
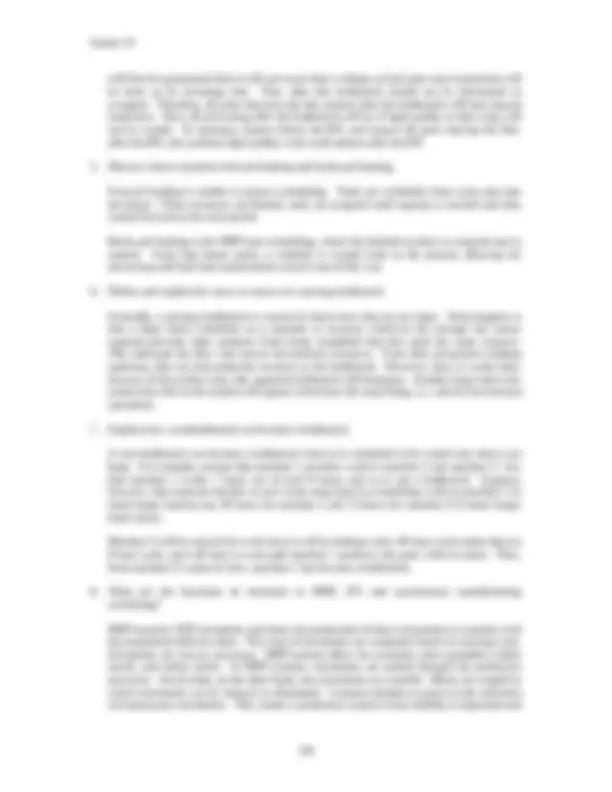
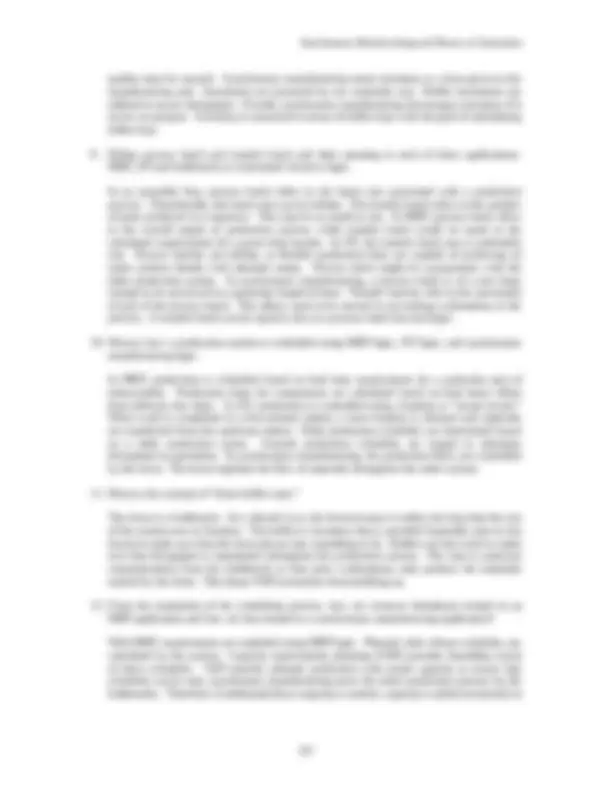
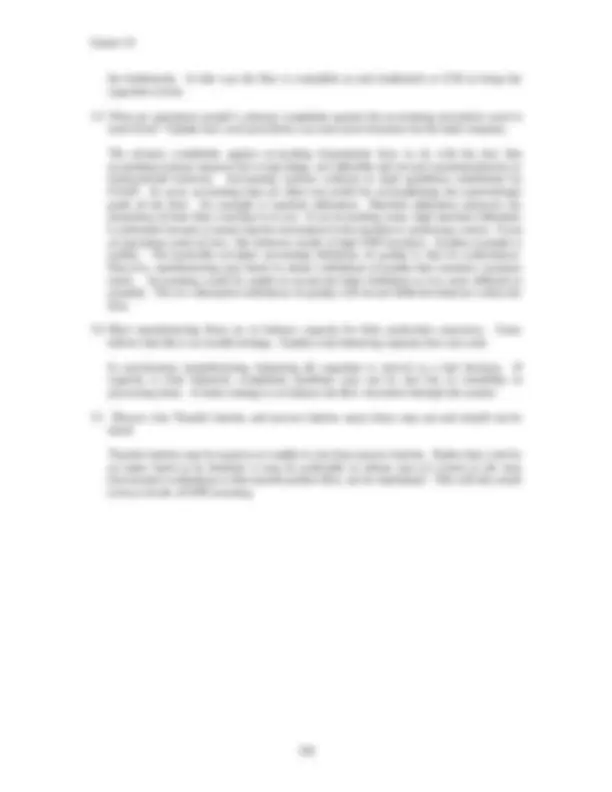
Study with the several resources on Docsity
Earn points by helping other students or get them with a premium plan
Prepare for your exams
Study with the several resources on Docsity
Earn points to download
Earn points by helping other students or get them with a premium plan
Community
Ask the community for help and clear up your study doubts
Discover the best universities in your country according to Docsity users
Free resources
Download our free guides on studying techniques, anxiety management strategies, and thesis advice from Docsity tutors
Material Type: Notes; Class: OPERATNS AND PRODUCTION MGT; Subject: Management; University: Idaho State University; Term: Unknown 1989;
Typology: Study notes
1 / 5
This page cannot be seen from the preview
Don't miss anything!
Synchronous Manufacturing and Theory of Constraints
Synchronous Manufacturing and Theory of Constraints quality must be assured. Synchronous manufacturing treats inventory as a loan given to the manufacturing unit. Inventories are measured by raw materials cost. Buffer inventories are utilized to assure throughput. Overall, synchronous manufacturing discourages inventory if it serves no purpose. Inventory is measured in terms of dollar days with the goal of minimizing dollar days.
Chapter 18 the bottlenecks. In this way the flow is controlled at each bottleneck or CCR to bring the capacities in line.