
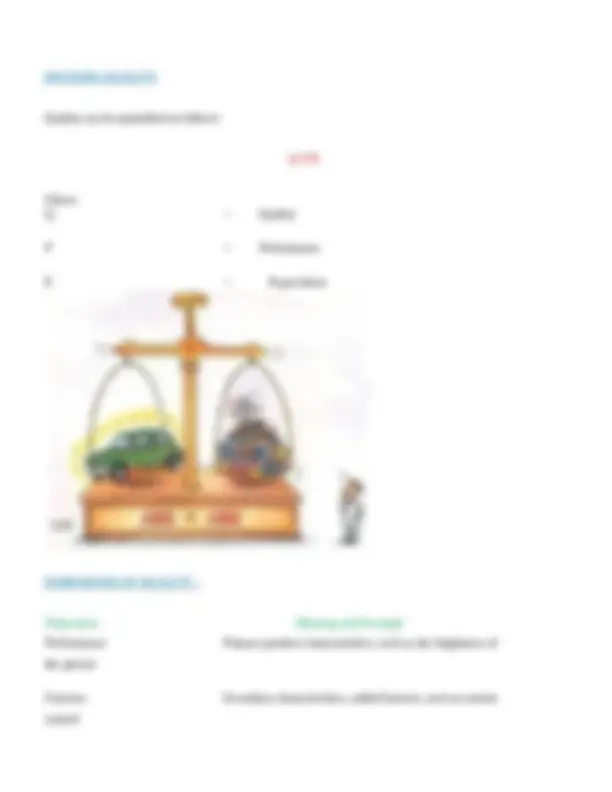
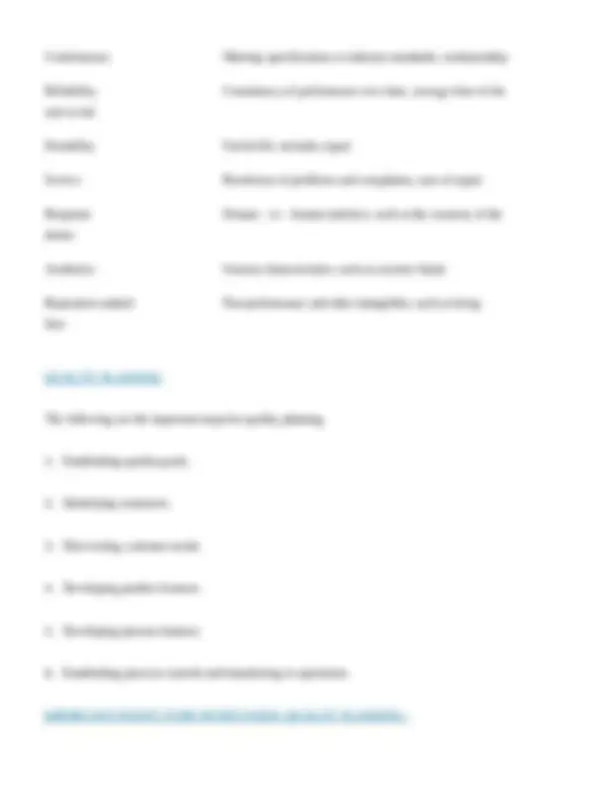
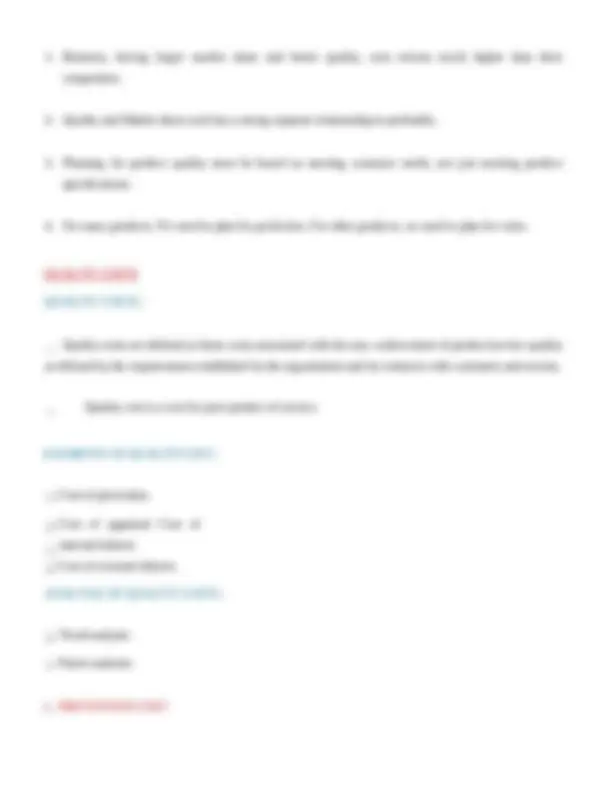
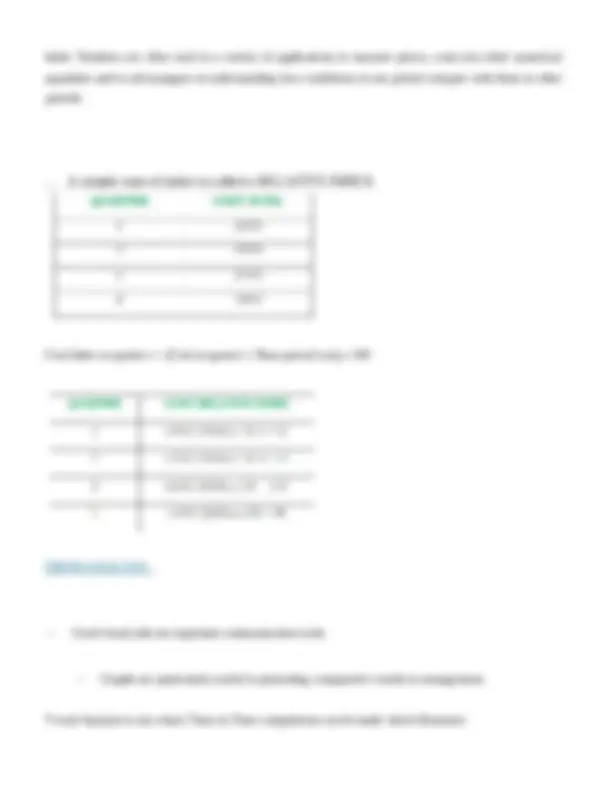
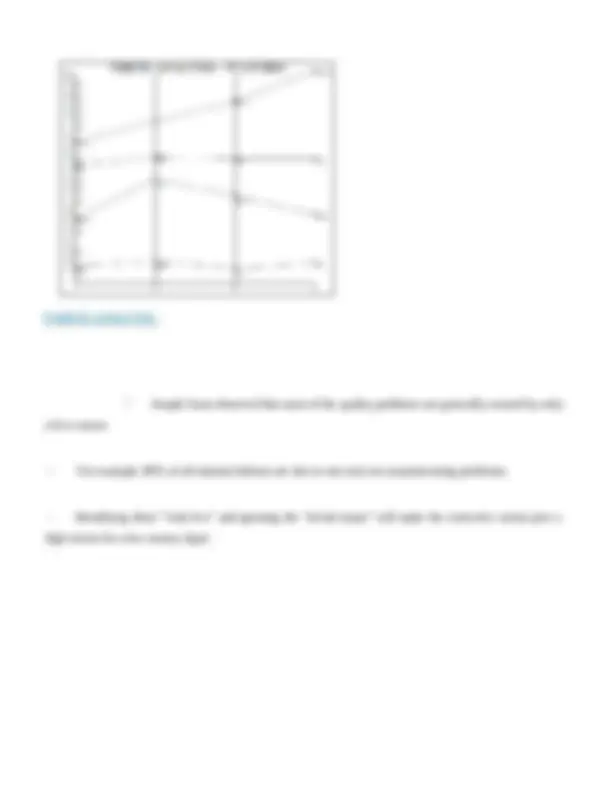
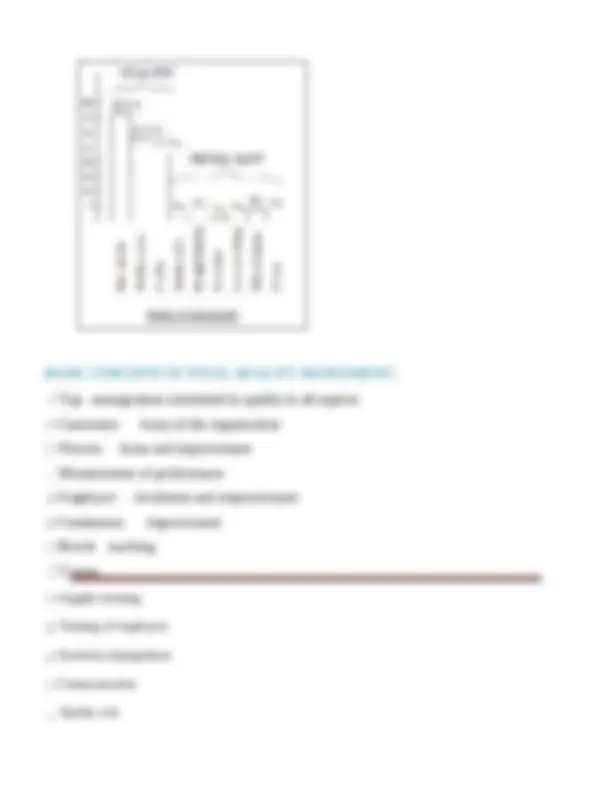
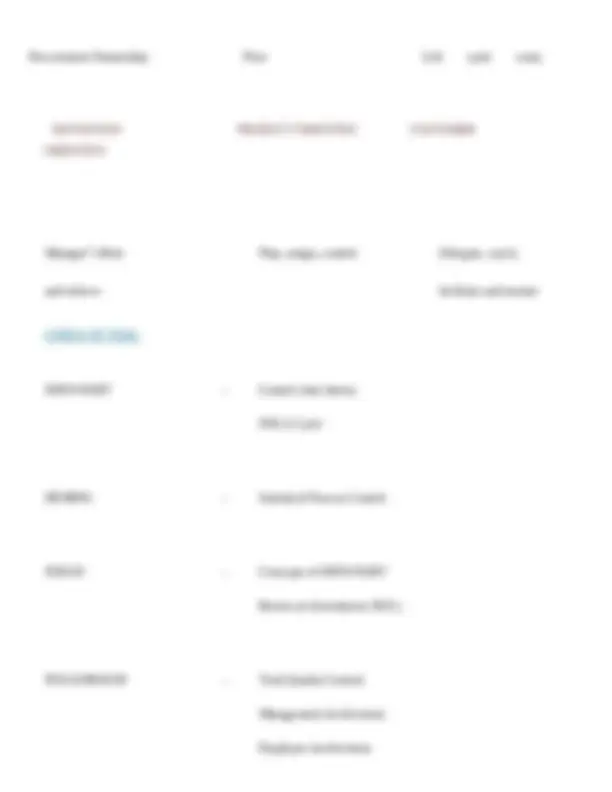
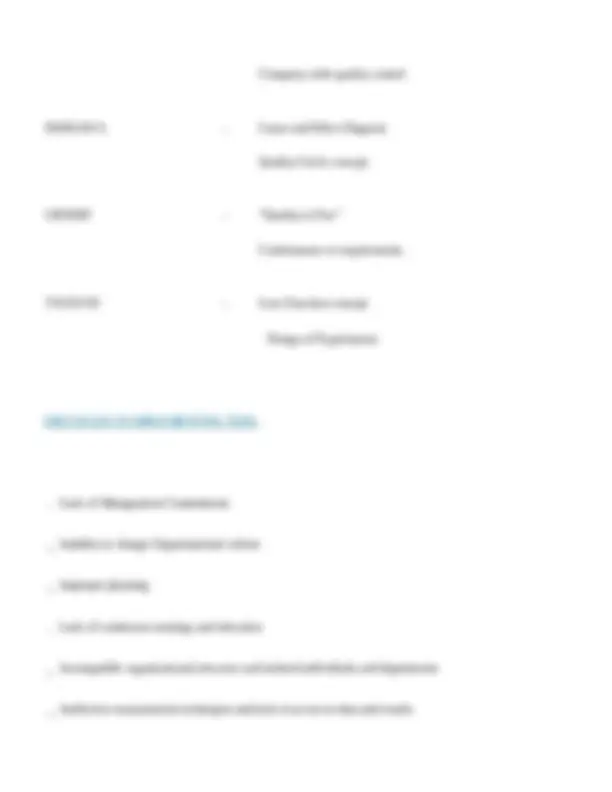
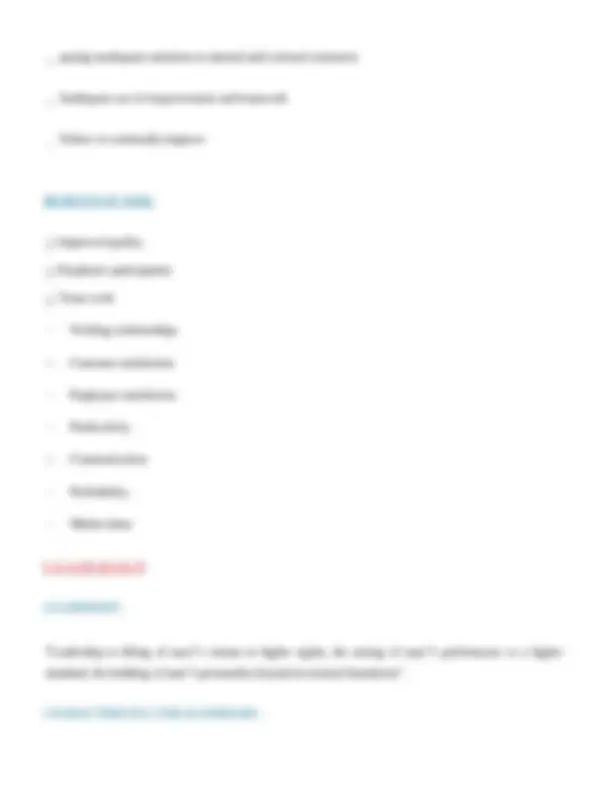
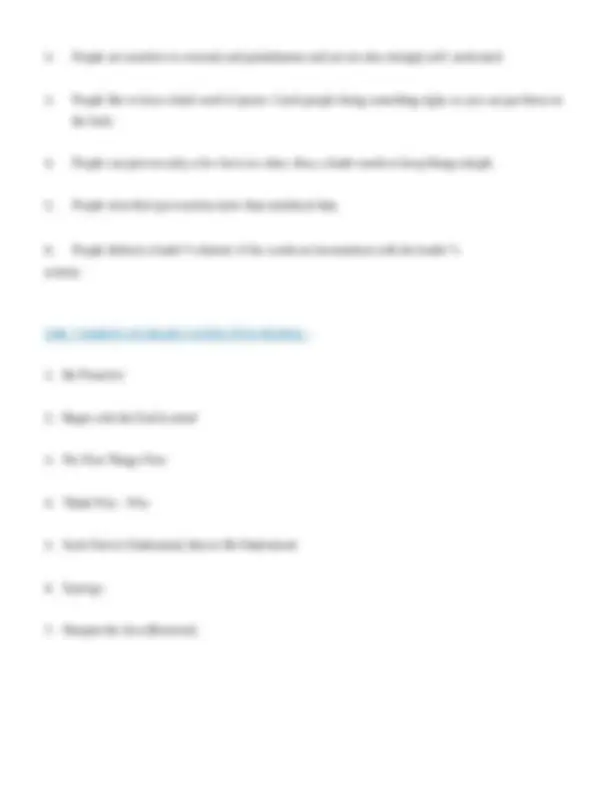
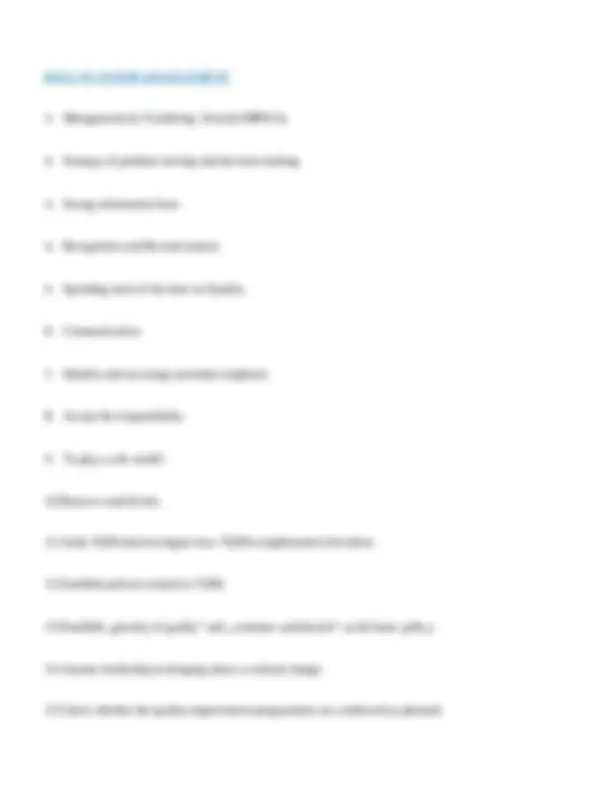
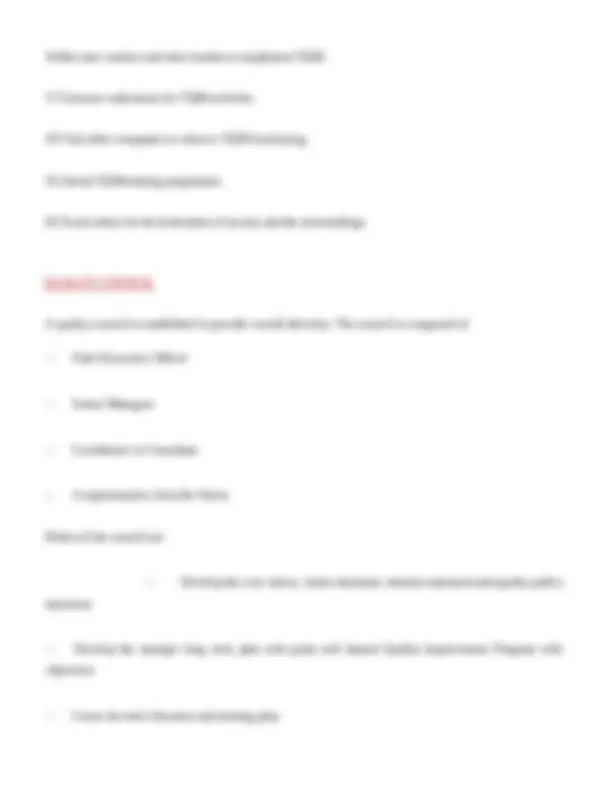
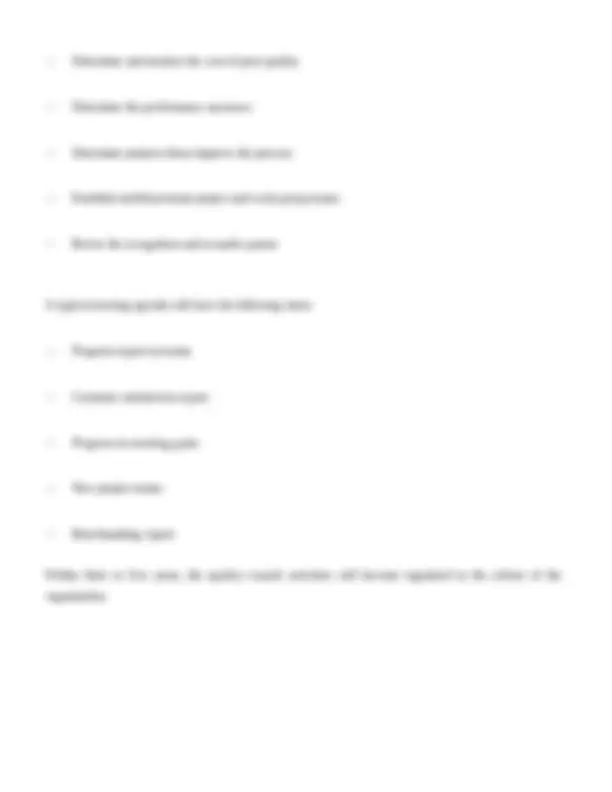
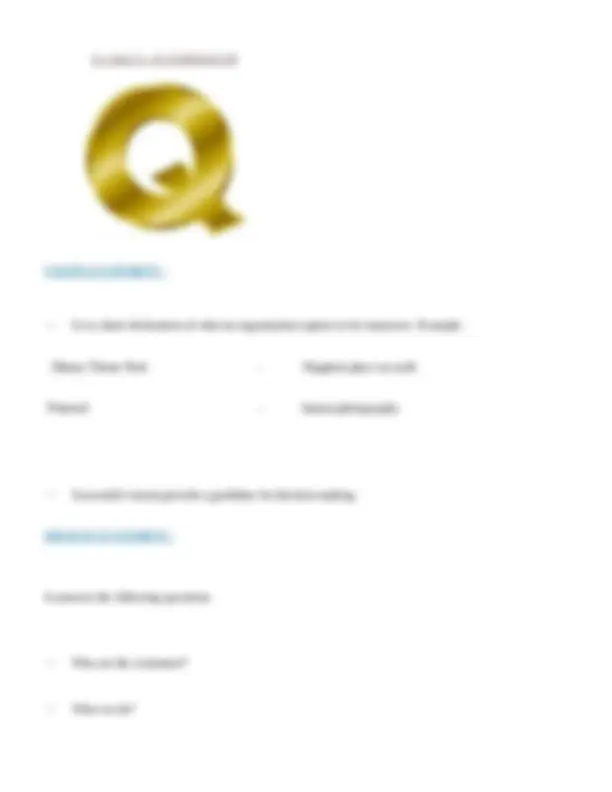
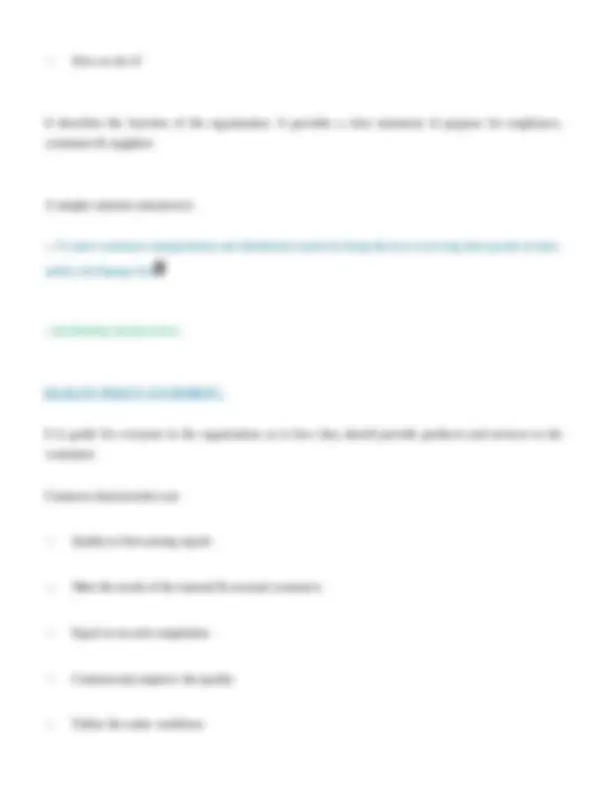
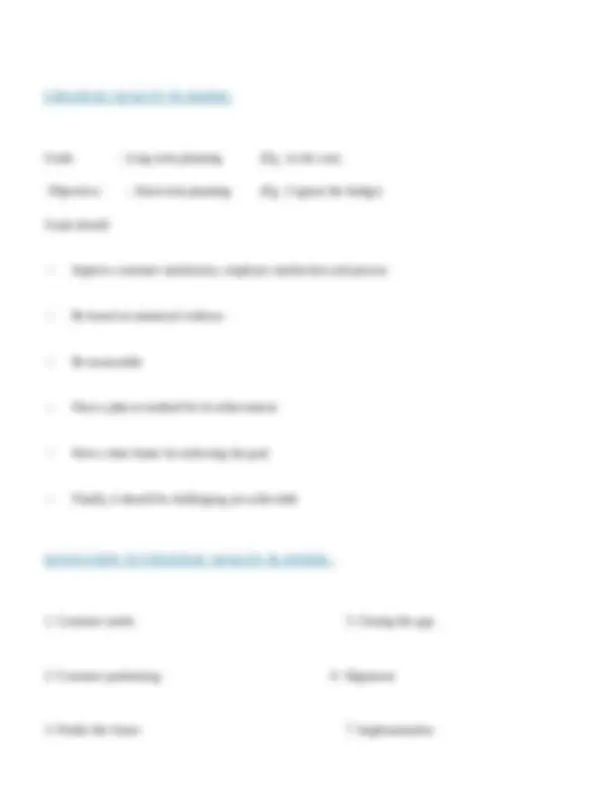
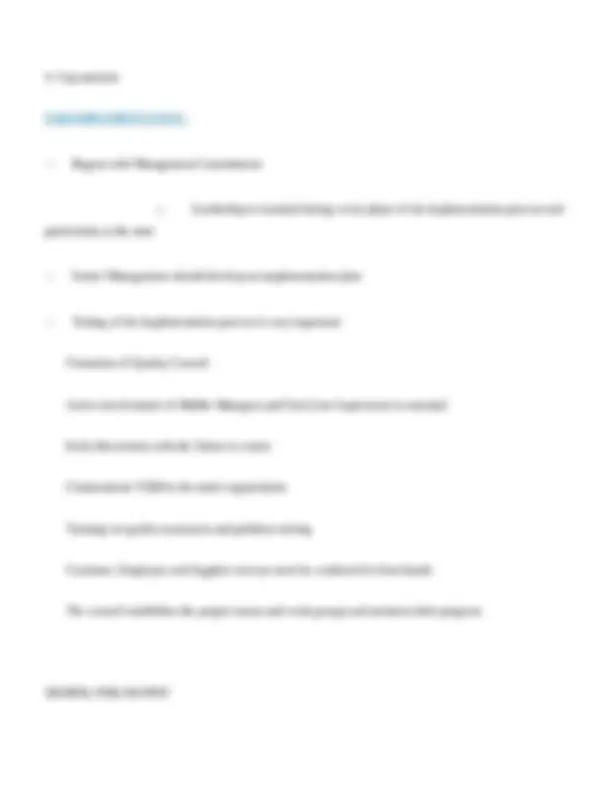
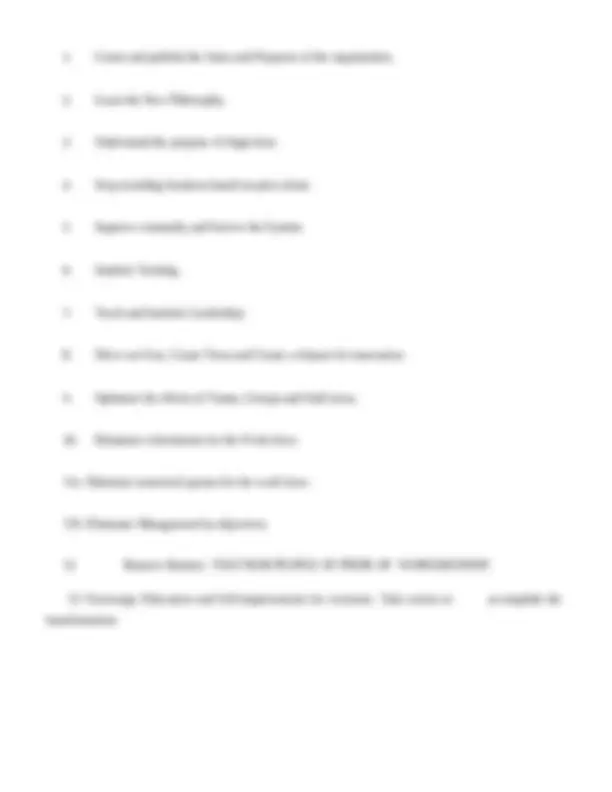
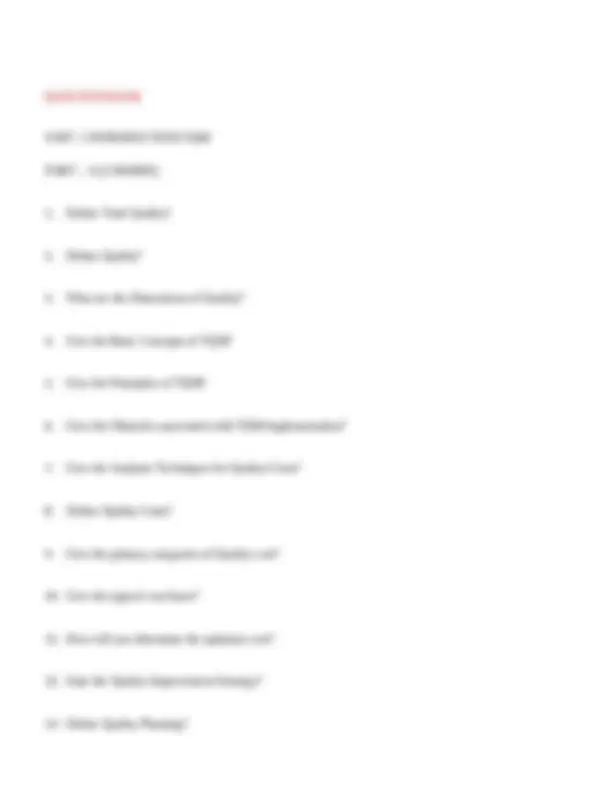
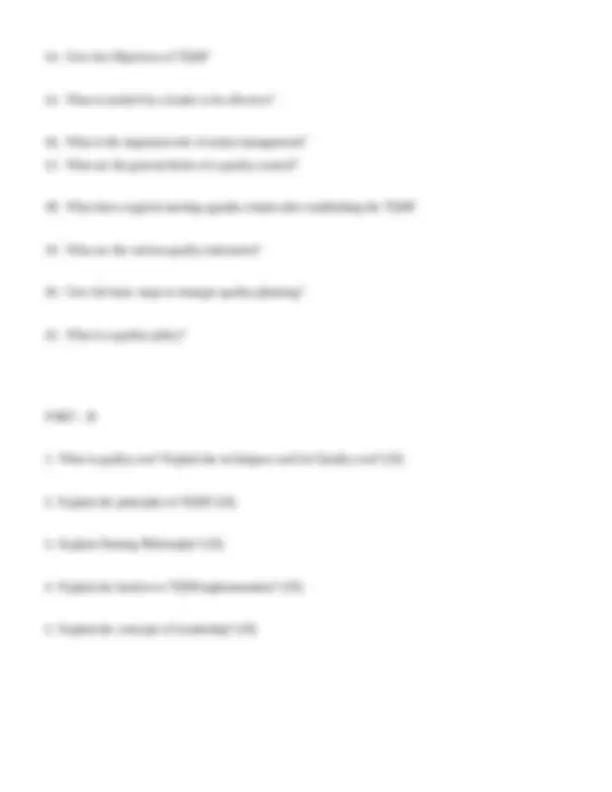
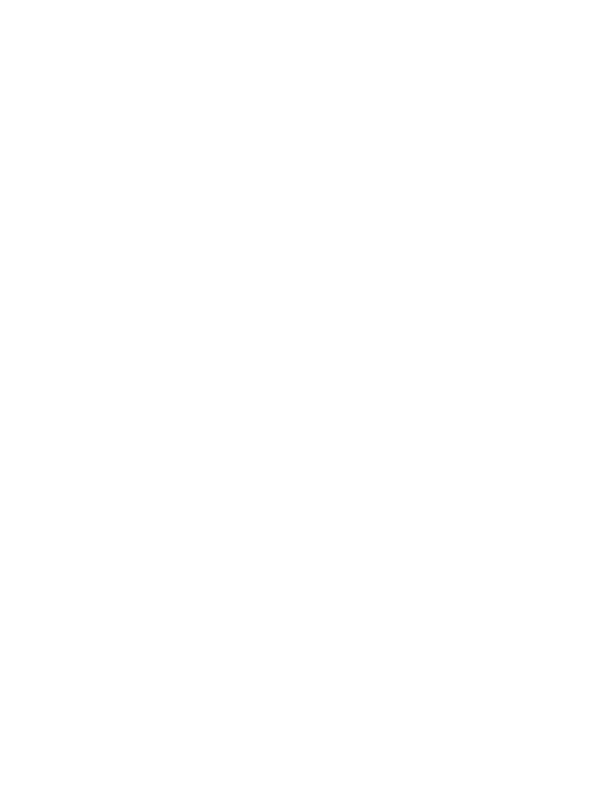
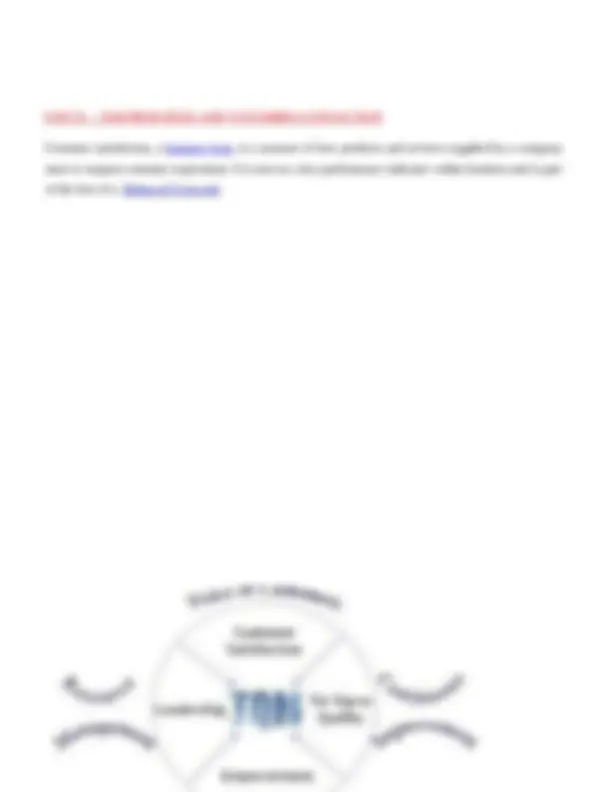
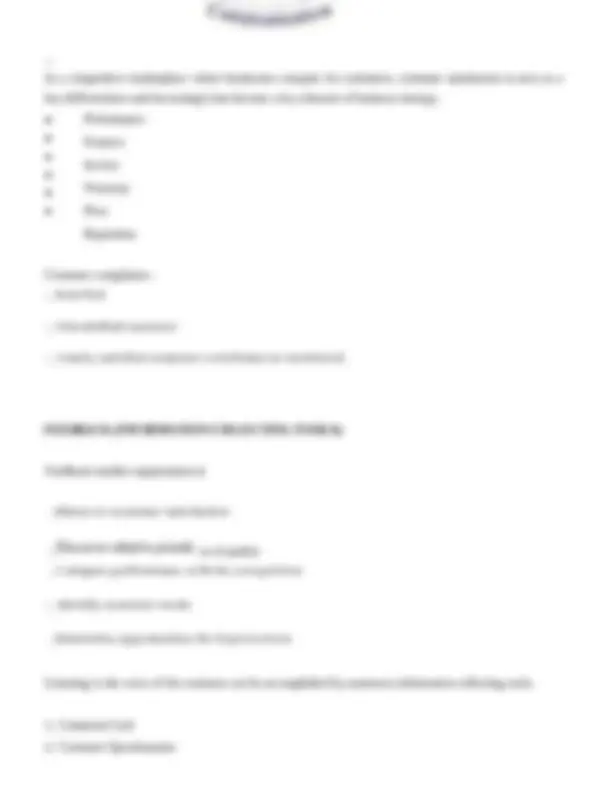
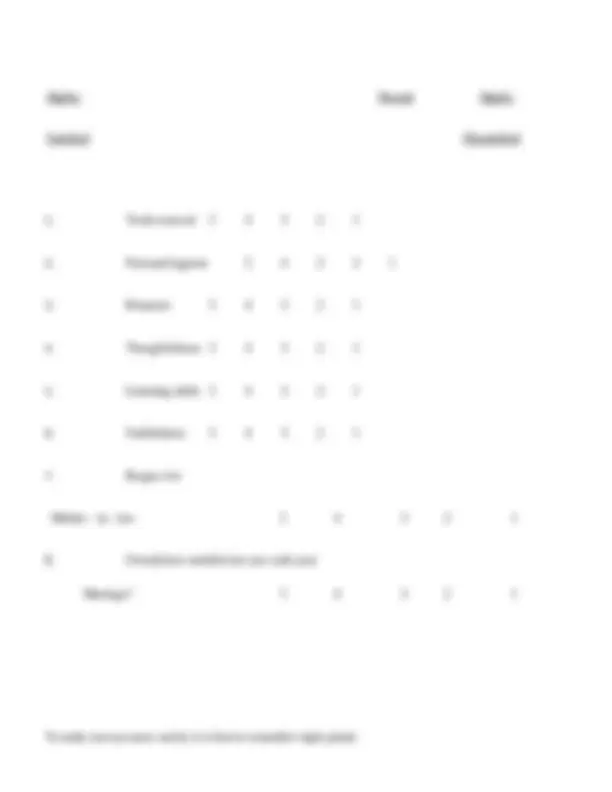
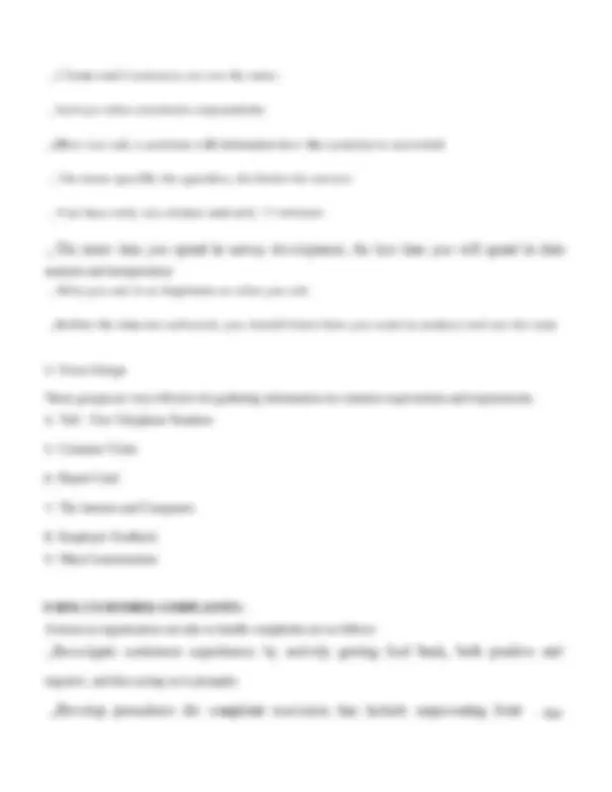
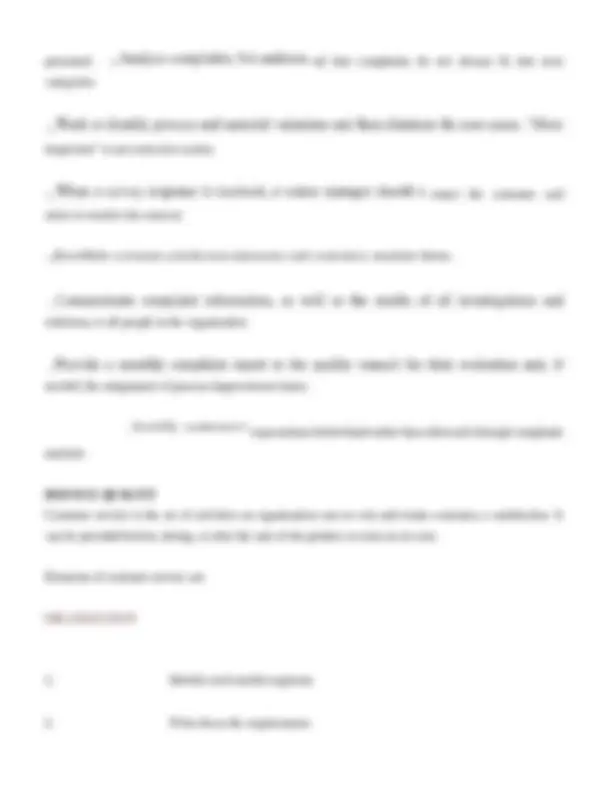
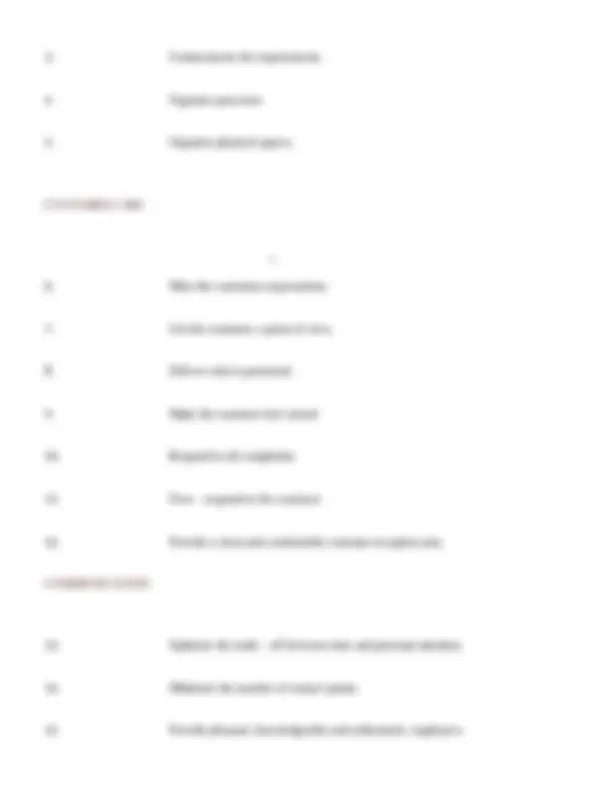
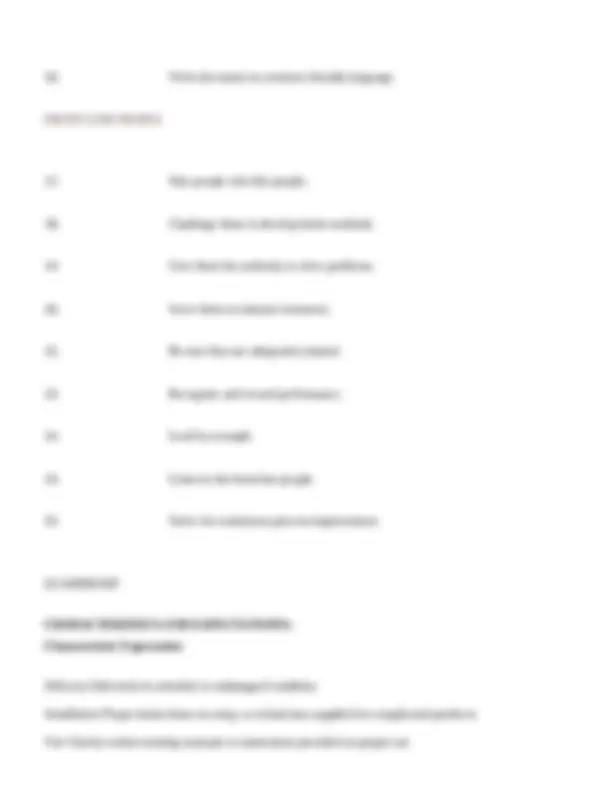
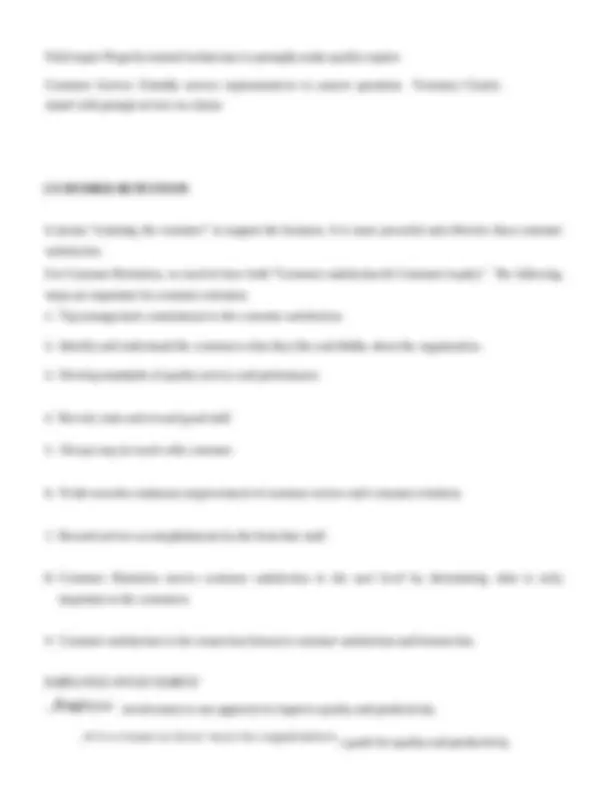
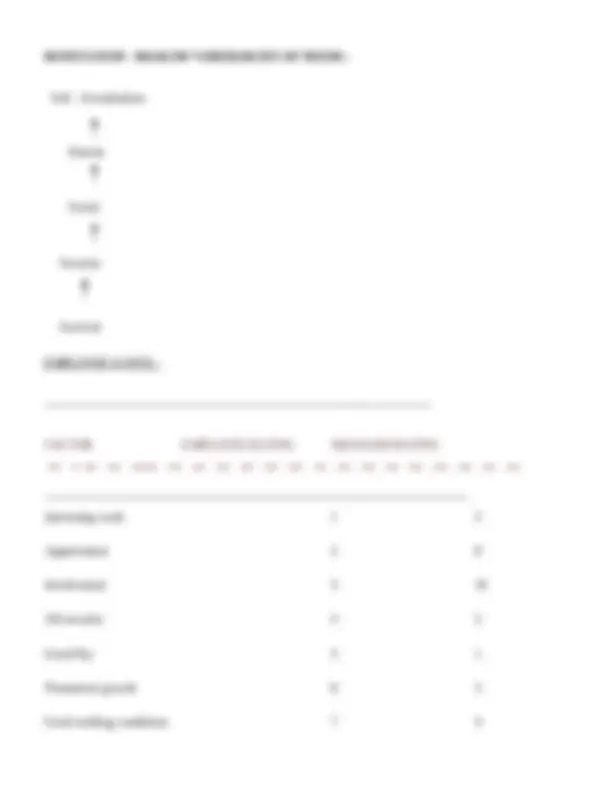
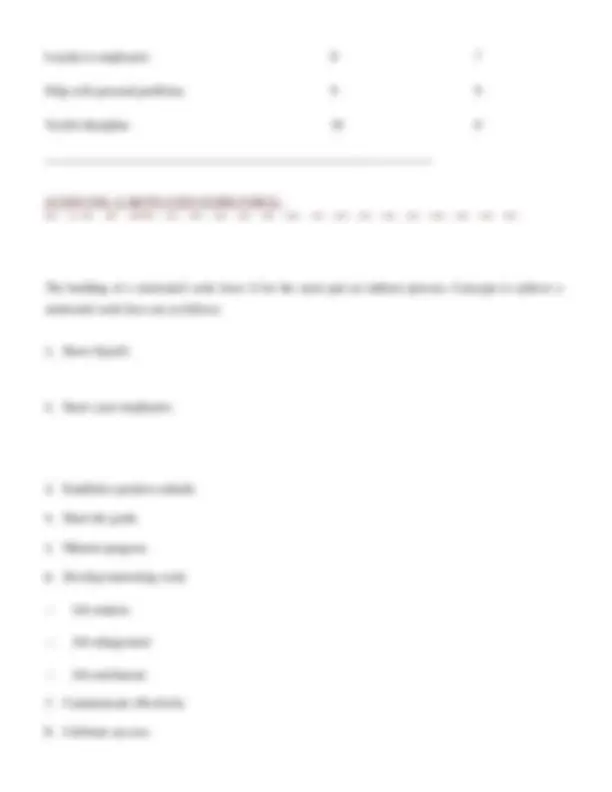
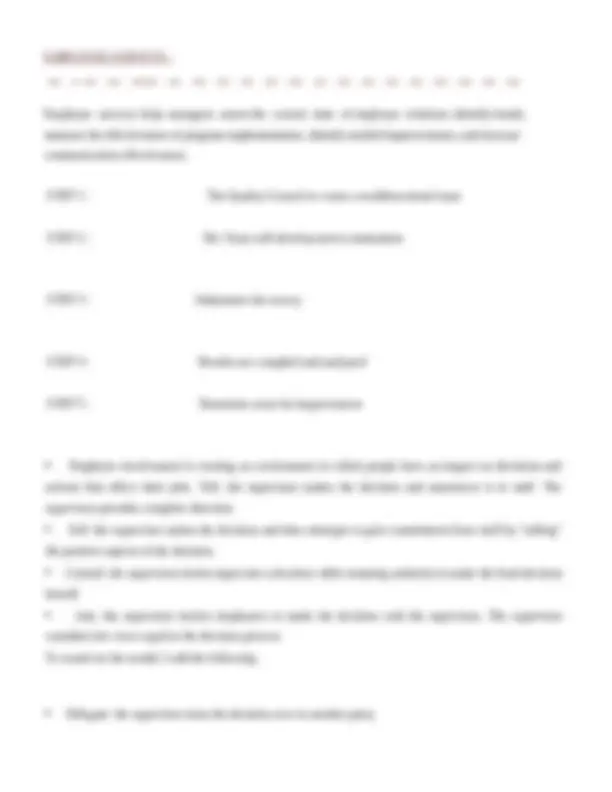
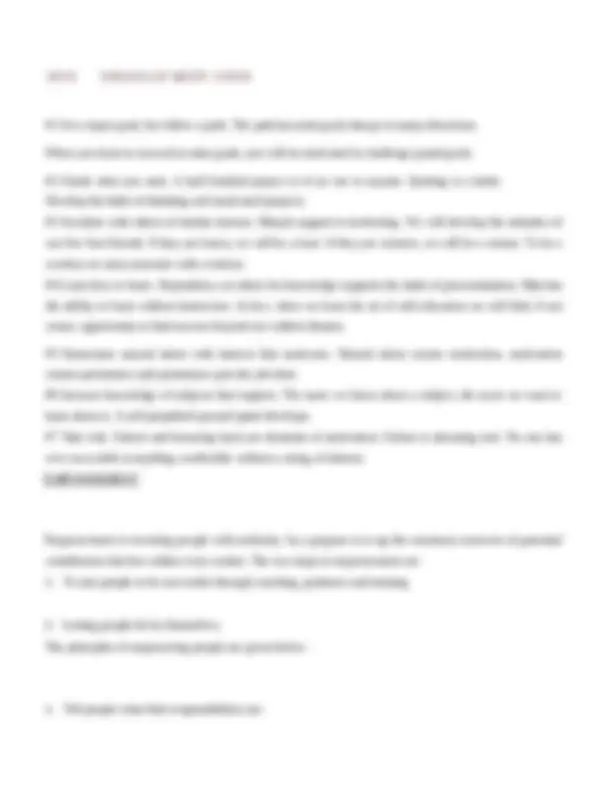
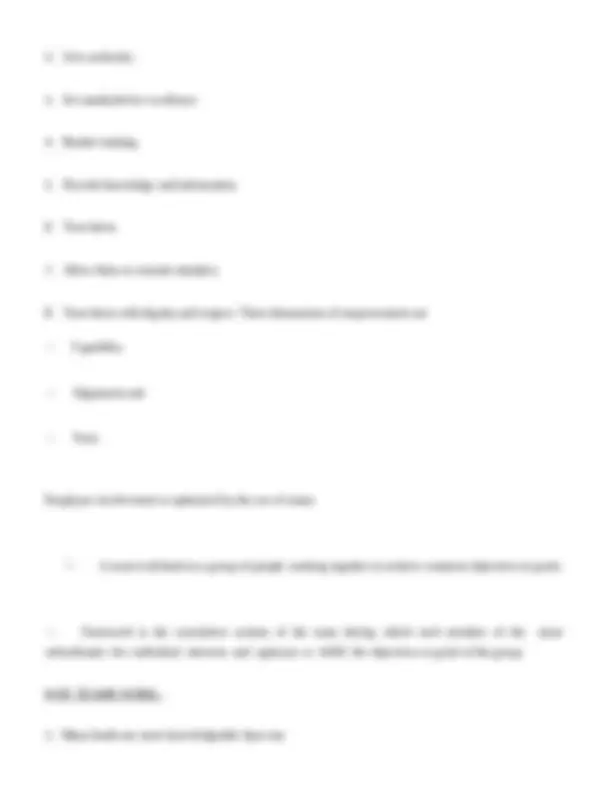
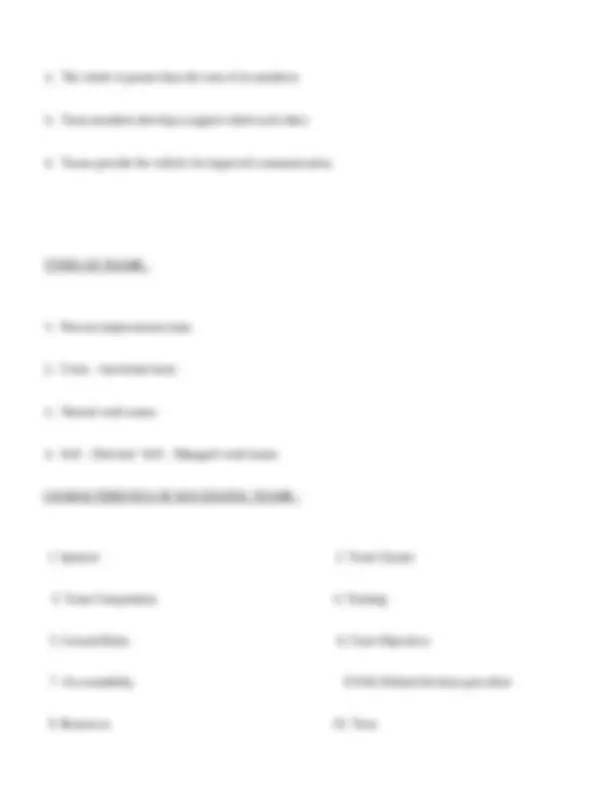
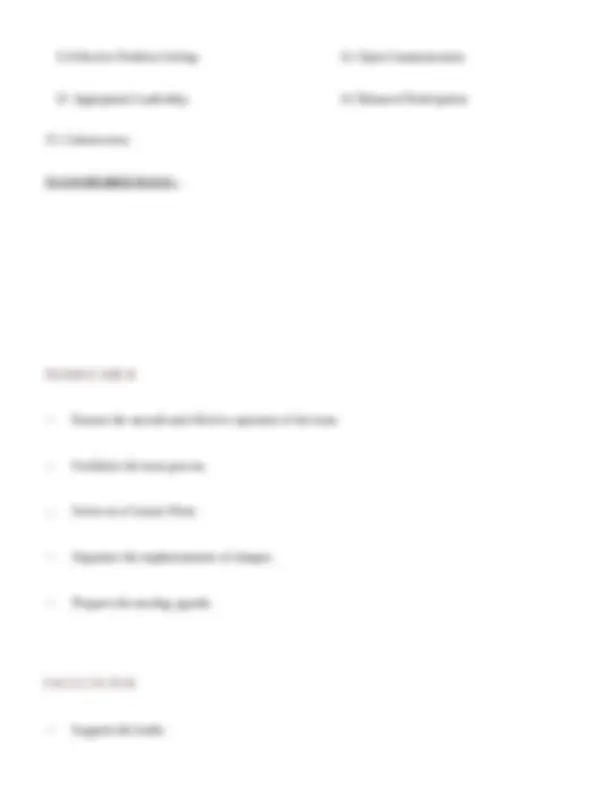
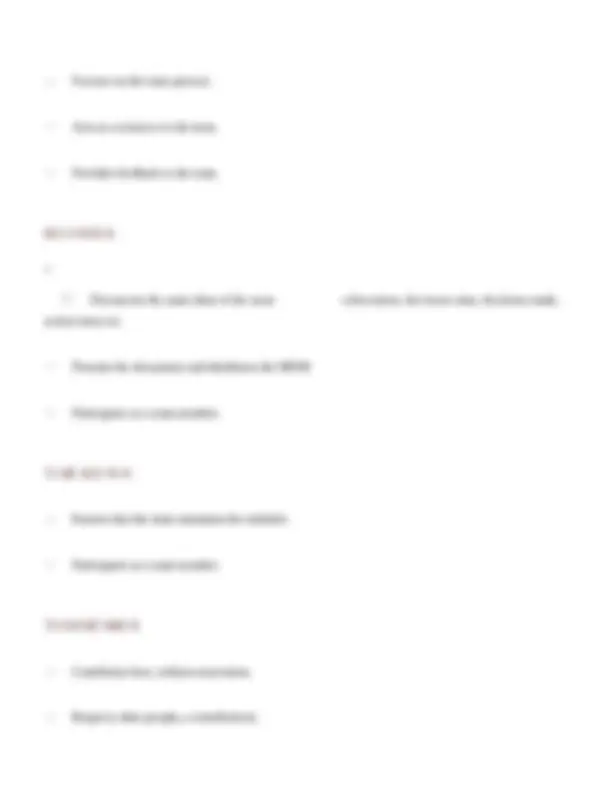
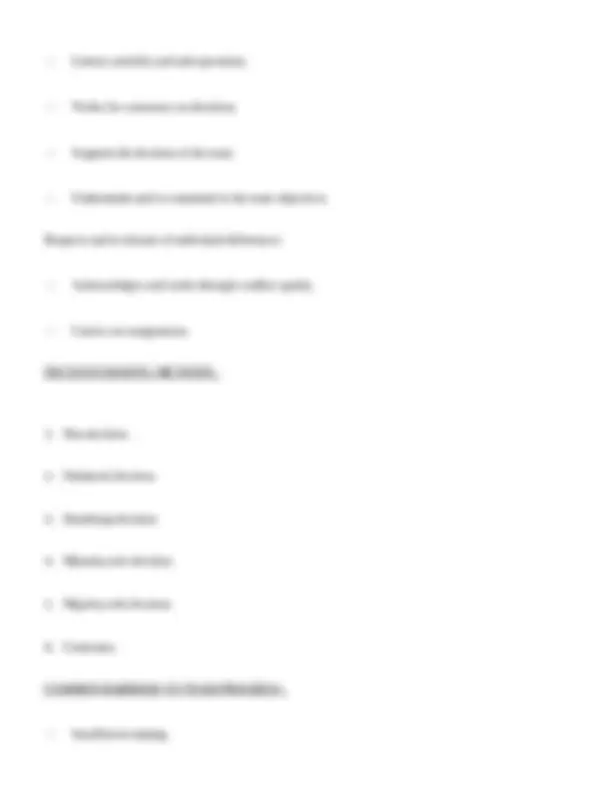

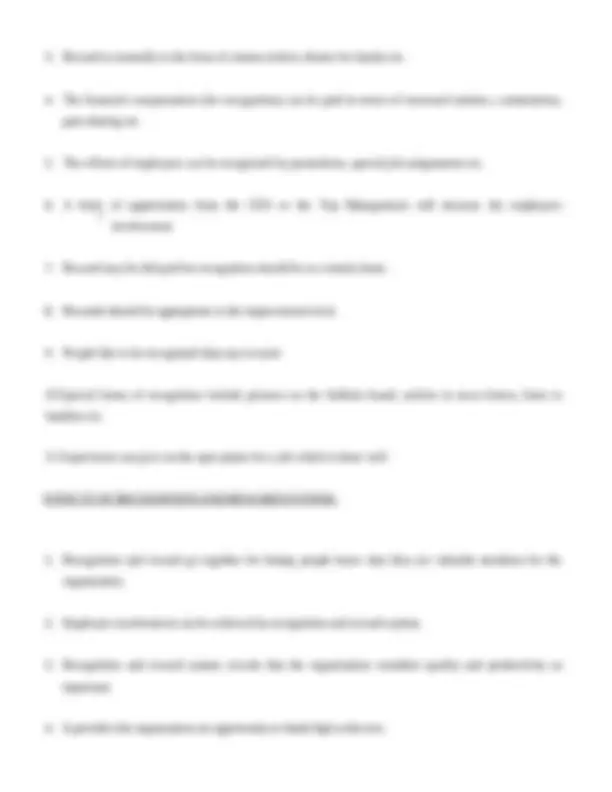
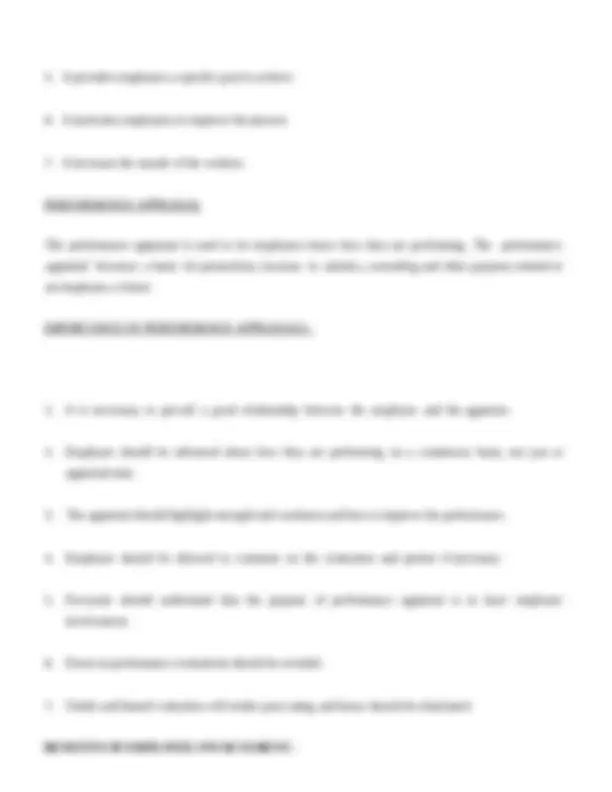
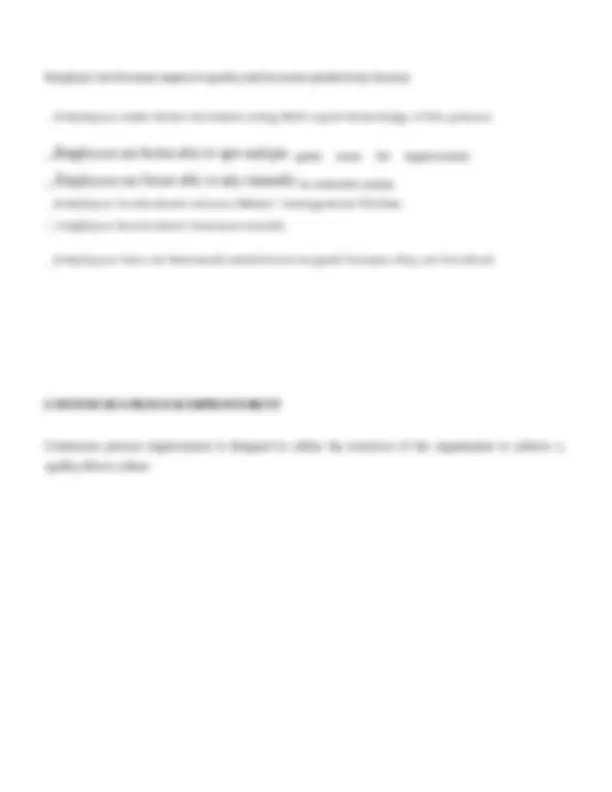
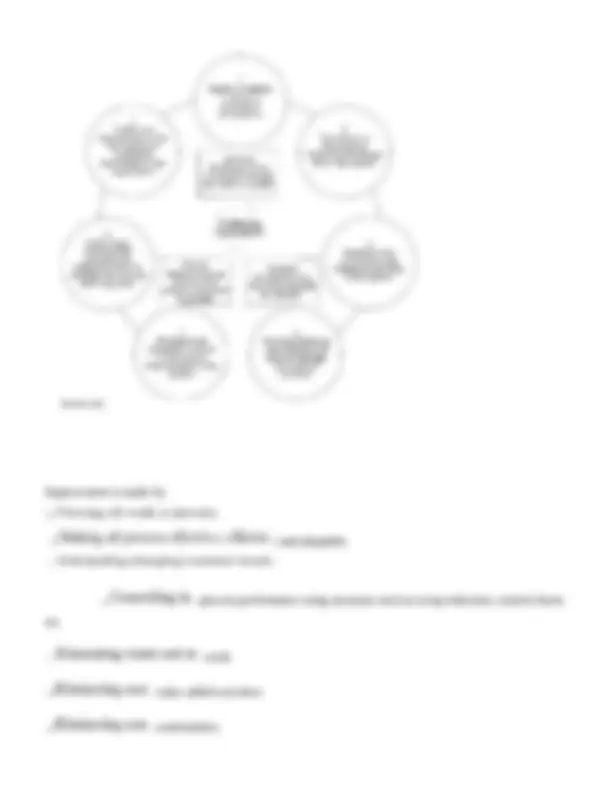
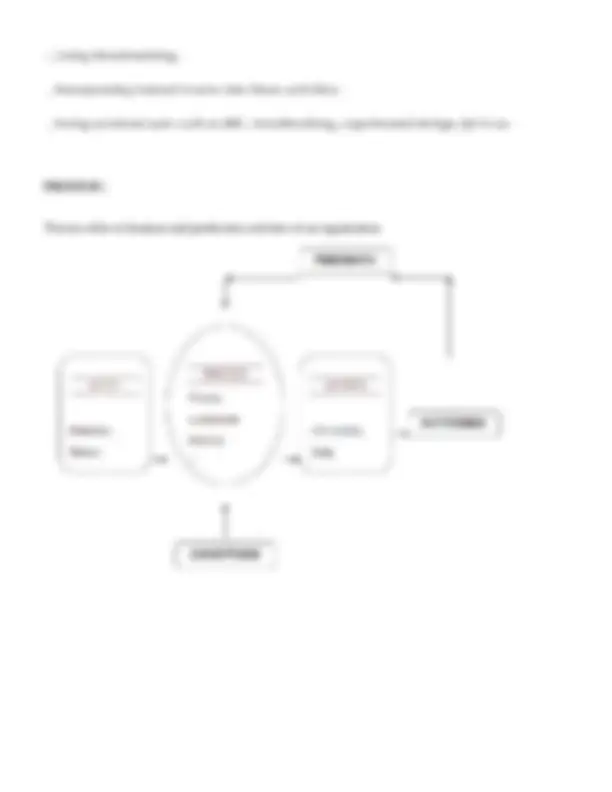
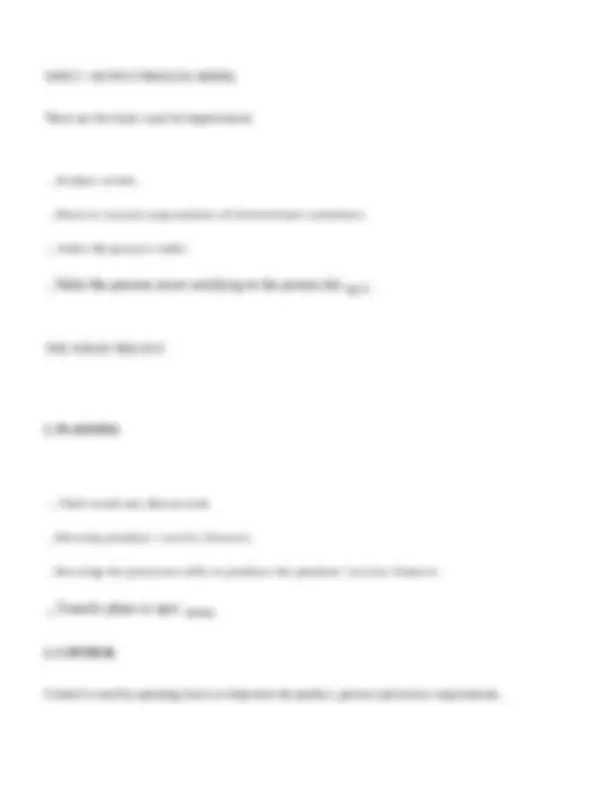
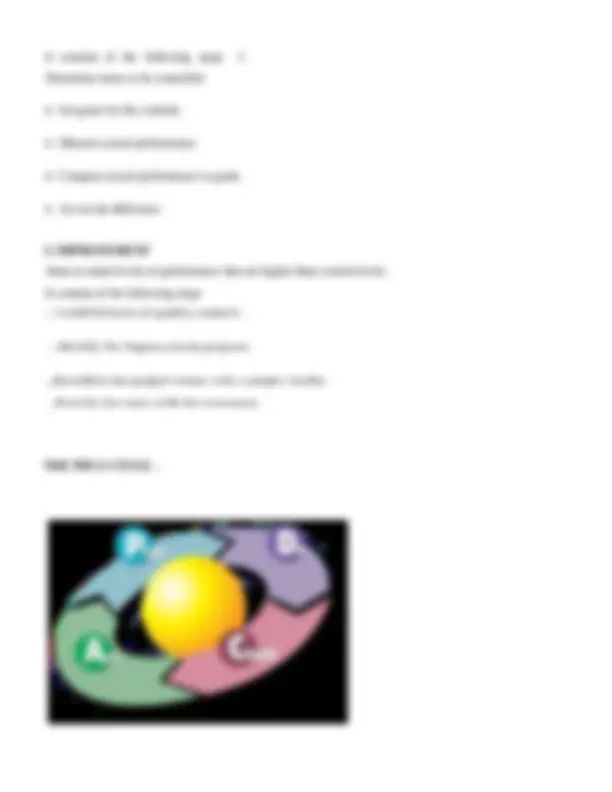
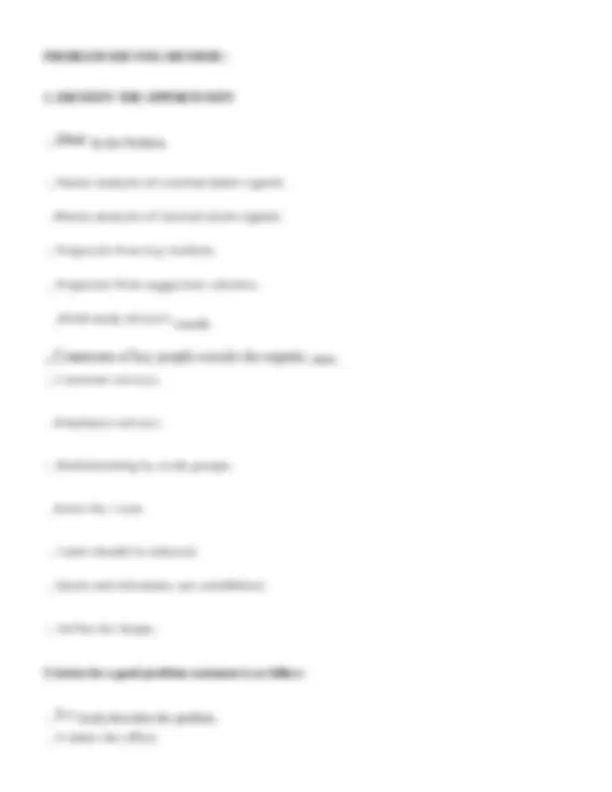
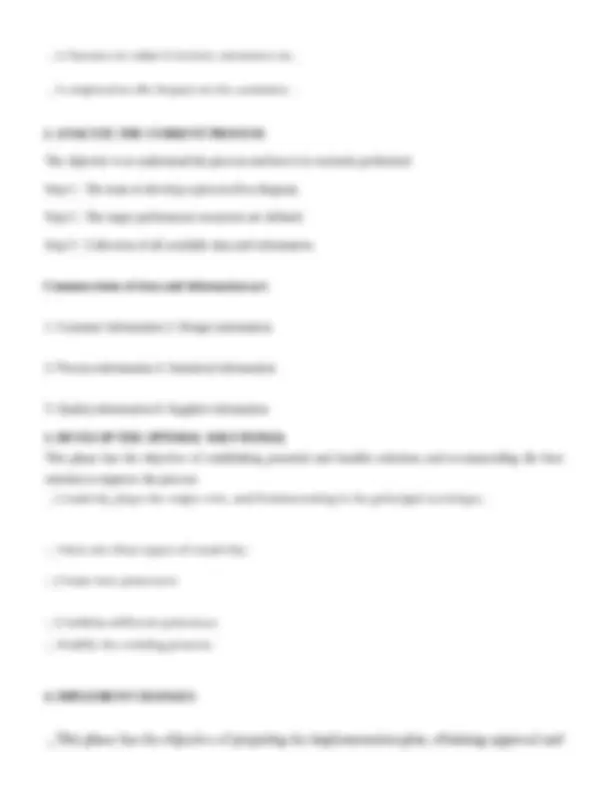
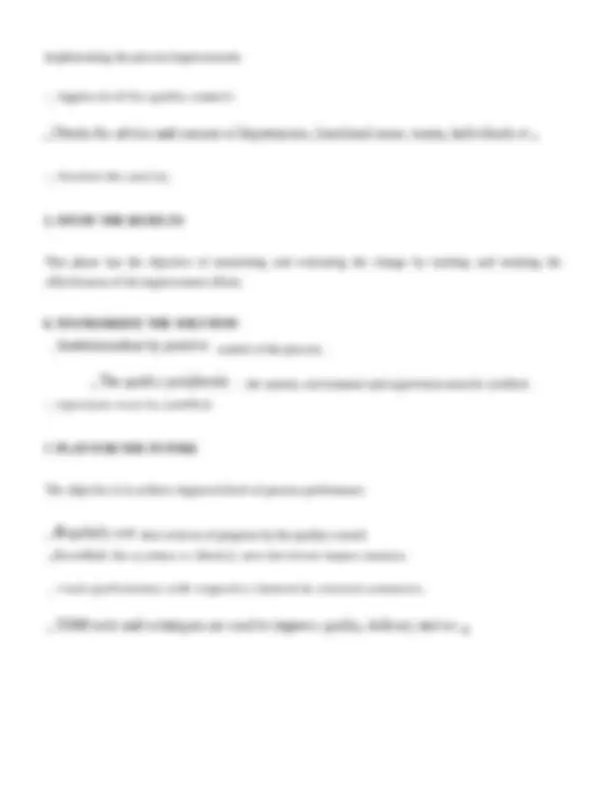
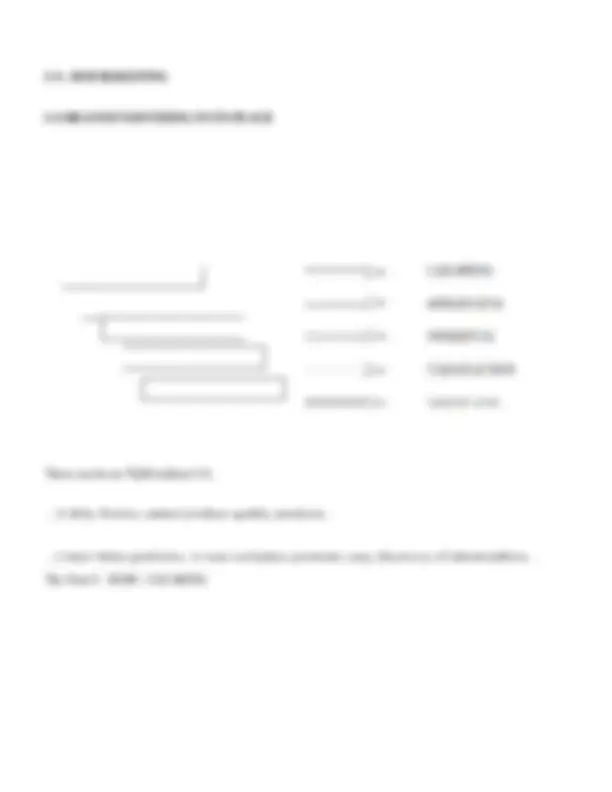
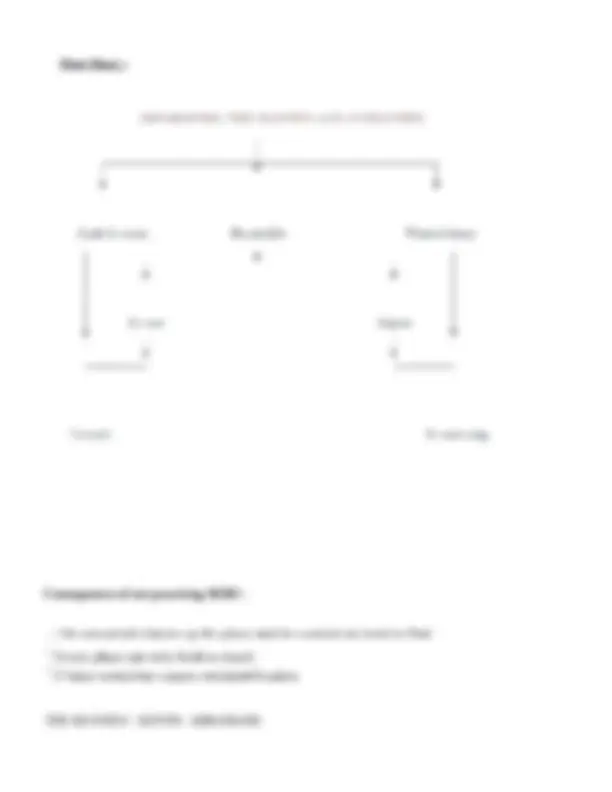
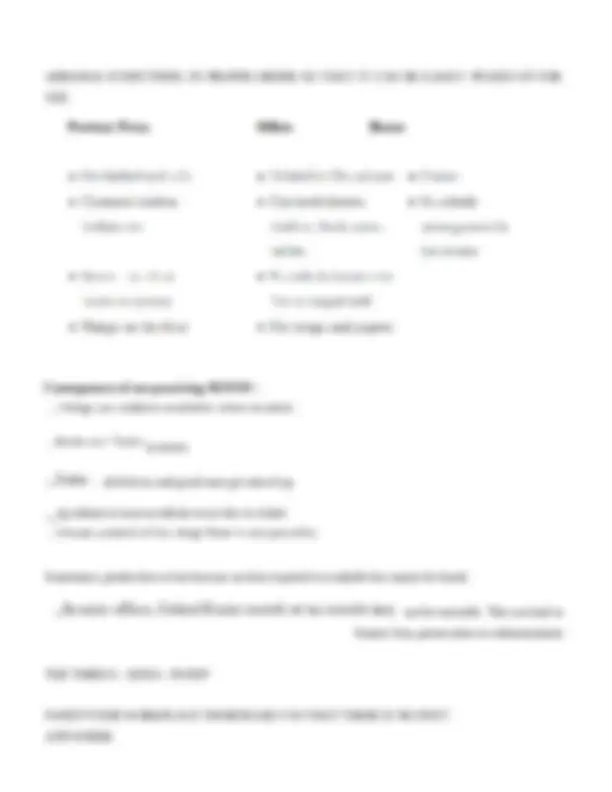
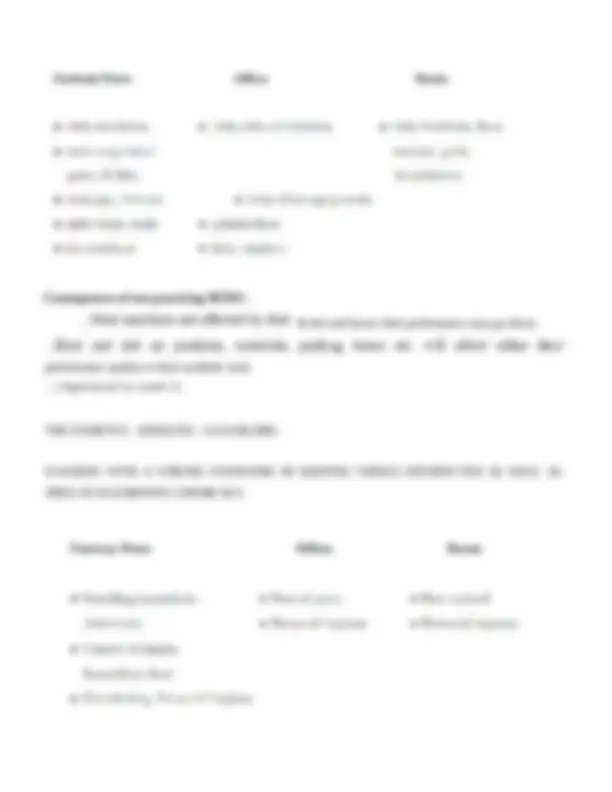
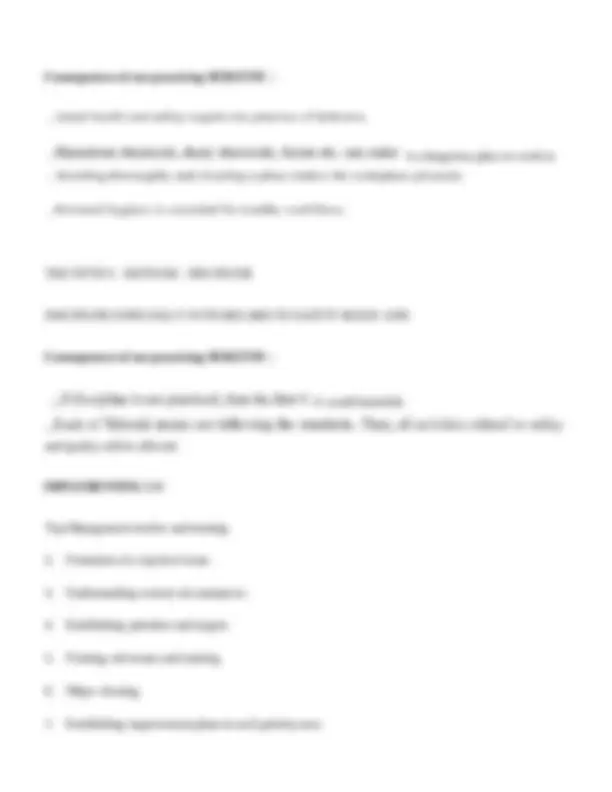
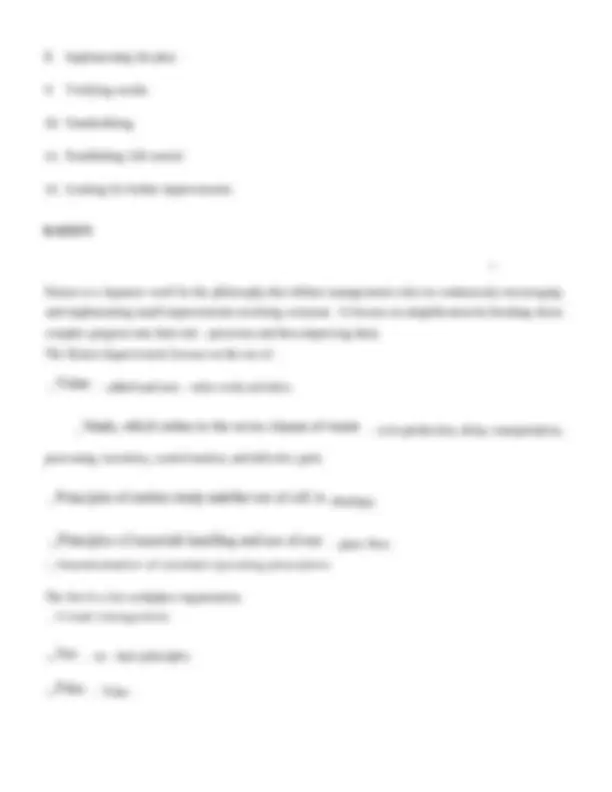
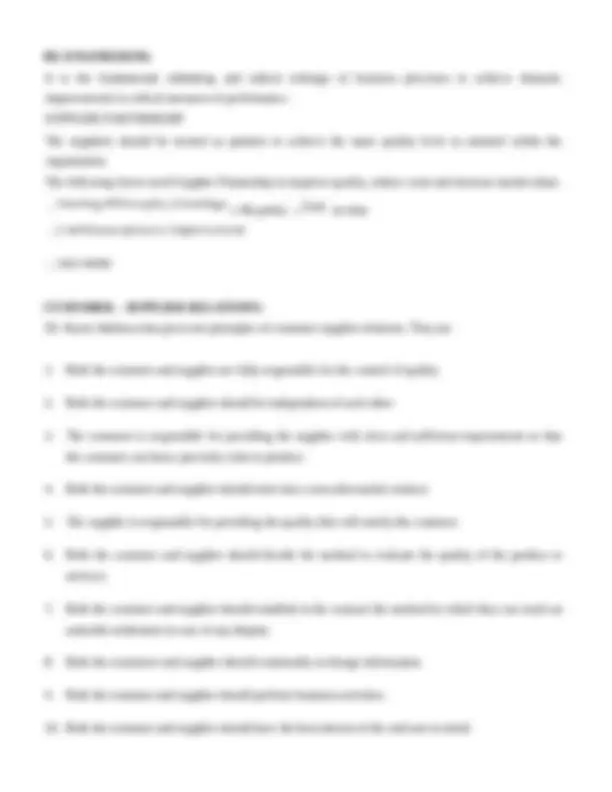
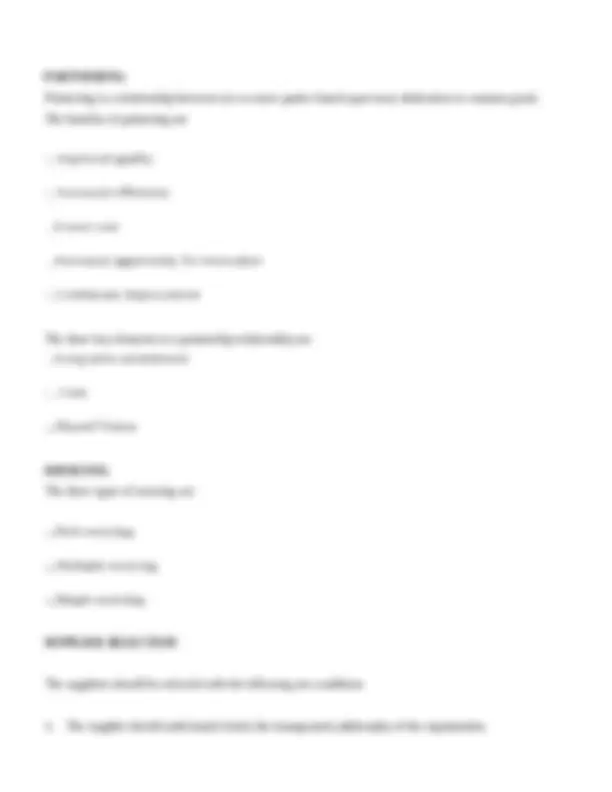
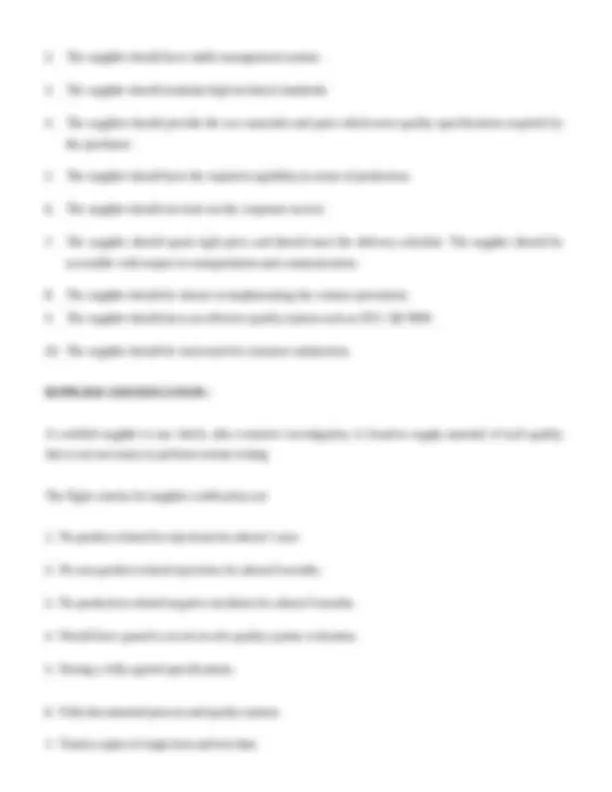
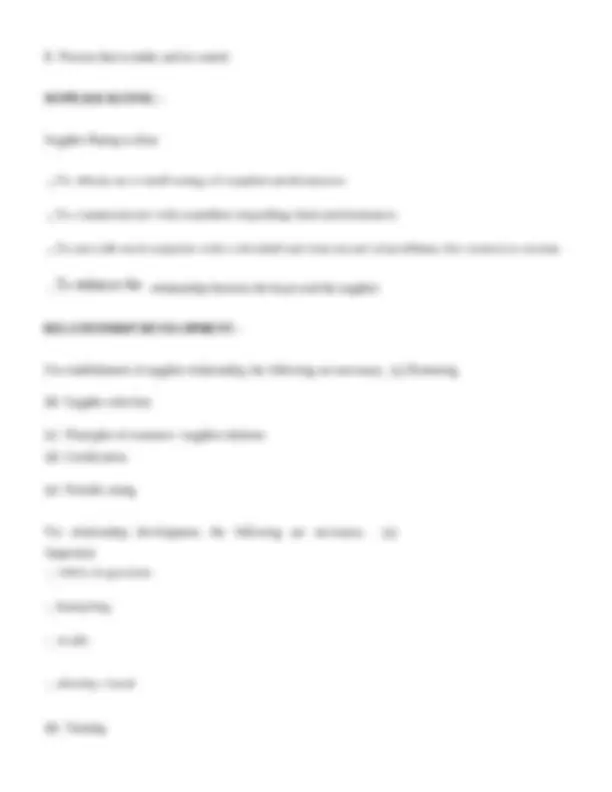
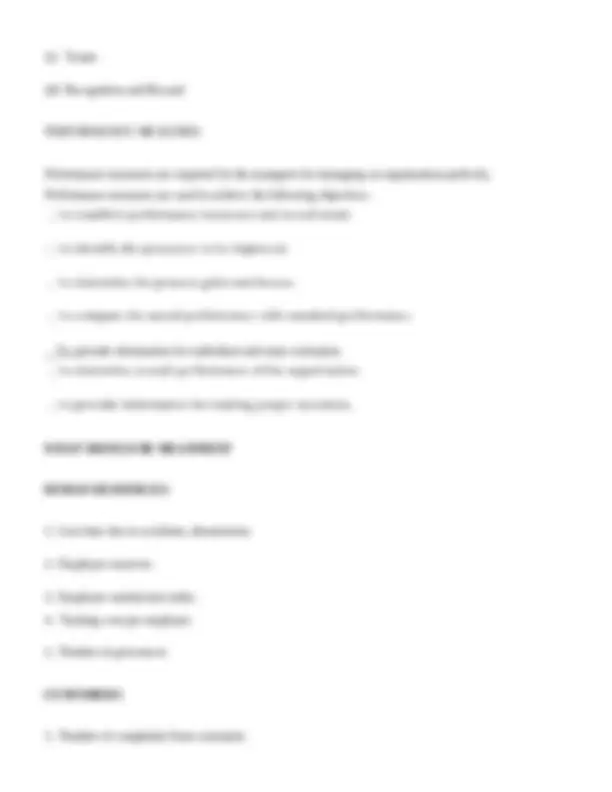
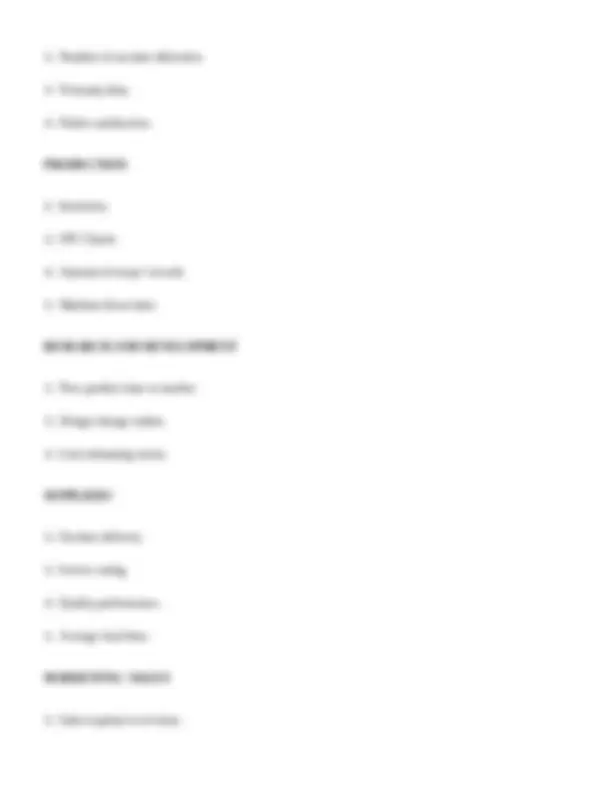
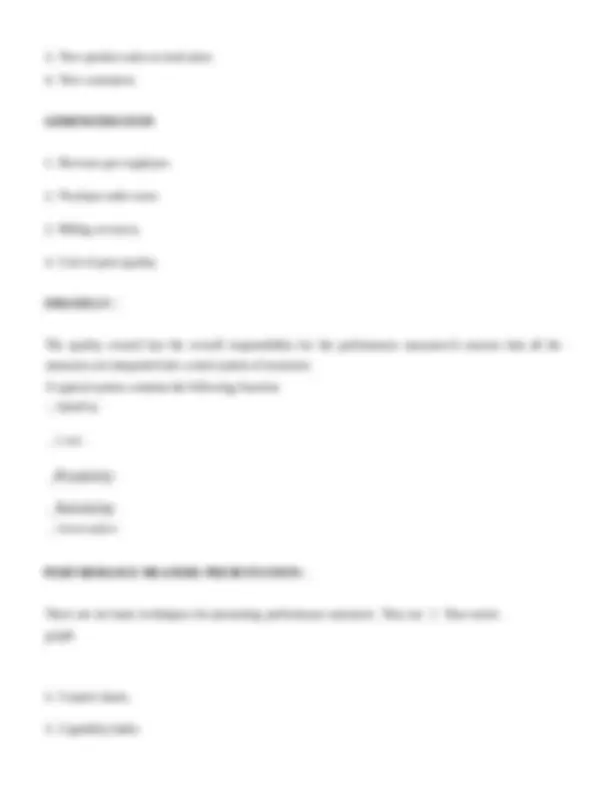
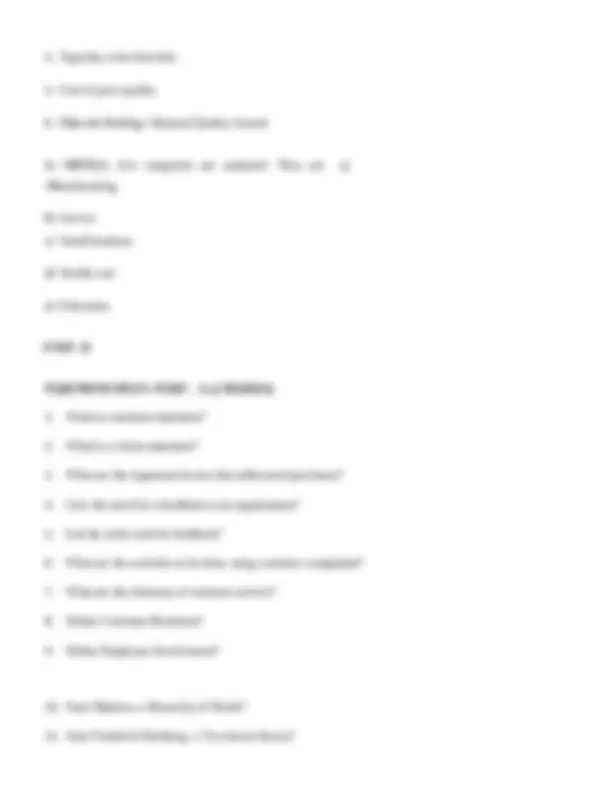
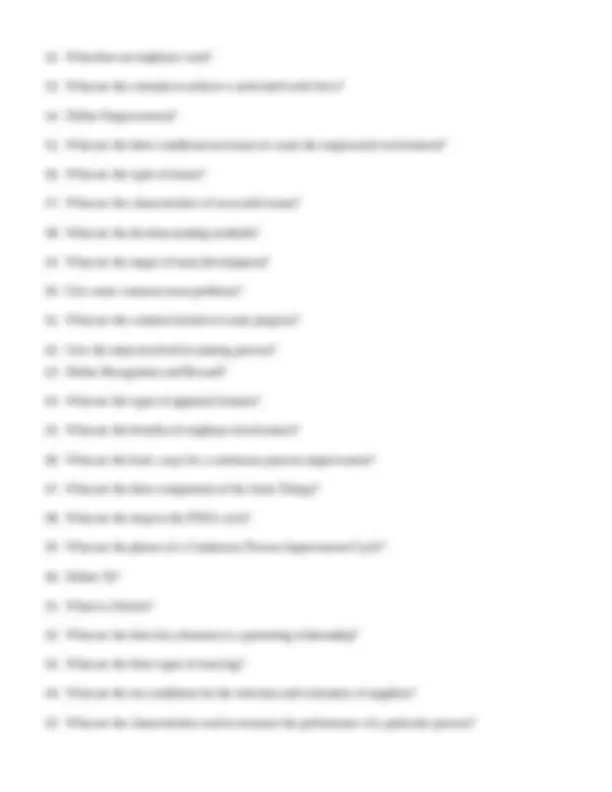
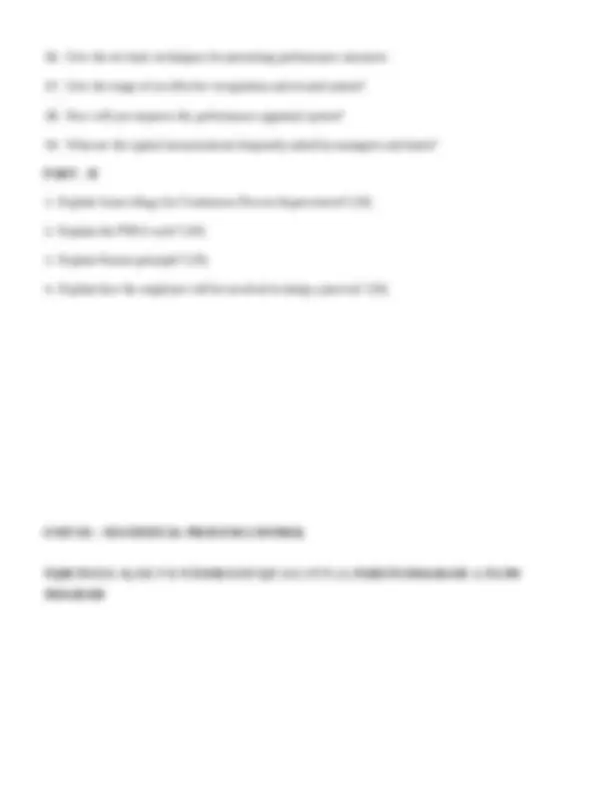
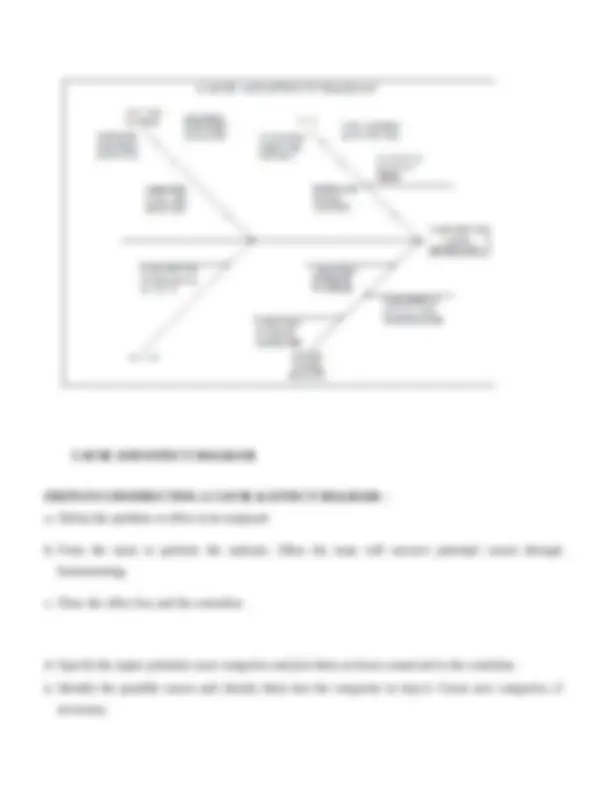
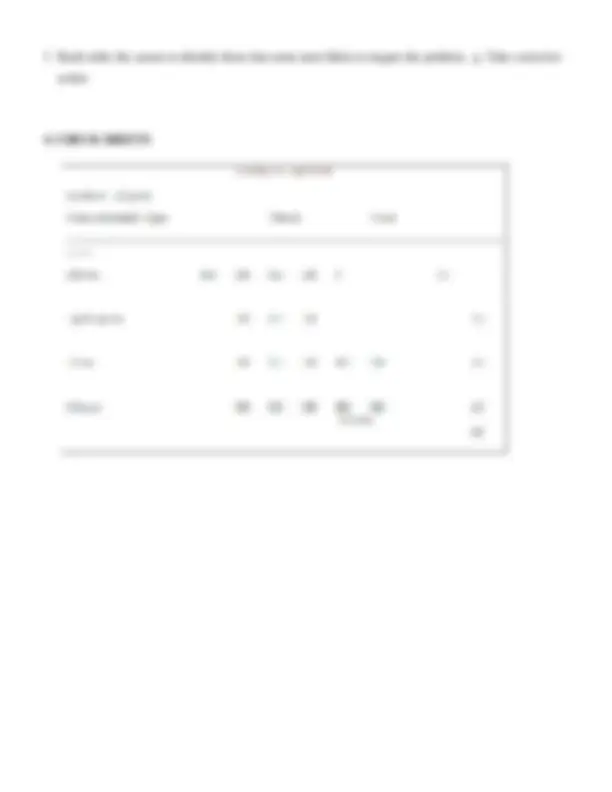
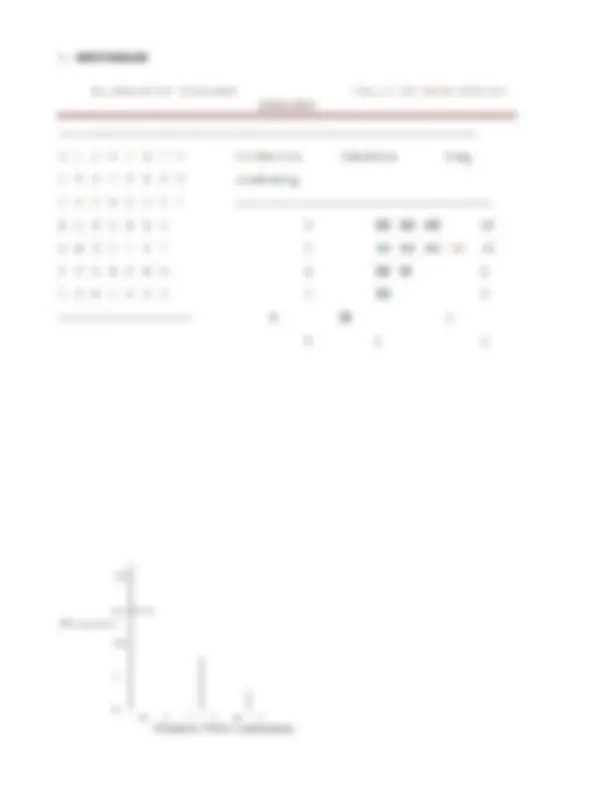
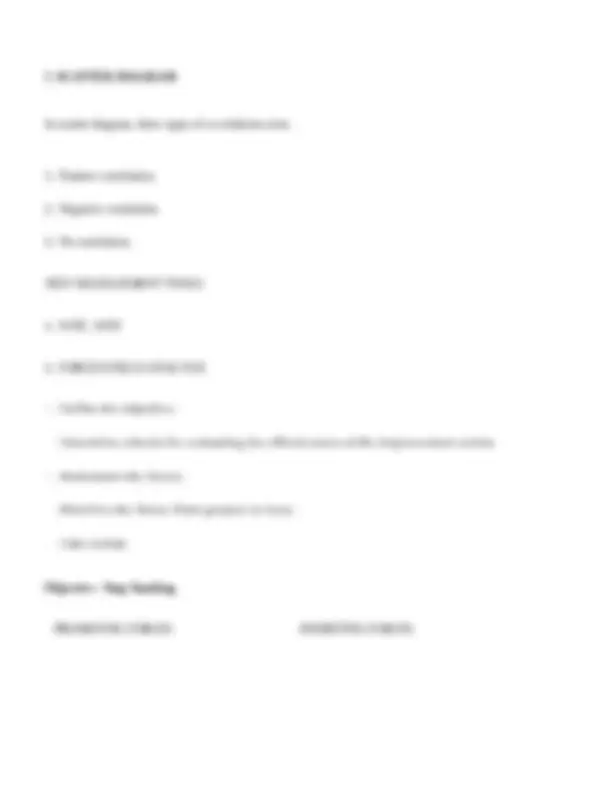
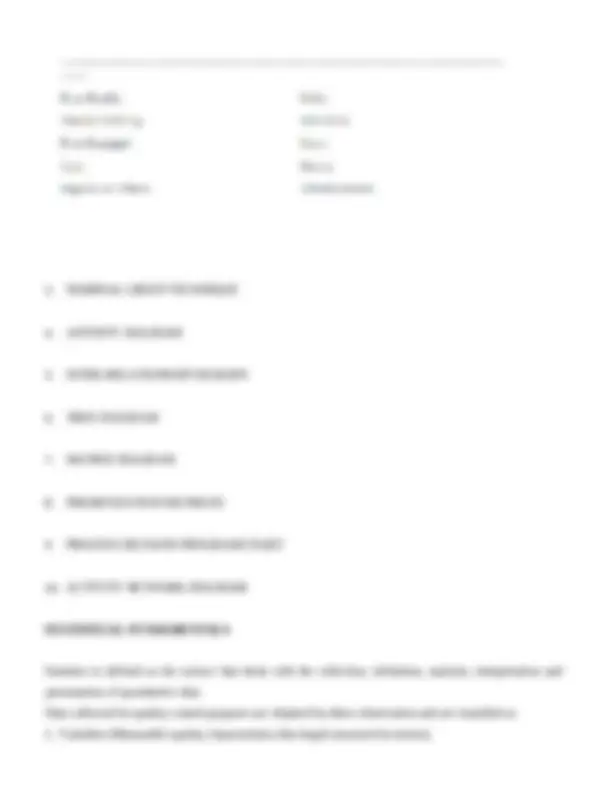
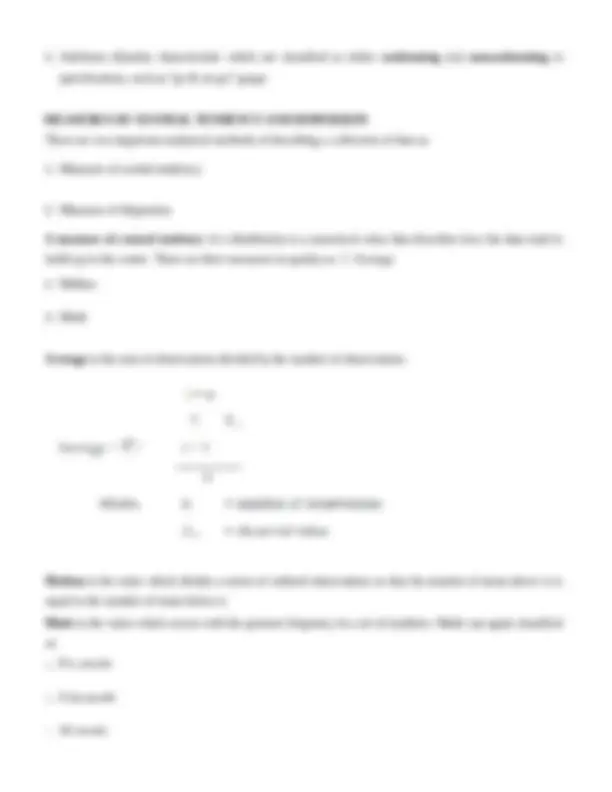
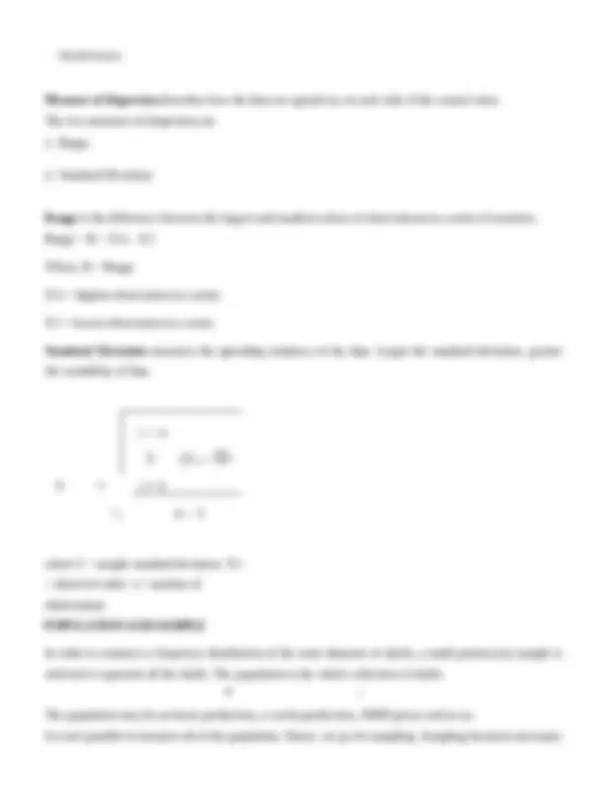
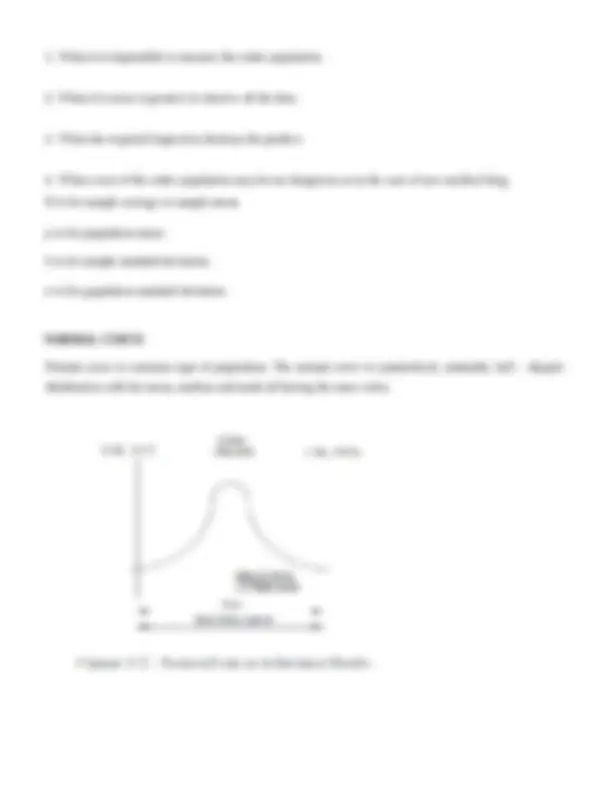
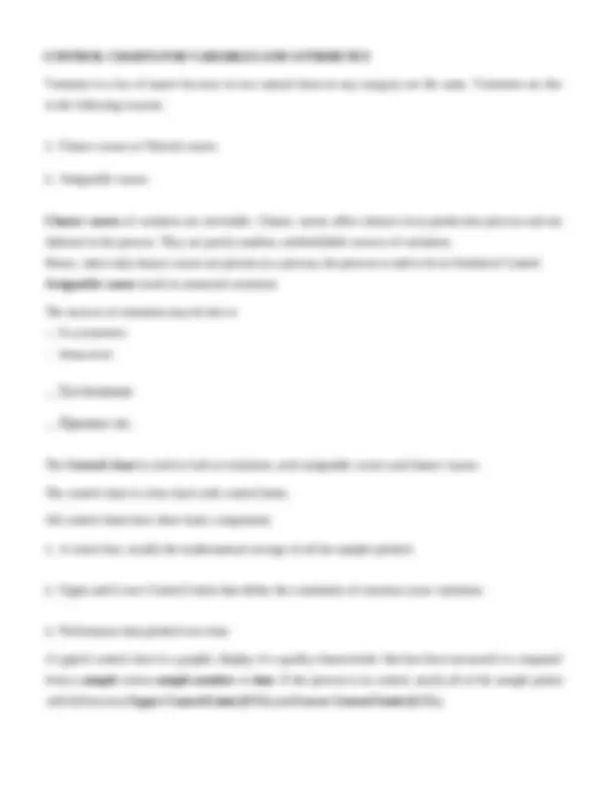
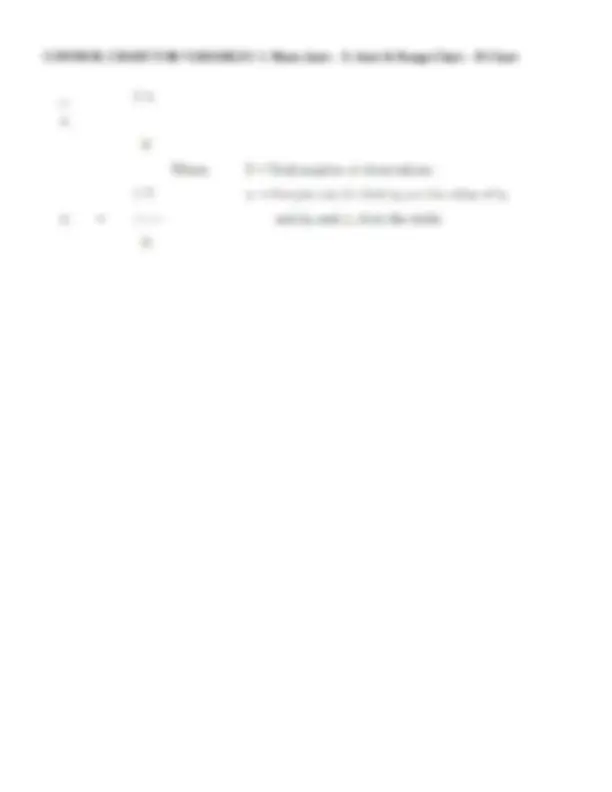
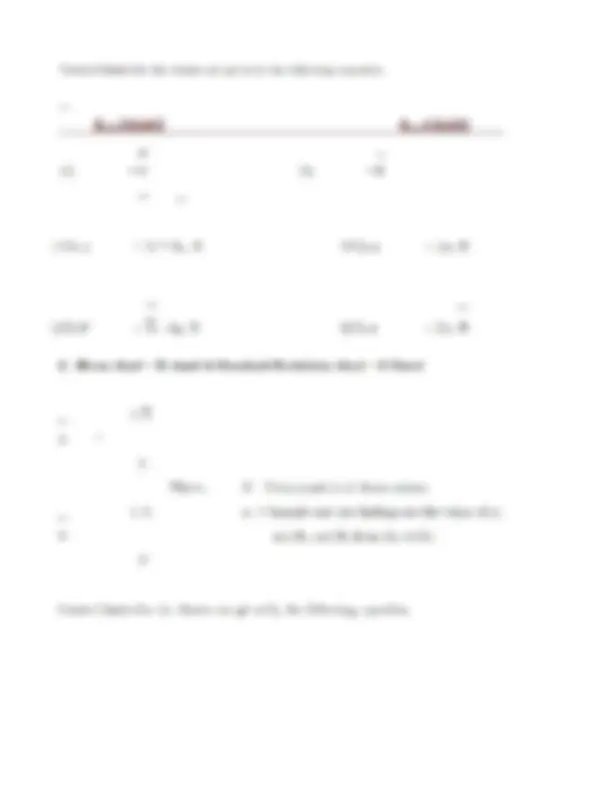
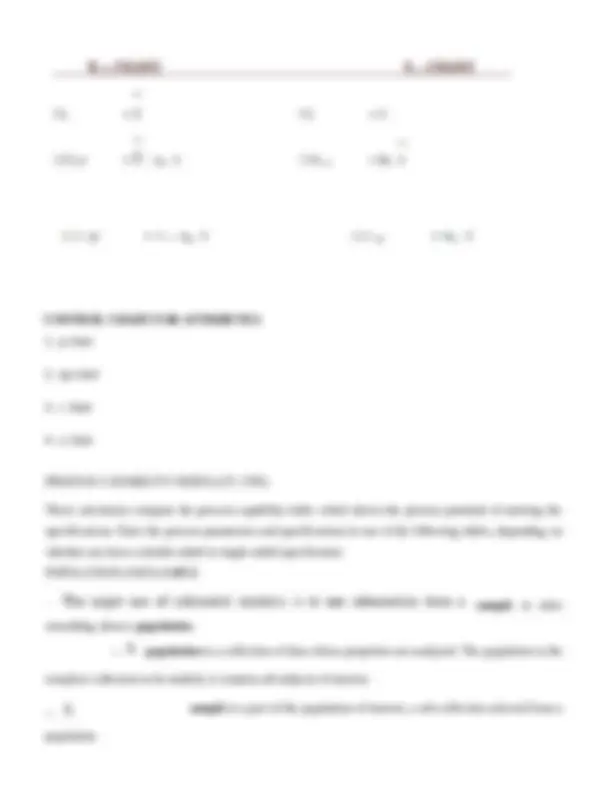
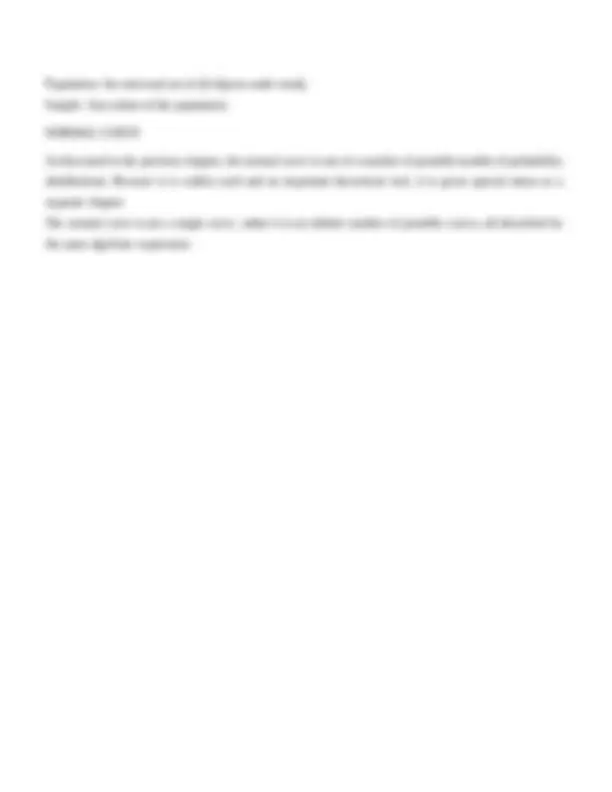
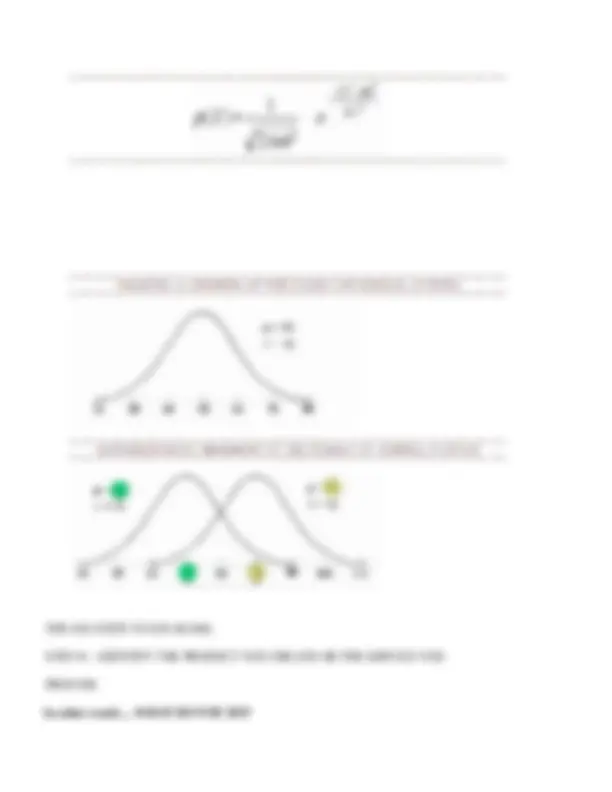
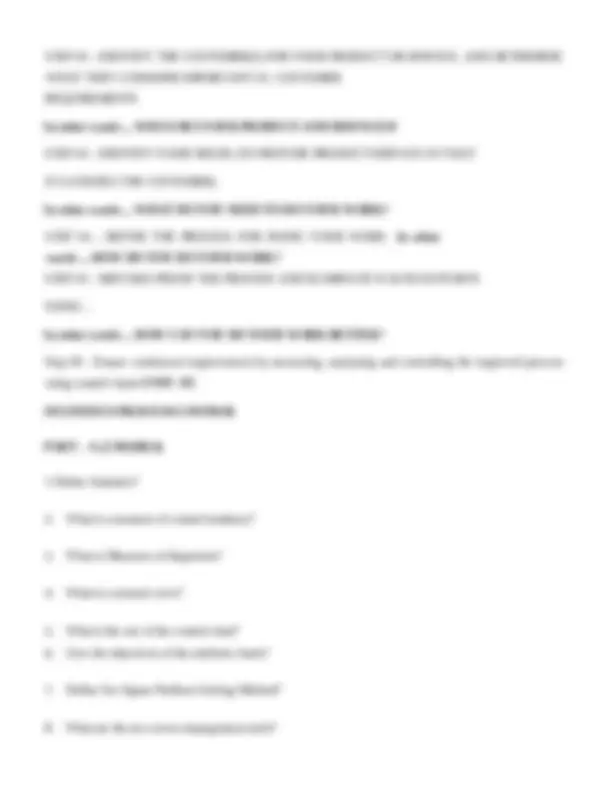
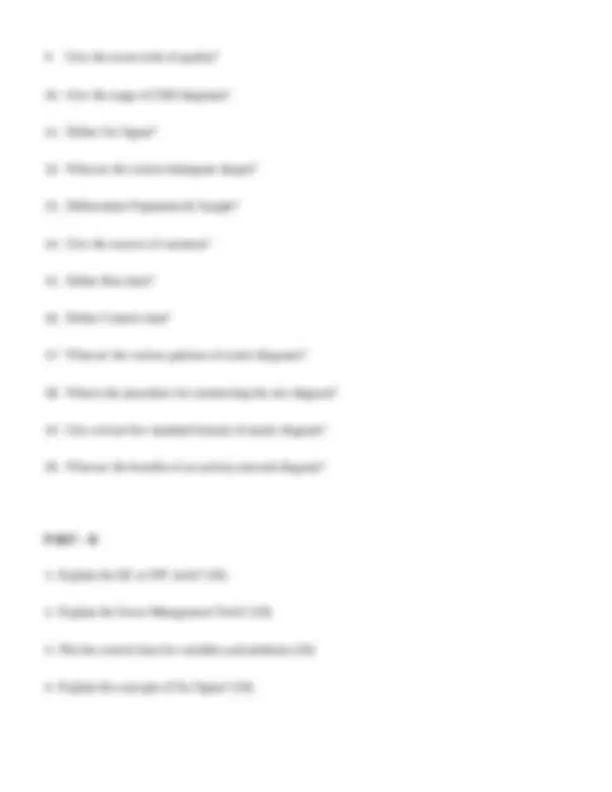
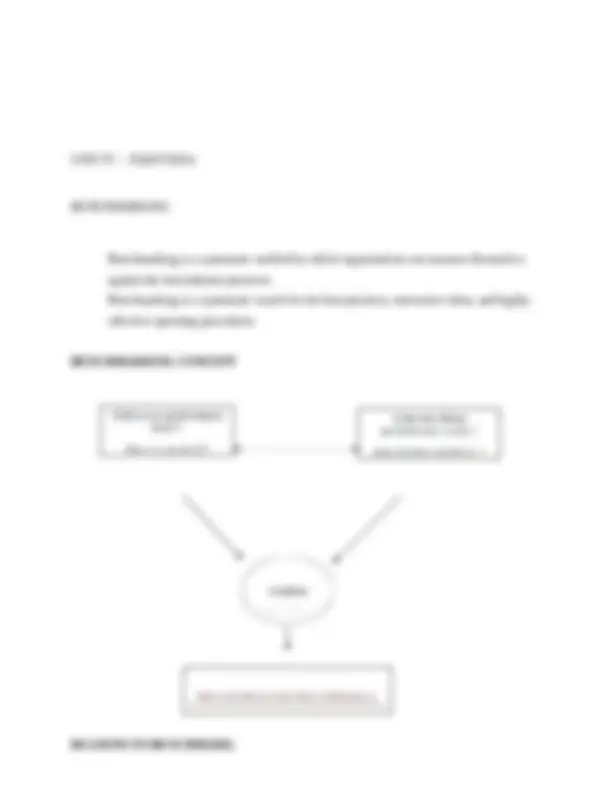
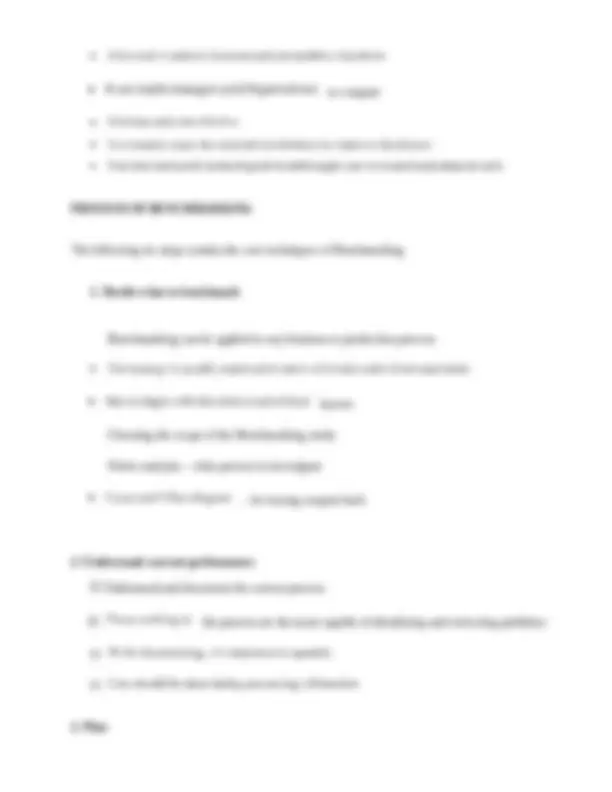
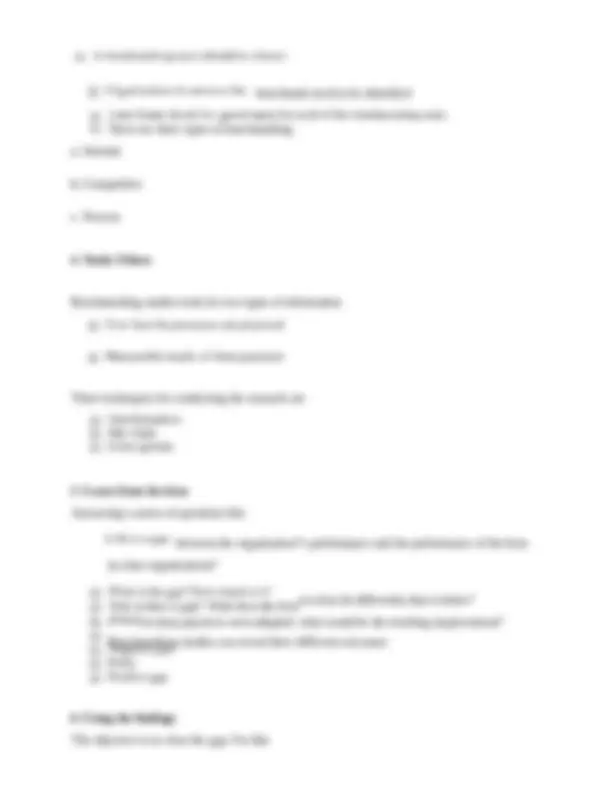
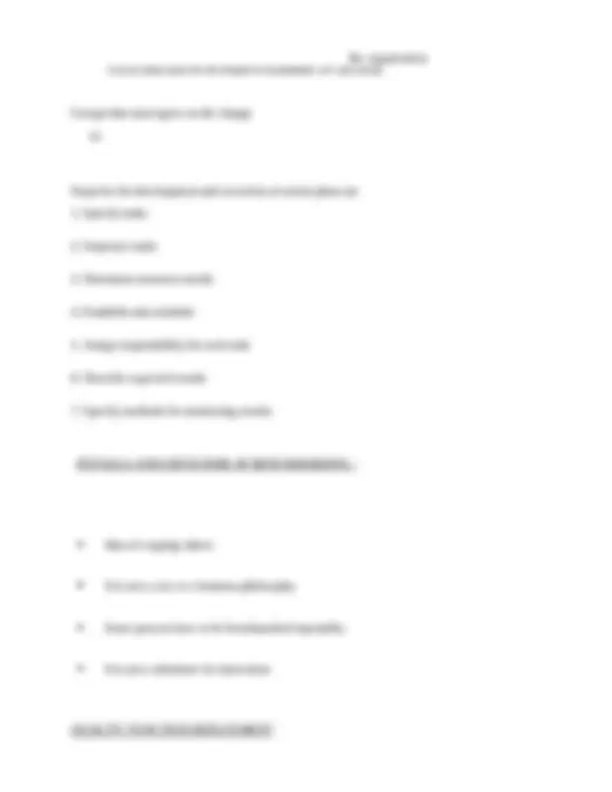
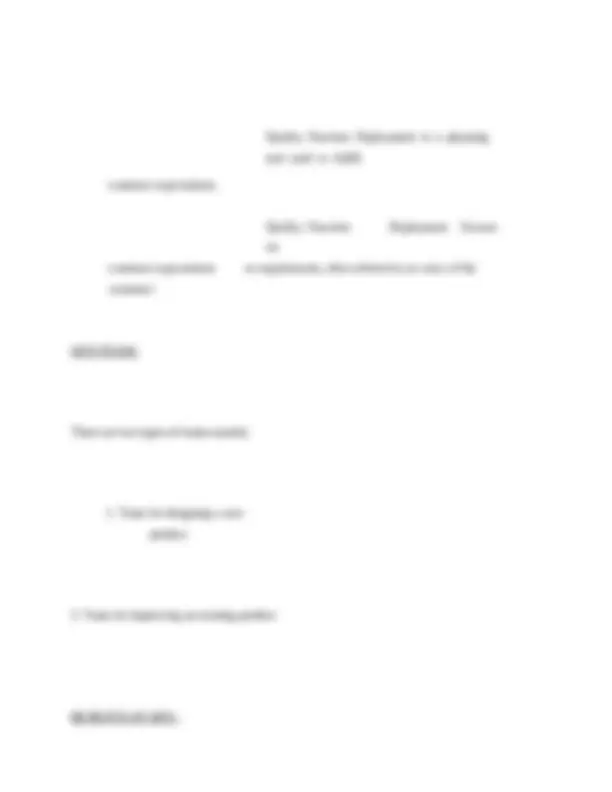
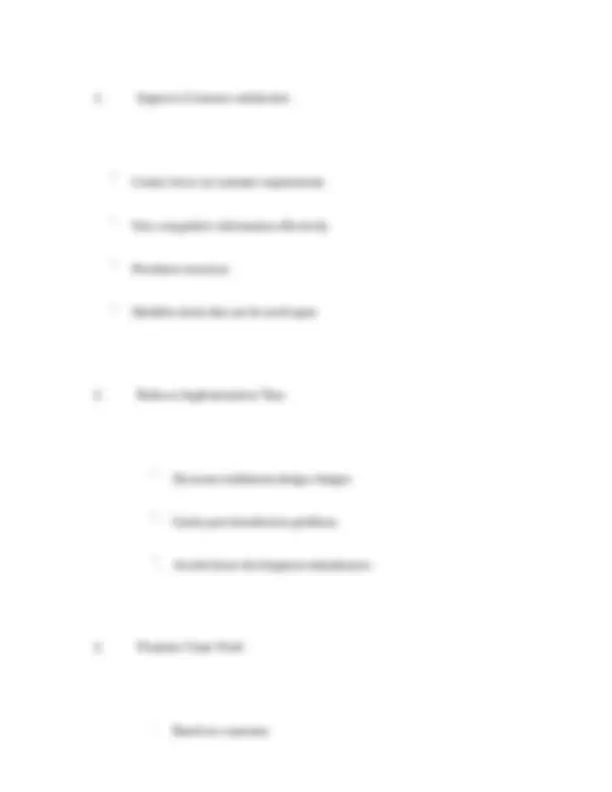

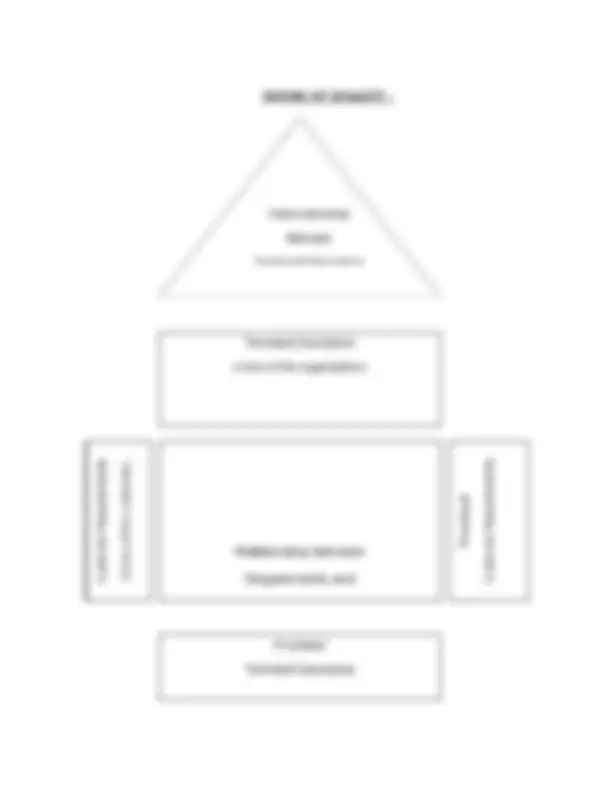
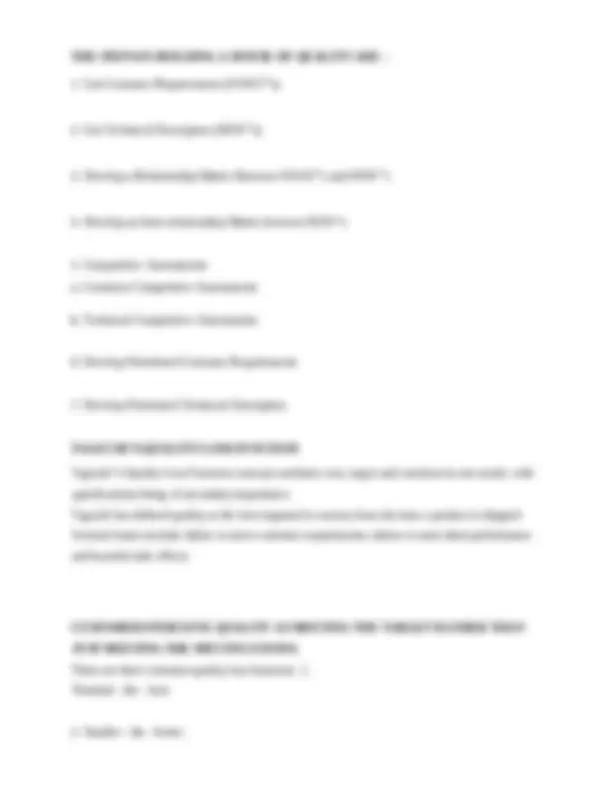
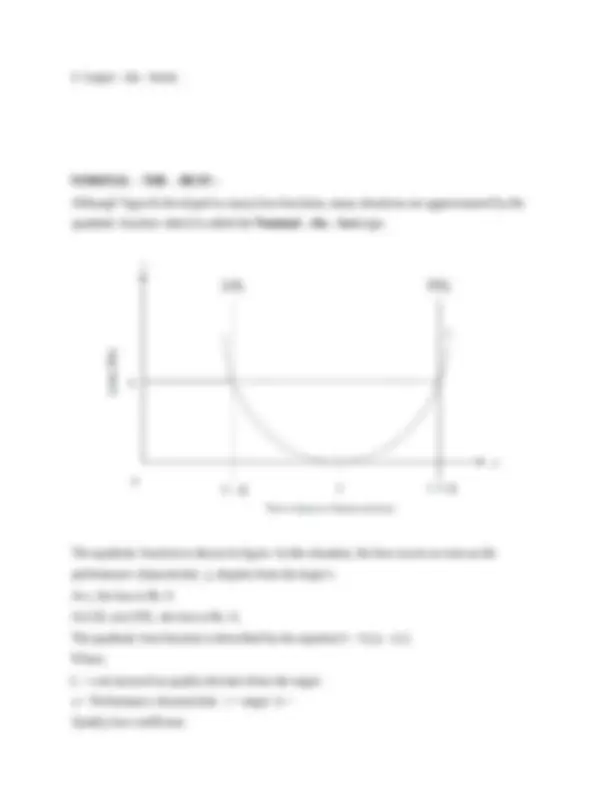
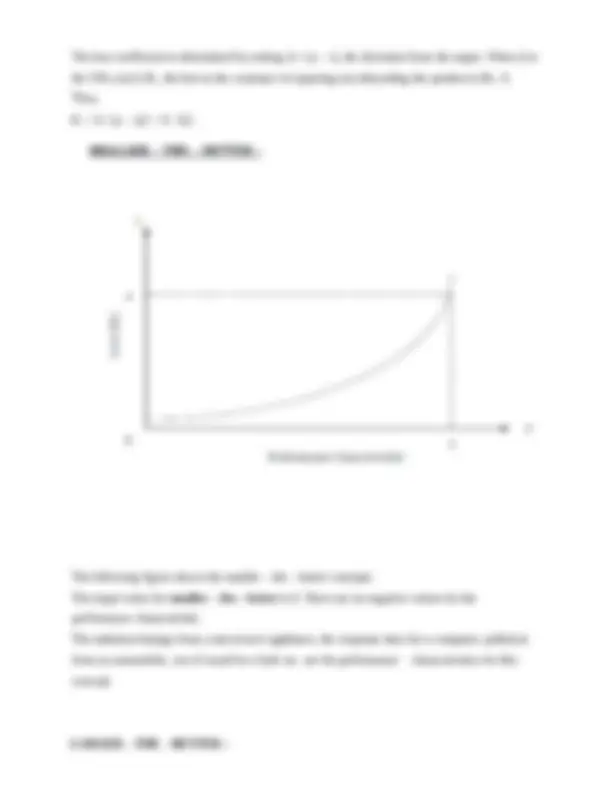
Study with the several resources on Docsity
Earn points by helping other students or get them with a premium plan
Prepare for your exams
Study with the several resources on Docsity
Earn points to download
Earn points by helping other students or get them with a premium plan
Community
Ask the community for help and clear up your study doubts
Discover the best universities in your country according to Docsity users
Free resources
Download our free guides on studying techniques, anxiety management strategies, and thesis advice from Docsity tutors
Introduction,service quality,jurans philosophy,principle of TQM ,e.t.c
Typology: Lecture notes
Limited-time offer
Uploaded on 11/30/2020
4.3
(3)2 documents
1 / 166
This page cannot be seen from the preview
Don't miss anything!
On special offer
Contact;Sodhiambo996@gmail.com LECTURE NOTES BAM 2201 – TOTAL QUALITY MANAGEMENT UNIT I INTRODUCTION Definition of quality – Dimensions of quality – Quality planning – Quality costs – Analysis techniques for quality costs – Basic concepts of total quality management – Historical review – Principles of TQM – Leadership – Concepts – Role of senior management – Quality council – Quality statements –Strategic planning – Deming philosophy – Barriers to TQM implementation. UNIT II TQM PRINCIPLES Customer satisfaction – Customer perception of quality – Customer complaints – Service quality – Customer retention – Employee involvement – Motivation, empowerment, teams, recognition and reward – Performance appraisal – Benefits – Continuous process improvement – Juran trilogy – PDSA cycle – 5S – Kaizen – Supplier partnership – Partnering – Sourcing – Supplier selection – Supplier rating – Relationship development – Performance measures – Basic concepts – Strategy –Performance measure. UNIT III STATISTICAL PROCESS CONTROL (SPC) The seven tools of quality – Statistical fundamentals – Measures of central tendency and dispersion – Population and sample – Normal curve – Control charts for variables and attributes – Process capability – Concept of six sigma – New seven management tools. UNIT IV TQM TOOLS
Benchmarking – Reasons to benchmark – Benchmarking process – Quality Function Deployment(QFD) – House of quality – QFD process – Benefits – Taguchi quality loss function – Total Productive Maintenance (TPM) – Concept – Improvement needs – FMEA – Stages of FMEA. UNIT V QUALITY SYSTEMS Need for ISO 9000 and other quality systems – ISO 9000:2000 Quality system – Elements – Implementation of quality system – Documentation – Quality auditing – TS 16949 – ISO 14000 –Concept
Total Quality Management (TQM) is an enhancement to the traditional way of doing business. Total - Made up of the whole Quality - Degree of Excellence a Product or Service provides. Management - Art of handling, controlling, directing etc. TQM is the application of quantitative methods and human resources to improve all the processes within an organization and exceed CUSTOMER NEEDS now and in the future.
Conformance Meeting specifications or industry standards, workmanship Reliability unit to fail Consistency of performance over time, average time of the Durability Useful life, includes repair Service Resolution of problems and complaints, ease of repair Response dealer Human – to – human interface, such as the courtesy of the Aesthetics Sensory characteristics, such as exterior finish Reputation ranked first Past performance and other intangibles, such as being QUALITY PLANNING The following are the important steps for quality planning.
Operations (Product or Service) Failure Costs
Index Numbers are often used in a variety of applications to measure prices, costs (or) other numerical quantities and to aid managers in understanding how conditions in one period compare with those in other periods. Cost Index in quarter t = (Cost in quarter t / Base period cost) x 100 TREND ANALYSIS : Good visual aids are important communication tools. Graphs are particularly useful in presenting comparative results to management. T rend Analysis is one where Time-to-Time comparisons can be made which illustrates
Supplier teaming Training of employees Inventory management Communication Quality cost.
Problem solving discipline Interpersonal skills Teamwork Quality improvement process. PRINCIPLES OF TQM:- Customer‟s requirements must be met the first time, every time. There must be agreed requirements, for both internal and external customers. Everybody must be involved, from all levels and across all functions. Regular communication with staff at levels is must. Two way communication at all levels must be promoted. Identifying training needs and relating them with individual capabilities and requirements is must. Top management‟s participation and commitment is must. A culture of continuous improvement must be established. Emphasis should be placed on purchasing and supplier management Every job must add value. Quality improvement must eliminate wastes and reduce total cost. There must be a focus on the prevention of problems. A culture of promoting creativity must be established. Performance measure is a must at organization, department and individual levels. It helps to asses and meet objectives of quality. There should be focus on team work.
Procurement Partnership Price Life cycle costs, DEFINITION PRODUCT ORIENTED CUSTOMER ORIENTED Manager‟s Role Plan, assign, control Delegate, coach, and enforce GURUS OF TQM : facilitate and mentor SHEWHART - Control chart theory PDCA Cycle DEMING - Statistical Process Control JURAN - Concepts of SHEWHART Return on Investment ( ROI ) FEIGANBAUM - Total Quality Control Management involvement Employee involvement
Company wide quality control ISHIKAWA - Cause and Effect Diagram Quality Circle concept CROSBY - “Quality is Free” Conformance to requirements TAGUCHI - Loss Function concept Design of Experiments OBSTACLES IN IMPLEMENTING TQM : Lack of Management Commitment Inability to change Organizational culture Improper planning Lack of continuous training and education Incompatible organizational structure and isolated individuals and departments Ineffective measurement techniques and lack of access to data and results
The customers first. Value people. Built supplier partnership. Empower people. Demonstrate involvement/commitment. Strive for excellence. Explain and deploy policy. Improve communication. Promote teamwork. Benchmark continuously. Establish system. Encourage collaboration. LEADERSHIP ROLES:-
16.Become coaches and cheer leaders to implement TQM. 17.Generate enthusiasm for TQM activities. 18.Visit other companies to observe TQM functioning. 19.Attend TQM training programme. 20.Teach others for the betterment of society and the surroundings. QUALITY COUNCIL A quality council is established to provide overall direction. The council is composed of Chief Executive Officer Senior Managers Coordinator or Consultant A representative from the Union Duties of the council are Develop the core values, vision statement, mission statement and quality policy statement Develop the strategic long term plan with goals and Annual Quality improvement Program with objectives Create the total education and training plan