
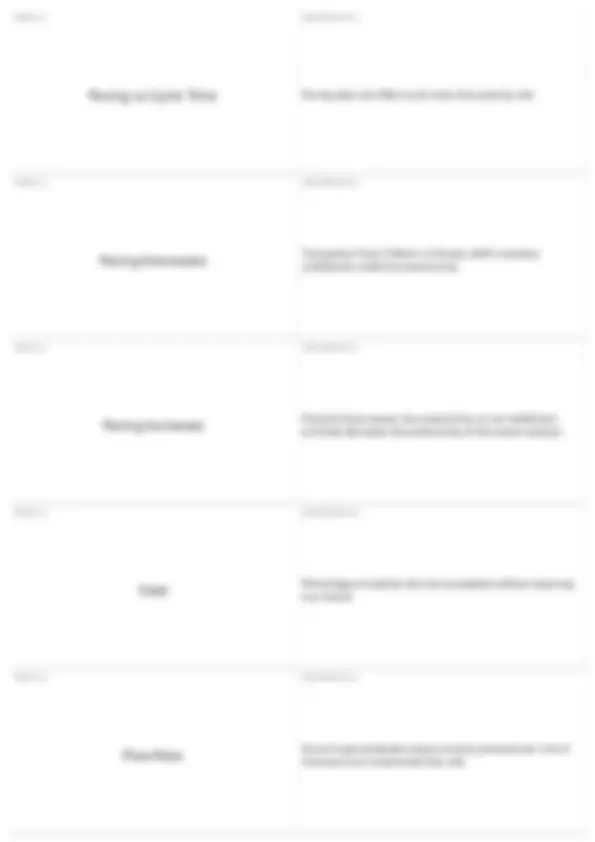
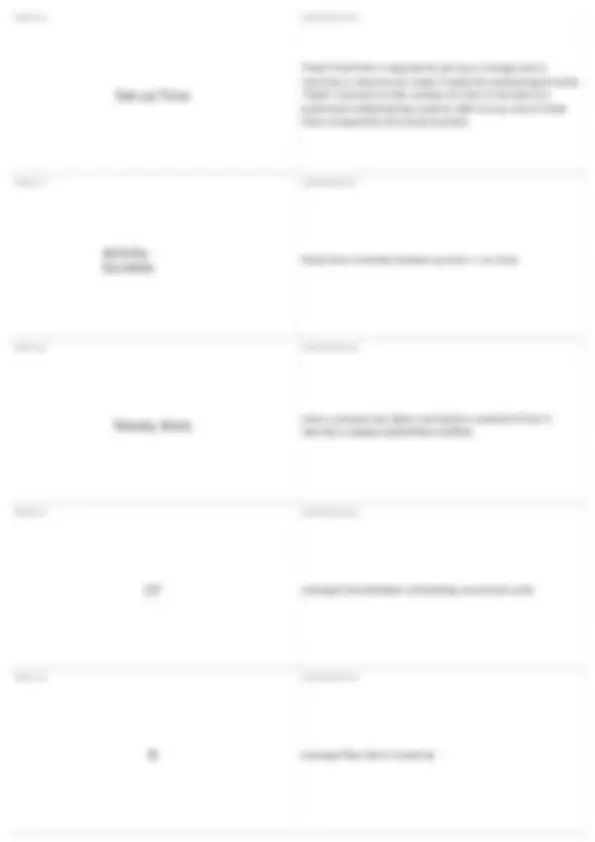
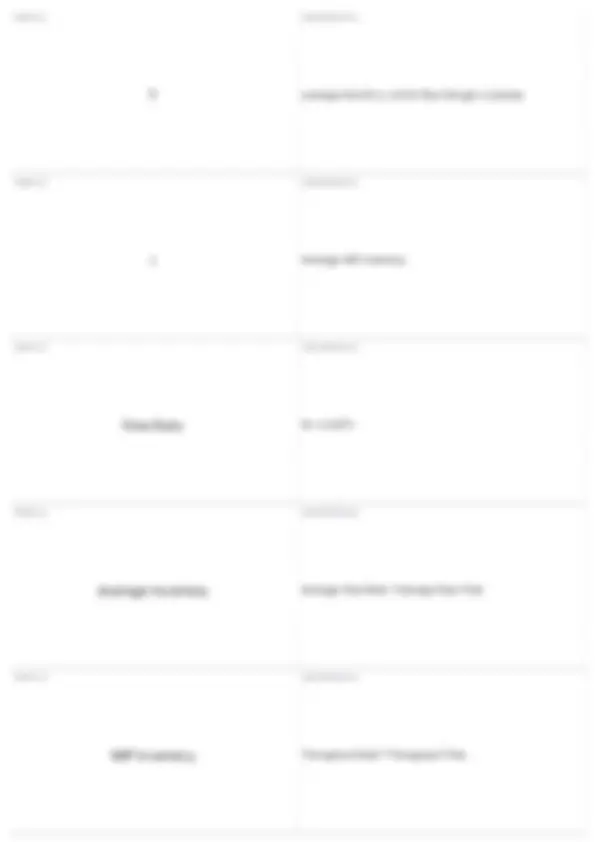
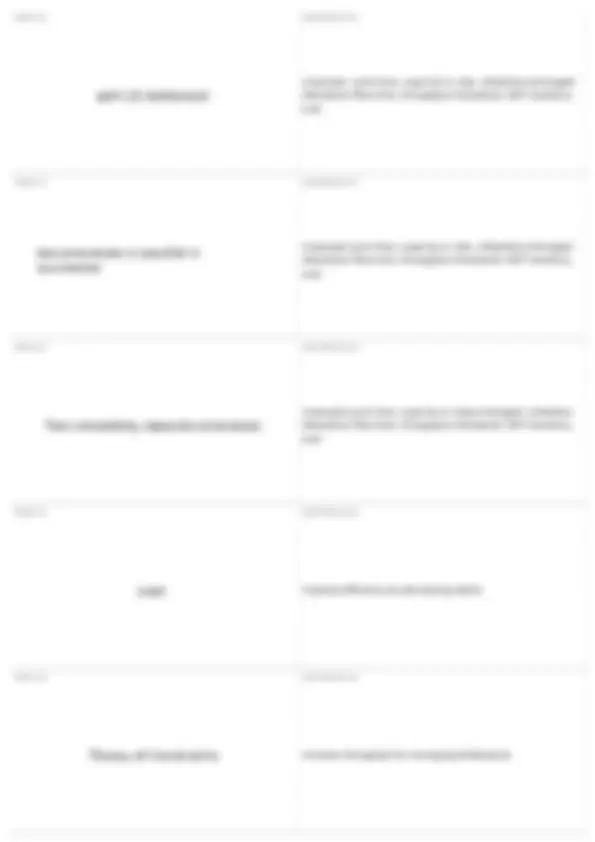
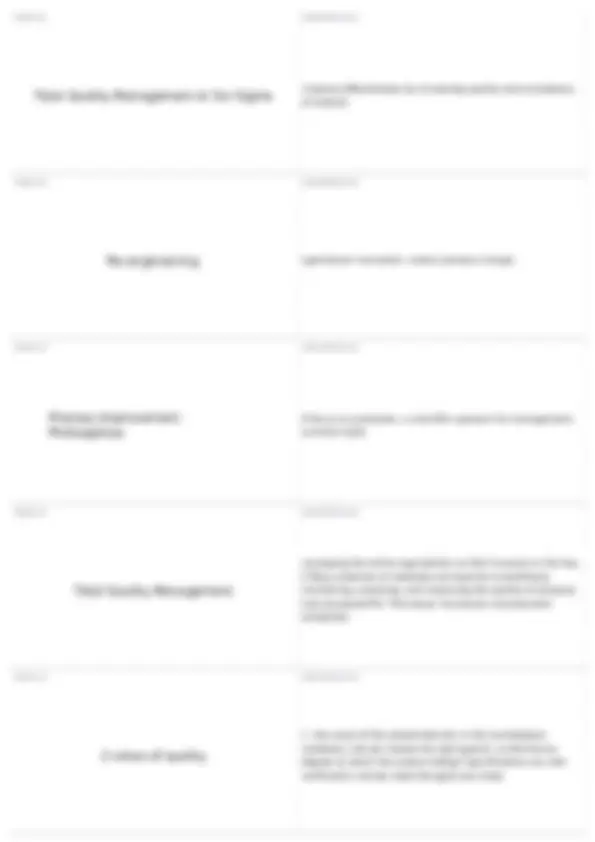
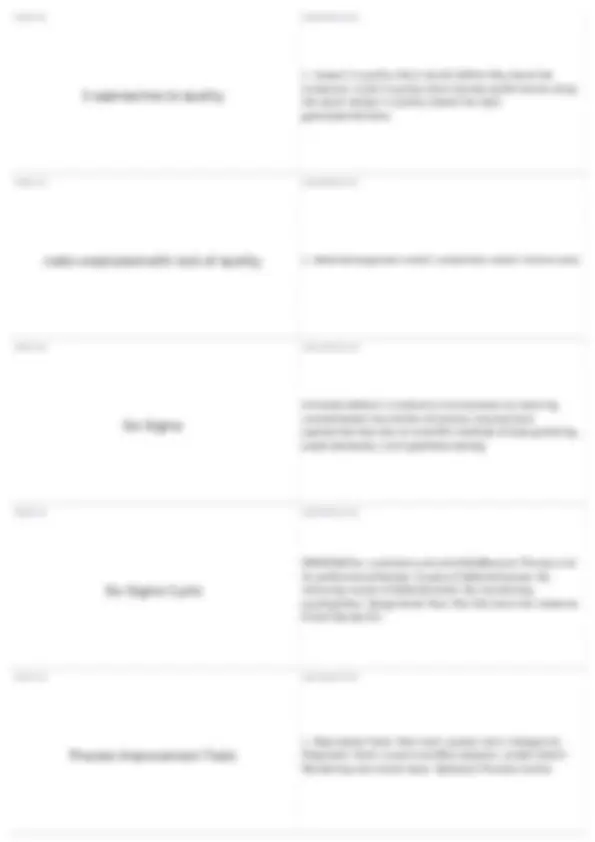
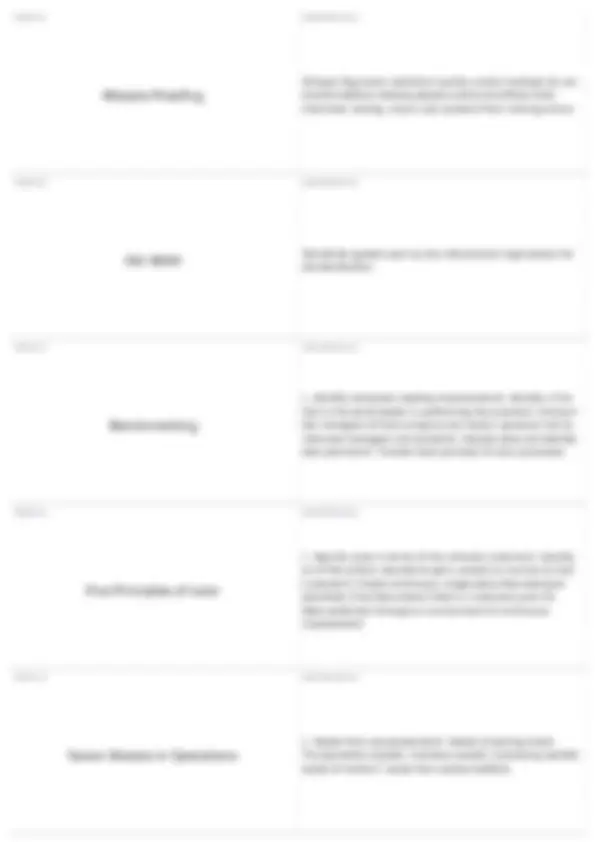
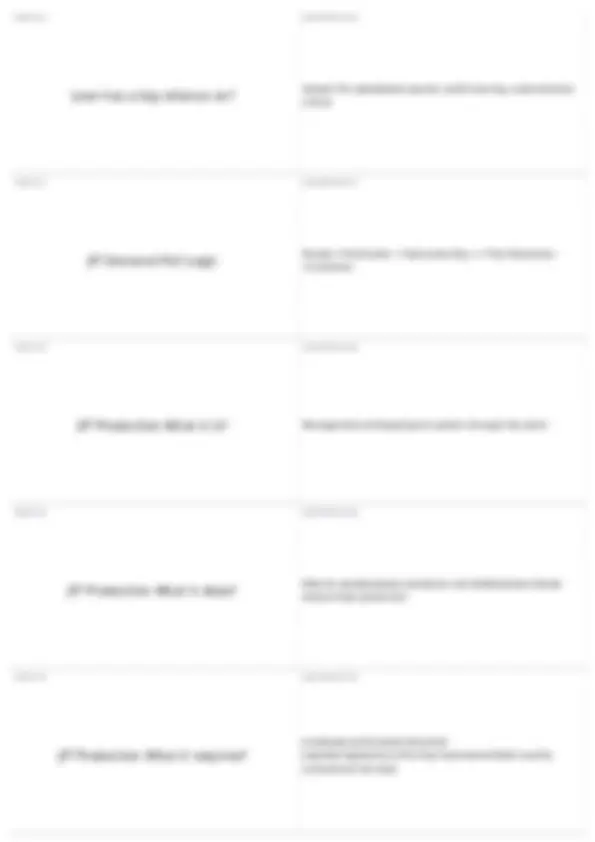
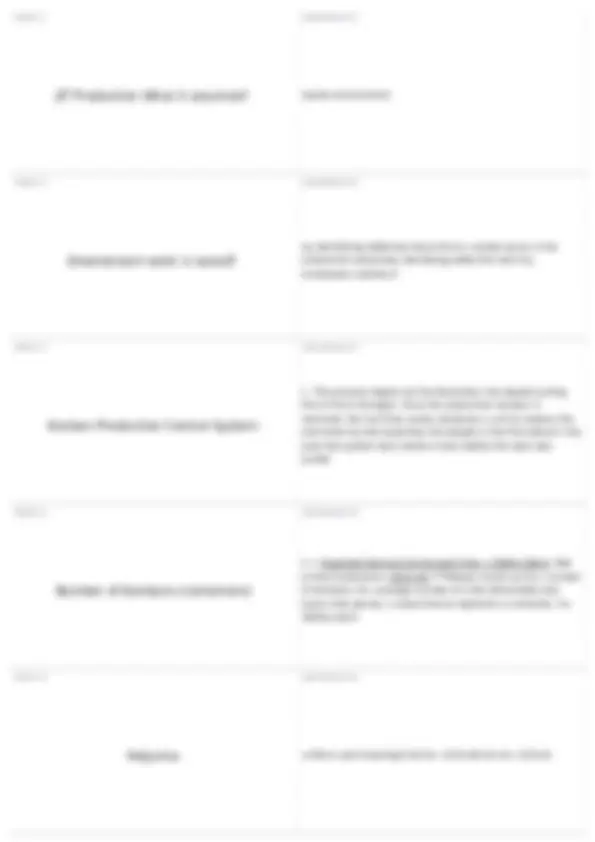
Study with the several resources on Docsity
Earn points by helping other students or get them with a premium plan
Prepare for your exams
Study with the several resources on Docsity
Earn points to download
Earn points by helping other students or get them with a premium plan
Community
Ask the community for help and clear up your study doubts
Discover the best universities in your country according to Docsity users
Free resources
Download our free guides on studying techniques, anxiety management strategies, and thesis advice from Docsity tutors
Definitions and explanations of various production-related terms, including blocking, starving, bottleneck, pacing, theoretical flow time, cycle time, utilization, and more. It covers concepts related to managing production processes and improving efficiency.
Typology: Quizzes
1 / 16
This page cannot be seen from the preview
Don't miss anything!
triangle shape can be within an activity and represents the output of one activity (WIP) is placed prior to being used by a downstream activity.Holding Inventory TERM 2
DEFINITION 2 when a flow unit must stop and wait because there is no place to put it (or activity is not ready for it) TERM 3
DEFINITION 3 when an activity cannot work because there is no input available.if an employee is waiting and no input is available the employee may have to remain idle until the next unit arrives TERM 4
DEFINITION 4 Constraintfactor that limits productionoccurs when the limited capacity of a process causes work to pile up or become unevenly distributedSlowest activity (longest cycle time)Scarcest resources (usually material or people)Blocking occurs before (upstream from) a bottleneckstarving occurs after (downstream from) a bottleneck TERM 5
DEFINITION 5 this is when you starve the bottleneck basically. You hold back producing so that your item can move right into the bottleneck and out.converts blocking into starving
Rush order flow timethe time it takes for a unit order to go through the process from beginning to end without any waiting TERM 7
DEFINITION 7 this is determined by the bottleneckaverage time between completion of successive units (often confused with throughput time)some define it as the minimum time between completion of successive units but be careful how it is definedActivity Cycle Time: no starving, blocking, downtimeProcess Cycle: accounts for waiting TERM 8
DEFINITION 8 flow rate, throughput rate, or theoretical capacityaverage output per unit of time, assuming no yield losses or downtime (full utilization)activity flow rate- is unconstrainedprocess flow rate is determined by the bottleneck TERM 9
DEFINITION 9 throughput time, flow time, lead timeaverage time for a unit to move through a process including any waitingactual measure depends on how the process is paced TERM 10
DEFINITION 10 the percentage of time (or other resource) spent actually working on the product or performing the serviceTime Activated/Time Available
Fixed TimeTime is required to set up or change over a machine or resource to make it ready for processingnormally "fixed" invariant vs the number of units in the batch or production lotSometimes used to refer to any and all fixed time components of activity duration TERM 17
DEFINITION 17 fixed time+variable timeset-up time + run time TERM 18
DEFINITION 18 once a process has been running for a period of time it reaches a steady stateinflow=outflow TERM 19
DEFINITION 19 average time between completing successive units TERM 20
DEFINITION 20 average flow rate or capacity
average time for a unit to flow through a process TERM 22
DEFINITION 22 Average WIP inventory TERM 23
DEFINITION 23 R= (1)/(CT) TERM 24
DEFINITION 24 Average Flow Rate * Average Flow Time TERM 25
DEFINITION 25 Throughout Rate * Throughput Time
cycle timecapacity/Rate TERM 32
DEFINITION 32 "Average"in flow = outflow TERM 33
DEFINITION 33 fixed set up timeinflow > Outflow TERM 34
DEFINITION 34 outflow > inflow TERM 35
DEFINITION 35 improved: Theoretical flow time, throughput time, WIP Inventoryunchanged: process cycle time, capacity or rate, utilization, cost
improved: cycle time, capacity or rate, utilizationunchanged: theoretical flow time, throughput timeworse: WIP inventory, cost TERM 37
DEFINITION 37 improved:cycle time, capacity or rate, utilizationunchanged: theoretical flow time, throughput timeworse: WIP inventory, cost TERM 38
DEFINITION 38 improved:cycle time, capacity or rateunchanged: utilization, theoretical flow time, throughput timeworse: WIP inventory, cost TERM 39
DEFINITION 39 improve efficiency by decreasing waste TERM 40
DEFINITION 40 increase throughput by managing bottlenecks
DEFINITION 47
DEFINITION 48 eliminate defects in products and processes by reducing variationlatest incarnation of process improvement approaches that rely on scientific methods of data gathering, experimentation, and hypothesis testing TERM 49
DEFINITION 49 DMIACDefine: customers and prioritiesMeasure: Process and its performanceAnalyze: Causes of defectsImprove: By removing causes of defectsControl: By maintaining qualityothers: Design Build Test, Plan Do Check Act, Observe Orient Decide Act TERM 50
DEFINITION 50
isolate one specific defect, problem, or conditionexcellent tool for maintaining structure in brainstorming TERM 52
DEFINITION 52 brings you to the real root of a cause TERM 53
DEFINITION 53 used to track defects TERM 54
DEFINITION 54 Positional Variation: Variation within batchesCyclical Variation: Variation between batchesTemporal Variation: Variation over time TERM 55
DEFINITION 55 Cumulative Percent Curve track defects
Shingos Argument: statistical quality control methods do not prevent defects (helping people avoid errors)Poka-Yoke: checklists, tooling, visual cues (prevent from making errors) TERM 62
DEFINITION 62 Standards agreed upon by the international organization for standardization TERM 63
DEFINITION 63
DEFINITION 64
DEFINITION 65
respect for peoplelevel payroll, profit sharing, subcontractor unions TERM 67
DEFINITION 67 Vendor->Fabricator-->Sub-assembly--> Final Assembly--
Customer TERM 68
DEFINITION 68 Management philosophypull system through the plant TERM 69
DEFINITION 69 Attacks wasteexposes problems and bottlenecksachieves streamlined production TERM 70
DEFINITION 70 employee participationindustrial engineering/basicscontinuing improvementtotal quality controlsmall lot sizes
L: remove non-value activities; demolish and old activity for newE: improve the value added by processes, ensuring activities and processes produce the right deliverables TERM 77
DEFINITION 77 effort * capability= Actual Performancetime: working increases and improving decreasescapability: down over timeActual performance: initial increase then decrease over time TERM 78
DEFINITION 78 effort * capability= Actual Performancetime: working decreases and improving increasescapability: rises over timeActual performance: initial decrease then increase over time