectin). (iii) Cross linked polymers : These are polymers in which monomers unit are crosslinked together to form a three dimensional network polymers. These polymers are hard, rigid and brittle because of network structure e. g ., Bakelite, malamine formaldehyde resin etc. (3) Classification based upon molecular forces : Depending upon the intermolecular forces, the polymers have been classified into four type. (i) Elastomers (ii) Fibres (iii) Thermoplastics (iv) Thermosetting polymers (i) Elastomers : The polymers that have elastic character like rubber (a material that can return to its original shape after stretching is said to be elastic) are called elastomers. In elastomers the polymers chains are held together by weak intermolecular forces. Because of the presence of weak forces, the polymers can be easily stretched by applying small stress and regains their original shape when the stress is removed. The most important example of elastomers is natural rubber. (ii) Fibres : These are the polymers which have strong intermolecular forces between the chain. These forces are either hydrogen bonds or dipole-dipole interaction. Because of strong forces, the chains are closely packed giving them high tensil strength and less
elasticity. Therefore, these polymers have sharp melting points. These polymers are long, thin and thread like and can be woven in fabric. Therefore, these are used for making fibres. Example : Nylon 66, dacron, silk etc. (iii) Thermoplastics : These are the polymers which can be easily softened repeatedly when heated and hardened when cooled with little change in their properties. The intermolecular forces in these polymers are intermediate between those of elastomers and fibres. There is no cross linking between the chain. The softening occurs as the polymer chain move more and more freely because of absence of cross link. When heated, they melt and form a fluid which can be moulded into any desired shapes and then cooled to get the desired product. Example : Polythene, polystyrene, PVC, teflon etc. (iv) Thermosetting polymers : These are the polymers which undergo permanent change on heating. They become hard and infusible on heating. They are generally prepared from low molecular mass semifluid substances. When heated they get highly cross linked to form hard infusible and insoluble products. The cross links hold the molecule in place so that heating does not allow them to move freely. Therefore a thermosetting plastic is cross linked and is permanently rigid. Example : Bakelite, melamine formaldehyde resin etc. Plasticizers do lower the softening point (so called melting point) of a polymer. A plasticizer cannot convert a thermosetting polymer into thermoplastic one. In fact plasticizers can convert a hard and brittle plastic into soft and easily pliable. Plasticizers reduce the interparticle forces between polymer molecules. Plasticizers are generally high-boiling esters or high- boiling haloalkanes. They are added to plastics to make them soft and rubber-like. For example, polyvinyl chloride as such is hard, stiff and glass-like, but the addition of plasticizers like dioctylphthalate (DOP) or dibutylphthalate (DBP) can make it soft and rubber like. Similarly, chlorinated paraffin wax (CPW) is used as a plasticizer in polythene. On long exposure to air and sunlight, these plasticizers evaporate and the plastic articles become hard and brittle. Table : 30.1 Difference between thermoplastic and thermosetting polymers Thermoplastic polymers
Thermosetting polymers (1) These soften and melt on heating.
These do not soften on heating but rather become hard in case prolonged heating is done these start burning. (2) These can be remoulded recast and
These can not be remoulded or reshaped.
It may be noted that many types of copolymers can be obtained depending upon the distribution of monomer units in the chain. Two monomers can combine in either regular fashion (although this is rare) or random fashion. For example, if monomer A is copolymerised with monomer B , the resultant product may have a random distribution of the two units throughout the chain or it might have alternating distribution. ( – A – B – A – B – A – B – A – B – ) Alternating copolymer ( – A – A – A – B – A – B – B – A – B – ) Random copolymer The exact distribution of monomer units depends on the initial proportion of the two-reactant monomers and their reactivities. Most copolymers have varying distributions. Two other types of copolymers that can be prepared under certain conditions are called block copolymers and graft copolymers. (a) Block copolymers are those in which different blocks of identical monomer units alternate with each other as ( – A–A–A–A–B–B–B–B–A–A–A–A–B–B–B–B– ) n These are prepared by initiating the polymerisation of one monomer as if growing a homopolymer and then adding an excess of second monomer to the active reaction mixture. (b) Graft polymers are those in which homopolymer branches of one monomer units are grafted on the homopolymer chains of another monomer units as : n
n n n
A
B
B
B
A A A A
B
B
B
A A A A A
B
B
B
( A A )
|
|
|
|
|
|
|
|
|
|
|
|
These are prepared by radiation of -rays on a completed homopolymer chain in the presence of the second monomer. The high energy radiation knocks hydrogen atoms of the homopolymer chain at random points resulting radical sites for initiation of the added monomer. By careful control of the polymerisation reaction, we can produce copolymers of desired properties by combination of different monomers in various ratios and geometric arrangements.
(1) Chain growth or addition polymerisation : It involve a series of reaction each of which consumes a reactive particle and produces another similar one. The reactive particle may be free radicals or ion (cation or anion) to which monomers get added by a chain reaction. The polymers thus formed are known as chain growth polymers. Chain growth polymerisation is an
important reaction of alkenes and conjugated dienes or indeed of all kinds of compounds that contain carbon- carbon double bond polythene, polypropylene, polybutadiene, teflon PVC, polystyrene are some of chain growth polymers. It is based on three mechanism (i) Free radical mechanism (ii) Cation mechanism (iii) Anion mechanism Each mechanism of polymerisation reaction involves an initiator of their corresponding nature. The addition polymerisation reaction is very rapid and is also characterized by three steps i.e. chain initiation, chain propogation and chain termination step. (i) Free-radical mechanism : Free-radical polymerisation is initiated by organic peroxide or other reagents which decompose to give free radicals. Following steps are involved. (a) Chain initiation : Organic peroxides undergo homolytic fission to form free radicals.
2 Unstable
heat ||
Peroxide
|| || O R CO
O R R C
O O O C
O R C
(b) Chain propagation : Free radical adds to an alkene molecule to form a new free radical. R CH 2 CH 2 R CH 2 CH 2 The free radical formed attacks another alkene molecule and the process continues in building a long chain. RCH (^) 2 CH 2 CH 2 CH 2 RCH 2 CH 2 CH 2 CH 2
(c) Chain termination : The chain reaction comes to halt when two free radical chains combine. 2 R ( CH 2 CH 2 ) n CH 2 CH 2 R ( CH 2 CH 2 ) nCH 2 CH 2
: CH (^) 2 CH 2 ( CH 2 CH 2 ) nR Benzoyl or t-Butyl peroxide are common initiators, used. Free radical polymerisation can also be initiated by a mixture of ferrous sulphate and hydrogen peroxide ( FeSO (^) 4 H 2 O 2 )^. (ii) Cationic mechanism : Cationic polymerisation is initiated by use of acids such as H 2 SO 4 , HF or BF 3 in H (^) 2 O. The following steps are involved : (a) Chain initiation : The acid furnishes proton. H 2 SO 4 ⇌ H ^ HSO 4 HF ⇌ H ^ F BF (^) 3 H 2 O^ ⇌ H ^ ^ BF 3 ( OH )
The proton adds to the carbon of the double bond of the alkene to form a carbonium ion.
H CH 2 CH 2 CH 3 CH 2 (b) Chain propagation : The carbonium ion combines with another molecule of alkene to form a new carbonium ion and the process continues to form a long chain.
CH (^) 3 CH 2 CH 2 CH 2 CH 3 CH 2 CH 2 CH 2
CH (^) 3 CH 2 CH 2 CH 2 nCH 2
= CH 2
CH (^) 3 CH 2 ( CH 2 CH 2 ) nCH 2 CH 2
(c) Chain termination : The chain may be halted by combination with negative ion or loss of a proton.
4
3 2 ( 2 2 ) | 2 HSO
H CH H
CH CH CHCH nC
CH (^) 3 CH 2 (Poly mer CH 2 CH 2 ) n CH CH 2 H 2 SO 4 (iii) Anionic polymerisation : This type of polymerisation is initiated by anion (Bases nucleophiles) it proceeds through the formation of carbanion. The initiation may be brought about by K NH 2 of L NH 2. The following steps are involved (a) Chain initiation : H W
H Nu CH C W
Nu CH 2 C | 2 |
(b) Chain propagation : H W
H Nu CH C W
Nu CH C 2 | 2 2 | 2 | 2 |
Repeat ^ 2 | H CH 2 W
Nu CH C n (c) Termination :
Poly mer
(^2) | (^22) | H CH 3 W
H CH H Nu CH C W
Nu CH C n n
Chain transfer agents : In Vinylic polymerisation various other molecules react with main growing chain to interrupt the further growth of the original chain. This leads to lowering of average molecular mass of the polymer such reagents are called chain transfer agents. The common example CCl 4 , CBr 4 etc.
For example in the presence of CCl 4 styrene polymerizes to form a polymer of lower average molecular mass which also contains some chlorine.
3 6 5
(^2) | 6 5
(^2) | Initiator 6 5
(^2) | Cl CCl CH
6 5
(^32) | 6 5
(^2) | 3 C H
ClC CH CH CH
CH CH CCl^
C H n
H CH C CH
ClC CH CH
6 5
| (^2) | 6 5
(^32) | Sty rene
Chain transfer agents determinate chain reaction and inhibit further polymerisation and are also called inhibitors. (2) Step growth or condensation polymerisation : In this type of polymerisation monomers generally contain two functional groups, i.e. , difunctional monomers. In this process no initiator is needed and each step is the same type of chemical reaction. Since in this polymerisation reaction the polymer is formed in a stepwise manner. It is called step growth polymer and the process is called step growth polymerisation. The process for two monomer A and B may be expressed as. Dimer
Condense Monomers A^ B ^ A B Trimer A B A Condense ^ A B A A B A B A B A B Alternatively, step growth can proceed as A B A B A B A B A B A B or ( A B ) 2 A B A B A B A B Poly mer ( A B ) n Some common examples of step growth polymers are Polymers Monomers Nylon- 66 Hexamethylenediamine and adipic acid Bakelite Phenol and formaldehyde Dacron (polyester)
Terephthalic acid and ethylene glycol
It is a polymer which is capable of returning to its original length, shape or size after being stretched or deformed. It is the example of elastomer. Rubber are of two types. (1) Natural rubber (2) Synthetic rubber (1) Natural rubber : It is obtained as latex from rubber trees. The latex is coagulated with acetic acid or formic acid. The coagulated mass is then squeezed.
(i) Neoprene rubber Chloroprene
Cl
n
CH CH Cl
CH C
2 | 2
Making automobile, refrigerator parts and electric wire. (ii) Styrene Butadiene Rubber (SBR) or Buna- S
(^2) Butadiene (75%) 2 CH CH CH CH^ and
n
(^) 2 2 2 Making of tyre and other mechanical rubber goods.
(iii) Butyl rubber
Isobuty lene(98%)
3
3
| (^2) |
(^) CH C and
Isoprene(2- 3 %)
2 3
(^2) | CH CH
CH C CH n
3
3
2
| (^2) |
|^3 2
Making of toys, tyre, tube etc.
(iv) Nitrile rubber or Buna N or GRA
(^2) Butadiene ( 75 %) 2 CH CH CH CH and
Acry lonitr^2 ile( 25 %)
n
Used for make of fuel tank.
(v) Polysulphid e rubber (Thiokol)
Ethy lene^2 dichloride^2
Cl CH CH Cl and Sodium tetrasulp^24 hide
NaS
( CH (^) 2 CH 2 S S S S ) n Used in the manufacture of hoses and tank lining, engine gasket and rocket fuel. (vi) Silicone rubber Chlorosilanes
3 3
| |
Cl
Cl Si n
O Si
3
3
| |
Silicon rubber
(vii) Polyurethan e rubber
Ethy lene^2 gly col^2
and Ethy lenedi-isocy anate
|| N CH CH N C O
O C
In the manufacture of fibre. Paints and heat insulator.
Table : 30.5 Plastics and resin Name of polymer Abbreviat
- ion
Starting materials (monomers)
Nature of polymer
Properties Applications
(i) Polyolefines (a) Polyethylene or polyethene
LDPE (Low density polyethene )
homopolymer (branched) chain growth.
Transparent, moderate tensile strength, high toughness.
Packing material carry bags, insulation for electrical wires and cables. HDPE (high density polyethene )
(linear) chain growth.
Transluscent, chemically inert, greater tensile strength, toughness.
Manufacture of buckets, tubs, house ware, pipes, bottles and toys.
(b) Polypropylene or polypropene
, linear, chain growth.
Harder and stronger than polyethene.
Packing of textiles and foods, liners for bags, heat shrinkage wraps, carpet fibres,
Styrene (25%)
ropes, automobile mouldings, stronger pipes and bottles.
(c) Polystyrene or Styron or styrofoam
, linear, chain growth
Transparent Plastic toys, house hold wares, radio and television bodies, refrigerator linings.
(ii) Polyhaloolefines
(a) Polyvinyl chloride
Vinylchloride
chains growth
Thermoplastic (i) Plasticised with high boiling esters PVC used in rain coats, hand bags, shower curtains, fabrics, shoe soles, vinyl flooring (ii) Good electrical insulator (iii) Hose pipes. (b) Polytetrafluoroet- hylene or Teflon
, high melting point
Flexible and inert to solvents boiling acids even aqua regia. Stable upto 598 K.
(i) For nonstick utensiles coating (ii) Making gaskets, pump packings valves, seals, non lubricated bearings. (c) Polymonochlorotri- fluroroethylene
PCTFE ClFC CF 2 Homopolymer Less resistant to heat and chemicals due to presence of chlorine atoms.
Similar to those of teflon.
(iii) Formaldehyde resins
(a) Phenol formaldehyde resin or Bakelite
Phenol and formaldehyde
Copolymer, step growth
Thermosettin g polymer, hard and brittle
(i) With low degree polymerisation as bindings glue for wood varnishes, lacquers. (ii) With high degree polymerisation for combs, for mica table tops,
resistant brushes etc. (ii) Substitute of metals in bearings. (iii) Gears elastic hosiery. (c) Nylon-6 or Perlon
Homopolymer , linear
Thermoplastic high tensile strength abrasion resistant.
Mountaineeri ng ropes, tyre cords, fabrics.
(iii) Polyacryloni- trile or orlon or acrilon
and high melting materials.
Orlon, arcrilon used for making clothes, carpets blankets and preparation of other polymers. Copolymer of acrylonitrile (40%) and vinyl chloride (60%) is called dynel it is used in hair wigs. Artificial silk is the term given to fibres derived from cellulose. The most important process for the production of artificial silk is viscose process. The difference between natural and artificial silk is natural silk contain nitrogen while artificial silk may not have nitrogen. Natural silk on burning gives a smell of burning hair and shrinks into a ball of cinder while artificial silk gives a thread of ash.
These are the polymers which are degraded by micro-organisms within a suitable period so that biodegradable polymers and their degraded products do not cause any serious affects on the environment. In biological systems, biopolymers degrade mainly by enzymatic hydrolysis and to some extent by oxidation. Therefore, in view of the disposal problems of polymer waste and for developing polymers for other safe uses in human systems, attempts have been made to develop biodegradable synthetic polymers. These synthetic polymers mostly have functional groups which are normally present in biopolymers and lipids. Among these aliphatic polyesters are one important class of biodegradable polymers which are commercially potential biomaterials. The common examples of biodegradable polymers are polyhydroxy butyrate (PHB), polyhydroxy butyrate – co- - hydroxy
valerate (PHBV), polyglycolic acid (PGA), polylactic acid (PLA), poly (-caprolactone) (PCL), etc. Uses : Biodegradable polymers are used mainly for medical goods such as surgical sutures, tissue in growth materials or for controlled drug release devices, plasma substitutes etc. The decomposition reactions usually involve hydrolysis (either enzymatically induced or by non-enzymatic mechanisms) to non-toxic small molecules which can be metabolized by or excreted from the body. These are also finding use in agriculture materials (such as films, seed coatings), fast food wrappers, personal hygiene products, etc. (i) Polyhydroxy butyrate (PHB) Polyhydroxy butyrate (PHB) is obtained from hydroxy butyric acid (3-hydroxy butanoic acid)
Poly hy droxy buty rate(PHB)
|| 2 3
|
Condensation
3 - Hy droxybutanoicacid
|| 2 3
| n
nHOCHC
(ii) Poly-Hydroxybutyrate-co- - Hydroxy valerate (PHBV) : It is copolymer of 3 - hydroxy butanoic acid and 3-hydroxy pentanoic acid, in which the monomer units are joined by ester linkages.
Caprolactum or H 2 N – [ CH 2 ] 5 – COOH -Aminocaproic acid
3 - Hy droxypentanoicacid
(^32) | 2 3 - Hy droxybutanoicacid
CHCOOH nCH CH CH OH
nCH CH
PHBV
|^2 || n
O O
H CH C R
O C
,
The properties of PHBV vary according to the ratio of both the acids. 3 - Hydroxy butanoic acid provides stiffness while 3-Hydroxypentanoic acid gives flexibility to the copolymer. (iii) Polyglycolic acid (PGA) : Polyglycolic acid (PGA) is obtained by the chain polymerisation of cyclic dimer of glycolic acid, HO CH 2 COOH.
Poly gly colicacid(PGA)
|| 2 Heat Gly colic acid^2 n
nHO CHCOOH OCH C
(iv) Polylactic acid ( PLA ) : Polylactic acid (PLA) is obtained by polymerisation of the cyclic dimer of lactic acid (^) ( HO CH ( CH 3 ) COOH ) or by microbiological synthesis of lactic acid followed by the polycondensation and removal of water by evaporation.
Poly lacticacid(PLA)
||
3
|
Condensation
Lactic 3 acid
|| | n
nHOCHC
(v) Poly ( - caprolactone) (PCL) : It is obtained by chain polymerisation of the lactone of 6-hydroxy hexanoic acid.
PCL
|| ( 2 ) 2 n
O O CH C
Uses : PGA and PLA (90 : 10) is used to make absorbable structure to close an internal of external wound and has replaced cat gut these are completely degraded and absorbed by the body within 15 days to one month of the surgery. Polyhydroxybutyrate (PHB) and (PHBV) have been used for making films for packaging and into moulded items.
A polymer sample contains chain of varying lengths and therefore its molecular mass is always expressed as an average on the other hand natural polymer such as proteins contain chain of identical
length and therefore they have definite molecular mass. The molecular mass of a polymer can be expressed in two ways. (1) Number average molecular mass( MN ) (2) Weight average molecular mass ( MW ). (1) Number average molecular mass ( MN ) : If N 1 , N 2 , N 3 …..^ are^ the^ number^ of^ molecules^ with molecular masses M 1 , M 2 , M 3 …… respectively, then the number average molecular mass is
...
1 2 3
1 1 2 2 3 3 N N N
This may be expressed as : i N i i N M NM
Where Ni is the number of molecules of the i th type with molecular mass (^) Mi. (2) Weight average molecular mass ( MW ) : If m 1 , m 2 , m 3 …. are the masses of species with molecular masses M 1 , M 2 , M 3 ….. respectively, then the weight average molecular mass is
...
1 2 3
1 1 2 2 3 3
m m m M mM mM m M W^ or i
i i m
mM
But mi NiMi , so that i i W i i NM
where Ni is the number of molecules of mass Mi. Polydispersity index : The ratio of weight average molecular mass to the number average molecular mass is called polydispersity index , PDI****.
n
W M PDI M
This gives an idea about the homogeneity of a polymer. (i) The polymers whose molecules have nearly same molecular masses are called monodisperse polymers. For these molecules, M (^) W MN and therefore, PDI is one. (ii) The polymers whose molecules have wide range of molecular masses are called polydisperse polymers. For these polymers, MW MN and therefore, their PDI is greater than one. Thus, it may be concluded that in general, natural polymers are more homogeneous than synthetic polymers.
(ii) Syndiotactic (Alternating order) : The Y and Z groups lie alternately on each side of the chain.
(iii) Atactic (Random order) : The Y and Z groups are arranged in a random fashion.
(4) Addition polymers, generally, have only carbon atoms in their main chain. On the other hand, condensation polymers, generally, have atoms other than carbon atoms, in their main chain. (5) Polyurethanes : Polyurethanes are polymers obtained by the polymerisation of a urethane. It is used for heat and sound insulation in the form of polyurethane foam. Mattresses, cushions and pillows made out of polyurethane foam are washable and long lasting.
urethane
||
|
A
O R O
C
H R N
(6) Epoxy resins : These are obtained by copolymerisation of epichlorohydrin and bisphenol-A. These resins have good adhesive strength. These are used for making adhesives (Araldite, M-seal etc.) for making glass reinforced plastic (fibre glass), for lamination, to impart crease resistance and shrinkage control to cotton, rayon and for making anti-skid surface for highways. (7) Polycarbonates : These are obtained by copolymerisation of diphenyl carbonate and bisphenol- A. It has very high optical transparency, high impact strength over wide range of temperature. It is used for making bullet-proof glass, baby-feed bottles, fridge containers, mixi jars etc. (8) Thermoplastics are also called cold setting polymers. They are moulded when hot but set into the required shape only on cooling. Thermosetting polymers are also called heat setting polymers. Such polymers are supplied in the partially polymerised form. (9) On long exposure to air and sun-light thermo- plastics becomes brittle. It is due to the evaporation of plasticizer with time. The faint smell associated with various thermoplastics is due to slow evaporation of this plasticizer.
(10) High density polyethene is a linear polymer. Carry bags made out of it are not so soft and make a crackling sound when crushed in hands. You can easily tear them in one direction, but not at right angle to it. Plastic twine is made out of such a polymer. They have very high tensile strength in one direction (along the polymer chain) and a low tensile strength at right angle to it. Such carry bags are used to carry clothes, note- books etc. Carry bags made of low density polyethene are soft, make no noise when crushed with hands, have same tensile strength in all directions. Such carry bags are used to carry heavy objects (vegetables, fruits etc.) (11) Kevlar is a nylon-polymer and is obtained by condensation copolymerization of terephthalic acid with 1, 4-diaminobenzene ( p - phenylenediamine). The fibres of this polymer are so strong that they are used to make bullet-proof vests. (12) Lexan is a polycarbonate(polyester) and is prepared by condensation copolymerization of diethyl carbonate and bisphenol A. It has unusually high impact strength and hence is used in making bullet- proof windows and safety or crash helmits. (13) Nomex is a polyamide made from m - phthalic acid and m - diaminobenzene. It is known for its fire- resistant properties and is used in protective clothing for firefighters, astronauts and race car drivers. (14) Ebonite is high sulphur (20-30 % S ) rubber and is obtained by vulcanization of natural rubber. (15) Rayon was originally called artificial silk but now the name rayon is given to all fibres obtained by chemical treatment of cellulose. Thus, artificial silk is polysaccharide, i.e. , cellulose derivative.
macromolecules are also regarded as polymers
rubber to protect it from degradation on exposure to air.
butylphthalate, tricresyl phosphates which are added to a polymer such as PVC to make it soft and readily workable on heating.
is prepared by free radical polymerization while high density polythene is a linear polymer and is prepared by coordination polymerization.
Zeigler and natta.
natural rubber in its stability to aerial oxidation and
resistance to oils, gasoline and solvents.
cyanoacrylate.
toluene diisocyanate with ethylene glycol. During polymerization, low boiling liquid such as Freon- 11 are added to the reaction mixture. The heat of polymerization vaporizes the volatile liquid producing bubble which convert the viscous polymer to a frothy mass of polyurethane foam.
obtained by vulcanization of natural rubber.